线束生产工艺流程
线束工艺流程
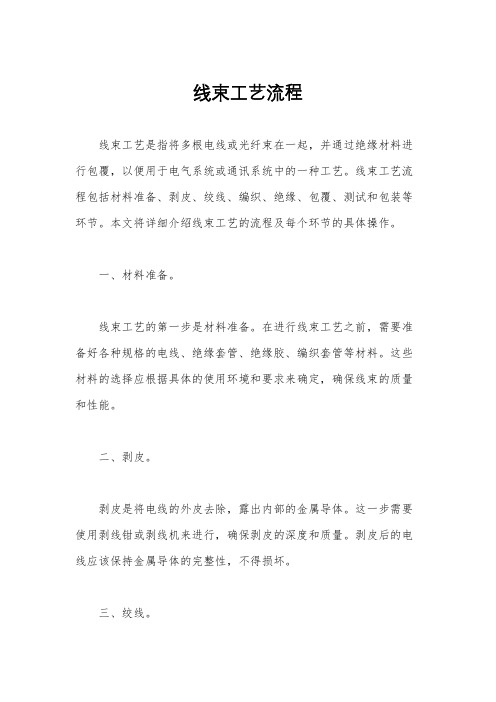
线束工艺流程线束工艺是指将多根电线或光纤束在一起,并通过绝缘材料进行包覆,以便用于电气系统或通讯系统中的一种工艺。
线束工艺流程包括材料准备、剥皮、绞线、编织、绝缘、包覆、测试和包装等环节。
本文将详细介绍线束工艺的流程及每个环节的具体操作。
一、材料准备。
线束工艺的第一步是材料准备。
在进行线束工艺之前,需要准备好各种规格的电线、绝缘套管、绝缘胶、编织套管等材料。
这些材料的选择应根据具体的使用环境和要求来确定,确保线束的质量和性能。
二、剥皮。
剥皮是将电线的外皮去除,露出内部的金属导体。
这一步需要使用剥线钳或剥线机来进行,确保剥皮的深度和质量。
剥皮后的电线应该保持金属导体的完整性,不得损坏。
三、绞线。
绞线是将多根电线按照一定的规则进行捆绑和绞合,使其成为一个整体。
这一步需要根据具体的线束设计要求进行操作,确保电线之间的布局合理、紧凑,并且不会相互干扰。
四、编织。
编织是将绞好的电线进行编织,以增强线束的抗拉强度和耐磨性。
编织材料可以是尼龙布、聚酯布等,根据具体的使用要求来选择。
编织后的线束应该外观整齐、紧密,不得有松散或交叉现象。
五、绝缘。
绝缘是为了保护线束中的电线不受外界环境的影响,使用绝缘套管或绝缘胶对电线进行包覆。
绝缘材料的选择应根据使用环境的温度、湿度等因素来确定,确保绝缘效果良好。
六、包覆。
包覆是将整个线束进行最终的包覆,通常使用PVC套管或热缩套管进行包覆。
包覆后的线束应该外观整洁、无气泡、无皱纹,确保线束的外观质量。
七、测试。
测试是对线束进行电学和机械性能的检测,确保线束的质量和性能达到要求。
电学测试包括导通测试、绝缘电阻测试等,机械性能测试包括拉力测试、耐磨测试等。
八、包装。
最后一步是将测试合格的线束进行包装,通常使用塑料袋或纸箱进行包装。
包装后的线束应该标明产品型号、规格、生产日期等信息,确保产品的追溯和售后服务。
以上就是线束工艺的流程及每个环节的具体操作。
通过严格的工艺流程和质量控制,可以生产出质量可靠的线束产品,满足不同领域的使用需求。
线束加工工艺流程
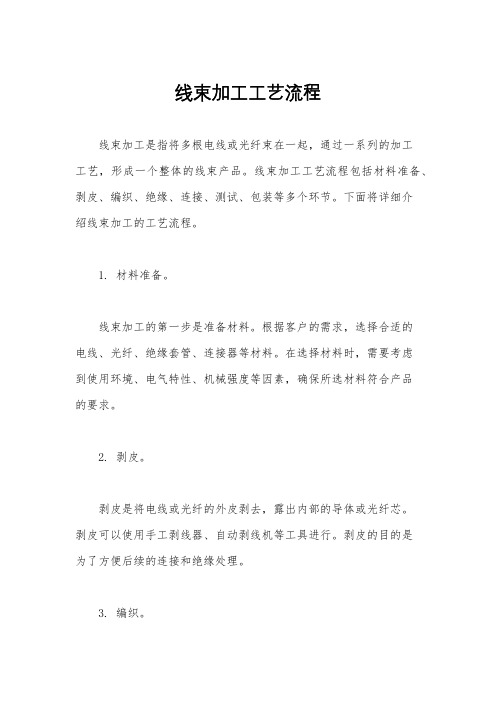
线束加工工艺流程线束加工是指将多根电线或光纤束在一起,通过一系列的加工工艺,形成一个整体的线束产品。
线束加工工艺流程包括材料准备、剥皮、编织、绝缘、连接、测试、包装等多个环节。
下面将详细介绍线束加工的工艺流程。
1. 材料准备。
线束加工的第一步是准备材料。
根据客户的需求,选择合适的电线、光纤、绝缘套管、连接器等材料。
在选择材料时,需要考虑到使用环境、电气特性、机械强度等因素,确保所选材料符合产品的要求。
2. 剥皮。
剥皮是将电线或光纤的外皮剥去,露出内部的导体或光纤芯。
剥皮可以使用手工剥线器、自动剥线机等工具进行。
剥皮的目的是为了方便后续的连接和绝缘处理。
3. 编织。
对于多根电线或光纤束,需要进行编织处理。
编织可以增加线束的机械强度,防止电磁干扰,提高线束的外观质量。
编织的方式有多种,可以根据产品的要求选择合适的编织工艺。
4. 绝缘。
绝缘是保护线束的重要工艺环节。
通过在导体或光纤周围套上绝缘套管或绝缘胶进行绝缘处理,确保线束在使用过程中不会因为外界环境导致短路或断线等问题。
5. 连接。
连接是将不同电线或光纤进行连接,形成一个完整的线束产品。
连接可以采用焊接、压接、插接等方式进行,确保连接牢固可靠,电气性能良好。
6. 测试。
在线束加工完成后,需要进行测试。
测试包括外观检查、电气性能测试、机械强度测试等多个方面。
通过测试,确保线束产品符合客户的要求和标准。
7. 包装。
最后一步是对线束产品进行包装。
包装可以采用盒装、卷装、托盘装等方式进行,确保产品在运输和储存过程中不受损坏。
通过以上的工艺流程,线束加工可以生产出符合客户要求的高质量线束产品。
线束加工工艺流程需要严格控制每个环节,确保产品的质量和性能达到标准要求。
同时,线束加工工艺流程也需要不断改进和优化,适应市场需求的变化,提高生产效率和产品质量。
线束生产工艺流程

线束生产工艺流程
线束生产工艺流程是指对线束的加工和组装过程进行规划和操作的一种方法。
下面是线束生产工艺流程的具体步骤:
1. 计划和准备:首先,根据订单要求和客户需求,制定生产计划,并准备所需的原材料、工具和设备。
2. 剥线:将线束的外皮剥离,露出内部的导线。
使用剥线机或手动剥线工具进行剥线操作。
3. 引线:根据线束设计图纸,将导线按照要求进行剪裁和引线操作。
使用剪线器、弯线器等工具,在导线两端制作引线。
4. 根据线束设计图纸进行组装:根据线束设计图纸上的标记,将引线和其他组件按照正确的顺序和位置进行组装。
在组装过程中,使用扭簧工具、码器、绝缘胶带等进行连接和固定。
5. 绝缘处理:将组装好的线束进行绝缘处理,以提高线束的安全性和可靠性。
可以使用热缩管、绝缘胶带等材料进行绝缘处理。
6. 测试和质检:对组装好的线束进行测试和质检,以确保其符合设计要求和客户需求。
使用测试仪器和设备,检测线束的电气性能和质量。
7. 包装和出货:对通过测试和质检的线束进行包装,确保其安全和易于运输。
根据客户要求,选择适当的包装材料和方法。
8. 收尾和记录:对生产过程进行收尾和记录。
清理和整理生产现场,记录生产过程中的关键数据和信息,以便日后追溯和改进。
以上就是线束生产工艺流程的主要步骤。
不同企业和产品的线束生产工艺流程可能略有差异,但整体流程大致相同。
通过严格按照工艺流程进行操作,可以确保线束生产的质量和效率,并满足客户的需求。
线束生产工艺流程

线束生产工艺流程一、材料准备线束生产的第一步是准备所需材料。
根据产品要求,选择适当的导电线、电缆、连接器和保护管等材料,并将其按照设计要求进行切割和标记。
同时,对必要的连接器和接线端子进行钝化处理,以提高其耐腐蚀性能。
二、导线剥皮和绝缘处理将准备好的导线放入自动剥皮机中进行剥皮处理,剥去一定长度的外皮,露出内部的导体。
随后,进行绝缘处理,将绝缘套和绝缘盖等绝缘材料套在导线上,确保导线的绝缘性能。
三、连接器组装将准备好的连接器和接线端子插入导线中,并使用压接工具进行压接。
压接时,要确保接线端子紧固可靠,并与导线的金属部分保持良好的接触,以保证电流的传输质量。
四、线束组装根据产品要求,将已经处理好的导线、连接器和保护管等器件进行组装。
在组装过程中,要注意线束的布线规划和布线路径,确保线束的结构紧凑和排列合理。
同时,根据需求使用束线带、束线管或绑扎带等材料对线束进行固定,以防止松动和磨损。
五、验收和测试线束组装完成后,进行质量验收和测试。
通过对线束的外观、尺寸、绝缘性能和连接性能等进行检查和测试,确保线束符合产品要求和标准。
特别是对连接器和接线端子的插拔性能、电阻和绝缘电阻等进行测试,以验证线束的性能和可靠性。
六、包装和出厂线束生产工艺流程主要包括材料准备、导线剥皮和绝缘处理、连接器组装、线束组装、验收和测试、包装和出厂等步骤。
通过严格按照流程进行生产,能够提高线束产品的质量和可靠性,满足客户的需求和要求。
同时,对每一道工序进行严格的质量控制,确保每一道工序的合格率和一次性合格率,降低不良品率,提高生产效率。
线束制作的流程范文
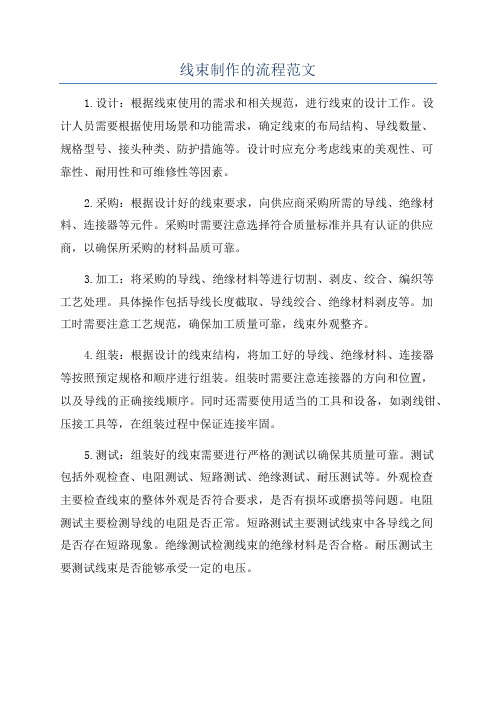
线束制作的流程范文1.设计:根据线束使用的需求和相关规范,进行线束的设计工作。
设计人员需要根据使用场景和功能需求,确定线束的布局结构、导线数量、规格型号、接头种类、防护措施等。
设计时应充分考虑线束的美观性、可靠性、耐用性和可维修性等因素。
2.采购:根据设计好的线束要求,向供应商采购所需的导线、绝缘材料、连接器等元件。
采购时需要注意选择符合质量标准并具有认证的供应商,以确保所采购的材料品质可靠。
3.加工:将采购的导线、绝缘材料等进行切割、剥皮、绞合、编织等工艺处理。
具体操作包括导线长度截取、导线绞合、绝缘材料剥皮等。
加工时需要注意工艺规范,确保加工质量可靠,线束外观整齐。
4.组装:根据设计的线束结构,将加工好的导线、绝缘材料、连接器等按照预定规格和顺序进行组装。
组装时需要注意连接器的方向和位置,以及导线的正确接线顺序。
同时还需要使用适当的工具和设备,如剥线钳、压接工具等,在组装过程中保证连接牢固。
5.测试:组装好的线束需要进行严格的测试以确保其质量可靠。
测试包括外观检查、电阻测试、短路测试、绝缘测试、耐压测试等。
外观检查主要检查线束的整体外观是否符合要求,是否有损坏或磨损等问题。
电阻测试主要检测导线的电阻是否正常。
短路测试主要测试线束中各导线之间是否存在短路现象。
绝缘测试检测线束的绝缘材料是否合格。
耐压测试主要测试线束是否能够承受一定的电压。
6.包装:经过测试合格的线束需要进行包装,以保护其不受外界环境的干扰和损坏。
包装时需要使用恰当的包装材料,如泡沫箱、缠绕胶带等,以确保线束运输过程中的安全性。
以上就是线束制作的大致流程,从设计到包装的每一步都需要精细操作以确保线束质量的可靠性和稳定性。
只有在每个环节都进行严格的把控,线束才能满足使用者的需求,并具有良好的性能和可靠性。
线束生产工艺流程
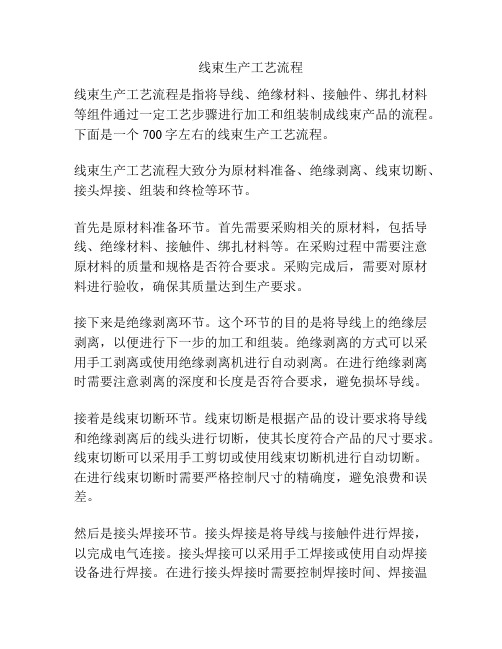
线束生产工艺流程线束生产工艺流程是指将导线、绝缘材料、接触件、绑扎材料等组件通过一定工艺步骤进行加工和组装制成线束产品的流程。
下面是一个700字左右的线束生产工艺流程。
线束生产工艺流程大致分为原材料准备、绝缘剥离、线束切断、接头焊接、组装和终检等环节。
首先是原材料准备环节。
首先需要采购相关的原材料,包括导线、绝缘材料、接触件、绑扎材料等。
在采购过程中需要注意原材料的质量和规格是否符合要求。
采购完成后,需要对原材料进行验收,确保其质量达到生产要求。
接下来是绝缘剥离环节。
这个环节的目的是将导线上的绝缘层剥离,以便进行下一步的加工和组装。
绝缘剥离的方式可以采用手工剥离或使用绝缘剥离机进行自动剥离。
在进行绝缘剥离时需要注意剥离的深度和长度是否符合要求,避免损坏导线。
接着是线束切断环节。
线束切断是根据产品的设计要求将导线和绝缘剥离后的线头进行切断,使其长度符合产品的尺寸要求。
线束切断可以采用手工剪切或使用线束切断机进行自动切断。
在进行线束切断时需要严格控制尺寸的精确度,避免浪费和误差。
然后是接头焊接环节。
接头焊接是将导线与接触件进行焊接,以完成电气连接。
接头焊接可以采用手工焊接或使用自动焊接设备进行焊接。
在进行接头焊接时需要控制焊接时间、焊接温度和焊接质量,确保焊接的牢固性和接触的可靠性。
接着是组装环节。
组装是将焊接好的导线和其他组件进行组合,形成成品线束。
在进行组装时需要根据产品的要求进行排列和布线,确保线束的结构紧凑和外观整洁。
在进行组装时还需要进行绑扎和定位,使线束的结构更加牢固和稳定。
最后是终检环节。
终检是对已组装好的线束产品进行检测和测试,以确保其质量达到要求。
终检的内容包括外观检查、电阻测量、绝缘性能测试等。
只有通过了终检的线束产品才能全部出厂。
以上就是线束生产工艺流程的简要介绍。
线束生产需要严格按照工艺流程进行操作,确保产品的质量和性能。
同时还需要不断改进工艺流程,提高生产效率和产品质量。
汽车线束工艺流程

汽车线束工艺流程汽车线束是连接汽车各个部件的重要组成部分,它承载着传输电力和信号的功能。
汽车线束工艺流程是指在汽车生产过程中,对汽车线束进行加工、组装和测试的一系列工艺流程。
下面将详细介绍汽车线束工艺流程的各个环节。
首先,汽车线束的制作需要根据汽车的具体设计图纸进行材料准备。
在这一阶段,工作人员需要根据设计要求选择合适的导线、绝缘套管、连接器等材料,并按照设计要求进行切割和加工,以备后续的组装工作。
接下来是线束的组装工艺。
在这一阶段,工作人员需要根据设计图纸,将准备好的导线、绝缘套管、连接器等材料进行组装。
这个过程需要非常精细的操作,确保每根导线都连接正确,每个连接器都牢固可靠,以保证线束在使用过程中不会出现故障。
然后是线束的绝缘处理。
在这一阶段,已经组装好的线束需要进行绝缘处理,以防止在汽车使用过程中受到外界环境的影响。
这个过程通常采用特殊的绝缘胶或绝缘套管来进行处理,确保线束在高温、潮湿等恶劣环境下仍能正常工作。
接着是线束的测试。
在这一阶段,已经绝缘处理好的线束需要进行电气测试和外观检查,以确保线束没有接线错误、短路等问题,并且外观符合汽车设计要求。
只有通过了严格的测试,线束才能被允许安装到汽车上去。
最后是线束的安装。
在这一阶段,经过严格测试的线束将被安装到汽车的各个部位,如发动机舱、车门、车厢等位置。
安装过程需要严格按照设计要求进行,确保线束不会被挤压、拉扯,以免影响线束的使用寿命和安全性能。
总的来说,汽车线束工艺流程是一个复杂而又精细的过程,需要严格按照设计要求进行操作,确保线束的质量和可靠性。
只有在每个环节都严格把关,才能生产出高质量的汽车线束,为汽车的安全性能和可靠性提供保障。
线束的工艺流程
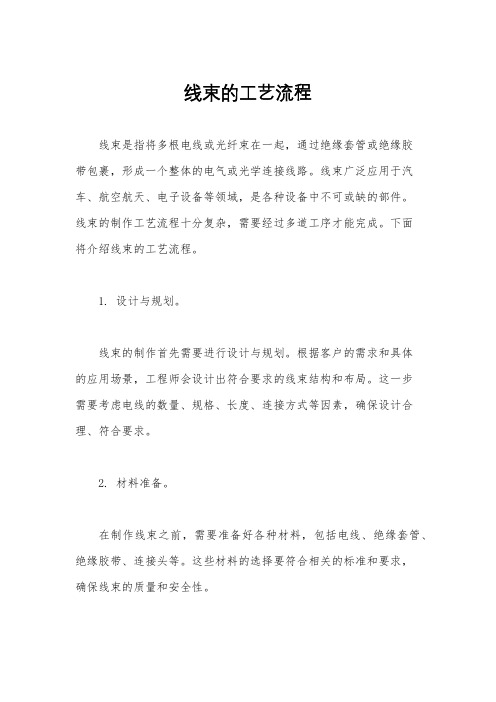
线束的工艺流程线束是指将多根电线或光纤束在一起,通过绝缘套管或绝缘胶带包裹,形成一个整体的电气或光学连接线路。
线束广泛应用于汽车、航空航天、电子设备等领域,是各种设备中不可或缺的部件。
线束的制作工艺流程十分复杂,需要经过多道工序才能完成。
下面将介绍线束的工艺流程。
1. 设计与规划。
线束的制作首先需要进行设计与规划。
根据客户的需求和具体的应用场景,工程师会设计出符合要求的线束结构和布局。
这一步需要考虑电线的数量、规格、长度、连接方式等因素,确保设计合理、符合要求。
2. 材料准备。
在制作线束之前,需要准备好各种材料,包括电线、绝缘套管、绝缘胶带、连接头等。
这些材料的选择要符合相关的标准和要求,确保线束的质量和安全性。
3. 剥线和组装。
接下来是剥线和组装的工序。
工人需要根据设计图纸和要求,将电线的外皮剥除,露出内部的金属导线。
然后根据设计要求,将各根电线按照一定的顺序和布局进行组装,通常会采用编织、捆扎或打包的方式进行组装。
4. 绝缘处理。
组装好的电线需要进行绝缘处理,以确保线束的安全性和耐用性。
这一步通常会采用绝缘套管或绝缘胶带进行包裹,同时需要进行压接或焊接等工艺处理,确保各根电线之间的连接牢固可靠。
5. 测试与检验。
制作完成的线束需要进行测试和检验,以确保质量合格。
通常会进行电气测试、耐压测试、绝缘测试等,确保线束符合相关的标准和要求。
6. 包装与出厂。
最后是线束的包装与出厂。
制作完成的线束会进行整理和包装,通常会采用盒装、托盘包装等方式进行包装,然后进行出厂检验,确保线束的质量符合要求后进行出厂。
通过以上工艺流程,线束的制作完成。
整个工艺流程需要严格按照标准和要求进行操作,确保线束的质量和安全性。
线束作为电气和光学连接的重要组成部分,在各种设备中发挥着重要的作用,其质量和稳定性直接关系到设备的性能和安全。
因此,制作线束的工艺流程非常重要,需要严格控制每一个环节,确保线束的质量和可靠性。
线束生产工艺流程
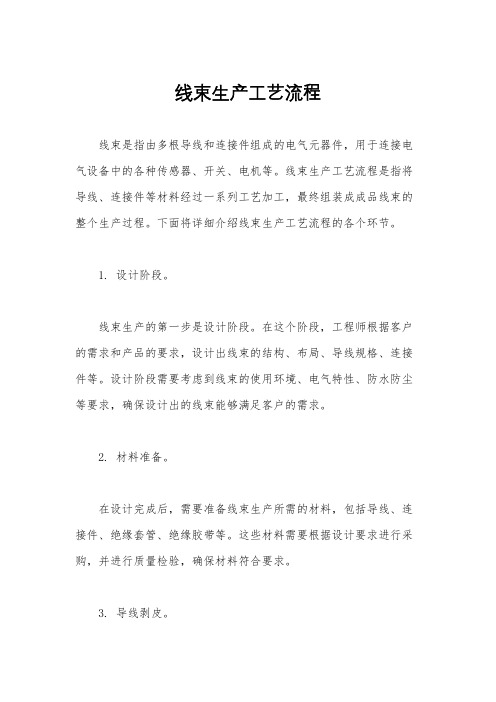
线束生产工艺流程线束是指由多根导线和连接件组成的电气元器件,用于连接电气设备中的各种传感器、开关、电机等。
线束生产工艺流程是指将导线、连接件等材料经过一系列工艺加工,最终组装成成品线束的整个生产过程。
下面将详细介绍线束生产工艺流程的各个环节。
1. 设计阶段。
线束生产的第一步是设计阶段。
在这个阶段,工程师根据客户的需求和产品的要求,设计出线束的结构、布局、导线规格、连接件等。
设计阶段需要考虑到线束的使用环境、电气特性、防水防尘等要求,确保设计出的线束能够满足客户的需求。
2. 材料准备。
在设计完成后,需要准备线束生产所需的材料,包括导线、连接件、绝缘套管、绝缘胶带等。
这些材料需要根据设计要求进行采购,并进行质量检验,确保材料符合要求。
3. 导线剥皮。
导线剥皮是线束生产的第一道工艺。
在这个环节,工人需要根据设计要求,将导线的外皮剥除,露出内部的金属导体。
导线剥皮需要使用专门的剥皮工具,确保剥皮的质量和速度。
4. 导线编织。
经过剥皮后的导线需要进行编织。
编织是指将多根导线按照设计要求进行组合和编织,形成线束的基本结构。
编织需要根据设计要求进行精确的排列和固定,确保线束的稳固性和电气性能。
5. 绝缘处理。
编织完成后的线束需要进行绝缘处理。
绝缘处理包括绝缘套管的安装、绝缘胶带的缠绕等工艺,确保线束在使用过程中能够有效地防水防尘,同时保护导线不受外部环境的影响。
6. 连接件安装。
线束中需要安装各种连接件,如插头、插座、端子等。
连接件安装需要根据设计要求进行精确的安装和固定,确保连接的可靠性和稳定性。
7. 终检。
线束生产的最后一道工艺是终检。
在终检环节,工人需要对线束进行外观检查、电气测试等,确保线束的质量和性能符合设计要求。
通过以上工艺流程,线束最终可以生产出符合客户要求的成品。
线束生产工艺流程需要严格按照设计要求和工艺标准进行操作,确保线束的质量和性能达到要求。
同时,线束生产工艺流程也需要不断改进和优化,以适应不同客户的需求和市场的变化。
线束加工工艺指导要求
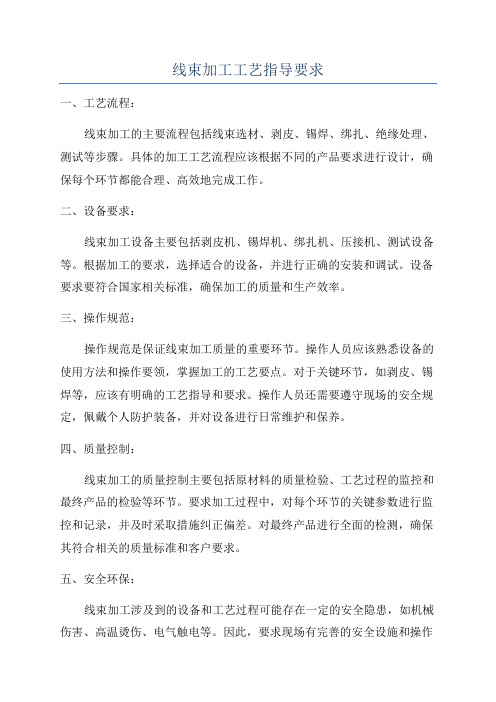
线束加工工艺指导要求
一、工艺流程:
线束加工的主要流程包括线束选材、剥皮、锡焊、绑扎、绝缘处理、测试等步骤。
具体的加工工艺流程应该根据不同的产品要求进行设计,确保每个环节都能合理、高效地完成工作。
二、设备要求:
线束加工设备主要包括剥皮机、锡焊机、绑扎机、压接机、测试设备等。
根据加工的要求,选择适合的设备,并进行正确的安装和调试。
设备要求要符合国家相关标准,确保加工的质量和生产效率。
三、操作规范:
操作规范是保证线束加工质量的重要环节。
操作人员应该熟悉设备的使用方法和操作要领,掌握加工的工艺要点。
对于关键环节,如剥皮、锡焊等,应该有明确的工艺指导和要求。
操作人员还需要遵守现场的安全规定,佩戴个人防护装备,并对设备进行日常维护和保养。
四、质量控制:
线束加工的质量控制主要包括原材料的质量检验、工艺过程的监控和最终产品的检验等环节。
要求加工过程中,对每个环节的关键参数进行监控和记录,并及时采取措施纠正偏差。
对最终产品进行全面的检测,确保其符合相关的质量标准和客户要求。
五、安全环保:
线束加工涉及到的设备和工艺过程可能存在一定的安全隐患,如机械伤害、高温烫伤、电气触电等。
因此,要求现场有完善的安全设施和操作
规范,并进行相关的培训和教育。
此外,还应该对废弃物的处理进行规范,遵守环保要求,减少对环境的污染。
六、持续改进:
在制定线束加工工艺指导要求时,需要结合具体的产品特点和生产环
境进行综合考虑。
同时,还要与相关部门和人员充分沟通和协调,确保指
导要求的有效实施。
线束加工的工艺流程
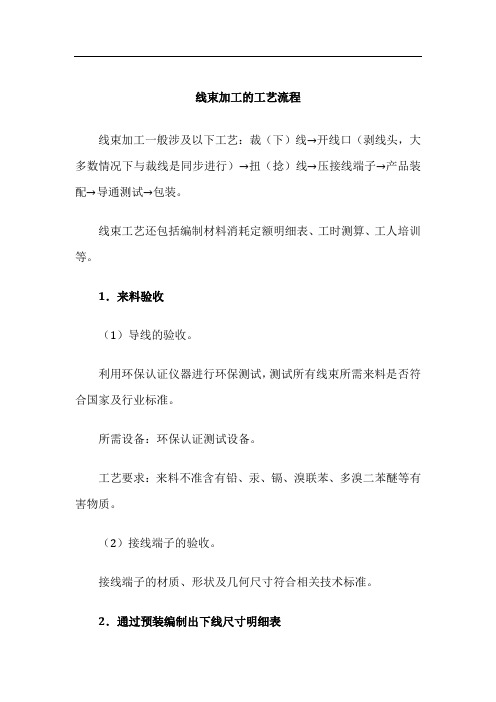
线束加工的工艺流程线束加工一般涉及以下工艺:裁(下)线→开线口(剥线头,大多数情况下与裁线是同步进行)→扭(捻)线→压接线端子→产品装配→导通测试→包装。
线束工艺还包括编制材料消耗定额明细表、工时测算、工人培训等。
1.来料验收(1)导线的验收。
利用环保认证仪器进行环保测试,测试所有线束所需来料是否符合国家及行业标准。
所需设备:环保认证测试设备。
工艺要求:来料不准含有铅、汞、镉、溴联苯、多溴二苯醚等有害物质。
(2)接线端子的验收。
接线端子的材质、形状及几何尺寸符合相关技术标准。
2.通过预装编制出下线尺寸明细表3.送线将线材放至送线器固定。
4.裁线(开线)将所需加工线材放到中转送线架上固定,利用裁线机将线材裁剪成要求长度。
在进行开线工艺之前,必须仔细研究线束图纸,根据图纸的要求,合理确定导线的开线尺寸、剥头尺寸,接着制作开线操作说明书,制作流程跟踪卡。
5.电线剥皮按标准要求剥除接头处电线对应长度的绝缘外皮。
6.扭线对接头处导体进行整理、扭线。
7.套线端标号管制作线端标号管,然后将标号管套入导线端头。
8.铆接端子铆接端子又称压接工艺或打端子。
根据图纸要求的端子类型确定压接参数,编写压接操作说明书,对于有特殊要求的需要在工艺文件上注明并培训操作工。
比如,有的导线需要先穿过护套后才可压接,它需要先预装导线然后从预装工位返回再压接;还有刺破式压接用到专用的压接工具,这种压接方式具有良好的电接触性能。
用端子压接机将接头处导体和插头端子进行铆接。
9.线束制作利用线卡子,根据《电气接线图》将相关联的导线制作成线束成品。
10.检验检验的目的是为了进行有效的质量控制,由工序检验和成品检验两个部分构成。
检验内容主要包括外观检查和利用导通测试仪进行线束的导通测试。
线束生产工艺详细流程
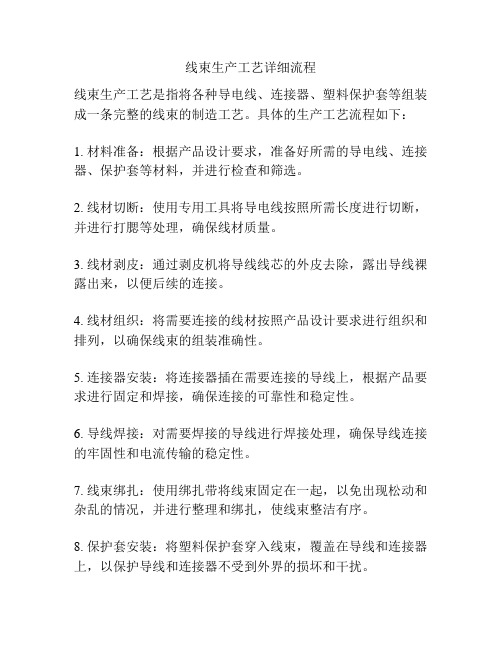
线束生产工艺详细流程
线束生产工艺是指将各种导电线、连接器、塑料保护套等组装成一条完整的线束的制造工艺。
具体的生产工艺流程如下:
1. 材料准备:根据产品设计要求,准备好所需的导电线、连接器、保护套等材料,并进行检查和筛选。
2. 线材切断:使用专用工具将导电线按照所需长度进行切断,并进行打腮等处理,确保线材质量。
3. 线材剥皮:通过剥皮机将导线线芯的外皮去除,露出导线裸露出来,以便后续的连接。
4. 线材组织:将需要连接的线材按照产品设计要求进行组织和排列,以确保线束的组装准确性。
5. 连接器安装:将连接器插在需要连接的导线上,根据产品要求进行固定和焊接,确保连接的可靠性和稳定性。
6. 导线焊接:对需要焊接的导线进行焊接处理,确保导线连接的牢固性和电流传输的稳定性。
7. 线束绑扎:使用绑扎带将线束固定在一起,以免出现松动和杂乱的情况,并进行整理和绑扎,使线束整洁有序。
8. 保护套安装:将塑料保护套穿入线束,覆盖在导线和连接器上,以保护导线和连接器不受到外界的损坏和干扰。
9. 绝缘处理:根据产品的要求,对整个线束进行绝缘处理,防止电线之间的短路和漏电,提高使用的安全性和可靠性。
10. 质量检验:对生产的线束进行质量检验,检查连接的牢固性、电阻和绝缘等指标是否合格。
11. 包装和出货:将合格的线束进行包装,并标明产品名称、规格、数量和生产日期等信息,然后装货出库。
通过以上的流程,可以保证线束的质量和可靠性,提高线束的生产效率和制造成本,并且可以适应不同的产品需求和生产要求。
同时,为了确保线束的有效运行和长期使用,还需要定期进行维护和保养,以延长线束的使用寿命。
线束生产流程

线束生产流程线束是一种由多根导线和连接器组成的电气元件,广泛应用于汽车、电子设备、家电等领域。
线束的生产流程对产品质量和生产效率有着重要影响。
下面将介绍线束生产的整个流程。
首先,线束生产的第一步是材料准备。
这包括各种规格的导线、绝缘套管、连接器、绝缘胶带等原材料的采购和储备。
在材料准备阶段,需要对原材料进行质量检验,确保符合生产要求。
接下来是导线的剥皮和组装。
在这一阶段,工人需要根据产品要求,使用自动剥线机或手动工具对导线进行剥皮,然后根据电路图纸和工艺要求,将导线按照一定的顺序组装成线束,并进行初步的电气测试。
然后是绝缘处理。
线束中的导线需要进行绝缘处理,以防止短路和漏电现象的发生。
通常采用绝缘套管、绝缘胶带等材料对导线进行包覆和绝缘处理,确保线束在使用过程中能够安全可靠地工作。
接着是连接器的安装。
线束中的连接器是用来连接不同部分的导线,因此连接器的安装非常重要。
在这一阶段,工人需要将连接器与导线进行连接,并进行必要的固定和封装,确保连接牢固可靠。
最后是整体包装和检验。
在线束生产的最后阶段,需要对整个线束进行包装和标识,以便于运输和使用。
同时,还需要进行全面的电气测试和外观检验,确保线束的质量符合产品标准和客户要求。
总的来说,线束生产流程包括材料准备、导线剥皮和组装、绝缘处理、连接器安装、整体包装和检验等多个环节。
每个环节都需要严格按照工艺要求和质量标准进行操作,以确保最终生产出的线束产品质量优良,性能稳定可靠。
只有严格执行生产流程,才能生产出符合要求的线束产品,满足客户的需求。
线束的工艺流程

线束的工艺流程线束工艺流程是指将电子设备中的各种电线、电缆、连接器等组合成一个完整的线束的过程。
线束的质量直接影响电子设备的性能和可靠性,因此线束工艺流程的规范和高效性非常重要。
下面将介绍线束的工艺流程。
第一步:设计和规划在开始线束的工艺流程之前,首先需要根据电子设备的规格和要求进行设计和规划。
设计人员需要确定线束的形状、尺寸、布线方式以及使用的电线、电缆的种类等。
设计完成后,可以进行下一步的操作。
第二步:裁剪和剥离根据设计图纸上的尺寸要求,将所需长度的电线、电缆切割成相应的长度。
然后通过剥离工具将电线、电缆的保护层剥离,露出内部的导线或导体。
第三步:组装和焊接在组装线束的过程中,需要根据设计要求将不同规格和颜色的电线、电缆进行组合。
然后使用焊接工具将各个电线焊接在连接器上,保证连接的牢固和可靠。
第四步:绝缘和包覆在连接好各个电线、电缆后,需要进行绝缘处理。
绝缘材料通常是用于包覆电线和电缆的外保护层,以防止电线短路或受到外界环境的影响。
常用的绝缘材料有PVC、PE、PET等。
第五步:标识和固定在线束的工艺流程中,需要使用标识工具将线束上的各个电线进行标记,以便于后续的维护和检修。
同时,还需要注意线束的固定,使用特定的夹具或胶粘剂等将线束固定在设备中的相应位置,以防止其在运输和使用过程中的松动和损坏。
第六步:测试和调试在线束完成后,还需要进行测试和调试,以确保线束的质量和性能符合规定标准。
常用的测试方法包括电容测试、电阻测试、绝缘测试等。
通过测试和调试可以及时发现线束中存在的问题,如短路、开路等,并进行修复或更换。
第七步:包装和出货线束完成所有的工艺流程后,需要进行包装和出货。
包装时要注意线束的保护,使用适当的包装材料进行包裹,以免在运输过程中被损坏。
然后按照客户的要求进行出货,确保线束按时送达客户手中。
总结线束的工艺流程是一个复杂而细致的过程,需要进行精心的规划和设计,严格的操作和质量控制。
只有在工艺流程的每一个环节都能够严格按照要求进行操作,才能制作出高质量、高可靠性的线束产品。
线束工艺流程
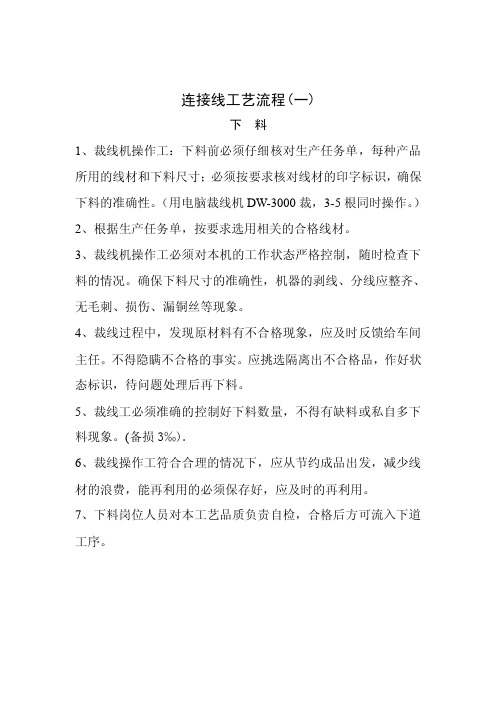
连接线工艺流程(一)下料1、裁线机操作工:下料前必须仔细核对生产任务单,每种产品所用的线材和下料尺寸;必须按要求核对线材的印字标识,确保下料的准确性。
(用电脑裁线机DW-3000裁,3-5根同时操作。
)2、根据生产任务单,按要求选用相关的合格线材。
3、裁线机操作工必须对本机的工作状态严格控制,随时检查下料的情况。
确保下料尺寸的准确性,机器的剥线、分线应整齐、无毛刺、损伤、漏铜丝等现象。
4、裁线过程中,发现原材料有不合格现象,应及时反馈给车间主任。
不得隐瞒不合格的事实。
应挑选隔离出不合格品,作好状态标识,待问题处理后再下料。
5、裁线工必须准确的控制好下料数量,不得有缺料或私自多下料现象。
(备损3‰).6、裁线操作工符合合理的情况下,应从节约成品出发,减少线材的浪费,能再利用的必须保存好,应及时的再利用。
7、下料岗位人员对本工艺品质负责自检,合格后方可流入下道工序。
捻线、沾锡1、捻线操作工必须需捻线、沾锡的产品要求掌握、明确。
2、选用适当的捻线头进行操作,铜丝经过捻线后应紧密均匀、直伸、无散碎铜丝和线头不紧呈散开状等现象。
3、捻线加工后的产品要小心放置好,保护好线头不被碰撞。
4、按照产品要求进行沾锡,控制沾锡部位尺寸的标准性,且沾锡表面应光亮、呈银白色、无余锡结集和漏沾锡现象的产品。
(线表皮无烧焦状态。
)5、沾锡操作工对自己的工艺质量负责、严格自选出漏沾锡,沾锡表面缺少和余锡结集不合格产品。
6、发现有导线表焊锡不良及其它质量问题要及时反馈给车间主任或主管部门,确保不良品的有效控制和及时的采取相应措施。
端子压接1、压接端操作者应先检查压接设备的通断运转是否完好,注意安全操作。
先给压接设备上油,以保证压接时正常生产。
2、操作者应按产品工艺标识卡上的要求领取相应的线材和端子进行压接,杜绝错压现象,要按照正确的压接方向和顺序。
3、随时检查端子的电镀质量,杜绝用氧化发黄、发黑和变形的不合格端子。
4、操作者应随时自检端子的压接抗拉力,是否达到标准要求。
线束制造工艺

检测工序:对线束进行电气性能 和外观质量的检测确保符合要求。
准备线束和连接器:选择合适的线束和连接器 确保线束的长度和连接器的型号符合要求。
剥线:根据需要使用剥线钳或剥线机将线束的外 皮剥离露出线芯。
压接:将剥好的线芯插入连接器中使用压接工具 将连接器的端子压接到线芯上。
检测:对压接好的线束进行电气性能和机械性能 检测确保符合要求。
添加 标题
注意事项:使用这些设备时需注意安全遵循操作规程避免发生意外事故。同时应定期维护和保养设备确 保其正常运转。
测量工具:用于测量线束的长度、直径、角度等尺寸保证线束的精度和质量。 检测工具:用于检测线束的导通性、绝缘性、耐压性等电气性能确保线束的质量和安全性。 检验夹具:用于检验线束的装配质量和外观保证线束的合格和美观。 测试设备:用于测试线束的整体性能和功能保证线束的性能和可靠性。
识别问题:对 生产过程中出 现的质量问题 进行准确判断
和记录
分析原因:对 每个问题进行 深入分析找出
根本原因
制定措施:根 据分析结果制 定有效的改进
措施
ห้องสมุดไป่ตู้
实施改进:确 保改进措施得 到有效执行并 进行持续监控
轻量化材料:如碳 纤维复合材料可提 高线束的强度和减 轻重量
高温材料:能够承 受更高的温度增强 线束的耐久性和安 全性
添加标题
智能化制造技术将逐步普及实现 生产过程的自动化和智能化。
定制化生产的需求将进一步增加 推动线束制造企业向个性化、柔 性化生产转型。
发展前景:随着汽车行业的不断 发展和智能化趋势线束制造行业 将迎来更多的发展机遇市场需求 将持续增长。
技术创新:为了应对挑战和抓住 机遇线束制造行业需要不断进行 技术创新和升级提高生产效率和 产品质量。
- 1、下载文档前请自行甄别文档内容的完整性,平台不提供额外的编辑、内容补充、找答案等附加服务。
- 2、"仅部分预览"的文档,不可在线预览部分如存在完整性等问题,可反馈申请退款(可完整预览的文档不适用该条件!)。
- 3、如文档侵犯您的权益,请联系客服反馈,我们会尽快为您处理(人工客服工作时间:9:00-18:30)。
線材生產線材生產工工艺流程流程培培训講師:陳代兵
2011年03月
歡迎大家參加培訓!
图一.電線生產
流程图
工艺流程
電線生產工
二.線材生產各段設備
三. 線材生產中品質管控點
一.電線生產電線生產工工艺流程流程图图銅線- 芯線- 對絞- 總絞- 外被
二. 線材生產各段設備(重點講芯線押出, 了解電線是怎麼生產的)芯線押出設備生產線:
1.放線裝置.
2.導體預熱器
3.擠出主機.
3.1料筒
3.2螺桿
3.3機頭
3.4模具
4.水槽.
5.印字設備
6.火花機.
7.OD測試儀.
8.牽引裝置
9.收線裝置
1.放線裝置作用:讓銅線均勻穩定的從軸子上放出.
2.預熱機
作用:使铜线等金属导体在线运动中连续加热,通過調節預熱可改變芯線附著力.
3. 押出機之料筒作用:用於儲存料及烘料
押出機之螺桿
作用:螺桿是擠塑機主機擠壓系統的關鍵部件之一, 它不僅起到輸送塑料的作用,同時對塑料的擠壓、塑化、成型的重要作用,所以合理選用螺桿結構和參數,是獲得理想的產品質量和產量的重要環節
押出機螺桿
料
筒
4. 水槽作用:冷卻電線
5. 印字設備: 在電線表面印字
6.火花機作用:檢測芯線絕緣性能
7. OD測試儀作用:在線測量電線外徑
9. 收線裝置作用: 使電線裝在軸子上
三. 線材生產中品質管控點
以及其它藍圖要求項目依據客戶或下工段生產要求
芯線包裝依據標準樣品
芯線顏色依據客戶或規范要求
火花測試依據客戶或規范要求
絕緣延伸抗張依據客戶或規范要求
銅導體電阻依據客戶或規范要求
絕緣皮厚依據客戶或規范要求
線材外徑光滑\平整
線材外觀芯線參考標准
品質主要控制項目生產工段。