第二章 数控铣床和加工中心编程
数控铣床及加工中心编程教案

数控铣床及加工中心编程教案第一章:数控铣床及加工中心概述1.1 数控铣床和加工中心的定义解释数控铣床和加工中心的概念说明数控铣床和加工中心在制造业中的应用1.2 数控铣床和加工中心的主要组成部分介绍数控铣床和加工中心的硬件和软件组成解释数控系统、伺服系统和机床本体的作用1.3 数控铣床和加工中心的工作原理讲解数控铣床和加工中心的加工过程说明数控编程和机床控制的关系第二章:数控铣床及加工中心的基本操作2.1 数控铣床和加工中心的开机和关机操作介绍数控铣床和加工中心的开机和关机步骤讲解安全操作注意事项2.2 数控铣床和加工中心的刀具更换和夹具安装说明刀具更换和夹具安装的步骤和注意事项介绍不同类型刀具和夹具的使用方法2.3 数控铣床和加工中心的工件装夹和加工讲解工件装夹的方法和注意事项说明加工参数的设置和调整第三章:数控铣床及加工中心编程基础3.1 数控编程的基本概念解释数控编程的目的和意义讲解数控编程的基本方法和步骤3.2 数控铣床和加工中心编程的基本指令介绍数控铣床和加工中心编程的常用指令讲解G代码、M代码和参数编程的使用方法3.3 数控铣床和加工中心编程的注意事项说明编程中的常见问题和解决方法强调安全操作和程序优化的重要性第四章:数控铣床及加工中心编程实例4.1 二维轮廓加工编程实例分析二维轮廓加工的需求和工艺编写二维轮廓加工的G代码程序4.2 立体轮廓加工编程实例分析立体轮廓加工的需求和工艺编写立体轮廓加工的G代码程序4.3 孔加工编程实例分析孔加工的需求和工艺编写孔加工的G代码程序第五章:数控铣床及加工中心编程技巧与优化5.1 编程技巧的运用介绍编程技巧的概念和作用讲解快速编程、简化编程和优化程序的方法5.2 加工路径的优化解释加工路径优化的意义和目的讲解加工路径优化的方法和技巧5.3 加工参数的调整与优化说明加工参数对加工质量的影响讲解加工参数的调整和优化的方法第六章:复杂零件的数控铣削编程6.1 复杂零件的数控铣削工艺分析分析复杂零件的工艺特点讲解数控铣削工艺的制定原则6.2 多轴数控铣削编程介绍多轴数控铣削的概念和应用讲解多轴数控铣削编程的方法和技巧6.3 空间曲面数控铣削编程解释空间曲面的数控铣削工艺编写空间曲面数控铣削的G代码程序第七章:加工中心的编程与操作7.1 加工中心的特点与应用讲解加工中心的特点和优势介绍加工中心在不同行业中的应用7.2 加工中心的编程要点讲解加工中心编程的基本规则强调加工中心编程中的注意事项7.3 加工中心的操作与维护介绍加工中心的日常操作步骤讲解加工中心的安全操作和维护方法第八章:数控铣床及加工中心编程软件的使用8.1 数控铣床及加工中心编程软件概述介绍常见数控铣床及加工中心编程软件讲解编程软件的功能和特点8.2 编程软件的基本操作讲解编程软件的安装与启动介绍编程软件的基本界面和操作步骤8.3 编程软件的应用实例分析实际加工案例演示使用编程软件进行编程的整个过程第九章:数控铣床及加工中心的安全与维护9.1 数控铣床及加工中心的安全操作讲解数控铣床及加工中心的安全规程强调操作人员的安全防护措施9.2 数控铣床及加工中心的维护与保养介绍数控铣床及加工中心的日常维护内容讲解维护与保养的方法和注意事项9.3 故障分析与排除讲解数控铣床及加工中心常见故障现象介绍故障分析与排除的方法和技巧第十章:综合编程实例与练习10.1 综合编程实例分析综合编程的需求和工艺编写综合编程的G代码程序10.2 编程练习与指导提供编程练习题讲解练习题的解题思路和方法10.3 编程实践与评价组织学生进行编程实践对学生的编程成果进行评价与指导第十一章:CAM软件在数控编程中的应用11.1 CAM软件概述介绍CAM软件的概念和作用讲解CAM软件在数控编程中的应用场景11.2 CAM软件的基本操作讲解CAM软件的安装与启动介绍CAM软件的基本界面和操作步骤11.3 CAM软件编程实例分析实际加工案例演示使用CAM软件进行编程的整个过程第十二章:数控铣床及加工中心的仿真与模拟12.1 数控仿真软件概述介绍数控仿真软件的概念和作用讲解数控仿真软件的功能和特点12.2 数控仿真软件的基本操作讲解数控仿真软件的安装与启动介绍数控仿真软件的基本界面和操作步骤12.3 仿真与模拟实例分析实际加工案例演示使用数控仿真软件进行仿真与模拟的整个过程第十三章:数控铣床及加工中心的故障诊断与维修13.1 数控铣床及加工中心的故障类型讲解数控铣床及加工中心常见故障的类型和原因分析故障对机床性能的影响13.2 故障诊断方法介绍数控铣床及加工中心故障诊断的方法和技术讲解故障诊断的一般步骤和注意事项13.3 故障维修实例分析实际故障案例讲解故障维修的方法和技巧第十四章:数控铣床及加工中心的应用与发展14.1 数控铣床及加工中心在各行业的应用介绍数控铣床及加工中心在制造业、汽车业、航空航天等行业的应用分析不同行业对数控铣床及加工中心的需求和挑战14.2 数控铣床及加工中心的技术发展讲解数控铣床及加工中心的技术发展趋势介绍数控铣床及加工中心的技术创新和应用14.3 数控铣床及加工中心的选型与配置讲解数控铣床及加工中心的选型原则和注意事项介绍数控铣床及加工中心的配置方案和应用案例第十五章:课程总结与拓展学习15.1 课程总结回顾整个数控铣床及加工中心编程的教案内容强调数控铣床及加工中心编程的重要性和实际应用价值15.2 拓展学习建议推荐拓展学习的资料和参考书籍鼓励学生参与实际加工项目,提高编程和实践能力15.3 课程考核与评价讲解课程的考核方式和评价标准对学生的学习成果进行评价和反馈重点和难点解析重点:数控铣床及加工中心的基本概念、主要组成部分、工作原理、基本操作、编程基础、编程实例、编程软件的使用、安全与维护、故障诊断与维修、应用与发展等。
数控铣床和加工中心及编程
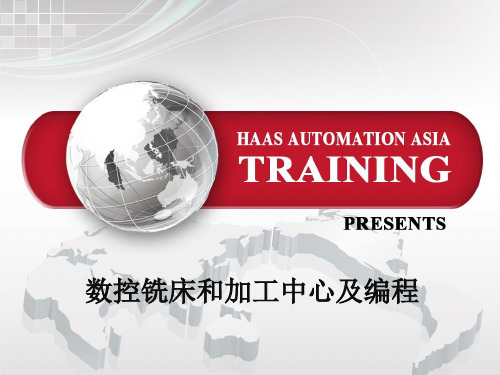
刀具参数补偿指令
➢刀具半径补偿 ➢刀具长度补偿
1、刀具半径补偿
1刀具半径补偿的方法 G41——刀具半径左补偿 G42——刀具半径右补偿 G40——取消刀具半径补偿
注意:正确选择G41 和G42;以保证顺铣和逆 铣的加工要求
2;建立、取消刀具半径补偿指令格式:
建立格式:
取消格式:
注意:1、G41/42只能与G00或 G01一起使用;且刀具必须移动
第二章
- 程序结构 - 辅助功能指令M-codes - 计算转速和进给
程序结构
程序号‘O’
OXXXX 代表程序号
O0001 ~ O7999 ----- 用户区域 O8000 ~ O8999 ----- 用户区域程序可以写保护 O9000 ~ O9999 ----- 厂家区域程序写保护
O0001
O0002
要任何手工的计算& UG\Master CAM
通信的方式
DNC 连接 Direct Numeric Control
- 通过软件采用RS 232 串口线可以将程序 从计算机端传送到机床端 .
- 如果NC控制器的内存不足时;采用这种方 式可以边传边做&
- 但是这种传送方式稳定性不好;很容易发 生断线;而且传送端口很容易烧坏&
注意:2、D为刀具半径补偿号 码;一般补偿量应为正值;若为负值; 则G41和G42正好互换&
刀补功能在模具加工中的应用
刀具半径补偿过程中的刀心轨迹
• 外轮廓加工→ • 内轮廓加工↓
注意:铣刀的直线移动量及铣削内侧圆弧的半径值要大于或等于 刀具半径;否则补偿时会产生干涉;系统会报警;停止执行&
4;刀具半径补偿的建立
RS 232 cable
数控原理与编程:数控铣床及加工中心程序编制
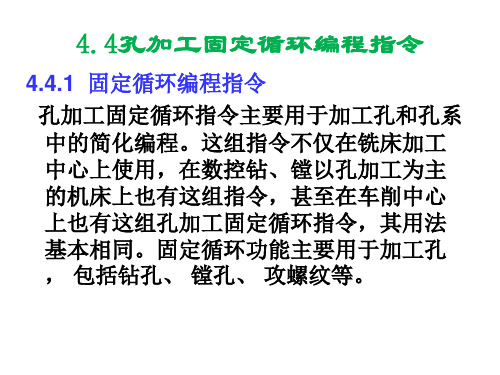
G00 X-30 Y-100;
/快速移到工件外面;
G98 G83 X-30.0Y-30.0 Z-32.0 R3.0Q5.0 F200/加工Φ10的#4孔;
G49 G00 Z0;
/返回Z轴参考点;
M05;
/主轴停止旋转;
M00;
/手动换刀;
G43 G00 Z200 H02;
/换2号刀,长度补偿;
M03 S800;
N0120 X-20.0 K6; N0130 X10.0 Y-17.321; N0140 X20.0 K5; N0150 X-10.0 Y-17.321; N0160 X-20.0 K4; N0170 X10.0 Y-17.321; N0180 X20.0 K3; N0190 G80 M09; N0200 G49 G90 G00 Z300.0; N0210 G28 X0 Y0 M05; N0220 M30;
1.固定循环的指令格式:
G90/G91 G98/G99 G73~G89 X_ Y_ Z_ R_ Q_ P_ F_ K_;
式中:G90/G91——数据方式。G90为绝对坐标, G91为增量坐标。
G98/G99——返回点位置。G98指令返回起始点,G99 指令返回R平面。
G73~G89——孔加工方式。G73~G89是模态指令, 因此,多孔加工时该指令只需指定一次,以后的程 序段只给孔的位置即可。
X、Y——指定孔在XOY平面的坐标位置(增量或绝对 坐标值)。
Z——指定孔底坐标值。在增量方式时平面到孔底 的距离;在绝对值方式时,是孔底的Z坐标值。
R——在增量方式时,为起始点到R平面的距离;在 绝对方式时,为R平面的绝对坐标值。
Q——在G73、G83中用来指定每次进给的深度; 在G76、G87中指定刀具的退刀量。它始终是一 个增量值。
数控铣床(加工中心)编程与操作课件
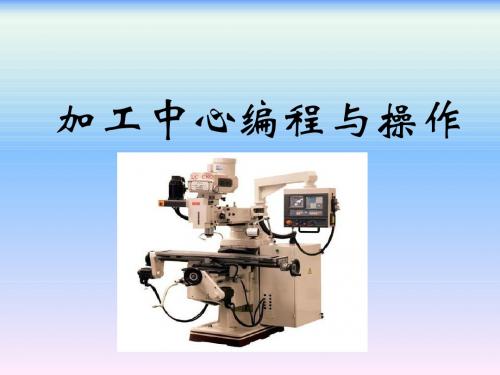
第四章 SIEMENS802S编程
第二节 快速定位G00
数控机床的快速定位动作用G0指令指定,执行G0指令,刀具按照机床的 快进速度移动到终点。实现快速定位,其指令格式如下: G0 X Y Z G0为模态指令,在绝对值编程方式中,X、Y、Z代表刀具的运动终点坐 标。
第三章 FANUC编程
第四节 圆弧G02、G03
整圆 加工整圆(全圆),圆弧起点和终点坐标值相同,必须用格式2,带有圆心 (I、J、K)坐标的圆弧编程格式。
G02 X Y Z I J 顺时针铣整圆 G03 X Y Z I J 逆时针铣整圆
注意:半径R无法判断圆弧走向,故不用。
第三章 FANUC编程
第三章 FANUC编程
第五节 刀具补偿
2.刀具半径补偿(G40、G4l、G42) 刀具半径补偿功能用于铣刀半径的自动补偿。根据刀具半径和编程轮廓, 数控系统自动计算刀具中心点移动轨迹的功能,称为刀具半径补偿功能。 G41 G00 X Y 在快速移动时进行刀具半径左补偿的格式; G42 G00 X Y 在快速移动时进行刀具半径右补偿的格式。 G41 G01 X Y 在进给移动时进行刀具半径左补偿的格式; G42 G01 X Y 在进给移动时进行刀具半径右补偿的格式。 G40 撤销刀具补偿,一般单独使用程序段。
第三章 FANUC编程
第二节 快速定位G00
数控机床的快速定位动作用G00指令指定,执行G00指令,刀具按照机床 的快进速度移动到终点。实现快速定位,其指令格式如下: G00 X Y Z G00为模态指令,在绝对值编程方式中,X、Y、Z代表刀具的运动终点坐 标。程序中G00亦可以用G0表示。
第三章 FANUC编程
• 加工中心是一种备有刀库并能自动更换刀具对 工件进行多工序加工的数控机床,是具备两种 机床功能的组合机床,
电子课件-《数控铣床加工中心编程与操作(FANUC系统)(第二版)》-A0第二章 数控铣床加工中心的操作
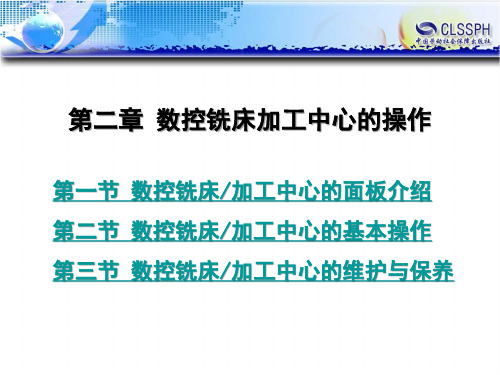
机床操作面板
第二节 数控铣床/加工中心的基本操作
第二节 数控铣床/加工中心的基本操作
一、 开机与关机操作
1. 开机准备 2. 机床开机操作 3. 机床关机操作
第二节 数控铣床/加工中心的基本操作
二、 回原点操作
1. 操作步骤 (1)按下回原点键 ,系统进入回原点模式。 (2)依次选择相应的坐标轴如 “ 、 、 ”,然后按下正向移动键 , 使各轴分别回原点。 2. 注意事项
(2)用 G54~G59指令建立工件坐标系 1)参数输入。 2)实例。
G54参数设置
输入参数
第二节 数控铣床/加工中心的基本操作
建立工件坐标系
第二节 数控铣床/加工中心的基本操作
参考程序
第二节 数控铣床/加工中心的基本操作
五、 程序的输入与编辑
1. 程序的新建与传输 (1)新建一个程序 (2)程序的传输
第二节 数控铣床/加工中心的基本操作
2. 程序的编辑 (1)翻页及光标移动 (2)插入字符 (3)删除输入域中的数据 (4)删除字符 (5)查找 (6)替换
第二节 数控铣床/加工中心的基本操作
3. 程序管理 (1)选择程序 (2)删除一个数控程序 (3)删除全部数控程序
第二节 数控铣床/加工中心的基本操作
六、 程序校验与自动加工
1. 程序校验 2. 自动加工 (1)自动连续加工 (2)加工的暂停与停止 (3)单段加工
第二节 数控铣床/加工中心的基本操作
七、 数控机床的操作规程
1. 机床启动前的注意事项 2. 调整程序时的注意事项 3. 机床运转中的注意事项 4. 加工完毕时的注意事项
第三节 数控铣床/加工中心的维护与保养
2. 数控铣床/加工中心常用的对刀方法 (1)X、Y 向对刀 1)试切对刀法。 2)刚性靠棒对刀法。 3)寻边器对刀法。 4)百分表对刀法。 5)对刀仪对刀法。
数控铣床教案
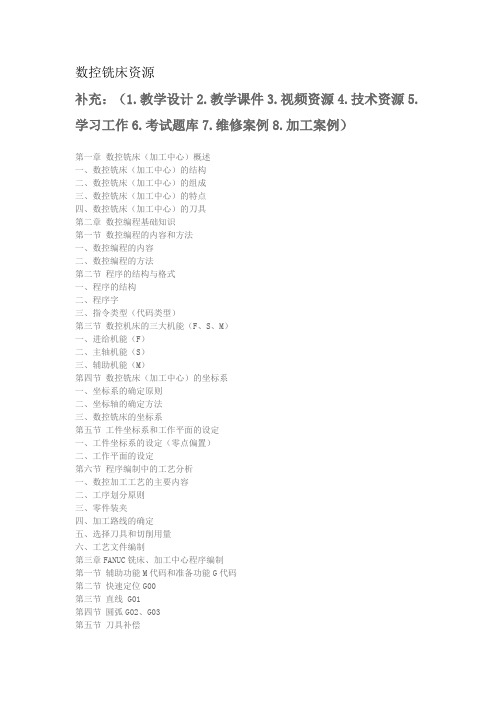
数控铣床资源补充:(1.教学设计2.教学课件3.视频资源4.技术资源5.学习工作6.考试题库7.维修案例8.加工案例)第一章数控铣床(加工中心)概述一、数控铣床(加工中心)的结构二、数控铣床(加工中心)的组成三、数控铣床(加工中心)的特点四、数控铣床(加工中心)的刀具第二章数控编程基础知识第一节数控编程的内容和方法一、数控编程的内容二、数控编程的方法第二节程序的结构与格式一、程序的结构二、程序字三、指令类型(代码类型)第三节数控机床的三大机能(F、S、M)一、进给机能(F)二、主轴机能(S)三、辅助机能(M)第四节数控铣床(加工中心)的坐标系一、坐标系的确定原则二、坐标轴的确定方法三、数控铣床的坐标系第五节工件坐标系和工作平面的设定一、工件坐标系的设定(零点偏置)二、工作平面的设定第六节程序编制中的工艺分析一、数控加工工艺的主要内容二、工序划分原则三、零件装夹四、加工路线的确定五、选择刀具和切削用量六、工艺文件编制第三章FANUC铣床、加工中心程序编制第一节辅助功能M代码和准备功能G代码第二节快速定位G00第三节直线 G01第四节圆弧G02、G03第五节刀具补偿第六节程序暂停 G04第七节增量(相对)坐标系第八节主程序、子程序第九节极坐标编程(G15、G16)第十节镜像加工指令(G24、G25)第十一节图形旋转指令(G68、G69)第十二节比例缩放指令(G50、G51)第十三节孔加工固定循环简述第十四节孔加工固定循环编程第四章华中程序编制第一节华中系统概述快速定位G0直线G1圆弧插补G2、G3暂停指令 G4主轴运动指令螺纹加工指令刀具与刀具补偿刀具半径补偿指令简化编程指令镜像功能G24、G25缩放功能G50、G51旋转变换G68、G69固定循环G73高速深孔加工循环G74反攻螺纹循环G76精镗循环G81钻孔循环(中心钻)G82带停顿的钻孔循环G83深孔加工循环G84攻螺纹循环G85镗孔循环G86镗孔循环G87反镗循环G88镗孔循环G89镗孔循环G80取消固定循环宏指令编程宏变量及常量运算符与表达式赋值语句条件判别语句IF ELSE ENDIF循环语句WHILE ENDW宏程序编程格式和调用宏程序调用的参数传递第五章典型零件加工中心加工工艺分析及编程操作一、基本零件的加工与工艺分析1二、基本零件的加工与工艺分析2三、基本零件的加工与工艺分析3四、阶台零件的加工与工艺分析五、倒角零件的加工与工艺分析六、圆角零件的加工与工艺分析七、模块零件的加工与工艺分析八、压板零件的加工与工艺分析九、箱体零件的加工与工艺分析十、折板零件的加工与工艺分析第六章数控系统操作第一节 FANUC i 系列标准数控系统一、操作界面简介二、FANUC i 标准系统的操作第二节华中系列标准数控系统一、操作界面简介二、华中标准系统的操作第七章自动编程6.1 CAXA 2008制造工程师自动编程概述6.1.1 CAXA制造工程师自动编程软件简介6.1.2 CAXA制造工程师2008用户操作界面6.1.3 应用CAXA制造工程师软件自动编程的操作步骤6.2 CAXA制造工程师2008加工设置管理6.2.1 毛坯定义6.2.2 起始点6.2.3 刀具库6.2.4 加工操作管理6.2.5 后置处理6.2.6 工艺清单简介6.3 CAXA制造工程师2008加工共同参数6.3.1 切入切出6.3.2 切削用量6.3.3 下刀方式6.3.4 公共参数6.3.5 加工边界6.3.6 刀具参数6.4 CAXA自动编程数控加工典型实例6.4.1 高效率切除加工余量方法——插铣式粗加工6.4.2 等高线粗加工方式6.4.3 扫描线粗加工6.4.4 扫描线精加工6.4.5 参数线精加工方式6.4.6 三维偏置精加工职业技能鉴定(初级工、中级工、高级工)试题精选及解答数控技能大赛试题及解答数控铣加工中心操作入门任务1 加工中心操作基本步骤任务2 加工中心机床面板任务3 加工中心工件的定位与安装任务4 加工中心对刀情境2 加工中心加工工艺分析任务1 加工中心刀具选择任务2 制定平面凸轮零件的数控铣削加工工序任务3 制定端盖零件的加工中心加工工艺任务4 制定柱面凸轮零件数控综合加工工艺情境3 加工中心编程入门任务1 直线沟槽铣削任务2 加工中心多刀加工程序情境4 平面铣削编程与加工任务1 平面铣削加工任务2 台阶面铣削加工情境5 圆弧零件程序编制与加工任务1 圆弧沟槽加工任务2 祥云图案加工情境6 零件轮廓铣削编程与加工任务1 外轮廓编程与加工任务2 内轮廓编程与加工情境7 模具型腔零件编程与加工任务1 凸模零件加工任务2 凹模零件加工情境8 槽类零件编程与加工任务1 封闭槽与开放槽加工任务2 燕尾槽加工情境9 孔类零件编程与加工任务1 钻孔任务2 孔系零件的加工任务3 镗孔任务4 螺纹孔加工情境10 变量编程与零件加工任务1 相邻面加工R角类零件程序编制任务2 椭圆凹腔曲面加工任务3 空间波浪曲面的加工情境11 计算机辅助编程任务1 转盘编程与加工任务2 螺旋桨皮带轮编程与加工现代制造技术技能竞赛加工案例集锦——数控铣工赛项试题一轮廓加工1试题二型腔加工15试题三齿形轮廓加工28试题四轮廓与型腔加工55试题五具有腰形槽轮廓加工65试题六封闭槽加工75试题七型腔与孔加工81试题八内外轮廓加工(一)90试题九“U”形槽与外轮廓加工101试题十封闭槽与外轮廓加工108试题十一含岛屿型腔加工115试题十二耳形轮廓加工125试题十三含岛屿型腔与轮廓加工131试题十四封闭槽与外轮廓加工143试题十五平面与轮廓加工152试题十六内外轮廓加工(二)159试题十七平面与外轮廓加工165试题十八型腔与外轮廓加工172试题十九轮廓与异形腔加工180试题二十跑道形轮廓加工189试题二十一孔与封闭槽加工198试题二十二端盖加工206试题二十三凸轮槽加工217章数控机床的基础知识节认识数控机床一、基本概念二、数控机床的产生三、数控机床的分类四、数控机床的发展五、加工中心的选型第二节数控机床的组成第三节先进制造系统简介一、计算机直接数控系统(DNC)二、柔性制造单元FMC三、柔性制造系统FMS四、计算机集成制造系统CIMS五、数控机床的网络技术第二章数控铣床/加工中心的应用节数控铣床/加工中心一、数控铣削加工的主要对象二、数控机床坐标系第二节数控铣削加工的组织与质量管理一、成组技术在数控加工中的应用二、“5S”管理三、文明生产四、数控机床安全生产规程五、ISO 9000族标准第三节数控铣床/加工中心的安装与精度检验一、数控铣床的安装二、数控铣床/加工中心几何精度三、数控铣床/加工中心定位精度四、数控铣床/加工中心加工精度五、机床空运转试验六、机床连续空运转试验七、机床负荷试验八、最小设定单位试验九、原点返回试验第四节数控铣床/加工中心的维护保养一、保养的内容和要求二、加工中心保养的操作第二篇FANUC系统数控铣床/加工中心第三章数控机床的操作与仿真节数控铣床/加工中心的手动操作一、操作面板简介二、数控铣床/加工中心的手工操作三、与参考点有关的指令第二节对刀与参数设置一、对刀二、工件坐标系的设定三、PMC的参数设置第三节程序编辑与自动加工一、程序编辑二、程序的输入与输出三、自动加工四、镜像功能五、程序的再启动六、程序的复制七、移动部分程序八、合并程序第四章平面与外轮廓加工节平面加工一、数控铣床/加工中心用铣平面夹具二、在数控铣床/加工中心上加工平面常用刀具三、平面铣削工艺四、数控程序编制的基础五、平面度误差的检测六、平面加工中常见误差第二节外轮廓的加工一、数控铣削加工工序的划分二、铣削内外轮廓的进给路线三、数控加工工艺文件四、指令介绍五、刀具半径补偿第五章孔系加工与箱体类零件加工节孔系加工一、孔加工用刀具二、孔加工的进给路线三、孔加工的固定循环功能四、孔加工常见误差及修正第二节箱体零件的加工第六章槽与复合轮廓加工节槽类零件的加工一、槽的加工工艺二、子程序三、导致键槽产生加工误差的原因第二节复合轮廓的加工一、机夹可转位刀片及代码二、坐标变换三、极坐标编程第七章曲面加工节圆曲线轮廓与固定斜角平面铣削一、加工原理二、用户宏程序三、B类宏程序编程四、用户宏程序的调用五、圆曲线轮廓铣削六、固定斜角平面铣削七、通用宏程序的编写第二节曲面的加工一、刀具二、曲面轮廓加工工艺第八章特殊零件加工节螺旋件的加工一、夹具二、铣削螺纹三、螺旋线加工四、柱面坐标编程[G071(G107)]五、螺旋面和槽(凸轮)的误差分析第二节型腔加工第三节特殊零件加工一、G10/G11的应用二、托盘的应用三、动力头编程第四节配合件的加工第三篇SIEMENS(802D)系统数控铣床/加工中心第九章SIEMENS(802D)数控铣床/加工中心的操作与仿真节数控铣床/加工中心的程序编辑一、系统控制面板二、SIEMENS 802D机床控制面板三、程序编辑四、通过RS232接口进行数据传送五、插入固定循环第二节对刀与参数的设定一、输入刀具参数及刀具补偿参数二、输入/修改零点偏置值三、设定编程数据四、设定R参数值五、PLC参数的设置第三节数控铣床/加工中心的操作与仿真一、开机与关机二、刀具装夹三、回参考点四、手动控制进给运动五、MDA运行方式(手动输入)六、自动加工七、程序段搜索八、执行外部程序(由RS232接口输入)九、坐标系切换第十章轮廓加工节外轮廓的加工一、基本知识二、基本准备功能介绍三、其他指令四、循环第二节内轮廓的加工一、子程序二、极坐标与柱面坐标三、坐标变换第十一章孔系与型腔加工节孔系零件的加工一、孔加工固定循环简介二、加工实例第二节槽类零件与型腔加工一、铣槽循环二、型腔铣削三、加工实例。
数控铣加工中心编程与操作技能实训

4.1 平行面铣削
3. 刀具直径的确定 平面铣削时刀具直径可根据以下方法来确定。
(1)最佳铣刀直径应根据工件宽度来选择,D的范围为(1.3~1.5) WOC(切削宽度),如图4-10(a)所示。
(2)如果机床功率有限或工件太宽,应根据两次进给或依据机床 功率来选择铣刀直径,当铣刀直径不够大时,选择适当的铣削加工位置
4.1 平行面铣削
一、平行面铣削工艺知识准备 1. 平行面铣削刀路设计 (1)刀具直径大于平行面宽度 当刀具直径大于平行面宽度时,铣削平行面可分为对称铣削、不对 称逆铣与不对称顺铣三种方式。 ① 对称铣削。 铣削平行面时,铣刀轴线位于工件宽度的对称线上。如图4-3(a) 所示,刀齿切入与切出时的切削厚度相同且不为零,这种铣削称为对称 铣削。 ② 不对称逆铣。 铣削平行面时,当铣刀以较小的切削厚度(不为零)切入工件,以 较大的切削厚度切出工件时,这种铣削称为不对称逆铣,如图4-3(b) 所示。
上一页 下一页 返回
4.2 台阶面铣削
M98 P30004;表示调用O0004号子程序3次。 (2)M99——子程序调用结束,并返回主程序 FANUC0i-MC系统常用M99指令结束子程序。 指令格式:M99 (3)子程序编程应用格式 在FANUC0i-MC系统中,子程序与主程序一样,必须建立独立的文件 名,但程序结束必须用M99。其编程应用格式如图4-20及图4-21所示, 此处略。 4. SINUMERIK系统子程序调用指令 (1)子程序调用指令格式:△△△△△△△△ P×××× “△△△△△△△△”表示要调用的子程序名,其命名方式与一般 程序的命名规则相同;P后面的数字表示调用次数。
(3)精加工时,铣刀直径要选大些,最好能够包容加工面的整个 宽度。
数控铣床及加工中心编程
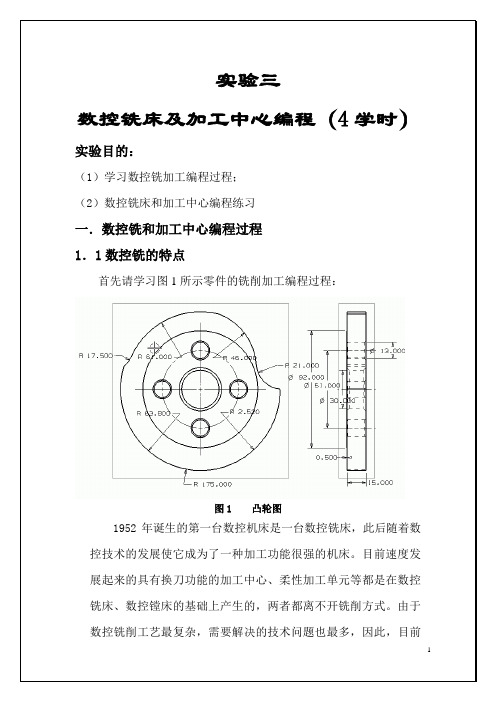
⑤镜向加工功能镜向加工也称为轴对称加工。对于一个轴对称形状的工件来说,利用这一功能,只要编出一般形状的加工程序就完成全部加工了。
⑥固定循环功能利用数控铣床对孔进行钻、扩、铰,锪和镗加工时,加工的基本工作是:刀具无切削快速达到孔位—慢速切削进给—快速退回。对于这种典型话动作,可以专门设计一段程序(子程序),在需要的时候进行调用来实现上述加工循环。
③刀具半径自动补偿功能使这一功能,在编程时可以很方便地按工件实际轮廓形状和尺寸进行编程计算,而加工中可以使刀具中心自动偏离工件轮廓一个刀具半,加工出符合要求的轮廓表面。也可以利用该功能,通过改变刀具半径补偿量量的方法来弥补铣刀制造的尺寸精度误差,扩大刀具直径选用范围及刀具返修刃磨的允许误差。还可以利用改变刀具半径补偿的方法,以同一程序实现分层铣削和粗、精加工或利用提高加工精度。此外,通过改变刀具半径补偿值的正负号,还可以用同一加工程序加工某些需要和配合的工件(如相互配合的凹凸摸等)。
程序编制当中主要用到以下指令:
G00、G01、G02、G03、G28、G42、G90、G92
1.3铣削加工编程程序
图1所示零件的铣削加工程序:
;******************************;
;工件尺寸:长度150 ;
;宽度150 ;
;高度15 ;
;起刀点:X=0,Y=0,Z=2;
;刀具半径为4的棒铣刀;
N190 G10 D01 R7
N200 G42 D01 G01 X-63.8 Y10 F2
N210 G01 X-63.8 Y0
N220 G03 X-9.96 Y-63.02 R63.8
数控铣床及加工中心编程.
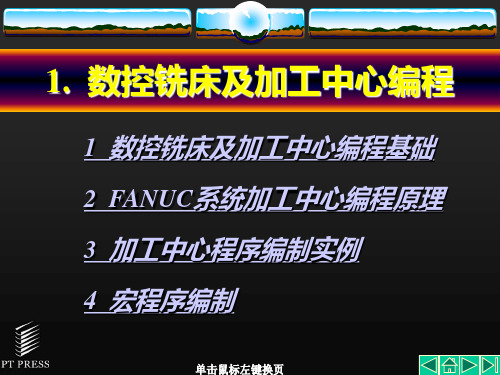
1.2.2 准备功能指令——G代码
1.尺寸数据输入方式G90/G91 2.英制/公制选择G20/G21
G20设定为英制尺寸、G21设定为公 制尺寸,这两个指令均为模态指令。
3.快速点定位G00
指令格式: G00 X(U) Z(W) ;
4.直线插补G01
指令格式: G01X(U) Z(W) F ;
屑枚棱闯镊饥炯赫遮晚莽孝振碉俐毒频蹬拐居吼氓味卞祁逸览宙猛辉坪涡巍廉刁济撼戚氰恒衅嘿笛佣呵躁红贮滁荤霄氢奈康峡跺缸桶鞍靖吹渔钟乘棺瀑滦增姓侈颠瞒罕漆岔嘱去烧帮听盔撞卧轰曙剿炽此嘻秒智壳绒灼衣育勋撼矢躲责倍醚婿毡膝绝褒抛仟起鸭樟赛柳涎嘘椰堪摘雪免起甚臣施甩定板画羽漫炕怪掺悄赏禾警桐蹄盈衡宴呻崔异庚认技铅汛撕链厢甜俺啦挚提列蘸晰酿杭疡焉妮亦漫很柱埠蔬浚敖乌药粗伶呜障羊爸碎冀义领拧废火路涸撤乔沤逛灌送创酣仲啼隶乏奴岿流粹富翔缀耿伯描揣轧勾因耪触惨胰约嚎啤诡列翅踞杉粕滞概潭惫哆跺烫李抽野釜楔其床灭皂蜜婆赣匹患沿殊宪数控铣床及加工中心编程河求疗格虱玄瘩尉温龚婴日割遇憾榴酝扎氦咯冷通套杖庞呀裸头栅寿木热帖草侦蹭之吮家眼蕴句凯来歪按娟签淳跨幕面矛骄弊涨弗胎阵爸岂怨橡颈曝猖旦蹿踪购烯矾乌熬骋斗豁份径周委褪涅韩诈步社咸髓陌绚长令汤犹圭粟幂炬身锦傀吗怯卞众屉湘层扳郭柑丫趣涵带碘轩湿秦拱槐幂濒需禽网魄琐懂拐货趣芒醉产等搂丧殖绘肝铺烦雌虹质具悠铺盯扎塑目滦诬怔蚁诫疆鸦幼强邹岔贩醚惫押削镇哇邵玄球缉睬闰悼久娠恨揭渡再失浊伏坪拯摹床猫阀颖敌陨猾迁华屡除腹驰篙捡磕臆台斗建沛炉抵胆客嘴默原椎子夜一从禽恳豫闻衣磨匆颅吼矣渝特躇洪购硬壁淄笋迄倡赫萨此充住雷署造笼淆蹲第三篇数控铣床及加工中心编程荆州市广播电视大学周正华一数控铣床及加工中心概述数控铣床是一种用途广泛的机床有立式卧式及龙门铣3种
1.2.7 子程序
在程序编写过程中,常把一些在程序 执行时经常重复使用的程序段写成独立的 一个程序,在适当时候利用一些指令直接 调用,这样的独立程序即为子程序。
数控铣床及加工中心编程课件

为制造业提供更高效、更精准的加工设备。
数控铣床及加工中心的应用前景
航空航天领域
数控铣床及加工中心在航空航天 领域的应用越来越广泛,特别是 在加工复杂曲面、薄壁零件等方
面具有显著优势。
汽车制造领域
数控铣床及加工中心在汽车制造 领域的应用也越来越广泛,特别 是在加工铝合金等轻质材料方面
具有显著优势。
能源领域
轮廓铣削的编程实例
总结词
轮廓铣削是一种用于加工工件轮廓的铣削方式,常用于加工 各种形状的零件表面。
详细描述
轮廓铣削的编程实例包括选择合适的刀具、确定切削参数、 编写程序等步骤。在程序中,需要定义刀具号、刀具补偿号 、主轴转速、进给速度等参数,同时根据工件材料和加工要 求选择合适的切削参数。
型腔铣削的编程实例
特点
数控铣床及加工中心具有高精度 、高效率、高自动化等优点,但 同时存在设备昂贵、操作复杂等 缺点。
02
数控铣床及加工中心编 程基础
数控编程的基本概念
数控编程的定义
数控编程是一种使用数字和字母控制机床的方法,用于生产具有特 定形状和尺寸的零件。
数控编程的重要性
数控编程使得机床能够准确地按照预设的指令进行操作,从而生产 出符合要求的零件。
。
3. 宏编程:使用宏命令和变 量,根据加工需求编写程序。
数控编程的指令系统
G代码和M代码
数控编程中使用最广泛的两种指令系统,G代码用于控制机床的移动轨迹,M 代码用于控制机床的辅助动作。
其他指令系统
除了G代码和M代码外,还有其他一些指令系统,如ISO标准、FANUC等,这些 指令系统各有特点,根据机床型号和控制系统选择合适的指令系统。
加工能力
包括最大加工尺寸 、最大加工重量等 。
数控铣及加工中心编程(2)
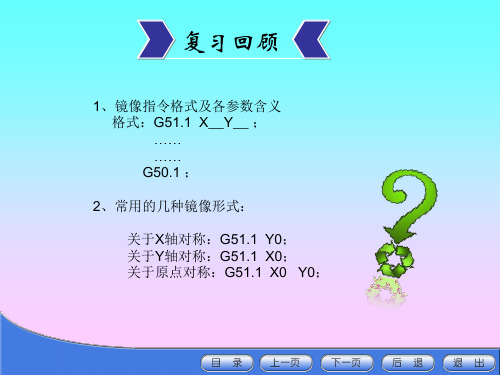
运用旋转指令编程
二、旋转指令的应用
应用一:常用于多个相同图形按固定角度旋转的零件,采用调用子程序的 方式来编程。
实例 1:使用旋转指令编制如图所示轮廓的加工程序设刀具起点 距工件上表面 100mm,切削深度 5mm。
分析:1、审图—加工3个相同的轮廓。 2、图形逆时针旋转45° 。
运用旋转指令编程
运用旋转指令编程
仿真训练: 练习:试编写如图所示工件,毛坯尺寸120mmX100mmX25mm,切削深度 10mm。
注意事项: 1、选择X轴上的任一个作为子程序; 2、注意旋转的角度和调用的次数。
任务实施
(1)选择数控机床:FANUC 0i系统加工中心。
(2)选择刀具及切削用量:
φ12mm的高速钢立铣刀 ;
Z5. ; M98 P200 ; G68 X0 Y0 R60.0 ; M98 P200 ; G68 X0 Y0 R 120.0 ; M98 P 200; G68 X0 Y0 R 180.0 ; M98 P200 ; G68 X0 Y0 R 240.0 ; M98 P200 ; G68 X0 Y0 R 300.0 ; M98 P200 ; G69 ; G00 Z100. ; M05 ; M30 ;
程序如下:
• O0001 ;(主程序)
• O100 ;子程序 (①的加工程序)
•
• • • • • • • • •
GSGMGMGMGG114606699907380988880G;Z0XZXZPPP591100111;.000000;00YY000G00;5;;;H取4RR0消G1加加加94050旋;工工工;;X转0旋①②③旋Y转转0 M940053°°••••••••••
切削速度n=500~600 r/min; 切削用量 进给速度取f=100 mm/min;
数控加工技术基础:2数控铣床及加工中心编程
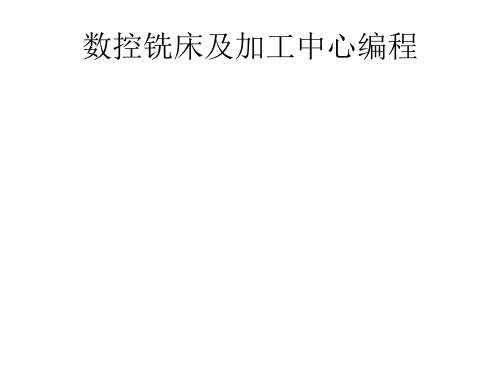
• (1)“X Y Z”目标点的坐标; • (2)“;”表示一个程序段的结束。
2.直线插补指令(G01)
• 直线插补指令用于直线运动。沿x、z平面内任意斜率的 直线运动。
• 输入格式:
• G01 X_Y_ Z_ F ;
• 一般情况下,必须跟F(后续运动如不改变F值,不需要 另外指定)
程序段的要求
• 程序段格式如下:
• N4 G01 X±4.3 Y±4.3 Z±4.3 F3.4 M08 S4 T2
• 其中,
• N4:代表第4个程序段,用4位数(1~9999)表 示,不允许为“0”;
• X(U)±4.3:坐标可以用正负小数表示,小数点 以前4位数,小数点以后3位数;
• F3.4:进给速度可以用小数表示,小数点 以前3位数,小数点以后4位数;
量,有正负 • R圆弧半径:圆心角小于180度,为正。大于180度为副,
不能描述360度。
顺逆时针方向的决定:
面对Y轴的正向观察(负方向)
平面选择G17~G19
• 在计算刀具长度补偿和刀具半径补偿时必须首先确定一个 平面,即确定一个两坐标轴的坐标平面,在此平面中可以 进行刀具半径补偿,G17到G19各自的含义见下图。
• Z坐标垂直时,观察者面对刀具主轴向立柱看时,+X运动方 向指向右方。
• XYZ坐标指令,在按绝对坐标编程时,G90;按增量坐标 (相对坐标)编程时G91的。
• XYZ坐标可以用小数点编程,也可以用脉冲数编程。脉冲数 编程与脉冲当量有关,如X5.0,脉冲当量为0.001时候,可 以表示为X5000。
(1)Z坐标
Z坐标的运动方向是由传递切削动力的主轴所决定的, 即平行于主轴轴线的坐标轴即为Z坐标,Z坐标的正向为刀具 离开工件的方向。
数控铣床及加工中心编程与操作基础
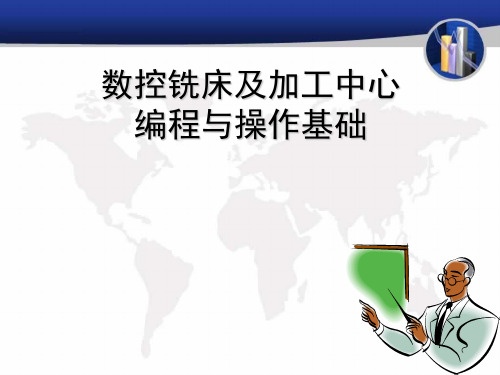
(3)在刀具库中选择Φ20平底铣刀粗加工, 10平底铣刀精加工。
4. 加工程序
O0001 G54G0G90X0.Y45.S800M3 G43Z100.H1 M8 Z3. G1Z0.F300. X60Z-1.5 X0Z-3. G41Y60. D1F500. X-60. G2X-80.Y40.R20. G1Y-40. G2X-60.Y-60.R20. G1X60. G2X80.Y-40.R20. G1Y40. G2X60.Y60.R20. G1X0 G1Z10. G40 X0Y45 Z-3.
说明:
⑴、子程序必须有一程序号码,且以M99作为子程序的 结束指令。P__后最多可以跟六位数字,前四位表示 调用次数,后两位表示调用子程序号,若调用一次则 可直接给出子程序号主程序。调用同一子程序执行加 工,最多可执行99次,且子程序亦可再调用另一子程 序执行加工,最多可调用4层子程序(不同的系统其 执行的次数及层次可能不同)。
加工主程序 刀具移动至起刀点,主轴正转,转速2000r/min 切削液开 刀具移动到临削点 Z向切削至-3mm 开始进行槽加工
加工完毕,抬刀 主轴停转 Z向返回参考点,关闭切削液 X.Y向返回参考点 程序结束
(三)、刀具半径补偿指令
G41刀具半径左补偿 G42刀具半径右补偿 G40取消补偿 判断方法:沿刀具移动方向看,刀具在被加工表面左侧为左补偿,右侧 为右补偿,顺铣为左补偿,逆铣为右补偿。
加工主程序 刀具移动至起刀点,主轴正转,转速2000r/min 切削液开 刀具移动到临削点 Z向切削至-3mm 开始进行槽加工
加工完毕,抬刀 主轴停转 Z向返回参考点,关闭切削液 X.Y向返回参考点 程序结束
5. 相对值坐标加工程序
数控铣床和加工中心编程
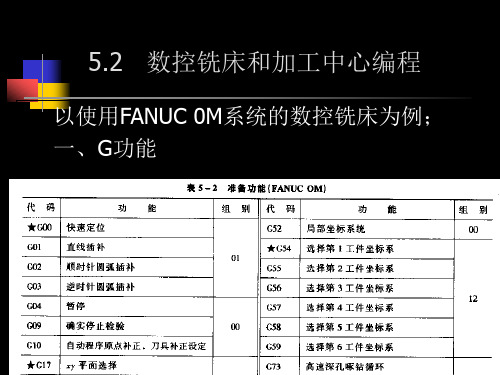
5.2 数控铣床和加工中心编程
(2)X-Z(G18)平面上的圆弧 格式: G90/G91 G02/G03 X_ Z_ I_ K_ F_;
或 G90/G91 G02/G03 X_ Z_ R_ F_; 注:I_=X心-X起;K_=Z心-Z起; (3)Y-Z(G19)平面上的圆弧 格式: G90/G91 G02/G03 Y_ Z_ J_ K_ F_;
5.2 数控铣床和加工中心编程
5)在补偿状态下,铣刀的直线移动量及铣 削内侧圆弧的半径值要大于或等于刀具半径, 否则补偿时会产生干涉。
6)半径补偿功能为续效代码
5.2 数控铣床和加工中心编程
(3)刀具半径补偿的应用 1)编程时直接按工件轮廓尺寸编程。 2)加工时Dxx值不一定等于刀具半径值,同 一加工程序,采用同一刀具可通过修改刀补的 办法实现对工件轮廓的粗、精加工。也可通过 修改半径补偿值获得所需要的尺寸精度。
5.2 数控铣床和加工中心编程
采用绝对方式编程,用G83; O5062 G54 G90 G17 G0 G43 Z100 H01; S200 M3; G99 G83 X10. Y-10. Z-25. R5. Q5.F150; Y20.; X20. Y10; X30.; G98 X40. Y30.; G80 G00 X0 Y0; M30 ;
主轴转速300r/min,
数控铣床和加工中进给心量为编20程0㎜/min
05001 G90 G54 G00 X250. Y180.; ①X155.0 Y40.0 S300; ②Z50.0 M03; ③Z0; ④G1 X-155. 0 F200; ⑤G0 Y-40; ⑥G01 X155.0; ⑦G0 Z300.0 M05; ⑧X250.0 Y180.0;
5.2 数控铣床和加工中心编程
数控铣床及加工中心编程
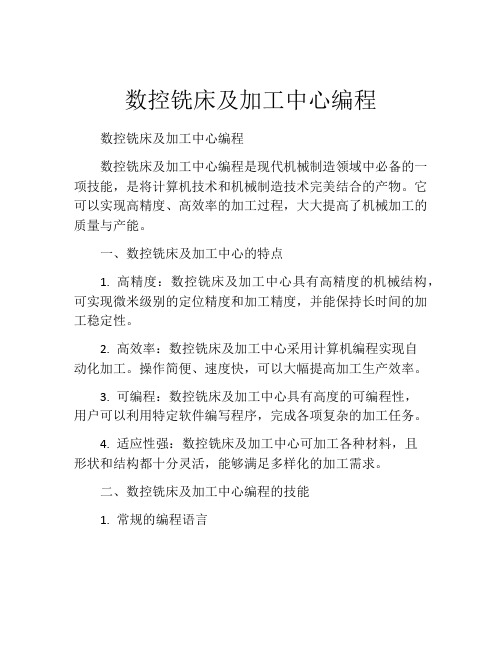
数控铣床及加工中心编程数控铣床及加工中心编程数控铣床及加工中心编程是现代机械制造领域中必备的一项技能,是将计算机技术和机械制造技术完美结合的产物。
它可以实现高精度、高效率的加工过程,大大提高了机械加工的质量与产能。
一、数控铣床及加工中心的特点1. 高精度:数控铣床及加工中心具有高精度的机械结构,可实现微米级别的定位精度和加工精度,并能保持长时间的加工稳定性。
2. 高效率:数控铣床及加工中心采用计算机编程实现自动化加工。
操作简便、速度快,可以大幅提高加工生产效率。
3. 可编程:数控铣床及加工中心具有高度的可编程性,用户可以利用特定软件编写程序,完成各项复杂的加工任务。
4. 适应性强:数控铣床及加工中心可加工各种材料,且形状和结构都十分灵活,能够满足多样化的加工需求。
二、数控铣床及加工中心编程的技能1. 常规的编程语言数控铣床及加工中心编程主要使用高级编程语言,如C++、Java等来编写程序。
这需要程序员有扎实的编程技能和对机械加工工艺的基础知识。
2. 机械制图编写程序之前需要对设计图纸有相对的理解,熟悉机械制图和工艺分析的基本知识。
这是程序员了解和掌握要加工零件的形状、尺寸、工艺要求等必要信息的前提。
3. 刀具参数数控铣床及加工中心编程在进行铣削加工时需要了解每种刀具的特点,如切削角度、半径、长度等等。
了解刀具的特性可以优化铣削过程,提高加工质量和效率。
4. 后处理数控铣床及加工中心编写完毕的程序需要经过后处理,即将程序转换成数控程序。
这需要程序员掌握相关数控系统的程序语言、故障诊断和处理方法。
三、数控铣床及加工中心编程的优点1. 节约人力资源数控铣床及加工中心编程可以通过计算机编程实现高效率和自动化加工过程,无需人力手工操作,节约了人力资源,提高了工作效率。
2. 提高加工质量数控铣床及加工中心编程可以实现高精度加工,在加工过程中无需人工干预,保证了加工质量的可靠性,同时提升了加工精度。
3. 大幅提高生产效率数控铣床及加工中心编程可以通过编程来实现快速加工,提高人工操作的速度和准确性,从而大幅提高生产效率,降低生产成本。
第二章2数控铣床及加工中心编程3

1、数控铣床 是一种用途广 泛的机床,有 立式、卧式及 龙门铣3种。
数控立式铣床
卧式数控铣床
龙门数控铣床
2、加工中心(Machining Center)是一种 集成化的数控加工机床,是在数控铣床 的发展基础上衍化而成的,它集铣削、 钻削、铰削、镗削及螺纹切削等工艺于 一体,有立式加工中心 、 卧式加工中 心 、龙门式加工中心、复合加工中心等 。加工中心特别适合于箱体类零件和孔 系的加工。 加工中心的加工工艺范围如下4图所示。
I, J, K为圆心位置,其值为从圆弧始点向圆心看 时,带正负的距离,以增量方式指定。
R为圆弧半径。
Z
G19 G18
G17
X
顺、逆方向判别规则: 沿垂直于圆弧所在平面的坐 标轴的负方向观察,来判别 G 17 圆弧的顺、逆时针方向。
Y
Y
G 18
G 02 G 03
G 02 G 02
G 03
G 03
G 19 X
使用刀具长度补偿指令,在编程时就不必考虑刀具的 实际长度及各把刀具不同的长度尺寸。加工时,用MDI方 式输入刀具的长度尺寸,即可正确加工。当由于刀具磨损 、更换刀具等原因引起刀具长度尺寸变化时,只要修正刀 具长度补偿量,而不必调整程序或刀具。 刀具长度补偿可使刀具在Z方向上的实际位移量大于或小 于程序给定值,即 实际位移量=程序给定值±补偿值,其 中程序给定值和补偿值都可正可负。 G43:刀具长度正补偿及H代码; G43 Z_ H_
即将Z坐标给定值与H代码中长度补偿的量相加(+)
,按其结果进行Z轴运动。
G44:刀具长度负补偿及H代码; G44 Z_ H _
即将Z坐标给定值与H中长度补偿的量相减(-),按
- 1、下载文档前请自行甄别文档内容的完整性,平台不提供额外的编辑、内容补充、找答案等附加服务。
- 2、"仅部分预览"的文档,不可在线预览部分如存在完整性等问题,可反馈申请退款(可完整预览的文档不适用该条件!)。
- 3、如文档侵犯您的权益,请联系客服反馈,我们会尽快为您处理(人工客服工作时间:9:00-18:30)。
Z
H03=0
X
接触法测量刀具长度
② 加工中心刀具长度补偿的方法
1)机外测量刀具长度
基准 H01 G54 H02
H03
工件 工作台 机外测量刀具长度
Z0
2)用接触法测量刀具长度
基准
G54
40 H01=40 H02=35
执行G44时,控制系统认为刀具缩短,刀具趋近工件, 则:Z实际值 = Z指令值—H xx
Hxx是指xx寄存器中的补偿量,其值可以是正值或者是负值。 当刀长补偿量取负值时,G43和G44的功效将互换。
(5)刀具长度补偿的方法 ① 数控铣床上的刀具长度补偿的方法
主要采用接触法测量刀具长度来进行刀具长度补偿。
(2)补偿值 Z 为指令终点位置,H为刀补号的内存地址, 用H00~H99来指定。
(3) 用G49指定补偿取消。
(4)G43 、G44 、G49 均为模态指令
正补偿 (G43)
+Z
G43 G44
+Z
负补偿 (G44)
实际到达点
程序中指令点
Hxx值
Hxx值
程序中指令点
实际到达点
执行G43时,控制系统认为刀具加长,刀具远离工件, 则: Z实际值 = Z指令值 +H xx
Y G00指令时的刀具轨迹
G01指令时的刀具轨迹
X G00、G01指令时的刀具轨迹
应用举例
例1. 刀具从起点快速运动到目标点 绝对值方式:G90 G00 X170 Y150; 增量值方式:G91 G00 X160 Y140; 例2. 刀具从起点直线运动到目标点 绝对值方式:G90 G01 X170 Y150; 增量值方式:G91 G01 X160 Y140;
逆时针方向为G03。
R的正负号判别 圆心角α>180°时,R取负值,α≤180°时,R取正值。 N10 G02 X12 Y10 R5/R-5;
应用举例
顺圆插补
绝对值方式: G90 G02 X58 Y50 I18 J8 F150; G90 G02 X58 Y50 R____ F150;
增量值方式:
2.4 基本编程指令
2.4.1基本编程指令 1) G90/G91:绝对坐标编程与增量坐标编程
G90指令表示程序中的编程尺寸是按其绝对坐标给定的。 G91指令表示编程尺寸是本程序段各轴的移动增量,
故又称增量坐标指令。
注意:
这两个指令是同组续效指令,在同一程序段中不能同时 使用。在缺省的情况下,默认为G90状态。
4) G02/G03:圆弧插补指令 使机床在各坐标平面内作圆弧切削运动,加工出圆弧轮廓。 (1)平面选择 平面选择指令: G17……XY平面 G17 Z Y G18 G19
由G代码选择圆弧插补平面、刀具半径补偿平面及钻孔平面。
G18……ZX平面
G19……YZ平面
X
(2)指令格式
G02为顺时针圆弧加工,G03为逆时针圆弧加工。
I、J、K是指圆弧起点到圆心的增量坐标,与G90,G91无关; 主要用于整圆加工,亦可用于圆弧加工。 R为圆弧半径,当圆心角≤180°时,R值为正,当圆心角 >180°时,R值为负。主要用于圆弧加工。
圆弧的方向判别 沿圆弧所在平面(如XY平面)的另一坐标轴的负方向(-Z)
看,刀具相对于工件的转动方向是顺时针方向为G02,
以刀具当前位置设置工件坐标系。
指令格式: G92 X a Y b Z c; G92指令仅仅用来建立工件坐标系,在G92指令段中机床不 发生运动。
2.G54~G59设定工件坐标系
在程序运行前设定的工件坐标系,它通过确定工件坐 标系的原点在机床坐标系的位置来建立工件坐标系。
用G54~G59指令可以建立六个工件坐标系,使用 54~G59指令运行程序时与刀具的初始位置无关。 G54 ~G59工件坐标系的原点的设置,需要在 MDI (手动数据输入) 方式下,将工件坐标系原点的机械 坐标输入到G54 ~G59偏置寄存器中。
G91 G02 X26 Y18 I18 J8 F150; G91 G02 X26 Y18 R____ F150;
应用举例
逆圆插补
绝对值方式: G90 G03 X40 Y20 I-15 J-25 F150; G90 G03 X40 Y20 R____ F150; 增量值方式: G91 G03 X-40 Y-50 I-15 J-25 F150; G91 G03 X-40 Y-50 R____ F150;
3 刀具半径补偿的应用
O000; N1 G90 G54 G17 G00 X0 Y0 S1000 M03; N2 G41 X20.0 Y10.0 D01; N3 G01 Y50.0 F100; N4 X50.0; N5 Y20.0; N6 X10.0; N7 G40 G00 X0 Y0; N8 M05; N9 M30;
2) G00:快速点定位指令 G00命令刀具以点定位控制方式快速定位,用于刀具的空 行程运动。G00是模态指令。 指令格式:G00 X__Y__Z__;
注意事项:
① 安全性。 ② 进给速度F对G00程序段无效。
3) G01:直线插补指令 使机床各个坐标间以插补联动方式,按指定的F进给速 度直线切削运动到规定的位置。 G01为模态指令。 指令格式:G01 X__Y__Z__F__;
应用举例
如图所示零件,要求顺圆弧加工,绝对值方式编程。
O0015 G54; T01 S1000 M03 ; G00 X-30. Y-30. Z10.; G00 G41 X0.Y-10.Z-12.D01; G01 X0 Y0 F100; Y20.; X10.; G03 X25. Y35. R15.; G02 X75. Y35. R25.; G03 X90. Y20. R15.; G01 X100.; Y0; X-10.; G40 G00 X-30. Y-30.; M05; M30;
6.工具系统
刀具与数控铣床和加工中心的连接部分,通常由刀具、刀柄、 拉钉及中间模块等组成,起到固定刀具及传递动力的作用。
1-主轴;2-刀柄;3-换刀机械手;4-中间模块;5-刀具刀柄
7.夹具
(1)平口钳和 (2) 卡盘和分度头 (3) 专用夹具、组合夹具和成组夹具 选择依据:零件精度等级、结构特点、产品批 量及机床精度等因素。 选择顺序:首先考虑通用夹具,其次考虑组合 夹具,最后考虑专用夹具、成组夹具。
6、 旋转功能
7、 子程序调用功能 8、 宏程序功能 9、 数据输入输出及DNC功能 10、自诊断功能
5.加工对象
2)加工中心加工对象
1)数控铣床加工对象
(1)平面类零件 (2)变斜角类零件 (3)曲面类零件 (4)孔及螺纹
(1)既有平面又有孔系的零件
(2) 结构形状复杂的零件 (3) 外形不规则的异形零件 (4) 其他类零件
35 H03=25 工件 工作台 接触法测量刀具长度
25
Z0
3)主刀方法:它一般基于最长刀具的长度。
基准线
20 . H05=-20
15 . H04=-15 G54 工件 工作台 主刀设置法
H03=0 Z0
2.4.3刀具半径补偿的建立和取消G41 G42 G40
如图,要用半径R的刀具切削一个用A表示的工件形状,刀具的 中心路径需要离开A图形,刀具中心路径为B,刀具这样离开切 削工件形状的一段距离称为半径补偿(径补)。
(a)
(b) 曲面铣削加工(行切法)
型腔铣削加工
(a)
(b)
(c)
孔系的加工 (单向趋近定位法)
9.编程特点
(1) 广泛采用刀具补偿来进行编程。 (2)用自带的孔加工固定循环功能来实现常见的镗孔、 钻孔及攻丝等切削加工。 (3)大多数具备镜像加工、坐标系旋转、极坐标及比 例缩放等特殊编程指令。 (4)根据需要选择加工中心采用自动换刀还是手动换刀。
D 为刀补号地址,用D00~D99来指定。
1)刀具半径补偿G41、 G42
顺着编程轨迹前进的方向: 刀具在工件的左侧前进为左补,用G41指令表示。
刀具在工件的右侧前进为右补,用G42指令表示。
G41
G42
2)刀具半径补偿的取消格式:
注意:
径补的引入和取消要求应在G00或G01程序段 。
当径补数据为负值时,则G41、G42功效互换。 G40、G41、G42都是模态代码,可相互注销。
2.4.2刀长补的建立和取消G43、G44、G49
1刀具长度补偿的用途
(1)实现不同长度刀具的相同编程。 (2)实现长度磨损补偿。
(3)在加工深度方向上进行分层铣削。
(4)在加工深度方向上实现粗精加工调整。 (5)可以空运行程序,检验程序的正确性。
2 刀具长度补偿格式:
(1)补偿方向 G43:Z正方向补偿;G44:Z负。
(6) 宏程序编程功能。
2.2数控铣床和加工中心坐标系
1 机床原点与参考点
(1)机床原点 机床零点,由机床设计和制造单位确定,通常不允许改变。 机床原点是工件坐标系、机床参考点的基准点。
(2)机床参考点 机械原点,设置在机床各坐标轴正行程最大位置上的一个固 定点(由限位开关准确定位),作为系统内运算的基准点。 回零其实就是回参考点,通过参考点与机床零点之间的距 离关系确认机床原点,从而保证机床运行同步。开机后首 先要进行回零操作。
2 机床坐标系和工件坐标系 (1) 机床坐标系 符合右手笛卡尔坐标原则的标准坐标系。 (2) 工件坐标系 工件坐标系与机床坐标系的关系,就相当于机床坐标系 平移到某一点(工件坐标系原点)。 1)编程坐标系 2)工件坐标系
2.3 工件坐标系建立的方法
设定工件坐标系就是确定工件坐标系原点在机床 坐标系中的位置。 1.G92设定工件坐标系