线束加工工艺流程图+图片-(百度)+含X-R控制图
线束生产工艺流程 ppt课件

图5, 不 合格压 接,绝缘 包筒刺 破线皮
9
端子外观检验
图4, 不合格压接,导体没有完全压 入导体包筒内
图5, 不合格,料带太 长
图6, 不合格, 料带不
可见,端子切伤
ppt课件
图7, 合 格, 热缩 套管完 全包住 导体
图8 不合 格 热缩 套管包的 太长
10
端子外观检验 合格
ppt课件
11
4.剥皮尺寸参考算法(如下图):
ppt课件
4
露出导体 导体铆压栅长度 可见导体和绝缘体
导体铆压栅长度
剥线长度
a 被覆铆压栅
可见导体 剥线长度
剥皮尺寸=导体铆压栅长度 +1/2a +0.5mm(线规: 0.3mm2 以下) 剥皮尺寸=导体铆压栅长度 +1mm (线规:0.3—1mm2 ) 剥皮尺寸=导体铆压栅长度 +2mm (最大线规:10mm2 )
开式端子
导体铆压栅 喇叭口 被覆铆压栅
嵌合部
卡口片
挤压沟
ppt课件
料带
8
端子外观检验
图1, 标准压接,外 皮处于导体包筒 和绝缘包筒之间
图2, 合格压接,外皮 刚好与导体包筒或 绝缘包筒平齐
图3, 不合格压接,外皮压入导体 包筒或绝缘包筒内
图4, 不 合格压 接,导 体伸入 到功能 区内
ppt课件
18
在铆压拉力和高度保证的前提下,理想的铆端状态:
1. 视窗 1 能看见导体又能看到绝缘体(外被)
2. 视窗 2 芯线(导体)露出长度0.5~1.5mm(具体依端子大小而定)
3. 嵌合部不可变形,卡口片不可变形
4. 芯线铆压栅、被覆固定栅中间沟槽不可有间隙,不可两边带毛刺
线束生产工艺流程
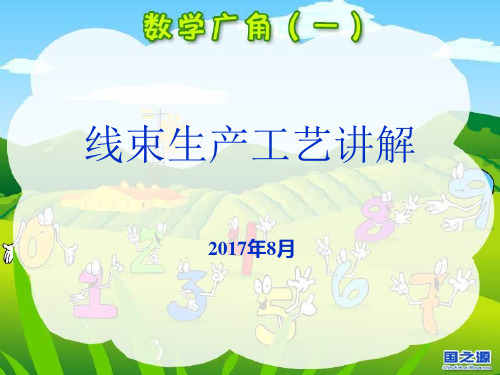
料带太长
料带不可见,
图7, 合格, 热缩 套管 完全 包 图8住 导 不体 合 格热 缩套 管包 的太 长
端子外观检验 合格
端子外观检验 不合格
端子高铆度端测量高度测量:作为确保正常压着性能的管 理方法,有必要进行铆端高度测定,设定高度虽然 是在铆端机方面设定的,但就其测定却是在铆端 之物上进行的,测试时使用铆端高度测定用仪器 ——千分尺,用其测定铆端体的“固定栅”和“ 挤压栅”的各中心部位,测试时需避开“挤压沟 ”,且确认用的线材应为生产使用之线材.
目视检测中拒绝接收的例举
四.组装胶壳
将铆压好之端子卡口片方向与塑壳卡同 向,再将端子平推入塑壳,当听到卡喀声后,再回 轻拉线材,以确定端子正确卡入塑壳,无脱落则 合格.注意依工程图要求组装,不可插错位.
卡片口卡于 卡位上
五.通电测试
测试目的:检测产品功能是否正常,以确定产品性 能是否符合客户要求.
在铆压拉力和高度保证的前提下,理想的铆端 状态: 1. 视窗 1 能看见导体又能看到绝缘体(外被) 2. 视窗 2 芯线(导体)露出长度0.5~1.5mm(具体 依端子大小而定) 3. 嵌合部不可变形,卡口片不可变形 4. 芯线铆压栅、被覆固定栅中间沟槽不可有
以下为在目视检测中拒绝接收的例举
目视检测中拒绝接收的例举
图1, 标准压 接,外皮处 于导体包筒 和绝缘包筒 之间
图2, 合格压 接,外皮刚好 与导体包筒 或 平绝齐缘图不包4合筒,
格压 接, 导体
图3, 不合格压接,外 皮压入导体包筒或 绝缘包筒内
图5, 不合 格压 接, 绝缘
端子外观检验
图4, 不合格压接,导体 没有完全压入导体包 筒内
图5, 不合格, 图6, 不合格,
线束生产工艺流程课件
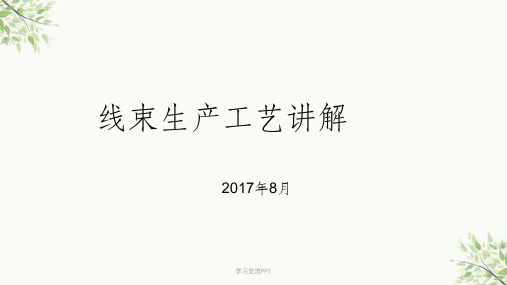
学习交流PPT
24
谢谢!
学习交流PPT
25
学习交流PPT
15
用拉力计测试端子拉力将端子固定好后,将拉力计归零,再进行拉力测试, 当拉力达到规定值时,停止拉动,固定位置,保持 1 分钟,如端子没有脱落则 合格,每 1—2 小时抽测一次。
学习交流PPT
16
国标GB17196-1997
m㎡
N
Kgf
0.5
56
5.8
0.75
84
8.6
1
108
11
2.4.剥皮尺寸参考算法(如下图):
学习交流PPT
4
露出导体 导体铆压栅长度 可见导体和绝缘体
导体铆压栅长度
剥线长度
a 被覆铆压栅
可见导体 剥线长度
剥皮尺寸=导体铆压栅长度 +1/2a +0.5mm(线规: 0.3mm2 以下) 剥皮尺寸=导体铆压栅长度 +1mm (线规:0.3—1mm2 ) 剥皮尺寸=导体铆压栅长度 +2mm (最大线规:10mm2 )
将铆压好之端子卡口片方向与塑壳卡同向,再将端子平推入塑壳,当 听到卡喀声后,再回轻拉线材,以确定端子正确卡入塑壳,无脱落则合格. 注意依工程图要求组装,不可插错位.
学习交流PPT
卡片口卡于 卡位上
ቤተ መጻሕፍቲ ባይዱ23
五.通电测试
测试目的:检测产品功能是否正常,以确定产品性能是否符合客户要求.
六.包装入库
包装时注意不可有少装或多装,以及混装,标识、字迹模糊不清等不良.
学习交流PPT
5
剥线正确图
学习交流PPT
6
剥线不正确图
剥离刀钝或刀之间距离不正确, 绝缘层切割不正确
线束生产工艺流程

線材生產線材生產工工艺流程流程培培训講師:陳代兵2011年03月歡迎大家參加培訓!图一.電線生產流程图工艺流程電線生產工二.線材生產各段設備三. 線材生產中品質管控點一.電線生產電線生產工工艺流程流程图图銅線- 芯線- 對絞- 總絞- 外被二. 線材生產各段設備(重點講芯線押出, 了解電線是怎麼生產的)芯線押出設備生產線:1.放線裝置.2.導體預熱器3.擠出主機.3.1料筒3.2螺桿3.3機頭3.4模具4.水槽.5.印字設備6.火花機.7.OD測試儀.8.牽引裝置9.收線裝置1.放線裝置作用:讓銅線均勻穩定的從軸子上放出.2.預熱機作用:使铜线等金属导体在线运动中连续加热,通過調節預熱可改變芯線附著力.3. 押出機之料筒作用:用於儲存料及烘料押出機之螺桿作用:螺桿是擠塑機主機擠壓系統的關鍵部件之一, 它不僅起到輸送塑料的作用,同時對塑料的擠壓、塑化、成型的重要作用,所以合理選用螺桿結構和參數,是獲得理想的產品質量和產量的重要環節押出機螺桿料筒4. 水槽作用:冷卻電線5. 印字設備: 在電線表面印字6.火花機作用:檢測芯線絕緣性能7. OD測試儀作用:在線測量電線外徑9. 收線裝置作用: 使電線裝在軸子上三. 線材生產中品質管控點以及其它藍圖要求項目依據客戶或下工段生產要求芯線包裝依據標準樣品芯線顏色依據客戶或規范要求火花測試依據客戶或規范要求絕緣延伸抗張依據客戶或規范要求銅導體電阻依據客戶或規范要求絕緣皮厚依據客戶或規范要求線材外徑光滑\平整線材外觀芯線參考標准品質主要控制項目生產工段。
EPB线束工艺流程图
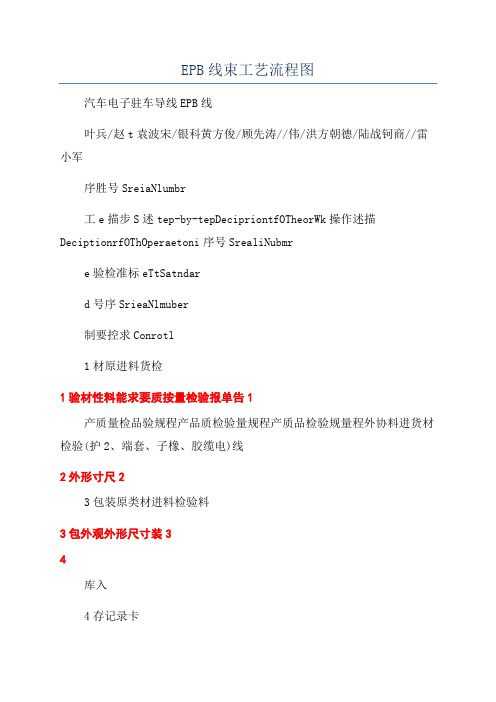
EPB线束工艺流程图汽车电子驻车导线EPB线叶兵/赵t袁波宋/银科黄方俊/顾先涛//伟/洪方朝德/陆战钶商//雷小军序胜号SreiaNlumbr工e描步S述tep-by-tepDecipriontfOTheorWk操作述描DeciptionrfOThOperaetoni序号SrealiNubmre验检准标eTtSatndard号序SrieaNlmuber制要控求Conrotl1材原进料货检1验材性料能求要质按量检验报单告1产质量检品验规程产品质检验量规程产质品检验规量程外协料进货材检验(护2、端套、子橡、胶缆电)线2外形寸尺23包装原类材进料检验料3包外观外形尺寸装34库入4存记录卡库4仓库管理规定5材料原存温度储计5仓库管理规5定协外材料存放6护套(端、子橡、胶、缆电)线6度计温6库仓管理规定7原材运料到料间烘烘温烘的温度箱、间7时按原要料求行执7烘参数箱照汽车电子驻车导线EPB线产对质量检验品程规8电缆线裁线8外观、寸尺8检单验产质量检品规验程9检首9外、尺观寸9检验单01生\产检自全检\产品质量检验程规10外观尺寸10、检单验外观、尺寸产品质检量规验程11巡检112时检小2.根检验1单产品质量检验程12规电线剥外缆部绝层缘12外观尺、寸21检单验品产质量验检程规31首检13外观、寸尺3验检单14生产\自检全\检品质量检产验程规14外观尺寸、41验检15单巡检51外观尺寸、2小时检2根品质产量检验程规15检单验产质品检验规量程16缆线电内剥绝部层缘16外观尺、寸16验检单产质品量检规验程71首检17观、外尺寸71检验单81生产自检\全检\产品质量检规程验81外、尺观寸81检验单9巡检19观外尺、寸2时小检2根产品质检验量程规19检验单品产质量验检规程20穿封堵密0外观22验检单品产质量验检规程12检首12外21观检验单22汽车电子驻车导线EPB线生产\自检全\产品质检检量规验程22外观22检验单23检巡32外观2小检时2根产品质量验检规程23验检单产品质检量规验程42接端子压2外4、性能2观4检单验品产量质检验规程52首检25外观、性能25检验单26生产\检\全检自产品质量验检规程26外观62验检2单7检巡27外观、能性2小检2时根外观性能、产品质量检规验程2 7检验单82装配护套品产量质验检程规2828检验单92首检29外观、性能产质品量验检规程29检验单30生产自\\检全检产质量品验检程规03观外30检验单31检巡31外观、性能2小检时2根电脑控监系统工/艺产品质量验检规程31检验单32半把品成线运到塑注车注塑间型成3I2卡32参工艺照卡参数33首检33观、尺寸、性外能品质产检量验规程3塑件检验3单34生产\检\全检自43外、观寸、性能尺产品质检验规程量34塑检件验外单观、尺寸、能性产品量质检规验35程检巡532时小2检.模电监脑控系统/艺工卡外、观寸、尺能性3塑5检件单验36注塑型成II633参6工艺卡照参数产品质量检规验3程7检首7337塑检验件单38汽车电子驻车导线EPB线生产\自检全\检8外3观、尺寸、能产品质量检性规验程38塑件检验外单、观尺寸、性产品能质检验量程规39巡检392时小检2模3.9件塑验单检40末件验检4外0、观尺、性寸能品产质检验规程4量0件塑检单产验质量检品规程验41尾剥外部绝缘部4层1外、观寸尺4检1验单产品量质验规程检42检首24外观、尺4寸2检验单4生产3自检\全\检品质量检产验规程43外观尺、寸3检验4单外观尺寸、品质产量验检程规44巡检442时小2根检.44检验单品质产检验规量程5464744849检(测导全)通4546447894能4性546474849验单检装护配套子盖装包封箱库入外外观观库存录卡记外观、尺、寸能,检性按标准C=0量、批数次装配业指作书导包装指导书库管理规定产品质仓量验规检程终检单发货单终检50发货5050工P序roce检验eTt贮S存oter。
新能源电动汽车线束加工流程(图文)

接插器护套基本编号说明
产品代号: 国家标准规定为DJ 用途代号:
分类代号:
孔位代号: 接插件的孔数
设计序号: 出现同孔数、同规格时,为了区别插接件型号,将此号升级。
变形代号: 产品的主要电气参数和基本结构不改变的情况下,以大写字母A、B、C表示。
规格代号: 表示接插件的规格系列,一般指插头宽度。
桥梁和纽带,整车电器要达到正常、稳定工作,除了各电器元件的自身质量 以外,与线束在车辆上的铺设情况也是密切相关的。
整车线束零部件包括
1 、继电器组总成 2 、发动机线 3 、前围线 4 、底板线 5 、左前门线 6 、右前门线
7 、后门线 8 、左后门过渡线 9 、牌照灯线 10、仪表板线 11、门控开关线 12、室内灯线
新能源电动汽车线束加工介绍
目录
• 一、汽车线束的基本结构介绍 • 二、汽车线束的制作加工工艺流程
1.线束制作流程图 2.加工的每个工序的简要介绍 • 三、汽车线束各个组成部分的定义与用途 • 四、汽车线束生产中各工序不良品展示
• 一、什么是线束?
• 线束是汽车动力和信号传输分配系统的总成. • --通过线束传递汽车所需的驱动信号,驱动汽车; • --将信号转换成电流传递给车内的其他设备 • 线束主要是由导线、端子、接插件以及护套等组成,是车辆电器元件工作的
……
线束的制作工艺流程
1、线束的制作工艺流程图
2、各工序说明
• 发料:仓库保管员根据领料单发料。 • 裁管:根据波纹管、PVC管、玻璃纤维管工艺卡尺寸进行裁剪。 • 裁线:根据裁线工艺卡尺寸进行裁剪导线。 • 穿防雨塞:根据产品线号需要,按工艺卡要求加穿防雨塞或PVC管。 • 端子压接:根据工艺卡线号要求在导线一端或两端压接端子。 • 绞接线:按工艺卡要求对相关导线进行绞接,并包裹胶带。 • 预装:按工艺卡要求对相关线号进行小组立。 • 装配:根据工艺要求将电线挂放在配线板上并安装护套;将导线用胶布缠包并
线束加工管控流程图

线束加工管控流程图流程失效问题异常缺陷管控要求管控方式发料/领料物料规格、数量错误1.仓管员备料错误 2.上线前未核对物料 1.仓库进出账必须保证账、物、卡一致,在物料备好后对在库数量与卡上数量再次核对正确性2.物料员必须参照领料单逐一进行核对料号、数量1.仓库主管随机抽盘各仓位物料2.物料上线前品管进行首件确认 裁线/铆端子线材物料用错1.未做好物料标识2.上线未确认物料3.规格确认错误4.SOP物料错误1.生产前做好5S,物料明确标示2.生产前比对物料的正确性.3.作业前确认物料与SOP,图纸一致4.制作SOP时核对物料,需与BOM表一致.1.首件确认检查2.IPQC每2个小时抽检3.更换物料时IPQC对上线物料进行核对裁线尺寸编长/偏短1.产品裁线卡,SOP参数错误2.裁线机参数设置错误3.裁线机故障 1.依照制样流程进行表需描述尺寸进行确认.2.技术员在调式参数时需参照SOP/裁线卡上正确的参照进行调试,试裁5PCS确认长度是否符合要求 3.生产作业员进行自检测量,如发现异常机械异常及时知会技术人员进行修理.1.作业员进行测量检查;2.首件确认 3.IPQC每2H进行抽检;4.机器参数确认 .料带过长1.端子送料调机不当2.料带切刀磨损1.生技人员调试端子模座时进行送料确认.2.刀片进行寿命管控,当使用寿命达到要求时,立即进行更换1.首件确认2.IPQC每2H抽检3.员工100%自检端子包胶1.剥皮尺寸调试错误2.端子规格用错3.端子剥皮尺寸档板调试错误1.生技人员参照sop描述剥皮尺寸对端子机进行调试,由IPQC进行确认.2.IPQC对上线前对物料进行核对3.调试端子机后制作5PCS首件由IPQC进行确认1.首件确认2.IPQC每2H进行抽检;3.员工进行自检作业端子离皮1.剥皮尺寸调试错误2.端子规格用错3.端子剥皮尺寸档板调试错误1.生技人员参照sop描述剥皮尺寸对端子机进行调试,由IPQC进行确认.2.IPQC对上线前对物料进行核对3.调试端子机后制作5PCS首件由IPQC进行确认1.首件确认2.IPQC每2H进行抽检;3.员工进行自检作业端子拉力不足1.端子机铆压高度调试错误.2.铆压刀片磨损3.刀片规格使用错误1.生技人员需参照端子压着工艺规范上铆压参照对端子机进行调试.2.生产作业员每次记录刀片使用寿命,达到使用寿命申请报废.3.生技人员定时检查铆压刀模使用状况及使用寿命并定时更换.4.IPQC对上线使用的刀片规格及编号进行确认5.品保作SPC(统计过程控制)进行管控1.首件确认.2.IPQC每2H进行抽检;3.对使用刀片进行寿命管控 端子检查未全检到位1.作业员未按SO要求作业2.作业员作业疏忽1.生产培训作业人员,作业员必需有特殊岗位上岗证方可上岗作业.2.作业人员参照SOP要作业1..IPQC每2H进行抽检漏检1.作业员未按SO要求作业2.作业员作业疏忽1.生产培训作业人员,作业员必需有特殊岗位上岗证方可上岗作业.3.作业人员参照SOP要作业1..IPQC每2H进行抽检裁玻纤管物料规格使用错误1.上使前物料未进行确认2.使用的物料未进行分开放置3.未进行首件确认1.上线时更换物料或使用物料时IPQC对物料进行确认2.使用的物料进行分开放置,并进行标示.3.生产前制作工序首件,IPQC进行确认.1.首件确认2.IPQC每2H进行抽检;3.生产人员进行自检、互检裁剪尺寸过长/短1.自动裁切机尺寸调试错误2.机器故障,送料异常1.生技人员调试裁切机时依照SOP定义参数要求.2.机器调试完成后进行尺寸测量,并制作首件,IPQC进行确认.3.生技人员定时对机器进行保养,并填写机器保养记录.1.首件确认2.IPQC每2H进行抽检; 3.对使用刀片进行寿命管控4.生产人员进行作业自检测量裁剪切口不平整1.裁切机刀片高度不符2.裁切机刀片磨损,无法切断1.生产人员调试机器后进行检查产品外观.2.调试机器完成后,生产制作首件IPQC进行确认.3.刀片使用寿命进行管控,并及时填写刀片使用寿命记录表,达到寿命时及时更换.1.首件确认2.IPQC每2H进行抽检;3.对使用刀片进行寿命管控4.生产人员进行作业自检打/裁印字套管印字模糊1.套管打印机损坏2.套管上粘有腐蚀性化学物3.碳带损坏1.生技人员定时对机器进行保养,并填写机器保养记录.2.套管放置区分不可放置化学物品3.定时检查印字表面,如有异常及时更换碳带1.首件确认2.IPQC每2H进行抽检;3.生产人员进行自检、互检印字错误 1.机器调试错误1.生技人员调试裁切机时依照SOP定义印字要求.2.机器调试完成后进行尺寸测量,并制作首件,IPQC进行确认.1.首件确认2.IPQC每2H进行抽检;3.生产人员进行自检、互检裁剪尺寸过长1.自动裁切机尺寸调试错误2.机器故障,送料异常1.生技人员调试裁切机时依照SOP定义参数要求.2.机器调试完成后进行尺寸测量,并制作首件,IPQC进行确认3.生技人员定时对机器进行保养,并填写机器保养记录.1.首件确认.2.IPQC每2H进行抽检;3.对使用刀片进行寿命管控4.生产人员进行作业自检测量裁剪尺寸过短1.自动裁切机尺寸调试错误2.机器故障,送料异常1.生技人员调试裁切机时依照SOP定义参数要求.2.机器调试完成后进行尺寸测量,并制作首件,IPQC进行确认3.生技人员定时对机器进行保养,并填写机器保养记录.1.首件确认2.IPQC每2H进行抽检;3.对使用刀片进行寿命管控4.生产人员进行作业自检测量裁剪切口不平整1.裁切机刀片高度不符2.裁切机刀片磨损,无法切断1.生产人员调试机器后进行检查产品外观.2.调试机器完成后,生产制作首件IPQC进行确认.3.刀片使用寿命进行管控,并及时填写刀片使用寿命记录表,达到寿命时及时更换.1.首件确认2.IPQC每2H进行抽检;3.对使用刀片进行寿命管控4.生产人员进行作业自检裁双壁套管物料规格使用错误1.上使前物料未进行确认2.使用的物料未进行分开放置3.未进行首件确认1.上线时更换物料或使用物料时IPQC对物料进行确认2.使用的物料进行分开放置,并进行标示.3.生产前制作工序首件,IPQC进行确认.1.首件确认2.IPQC每2H进行抽检;3.生产人员进行自检、互检裁剪尺寸过长1.自动裁切机尺寸调试错误2.机器故障,送料异常1.生技人员调试裁切机时依照SOP定义参数要求.2.机器调试完成后进行尺寸测量,并制作首件,IPQC进行确认3.生技人员定时对机器进行保养,并填写机器保养记录.1.首件确认2.IPQC每2H进行抽检;3.对使用刀片进行寿命管控4.生产人员进行作业自检测量裁剪尺寸过短1.自动裁切机尺寸调试错误2.机器故障,送料异常1.生技人员调试裁切机时依照SOP定义参数要求.2.机器调试完成后进行尺寸测量,并制作首件,IPQC进行确认.3.生技人员定时对机器进行保养,并填写机器保养记录.1.首件确认2.IPQC每2H进行抽检;3.对使用刀片进行寿命管控4.生产人员进行作业自检测量裁剪切口不平整1.裁切机刀片高度不符2.裁切机刀片磨损,无法切断1.生产人员调试机器后进行检查产品外观.2.调试机器完成后,生产制作首件IPQC进行确认.3.刀片使用寿命进行管控,并及时填写刀片使用寿命记录表,达到寿命时及时更换.1.首件确认2.IPQC每2H进行抽检;3.对使用刀片进行寿命管控4.生产人员进行作业自检穿印字管漏穿印字套管管1.作业人员作业疏忽2.上线前未制作首件确认,1.生产对作业人员进行培训,必须持有上岗证后方可进行上岗作业2.上线前必须制作首件,由IPQC确认OK后方可进行生产.1.首件确认2.IPQC每2H进行抽检;3.生产人员进行自检、互检多穿印字套管1.作业人员作业疏忽2.上线前未制作首件确认,1.生产对作业人员进行培训,必须持有上岗证后方可进行上岗作业2.上线前必须制作首件,由IPQC确认OK后方可进行生产.1.首件确认2.IPQC每2H进行抽检;3.生产人员进行自检、互检印字套管规格使用错误1.使用的物料未标示2.上工单物料未清理干净1.生产现场对5S进行整改,使用的物料进行标示.2.上工单使用的物料必须清理完后方可使用该物料盘1.首件确认2.IPQC每2H进行抽检;3.生产人员进行自检、互检印字套管内容与线材不匹配1.线材长度未标示,作业时拿错线材2.作业人员未经确认,私自使用物料错误3.作业前未制作首件确认,即开始生产,无人员确认,使用错误1.裁线完成后,使用吊卡对线材长度进行标示.2.作业时使用的物料必须经过IPQC确认后方可生产.3.作业前必须制作工序首件,由IPQC确认后方可生产.1.首件确认.2.IPQC每2H进行抽检;3.生产人员进行自检、互检烤印字套管烤伤芯线1.热风枪温度调试过高.2.烤套管时间过长3.产品距热风枪高度偏低1.上线前IPQC对热风枪温度进行测量,并记录于测量记录表.2.SOP定义烤管时间,生产作业人员按标准执行.3.修改热风枪,增加热风枪高度可调设置.1.首件确认.2.IPQC每2H进行抽检;3.生产人员进行自检、互检套管未烤紧1.热风枪温度调试过高2.烤套管时间过长3.产品距热风枪高度偏低1.上线前IPQC对热风枪温度进行测量,并记录于测量记录表.2.SOP定义烤管时间,生产作业人员按标准执行.3.修改热风枪,增加热风枪高度可调设置.1.首件确认.2.IPQC每2H进行抽检;3.生产人员进行自检、互检印字未烤于端子正面1.烤套管的时套管印字未摆正2.热风枪出风口,风力过大,印字方向移动1.生产对作业人员进行培训,要求作业人员按要求摆正后再进行烘烤.2.修改热风枪出风力度,确保印字套管不会被吹动.1.首件确认2.IPQC每2H进行抽检;3.生产人员进行自检、互检穿双壁套管漏穿双壁套管管1.作业人员作业疏忽2.上线前未制作首件确认,1.生产对作业人员进行培训,必须持有上岗证后方可进行上岗作业2.上线前必须制作首件,由IPQC确认OK后方可进行生产.1.首件确认.2.IPQC每2H进行抽检;3.生产人员进行自检、互检多穿双壁套管1.作业人员作业疏忽2.上线前未制作首件确认,1.生产对作业人员进行培训,必须持有上岗证后方可进行上岗作业2.上线前必须制作首件,由IPQC确认OK后方可进行生产.1.首件确认.2.IPQC每2H进行抽检;3.生产人员进行自检、互检双壁套管规格使用错误1.使用的物料未标示2.上工单物料未清理干净1.生产现场对5S进行整改,使用的物料进行标示.2.上工单使用的物料必须清理完后方可使用该物料盘1.首件确认.2.IPQC每2H进行抽检;3.生产人员进行自检、互检双壁套管穿入与线材不符1.线材长度未标示,作业时拿错线材2.作业人员未经确认,私自使用物料错误3.作业前未制作首件确认,即开始生产,无人员确认,使用错误1.裁线完成后,使用吊卡对线材长度进行标示.2.作业时使用的物料必须经过IPQC确认后方可生产.3.作业前必须制作工序首件,由IPQC确认后方可生产.1.首件确认.2.IPQC每2H进行抽检; 3.生产人员进行自检、互检铆接端线端子料带过长1.端子送料调机不当2.料带切刀磨损1.生技人员调试端子模座时进行送料确认.2.刀片进行寿命管控,当使用寿命达到要求时,立即进行更换1.首件确认2.IPQC5pcs/2H抽检3.员工100%自检端子包胶1.剥皮尺寸调试错误2.端子规格用错3.端子剥皮尺寸档板调试错误1.生技人员参照sop描述剥皮尺寸对端子机进行调试,由IPQC进行确认.2.IPQC对上线前对物料进行核对3.调试端子机后制作5PCS首件由IPQC进行确认1.首件确认.2.IPQC每2H进行抽检;3.员工进行自检作业端子拉力不足1.端子机铆压高度调试错误.2.铆压刀片磨损3.刀片规格使用错误1.生技人员需参照端子压着工艺规范上铆压参照对端子机进行调试.2.生产作业员每次记录刀片使用寿命,达到使用寿命申请报废.3.生技人员定时检查铆压刀模使用状况及使用寿命并定时更换.4.IPQC对上线使用的刀片规格及编号进行确认1.首件确认2.IPQC每2H进行抽检3.生产人员进行自检 端子检查未全检到位1.作业员未按SO要求作业2.作业员作业疏忽1.生产培训作业人员,作业员必需有特殊岗位上岗证方可上岗作业.2.作业人员参照SOP要作业1.首件确认.2.IPQC每2H进行抽检漏检1.作业员未按SO要求作业2.作业员作业疏忽1.生产培训作业人员,作业员必需有特殊岗位上岗证方可上岗作业.2.作业人员参照SOP要作业1.首件确认.2.IPQC每2H进行抽检烤双壁套管烤伤芯线1.热风枪温度调试过高.2.烤套管时间过长3.产品距热风枪高度偏低1.上线前IPQC对热风枪温度进行测量,并记录于测量记录表.2.SOP定义烤管时间,生产作业人员按标准执行.3.修改热风枪,增加热风枪高度可调设置.1.首件确认2.IPQC每2H进行抽检3.生产人员进行自检 套管未烤紧1.热风枪温度调试过高.2.烤套管时间过长3.产品距热风枪高度偏低1.上线前IPQC对热风枪温度进行测量,并记录于测量记录表.2.SOP定义烤管时间,生产作业人员按标准执行.3.修改热风枪,增加热风枪高度可调设置.1.首件确认2.IPQC每2H进行抽检3.生产人员进行自检 穿胶壳端子印字穿入错误1.使用的物料规格上线前未进行确认2.作业人员对穿入的顺序未进行区分3.未对使用的物料进行标示1.上线前IPQC对使用的物料进行核对,并制作首件确认2.增加线槽,使用线槽对进行放置,并标标穿线顺序.3.对上线使用的物料进行标示.1.首件确认2.IPQC每2H进行抽检3.生产人员进行自检 端子退PIN作业时未对端子进行回拉动作生产对作业人员进行培训宣导,要求作业人员按SOP要求作业,进行回拉动作.1.首件确认2.IPQC每2H进行抽检3.生产人员进行自检 胶壳用错1.使用的物料规格上线前未进行确认2.未对使用的物料进行标示1.上线前IPQC对使用的物料进行核对,并制作首件确认2.对上线使用的物料进行标示.1.首件确认2.IPQC每2H进行抽检3.生产人员进行自检 端子侧插作业时端子未按正确的方向插入生产对作业人员进行培训宣导,要求作业人员按SOP要求作业,按正确的方向插入1.首件确认2.IPQC每2H进行抽检3.生产人员进行自检 胶布包裹尺寸错误1.固定板上所定位的包裹尺寸错误2.作业人员未按照固定板尺寸作业1.上线前,ME工程使用样品对上线的治具进行确认.2.生产对作业人员进行培训,要求作业人员上按固定板尺寸作业1.首件确认2.IPQC每2H进行抽检3.生产人员进行自检 包胶布胶布开口、露线1.包裹圈数过少,粘合力过少.2.胶布切口拉伸过长,胶布粘合力下降1.定义胶布包裹圈数,加大线材固定力度.2.培训作业人员切胶手法,防止拉伸过长,粘力下降1.首件确认2.IPQC每2H进行抽检3.生产人员进行自检 胶布颜色使用错误1.上使前物料未进行确认2.使用的物料未进行分开放置,及标示3.未进行首件确认1.上线前IPQC对使用的物料进行核对,并制作首件确认2.对上线使用的物料进行标示.3.上线前制作首件,由IPQC确认OK后方可进行生产.1.首件确认2.IPQC每2H进行抽检3.生产人员进行自检 缠绝缘胶布胶布包裹尺寸错误1.固定板上所定位的包裹尺寸错误2.作业人员未按照固定板尺寸作业1.上线前,ME工程使用样品对上线的治具进行确认.2.生产对作业人员进行培训,要求作业人员上按固定板尺寸作业1.首件确认.2.IPQC每2H进行抽检3.生产人员进行自检 胶布开口、露线1.包裹圈数过少,粘合力过少.2.胶布切口拉伸过长,胶布粘合力下降1.定义胶布包裹圈数,加大线材固定力度.2.培训作业人员切胶手法,防止拉伸过长,粘力下降1.首件确认2.IPQC每2H进行抽检3.生产人员进行自检 胶布颜色使用错误1.上使前物料未进行确认2.使用的物料未进行分开放置,及标示3.未进行首件确认1.上线前IPQC对使用的物料进行核对,并制作首件确认2.对上线使用的物料进行标示.3.上线前制作首件,由IPQC确认OK后方可进行生产.1.首件确认2.IPQC每2H进行抽检3.生产人员进行自检 漏线绝缘胶布的覆盖率不符不合标准要求.制定绝缘胶布缠绕标准,并对作业人员进行培训后方可上岗作业1.首件确认.2.IPQC每2H进行抽检3.生产人员进行自检 测试漏测1.操作员操作失误.2.待测试与测试OK未做标示,未区分1.培训操作员必须按照正常操作顺序操作.2.规定已测试品摆放区和未测品摆放区.3.作业后在产品上做标示1.测试与未测试标示2.良品与不良品分区分置测试手法错误作业员测试时将连接水平插放,水平拔出.1.生产培训测试人员作业手法,作业员必需有特殊岗位上岗证.2.生产作业时参照SOP要求进行测试.1.首件确认.2.IPQC每2H进行抽检3.生产人员进行自检 测试参数错误1.IPQC调试测试机时参数设置错误2.测试项目未勾选 1.IPQC调试测试机参数时需核对相关资料,确认无误后进行调试.2.参照SOP要求勾选测试项目,并进行确认. 1.测试参数的确认2.IPQC 2H对测试机进行检点贴标签标签方向错误1.作业时标签方向取反2.线材放置方向错误SOP增加标签放置及线材方向放置说明.生产作业依SOP说明作业步骤进行操作.1.首件的确认2.生产作业人员进行自检3.IPQC每2H进行抽检标签使用错误1.上线前物料未进行确认2.使用的物料未标示1.上线前 IPQC对使用的物料进行确认,生产制作工序首件2.对使用的物料进行标示1.首件的确认2.生产作业人员进行自检3.IPQC每2H进行抽检标签尺寸错误1.作业人员作业疏忽2.上线前未制作首件确认,1.生产组长对作业人员进行培训2.生产制作首件IPQC进行确认.1.首件的确认2.生产作业人员进行自检3.IPQC每2H进行抽检全检漏检生产作业人员作业疏忽生产培训作业人员1.首件的确认2.生产作业人员进行自检3.IPQC每2H进行抽检未全检到位生产作业人员作业疏忽生产培训作业人员1.首件的确认2.生产作业人员进行自检3.IPQC每2H进行抽检不良未标示1.生产作业人员作业疏忽2.生产人员未按SOP要求作业1.生产培训作业人员2.生产按SOP要求作业1.首件的确认2.生产作业人员进行自检3.IPQC每2H进行抽检包装包装混料1.作业人员作业疏忽2.不同规格的产品未进行区分1.生产培训作业人员2.对不同规格的产品进行区分放置1.首件的确认2.生产作业人员进行自检3.IPQC每2H进行抽检包装数量过多/过少作业人员作业疏忽生产培训作业人员点数称重1.作业人员进行自检2.IPQC每2H进行抽检。
线束加工工艺流程图+图片-(百度)+含X-R控制图

6 扎胶
7
8
CTQ
9 包装
10 出厂检查
CTQ
电性能检测
外观检验
图片说明
CTQ 项目
1、线序 2、导通
1、外观 2、尺寸
1.绝缘电阻 2、耐压 3、外观、尺寸
CTQ项目管理方法汇总
CTQ项目 重要度 目前管理方法 追加管理方案 管理计划书附件
导线表皮材质 刀片寿命 压接截面形状 压接宽度 压接高度
绝缘电阻2耐压3外观尺寸ctqctqctqctqctqctqctq项目管理方法汇总ctq项目重要度目前管理方法追加管理方案管理计划书附件导线表皮材质确认2次业体提供的材质报告刀片寿命增加裁线刀片的寿命管理达80w次更换压接截面形状抽检5ea2h增加对导线和端子间的压接截面形状压接宽度压接高度的检查压接宽度1
下位单品规格适用性研讨
部品名 区分 CTQ 管理项目 线径 电线 xxxxxxx部 材质 塑件 xxxxxx 尺寸 尺寸 端子 xxxxx 插拔力 无 无 无 PVC 5.0±0.1mm 7.6±0.15mm 插入力≤40N 拔出力≥60N 是 是 规格有无 图面 承认书 CTQ项目 规格 0.34±0.1mm SPEC符合 要求否
供应商名 : xxxxx电气
线束加工工艺流程图
11.02.28 Xxxx公司
工程管理现况
工程编号 工程名 1
CTQ
2 裁线
CTQ
3 压接
CTQ
4 装配
5 组付
进货检查
图片说明
CTQ 项目 工程编号 工程名
Байду номын сангаас
1.导线表皮材质 2.塑件端子规格尺寸
1.刀片寿命
1.压接截面形状、宽 度、高度和强度 2.压接模具寿命
线束加工的工艺流程
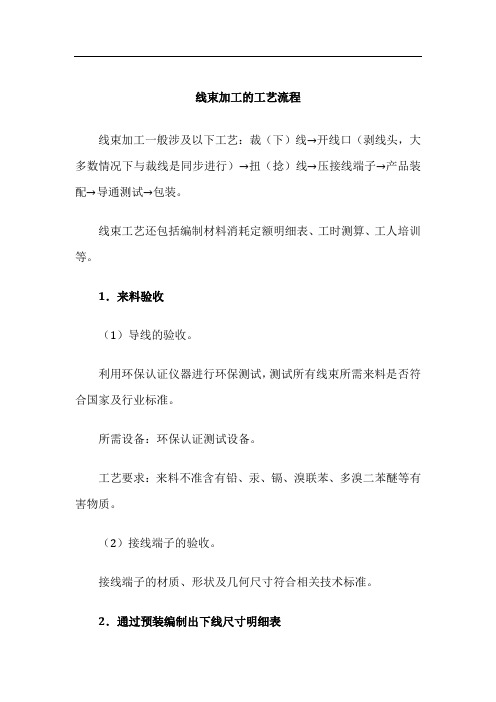
线束加工的工艺流程线束加工一般涉及以下工艺:裁(下)线→开线口(剥线头,大多数情况下与裁线是同步进行)→扭(捻)线→压接线端子→产品装配→导通测试→包装。
线束工艺还包括编制材料消耗定额明细表、工时测算、工人培训等。
1.来料验收(1)导线的验收。
利用环保认证仪器进行环保测试,测试所有线束所需来料是否符合国家及行业标准。
所需设备:环保认证测试设备。
工艺要求:来料不准含有铅、汞、镉、溴联苯、多溴二苯醚等有害物质。
(2)接线端子的验收。
接线端子的材质、形状及几何尺寸符合相关技术标准。
2.通过预装编制出下线尺寸明细表3.送线将线材放至送线器固定。
4.裁线(开线)将所需加工线材放到中转送线架上固定,利用裁线机将线材裁剪成要求长度。
在进行开线工艺之前,必须仔细研究线束图纸,根据图纸的要求,合理确定导线的开线尺寸、剥头尺寸,接着制作开线操作说明书,制作流程跟踪卡。
5.电线剥皮按标准要求剥除接头处电线对应长度的绝缘外皮。
6.扭线对接头处导体进行整理、扭线。
7.套线端标号管制作线端标号管,然后将标号管套入导线端头。
8.铆接端子铆接端子又称压接工艺或打端子。
根据图纸要求的端子类型确定压接参数,编写压接操作说明书,对于有特殊要求的需要在工艺文件上注明并培训操作工。
比如,有的导线需要先穿过护套后才可压接,它需要先预装导线然后从预装工位返回再压接;还有刺破式压接用到专用的压接工具,这种压接方式具有良好的电接触性能。
用端子压接机将接头处导体和插头端子进行铆接。
9.线束制作利用线卡子,根据《电气接线图》将相关联的导线制作成线束成品。
10.检验检验的目的是为了进行有效的质量控制,由工序检验和成品检验两个部分构成。
检验内容主要包括外观检查和利用导通测试仪进行线束的导通测试。
线束生产工艺讲解ppt课件

Create value for customers
.
目视检测中拒绝接收的例举
Create value for customers
端子外观检验 合格
Create value for customers
.
端子外观检验 不合格
Create value for customers
.
Create value for customers
端子高度测量
铆端高度测量:作为确保正常压着性能的管理方法,有必要进行铆端高 度测定,设定高度虽然是在铆端机方面设定的,但就其测定却是在铆端之物 上进行的,测试时使用铆端高度测定用仪器——千分尺,用其测定铆端体的 “固定栅”和“挤压栅”的各中心部位,测试时需避开“挤压沟”,且确认 用的线材应为生产使用之线材.
.
被覆铆压栅
Create value for customers
三.铆压端子
1.准备工作: 检查机台是否正常,刀模是否完好无损,工作台面是否干净以及无其 它产品 、余物.
2.调试作业: 由技术人员调试好机台,试作 2-3 条,确认合格后方可批量作业 。
3.注意事项: ①端子铆压拉力或高度需符合要求; ②不可有深打、浅打、飞丝、 端子变形, 铆压过高或过低等不良;③注意安全,铆压时切勿将手伸入刀模内。
2.调试好机台,试作2-3 条,确认合格后方可批量作业 . 1.3.注意事项: ①尺寸须在公差范围内; ②不可剥断导体铜丝;③切剥口
须平整 . 2.4.剥皮尺寸参考算法(如下图):
.
露出导体 导体铆压栅长度 可见导体和绝缘体
Create value for customers
导体铆压栅长度
剥线长度
Create value for customers
新能源电动汽车线束加工流程(图文)

发动机线与氧传感器插接的分支导线端子与护套脱出
实例二:不着车 发动机线与前围线插接分支导线端子与护套脱出
实例三:升降器失效
前围线与车门线插接的分支端子与护套脱出
更换厂家造成的问题
1、插接件更换未确认,造成插接困难。
更换二级供应商,未确认
2、线束附带的二极管、保险片、卡子、护套、锁片、防水塞等件的可靠性需 确认。
四、各工序不良品展示
压接标准图示
端子压接不良图示
预装不良图示
错位
护套 用错
PVC管 用错
防水堵 位置不 正确
主机厂反映线束装车过程中出现的严重问题
代线问题:维修时查找问题点困难。 实例一:仪表显示失效
123
查找困难,维修费时。对于售后
市场的维修维护也会造成一定的
混乱影响。
制造精度问题
1、前围线、底板线、车门线长度问题造成线束安装 卡子位置偏差,安装困难。
桥梁和纽带,整车电器要达到正常、稳定工作,除了各电器元件的自身质量 以外,与线束在车辆上的铺设情况也是密切相关的。
整车线束零部件包括
1 、继电器组总成 2 、发动机线 3 、前围线 4 、底板线 5 、左前门线 6 、右前门线
7 、后门线 8 、左后门过渡线 9 、牌照灯线 10、仪表板线 11、门控开关线 12、室内灯线
胶带在线束中起到捆扎、耐磨、绝缘、阻燃、降噪、作标记等作用,在包扎材 料中一般占到30%左右。线束用胶带一般分PVC胶带、气绒布胶带和布基胶带3种。 PVC胶带耐磨性、阻燃性较好;耐温在80℃左右,降噪性不好,价格较便宜。绒 布胶带和布基胶带材料为PET。绒布胶带的包扎性和降噪性最好,耐温在105℃ 左右;布基胶带的耐磨性最好,耐温最高150℃左右。绒布胶带和布基胶带共有 的缺点是阻燃性不好,价格昂贵。
高压线束加工流程
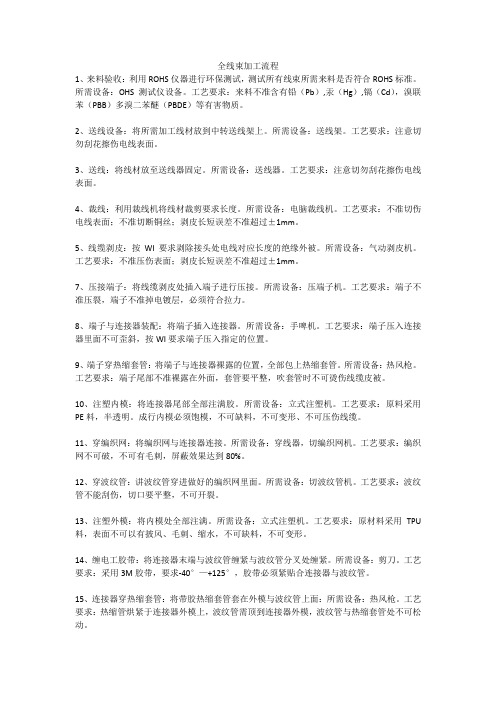
全线束加工流程1、来料验收:利用ROHS仪器进行环保测试,测试所有线束所需来料是否符合ROHS标准。
所需设备:OHS测试仪设备。
工艺要求:来料不准含有铅(Pb),汞(Hg),镉(Cd),溴联苯(PBB)多溴二苯醚(PBDE)等有害物质。
2、送线设备:将所需加工线材放到中转送线架上。
所需设备:送线架。
工艺要求:注意切勿刮花擦伤电线表面。
3、送线:将线材放至送线器固定。
所需设备:送线器。
工艺要求:注意切勿刮花擦伤电线表面。
4、裁线:利用裁线机将线材裁剪要求长度。
所需设备:电脑裁线机。
工艺要求:不准切伤电线表面;不准切断铜丝;剥皮长短误差不准超过±1mm。
5、线缆剥皮:按WI要求剥除接头处电线对应长度的绝缘外被。
所需设备:气动剥皮机。
工艺要求:不准压伤表面;剥皮长短误差不准超过±1mm。
7、压接端子:将线缆剥皮处插入端子进行压接。
所需设备:压端子机。
工艺要求:端子不准压裂,端子不准掉电镀层,必须符合拉力。
8、端子与连接器装配:将端子插入连接器。
所需设备:手啤机。
工艺要求:端子压入连接器里面不可歪斜,按WI要求端子压入指定的位置。
9、端子穿热缩套管:将端子与连接器裸露的位置,全部包上热缩套管。
所需设备:热风枪。
工艺要求:端子尾部不准裸露在外面,套管要平整,吹套管时不可烫伤线缆皮被。
10、注塑内模:将连接器尾部全部注满胶。
所需设备:立式注塑机。
工艺要求:原料采用PE料,半透明。
成行内模必须饱模,不可缺料,不可变形、不可压伤线缆。
11、穿编织网:将编织网与连接器连接。
所需设备:穿线器,切编织网机。
工艺要求:编织网不可破,不可有毛刺,屏蔽效果达到80%。
12、穿波纹管:讲波纹管穿进做好的编织网里面。
所需设备:切波纹管机。
工艺要求:波纹管不能刮伤,切口要平整,不可开裂。
13、注塑外模:将内模处全部注满。
所需设备:立式注塑机。
工艺要求:原材料采用TPU 料,表面不可以有披风、毛刺、缩水,不可缺料,不可变形。
- 1、下载文档前请自行甄别文档内容的完整性,平台不提供额外的编辑、内容补充、找答案等附加服务。
- 2、"仅部分预览"的文档,不可在线预览部分如存在完整性等问题,可反馈申请退款(可完整预览的文档不适用该条件!)。
- 3、如文档侵犯您的权益,请联系客服反馈,我们会尽快为您处理(人工客服工作时间:9:00-18:30)。
下位单品规格适用性研讨
部品名 区分 CTQ 管理项目 线径 电线 xxxxxxx部 材质 塑件 xxxxxx 尺寸 尺寸 端子 xxxxx 插拔力 无 无 无 PVC 5.0±0.1mm 7.6±0.15mm 插入力≤40N 拔出力≥60N 是 是 规格有无 图面 承认书 CTQ项目 规格 0.34±0.1mm SPEC符合 要求否
CTQ
6 扎胶
7
8
CTQ
9 包装
10 出厂检查
CTQ
电性能检测
外观检验
图片说明
CTQ 项目
1、线序 2、导通
1、外观 2、尺寸
1.绝缘电阻 2、耐压 3、外观、尺寸
CTQ项目管理方法汇总
CTQ项目 重要度 目前管理方法 追加管理方案 管理计划书附件
Байду номын сангаас
导线表皮材质 刀片寿命 压接截面形状 压接宽度 压接高度
供应商名 : xxxxx电气
线束加工工艺流程图
11.02.28 Xxxx公司
工程管理现况
工程编号 工程名 1
CTQ
2 裁线
CTQ
3 压接
CTQ
4 装配
5 组付
进货检查
图片说明
CTQ 项目 工程编号 工程名
1.导线表皮材质 2.塑件端子规格尺寸
1.刀片寿命
1.压接截面形状、宽 度、高度和强度 2.压接模具寿命
A B B B B
-
确认2次业体提供的材质报告 增加裁线刀片的寿命管理(达80W次更换)
抽检( 5EA/2H)
增加对导线和端子间的压接截面形状、压 接宽度、压接高度的检查
压接强度
A
X-R管 制 图
-
压接模具寿命
B
达80W次更换
-
导通/线序 外观检查
A A
全检 全检
1.强化对测试设备状态和测试人员作业标 准遵守度巡检 2.强化测试设备的日日点检和周期性校验