锥齿轮传动计算
锥齿轮理论计算

四驱变速箱锥齿轮计算基本参数:整车满载重量6.5吨,前轮直径0.86米;后轮直径0.745米。
马达排量:56ml/r1.四驱啮合状态下,因为是四轮驱动,整车质量6.5T。
前后桥计算均摊6.5吨/2=3.25吨。
后桥所需驱动力计算如下:T=3250*9.8*(0.745/2)*1*0.94=11152.28 N.m(机械传动效率0.94,摩擦系数选择1最大值)T1(马达分配动力)=11152.28/119.57=93.26 N.mP1=93.26*2π/56=10.45 KW以后桥分配11 KW计算,见以下公式功率(千瓦)P = 11小齿轮转速(转/分)n1 = 309大端端面模数(mm)m = 5.5工作齿宽(mm) b = 26使用系数KA=1.50轴承系数KHβbe=1.10润滑油粘度(mm2/s)ν40= 67设计寿命: 1000 小时类型: 动载直齿锥齿轮和零度锥齿轮类型为非鼓形直齿锥齿轮齿面点蚀: 允许少量点蚀第Ⅱ组公差等级: 8轴交角(°)Σ= 90齿形角(°)α= 20齿宽中点螺旋角(°)βm= 0最小接触强度安全系数SHmin= 1最小弯曲强度安全系数SFmin= 1.25小齿轮大齿轮齿数Z = 18 26高变位系数x1 =0.0000 x2=0.0000切向变位系数xt1 =0.0000 xt2=0.0000齿轮材料: 渗碳淬火的渗碳钢渗碳淬火的渗碳钢齿面粗糙度(μm)Ra = 1.6 1.6接触强度极限(MPa)ζHlim= 1500 1500弯曲强度极限(MPa)ζFlim= 400 400----------------------几何及精度参数-------------------------------小齿轮大齿轮当量圆柱齿轮分度圆直径(mm)dv =102.410 213.670 当量圆柱齿轮顶圆直径(mm)dva =111.765 223.025 当量圆柱齿轮基圆直径(mm)db =96.234 200.784 齿宽中点分度圆直径(mm)dm =84.201 121.623 参考点分度锥距(mm) Rm =73.963大轮齿距极限偏差(μm)fpt =25当量中心距(mm)av =158.040当量端面齿形角(°)αvt=20.000有效工作齿宽(mm)be =22.100当量端面重合度εvα=1.659当量纵向重合度εvβ=0.000当量总重合度εvγ=1.659齿宽中点分度圆上的名义切向力(N) Fmt=8074.343齿数比u=1.444当量圆柱齿轮齿数比uv=2.086当量啮合线长度(mm) gva=22.910无量纲的基准速度N=0.017共振转速(r/min) nE1 =18330.33两齿轮诱导质量(kg/mm) mredx=0.017中点圆周速度(m/s) vmt=1.362跑合量(μm) yα=1.875cv1=0.320cv2=0.340cv3=0.230cv4=0.900cv5=0.470cv6=0.470cv7=0.765名义转矩(Nm) T1=339.932齿宽中点法向模数(mm) mnm=4.678当量圆柱齿轮的齿数zvn=45.677βvb=0.000------------------------接触强度系数-------------------------------动载系数Kv =1.012轮齿中点接触线长度(mm) lbm =25.445齿向载荷分布系数KHβ=1.898齿间载荷分配系数KHα=1.000节点区域系数ZH =2.495弹性系数ZE =189.812螺旋角系数Zβ=1.000锥齿轮系数ZK =0.800润滑剂系数ZL =0.945速度系数ZV =0.958粗糙度系数ZR =0.915尺寸系数ZX =1.000中点区域系数ZM =1.054工作硬化系数ZW =1.000载荷分配系数ZLS =1.000小齿轮大齿轮寿命系数ZNT =1.255 1.282------------------------弯曲强度系数-------------------------------齿向载荷分布系数KFβ=1.898齿间载荷分配系数KFα=1.000重合度系数Yε=0.702螺旋角系数Yβ=1.000锥齿轮系数YK =1.000试验齿轮的应力修正系数YST =2.000载荷分配系数YLS =1.000小齿轮大齿轮尺寸系数YX =1.000 1.000齿形系数YFa =2.824 2.402应力修正系数YSa =1.624 1.782相对齿根圆角敏感系数YδrelT=0.995 1.000相对齿根表面状况系数YRrelT=1.004 1.004弯曲疲劳寿命系数YNT =0.964 0.971--------------------接触疲劳强度计算结果------------------------------接触强度极限(MPa)ζHlim=1500.000 1500.000计算齿轮接触极限应力(MPa)ζHP=1561.008 1594.072计算接触应力(MPa)ζH=1450.173 1450.173接触安全系数Sh =1.076 1.099小轮接触强度足够!大轮接触强度足够!--------------------弯曲疲劳强度计算结果------------------------------弯曲强度极限(MPa)ζFlim=400.000 400.000计算齿轮弯曲极限应力(MPa)ζFP=770.735 780.390计算弯曲应力(MPa)ζF=615.356 574.515弯曲安全系数Sf =1.253 1.358小轮弯曲强度足够!大轮弯曲强度足够!。
锥齿轮传动计算2013C
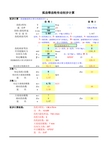
弧齿锥齿轮传动初步计算
初步计算(按接触强度计算分度圆直径):
齿 轮 1齿 轮 2
齿轮1转矩T m 136.4500.1788
或
功率P 10136.4 N·m 齿轮1最低转速n min 初 定 速 比u 01 3.667齿轮材质代码说明:1—结构钢正火,2—碳钢调质或正火,3—合金钢调质,4—调质钢表面淬火,5—合金钢
7—调质钢、渗碳钢长时间气体氮化, 8—调质钢、渗碳钢短时间气体氮化或液体氮化,
1114—铸钢。
不输入默认 5
5
5
5齿轮材质等次—低等,中等不输入。
2许用接触应力σHP 1181.8法向压力角αn 20 度
初定螺旋角
β
10
0按接触强度计算分度圆直径
228.8初定齿轮1齿数
Z 109Z 20
33
相应的大端端面模数
m 07毫米
速 比
u 3.67方案二:
初定大端端面模数
m 0 4.75取消!
相应的齿数Z 101348
速 比u 3.69初步计算结果:
齿轮1转矩:136.4 N·m 功 率:10 kW
齿轮1最低转速:700 r/min 齿轮1齿数:9齿轮2齿数:33
大端端面模数:7 mm 法向压力角:20º中点螺旋角:10º0'0"速 比:3.67
*
TRUE 质钢表面淬火,5—合金钢渗碳淬火,6—氮化钢气体氮化,
时间气体氮化或液体氮化, 9—碳素铸钢, 10—合金铸钢,
TRUE TRUE
注:不输入则与齿轮 1 相同
N/mm2
20TRUE
10
TRUE
毫米毫米
TRUE
TRUE。
圆弧齿锥齿轮传动设计几何计算过程
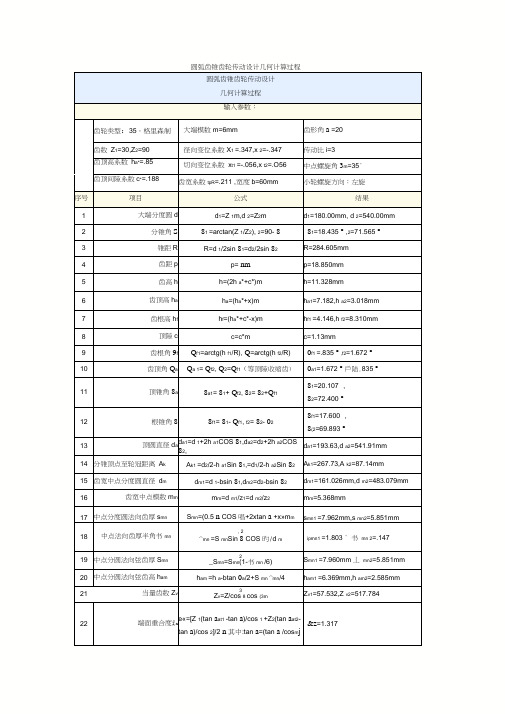
圆弧齿锥齿轮传动设计几何计算过程圆弧齿锥齿轮传动设计几何计算过程输入参数:齿轮类型:35。
格里森制大端模数m=6mm齿形角a =20°齿数 Z 1=30,Z 2=90径向变位系数X 1 =.347,x 2=-.347 传动比i=3齿顶高系数 h a*=.85 切向变位系数 x t1 =-.056,x t2=.O56 中点螺旋角3m =35°齿顶间隙系数c *=.188齿宽系数tpR =.211 ,宽度b=60mm小轮螺旋方向:左旋序号 项目公式 结果1 大端分度圆dd 1=Z 1m,d 2=Z 2md 1=180.00mm, d 2=540.00mm2 分锥角S 81 =arctan(Z 1/Z 2), 2=90- 881=18.435 ° ,2=71.565 °3 锥距R R=d 1/2sin 81=d 2/2sin 82R=284.605mm 4 齿距p p= nm p=18.850mm 5 齿高h h=(2h a *+c*)m h=11.328mm6 齿顶高h a h a =(h a *+x)m h a1=7.182,h a2=3.018mm7 齿根高h fh f =(h a *+c*-x)mh f1 =4.146,h f2=8.310mm 8 顶隙c c=c*mc=1.13mm9 齿根角9f Q f1=arctg(h f1/R), Q =arctg(h f2/R) 0f1 =.835 ° ,f2=1.672 ° 10 齿顶角Q a Q a 1= Q f2, Q 2=Q f1(等顶隙收缩齿)0a1=1.672 ° 戶陆.835 ° 11顶锥角8a8a1= 81+ Q f2, 82= 82+Q f181=20.107 °, 82=72.400 ° 12 根锥角8 8f1= 81- Q f1, f2= 82- 028f1=17.600 °, 8(2=69.893 °13顶圆直径d a d a1=d 1+2h a1COS 81,d a2=d 2+2h a2COS82,d a1=193.63,d a2=541.91mm14 分锥顶点至轮冠距离 A k A k1 =d 2/2-h a1Sin 81,=d 1/2-h a2Sin 82A k1=267.73,A k2=87.14mm 15 齿宽中点分度圆直径 d m d m1=d 1-bsin 81,d m2=d 2-bsin 82d m1=161.026mm,d m2=483.079mm 16齿宽中点模数m mm m =d m1/z 1=d m2/z 2m m =5.368mm17 中点分度圆法向齿厚s mn S mn =(0.5 n COS 唱+2xtan a +x»m ms mn1 =7.962mm,s mn2=5.851mm18中点法向齿厚半角书mn, 2^mn =S mn Sin 8 COS 旳/d mipmn1 =1.803 ° 书 mn 2=.14719 中点分圆法向弦齿厚S mn 2_S mn =S mn (1-书mn /6) S mn1 =7.960mm 丄 mn2=5.851mm 20 中点分圆法向弦齿高h am h am =h a -btan 0a /2+S mn ^mn /4h am1 =6.369mm,h am2=2.585mm 21当量齿数Z v3Z v =Z/cos 8 cos (3mZ v1=57.532,Z v2=517.78422端面重合度£a e«=[Z 1(tan a at1 -tan a )/cos 1 +Z 2(tan a at2-tan a )/cos 2]/2 n 其中:tan a =(tan a /cos m j&z =1.317nCOS a vat=[ZCOS l/(Z+2(h a*+X)COSS )]23 齿线重合度邙£B=btan 3m n /m £=2.49124 总重合度 2 2 1/2£ =(a 才£|3 ) £ =2.818。
机械设计-锥齿轮

一、设计参数
直齿圆锥齿轮传动设计
锥齿传动
几何参数标准: 大端分度圆处 m、α为大端参数 强度计算推导思路: 锥齿轮→当量直齿轮 强度计算: 平均分度圆处 当量齿轮。
DUT-MYL
DUT-MYL
锥齿轮 齿数比: 锥距:
d1 d 2 R = + = d1 2 2
DUT-MYL
五、锥齿轮接触强度计算 按平均分度圆处的当量直齿圆柱齿轮计算,m代入mm 1、基本公式 赫兹公式:
Fnca σ H = ZE ⋅ ≤ [σ]H L ρΣ
DUT-MYL
强度校核公式:
σH
4 KT1 ≤ [σ H ] 2 3 φR (1 − 0.5φR ) d1 u
Z H Z E Zε
动载系数Kν ——按Vm 并降低一级精度查图7-9 齿间载荷分配系数 齿向载荷分布系数
Khβbe —— 轴承系数,查表7-11
3、YFa、Ysa 按当量齿数查表7-9
DUT-MYL
锥齿受力分析
Fr1= F’ cos δ1= Ft tgα cos δ1 = - Fa2 Fa1 = F’sinδ1 = Ft tg δ1 = -Fr2 主动轮 —— 与其转向n1相反 从动轮 —— 与其转向n2相同
Ft Fr Fa
Ft1= -Ft2 Fr1= -Fa2 Fa1= -Fr2
82
各力方向
分别指向各自轮心 指向各齿轮大端
DUT-MYL
例:受力分析
n1
Fr1 Fr2 Ft1 Fa1 Fa2 Ft2
n2
Fr1= -Fa2 Fr2= -Fa1
DUT-MYL
三、锥齿轮特点 1、锥齿轮齿廓大小沿齿宽方向变化,与其距锥顶距离 成正比; 2、轮齿大、小端刚度不同,沿齿宽的载荷分布不均; 3、锥齿轮较直齿轮精度低, 振动噪声大,速度不宜过高; 4、参数计算——大端为标准—— m ; 强度计算——齿宽中点的当量圆柱齿轮为准,— mm
标准锥齿轮传动的强度计算
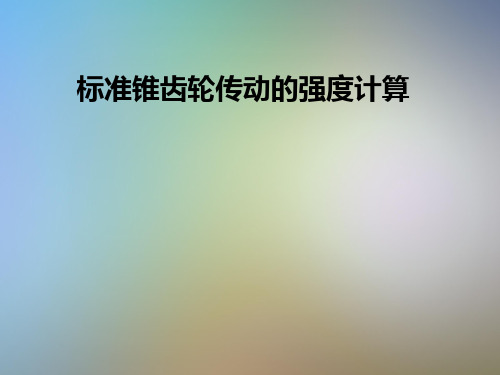
在综合考虑齿轮几何尺寸,毛坯,材料,加工方法,使用 要求及经济性等各方面因素的基础上,按齿轮的直径大小,选 定合适的结构形式,再根据推荐的经验数据进行结构尺寸计算 。
常见齿轮结构形式
⑴ 齿轮轴 ⑵ 实心式结构 ⑶ 腹板式结构 ⑷ 轮辐式结构
标准锥齿轮传动的强度计算
1 设计参数
直齿锥齿轮传动是以大端参数为标准值,强度计算时,是 以锥齿轮齿宽中点处的当量齿轮作为计算时的依据。
轴交角∑,齿数比u,齿 数z1、z2,锥距R,分 度圆锥角δ1、 δ2,分度 圆直径d1、d2,齿宽中点 处即平均分度圆的直径为
dm1、dm2,当量齿轮 齿数zv1、zv2,当量齿轮 的分度圆直径dv1、dv2,
很显然,当两齿轮平均齿宽处两当量齿轮在节点上的啮 合曲率半径为:
从而可得到 :
若将上式(综合曲率表达式)及uv=u2、 等式代入赫兹公式,并令接触线长度L=b,得到:
若α=20°,则得到: 校核式 设计式
§10-10 齿轮的结构设计
通过强度计算确定出了齿轮的齿数z、模数m、齿宽B、螺
旋角b、分度圆直径d 等主要尺寸。
常见齿轮结构形式
⑴齿轮轴
直径较小的钢质齿轮,当齿根圆直径与轴径 接近时,可以将齿轮与轴做成一体,称为齿轮轴
圆柱齿轮轴
圆锥齿轮轴
圆柱齿轮轴
圆柱齿轮e<2mt
圆锥齿轮轴
< (对锥齿轮指小端)
圆锥齿轮轴பைடு நூலகம்
e
⑵实心式结构
< 160mm
实心式圆柱齿轮
但航空齿轮为减轻重量, 腹板式结构。
实心式圆锥齿轮 < 160mm 时,有时也设计为
锥齿轮传动设计计算

中点分度圆弧长之半
Dc0
152.4 毫米
K11
1
K12
0
K13
0.25
Ki
1
5.48650737 3.9382706 1.8671673 3.37400407 0.85689165 2.07110329 2.11250329 0.21810139 0.03913885 5.44301014 3.93726512
0
Zvn2
dvn2
dvan2
dvbn2
刀具齿顶高 名义切向力 使用系数 动载系数 齿向载荷分布系数
齿间载荷分布系数
ha0 Fmt
KA m1 N cv4 KV KHβ
KHα0
2.49505638
刀尖圆角半径
13867.4221 N
(工作条件 原动机均匀
平稳,从动
机中等振
1.5 动)
0.00454422 m2
许用齿根应力 计算齿根应力
弯曲强度计算安全系数
E
SFn/mmn
αFan Yfa YK
σFmin
SFmin σFP σF
SF
小齿轮:
0.76139217 G
-0.568193201
0.40932318 ρf/mmn 0.60055177 hFa/mmn
0.26766168 1.767694416
55.5784585 Ysa
渗碳淬火钢软氮化
说明:1—大小轮都
是两端支承, 2—
一个是两端支承,
另一个是悬臂, 3
—两者都是悬臂
小轮名义功率
P1
T1
单变量求解 计算:
可变格
锥齿轮传动设计计算
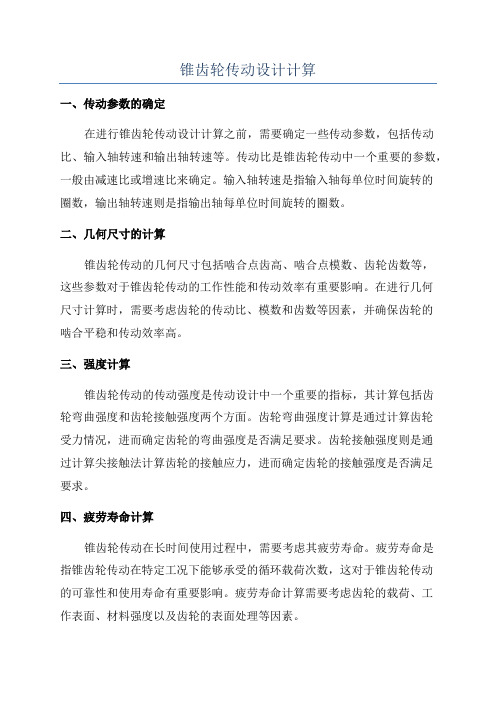
锥齿轮传动设计计算
一、传动参数的确定
在进行锥齿轮传动设计计算之前,需要确定一些传动参数,包括传动比、输入轴转速和输出轴转速等。
传动比是锥齿轮传动中一个重要的参数,一般由减速比或增速比来确定。
输入轴转速是指输入轴每单位时间旋转的
圈数,输出轴转速则是指输出轴每单位时间旋转的圈数。
二、几何尺寸的计算
锥齿轮传动的几何尺寸包括啮合点齿高、啮合点模数、齿轮齿数等,
这些参数对于锥齿轮传动的工作性能和传动效率有重要影响。
在进行几何
尺寸计算时,需要考虑齿轮的传动比、模数和齿数等因素,并确保齿轮的
啮合平稳和传动效率高。
三、强度计算
锥齿轮传动的传动强度是传动设计中一个重要的指标,其计算包括齿
轮弯曲强度和齿轮接触强度两个方面。
齿轮弯曲强度计算是通过计算齿轮
受力情况,进而确定齿轮的弯曲强度是否满足要求。
齿轮接触强度则是通
过计算尖接触法计算齿轮的接触应力,进而确定齿轮的接触强度是否满足
要求。
四、疲劳寿命计算
锥齿轮传动在长时间使用过程中,需要考虑其疲劳寿命。
疲劳寿命是
指锥齿轮传动在特定工况下能够承受的循环载荷次数,这对于锥齿轮传动
的可靠性和使用寿命有重要影响。
疲劳寿命计算需要考虑齿轮的载荷、工
作表面、材料强度以及齿轮的表面处理等因素。
五、稳定性分析
综上所述,锥齿轮传动设计计算需要考虑多个方面的因素,包括传动
参数的确定、几何尺寸的计算、强度计算、疲劳寿命计算和稳定性分析等。
只有在全面考虑传动要求的前提下,才能设计出安全可靠、经济高效的锥
齿轮传动。
锥齿轮

塑料、 塑料、铸 铁、青铜
<0.5
齿轮传动润滑油粘度荐用值 圆周速度 v (m/s)
0.5~1 1~2.5 2.5~5 5~12.5 12.5 ~25 >25
运动粘度 v/cSt(40℃ ) (
350 220 350 500 500 150 220 350 500 100 150 220 350 80 100 150 220 55 80 100 150 55 80 100 500 500
钢
渗碳或表 面淬火钢
450~1000 1000~1250
1250~1580 900
表6-12 齿轮传动常用的润滑剂
续表6 续表6-12 齿轮传动常用的润滑剂
啮合中的摩擦损耗; 啮合中的摩擦损耗; 齿轮传动的损耗: 搅动润滑油的油阻损耗; 齿轮传动的损耗: 搅动润滑油的油阻损耗; 轴承中的摩擦损耗。 轴承中的摩擦损耗。 表6-13 齿轮传动的平均效率 8级精度的 级精度的 闭式传动 0.97 0.96 开式传动 0.95 0.93
Y Sa
1 2
3 3
50 45
17 60
2.97 2.28
1.52 1.73
[σ ]H 500 450
[σ ]F 420 390
因为相啮合齿轮接触应力相等,所以[σ 大的接触 解:因为相啮合齿轮接触应力相等,所以[σH]大的接触 强度高 接触强度高。 强度高,所以齿轮 1 接触强度高。 因为相啮合齿轮的 [σ ]F 曲强度高, 曲强度高,求: [σ F 1 ] 420
其它尺寸由结构设计确定
二、常见的结构形式 1. 齿轮轴 直径较小的钢质齿轮, 直径较小的钢质齿轮,当齿根圆 直径与轴径接近时, 直径与轴径接近时,可以将齿轮与 轴做成一体,称为齿轮轴 齿轮轴。 轴做成一体,称为齿轮轴。否则可 能引起轮缘断裂 轮缘断裂。 能引起轮缘断裂。