零部件入库检验作业指导书
(完整版)检验作业指导书

检验作业指导书1.进料检验1.1 定义进料检验又称来料检验,是制止不良物料进入生产环节的首要控制点。
进料检验由IQC执行。
1.2 检测要项IQC在对来货检验前,首先应清楚该批货物的品质检测要项,不明之处要向本部门主管问询,直到清楚明了为止。
在必要时,IQC验货员可从来货中随机抽取两件来货样,交IQC主管签发来货检验临时样品,并附相应的品质检测说明,不得在不明来货检验与验证项目、方法和品质允收标准的情况下进行验收。
1.3 检验项目与方法1.3.1 外观检测一般用目视、手感、限度样品进行验证。
1.3.2 尺寸检测一般用卡尺、千分尺、塞规等量具验证。
1.3.3 结构检测一般用拉力器、扭力器、压力器验证。
1.3.4 特性检测如电气的、物理的、化学的、机械的特性一般采用检测仪器和特定方法来验证。
1.4 检验方式的选择1.4.1 全检方式适用于来货数量少、价值高、不允许有不合格品物料或公司指定进行全检的物料。
1.4.2 免检方式适用于低值、辅助性材料或经认定的免检厂来料以及生产急用而特批免检的,对于后者IQC应跟进生产时的品质状况。
1.4.3 抽样检验方式适用于平均数量较多、经常性使用的物料。
样本大小:批量的10%(不少于20件),允收数AC=0,拒收数RE=1。
1.5 检验结果的处理方式1.5.1 允收经IQC验证,不合格品数低于限定的不合格品个数时,则判为该批来货允收。
IQC应在验收单上签名,盖检验合格印章,通知货仓收货。
若不合格品数大于限定的不良品个数,则判定该送检批为拒收。
IQC应及时填制《IQC退货报告》,经相关部门会签后,交仓库、采购办理退货事宜。
同时在该送检批货品外箱标签上盖“退货”字样,并挂“退货”标牌。
1.5.3 特采特采,即进料经IQC检验,品质低于允许水准。
IQC虽提出“退货”的要求,但由于生产的原因,而做出的“特别采用”的要求。
若非迫不得已,公司应尽可能不启用“特采”。
“特采”必须由总经理批准,可行时还必须征得客户的书面许可。
检验作业指导书
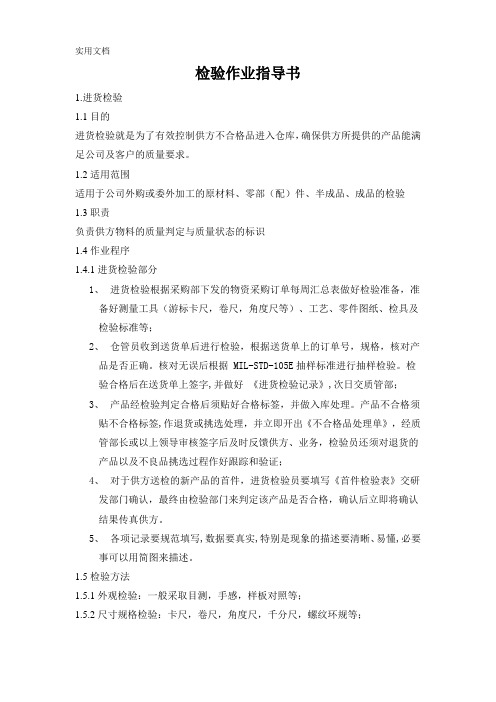
检验作业指导书1.进货检验1.1目的进货检验就是为了有效控制供方不合格品进入仓库,确保供方所提供的产品能满足公司及客户的质量要求。
1.2适用范围适用于公司外购或委外加工的原材料、零部(配)件、半成品、成品的检验1.3职责负责供方物料的质量判定与质量状态的标识1.4作业程序1.4.1进货检验部分1、进货检验根据采购部下发的物资采购订单每周汇总表做好检验准备,准备好测量工具(游标卡尺,卷尺,角度尺等)、工艺、零件图纸、检具及检验标准等;2、仓管员收到送货单后进行检验,根据送货单上的订单号,规格,核对产品是否正确。
核对无误后根据 MIL-STD-105E抽样标准进行抽样检验。
检验合格后在送货单上签字,并做好《进货检验记录》,次日交质管部;3、产品经检验判定合格后须贴好合格标签,并做入库处理。
产品不合格须贴不合格标签,作退货或挑选处理,并立即开出《不合格品处理单》,经质管部长或以上领导审核签字后及时反馈供方、业务,检验员还须对退货的产品以及不良品挑选过程作好跟踪和验证;4、对于供方送检的新产品的首件,进货检验员要填写《首件检验表》交研发部门确认,最终由检验部门来判定该产品是否合格,确认后立即将确认结果传真供方。
5、各项记录要规范填写,数据要真实,特别是现象的描述要清晰、易懂,必要事可以用简图来描述。
1.5检验方法1.5.1外观检验:一般采取目测,手感,样板对照等;1.5.2尺寸规格检验:卡尺,卷尺,角度尺,千分尺,螺纹环规等;1.5.3承重测试:按指导书要求加载相应的重物作禁止和滚动测试;1.5.4组装测试:与配套的产品进行组装。
1.6检验项目1.6.1管材类1、依采购订单型号,规格与送货单核对,有无质保书;2、管材表面擦拭干净,检查表面有无焊道开裂、模具压痕及材质麻点、凹坑等,方管四处R角是否一致;3、检查尺寸是否正确,方管及圆管壁厚公差±0.05;4、管材直线度、平面度、扭曲度能否满足加工要求,公差范围参照《管材的质量要求》;5、表面要求无严重的划伤,无明显的麻点凹坑,无锈斑等;6、一般管材接头管≤2%, 如有特殊要求则不可有接头管;7、特殊管材类检查捆包是否符合要求,有无因保护不当导致运输过程中造成的划伤。
(完整版)检验作业指导书

检验作业指导书1.进料检验1.1 定义进料检验又称来料检验,是制止不良物料进入生产环节的首要控制点。
进料检验由IQC执行。
1.2 检测要项IQC在对来货检验前,首先应清楚该批货物的品质检测要项,不明之处要向本部门主管问询,直到清楚明了为止。
在必要时,IQC验货员可从来货中随机抽取两件来货样,交IQC主管签发来货检验临时样品,并附相应的品质检测说明,不得在不明来货检验与验证项目、方法和品质允收标准的情况下进行验收。
1.3 检验项目与方法1.3.1 外观检测一般用目视、手感、限度样品进行验证。
1.3.2 尺寸检测一般用卡尺、千分尺、塞规等量具验证。
1.3.3 结构检测一般用拉力器、扭力器、压力器验证。
1.3.4 特性检测如电气的、物理的、化学的、机械的特性一般采用检测仪器和特定方法来验证。
1.4 检验方式的选择1.4.1 全检方式适用于来货数量少、价值高、不允许有不合格品物料或公司指定进行全检的物料。
1.4.2 免检方式适用于低值、辅助性材料或经认定的免检厂来料以及生产急用而特批免检的,对于后者IQC应跟进生产时的品质状况。
1.4.3 抽样检验方式适用于平均数量较多、经常性使用的物料。
样本大小:批量的10%(不少于20件),允收数AC=0,拒收数RE=1。
1.5 检验结果的处理方式1.5.1 允收经IQC验证,不合格品数低于限定的不合格品个数时,则判为该批来货允收。
IQC应在验收单上签名,盖检验合格印章,通知货仓收货。
若不合格品数大于限定的不良品个数,则判定该送检批为拒收。
IQC应及时填制《IQC退货报告》,经相关部门会签后,交仓库、采购办理退货事宜。
同时在该送检批货品外箱标签上盖“退货”字样,并挂“退货”标牌。
1.5.3 特采特采,即进料经IQC检验,品质低于允许水准。
IQC虽提出“退货”的要求,但由于生产的原因,而做出的“特别采用”的要求。
若非迫不得已,公司应尽可能不启用“特采”。
“特采”必须由总经理批准,可行时还必须征得客户的书面许可。
入厂检验作业指导书

入厂检验作业指导书一、目的入厂检验是确保原材料、零部件及外协加工件等符合企业质量要求的重要环节。
本作业指导书旨在规范入厂检验的流程和方法,保证检验结果的准确性和可靠性,防止不合格品流入生产环节,从而提高产品质量,降低生产成本。
二、适用范围本作业指导书适用于所有进入本企业的原材料、零部件、外协加工件以及包装材料等的入厂检验。
三、职责分工1、质量检验部门负责制定入厂检验标准和检验计划,并组织实施入厂检验工作。
2、采购部门负责及时通知质量检验部门进行入厂检验,并提供相关的采购合同、技术协议等文件。
3、仓库部门负责对入厂物资进行初步验收和保管,配合质量检验部门进行检验工作。
四、检验准备1、质量检验部门应收集并熟悉相关的产品标准、技术规范、采购合同及技术协议等文件,明确检验要求和验收标准。
2、准备好检验所需的量具、仪器设备,并确保其处于良好的工作状态,且在检定或校准有效期内。
3、设计并填写好检验记录表格,确保检验数据的准确记录和可追溯性。
五、检验流程1、报检采购部门在物资到货后,应及时填写《入厂检验通知单》,通知质量检验部门进行检验。
2、抽样检验人员应根据相关标准和规范,确定抽样方案和抽样数量。
抽样应具有代表性,避免抽样偏差。
3、检验项目及方法(1)外观检验检查物资的外观是否完好,有无变形、划伤、锈蚀、裂纹等缺陷。
(2)尺寸检验使用相应的量具测量物资的关键尺寸,如长度、宽度、厚度、直径等,判断其是否符合要求。
(3)性能检验对于有性能要求的物资,如原材料的化学成分、机械性能,零部件的功能、可靠性等,应按照相关标准进行测试和检验。
(4)标识和包装检验检查物资的标识是否清晰、准确,包装是否完好,防护措施是否得当。
4、判定检验人员根据检验结果,对照验收标准,对物资进行判定。
判定结果分为合格、不合格和待定三种。
(1)合格:物资各项检验指标均符合要求,判定为合格,准予入库。
(2)不合格:物资存在一项或多项检验指标不符合要求,判定为不合格。
进货检验作业指导书
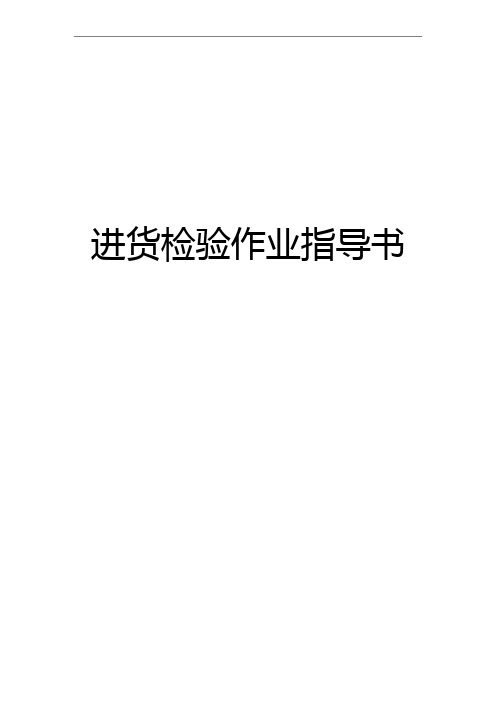
进货检验作业指导书目录一、进货检验作业指导书 (1)1、目的 (3)2、合用范围 (3)3、引用文件 (3)4、定义 (3)4.1重缺陷 (3)4.2轻缺陷 (3)5、工作程序及要求 (3)5.1抽样标准 (3)5.2目检要求 (3)5.3检验设备/工具 (3)5.4检验环境要求 (3)5.5FSD 防护要求 (3)5.6来料待检区 (3)5.7来料检验要求 (3)5.8涉及测试电路 (3)5.9关于垫片的检验 (3)6、检验内容及判定标准 (4)6.3二极管 (4)6.4发光二极管 (5)6.5三极管 (5)6.9PCB 板 (6)6.10端子 (7)6.11自恢复保险丝 (7)6.12电阻 (7)6.13电容 (8)6.14DIP 开关 (8)6.15电源模块 (8)6.16接插件 (9)6.17集成芯片 (9)6.18磁珠 (9)6.19晶振 (10)保证公司所购元器件的质量符合要求,为了指导来料检验和来料质量控制而特殊指定此作业指导书。
本作业指导书合用于公司的来料检验3.1 GB2828-2003 《计数抽样检验程序》标准;4.1 重缺陷:指损坏、功能不良等影响将来产品的实质功能失去或者造成可靠度降低的缺陷,包括产品的缺陷对未来产品的实质功能可能影响较大但又无法预料的缺陷,以及明显影响产品质量之缺陷,以 MA 表示之;4.2 轻缺陷:系指来料的缺陷并不会明显影响未来产品的外观、组装、功能,以MI 表示之。
5.1 来料按照 GB2828-2003 《计数抽样检验程序》标准抽检,抽样等级:正常抽样(II) ,重缺陷 AQL=0.65,轻缺陷 AQL=2.5:来料数量较多时,如有些盘装料体积小,数量多,由来料检验员按照“特殊 S-2 水平,AQL=1.0”执行抽样检验;5.2 目检:肉眼直接看不清晰的,可采用放大镜或者显微镜检查;5.3 检验设备/工具: XJ4810 半导体管特性图示仪、检验图纸、万用表、数显卡尺、防静电手环、手套、放大镜(5 倍)5.4 检验环境照明:照度不低于 300LUX (普通距 60W 台灯 60cm 桌面为 300LUX);5.5 ESD 防护:凡接触电子元器件体必需佩带良好静电防护措施, IO 卡件铝型材、卡件面板、外壳、侧封板等结构件不用做 ESD 防护;5.6 来料首先存放在来料待检验区,来料检验合格后方能入库,研发使用物料也暂存在来料待检验区,由研发确认使用。
进货检验作业指导书

进货检验作业指导书一、背景介绍进货检验是指在企业采购原材料、零部件或成品时,对所采购物品进行检验和验证,确保所购物品的质量符合企业的要求和标准。
进货检验是企业质量管理体系中重要的一环,对于保证产品质量、减少不合格品流入生产环节具有重要意义。
本文档旨在为企业制定进货检验作业指导书提供详细的指导和要求。
二、进货检验的目的1. 确保所进货物品的质量符合企业的要求和标准。
2. 防止不合格品流入生产环节,影响产品质量和生产效率。
3. 保护企业的利益,减少质量问题带来的经济损失和声誉影响。
4. 优化供应链管理,提高供应商的质量水平和服务水平。
三、进货检验的流程1. 采购准备阶段:a. 制定进货检验计划,明确检验的范围、标准和要求。
b. 确定供应商的选择标准,建立供应商评估体系。
c. 与供应商沟通,明确物品的技术要求和交货期限。
d. 确定进货检验的检验方法和检验设备。
2. 进货检验操作:a. 检验员根据进货检验计划,到达供应商处进行检验。
b. 检验员对所进货物品进行外观检查、尺寸测量、功能测试等。
c. 检验员根据检验结果,判断物品是否合格,记录检验数据。
d. 如发现不合格品,及时通知供应商,要求其采取纠正措施。
e. 如发现重大不合格品或频繁不合格品,可以暂停供应商的供货。
3. 检验结果处理:a. 合格品:将合格品移交给仓库,进行入库操作。
b. 不合格品:按照不合格品处理程序进行处理,如退货、返修等。
c. 不确定品:如遇到无法确定是否合格的物品,应进行进一步的测试或鉴定。
4. 数据分析和改进:a. 对进货检验的数据进行统计和分析,发现问题并制定改进措施。
b. 定期评估供应商的质量水平,对不合格率较高的供应商采取相应的措施。
c. 不断优化进货检验的流程和方法,提高检验效率和准确性。
四、进货检验的注意事项1. 检验员应具备专业的技术知识和丰富的实践经验。
2. 检验员应遵循检验标准和操作规程,确保检验结果的准确性和可靠性。
检验作业指导书【范本模板】
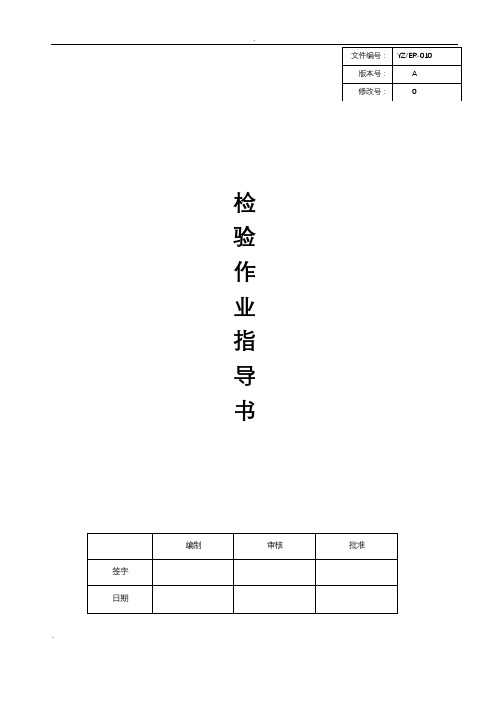
检验作业指导书1.目的:对进厂的原材料及过程、产品等进行规定的检验和试验,确保产品符合规定的要求。
2.范围:适用于直接用在本厂产品上的原材料、及产品、半成品进行检验。
3.。
职责:质量部负责对原材料及产品的验证及检验。
4.程序:4.1原材料的检验4.1.1.原材料采购进厂后,采购员按定货合同及相关采购文件,对实物规格、型号、等级、数量、重量等验证无误后,通知质检员进行检验。
4.1.2.质检员核实交检内容和质量证件齐全后方可进行检验。
4.1.3.检验和验证a)对客户有特殊要求的,按要求进行检验。
b)按国家标准进行抽样检验,具体见《原材料检验卡》。
c)质检员按照工艺文件进行检验,填写相关检验记录。
4.2.不合格品处置4.2.1.经检验和试验确定为不合格品的原辅料,按《不合格品控制程序》规定执行.4.3.过程产品检验4.3.1.操作工必须在自检合格的基础上,质检员及时进行首件检验;并将检验结果向操作者交待清楚。
4.3.2.首检合格,质检员通知操作工继续生产。
4.3.3.在首检合格的基础上,质检员和班组长人员应做好中间抽检,发现问题,采取措施及时处理,把发现的质量问题向工人交待清楚.质检员及时填写相关检验记录《不合格生产整改通知单》.4.3.4.经质检员检验出的不合格品应填写《不合格品评审单》,经主管人员签字后方可回用。
4.3.5.质检员按照产品加工工艺进行检验,填写相关检验记录。
4.4.最终产品出厂检验4.4.1.全性能检测委托检验;4.4.2.本公司能进行检验的项目及时检测,结果填写在检验报告单上。
5.相关文件5.1.《不合格品控制程序》6.记录。
(完整版)检验作业指导书

1.5.3.3重工
送检批几乎全部不合格,但经过加工处理后,货品即可接受。在此情况下,由公司抽调人力进行来货再处理。IQC对加工后的货品进行重检,对合格品接受,对不合格品开出《IQC退货报告》交相关部门办理退货。此类货品由IQC统计加工工时,对供应商做扣款处理。
2.1.3通过过程检验,防止不合格品流入下一道工序,甚至可能装在最终的产品上,以致造成不合格品出厂。
2.2首件检验
2.2.1定义及目的
首件检验是在生产开始时(上班或换班)或工序因素调整后(换人、换料、换活、换工装、调整设备等)对制造的第1件(大件产品)或前3件(非大件)产品进行的检验。目的是为了尽早发现过程中影响产品质量的系统因素,防止产品成批报废。
适用于来货数量少、价值高、不允许有不合格品物料或公司指定进行全检的物料。
1.4.2免检方式
适用于低值、辅助性材料或经认定的免检厂来料以及生产急用而特批免检的,对于后者IQC应跟进生产时的品质状况。
1.4.3抽样检验方式
适用于平均数量较多、经常性使用的物料。
样本大小:批量的10%(不少于20件),允收数AC=0,拒收数RE=1。
检验作业指导书
1.进料检验
1.1定义
进料检验又称来料检验,是制止不良物料进入生产环节的首要控制点。进料检验由IQC执行。
1.2检测要项
IQC在对来货检验前,首先应清楚该批货物的品质检测要项,不明之处要向本部门主管问询,直到清楚明了为止。在必要时,IQC验货员可从来货中随机抽取两件来货样,交IQC主管签发来货检验临时样品,并附相应的品质检测说明,不得在不明来货检验与验证项目、方法和品质允收标准的情况下进行验收。
进料检验作业指导书

1.0目的:为检验员提供检验规则和检验方法,指导其正确检验从而稳定产品质量,保证产品满足符合性要求及生产计划用料及时入库。
2.0 范围:所有非本公司生产加工的外协、外购件,经过加工或不经过加工而直接用于本公司产品上的零部件的检验。
3.0 检验工具:卡尺(300㎜/150㎜)/卷尺(300㎜)/千分尺(0-25㎜)扭力批/样板/自制检具、推力计、色差仪、百个格刀、盐雾实验箱、ROHS测试仪等4.0 引用标准:国家标准/客户标准/公司检验标准/作业指导书等5.0 术语和定义:5.1拉丝:是一种砂带磨削加工,通过砂带对金属表面进行磨削加工,去除金属表面缺陷,并形成具有一定粗糙度、纹路均匀的装饰表面。
5.2镀前划痕:指电镀或氧化之前因操作不当、或对明显缺陷进行粗打磨等人为造成的基体材料上的一般呈细线型划伤或局部磨擦的痕迹。
5.3浅划痕:膜层表面划伤,但未伤至底层(即底层未暴露);对其它无膜层表面则为:目测不明显、手指甲触摸无凹凸感、未伤及材料本体伤痕。
5.4深划痕:表面膜层划伤且已伤至底层(即底层已暴露出来);对无膜层表面则为:目测明显手指甲触摸有凹凸感、伤及材料本体的伤痕。
5.5基材花斑:电镀或氧化前因基体材料腐蚀、或者材料中的杂质、或者材料微孔等原因所造成的、与周围材质表面不同光泽或粗糙度的斑块状花纹外观。
5.6凹坑:由于基体材料缺陷、或在加工过程中操作不当等原因而在材料表面留下的小坑状痕迹。
5.7水印:电镀或氧化后因清洗水未及时干燥或干燥不彻底所形成的斑纹、印迹。
5.8水纹:塑胶或压铸件成形时,熔体流动产生的可见条纹。
5.9缩水:因材料、工艺等原因使塑胶或压铸件表面出现凹陷的收缩现象。
抄送:□总经理□市场部□工艺技术部□计划部□采购部□生产部□品质部□人力资源部□财务部□文控中心5.10气泡:批塑胶件因工艺原因内部出现的可见空气泡。
5.11砂眼:塑胶或压铸件表面的疏松针孔。
5.12披锋:压铸件或塑胶件的分模面上出现或残留的毛刺。
进货检验作业指导书
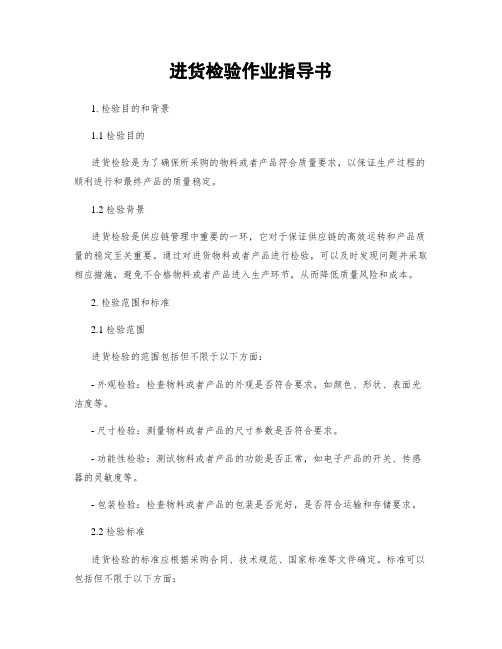
进货检验作业指导书1. 检验目的和背景1.1 检验目的进货检验是为了确保所采购的物料或者产品符合质量要求,以保证生产过程的顺利进行和最终产品的质量稳定。
1.2 检验背景进货检验是供应链管理中重要的一环,它对于保证供应链的高效运转和产品质量的稳定至关重要。
通过对进货物料或者产品进行检验,可以及时发现问题并采取相应措施,避免不合格物料或者产品进入生产环节,从而降低质量风险和成本。
2. 检验范围和标准2.1 检验范围进货检验的范围包括但不限于以下方面:- 外观检验:检查物料或者产品的外观是否符合要求,如颜色、形状、表面光洁度等。
- 尺寸检验:测量物料或者产品的尺寸参数是否符合要求。
- 功能性检验:测试物料或者产品的功能是否正常,如电子产品的开关、传感器的灵敏度等。
- 包装检验:检查物料或者产品的包装是否完好,是否符合运输和存储要求。
2.2 检验标准进货检验的标准应根据采购合同、技术规范、国家标准等文件确定。
标准可以包括但不限于以下方面:- 外观标准:规定物料或者产品的颜色、形状、表面光洁度等外观要求。
- 尺寸标准:规定物料或者产品的尺寸参数的上下限或者允许偏差范围。
- 功能性标准:规定物料或者产品的功能性能要求,如电子产品的工作电压范围、传感器的灵敏度等。
- 包装标准:规定物料或者产品的包装方式、包装材料、运输标志等要求。
3. 检验流程和方法3.1 检验流程进货检验的普通流程包括以下步骤:- 接收物料或者产品:接收到供应商交付的物料或者产品,并记录相关信息,如交货单号、供应商信息等。
- 外观检验:对物料或者产品的外观进行检查,记录外观缺陷情况。
- 尺寸检验:使用相应的测量工具对物料或者产品的尺寸进行测量,并与标准进行比对。
- 功能性检验:根据标准要求,对物料或者产品的功能进行测试,记录测试结果。
- 包装检验:检查物料或者产品的包装是否完好,并记录包装情况。
- 判定结果:根据检验结果,判断物料或者产品是否合格,如果有不合格项,需要采取相应措施。
检验作业指导书

件 名序 号件 号机 种1首件
2次/4h
1末件
外观表面无拉伤无裂纹目测100%全检
确认1首件
★2次/4h
1末件
1首件
2次/4h
1末件
1首件
2次/4h 1末件入
尺寸170.5±0.2库
2144.5±0.5或
325±0.3出
435.6±0.3厂焊接渗透不小于板厚的20%
频率全检检 验 指 导 书
工序
过程名称检验项目技术要求特性等级测量方式检测数量过程检验记录毛刺≤0.1mm 记录与注意事项各序实物图片、简图或可视化辅助1序落片外观成型形状见图一无毛边,无缺
料,无锈蚀目测100%
成型尺寸成型形状见图三过程检验记录3序冲长圆孔尺寸成型形状见图二游标卡尺游标卡尺过程检验记录成型尺寸与样件一致4序冲圆孔尺寸成型形状见图四游标卡尺过程检验记录毛刺≤0.1mm 3序确认5序焊接成品检验外观
表面防锈漆涂布、焊点牢固无积瘤、无锈蚀、无拉伤 无裂纹目测外观成型形状见图五;
焊接牢固无虚焊,无夹渣气孔成品检验记录游标卡尺目测5批图五
R5.2+0.21591φ6.1+0.2。
入厂检验作业指导书

入厂检验作业指导书1. 引言入厂检验是指在原材料、零部件等进入生产车间之前,对其进行质量检验的工作。
它是质量控制体系中至关重要的一环,能够有效地提高产品质量,并确保生产过程的顺利进行。
本文档旨在为入厂检验作业提供详细的指导,确保操作的准确性和一致性。
2. 应用范围本作业指导书适用于所有需要进行入厂检验的企业和组织。
3. 作业流程3.1 材料接收3.1.1 检查送检单在接收材料时,首先要查看送检单,确认送检材料的数量、规格和其他相关信息是否与送检单一致。
如发现不符,应立即通知供应商或相关人员进行处理。
3.1.2 检查外包装接下来要检查送检材料的外包装是否完好无损,有无湿漏、破损等情况。
若有异常情况,应及时记录并通知相关人员处理。
3.1.3 材料标识对已检验合格的材料,应在外包装上标注检验日期、检验结果和检验员姓名等信息,以便跟踪和追溯。
3.2 检验工艺3.2.1 样品准备根据检验要求,取出样品,并按照要求进行处理和加工。
如需特殊处理,如切割、破碎等,应遵守安全操作规程,确保操作人员的人身安全。
3.2.2 检验方法根据不同的材料和性质,选择相应的检验方法进行检验。
对于常见的方法,如外观检查、尺寸测量、验光仪测试等,要求检验员熟悉操作流程和仪器的使用方法,并确保准确性和可靠性。
3.2.3 检验记录在检验过程中,要及时记录检验结果、检验员姓名、检验日期等信息,并签名确认。
记录应准确、清晰,便于查阅和追溯。
3.3 检验结果判定将检验结果与标准进行对比,判断样品是否合格。
判定依据应明确,并经过相关人员的共识。
如有争议,应将样品留样,并及时与供应商联系进行沟通和协商,避免不必要的纠纷与损失。
3.4 合格材料处理对于检验合格的材料,应及时进行入库处理,并在相应资料中进行记录,如供应商信息、采购信息、入库日期等。
同时,应确保材料的存放环境和条件符合要求,避免损坏和质量问题。
3.5 不合格材料处理对于检验不合格的材料,应按照质量控制程序进行处理。
(实践手册)检查汽车零部件的进货验收制度
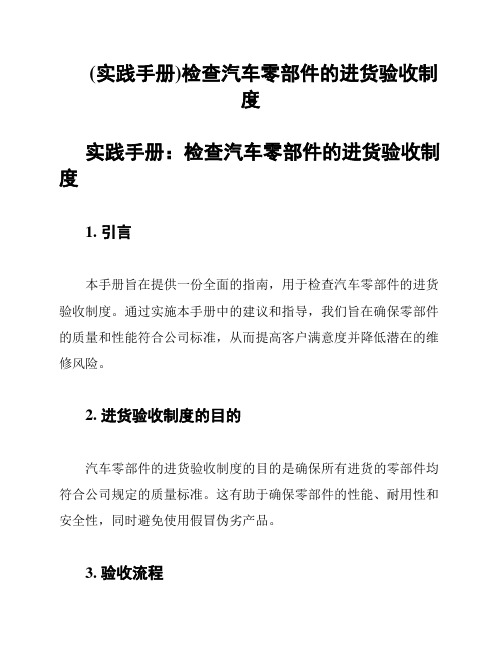
(实践手册)检查汽车零部件的进货验收制度实践手册:检查汽车零部件的进货验收制度1. 引言本手册旨在提供一份全面的指南,用于检查汽车零部件的进货验收制度。
通过实施本手册中的建议和指导,我们旨在确保零部件的质量和性能符合公司标准,从而提高客户满意度并降低潜在的维修风险。
2. 进货验收制度的目的汽车零部件的进货验收制度的目的是确保所有进货的零部件均符合公司规定的质量标准。
这有助于确保零部件的性能、耐用性和安全性,同时避免使用假冒伪劣产品。
3. 验收流程3.1 收货确认在收到零部件时,验收人员应首先进行外观检查。
应检查包装是否完好无损,确保零部件没有明显的损坏或缺陷。
3.2 型号和规格检查验收人员应核对收到的零部件的型号和规格是否与采购订单和制造商提供的技术文件相符。
任何不符的情况都应立即通知采购部门和供应商。
3.3 质量控制检查验收人员应根据制造商提供的质量控制文件进行零部件的性能测试。
这些测试可能包括但不限于负载测试、耐久性测试和功能测试。
3.4 证书和合规性文件检查验收人员应检查零部件的证书和合规性文件,以确保零部件符合相关的行业标准和法规要求。
这些文件可能包括CE认证、RoHS 合规性证书等。
3.5 记录和反馈验收人员应详细记录验收过程中的所有发现,并将验收报告反馈给采购部门和供应商。
任何不符合要求的零部件都应标记并进行适当的处理。
4. 培训和要求4.1 验收人员的培训所有验收人员都应接受有关零部件验收流程的培训。
培训内容应包括零部件的检查方法、测试设备和工具的使用,以及记录和反馈的技巧。
4.2 技能和要求验收人员应具备一定的机械和电子知识,能够理解和执行验收流程。
此外,验收人员应具备良好的观察力和判断力,能够准确识别不合格的零部件。
5. 持续改进汽车零部件的进货验收制度应不断进行改进,以适应不断变化的行业要求和客户需求。
公司应定期审查验收流程,并根据反馈和市场变化进行必要的调整。
6. 总结通过实施本手册中推荐的进货验收制度,公司可以确保汽车零部件的质量和性能符合标准,从而提高客户满意度和公司的声誉。
进货检验作业指导书

进货检验作业指导书一、背景介绍进货检验是指在采购过程中对供应商提供的货物进行检查和验证,以确保货物的质量和规格符合采购方的要求。
本作业指导书旨在提供一套标准的操作流程,以帮助员工正确进行进货检验工作,确保采购的货物符合质量标准。
二、作业目的进货检验作业的目的是确保采购的货物符合质量要求,减少不合格货物的入库,保证供应链的稳定和产品质量的可控性。
通过严格的进货检验,可以降低不合格品的风险,提高产品质量和客户满意度。
三、作业流程1. 接收货物- 在货物到达时,及时通知相关人员进行接收。
- 检查货物的数量和外包装完好性,如有异常及时记录并与供应商联系。
2. 质量检查- 根据采购合同和规格要求,对货物进行质量检查。
- 使用适当的检测设备和工具,如计量仪器、试验设备等,对货物进行检测。
- 检查货物的外观、尺寸、重量、颜色、材料等方面是否符合要求。
- 进行必要的功能性测试,如电器设备的开关、机械设备的运转等。
- 如发现不合格品,及时记录并与供应商协商解决方案。
3. 抽样检验- 对大批量货物进行抽样检验,以减少检验成本和时间。
- 根据国家标准或行业标准,制定合理的抽样方案。
- 选择合适的样品数量和抽样方法,确保样品的代表性和可靠性。
4. 检验记录- 对每一批次的货物进行详细的检验记录,包括检验日期、批次号、供应商信息等。
- 记录检验结果,包括合格品数量、不合格品数量和不合格品的具体问题。
- 如有需要,拍摄照片或制作样品展示,以便后续分析和处理。
5. 处理不合格品- 对于不合格品,根据公司的处理流程进行处理。
- 如可以修复,安排相关人员进行修复工作。
- 如不可修复,与供应商协商退换货或索赔事宜。
6. 检验报告- 撰写进货检验报告,包括检验结果、不合格品情况、处理措施等。
- 将报告及时提交给相关部门,如采购部、质量管理部等。
四、作业注意事项1. 严格按照作业流程进行操作,确保每一步都得到正确执行。
2. 使用适当的检测设备和工具,保证检验结果的准确性和可靠性。
仓库作业指导书

仓库作业指导书1.目的为规范原材料入库过程,确保合格原材料流转入生产环节,制定本作业指导书。
2.范围本作业指导书适用于原材料入库全过程。
3.职责3.1 采购部:负责收料通知单的下推和告知;3.2 仓储物流部:负责来料的核对、入库;3.3 品质管理部:负责来料的检验和判定。
4.收货就位货物清点、分包取单作业流程5.作业流程内容描述5.1 收货5.1.1 供应商送货:供应商通知采购人员到货信息,由采购通知检验验收,确认合格后交由入库办事员签收。
5.1.2 物流送货:由入库办事员负责签收。
签收前需确认产品外包装有无损坏;货运单号、件数是否一致;必要时需核对数量,正常方可签收。
如有疑问的部分需立即与采购部门沟通确认、及时处理。
5.2 就位5.2.1 物料签收后及时将原材料放置待检区。
5.2.2 大件物料可放于相应库区并挂上待检牌。
5.3 货物清点、分包5.3.1 打开物料外包装箱,取出送货单。
(送货单需供应商提供一式两份,一份采购留底,一份入库办事员清点用。
)5.3.2 依据送货单,核对物料名称、型号、数量,并在送货单上做好相应的记录。
需要分包的配件,在清点过程中应按照我们的需求做好分包工作。
如有差异应及时将信息反馈给采购处理。
5.3.3 货物进出应做到帐物同步。
随货必须有供应商提供的送货单才能办理入库。
如无送货单的部分应及时告知采购通知供应商办理。
5.4 取单5.4.1 物料清点确认无误后,依据送货单上提供的采购订单号及物料名称、型号、单位、数量(实收)等信息,同时结合系统中相应的收料通知单,下推生成外购入库单并保存,同时完成一级审核工作。
5.5 送检5.5.1 取单完毕后,进入外购入库序时薄界面,选中需要送检的物料记录。
每条记录应包含日期、供应商、物料长代码、物料名称、规格型号、长描述、单位、实收数量、备注、一级审核人等信息。
5.5.2 预览、打印一式两份。
一份送检、一份入库办事员留档。
检验员在接到外购入库单时需在该单据上签收接收时间及姓名。
入库检验作业指导书
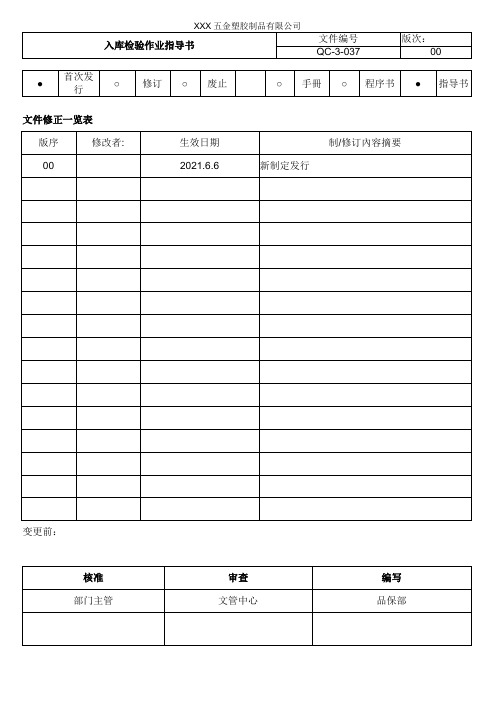
文件修正一览表变更前:1. 目的规范FQC入库检验作业行为。
2. 范围适用我司所有的入库检验作业。
3. 参考记录3.1 《生产派工单》3.2 《产品标签制作作业指导书》3.3 《品质异常反馈单》3.4 《留样标识卡》3.5 《组装PQC入库检验记录表》4.维护单位品保部5. 权责生产部:负责入库检验需求的提出品保部:负责待入库产品的检验及结果反馈6. 作业程序与说明6.1 检验时机:生产部将已生产完成的产品包装好后置于待检区,通知FQC进行入库前最终检验。
6.2 入库检验项目:6.3.1 依《生产派工单》核对实物与标签是否相符。
6.3.2 对重点尺寸进行5PCS检查,.此重点尺寸定义为1.带针脚类产品为外露脚长加总长,2.无针脚类产品为总长加总P距。
3.记录其中一个最大值,一个最小值。
6.3.3 依包装规范检验产线包装方式是否正确。
6.3.4 依包装明细检验包装数量是否正确。
6.3.5 依《产品标签制作作业指导书》检验内/外盒及尾数盒标签是否正确。
6.3.6 依AQL抽样计划对每批成品进行外观抽检。
6.3.7 每批产品的FQC至少检验尾数盒加一个整数盒的包装方式、包装数量和标签。
6.4 检验标识:如全部检验合格,FQC需在所有内盒标签上加盖PASS章。
并通知生产单位可以进行入库作业。
6.5 检验异常处理:6.5.2 FQC检验时如发现不良,整批产品全数退产线重工处理。
并开立《品质异常反馈单》,要求产线改善。
6.6 留样:6.5.1 成型FQC需要求成型技术员在生产完成后停机前将最后一模送FQC进行末件确认,如末件检验无误,成型FQC将整模穴样品作为末件留样,并填写完整《留样标识卡》留样保存。
6.5.2 组装FQC在对产品抽检无误后,需留取1PCS作为末件留样,并填写完整《留样标识卡》留样保存。
6.7 FQC将以上检验结果记录在《组装PQC入库检验记录表》上,并归档留存。
元器件入库检验作业指导书
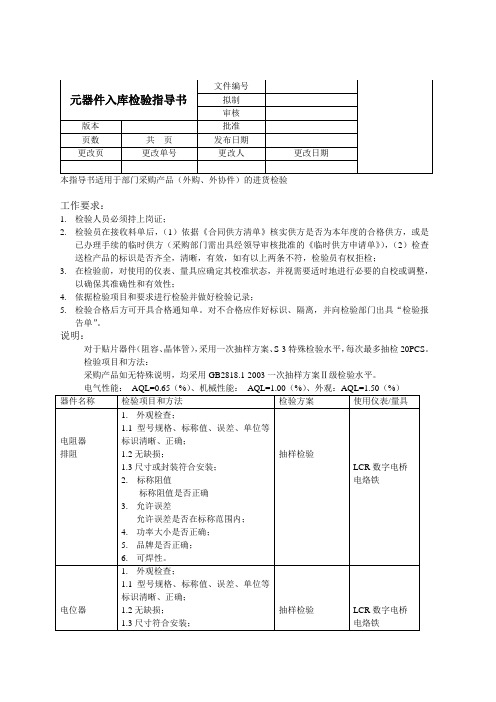
工作要求:
1.检验人员必须持上岗证;
2.检验员在接收料单后,(1)依据《合同供方清单》核实供方是否为本年度的合格供方,或是
已办理手续的临时供方(采购部门需出具经领导审核批准的《临时供方申请单》),(2)检查送检产品的标识是否齐全,清晰,有效,如有以上两条不符,检验员有权拒检;
3.在检验前,对使用的仪表、量具应确定其校准状态,并视需要适时地进行必要的自校或调整,
以确保其准确性和有效性;
4.依据检验项目和要求进行检验并做好检验记录;
5.检验合格后方可开具合格通知单。
对不合格应作好标识、隔离,并向检验部门出具“检验报
告单”。
说明:
对于贴片器件(阻容、晶体管),采用一次抽样方案、S-3特殊检验水平,每次最多抽检20PCS。
检验项目和方法:
采购产品如无特殊说明,均采用GB2818.1-2003一次抽样方案Ⅱ级检验水平。
检验作业指导书

检验作业指导书1.目的规范检验工作,提高产品质量,确保产品满足组织的品质要求。
2.范围适用于我司自制或委外协作加工的所有加工件。
3.职责品质部是本公司的质量管理部门,负责产品检验工作并记录验收结果。
4.内容检验流程-检验方法-判定标准-检验报告-不良品处理-纠正预防措施4.1检验流程供应商按照采购订单送货到公司将送货单给仓库,仓库按照采购订单及收货单上的名称、编号、数量对来料进行验收;如发现有缺件、编号与名称不符等情况验可退货给供应商,验收合格后,仓库开立《来料检验通知单》交品质部检验,品质部按照图纸、技术规范、及抽样水准对来料进行抽样检验。
接到仓库开立的来料检验通知单后,检验员需在半小时内进行检验工作,整理好该批次的相关图纸及检验工具,到现场进行验收工作,检验合格的部件粘贴“绿色”合格标签;检验不合格粘贴“红色”不良标签,并填写《品质异常处理单》召集相关部门进行原因分析和改善;将检验结果记录每日检验日报表中;并跟进不合格品的处理及改善效果,将检验合格的产品交由仓库入库。
相关表单文件及抽样水准《进料品质控制流程》《来料检验通知单》《机架过程品质控制流程》《品质异常处理单》《来料检验日报表》《问题点记录表》4.2 检验方法原材料核对:核对产品的名称、材质、型号规格、图号、材质证明、厂家的出厂检验记录。
成品外观检验:表面不允许有砂孔、毛刺、裂纹、塑性变形,不允许有明显的划痕、凹凸、折痕、污渍、色差等,必须符合工艺或技术文件标准,零部件的编号规则及位置与相关技术文件或图纸规定要一致。
尺寸、角度、形位误差的检验:根据标准要求选择合适的检验器具或配合其他辅助检测工具进行检验,并详细真实的记录检验结果。
按照图纸标注的长宽、孔径、距离、角度、槽、标注公差、螺纹长宽及纹牙、表面处理,逐一进行检验,重要部件做好检验数据记录,必要时可进行简单的装配查看配合是否异常,必须符合图纸技术要求。
机架件注意其图纸要求的材质及表面处理要求,严格按照图纸尺寸公差验收,加工成型后不得有沟痕、碰伤等损坏表面,降低强度及寿命的缺陷,去边角及毛刺。
零部件检测作业指导书
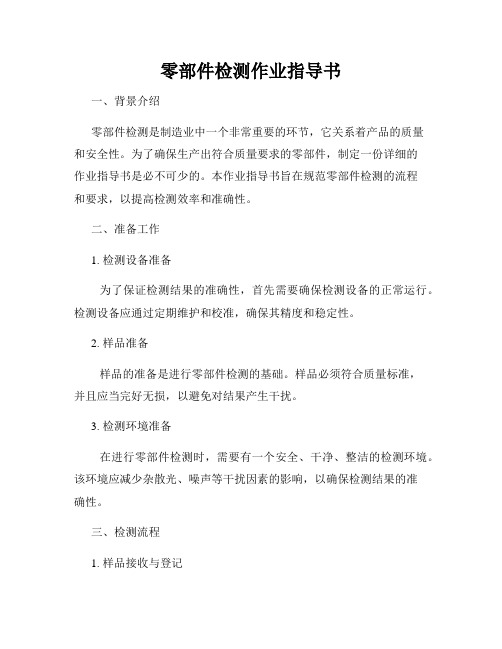
零部件检测作业指导书一、背景介绍零部件检测是制造业中一个非常重要的环节,它关系着产品的质量和安全性。
为了确保生产出符合质量要求的零部件,制定一份详细的作业指导书是必不可少的。
本作业指导书旨在规范零部件检测的流程和要求,以提高检测效率和准确性。
二、准备工作1. 检测设备准备为了保证检测结果的准确性,首先需要确保检测设备的正常运行。
检测设备应通过定期维护和校准,确保其精度和稳定性。
2. 样品准备样品的准备是进行零部件检测的基础。
样品必须符合质量标准,并且应当完好无损,以避免对结果产生干扰。
3. 检测环境准备在进行零部件检测时,需要有一个安全、干净、整洁的检测环境。
该环境应减少杂散光、噪声等干扰因素的影响,以确保检测结果的准确性。
三、检测流程1. 样品接收与登记在接收到样品后,务必进行登记和标识,以避免样品混淆或丢失。
登记信息应包括样品名称、数量、接收时间等。
2. 样品检查对接收到的样品进行外观检查,确保样品完好无损,没有明显缺陷或污损。
3. 选择检测方法根据零部件的特点和检测要求,选择合适的检测方法,如尺寸测量、材质分析、表面缺陷检测等。
4. 检测操作按照选定的检测方法,进行具体的操作步骤。
操作人员应严格按照操作规程进行操作,并记录每一步的操作细节。
5. 结果分析与判定在获得检测数据后,根据标准和规范对结果进行分析和判定。
分析应当综合考虑各项指标,并将结果以合理的方式进行记录和展示。
6. 偏差处理如果检测结果与标准要求存在偏差,应及时采取措施进行处理。
偏差处理的具体方式应根据不同的情况而定。
四、检测要求1. 准确性和可靠性零部件检测的结果应具有准确性和可靠性,即在相同的条件下,能够得到相同的结果。
为了提高检测的准确性和可靠性,应使用合适的检测设备和方法,并控制和记录所有可能影响结果的因素。
2. 及时性零部件检测应及时完成,以满足生产的需要。
检测结果应及时向相关人员反馈,以便于后续的生产安排和处理。
3. 文件记录所有的检测操作和结果应当详细记录在相关文件中,包括样品登记表、检测记录表、检测结果报告等。
- 1、下载文档前请自行甄别文档内容的完整性,平台不提供额外的编辑、内容补充、找答案等附加服务。
- 2、"仅部分预览"的文档,不可在线预览部分如存在完整性等问题,可反馈申请退款(可完整预览的文档不适用该条件!)。
- 3、如文档侵犯您的权益,请联系客服反馈,我们会尽快为您处理(人工客服工作时间:9:00-18:30)。
4、外观检验:
4.1 CCC标示完整、牢固。
4.2弧度尺寸与样板不吻合度≤3mm。
目测
卷尺
样板
1次/批
A
前、后风窗玻璃
(关键件)
1、生产厂家确认:上海福耀玻璃有限公司/常州工业技术有限公司。
2、每批零件应有供应商提供的有效的检测报告。
3、外观检验:
3.1玻璃表面洁净,无划痕、损伤;CCC标识以及各类标示清晰、完整。
3.2外观饱满、流畅,周边圆润、无跳砂等缺陷;
2、规格、型号:幅宽2000mm,厚度2.2mm灰色、小方格。
3、每批零件应有供应商提供的有效的检测报告。
4、外观质量:表面洁净,图案清晰,无划痕、损伤、折痕等缺陷。
5、尺寸检验:幅宽2000±3mm;厚度2.2-0.1mm。
目测
卷尺
游标卡尺
1次/批
A
后视镜
(关键件)
1、生产厂家确认:丹阳东港灯具有限公司。
共8页
文件编号
311002
共8页
第1页
工序名称
检 验 标 准
检查工具及方法
专检频次
重要程度
备注
侧窗总成
(关键件)
1、生产厂家确认。
1.1推拉侧窗总成:泰州市第一铝材厂有限公司/成都华西汽车附件有限公司。
推拉窗玻璃:泰州市阳光玻璃有限公司/福耀玻璃工业集团股份有限公司/常州工业
技术玻璃有限公司
1.2封闭侧窗的粘接玻璃:福耀玻璃工业集团股份有限公司/常州工业技术玻璃有限
5、功能检验
5.1驾驶员安全带在缓慢拉动时流畅,回缩自如;快速拉动下,安全带卡止可靠。
5.2安全带与安全带底座接插轻松,卡止可靠,解除接插轻松。
目测
牙规
1次/件
A
座椅
(关键件)
1、生产厂家确认:江苏友邦精工实业有限公司。
2、规格、型号:驾驶员座椅YB-JS-05其他乘员座椅YB-KP-05C、YB-KH-066。
3.3前风窗玻璃为夹胶玻璃3+0.76+3,无气泡现象;
3.4后风窗玻璃为5mm钢化玻璃;
4、尺寸检验:
4.1轮廓尺寸与检具A-2mm。
4.2弧度尺寸与检具不吻合度≤2mm。
目测
卷尺
检具
1次/批
A
更改
标记
处数
更改文件号
签名
日期
标记
处数
更改文件号
签名
日期
编制
审批
日期
零部件入库检验作业指导书
产品型号
产品名称
公司。
2、每批零件应有供应商提供的有效的检测报告。
3、推拉窗外观检验:
3.1玻璃表面洁净,无划痕、损伤;CCC标识以及各类标示清晰、完整。
3.2窗框为黑色喷塑处理或氧化黑色处理,色泽均匀、一致。窗框表面洁净,表面颗粒
直径≤Φ0.2,颗粒数1米内≤3颗。窗框规整、饱满,无翘边或变形现象;窗框型
材接缝处接缝密实、牢固可靠;接缝处型材同面,错位误差≤0.5mm。
零部件入库检验作业指导书
产品型号
产品名称
文件编号
312001
共1页
第1页
零部件名称
检 验 标 准
检查工具及方法
专检频次
重要程度
备注
顶棚内饰及驾驶门护板
(关键件)
1、生产厂家确认:湖南亚太实业有限公司或江苏洪昌科技股份有限公司。
2、每批零件应有供应商提供的有效的检测报告。
3、外观检验:
3.1内饰面料表面洁净,无划痕、损伤;
5、功能检验:琐舌伸、缩可靠,锁体运动件、琐止件运动正常,琐止可靠。
目测
启子
1次/批
A
更改
标记
处数
更改文件号
签字
日期
标记
处数
更改文件号
签字
日期
编制
审批
日期
零部件入库检验作业指导书
产品型号
产品名称
共8页
文件编号
311002
共8页
第3页
工序名称
检 验 标 准
检查工具及方法
专检频次
重要程度
备注
安全带
(关键件)
5.3外表面弧度尺寸与检验样板不贴合间隙≤1mm。
目测
卷尺
样板
直靠板
1次/批
A
更改
标记
处数
更改文件号
签字
日期
标记
处数
更改文件号
签字
日期
编制
审批
日期
零部件入库检验作业指导书
产品型号
产品名称
共8页
文件编号
311002
共8页
第2页
工序名称
检 验 标 准
检查工具及方法
专检频次
重要程度
备注
地板革
(关键件)
1、生产厂家确认:无锡八一塑料有限公司/无锡市新区八一塑料厂。
4、封闭侧窗玻璃外观检验:
4.1玻璃洁净,饱满,圆润,无划痕,周边无损伤。
4.2CCC标识以及各类标示清晰、完整。
4.3黑边完整、无透光现象;网点规范、整齐。
5、尺寸检验:
5.1窗框轮廓尺寸A-1mm;对角线误差≤2mm;周边直线度误差≤1mm。
5.2玻璃轮廓尺寸A-1mm;对角线误差≤2mm;周边直线度误差≤1mm。
1、生产厂家确认:浙江赛凯车业有限公司。
2、规格、型号:驾驶员安全带(三点式)LSQA-1其他乘员安全带(两点式)LSQD。
3、每批安全带入库应有供应商提供的有效的检测报告。
4、外观检验:
4.1 CCC标示完整、牢固。
4.2安全带颜色为黑色或灰色。
4.3安全带壳体完好,圆润、饱满,色泽均匀。
4.4连接支架镀锌规范;连接螺栓M12×1.5及琐止垫片齐全。
3.3锁扣与玻璃连接牢固,规整,锁扣琐止运动轻松;锁扣与挂钩配合良好,琐止状态
时,玻璃与窗框絨槽胶条贴合良好。侧窗琐止、开启可靠、轻松。
3.4玻璃在窗框内滑动自如,无晃动现象。
3.5絨槽胶条规范、舒展,接缝处密实,与型材内表面粘接牢固,有效。
3.6条形排水孔开孔6×30规范;排水孔无遮盖现象。
3.7底边3块5mm厚的橡胶垫块分布规范,与型材底板粘接牢固。
5、功能检验:
5.1镜杆角度调节自如,琐止可靠。
5.2镜片角度调节自如,琐止可靠。
目测
卷尺
1次/批
A
门锁
(关键件)
1、生产厂家确认:浙江中特力制锁有限公司。
2、规格、型号:107C、121-1C、157E、161、163。
3、每批零件应有供应商提供的有效的检测报告。
4、外观检验:表面镀铬完整、均匀,表面光亮无瑕疵。
3.2内饰板直边整齐,面料包边规整,包边密实、牢固;开孔处开孔规范,
开孔处面料包边密实、牢固;
3.3前后顶成型规范,周边切边顺畅,无分层现象;
3.4风道直、挺,槽口规范,周边切边平直,无分层现象;隔热层粘贴严密、
可靠。
3.5出风口风球转动灵活;表面色泽均匀,无瑕疵、型号:DG2001。
3、每批后视镜入库应有供应商提供的有效的检测报告。
4、外观检验:
4.1 CCC标识完整、清晰。
4.2表面洁净、弧面饱满、圆润、规范。
4.3镜片大小:长×高=253±2×160±2。
4.4镜面塑料底座黑色匀称,镜面与镜座连接可靠。
4.5镜杆黑色喷塑,色泽一致,无划伤。
4.6连接底座与橡胶垫配合良好。