OQA出货检验作业流程图
(完整)OQC检验流程图

Y
Y
生产部/采购部
品质部
品质部
品质部
品质部
生产部
采购部
品质部
品质部
《送验单》
《出厂检厂检验记录》
6。相关文件
6.1《不合格品控制程序》
6.2《纠正措施的控制程序》
6。3《预防措施的控制程序》
7。相关表单
7.1《成品检验记录表》
7。2《不合品通知单》
7。3《纠正预防措施验证表》
1.目的
对外购成品及公司自产产品之品质制定检验标准,管制其成品之品质,确保本公司品质达到应有之水准
2.适用范围
本规范适用于本公司成品品质检验。。
3。检验依据:
见检验卡片
4.名词定义:
OQC:对外购及自产产品进行入库前及出库之品质管控.
5.检验流程:
成品检验流程图
成品检验流程图
作 业 流 程
权责单位
记录表单
OQA作业规范

3. 权责 权责:
3.1 OQA 检验员:负责对制造部门送检入库的成品或半成品进行出货检验。 3.2 OQA 领班:及时安排检验员对送检产品进行检验并监督检验员按照规范正确作业,对检验数据进行统 计整理,定期发放产品出货品质报告,并监督确认因此产生的矫正预防措施执行性和有效性。 3.3 组长: 负责 OQA 检验作业指导书的制定,修改,指导和确认检验员作业,对异常进行追踪和确认。 3.4 制造: 负责成品和半成品的送检,对 OQA 判退品执行矫正预防措施。 3.5 PE: 负责对 OQA 检验发现的电性不良板进行分析,并依据分析结果拟定矫正预防措施。
轩敏电子(深圳) 轩敏电子(深圳)有限公司
Plexton Electronics(Shenzhen)Limited OQA 作业规范
版本 V1.0 新发行 修订内容 修订页次 文件编号 生效日期 版本 V1.0 修订日期 页次 修订者
NO
1
2
3
4
5
6
7
8
9
10
11
12
13
14
15
16
17
18
分 发 单 位
施行正常检 验 10 批中, 无 1 批被拒收 则用减量检 验
严格检验
减量检验
抽样转换图 抽样转换图
6.15:抽样计划调整转换只针对同一机种,如客户有特殊要求则依客户提供之抽样计划与允收 标准执行.
6.2 OQA 检验作业: 检验作业:
6.2.1: 送检单位需按正常送检批量为单位将包装好的产品送至待验区, 并立即开送检单给 OQA 检验员检验. 6.2.2: 送检核对: 检验员根据生产单位所开的送检单首先进行资料核对, 核对内容: 产品客户, 规格,机种名称,工单号,数量,要与生管出货排程和客户出货要求相关资料相符才接受检验. 6.2.3: 资料准备: 对应机种的 PACK JOB-BOM, 验收规范, 生产通知单, 出货排程, PI, ECN, OTCN, SPEC 及客户要求的相关文件. 6.2.4:具体检验内容: 6.2.4.1:核对客户提供的备忘录,查看出货客户有无特别要求,逐行核对 JOB-BOM 料号是否 与包装实物相符,验收规范核对要素以从里到外的原则检验, 6.2.4.2:半成品出货工令/风扇是否与出货排程要求一致,频率贴纸/风扇贴纸内容需与生产通 知单/PI 内容一致。若不相符首先查看有无 ECN 更改。条码贴纸位置,条码编排格式,附件放置 位置,彩盒贴纸位置是否与规范一致,彩盒贴纸内容需与料号描述一致,条码内容必需与出货排 程、PI 要求一致。 6.2.4.3: 对半成品功能测试依据《OQA 检验报表》上的项目逐一进行检验,并填写记录。对 所配出货附件必须实装使用,确保其功能正常,检验到不良项目时,需在该项目上注明 NG。 6.2.4.4: 根据检验情况在送检单上注明检验判定结果,如合格在送检单上签字放行。
OQC出货检验流程图

OQC出货检验流程图
作成日期: 批准 审核
作成
备货至出货区 OK 仓库 追溯同类不良 OQC
贴不良标识
OQC
出货报验
品质异常报告
ห้องสมุดไป่ตู้
OQC NG OQC 出货检验
置不合格物料区
仓库
不良原因分析 OK 制造 返工 OQC 重新检验 顾客特采 OQC 特采标识 业务 反馈给顾客 各相关部门 提出纠正预防措施 制造部 纠正预防措施实施 品管部 措施效果确认 项目部 特许出货 名词注解:1、 IQC 进料检验 2、 IPQC 制程检验 3、 PQC 半成品检验 4、 FQC 成品检验 5、 OQC 出货检验 效果标准化 出 货 仓库 报废 开具《出货检 验报告》
OQA 成品出货指引

1目的/ Purpose对出货的成品及配件的包装、外观质量及数量进行检验确认,保证产品出货前百分百的合格。
To check the package/appearance of shipment FG and Spare parts and confirm the quantity, Assure the hundred percent conformity to shipment.2适用范围/ Scope本指引适用于成品及配件出货品质检验。
This instruction is applied to the inspection process of FG and Spare parts shipment.3程序/ Procedure3.1 成品出货检验/FG shipment inspection.3.1.1 检查货柜要干净、干燥无破损。
Check the container which is required to clean, dry and undamaged.3.1.2 检查出货产品的包装标志与铭牌粘贴齐全、位置正确无破损。
Check the product’s packing label and nameplate which are required to complete , undamaged and rightposition.3.1.3 检查产品包装外观无变形、受潮破损。
Check the carton which is required to no distortion, dampness and damage.3.1.4 检查堆放产品的卡板使用正确(出口产品卡板使用非原木材质)、成品须完全摆放在卡板上、不可超出卡板(散装货除外),卡板无受潮、破损。
Check the pallet which is required to right and no dampness and damage, and the FG which is requiredto completely pile on the pallet and no excess (Exclude bulk).3.1.5 检查每板产品的打包带,固定牢靠无松脱,打包扣无尖锐凸起,应有的缠绕膜无脱落。
OQA出货检验作业流程图
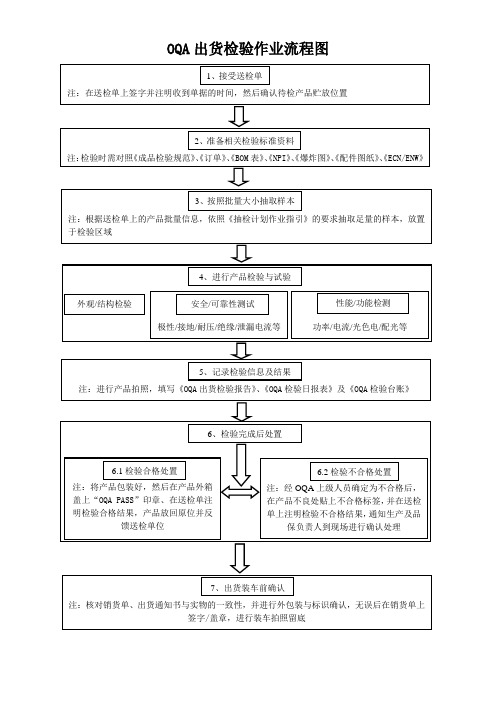
OQA 出货检验作业流程图
注:在送检单上签字并注明收到单据的时间,然后确认待检产品贮放位置 功率/电流/光色电/配光等 极性/
接地/耐压/绝缘/泄漏电流等 4、进行产品检验与试验 安全/可靠性测试 性能/功能检测 外观/结构检验 注:检验时需对照《成品检验规范》、《订单》、《BOM 表》、《NPI 》、《爆炸图》、《配件图纸》、《ECN/ENW 》 2、准备相关检验标准资料 1、接受送检单 注:进行产品拍照,填写《OQA 出货检验报告》、《OQA 检验日报表》及《OQA 检验台账》 5、记录检验信息及结果 注:根据送检单上的产品批量信息,依照《抽检计划作业指引》的要求抽取足量的样本,放置于检验区域 3、按照批量大小抽取样本。
OQC出货检验程序(含表格)

OQC出货检验程序(ISO9001-2015)1.0目的:为确保生产线所生产的成品品质符合客户品质要求,对整个出货检验过程进行有效的管理,特制定本程序.2.0范围:适用于汕头市万晖实业有限公司所有产品出货品质检验作业.3.0职责:3.1OQC:出货品质检验、品质判定、状态标识、异常反馈与跟踪、检验结果记录。
3.2QE:制定或修订出货品质检验标准、异常原因分析、异常跟踪及作业指导。
3.3生产部:出货待检通知、不合格批的重工作业、不合格品处理.3.4仓库:成品入库管理、库存超保质期成品再检通知。
3.5业务部:成品特采申请、重工作业安排.4.0定义无5.0作业内容5.1入库成品待检通知生产部入库待检的成品必须是经FQC全检并判定合格(需贴合格标识)的产品,入库前需核对入库数量与检验数量是否相符,最后将待检之成品移入成品仓库指定的出货待检区域。
然后开立《出货待检通知单》通知OQC进行出货检验。
5.3出货品质检验作业5.3.1检验依据OQC检验时依据《成品检验规范》、《产品检验标准书》、工程样办等对产品进行品质检验和判定,抽样作业时按照MIL-STD-105E普通Ⅱ级抽样,合格质量允收水准(AQL):致命缺陷(CRI):0、主要缺陷(MAJ):0.65、次要缺陷(MIN):1.5,若客户有特别要求按照客户要求的允收水准进行抽样作业,具体参照《抽样检验计划》执行.5.3.2检验项目检验项目包括:外观/尺寸/结构/特性/包装/标识等项目,具体检验项目参照《成品检验规范》中规定检验项目进行检验.5.3.3OQC出货检验作业时应按照抽样计划规定的抽检数量从待检批中的不同部位、不同箱号的箱子中抽取指定数量进行检验,尽量减少不量流入客户端.检验完成后需在《出货待检通知单》上进行品质判定,然后将《出货待检通知单》归还生产部.5.3.4正常情况出货检验需在6个工作小时内完成,急出货情形需在2个工作小时内完成检验.检验结果是否合格都需真实且详细的记录于《OQC成品检查报告》上,以便追溯和统计分析.5.3.5经OQC检验合格批次,由生产部门填写《成品入仓单》办理入库.5.4检验状态标识检验合格在标签上盖PASS印章,不合格贴红色REJECT标签,特采使用贴黄色特采使用标签.挑选或加工使用则贴挑选/加工使用标签.具体参考《产品标识与追溯性控制程序》.5.5品质异常反馈及处理经抽检判不合格批次,需在产品外箱上贴上红色的不合格(REJECT)标签,并将判定结果记录于《成品待检通知单》上并归还仓库,同时OQC开立《出货检验异常报告》给OQC组长确认/主管审核/经理核准,然后由业务/PMC/生产/品质/工程等相关单位会签评审.最终由(副)总经理批准,不合格批的处理方式按(副)总经理批准意见执行,会签完后将此单给责任单位进行原因分析和制定改善对策,至于检验发现之不合格品的处理方式参照《不合格品的控制程序》执行.5.6特采放行作业5.6.1经OQC检验不合格批产品,经公司(副)总经理批准决定特采使用的,由业务开立《特采申请单》并附上《出货检验异常报告》给品质部/工程部/生产部/PMC等相关单位会签评审,由公司(副)总经理批准执行,最后由OQC将不合格标签撕下,在标签上盖PASS印章,若是经客户同意特采使用需在外箱贴特采使用标识.5.7不合格批重工再检判重工的不合格批,OQC需对重工过程进行跟踪(包括重工项目是否与反馈之项目相符,重工之数量是否与判退的数量相符等内容),重工后生产部必须重新报验此批,并在《出货待检通知单》上注明”已重工”字样.重工再检OQC必须再次填写《OQC成品检查报告》,报告上需详细注明为”重工再检”字样,并详细记录《出货检验异常报告》编号和其他相关信息,以便于追溯.5.8库存成品再检所有库存成品超过保存期限,仓库必须重新提报给OQC重检和判定.重检后原标识需更换,若重检判不合格,需开立《出货检验异常报告》给相关单位会签评审,不合格批的处理参照5.5/5.6/5.7执行,不合格品参照《不合格品控制程序》执行.5.9控制计划的传递和执行5.9.1在新产品投产之前,由品质经理针对此项产品的特殊特性内容,对检查员进行培训,要求品管员严格按特殊特性的内容执行检查。
工厂出货检验流程图及工作细则

4、OQC根据《发货单》,按《组件出货检查表》进行检验检查。
5、OQC检验完毕,填写《组件出货检查表》进行检验检查。
6、OQC检验合格,在发货单上签名(须签全名,不允许只签姓名或者一个字、或字迹潦草—详见范本一);如发现不符合项,处理流程参见《不合格品控制程序》。
各种表单需经相关部门领导审批后方可生效。
7、仓管员在得到OQC检验员确认货物合格之后,尽快装箱发货,不得以各种理由推迟发货。
8、该批产品在厂门检查,保安人员须确认《发货单》上具备可识别的OQC人员的签名,否则不得放行出货。
《发货单》
《销售出库单》
《组件出货检查表》、《唛头打印规范》、《组件成品检验标准》
《不合格品控制程序》、《HOLD单》、《重工作业程序》、《重工单》
流程
责任部门
工作内容
相关文件/表单
商务部
商务部、仓库
仓库
OQC检பைடு நூலகம்员
OQC检验员
OQC检验员
仓库
保安
1、商务部根据出货计划安排,在OA上公布具体出货明细。
2、商务制定《发货单》,并督促销售和财务审核,由仓库打印、仓管员签名确认。仓管员确认单据明细无误后,由仓库账务员做销售出库单,将帐调出仓库,打印《销售出库单》并由仓管员和OQC共同签名确认。
OQC作业流程图
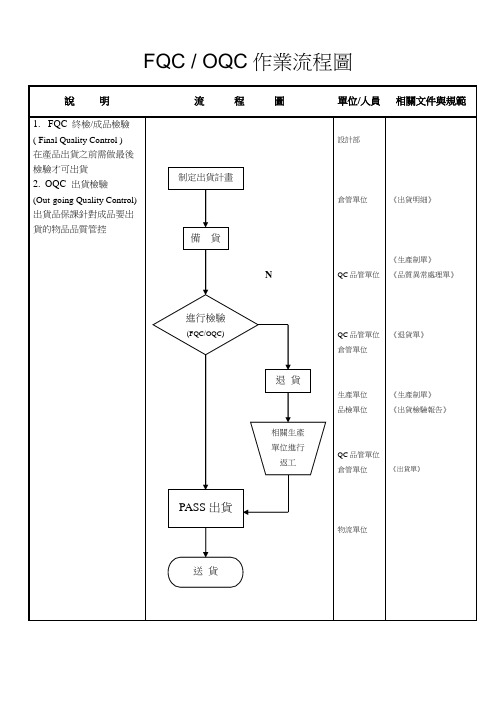
FQC / OQC作業流程圖製程巡檢作業辦法目的:落實品質意識在現場作業人員于制程過程中,實施檢驗或試驗以查證制程之合格性。
三〃範圍:凡本公司產品之各制程。
四、職責:生產部門:負責自製品自檢、送檢、重工、維修及入庫。
品保部門:負責自製品檢驗及記錄、標示。
五、內容:1、首件(產前樣/批版)、自主、巡迴檢驗:(1)品保部門IPQC人員在以下時段需做首件檢驗。
(1)每台機開始生產前開機需做首件檢驗。
(2)設計規格變更時需做首件檢驗。
(3)人員或材料更換時需做首件檢驗。
(2)生產部門作業人員應隨時注意生產產品品質狀況,並按照規定做好自主檢驗。
(3)品保部門IPQC人員應到現場做巡迴檢驗並做好記錄。
(4)品保部門檢驗管制程式,應按照規範和作業指導書之要求訂制(QC工程圖)。
(5)生產部門相關人員在制程中,發現不合格又無法矯正時,應及時停機報告主管,並通知品保部門,而品保部門應按照相關程式處理。
(6)品保部門IPQC人員按照實際檢驗情況記錄不合格品,並對制程式不良品作統計分析把結果回饋於相關部門,作糾正預防對策之依據。
(7)不合格品處理與標示(紅豆標&件投標):(1)、經判定為不合格品時,應在該批半成品貼上紅色圓點貼紙(故障貼紙)又稱紅豆,並加以區分,隨後將不合格批移至返工區或報廢區進行處理。
(2)、發生不合格品時,品保部門IPQC人員應填寫《IPQC服裝(巡廠)驗貨報告》加以記錄,並按照相關程序處理,並通知相關部門處理。
六〃使用表單:1、首件(制前樣/批版)吊卡2、特采申請單3、IPQC服裝(巡廠)驗貨報告4、返工\返修單5、報廢單6、制程異常備忘錄不合格品處理作業辦法一、目的:按照品質計畫及管制措施找出不合格品,採取各項管理及處理措施,並對不合格品進行分析,以防誤用。
二、範圍:供方之原材料、主輔料;廠內制程中之半成品、成品和庫存品;顧客之退貨品。
三、職責:生產、資材部門:負責不合格品標示、隔離及處理,必要時參與評審。
成品检验工作流程图

已投产机返工,生产再重送首件
首件检验合格,OQC通知生产线组长在《首件确认表》上签字确认后,生产部批量生产
首件检验合格,OQC批量抽检
根据产品检验标准、规范,《产品检验抽样规定》,设计文件,批量抽检
记录抽检的每台机流水号
首批检验合格机抽一箱做整箱落地试验
首批检验合格机(配有电源的产品)抽一箱做24小时煲机试验
检验员
OQC组长/PQC组长/PIE
OQC主管
检验员
PIE
每一订单生产的第一台机送OQC检验
按订单、样机、检验标准或规范、说明书、ECN、料表、设计文件作首件检验
填写《首件检查表》(外观、功能)
QE对首件及《首件检查表》确认,并签署合格与否意见
OQC、PQC和PIE对机确认,
不合格发出《OQC检验报告》,注明首件检查
根据抽检结果填写OQC检验报告
批量抽检不合格PQC、OQC、PIE对机确认
OQC主管在OQC检验报告上签字确认
OQC在生产部产成品送检单上填写REJ,注明不良项目,发出《OQC检验报告》,
工程PIE发出《坏机分析报告》,在线指导生产线返工,返工后重新送检
《首件检查表》
《检验流程,防止不合格出货,及时发现、纠正产品质量隐患,保证产品质量。
2.适用范围
适用于本厂加工、制造的各类产品的成品出货前的检验。
3.QA检验流程/职责和工作要求
流程
职责
工作要求
相关文件
/记录
首件检验
生产
生产
检验员
OQC组长
QE
PIE/OQC组长/PQC组长
OQC
PIE
生产部
OQC组长
品质检验流程

中山市木林森电子有限公司
中森(品)字第(200710)04号总第(104)号
三、 作业流程:退货供应商对策回复
特采NG 特采原物料(IQA)进料检验流程
成品(OQA)出货检验流程
关尺寸、外观、性能均以工程标准进行检验。
一、 目的:
二、 内容:
为确保原物料、成品品质有所保障,公司品质部门作业流程更加规范、统一。
关于灯具部及显示屏事业部原物料\成品检验的通知
合格后贴ACC
IQA签入库单
入库不良客诉(来料异常报告)供应商来料
仓库点收、开单
IQA检验
品质部门“IQA、OQA”从11/1起将按下列作业流程对原物料及成品做检验, 并以品质部门目前的检验方式和工程提供的标准进行作业、其原物料、成品之相业务通知单
仓库备货
OQA检验(数量、标签
、型号、装箱单)
贴ACC盖PASS章出货
厂内退货单
重工/人库
四、注意事项:
4-1、仓库管理员对原物料入库时必须确认其外包装是否有贴“ACC”标签,
否之不能够办理入库。
4-2、原物料出现异常需要特采时,必须由采购部门开立特采单以特采签核
程序完成签核,仓库方可发料。
4-3、当产线使用之原物料出显异常时,由生产部门以反馈单书面描述其不
良现象、比例经过技术部门确认、验证后转“IQA”开立“来料品质异常处
理报告”客诉供应商。
4-4、人库单据必须经过“IQA”检验人员确认后,材料方可人库。
由财务/
仓库确认稽核。
会签:
显示屏事业部:
灯具事业部:
采购部:
仓库:
品质部:
品质部:
2007-10-18。
QA出货检验流程图
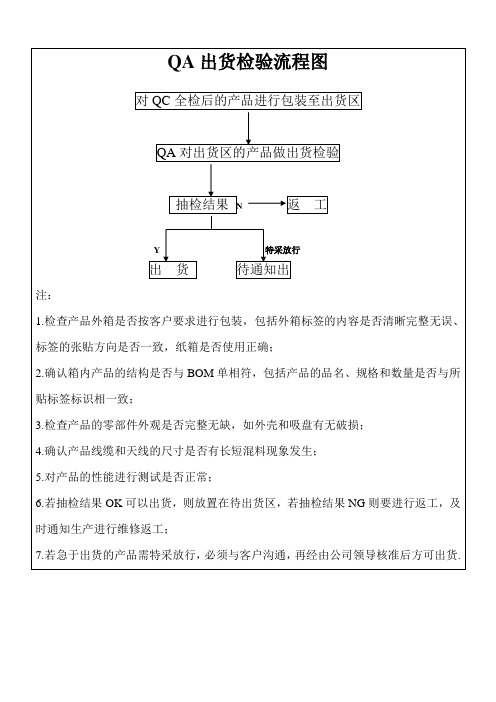
QA 对出货区的产品做出货检验
抽检结果
N
返
工
Y
特采放行
出
注:
货
待通知出
1.检查产品外箱是否按客户要求进行包装,包括外箱标签的内容是否清晰完整无误、 标签的张贴方向是否一致,纸箱是否使用正确; 2.确认箱内产品的结构是否与 BOM 单相符,包括产品的品名、规格和数量是否与所 贴标签标识相一致; 3.检查产品的零部件外观是否完整无缺,如外壳和吸盘有无破损; 4.确认产品线缆和天线的尺寸是否有长短混料现象发生; 5.对产品的性能进行测试是否正常; 6.若抽检结果 OK 可以出货,则放置在待出货区,若抽检结果 NG 则要进行返工,及 时通知生产进行维修返工; 7.若急于出货的产品需特采放行, 必须与客户沟通, 再经由公司领导核准后方可出货.
【推荐】2019年oqc出货检验流程图

OQC 出货检验流程图
OQC :成品出货检验 FQC :最终检验
追溯同类不良 贴不良标识
品质异常报告 置不合格物料区 不良原因分析
提出纠正预防措施
纠正预防措施实施
反馈给顾客 返 工 报 废
生产 业务 各相关部门 仓库
备货至出货区
出货报检
出货检验
NG
措施效果确认
效果标准化
生产部
质量执行科
自动化部
出 货
仓库 OK
FQC
FQC
FQC
仓库
OK
OQC 出货检验流程图
业务 自动化部
各相关部门
生产部 仓库 质量执行科
OK
NG
备货至出货区 出货报检
出货检验 追溯同类不良 贴不良标识 品质异常报告
措施效果确认 出 货 提出纠正预防措施
不良原因分析
置不合格物料区
反馈给顾客
纠正预防措施实施 效果标准化 返 工
报 废。
工厂出货检验流程图及工作细则
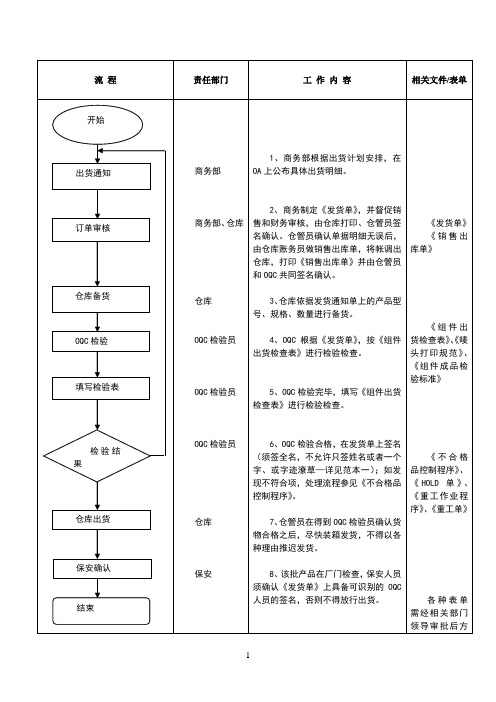
流程责任部门工Fra bibliotek内容相关文件/表单
商务部
商务部、仓库
仓库
OQC检验员
OQC检验员
OQC检验员
仓库
保安
1、商务部根据出货计划安排,在OA上公布具体出货明细。
2、商务制定《发货单》,并督促销售和财务审核,由仓库打印、仓管员签名确认。仓管员确认单据明细无误后,由仓库账务员做销售出库单,将帐调出仓库,打印《销售出库单》并由仓管员和OQC共同签名确认。
3、仓库依据发货通知单上的产品型号、规格、数量进行备货。
4、OQC根据《发货单》,按《组件出货检查表》进行检验检查。
5、OQC检验完毕,填写《组件出货检查表》进行检验检查。
6、OQC检验合格,在发货单上签名(须签全名,不允许只签姓名或者一个字、或字迹潦草—详见范本一);如发现不符合项,处理流程参见《不合格品控制程序》。
7、仓管员在得到OQC检验员确认货物合格之后,尽快装箱发货,不得以各种理由推迟发货。
8、该批产品在厂门检查,保安人员须确认《发货单》上具备可识别的OQC人员的签名,否则不得放行出货。
《发货单》
《销售出库单》
《组件出货检查表》、《唛头打印规范》、《组件成品检验标准》
《不合格品控制程序》、《HOLD单》、《重工作业程序》、《重工单》
成品检验出货作业流程图

OQC月報
3. QE﹑IPQC需對檢驗問題點進行追蹤,協助MFG進行品質改善.
審核:
時效
分析時間60分鐘,短 期對策24小時,長期 對策72小時
制作:
1. 需查詢相關工作報告,BOM﹑工單、FCN等,確保產品符合規格要求 2. 核對無誤后,準備該機種的SIP,准備所需檢驗工具 、量具.
1. 抽樣與收退參照MIL-STD-105E LEVEL Ⅱ. AQL﹕ 0.65% (2MI=1MA)
2.檢驗時參照成品檢驗作業標準 3. 在檢驗時需做好靜電防護.
成品判定單
BOM&FCN
MIL-STD -105E 抽樣計划表
Corrective Action Requisition Sheet
Reject Label CAR單
作 業說明
1. 送驗品必須經100%功能測試、外觀檢驗、 附件、包裝無問題方能送于QA檢驗.
1.成品判定單需填寫清楚批量﹑工單號﹑產品型號、客戶. 2. 需與實物相核對,成品判定上所寫與實物需完全相符.
出貨資料確認表 出貨單
OQC出貨檢查表
1.每批訂單出貨均需填寫OQC出貨檢查表,核對S/I,嘜頭,規格,數量等避免出錯貨或地方. 2. 出完貨后需把出貨資料確認表,出貨單,出貨檢驗表存檔,以便后續品質追蹤.
OQC周報
1. 每周一需匯總日報 交于助理制作OQC檢驗周報. 2.每月初需匯總周報 交于助理制作月報
OQC Inspection Report 1. 填寫 OQC Pass單貼于該批產品之成品判定單上 OQC Pass Label 2.檢驗結果記錄于OQC檢驗日報表
工單繳庫單
1. 當包裝繳庫時,OQC人員需在繳庫單上簽字確認.
PZ-003 OQA出货检验规范
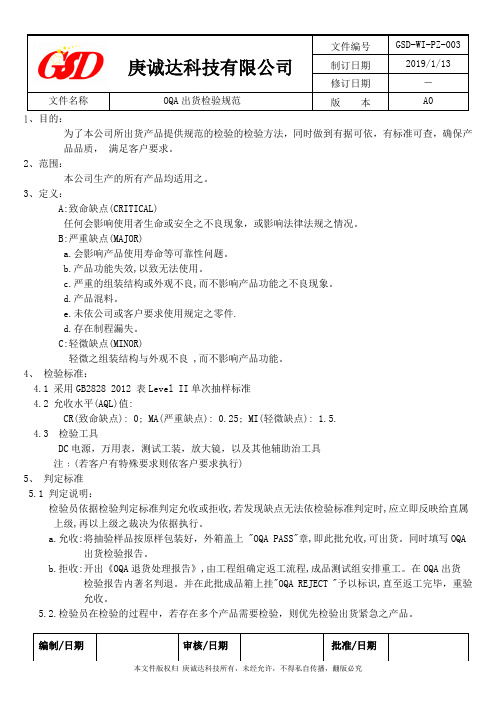
文件名称1、目的:为了本公司所出货产品提供规范的检验的检验方法,同时做到有据可依,有标准可查,确保产品品质,满足客户要求。
2、范围:本公司生产的所有产品均适用之。
3、定义:A:致命缺点(CRITICAL)任何会影响使用者生命或安全之不良现象,或影响法律法规之情况。
B:严重缺点(MAJOR)a.会影响产品使用寿命等可靠性问题。
b.产品功能失效,以致无法使用。
c.严重的组装结构或外观不良,而不影响产品功能之不良现象。
d.产品混料。
e.未依公司或客户要求使用规定之零件.d.存在制程漏失。
C:轻微缺点(MINOR)轻微之组装结构与外观不良 ,而不影响产品功能。
4、检验标准:4.1 采用GB2828 2012 表Level II单次抽样标准4.2 允收水平(AQL)值:CR(致命缺点): 0; MA(严重缺点): 0.25; MI(轻微缺点): 1.5.4.3 检验工具DC电源,万用表,测试工装,放大镜,以及其他辅助治工具注﹕(若客户有特殊要求则依客户要求执行)5、判定标准5.1 判定说明:检验员依据检验判定标准判定允收或拒收,若发现缺点无法依检验标准判定时,应立即反映给直属上级,再以上级之裁决为依据执行。
a.允收:将抽验样品按原样包装好,外箱盖上 "OQA PASS"章,即此批允收,可出货。
同时填写OQA出货检验报告。
b.拒收:开出《OQA退货处理报告》,由工程组确定返工流程,成品测试组安排重工。
在OQA出货检验报告内著名判退。
并在此批成品箱上挂"OQA REJECT "予以标识,直至返工完毕,重验允收。
5.2.检验员在检验的过程中,若存在多个产品需要检验,则优先检验出货紧急之产品。
文件名称6、作业流程6.1 作业流程图7、作业内容:7.1 开包装检查:7.1.1 检查包装内产品是否会挤压,拉扯,是否符合要求。
文件名称 7.1.2 注意无混产品现象。
7.2 外观检查: 7.2.1 产品外观无明显脏污异物,无破损 7.2.2 铜皮无明显受损,大器件无影响客户组装之倾斜不良 。
- 1、下载文档前请自行甄别文档内容的完整性,平台不提供额外的编辑、内容补充、找答案等附加服务。
- 2、"仅部分预览"的文档,不可在线预览部分如存在完整性等问题,可反馈申请退款(可完整预览的文档不适用该条件!)。
- 3、如文档侵犯您的权益,请联系客服反馈,我们会尽快为您处理(人工客服工作时间:9:00-18:30)。
OQA 出货检验作业流程图
注:在送检单上签字并注明收到单据的时间,然后确认待检产品贮放位置 功率/电流/光色电/配光等 极性/
接地/耐压/绝缘/泄漏电流等 4、进行产品检验与试验 安全/可靠性测试 性能/功能检测 外观/结构检验 注:检验时需对照《成品检验规范》、《订单》、《BOM 表》、《NPI 》、《爆炸图》、《配件图纸》、《ECN/ENW 》 2、准备相关检验标准资料 1、接受送检单 注:进行产品拍照,填写《OQA 出货检验报告》、《OQA 检验日报表》及《OQA 检验台账》 5、记录检验信息及结果 注:根据送检单上的产品批量信息,依照《抽检计划作业指引》的要求抽取足量的样本,放置于检验区域 3、按照批量大小抽取样本。