丁辛醇工艺技术进展及选择
丁辛醇装置工艺技术比选及技术可获得性分析
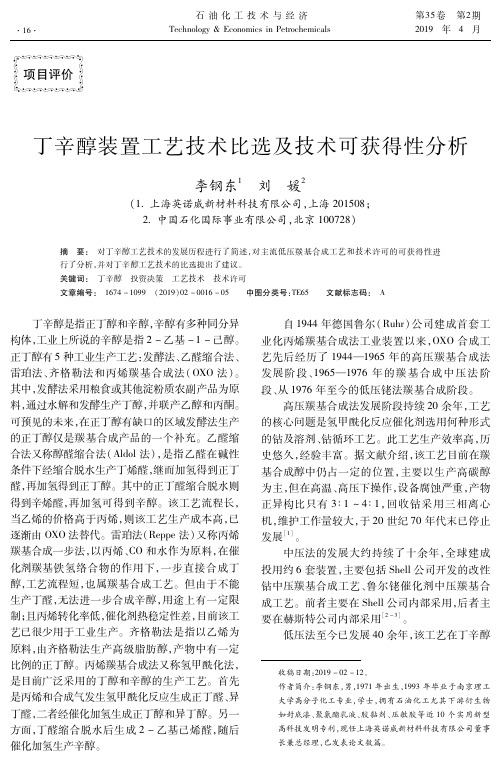
工艺技术及技术可获得性进行分析和比较,为投 资决策者提供决策依据。
1 Davy/Dow工艺技术及许可转让 11 工艺技术
按照羰基合成催化剂的循环方式不同,该技术 先后经历了气相循环工艺和液相循环工艺。前者 是指羰基合成催化剂保留在反应器内,催化剂不随 低碳醛类产物蒸发,从而不需设催化剂回收循环系 统,气相产物经冷凝可分离出醛类,未反应的丙烯、 氢气和一氧化碳等经增压后循环回到反应器;后者 是指羰基合成反应产物和催化剂共同离开反应器, 采用闪蒸和蒸发将催化剂溶液进行分离,从而循环 回到反应器,液相循环工艺于 1984年实现了工业 化[5]。与气相循环工艺相比,液相循环工艺主要是 将两台并联反应器变更为两台串联,提高了反应器 容积利用率,加快了反应速率,同样容积的反应器 能力则提高了 50% ~80%。最近 10年新建装置均 是采用液相循环工艺。
摘 要: 对丁辛醇工艺技术的发展历程进行了简述,对主流低压羰基合成工艺和技术许可的可获得性进 行了分析,并对丁辛醇工艺技术的比选提出了建议。 关键词: 丁辛醇 投资决策 工艺技术 技术许可 文章编号: 1674-1099 (2019)02-0016-05 中图分类号:TE65 文献标志码: A
丁辛醇是指正丁醇和辛醇,辛醇有多种同分异 构体,工业上所说的辛醇是指 2-乙基 -1-己醇。 正丁醇有 5种工业生产工艺:发酵法、乙醛缩合法、 雷珀 法、齐 格 勒 法 和 丙 烯 羰 基 合 成 法 (OXO法 )。 其中,发酵法采用粮食或其他淀粉质农副产品为原 料,通过水解和发酵生产丁醇,并联产乙醇和丙酮。 可预见的未来,在正丁醇有缺口的区域发酵法生产 的正丁醇仅是羰基合成产品的一个补充。乙醛缩 合法又称醇醛缩合法(Aldol法),是指乙醛在碱性 条件下经缩合脱水生产丁烯醛,继而加氢得到正丁 醛,再加氢得到正丁醇。其中的正丁醛缩合脱水则 得到辛烯醛,再加氢可得到辛醇。该工艺流程长, 当乙烯的价格高于丙烯,则该工艺生产成本高,已 逐渐由 OXO法替代。雷珀法(Reppe法)又称丙烯 羰基合成一步法,以丙烯、CO和水作为原料,在催 化剂羰基铁氢络合物的作用下,一步直接合成丁 醇,工艺流程短,也属羰基合成工艺。但由于不能 生产丁醛,无法进一步合成辛醇,用途上有一定限 制;且丙烯转化率低,催化剂热稳定性差,目前该工 艺已很少用于工业生产。齐格勒法是指以乙烯为 原料,由齐格勒法生产高级脂肪醇,产物中有一定 比例的正丁醇。丙烯羰基合成法又称氢甲酰化法, 是目前广泛采用的丁醇和辛醇的生产工艺。首先 是丙烯和合成气发生氢甲酰化反应生成正丁醛、异 丁醛,二者经催化加氢生成正丁醇和异丁醇。另一 方面,丁醛缩合脱水后生成 2-乙基己烯醛,随后 催化加氢生产辛醇。
丁辛醇生产工艺技术研究

丁辛醇生产工艺技术研究丁辛醇是一种重要的有机化工原料,广泛应用于涂料、溶剂、合成橡胶、树脂、塑料等工业中。
它的生产工艺技术研究对于提高产品质量、降低生产成本、减少对环境的污染具有重要意义。
丁辛醇的生产工艺通常采用乙烯与异癸醇经醇酸发酵和醇醚酸化两个步骤进行。
首先,乙烯和异癸醇经过混合、调温后进入乙烯异癸醇醇酸发酵罐,加入催化剂和适量的酸催化剂,在一定温度和压力下进行反应,产生丁醇、辛醇和副产物。
乙烯异癸醇醇酸发酵反应是一个复杂的过程,其速度受到多种因素的影响,如反应温度、压力、酸催化剂的种类和浓度等。
通过对这些因素进行优化调控,可以提高丁辛醇的产率和选择性。
此外,还可以通过改变酸催化剂的种类和浓度,改变反应的速度和产物的比例。
在丁辛醇的生产过程中,酸醚酸化是一个非常重要的步骤。
酸醚酸化是指将丁醇和辛醇与过量的醋酸和浓硫酸反应,产生醋酸丁酯和醋酸辛酯。
该过程需要控制反应的温度、酸碱度和酸催化剂的浓度等条件,以避免副反应的发生。
在丁辛醇的生产过程中,还需要进行脱硫、脱碱、脱水等后续处理工艺,以提高产品的纯度和质量。
在脱硫工艺中,可以采用加氢脱硫、碳酸氢钠洗涤等方法,以去除硫化物的残留。
在脱碱工艺中,可以使用稀酸洗涤的方法,以去除碱性残留物。
在脱水工艺中,可以通过加热、蒸馏等方法,以去除水分。
丁辛醇的生产工艺技术研究还可从原料选择、反应条件优化、催化剂研究、废水处理等方面展开。
通过改进工艺流程、提高产品质量和选择性、降低生产成本和对环境的污染,可以提高丁辛醇的生产效益和竞争力。
总之,丁辛醇的生产工艺技术研究对于工业生产具有重要意义。
通过优化反应条件、改进工艺流程和后续处理方法,可以提高产品质量、降低生产成本、减少对环境的污染。
随着科学技术的不断进步,相信丁辛醇的生产工艺技术还将不断改进和创新,为相关产业的发展做出更大贡献。
丁辛醇生产工艺
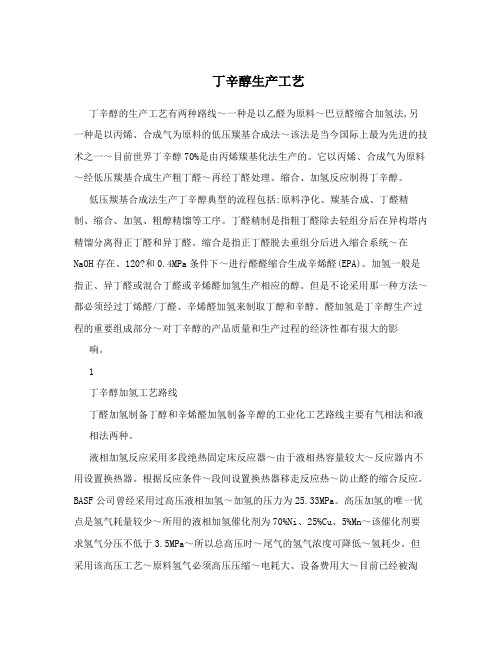
丁辛醇生产工艺丁辛醇的生产工艺有两种路线~一种是以乙醛为原料~巴豆醛缩合加氢法,另一种是以丙烯、合成气为原料的低压羰基合成法~该法是当今国际上最为先进的技术之一~目前世界丁辛醇70%是由丙烯羰基化法生产的。
它以丙烯、合成气为原料~经低压羰基合成生产粗丁醛~再经丁醛处理、缩合、加氢反应制得丁辛醇。
低压羰基合成法生产丁辛醇典型的流程包括:原料净化、羰基合成、丁醛精制、缩合、加氢、粗醇精馏等工序。
丁醛精制是指粗丁醛除去轻组分后在异构塔内精馏分离得正丁醛和异丁醛。
缩合是指正丁醛脱去重组分后进入缩合系统~在NaOH存在、120?和0.4MPa条件下~进行醛醛缩合生成辛烯醛(EPA)。
加氢一般是指正、异丁醛或混合丁醛或辛烯醛加氢生产相应的醇。
但是不论采用那一种方法~都必须经过丁烯醛/丁醛、辛烯醛加氢来制取丁醇和辛醇。
醛加氢是丁辛醇生产过程的重要组成部分~对丁辛醇的产品质量和生产过程的经济性都有很大的影响。
1丁辛醇加氢工艺路线丁醛加氢制备丁醇和辛烯醛加氢制备辛醇的工业化工艺路线主要有气相法和液相法两种。
液相加氢反应采用多段绝热固定床反应器~由于液相热容量较大~反应器内不用设置换热器。
根据反应条件~段间设置换热器移走反应热~防止醛的缩合反应。
BASF公司曾经采用过高压液相加氢~加氢的压力为25.33MPa。
高压加氢的唯一优点是氢气耗量较少~所用的液相加氢催化剂为70%Ni、25%Cu、5%Mn~该催化剂要求氢气分压不低于3.5MPa~所以总高压时~尾气的氢气浓度可降低~氢耗少。
但采用该高压工艺~原料氢气必须高压压缩~电耗大、设备费用大~目前已经被淘汰。
BASF公司和三菱化成工艺中醛的加氢采用中压液相加氢工艺~加氢压力为4.0-5.0MPa~加氢反应器形式采用填充床~反应温度为60-190?。
气相加氢法由于操作压力相对较低~工艺设备简单而被广泛应用。
目前~工业上丁辛醇装置上大多采用铜系催化剂气相加氢工艺。
如U.D.J联合工艺中采用低压气相加氢~压力为0.59-0.69MPa。
丁辛醇的生产工艺与技术路线的选择

丁/辛醇的生产工艺与技术路线的选择2.1 丁辛醇生产方法丁辛醇是随着石油化工、聚氯乙烯材料工业以及羰基合成工业技术的发展而迅速发展起来的。
丁辛醇的工业化生产方法主要有乙醛缩合法、发酵法、齐格勒法和羰基合成法等。
2.1.1乙醛缩合法二战期间,德国开发了乙醛缩合法(Aldo1)法。
……2.1.2发酵法发酵法是粮食或其它淀粉质农副产品,经水解得到发酵液,然后在丙酮-丁醇菌作用下,经发酵制得丁醇、丙酮及乙醇的混合物,通常的比例为……2.1.3齐格勒法齐格勒丁辛醇生产方法是以乙烯为原料,采用齐格勒法生产高级脂肪醇,同时副产丁醇的方法。
2.1.4羰基合成法……2.2 丁辛醇生产工艺技术比较及选择2.2.1 国外丁辛醇生产工艺对比……丁辛醇主要生产工艺的比较见表2.1。
表2.1 丁辛醇主要生产工艺的比较关于丁辛醇生产的几种主要工艺技术方法列表如下。
表2.2 丁辛醇工艺技术方案对比表2.2.2 国外丁辛醇生产工艺选择……2.3 丁辛醇合成工艺技术进展及发展趋势2.3.1 国外丁辛醇合成工艺技术进展丁醇和辛醇是用途广泛的重要精细化工原料,随着生产规模的不断扩大,丁辛醇技术发展重点集中在合成工艺和催化剂的研究和开发上,国外生产商改进丁辛醇合成工艺形成了各具特色的专有技术,引起了业内人士的极大关注。
……2.3.2 国内丁辛醇合成工艺技术进展……2.3.3 国内丁辛醇合成工艺技术发展趋势随着世界经济全球化及规模生产经济最大化,丁辛醇工业发展的重点将集中在催化剂的研究和开发上。
其技术发展趋势是:……2.4 丁辛醇质量指标2.4.1 丁醇质量指标工业正丁醇:执行标准:GB/T 6027/1998,该标准适用于合成法与发酵法生产的工业正丁醇。
要求:外观:透明液体,无可见杂质。
表2.3 正丁醇质量指标项目指标分析方法优等品一等品合格品色度,Hazen单位(铂-钴色号)≤10 15 GB/T3143密度(20℃)g/cm30.809~0.811 0.808~0.812 GB/T4472 沸程(0℃,101.325Kpa)包括(117.7℃),℃≤ 1.0 2.0 3.0 GB/T7534 正丁醇含量,% ≥99.5 99.0 98.0 色谱法硫酸显色试验(铂-钴色号)≤20 40 比色法酸度(以乙酸计),% ≤0.003 0.005 0.01 容量法水分,% ≤0.1 0.2 GB/T6283 蒸发残渣,% ≤0.003 0.005 0.01 重量法2.4.2 辛醇质量指标辛醇:执行标准:GB/T 6818/1993,本标准适用于由丙烯羰基合成法及乙醛缩合法制得的工业辛醇。
25万吨年丁辛醇工艺分析及优化

25万吨/年丁辛醇工艺分析及优化
丁辛醇是重要基本的有机化工原材料,在化工、石油、医药等方面具有非常广泛的用途。
以惠生(南京)化工有限公司年产25万吨丁辛醇装置研究为对象,通过分析比较不同丁辛醇合成工艺及装置的特点和运行要求,选择了 DAVY/DOW 丙烯铑低压羰基合成-液相循环工艺技术,确定了工艺流程,计算该工艺的生产消耗及物料平衡。
根据年产25万吨丁辛醇生产要求,设计了羰基合成反应器,研究了影响羰基合成反应的因素,包括原料杂质、合成气中氢碳比、温度、压力、三苯基膦浓度及铑催化剂失活对羰基合成反应的影响,并提出了相应改善措施,以保证装置安全、稳定、长周期、满负荷、优化运行。
介绍了羰基合成催化剂失活原因,并简单阐述了本装置催化剂回收方式。
丁辛醇生产工艺

丁辛醇生产工艺
丁辛醇的生产工艺有两种路线:
一种是以乙醛为原料,巴豆醛缩合加氢法;
另一种是以丙烯、合成气为原料的低压羰基合成法。
该法是当今国际上最为先进的技术之一,目前世界丁辛醇70%是由丙烯羰基化法生产的。
它以丙烯、合成气为原料,经低压羰基合成生产粗丁醛,再经丁醛处理、缩合、加氢反应制得丁辛醇。
低压羰基合成法生产丁辛醇典型的流程包括:原料净化、羰基合成、丁醛精制、缩合、加氢、粗醇精馏等工序。
丁醛精制是指粗丁醛除去轻组分后在异构塔内精馏分离得正丁醛和异丁醛。
缩合是指正丁醛脱去重组分后进入缩合系统,在NaOH存在、120?和0.4MPa条件下,进行醛醛缩合生成辛烯醛(EPA)。
加氢一般是指正、异丁醛或混合丁醛或辛烯醛加氢生产相应的醇。
但是不论采用那一种方法,都必须经过丁烯醛/丁醛、辛烯醛加氢来制取丁醇和辛醇。
醛加氢是丁辛醇生产过程的重要组成部分,对丁辛醇的产品质量和生产过程的经济性都有很大的影响。
丁辛醇生产工艺
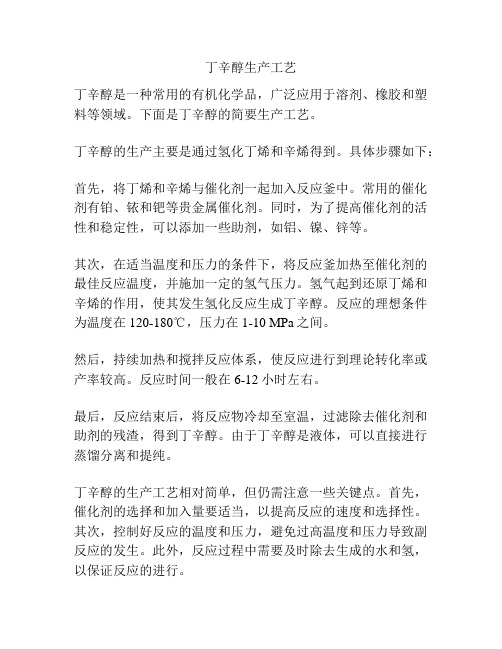
丁辛醇生产工艺
丁辛醇是一种常用的有机化学品,广泛应用于溶剂、橡胶和塑料等领域。
下面是丁辛醇的简要生产工艺。
丁辛醇的生产主要是通过氢化丁烯和辛烯得到。
具体步骤如下:
首先,将丁烯和辛烯与催化剂一起加入反应釜中。
常用的催化剂有铂、铱和钯等贵金属催化剂。
同时,为了提高催化剂的活性和稳定性,可以添加一些助剂,如铝、镍、锌等。
其次,在适当温度和压力的条件下,将反应釜加热至催化剂的最佳反应温度,并施加一定的氢气压力。
氢气起到还原丁烯和辛烯的作用,使其发生氢化反应生成丁辛醇。
反应的理想条件为温度在120-180℃,压力在1-10 MPa之间。
然后,持续加热和搅拌反应体系,使反应进行到理论转化率或产率较高。
反应时间一般在6-12小时左右。
最后,反应结束后,将反应物冷却至室温,过滤除去催化剂和助剂的残渣,得到丁辛醇。
由于丁辛醇是液体,可以直接进行蒸馏分离和提纯。
丁辛醇的生产工艺相对简单,但仍需注意一些关键点。
首先,催化剂的选择和加入量要适当,以提高反应的速度和选择性。
其次,控制好反应的温度和压力,避免过高温度和压力导致副反应的发生。
此外,反应过程中需要及时除去生成的水和氢,以保证反应的进行。
总结起来,丁辛醇的生产主要是通过氢化丁烯和辛烯得到,条件是适当温度和压力下,在催化剂的作用下进行反应。
这种生产工艺简单可行,但仍需要注意控制好关键条件,以提高产率和纯度。
丁辛醇生产技术及发展

2. 2 国内发展概况 我国的丁辛醇生产技术在 1980 年以前主要采 用粮食发酵法制丁醇 ;采用乙醛缩合制巴豆醛 (丁烯 醛) ,巴豆醛缩合 、加氢制辛醇 。由于工艺技术落后 , 这一类的丁辛醇生产装置均已停产 。 1976 年 , 吉化公司从德国 BASF 公司引进 50 kt/ a 年的高压钴法丁辛醇装置 , 1982 年建成投产 。 随后 ,大庆石化总厂 、齐鲁石化公司从英国 DAV Y 公 司成套引进丁辛醇生产技术 ,并在 1986 年 、1987 年 相继投产 。 1992 年北京化工四厂从日本三菱化学公司引进 丁辛醇生产的专利技术及关键设备 , 于 1996 年投 产。 1996 年齐鲁石化公司在原有装置基础上 ,将原 来低压羰基合成气相循环法改为液相循环法 ,在反 应器不变的情况下 ,将产量扩大为原产量的 1. 9 倍 。 1998 年吉化公司对原有的 BASF 高压羰基合成装置 进行改造 ,引进了 UCC/ DAV Y 第四代低压液相循环 羰基合成技术 ,在保留了原装置的异构物分离 、丁醛 缩合 、辛烯醛液相加氢 、醇的精馏分离等几部分基础 上 ,另外扩建了一套气相加氢 、丁醛缩合 、液相加氢 、 醇精馏分离系统 ,改造后装置于 2000 年 8 月投产 ,目 前吉化公司丁醇 、辛醇合计最大生产能力可达 120 kt/ a 。 3 丁辛醇生产技术概况 丁辛醇的生产工艺有两种路线 ,一种是以乙醛 为原料 ,巴豆醛缩合加氢法 ;另一种是以丙烯为原料 的羰基合成法 ,
丁辛醇的技术进展和市场分析

化工市场
丁辛醇的技术进展和市场分析
丁醇和辛醇是重要的精细化工原料,用途十分广泛。丁 醇可用作溶剂、 生产邻苯二甲酸二丁酯 ( 、 邻苯二甲酸丁 !"#) 苄酯 ( ""#) 等增塑剂及醋酸丁酯、甲基丙烯酸丁酯等化学 品。辛醇主要用于生产邻苯二甲酸二辛酯 ( 、 已二酸二 !$#) 辛酯 ( 等增塑剂及丙烯酸辛酯、 表面活性剂等。 !$%) 统计表明,全球辛醇年消费量约 &’’ 万吨以上,其中美 国、 西欧、 日本、 中东、 亚洲 ( 个地区为 )(*+ , 万吨, ( 个地区 的产量达 )-&+ ) 万吨。美国、 西欧、 日本, 亚洲、 南美 ( 个地区 的丁醇产量为 ).(+ * 万吨, 消费量为 ).(+ ( 万吨。 早期的丁醇生产采用发酵法,生产 . 吨丁醇产品需耗粮 耗蒸汽 .& 吨以上, 经济效益差, 故 食 - 吨或糖蜜 / 吨以上, 在国外已经全部被淘汰。二次世界大战期间德国开发了乙醛 缩合法 0 %1231 法 4 , 其优点是反应压力低, 可任意调节丁辛醇 生产比例,且不生成副产品异丁醇等。但工艺流程长、收率 低、 成本较高, 故在国外也已被淘汰。目前全球丁辛醇主要生 产方法为丙烯羰基合成法, 或称氢甲酰化合成法。 丙烯羰基合成生产丁辛醇工艺过程为: 0 . 4 丙烯氢甲酰化反应, 粗醛精制得到正丁醛和异丁醛; 0 ) 4 正丁醛和异丁醛加氢得到产品正丁醇和异丁醇; 0 & 4 正丁醛经缩合、 加氢得到产品辛醇。 根据所采用的压力和催化剂的不同,氢甲酰化反应分高 压钴法、 改性钴法、 高压铑法、 改性铑法等工艺, 其中改性铑 法具有温度低、 压力低、 速率高、 正异构比高、 副反应少、 铑催 欢迎, 市场潜力巨大。纳米级有机膨润土还用于尼龙、 聚酯、 聚烯烃 ( 乙烯、 丙烯、 苯乙烯、 氯乙烯 ) 和环氧树脂等塑料的纳 米改性, 改善其耐热性、 强度、 耐磨性、 气体阻隔性和比重。 ( 活性白土 ( 颗粒白土 ) 活性白土是用膨润土为原料,经无机酸化处理,再经水 漂洗、 干燥制成的吸附剂, 外观为乳白色粉末, 无臭、 无味、 无 毒、 吸附性能很强, 能吸附有色物质、 有机物质。广泛用于矿 物油、 动植物油脂、 制蜡及有机液体的脱色精制。 还可用作无 碳复写纸显色剂、水分干燥剂,内服药物碱解毒剂,维生素 润滑油重合接触剂, 汽油气相精制剂等, 还可用 %、 " 吸附剂, 作中温聚合催化剂、高温聚合剂和制造颗粒白土的原料。膨 润土为原料的活性白土加工生产方法主要有全湿法、全干 法、 半湿法、 汽相法、 煅烧法等。 根据工艺不同, 活性白土还可 联产硫酸铝、 硅铝白硫酸钠、 石膏等。活性白土的加工流程一 般为:膨润土* 破碎 * 加入盐酸或硫酸 0 湿法需加水和分散 剂 4 * 充分搅拌 * 混合挤压 * 回转炉干燥 * 加热空气粉磨 * 空气分级 * 储存。 颗粒白土是以活性白土为主要原料经化学 处理而成的,外观为不定型小颗粒状,它比活性白土有更高 的比表面积,具有很高的吸附能力,广泛用于石化行业芳烃 提纯, 航空煤油精炼, 及润滑油、 基础油、 柴油等油品的精制, 脱除油品中残余的烯烃、 胶质、 沥青、 碱性氮化物等杂质。 * 化剂用量少、寿命长、催化剂可回收再用以及设备少、投资 省、 丁醇和辛醇可切换生产等优点。 现道化学公司 ) 、 上世纪 /’ 年代联碳 ( 566, !789 :;<== 0 现 >#? @ >87=AB=A 过程技术公司 4 和 C3DBE3B :7FFD=9 0 566 G 低压羰基合成工艺 ” !789 G C: 4 共同开发的改性铑法,即 “ ( H#$)采用油溶性三苯基膦 0 ?## 4 配体改性的铑为催化剂, 产物丁醛靠大量未反应的合成气和丙烯从反应釜中带出,从 而实现产物和催化剂的分离,称为气相循环工艺。为减少大 量气体循环而带来的能量消耗, I’ 年代初成功开发了低压羰 基合成液相循环工艺,即反应产物丁醛和催化剂溶液一起自 反应釜中排出,然后对产物丁醛和催化剂溶液进行气化分 离。该工艺为双釜串联工艺, 采用铑 G ?## 为催化剂。 566 G >#? 后来又开发的 6& 吸附回收液相工艺采用的是铑 G 亚磷 酸盐络合环氧化物催化剂, 其活性比铑 G ?## 高, 所以在相接 近的反应温度下该工艺的反应压力更低。由于原料转化率极 高,故可使烯烃氢甲酰化反应实现一次性转化,而不必循 环。该催化剂为最新一代催化剂,其相关工艺名称为 “ 。 H#$J$ @ :>KL” 我国吉化公司羰基醇装置是 >#? G 道化学公司低压羰基 合成工艺第 - 次技术转让给中国的装置, 该装置设计生产 .万吨・年 @ . 丁醛,然后再转化生产丁醇和辛醇,丁辛醇生产 能力为 / 万吨・年 @ . 。 齐鲁石化公司丁辛醇装置技术改造项目,于 )’’& 年 .. 白炭黑 白炭黑即水合二氧化硅,是微细粉末状或超细粒子状的 二氧化硅。是用于彩色、 浅色橡胶制品的主要补强填料之一, 是德国在 -’ 年代作为炭黑的代用品开发出来的,现在已广 泛地用于橡胶、 制鞋、 塑料、 油漆、 造纸、 合成树脂和油脂等工 业部门, 其中橡胶、 制鞋用量最大。 .,(I 年前后我国开始研制 白炭黑在轮胎 生产白炭黑。有人称 ). 世纪是绿色轮胎时代, 行业的使用将大大刺激白炭黑的需求;另外橡胶制品的彩 色、浅色化发展趋势以及其他工业领域应用的开拓也必将极 大地刺激白炭黑的需求。以膨润土为主要原料生产白炭黑生 产工艺新颖先进, 流程合理, 能耗低, 原料易得价格低廉, 是 国家鼓励开发的国家级重点新产品,具有强劲的市场竞争优 势。我国膨润土资源非常丰富, 居世界首位, 分布广, 易开采, 但目前仅仅提供初级产品, 效益低。利用膨润土生产白炭黑, 增加膨润土的附加值,且成本低,为白炭黑在更广泛的领域 应用创造了条件。用膨润土制备白炭黑能耗只为沉淀法 ( 酸 原材料消耗成本只为沉淀法的 . G & , 与 中和水玻璃 ) 的 . G (, 沉淀法生产的白炭黑相比每吨成本约低 .’’’ M )’’’ 元。白 炭黑的用途很广, 目前国内年产量低, 不能满足需求, 市场缺 口很大。 0 金山 4
丁辛醇生产工艺

丁辛醇的生产工艺有两种路线,一种是以乙醛为原料,巴豆醛缩合加氢法;另一种是以丙烯、合成气为原料的低压羰基合成法,该法是当今国际上最为先进的技术之一,目前世界丁辛醇70%是由丙烯羰基化法生产的。
它以丙烯、合成气为原料,经低压羰基合成生产粗丁醛,再经丁醛处理、缩合、加氢反应制得丁辛醇。
低压羰基合成法生产丁辛醇典型的流程包括:原料净化、羰基合成、丁醛精制、缩合、加氢、粗醇精馏等工序。
丁醛精制是指粗丁醛除去轻组分后在异构塔内精馏分离得正丁醛和异丁醛。
缩合是指正丁醛脱去重组分后进入缩合系统,在NaOH 存在、120℃和0.4MPa条件下,进行醛醛缩合生成辛烯醛(EPA)。
加氢一般是指正、异丁醛或混合丁醛或辛烯醛加氢生产相应的醇。
但是不论采用那一种方法,都必须经过丁烯醛/丁醛、辛烯醛加氢来制取丁醇和辛醇。
醛加氢是丁辛醇生产过程的重要组成部分,对丁辛醇的产品质量和生产过程的经济性都有很大的影响。
1丁辛醇加氢工艺路线丁醛加氢制备丁醇和辛烯醛加氢制备辛醇的工业化工艺路线主要有气相法和液相法两种。
液相加氢反应采用多段绝热固定床反应器,由于液相热容量较大,反应器内不用设置换热器。
根据反应条件,段间设置换热器移走反应热,防止醛的缩合反应。
BASF公司曾经采用过高压液相加氢,加氢的压力为25.33MPa。
高压加氢的唯一优点是氢气耗量较少,所用的液相加氢催化剂为70%Ni、25%Cu、5%Mn,该催化剂要求氢气分压不低于3.5MPa,所以总高压时,尾气的氢气浓度可降低,氢耗少。
但采用该高压工艺,原料氢气必须高压压缩,电耗大、设备费用大,目前已经被淘汰。
BASF公司和三菱化成工艺中醛的加氢采用中压液相加氢工艺,加氢压力为4.0-5.0MPa,加氢反应器形式采用填充床,反应温度为60-190℃。
气相加氢法由于操作压力相对较低,工艺设备简单而被广泛应用。
目前,工业上丁辛醇装置上大多采用铜系催化剂气相加氢工艺。
如U.D.J联合工艺中采用低压气相加氢,压力为0.59-0.69MPa。
低压羰基法生产丁辛醇工艺技术进展

・
1 6・
C e iaItr da hmclnemeie t
羰 基合成 法
中间体 ・
2t 年 第 0 08 ) 7期
21 A . D W
巴斯 夫 合 成 法 是 德 国 B S A F公 用 的 D V 羰 基 合 成 法 是 由 B S AY A F公 司 的低 压羰 基 合 成工 艺 采 用铑 的络 合 物 为催
i c u i g Da y Do M C a d AS , w r i u s d n l d n v / w、 C n B F e e d s s e .An h tae i i ci n o h y t e ii g c d t e sr t gc d r t f t e s n h szn e o
nl y
Ab ta tT re sr c : h e man e h oo is n o i tc n lge i lw p es r s nh szn b tn l n o tn l t c r o y, rsu e y te iig ua o a d ca o wi h ab n l
T e De eo me to o P e f r y t e i fB tn la d Oea o i h v lp n f L w rs u e S n h ss o u a o n tn lw t C ̄ h
S i- a , Z e- in , Z HIJn y n OU P i l g a HANG u — in J n xa
丁 醇 ( 括 正 丁 醇 和 异 丁 醇 ) 辛 醇 (一乙基 己 应条 件温 和 , 包 和 2 备受 生产 企业 的青 睐 。 目前 , 压羰 基法 低 醇, - H 是重 要 的精细 化工 原料 , 途十 分 广泛 。正 主 要 有 戴 维羰 基 合 成 法 、 菱 化 成 合 成法 、 2 E) 用 三 巴斯 夫 合 丁 醇 可 作溶 剂 、 产邻 苯 二 甲酸二 丁 酯 、 酸丁 酯 、 生 醋 磷 成法 等 。 酸 酯 类 增 塑 剂 , 可 以用 于 生 产 丁 醛 、 酸 、 胺 、 还 丁 丁 乳
丁辛醇生产工艺技术

丁辛醇生产工艺技术丁辛醇是一种重要的有机化工原料,广泛应用于化学、医药、农药、塑料等行业。
下面我们来介绍一下丁辛醇的生产工艺技术。
丁辛醇的主要生产工艺有两步法和一步法。
首先介绍两步法。
两步法生产丁辛醇主要包括醇酸法和醇醚法。
醇酸法是利用丁烯为原料,通过醇酸浓度温和酸催化剂进行酸醇缩合反应,生成丁辛醇。
这个过程需要在合适的温度和压力下进行。
反应结束后,通过蒸馏分离纯化,即可得到丁辛醇。
醇醚法是将丁醇和辛醇分别与硫酸或磷酸等酸催化剂进行酯交换反应,生成对应的丁酯和辛酯。
然后,将丁酯和辛酯在高温下进行酯加成反应,生成丁辛醇。
这个过程同样需要进行蒸馏纯化,从而得到纯净丁辛醇。
两步法生产工艺相对比较复杂,需要多个步骤和反应器,并且对催化剂和温度等条件有较高的要求。
因此,虽然两步法可以得到高纯度的丁辛醇,但生产成本较高,工艺相对繁琐。
另外一步法是将1,3丁二醇和辛醇通过一步法直接脱羟酯化反应得到丁辛醇。
这个过程相对简单,只需要进行一次反应即可得到丁辛醇。
首先将1,3丁二醇和辛醇与脱水剂进行酯化反应,生成丁辛酸酯。
然后通过加热脱羟反应,将丁辛酸酯脱羟生成丁辛醇。
最后进行蒸馏纯化即可得到丁辛醇。
这个工艺相对比较简单,生产成本较低。
无论采用哪种生产工艺,丁辛醇的生产工艺都需要严格控制反应的条件和过程,以保证产品的质量。
同时,在生产过程中需要注意安全生产,避免发生事故。
总的来说,丁辛醇的生产工艺技术涉及到酯交换、酯加成、酸醇缩合等反应,采用两步法或一步法进行。
无论采用哪种工艺,都需要严格控制反应条件和过程,以获得高纯度的丁辛醇。
同时,生产过程中需要注重安全生产,避免事故发生。
丁辛醇的生产工艺随着科技的发展和技术的进步,也在不断的改进和完善。
丁辛醇生产工艺
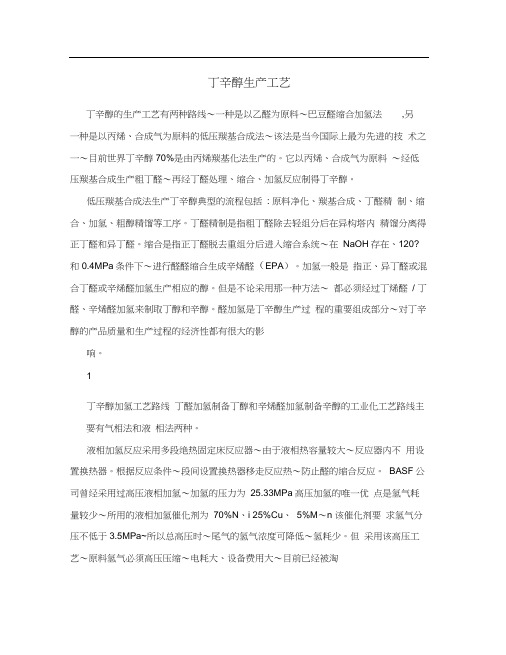
丁辛醇生产工艺丁辛醇的生产工艺有两种路线〜一种是以乙醛为原料〜巴豆醛缩合加氢法,另一种是以丙烯、合成气为原料的低压羰基合成法〜该法是当今国际上最为先进的技术之一〜目前世界丁辛醇70%是由丙烯羰基化法生产的。
它以丙烯、合成气为原料〜经低压羰基合成生产粗丁醛〜再经丁醛处理、缩合、加氢反应制得丁辛醇。
低压羰基合成法生产丁辛醇典型的流程包括: 原料净化、羰基合成、丁醛精制、缩合、加氢、粗醇精馏等工序。
丁醛精制是指粗丁醛除去轻组分后在异构塔内精馏分离得正丁醛和异丁醛。
缩合是指正丁醛脱去重组分后进入缩合系统〜在NaOH存在、120?和0.4MPa条件下〜进行醛醛缩合生成辛烯醛(EPA)。
加氢一般是指正、异丁醛或混合丁醛或辛烯醛加氢生产相应的醇。
但是不论采用那一种方法〜都必须经过丁烯醛/ 丁醛、辛烯醛加氢来制取丁醇和辛醇。
醛加氢是丁辛醇生产过程的重要组成部分〜对丁辛醇的产品质量和生产过程的经济性都有很大的影响。
1丁辛醇加氢工艺路线丁醛加氢制备丁醇和辛烯醛加氢制备辛醇的工业化工艺路线主要有气相法和液相法两种。
液相加氢反应采用多段绝热固定床反应器〜由于液相热容量较大〜反应器内不用设置换热器。
根据反应条件〜段间设置换热器移走反应热〜防止醛的缩合反应。
BASF公司曾经采用过高压液相加氢〜加氢的压力为25.33MPa高压加氢的唯一优点是氢气耗量较少〜所用的液相加氢催化剂为70%N、i 25%Cu、5%M〜n 该催化剂要求氢气分压不低于3.5MPa~所以总高压时〜尾气的氢气浓度可降低〜氢耗少。
但采用该高压工艺〜原料氢气必须高压压缩〜电耗大、设备费用大〜目前已经被淘汰。
BASF公司和三菱化成工艺中醛的加氢采用中压液相加氢工艺〜加氢压力为 4.0-5.0MPa〜加氢反应器形式采用填充床〜反应温度为60-190?。
气相加氢法由于操作压力相对较低〜工艺设备简单而被广泛应用。
目前〜工业上丁辛醇装置上大多采用铜系催化剂气相加氢工艺。
丁辛醇工艺技术进展及选择_李仕超

丁辛醇工艺技术进展及选择李仕超孔艳(兖矿国宏化工有限责任公司,山东邹城,273512)摘要介绍了国内外合成丁辛醇的工艺技术进展情况,包括戴维合成法、三菱化成合成法、巴斯夫合成法等。
在比较不同生产工艺路线的同时,从现有技术成熟角度和应用情况对比,提出了低压羰基法合成丁辛醇的选择原则。
同时阐述了未来丁辛醇合成技术的发展趋势。
关键词:羰基法丁辛醇工艺进展1概述丁辛醇是重要的基本有机化工原料.它有三个重要的品种:正丁醇、异丁醇、辛醇(或称2-乙基己醇)。
用正丁醇生产的邻苯二甲酸二丁酯和脂肪族二元酸酯类增塑剂,广泛用于各种塑料和橡胶制品的生产;用正丁醇生产的丙烯酸丁酯可用于涂料和粘合剂;正丁醇还是生产丁醛、丁酸、丁胺和醋酸丁酯等有机化合物的原料,可用作树脂、油漆、粘接剂的溶剂及选矿用消泡剂,也可用做油脂、药物(如抗菌素、激素和维生素)和香料的萃取剂及醇酸树脂涂料的添加剂。
辛醇主要用于生产苯二甲酸二辛酯(DOP)。
DOP产品素有王牌增塑剂之称,广泛用于聚氯乙烯、合成橡胶、纤维素酯的加工等。
辛醇还可用作柴油和润滑油的添加剂,以及照相、造纸、涂料、油漆和纺织等行业的溶剂、陶瓷工业釉浆分散剂、矿石浮选剂、消泡剂、清净剂等。
2国外丁辛醇生产工艺发展情况丁辛醇产品是随着石油化工、聚氯乙烯塑料工业、有机化学工业的发展及羰基合成技术的发展而迅速发展起来的。
丁辛醇的工业化生产方法主要有乙醛缩合法、发酵法、齐格勒法和羰基合成法等。
211乙醛缩合法二战期间,德国开发了乙醛缩合法(Aldol)法,是乙醛在碱性条件下进行缩合和脱水生成丁烯醛(巴豆醛),丁烯醛加氢制得丁醇,然后经选择加氢得到丁醛,丁醛经醇醛缩合、加氢制得2-乙基己醇(辛醇)。
由于其工艺流程长,收率低,生产成本高,此方法已基本被淘汰。
212发酵法发酵法是粮食或其它淀粉质农副产品,经水解得到发酵液,然后在丙酮-丁醇菌作用下,经发酵制得丁醇、丙酮及乙醇的混合物,通常的比例为6:3: 1,再经精馏得到相应产品。
丁辛醇生产工艺技术规程

丁辛醇生产工艺技术规程丁辛醇是一种无色透明的液体,具有良好的溶解性和稳定性。
它广泛应用于合成树脂、塑料、溶剂和涂料等行业。
下面是丁辛醇的生产工艺技术规程。
一、原料准备1. 丁辛醇的主要原料为丁烯和辛醇。
2. 丁烯和辛醇的纯度需达到99%以上。
3. 其它辅助原料包括催化剂、溶剂和助剂等。
二、工艺流程1. 玉米糖浆获得丁烯:将玉米糖浆经过酸液处理和蒸馏,获得纯度达到90%以上的丁烯。
2. 丁辛醇制备:将丁烯与辛醇在反应釜中进行氢化反应,反应温度控制在100-120℃,压力控制在1-3 MPa范围内,反应时间为4-6小时。
3. 分离提纯:经过氢化反应后,将产物进行脱氢反应,去除未反应的氢气。
再通过蒸馏、结晶等工艺过程,分离得到纯度达到99%以上的丁辛醇。
三、关键工艺参数1. 反应温度:控制在100-120℃,过高温度会导致副反应的发生,过低温度则反应速率较慢。
2. 压力:控制在1-3 MPa范围内,高压有利于反应的进行,但过高压力会增加设备的投资和能耗。
3. 反应时间:反应时间为4-6小时,过长时间会导致副反应的发生,过短时间则反应不完全。
四、设备要求1. 反应釜:选择耐高温、耐腐蚀的材质制成,容积应根据生产规模进行选择。
2. 蒸馏塔:采用分馏和萃取等工艺,需要具备高效脱水和分离的能力。
3. 精馏塔:用于去除未反应的氢气,要求具备高效脱气的能力。
五、安全措施1. 工艺过程中要保持设备的密封性,防止气体泄漏和溶剂挥发造成爆炸和污染环境。
2. 操作人员应佩戴防护装备,避免直接接触有毒物质。
3. 严格控制反应温度和压力,防止设备过热或过压造成事故。
六、产品质量检验1. 丁辛醇的外观应无色透明,无杂质。
2. 需经过色度检验,颜色不能超过标准。
3. 根据工业标准进行纯度检验,纯度需达到99%以上。
4. 根据用户要求进行包装和出厂检验。
以上是丁辛醇的生产工艺技术规程,通过合理的生产工艺和严格的质量检验,可保证生产出高质量的丁辛醇产品。
丁辛醇生产工艺技术标准

丁辛醇生产工艺技术标准丁辛醇是一种重要的有机合成原料,被广泛应用于化工、医药、农药等领域。
为了确保丁辛醇的质量稳定和生产效率,制定和实施相应的工艺技术标准是非常重要的。
一、原料选用1. 丁烯:99%以上的纯度,含水量不超过0.1%。
2. 硫酸:纯度大于98%,含水量不超过0.1%。
3. 氢气:氧气含量低于10ppm,水含量不超过0.1%。
二、生产工艺流程1. 丁烯和硫酸的反应:将丁烯和硫酸按照一定的摩尔比加入反应釜中,反应温度控制在100℃-130℃,反应时间需要根据具体情况进行调整,通常为2-3小时。
反应后,将反应物进行分离处理。
2. 含硫酸分离:将反应后得到的含硫酸混合液进行净化处理,通过蒸馏、过滤等方法去除杂质。
3. 脱硫反应:将净化后的含硫酸混合液与氢气进行反应,反应温度在120℃-150℃之间,反应时间约为1-2小时,将反应后得到的产物经过分离处理。
4. 脱水反应:将脱硫后的产物与氢气进行反应,反应温度控制在150℃-200℃,反应时间约为1-2小时,将反应后得到的产物进行分离处理。
5. 丁辛醇的提纯:通过蒸馏、结晶等方法,对产物进行多次提纯,确保丁辛醇的纯度达到99%以上。
三、工艺控制1. 温度控制:根据不同的反应步骤,控制反应温度在适宜的范围内,以确保反应的进行和产物质量的稳定。
2. 气体流量控制:控制氢气的流量,以保证反应物料中的氧气含量在合理的范围内,避免氧气对反应的干扰。
3. 反应时间控制:根据反应的速度和产物的品质要求,控制反应时间,以确保充分反应。
4. 生产过程监控:通过对反应釜内压力、温度、气体流量等参数的实时监控,掌握生产过程中的动态变化,及时调整工艺参数,确保生产的连续性和稳定性。
四、安全和环保要求1. 生产过程中严格遵守相关安全操作规程,确保操作人员的人身安全和设备的正常运行。
2. 定期对生产设备进行检修和保养,保证设备的正常运行和安全性。
3. 对反应废水、废气以及废酸等进行合理处理,遵守环保法规,减少对环境的污染。
丁辛醇技术进展及市场分析

丁辛醇●●技术进展及市场分析◎鲁凤兰中国石油和化工・综合版弋‘辛醇是重要的基本有机化工原料,它有三个重要的品种:正丁醇、异丁醇、辛醇(或称2一乙基己醇)。
用正丁醇生产的邻苯二甲酸二丁酯和脂肪族二元酸酯类增塑剂.广泛用于各种塑料和橡胶制品的生产;用正丁醇生产的丙烯酸丁脂可用于涂料和粘合剂;正丁醇还是生产丁醛、丁酸、丁胺和醋酸丁酯等有机化合物的原料,可用作树脂、油漆、粘接剂的溶剂及选矿用消泡剂.也可用做油脂、药物(如抗菌素、激素和维生素)和香料的萃取剂及醇酸树脂涂料的添加剂。
辛醇主要用于生产苯二甲酸二辛酯(DOP)。
DOP产品素有王牌增塑剂之称,是一种物美价廉的理想增塑剂,广泛用于聚氯乙烯、合成橡胶、纤维素脂的加工等。
辛醇还可用作柴油和润滑油的添加剂,以及照相、造纸、涂料、油漆和纺织等行业的溶剂、陶瓷工业釉浆分散剂、矿石浮选剂、消泡剂、清净剂等。
1、丁辛醇的生产技术及发展动向生产工艺技术二战期间,德国开发了乙醛缩合法(Ald01)法,其工艺流程长,收率低,成本囫较高。
故在国外也已被淘汰。
目前全球丁辛醇的主要生产方法为丙烯羰基合成法,或称为氢甲酰化合成法。
丙烯羰基合成法的主要工艺过程为:(1)丙烯氢甲酰化反应,粗醛精制得到正丁醛和异丁醛;(2)正丁醛和异丁醛加氢得到产品正丁醇和异丁醇;(3)正丁醛经缩合,加氢得到产品丁辛醇。
根据压力和催化剂的不同,丙烯羰基合成反应分为钻法f高压钻法、改性钻法)和铑法(高压铑法、改性铑法)两种。
其中改性铑法具有温度低、压力低、催化剂寿命长并可回收再利用以及没备少、投资小、丁醇和辛醇可切换生产等优点.是当代丁辛醇合成技术的主流。
改性铑法又分为气相循环法和液相循环法两种。
经过若干年的发展.液相循环改性铑法已成为当今世界最先进、应用最广泛的丁辛醇合成技术。
目前主要有戴维、三菱化成、鲁尔化学和巴斯夫4家公司拥有此项专利技术。
(1)DAvY羰基合成工艺DAVY/DOWf原Kvaemer/UCC)联合开发了第二代低压铑法羰基合成工艺——液相循环工艺。
丁辛醇生产工艺研究进展

三菱化成工艺 100 ~ 120 95 10:1 可调 8:1 蒸发分离 液相循环 带冷却盘管的 搅拌釜 长 多
鲁尔工艺 100 ~ 130 19:1
水相循环
装若干个降膜蒸发 器的搅拌釜 较长 较多
BASF 工艺 ~ 100 >99 9:1 ~ 8:1 蒸发分离 液相循环
塔式
较长 较多
2 戴维 / 陶氏液相循环低压铑法工艺 戴维 / 陶氏液相循环低压铑法生产工艺的几个工段为:羰基合成反应;正丁醛缩合反应;正 / 异丁醛、辛烯醛 加氢反应;正 / 异丁醇、辛醇精馏精制。其工艺流程示意图参见图 1:
醋 酸 铑、 三 苯 基 磷 三磺酸钠盐
铑、三苯基磷
甲苯
水
正 异 构 丁 醛、 高 沸 物
≥ 1.7
5.0 ~ 7.0
~ 2.0
比较项目 反应温度 /℃
转化率 /% 正异构比例
催化剂 循环vy/Dow 工艺 85 ~ 110 91 ~ 93 10:1(可调) 蒸发分离 液相循环 槽式带搅拌、2 台串 联 短 少
图 1 液相循环低压铑法工艺流程示意图 2.1 羰基合成反应 丙烯与一氧化碳、氢气反应生成丁醛混合物,主产品是直链正丁醛。同时也有少量的异丁醛、丙烷和醛的各 种自冷凝反应产物。在压力 1.85 MPa G,温度 85~110℃,且有过量三苯基膦存在的条件下,在铑膦络合物催化作 用下发生反应。 主反应——丙烯氢甲酰化生成正丁醛 CH3CH=CH2 + CO + H2 → CH3CH2CH2CHO 副反应——丙烯氢甲酰化生成异丁醛 CH3CH=CH2 + CO + H2 →(CH3)2CHCHO 这一步反应是该工艺的核心部分。多年来该工艺的改革进步都围绕着这一步反应而有所作为。 2.2 正丁醛缩合反应 两分子正丁醛缩合,再脱去一份子水后生成辛烯醛,从而具备了生产辛醇的条件。 2CH3CH2CH2CHO → CH3CH2CH2CH=C(CH2CH3)CHO + H2O 丁醛缩合和脱水反应是在含有 NaOH 水溶液并带有液相搅拌的缩合反应器中进行的。只要正确掌握碱催化剂 的含量,反应温度,平均停留时间等几个主要参数,就可以控制转化率及收率。 2.3 正 / 异丁醛、辛烯醛加氢反应 加氢反应的操作可采用气相加氢,也可采用液相加氢。液相加氢法设备少、流程简单、压力较高,约 2.6MPa G。气相加氢法设备较多、流程略为复杂、压力低,约 0.45MPa G。 正丁醛加氢生成正丁醇 CH3CH2CH2CHO + H2 → CH3CH2CH2CH2OH 异丁醛加氢生成异丁醇 (CH3)2CHCHO + H2 →(CH3)2CHCH2OH 辛烯醛加氢生成辛醇 CH3CH2CH2CH=C(CH2CH3)CHO + 2H2 → CH3CH2CH2CH2CH(CH2CH3)CH2OH 2.4 正 / 异丁醇、辛醇精馏精制 粗丁醇通过两个塔精制。首先在预精馏塔中,轻组分(未反应的有机物、水及溶解的气体)被脱除到塔顶产 物中;在精馏塔中,所有的高沸点重组分副产品被脱除到塔底物流中。 辛醇精制与丁醇类似,不再赘述。 3 结束语 我国丁辛醇产业已步入高速扩张时期,多套项目仍在建设中,国内产品自给率将显著提升。新装置的投产将 打破丁辛醇市场卖方强势的局面。随着丁辛醇行业投资增加,需求增长放缓,市场供需格局将趋向平衡。大批丁 辛醇装置的投产,将使国内市场竞争更加激烈,部分规模偏小、能耗物耗高的落后技术将被淘汰。 铑催化技术是当前丁醛衍生醇领域的主流技术,但由于铑金属资源稀缺,价格昂贵,许多公司着眼于开发新 型的催化剂以及配体。例如 HOECHST 公司开放了一种水溶性钴族化合物催化剂,可以使烯烃在聚乙二醇做极性 相的两相溶剂体系中有效的进行氢甲酰化。高碳烯烃对聚乙二醇的亲和力比水好,因此可以提高反应速率。[1] BASF 公司开发了一种新型的以丁二烯为原料制 OXO 醇的工艺。该工艺可利用低成本的原料丁二烯,同时省 去合成气,改进了传统工艺。[2] 另外,日本工业技术研究所在 SnCl2 存在下,以环烷连接的双磷配位体的铂系催 化剂,SHELL 公司开发的铂系络合物催化剂,以及 UCC 公司开发的非金属铂系催化剂等,也取得了一定进展。 除了催化剂,羰基合成反应器的制造也是丁辛醇装置的关键所在。预计 2015 年我国正丁醇和辛醇的市场供 需缺口分别约为 24.8 万吨和 11.2 万吨,我国仍将是世界上主要的丁辛醇进口国。对羰基合成反应器进行攻关,同 时深入开展高效催化剂的研发工作,力求开发具有自主知识产权的全套丁辛醇生产技术,将是近期国内有关科研 设计单位工作的重中之重。
丁辛醇生产技术现状及其发展趋势[1]
![丁辛醇生产技术现状及其发展趋势[1]](https://img.taocdn.com/s3/m/f4d0a84633687e21af45a9a5.png)
丁辛醇生产技术现状及其发展趋势总工办刘 军摘 要 简要介绍了丁辛醇的用途和几种主要的生产工艺,详述了国内外丁辛醇生产技术的现状,阐明了其发展趋势。
关键词 丁辛醇 生产技术 发展趋势1 概 述丁醇有4种异构体,分别是正丁醇(12丁醇)、异丁醇、叔丁醇、仲丁醇(22丁醇)。
通常所说的丁醇是指正丁醇。
辛醇异构体很多,最重要的是异辛醇(22乙基己醇)、仲辛醇(22辛醇)、正辛醇(12辛醇)。
通常所说的辛醇是指异辛醇。
丁醇和辛醇(下称丁辛醇)都是重要的有机化工原料,用途广泛。
丁醇主要用于生产邻苯二甲酸二丁酯(DBP)、邻苯二甲酸丁苄酯(BBP)、脂肪族二元酸酯类等增塑剂和醋酸丁酯、丙烯酸丁酯、甲基丙烯酸丁酯等,还是生产丁醛、丁酸以及醚类、胺类等的原料。
辛醇主要用于生产邻苯二甲酸二辛酯(DOP)、对苯二甲酸二辛酯(DOTP)、己二酸二辛酯(DOA)等增塑剂和丙烯酸辛酯(22乙基己基丙烯酸酯)、表面活性剂等,还可用作照相、造纸、涂料和纺织等行业的溶剂,柴油和润滑油的添加剂,陶瓷行业釉浆分散剂,矿石浮选剂,消泡剂,清净剂等[1]。
2 丁辛醇的生产技术现状丁辛醇是随着石油化工、聚氯乙烯材料工业以及羰基合成工业技术的发展而迅速发展起来的。
丁辛醇的工业化生产方法主要有乙醛缩合法、发酵法、齐格勒法和羰基合成法等。
早期的丁醇生产采用发酵法,生产1t丁醇产品需耗粮食4t或糖蜜7t以上,耗蒸汽13t以上,经济效益差,故在国外已经全部被淘汰。
二次世界大战期间德国开发了乙醛缩合法(A ldol 法),其优点是反应压力低,可任意调节丁辛醇生产比例,且不生成副产品异丁醇等,但工艺流程长,收率低,成本较高,故在国外也已被淘汰。
目前全球丁辛醇主要生产方法为丙烯羰基合成法(亦称氢甲酰化合成法)。
2.1 主要生产工艺2.1.1 发酵法发酵法是采用粮食或其他淀粉质农副产品,经水解得到发酵液,然后在丙酮-丁醇菌作用下,经发酵制得丁醇、丙酮及乙醇的混合物,通常的比例为6∶3∶1,再经精馏得到相应产品。
探析丁辛醇加氢催化的技术进展

探析丁辛醇加氢催化的技术进展本文重点介绍了丁辛醇工业生产流程当中,加氢生产环节的相关工艺技术以及相关的催化剂使用情况,同时针对加氢催化剂在我国丁辛醇生产过程当中的相关作用要点进行了介绍。
通过相关工作人员的研究和分析可以看出,丙烯氢甲酰化的研究工作和开发项目当中的加氢技术环节,在催化剂的选择方面可以达到相应的生产目标和生产效果,对推动我国工业生产整体质量有着重要的保障。
标签:丁辛醇;加氢催化;催化剂丁辛醇产品是一种非常重要的化工原材料,在我国各大化工领域当中的应用程度相对较高,丁醇主要是用于制造磷苯二甲酸以及正丁酯类物质,被广泛地运用在各种高强度的塑料以及橡胶产品当中。
现阶段,我国在丁辛醇产品的整体生产量以及生产状况,明显落后于我国社会经济的发展需求,并且在最近几年当中,国内对丁辛醇产品的供需矛盾正在不断加大。
丁辛醇的生产方法分为了两种形式,第一种是通过乙醛作为反应的原材料,通过使用巴豆醛通过缩合加氢的生产工艺来进行生产;另外一种是使用丙烯材料通过低压羟基合成的方法来进行生产,这种生产模式是国际上比较先进的丁辛醇产品生产技术类型,并且世界上70%的丁辛醇是通过丙烯羟基化法所生成。
通过使用丙烯和合成气作为主要的原材料,通过低压羟基合成相应的异丁醛,然后再通过丁醛的后续处理,制取相应的丁辛醇产品。
1.丁辛醇加氢工艺路线在丁辛醇的加氢生产工艺路线当中主要分为了两种方法:首先,是通过液相加氢反应方法,以多断绝热的反应器具来不断提高整个反应流程的效率以及质量。
在生产过程当中,反应器内部设置了不同型号的换热器设备,依照实际的反应条件,加氢设备的压力大小为25.55MPa,高压加氢的唯一优势在于氢气的消耗量相对较少,同时所运用的液相加氢剂,为70%的Ni和25%的Cu以及5%的Mn。
通过对这种催化剂的使用,在实际的反应过程中要求氢气的分压大小不能小于3.5MPa,因此在高压反应过程中,尾气区域的氢气浓度有着明显的下降,并且对氢气的消耗量相对较少,通过这种高压生产工艺,在原材料的氢气当中必须要通过高压压缩的方式来进行生产,整体的电能消耗量相对较大,并且设备的费用消耗相对较大,当前该设备已经被完全淘汰。
- 1、下载文档前请自行甄别文档内容的完整性,平台不提供额外的编辑、内容补充、找答案等附加服务。
- 2、"仅部分预览"的文档,不可在线预览部分如存在完整性等问题,可反馈申请退款(可完整预览的文档不适用该条件!)。
- 3、如文档侵犯您的权益,请联系客服反馈,我们会尽快为您处理(人工客服工作时间:9:00-18:30)。
1。[2t引
(2)吉林石化公司研究院于2001年成功开发了 国内首创的辛烯醛高压液相加氢制辛醇催化剂,经 在吉化化肥厂丁辛醇装置上两年的应用证明,可以
丙爆一
问1j】换
谨记翘再 生与琅缩 I
I糯辛尊(:.乙基己尊)
蛩吨囹一异丁啐
对材质的要求最低,大部为碳钢,少量的为304不锈 钢;从流程的长度和装置的复杂性来说,戴维的最 短、最简单;从使用的情况看,戴维合成工艺使用最 多;但是伊斯曼乙烯一丙烯共迸料工艺技术可同时生 产丁醛和丙醛,产品灵活多样,对市场变化有较好的
法合成丁辛醇的选择原则。同时阐述了未来丁辛醇合成技术的发展趋势。
关键词:羰基法丁辛醇工艺进展
1概述
丁辛醇是重要的基本有机化工原料.它有三个
重要的品种:正丁醇、异丁醇、辛醇(或称2一乙基己
到丁醛,丁醛经醇醛缩合、加氢制得2一乙基己醇(辛 醇)。由于其工艺流程长,收率低,生产成本高,此方
法已基本被淘汰。
125 2.5 3~10/l ~9l 332
50
无铁丁醛 三苯基膦羰基铑 催化剂 蒸发分离、 液相循环 ∞~95
1.8~1.9 4~25/I 91~93
278.8
5
催化剂 催化剂 蒸发分离,
6
催化剂分离方式 液相循环 温度℃ 1∞
2 8~9/1
%
7
主要技术参 数
压力-眈
正/异比 转化率 循环水 电
~%
巴斯夫羰基合成工艺采用铑化合物为催化剂,
万方数据
四川化工 近年来,联碳与戴维公司又开发了第四代低压
第12卷2009年第3期
3.2
国外丁辛醇生产工艺选择 高压的羰基合成技术,由于选择性较差,副产品
液相羰基合成工艺——。UOC/DAVY MK-IV”工
艺。该工艺与原液相循环法的主要区别在于使用 铑/异一44双亚磷酸盐催化体系,其活性比第二代工 艺所使用的铑/三苯基膦(TPP)催化体系活性高,铑 浓度大幅降低,在相近的反应温度下该工艺的反应 压力更低。由于原料转化率极高,故可使烯烃氢甲 酰化反应实现一次性转化,不需循环。该工艺特点: a、投资少.b、工艺简单,反应温度较低,单程操作;c、 操作费用低;d、丙烯和合成气几乎全部转化,损失 少,醛重组分产率低;e、铑用量少;f、正异比可高达
b.三菱化成技术 三菱化成技术是三菱化成公司的专利技术,它 是以铑为催化剂,甲苯作溶剂的新工艺,粘度低、传
热好、催化剂活性较高、铑夹带损失小,催化剂可采 用结晶,离心过滤加以回收,装置内设有失活催化剂 就地再生设施。三菱化成工艺技术,1981年在巴西 建成5.4万吨/年辛醇,1984年投产至今。1992年 在日本水岛工厂建成13万吨/年的丁醛装置,并投 入生产。我国北京化工四厂也于1992年引进了三 菱化成技术,现已稳定运行。
流程短;流程短:正/异比较高;
表1
序号
l
工艺技术方案对比表
羰基合成低压“液相循环”法 巴斯夫 伊士曼
≥97%
方案指标
单位
戴维
≥99.5%
2
产品质量(纯度) 丙烯 t/t产品
≥99.5%
O.6l
0.61
0.∞2
3
原料单耗
(10暇计)
合成气
瞄。/t产品
719
690
715
4
溶剂
正异构丁醛 三苯基瞬羰基铑 铑基 催化荆 蒸发分离, 气相循环
业、有机化学工业的发展及羰基合成技术的发展而
迅速发展起来的。丁辛醇的工业化生产方法主要有 乙醛缩合法、发酵法、齐格勒法和羰基合成法等。
2.1
乙醛缩合法 二战期间,德国开发了乙醛缩合法(Ald01)法,
是乙醛在碱性条件下进行缩合和脱水生成丁烯醛
(巴豆醛),丁烯醛加氢制得丁醇,然后经选择加氢得
・高压法:鲁尔(Ruhr)技术、巴斯夫(BASF)技
2.2
发酵法
醇)。用正丁醇生产的邻苯二甲酸二丁酯和脂肪族
二元酸酯类增塑剂,广泛用于各种塑料和橡胶制品 的生产;用正丁醇生产的丙烯酸丁酯可用于涂料和
发酵法是粮食或其它淀粉质农副产品,经水解
得到发酵液,然后在丙酮一丁醇菌作用下,经发酵制
粘合剂;正丁醇还是生产丁醛、丁酸、丁胺和醋酸丁
酯等有机化合物的原料.可用作树脂、油漆、粘接剂 的溶剂及选矿用消泡剂,也可用做油脂、药物(如抗 菌素、激素和维生素)和香料的萃取剂及醇酸树脂涂 料的添加剂。辛醇主要用于生产苯二甲酸二辛酯 (D()P)。D()P产品素有王牌增塑剂之称。广泛用于
中期才工业化的一项新工艺,这是由美国联合碳化
物公司、英国戴维公司和英国约翰逊马瑟公司联合 开发的新技术,于1976年在美国庞塞厂建成了世界
上第一套年产13。6万吨/年丁醛的铑法低压羰基合 成装置。这种技术是以丙烯、合成气为原料,羰基 铑/三苯基膦络合物为催化剂,在低压1.76MPa的 操作压力下,郎能完成反应。此法具有流程短、设备 少、反应条件要求低、正/异比高、无腐蚀、对设备材 质要求低、催化剂活性高、操作平稳、产品比例方便
的,六十年代建了大量装置,但由于此法反应温度 高,反应需要在20~30MPa的高压下操作,反应产 物的正、异构比只有3~4:1,设备腐蚀严重,因此,
该法自七十年代中后期,几乎全部被低压羰基合成 法所取代。
(2)中压法撰基合成技术是六十年代出现的壳
牌公司的中压改性钴法技术,七十年代,日本三菱化 成公司也开发了铑法的中压羰基合成技术。到八十 年代初,Ruhrchemic又研制出一套成熟的羰基合成 工艺,是采用水溶性铑催化剂系统,1984年在Ru- hrchemic厂建成10万吨/年丁醛装置,1988年又以
该技术,建成了一套17万吨/年的装置,运行情况较
好。该生产装置能力约占目前世界铑法工艺技术总 能力的9"A左右。这种方法在世界土未得到广泛应 用。[1]
合
、囤2三菱化成开发的铑法低压羰基 合成技术工艺流程示意图
(3)低压法又分雷普法、伊士曼技术、三菱化成
技术及戴维技术。雷普法是以丙烯、一氧化碳和水 为原料,以五羰基铁作催化剂一步合成丁醇,该法是 五十年代初由西德巴斯夫公司首次发现,并于六十 年代建设了工业化装置,之后日本也曾采用了该技 术建立了工业化装置,但由于该法只能生产丁醇,因 此没有得以推广。[3】 c.DAVY羰基合成工艺 低压羰基合成戴维技术生产丁辛醇是七十年代
万方数据
第3期 术、三菱(MCC)技术、壳牌(Shell)技术。
丁辛醇工艺技术进展及选择
21
三苯基膦为配位体,产物丁醛的正异构比为(9---8): 1。此法具有催化剂活性高、丙烯转化率高(99%以
上)、消耗定额低、反应压力低、设备少、操作维修方 便的优点。
・中压法:壳牌(Shell)技术、鲁尔一化学(Ruhv chemic)技术、三菱(MCC)铑法技术。 ・低压法:雷普法(Reppe)技术、伊士曼(East— man)技术、戴维(Davy UCC Johnson Matthey)技 术、三菱化成(MCC)技术。[2】 (1)高压法羰基合成技术是四十年代开发成功
得丁醇、丙酮及乙醇的混合物,通常的比例为6:3:
1,再经精馏得到相应产品。由于石油化工业的迅猛 发展,发酵法已很难与以丙烯为原料的羰基合成法 竞争,因此近年来已很少采用该方法生产丁辛醇产
品。从长远看,发酵法的生存取决于其原料与丙烯
的相对价格以及生物工程的发展程度。
2.3
聚氯乙烯、合成橡胶、纤维素酯的加工等。辛醇还可
73 109
t/t产品 k■h/t产品 z/t产品
8
69.2 1.6
单位能耗
2
蒸汽1.S(4.1肝)(3.5盱a)9
反应器形式
塔式(一台) 原料来源广泛: 催化剂活性好;
内装若磊主鬈譬蒸发器
原料来源广泛: 催化剂活性好l
槽式.带搅拌,两台串联 原料来源广泛: 催化剂活性高;
消耗定额低。操作消耗定额低.操作消耗定额较高。 温度、压力较高;温度,压力较高; 操作温度、压力低2
自1938年德国首先发现羰基合成技术到现在, 丁辛醇生产的工艺技术已有五、六十年的历史,是当 今最主要的丁辛醇生产技术。丙烯羰基合成生产丁 辛醇工艺过程:(1)丙烯氢甲酰化反应,粗醛精制得
到正丁醛和异丁醛;(2)正丁醛和异丁醛加氢得到产 品正丁醇和异丁醇I(3)正丁醛经缩合,加氢得到产 品丁辛醇。/-11丙烯羰基合成法又分为高压法、中压法 和低压法。该法又分为高压法、中压法和低压法,其 中主流技术专利商如下:
20
四川化工
第12卷2009年第3期
丁辛醇工艺技术进展及选择
李仕超孔艳 (兖矿国宏41,..T-有限责任公司,山东邹城,273512) 摘 要
介绍了国内外合成丁辛醇的工艺技术进展情况,包括戴维合成法、三菱化成合成法、巴斯夫合
成法等。在比较不同生产工艺路线的同时,从现有技术成熟角度和应用情况对比,提出了低压羰基
国内技术进展
国内丁辛醇技术开发中,重点在于催化剂的研
究开发。
(1)北京化工研究院研制成功丙烯低压羰基合
成铑膦络合催化剂、合成气净化催化剂和丙净化催 化剂,均在大庆和齐鲁的装置上使用多年,达到了国
外同类催化剂水平。2001年该研究院“低压羰基合
成铑一双膦催化体系研究”项目通过国家验收,采用
开发的铑一双膦配体的催化体系用于丙烯羰基合成
I芝兰墨..同.al丽.征Tilt
DAVY/IX)W的第二代西烯铑法低压羰基 合成技术一液相循环工艺流程示意图
图3
适应性.在市场变化较大的情况下,可以通过调整产 品结构的方式为企业的生存和发展赢得先机。 4
采用新一代催化剂的“UOC/DAVY MK—IV” 工艺是目前世界上最新一代丁辛醇生产工艺。其同 等规模的丁辛醇装置的投资费用和总固定成本明显 低于传统双反应釜油溶铑膦工艺,具有良好的发展 前景。目前其装置生产能力约占世界羰基合成总量 的40%,中国石化齐鲁分公于2005年建成250kt/a 装置。 d.低压羰基合成伊士曼技术 低压羰基合成伊士曼技术是1952年在德克萨 斯的研究机构发明了低压羰基合成醛的工艺,70年 代得到进一步发展,并予80年代完成商业化运营。 伊士曼技术的主要特点是产品方案灵话。可同时生 产相关醛类和醇类产品,以适应市场需求。该技术 在世界上有运行的生产装置,成熟可靠。 3