一种从废三元催化剂中提纯铂族金属的方法
从废催化剂中回收铂的方法

从废催化剂中回收铂的方法废催化剂是一种含有铂催化剂的废弃材料,常见于石油炼制、化工和汽车尾气处理等工业过程中。
由于铂是一种稀有且贵重的金属,因此废催化剂中的铂可以通过回收和再利用来降低成本和减少环境影响。
下面将介绍一些常见的废催化剂回收铂的方法。
1.物理方法:物理方法主要通过物理分离和提纯的方式来回收铂。
首先,可以采用磁力分离或重力分离的方法将废催化剂与其他杂质分离。
随后,可以通过重力沉淀、离心、过滤等方法去除悬浮颗粒和固体杂质。
最后,通过高温煅烧或浸泡在强酸溶液中使铂与其他杂质分离,得到纯铂颗粒。
然而,物理方法的回收率有限,无法完全分离铂与其他金属元素。
2.化学方法:化学方法主要通过溶解和沉淀反应来回收铂。
在一定温度和压力条件下,可以使用浓硫酸、浓盐酸、硝酸等强酸溶液来将废催化剂中的铂溶解为金属离子。
然后,通过还原剂如次氯酸钠、亚硫酸钠等将铂离子还原为金属铂。
最后,通过沉淀反应使铂沉淀下来。
该方法可以实现较高的回收率,但需要考虑使用和处理强酸的安全性和环境影响。
3.浸提法:浸提法主要通过有机溶剂和络合剂来回收铂。
废催化剂首先与有机溶剂如醇类、酮类等进行浸泡,使铂与有机溶剂发生萃取反应。
然后,加入络合剂如饮用水硷、乙二胺四乙酸等,使铂形成稳定络合物。
最后,通过蒸馏或萃取的方式将铂从络合物中分离出来得到纯铂。
但该方法在工业上应用较少,需要考虑有机溶剂和络合剂的选择和再生。
4.焙烧还原法:焙烧还原法主要通过高温下将废催化剂焙烧,使其与氧气反应生成氧化物。
随后,通过还原剂如氢气将氧化物还原为纯净的金属铂。
该方法具有简单易行、高效节能的优点,但需要考虑气体排放和设备安全。
在实际的铂回收过程中,通常会综合运用上述的多种方法。
同时,为了提高回收率和降低成本,可以针对废催化剂的物化性质和含铂量进行预处理和优化设计。
此外,回收铂的过程还需要关注环境污染和职业健康安全问题,选择适当的处理设备和工艺流程,确保回收过程的可持续性和减少对环境的影响。
从废三元催化剂中提纯铂族金属的方法
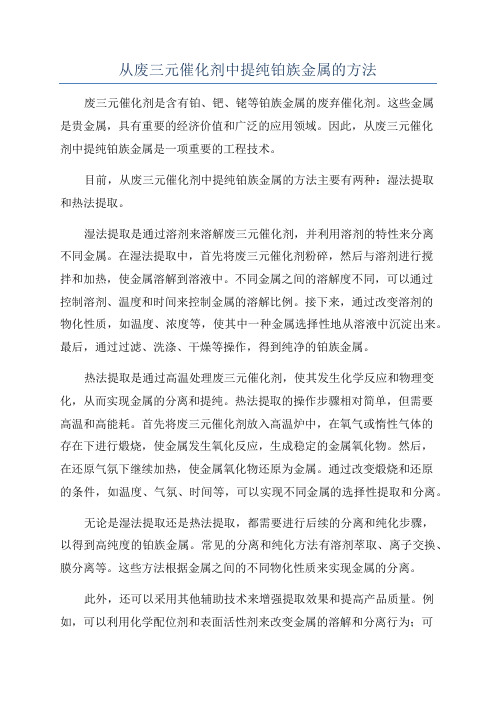
从废三元催化剂中提纯铂族金属的方法废三元催化剂是含有铂、钯、铑等铂族金属的废弃催化剂。
这些金属是贵金属,具有重要的经济价值和广泛的应用领域。
因此,从废三元催化剂中提纯铂族金属是一项重要的工程技术。
目前,从废三元催化剂中提纯铂族金属的方法主要有两种:湿法提取和热法提取。
湿法提取是通过溶剂来溶解废三元催化剂,并利用溶剂的特性来分离不同金属。
在湿法提取中,首先将废三元催化剂粉碎,然后与溶剂进行搅拌和加热,使金属溶解到溶液中。
不同金属之间的溶解度不同,可以通过控制溶剂、温度和时间来控制金属的溶解比例。
接下来,通过改变溶剂的物化性质,如温度、浓度等,使其中一种金属选择性地从溶液中沉淀出来。
最后,通过过滤、洗涤、干燥等操作,得到纯净的铂族金属。
热法提取是通过高温处理废三元催化剂,使其发生化学反应和物理变化,从而实现金属的分离和提纯。
热法提取的操作步骤相对简单,但需要高温和高能耗。
首先将废三元催化剂放入高温炉中,在氧气或惰性气体的存在下进行煅烧,使金属发生氧化反应,生成稳定的金属氧化物。
然后,在还原气氛下继续加热,使金属氧化物还原为金属。
通过改变煅烧和还原的条件,如温度、气氛、时间等,可以实现不同金属的选择性提取和分离。
无论是湿法提取还是热法提取,都需要进行后续的分离和纯化步骤,以得到高纯度的铂族金属。
常见的分离和纯化方法有溶剂萃取、离子交换、膜分离等。
这些方法根据金属之间的不同物化性质来实现金属的分离。
此外,还可以采用其他辅助技术来增强提取效果和提高产品质量。
例如,可以利用化学配位剂和表面活性剂来改变金属的溶解和分离行为;可以采用电化学和电解方法,通过电极反应将金属还原或沉积到电极上;可以利用微生物和生物技术,利用生物体的特殊功能来分离金属。
总之,从废三元催化剂中提纯铂族金属是一项复杂的工程技术,需要采用适当的方法和技术,经过多个步骤的操作和处理。
这不仅对于节约资源、保护环境具有重要意义,也可以有效地回收和利用贵金属资源,实现资源的循环利用。
从废催化剂中回收铂的方法

从废催化剂中回收铂的方法
废催化剂是指在化学反应中使用完毕或失效的催化剂,其中包含有价
值的金属铂。
回收废催化剂中的铂对于资源的高效利用具有重要意义。
以
下是从废催化剂中回收铂的几种常见方法。
1.干法氯化铂法:
首先,将废催化剂和氯化铁一起加热到高温,产生化学反应,将铂氯
化为氯化铂。
然后,将混合物与氯化铈一起再次加热,将氯化铂还原为金
属铂。
最后,用水洗涤,析出纯净的金属铂粉末。
2.湿法铂电解法:
将废催化剂与硫酸浸泡,使铂溶解在硫酸中形成铂酸盐。
然后,将铂
酸盐溶液转移到电解槽中,通过电流进行电解,沉积出纯净的金属铂。
3.湿法溶解法:
将废催化剂与盐酸浸泡,将铂溶解在盐酸中形成铂氯化物。
然后,将
溶液过滤,去除杂质。
接下来,将过滤后的溶液与电解质澄清剂混合,通
过反应使铂离子还原为金属铂沉淀。
最后,用水洗涤,得到纯净的金属铂。
4.溅射法:
将废催化剂中的铂物质喷涂在基底上,并在真空环境中使用溅射方法,将铂物质从废催化剂上剥离出来,沉积在基底上形成铂膜。
然后,将铂膜
从基底上取下,进行进一步的加工和处理,得到纯净的金属铂。
以上是几种常见的从废催化剂中回收铂的方法。
不同的方法适用于不
同的废催化剂,具体的回收工艺需要根据实际情况进行选择。
此外,在回
收过程中要注意环保,防止废弃物排放对环境造成污染。
同时,提高废催
化剂中铂的回收率和纯度,对于资源的高效利用和经济效益都具有重要意义。
从a-Al2O3载体废催化剂中回收铂

从a-Al2O3载体废催化剂中回收铂背景铂是一种贵重金属,广泛应用于工业生产和高科技制造,如汽车催化剂和电子器件等。
由于其资源稀缺,铂的回收利用已成为重要的经济和环境问题。
a-Al2O3载体废催化剂中铂含量较高,是回收铂的重要来源之一。
本文将介绍一种从a-Al2O3载体废催化剂中提取铂的方法。
实验原理将废催化剂样品与盐酸和硝酸混合,进行酸处理,使载体中的铝等杂质离解溶解在溶液中。
经过过滤和洗涤等工序,使铝离子从溶液中去除。
接着使用NH4Cl还原还原铂离子生成Pt颗粒。
最后通过加热使Pt颗粒与载体分离,实现铂的回收。
实验步骤1.将废催化剂样品放到荧光屏下观察,确认粉末是否为细小颗粒,判断是否要进行打球操作。
2.将废催化剂样品放入酸洗锅中,加盖并啓动加热装置(需注意安全)。
3.将HCl与HNO3按体积比2:1添加到酸洗锅中,加盖防止外泼。
4.制备铝用控制,加入0.1 g/L。
盐酸和硝酸混合后倒入酸洗锅中使其与废催化剂样品接触1h.5.形成悬浮液之后,用玻璃棒搅拌,使溶液均匀。
催化剂处理结束后,将水龙头开至最大,把酸洗锅中的物料倒到过滤袋中进行过滤。
然后用纯水反复冲洗,并用无尘纸吸干。
6.在重量为15 g的聚酰胺切割机中,先切下聚酰胺膜片,然后在机上修正重量为12 g。
将切好的膜片悬挂在过滤带上。
7.将精细Pt 0.05 g和NH4Cl10g 混合后加入聚酰胺膜片中用平板式反应器进行还原反应。
控制初始温度为60℃,10min后升温到80-90℃,反应1h。
还原反应完后,过滤洗涤,脱水干燥获取回收物。
结果分析通过上述实验,成功从a-Al2O3载体废催化剂中回收了铂元素。
铂的回收率取决于样品的质量、初始铂含量和实验操作等多个因素。
铂的纯度也可能会受到样品的其他成分的污染而降低。
结论本实验成功从a-Al2O3载体废催化剂中回收了铂元素,方法简单有效。
但回收率受到诸多因素影响,需要通过多次实验确定最佳操作条件,以提高回收效率和纯度。
废三元催化中提取铂

从废三元催化剂中提纯铂族金属的方法本发明涉及一种废汽车催化剂的回收利用方法,特别是涉及一种从废三元催化剂中提纯铂族金属的方法,是对现有废汽车催化剂中铂族金属的回收方法的改进,属于废物回收利用和贵金属冶金技术领域。
背景技术。
目前废汽车催化剂中铂族金属的回收方法主要可以分为火法和湿法。
火法提取铂族金属的基本流程是将汽车催化剂加入熔化的金属收集剂中加热熔融、合金相与炉渣相的分离、合金相用强酸溶解使铂族金属进入溶液。
但是火法冶金提取铂族金属工艺复杂,能量和原料消耗大,设备要求高,环境污染问题不易解决,不宜推广。
湿法处理废催化剂有载体溶解法、全溶解法和活性组分溶解法等工艺。
与火法工艺相比,湿法处理废催化剂具有流程短、投资节省等特点,湿法工艺的不足在于铑的提取率低,一般为65—80%左右,回收率偏低。
终上所述,现有的由废汽车催化剂提取铂族金属方法中,无论是湿法还是火法工艺,都或存在作业环境差、铂族金属收率低、能量消耗大等问题,还有待于进一步改进和完善。
发明内容本发明的目的就在于克服现有技术存在的不足,针对现有从废汽车催化剂铂族金属回收方法存在的问题,给出了在回收铂族金属流程中加入催化剂预处理和使用不同氧化剂做浸出剂的一种从废三元催化剂中提纯铂族金属的方法,具有作业环境好、铂族金属收率高、能量消耗小的特点。
本发明给出的技术解决方案是:这种从废三元催化剂中提纯铂族金属的方法,其特点是:首先对废三元催化剂破碎研磨至少200目,并进行高温焙烧除碳、硫,后经硼氢化钠水溶液还原。
并在浸出时加入亚氯酸钠作为氧化剂,具体有以下步骤。
(1)经破碎研磨、高温焙烧得到的废三元催化剂,加入2~4%质量比的硼氢化钠水溶液煮沸还原,铂族金属活性得到增强。
(2)将步骤(1)得到的还原液过滤,配入氯化钠和亚氯酸钠的盐酸溶液,混匀后转入浸出装置,然后在85~90℃进行浸出时间至少180min,过滤得到固体催化剂,再加入10%HCl酸洗(80℃,20min)和水洗(80℃,20min),将洗液和浸出液合并,浓缩,化验。
三元催化提炼贵金属方法

三元催化提炼贵金属方法
1、三元催化剂粉碎后焙烧:将废三元催化剂粉碎粉碎至200目以上,高温焙烧去除碳和硫,用硼氢化钠水溶液还原。
在浸出过程中加入亚氯酸钠作为氧化剂。
2、加入硼氢化钠溶液煮沸:加入质量比为2~4%的硼氢化钠溶液煮沸,得到的还原液经过滤后与氯化钠、亚氯酸钠盐酸溶液混合,混匀后转入浸出装置。
3、过滤得固体催化剂:在85℃~90℃温度下,浸出时间至少需要180min,过滤可以获得固体催化剂。
4、加入酸洗和水洗分离纯化得铂族金属:加入10%HC1酸洗(80℃,
20min)和水洗(80℃,20min),将洗涤液和浸出液结合,浓缩,分析,得到浓缩浸出液,对铂族金属进行分离纯化,可以得到高纯度的铂族金属。
- 1、下载文档前请自行甄别文档内容的完整性,平台不提供额外的编辑、内容补充、找答案等附加服务。
- 2、"仅部分预览"的文档,不可在线预览部分如存在完整性等问题,可反馈申请退款(可完整预览的文档不适用该条件!)。
- 3、如文档侵犯您的权益,请联系客服反馈,我们会尽快为您处理(人工客服工作时间:9:00-18:30)。
1/1页
1.一种从废三元催化剂中提纯铂族金属的方法,其特征在于首先对废三元催化剂破碎研磨,并进行高温焙烧除碳、硫后,经硼氢化钠水溶液还原,并在浸出时加入亚氯酸钠作为氧化剂,具体有以下步骤:
(1) 经破碎研磨、高温焙烧得到的废三元催化剂,加入2~4%质量比的硼氢化钠水溶液煮沸还原,铂族金属活性得到增强;
(2) 将步骤(1)得到的还原液过滤,配入氯化钠和亚氯酸钠的盐酸溶液,混匀后转入浸出装置,然后在85~90℃进行浸出时间至少180min ,过滤得到固体催化剂,再加入10%HCl 酸洗(80℃,20min )和水洗(80℃,20min ),将洗液和浸出液合并,浓缩,化验;
(3)将步骤(2)得到浓缩后的浸出液,进行铂族金属分离,提纯,得到高纯铂族金属。
2.根据权利要求1所述从废三元催化剂中提纯铂族金属的方法,其特征在于步骤(1)中对废三元催化剂破碎研磨至少200目,并在600℃下高温焙烧。
3.根据权利要求1所述从废三元催化剂中提纯铂族金属的方法,其特征在于步骤(2)中加入10%HCl 酸洗至少两次。
权 利 要 求 书CN 103131857 A
一种从废三元催化剂中提纯铂族金属的方法
技术领域
[0001] 本发明涉及一种废汽车催化剂的回收利用方法,特别是涉及一种从废三元催化剂中提纯铂族金属的方法,是对现有废汽车催化剂中铂族金属的回收方法的改进,属于废物回收利用和贵金属冶金技术领域。
背景技术
[0002] 目前废汽车催化剂中铂族金属的回收方法主要可以分为火法和湿法。
火法提取铂族金属的基本流程是将汽车催化剂加入熔化的金属收集剂中加热熔融、合金相与炉渣相的分离、合金相用强酸溶解使铂族金属进入溶液。
但是火法冶金提取铂族金属工艺复杂,能量和原料消耗大,设备要求高,环境污染问题不易解决,不宜推广。
[0003] 湿法处理废催化剂有载体溶解法、全溶解法和活性组分溶解法等工艺。
与火法工艺相比,湿法处理废催化剂具有流程短、投资节省等特点,湿法工艺的不足在于铑的提取率低,一般为65—80%左右,回收率偏低。
[0004] 终上所述,现有的由废汽车催化剂提取铂族金属方法中,无论是湿法还是火法工艺,都或存在作业环境差、铂族金属收率低、能量消耗大等问题,还有待于进一步改进和完善。
发明内容
[0005] 本发明的目的就在于克服现有技术存在的不足,针对现有从废汽车催化剂铂族金属回收方法存在的问题,给出了在回收铂族金属流程中加入催化剂预处理和使用不同氧化剂做浸出剂的一种从废三元催化剂中提纯铂族金属的方法,具有作业环境好、铂族金属收率高、能量消耗小的特点。
[0006] 本发明给出的技术解决方案是:这种从废三元催化剂中提纯铂族金属的方法,其特点是:首先对废三元催化剂破碎研磨至少200目,并进行高温焙烧除碳、硫,后经硼氢化钠水溶液还原。
并在浸出时加入亚氯酸钠作为氧化剂,具体有以下步骤。
[0007] (1)经破碎研磨、高温焙烧得到的废三元催化剂,加入2~4%质量比的硼氢化钠水溶液煮沸还原,铂族金属活性得到增强。
[0008] (2)将步骤(1)得到的还原液过滤,配入氯化钠和亚氯酸钠的盐酸溶液,混匀后转入浸出装置,然后在85~90℃进行浸出时间至少180min,过滤得到固体催化剂,再加入10%HCl酸洗(80℃,20min)和水洗(80℃,20min),将洗液和浸出液合并,浓缩,化验。
[0009] (3)将步骤(2)得到浓缩后的浸出液,进行铂族金属分离,提纯,得到高纯铂族金属。
[0010] 为更好的实现本发明的目的,步骤(1)中对废三元催化剂破碎研磨至200目,并在600℃下高温焙烧。
[0011] 为更好的实现本发明的目的,步骤(2)中加入10%HCl酸洗至少两次。
[0012] 与现有技术相比,本发明的有益效果是。
[0013] 对汽车催化剂进行破碎到至少200目,增加铂族金属与浸出剂接触面积,提高了浸出率。
浸出剂选择方面考察NaClO 、NaClO 2、NaClO 3为不同氧化剂,浸出剂为等量Hcl-Nacl 体系,创新性的选择NaClO 2 为氧化剂提高铂族金属浸出率。
[0014] 表1 不同氧化剂浸出铂族金属数据表。
NaClO NaClO 2NaClO 3Pt
96%97.6%97.4%Pd
96.46%98.22%97.6%Rh 80.76%89.46%84.91%
具体实施方案
[0015] 实施例1。
[0016] 取含铂钯铑三种贵金属元素的废三元催化剂2000g ,用颚式破碎机粉碎至多少200目后,600℃下焙烧2h ,含40g 质量比硼氢化钠的纯水3L 煮沸20min,再用80℃纯水3L 浸泡20min 。
加入130g 氯化钠,60g 亚氯酸钠0.5LHCl 的3L 水溶液中浸出3小时,然后抽滤,10%的稀HCl 酸洗2次、水洗1次将浸出液洗液合并,浓缩至3L ,将浓缩后浸出液加入树脂分离铂族金属,提纯,并进行化验。
[0017] 结果。
[0018] 铂回收率:95.5%,产出海绵铂的纯度99.95。
[0019] 钯回收率:95.87%,产出海绵钯纯度99.96。
[0020] 铑回收率:85.8%,产出海绵铑纯度99.95。
[0021] 实施例2。
[0022] 取含铂钯铑三种贵金属元素的废催化剂2000g ,用颚式破碎机粉碎200目后,600℃下焙烧2h ,含60g 硼氢化钠的纯水3L 煮沸20min,再用80℃纯水3L 浸泡20min 。
加入150g 氯化钠,80g 亚氯酸钠0.5LHCl 的3L 水溶液中浸出4小时,然后抽滤,10%的稀HCl 酸洗2次、水洗1次将浸出液洗液合并,浓缩至3L ,将浸出液加入树脂分离铂族金属,提纯,并进行化验。
[0023] 结果。
[0024] 铂回收率:95.5%,产出海绵铂的纯度99.95。
[0025] 钯回收率:95.87%,产出海绵钯纯度99.96。
[0026] 铑回收率:85.8%,产出海绵铑纯度99.95。
[0027] 实施例3。
[0028] 取含铂钯铑三种贵金属元素的废催化剂1000g ,用颚式破碎机粉碎200目后,600℃下焙烧1h ,含30g 硼氢化钠的纯水3L 煮沸20min,再用80℃纯水3L 浸泡20min 。
加入120g 氯化钠,40g 亚氯酸钠0.4LHCl 的3L 水溶液中浸出3小时,然后抽滤,10%的稀HCl 酸洗2次、水洗1次将浸出液洗液合并,浓缩至3L ,将浸出液加入树脂分离铂族金属,提纯,并进行化验。
[0029] 结果。
[0030] 铂回收率:95.45%,产出海绵铂的纯度99.95。
[0031] 钯回收率:95.6%,产出海绵钯纯度99.95。
[0032] 铑回收率:85%,产出海绵铑纯度99.95。