可靠性试验设计与分析1
可靠性设计与分析报告

可靠性设计与分析报告1. 引言可靠性是一个系统是否可以在适定的时间内、在适定的条件下,按照既定的功能要求,以期望的性能运行的能力。
在设计与开发软件、硬件以及其他复杂系统时,可靠性设计是至关重要的一环。
可靠性分析则是评估系统的可靠性,识别潜在的故障点并提出相应的改进方案。
本报告将重点讨论可靠性设计与分析的一些重要概念和方法,并对一个实际的系统进行分析,提出可能的优化建议。
2. 可靠性设计的原则在进行可靠性设计时,需要考虑以下几个原则:2.1. 冗余设计冗余设计是通过增加系统中的备用部件来提高系统的可靠性。
常见的冗余设计包括备份服务器、硬盘阵列、双机热备等。
冗余设计可以在一个组件发生故障时,自动切换到备用组件,从而避免系统的停机损失。
2.2. 容错设计容错设计是通过在系统中加入错误处理机制,在出现错误时可以尽量保证系统的正常工作。
容错设计可以包括错误检测、错误恢复、错误传递等。
例如,在软件开发中,可以使用异常处理来处理可能出现的错误情况,从而避免程序崩溃。
2.3. 系统监测系统监测是通过对系统运行时的状态进行实时监测,及时发现并处理可能的故障。
监测可以包括对硬件设备的状态监测、对软件运行的监测等。
通过系统监测,可以及时采取相应的措施,防止故障进一步扩大。
3. 可靠性分析方法可靠性分析是评估系统可靠性的一项重要工作。
以下将简要介绍一些常用的可靠性分析方法:3.1. 故障模式与影响分析(FMEA)故障模式与影响分析是一种通过分析系统的故障模式和故障后果,评估系统可靠性的方法。
通过对系统中各个组件的故障模式及其对系统的影响进行分析,可以确定系统的关键故障点,并提出相应的改进措施。
3.2. 可靠性指标分析可靠性指标分析是通过对系统的各项指标进行分析,评估系统的可靠性水平。
常见的可靠性指标包括平均无故障时间(MTTF)、平均修复时间(MTTR)、故障率等。
通过对这些指标进行分析,可以判断系统是否满足要求,以及提出相应的改进措施。
计算机网络可靠性分析与设计(1)
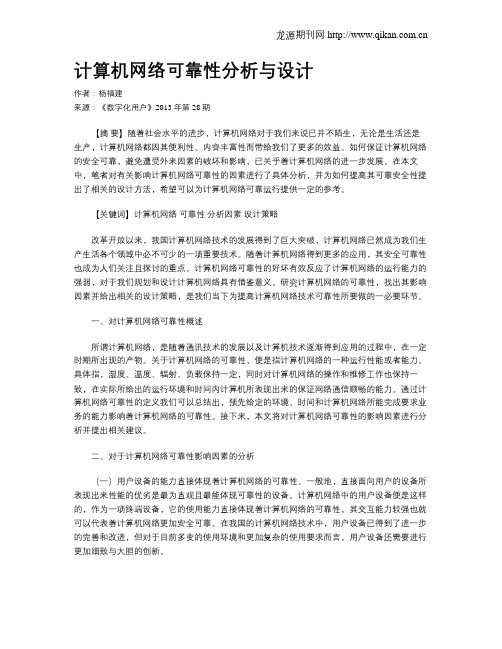
计算机网络可靠性分析与设计作者:杨福建来源:《数字化用户》2013年第28期【摘要】随着社会水平的进步,计算机网络对于我们来说已并不陌生,无论是生活还是生产,计算机网络都因其便利性、内容丰富性而带给我们了更多的效益。
如何保证计算机网络的安全可靠,避免遭受外来因素的破坏和影响,已关乎着计算机网络的进一步发展。
在本文中,笔者对有关影响计算机网络可靠性的因素进行了具体分析,并为如何提高其可靠安全性提出了相关的设计方法,希望可以为计算机网络可靠运行提供一定的参考。
【关键词】计算机网络可靠性分析因素设计策略改革开放以来,我国计算机网络技术的发展得到了巨大突破,计算机网络已然成为我们生产生活各个领域中必不可少的一项重要技术。
随着计算机网络得到更多的应用,其安全可靠性也成为人们关注且探讨的重点。
计算机网络可靠性的好坏有效反应了计算机网络的运行能力的强弱,对于我们规划和设计计算机网络具有借鉴意义。
研究计算机网络的可靠性,找出其影响因素并给出相关的设计策略,是我们当下为提高计算机网络技术可靠性所要做的一必要环节。
一、对计算机网络可靠性概述所谓计算机网络,是随着通讯技术的发展以及计算机技术逐渐得到应用的过程中,在一定时期所出现的产物。
关于计算机网络的可靠性,便是指计算机网络的一种运行性能或者能力。
具体指,湿度、温度、辐射、负载保持一定,同时对计算机网络的操作和维修工作也保持一致,在实际所给出的运行环境和时间内计算机所表现出来的保证网络通信顺畅的能力。
通过计算机网络可靠性的定义我们可以总结出,预先给定的环境、时间和计算机网络所能完成要求业务的能力影响着计算机网络的可靠性。
接下来,本文将对计算机网络可靠性的影响因素进行分析并提出相关建议。
二、对于计算机网络可靠性影响因素的分析(一)用户设备的能力直接体现着计算机网络的可靠性。
一般地,直接面向用户的设备所表现出来性能的优劣是最为直观且最能体现可靠性的设备。
计算机网络中的用户设备便是这样的,作为一项终端设备,它的使用能力直接体现着计算机网络的可靠性,其交互能力较强也就可以代表着计算机网络更加安全可靠。
电子产品可靠性设计与试验技术及经典案例分析

电子产品可靠性设计与试验技术及经典案例分析课程背景――为什么我们的产品设计好了,到了用户(现场)却返修率很高?――如何为客户提供有力的可靠性指标证据?MTBF的真正含义是什么?――MTBF与可靠度、失效率、Downtime 的关系如何?提高可靠真的降低返修率?――为何功率管在没超额定功率时仍然烧毁?――塑封集成电路为何有防潮要求?――如何开展热设计?――如何开展降额设计?――如何开展电路可靠性设计,例如继电器用在电路中,是否有潜在通路?CMOS电路真的省电吗?――如何开展加速寿命试验?――如何权衡试验应力?对于企业领导和研发工程师而言,诸如此类的问题可谓太多,尽快明白可靠性的指标和基本原理,使设计人员掌握一些可靠性设计技能,是我们迫切需要研究和解决的重大课题。
目前很多企业工程师在这方面缺乏实践经验,很多相关知识都是网络和书籍上面了解,但是,一方面在解决实际问题时光靠这些零散的理论是不足的,另一方面,这些“知识”也有可能对可靠性的实质理解造成误解,为帮助企业以及研发人员解决在实际产品设计过程中遇到的问题与困惑,我们举办此次《电子产品可靠性设计与试验技术及经典案例分析》高级训练班,培训通过大量的实际产品可靠性案例讲解,使得学员可以在较短时间内掌握解决可靠性技术问题的技能并掌握可靠性设计的基本思路!同时对企业缩短产品研发周期、降低产品研发与物料成本具有重要意义!======================================================================================课程特色---系统性:课程着重系统地讲述产品可靠性设计和试验的原理,产品可靠性设计的主要方法,产品常见的故障模式及其预防方法,课程以大量的案例来阐述产品可靠性设计的思路与方法,以及可靠性工作重点、工作方法、解决问题的技巧。
---针对性:主要针对电子产品可靠性设计和测试项目,及各种典型产品出现的不同问题时候的解决思路与方法。
机械设计中的可靠性建模与分析

机械设计中的可靠性建模与分析随着科技的不断发展,机械设计在各个领域中扮演着重要的角色。
无论是汽车、航空、船舶还是家电,机械设计的可靠性都是至关重要的。
在设计过程中,可靠性建模与分析对于保障产品质量和性能至关重要。
本文将探讨机械设计中的可靠性建模与分析方法,以及其在实际应用中的意义。
1. 可靠性概念与指标可靠性是指产品在预定条件下,在一定时间内完成特定功能的能力。
在机械设计中,可靠性是评估产品寿命和正常运行时间的重要指标。
常用的可靠性指标包括故障率、平均寿命、失效率等。
故障率是指在单位时间内产品发生故障的概率;平均寿命是指产品从生产到终止使用所经历的时间;失效率是指在单位时间内产品失效的概率。
2. 可靠性建模方法在机械设计中,可靠性建模是衡量产品可靠性的重要手段之一。
常用的可靠性建模方法包括状态空间模型、Markov模型、故障树分析等。
其中,状态空间模型是最常用的一种建模方法,它将系统状态用状态变量表示,通过状态转移概率描述系统状态的变化过程。
Markov模型则是一种基于状态转移概率描述系统状态变化的方法,它适用于状态离散、状态转移概率恒定的系统。
而故障树分析则是一种通过概率逻辑关系构建系统失效的一种方法,它能够分析系统失效的原因和概率。
3. 可靠性分析方法除了可靠性建模方法外,可靠性分析方法也是评估产品可靠性的重要手段之一。
常用的可靠性分析方法包括可靠性数据分析、故障模式与影响分析、可靠性试验等。
可靠性数据分析通过统计搜集的故障数据,分析故障模式和失效率,从而评估产品的可靠性。
故障模式与影响分析则是通过对产品的设计、制造和使用环节进行分析,确定可能出现的故障模式和相应的影响,从而提出改进措施。
而可靠性试验则是通过对产品进行加速寿命试验或可靠性验证试验,评估产品的可靠性水平。
4. 可靠性建模与分析的意义机械设计中的可靠性建模与分析在实际应用中具有重要的意义。
首先,它可以帮助设计人员评估产品的可靠性水平,为产品的改进和优化提供依据。
汽车零部件的可靠性设计与验证方法研究
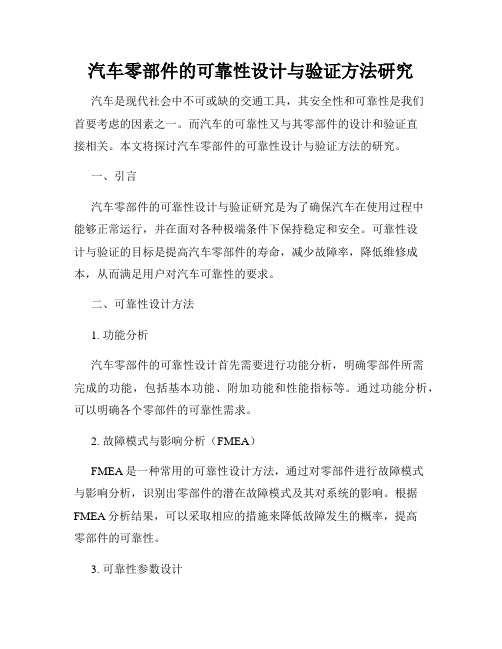
汽车零部件的可靠性设计与验证方法研究汽车是现代社会中不可或缺的交通工具,其安全性和可靠性是我们首要考虑的因素之一。
而汽车的可靠性又与其零部件的设计和验证直接相关。
本文将探讨汽车零部件的可靠性设计与验证方法的研究。
一、引言汽车零部件的可靠性设计与验证研究是为了确保汽车在使用过程中能够正常运行,并在面对各种极端条件下保持稳定和安全。
可靠性设计与验证的目标是提高汽车零部件的寿命,减少故障率,降低维修成本,从而满足用户对汽车可靠性的要求。
二、可靠性设计方法1. 功能分析汽车零部件的可靠性设计首先需要进行功能分析,明确零部件所需完成的功能,包括基本功能、附加功能和性能指标等。
通过功能分析,可以明确各个零部件的可靠性需求。
2. 故障模式与影响分析(FMEA)FMEA是一种常用的可靠性设计方法,通过对零部件进行故障模式与影响分析,识别出零部件的潜在故障模式及其对系统的影响。
根据FMEA分析结果,可以采取相应的措施来降低故障发生的概率,提高零部件的可靠性。
3. 可靠性参数设计可靠性参数设计是指根据零部件的使用环境和工作要求,确定与可靠性相关的参数,包括可靠性指标、寿命要求、故障率等。
通过合理确定这些参数,可以为零部件的可靠性设计提供有效的依据。
三、可靠性验证方法1. 试验验证试验验证是一种常用的可靠性验证方法,通过设置相应试验方案和测试条件,对零部件进行试验,检验其在实际工作环境下的可靠性表现。
试验验证可以包括寿命试验、环境试验、振动试验等,通过试验结果可以评估零部件的可靠性。
2. 数值仿真数值仿真在汽车零部件的可靠性验证中起到了重要的作用。
通过建立合适的数值模型,可以模拟零部件在各种工况下的工作情况,并预测其可靠性表现。
数值仿真不仅可以节省试验成本,而且可以提前发现潜在问题,指导零部件的设计改进。
3. 可靠性统计分析可靠性统计分析是通过对零部件在大量使用环境下的实测数据进行统计和分析,评估其可靠性水平。
常用的统计分析方法包括可靠性函数拟合、可靠性指标计算等,通过对实测数据的分析,可以得到零部件的可靠性参数和可靠性评估结果。
可靠性分析报告

可靠性分析报告在当今复杂多变的社会和经济环境中,产品和服务的可靠性成为了企业竞争的关键因素之一。
可靠性不仅关乎用户的满意度和忠诚度,还直接影响着企业的声誉和经济效益。
本报告将对可靠性的相关概念、重要性、影响因素以及评估方法进行详细的分析,并通过实际案例探讨如何提高可靠性。
一、可靠性的定义与内涵可靠性是指产品或系统在规定的条件下和规定的时间内,完成规定功能的能力。
它是一个综合性的指标,涵盖了产品的稳定性、耐久性、可维护性等多个方面。
简单来说,就是产品或系统在使用过程中不出现故障或失效的概率。
例如,一辆汽车的可靠性可以通过其在一定行驶里程内不发生重大故障的概率来衡量;一个软件系统的可靠性可以通过其在连续运行一定时间内不出现崩溃或错误的概率来评估。
二、可靠性的重要性1、满足用户需求用户在购买产品或使用服务时,期望其能够稳定、可靠地运行。
如果产品频繁出现故障,会给用户带来极大的不便和困扰,甚至可能造成安全隐患。
高可靠性的产品能够提升用户的满意度和信任度,从而增强企业的市场竞争力。
2、降低成本频繁的故障维修和更换零部件会增加企业的生产成本和售后服务成本。
而可靠的产品可以减少维修次数和维修费用,提高生产效率,降低总成本。
3、提升企业声誉一个以可靠性著称的企业往往能够在市场上树立良好的品牌形象,吸引更多的客户和合作伙伴。
相反,产品可靠性差的企业可能会面临声誉受损、市场份额下降等问题。
三、影响可靠性的因素1、设计因素产品或系统的设计方案直接决定了其可靠性的基础。
合理的设计应考虑到零部件的选型、结构的合理性、工作环境的适应性等方面。
如果在设计阶段存在缺陷,后续很难通过其他手段完全弥补。
2、制造工艺制造过程中的工艺水平、质量控制等因素会影响产品的一致性和稳定性。
粗糙的制造工艺可能导致零部件的精度不足、装配不良等问题,从而降低产品的可靠性。
3、原材料质量原材料的质量直接关系到产品的性能和寿命。
使用低质量的原材料容易导致产品在使用过程中过早失效。
机械零部件 的可靠性设计分析

机械零部件的可靠性设计分析摘要:机械零部件是机械设备的运行基础,其质量、性能等代表着机械设备的工作精度与生命周期。
为此,应定期对机械零部件进行维修养护,通过参数基准检测零部件动态化运行模式,以提升零部件的可靠性。
文章对机械零部件的可靠性进行论述,并对机械零部件的可靠性设计进行研究。
关键词:机械零部件;可靠性设计;分析对于机械零部件的质量来说,它的可靠性是十分重要的,它可以保证机械的使用寿命以及质量,是我国机械加工时应该注意的一项。
1 机械零部件的可靠性概述零部件在机械设备中起到负载、部件联动、动力传输的重要作用,在设备长时间工作状态下,零部件易发生是失效现象,令机械设备产生故障。
当零部件发生损毁现象时,例如老化、堵塞、松脱等,将增加联动部件的运行压力,提升零部件故障检测的难度。
此外,机械设备加工工艺、工作原理存在差异性,在零部件基准参数方面难以进行统一,只有少部分密封件、阀门、泵体等零部件实现通用化、标准化。
为此,在对零部件的可靠性进行设计时,零部件的荷载分布能力、材料强度等则应作为主要突破点。
2 机械零部件的可靠性设计分析2.1 可靠性优化设计可靠性优化设计是以可靠性为前提而开展的更完善的设计工作,不仅可以满足产品在使用过程中的可靠性,还将产品的尺寸、成本、质量、体积与安全性能等得到进一步的改善提高,进而保障结构的预测工作和实际工作性能更契合,能够把可靠性分析理论和数学规划方法合理地融合到一起。
在对各参数开始可靠性优化设计时,首先把机械零部件的可靠度当成优化的目标函数,把零部件的部分标准如成本、质量、体积、尺寸最大限度地缩小,再把强度、刚度、稳定性等设计标准作为约束基础设立可靠性优化设计数学模型,依据模型的规模、性能、复杂程度等确定适宜的优化方式,最后得出最优设计变量。
2.2 可靠性灵敏度设计可靠性灵敏度设计指的是确定机械零部件中的各个参数的变化情况对机械零部件时效的影响程度。
通过灵敏度设计,便于我们找到那些对可靠性设计敏感性较大的参数,后续对这些参数进一步分析并重新设计。
车辆可靠性分析与设计方案

车辆可靠性分析与设计方案一、引言随着社会发展和技术进步,汽车作为人们出行的主要方式之一,已经成为人们日常生活中不可或缺的交通工具。
车辆的可靠性是其作为交通工具的重要属性之一,对车辆的安全、经济以及实用性都有着重要的影响。
因此,车辆可靠性的分析和设计方案也是车辆设计和制造过程中极为重要的环节。
本文将从车辆可靠性的概念、影响因素以及分析方法等方面进行阐述,最后提出相应的设计方案,旨在为车辆可靠性的提高和改进提供一定的参考。
二、车辆可靠性概念车辆可靠性是指汽车在一定的使用条件下,能够保持所规定的功能、性能和指标的稳定性,并不断发挥其所具有的功能和性能,同时还能够在一定的寿命内保持在一定的性能稳定水平上的能力。
常见的评估车辆可靠性的指标有:•故障率•故障间隔时间•故障恢复时间•故障维修费用•生命周期费用等等三、车辆可靠性影响因素1.零部件的质量和设计车辆的可靠性和零部件质量密切相关,零部件的设计和制造质量好坏直接影响到汽车的可靠性和安全性。
因此,零部件的设计规范和制造技术标准也是提高车辆可靠性的关键所在。
2.车辆的使用环境车辆的使用环境也是影响车辆可靠性的重要因素之一。
不同的使用环境对于不同的车辆具有不同的影响。
例如,道路条件的恶劣与否、地形的起伏、气候的变化等都会对车辆可靠性产生不同程度的影响。
3.车辆的维护保养车辆的维护保养也是影响车辆可靠性的因素之一。
及时的维护和保养能够有效的减少车辆故障的概率,提高车辆的可靠性。
四、车辆可靠性分析方法为了有效地评估车辆的可靠性,需要采用一定的分析方法。
常见的分析方法包括:1.监控和检测法监控和检测法是通过对汽车零部件的工作状态进行监控和检测来评估车辆可靠性的方法。
常见的监控和检测手段包括传感器、数据采集系统等。
2.寿命测试法寿命测试法是通过长期的试验和观察来评估车辆可靠性的方法,例如通过进行人工加速老化测试、生命周期试验等。
五、车辆可靠性设计方案1.加强对零部件质量的把控通过加强对零部件质量的把控,采用高质量的材料和制造工艺,提高零部件的品质和可靠性。
- 1、下载文档前请自行甄别文档内容的完整性,平台不提供额外的编辑、内容补充、找答案等附加服务。
- 2、"仅部分预览"的文档,不可在线预览部分如存在完整性等问题,可反馈申请退款(可完整预览的文档不适用该条件!)。
- 3、如文档侵犯您的权益,请联系客服反馈,我们会尽快为您处理(人工客服工作时间:9:00-18:30)。
第四章 (46)可靠性试验设计与分析§4.6 加速寿命试验(Accelerated Life Testing)随着科学技术的发展,高可靠性、长寿命的产品愈来愈多,前面讲的截尾寿命试验也不能适应这种要求,如,不少电子元器件寿命很长,在正常工作温度040C 下,寿命可达数百万小时以上,若取1000个这种元件可能只有1~2个失效,甚至没失效的情况。
假如我们把温度提高到060C ,甚至080C ,只要失效机理不变,仅环境更恶劣一些,则失效数会增加,这种超过正常应力下的寿命试验称为加速寿命试验。
加速寿命试验的目的:用加强应力的办法,加快产品故障,缩短试验时间,以便在较短的时间内预测出产品在正常应力作用下的寿命特征。
其基本原则是失效机理不变。
一. 加速寿命试验的类型(1).恒定应力加速寿命试验(简称恒加试验)试验之前,先选一组加速应力水平,如12,,......,k s s s ,它们都是高于正常应力水平0s ,一般取012k s s s s <<<鬃鬃鬃<。
然后将一定数量的样品分成k 组,每组在一个加速应力下进行寿命试验,直到各组均有一定数量的样品失效为止(如定数截尾0r r )。
从图4.32可以看出,恒加试验是由若干个寿命试验组成,为了缩短寿命试验,特别是低应力水平下的寿命试验采用截尾试验,这样才能更好地发挥加速寿命试验缩短试验时间地优点。
(2).步进应力加速寿命试验(简称步加试验)它也选定一组加速应力水平0s 12k s s s <<<鬃鬃鬃<, (0s 为正常应力水平) 试验时把一定数量的样品都置于应力水平1s 进行寿命,经过一段时间,如1t 小时后,把应力提高到2s ,将未失效的样品在2s 应力下继续进行寿命试验,一直到有一定数量的样品发生失效为止。
如图4.33所示。
在本试验中,一个样品先在加速应力1s 下试验一段时间,若失效,则退出试验,若没有失效,将进入2s应力下的试验,如此下去,一个样品可能会遭遇若干个加速应力水平的考验。
而在恒加试验中,一个样品自始至终都在同一个应力水平下试验,相比之下,步加试验可使样品失效更快一些,这是步加试验的优点之一,步加试验的另一优点可以减少参试样品的个数,与恒加试验相比的缺点:可靠性特征量估计不如恒加试验下的估计准确(有时可安排二组平行进行步加试验,以次来增加失效个数,提高估计精度)。
(3).序进应力加速寿命试验(简称序加试验)它与步加试验基本相同,不同之处仅在于它们施加的加速应力水平将随时间连续增加。
图 4.34最简单是直线上升,如上图:特点:应力变化快,失效也来得快。
实施序加试验需要有专门的控制应力水平变化的设备和跟踪产品失效的记录设备,否则难以实现序加试验。
上述三种加速寿命试验我国都有应用,都有一批成功的实例,但以恒加速试验实例为多,这是因为恒加速试验方法操作简单,数据处理技术也成熟,尽管它所需试验时间不是最短,但仍比一般寿命试验成倍地缩短试验时间,故常被实际采用,我国对恒加试验还制定了国家标准GB2689.1~4。
(4).变应力加速寿命试验将一定数量的试件在任意变动的应力载荷谱下做寿命试验。
如循环应力试验和随机应力如电气中对绝缘体施加或低或高的周期变化电压(如图4-35),又如飞机部件、桥梁部件都经受随机变化的风力冲击,风力是随机变化。
目前尚缺少这种试验数据的处理方法。
故常在一定的约束下,近似地看作恒加速试验处理。
二.故障模型1.寿命与应力之间的关系加速寿命试验的基本思想是利用高应力水平下的寿命特征去外推正常应力水平下的寿命特征,实现这个基本思想的关键在于建立寿命与应力水平之间关系,借用这个关系才能实现外推。
众多实验证明,总体看,低应力下寿命高于高应力下的寿命,也有可能少数例外。
所以着眼于个别产品的寿命似乎很难建立寿命与应力关系,但若我们着眼于每个应力水平下寿命数据的总体特征(如中位寿命、平均寿命、特征寿命,有时也用10%分位寿命、90%分位寿命等),则在寿命曲线上可以画出一条光滑曲线,可以表明,中位寿命(或平均寿命)是应力水平的递减函数。
因此,我们需要建立寿命特征(如中位寿命、平均寿命等总体特征)与应力水平之间的关系。
这种关系称为加速模型,又称加速方程。
寿命特征与应力之间关系常是非线性的曲线,假如我们经适当变换,如对数变换、倒数变换,就有可能变成直线,直线不仅容易拟合,而且方便外推。
2、加速模型 (1)故障模式加速寿命的前提必须是不改变产品的故障机理,否则用一种故障机理的数据去测量另一种故障机理的可靠性寿命特征是不合理的,因此在研究产品故障时经常要区分故障物理、故障模式、故障机理这几种概念。
故障物理:简单说,从原子和分子自由度出发,来解释产品故障现象,是故障分析的基础。
故障模式:产品故障时可观察到的外部现象。
如断线、短路、裂纹、退化、泄漏等现象,即使是故障机理不明,但产品的故障模式也是可以观察到的。
故障机理:产品故障的内在原因,即导致发生故障的物理、化学或机械的过程。
如磨损、疲劳腐蚀、氧化、老化、断裂等形式表现出来。
故障的外因:承受工作应力、环境应力和工作时间。
内因:故障机理。
不同的应力促进不同的故障机理发展,产生不同的故障模式,通过机理分析,提出改进措施。
根据不同的故障模式,选用不同的加速模型。
(2)反应论模型由于氧化、电解、扩散、磨损和疲劳等原因造成故障的产品,其从正常状态进入退化状态的过程中,存在着能量势垒,越过此能量势垒故障将按一定的概率发生。
属于反应论模型的故障模型有:(a )阿伦尼斯(Arrhenius)模型在加速寿命试验中,用温度作为加速应力是常见的,因为温度使产品(如电子器件、绝缘材料等)内部加快化学反映,促使产品提前失效。
阿伦尼斯在1880年研究了这类化学反应,在大量数据的基础上,提出如下加速模型:EkTL A e-=其中 L ――某寿命特征(中位寿命、平均寿命),A----是个常数,且0A >(也称频数因子);E ――激活能,与材料有关,单位是电子伏特,以ev 表示;K ――波尔兹曼常数,50.816710/ev c -´,/E K 的单位为温度,又称激活温度;T ――绝对温度,等于摄氏温度加273这种模型表明,寿命特征随着温度上升而指数下降。
对上式两边取对数:ln b L a T =-,ln ,E a A b k==,a 和b 都是待定参数。
其寿命特征的对数是温度倒数的线性函数。
假设在标准应力下的产品寿命为0L ,在加大应力状态下,产品寿命缩短为L ,0L L <。
则加速寿命试验的加速系数(正常应力下某种寿命特征与加速应力相应寿命特征的比值)为:11()0b T T LeL t --==一般来说,温度在005~20之间。
温度上升010c ,电子元件退化的经验数据表明,使平均寿命缩短11~32,这个经验数据称为010c 法则。
(b )幂律模型对温度以外的模型,假设其应力为s ,如电应力(电压、电流、功率),若加大电压亦能促使产品提前失效。
产品寿命特征表达式为:K A s a =K ――特征寿命,如中位寿命,平均寿命等,或称为产品参数的退化率;A ――是一个正常数 s ――应力;a ――是一个与激活能有关的正常数。
如电容器,s 为直流电压,5a =;对聚乙烯类绝缘材料,s 为交流电压,11~13a =;对滚珠轴承及钢材断裂,3~4a =。
此外,用压力、转速以及某些疲劳寿命的s N -曲线,有也属于这种类型。
当退化量达到极限时,产品故障。
这种模型的加速系数为:0s s at 骣÷ç=÷ç桫上述两种模型统一的形式是ln ()a b s x j =+,通过加速寿命试验数据分析,获得两个未知参数a 和b 的估计值,若有了加速模型ˆˆˆln ()a b s x j =+,就可对正常应力水平0s 下的寿命x 作出估计。
这类加速模型在常用的寿命分布中的应用如下:a)、当寿命分布服从指数分布时,常用平均寿命θ作为寿命特征,于是加速模型为ln ()a b s θϕ=+b)、当寿命分布服从威布尔分布时,常用特征寿命η作为寿命特征,于是加速模型为ln ()a b s ηϕ=+c)、当寿命分布服从对数正态分布时,常用中位寿命0.5t 作为寿命特征,于是加速模型为0.5ln ()t a b s ϕ=+例:某一材料的寿命假设服从对数正态分布,经过四种不同温度的加速寿命试验,得到了平均寿命估计值,并用阿伦尼斯模型得到其加速方程ln 3.69755675/s θ=-+ 其中θ表示平均寿命,s 为绝对温度,假设加速温度1200(472)s C K =︒,正常工作温度0150(423)S C K =︒,求加速系数。
解:在01S S 和下的平均寿命估计值分别为0011ln 3.69755675/42316624ln 3.69755675/4724129θθθθ=-+==-+=所以加速系数的估计值01/16624/4129 4.026τθθ===这个结果表明,在0150S C =︒下的平均寿命约为1200S C =︒下的平均寿命的4倍。
(c )广义艾林模型(Egrins )这种模型表达产品故障是由两种应力造成的,一种是温度应力,另一种是温度以外的应力s ,其表达式为: bT K ATe s a-¢=则加速系数:01100b T T s T e s T at 骣÷ç÷ç--÷ç÷ç÷桫骣骣鼢珑鼢=珑鼢鼢珑桫桫(3).损伤累积模型用于材料在不加应力或施加变应力下的退化过程描述,这类模型广泛采用的是线性损伤累积模型。
又称迈因纳法则。
假定:即使应力大小在变化,而退化机理或故障机理不变,可以认为一个产品在施加交变应力下,材料的损伤是线性累积的,当累积能量达到一定值时(所做的功W )就会引起故障。
设交变应力i s 作用下,材料循环寿命次数为i N ,所做的功为i W ;若交变应力1s 作用1n 次循环,交变应力2s 作用下循环为2n 次鬃鬃鬃,不断改变应力等级直至材料或元件故障,其所作的功i W W =å,它们之间存在iii W n WN =成线性比例关系。
假定每个交变应力下发生故障是随机的,在时间上是服从指数分布,那末这些故障事件同时发生的概率为:iiiin n N N ee--å=Õ当1iin N=å,概率为1e -所经历的时间就是平均寿命。
从1iin N =å中,可以求得循环寿命次数的期望值i n å。
在前面三个反应论模型中,对应迈因纳法则,退化量取决于K,则可将迈因纳法则推广为:1iit L =å元件或材料的期望寿命为满足上式的i t å。