汽车产品开发流程
汽车部新产品开发流程PPT课件
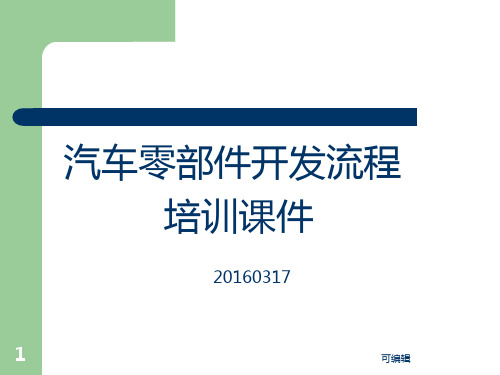
可编辑
12
岗位职责:
三、开发:
1、产品图面评审;
2、主导新产品开发全过程;
3、产品技术规范;
4、产品cc/sc清单;
5、PFMEA编制;
6、设变管理及设变通知单发放;
7、主导新产品试做;
8、试做问题点对策及追踪;
9、BOM表;
10、OTS资料提交可编辑
13
岗位职责:
四、品质:
1、检具规划、执行、改善; 2、试验大纲编制及执行; 3、初期品质管理计划制定(初流管理); 4、试作品质评定; 5、参与新产品试做全过程; 6、供应商OTS,PPAP资料的取得; 7、主导项目PPAP资料的提交及审批;
可编辑
26
工作定时 汇报
进度怎么样?有哪些方面的问题( 成本、资金、时间、人力……)需
要我来解决?
可编辑
27
3、过程确认阶段
可编辑
28
过程确认阶段
项目\开发需要完成的工作:
1、设变管控; 2、试生产通知单; 3、试生产问题整改; 4、客户端问题关闭; 5、过程流程图更新; 6、 PFMEA更新; 7、BOM表更新;
9、过程审核;
可编辑
30
过程确认阶段
制造需要完成的工作: 1、生产产地确认; 2、试制试生产; 3、作业指导书更新; 4、人员培训;
可编辑
31
过程确认阶段
生物管需要完成工作: 1、供应商交货周期调查; 2、客户订单接收及物料按时交付; 3、安排试生产; 4、人员培训
可编辑
32
过程确认阶段
工装\模具需要完成的工作: 1、工装调试、整改完成,满足正常生产; 2、模具试制、整改完成,满足正常生产;
可编辑
汽车零部件产品开发流程

汽车零部件产品开发流程1.需求分析:在汽车零部件产品开发过程中,首先需要进行市场调研和需求分析。
通过了解市场需求和竞争对手的产品情况,确定产品的需求和定位,明确产品的功能、性能、质量标准、成本限制以及安全要求等。
2.概念设计:根据需求分析的结果,进行概念设计。
这一阶段包括以下内容:a.设计思路的确定:确定产品的总体设计思路,包括外观、结构、材料等。
b.执行评估:通过计算和仿真等手段,评估产品的可行性和性能。
3.详细设计:在概念设计阶段确定后,需要进行详细设计。
这一阶段包括以下内容:a.零部件的结构设计:确定零部件的具体结构,包括尺寸、形状、连接方式等。
b.零部件的材料选择:选择合适的材料,满足产品的性能和质量要求。
c.零部件的装配设计:确定零部件之间的装配方式和工艺。
4.原型制作:通过三维打印、模具制作等方式制作产品的原型。
原型通常用于测试验证产品的可行性、性能和质量。
5.测试验证:进行产品的各种测试验证,包括性能测试、可靠性测试、安全性测试等。
根据测试结果进行产品的优化和改进。
6.生产制造:根据产品设计和测试验证的结果,进行产品的生产制造。
这包括制定生产计划、采购零部件、生产装配、质量控制等。
7.市场推广:产品生产完成后,进行市场推广。
这包括制定市场营销策略、推广产品特点、与销售渠道合作等方式。
8.售后服务:对于汽车零部件产品来说,售后服务非常重要。
提供及时的售后服务可以增加客户对产品的满意度和忠诚度,同时也可以收集用户的反馈信息,为产品的改进提供参考。
汽车零部件产品开发流程是一个复杂的过程,需要涉及到多个专业领域的知识和技术,包括市场调研、设计、工程制图、材料选择、制造工艺、测试验证等。
以上是汽车零部件产品开发的主要流程,但实际情况可能因不同的企业、产品和市场需求而有所不同。
汽车产品开发流程

汽车产品开发流程汽车产品开发是一个复杂的过程,需要经过多个阶段的设计、测试和验证。
这个过程需要涉及到多个部门和团队的协作,包括设计师、工程师、测试人员和市场营销人员等。
下面将介绍汽车产品开发的流程。
第一阶段:概念设计概念设计是汽车产品开发的第一阶段,这个阶段的目的是确定产品的基本设计方向和特点。
在这个阶段,设计师和工程师会进行大量的市场调研和用户需求分析,以确定产品的定位和目标用户。
然后,他们会进行初步的设计和模型制作,以便在后续的阶段进行测试和验证。
第二阶段:详细设计在概念设计阶段确定了产品的基本方向和特点之后,就需要进入详细设计阶段。
在这个阶段,设计师和工程师会进行更加详细的设计和模型制作,以便进行更加精确的测试和验证。
这个阶段需要涉及到多个方面的设计,包括外观设计、内饰设计、底盘设计、动力系统设计等。
第三阶段:工程开发在详细设计阶段完成之后,就需要进入工程开发阶段。
在这个阶段,工程师会进行更加深入的设计和制造,以便进行更加精确的测试和验证。
这个阶段需要涉及到多个方面的工程开发,包括零部件制造、装配、测试和验证等。
第四阶段:测试和验证在工程开发阶段完成之后,就需要进行测试和验证。
在这个阶段,测试人员会对汽车进行各种测试和验证,以确保汽车的性能和安全性能符合要求。
这个阶段需要涉及到多个方面的测试和验证,包括性能测试、安全测试、耐久性测试等。
第五阶段:生产和销售在测试和验证阶段完成之后,就需要进入生产和销售阶段。
在这个阶段,汽车制造商会进行汽车的生产和销售,以满足市场需求。
这个阶段需要涉及到多个方面的生产和销售,包括零部件制造、装配、销售和售后服务等。
总结汽车产品开发是一个复杂的过程,需要经过多个阶段的设计、测试和验证。
这个过程需要涉及到多个部门和团队的协作,包括设计师、工程师、测试人员和市场营销人员等。
只有经过严格的测试和验证,才能确保汽车的性能和安全性能符合要求,从而满足市场需求。
汽车行业流程体系
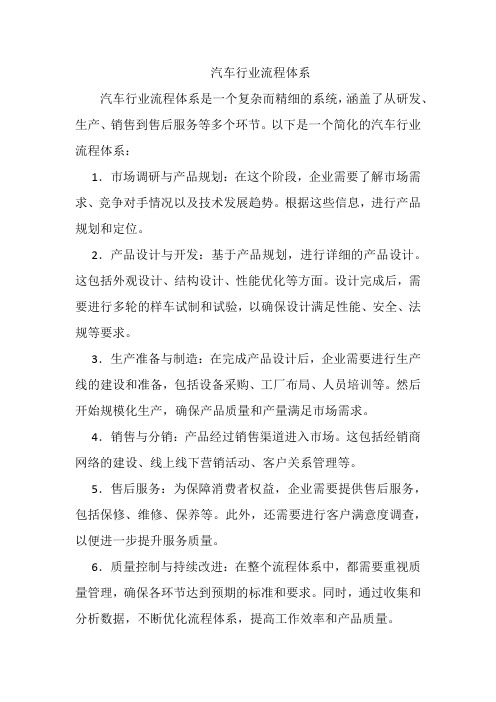
汽车行业流程体系
汽车行业流程体系是一个复杂而精细的系统,涵盖了从研发、生产、销售到售后服务等多个环节。
以下是一个简化的汽车行业流程体系:
1.市场调研与产品规划:在这个阶段,企业需要了解市场需求、竞争对手情况以及技术发展趋势。
根据这些信息,进行产品规划和定位。
2.产品设计与开发:基于产品规划,进行详细的产品设计。
这包括外观设计、结构设计、性能优化等方面。
设计完成后,需要进行多轮的样车试制和试验,以确保设计满足性能、安全、法规等要求。
3.生产准备与制造:在完成产品设计后,企业需要进行生产线的建设和准备,包括设备采购、工厂布局、人员培训等。
然后开始规模化生产,确保产品质量和产量满足市场需求。
4.销售与分销:产品经过销售渠道进入市场。
这包括经销商网络的建设、线上线下营销活动、客户关系管理等。
5.售后服务:为保障消费者权益,企业需要提供售后服务,包括保修、维修、保养等。
此外,还需要进行客户满意度调查,以便进一步提升服务质量。
6.质量控制与持续改进:在整个流程体系中,都需要重视质量管理,确保各环节达到预期的标准和要求。
同时,通过收集和分析数据,不断优化流程体系,提高工作效率和产品质量。
汽车行业流程体系的各个环节紧密相连,相互影响。
企业需要建立起完善的流程体系,确保各环节的高效协同,以提升整体竞争力。
同时,还需要不断适应市场变化和技术发展,持续优化和创新流程体系,以满足消费者日益增长的需求。
汽车行业产品开发流程
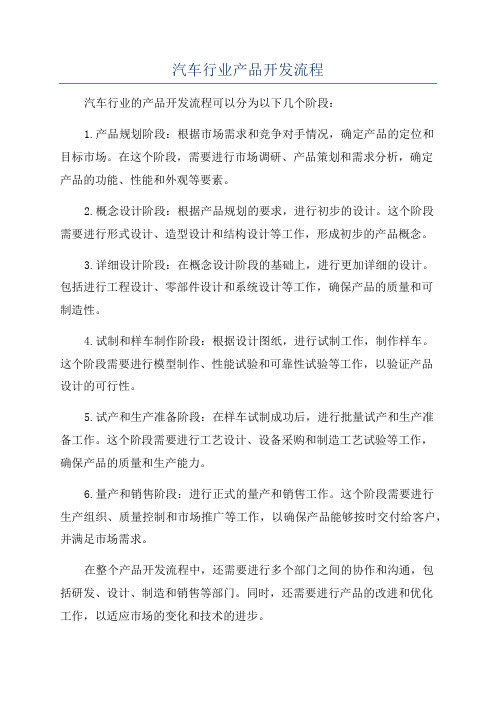
汽车行业产品开发流程汽车行业的产品开发流程可以分为以下几个阶段:1.产品规划阶段:根据市场需求和竞争对手情况,确定产品的定位和目标市场。
在这个阶段,需要进行市场调研、产品策划和需求分析,确定产品的功能、性能和外观等要素。
2.概念设计阶段:根据产品规划的要求,进行初步的设计。
这个阶段需要进行形式设计、造型设计和结构设计等工作,形成初步的产品概念。
3.详细设计阶段:在概念设计阶段的基础上,进行更加详细的设计。
包括进行工程设计、零部件设计和系统设计等工作,确保产品的质量和可制造性。
4.试制和样车制作阶段:根据设计图纸,进行试制工作,制作样车。
这个阶段需要进行模型制作、性能试验和可靠性试验等工作,以验证产品设计的可行性。
5.试产和生产准备阶段:在样车试制成功后,进行批量试产和生产准备工作。
这个阶段需要进行工艺设计、设备采购和制造工艺试验等工作,确保产品的质量和生产能力。
6.量产和销售阶段:进行正式的量产和销售工作。
这个阶段需要进行生产组织、质量控制和市场推广等工作,以确保产品能够按时交付给客户,并满足市场需求。
在整个产品开发流程中,还需要进行多个部门之间的协作和沟通,包括研发、设计、制造和销售等部门。
同时,还需要进行产品的改进和优化工作,以适应市场的变化和技术的进步。
在汽车行业,产品开发流程一般较为复杂和漫长,涉及到多个方面的知识和技能。
因此,汽车制造商通常会投入大量的人力、物力和财力,以保证产品的质量和竞争力。
总体而言,汽车行业的产品开发流程包括产品规划、概念设计、详细设计、试制和样车制作、试产和生产准备、量产和销售等阶段,其中每个阶段都有具体的工作内容和任务。
通过科学的产品开发流程,汽车制造商能够有效地开发出具有竞争力的产品,满足市场的需求。
汽车研发流程

汽车研发流程汽车研发流程之一:一、方案策划阶段一个全新车型的开发需要几亿甚至十几亿的大量资金投入,投资风险非常大,如果不经过周密调查研究与论证,就草率上马新项目,轻则会造成产品先天不足,投产后问题成堆;重则造成产品不符合消费者需求,没有市场竞争力。
因此市场调研和项目可行性分析就成为了新项目至关重要的部分。
通过市场调研对相关的市场信息进行系统的收集、整理、纪录和分析,可以了解和掌握消费者的汽车消费趋势、消费偏好和消费要求的变化,确定顾客对新的汽车产品是否有需求,或者是否有潜在的需求等待开发,然后根据调研数据进行分析研究,总结出科学可靠的市场调研报告,为企业决策者的新车型研发项目计划,提供科学合理的参考与建议。
汽车市场调研包括市场细分、目标市场选择、产品定位等几个方面。
项目可行性分析是在市场调研的基础上进行的,根据市场调研报告生成项目建议书,进一步明确汽车形式(也就是车型确定是微型车还是中高级车)以及市场目标。
可行性分析包括外部的政策法规分析、以及内部的自身资源和研发能力的分析,包括设计、工艺、生产以及成本等方面的内容。
在完成可行性分析后,就可以对新车型的设计目标进行初步的设定,设定的内容包括车辆形式、动力参数、底盘各个总成要求、车身形式及强度要求等。
将初步设定的要求发放给相应的设计部门,各部门确认各个总成部件要求的可行性以后,确认项目设计目标,编制最初版本的产品技术描述说明书,将新车型的一些重要参数和使用性能确定下来。
在方案策划阶段还有确定新车型是否开发相应的变形车,确定变形车的形式以及种类。
项目策划阶段的最终成果是一份符合市场要求,开发可行性能够保证得到研发各个部门确认的新车型设计目标大纲。
该大纲明确了新车型的形式、功能以及技术特点,描述了产品车型的最终定位,是后续研发各个过程的依据和要求,是一份指导性文件。
汽车研发流程之二:二、概念设计阶段概念设计阶段开始后就要制定详细的研发计划,确定各个设计阶段的时间节点;评估研发工作量,合理分配工作任务;进行成本预算,及时控制开发成本;制作零部件清单表格,以便进行后续开发工作。
汽车v型开发流程

汽车v型开发流程汽车V型开发流程。
汽车V型开发流程是指汽车产品开发的整个生命周期过程,它包括了从产品概念形成到产品最终交付使用的全过程。
在汽车行业中,V型开发流程已经成为了一种标准的产品开发模式,它以其严谨的流程和规范的管理方式,为汽车产品的开发提供了有力的支持。
首先,产品概念阶段是汽车V型开发流程的起点。
在这个阶段,产品经理和市场分析师会对市场需求进行调研,确定产品的定位和目标用户群体。
同时,工程师团队也会进行技术可行性分析,确定产品的技术路线和关键技术方案。
这一阶段的主要任务是明确产品的功能和性能指标,为后续的设计和开发工作奠定基础。
接下来是需求分析和系统设计阶段。
在这个阶段,产品经理会与用户进行深入的沟通,收集用户需求,并将其转化为产品的功能需求和性能需求。
同时,系统工程师会对产品进行系统设计,确定产品的整体架构和各个子系统之间的接口关系。
这一阶段的主要任务是明确产品的功能和性能需求,为后续的详细设计和开发工作提供依据。
然后是详细设计和开发阶段。
在这个阶段,各个子系统的设计团队会根据系统设计的要求,分别进行详细设计和开发工作。
同时,测试团队也会进行测试用例的设计和测试环境的搭建。
这一阶段的主要任务是完成产品各个子系统的详细设计和开发工作,为后续的集成和测试工作做好准备。
接着是集成和测试阶段。
在这个阶段,各个子系统的设计团队会进行集成测试,验证各个子系统之间的接口和交互关系。
同时,测试团队也会进行系统测试,验证产品的功能和性能指标是否符合需求。
这一阶段的主要任务是完成产品各个子系统的集成和测试工作,为产品的交付使用做好准备。
最后是产品交付和使用阶段。
在这个阶段,产品经理会与用户进行产品交付和培训,确保用户能够正确地使用产品。
同时,售后服务团队也会进行产品的售后服务和维护工作,确保产品能够稳定地运行。
这一阶段的主要任务是完成产品的交付和使用,为产品的市场推广和销售做好准备。
总的来说,汽车V型开发流程是一个从产品概念形成到产品最终交付使用的全过程,它包括了产品概念阶段、需求分析和系统设计阶段、详细设计和开发阶段、集成和测试阶段以及产品交付和使用阶段。
汽车行业产品开发流程

执行《商品企划与收益管理程序》
组 织 详 细 投 资 收 益 分 析
组织项目策划—项目目 标、可行性分析]项目 计划、项目组织机构
车型 方案 最终 批准
车型方案批准
评审、决策商品 收益分析
Y N
P2: 产品定 义完成, 项目工 程启动
批准 详细 投资 收益 分析 报告
批准 拟定供应商批准
整车目标成本达成活动展开
质量管理体系文件 Ⅰ级全新平台产品开发流程
发布日期: 生效日期: 编号:xxxx 版本:01 替代版本:/ 页号:1/7 附录:3
编制/日期 : 编制负责人/日期:
审核/日期: 批准/日期:
修
编制/修订原因说明:新建。 颁布说明:
订
页
1、新产品开发体系分:新产品开发、重大商品改进、一般商品改进三大类,六个级别开发体系;三类六 级产品开发体系整体描述将在《产品开发手册》里进行阐述; 2、本流程为新产品开发系统最高级开发流程(Ⅰ级开发中全新平台开发);而Ⅰ级开发中的换代产品开 发、变型开发、特种车系列/先进性技术展示车开发仅是该过程的简化,其内容可在具体的项目计划、项 目定义与策划中进一步明确; 3、对新产品开发中的:II级核心部件开发、III级重要部件开发,在《核心重要部件开发管理程序》中予 以描述;对重大商品改进中IV级重要部件开发,在《重大商品改进程序》中予以描述;对一般商品改进的 V级拓展开发、VI级商品改进开发,在《一般商品改进程序》中予以描述; 4、本流程以Ⅰ级开发中全新平台开发为模板阐述了全新平台产品的开发过程;主要体现的是商品研发各 阶段主责单位的主要工作内容及过程标志性节点进程,仅对各阶段主要及关键的工作进行描述,同时确定 了各进程的上、下序接口关系,及输入/输出关系;主责单位与参与单位的工作详细内容请见《产品开发 手册》; 3、对流程中流程时间,因目前项目方面经验不足,各任务进程的时间难以明确,因而流程中各节点时间 及任务时间跨度目前暂为空缺,后续根据多个项目的经验在流程持续改进优化过程中予以制定; 5、某一开发项目属于何种类型,哪个级别,应由各有关业务部门在项目启动时,根据项目内容而定。 6、本流程先后经过公司各个部门内部充分讨论、评审、修订,并向公司领导汇报修订完善后发布试运 行,发布后将通过适当方式对相关人员进行培训,以利执行。 7、各主责单位需在此流程的基础上建立自己的控制流程:《产品设计控制流程》、《生产准备控制流程 》、《供应上开发与管理控制流程》、《新品上市营销与服务控制流程》、《新品上市初期流动质量保证 流程》、《商品企划流程》作为该流程的支持流程,以便商品研发过程中各阶段主责单位的主要工作内容 及过程标志性节点进程等得到细化和实施,确保本流程的落实。 原章节号 现章节号 修订内容说明 备注
乘用车开发流程
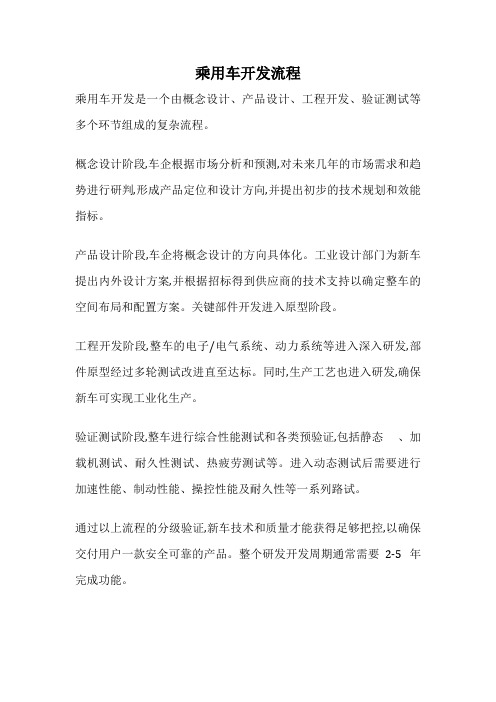
乘用车开发流程
乘用车开发是一个由概念设计、产品设计、工程开发、验证测试等多个环节组成的复杂流程。
概念设计阶段,车企根据市场分析和预测,对未来几年的市场需求和趋势进行研判,形成产品定位和设计方向,并提出初步的技术规划和效能指标。
产品设计阶段,车企将概念设计的方向具体化。
工业设计部门为新车提出内外设计方案,并根据招标得到供应商的技术支持以确定整车的空间布局和配置方案。
关键部件开发进入原型阶段。
工程开发阶段,整车的电子/电气系统、动力系统等进入深入研发,部件原型经过多轮测试改进直至达标。
同时,生产工艺也进入研发,确保新车可实现工业化生产。
验证测试阶段,整车进行综合性能测试和各类预验证,包括静态、加载机测试、耐久性测试、热疲劳测试等。
进入动态测试后需要进行加速性能、制动性能、操控性能及耐久性等一系列路试。
通过以上流程的分级验证,新车技术和质量才能获得足够把控,以确保交付用户一款安全可靠的产品。
整个研发开发周期通常需要2-5年完成功能。
汽车产品开发流程

汽车产品开发流程1.概念开发阶段:概念开发阶段是汽车产品开发的第一步,也是最为重要的阶段之一、在这个阶段,团队需要进行市场调研和产品规划,确定产品的核心理念、目标市场、定位和竞争策略等。
同时,还需要进行初步的设计和草图的绘制,以便在后续的阶段继续完善和优化。
2.设计开发阶段:设计开发阶段是围绕着产品设计而展开的。
在这个阶段,设计师将概念转化为具体的设计方案,并进行详细的设计和制造工艺规划。
同时,还需要进行各种模型和原型的制作和测试,以确保设计的可行性和质量。
这个阶段还需要团队与供应商和合作伙伴进行密切的沟通和协作,保证设计的顺利进行。
3.工程开发阶段:工程开发阶段是在设计阶段的基础上进行的,主要涉及到产品的工程参数和技术开发。
在这个阶段,工程师和技术人员需要进行各种工程计算和分析,进行材料选型和工艺研究,以确保产品的安全性和性能。
同时,还需要进行各种试验和验证,以确保产品能够满足市场和消费者的需求。
4.生产开发阶段:生产开发阶段是将设计和工程开发的结果转化为实际产品的过程。
在这个阶段,团队需要进行生产设备的采购和调试,制定生产工艺和流程,培训生产人员,并进行小批量和大规模的试生产。
同时,还需要进行质量控制和检验,以确保产品的质量稳定和生产效率。
5.市场推广阶段:市场推广阶段是将产品推向市场的重要阶段。
在这个阶段,企业需要进行市场营销和品牌宣传,制定销售策略和渠道管理。
同时,还需要进行产品售后服务和用户反馈的收集和处理,以不断改进和提升产品。
以上是汽车产品开发的主要流程和阶段。
每个阶段都需要不同的团队和专业的知识,需要紧密合作和沟通,以确保产品从概念到实际产品的顺利过渡。
同时,还需要考虑到市场和技术的变化以及消费者的需求,不断进行创新和改进,才能够在竞争激烈的市场中占据优势。
主机厂整车开发流程
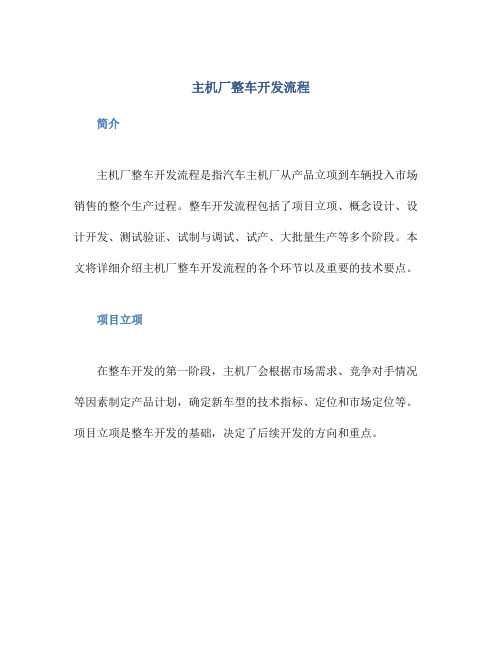
主机厂整车开发流程简介主机厂整车开发流程是指汽车主机厂从产品立项到车辆投入市场销售的整个生产过程。
整车开发流程包括了项目立项、概念设计、设计开发、测试验证、试制与调试、试产、大批量生产等多个阶段。
本文将详细介绍主机厂整车开发流程的各个环节以及重要的技术要点。
项目立项在整车开发的第一阶段,主机厂会根据市场需求、竞争对手情况等因素制定产品计划,确定新车型的技术指标、定位和市场定位等。
项目立项是整车开发的基础,决定了后续开发的方向和重点。
在项目立项之后,主机厂进行概念设计,确定车辆整体结构、动力总成和车身外观等。
概念设计阶段需要综合考虑外部市场需求、内部技术条件、成本控制等多方面因素。
设计开发设计开发是整车开发中最为关键的阶段。
在这个阶段,主机厂要进行详细的工程设计,包括车身设计、底盘设计、动力总成设计等。
设计开发需要高度的工程技术支持,包括CAD软件、仿真软件等。
测试验证在设计开发完成之后,主机厂会进行测试验证,包括底盘性能测试、碰撞测试、整车试验等。
测试验证是确保车辆符合技术标准和安全标准的重要环节。
试制与调试阶段是整车开发中的关键阶段之一。
在这个阶段,主机厂会进行小批量车辆的试制和试验,验证车辆设计的合理性和可行性。
同时,对车辆的性能、安全等方面进行调试和优化。
试产试产阶段是整车开发的最后一道关卡。
在这个阶段,主机厂会进行小规模的批量生产,验证生产线的稳定性和车辆的质量稳定性。
试产的成功与否直接决定了车辆是否可以顺利进行大批量生产。
大批量生产大批量生产是整车开发的最终目标。
一旦试产成功,主机厂就可以进行大规模的车辆生产。
在生产过程中,主机厂还需要实施质量控制、成本控制等措施,确保车辆质量和成本的稳定性。
结语主机厂整车开发流程是一个复杂而严谨的过程,需要主机厂精心组织和管理,同时还需要各个部门的密切合作。
只有在每个环节都做到严格把控和优化,主机厂才能成功推出市场合格的新车型。
APQP产品开发流程与管理(汽车行业)

供应商选择管理与质 量管理
产品开发阶段 供应商选择管理与质量管理 1、供应商选择 2、供应商认可 3、供应商管理
产品开发阶段 供应商选择管理与质量管理
有效利用和管理供应商很大程度决定了产品开发的 成功与否。 供应商:
在一个特定长的时间内与客户就某些产品和/服务达成一定 的承诺和/协议,包括信息共享,风险和利益共享。
FMEA常识
FMEA是什么 ?
FMEA是一种可靠性设计的重要方法,制造过程及服务还未到达顾客已知的或潜 在的失效问题等. 是分析系统中每一产品所有可能产生的故障模 式及其对系统造成的所有可能影响,并按每一 个故障模式的严重程度、检测难易程度以及发生 频度予以分类的一种归纳分析方法。
关系:
合作伙伴、 长期、短期、双赢
依据公司发展、销售目标建立供应商体系
产品开发阶段 供应商选择管理与质量管理
一、供应商选择
1.分类 2. 对供应商的考察 3. 评价的考评因素 4. 供应商现场审核
产品开发阶段 供应商选择管理与质量管理
二、供应商认可 1、符合质量目标 2、价格优势 3、服务体系
产品开发阶段 供应商选择管理与质量管理
产品设计阶段 Detail Design
在发动机上的应用: 1.电子控制喷油装置 2.电子点火装置(ESA) 电子技术在底盘上的应用: 1. 电控自动变速器(ECAT) 2. 防抱死制动系统(ABS) 3.电子转向助力系统 4.适时调节的自适应悬挂系统 5.常速巡行自动控制系统(CCS) 6 . 倒车雷达
产品设计阶段 Detail Design
工艺同步工程
PSE(Process Simultaneous Engineering)
车身结构 校核、分析 同步工程 介入 内、外饰模 型数据採集
汽车开发流程(策划→设计→试制→生产)

SI
SC
PH
启动
战略策划
战略决策
比例及硬点
PA
项目执行批准
ST
表面提交
PT
PR
CC
LR
LS
J1
CP
FS
整车
系统
部件
动力系统设计完成
产品准备
样车制作
变更冻结
试产准备
投产签署
量产开始
项目总结
福特产品开发系统 Ford Product Development System
宝马产品开发同步图
宝马作为国际顶尖汽车公司,花费了10年时间来进行流程,使其流程的合理性与先进性处于国际领先地位;其同步图作为流程的纲领性文件甚至已经成为同行业的一个范本.它以时间为横轴,以各系统子流程为纵轴,在一张图上清楚的表明了产品开发的时间周期和各系统的先后顺序;并成立公司级别的产品开发管理委员会进行监督管理。宝马公司设有数十人的流程部,负责产品开发流程的监督管理和持续改进。
性能设计及验证
电子电器
公告
3C
环保
海外体系认证
样车试制
试验
虚拟验证
产品认证
设计验证
研究院为主
研究院辅助
造型设计
项目管理
汽车新产品开发
性能开发
结构开发
三维造型设计
二维造型设计
实体模型验证
整车产品开发业务中的工作分析
引言2:在整车产品开发业务中的工作分析-续
产品开发涵盖业务
工艺设计及制造工程
TTO连线
给用户创造独特的利益点技术领先,打造产品科技品牌市场最终领先者的基础
逆向开发
正向开发
双导向阶段
技术引导阶段
智能汽车 开发流程
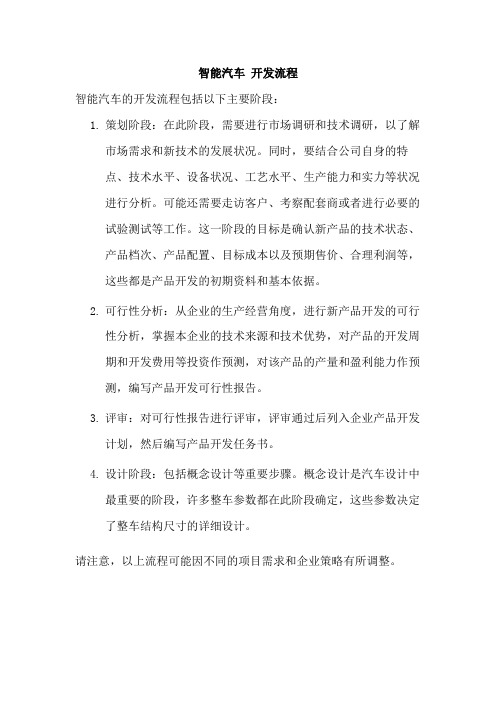
智能汽车开发流程
智能汽车的开发流程包括以下主要阶段:
1.策划阶段:在此阶段,需要进行市场调研和技术调研,以了解
市场需求和新技术的发展状况。
同时,要结合公司自身的特
点、技术水平、设备状况、工艺水平、生产能力和实力等状况进行分析。
可能还需要走访客户、考察配套商或者进行必要的试验测试等工作。
这一阶段的目标是确认新产品的技术状态、产品档次、产品配置、目标成本以及预期售价、合理利润等,这些都是产品开发的初期资料和基本依据。
2.可行性分析:从企业的生产经营角度,进行新产品开发的可行
性分析,掌握本企业的技术来源和技术优势,对产品的开发周期和开发费用等投资作预测,对该产品的产量和盈利能力作预测,编写产品开发可行性报告。
3.评审:对可行性报告进行评审,评审通过后列入企业产品开发
计划,然后编写产品开发任务书。
4.设计阶段:包括概念设计等重要步骤。
概念设计是汽车设计中
最重要的阶段,许多整车参数都在此阶段确定,这些参数决定了整车结构尺寸的详细设计。
请注意,以上流程可能因不同的项目需求和企业策略有所调整。
上海通用整车开发流程

上海通用整车开发流程一、需求调研和定义:在上海通用整车开发过程中,首先需要进行市场调研,了解消费者需求、竞争对手产品和市场趋势等信息,然后与市场部门、设计师和工程师等进行沟通和讨论,确定产品的基本特性和设计要求,最终形成整车的需求定义文档。
二、设计和开发:在需求定义的基础上,设计师和工程师团队开始进行整车的设计和开发工作。
设计团队进行外观设计、内饰设计和汽车配色方案等工作,工程师团队则进行车身结构设计、动力系统设计、底盘设计等技术性工作。
设计和开发过程中需要进行多次评审,优化设计,确保最终产品符合设计要求。
三、验证和测试:在设计和开发完成后,需要进行验证和测试工作,以确保整车的质量和性能。
验证和测试包括整车的原型制作和试验、工艺验证、安全性能验证、动力性能验证、悬挂系统验证等多个方面。
验证和测试过程中需要对结果进行分析,并进行必要的改进和优化。
四、试制和上市:在验证和测试通过后,开始进行试制和上市前准备工作。
试制过程中,需要生产少量的整车进行试驾和测试,以确认整车的可靠性和性能。
试制过程中也会进行产品的调整和改进。
同时,还需要进行相关证书和许可的申请。
试制完成后,整车正式进入上市准备阶段,包括营销宣传、销售培训、渠道建设等。
五、产销:整车上市后,上海通用将进行产销工作。
包括生产线建设和设备采购、生产流程安排和组织、供应链管理、销售渠道建设和销售推广等。
在整个产销过程中,还需要进行售后服务体系的建设和维护,以提供良好的售后服务。
六、售后服务:整车销售后,上海通用将提供全面的售后服务,包括保修、维修、配件供应、故障排除和召回等。
通过建立完善的售后服务网络和服务体系,使消费者能够获得及时、有效的售后支持。
总结:上海通用整车开发流程包括需求调研和定义、设计和开发、验证和测试、试制和上市、产销、售后服务等步骤。
通过从市场需求调研到整车设计和开发,再到验证和测试,再到试制和上市,最终营销推广和售后服务,上海通用能够提供高质量的整车产品,并为消费者提供完善的售前和售后支持,以满足消费者需求。
汽车零部件产品开发流程

汽车零部件产品开发流程一、需求分析阶段1.1 确定产品需求:确定新产品的类型、性能、规格等基本要求,以及市场需求和竞争对手情况。
1.2 市场调研:通过市场调研和用户反馈,收集相关信息,了解用户需求和市场趋势。
1.3 技术分析:对技术可行性进行评估,确定技术路线和方案。
二、设计阶段2.1 概念设计:根据需求分析结果,进行创意构思和方案设计,并绘制草图或模型。
2.2 详细设计:在概念设计的基础上,进行更加详细的设计工作,包括结构设计、材料选择等。
2.3 仿真验证:利用计算机辅助工具进行仿真验证,评估产品性能和可靠性。
三、开发阶段3.1 零部件制造:根据设计图纸或模型制造零部件,并进行质量检测。
3.2 组装调试:将零部件组装成整体产品,并进行调试和测试。
3.3 样品制作:制作样品并进行测试验证。
四、试产阶段4.1 试产准备:准备试产所需的设备、工具和人员等资源。
4.2 试产生产:进行试产生产,并进行质量检测和性能测试。
4.3 试产改进:根据试产结果,对产品进行改进和优化。
五、批量生产阶段5.1 工艺规程编制:制定产品的加工工艺规程,确保产品的一致性和稳定性。
5.2 生产准备:准备生产所需的设备、材料和人员等资源。
5.3 批量生产:进行批量生产,并进行质量检测和性能测试。
六、售后服务阶段6.1 售后服务准备:准备售后服务所需的设备、工具和人员等资源。
6.2 售后服务实施:对用户提出的问题进行解答和处理,并提供维修、保养等服务。
6.3 用户反馈收集:收集用户反馈意见,不断改进产品设计和售后服务。
七、总结汽车零部件产品开发流程是一个复杂而又漫长的过程,需要团队成员之间密切合作,充分利用各种技术手段,不断改进和优化产品设计。
通过以上流程可以使得汽车零部件产品开发更加科学化、规范化,从而提高产品质量和市场竞争力。
长安汽车开发流程

长安汽车开发流程随着汽车行业的迅猛发展,长安汽车作为中国汽车制造业的重要企业,其开发流程备受关注。
本文将介绍长安汽车的开发流程,使读者对其整个开发过程有一个清晰的了解。
一、需求调研和分析长安汽车开发流程的第一步是需求调研和分析。
在这个阶段,长安汽车会与市场调研机构合作,通过市场调研和用户反馈来确定消费者对于汽车的需求和期望。
这些需求和期望将成为后续开发的基础。
二、概念设计在需求调研和分析的基础上,长安汽车开始进行概念设计。
这个阶段的目标是确定汽车的整体设计理念和风格。
长安汽车的设计团队将进行创意激发和设计方案的探索,最终确定一个初步的概念设计。
三、产品设计概念设计确定后,长安汽车开始进行产品设计。
在这个阶段,设计师将对汽车的外观、内饰、功能配置等进行具体的设计。
设计师将运用CAD、CAE等工具进行建模和分析,确保设计的可行性和合理性。
四、零部件设计和制造产品设计确定后,长安汽车将进行零部件设计和制造。
长安汽车拥有强大的研发和制造能力,能够自主研发和制造汽车的各个零部件。
长安汽车会与供应商合作,确保零部件的质量和供应的及时性。
五、试制和测试零部件设计和制造完成后,长安汽车将进行试制和测试。
在这个阶段,长安汽车会生产少量样车进行试制,并进行各项测试,包括性能测试、安全测试、可靠性测试等。
通过测试,长安汽车能够发现并解决问题,确保产品的质量和可靠性。
六、量产和销售试制和测试通过后,长安汽车将进行量产和销售。
在这个阶段,长安汽车将进行大规模的生产,并推出市场。
长安汽车与经销商合作,通过各种渠道进行销售和推广。
同时,长安汽车将建立售后服务体系,提供优质的售后服务。
七、市场反馈和改进长安汽车开发流程的最后一步是市场反馈和改进。
通过与消费者的交流和反馈,长安汽车能够了解消费者对产品的评价和需求,及时进行改进和优化。
长安汽车将不断改进产品,以满足消费者的需求,并提高产品的竞争力。
总结长安汽车的开发流程包括需求调研和分析、概念设计、产品设计、零部件设计和制造、试制和测试、量产和销售、市场反馈和改进等步骤。
汽车产品开发流程
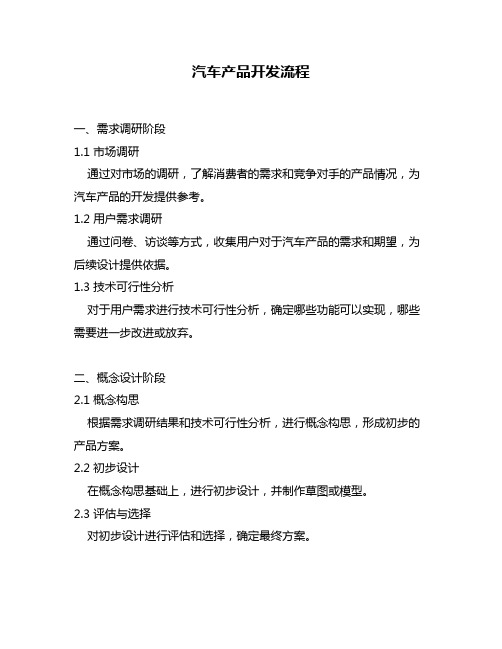
汽车产品开发流程一、需求调研阶段1.1 市场调研通过对市场的调研,了解消费者的需求和竞争对手的产品情况,为汽车产品的开发提供参考。
1.2 用户需求调研通过问卷、访谈等方式,收集用户对于汽车产品的需求和期望,为后续设计提供依据。
1.3 技术可行性分析对于用户需求进行技术可行性分析,确定哪些功能可以实现,哪些需要进一步改进或放弃。
二、概念设计阶段2.1 概念构思根据需求调研结果和技术可行性分析,进行概念构思,形成初步的产品方案。
2.2 初步设计在概念构思基础上,进行初步设计,并制作草图或模型。
2.3 评估与选择对初步设计进行评估和选择,确定最终方案。
三、详细设计阶段3.1 详细设计在最终方案基础上进行详细设计,并制作CAD图纸。
3.2 材料选用与零部件采购根据详细设计确定所需材料和零部件,并进行采购。
3.3 制造工艺设计根据详细设计确定制造工艺,并进行工艺设计。
四、制造阶段4.1 零部件制造根据材料选用和零部件采购结果,进行零部件的制造。
4.2 车身组装将各个零部件按照详细设计和制造工艺进行组装,形成汽车产品的基本结构。
4.3 车辆调试与测试对于组装完成的汽车产品进行调试和测试,确保其性能符合设计要求。
五、销售与售后服务阶段5.1 市场推广通过广告宣传、展会等方式,将汽车产品推向市场。
5.2 销售与交付对于客户的需求进行销售和交付。
5.3 售后服务提供售后服务,包括保修、维修等。
六、持续改进阶段6.1 用户反馈收集收集用户对于汽车产品的反馈和意见。
6.2 问题分析与改进方案确定对于用户反馈进行问题分析,并确定改进方案。
6.3 改进实施与评估实施改进方案,并对其效果进行评估。
七、总结与分享阶段7.1 总结经验对于整个汽车产品开发流程进行总结和经验积累。
7.2 分享成果分享汽车产品开发成果,为行业提供参考和借鉴。
- 1、下载文档前请自行甄别文档内容的完整性,平台不提供额外的编辑、内容补充、找答案等附加服务。
- 2、"仅部分预览"的文档,不可在线预览部分如存在完整性等问题,可反馈申请退款(可完整预览的文档不适用该条件!)。
- 3、如文档侵犯您的权益,请联系客服反馈,我们会尽快为您处理(人工客服工作时间:9:00-18:30)。
Ulrich Näher, Wolfgang Neubert, Arno AntlitzProduct Development in the Automotive Industry: Strategies to Circumvent the Complexity ChallengeJanuary 31, 20020Number of models is increasing and product life cycles are decreasing1987Models per brand Number12 112000+25 % +25 %10 9 8 7 6 5 4 5.0 7.5 10.0 12.5Product life cycle 15.0 Years-30 % -30 %Source: Press clippings1OUTSIDE-IN ANALYSISTime-to-market is reduced dramaticallyMONTH FROM DESIGN FREEZE TO SOP* Golf III / IV 1991/96 C-class 1995/2000 Mondeo 1993/2000Reduction driven by implementation of simulation technologiesReduction driven by implementation of stringent quality gates6038 324016%2928%2460%* Start of production Source: Automobile production, AN, MID2In addition, urgency towards innovation drives vehicle complexityType of innovation in electronics Percent100%Vehicle complexity – example BMW Z22Radical innovationIndividual innovation30 43• BMW Z22 carries 70 major innovations20 27Incremental modification50 30Today2010Source: Automobil Entwicklung, survey results, McKinsey/ikaand 61 patents • Objective is to ensure new technology concepts for 2005 and beyond • Approx. 70 - 80% of innovations are in the field of electronics: – X-by-wire – Integrated starter/ – Car PC alternator – Center monitor – Curvelight – Fingerprint – Speech control recognition – Cameras for rear – Head-up display view – Telematics Integration challenge3Key levers to address complexity challenge1 2 3 4 5 6Source: McKinseyClear and precise customer knowledge and orientation Efficient product architecture – from identity to similarity Value chain adaptation towards competence based structures Improved development processes leveraging IT opportunities Stringent quality processes along entire development process Project organization combining high functional and integration capabilities4Increase in product variety and model change rate is driving passenger car market fragmentationSHARE OF TOP-10 SELLING MODELS WESTERN EUROPE, 1980 - 2000 Percentage of total sales units27.214.6 10.2198019902000Source: Schwacke 1998, Marketing Systems, EIU, Automobil revue, press clippings, McKinsey5CONCEPTUALIn mature and highly fragmented markets two strategies are possible: Targeting average vs. tailored market segmentMarket sizeMarket segments Competing vehicles A, B, C, DA Coverage ofDimension 1 A 2 B OEM's model D C 3 4 1 Dimension 2many prominent market segmentsDimension 1 A B C Dimension 2B Tailoring of models to specific customer segmentsDimension 1 A 2 B D C 3 OEM's model 4 1 Dimension 2Market creationSource: McKinseyMarket maturationTime6To understand what customers really want is keyCustomer want and state it Customer want but don't state it Customer state though really don't want it0.60Derived importance dominated by 0.50 emotional attributes Derived Importance0.40Showroom experience positive Proud to show this offFor people like meSupport is good value Fun to drive0.300.20Attractive Delivers what internally it promises I feel attractive Cost is good value Most highly regarded A leader Won't break down Comfortable Superior Agile Exclusive Safe to drive Stands out I look Won't let you down speeds successful Sufficient space Modern Sporty For people Exciting Value Efficient fuel usage Acceptable in the know Elegant Running costs customerresale Innovative An escape reasonable Around in Information Manly Youthful 20 years easy Environmentally friendly Negotiations straightforward UnderstatedAttractive externally0.100.00 5 5.5 6 6.5 7 7.5Stated importance dominated by rational attributes 8 8.599.510Stated Importance Out of 10Source: Automotive branding survey, May 20017Key levers to address complexity challenge1 2 3 4 5 6Source: McKinseyClear and precise customer knowledge and orientation Efficient product architecture – from identity to similarity Value chain adaptation towards competence based structures Improved development processes leveraging IT opportunities Stringent quality processes along entire development process Project organization combining high functional and integration capabilities8Efficient architectures have to be optimized on vehicle and component levelVehicle design (macroarchitecture) Interior dimensions, interior packaging Organization of engine components Component design (microarchitecture) Foot controls exampleFoot controls for vehicle type A Foot controls for vehicle type BArchitecture redesign Cable harnessJoint component for vehicle family• Define packaging zones • Determine organization of components • Define levels of freedom formicroarchitecture• Design components • Systematically optimize number of variantsFocus of a standardized parts strategySource: McKinseyEnsure compatibility of macroarchitecture in family concepts (e.g., electronics architecture)Increase share of standardized parts in vehicle family9Existing product architectures are redesigned with highest share of identical parts possible while maintaining sufficient differentiationProduct architecture Function separation Function integration Function elimination Foot controls example Variant combination Foot controls for vehicle type A Foot controls for vehicle type B Adapted parts/modules Principle or concept parts/modules Solitary parts/modules Parts/module architecture Identity 100%Identical parts/modules• 100% identicalparts • Same variants across vehicle types • Building block modules• Existing parts/modules with adjustmentsRestructuring• Related functionsor geometries ("pantograph")Combination reductionSource: McKinsey• Parts/modulesspecific to vehicle types 0%10For deriving communality potentials four cost levers have to be understoodPotential Fixed-cost levers dilutionPTechnology leapsPFlexibility reserves Complexity reduction cost reductionUnits BR A & BR B400,000 200,000BR A400,000800,000400,000800,000200520102015Description• Payback oninvestments across large numbers of units• Reduction ofvariable costs by changing production concept• Lower flexibility• Reduction ofrequirements due to variety costs higher share of ongoing core operationsExamples • Much lower development costs for vehicle type B • Higher utilization of machinery• Increase in level of • Increasedautomation • Optimization of production site concept production on highly specialized, constantly running lines (fewer variants on one line)• Reduction ofprocess costs at supplier: Purchasing, sales, production planning, administration, logistics, etc.Increase in potential dependent on • Blocking type • Blocking levelSource: McKinsey11EXAMPLECost types are impacted differently by cost leversHigh impact Partial impact Low impactFixed-cost dilution Cost type Bought-in materials Manufacturing costs Research and development Warranty and goodwill Administration and sales costsTechnology leapsFlexibility reserves reductionComplexity reductionImpact at 100% communality Percent 7-9 9 - 10 10 10 5Impact depends upon level of similarity/identitySource: McKinsey12Key levers to address complexity challenge1 2 3 4 5 6Source: McKinseyClear and precise customer knowledge and orientation Efficient product architecture – from identity to similarity Value chain adaptation towards competence based structures Improved development processes leveraging IT opportunities Stringent quality processes along entire development process Project organization combining high functional and integration capabilities13 Source: McKinseyPrice increases above the inflation rate cannot be enforced despite new technologiesHistorical price developmentList price VW Golf base model* EURNot inflation-adjusted Inflation-adjustedAdditional charge potential for new technologies – example brake-by-wireAverage additional costs for brake-by-wire Luxury car segment Large car segment Additional Medium car charge segment potential 5,000 end customers surveyed~ 1,000**~ 30015,00010,000CAGR 3.2%4003005,000Golf IIIGolf IVCompact car segment Small car segment2500 1993 1994 1995 1996 1997 1998 1999 2000 2001200* Incl. value added tax ** Statistically not significant Source: HAWK project team14Cost due to additional features have to be compensated by optimizing the value chainPRODUCTION COSTS COMPACT CAR, NOT INFLATION-ADJUSTED EUR/unit15.000 4.000 11.000CAGR 2.4% ~ 20% cost effect through best practice value chain architecture and CIP Electronics share 40% Car 2015 Synergy and enhancement (with old processes industry structures) Car 2015 best practice value chain architecture3.00012.000Electronics share 20% Car today Additional costs through new technologiesSource: HAWK project team15EXAMPLE: CHASSISFunctional value chain architecture will give way to one that is knowhow-drivenINDUSTRY STRUCTURE TodayBrake system System development System integration Electronics Mechanical Brake system integrator Steering Suspensystem sion AxlesIn the futureBrake system Brake system integrator Steering Suspensystem sion OEM AxlesLenksystemintegratorOEMMechanical integrator X-by-wire integratorSteering system manufacturerSpring and shock absorber specialistMechatronics specialistMechanical specialist Mechanical specialistMechanical specialistMechanical specialistDivision mainly by function (system) or spatial placement (module)Division mainly by know-how because of • Economies of scale • Development synergies • Complexity Know-how-drivenFunctionality-/position-drivenSource: Expert interviews, HAWK project team16EXAMPLE CHASSISSpecific competencies are required to capture new synergiesNEW SYNERGY POTENTIAL IN CHASSIS SEGMENT USD per vehicle Synergies199X-by-wire-integrator • Centralization of ECUs and basis software • Scale effects and optimization of interfaces between new electronic components • Economics of scope in production of sensors and actuators Mechanical specialists • Economics of specialization for mechanical components OEM • Avoidance of interfaces through centralized chassis control via software Required competencies• System integration (e.g.,ECU centralization) • Innovative creativity (e.g., ECU and Software design) • Development efficiency in electronics (e.g., sensors) • Operational excellence (e.g., actuators, sensors)1303831• Operational excellence • Ability to capture scaleeffects • Factor cost efficiencySynergy potential through value chain optimizationSource: Team HAWKSynergy potential for x-bywire integratorSynergy potential for mechanical specialistsSynergy potential for OEM• Transaction costefficiency • Understanding of customer needs17EXAMPLE: CHASSISDetailed analysis of competency gaps helps to derive specific activitiesCOST REDUCTION POTENTIAL FOR FUTURE STEERING SYSTEM INTEGRATOR Percent Sample company Competencies Mechanical development efficiency Electronics development efficiency Innovative drive Module/system integration Realizing operational excellence/economies of scale Factor cost efficiency Purchasing efficiency Overhead/transaction cost efficiency Understanding of end customerSource: HAWK project team06Best-practice company Competency gap• Competency building isneeded, particularly in the areas of development efficiency for electronics and innovative drive• Competency gap could beclosed by means of cooperating with an innovative electronics specialist18Key levers to address complexity challenge1 2 3 4 5 6Source: McKinseyClear and precise customer knowledge and orientation Efficient product architecture – from identity to similarity Value chain adaptation towards competence based structures Improved development processes leveraging IT opportunities Stringent quality processes along entire development process Project organization combining high functional and integration capabilities19The 2005 target requires a reduction of development times by 50%AVERAGE DEVELOPMENT TIMES, PROJECT DECISION TO SOP Month8060 months (1988)6042 months (1991)4040 months (1994)35 months* (1999)-50%20Target 30 months or less1990 1995 2000 20050 1985* Concept-freeze to SOP Source: Publications on vehicle development times (70 vehicles worldwide) between 1988 and 2000, McKinsey-Research20A near future development process is characterized by virtual techniques and only 1 prototype cycle30 MONTH DEVELOPMENT PROCESS Month -35 -30 Steps Gateways Package Styling-23 -5 0Project Concept planning development Series development/-preparationStart of project Concept decision Package definition (-23) Package freeze (-19)RampupProduction Start of test series productionPackage Exterior/Interior DesignDesign freeze (-23)Engineering/ CAEVirtual steps/process developmentDesign cyclesPrototypes TestingMassive use of virtual simulationOptimized test strategy driving cross functional vehicle perspectiveCAD 100% (-17)Prototype cycleOne prototype cycle for critical validation tests onlyPre-series Industrialitests zationIntegration tests Component testsValidation Endurance testsSource: Harvard Business Review21AUTOMOTIVE EXAMPLEProduct testing must be optimized along different dimensions1 Effective concept Complete product System Component Simulation Impact Laboratory Field test 2 Efficient execution• Test planning– Risk prioritization – Optimization of utilization – Cross-functional use of prototypes • Execution of tests – Automation – Up-Speeding• Specific parameters can be testedvery early • Test of more variants/options due to faster test cycles • Significant reduction of effort• Early test of highly criticalcriteria/properties • Cost reductionSource: McKinsey22Key levers to address complexity challenge1 2 3 4 5 6Source: McKinseyClear and precise customer knowledge and orientation Efficient product architecture – from identity to similarity Value chain adaptation towards competence based structures Improved development processes leveraging IT opportunities Stringent quality processes along entire development process Project organization combining high functional and integration capabilities23Maturity problems at ramp-up/SOP have significant impact on profitability Possible SOP problems(assumptions) Late market launch Forgone sales Market launch 6 months late 15 percent migration of former customers Full production reached 6 months late 10 percent over target production cost 15 percent over target development cost 50 percent over target SOP cost Long-term quality problems Ø USD 400/vehicle Changes to body pressing tools 6 months before SOPOpportunity potential* USD millions** ~750 ~1,250 ~500 ~2,000Customer migration Reduced production capacity Target production cost exceeded Target development cost exceededReduced profitability through potential problems at ramp-up/ SOP~190 ~125 ~1,400 ~250Increased costResources used for ramp-up/SOP Warranty and goodwill cost Cost of changes* Profit contribution from profits or cost differences over life cycle, assuming: 500,000 units p.a., USD 5,000 profit contribution/vehicle, production time 7 years ** Over total production time Source:McKinsey24Software maturity is becoming a critical factor in automotive product Software-related developmentSource of quality problems Share of electronics and software problems Failures per 1000 vehicles thereof caused by electronics and SW 55% Saab 66.4 44% Alfa 52.8 48% Daewoo 42.4 45% Fiat 41.9 BMW Nissan VW Porsche Audi Mazda Subaru Honda ToyotaMalfunction in Percent Infotainment and body electronics Injection/ignition system Engine (w/o injection)32 20 12 8 7 6 6 4 519.9 19.2 18.4 17.7 15.3 13.2 12.7 11.3 10.646% 46% 48% 53% 44% 55% 49% 48% 53%Radiator/cooling Wheels/tires Fuel systems Gears/transmission Chassis OtherSW problems are reasons for recall of more than 700.000 vehicles in 2002Source: McKinsey, Business Week, ADAC-AutoMarxX (3-5 year old car failures 1998-2001), cars in Germany only25Automotive software development adds a new layer of complexity compared to hardware• High number of tacit requirements More complexity • Heavy software and hardware interaction for embedded systems • Project complexity growing steeply with product sizeLess transparency Fundamental Fundamental differences: differences: Find specific Find specific solution solution• Intangible product, hard visualization and performance tracking • General mismatch between scope and available resources projects always seem to be "nearly" completeLess discipline More technological risk More business risk• Inherent tendency to over-engineering • Seemingly low cost of changes • Invariant resource under-estimation • Irrational developer preferences • High degree of change in underlying complex technologies • No widely accepted platform standards • Immature tool landscape • Fast-moving (and in many cases immature) markets • Customer value hard to assess • Lack of experience translating customer requirements intofunctionalityWill disappear Will disappear as industry as industry matures: matures: Learn from Learn from hardware hardwareSource: Brooks: The Mythical Man-Month, McKinsey26Operational improvement can be achieved in a three step approachDevelopment organization• Restructuring of development organization forspecific needs of SW projects is necessary• Building of specific skills in SW development andSW project management is neededProcess efficiency• Complex software projects are only feasible withstandardized, repeatable processes• Development effort depends heavily on processmaturity - efficiency potentials of up to 90% are possibleProduct architecture• Modular, feature specific product design is key toreduce complexity and enable concurrent engineering• Platforming and maximal degree of reuse is necessary to overcome complexity challenge and ensure software qualitySource: McKinsey27Process maturity is key for product qualityStandard consistent process Predictable processContinuously improving process OptimizingDisciplined process CMM levelManaged DefinedRepeatable Initial• Process change • Quantitative • Standard progoals for product and process • Tracking of goals by metrics and statistical analysis management • Defect prevention processes • Technology charge management• Process owned • Undefined proCharacteristicscesses, ad hoc working methods • Success depends on few specialists • Schedule, quality and cost unforeseeable by project manager • Disciplined project management • Process varies from project to projectcess owned by organization • Process-specific tailoring of the standard processAutomotive industrySource: McKinseyAutomotive industry target!Aircraft industry28Key levers to address complexity challenge1 2 3 4 5 6Source: McKinseyClear and precise customer knowledge and orientation Efficient product architecture – from identity to similarity Value chain adaptation towards competence based structures Improved development processes leveraging IT opportunities Stringent quality processes along entire development process Project organization combining high functional and integration capabilities29QUALITATIVELYSignificant issues after reorganizationsCHANGES IN ORGANISATIONAL ORIENTATIONDivisional organizationCritical issues Chrysler (reorg. since 1989)• "Empire strikes back" –change not sustainable – Project management without real power – Support from top management and organization too weakProject organizationToyota (reorg. since 1992) BMW (reorg. since 1995) Mercedes (reorg. since 1997) VW/Audi (reorg. since 1993)Functional organization Time ~1990 ~2000• Organization unable toaccept shared responsibilitiesSource: Interviews, press clippings30CONCEPTUALProject organizations must combine high integration and functional development capabilitiesEVALUATION OF DEVELOPMENT CAPABILITIES High Divisional organization High competenceIntegration capabilities• Development time • Target costs • Known customerrequirements • Platform concepts Limited competence Low"LowProject organizationProject organizationFunctional organization HighFunctional capabilities• Commercialized innovations • Quality of vehicle features • Efficiency of functionSource: McKinsey31Structure and roles within project organization defined to ensure high competencyCEO RolesProgram manager Functional managersDevelopment Sales Procurement ControllingHeavy weightFunctional know-how and integration Single-project orientation Module orientationProductionProject managers Module managersLimousine Coupé ConvertibleBodyElectronicsChassisPowertrainManufacturing/ EngineeringCross-functional teamsSource: McKinsey32Organizational setup of line functions based on individual functionCEO Types of line organizations Line function segmentation Program management A B C R&D departments* Other line functions• Marketing • Vehicleintegration• Controlling • ManufacturingEngineeringBodyElectronicsChassisPowertrainManufacturing/ engineeringPartial segmentation A B C• Body • Chassis • Electronics • Powertrain• QualityassuranceCross-functional teams Functional A B C• Purchasing*• Design • Conceptdevelopment* Best organized along modules Source: McKinseyA, B, C programs33The necessary change process must be driven by top management and requires a long term change in people's mindsets1 2 3 4 5 6Source: McKinseyClear and precise customer knowledge and orientation Efficient product architecture – from identity to similarity Value chain adaptation towards competence based structures Improved development processes leveraging IT opportunities Stringent quality processes along entire development process Project organization combining high functional and integration capabilitiesCharacteristics of change process• Top management topic • Change managementapproach required• Long term processAct now forward instead of reacting afterwards34。