1450mm冷轧机液压压下(或压上)简介
1450五机架UCMW冷连轧轧机简介解析
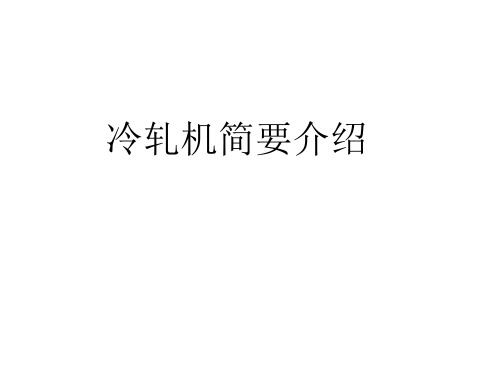
名称
型号
数量 供货 重量 备注
对中行程:
+/- 100 mm
精确度: 纠偏辊 压辊
+/- 1mm以内
Φ1200mm(包括15mm的聚氨酯外 壳)×1700mm
2
Φ280mm×1700mm
1
带钢对中液压缸:
Ф180/100 mm X 280 mm
1
压辊气缸:
Ф250/63 mm X 100 mm
2
3.04 轧机入口液压剪
名称
型号/参数
数量
供货 重量
备注
开口度
720-1740mm
液压马达
13.7 Mpa×Approx.67 r/min 1套
宽度调整速度 10mm/s(单侧)
垂直辊子
Φ100mm×300mm
每侧2个
3.06.2 Three Roll Bridle
类型:中间下压型 位置:1号轧机入口末端,装在轧机牌坊立柱间。 功能:通过液压压下中间辊,防止带钢在轧机入口跑偏。 中间辊的提升和降落是靠齿条齿轮同步机构实现同步。
辊颈轴承: 型号: φ245 mm/φ345 mm × 310 mm ,四列圆锥滚子 轴承; 厂家: KOYO, NSK, NTN 或同类轴承 单个轴承座重量:1003 kg/pc. 轧辊和轴承座装配后的总重: 5070 kg
3.07.3.2 中间辊轴承座
辊颈轴承: 型号: φ279.4 mm/φ393.7 mm × 320 mm ,四列圆锥滚子 轴承; 厂家: KOYO, NSK, NTN 或同类轴承 单个轴承座重量:1120 kg/pc. 轧辊和轴承座装配后的总重:6356 kg
压力测量: No.1 mill, Load cells No.2 --- No.5 mills, Pressure cells
1450mm铝带冷轧机使用维护规程
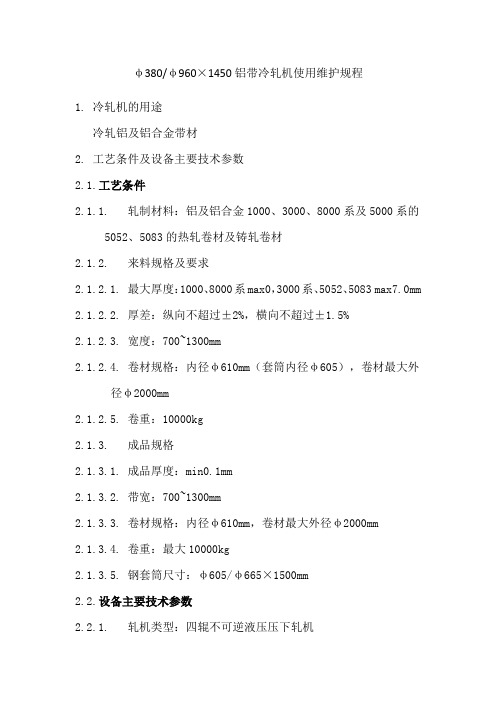
φ380/φ960×1450铝带冷轧机使用维护规程1.冷轧机的用途冷轧铝及铝合金带材2.工艺条件及设备主要技术参数2.1.工艺条件2.1.1.轧制材料:铝及铝合金1000、3000、8000系及5000系的5052、5083的热轧卷材及铸轧卷材2.1.2.来料规格及要求2.1.2.1.最大厚度:1000、8000系max0,3000系、5052、5083 max7.0mm 2.1.2.2.厚差:纵向不超过±2%,横向不超过±1.5%2.1.2.3.宽度:700~1300mm2.1.2.4.卷材规格:内径φ610mm(套筒内径φ605),卷材最大外径φ2000mm2.1.2.5.卷重:10000kg2.1.3.成品规格2.1.3.1.成品厚度:min0.1mm2.1.3.2.带宽:700~1300mm2.1.3.3.卷材规格:内径φ610mm,卷材最大外径φ2000mm2.1.3.4.卷重:最大10000kg2.1.3.5.钢套筒尺寸:φ605/φ665×1500mm2.2.设备主要技术参数2.2.1.轧机类型:四辊不可逆液压压下轧机2.2.2.轧机规格:φ380/φ960×1450mm2.2.3.道次压下率:20~60%2.2.4.轧制速度:max900m/min2.2.5.穿带速度:12~18 m/min2.2.6.最大轧制力:10000kN2.2.7.额定输出力矩:150kN.m2.2.8.开卷张力:3.5~150kN2.2.9.卷取张力:2.2~150kN2.2.10.轧制方向:左侧上卷,右侧卸卷(站在轧机操作侧面向轧机)2.2.11.轧制线标高:待定2.2.12.工艺润滑:介质为煤油基润滑介质,供油量4500l/min(暂定)3.将冷轧带坯用车间吊车吊放在储运装置上,储运辊道启动,将带有料卷的托盘运送至开卷机上卷位置,此时上卷车已停在辊道下面,上卷车托座升起,将带有料卷的托盘托起,上卷车沿轨道运行至开卷准备位置停止,高度自动对中装置摆臂摆下,使卷材中心高度与开卷卷轴高度一致,此时带宽测量装置亦投入工作,高度对中装置摆架摆上恢复原位,带卷托盘被上卷车继续运送至开卷机卷轴处,此时开卷机侧支撑已退回至非工作位置,开卷机卷轴已缩径,压辊摆起,带卷被套在开卷机卷轴上,开卷机涨径,侧支撑进入工作位置,开卷机压辊摆下压住带卷,上卷车托座下降,上卷车向辊道方向运行至辊道前托座升起,上卷车将空托盘送回至储运辊道,储运辊道运行,将空托盘运至卷取侧准备卸卷,此时上卷车托座下降准备上第二个带卷,完成上卷工作,以上操作均为PLC控制。
1450mm冷轧机液压压下(或压上)简介
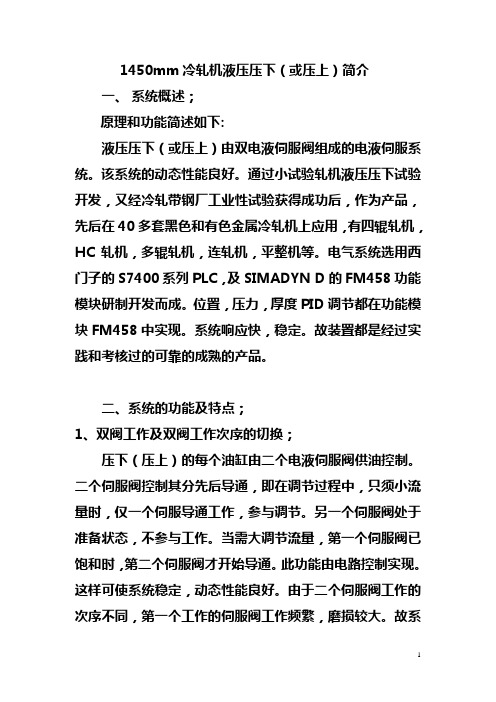
1450mm冷轧机液压压下(或压上)简介一、系统概述;原理和功能简述如下:液压压下(或压上)由双电液伺服阀组成的电液伺服系统。
该系统的动态性能良好。
通过小试验轧机液压压下试验开发,又经冷轧带钢厂工业性试验获得成功后,作为产品,先后在40多套黑色和有色金属冷轧机上应用,有四辊轧机,HC轧机,多辊轧机,连轧机,平整机等。
电气系统选用西门子的S7400系列PLC,及SIMADYN D的FM458功能模块研制开发而成。
位置,压力,厚度PID调节都在功能模块FM458中实现。
系统响应快,稳定。
故装置都是经过实践和考核过的可靠的成熟的产品。
二、系统的功能及特点;1、双阀工作及双阀工作次序的切换;压下(压上)的每个油缸由二个电液伺服阀供油控制。
二个伺服阀控制其分先后导通,即在调节过程中,只须小流量时,仅一个伺服导通工作,参与调节。
另一个伺服阀处于准备状态,不参与工作。
当需大调节流量,第一个伺服阀已饱和时,第二个伺服阀才开始导通。
此功能由电路控制实现。
这样可使系统稳定,动态性能良好。
由于二个伺服阀工作的次序不同,第一个工作的伺服阀工作频繁,磨损较大。
故系统设有工作次序选择切换开关,控制二个阀的磨损程度均衡,提高伺服阀的使用寿命。
如由于伺服阀故障需检修时,系统可选择切换为一个阀工作。
液压压下能继续正常工作。
从而减少停机率。
但必须注意操作侧、传动侧二侧同时选择单阀工作。
此时压下速度减小一半。
2、压下系统的二种闭环调节功能;分别介绍如下:(1)、A.P.C.系统;A.P.C. 系统,由进口的微脉冲位置传感器作为油缸位移的位置实际值,组成位置闭环系统。
系统稳定性好,分辨率高。
可确保分辨0.001mm。
系统设有零辊缝压靠,位置快、慢二挡压下速度给定及快速抬辊。
辊缝倾斜给定、及操作侧、传动侧二侧油缸同步控制环节。
系统能确保压下过程中,轧辊平行移动。
(2)、A.F.C.;(轧制力闭环)A.F.C.由负载腔油压压力传感器作为反馈元件,并经计算机数据处理后作为负载力显示。
1450mm冷连轧机双活套及轧机入口张力控制系统

t e po iins a e dif r nt So t tt h nge ft nso c n lc ih t ile r e son s a lt . Do l h sto r fe e . ha he c a so e in o fitw t hem l nt y t n i t biiy ub e
r tt a etm e,t e rt n i ontoli e uie o e ur he r ltv t biiy oft t i e i n a he un a hes m i h i e son c r sr q r d t ns et ea i e sa lt hes rp t nso nd t
LI AN G u- a, Xi xi ZH A N G in n Pe- a
轧机的液压压下装置
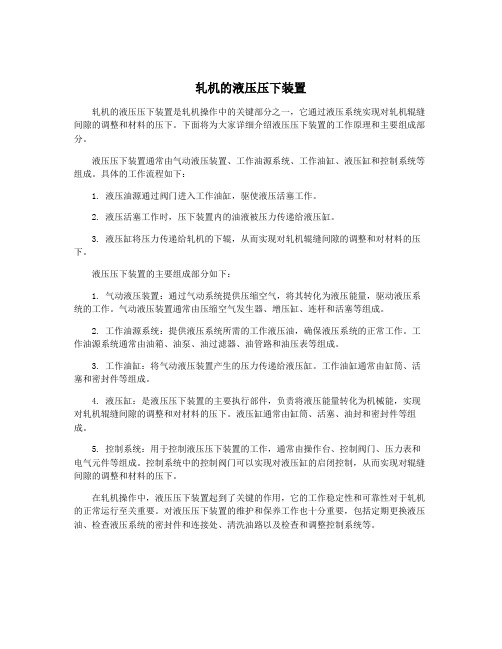
轧机的液压压下装置轧机的液压压下装置是轧机操作中的关键部分之一,它通过液压系统实现对轧机辊缝间隙的调整和材料的压下。
下面将为大家详细介绍液压压下装置的工作原理和主要组成部分。
液压压下装置通常由气动液压装置、工作油源系统、工作油缸、液压缸和控制系统等组成。
具体的工作流程如下:1. 液压油源通过阀门进入工作油缸,驱使液压活塞工作。
2. 液压活塞工作时,压下装置内的油液被压力传递给液压缸。
3. 液压缸将压力传递给轧机的下辊,从而实现对轧机辊缝间隙的调整和对材料的压下。
液压压下装置的主要组成部分如下:1. 气动液压装置:通过气动系统提供压缩空气,将其转化为液压能量,驱动液压系统的工作。
气动液压装置通常由压缩空气发生器、增压缸、连杆和活塞等组成。
2. 工作油源系统:提供液压系统所需的工作液压油,确保液压系统的正常工作。
工作油源系统通常由油箱、油泵、油过滤器、油管路和油压表等组成。
3. 工作油缸:将气动液压装置产生的压力传递给液压缸。
工作油缸通常由缸筒、活塞和密封件等组成。
4. 液压缸:是液压压下装置的主要执行部件,负责将液压能量转化为机械能,实现对轧机辊缝间隙的调整和对材料的压下。
液压缸通常由缸筒、活塞、油封和密封件等组成。
5. 控制系统:用于控制液压压下装置的工作,通常由操作台、控制阀门、压力表和电气元件等组成。
控制系统中的控制阀门可以实现对液压缸的启闭控制,从而实现对辊缝间隙的调整和材料的压下。
在轧机操作中,液压压下装置起到了关键的作用,它的工作稳定性和可靠性对于轧机的正常运行至关重要。
对液压压下装置的维护和保养工作也十分重要,包括定期更换液压油、检查液压系统的密封件和连接处、清洗油路以及检查和调整控制系统等。
热轧1450精轧机设备组成及原理简介

精轧机压下装置 • 3、上阶梯垫装置:
• 位于AGC液压缸与上支承辊之间,通过螺栓把合在AGC液 压缸上。每架轧机有1套上阶梯垫装置,阶梯垫窜动液压缸 安装在传动侧(行程600,一级行程150),2块阶梯垫中间 通过连杆铰接。4级高差,F1-F6高差80(F5-F6最后一级高 度(最厚一级)不采用,故而实际使用高差60)。
AdwF5-F6= h+(D F5-F6/2+ dF5-F6)-625
• 例 如: F1-F4 下工作辊 直径 720mm , 下支承辊 直径 1351mm 时,(d+D)/2=1395.5mm,按上表用第9阶梯垫, h=170mm。 • 下工作辊上辊面标高 : • AdwF1-F4=170+1395.5-755=+810.5mm
• 轧线标高的确定 轧线名义标高为+815mm,允许偏差为 ±5mm,标高A在+820~+810范围内(即下工作辊上辊面标 高),其参考点为车间地平面为±0。
精轧机下阶梯垫
• 轧线标高Adw与下阶梯垫厚度h、工作辊直径d和支承辊直 径D的关系为:(见上页附表)
• F1-F4
• F5-F6
AdwF1-F4= h+(D F1-F4/2+ dF1-F4)-755
精轧机压下装置
• 主要补偿工作辊重磨量,支承辊磨损后的调节靠人工在承 压垫板底部加垫板(垫板共3种,厚度分类:20、40、 50)。另上阶梯垫可以实现快速换辊(直接达到最薄厚度)
支承辊直径 1450~1410 1410~1370 1370~1330 1330~1300 垫板厚度 0(不采用垫板) 20 40(20+20) 50(20+20+10)
全国产1450mm五机架全连续冷轧机组

司设 计 成套 ,按 照可靠 、稳 定 、经 济 、实 用 的原
l 刖 舌
则 ,除 部分硬 件 和仪表 外 ,全部 采用 国产 化 技术 和设 备 ,国产 化 的过程 控制 系统 进行 轧制 参 数设 定计 算 、模 型 自适 应 及 自学 习 、轧 制 程 序 优 化 ,
以保 证技 术指 标 的先进 性 和关键 技术 的可 靠性 。
Z HAO T a — n, HU u n mi ANG Y u, Z HA a ,J in NG K i IJ g a ( h aN t n l ay Mahn r ee rh Is tt C . t. i n 1 0 2,C ia C i a o a Hev c i yR sac nt u o,Ld ,X ’ 0 3 n i e i e a7 h ) n
eg ts t f h g — rc so P ih e s o i h p e i n C C,e c AGC s se a o t a v n e h c n s o to e h oo i s u h a i t. y tm d p s d a c d ti k e s c n r lt c n lg e ,s c s f e f r a d c n r l e d a k c n r l n e so ls — o o t 1 ic CM a e n p t no p o u t n, e d o w r o to ,fe b c o to d t n i n c o e l p c nr .S n e T a o o h sb e u t r d c i i o
权 一套 国产 化 的高 速冷 连轧 设备 。15 m 五机 40m
Ab ta t 0 mm 5 s n a d m cl l ( C s c :1 5 -t d t e o mi T M)d v lp d i e e d nl b h aN t n l e v — r 4 a n d l eeo e d p n e t yC i a o a H ay Ma n y n i
1450四辊可逆冷轧机压下规程设计及机架设计与分析 (最终)
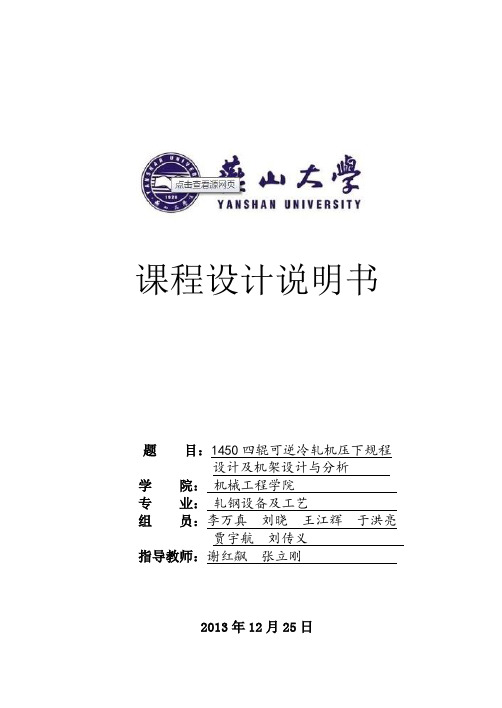
二、 轧辊尺寸的预设定
设计课题为“1450 四辊可逆冷轧机压下规程设计及机架设计与分析” , 则工作辊的辊身长度 L=1450mm,辊身长度确定后即可根据经验比例值法确 定轧辊直径,冷轧板带轧机
L D1 2.3 ~ 3.0 L D2 0.8 ~ 1.8 D1 D2 2.3 ~ 3.5 D1 500 ~ 580mm
——咬入角,rad
R ——轧辊半径,mm
3.3 初步制定压下规程
轧制道次 n 轧 前 厚 度 h0 (mm) 1 3 表 3.1 2 2.29 08F 压下规程 3 1.49 4 1.01 5 0.76
4
燕山大学专业综合训练(论文)说明书
轧 后 厚 度 h1 (mm) 压 下 量 h (mm) 压下率ε 累计压下率 ε' 咬 入 角 /rad
2
燕山大学专业综合训练(论文)说明书
一、 原料及设计技术参数
1.1、原料:
08F Q195 20 来料尺寸 3.0mm×1300mm 成品尺寸 0.7mm×1300mm 来料尺寸 2.6mm×1300mm 成品尺寸 0.6mm×1300mm 来料尺寸 2.2mm×1300mm 成品尺寸 0.5mm×1300mm 成品出口速度 v=8m/s。 开卷机最大张力 5 吨,卷取机最大张力 25 吨。
2.29
1.49
1.01
0.76
0.7
0.71
0.8
0.48
0.25
0.06
0.237 0.237 0.053
0.349 0.503 0.057
0.322 0.663 0.044
0.248 0.747 0.032
0.079 0.767 0.015
课程设计说明书
轧机的液压压下装置

轧机的液压压下装置液压压下装置是轧机中非常重要的组成部分,它主要用于在轧制过程中对轧辊进行压下,以使金属材料在轧制过程中得到良好的形状和尺寸。
液压压下装置一般由液压系统、主缸、液压缸、液压管路等部分组成。
下面将从这几个方面对液压压下装置作详细介绍。
一、液压系统液压系统是液压压下装置中最为核心的部分,它主要由油箱、油泵、阀门和油管等组成。
油箱主要用于储存液压油,并且在油箱中放置油滤器和油温计等,以确保液压系统中的油液清洁和温度适宜。
油泵的作用是将液压油从油箱中抽出并送入液压缸内,从而使液压缸对轧辊进行压下。
油泵一般有液压柱塞泵、液压齿轮泵和液压叶片泵等几种类型。
阀门主要用于控制液压系统中的液压油流动方向、流量和压力等参数,以实现对液压压下装置的控制。
油管主要用于将液压系统中的液压油输送到液压缸中,并且使液压油在液压缸内进行压力传递。
二、主缸主缸是液压压下装置中的一个重要部件,它主要由液压缸筒、活塞、活塞杆、活塞密封等组成。
液压缸筒一般由优质的合金钢材料制造而成,并且经过热处理和精密加工等工艺,以确保其具有足够的强度和刚性。
活塞是主缸内部的运动部件,它的作用是在液压压下装置工作时对轧辊进行压下,从而使金属材料在轧制过程中得到压制和塑性变形。
活塞杆是连接活塞和液压缸筒的部件,它的结构要求具有足够的强度和刚性,以承受液压压下装置工作时产生的巨大作用力。
活塞密封是主缸内部的关键部件,它的作用是防止液压缸内的液压油泄漏,并且保证液压系统的密封性和工作可靠性。
四、液压管路液压管路是液压压下装置中非常重要的部分,它主要由液压管、接头、接头密封等组成。
液压管一般由优质的碳钢管或不锈钢管制造而成,并经过加工和抛光等工艺,以确保其具有足够的强度和耐腐蚀性。
接头主要用于连接液压管和液压缸、液压泵、阀门等部件,使液压油能够顺畅流动。
接头密封一般采用油封圈、O型圈等密封件,它的作用是防止液压管路中的液压油泄漏,并且保持液压系统的密封性和工作可靠性。
轧机的液压压下装置

轧机的液压压下装置轧机的液压压下装置是轧机的重要部件之一,它主要用于轧机在工作过程中对板材进行压下作用。
液压压下装置的设计和性能对轧机的工作效率、产品质量和设备寿命有着重要的影响。
一、液压压下装置的主要功能液压压下装置是轧机的重要部件,主要功能有以下几点:1. 对轧机辊缝中的板材进行压下,保证板材在轧制过程中不会产生变形或者变形较小,从而提高产品的成形精度和表面质量。
2. 通过调整液压压下装置的压下力,可以调节轧机的压下量,满足不同板材的轧制需要。
3. 调整液压压下装置的工作方式和参数,可以适应不同的轧制工艺和板材材质,提高轧机的生产适应性和生产效率。
二、液压压下装置的结构和工作原理液压压下装置通常由液压缸、油缸、阀门、油泵以及压力传感器等部件组成。
其结构如图所示,通过控制阀门的调节,液压系统可以实现对液压缸的压力调节,从而实现对板材的压下作用。
液压压下装置的工作原理如下:当轧机开始工作时,液压系统通过油泵将液压油送入油缸中,使得油缸内的液压缸得以推动,从而对板材进行压下作用。
通过调节液压系统中的阀门,可以控制液压缸的工作压力和压下力的大小,满足不同板材的轧制需要。
通过压力传感器可以实时监测液压系统的工作压力,从而保证轧机的安全运行。
三、液压压下装置的优点液压压下装置相对于机械式压下装置具有以下几个优点:1. 调节性好:液压系统通过调节阀门可以实现对压下力的精确控制,且调节范围大,能够满足不同板材的轧制需求。
2. 压力稳定:液压系统具有压力稳定的特点,能够保证压下力的稳定输出,从而保证产品的成形精度和表面质量。
3. 响应速度快:液压系统的响应速度快,能够满足轧机在工作过程中对压下力的快速调节需求,提高轧机的生产效率。
4. 可靠性好:液压系统的工作过程相对平稳,不易发生振动和冲击,能够保证轧机的稳定运行,延长设备的使用寿命。
四、液压压下装置的应用现状及发展趋势目前,液压压下装置已经在轧机中得到了广泛应用,在改进轧机的生产效率、产品质量和设备可靠性等方面发挥了重要作用。
1450热轧板厂AGC液压系统浅析

1450热轧板厂AGC液压系统浅析陈好庆1450热轧板厂AGC液压系统浅析陈好庆摘要:本文介绍了热轧板厂精轧区AGC(厚度自动控制)液压系统的基本工作原理以及结构性能,对实际生产应用情况中存在的问题进行分析浅析,针对问题提出了处理措施和方法,较好的解决了液压压下系统的工作稳定性,满足生产要求,为相似设备运行管理提供经验以及系统日常维护的要点。
对于设备使用和维护管理具有重要的实际意义。
[关键词]:AGC 液压压下系统HAGC系统改造一引言攀钢1450热轧板厂AGC液压压下系统主要服务于精轧F1-F6轧机液压压下控制,AGC英文是Automatic Gain Control(自动厚度控制)的缩写,该系统是厦门海德科液压机械设备有限公司的一套先进自动化设备,安装于精轧机的F1-F6轧机之上)其主要作用是:在轧钢过程中,对轧辊进行精确定位,控制板材的轧制厚度,提高板形质量。
AGC液压系统的主要功能是为精轧F1-F6轧机动作提供动力源。
二 AGC系统工作原理及主要设备介绍1,AGC系统的工作原理AGC液压系统主要由动力元件、控制元件、执行元件、辅助元件、工作介质五部分组成。
动力元件的功用是将原动机输出的机械能转化为液体的压力能,其主要设备为三台(两用一备)通轴斜盘式恒压变量柱塞泵;控制元件的功用是控制和调节系统中油液的压力大小、流量大小和液流方向,其主要为伺服液压缸;辅助元件的功用是输油、集油、辅助改善系统性能, 其主要元件有油箱、滤油器、蓄能器等设备;工作介质的功用是传递动力和信号,同时还起到润滑、冷却、防锈的作用,其主要由液压油液组成。
AGC液压系统工作原理:系统正常工作时,主泵(两台工作,一台备用)打出的压力油,通过泵出口控制阀架分为两路:一路为主油路,一路为蓄能器储存及泄压油路。
轧机正常工作时,主油路的压力油经过伺服阀控制伺服液压缸工作,以达到轧机轧辊定位和控制板坯轧制厚度的目的。
AGC系统液压站由油箱装置、主泵供油系统、蓄能器装置、循环过滤冷却系统和回油过滤装置组成。
轧机的液压压下装置
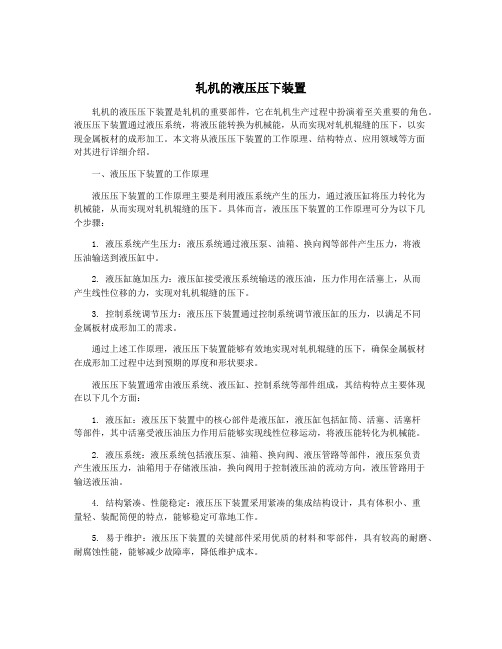
轧机的液压压下装置轧机的液压压下装置是轧机的重要部件,它在轧机生产过程中扮演着至关重要的角色。
液压压下装置通过液压系统,将液压能转换为机械能,从而实现对轧机辊缝的压下,以实现金属板材的成形加工。
本文将从液压压下装置的工作原理、结构特点、应用领域等方面对其进行详细介绍。
一、液压压下装置的工作原理液压压下装置的工作原理主要是利用液压系统产生的压力,通过液压缸将压力转化为机械能,从而实现对轧机辊缝的压下。
具体而言,液压压下装置的工作原理可分为以下几个步骤:1. 液压系统产生压力:液压系统通过液压泵、油箱、换向阀等部件产生压力,将液压油输送到液压缸中。
2. 液压缸施加压力:液压缸接受液压系统输送的液压油,压力作用在活塞上,从而产生线性位移的力,实现对轧机辊缝的压下。
3. 控制系统调节压力:液压压下装置通过控制系统调节液压缸的压力,以满足不同金属板材成形加工的需求。
通过上述工作原理,液压压下装置能够有效地实现对轧机辊缝的压下,确保金属板材在成形加工过程中达到预期的厚度和形状要求。
液压压下装置通常由液压系统、液压缸、控制系统等部件组成,其结构特点主要体现在以下几个方面:1. 液压缸:液压压下装置中的核心部件是液压缸,液压缸包括缸筒、活塞、活塞杆等部件,其中活塞受液压油压力作用后能够实现线性位移运动,将液压能转化为机械能。
2. 液压系统:液压系统包括液压泵、油箱、换向阀、液压管路等部件,液压泵负责产生液压压力,油箱用于存储液压油,换向阀用于控制液压油的流动方向,液压管路用于输送液压油。
4. 结构紧凑、性能稳定:液压压下装置采用紧凑的集成结构设计,具有体积小、重量轻、装配简便的特点,能够稳定可靠地工作。
5. 易于维护:液压压下装置的关键部件采用优质的材料和零部件,具有较高的耐磨、耐腐蚀性能,能够减少故障率,降低维护成本。
通过以上结构特点,液压压下装置能够实现对轧机辊缝的有效压下,具有结构紧凑、性能稳定、易于维护等优点。
1450六辊冷轧机(600m)

高速高精度宽带1450mm六辊可逆冷轧机组技术附件机组速度:600m/min唐山宏德伟业实业有限公司2010年6月目录1 附件一概述及工艺描述……………………………………2 附件二机组设备技术描述…………………………………3 附件三电气自动化描述及马达表…………………………4 附件四设计和设备分交……………………………………5 附件五供方提供技术资料的范围、进度…………………6 附件六需方提供技术资料的范围、进度…………………7 附件七外购标准件及生产厂家……………………………8 附件八设备安装与调试……………………………………9 附件九售后服务……………………………………………附件一概述及工艺描述目录1 概述………………………………………………………………2 机组主要工艺参数………………………………………………3 机组工艺流程……………………………………………………4装机水平…………………………………………………………5 主要电机功率……………………………………………………1. 概述1450毫米六辊可逆冷轧机组是在常温状态下,将材质为普通碳素钢和低合金优质钢,厚度为2.0~3.0mm的经过酸洗后的热轧带卷,经过若干道次的轧制,使其成为具有所需厚度、表面粗糙度的各种规格的冷轧带卷。
2 . 机组主要工艺参数2.1 原料状态:经过酸洗(可切边或不切边)后的热轧钢卷。
2.1.1 原料材质:低碳钢、中碳钢。
代表钢号:Q195、Q215、Q2352.1.2 厚度: 1.0~3.0mm2.1.3 宽度:1000~1250mm2.1.4 卷材内径:φ508mm/φ610mm2.1.5 卷材外径:φ1000~φ2000mm(设计考虑φ2100mm)2.1.6 最大卷重:28t2.2 成品:2.2.1 厚度:0.25~1.5mm2.2.2 宽度:800~1000mm2.2.3 卷材内径:φ508mm2.2.4 卷材外径:φ1000~φ1800mm(设计考虑φ2100mm)2.2.5 最大卷重:28t(设备能力)2.3 成品纵向厚度偏差:稳态轧制:1.5% h;加减速轧制:2%h;。
1450mm六辊可逆冷轧机组液压系统配置

1450mm六辊可逆冷轧机组液压系统配置根据机组技术规格书对流体部分的技术要求结合初步设计对该机组的液压系统作出如下配置:一、传动液压站及阀组1.1、用途:用于对开卷机、六辊可逆轧机、卷取机等各辅助液压传动机构提供压力油。
系统压力:12Mpa系统流量:125L/min ×2工作介质:抗磨液压油介质清洁度:NAS 9级1.2、设备组成1)设一台不锈钢油箱,外型初定2500L,箱上设有液位、油温控制仪表、加热器、冷却器、过滤器、蓄能器等。
2)工作泵二台(一用一备),采用进口VICKERS恒压变量泵3)循环泵一台,采用榆次叶片泵4)比例阀,采用进口VICKERS产品5)其它低压电磁阀,球阀、单向阀等采用北京华德液压件公司产品二、高压系统液压站及阀组2.1、用途:问六辊可逆轧机液压AGC系统、平衡、弯辊、窜辊系统提供压力油,该液压站由液压AGC系统平衡、弯辊、窜辊两个系统组成。
AGC系统:(泵站、阀组)系统压力:28Mpa系统流量:250L/min平辊、窜辊系统:(泵站、阀组)系统压力:25Mpa系统流量:80L/min工作介质:ISOVG46抗磨液压油介质清洁度:NAS6级2.2、设备组成:1、AGC液压系统及阀组高压泵二台(一用一备),采用进口VICKERS恒压变量泵中压泵二台(一用一备),采用进口VICKERS产品循环泵一台,采用榆次叶片泵伺服阀二台,采用美国Moog阀(带放大器)比例阀三台,采用进口VICKERS产品溢流阀七台,采用进口VICKERS产品压力传感器二个,采用德国HYDAC产品其它低压电磁阀、球阀、单向阀等采用北京华德液压件公司产品。
泵站配有加热器、冷却器、过滤器、液位计、温度控制器,蓄能器等,泵站管道、油箱采用不锈钢制作。
2、平衡、弯辊、窜辊泵站及阀组高压泵二台(一用一备),采用进口VICKERS恒压变量泵循环一台,采用榆次叶片泵比例减压阀六台,采用进口ATOS产品比例阀方向阀四台、采用进口VICKERS产品泵站配有加热器、冷却器、过滤器、蓄势器、液位计、温度控制器等油箱、泵站管道采用不锈钢制作三、稀油润滑系统、干油润滑系统及油气润滑站系统压力:0.5Mpa系统流量:800L/min工作介质:工业润滑油介质清洁度:0.12mm设备组成:工作泵2台(一用一备),采用进口VICKERS产品油箱及管路采用不锈钢制作,站上配有冷却器、滤油器、阀门等。
1450mm热连轧精轧液压AGC控制系统简介
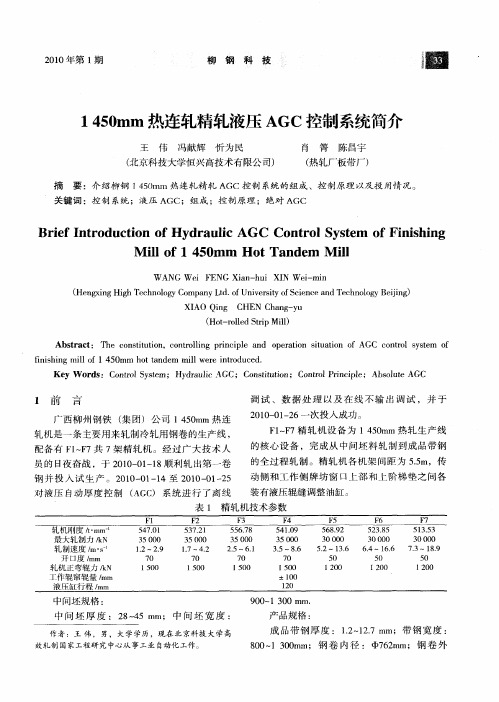
关键 词 :控制 系统 ;液 压 AG C;组 成 ;控 制 原理 ;绝 对 A GC
Bre n r d c i n o d a l ifI t o u to fHy r u i AG C n r lS se fF n s i g c Co t o y t m o i ih n
科 技
2 1 年第 1 00 期
以期 达到 目标 板厚 。在 A C中 , 型 的控制 方式 G 典
是反馈 控制方 式 (IR 。其控制 原理见 图 1 BS A) 。
偏差 调 节量
j
部 ,用 于补 偿 上 支承 辊 和 工作 辊磨 损 后 的位置 变 化 ,减 少 A C 的行 程 ,提 高 轧 机 的控 制 精 G 度 。上 阶梯 垫是 通 过 一个 带 位 置传 感 器 的液 压
21 0 0年第 1 期
柳
钢
科
技
1 5mm 热连轧精轧液压 AGC控制系统简介 0 4
王 伟 冯献辉 忻 为 民 肖 箐 陈 昌宇
( 京科 技大 学恒 兴 高技 术有 限公 司) 北 摘
( 轧厂板 带厂 ) 热
要 :介绍柳 钢 1 5mm 热 连轧精 轧 A 0 4 GC控 制 系统的组 成 、控 制原 理 以及投 用情 况。
柳 钢
径 :ql2 0 m ~ 5 r b 0 r a 20 0 m;最 大卷 重 :2 t a 5 ;钢 卷单 重 :1 . gm ( x。 5 / m ma) 9k 精 轧 压下 厚 度 控制 系 统 包括 上 阶 梯垫 装 置 及 A C系统 。上 阶梯垫 装置 安装 在液 压缸 的下 G
F ~ 7精 轧机 设 备 为 14 0 1F 5 mm热 轧 生 产 线
1450mm六辊可逆冷轧机自动控制系统的研究与应用

来料宽度 90—15 mm; 0 20
成 品厚 度 02—1 m; . . 0m 成 品 内径 5 0mm; 1 成 品 外 径 ( 0 —9 0 m 1 0 0 m; 9 最 大 轧 制 力 1 0 N; 500k
2 设 备组成
摘 要: 介绍 了 自主开发设计的 六辊 可逆冷轧机的主要参数 、 备构成及 自动控制 系统的组成 、 设 结构和功 能, 由于 自动控制 系统 采用
了 先进的网络通讯技术及灵活多变 的控制方式. 所以实 现了高 速轧制, 且保证了 产品质量。
关键词 : 辊可逆冷轧机 ; 六 自动 控 制 系统 ; 能 功 中 图分 类 号 : G3 T 3 文献标识码 : B 文章 编 号 :6 2 5 5 ( 0 0)s-o 8 0 17 - 4 X 2 1 o . 8 - 2 : o
15 l 4 0mn六辊可逆冷 轧机是 中冶陕压重工设备 有限公 司 具有 自主知识 产权 、 自主研 制开发 的机 、 、 电 液一体化 全部成
轧制速度( x 0 / i( Ma )1 0mr n8=02~08衄 ) 0 a . . ;
穿 带 速 度 1 / i。 8mr n a
运行 状态 的监视 和报警 , 液压 站 、 滑站 等的工艺 控 制 , 润 主轧
机 的速度 控制 和显示 , 开卷 机和卷取 机的恒张力 控制 , 主轧机 轧辊 负荷 平衡控 制 , 断带检测 和保护 , 上卷小 车 、 卸卷小 车、 乳Байду номын сангаас 液流量 、 向等 工艺操 作控 制 , 长计算 , L 、2级系 统进 方 带 与 DL 行信息交换 。 L 2级系统 为监控级 自动化系统 ,主要 由装 在研华工控机 中的 WiC n C监控 系统组 成 , 主要实 现 以下 功能 : 其 轧机 生产
国产1450mm六辊可逆冷轧机组的特点

da l ce o n t v r o o t m da o s a tm t a g o t l A C) w o i t C d v o t l rui srw d w , r es m t no i e e i erl , u a cg u ecnr ( G , h l dg r ec n o , c a e i fn r t l o i o e iD i r
有全液压压下 、 中间辊横移 、 厚度 自动 控制 、 数字 直流传 动控 制 、 全 工艺 润滑 分段 冷却 等特 点 , 可轧 制出 0 2 .5
mm 以下 的产 品 。
关键词 : 六辊可逆冷轧机组 ; 中间辊横移 ; 厚度 自动控制
中 图分 类 号 :G 3 .2 T 3 5 1 文 献标 识 码 : A
K y w r ss — i v r n o ln i ; r e em t no t m da l : u m t ag ot l A E e o d : x hg r e i c l r l gm l t v r o o f n r e i er l a t a cg uecnr ( G ) i h e s g d oi l a s i ie t os o i o
任 来锁 黄 煜 王 斌
(. 1 山东泰 山钢铁 公司 , 山东 2 12 ;. 7 16 2 中国重型机械研究院 , 陕西 7 0 3 ) 10 2 摘要 : 详细介绍 了 1 5 m六辊可逆冷 轧机 组的设备组成 、 0m 4 主要 技术 参数及 机组 的装 机水 平。该机组 具
l l4 0 m 六辊 可逆 冷轧 机组 的基 本参 数 5 m 1 来料 规格 : ) 厚 度/ m: . 4 0 宽 度/ m 2 0~ . ; mm:0 2 0 8 0~ 5 2 成 品规格 ) 厚 度/ m:.0~ . ; 度/ m:0 m 02 08宽 m 8 0—12 0 5 ; 厚度 公差/ mm: 0 05 卷重/ :5 最 大 ) ± .0 ; t2 (
冷轧平整机工作原理简介

冷轧平整机工作原理简介摘要:平整机在冷轧产品的生产过程中至关重要,文章从冷轧工艺原理入手,介绍了平整机的工作方式、工作原理和工艺的特点,阐述了平整机在提产冷轧产品质量上所起到的关键作用。
关键词:平整机原理作用通过冷轧而变成纤维状组织的带钢,在退火工序中由于再结晶而变为具有新的结晶组织的带钢。
这种退火后的带钢几乎完全成为软质状态,因此不适用于加工,只要稍稍给予轻度冲压加工,带钢表面就会产生拉伸应变和不规则的滑移线,明显有碍外观。
这种退火带钢办不能直接供给用户使用,必须进行平整轧制,即通过轻度的冷轧加工改善其材质、平整钢板形状。
一、平整轧制的目的简单来说平整机的主要目的就是消除材料的屈服平台,防止加工时的拉伸应变;提高材料的屈服极限、降低屈服极限,以及扩大塑性加工范围;使带钢表面获得需要的粗糙度和光泽;矫正板材形状。
经过冷轧和退火后的带钢表面会多少粘有一些脏物,其主要成分是铁、铁离子和碳,在干平整时这些脏物会污染环境。
随着粘附程度的不同,在干平整时这些脏物会玷污工作辊。
通常它们粘附在工作辊的端部,且以点状或凸斑状粘附在打毛的轧辊表面上,在平整时粘附了脏物的工作辊会在带钢边部留下周期性的压痕,最终导致带钢质量的降低。
二、平整机工艺特点介绍带钢在平整时采用干平整及湿平整工艺。
各自特点如下:(1)干平整特点所轧带材的表面可保持不受玷污;为下一步加工(渡锡)做准备;在轧辊与轧件间产生大的摩擦;保证只给轧件以有限延伸量和压下量;压下率一般为0.5%~6%。
(2)湿平整特点不易压入杂质,或粘着杂质而产生辊痕缺陷,可以获得较大的压下量,确保延伸率;在平整后的带钢表面留下一层润滑的抗腐蚀或其他形式的薄膜;压下率可达10%。
平整率由于平整压下率很小,难以测准其厚度差,因此用与压下率成比例的带钢长度变化率即延伸率来表示平整率,其表示式为:μ=(l1-l0)/l0*100%式中,μ-平整带钢延伸率;l0、l1-平整前、后带钢长度。
一、1450mm不可逆式四辊轧机技术参数及设备组件

一、1450mm不可逆式四辊轧机技术参数及设备组件轧制材料:铝合金轧制宽度:850mm-1320mm入口厚度:0.9mm出口厚度:0.1mm卷材内孔:不带套筒¢520套筒:¢505*¢565*1650 锥面15º最大卷重:10吨最大轧制力:3000KN轧制速度:420米/分主机电机额定功率:450KW*1台开卷电机额定功率:67KW*2台卷取电机额定功率:287KW*1台最大开卷张力:24 KN最大卷取张力:20 KN工作辊:¢260*1500mm(2根)备用8根(4付)共5付支撑辊:¢660*1450mm(2根)备用2根(1付)共2付注:1450箔轧机目前正常运行,如需采购,包含滤油机、冷却器等辅助设备均包括在内,可做交钥匙工程。
联系人:朱部长135****1616孙部长138****0198二、1650mm不可逆式四辊轧机1、1650mm轧机技术参数轧制材料:铝合金宽度:850mm-1500mm入口厚度:1.2mm出口厚度:0.1mm卷材内孔:不带套筒¢520套筒:¢505*¢565*1650 锥面15º最大卷重:10吨最大轧制力:3000KN(300吨)轧制速度:420米/分主机电机额定功率:450KW*1台开卷电机额定功率:99KW*2台卷取电机额定功率:284KW*1台最大开卷张力:24 KN最大卷取张力:20 KN工作辊:¢260*1650mm支撑辊:¢660*1550mm目前1650mm轧机已拆除,不能作为整机出售,只能出售以下组件:2、1650箔轧机组件偏导辊:4根¢320*1650展平辊:2根(聚氨酯胶)¢180*15003根(40GrMO)¢160*1500主机减速机备用:2台(LH290)净、污油泵:各1台压面辊:1根(聚氨酯胶)¢170*1500主机传动轴:4根(SWC225BH-1100)压上缸:2台¢360/¢250*70锥头油缸:5台旧工作辊轴承箱:2副(8件)弯辊缸压盖:47件活塞:28件,正弯:10件,¢45*75 负弯:10件,¢45*85 平衡缸:8件,¢45*95圆盘刀:¢120*¢125*20 30片工作辊轴承箱定位套:12个¢145*169*80工作辊圆螺母带丝瓦:5套M155*3滑动联轴器:1套开卷M1联轴器:85*172/95*132(GIICL6)1件开卷M2联轴器:85*172/175*142(GIICL5)1件卷取联轴器:110*212/120*167(GIICL8) 1件卷取缠边机:1套换支撑辊架子:1件工作辊联轴节:2件¢225*275联系人:朱部长135****1616孙部长138****0198。
- 1、下载文档前请自行甄别文档内容的完整性,平台不提供额外的编辑、内容补充、找答案等附加服务。
- 2、"仅部分预览"的文档,不可在线预览部分如存在完整性等问题,可反馈申请退款(可完整预览的文档不适用该条件!)。
- 3、如文档侵犯您的权益,请联系客服反馈,我们会尽快为您处理(人工客服工作时间:9:00-18:30)。
1450mm冷轧机液压压下(或压上)简介
一、系统概述;
原理和功能简述如下:
液压压下(或压上)由双电液伺服阀组成的电液伺服系统。
该系统的动态性能良好。
通过小试验轧机液压压下试验开发,又经冷轧带钢厂工业性试验获得成功后,作为产品,先后在40多套黑色和有色金属冷轧机上应用,有四辊轧机,HC轧机,多辊轧机,连轧机,平整机等。
电气系统选用西门子的S7400系列PLC,及SIMADYN D的FM458功能模块研制开发而成。
位置,压力,厚度PID调节都在功能模块FM458中实现。
系统响应快,稳定。
故装置都是经过实践和考核过的可靠的成熟的产品。
二、系统的功能及特点;
1、双阀工作及双阀工作次序的切换;
压下(压上)的每个油缸由二个电液伺服阀供油控制。
二个伺服阀控制其分先后导通,即在调节过程中,只须小流量时,仅一个伺服导通工作,参与调节。
另一个伺服阀处于准备状态,不参与工作。
当需大调节流量,第一个伺服阀已饱和时,第二个伺服阀才开始导通。
此功能由电路控制实现。
这样可使系统稳定,动态性能良好。
由于二个伺服阀工作的次序不同,第一个工作的伺服阀工作频繁,磨损较大。
故系
统设有工作次序选择切换开关,控制二个阀的磨损程度均衡,提高伺服阀的使用寿命。
如由于伺服阀故障需检修时,系统可选择切换为一个阀工作。
液压压下能继续正常工作。
从而减少停机率。
但必须注意操作侧、传动侧二侧同时选择单阀工作。
此时压下速度减小一半。
2、压下系统的二种闭环调节功能;
分别介绍如下:
(1)、A.P.C.系统;
A.P.C. 系统,由进口的微脉冲位置传感器作为油缸位移的位置实际值,组成位置闭环系统。
系统稳定性好,分辨率高。
可确保分辨0.001mm。
系统设有零辊缝压靠,位置快、慢二挡压下速度给定及快速抬辊。
辊缝倾斜给定、及操作侧、传动侧二侧油缸同步控制环节。
系统能确保压下过程中,轧辊平行移动。
(2)、A.F.C.;(轧制力闭环)
A.F.C.由负载腔油压压力传感器作为反馈元件,并经计算机数据处理后作为负载力显示。
油缸移动时,能确保同步移动,受负载时,进入轧制力闭环控制。
同样设有快、慢二挡压力给定,不对称压力给定、快抬等功能。
位置、压力给定、倾斜给定都由数字式给定积分器实现。
位置、压力给定有快、慢二个不同的积分时间常数,供操作工选择。
3、厚度自动控制(A.G.C.)。
系统与测厚仪组合后具有带材厚度自动控制功能。
厚度自动控制根据带材及工艺需求的不同,有多种模式可供选用。
压下系统的位置闭环系统(A.P.C.)及压力闭环系统(A.F.C.)。
可根据工艺需要任意选择工作制形式。
(1)、板材轧制时,压下以位置控制为基准的予控与监控A.G.C.。
即以产生的厚差值,运算处理分别输出压下位置调整量的前馈、后馈的控制模式;
(2)以轧制力为基准的控制模式。
当轧簿材时,辊缝已充分压靠,位置控制已失去作用,压下系统可A.F.C.工作。
(也可自动切换压下工作状态)。
此时 A.G.C.系统以厚差值根据厚度控制的不同模式数学关系式,求出应调节的轧制力,去修正轧制力,达到厚控的目的。
当轧制力饱和时,系统能自动提示或根据用户需要自动调节带材张力,进入张力A.G.C. 模式工作。
4、数字化及P.L.C.逻辑控制;
液压压下(压上)及厚度自动控制功能,除压力传感器、位置传感器及伺服阀的功放板外,全部由西门子S7-400PLC (及FM458系统)来实现,其给定积分器、调节器等都数字化,输入、输出都经由模、数和数、模转换,转换位数高,
精度高。
操作、显示、控制都由P.L.C.实现逻辑控制,控制可靠。
5、显示、报警、保护功能;装置设有操作侧、传动侧的辊缝值、轧制力值数字显示。
总轧制力、轧辊倾斜显示。
超压、超压差、过倾斜、欠压、系统故障等报警。
断带抬辊、紧急压下卸负、紧急油站的系统压力卸压等功能。
三、电气系统技术指标:
位置分辨率: <0.001mm。
位置给定分辨率: <0.001mm。
四、提供资料范围;
压下电气图、电气设备明细表、使用说明书。
五、装置组成:
1、压下电控箱1台(含P.L.C.1套)
2、机旁操作盘1台(含PC分布I/O 1套)
3、人机界面TP270操作面板1件
4、位置传感器4支(外置式)
5、压力传感器2只;
6、接线盒及连接插件1套
说明:1、系统中测厚仪2台。
2、系统现场电气设备间连接用的外部接线电缆。
3、中间辊抽动如用液压抽动更好。
4、压下泵站、辅助泵站、稀油站、压下油缸如
需要可另行添加。