数字化段修生产调度指挥系统
铁路列车调度指挥系统(TDCS)、调度集中系统(CTC)维护管理办法

铁路列车调度指挥系统(TDCS)、调度集中系统(CTC)维护管理办法第一章总则第一条铁路列车调度指挥系统(以下简称TDCS)和调度集中系统(以下简称CTC)是全路各级调度指挥的基础装备,是重要的行车设备。
为规范TDCS/CTC系统的维护管理,提高系统的稳定可靠性,确保系统正常运行,制定本办法。
第二条 TDCS/CTC系统由中国铁路总公司(以下简称总公司)、铁路局、车站三级构成,综合了铁路信号、计算机、网络通信和现代控制技术,具有点多线长、布局成网、分散维护和集中管理的特点。
第三条 TDCS/CTC系统直接涉及行车安全,必须自成体系,单独成网,独立运行,严禁与其它系统直接联网。
对外提供信息和增加标准用户外终端时,应经总公司运输局电务部批准。
第四条 TDCS/CTC系统应采用网络安全技术,在与其它系统交换信息时,应采用安全可靠的网络隔离设备和措施,确保系统网络安全和信息安全。
第五条本办法适用于普速铁路TDCS/CTC、高速铁路CTC系统的维护管理。
第二章组织机构与职责第一节组织机构第六条 TDCS/CTC系统维护管理实行总公司、铁路局、电务段三级管理。
第七条总公司运输局电务部是全路TDCS/CTC系统的业务主管部门。
电务部电务试验室负责总公司TDCS/CTC中心系统的维护管理,并指导全路TDCS/CTC系统维护工作。
第八条铁路局电务处是铁路局TDCS/CTC系统的业务主管部门。
第九条铁路局TDCS/CTC中心机房所在地应设立TDCS/CTC维护机构,维护机构一般设置在电务段,也可设置在铁路局。
第十条电务段是TDCS/CTC系统的维护单位,应设置专业技术主管人员。
第二节工作职责第十一条总公司运输局电务部负责制定TDCS/CTC系统技术政策、技术标准及规章制度,负责全路TDCS/CTC系统网络的规划。
第十二条总公司电务部电务试验室职责:(一)负责总公司TDCS/CTC中心系统的日常维护和管理。
(二)指导和协调铁路局TDCS/CTC系统维护工作。
《铁路列车调度指挥系统(TDCS)、调度集中系统(CTC)维护管理办法》(2014)330

TG /XH 211 -2014铁路列车调度指挥系统(TDCS)、调度集中系统(CTC)维护管理办法第一章总则第一条铁路列车调度指挥系统(以下简称TDCS)和调度集中系统(以下简称CTC)是全路各级调度指挥的基础装备,是重要的行车设备。
为规范TDCS/CTC系统的维护管理,提高系统的稳定可靠性,确保系统正常运行,制定本办法。
第二条 TDCS/CTC系统由中国铁路总公司(以下简称总公司)、铁路局、车站三级构成,综合了铁路信号、计算机、网络通信和现代控制技术,具有点多线长、布局成网、分散维护和集中管理的特点。
第三条 TDCS/CTC系统直接涉及行车安全,必须自成体系,单独成网,独立运行,严禁与其它系统直接联网。
对外提供信息和增加标准用户外终端时,应经总公司运输局电务部批准。
第四条 TDCS/CTC系统应采用网络安全技术,在与其它系统交换信息时,应采用安全可靠的网络隔离设备和措施,确保系统网络安全和信息安全。
第五条本办法适用于普速铁路TDCS/CTC、高速铁路CTC系统的维护管理。
第二章组织机构与职责第一节组织机构第六条 TDCS/CTC系统维护管理实行总公司、铁路局、电务段三级管理。
第七条总公司运输局电务部是全路TDCS/CTC系统的业务主管部门。
电务部电务试验室负责总公司TDCS/CTC中心系统的维护管理,并指导全路TDCS/CTC系统维护工作。
第八条铁路局电务处是铁路局TDCS/CTC系统的业务主管部门。
第九条铁路局TDCS/CTC中心机房所在地应设立TDCS/CTC维护机构,维护机构一般设置在电务段,也可设置在铁路局。
第十条电务段是TDCS/CTC系统的维护单位,应设置专业技术主管人员。
第二节工作职责第十一条总公司运输局电务部负责制定TDCS/CTC系统技术政策、技术标准及规章制度,负责全路TDCS/CTC系统网络的规划。
第十二条总公司电务部电务试验室职责:(一)负责总公司TDCS/CTC中心系统的日常维护和管理。
生产指挥系统方案

生产指挥系统方案引言生产指挥系统是一个用于管理和控制生产任务的软件系统。
它集成了生产计划、物料管理、设备调度、质量控制等功能,旨在提高生产效率、降低成本,并确保产品质量和交货周期的稳定性。
本文档将分析生产指挥系统的需求,并提出相应的解决方案。
一、需求分析1.1 功能需求生产指挥系统应具备以下基本功能:•生成生产计划:根据客户订单和库存情况,生成生产计划并进行排程。
•物料管理:管理采购、入库、出库、退货等物料操作,确保生产所需物料的供应。
•设备调度:根据生产计划和设备利用率,进行设备的调度和维护。
•质量控制:通过检测和追溯,确保产品质量符合标准要求。
•任务分配:将生产计划转化为具体的操作任务,并分配给相应的人员执行。
•实时监控:提供实时看板和报表,监控生产状态、物料库存、设备稼动率等关键指标。
1.2 性能需求生产指挥系统的性能需求包括以下几个方面:•响应时间:系统响应用户操作的时间应控制在毫秒级别,以提供良好的用户体验。
•数据处理能力:系统应能处理大量的数据,并支持快速查询和分析能力。
•并发处理能力:系统应能同时处理多个用户的请求,保证稳定的性能表现。
•可扩展性:系统应支持灵活的扩展,以满足不同规模企业的需求。
二、系统架构生产指挥系统的架构设计如下:2.1 前端架构前端采用Web应用程序的形式实现,主要使用HTML、CSS和JavaScript技术。
前端应用通过HTTP协议与后端进行通信,并向用户提供交互界面。
2.2 后端架构后端采用三层架构,分为表现层、业务逻辑层和数据访问层。
•表现层:接收用户请求,向用户返回响应结果,并进行用户界面的渲染。
前端界面通过HTTP请求调用表现层的API接口。
•业务逻辑层:处理用户请求的业务逻辑,包括生成生产计划、物料管理、设备调度、质量控制等功能。
•数据访问层:负责与数据库进行交互,提供数据的访问和存储功能。
2.3 数据库架构系统采用关系型数据库存储数据,可选择MySQL、Oracle等数据库管理系统。
指挥调度系统解决方案

指挥调度系统解决方案
《指挥调度系统解决方案》
随着科技的不断发展,各行各业对于提高工作效率和管理能力的需求也越来越高。
在交通运输、物流配送、应急救援等需要大量协调和调度的行业中,指挥调度系统成为了一种重要的解决方案。
指挥调度系统是一种利用信息技术实现对人、车、物等资源进行有效调度和管理的系统。
通过集成GPS定位、移动通信、
数据分析和人工智能等技术,可以实现对车辆位置、运输路线、货物状态等信息的实时监控和管理,从而提高工作效率、降低成本、减少事故风险。
在交通运输行业,指挥调度系统可以帮助企业实现对车辆的实时监控和调度,提高运输效率和安全性。
在物流配送行业,系统可以帮助企业优化路线规划和货物跟踪,提高配送效率和客户满意度。
在应急救援行业,系统可以帮助相关部门对资源进行快速调配和协调,提高救援效率和响应速度。
指挥调度系统的应用不仅可以帮助企业提高管理效率,也可以为用户提供更加便捷、安全的服务体验。
随着技术的不断进步,指挥调度系统将会在更多行业中得到应用,为企业和社会带来更多的便利和效益。
铁路调度指挥系统

铁路调度指挥系统铁路调度指挥系统是指用于管理和控制铁路运输的信息化系统。
随着铁路运输的快速发展和需求的增加,传统的人工调度已经无法满足要求。
铁路调度指挥系统的出现,极大地提高了铁路运输的效率和安全性。
一、概述铁路调度指挥系统是基于计算机技术和通信技术的综合应用。
它集成了列车运行计划、列车运行控制、调度命令发布、车辆位置跟踪等功能,实现了对铁路运输全过程的监控和管理。
二、系统架构铁路调度指挥系统采用分布式架构,包括中央调度台、地方调度台和车站终端。
中央调度台负责全网的调度和控制,地方调度台负责区域内的细致管理,车站终端用于与列车进行交互。
三、功能特点1. 调度优化:铁路调度指挥系统通过模型算法和优化技术,实现列车运行计划的自动化生成和优化,减少列车之间的间隔时间,提高线路的通行能力。
2. 实时监控:系统能够实时监控列车的位置、速度、状态等信息,及时发现和处理运行异常情况,确保列车安全运行。
3. 快速响应:系统能够根据实时交通情况,快速生成调度命令并下发给相关人员和设备,以保证列车运行的平稳性和高效性。
4. 数据分析:系统可以对历史数据进行分析和统计,为运输部门提供决策支持和运营优化建议。
四、运行流程1. 列车运行计划制定:基于列车的时刻表和运行需求,系统自动生成列车运行计划。
2. 调度命令发布:中央调度台根据运输需求,生成调度命令并下发给地方调度台和车站终端。
3. 列车运行控制:地方调度台和车站终端通过系统对列车进行运行控制,包括发车、停车、调速等操作。
4. 列车状态监控:系统实时监控列车位置、速度和状态,及时发现运行异常情况。
5. 故障处理:系统能够自动检测列车故障情况,并协助调度人员进行故障处理和应急措施的调度。
五、应用效果铁路调度指挥系统的应用,使得铁路运输的效率大大提升。
它能够有效减少列车之间的间隔时间,提高线路的通行能力,降低了运输成本。
同时,系统的实时监控和快速响应能力,保障了列车的安全运行,减少了事故的发生。
建设智能化生产调度系统的工作方案

建设智能化生产调度系统的工作方案如今,随着工业化和信息化水平的不断提升,传统的生产调度方式已经不能满足现代企业生产的需求。
为了提高生产效率、降低生产成本、优化生产调度流程,建设智能化生产调度系统已成为众多企业的共同选择。
本文将从系统建设的背景与意义、关键技术及应用、工作方案执行及效果评估等方面,详细阐述建设智能化生产调度系统的工作方案。
一、背景与意义随着市场竞争日益激烈,企业需要不断提高生产效率,降低生产成本,以保持竞争力。
传统的生产调度方式主要依靠人工经验和简单的排程规则,容易受到诸多因素的影响,如订单变化、设备故障等,导致生产计划经常无法及时响应。
而建设智能化生产调度系统,可以利用先进的信息技术,实现生产过程的自动化监控、优化调度,提高生产效率,降低生产成本,增强企业市场竞争力。
二、关键技术及应用1. 数据采集与传输:智能化生产调度系统需要实时监控生产数据,包括设备运行状态、生产任务进度、人员配备等信息,可以通过传感器、RFID等技术实现数据的采集和传输。
2. 数据分析与决策:系统需要具备数据分析和算法优化能力,通过对生产数据的实时分析,对生产任务进行智能调度和优化决策,以提高生产效率。
3. 智能控制与执行:系统需要具备智能控制和执行功能,可以实现自动化生产调度、设备控制,提高生产线的利用率和效率。
4. 用户界面设计:为了方便用户操作和监控生产状态,系统还需要设计友好的用户界面,包括实时监控界面、报表查询模块等功能。
三、工作方案执行1. 系统需求分析:首先需要进行企业生产流程分析和需求调研,确定系统功能和性能需求,以及用户需求和期望。
2. 系统设计与开发:根据需求分析结果,进行系统设计和开发,包括数据模型设计、算法实现、用户界面设计等工作。
3. 系统测试与调优:系统开发完成后,需要进行全面的测试和调优工作,确保系统稳定性和性能。
4. 系统部署与培训:系统测试通过后,进行系统部署和用户培训工作,确保用户能够正确操作并熟练使用系统。
2024年指挥调度系统市场发展现状

指挥调度系统市场发展现状简介指挥调度系统是一种集成了通信、数据传输、地理信息系统(GIS)、图像识别等技术的综合性系统。
它可以实现资源调度、任务分配、指挥指挥等功能,广泛应用于交通管理、紧急救援、物流配送、安防监控等领域。
本文将对指挥调度系统市场的发展现状进行分析。
市场规模指挥调度系统市场近年来呈现快速增长的趋势。
据市场研究机构统计,全球指挥调度系统市场规模预计在2025年将达到1000亿美元。
这主要受到以下因素的影响:1.日益增长的安全与紧急救援需求:随着城市化进程的加速和人口增长,对于安全和紧急救援的需求也不断增加。
指挥调度系统可以实时监控、调度和响应各类紧急事件,提高应急处理的效率和准确性。
2.交通拥堵与物流需求增加:现代城市面临着严峻的交通拥堵问题,物流配送效率亟待提升。
指挥调度系统可以优化交通流量、指挥道路交通,并实现物流车辆的实时调度,提高交通运输的效率和运输成本的核算。
3.安全监控与防控要求增强:随着社会安全形势的复杂化,对于安全监控与防控的要求也越来越高。
指挥调度系统可以整合安防监控设备,实现对重要区域的实时监测与响应,提高安全防控的能力。
主要产品指挥调度系统市场的主要产品包括以下几类:1.通信设备:指挥调度系统依赖于稳定的通信设备进行数据传输和指挥指令的下达。
目前市场上主流的通信设备包括有线电话、移动电话、对讲机等,以及使用卫星通信技术的卫星电话。
2.数据传输设备:指挥调度系统需要实时传输大量的数据,因此需要稳定高效的数据传输设备。
目前主流的数据传输设备包括有线网络、无线网络、光纤网络等,以及近年来兴起的5G网络。
3.地理信息系统(GIS):GIS是指挥调度系统的核心技术之一,它用于实现地理位置信息的采集、存储、处理和展示。
目前市场上主流的GIS产品包括ArcGIS、Google Maps、百度地图等。
4.图像识别设备:图像识别设备可以通过摄像头、监控器等途径获取实时图像信息,并通过图像处理算法进行目标识别和分析。
调度指挥系统
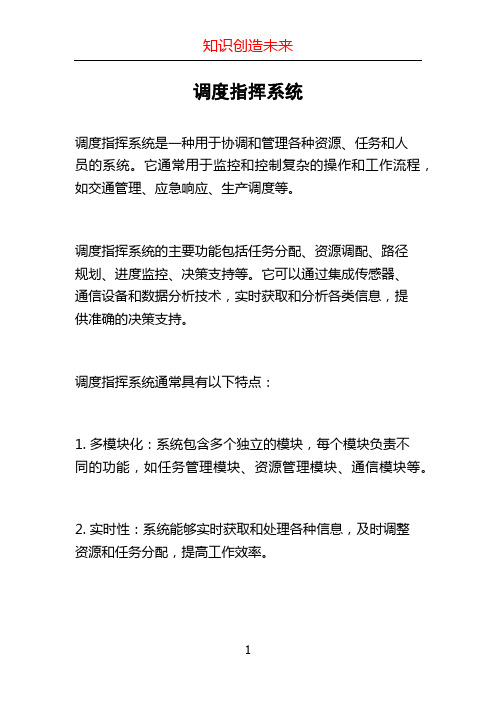
调度指挥系统
调度指挥系统是一种用于协调和管理各种资源、任务和人
员的系统。
它通常用于监控和控制复杂的操作和工作流程,如交通管理、应急响应、生产调度等。
调度指挥系统的主要功能包括任务分配、资源调配、路径
规划、进度监控、决策支持等。
它可以通过集成传感器、
通信设备和数据分析技术,实时获取和分析各类信息,提
供准确的决策支持。
调度指挥系统通常具有以下特点:
1. 多模块化:系统包含多个独立的模块,每个模块负责不
同的功能,如任务管理模块、资源管理模块、通信模块等。
2. 实时性:系统能够实时获取和处理各种信息,及时调整
资源和任务分配,提高工作效率。
3. 可视化:系统通过图形界面展示各种信息,如地图、图
表等,帮助用户直观地理解和管理工作流程。
4. 安全性:系统采用加密和权限控制等技术,保障数据和
系统的安全性。
5. 可扩展性:系统可以根据需求扩展和定制功能,适应不
同的应用场景。
调度指挥系统的应用范围很广,可以用于交通管理、公共
安全、物流调度、生产调度等领域。
它可以提高工作效率、减少人工错误、提高决策精度,对于提升整体效益和减少
资源浪费具有重要作用。
生产调度指挥中心

生产调度指挥中心工作流程介绍随着铁路跨越式发展进入关键阶段,各项工作全面推进,路局直管站段、站段管理区域不断扩大、现场控制难度增强、安全预测不确定因素增多的实际,不断改善信息管理方式,使生产组织和信息结构更趋合理,成立了生产调度指挥中心。
目的在于实现段上统一指挥、车间组织实施、工队或工区组织落实,直接控制现场作业,掌握现场作业的效率。
切实提高现场作业质量,落实闭环管理机制。
实现精细化、扁平化管理。
以科学、精细、严谨、务实为宗旨,努力使我段的安全生产管理工作迈向一个新的台阶。
现将我段生产调度指挥中心的工作流程向各位领导作简要介绍。
生产调度指挥中心由生产调度台、信息管理台和综合分析台三个工作台组成。
(进入生产调度指挥主页)。
现在大家看到的是我段生产调度指挥系统的主界面,在这里,我们可以十分清楚地掌握全段的天窗信息、慢行地点等日常生产信息,32点闪烁表示该区间或该站区有天窗或慢行地点信息,移动鼠标至红点上,便可显示出详细信息。
这样全段的生产信息状况可以清楚地显示在段管界图上,十分方便。
生产调度台:主要负责处理各类信息,协调、组织处理生产中的各类问题,根据线路设备病害,申请天窗计划,下达生产任务,落实闭环管理机制;首先看生产任务单,生产任务单是根据车间上报的病害反馈单,对病害里程、轨号、枕号和病害类型(A、B、C类),以指令的形式下达到车间,由车间组织实施,工队组织落实,A类病害二日内消灭,B、C类病害七日内整治。
以仁爱车间为例。
第一步是病害反馈,现在显示的是4月26日白银西车间线路病害反馈表,表内有负责人、防护员、包保人、病害里程、轨号、枕号、病害分类和病害详情。
第二步是天窗预报,生产调度台收到病害反馈表后,进行病害分析,申请4月28日天窗计划,现在显示的是维修天窗预报表,申请时间为15:42-16:42,计60分钟。
第三步是下达指令,4月27日根据天窗批准计划,下达任务通知单。
现在显示指令是白银西线路车间4月28日天窗生产任务通知单,当日回检并反馈整治情况。
TDCS系统简介

TDCS系统系统简介TDCS(Train Operation Dispatching Command System)是覆盖全路的调度指挥管理系统,能及时、准确地为全路各级调度指挥管理人员提供现代化的调度指挥管理手段和平台。
TDCS 以现代计算机技术、计算机网络技术、通信技术、多媒体技术、数据库技术为基本技术手段,实现对列车在车站和区间运行的实时监视,动态调整、自动生成列车运行三小时阶段计划,实现列车调度命令的自动下达和实迹运行图的自动描绘;实现分界口交接列车数、列车运行正点率、行车密度、早晚点原因、重点列车跟踪等实时宏观统计分析并形成相关统计报表;为各级调度人员提供列车的动态运行情况,便于机车合理调配,提高运输能力和安全程度;显示铁路路网、沿线线路、车站、重要列车和救援列车分布等主要信息,为铁路事故救援、灾害抢险、防洪等提供决策参考。
TDCS系统采用各种新技术与铁路信号技术的特点相互融合,把传统的以车站为单位的分散信号系统逐步改造成为一个全国统一的网络信号系统,由提高安全提高效率向提高运输效能转变,由单一功能向综合功能转变,由模拟传输向数字传输转变,由手工绘制向辅助及自动绘制转变;通过建立一个融先进通信、信号、计算机网络、数据传输、多媒体技术为一体的现代化信息系统,为各级调度人员提供先进的调度指挥和处理手段,提高应变和处理能力,减少调度人员通话和手工制表数量,改善调度指挥人员的工作条件,从而提高铁路运输组织的科学性、劳动生产效率和铁路服务质量,为铁道部生产布局的调整打下了坚实的基础。
系统结构中心局域网采用高性能的交换机组成双100M 高速以太网,所有设备通过双网卡连接到双局域网上,确保各节点数据传输的可靠性。
车站局域网采用高性能的交换机组成双100M 高速以太网,所有车站设备通过双网卡连接到双局域网上,确保各节点数据传输的可靠性。
调度中心子系统中各子系统之间为通过双冗余局域网实现的以太网网络接口,接口为RJ45 接口规范、网络介质为5 类双绞线,速率为100M。
数字化段修生产调度指挥系统

数字化段修调度生产指挥系统在昆明北的应用北京京天威科技发展有限公司Beijing JingTianWei Science&Technology Development LTD.目录1概述 (3)1.1铁路车辆段信息化现状简况 (3)1.2铁路货车车辆段信息化规划背景 (3)2数字化车辆段建设的总体思路 (4)3系统整体业务架构 (5)4系统实现的主要功能 (5)4.1数字化车辆段图形化基础空间资源 (5)4.1.1局管内线路及站点数字化布局图 (5)4.1.2车辆段段管线线路数字化布局 (6)4.1.3虚拟化车辆段数字化展现 (6)4.1.4段内主要设备的数字化展现 (7)4.2管内检修车分析 (8)4.2.1管内检修车分析GIS图形分析 (8)4.2.2管内检修车分析 (8)4.2.3管内现在车位置进行分析 (9)4.2.4固定配属车实时跟踪 (9)4.2.5检修车扣留情况分析 (10)4.2.6列车跟踪分析 (10)4.2.75T联合预警 (10)4.3段修生产指挥 (11)4.3.1智能化调车管理 (11)4.3.2货车检修指导方案 (12)4.3.3现场进度监控预案 (13)4.3.4现场物料配送方案 (14)4.3.5生产质量控制预案 (15)4.3.6其他工序生产计划 (15)4.3.7台位摆车作业 (16)4.3.8生产作业执行 (17)4.3.9生产进度监控 (19)4.4平板电脑、手机等移动端应用 (20)4.4.1平板电脑生产监控 (20)4.4.2生产现场的物料配送接收和任务分配 (21)4.5生产大数据分析 (22)4.5.1列检作业量分析 (23)4.5.2列检劳动生产率分析 (23)4.5.3修竣车工作量分析 (24)4.5.4加装改造工作量分析 (24)1概述1.1铁路车辆段信息化现状简况车辆信息化检修信息化建设是保障车辆运行安全、提高生产效率和管理水平的重要手段。
生产指挥调度系统

生产指挥调度系统生产指挥调度系统是一种用于管理和协调生产活动的工具,它能够帮助企业提高生产效率、降低成本、提供及时的生产指导和决策支持。
本文将详细介绍生产指挥调度系统的概念、功能和优势,并探讨其在实际应用中的应用范围和效果。
生产指挥调度系统,顾名思义,是一个用于指挥和调度生产活动的系统。
它通过整合生产线上的各个环节信息,实时监控生产状态,协调不同部门之间的合作,确保生产过程的顺利进行。
这个系统可以采用各种传感器和信息收集装置,将实时数据传输到计算机系统中进行分析和处理。
在此基础上,通过算法和模型的支持,系统可以生成生产目标、计划和调度,并提供必要的监控和决策支持。
生产指挥调度系统的主要功能包括生产计划制定、生产进度跟踪、资源调度和质量控制等。
首先,通过分析市场需求和生产能力,系统可以制定出合理的生产计划,包括生产数量、交货期限、生产线配置等等。
其次,在生产过程中,系统可以实时跟踪生产进度,并提醒相关部门及时处理可能出现的问题。
此外,系统还可以根据生产线的负荷情况,对资源进行合理的分配和调度,以提高生产效率和资源利用率。
最后,在生产完成后,系统可以通过检测和分析数据,对产品质量进行评估和控制,确保产品符合质量标准。
生产指挥调度系统的应用范围非常广泛。
它可以应用于各种生产型企业,包括制造业、物流业、能源行业等等。
无论是大型企业还是中小型企业,都可以通过引入生产指挥调度系统来优化生产过程,提高生产效率和质量。
此外,生产指挥调度系统还可以与其他管理系统进行集成,如企业资源计划(ERP)系统、供应链管理(SCM)系统等,实现信息的无缝传递和共享,提高整体企业运作的效率。
使用生产指挥调度系统的企业可以享受到许多优势。
首先,系统可以大大减少人为错误和人力成本。
相比于传统的人工调度方式,自动化的生产指挥调度系统能够更加精准和高效地进行调度,避免了因人为因素导致的错误和延误。
其次,系统可以提供全面的实时监控和报告功能。
智慧调度指挥系统设计方案

智慧调度指挥系统设计方案智慧调度指挥系统是一款利用人工智能、大数据分析等技术手段,实现对调度指挥中心的智能化管理与优化的系统。
下面是一份关于智慧调度指挥系统的设计方案。
一、系统概述智慧调度指挥系统旨在通过对接各种数据源和调度设备,将实时数据进行分析和处理,实现对指挥中心的智能调度管理和决策支持。
系统包括调度指挥中心、数据采集和处理模块、数据分析和决策模块以及应急响应模块等。
二、系统功能1. 数据采集与处理:通过与各种数据源对接,实时采集、处理、存储和分析各类数据,包括交通流量、车辆定位、突发事件等。
2. 调度任务管理:支持调度任务的发布、分配和跟踪,实现对任务执行情况的实时监控和控制。
3. 调度资源管理:对所有调度资源进行管理,包括车辆、人员和设备等,实时追踪调度资源的位置和状态,以提供最优的调度决策。
4. 数据分析和决策支持:通过大数据分析、机器学习和人工智能等技术手段,对采集到的数据进行深入分析和挖掘,为指挥中心提供决策支持和预测能力。
5. 应急响应:在突发事件发生时,系统能够快速响应并发布应急指令,调度资源进行应急处置,并提供实时的事件情况监控。
三、系统架构智慧调度指挥系统采用分布式架构,将系统划分为调度指挥中心、数据采集和处理模块、数据分析和决策模块以及应急响应模块四个主要模块,并通过统一的消息队列和数据库进行数据交互。
1. 调度指挥中心:负责任务发布、调度资源管理、决策支持和应急响应等功能,提供用户界面和操作接口。
2. 数据采集和处理模块:负责和各种数据源对接,采集实时数据并进行处理和转换,将数据发送至数据分析和决策模块。
3. 数据分析和决策模块:负责对采集到的数据进行分析和挖掘,生成调度决策和预测结果,并将结果发送至调度指挥中心。
4. 应急响应模块:负责突发事件的实时监测和响应,根据事件情况发布应急指令并调度资源进行应急处置。
四、关键技术1. 数据采集与处理:使用物联网技术,通过各种传感器和设备对相关数据进行实时采集和处理,并对数据进行预处理和清洗,确保数据的准确性和完整性。
生产调度指挥系统

生产调度指挥系统生产调度指挥系统是一个重要的生产管理工具,它能够帮助企业实现生产调度的自动化和优化,提高生产效率和产品质量。
本文将从系统的作用、功能、架构和实施等方面进行探讨,以便读者更好地了解和应用这一系统。
一、系统的作用生产调度指挥系统是一个集成化的软件系统,其作用主要有以下几点:1. 实时监控生产进度:生产调度指挥系统可以实时监控生产车间的各个工序的生产进度,包括原材料的投入、生产设备的运行状况、生产工人的工作状态等。
通过对数据的采集和分析,系统可以提供准确的生产进度信息,以便及时做出调整和决策,确保生产计划的顺利执行。
2. 自动化生产调度:生产调度指挥系统可以根据企业的生产计划和资源情况,自动生成生产调度方案,并将其下达给各个工序的操作人员和设备。
系统可以根据生产车间的实际情况,动态调整和优化生产调度,以便最大限度地提高生产效率和生产能力。
3. 资源优化配置:生产调度指挥系统可以根据生产计划和资源情况,对生产车间的各个工序进行统一调度和协调,避免资源的浪费和闲置。
系统可以根据生产车间的实时情况,智能地调整资源的配置,以便最大限度地提高资源的利用效率和产能。
二、系统的功能生产调度指挥系统具有多种功能,主要包括以下几个方面:1. 生产计划管理:系统可以对生产计划进行维护和管理,包括计划的制定、下达、修改和追踪等。
系统可以根据用户对生产计划的要求,自动生成合理的生产调度方案,并将其下达给各个工序的操作人员和设备。
2. 生产进度监控:系统可以实时监控生产车间的各个工序的生产进度,并将其以可视化的方式展示给用户。
用户可以通过系统的界面,实时了解生产车间的生产状况,以便及时做出调整和决策,确保生产任务按时完成。
3. 资源管理:系统可以对生产车间的各类资源进行管理,包括原材料、设备、工人等。
系统可以根据生产计划和资源情况,智能地调整资源的配置和使用,以便最大限度地提高资源的利用效率和产能。
4. 故障修复与维护:系统可以对生产车间的设备进行故障诊断和维护管理。
CTC、DMIS、TDCS区别

CTC系统概述:CTC系统概述:调度集中是调度中心(调度员)对某一区段内的信号设备进行集中控制、对列车运行直接指挥、管理的技术装备。
分散自律调度集中系统是综合了计算机技术、网络通信技术和现代控制技术,采用智能化分散自律设计原则,以列车运行调整计划控制为中心,兼顾列车与调车作业的高度自动化的调度指挥系统。
1.1 分散自律调度集中系统是铁路现代化的重要技术装备,是现代铁路综合信息化建设的重要内容,也是现代铁路的新型运输组织形式。
必须与我国铁路路情紧密结合,做到以DMIS 为平台,以调度中心为核心,以行车指挥自动化为目标,实现铁路运输指挥的现代化。
1.2 分散自律调度集中系统采用计算机分布式网络控制技术、信息化处理技术,将列车运行调整计划下传到各个车站自律机中自主自动执行;在列车运行调整计划的基础上,解决列车作业与调车作业在时间与空间上的冲突,实现列车和调车作业的统一控制。
1.3 分散自律调度集中系统在信号设备控制与行车指挥方式上仅设有分散自律控制与非常站控两种模式。
系统分散自律控制时,只有控制指令不同来源,没有中心与车站控制权的转换;非常站控为车站人工控制方式,中心不具备直接控制权,系统完好时应具备DMIS 功能。
1.4 分散自律调度集中系统适用不同牵引动力、运行速度、运量、线路类型的区段与枢纽地区,可实现不办理客货运业务、调车作业量较小、列车和调车进路由调度中心远程控制的车站行车岗位无人化(简称无人车站,下同)。
1.5 本技术条件(暂行)规定了分散自律调度集中系统(以下简称调度集中或系统)的基本原则、基本功能、系统构成和技术要求,可作为系统研制、工程设计的依据,运营和维修部门也应参照执行。
CTC系统介绍:调度集中对车站实行分散自律控制时, 联锁关系仍由车站联锁设备保证. 实现各种功能时,应保证既有联锁关系的完整性。
调度集中与车站联锁的接口,应按继电联锁和计算机联锁分类,采用统一标准。
接口应不影响车站联锁的安全性。
调度自动化系统简介

调度自动化系统简介随着生产生活的不断发展,人们对效率与成本的要求越来越高。
自动化成为了解决问题的重要手段。
在生产制造领域,调度自动化系统是实现生产安排、生产调度、生产监控的重要工具。
调度自动化系统定义调度自动化系统是指在制造生产和劳动中,利用电子、计算机及通讯等现代科技手段,通过智能化、自动化的方法对复杂的生产调度问题进行分析与决策,实现对生产活动的智能化管理。
调度自动化系统的组成调度自动化系统由以下几个部分组成:1. 生产调度系统生产调度系统负责生产计划、生产任务下发、生产过程监控、生产数据管理与分析等任务。
通过对生产过程的掌控,实现生产资源最大化利用,提高生产效率,缩短生产周期。
2. 设备管理系统设备管理系统旨在通过实时监控设备的运行状态,及时发现设备故障,预估设备维护周期,提前对设备进行维护保养,延长设备使用寿命,并且保障设备的安全性能。
3. 质量管理系统质量管理系统负责实现对生产全过程的质量控制。
通过对生产过程中的质量控制点及时监测、剔除不合格品等方法,保证产品的质量符合标准要求。
4. 物资管理系统物资管理系统旨在保障生产所需的物资及时到位、数量足够、质量符合要求,以此实现生产流程的顺利进行,同时还需对物资的采购、库存等进行管理,以节约成本,提高效率。
5. 成本管理系统成本管理系统负责对生产过程中的各个环节进行成本核算和分析,提出优化和改进方案,实现成本最小化,提高企业竞争力。
调度自动化系统的优势调度自动化系统的优势主要表现在以下几个方面:1. 人工排产的缺陷人工排产往往受到人的因素影响较大,一些因生产过程中的临时变更或其他突发情况往往需要即时调整,而这些调整对于人工调度来说往往具有较大的难度。
而调度自动化系统则可以实现对生产过程中的各种情况的即时调整,快速反应,提高生产效率。
2. 提高生产效率调度自动化系统实现了对生产过程的智能掌控,能够对繁琐的生产计划、生产排产及物资管理等工作进行自动化处理,避免了人工操作的时间浪费,提高了生产效率。
电厂数字程控调度系统技术方案

电厂数字程控调度系统技术方案嘿,小伙伴们,今天给大家带来一份关于电厂数字程控调度系统的技术方案。
这个方案可是我积累了10年写作经验的心血之作,保证让你看完后眼前一亮!一、项目背景随着科技的飞速发展,电力行业对调度系统的需求日益增长。
传统的调度系统已经无法满足现代电力行业的运行需求,因此,电厂数字程控调度系统应运而生。
本项目旨在为我国电力行业打造一款高效、稳定、智能的调度系统,提高电力系统的运行效率。
二、系统架构1.硬件架构电厂数字程控调度系统硬件架构主要包括:服务器、调度员工作站、通信设备、现场控制器、传感器等。
2.软件架构软件架构分为四个层次:数据采集与传输层、数据处理与分析层、调度决策层、人机交互层。
三、系统功能1.数据采集与传输系统通过传感器实时采集现场设备的运行数据,包括电压、电流、温度等参数。
数据通过通信设备传输至服务器,进行统一存储和处理。
2.数据处理与分析服务器对采集到的数据进行分析,各类报表和曲线图,为调度员提供实时数据支持。
3.调度决策调度决策层根据实时数据和历史数据,结合专家系统,为调度员提供最优的调度方案。
4.人机交互四、系统优势1.高度集成电厂数字程控调度系统将数据采集、传输、处理、调度等功能集成在一个平台上,简化了系统结构,提高了运行效率。
2.智能调度系统采用专家系统,可根据实时数据和历史数据,为调度员提供最优调度方案,降低人为误操作的风险。
3.实时监控系统实时监控设备运行状态,发现异常情况可立即报警,确保电力系统安全稳定运行。
4.灵活扩展系统采用模块化设计,可根据实际需求进行灵活扩展,满足不断变化的电力行业需求。
五、项目实施1.项目启动项目启动阶段,我们将组织专业团队对现场设备进行详细调研,明确项目需求。
2.系统设计根据项目需求,设计合理的系统架构和功能模块,确保系统的高效稳定运行。
3.系统开发采用先进的编程技术和开发工具,进行系统开发,确保系统的性能和安全性。
4.系统部署在项目现场进行系统部署,确保硬件设备和软件系统的正常运行。
- 1、下载文档前请自行甄别文档内容的完整性,平台不提供额外的编辑、内容补充、找答案等附加服务。
- 2、"仅部分预览"的文档,不可在线预览部分如存在完整性等问题,可反馈申请退款(可完整预览的文档不适用该条件!)。
- 3、如文档侵犯您的权益,请联系客服反馈,我们会尽快为您处理(人工客服工作时间:9:00-18:30)。
实现回送检修车和管内循环车运行状态跟踪,防止已扣车源流失,掌握回送车源到达情况。对管内集结的成组挂运的检修车、管内循环车实现自动跟踪,防止车辆出局、流失。含小运转车的维护,针对这些车进行跟踪。对重点列车进行实时跟踪,及时掌握列车运行信息。
4.2.7
1、5T预警自动提示
各个5T站点发现故障时,系统自动在GIS地图上闪亮,点击后,系统弹出显示界面,提示5T具体故障。
管理流程思路:铁路货车车辆段是典型的离散为主、流程为辅单件、小批量制造维修企业。此类企业的生产作业计划及完成情况的跟踪非常复杂,来车的基本情况、配件装用情况、运行过程中的故障情况等均影响生产组织,每一个货车的检修过程可以模拟为一个项目管理过程。因此在信息化设计的管理思路中引入项目管理时间、质量、物料三要素的方法,在HMIS修车日计划的发布同时发布货车检修生产进度节点跟踪计划、货车检修质量预警控制及跟踪计划、货车检修物料配送计划,通过对时间、质量、物料的三个维度的管理,保证整车修车作业计划高质量、高效率的完成。
4.3.9
根据工位的生产进度情况展现整车的生产控制时间表。
系统程序界面
原手工管理计划执行情况跟踪
4.4
4.4.1
在每个生产工位旁边部署平板电脑,每个平板电脑展现本工位的车,实现对本车的进度、质量、物料过程监控。
进度报工及监控界面
质量反馈及控制界面
物料配送监控界面
4.4.2
现场生产物料配送及任务分配人员均采用手机进行临时用料的提报、任务分配和物料配送,可以通过手机的震动和声音提示随时知道生产现场的物料需求。
3
系统架构以货车段修数字化生产调度指挥为核心功能,满足“生产组织科学化、信息分析自动化、调度指挥智能化、基础数据网络化、设备设施标准化”的调度工作要求。提出生产关键工序及工艺流程的虚拟化货车检修模型。将生产调度指挥平台功能分为网络扣车管理拓展、5T指导检修综合应用、生产计划制定、生产进度实时监控、检修质量实时跟踪、生产物料配送、生产数据分析等模块。
系统程序界面
4.3.5
针对关键工序系统设置侧重点维护,可以根据来车的装用配件情况和加修工艺方案维护针对某个工序的检修质量侧重点,并在生产过程中工序开完工进行控制。
4.3.6
各项生产计划的制定是调度的一个重要工作,全段各车间均需按照段调度的计划进行生产检修,使用信息系统前,调度每日需通过电子邮件、电话、纸张传递等方式与各个车间进行联系,指导生产。调度工作忙碌且效率不高,以轴承质保期计划为例,调度需要针对每个车计算下次定检到期时间及本次检修是超期还是提前检修,方可确定本次装用轮对的轴承质保期,应用系统后原需要调度纸质方式、邮件形式传递的单据,包括复杂的计算全部由系统自动生成,调度不增加任何工作量,仅对原HMIS修车作业计划其他一切其他计划系统自动送达。大大节约了调度进行生产组织的时间。
数字化段修调度生产指挥系统在昆明北的应用
北京京天威科技发展有限公司
Beijing JingTianWei Science & Technology Development LTD.
1
1.1
车辆信息化检修信息化建设是保障车辆运行安全、提高生产效率和管理水平的重要手段。“铁路货车技术管理信息系统(HMIS)”已经全面推广运行10年了,在铁道部已基本实现全路货车动态技术履历信息采集和全路货车技术信息库的建设。车辆段作为货车段修、辅修、通过修一体的综合性铁路货车检修基地,目前全路大部分“HMIS系统”主要完成了货车检修信息的采集与上报,主要采用集中手工录入或半集中手工录入方式。
4.3.4
为应对离散型维修行业面临的物料准备计划性不强的特点,系统根据来车的技术状态及需要做的加装改造等特点,建立有针对性的必换配件配送模板,在车辆上台位前就实现全部必换配件的配送工作,另外对生产过程中常用料采用周转互换的管理模式,检修现场仅仅对非常用的零星料进行配送,大大降低了物料对生产进度的影响。
1.2
随着大数据时代的到来,传统产业目前正处于一个新的变革周期,以数据分析为思维的经营和管理思路将成为大多数企业进行企业日常管理的依据,而在这种以数据为标的的决策制定中,企业获取的分析数据需要是直观的,动态的,及时的,具有了大数据和全样本的优势,将能够直接指导企业进行生产和经营决策。数据资源将成为企业重要的,甚至是核心的资产组成。数据,不再是简单的报表数据,而是以搜索、定位、地图、APP、管理系统等多种渠道建立的海量的,全样本的,动态的大数据。掌握这些数据的企业将是本轮变革的胜利者。
2、5T联合查询
输入一个车号,系统支持将一段时间内全路发生的 5T故障显示出来。
4.3
生产现场的实时进度是本次调度指挥重点,能充分体现生产调度指挥的优势,并且和影响生产的关键工序转向架流水线实时动态关联,用全局的视角实时展示现场生产进度情况,因此本次增加的主要硬件费用在生产现场部分。首先以段修台位阶段计划为基础,用大屏幕及台位电脑显示,由工位作业者上传现车主要工序的实时进度,转向架各工序进度自动采集,提供管理人员日生产交车、调车的决策依据,及时干预。
பைடு நூலகம்4.5
4.5.1
4.5.2
4.5.3
4.5.4
随着生产节拍加快、数字检修设备增加、精细管理的管理思想逐步深化,车辆段的信息化建设已经不满足于仅仅作为铁道部货车检修数据库“信息采集终端”的角色,迫切希望建设一套服务于现场基础数据采集、生产过程控制、成本管理分析、支持数字化决策的智能化信息系统。满足《段规》 、《轮规》及(《关于做好2012年检修工作的通知》运辆货车函[2012] 44 号)以及“货车检修图形化管理”的要求,数字化车辆段的设计拟对HMIS系统进行整体规划,不但强化货车检修工装、工艺,更进一步从管理思路的转变、管理方式的变革,来提高生产效率、促进产业升级。
本次数字化车辆段以建立货车检修数据库为出发点,实现货车检修基础数据、生产过程数据、成本控制数据、决策分析数据的基本模型,并形成综合应用。
2
紧紧围绕“精益管理,创新发展”的企业管理核心理念,形成以GIS基础空间平台、数字化生产调度指挥、生产现场物料配送管理的数字化管理模型,以修车日计划为货车检修的出发点、派生出生产进度跟踪计划、质量跟踪计划、物料跟踪计划,形成货车检修全过程的数字化跟踪,确保货车检修安全、进度、质量,发挥信息化建设在铁路运输安全工作中的重要保证作用。
点进车号后系统自动显示某个股道台位车本工作者权限内的车及该车的工序,并自动携带该工序的计划完成时间,工作者仅仅需要对本工序开工、完工操作,就可以在生产进度大屏同步本工位作业的开完工时间,各工序之间有相互间工位的卡控顺序。
针对有5T报警,并且需要本岗位关注的故障,系统直接分配给相关岗位,相关岗位点击5T进入5T明细数界面,必须对所分配的5T故障确定施修方法,本岗位方可保存完工,将5T预报的落实细化到工位,关联到生产进度大屏的跟踪展现。对本工序需要关注的重要质量关键点,一样处理方法,将重点关注的质量点直接发送到所需注意的工位,引起加工者的重视。
4
4.1
4.1.1
根据车辆段提供的布局基础图,形成局管内线路及5T设备布点GIS图,实现5T设备、列建作业场、车辆段位置的矢量图展现,支持对地图的放大缩小,并对关键设备点的基础信息支持数据挖掘。实现管内货车线路上待扣车车辆的状态的动态展现。
4.1.2
形成车辆段内段管线的GIS布局图,结合调车车管理软件实景展现车辆段的段管线内存车的数量、状态、位置,并支持对段管线上的车辆调用扣车记录、车统-22B等检修记录,支持对车辆休时时长的颜色展现报警。
4.2.2
对管内的过期、到期、即将1月到期、即将2月到期进行统计分析。
4.2.3
对管内检修车经过的站点、实际已扣、过期未扣或已扣、到期未扣或已扣、即将一个到期未扣或已扣等情况进行统计分析。
4.2.4
实现对管内固定配属车位置及检修状态的跟踪。
4.2.5
对已扣检修车情况进行分析,掌握沿线扣车情况,实现自动显示,提示位置、数量信息,为扣车跟踪、掌握车源、甩挂作业提供数据,并有效掌握可用检修车资源,指导扣车工作。
建立在局管内:检修车进入铁路局全程跟踪扣修回送情况;重点跟踪车、管内循环车盯控运转过程及车辆状态。建立在段管内数字化调车作业流程,全程跟踪货车检修进度、质量、物料配送过程。系统架构GIS平台为支撑展现平台,建立虚拟数字化车辆段作业模型,将货车的台位、检修状态、设备位置及基本信息挂接,实景展现货车检修的大数据之间逻辑关联关系。
4.3.1
智能调车管理及股道车辆显示功能,段修生产管理功能。智能调车管理及股道车辆显示功能,根据段内股道情况及各车型的换长,验证计划员编制的作业计划是否可行,统计显示段内股道检修车、交验车、待修车实时存放情况。调车结束后,系统自动在段GIS存车线上显示出来。
4.3.2
为应对离散为主、流程为辅单件、小批量的货车维修行业无法应对来车情况,每个车的修理工艺多样性的特点,系统将原来无法预测的货车基本情况、5T故障情况、包括该车的运行典故情况及近期铁道部要求的关注质量侧重点,通过全路流转的大数据及本单位的数据管理,在调度做计划的同时生成每个货车不同的有针对性的检修指导方案,指导生产检修。
4.2
通过网络扣车系统预报数据,结合管内现车、AEI系统,实现当月厂修,段修车数量,所在位置情况的查询,实现管内检修车分析-位置,管内检修车分析-车型,运用车间分析-辖区,次月到期车数量情况查询分析,为检修车扣留组织、分析提供基础数据。
4.2.1
对于要查询的检修车在GIS图形上进行跟踪查询,形象显示其具体位置。
4.3.7
每次调车组调车作业后会直接对调度已经做好的计划进行上台位操作,保证现场工作者工位机上展现当天在台位上的全部车辆。
4.3.8
由于各项计划及预案维护的细致准确,工作者在线录入界面非常简单,登陆界面是当天的检修车列表,并且每个车按今天的修车落成时间顺序排序,每个工序工作者知道今天工作的车和车的工作顺序。