双面胶涂布的工艺控制要点
双面胶成型工艺
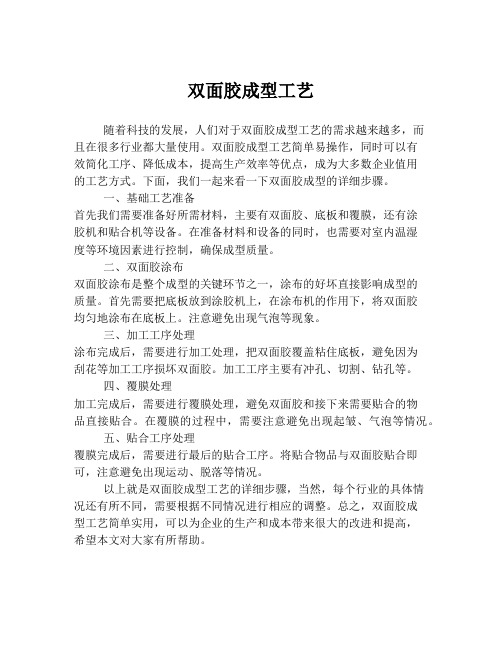
双面胶成型工艺
随着科技的发展,人们对于双面胶成型工艺的需求越来越多,而
且在很多行业都大量使用。
双面胶成型工艺简单易操作,同时可以有
效简化工序、降低成本,提高生产效率等优点,成为大多数企业值用
的工艺方式。
下面,我们一起来看一下双面胶成型的详细步骤。
一、基础工艺准备
首先我们需要准备好所需材料,主要有双面胶、底板和覆膜,还有涂
胶机和贴合机等设备。
在准备材料和设备的同时,也需要对室内温湿
度等环境因素进行控制,确保成型质量。
二、双面胶涂布
双面胶涂布是整个成型的关键环节之一,涂布的好坏直接影响成型的
质量。
首先需要把底板放到涂胶机上,在涂布机的作用下,将双面胶
均匀地涂布在底板上。
注意避免出现气泡等现象。
三、加工工序处理
涂布完成后,需要进行加工处理,把双面胶覆盖粘住底板,避免因为
刮花等加工工序损坏双面胶。
加工工序主要有冲孔、切割、钻孔等。
四、覆膜处理
加工完成后,需要进行覆膜处理,避免双面胶和接下来需要贴合的物
品直接贴合。
在覆膜的过程中,需要注意避免出现起皱、气泡等情况。
五、贴合工序处理
覆膜完成后,需要进行最后的贴合工序。
将贴合物品与双面胶贴合即可,注意避免出现运动、脱落等情况。
以上就是双面胶成型工艺的详细步骤,当然,每个行业的具体情
况还有所不同,需要根据不同情况进行相应的调整。
总之,双面胶成
型工艺简单实用,可以为企业的生产和成本带来很大的改进和提高,
希望本文对大家有所帮助。
涂布的流程及控制要点
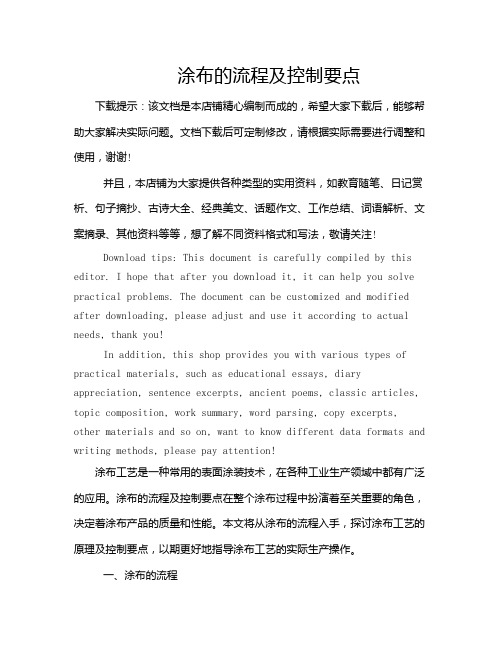
涂布的流程及控制要点下载提示:该文档是本店铺精心编制而成的,希望大家下载后,能够帮助大家解决实际问题。
文档下载后可定制修改,请根据实际需要进行调整和使用,谢谢!并且,本店铺为大家提供各种类型的实用资料,如教育随笔、日记赏析、句子摘抄、古诗大全、经典美文、话题作文、工作总结、词语解析、文案摘录、其他资料等等,想了解不同资料格式和写法,敬请关注!Download tips: This document is carefully compiled by this editor. I hope that after you download it, it can help you solve practical problems. The document can be customized and modified after downloading, please adjust and use it according to actual needs, thank you!In addition, this shop provides you with various types of practical materials, such as educational essays, diary appreciation, sentence excerpts, ancient poems, classic articles, topic composition, work summary, word parsing, copy excerpts, other materials and so on, want to know different data formats and writing methods, please pay attention!涂布工艺是一种常用的表面涂装技术,在各种工业生产领域中都有广泛的应用。
涂覆胶安全生产操作规程

涂覆胶安全生产操作规程一、目的与范围为了确保涂覆胶生产过程中人身安全和工作区环境的安全,规范涂覆胶的安全生产操作,促进生产效率提高,减少事故发生,特制定本操作规程。
本操作规程适用于涂覆胶生产单位,涉及到涂覆胶操作及相关设备的日常检查、操作操作要求。
二、涂覆胶生产操作要求1.操作前必须参加安全培训,熟悉涂覆胶生产操作规程。
2.工作人员在涂覆胶操作过程中必须穿戴好劳动防护用品,包括帽子、口罩、手套、工作服、防滑鞋等。
3.在涂覆胶操作区域应设立明显的安全警示标志,确保工作人员安全意识。
4.涂覆胶操作室内必须保持清洁整齐,不得摆放杂物,保持通风良好。
5.涂覆胶操作室内禁止吸烟、饮食、乱丢废弃物等行为。
三、涂覆胶操作流程1.准备工作–检查涂覆胶设备是否正常运转,并进行日常维护和检修。
–准备涂覆胶材料,确认材料质量符合要求。
–检查并准备好所需的劳动防护用品,确保工作人员的安全。
–操作前进行设备预热,确保设备正常工作状态。
2.涂覆胶操作–打开涂覆胶设备,调整操作参数,确保符合工艺要求。
–将待涂覆的材料放置在操作区域。
–将材料放置在输送带上,逐步将其送入涂覆机中。
–确认涂覆机工作正常后,控制涂覆速度,保证涂布均匀、稳定。
–完成涂覆后,设备停止运行,清理涂覆机和操作区域。
3.收尾工作–对涂覆胶设备进行日常清理和检查,并做好设备维护记录。
–清理涂覆胶操作区域,确保整洁无障碍。
–停止涂覆胶生产设备并切断电源。
–整理劳动防护用品,并妥善存放。
四、涂覆胶安全注意事项1.涂覆胶操作过程中要时刻保持警觉,防止发生火灾、化学品泄露等意外情况。
2.涂覆胶设备维护时,必须切断电源,并将设备完全停止运行之后才能进行操作。
3.使用涂覆胶材料时,必须遵守使用说明,并注意防止接触眼睛和皮肤。
4.发生事故或异常情况时,应立即停止涂覆胶操作,并报告相关负责人。
五、涂覆胶安全故障处理1.发生设备故障时,应立即停止涂覆胶操作,通知维修人员进行维修处理。
涂胶控制计划做
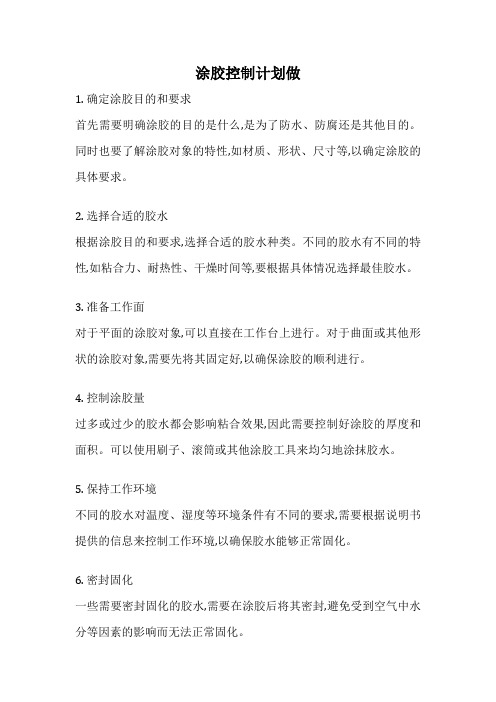
涂胶控制计划做
1. 确定涂胶目的和要求
首先需要明确涂胶的目的是什么,是为了防水、防腐还是其他目的。
同时也要了解涂胶对象的特性,如材质、形状、尺寸等,以确定涂胶的具体要求。
2. 选择合适的胶水
根据涂胶目的和要求,选择合适的胶水种类。
不同的胶水有不同的特性,如粘合力、耐热性、干燥时间等,要根据具体情况选择最佳胶水。
3. 准备工作面
对于平面的涂胶对象,可以直接在工作台上进行。
对于曲面或其他形状的涂胶对象,需要先将其固定好,以确保涂胶的顺利进行。
4. 控制涂胶量
过多或过少的胶水都会影响粘合效果,因此需要控制好涂胶的厚度和面积。
可以使用刷子、滚筒或其他涂胶工具来均匀地涂抹胶水。
5. 保持工作环境
不同的胶水对温度、湿度等环境条件有不同的要求,需要根据说明书提供的信息来控制工作环境,以确保胶水能够正常固化。
6. 密封固化
一些需要密封固化的胶水,需要在涂胶后将其密封,避免受到空气中水分等因素的影响而无法正常固化。
7. 监控固化过程
固化过程中需要持续监控,确保符合要求。
如果出现不正常情况,要及时采取应对措施。
8. 检查粘合效果
固化完成后,检查粘合效果是否符合要求,如有需要可以进行返工或重新涂胶。
以上是一个较为完整的涂胶控制计划,具体操作时可以根据实际情况进行调整和完善。
严格执行计划,可以保证涂胶质量,避免不必要的返工和浪费。
泡棉双面胶涂布工艺

泡棉双面胶涂布工艺【泡棉双面胶涂布工艺】一、泡棉双面胶涂布工艺的历史1.1 从无到有的发展历程其实啊,泡棉双面胶涂布工艺并不是一下子就出现的,它也有一个逐渐发展的过程。
在过去,人们想要将两个物体粘贴在一起,可能会使用胶水或者简单的单面胶带。
但随着科技的进步和需求的增加,泡棉双面胶涂布工艺应运而生。
1.2 不断改进的关键节点说白了就是,当最初的泡棉双面胶出现后,它的性能和质量并不是完美的。
在不断的实践和研究中,工艺不断改进。
比如,早期的泡棉双面胶可能粘性不够强,容易脱落,经过多次试验和改进,如今的泡棉双面胶在粘性、耐久性等方面都有了极大的提升。
二、泡棉双面胶涂布工艺的制作过程2.1 准备工作首先,得准备好制作泡棉双面胶所需的原材料,这就像是做菜前要准备好食材一样。
泡棉材料、胶粘剂、离型纸等都是必不可少的。
2.2 涂布胶粘剂接下来,就是把胶粘剂均匀地涂布在泡棉材料的一面。
这一步可是个技术活,就好比给蛋糕抹奶油,要抹得均匀、平整,不能有厚有薄。
2.3 贴合离型纸然后,在涂布好胶粘剂的泡棉材料上贴合离型纸,以保护胶粘剂的粘性。
这就好像给珍贵的东西盖上一层保护罩。
2.4 分切和包装最后,把制作好的泡棉双面胶按照一定的尺寸进行分切,并进行包装,方便使用和销售。
三、泡棉双面胶涂布工艺的特点3.1 良好的缓冲性能泡棉双面胶具有很好的缓冲性能,就像给物体穿上了一件“减震衣”。
比如说,在运输一些易碎物品时,用泡棉双面胶固定,可以有效减少物品在运输过程中受到的冲击和震动。
3.2 强大的粘性它的粘性那可是相当厉害,一旦粘上,就像“老铁”一样不离不弃。
无论是光滑的表面还是粗糙的表面,都能紧紧贴合。
3.3 适应各种环境不管是高温还是低温,潮湿还是干燥的环境,泡棉双面胶都能保持良好的性能。
这就好比一个全能的运动员,无论在什么场地都能发挥出色。
四、泡棉双面胶涂布工艺的应用4.1 电子行业在电子行业中,泡棉双面胶可是大显身手。
比如说手机、电脑等电子产品内部的零部件固定,经常会用到它。
涂布作业指导书
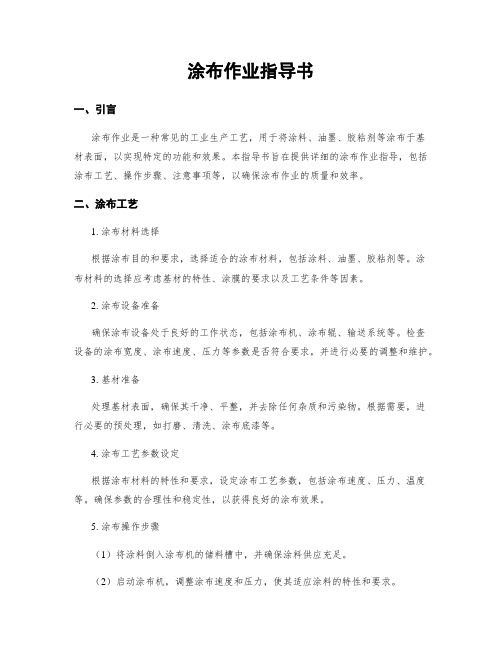
涂布作业指导书一、引言涂布作业是一种常见的工业生产工艺,用于将涂料、油墨、胶粘剂等涂布于基材表面,以实现特定的功能和效果。
本指导书旨在提供详细的涂布作业指导,包括涂布工艺、操作步骤、注意事项等,以确保涂布作业的质量和效率。
二、涂布工艺1. 涂布材料选择根据涂布目的和要求,选择适合的涂布材料,包括涂料、油墨、胶粘剂等。
涂布材料的选择应考虑基材的特性、涂膜的要求以及工艺条件等因素。
2. 涂布设备准备确保涂布设备处于良好的工作状态,包括涂布机、涂布辊、输送系统等。
检查设备的涂布宽度、涂布速度、压力等参数是否符合要求,并进行必要的调整和维护。
3. 基材准备处理基材表面,确保其干净、平整,并去除任何杂质和污染物。
根据需要,进行必要的预处理,如打磨、清洗、涂布底漆等。
4. 涂布工艺参数设定根据涂布材料的特性和要求,设定涂布工艺参数,包括涂布速度、压力、温度等。
确保参数的合理性和稳定性,以获得良好的涂布效果。
5. 涂布操作步骤(1)将涂料倒入涂布机的储料槽中,并确保涂料供应充足。
(2)启动涂布机,调整涂布速度和压力,使其适应涂料的特性和要求。
(3)将基材送入涂布机,确保其与涂布辊之间的接触均匀和稳定。
(4)控制涂布机的运行速度和涂布厚度,以实现所需的涂布效果。
(5)涂布完成后,住手涂布机的运行,并进行涂布辊的清洗和维护。
三、注意事项1. 安全操作涂布作业涉及到涂料、溶剂等化学物质,操作人员应佩戴防护手套、护目镜等个人防护装备,并遵守相关的安全操作规程。
2. 环境控制涂布作业应在适宜的环境条件下进行,包括温度、湿度、通风等。
确保环境条件符合涂布材料的要求,以避免涂膜浮现质量问题。
3. 涂布质量控制对涂布作业进行质量控制,包括涂布厚度、涂布均匀性、附着力等方面的检测和评估。
根据需要,进行必要的调整和改进,以提高涂布质量。
4. 设备维护定期检查和维护涂布设备,包括清洗涂布辊、更换涂布刀片等。
确保设备的正常运行和长期稳定性。
双面涂胶工序作业指导书
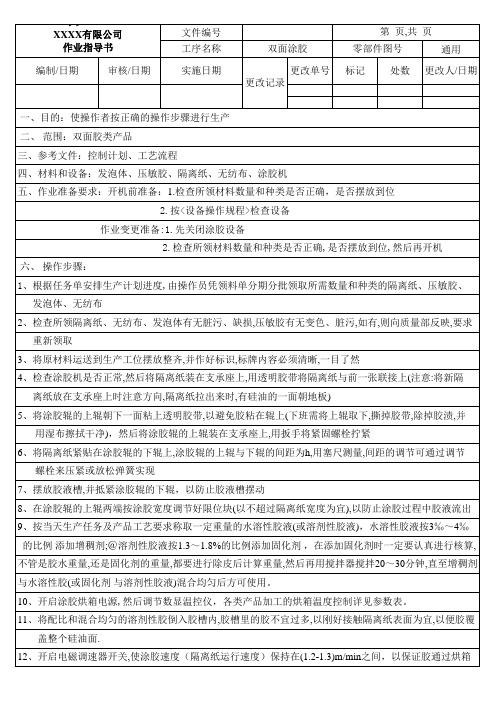
2.按<设备操作规程>检查设备 作业变更准备:1.先关闭涂胶设备
2.检查所领材料数量和种类是否正确,是否摆放到位,然后再开机 六、 操作步骤: 1、根据任务单安排生产计划进度,由操作员凭领料单分期分批领取所需数量和种类的隔离纸、压敏胶、
发泡体、无纺布 2、检查所领隔离纸、无纺布、发泡体有无脏污、缺损,压敏胶有无变色、脏污,如有,则向质量部反映,要求
重新领取 3、将原材料运送到生产工位摆放整齐,并作好标识,标牌内容必须清晰,一目了然 4、检查涂胶机是否正常,然后将隔离纸装在支承座上,用透明胶带将隔离纸与前一张联接上(注意:将新隔
离纸放在支承座上时注意方向,隔离纸拉出来时,有硅油的一面朝地板) 5、将涂胶辊的上辊朝下一面粘上透明胶带,以避免胶粘在辊上(下班需将上辊取下,撕掉胶带,除掉胶渍,并
盖整个硅油面. 12、开启电磁调速器开关,使涂胶速度(隔离纸运行速度)保持在(1.2-1.3)m/min之间,以保证胶通过烘箱
时能充分烘干(隔离纸运行速度测定方法:在紧贴隔离纸边工作台面上量取1.3m长度,并在0m、1.2m、 1.3m处作好标识,先在隔离纸边缘上用记号笔作一标识,当该标识运行至0m时,用秒表开始记时一分钟, 观测隔离纸边缘上的标识是否运行至(1.2-1.3)m区间内,如不在该区间,微调电磁调速器旋钮开关直至达 到要求为止) 13、从烘箱出来粘胶的粘附状态,每10分钟观察一次,通过用食指指背接触粘胶面,粘胶如能被带起,呈无 色透明的固态,既可认为胶粘附程度和外观合格 14、将无纺布放在烘箱另一侧的支撑座上,并确保无纺布筒芯的调节槽与调节旋钮相啮合,然后将无纺布 通过过度张紧辊、调节压辊,平铺在附有粘胶的隔离纸上。由于无纺布在铺设过程中容易产生折皱,此 时需通过张紧辊调节旋钮将无纺布抚平,与附有粘胶的隔离纸复合后经过张紧辊,最后缠绕在卷取筒上 15、将卷取筒上复合好的无纺布取下,放于一侧的支撑平台上,将无纺布与隔离纸轻轻剥离,并且使无 纺布有胶的一面朝上,然后将准备好的发泡体平铺在有胶一面的无纺布上,通过双面压辊将发泡体 与无纺布紧密粘合在一起 16、无纺布与发泡体通过压辊机复合后,用刀将复合后的前后两张发泡体割开,同时检查发泡体上应 100%被无纺布覆盖,否则需将未被覆盖的地方重新补胶覆盖后才能摆放在指定位置 17、按当天生产任务及产品工艺要求称取一定重量的水溶性胶液(或溶剂性胶液),水溶性胶液按3‰~4‰ 的比例 添加增稠剂;@溶剂性胶液按1.3~1.8%的比例添加固化剂 ,在添加固化剂时一定要认真进行核算, 不管是胶水重量,还是固化剂的重量,都要进行除皮后计算重量,然后再用搅拌器搅拌20~30分钟,直至增稠剂 与水溶性胶(或固化剂 与溶剂性胶液)混合均匀后方可使用。 18、重新摆放胶液槽,并抵紧涂胶辊的下辊,以防止胶液槽摆动 19、开启涂胶烘箱电源,调节数显温控仪控制烘箱温度,各产品控制要求详见涂胶机复合参数标准表。 20、将配比好的水溶性胶液倒入胶液槽内,使胶液与隔离纸表面能充分接触,以便胶覆盖整个隔离纸表面 21、开启电磁调速器开关,使涂胶速度(隔离纸运行速度)保持在(1.2-1.3)m/min之间,以保证胶通过烘箱 时能充分烘干 22、从烘箱出来粘胶的粘附状态,每10分钟观察一次,通过用食指指背接触粘胶面,粘胶如能被带起,呈无 色透明的固态,既可认为胶粘附程度和外观合格 23、将复合后的发泡体有无纺布的一面平铺在涂有粘胶的隔离纸上,通过涂胶机双面压辊、调节辊将发 泡体、无纺布、隔离纸紧密粘合在一起 24、发泡体、无纺布、隔离纸通过压辊机复合后,用刀将复合后的前后两张发泡体割开,同时检查无纺 布上应100%被压敏胶液覆盖,否则需将未被覆盖的地方重新补胶覆盖后才能摆放在指定位置 25、生产中如遇异常情况必须立刻向上级领导报告 七、维护要求:定期检查涂胶机使用状况,如有异常应及时处理 八、安全要求:1.为保证产品完好性,不得对产品随意乱丢乱放,应在规定位置轻拿轻放
涂布操作及质量控制注意事项
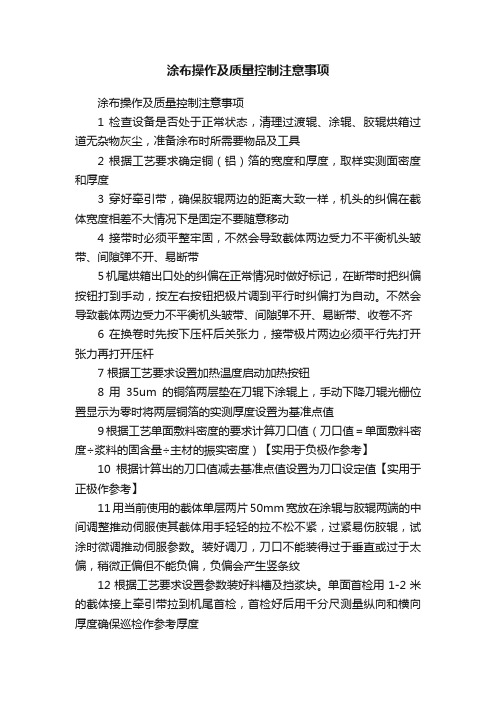
涂布操作及质量控制注意事项涂布操作及质量控制注意事项1 检查设备是否处于正常状态,清理过渡辊、涂辊、胶辊烘箱过道无杂物灰尘,准备涂布时所需要物品及工具2 根据工艺要求确定铜(铝)箔的宽度和厚度,取样实测面密度和厚度3 穿好牵引带,确保胶辊两边的距离大致一样,机头的纠偏在截体宽度相差不大情况下是固定不要随意移动4 接带时必须平整牢固,不然会导致截体两边受力不平衡机头皱带、间隙弹不开、易断带5机尾烘箱出口处的纠偏在正常情况时做好标记,在断带时把纠偏按钮打到手动,按左右按钮把极片调到平行时纠偏打为自动。
不然会导致截体两边受力不平衡机头皱带、间隙弹不开、易断带、收卷不齐6 在换卷时先按下压杆后关张力,接带极片两边必须平行先打开张力再打开压杆7 根据工艺要求设置加热温度启动加热按钮8 用35um的铜箔两层垫在刀辊下涂辊上,手动下降刀辊光栅位置显示为零时将两层铜箔的实测厚度设置为基准点值9根据工艺单面敷料密度的要求计算刀口值(刀口值=单面敷料密度÷浆料的固含量÷主材的振实密度)【实用于负极作参考】10根据计算出的刀口值减去基准点值设置为刀口设定值【实用于正极作参考】11用当前使用的截体单层两片50mm宽放在涂辊与胶辊两端的中间调整推动伺服使其截体用手轻轻的拉不松不紧,过紧易伤胶辊,试涂时微调推动伺服参数。
装好调刀,刀口不能装得过于垂直或过于太偏,稍微正偏但不能负偏,负偏会产生竖条纹12根据工艺要求设置参数装好料槽及挡浆块。
单面首检用1-2米的截体接上牵引带拉到机尾首检,首检好后用千分尺测量纵向和横向厚度确保巡检作参考厚度13正极涂布速比一般情况下设置为1.2,负极设置为80﹪(暂时作参考)。
头尾修调参数根据实际厚度作调整,留白速比和头部速比设置一致,其它根据实际情况作调整14单面涂完后拉空箔到机尾再涂1-2米长拉到机尾作双面首检,单面尾检合格刀口参数不要调整,若不合格,刀口参数适当调整,双面首检将涂单面1-2米长的那段涂布拉到机尾首检,首检好后用千分尺测量纵向和横向厚度确保巡检作参考厚度15看机头的注意事项:料槽浆料的液面,随时用塞尺清理刀口里的干浆避免浆料在刀口内积累干后影响涂布厚度和敷料密度。
涂胶控制计划做

涂胶控制计划做一、引言在各行业中,涂胶是一项常见的工艺操作。
涂胶不仅可以提高产品的美观度,还可以增强产品的耐水性、耐化学性和耐磨性。
然而,涂胶操作中存在着一些问题,比如涂胶不均匀、涂胶厚度不一致、涂胶流动性差等。
因此,必须采取一些控制措施,保证涂胶的质量稳定性和均匀性。
本文将介绍涂胶控制计划的制定和实施方法。
二、涂胶控制计划的制定1.确定目标和指标在制定涂胶控制计划时,首先需要确定涂胶的质量目标和指标。
具体包括涂胶的均匀性、厚度、流动性、粘度等指标。
这些指标不仅可以为涂胶操作提供参考,还可以为质量检验提供依据。
2.分析涂胶工艺流程涂胶工艺包括涂胶准备、涂布、固化等几个环节。
在制定涂胶控制计划时,需要深入分析涂胶的工艺流程,找出可能存在的问题和风险点。
比如,涂胶准备环节可能存在着涂胶配方不准确、涂胶材料不干净等问题,涂布环节可能存在着涂胶不均匀、涂胶厚度不一致等问题,固化环节可能存在着固化温度不合适、固化时间不足等问题。
3.制定控制方案针对分析出的问题和风险点,需要制定相应的涂胶控制方案。
比如,可以采用自动化涂胶设备代替手工涂胶,提高涂胶的均匀性和一致性;可以引入涂胶配方管理系统,确保涂胶材料的配方准确性和一致性;可以建立涂胶操作规范,规范涂胶的操作流程,减少操作人员的误操作。
4.确定控制措施在确定涂胶控制方案的基础上,需要详细确定具体的控制措施。
比如,在涂胶准备环节,可以要求严格按照涂胶配方进行配料,并实施配方调整记录和管理;在涂布环节,可以要求操作人员定期进行涂胶机清洁和维护,确保涂胶的均匀性和一致性;在固化环节,可以要求建立固化温度和时间的记录表,进行固化参数的监控和调整。
5.确定控制频次为了保证涂胶质量的稳定性,需要确定控制频次。
具体包括涂胶设备的维护频次、涂胶配方的调整频次、涂胶操作规范的审核频次等。
通过合理确定控制频次,可以有效地控制涂胶的质量。
三、涂胶控制计划的实施1.组织实施在确定了涂胶控制计划后,需要对其进行组织实施。
双面胶涂布的工艺控制要点
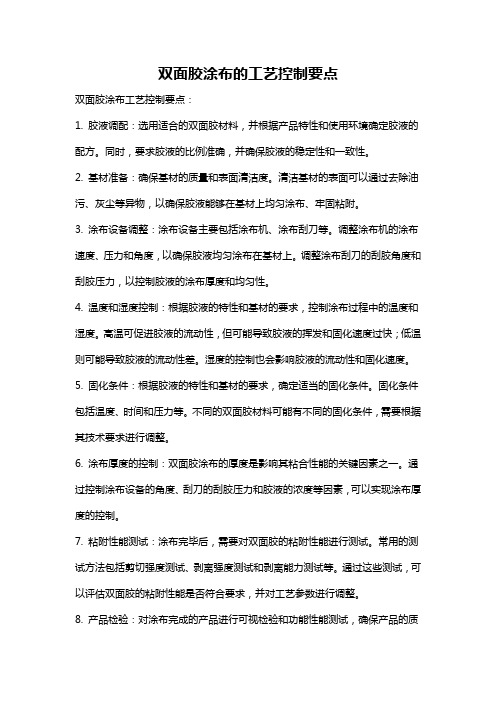
双面胶涂布的工艺控制要点双面胶涂布工艺控制要点:1. 胶液调配:选用适合的双面胶材料,并根据产品特性和使用环境确定胶液的配方。
同时,要求胶液的比例准确,并确保胶液的稳定性和一致性。
2. 基材准备:确保基材的质量和表面清洁度。
清洁基材的表面可以通过去除油污、灰尘等异物,以确保胶液能够在基材上均匀涂布、牢固粘附。
3. 涂布设备调整:涂布设备主要包括涂布机、涂布刮刀等。
调整涂布机的涂布速度、压力和角度,以确保胶液均匀涂布在基材上。
调整涂布刮刀的刮胶角度和刮胶压力,以控制胶液的涂布厚度和均匀性。
4. 温度和湿度控制:根据胶液的特性和基材的要求,控制涂布过程中的温度和湿度。
高温可促进胶液的流动性,但可能导致胶液的挥发和固化速度过快;低温则可能导致胶液的流动性差。
湿度的控制也会影响胶液的流动性和固化速度。
5. 固化条件:根据胶液的特性和基材的要求,确定适当的固化条件。
固化条件包括温度、时间和压力等。
不同的双面胶材料可能有不同的固化条件,需要根据其技术要求进行调整。
6. 涂布厚度的控制:双面胶涂布的厚度是影响其粘合性能的关键因素之一。
通过控制涂布设备的角度、刮刀的刮胶压力和胶液的浓度等因素,可以实现涂布厚度的控制。
7. 粘附性能测试:涂布完毕后,需要对双面胶的粘附性能进行测试。
常用的测试方法包括剪切强度测试、剥离强度测试和剥离能力测试等。
通过这些测试,可以评估双面胶的粘附性能是否符合要求,并对工艺参数进行调整。
8. 产品检验:对涂布完成的产品进行可视检验和功能性能测试,确保产品的质量和稳定性。
根据产品的使用情况和要求,可以对产品的粘附性能、耐温性、耐候性等进行全面的测试。
9. 工艺记录:在涂布过程中,需要及时记录关键参数,如涂布速度、涂布厚度、温度等。
这些记录可以用于工艺的优化和问题的排查,有助于提高生产效率和产品质量。
10. 不断改进:根据生产中的实际情况,及时总结经验教训,提出改进方案,不断优化双面胶涂布的工艺流程和控制方法,以提高生产效率和产品质量。
双面胶涂布的工艺控制要点
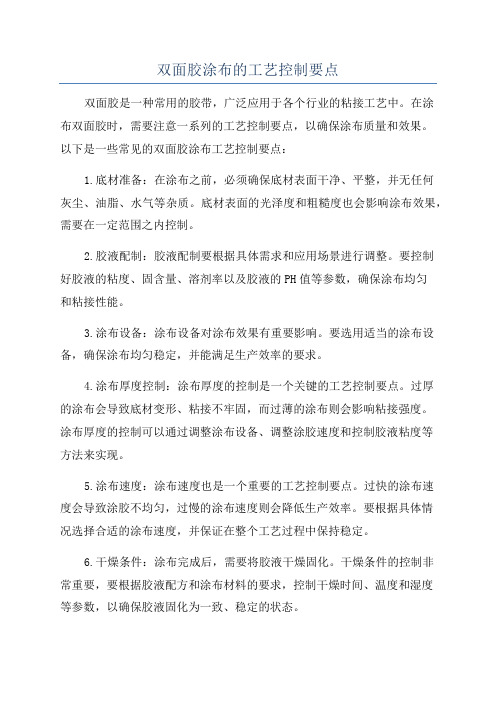
双面胶涂布的工艺控制要点双面胶是一种常用的胶带,广泛应用于各个行业的粘接工艺中。
在涂布双面胶时,需要注意一系列的工艺控制要点,以确保涂布质量和效果。
以下是一些常见的双面胶涂布工艺控制要点:1.底材准备:在涂布之前,必须确保底材表面干净、平整,并无任何灰尘、油脂、水气等杂质。
底材表面的光泽度和粗糙度也会影响涂布效果,需要在一定范围之内控制。
2.胶液配制:胶液配制要根据具体需求和应用场景进行调整。
要控制好胶液的粘度、固含量、溶剂率以及胶液的PH值等参数,确保涂布均匀和粘接性能。
3.涂布设备:涂布设备对涂布效果有重要影响。
要选用适当的涂布设备,确保涂布均匀稳定,并能满足生产效率的要求。
4.涂布厚度控制:涂布厚度的控制是一个关键的工艺控制要点。
过厚的涂布会导致底材变形、粘接不牢固,而过薄的涂布则会影响粘接强度。
涂布厚度的控制可以通过调整涂布设备、调整涂胶速度和控制胶液粘度等方法来实现。
5.涂布速度:涂布速度也是一个重要的工艺控制要点。
过快的涂布速度会导致涂胶不均匀,过慢的涂布速度则会降低生产效率。
要根据具体情况选择合适的涂布速度,并保证在整个工艺过程中保持稳定。
6.干燥条件:涂布完成后,需要将胶液干燥固化。
干燥条件的控制非常重要,要根据胶液配方和涂布材料的要求,控制干燥时间、温度和湿度等参数,以确保胶液固化为一致、稳定的状态。
7.质量检验:在涂布过程中,要设置必要的质量检验措施,及时发现和解决涂布质量问题。
质量检验的手段可以包括目测、检测仪器和实验室分析等。
8.工艺记录和调整:在涂布的过程中,要做好全面的记录,包括涂布设备的参数、涂布材料的配方、实际涂布厚度和质量检验结果等。
这些记录可以用于工艺调整和问题排查。
总之,双面胶涂布的工艺控制要点很多,包括底材准备、胶液配制、涂布设备、涂布厚度控制、涂布速度、干燥条件、质量检验以及工艺记录和调整等。
通过对这些要点的控制,可以提高涂布质量和效率,确保粘接性能和产品质量。
双面胶涂布的工艺控制要点

双面胶涂布的工艺控制要点
双面胶涂布的工艺控制要点包括以下几个方面:
1. 胶涂薄度控制:控制双面胶涂布的薄度是确保粘接质量的关键。
需要根据具体应用需求,选择合适的涂布设备,控制涂布速度和胶液流量,确保胶液均匀地分布在胶布上,避免出现厚度不均匀的情况。
2. 粘度控制:胶液的粘度对于涂布的均匀性有很大影响。
需要通过调整胶液的成分配比,控制胶液的粘度,确保胶液在涂布过程中能够顺利流动,并且不会在胶布表面产生滴落现象。
3. 表面张力控制:双面胶涂布前需要确保胶布表面的清洁度和适度的表面张力。
通过对胶布进行表面处理,例如使用特殊的涂布刷头或者高压空气喷雾进行清洁,可以提高胶布表面的张力,使胶液更好地附着在胶布上。
4. 涂布压力控制:涂布过程中的压力对于胶液的均匀分布起着重要作用。
需要通过调整涂布辊的压力或者加装压力控制装置,确保胶液在涂布过程中能够均匀地分布在胶布上。
5. 温度控制:涂布温度对于胶液的流动性和干燥速度有一定影响。
需要根据具体胶液的特性,控制涂布环境中的温度,确保胶液在涂布过程中流动性良好,并且能够在适当的时间内干燥。
6. 涂布速度控制:涂布速度对于胶液的均匀性和干燥效果有影响。
需要控制涂布机械设备的运行速度,确保胶液在涂布过程中能够均匀地分布在胶布上,并且能够在适当的时间内干燥。
通过以上的工艺控制要点,可以确保双面胶涂布的质量和性能,达到预期的效果。
同时,还可以根据具体应用需求进行细化调整和优化。
pvc双面胶工艺流程

pvc双面胶工艺流程
PVC双面胶是一种常用的胶粘剂,可以用于固定和粘合多种
材料,如纸张、塑料、金属等。
以下是一份PVC双面胶的工
艺流程。
1. 原料准备:首先要准备PVC树脂和增塑剂,它们是制作
PVC双面胶的主要成分。
根据不同的需求,还可以添加填充剂、增粘剂和稳定剂等辅助材料。
2. 混合:将PVC树脂和增塑剂按照一定比例投入混合机中进
行混合。
混合的目的是使树脂和增塑剂充分均匀地混合在一起,形成胶体状的物质。
3. 加热:将混合好的物质进行加热,一般采用加热槽或者加热管进行加热。
加热的温度和时间是根据原料的特性和工艺要求来确定的,一般在80℃到120℃之间。
4. 涂布:将加热好的物质通过涂布机进行涂布。
涂布机是一种专用的设备,可以将物质均匀地涂布到基材上。
在涂布之前,要先调整好涂布机的参数,如涂布速度、压力等。
5. 干燥:涂布完后的双面胶需要进行干燥。
一般使用烘箱进行干燥,温度和时间根据涂布的厚度和涂布的速度来确定。
6. 切割:干燥后的双面胶需要进行切割。
根据需要,可以将双面胶切割成不同的尺寸和形状,一般使用切割机进行切割。
7. 包装:切割好的双面胶需要进行包装。
一般采用纸盒或塑料袋进行包装,以保护双面胶免受外界的影响。
以上就是PVC双面胶的工艺流程。
通过以上的步骤,原料经过混合、加热、涂布、干燥、切割和包装等过程,最终制成PVC双面胶。
这种胶粘剂具有粘性强、粘接牢固、耐高温、耐油脂等特点,广泛应用于家电、电子、广告、建筑等领域。
双面胶生产执行标准
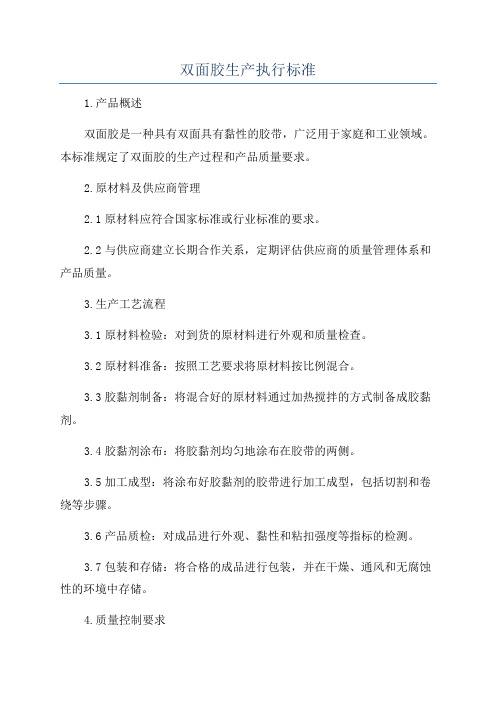
双面胶生产执行标准1.产品概述双面胶是一种具有双面具有黏性的胶带,广泛用于家庭和工业领域。
本标准规定了双面胶的生产过程和产品质量要求。
2.原材料及供应商管理2.1原材料应符合国家标准或行业标准的要求。
2.2与供应商建立长期合作关系,定期评估供应商的质量管理体系和产品质量。
3.生产工艺流程3.1原材料检验:对到货的原材料进行外观和质量检查。
3.2原材料准备:按照工艺要求将原材料按比例混合。
3.3胶黏剂制备:将混合好的原材料通过加热搅拌的方式制备成胶黏剂。
3.4胶黏剂涂布:将胶黏剂均匀地涂布在胶带的两侧。
3.5加工成型:将涂布好胶黏剂的胶带进行加工成型,包括切割和卷绕等步骤。
3.6产品质检:对成品进行外观、黏性和粘扣强度等指标的检测。
3.7包装和存储:将合格的成品进行包装,并在干燥、通风和无腐蚀性的环境中存储。
4.质量控制要求4.1原材料检验要求:对到货原材料进行外观和质量检查,确保原材料的质量符合要求。
4.2胶黏剂制备要求:按照工艺要求将原材料制备成胶黏剂,确保胶黏剂的黏度、粘度和干燥时间等指标符合要求。
4.3胶黏剂涂布要求:确保胶黏剂均匀地涂布在胶带的两侧,无滴落和气泡等缺陷。
4.4产品质检要求:对成品进行外观、黏性和粘扣强度等指标的检测,确保产品质量符合要求。
4.5包装和存储要求:将合格的成品进行包装,并在干燥、通风和无腐蚀性的环境中存储,以防止产品质量的变化。
5.设备维护5.1定期对生产设备进行检修和维护,确保设备的正常运转。
5.2对设备进行清洁和消毒,以防止产品受到污染。
6.不良品处理6.1不良品应在发现后立即停产,排除不良原因后方可继续生产。
6.2不良品应进行分类和记录,并进行相应的处罚和整改。
6.3对不良品的原因进行分析和改进,以预防和避免不良品的发生。
7.提交样品和报告7.1定期向技术部门提交样品和测试报告,以检验产品的质量。
7.2根据客户需求,提供符合其需求的产品样本和报告。
8.培训和宣传8.1定期组织员工参加培训,提升员工对生产标准和质量控制要求的认识和理解。
双面胶涂布的工艺控制要点

双面胶涂布的工艺控制要点双面胶涂布工艺控制要点说明1.涂布方式:转涂:剥离纸上胶经烘箱干燥后,与覆合材料贴合,使胶转移到覆合材料。
适用于双面胶带、标签类单面胶带和发泡体类基材胶带等。
特点:①胶膜厚度均一,胶带总厚度取决于覆合材的厚度偏差;②成品胶带或过程中需使用剥离纸。
③使用剥离纸时烘箱最高温度能控制到120°C。
直涂:胶粘剂直接涂在基材上卷取而成,也称自背面卷取。
适宜包装胶带、再剥离型胶带。
特点:①胶易渗入到基材的内部,密着性好。
②胶带总厚度一致,材料有偏差时,胶层厚度变化正好呈反方向。
③干燥速度和温度取决于基材的种类。
2.逗号轴刮胶器:优点:①兼有刃刮刀涂布器和辊刮刀涂布器的特点。
②剪切应力比刃刮刀涂布器小;③能涂布高粘度胶粘剂;④涂布面光滑。
缺点:①刀口易被颗粒物堵塞;②胶层内气泡不易消除。
ú注意点:刀口角度调节是否合理,直接影响到涂胶面的光滑度,透明胶带生产时如出现纵向胶痕,则说明角度未调整到理想状态。
所以操作时确认刀口是否到位。
3.干燥过程及原理:干燥是指胶粘剂涂布于基材上,以一定的速度使胶粘剂中水分、溶剂挥发得到干燥胶膜。
干燥过程是生产胶带的重要环节,对产品质量影响很大。
干燥过程中热量和物质同时在变化,最初的干燥阶段主要是热量不断从空气传入胶粘剂中,使溶剂不断从胶层内部向表面扩散,在表面达到饱和状态,这段称为恒率干燥。
物质的移动速度取决于传递到胶粘剂中热量多少。
溶剂在表面汽化后,干燥进入减率阶段,胶粘剂表面温度在短时间内上升,并进入更高温度的烘箱,底层溶剂逐步通过表面胶膜向外扩散,如初期温度偏高,表层胶膜过早变硬,则会影响内部溶剂蒸气的挥发,当温度高于溶剂的沸点后,胶层内溶剂气体会出现膨胀而出现发泡问题,最终影响胶层的内聚强度,所以经常性要求监视胶面是否有发泡现象。
同时确认胶的气味是否过重,从另一面来说在检验涂胶层的厚度是否正常和干燥效果是否充分。
干燥速度和干燥时间变化趋势(图示),压敏胶涂布后未进入烘箱溶剂已开始挥发,由于挥发吸热使胶层的表面温度降低,因而挥发速度也下降,为图示中AB段曲线。
双面胶使用工艺

双面胶的使用工艺有以下几个步骤:
准备:首先要准备好需要使用双面胶粘接的材料,确保表面干燥清洁,无油污和灰尘等杂质。
切割:根据需要,将双面胶割成适当尺寸的大小。
把双面胶粘在其中一个材料上。
压缩:将粘有双面胶的材料和另一个材料压在一起。
调整位置:如果材料在压缩过程中移位了,需要在完成粘接之前及时调整位置。
压实:用适当的压力压实粘合面,确保双面胶完全贴合两个材料。
固化:留给双面胶充分的固化时间,这样才能实现最佳的粘合效果。
总之,使用双面胶时需要注意材料的表面清洁和干燥,确保粘合的位置和方向准确,以及固化的时间。
不同的材料和使用环境可能需要不同类型的双面胶,因此应根据需要选择适合的双面胶产品。
双面涂布工艺优化方案
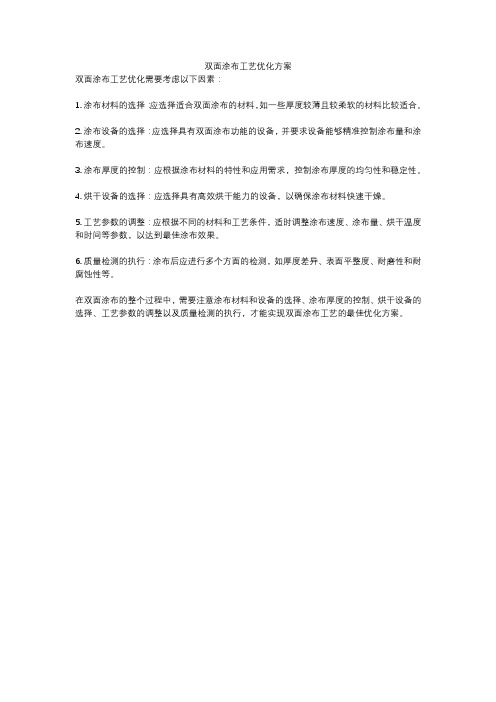
双面涂布工艺优化方案
双面涂布工艺优化需要考虑以下因素:
1. 涂布材料的选择:应选择适合双面涂布的材料,如一些厚度较薄且较柔软的材料比较适合。
2. 涂布设备的选择:应选择具有双面涂布功能的设备,并要求设备能够精准控制涂布量和涂布速度。
3. 涂布厚度的控制:应根据涂布材料的特性和应用需求,控制涂布厚度的均匀性和稳定性。
4. 烘干设备的选择:应选择具有高效烘干能力的设备,以确保涂布材料快速干燥。
5. 工艺参数的调整:应根据不同的材料和工艺条件,适时调整涂布速度、涂布量、烘干温度和时间等参数,以达到最佳涂布效果。
6. 质量检测的执行:涂布后应进行多个方面的检测,如厚度差异、表面平整度、耐磨性和耐腐蚀性等。
在双面涂布的整个过程中,需要注意涂布材料和设备的选择、涂布厚度的控制、烘干设备的选择、工艺参数的调整以及质量检测的执行,才能实现双面涂布工艺的最佳优化方案。
双面胶生产工艺
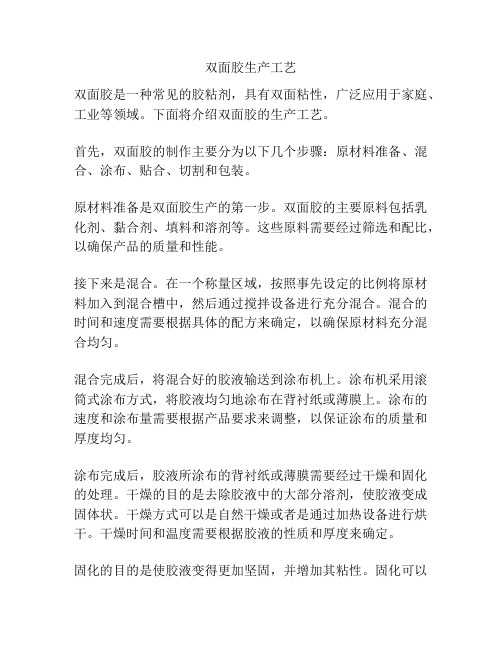
双面胶生产工艺双面胶是一种常见的胶粘剂,具有双面粘性,广泛应用于家庭、工业等领域。
下面将介绍双面胶的生产工艺。
首先,双面胶的制作主要分为以下几个步骤:原材料准备、混合、涂布、贴合、切割和包装。
原材料准备是双面胶生产的第一步。
双面胶的主要原料包括乳化剂、黏合剂、填料和溶剂等。
这些原料需要经过筛选和配比,以确保产品的质量和性能。
接下来是混合。
在一个称量区域,按照事先设定的比例将原材料加入到混合槽中,然后通过搅拌设备进行充分混合。
混合的时间和速度需要根据具体的配方来确定,以确保原材料充分混合均匀。
混合完成后,将混合好的胶液输送到涂布机上。
涂布机采用滚筒式涂布方式,将胶液均匀地涂布在背衬纸或薄膜上。
涂布的速度和涂布量需要根据产品要求来调整,以保证涂布的质量和厚度均匀。
涂布完成后,胶液所涂布的背衬纸或薄膜需要经过干燥和固化的处理。
干燥的目的是去除胶液中的大部分溶剂,使胶液变成固体状。
干燥方式可以是自然干燥或者是通过加热设备进行烘干。
干燥时间和温度需要根据胶液的性质和厚度来确定。
固化的目的是使胶液变得更加坚固,并增加其粘性。
固化可以通过自然固化或者是通过加热设备进行加热固化。
固化的时间和温度也需要根据具体产品的要求来确定,以保证胶液的质量和性能。
固化完成后,双面胶需要经过切割和包装的处理。
切割的目的是将大片的双面胶切割成所需要的尺寸。
切割可以采用手工切割或者是自动切割设备。
切割完成后,将双面胶进行包装,可以根据不同的需求选择合适的包装方式,如卷装、片装、散装等。
总之,双面胶的生产工艺包括原材料准备、混合、涂布、干燥、固化、切割和包装。
每个步骤都需要严格控制和操作,以确保双面胶的质量和性能符合要求。
双面胶的制作需要科学、高效的生产工艺,以满足市场和消费者的需求。
涂胶工艺中的注意事项如下

涂胶工艺中的注意事项如下
①涂胶量和涂覆遍数因胶粘剂不同而异应按规定说明进行像环氧胶只涂刷一遍而多数的溶液胶粘剂都要涂覆两遍甚至三遍另外对于多孔材料的粘接也要适当地增加涂胶量和涂胶遍数。
多遍涂胶时一定要待前遍溶剂基本挥发之后再涂一遍
而且第一层要尽量薄。
②控制胶层厚度涂胶量的多少能够控制胶层的厚度胶层的厚度与粘接强度有密度关系。
一般的规律是粘接强度随胶层厚度的减小而有所增加胶层越薄产生缺胶的可能性越小因此产生的内应力也小则粘接强度就越高。
但是胶层的厚度小于一定值之后由于不能形成连续的胶层粘接强度反而下降受剥离力时厚度大些剥离强度高些。
不同类型的胶粘剂适宜的胶层厚度不同一般无机胶粘剂为0、1~0、2mm有机胶粘剂为0、3~0、5mm。
③胶层均匀胶层中含有气泡或缺胶使粘接头产生薄弱环节严重影响粘接头的粘接强度涂胶时应注意胶层均匀尤其是涂覆粘度较大的糊状胶粘剂要防止由于不均匀而在胶层中产生气泡的现象。
④胶层中溶剂应充分挥发在胶层中残留溶剂会严重损害粘接接头的性能。
对金属的粘接接头尤为重要为使胶层中的溶剂充
分挥发在涂覆含溶剂的胶粘剂时应分次进行。
晾置切勿过度尤其是最后一次晾置不然粘度太大无法胶合晾置过程中应避免胶面受到空气中灰尘的污染。
⑤适时粘合对于不含溶剂的胶粘剂在涂胶后可立即进行胶合对于含有溶剂的胶粘剂涂胶经过晾置的粘接表面再紧贴合在一起注意对准位置。
对于液态无溶剂胶粘剂胶合时最好来回错动几次以增加接触排除空气。
复面纸上胶安全操作规程
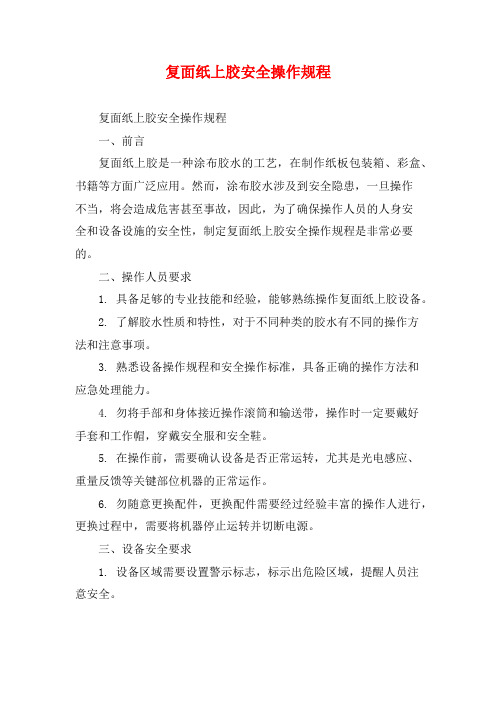
复面纸上胶安全操作规程复面纸上胶安全操作规程一、前言复面纸上胶是一种涂布胶水的工艺,在制作纸板包装箱、彩盒、书籍等方面广泛应用。
然而,涂布胶水涉及到安全隐患,一旦操作不当,将会造成危害甚至事故,因此,为了确保操作人员的人身安全和设备设施的安全性,制定复面纸上胶安全操作规程是非常必要的。
二、操作人员要求1. 具备足够的专业技能和经验,能够熟练操作复面纸上胶设备。
2. 了解胶水性质和特性,对于不同种类的胶水有不同的操作方法和注意事项。
3. 熟悉设备操作规程和安全操作标准,具备正确的操作方法和应急处理能力。
4. 勿将手部和身体接近操作滚筒和输送带,操作时一定要戴好手套和工作帽,穿戴安全服和安全鞋。
5. 在操作前,需要确认设备是否正常运转,尤其是光电感应、重量反馈等关键部位机器的正常运作。
6. 勿随意更换配件,更换配件需要经过经验丰富的操作人进行,更换过程中,需要将机器停止运转并切断电源。
三、设备安全要求1. 设备区域需要设置警示标志,标示出危险区域,提醒人员注意安全。
2. 设备移动时需要坚持“一机一明策略”,防止设备撞击或者碰撞造成损失和人员伤亡。
3. 设备的电气线路和主要部件应全部切断,禁止任何人未授权擅自接触设备。
4. 定期保养设备,确保设备每天正常运转,避免设备故障和事故。
5. 在使用过程中,设备应避免重量负荷过高、长时间连续运转等不正常运转状况。
四、现场安全要求1. 现场要保持清洁卫生,尤其避免纸屑和胶水的聚集。
2. 吸风口的气密密封要保证,以免将切碎的纸屑、胶水和其它异物吸入空气造成污染和危害人体健康。
3. 不得将带电工具和其它杂物放在机器上。
4. 务必保持操作人员的集中注意力和正确操作方法。
操作人员坚决避免和咳嗽、流鼻涕等症状严重的工友接触。
5. 操作员必须保持机器每个部位的干燥和清洁。
尤其要定期检查滚筒及配件,必要时用抹布轻轻擦拭。
六、设备运行时的注意事项1. 在设备运行时不得打开机器保护罩,不得将手插入机器内部。
- 1、下载文档前请自行甄别文档内容的完整性,平台不提供额外的编辑、内容补充、找答案等附加服务。
- 2、"仅部分预览"的文档,不可在线预览部分如存在完整性等问题,可反馈申请退款(可完整预览的文档不适用该条件!)。
- 3、如文档侵犯您的权益,请联系客服反馈,我们会尽快为您处理(人工客服工作时间:9:00-18:30)。
双面胶涂布工艺控制要点说明1.涂布方式:»转涂:剥离纸上胶经烘箱干燥后,与覆合材料贴合,使胶转移到覆合材料。
适用于双面胶带、标签类单面胶带和发泡体类基材胶带等。
特点:①胶膜厚度均一,胶带总厚度取决于覆合材的厚度偏差;②成品胶带或过程中需使用剥离纸。
③使用剥离纸时烘箱最高温度能控制到120°C。
»直涂:胶粘剂直接涂在基材上卷取而成,也称自背面卷取。
适宜包装胶带、再剥离型胶带。
特点:①胶易渗入到基材的内部,密着性好。
②胶带总厚度一致,材料有偏差时,胶层厚度变化正好呈反方向。
③干燥速度和温度取决于基材的种类。
2.逗号轴刮胶器:优点:①兼有刃刮刀涂布器和辊刮刀涂布器的特点。
②剪切应力比刃刮刀涂布器小;③能涂布高粘度胶粘剂;④涂布面光滑。
缺点:①刀口易被颗粒物堵塞;②胶层内气泡不易消除。
Ú注意点:刀口角度调节是否合理,直接影响到涂胶面的光滑度,透明胶带生产时如出现纵向胶痕,则说明角度未调整到理想状态。
所以操作时确认刀口是否到位。
3.干燥过程及原理:干燥是指胶粘剂涂布于基材上,以一定的速度使胶粘剂中水分、溶剂挥发得到干燥胶膜。
干燥过程是生产胶带的重要环节,对产品质量影响很大。
干燥过程中热量和物质同时在变化,最初的干燥阶段主要是热量不断从空气传入胶粘剂中,使溶剂不断从胶层内部向表面扩散,在表面达到饱和状态,这段称为恒率干燥。
物质的移动速度取决于传递到胶粘剂中热量多少。
溶剂在表面汽化后,干燥进入减率阶段,胶粘剂表面温度在短时间内上升,并进入更高温度的烘箱,底层溶剂逐步通过表面胶膜向外扩散,如初期温度偏高,表层胶膜过早变硬,则会影响内部溶剂蒸气的挥发,当温度高于溶剂的沸点后,胶层内溶剂气体会出现膨胀而出现发泡问题,最终影响胶层的内聚强度,所以经常性要求监视胶面是否有发泡现象。
同时确认胶的气味是否过重,从另一面来说在检验涂胶层的厚度是否正常和干燥效果是否充分。
干燥速度和干燥时间变化趋势(图示),压敏胶涂布后未进入烘箱溶剂已开始挥发,由于挥发吸热使胶层的表面温度降低,因而挥发速度也下降,为图示中AB段曲线。
当胶粘剂进入烘箱后,溶剂挥发所吸收的热量从外部来的热量得到补充,在热量达到平衡时,胶层的表面温度以及溶剂的挥发速度保持恒定,为BC段曲线,随着胶层中溶剂浓度降低,溶剂从胶层内部向表面扩散的速度也相应降低,当扩散速度小于挥发速度时,溶剂的挥发速度就开始下降。
此时外部传导的热量超过溶剂挥发所吸收的热量,胶层表面温度则开始上升,为CD段曲线。
胶层的表面温度上升到接近烘箱的温度,干燥速度完全受到溶剂在胶层中扩散速度的制约而越来越小,为DE段曲线,这部分占据大部分干燥时间。
加速干燥过程必须缩短DE部分时间,而关键的问题是如何提高溶剂在胶层中的挥发速度。
一般对No.1烘箱设定温度偏低60~70°C,延长恒率干燥时间,后面烘箱温度逐步升高,可增加后期干燥速度。
残留溶剂量过多会造成胶带初粘力大,胶带老化后性能容易变化,同时会加重剥离纸剥离性,对使用来说溶剂量过多会影响耐溶剂性差的被粘物或印刷层,使用中气味过重对作业环境带来影响。
我公司生产的A-500胶带残留溶剂量约为1.5%。
胶粘剂干燥效果主要取决于热量的传递,为达到足够的热量供给必须保证烘箱热风的循环,所以有必要对烘箱的过滤网进行定期检查和及时清理。
干燥速度和干燥时间关系例:对LT-100胶带生产时产生的网格痕迹残留问题进行说明。
涂布PET基材直接与输送带接触,而输送带为网格编织结构,进入烘箱后输送带吸收热量,热量传导给底层胶粘剂,网格凸起部分先促使胶层溶剂挥发而变硬,与凹陷部分形成干燥速度差距;另风压过大和张力过大也是形成此问题的因素。
♣对废气产生量和供给空气计算进行简单介绍。
溶剂一般物理性能:分子量蒸发密度比重蒸汽压沸点°C爆炸限界容量EtAc 88 3.04 0.9 55 77 2.2~11.4 To 92 3.1 0.87 22 110.6 1.27~7.0 烘箱内增发溶剂量过多时,静电产生时可能会出现爆炸,所以从安全方面考虑,对烘箱设定废气浓度极限值,一般以爆发限界容量的1/4左右。
例:幅宽为1m的基材上涂胶20g/m2(干胶)、固含量为40%,则溶剂约有30g/m2,以60m/min 的速度运转,1分钟内蒸发的溶剂为30g/m2×1m×60m/min=1800g/min。
溶剂为气体时,1摩尔气体为22.4L,如溶剂为To时,分子量为92g废气产生量:22.4L×1800g/min÷92g=438.3L/min=0.438m3/min供给空气量:0.438m3/min÷(0.0127×0.25)=138 m3/min判定溶剂挥发情况:I.通过高温实验测试胶带中溶剂含量;II.观察烘箱出口侧胶层气味和发泡现象;III.通过对No.1烘箱废气量分析挥发量是否合理。
4.泡沫类材料贴合间隙选定依据:① 控制泡沫收缩率:泡沫类材料一般厚度较厚,而根据泡沫种类的不同,材料变形程度和延伸性不一样,涂胶时一般在贴合装置部位采用压合的方法,如贴合间隙小于材料的厚度,运转时受到挤压后造成材料变形拉长,而剥离纸与泡沫覆合的产品,经冲切加工后,在实际使用时就会出现收缩的问题,最终造成尺寸与图纸不符而影响产品使用,所以生产的泡沫类胶粘制品要求严格控制产品收缩率。
② 控制胶渗入量:泡沫材料表面为泡孔结构,胶粘剂容易渗入到泡沫孔内,如渗入量过多会降低与被粘物的粘接强度,相反如未渗入到泡沫中,则与被粘体贴合后会影响曲面性能等问题,所以一般控制渗入量以用手粘合后胶不被带起为准。
现生产的泡沫胶带以压缩变形小的PE(聚乙烯)泡沫为例,从胶带外观(剥离纸起皱)方面和综合性能考虑选择贴合间隙时略低于材料厚度较合理,材料收缩能控制到0.6%以下(具体参照下表)。
压缩变形大的PU(聚氨酯)泡沫,一般贴合间隙选择30%较为合理。
为减轻胶带起皱问题,注意贴合角度的调整。
5.增湿目的:剥离纸经烘箱过程中水分挥发而破坏平衡,采用增湿方法进行调节水分,可避免在后工程出现剥离纸强度不足的问题;降低静电的产生量;防止胶带卷曲而造成产品品质低下。
但增湿也会影响胶带外观,如铜箔胶带的铜箔与背面剥离纸长时间接触,剥离纸的水分(尤其在高温环境)会造成铜箔氧化发黑问题。
卷曲现象分析:①吸湿和水分挥发胶粘制品一般需符合冲切、印刷等再加工要求,要求胶带的尺寸变化小,在不同的环境(温度、湿度)适应性强,所以不同季节生产的产品尺寸稳定性、胶带平整度偏差较大,在生产时必须注意各个环节的控制。
采用剥离纸转涂方法涂胶时,覆合材料为薄膜时,尤其会产生胶带卷曲问题,产生的原因是水分的挥发和吸湿引起,达到平衡的产品吸湿量过多时,剥离纸受膨胀后会出现产品卷取和剥离纸拱起问题。
②贴合压力. 贴合压力过大也是产生卷曲的一个重要因素,如PET双面胶带贴合压力超过 3.5 Kg/cm2就会出现卷曲问题,但厚PET膜如不提高压力,对贴合会带来一定影响,如过高会影响成品率。
③张力No.2卷出张力的合理调节对解决卷曲也较重要,一般在贴合的初期割取圆状小样,确认张力是否适宜,PVC电池膜胶带尤其须注意PVC膜反翘性。
下降贴合前张力值和下降最后烘箱的温度也能改善卷曲的问题。
7.双面胶带剥离方式:双面胶带第二工程生产时,通过剥离纸(工程纸)涂胶后转移到第一工程品后再剥离,为达到胶面的光滑性和不出现横向起皱,需考虑采用哪种通纸路线更合理,当第一工程面剥离性比较小时或胶层较薄易变形时,采用工程纸方向剥离时,尤其No.2卷取张力过大情况下,胶层易被拉起而进入空气,所以采用胶带方向剥离更合理,并且降低No.2卷取张力能改善胶层被拉起的问题,如生产泡棉双面胶带为避免工程纸起皱,也可采用预先把胶带往下剥离的方法。
但一般性双面胶带采用工程纸方向剥离较易控制。
8.卷取说明:卷取部设计需考虑张力控制,卷取时基材的张力随卷取直径变化而变化,呈逐步下降趋势,一般采用斜率来调节,以减少张力下降趋势,可克服卷取过松时空气的进入和过紧时跑卷的问题,卷取部设计时采用特殊的驱动装置和压合装置。
当生产单层剥离纸的双面胶带和PE保护膜胶带时,如卷入空气则会造成胶层表面有花纹状痕迹,保护膜胶带外观上如存在气泡痕迹,则会限制产品的应用范围(外观要求高产品不能使用),而双面胶带卷入的空气(空气中有水分)会影响L-45类硬化剂交联效果,会造成产品持粘力性能下降问题(尤其是空气湿度过大时),所以在卷取时最好使用压紧轴贴合消除空气卷入。
♣例:卷取直径例幅宽为1000mm的基材以60m/min的速度卷取,设定值为30Kg,纸管为Φ100mm,最后卷取直径为Φ600mm。
力矩(M):初 30Kg×0.05m=1.5 Kg⋅m后 30Kg×0.3m=9 Kg⋅m卷取后期力矩相当于初期的6倍。
转速:初期 60m/min÷(3.14×0.1)=191rpm后期 60m/min÷(3.14×0.6)=32rpm9.提高胶与基材密着性方法:上图A表示胶粘剂与基材粘接力,反映胶与基材的密着性情况,A和B值大于C值是理想的状态,特别是再剥离型(低粘性保护膜类)胶带必须达到的要求,如果A值比B或C 小的时候,剥离后会出现胶残留到被粘物上。
为满足A大于B要求,可考虑采用以下方法:①.采用底涂剂处理;②.电晕处理塑料一般表面能量较低具有惰性,湿润性不好,处理后可提高表面能量来改善接着性和印刷性。
通过电晕放电后,破坏了材料表面分子,变成极性状态,达到表面张力上升。
处理效果取决于放电功率和运转速度。
注意点:I.导电类材料不能处理;II.处理前需测试原来材料的表面张力,并确认处理后变化;III.处理放电功率不能过分大,材料较薄时可能击穿材料;IV.处理时即时消除静电,以避免破坏背面材质。
V.处理效果随放置时间增长会逐渐下降,加工前必须确认表面张力。
③.转涂时贴合前材料表面通过加热轴加温或材料预热。
④.提高最后烘箱温度以提高胶体温度或提高贴合金属轴温度。
10.其它注意点:① 静电一般由摩擦产生,涂布时剥离纸(尤其是薄膜)在连续运转容易产生静电,如积聚到一定量后会出现放电,就有可能破坏剥离纸表面硅层,另胶粘剂为溶剂型,静电产生的电火花是最危险。
解决方法:采取放电的装置(金属引线等);增加环境湿度;及时清理除电装置。
② 有机硅胶粘剂涂布时,必须把烘箱的废气检测器拆除,否则会损坏。
③ 涂布所用的材料基本为卷材,而生产卷材的流水作业中最会出现的问题是在最起初部分、最后部分及材料接头附近,所以对我公司来说,过程控制时尤其要注意此方面问题,最好养成此方面习惯。