PLATO软件操作手册-FMEA模块
FMEA手册
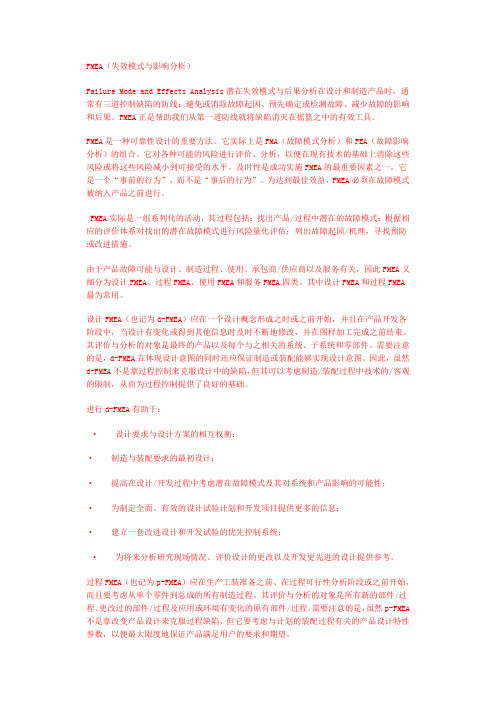
FMEA(失效模式与影响分析)Failure Mode and Effects Analysis潜在失效模式与后果分析在设计和制造产品时,通常有三道控制缺陷的防线:避免或消除故障起因、预先确定或检测故障、减少故障的影响和后果。
FMEA正是帮助我们从第一道防线就将缺陷消灭在摇篮之中的有效工具。
FMEA是一种可靠性设计的重要方法。
它实际上是FMA(故障模式分析)和FEA(故障影响分析)的组合。
它对各种可能的风险进行评价、分析,以便在现有技术的基础上消除这些风险或将这些风险减小到可接受的水平。
及时性是成功实施FMEA的最重要因素之一,它是一个“事前的行为”,而不是“事后的行为”。
为达到最佳效益,FMEA必须在故障模式被纳入产品之前进行。
FMEA实际是一组系列化的活动,其过程包括:找出产品/过程中潜在的故障模式;根据相应的评价体系对找出的潜在故障模式进行风险量化评估;列出故障起因/机理,寻找预防或改进措施。
由于产品故障可能与设计、制造过程、使用、承包商/供应商以及服务有关,因此FMEA又细分为设计FMEA、过程FMEA、使用FMEA和服务FMEA四类。
其中设计FMEA和过程FMEA 最为常用。
设计FMEA(也记为d-FMEA)应在一个设计概念形成之时或之前开始,并且在产品开发各阶段中,当设计有变化或得到其他信息时及时不断地修改,并在图样加工完成之前结束。
其评价与分析的对象是最终的产品以及每个与之相关的系统、子系统和零部件。
需要注意的是,d-FMEA在体现设计意图的同时还应保证制造或装配能够实现设计意图。
因此,虽然d-FMEA不是靠过程控制来克服设计中的缺陷,但其可以考虑制造/装配过程中技术的/客观的限制,从而为过程控制提供了良好的基础。
进行d-FMEA有助于:·设计要求与设计方案的相互权衡;·制造与装配要求的最初设计;·提高在设计/开发过程中考虑潜在故障模式及其对系统和产品影响的可能性;·为制定全面、有效的设计试验计划和开发项目提供更多的信息;·建立一套改进设计和开发试验的优先控制系统;·为将来分析研究现场情况、评价设计的更改以及开发更先进的设计提供参考。
最全的FMEA教程和讲解
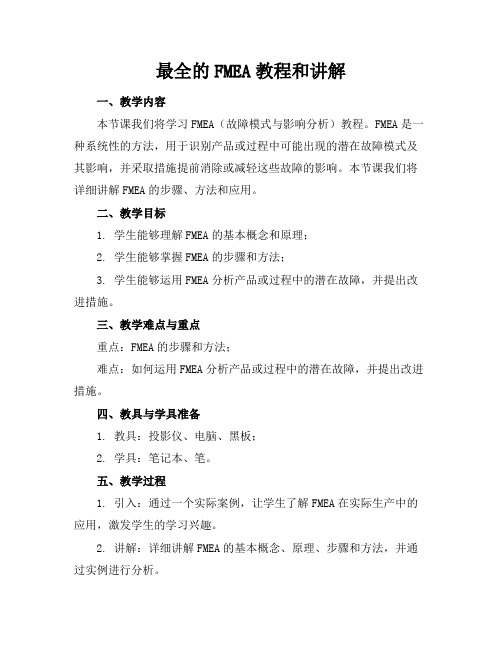
最全的FMEA教程和讲解一、教学内容本节课我们将学习FMEA(故障模式与影响分析)教程。
FMEA是一种系统性的方法,用于识别产品或过程中可能出现的潜在故障模式及其影响,并采取措施提前消除或减轻这些故障的影响。
本节课我们将详细讲解FMEA的步骤、方法和应用。
二、教学目标1. 学生能够理解FMEA的基本概念和原理;2. 学生能够掌握FMEA的步骤和方法;3. 学生能够运用FMEA分析产品或过程中的潜在故障,并提出改进措施。
三、教学难点与重点重点:FMEA的步骤和方法;难点:如何运用FMEA分析产品或过程中的潜在故障,并提出改进措施。
四、教具与学具准备1. 教具:投影仪、电脑、黑板;2. 学具:笔记本、笔。
五、教学过程1. 引入:通过一个实际案例,让学生了解FMEA在实际生产中的应用,激发学生的学习兴趣。
2. 讲解:详细讲解FMEA的基本概念、原理、步骤和方法,并通过实例进行分析。
3. 练习:让学生分组进行练习,运用FMEA分析给定的产品或过程,并提出改进措施。
4. 讨论:让学生分享各自的分组练习成果,讨论改进措施的可行性和有效性。
六、板书设计1. FMEA的基本概念和原理;2. FMEA的步骤和方法;3. 实例分析。
七、作业设计1. 题目:请运用FMEA分析给你们分组的产品或过程,并提出改进措施。
2. 答案:根据实际分析结果,给出改进措施。
八、课后反思及拓展延伸1. 反思:回顾本节课的教学内容,思考如何更好地让学生掌握FMEA的方法和应用。
2. 拓展延伸:研究FMEA在其他领域的应用,如质量管理、安全管理等,并尝试将其应用于实际工作中。
教学内容完毕。
重点和难点解析一、教学内容本节课我们将学习FMEA(故障模式与影响分析)教程。
FMEA是一种系统性的方法,用于识别产品或过程中可能出现的潜在故障模式及其影响,并采取措施提前消除或减轻这些故障的影响。
本节课我们将详细讲解FMEA的步骤、方法和应用。
重点和难点解析:1. 重点:FMEA的步骤、方法和应用;2. 难点:如何运用FMEA分析产品或过程中的潜在故障,并提出改进措施。
FMEA操作方法

初始 FMEA
修正 FMEA1
修正 FMEA2 各项未考虑的失效 模式的发现、评审 和更新
时间
DFMEA必须在计划 各项未考虑的失效 的生产设计发布前 模式的发现、评审 PFMEA必须在计划 和更新 的试生产日期前
30
5、 FMEA的 應 用 范圍(1)
1、 設 計階段 的 FMEA (DFMEA---Design FMEA):
* 哪一种失效會發生? Failure mode * 發生后會造成什么影響? Effect * 其影響的嚴重性有多大? Severity * 是哪一种原因導致失效? Cause * 失效發生概率? Occurrence
* 當前工序控制方法?
* 檢測失效的能力? * 風險优先指數? * 改善方案?
Current Process Control Plan
如 新 工 序 的 設計,我 們 可 以 預先進行DFMEA,盡 可 能周 全 地考慮 產 品 規 格,工 序 操 作 水 平 、 工 序 能力 等 諸多 因 素,使 工 序 符 合 規定 的 要求
Not Trained 未培訓
Operator Error 操作員 錯誤
No Function 沒有 功能
Operator Tired 操作人員 疲勞
Board Error 電路板 錯誤
Crossed Wire 交叉的 電線
14
失效的定义
产品在工作 范围內, 导 致零组件的 破裂、断裂、 卡死、損坏 現象 在規定条件 下, (环境、 操作、时间) 不能完成既 定功能。
9
FMEA
Failure Mode (cause) Effect Analysis 在有限resource的狀況下, 從失效最多的狀況開始著手, 此即Failure Mode
FMEA教程
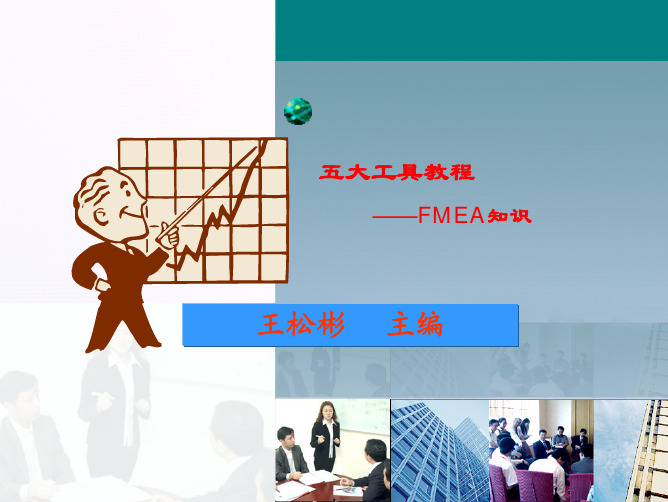
wsb
6
FMEA概述
•虽然FMEA的编制责任通常都指派到某个 人,但是FMEA的输入应是小组的努力。 小组应由知识丰富的人员组成(如设计 、分析/试验、制造、装配、服务、回收 、质量及可靠性等方面有丰富经验的工 程师)。FMEA由责任单位的工程师开始 启动,责任单位可能是原设备制造厂( OEM,即生产最终产品)、供方或分承包 方。
wsb
24
设计潜在失效模式
•典型的失效模式可包括,但不限于:
•裂纹、变形
•松动、泄漏
•粘结、氧化
•断裂、不传输扭矩
•打滑(不能承受全部扭矩)、无支撑(结
构的)
•支撑不足(结构的)、刚性啮合
•脱离太快、信号不足
•信号间断、无信号
•漂移
wsb
25
设计潜在失效模式
•注:潜在失效模式应以规范化或技术术语来 描述,不必与顾客察觉的现象相同
FMEA编号 1234 ①
X子系统
(设计FMEA)
共 1 页,第 1 页
部件 01.03/车密封 ② 设计责任 车身工程部队
③ 编制人 泰特-X6412-车身工程师 ④
车型年/车辆类型 199X/狮牌 4门/旅行车 ⑤ 关键日期 9X年03 01
⑹ FMEA日期(编制)8X 03 22修订 8X
07 14⑦
wsb
7
FMEA 之沿革
Chrysler, Ford GM, ASQ, AIAG
1993出版FMEA手冊 1995出版FMEA手冊 2001出版FMEA手冊
Grumman Aircraft Company
1950 FMEA飛機主 操縱系統失效分析
Boeing & Martin Marietta Aerospace Company
fmea手册策划步骤
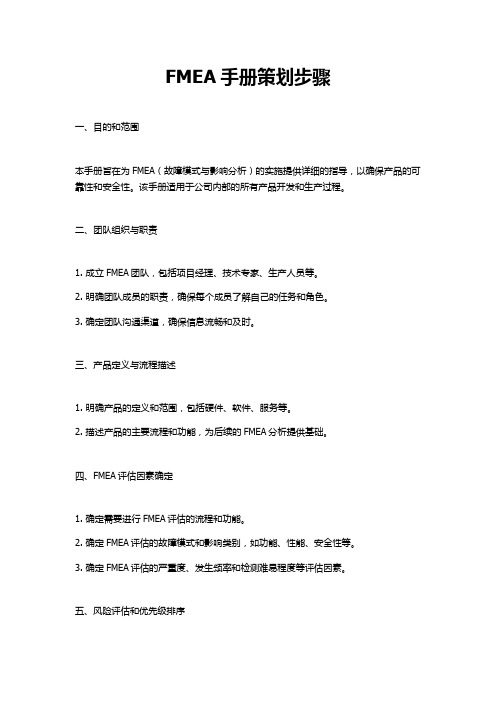
FMEA手册策划步骤一、目的和范围本手册旨在为FMEA(故障模式与影响分析)的实施提供详细的指导,以确保产品的可靠性和安全性。
该手册适用于公司内部的所有产品开发和生产过程。
二、团队组织与职责1. 成立FMEA团队,包括项目经理、技术专家、生产人员等。
2. 明确团队成员的职责,确保每个成员了解自己的任务和角色。
3. 确定团队沟通渠道,确保信息流畅和及时。
三、产品定义与流程描述1. 明确产品的定义和范围,包括硬件、软件、服务等。
2. 描述产品的主要流程和功能,为后续的FMEA分析提供基础。
四、FMEA评估因素确定1. 确定需要进行FMEA评估的流程和功能。
2. 确定FMEA评估的故障模式和影响类别,如功能、性能、安全性等。
3. 确定FMEA评估的严重度、发生频率和检测难易程度等评估因素。
五、风险评估和优先级排序1. 根据确定的评估因素,对每个故障模式进行风险评估。
2. 根据风险评估结果,对故障模式进行优先级排序。
3. 制定相应的纠正措施和预防措施,降低风险并提高产品的可靠性和安全性。
六、纠正措施和预防措施1. 制定针对高优先级故障模式的纠正措施,确保问题得到有效解决。
2. 制定预防措施,防止类似故障模式的再次发生。
3. 对纠正措施和预防措施进行跟踪和验证,确保其有效性和可行性。
七、FMEA持续改进1. 对FMEA过程进行定期审查和更新,以确保其与当前的产品和流程保持一致。
2. 不断收集和更新故障数据,以优化FMEA评估结果和优先级排序。
3. 鼓励团队成员提出改进意见和建议,以不断完善FMEA过程。
八、评审与批准1. 对完成的FMEA手册进行内部评审,确保其完整性和准确性。
2. 将评审结果提交给相关部门或领导进行审批。
3. 根据评审和审批意见,对FMEA手册进行必要的修改和完善。
九、报告编制与发布1. 根据评审和审批通过的FMEA手册,编制相应的报告。
2. 将报告发布给相关部门和团队成员,确保其了解和遵循FMEA手册的要求。
FMEA培训课件(五大工具)
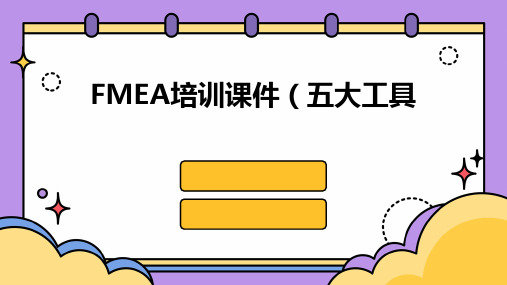
FMEDA不仅关注故障模式的影响,还特别强调对检测性的评估,以便更全面地了解潜在问题的影响以及在出现故障时能否及时发现并进行修复。
在FMEDA中,检测性的评估通常采用量化的方式进行,以便更准确地确定故障模式的可检测性。通过提高检测性,可以降低因未及时发现故障而导致的事故风险。
详细描述
在FMESi中,严重度评估通常采用量化的方式进行,以便更准确地确定故障模式对系统性能的影响程度。
总结词:故障模式、影响与风险优先数分析(FMERP)是一种综合性的质量工具,旨在识别、评估和解决潜在的故障模式及其对系统性能的影响。
总结词
故障模式、影响与检测性分析(FMEDA)是一种质量工具,用于评估潜在的故障模式及其对系统性能的影响以及检测的可能性。
详细描述
DFSS(Design for Six Sigma)是一种设计方法论,旨在提高产品的设计质量和可靠性。通过结合FMEA,可以对产品设计中的潜在失效模式进行分析和预防,从而提高产品的设计质量和可靠性。这种结合有助于在设计阶段就考虑产品的性能、可靠性和安全性,从而减少后期的改进成本和时间。
THANKS
总结词
电子产品行业对质量和可靠性要求极高,FMEA在此领域的应用同样广泛且重要。
在电子产品案例中,FMEA被用于分析电子产品的设计和生产过程。通过FMEA分析,可以发现潜在的故障模式,并采取相应的预防措施,提高产品的可靠性和稳定性。此外,FMEA还可以帮助企业优化产品设计,降低生产成本,提高市场竞争力。
FMEA培训课件(五大工具
FMEA基础介绍FMEA实施流程FMEA分析方法FMEA应用案例FMEA与其他工具的结合应用
FMEA 步骤图
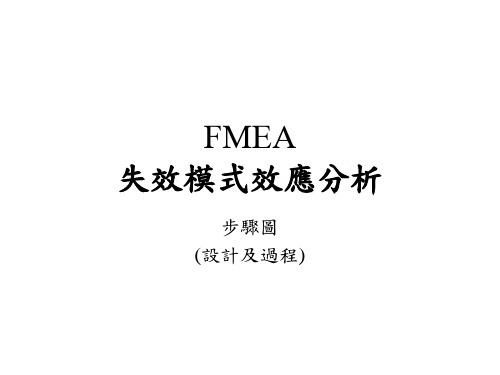
嚴重度Severity
頻度的評份準則
頻度是指具體的失效起因/機理發生的頻率。
頻度Occurrence
步驟 5 確定原因
潛在失效的原因
所謂潛在失效的原因是指一個設計薄弱部 分的跡象,其作用結果就是失效模式。 常用查明失效起因的方法:
– 腦激盪(Brainstorming) – 魚骨圖(Fishbone Diagram) – 實驗設計(Design EA
等與原先產品設定機能的目標不符的情形。這些 狀況的產生會造成顧客對製造者與銷售者的不滿, 可能產生的情形有大有小、也因使用時間有長有 短而發生,對於設計、生產乃至檢驗者而言,都 需要對自己負責的部份將隱藏的失效因素排除。 所以失效是客戶抱怨的主要來源,必頇依照一定 的步驟予以分析解構,將這樣具模組化的作業方 式整合成一種模式,稱之為失效模式分析 (FMEA)。
步驟 6 現行的探測方法/過程控制
現有的措施
列出預防措施,設計確認/驗証或其他活動, 這些活動將保証該設計對於考慮的失效模 式和/或原因來說是恰當的。可從以不三種 控制方法考慮:
1. 防止或減小失效模式出現 2. 查出原因并找到糾正措施 3. 查明失效模式
不易探測度評份準則
不易探測度是指在零部件離開制造工序或 裝配工序之前,於現行的探測方法/過程控 制方法找出失效原因/過程缺陷的可能性的 評份指標。
Power adaptor
Buzzer and earpiece jet for stereo
Earpiece and Off-hook button
Removable earpiece for stereo
Functional block diagram Bluetooth stereo clip headset
(品管工具FMEA)FMEA工作指南
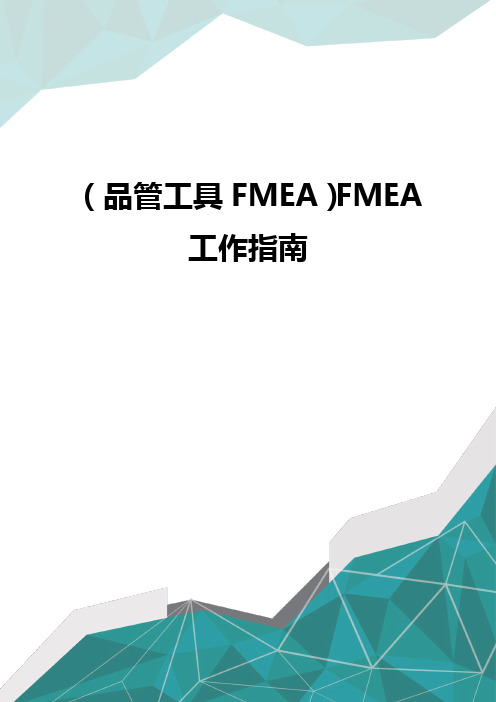
(品管工具FMEA)FMEA工作指南编制:张国英审核:杨林、王学明批准:王凤波4.3.2DFMEA功能框图多方论证小组应制定DFMEA框图,框图说明应包括各项目之间的主要关系,并建立DFMEA分析的逻辑顺序。
4.3.3多方论证小组结合功能框图并根据所设计产品的性能、装配情况以及设计参数的选择等进行DFMEA分析。
4.4设计工程师根据分析结果填写《潜在失效模式及后果分析-DFMEA》表格。
4.4.1填写表头●总成、分总成、零部件:填入所分析的总成、分总成、零部件的名称及编号。
●FMEA编号:填入DFMEA的文件编号。
文件编号组成:DFMEA-总成编号-年份-序号。
●设计责任:填入设计责任部门或小组。
●匹配车辆:填入与之相配套的车型及名称(在已知的前提下)。
●编制者:填入负责设计的工程师或工程师小组成员名单。
●关键日期:填入初次FMEA预定完成的日期,该日期不应超过设计图样完成日期。
●DFMEA日期:填入FMEA初稿的日期及最新修订的日期。
●主要参加人:填入DFMEA多方论证小组成员名单。
4.4.2项目/功能:填入将被分析的项目的名称和其他适当的信息。
用简洁文字说明被分析项目要满足设计意图的功能,包括该系统运行环境及相关的信息,如果项目有多种功能,且有不同的失效模式,应把所有功能都单独列出。
4.4.3潜在失效模式指部件、子系统或系统有可能会未达到或不能实现项目/功能栏中所描述的预期功能的情况。
对于特定的项目及其功能,应列出每一个潜在的失效模式,并使用规范化、专业化的术语来描述。
典型失效模式有两大类型:Ⅰ类失效指的是不能完成规定的功能,典型模式有(但不限于):●对上一级系统完成功能的影响;●对系统内其他零件的影响;●对顾客满意的影响;●对安全和法规符合性的影响;●对整车系统的影响。
典型的失效后果可能是但不限于以下情况:噪音、粗糙、工作不正常、不良外观、工作不稳定、间歇性工作、运行发热、失去功能、异味、泄露、不符合法规。
FMEA操作方法范新

5.1.3.4进行风险分析
按失效影响的严重程度(严重度S)、发生的频繁程度(频度 O)、发现的难易程度(发现难度D)估计风险顺序数。
3.2 DFMEA—设计潜在失效模式及后果分析,用来在生产交付前,重点分析由设 计缺陷引起的产品潜在失效模式。
3.3 PFMEA—过程潜在失效模式及后果分析,用来分析制造与装配过程,重点分 析由制造或装配过程缺陷引起的潜在失效。
4.职责
4.1技术中心产品设计部负责组织成立 DFMEA(设计 FMEA)小组,负责DFMEA活动的管理。
5.1.1.2 在出现下列情况时,DFMEA小组应在产品零件图纸设计之前进行 DFMEA活动:
a开发新产品/产品更改;
b产品应用的环境发生变化;
c材料或零部件发生变化。
5.1.2 DFMEA 实施前的准备工作
5.1.2.1技术中心产品设计部牵头成立 DFMEA(设计 FMEA)小组,产品工程部、质量部、生产部、
在产品有了改进或产品使用环境发生变化时,应根据需要适时修订以上标准。
5.1.3 DFMEA 部编写产品标准,确定产品的要求,包括产品的功能、用途、性能、使用条件等。
5.1.3.2划分功能块
DFMEA小组按产品的功能,将产品逐级分解,直到最基本的零件、构件。
一般根据分析目的,可仅将产品分解到某一水平。根据分解结果绘制出产品功能逻辑框图(参见正文 3.2.5 章节)。
业务总部、制造技术部、生技部、采购部等部门指定人员参加 DFMEA小组,必要时,由质量部邀请供应商、客户参加。
FMEA步骤

FMEA步骤1,FMEA 步骤(1)明确系统本身的情况(2)确定分析程度和水平(对关键的子系统可以分析得深一些,不重要的分析得浅一些,甚至可以不进行分析。
)(3)绘制系统图和可靠性框图(4)列出所有故障类型,并选出对系统有影响的故障类型(5)列出造成故障的原因(6)分析事故后果(7)等级划分(8)研究故障检测方法(6)提出预防措施(10)整理出FMEA表格FMEA的目的是辨识单一设备和系统的故障模式及每种故障模式对系统或装置造成的影响元件、子系统、系统在运行时,达不到设计规定的要求,不能完成任务的情况称为故障。
根据故障类型对系统或子系统影响程度的不同而划分的等级称为故障等级2,预先危险性分析在每项生产活动之前,特别是在设计开始阶段,预先对系统中存在的危险类别、危险产生条件、事故后果等概略地进行的分析称为预先危险分析。
预先危险分析步骤(6步)(1)通过经验判断、技术诊断或其他方法调查确定危险源(2)根据过去的经验教训及同类行业生产中发生的事故(或灾害)情况(3)对确定的危险源分类,制成预先危险性分析表;(4)转化条件分析(5)进行危险性分级(6)制定事故(或灾害)的预防性对策措施。
PHA表格中应有以下内容:①评价系统的基本目的、工艺过程、控制条件及环境因素②划分子系统(单元)的名称;③查明分析单元可能出现的危害;④确定危害的起因;⑤提出消除或控制危险的对策。
预先危险性分析适应条件:预先危险分析应该在系统或设备研制的初期进行,随着设计研制工作的进展,这种分析应不断进行,分析结果用于改进设计和制造。
对于现役的系统或设备也可采用预先危险分析,考察其安全性。
预先危险分析的主要优点有:1)最初产品设计或系统开发时,可以利用预先危险分析的结果,提出应遵循的注意事项和对策措施,使得设计更安全可靠2)由于在产品设计时,即可指出存在的主要危险,从一开始便可采取措施,排除、除低和控制危险,大大降低因产品造成危险的可能性和严重程度3)可用来制定设计管理方法和制定设计技术责任,以保证提高设计和加工的可靠性。
PLATO软件操作手册-FMEA模块

PLATO软件操作手册-FMEA模块目录一、FMEA模块简介 (1)1.1 打开程序 (1)1.2 FMEA工作界面 (1)二、完成FMEA表格过程 (3)2.1 风险分析 (3)2.2 优化改进(Optimization) (5)三、打印文档 (7)3.1 快速打印(Fast print) (7)3.2 转换为Excel文档(Excel-Transfer) (9)一、FMEA模块简介前两个模块工作完成以后,下一步工作就进入到FMEA 模块。
此模块主要工作是对失效进行风险评估,并进行优化改进。
1.1 打开程序从开始菜单中找到SCIO-FMEA 程序( )并打开,会出现以下登录界面:输入用户名与密码,点击OK 即可登入到程序中。
(注:默认用户名与密码皆为plato)各菜单栏及结构树、功能树与Matrix 模块类似,此章节不再一一详述。
1.2 FMEA 工作界面进入FMEA 模块后,打开某一系统元素,工作界面如下图所示:图中功能失效描述及分析部分已经在前两个模块中完成,在FMEA 表格中会自动导入。
FMEA 模块中需要进行风险分析以及优化改进两部分工作。
FMEA 表格有不同的显示格式,在主菜单进行如下选择:出现如下对话框,其中AIAG 3rd Edition 格式更易于理解,一般选择此格式下工作,若需VDA 评审,则工作完成后将格式转换为VDA 即可。
二、完成FMEA 表格过程2.1 风险分析在FMEA 模块中打开“屏幕组件”元素,如下图所示,红色部分即为风险分析部分,此部分内容包括:现有预防措施(P-action)和检测措施(D-action),S,O,D 评分,RPN 值。
此表格中首先需要填写P-action 和D-action 两栏,因O 和D 是分别与此两项相关的。
此后分别对O,S,D 评分,RPN 值会根据O,S,D 自动算出。
注:若要删除某项措施,选择该措施,点击键盘Delete,若要彻底从数据库中删除,再次按下F9 即可。
失败模式效果分析(FMEA)标准操作规程
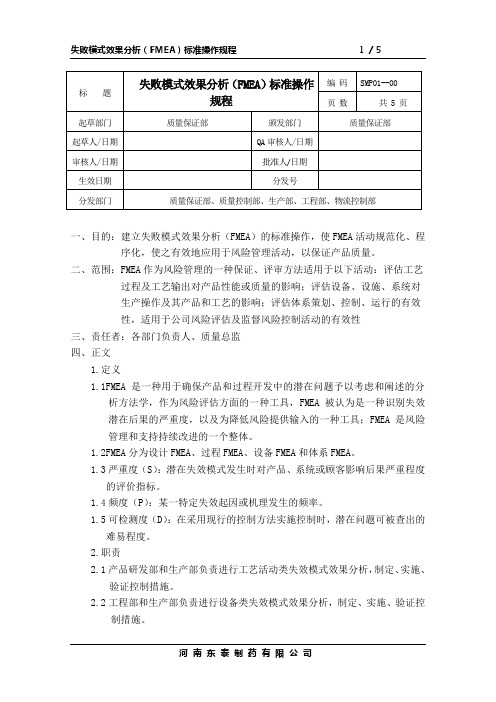
一、目的:建立失败模式效果分析(FMEA)的标准操作,使FMEA活动规范化、程序化,使之有效地应用于风险管理活动,以保证产品质量。
二、范围:FMEA作为风险管理的一种保证、评审方法适用于以下活动:评估工艺过程及工艺输出对产品性能或质量的影响;评估设备、设施、系统对生产操作及其产品和工艺的影响;评估体系策划、控制、运行的有效性,适用于公司风险评估及监督风险控制活动的有效性三、责任者:各部门负责人、质量总监四、正文1.定义1.1FMEA是一种用于确保产品和过程开发中的潜在问题予以考虑和阐述的分析方法学,作为风险评估方面的一种工具,FMEA被认为是一种识别失效潜在后果的严重度,以及为降低风险提供输入的一种工具;FMEA是风险管理和支持持续改进的一个整体。
1.2FMEA分为设计FMEA、过程FMEA、设备FMEA和体系FMEA。
1.3严重度(S):潜在失效模式发生时对产品、系统或顾客影响后果严重程度的评价指标。
1.4频度(P):某一特定失效起因或机理发生的频率。
1.5可检测度(D):在采用现行的控制方法实施控制时,潜在问题可被查出的难易程度。
2.职责2.1产品研发部和生产部负责进行工艺活动类失效模式效果分析,制定、实施、验证控制措施。
2.2工程部和生产部负责进行设备类失效模式效果分析,制定、实施、验证控制措施。
2.3质量保证部负责监控FMEA活动的进行。
3.程序3.1 规划FMEA活动3.1.1确定分析对象及FMEA活动发起时机3.1.1.1在新产品的设计阶段,以产品的质量属性为分析对象发起设计FMEA活动。
3.1.1.2在工艺活动中,以工艺设计空间为分析对象发起过程FMEA活动。
3.1.1.3在新设备选型及设备变更时,以设备的原理、结构、部件、系统等为分析对象发起设备FMEA活动。
3.1.1.4在管理评审中,以体系为分析对象发起体系FMEA活动。
3.1.2建立FMEA小组,负责FMEA活动的组织与实施。
FMEA标准手册(完整资料).doc

FMEA
Potential Failure Mode and Effect Analysis
潜在失效模式与后果分析
概 要
概 述
本手册介绍了潜在失效模式及后果分析(FMEA)的概念,给出了运用FMEA技术的通用指南。FMEA可以描述为一组系统化的活动,其目的是:
1)发现、评价产品/过程中潜在的失效及其后果;
时间性是成功实施FMEA的最重要因素之一,它是一个“事前行为”,而不是“事后练习”。为达到最佳效益,FMEA必须在设计或过程失效模式被无意地纳人设计产品之前进行。事先花时间很好地进行综合的FMEA分析,能够容易、低成本地对产品或过程进行修改,从而减轻事后修改的危机。FMEA能够减少或消除因修改而带采更大损失的机会。适当地加以应用,FMEA是一个相互作用的过程,永无止境。
设计FMEA
简 介
设计FMEA主要是由“负责设计的工程师/小组”采用的一种分析技术,用来保证在可能的范围内已充分地考虑到并指明各种潜在的失效模式及其相关的起因/机理。应评估最终的产品以及每个与之相关的系统、子系统和零部件。FMEA以其最严密的形式总结了设计一个零部件、子系统或系统时,一个工程师和设计组的设计思想(包括根据以往的经验和教训对可能出现问题的项目的分析)。这种系统化的方法体现了一个工程师在任何设计过程中正常经历过程,并使之规范化、文件化。
·为推荐和跟踪降低风险的措施提供一个公开的讨论形式;
·为将来分析研究现场情况、评价设计的更改及开发更先进的设计提供参考。
顾客的定义
设计FMEA中“顾客”的定义,不仅仅是指“最终使用者”,还包括负责车型更高一级装配过程设计的工程师/小组,以及在生产过程中负责制造和售后服务的工程师。
FMEA的全面实施要求对所有新的部件、更改的部件以及应用或环境有变化的沿用零件进行设计FMEA。FMEA始于负责设计工作的工程师,但对有专有权的设计来说,可能始于其供方。
FMEA 分析指南
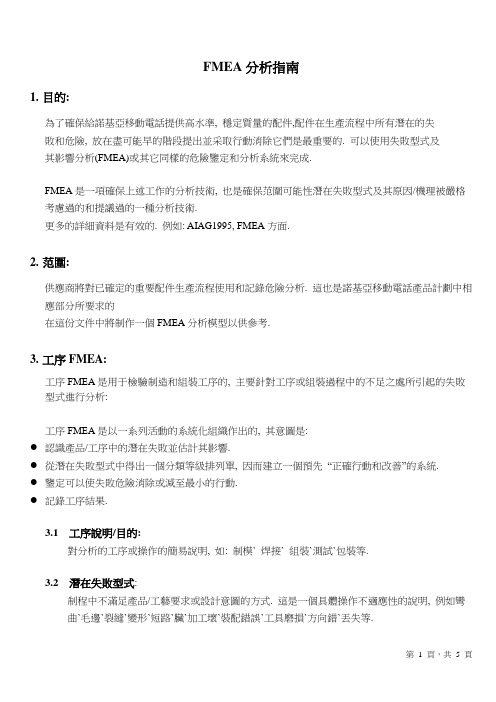
FMEA分析指南1.目的:為了確保給諾基亞移動電話提供高水準, 穩定質量的配件,配件在生產流程中所有潛在的失敗和危險, 放在盡可能早的階段提出並采取行動消除它們是最重要的. 可以使用失敗型式及其影響分析(FMEA)或其它同樣的危險鑒定和分析系統來完成.FMEA是一項確保上述工作的分析技術, 也是確保范圍可能性潛在失敗型式及其原因/機理被嚴格考慮過的和提議過的一種分析技術.更多的詳細資料是有效的. 例如: AIAG1995, FMEA方面.2.范圍:供應商將對已確定的重要配件生產流程使用和記錄危險分析. 這也是諾基亞移動電話產品計劃中相應部分所要求的在這份文件中將制作一個FMEA分析模型以供參考.3.工序FMEA:工序FMEA是用于檢驗制造和組裝工序的, 主要針對工序或組裝過程中的不足之處所引起的失敗型式進行分析:工序FMEA是以一系列活動的系統化組織作出的, 其意圖是:●認識產品/工序中的潛在失敗並估計其影響.●從潛在失敗型式中得出一個分類等級排列單, 因而建立一個預先“正確行動和改善”的系統.●鑒定可以使失敗危險消除或減至最小的行動.●記錄工序結果.3.1 工序說明/目的:對分析的工序或操作的簡易說明, 如: 制模` 焊接` 組裝`測試`包裝等.3.2 潛在失敗型式:制程中不滿足產品/工藝要求或設計意圖的方式. 這是一個具體操作不適應性的說明, 例如彎曲`毛邊`裂縫`變形`短路`臟`加工壞`裝配錯誤`工具磨損`方向錯`丟失等.3.3潛在失敗影響:失敗型式對顧客的影響, 從顧客可能留意或經歷的觀點來看失敗影響的說明, 如: 噪音` 失效` 性能差` 粗糙` 不穩定` 不適合(不能裝配)等.3.4潛在失敗原因:失敗可能發生的方式的說明, 從能被校正或控制的觀點來看. 只有特定誤差或誤動作才得以列出, 如:(1)不正確的熱處理; (2)制品丟失或放錯位置; (3)不正確的轉矩; (4)不妥當的管理步驟; (5)錯用; (6)人為誤差; (7)不正確的操作指引; 等.3.5現行工序之管理就目前的或計劃的管理內容. 在可能范圍內要麼預防失敗型式的發生, 要麼讓其發生, 鑒別它.焦點一定要在產品沒有發送給客戶之前用于鑒別失敗的方法之效果上.管理方法可能涉及: (1) 穩定性測試(可靠性檢驗) (例如:工序能力分析); (2) 統計工序管理(SPC); (3) 后續工序3.6 危險分析:1) 嚴重(S評估;ev.): 評估潛在失敗型式對客戶的影響;2)存在(Occ.): 設想壞品原因/機理會發生的頻率(出現率);3)檢測:(Det.) 制品離開制造或組裝場所之前, 失敗被制定的工序管理查出的可能性(概率).每一要素按照下面的指引分類標示1……10.危險優先系數(RPN):RPN = ( Sev.) x (Occ.) x (Det.)≦1000.在RPN高的情況下, 供應商必須采取正確行動減小被預測出來的危險, 一般來說, 要特別注意高度嚴重, 與總RPN結果無關.工序失敗型式及其影響分析對嚴重(Severity(S))提出的評估標準類別失敗可能性1輕微: 希望失敗的輕微特征對產品或服務產生真正的影響是不合理的. 顧客可能根本不注意這種失敗.2-3低: 低的“嚴重”, 分類是, 由于失敗只引起輕微的顧客煩惱. 客戶可能會注意產品或服務(質量)的輕微降低,下道工序的便利就會輕微降低或造成輕微的返工.4-6中: 中的分類是因為失敗引起不滿. 客戶會因失敗產生煩惱或不舒服. 可能引起不定時的維修或設備的損壞.7-8高: 因為失敗的特征引起顧客的強烈不滿. 例如某一產品不能使用或不方便使用, 不包含安全規定或政府規定, 可能引起后序工藝的損壞或設備的損壞(如爆炸` 破裂等) 9-10很高: 很高“嚴重”, 使用在失敗影響安全, 並涉及到不符合政府規定.如果評出來的數值, 落在某一類別的兩個數之間, 以較高的數值為準.如果大家對于評值有巽議, 可用以下方法尋求解決1. 如巽議保持在鄰近的某一類別的范圍內,就取其平均值, 例: 一個人認為是2, 但另外有人認為是6, 那評級應是4.2.如巽議跳過一個類別, 那就必須達成共識. 只能選擇某一個人的數值, 總體必須達成共識.沒有平均數, 沒有大多數, 組中每一人都有權利評估, 他們可能不會取得100%的一致, 但他們都要接受.對存在(Qccurrence(O))提出的評估標准類別失敗可能性可能失敗率Cpk dpm1.輕微: 失敗几乎看不出來,和正常的制程几乎沒有區別<1 in 1500 000 ≧1.67 0.672.很低: 查出的失敗和正常制程相差很小 1 in 1500 00 ≧1.5 6.673.低: 查出的失敗與正常制程很相似 1 in 15000 ≧1.33 66.674-6 中: 通常其制程類似于以前曾偶爾遭到失敗的制程 1 in 2 000 ≧1.17 5001 in 400 ≧1.00 25001 in 80 ≧0.83 125007-8 高: 涉及的工序類似于以前常失敗的制程 1 in 20 ≧0.67 500001 in 8 ≧0.51 1250009-10 很高: 失敗是几乎不可避免 1 in 3 ≧0.33 333333.3>1 in 2 < 0.33 500000 如果評出來的數值, 落在某一類別的兩個數之間, 以較高的數值為準.如果大家對于評值有巽議, 可用以下方法尋求解決1. 如巽議保持在鄰近的某一類別的范圍內出現, 就取其平均值, 例: 一個人認為是2, 但另外有人認為是6, 那評級應是4.2. 如巽議跳過一個類別, 那就必須達成共識.只能選擇某一個人的數值, 總體必須達成共識.沒有平均數, 沒有大多數, 組中每一人都有權利評估, 他們可能不會取得100%的一致, 但他們都要接受.對檢測(Detection(D) 提出的評估標準類別失敗可能性檢測可靠性1-2 很高:從管制上明顯可以檢測到疵點的存在≧99.99%3-5 高: 從管制上有很大機會可檢測到疵點的存在≧99.80%6-8 中: 從管制上有可能檢測到疵點的存在≧98.80%9 低: 從管制上很可能檢測不到缺點的存在≧90.00%10 很低: 在管制程序上很大可能檢測不到缺點的存在≦90.00%如果評出來的數值, 落在某一類別的兩個數之間, 以較高的數值為準.如果大家對于評值有巽議, 可用以下方法尋求解決1.如巽議保持在鄰近的某一類別的范圍內, 就取其平均值, 例: 一個人認為是2, 但另外有人認為是6, 那評級應是4.2.如巽議跳過一個類別, 那就必須達成共識.只能選擇某一個人的數值, 總體必須達成共識,沒有平均數, 沒有大多數, 組中每一人都有權利評估, 他們可能不會取得100%的一致, 但他們都要接受.出版說明Failure Mode and Effect Analysis (FMEA)本書中譯為“失敗型式及其影響分析”,它是對工序中潛在失敗或危險及其所帶來的不良影響進行的分析, (即從工程可靠性反面所進行的分析). 若能經常認真做FMEA, 必將給我們的製造工程帶來潛在的益處.FMEA考察的對象是製造工程. 其目的在於調查製造工藝.譯者: 司如雪Dec.13,1999於朝日集團FMEA分析指南。
(品管工具FMEA)-FMEA应用指导书
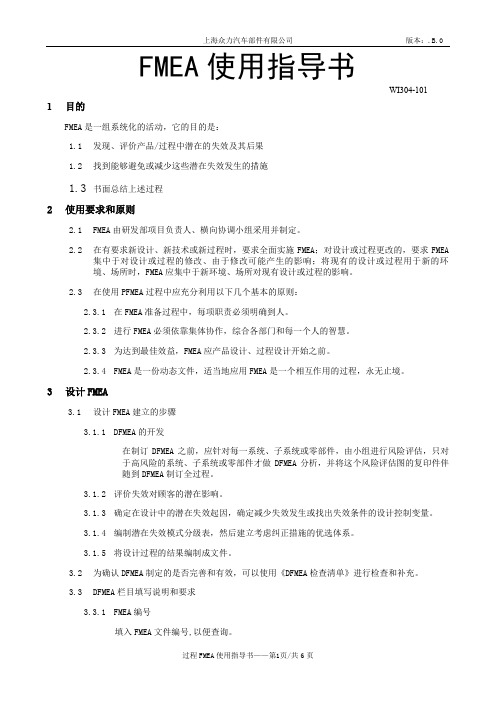
FMEA使用指导书WI304-1011目的FMEA是一组系统化的活动,它的目的是:1.1发现、评价产品/过程中潜在的失效及其后果1.2找到能够避免或减少这些潜在失效发生的措施1.3书面总结上述过程2使用要求和原则2.1FMEA由研发部项目负责人、横向协调小组采用并制定。
2.2在有要求新设计、新技术或新过程时,要求全面实施FMEA;对设计或过程更改的,要求FMEA集中于对设计或过程的修改、由于修改可能产生的影响;将现有的设计或过程用于新的环境、场所时,FMEA应集中于新环境、场所对现有设计或过程的影响。
2.3在使用PFMEA过程中应充分利用以下几个基本的原则:2.3.1在FMEA准备过程中,每项职责必须明确到人。
2.3.2进行FMEA必须依靠集体协作,综合各部门和每一个人的智慧。
2.3.3为达到最佳效益,FMEA应产品设计、过程设计开始之前。
2.3.4FMEA是一份动态文件,适当地应用FMEA是一个相互作用的过程,永无止境。
3设计FMEA3.1设计FMEA建立的步骤3.1.1DFMEA的开发在制订DFMEA之前,应针对每一系统、子系统或零部件,由小组进行风险评估,只对于高风险的系统、子系统或零部件才做DFMEA分析,并将这个风险评估图的复印件伴随到DFMEA制订全过程。
3.1.2评价失效对顾客的潜在影响。
3.1.3确定在设计中的潜在失效起因,确定减少失效发生或找出失效条件的设计控制变量。
3.1.4编制潜在失效模式分级表,然后建立考虑纠正措施的优选体系。
3.1.5将设计过程的结果编制成文件。
3.2为确认DFMEA制定的是否完善和有效,可以使用《DFMEA检查清单》进行检查和补充。
3.3DFMEA栏目填写说明和要求3.3.1FMEA编号填入FMEA文件编号,以便查询。
3.3.2项目名称填入所分析的系统、子系统或零件的名称、编号。
3.3.3设计责任部门填入整车厂、部门和横向协调小组。
如果知道,还应包括供方的名称。
【技术分享】如何使用FMEA解决问题?
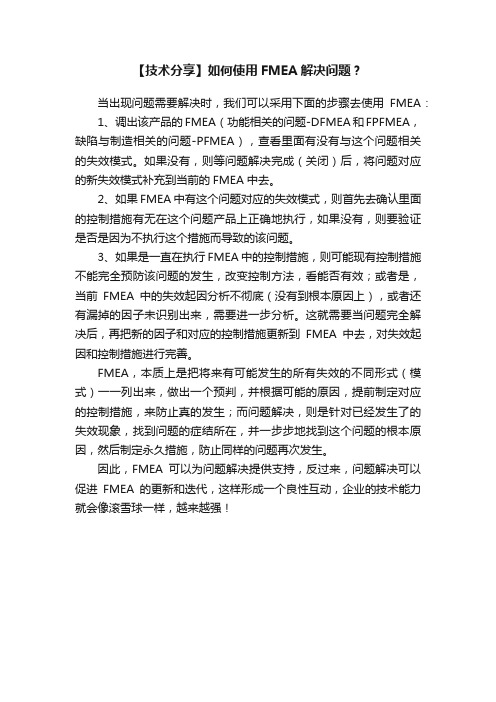
【技术分享】如何使用FMEA解决问题?
当出现问题需要解决时,我们可以采用下面的步骤去使用FMEA:
1、调出该产品的FMEA(功能相关的问题-DFMEA和FPFMEA,缺陷与制造相关的问题-PFMEA),查看里面有没有与这个问题相关的失效模式。
如果没有,则等问题解决完成(关闭)后,将问题对应的新失效模式补充到当前的FMEA中去。
2、如果FMEA中有这个问题对应的失效模式,则首先去确认里面的控制措施有无在这个问题产品上正确地执行,如果没有,则要验证是否是因为不执行这个措施而导致的该问题。
3、如果是一直在执行FMEA中的控制措施,则可能现有控制措施不能完全预防该问题的发生,改变控制方法,看能否有效;或者是,当前FMEA中的失效起因分析不彻底(没有到根本原因上),或者还有漏掉的因子未识别出来,需要进一步分析。
这就需要当问题完全解决后,再把新的因子和对应的控制措施更新到FMEA中去,对失效起因和控制措施进行完善。
FMEA,本质上是把将来有可能发生的所有失效的不同形式(模式)一一列出来,做出一个预判,并根据可能的原因,提前制定对应的控制措施,来防止真的发生;而问题解决,则是针对已经发生了的失效现象,找到问题的症结所在,并一步步地找到这个问题的根本原因,然后制定永久措施,防止同样的问题再次发生。
因此,FMEA可以为问题解决提供支持,反过来,问题解决可以促进FMEA的更新和迭代,这样形成一个良性互动,企业的技术能力就会像滚雪球一样,越来越强!。
- 1、下载文档前请自行甄别文档内容的完整性,平台不提供额外的编辑、内容补充、找答案等附加服务。
- 2、"仅部分预览"的文档,不可在线预览部分如存在完整性等问题,可反馈申请退款(可完整预览的文档不适用该条件!)。
- 3、如文档侵犯您的权益,请联系客服反馈,我们会尽快为您处理(人工客服工作时间:9:00-18:30)。
目录
一、FMEA模块简介 (1)
1.1 打开程序 (1)
1.2 FMEA工作界面 (1)
二、完成FMEA表格过程 (3)
2.1 风险分析 (3)
2.2 优化改进(Optimization) (5)
三、打印文档 (7)
3.1 快速打印(Fast print) (7)
3.2 转换为Excel文档(Excel-Transfer) (9)
一、FMEA模块简介
前两个模块工作完成以后,下一步工作就进入到FMEA 模块。
此模块主要工作是对失效进行风险评估,并进行优化改进。
1.1 打开程序
从开始菜单中找到SCIO-FMEA 程序( )并打开,会出现以下登录界面:
输入用户名与密码,点击OK 即可登入到程序中。
(注:默认用户名与密码皆为plato)
各菜单栏及结构树、功能树与Matrix 模块类似,此章节不再一一详述。
1.2 FMEA 工作界面
进入FMEA 模块后,打开某一系统元素,工作界面如下图所示:
图中功能失效描述及分析部分已经在前两个模块中完成,在FMEA 表格中会自动导入。
FMEA 模块中需要进行风险分析以及优化改进两部分工作。
FMEA 表格有不同的显示格式,在主菜单进行如下选择:
出现如下对话框,其中AIAG 3rd Edition 格式更易于理解,一般选择此格式下工作,若
需VDA 评审,则工作完成后将格式转换为VDA 即可。
二、完成FMEA 表格过程
2.1 风险分析
在FMEA 模块中打开“屏幕组件”元素,如下图所示,红色部分即为风险分析部分,此部分内容包括:现有预防措施(P-action)和检测措施(D-action),S,O,D 评分,RPN 值。
此表格中首先需要填写P-action 和D-action 两栏,因O 和D 是分别与此两项相关的。
此后分别对O,S,D 评分,RPN 值会根据O,S,D 自动算出。
注:若要删除某项措施,选择该措施,点击键盘Delete,若要彻底从数据库中删除,再次按下F9 即可。
失效严重度(S)有一个继承功能,即最顶层某失效的严重度为某一数值,则往下传递的该失效链上所有下级失效严重度都亦为此值。
如下图所示,,Iphone4s 层级失效“外观不满足要求”,它的影响严重度为6;它的下层
级屏幕组件该失效链上的失效“屏幕出现尖锐边角”若手动给赋予严重度5,则会在框中上方以红色底显示“”,表示该失效影响的严重度与上级严重度没有继承。
若要继承,按以下操作:
出现如下对话框中继续操作,
按此操作完以后,所有与“外观不满足要求”失效链上的失效影响严重度S 会自动赋予6,如下图所示:
2.2 优化改进(Optimization)
当第一个RPN 评估完成以后,当前状态的失效分析就得以确认。
下一步工作需要对高风险失效进行优化。
此时诸如优化措施,截止日期,负责人等信息都需要输入,当优化措施采用后,会得到新的一个RPN 值。
如下图红色框选区域所示。
若优化措施不止一个,此时可以生成一个措施包。
同样Ctrl + Enter 操作另起一行输入新的
优化措施。
如下图所示,共两个优化措施形成一个措施包,对这个措施包会有一个新的负责人和截止日期,如下图所示。
可以有两个不同的措施包,这样可以对两个措施包进行比较,采取效果好的措施包而驳回效果较差的。
操作方法如下:在上图的优化措施上点击鼠标右键,选择“add action package”,
在新的表格中输入新的措施包。
比较两个措施包,1 的效果好于2,故将2 措施驳回。
注:最后一列有一状态栏(status),此栏中各数字表示各措施的完成情况,closed 表示措施完成采取,rejected 表示该措施被驳回。
三、打印文档
FMEA 表格完成以后,若需将表格打印,有两种方法:一是快速打印,二是转换为Excel 文档。
3.1 快速打印(Fast print)
使用快速打印功能可以直接打印当前打开的工作表格。
在主菜单按下图所示选择:
在弹出对话框中勾选“system element name”,OK 确认。
然后在主菜单中按下图所示选择“printable”
如此设置完成后点击主菜单System Element/FastPrint…/Printer Setup…,打印页面设
置完后,即可直接打印。
3.2 转换为Excel 文档(Excel-Transfer)
点击主菜单“”图标,进入转换设置对话框,如下图所示:
对话框中Groups/components 标签栏下,选择需要转换打印的内容,勾选即可,对话框
左侧会显示当前勾选的内容。
对话框中Data configuration 标签栏下,下图画圈处需注意选择:选择0,则表示只转换
打印当前选择层级,对其子级元素并不转换打印;选择1,则表示转换包含本级及它的下一层子级共两个层级的数据;选择-1,则表示选择本级以及它所包含的所有子级的数据。
在转换前也可以调整转换文档的格式,操作如下图所示,若当前FMEA 表格是AIAG 3rd 格
式,若要转换为VDA 格式,进行选择即可。
所有设置完成以后,点击start 即可转换为Excel 文档。
10。