40万吨汽油加氢装置开工及运行总结
加氢装置开车工作总结
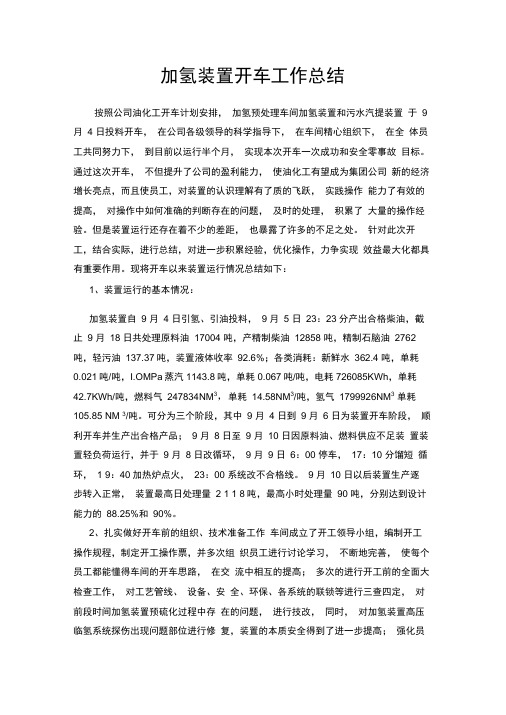
加氢装置开车工作总结按照公司油化工开车计划安排,加氢预处理车间加氢装置和污水汽提装置于9 月 4 日投料开车,在公司各级领导的科学指导下,在车间精心组织下,在全体员工共同努力下,到目前以运行半个月,实现本次开车一次成功和安全零事故目标。
通过这次开车,不但提升了公司的盈利能力,使油化工有望成为集团公司新的经济增长亮点,而且使员工,对装置的认识理解有了质的飞跃,实践操作能力了有效的提高,对操作中如何准确的判断存在的问题,及时的处理,积累了大量的操作经验。
但是装置运行还存在着不少的差距,也暴露了许多的不足之处。
针对此次开工,结合实际,进行总结,对进一步积累经验,优化操作,力争实现效益最大化都具有重要作用。
现将开车以来装置运行情况总结如下:1、装置运行的基本情况:加氢装置自9 月 4 日引氢、引油投料,9 月 5 日23:23分产出合格柴油,截止9 月18 日共处理原料油17004 吨,产精制柴油12858 吨,精制石脑油2762 吨,轻污油137.37吨,装置液体收率92.6%;各类消耗:新鲜水362.4 吨,单耗0.021吨/吨,I.OMPa蒸汽1143.8吨,单耗0.067吨/吨,电耗726085KWh,单耗42.7KWh/吨,燃料气247834NM3,单耗14.58NM3/吨,氢气1799926NM3单耗105.85 NM 3/吨。
可分为三个阶段,其中9 月4 日到9 月6 日为装置开车阶段,顺利开车并生产出合格产品;9 月8 日至9 月10 日因原料油、燃料供应不足装置装置轻负荷运行,并于9 月8 日改循环,9 月9 日6:00 停车,17:10 分馏短循环, 1 9:40加热炉点火,23:00 系统改不合格线。
9 月10 日以后装置生产逐步转入正常,装置最高日处理量 2 1 1 8吨,最高小时处理量90 吨,分别达到设计能力的88.25%和90%。
2、扎实做好开车前的组织、技术准备工作车间成立了开工领导小组,编制开工操作规程,制定开工操作票,并多次组织员工进行讨论学习,不断地完善,使每个员工都能懂得车间的开车思路,在交流中相互的提高;多次的进行开工前的全面大检查工作,对工艺管线、设备、安全、环保、各系统的联锁等进行三查四定,对前段时间加氢装置预硫化过程中存在的问题,进行技改,同时,对加氢装置高压临氢系统探伤出现问题部位进行修复,装置的本质安全得到了进一步提高;强化员工的业务知识培训,熟练掌握开车方案,岗位操作法等基本操作技能,特别是针对年前加热炉的烘炉、催化剂的干燥及预硫化过程中积累的经验进行交流,实践操作存在的问题再次的进行学习,班组之间达成的共识,规范操作行为,以利于提高员工的操作技能,使员工能够规范、稳定、快速、高效的处理操作中的问题;强化安全教育提高员工安全意识与安全技能,每天早来迟走学习炼化安全知识,以班组为单位,进行多轮次事故预案的演练。
全氢型炼油厂渣油加氢装置长周期运行总结

全氢型炼油厂渣油加氢装置长周期运行总结全氢型炼油厂渣油加氢装置长周期运行总结近年来,随着能源需求的不断增长,炼油行业在全球范围内得到了快速发展。
全氢型炼油厂渣油加氢装置作为关键设备之一,承担着将高硫渣油转化为高品质产品的重要任务。
本文将对全氢型炼油厂渣油加氢装置长周期运行进行总结,希望能够为相关从业人员提供一定的参考和借鉴。
一、设备运行概况全氢型炼油厂渣油加氢装置是在高温高压条件下,通过加氢反应将渣油中的硫、氮等杂质去除,并发生脱氢、裂解等反应,得到更高品质的产品。
该装置主要由反应器、加热炉、换热器和分离器等组成。
装置在正常运行情况下,具有高效、环保、低能耗等特点。
二、运行中遇到的问题在长周期运行的过程中,全氢型炼油厂渣油加氢装置可能会遇到一些问题。
首先,随着运行时间的延长,反应器内壁会出现积碳和结焦问题,降低了反应效率。
其次,由于原料渣油中含有硫、氮等杂质,会引起催化剂的中毒和失活,进而影响反应的进行。
此外,还可能出现腐蚀、泄漏和设备老化等问题,需要及时进行维修和更换。
这些问题都对装置的正常运行产生一定的影响。
三、问题解决及运行优化针对以上问题,全氢型炼油厂渣油加氢装置可以采取一系列措施进行解决和优化。
首先,在反应器内部加入优质催化剂,通过周期更换催化剂,减少催化剂的中毒和失活现象。
其次,对于积碳和结焦问题,可以进行定期的反应器清洗和热解操作,保证反应器内部的清洁和正常运行。
此外,加强设备的维护保养工作,及时发现并修复设备的腐蚀和泄漏问题,提高设备的使用寿命。
四、运行优势及创新点全氢型炼油厂渣油加氢装置在长周期运行中不断优化,取得了较好的运行效果和经济效益。
首先,催化剂的周期更换和定期清洗操作,提高了反应器内的反应效率,减少了中毒和失活现象,有利于提高产品的质量和产量。
其次,设备的维护保养工作有效地减少了设备的故障和停机时间,提高了装置的运行稳定性和可靠性。
此外,全氢型炼油厂渣油加氢装置在运行过程中也不断创新,引入先进技术和设备,提高了加氢反应的效率和产量,降低了能耗和物料消耗量。
40万吨年汽油加氢装置机泵运行及缺陷记录
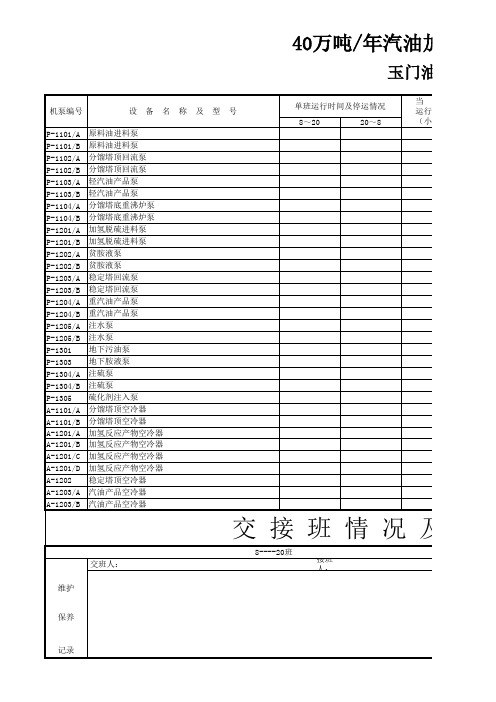
40万吨/年汽油加氢
玉门油田
说明:1.设备停运情况记录:①正常停运记录“△”;②事故停运记录“×”;③维修停运“-”;
2.巡回检查记录内容:①设备的动密封及管道静密封泄露情况;②主付机轴承温度及润滑点或液面,冷却水压力是否
3.维护保养记录内容:①各机泵每次加油量及加油时间;②设备以及周围环境清洁部位、区域;③“十字作业”项其
4.设备缺陷记录内容: ①交班应说明每台设备的运行或停运状况;②本班所出现、处理或交班处理的事件;③提请下
油加氢装置机泵运行及缺陷记录
门油田公司炼油化工总厂
及 设 备 保 养 缺 陷 记 录
润滑点或液面,冷却水压力是否符合规定;③主付机运行是否正常;④其它。
位、区域;③“十字作业”项其他内容;④设备维护修理情况
理或交班处理的事件;③提请下班注意的事件;④其它。
装置开工工作总结

装置开工工作总结
在过去的一段时间里,我们团队一直在为新的装置开工工作而努力。
经过不懈
的努力和团队的协作,我们终于完成了这项任务。
在这个过程中,我们遇到了许多挑战,但也取得了许多成功。
现在,我想对我们的工作进行总结,以便我们能够更好地总结经验教训,为未来的工作做好准备。
首先,我们在规划阶段就遇到了很多问题。
我们需要考虑到装置的设计、材料
的采购、人员的安排等多个方面。
在这个阶段,我们遇到了很多困难,但通过团队的合作和沟通,我们最终找到了解决问题的方法。
我们学会了更加有效地分工合作,使得每个人都能够充分发挥自己的优势,从而提高了工作效率。
其次,在实施阶段,我们也遇到了很多挑战。
装置的制作需要精准的技术和耐
心的工作,而且还需要考虑到安全和环保等方面。
在这个阶段,我们不断进行试验和改进,最终成功地完成了装置的制作。
我们学会了在面对问题时不要轻易放弃,要不断尝试和改进,直到找到解决问题的方法。
最后,在验收阶段,我们也经历了一些波折。
由于装置的特殊性,我们需要进
行多次的测试和调整,以确保其能够正常运行。
在这个阶段,我们需要保持耐心和细心,不断进行检查和改进。
最终,我们成功地通过了验收,得到了领导和客户的认可。
总的来说,这次装置开工工作虽然充满了挑战,但我们团队最终取得了成功。
通过这次工作,我们学会了更加有效地合作,更加耐心地面对问题,更加细心地进行工作。
我相信,这些经验和教训将会对我们未来的工作产生积极的影响。
希望我们能够在未来的工作中继续保持团队精神和努力工作,为公司的发展做出更大的贡献。
40万吨汽油加氢装置监理报告
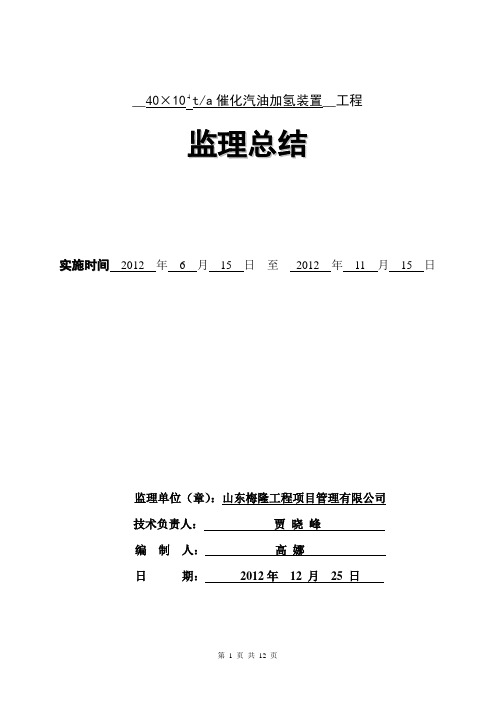
_40×104t/a催化汽油加氢装置_工程监理总结实施时间2012年6月15日至2012年11月15日监理单位(章):山东梅隆工程项目管理有限公司技术负责人:贾晓峰编制人:高娜日期:2012年12 月25 日目录第一章概述 (3)第一节工程概况 (3)第二节监理机构及监理业务范围 (3)第二章工期、质量、安全的控制措施和效果 (5)第一节工期控制措施及效果 (5)第二节质量控制措施及效果 (5)第三章信息管理 (10)第四章结束语 (12)第一章概述第一节工程概况一、建设项目1.项目名称:40×104t/a催化汽油加氢装置2.项目建筑地点:山东菏泽市开发区长江东路4666号3.建设单位:山东玉皇盛世化工有限公司4.施工单位:山东圣世安装有限公司5.监理单位:山东梅隆工程项目管理有限公司6.设计单位:海工英派尔工程有限公司7.工程质量等级目标:合格工程8.计划工期:150 天第二节监理机构及监理业务范围1.监理机构组成:项目监理工程师均为从事多年设计工作的专业技术人员和具有多年基建项目管理经验管理者,从造价人才网事监理工作多年,省级、国家级监理证书。
2.监理业务范围:通过目标规划、动态控制、组织协调、信息管理、等方面的监理工作,确保实现40×104t/a催化汽油加氢装置项目的投资、进度、质量及安全方面的预期目标。
3.监理工作依据:(1)依据中华人民共和国建筑法、工程建设质量管理条理及建设工程监理规范和相关的法律、工程监理法规;(2)依据项目的设计图纸、文件等技术资料;(3)依据监理合同文件、施工合同文件、业主批准的监理规划及建设工程项目相关的文件。
4.监理实施情况:监理人员于施工准备阶段进入施工现场,对本工程项目监理工作进行了规划和准备工作,具体实施情况如下:(1)审查并审批了施工单位报送的公司资质、施工组织设计及相关的安全生产施工方案、特殊工种作业证等等。
(2)检查了施工单位质量、安全保证体系和质量、安全管理体系的建立情况,现场管理制度和责任制度的建立和落实情况;(3)检查了施工单位施工技术、施工机具、设备、物质、临时设施的准备情况;(4)参加了设计技术交底会议,并提出了建设性的意见和建议;(5)编制了施工监理规划及关键分部分项工程的监理细则;(6)组织监理人员认真熟悉图纸,找出施工质量控制的重点和难点,制定应对措施;(7)建立了施工现场会议制度,每周六下午四点设立监理例会,同时进行了监理工作交底。
年产40万吨汽油加氢装置建设融资投资立项项目可行性研究报告(中撰咨询)

年产40万吨汽油加氢装置建设立项投资融资项目可行性研究报告(典型案例〃仅供参考)广州中撰企业投资咨询有限公司地址:中国〃广州目录第一章年产40万吨汽油加氢装臵建设项目概论 (1)一、年产40万吨汽油加氢装臵建设项目名称及承办单位 (1)二、年产40万吨汽油加氢装臵建设项目可行性研究报告委托编制单位 (1)三、可行性研究的目的 (1)四、可行性研究报告编制依据原则和范围 (2)(一)项目可行性报告编制依据 (2)(二)可行性研究报告编制原则 (2)(三)可行性研究报告编制范围 (4)五、研究的主要过程 (5)六、年产40万吨汽油加氢装臵建设产品方案及建设规模 (6)七、年产40万吨汽油加氢装臵建设项目总投资估算 (6)八、工艺技术装备方案的选择 (6)九、项目实施进度建议 (6)十、研究结论 (7)十一、年产40万吨汽油加氢装臵建设项目主要经济技术指标 (9)项目主要经济技术指标一览表 (9)第二章年产40万吨汽油加氢装臵建设产品说明 (15)第三章年产40万吨汽油加氢装臵建设项目市场分析预测 (15)第四章项目选址科学性分析 (15)一、厂址的选择原则 (15)二、厂址选择方案 (16)四、选址用地权属性质类别及占地面积 (17)五、项目用地利用指标 (17)项目占地及建筑工程投资一览表 (17)六、项目选址综合评价 (18)第五章项目建设内容与建设规模 (19)一、建设内容 (19)(一)土建工程 (20)(二)设备购臵 (20)二、建设规模 (20)第六章原辅材料供应及基本生产条件 (21)一、原辅材料供应条件 (21)(一)主要原辅材料供应 (21)(二)原辅材料来源 (21)原辅材料及能源供应情况一览表 (21)二、基本生产条件 (23)第七章工程技术方案 (24)一、工艺技术方案的选用原则 (24)二、工艺技术方案 (25)(一)工艺技术来源及特点 (25)(二)技术保障措施 (25)(三)产品生产工艺流程 (25)年产40万吨汽油加氢装臵建设生产工艺流程示意简图 (26)三、设备的选择 (26)(一)设备配臵原则 (26)(二)设备配臵方案 (27)主要设备投资明细表 (28)第八章环境保护 (28)一、环境保护设计依据 (29)二、污染物的来源 (30)(一)年产40万吨汽油加氢装臵建设项目建设期污染源 (30)(二)年产40万吨汽油加氢装臵建设项目运营期污染源 (31)三、污染物的治理 (31)(一)项目施工期环境影响简要分析及治理措施 (31)1、施工期大气环境影响分析和防治对策 (32)2、施工期水环境影响分析和防治对策 (35)3、施工期固体废弃物环境影响分析和防治对策 (37)4、施工期噪声环境影响分析和防治对策 (38)5、施工建议及要求 (39)施工期间主要污染物产生及预计排放情况一览表 (41)(二)项目营运期环境影响分析及治理措施 (42)1、废水的治理 (42)办公及生活废水处理流程图 (42)生活及办公废水治理效果比较一览表 (43)生活及办公废水治理效果一览表 (43)2、固体废弃物的治理措施及排放分析 (43)3、噪声治理措施及排放分析 (45)主要噪声源治理情况一览表 (46)四、环境保护投资分析 (46)(一)环境保护设施投资 (46)(二)环境效益分析 (47)五、厂区绿化工程 (47)六、清洁生产 (48)七、环境保护结论 (48)施工期主要污染物产生、排放及预期效果一览表 (50)第九章项目节能分析 (51)一、项目建设的节能原则 (51)二、设计依据及用能标准 (51)(一)节能政策依据 (51)(二)国家及省、市节能目标 (52)(三)行业标准、规范、技术规定和技术指导 (53)三、项目节能背景分析 (53)四、项目能源消耗种类和数量分析 (55)(一)主要耗能装臵及能耗种类和数量 (55)1、主要耗能装臵 (55)2、主要能耗种类及数量 (55)项目综合用能测算一览表 (56)(二)单位产品能耗指标测算 (56)单位能耗估算一览表 (57)五、项目用能品种选择的可靠性分析 (58)六、工艺设备节能措施 (58)七、电力节能措施 (59)八、节水措施 (60)九、项目运营期节能原则 (60)十、运营期主要节能措施 (61)十一、能源管理 (62)(一)管理组织和制度 (62)(二)能源计量管理 (62)十二、节能建议及效果分析 (63)(一)节能建议 (63)(二)节能效果分析 (64)第十章组织机构工作制度和劳动定员 (64)一、组织机构 (64)二、工作制度 (64)三、劳动定员 (65)四、人员培训 (66)(一)人员技术水平与要求 (66)(二)培训规划建议 (66)第十一章年产40万吨汽油加氢装臵建设项目投资估算与资金筹措 (67)一、投资估算依据和说明 (67)(一)编制依据 (67)(二)投资费用分析 (69)(三)工程建设投资(固定资产)投资 (69)1、设备投资估算 (69)2、土建投资估算 (69)3、其它费用 (70)4、工程建设投资(固定资产)投资 (70)固定资产投资估算表 (70)5、铺底流动资金估算 (71)铺底流动资金估算一览表 (71)6、年产40万吨汽油加氢装臵建设项目总投资估算 (71)总投资构成分析一览表 (72)二、资金筹措 (72)投资计划与资金筹措表 (73)三、年产40万吨汽油加氢装臵建设项目资金使用计划 (73)资金使用计划与运用表 (74)第十二章经济评价 (74)一、经济评价的依据和范围 (74)二、基础数据与参数选取 (75)三、财务效益与费用估算 (76)(一)销售收入估算 (76)产品销售收入及税金估算一览表 (76)(二)综合总成本估算 (77)综合总成本费用估算表 (77)(三)利润总额估算 (78)(四)所得税及税后利润 (78)(五)项目投资收益率测算 (78)项目综合损益表 (79)四、财务分析 (79)财务现金流量表(全部投资) (81)财务现金流量表(固定投资) (83)五、不确定性分析 (84)盈亏平衡分析表 (85)六、敏感性分析 (85)单因素敏感性分析表 (86)第十三章年产40万吨汽油加氢装臵建设项目综合评价 (87)第一章项目概论一、项目名称及承办单位1、项目名称:年产40万吨汽油加氢装臵建设投资建设项目2、项目建设性质:新建3、项目承办单位:广州中撰企业投资咨询有限公司4、企业类型:有限责任公司5、注册资金:100万元人民币二、项目可行性研究报告委托编制单位1、编制单位:广州中撰企业投资咨询有限公司三、可行性研究的目的本可行性研究报告对该年产40万吨汽油加氢装臵建设项目所涉及的主要问题,例如:资源条件、原辅材料、燃料和动力的供应、交通运输条件、建厂规模、投资规模、生产工艺和设备选型、产品类别、项目节能技术和措施、环境影响评价和劳动卫生保障等,从技术、经济和环境保护等多个方面进行较为详细的调查研究。
汽油加氢培训总结汇报材料

汽油加氢培训总结汇报材料汽油加氢技术培训总结一、培训概述本次培训内容主要涵盖了汽油加氢的基本原理、操作流程以及安全注意事项。
通过培训,进一步提升了参训人员的技术水平和操作能力。
二、培训内容1. 汽油加氢原理汽油加氢是通过在汽油中加入一定的氢气,利用加氢反应使石脑油、汽油等不饱和烃类转化为饱和烃类。
通过培训,我们了解到了汽油加氢的化学反应机理和反应过程,深入理解了加氢技术的重要性和应用前景。
2. 操作流程培训中,我们学习了汽油加氢的具体操作流程。
包括加氢装置的启停及调试操作、催化剂的投料和灭活操作、燃料气体的控制操作等。
通过反复的理论和实践操作,我们掌握了汽油加氢操作的基本技能。
3. 安全注意事项在汽油加氢过程中,安全是至关重要的。
培训中,我们详细了解了加氢装置的安全防护装置和应急处理措施。
同时,我们学会了正确佩戴个人防护装备,掌握了使用消防器材及应对突发情况的方法。
这些安全培训措施的运用,有助于减少事故发生的可能性,保护员工的人身安全和设备的安全。
三、培训收获通过本次加氢技术培训,我们参训人员获得了以下收获:1. 知识增长:通过系统的学习和培训,我们对汽油加氢的原理和操作流程有了更为深入的了解,增进了我们的专业知识。
2. 技能提升:通过实践操作,我们掌握了汽油加氢的操作技能,能够独立进行相关工作,并具备一定的解决问题的能力。
3. 安全意识加强:培训中的安全注意事项提醒我们,安全是首要的,我们要时刻保持警惕,遵守规章制度,确保工作安全。
4. 团队协作能力:培训现场的小组合作,加强了我们之间的沟通和配合,使我们更加懂得团队合作的重要性。
四、总结与展望本次汽油加氢技术培训为我们提供了一个宝贵的学习机会,使我们进一步强化了汽油加氢技术的应用。
通过学习和培训,我们掌握了汽油加氢的基本原理和操作流程,并在实践中将其熟练应用。
在未来的工作中,我们将更加注重安全,准确把握技术细节,为企业的发展贡献自己的力量。
通过本次培训,我们相信我们的业务和技术水平能够得到进一步提升,为企业的发展和提升竞争力做出更大的贡献!。
汽柴油加氢技术总结汇报
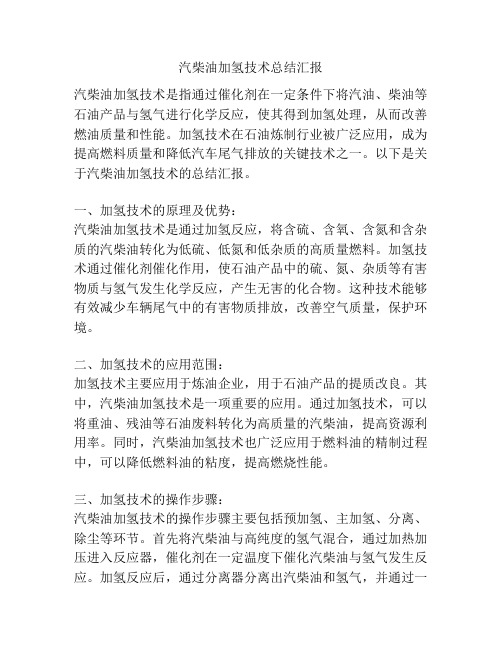
汽柴油加氢技术总结汇报汽柴油加氢技术是指通过催化剂在一定条件下将汽油、柴油等石油产品与氢气进行化学反应,使其得到加氢处理,从而改善燃油质量和性能。
加氢技术在石油炼制行业被广泛应用,成为提高燃料质量和降低汽车尾气排放的关键技术之一。
以下是关于汽柴油加氢技术的总结汇报。
一、加氢技术的原理及优势:汽柴油加氢技术是通过加氢反应,将含硫、含氧、含氮和含杂质的汽柴油转化为低硫、低氮和低杂质的高质量燃料。
加氢技术通过催化剂催化作用,使石油产品中的硫、氮、杂质等有害物质与氢气发生化学反应,产生无害的化合物。
这种技术能够有效减少车辆尾气中的有害物质排放,改善空气质量,保护环境。
二、加氢技术的应用范围:加氢技术主要应用于炼油企业,用于石油产品的提质改良。
其中,汽柴油加氢技术是一项重要的应用。
通过加氢技术,可以将重油、残油等石油废料转化为高质量的汽柴油,提高资源利用率。
同时,汽柴油加氢技术也广泛应用于燃料油的精制过程中,可以降低燃料油的粘度,提高燃烧性能。
三、加氢技术的操作步骤:汽柴油加氢技术的操作步骤主要包括预加氢、主加氢、分离、除尘等环节。
首先将汽柴油与高纯度的氢气混合,通过加热加压进入反应器,催化剂在一定温度下催化汽柴油与氢气发生反应。
加氢反应后,通过分离器分离出汽柴油和氢气,并通过一系列的脱硫、脱氮、脱杂等工艺处理,最终得到高质量的汽柴油产品。
四、加氢技术的优势与不足:加氢技术具有以下优势:1. 改善燃料质量:通过加氢处理,汽柴油的硫含量、氮含量和杂质含量得到有效降低,提高了燃料的质量。
2. 降低尾气排放:加氢技术能够减少燃料中的有害物质含量,从而降低了汽车尾气中的污染物排放,改善环境质量。
3. 提高能源利用率:通过将废料油转化为汽柴油,提高了资源利用效率,减少了能源浪费。
不足之处:1. 技术要求高:加氢技术对催化剂稳定性、反应条件、操作参数等要求较高,需要专业技术人员掌握和操作。
2. 设备投资大:加氢技术需要投入大量设备和催化剂,投资成本较高。
石化加氢工作总结

石化加氢工作总结
石化加氢是炼油工业中非常重要的工艺之一,它通过加氢反应将重质石油产品
转化为轻质产品,提高产品的质量和减少环境污染。
在过去的一段时间里,我们团队在石化加氢工作中取得了一定的成绩,现在我将对我们的工作进行总结。
首先,我们在石化加氢工作中注重了安全生产。
加氢反应是高温高压下进行的,一旦发生事故后果将不堪设想。
因此,我们严格执行安全操作规程,定期进行设备检修和维护,确保设备运行的安全可靠。
同时,我们也加强了员工的安全培训,提高了员工的安全意识和应急处理能力,有效地保障了生产安全。
其次,我们在工艺优化方面取得了一些进展。
我们对加氢反应的工艺参数进行
了优化调整,提高了产品的收率和质量。
通过改进催化剂的配方和制备工艺,我们成功地降低了生产成本,提高了生产效率。
此外,我们还引进了先进的自动化控制系统,实现了设备的智能化运行,进一步提高了生产的稳定性和可靠性。
最后,我们在环保方面也做出了一些努力。
石化加氢工艺会产生大量的硫化氢
和硫化物等有害气体,对环境造成严重污染。
为了减少排放,我们加强了废气处理设施的建设和运行,有效地净化了废气排放。
同时,我们还对废水处理系统进行了改造升级,减少了废水排放对水环境的影响。
总的来说,我们在石化加氢工作中取得了一些成绩,但也存在一些问题和不足。
未来,我们将继续努力,不断改进工艺,提高生产效率和产品质量,同时加强安全生产和环保工作,为炼油工业的可持续发展做出更大的贡献。
加氢装置开工个人工作总结
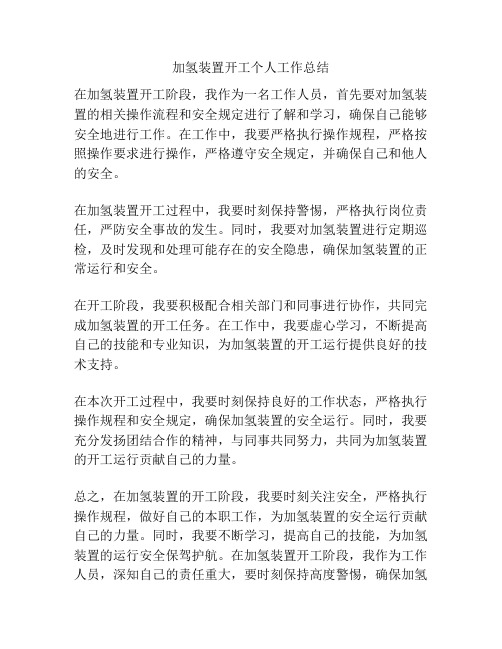
加氢装置开工个人工作总结在加氢装置开工阶段,我作为一名工作人员,首先要对加氢装置的相关操作流程和安全规定进行了解和学习,确保自己能够安全地进行工作。
在工作中,我要严格执行操作规程,严格按照操作要求进行操作,严格遵守安全规定,并确保自己和他人的安全。
在加氢装置开工过程中,我要时刻保持警惕,严格执行岗位责任,严防安全事故的发生。
同时,我要对加氢装置进行定期巡检,及时发现和处理可能存在的安全隐患,确保加氢装置的正常运行和安全。
在开工阶段,我要积极配合相关部门和同事进行协作,共同完成加氢装置的开工任务。
在工作中,我要虚心学习,不断提高自己的技能和专业知识,为加氢装置的开工运行提供良好的技术支持。
在本次开工过程中,我要时刻保持良好的工作状态,严格执行操作规程和安全规定,确保加氢装置的安全运行。
同时,我要充分发扬团结合作的精神,与同事共同努力,共同为加氢装置的开工运行贡献自己的力量。
总之,在加氢装置的开工阶段,我要时刻关注安全,严格执行操作规程,做好自己的本职工作,为加氢装置的安全运行贡献自己的力量。
同时,我要不断学习,提高自己的技能,为加氢装置的运行安全保驾护航。
在加氢装置开工阶段,我作为工作人员,深知自己的责任重大,要时刻保持高度警惕,确保加氢装置的安全运行。
在工作中,我要严格按照操作规程进行操作,确保操作步骤的准确性和规范性。
同时,我要认真履行岗位职责,积极主动地发现和处理可能存在的问题,确保加氢装置的运行安全稳定。
为了保证加氢装置的运行状态,我要进行定期巡检和维护工作,及时发现和解决可能存在的故障和问题。
在开工阶段,特别要注意加氢装置的相关设备和管道是否存在泄漏、腐蚀等现象,及时进行维修和更换,确保设备的正常运行。
在加氢装置开工的过程中,我要密切配合相关部门和同事进行协作,共同努力完成加氢装置的开工任务。
在工作中,我要主动沟通,及时交流工作进展和问题,确保工作的顺利进行。
同时,我也要尊重和支持同事,发挥团队合作精神,共同为加氢装置的开工运行贡献自己的力量。
炼油化工装置开工一次成功总结

炼油化工装置开工一次成功总结公司油品质量升级改扩建项目安装工程于2009年11月正式启动,克服了施工场地狭窄,阴雨天气较多,地质条件复杂等诸多困难,发扬不拍疲劳,连续作战的工作作风,科学管理,精心策划,严格把关,实现了各装置的正点中交:1000万吨/年常减压装置2010年10月8日装置中交,280万吨/年常催化裂化装置2010年9月25日装置中交,,280万吨/年汽柴油加氢装置2010年9月25日装置中交,120万吨/年S-Zorb装置2010年8月20日装置中交。
6万吨/年硫磺装置2010年9月15日装置中交,60万吨/年气分装置8月25日装置中交,产品精制装置7月31日装置中交。
各装置中交以后,公司精心组织,科学管理,严格控制,于2010年11月26日打通全流程,实现了开工一次成功的目标。
一、领导重视团队合作公司油品质量升级改扩建项目作为炼油改造工程,存在系统配套复杂,新老衔接紧密,影响因素繁多等诸多困难,在项目设计与建设阶段前期阶段,公司就成立以公司主要领导牵头的领导小组与工作小组,公司各职能处室参与的系统、技术等工作小组,从设计、建设阶段就保证了方案的符合性、正确性、合理性、有效性,切实做到了不漏项、不缺陷、考虑周全。
中交以后,进入装置开工试运阶段,公司成立了主要领导为首的开工领导小组及开工现场指挥部,公司各职能处室专家、工程技术人员参与的13个现场职能组,做到人员到位,职责明确,层次清晰。
在中交前的关键阶段,总部高级副总裁章建华亲自率队在召开了项目开工动员与协调会,对开工试运提出了明确的要求。
总部炼油事业部、工程部、安环局亲自参加开工,并及时协调组织了相关企业的技术专家支持团队,对我公司开工试运进行全方位的指导与把关。
总部的高度重视与全力支持,公司领导的亲自把关与参与,各部门、各团队的通力合作为我公司的项目开车一次成功奠定了坚实的组织基础。
二、科学筹划提前准备公司油品质量升级改扩建项目开工试运工作,公司层面非常重视,在中交前四个月,公司就安排对开工试运的时间统筹、组织机构、管理模式、运行方式、考核奖惩、后勤保障等诸多方面进行筹划,并且多次召开专题会进行讨论与安排。
加氢改质装置掺炼焦化汽柴油运行总结

加氢改质装置掺炼焦化汽柴油运行总结张铁柱(中国石油天然气股份有限公司锦州石化分公司,辽宁省锦州市121001)摘要:为解决加氢改质装置负荷低、焦化汽柴油加工流程长、加工费用高的问题,中国石油天然气股份有限公司锦州石化分公司通过技术改造将焦化汽柴油并入加氢改质装置加工。
加氢改质装置新增焦化汽柴油过滤器和脱丁烷塔塔顶水冷器,并调整了催化剂装填方案和生产方案。
加氢改质装置掺炼焦化汽柴油后,反应一床层温升增加近一倍,各产品性质均有向好趋势,循环氢纯度有所下降,铵盐结盐点前移,装置结盐腐蚀风险增大,但总体运行稳定。
通过分析掺炼前后运行条件和产品性质,提出加氢改质装置掺炼焦化汽柴油的可行性、存在问题及解决措施,探索出新的焦化汽柴油加工路线。
关键词:加氢改质 掺炼 焦化汽柴油 过滤器 催化剂 脱丁烷塔塔顶水冷器 中国石油天然气股份有限公司锦州石化分公司(锦州石化公司)加氢改质装置设计规模为2.8Mt/a,采用中压加氢改质工艺技术(MHUG),反应操作压力12MPa,原设计以催化裂化柴油、直馏柴油混合油(催化直馏柴油)为原料,经过脱硫、脱氮、芳烃饱和、烯烃饱和,生产液化石油气、轻石脑油、重石脑油、煤油和精制柴油,其中精制柴油满足国Ⅴ车用柴油标准。
锦州石化公司焦化汽柴油加氢精制装置原设计规模为400kt/a,后扩能改造至600kt/a,虽经多次技术改造,但由于装置工艺落后、设备老化等问题,安全性和产品质量都无法满足现行标准要求,产品需要经过二次加工才能满足国Ⅴ标准,加工费用高。
焦化汽柴油中多环芳烃在加氢改质装置中进行裂化反应后,主要集中在石脑油馏分和中间馏分中,使石脑油馏分的芳烃潜含量增高,是较好的重整装置原料,煤油、柴油馏分中的环烷烃也能保持较好的燃烧性能和较高的热值[1],因此柴油加氢改质装置掺炼焦化汽柴油在理论上是可行的。
但是鉴于焦化装置的生产特点,焦化汽柴油会携带焦粉和微量硅,会堵塞加氢催化剂床层,并使加氢催化剂中毒,因此焦化汽柴油不适宜直接进入加氢改质装置进行掺炼[2]。
加氢岗位工作总结
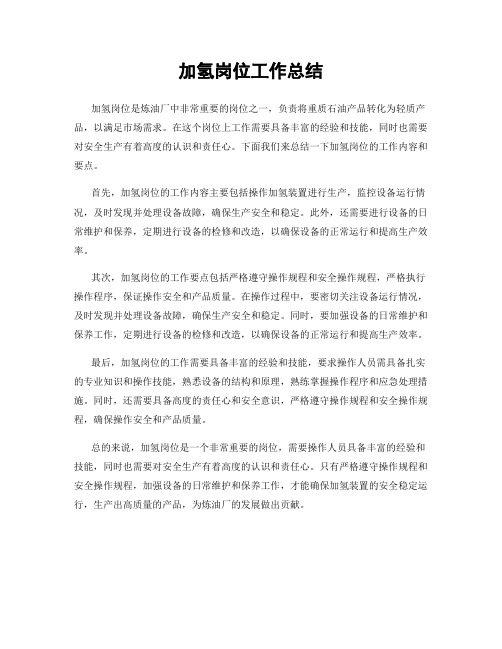
加氢岗位工作总结
加氢岗位是炼油厂中非常重要的岗位之一,负责将重质石油产品转化为轻质产品,以满足市场需求。
在这个岗位上工作需要具备丰富的经验和技能,同时也需要对安全生产有着高度的认识和责任心。
下面我们来总结一下加氢岗位的工作内容和要点。
首先,加氢岗位的工作内容主要包括操作加氢装置进行生产,监控设备运行情况,及时发现并处理设备故障,确保生产安全和稳定。
此外,还需要进行设备的日常维护和保养,定期进行设备的检修和改造,以确保设备的正常运行和提高生产效率。
其次,加氢岗位的工作要点包括严格遵守操作规程和安全操作规程,严格执行操作程序,保证操作安全和产品质量。
在操作过程中,要密切关注设备运行情况,及时发现并处理设备故障,确保生产安全和稳定。
同时,要加强设备的日常维护和保养工作,定期进行设备的检修和改造,以确保设备的正常运行和提高生产效率。
最后,加氢岗位的工作需要具备丰富的经验和技能,要求操作人员需具备扎实的专业知识和操作技能,熟悉设备的结构和原理,熟练掌握操作程序和应急处理措施。
同时,还需要具备高度的责任心和安全意识,严格遵守操作规程和安全操作规程,确保操作安全和产品质量。
总的来说,加氢岗位是一个非常重要的岗位,需要操作人员具备丰富的经验和技能,同时也需要对安全生产有着高度的认识和责任心。
只有严格遵守操作规程和安全操作规程,加强设备的日常维护和保养工作,才能确保加氢装置的安全稳定运行,生产出高质量的产品,为炼油厂的发展做出贡献。
化工加氢工作总结范文(3篇)
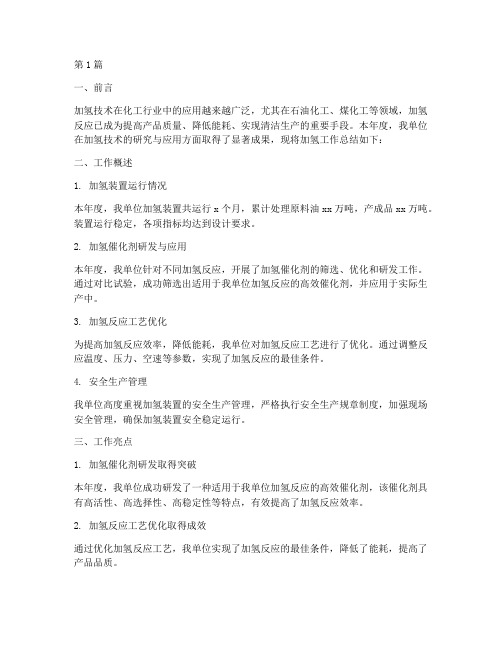
第1篇一、前言加氢技术在化工行业中的应用越来越广泛,尤其在石油化工、煤化工等领域,加氢反应已成为提高产品质量、降低能耗、实现清洁生产的重要手段。
本年度,我单位在加氢技术的研究与应用方面取得了显著成果,现将加氢工作总结如下:二、工作概述1. 加氢装置运行情况本年度,我单位加氢装置共运行x个月,累计处理原料油xx万吨,产成品xx万吨。
装置运行稳定,各项指标均达到设计要求。
2. 加氢催化剂研发与应用本年度,我单位针对不同加氢反应,开展了加氢催化剂的筛选、优化和研发工作。
通过对比试验,成功筛选出适用于我单位加氢反应的高效催化剂,并应用于实际生产中。
3. 加氢反应工艺优化为提高加氢反应效率,降低能耗,我单位对加氢反应工艺进行了优化。
通过调整反应温度、压力、空速等参数,实现了加氢反应的最佳条件。
4. 安全生产管理我单位高度重视加氢装置的安全生产管理,严格执行安全生产规章制度,加强现场安全管理,确保加氢装置安全稳定运行。
三、工作亮点1. 加氢催化剂研发取得突破本年度,我单位成功研发了一种适用于我单位加氢反应的高效催化剂,该催化剂具有高活性、高选择性、高稳定性等特点,有效提高了加氢反应效率。
2. 加氢反应工艺优化取得成效通过优化加氢反应工艺,我单位实现了加氢反应的最佳条件,降低了能耗,提高了产品品质。
3. 安全生产管理成效显著我单位严格执行安全生产规章制度,加强现场安全管理,确保加氢装置安全稳定运行,全年未发生安全事故。
四、存在问题及改进措施1. 存在问题(1)加氢催化剂研发周期较长,部分催化剂性能有待进一步提高。
(2)加氢反应工艺优化仍有空间,能耗降低潜力较大。
(3)安全生产管理仍需加强,尤其在现场操作人员的安全意识方面。
2. 改进措施(1)加强加氢催化剂研发,缩短研发周期,提高催化剂性能。
(2)持续优化加氢反应工艺,降低能耗,提高产品品质。
(3)加强安全生产管理,提高现场操作人员的安全意识,确保加氢装置安全稳定运行。
炼油厂实习个人总结(通用7篇)

炼油厂实习个人总结(通用7篇)炼油厂实习个人总结 1有一句古语:纸上得来终觉浅,绝知此事要躬行,在石油石化行业也是如此。
在自己这些天的实习过程中,真正的脱离了课本,投入到石化行业的设备认识中,学到了许多原先在课本上学不到的东西,也为自己进一步步投入石化行业获得了一个更好的机会。
课本上学到的是理论知识,而化工厂的实习则是对石化行业的熟悉与认识,也为自己以后的工作环境有了心理准备。
虽然认识实习的时间不长,但收获还是颇丰的,下面我就说一说这几天实习的心得以及对我国未来石油化工中催化裂化行业的展望。
这次实习一共有两个阶段,第一阶段在青岛地区实习,第二阶段在东营地区实习,而这两个阶段的'实习都是从安全教育开始的,这也足以说明安全在石油化工行业是最重要的。
毕竟只有安全有了保障,炼厂才能生产下去,石油化工行业才能安全发展下去。
目前全国的化工方面安全形势依然严峻,每年都有数万人死亡,因此不管前期准备多么充足,设备检修多么频繁,安全一定要放在心上,进入工厂手机关机,穿长袖衣服,戴安全帽,小心明火,不带打火机等等。
经过几天对化工设备工作原理的讲解,对模型的讲解,我们于7月7日下午进入了青岛大炼油进行了第一次参观与学习,随后我们又在东营的石大科技集团以及位于垦利的胜华炼厂进行参观学习。
在这几次参观学习中,我们了解了炼化厂的常减压装置、催化炼化装置等几套核心装置的工作顺序与工作原理。
随后在11号下午,我们又参观了模型室,通过对一些拆分的装置讲解以及能转动的压缩泵等进一步了解了化工行业的一些重要核心部位的工作原理。
1、常减压蒸馏设备常减压蒸馏基本属物理过程,原料油在蒸馏塔里按蒸发能力分成沸点范围不同的油品(称为馏分),这些油有的经调合、加添加剂后以产品形式出厂,相当大的部分是后续加工装置的原料,因此,常减压蒸馏又被称为原油的一次加工。
包括三个工序:原油的脱盐、脱水;常压蒸馏;减压蒸馏。
2、催化裂化催化裂化是提高原油加工深度,生产优质汽油、柴油最重要的工艺操作。
装置开工总结
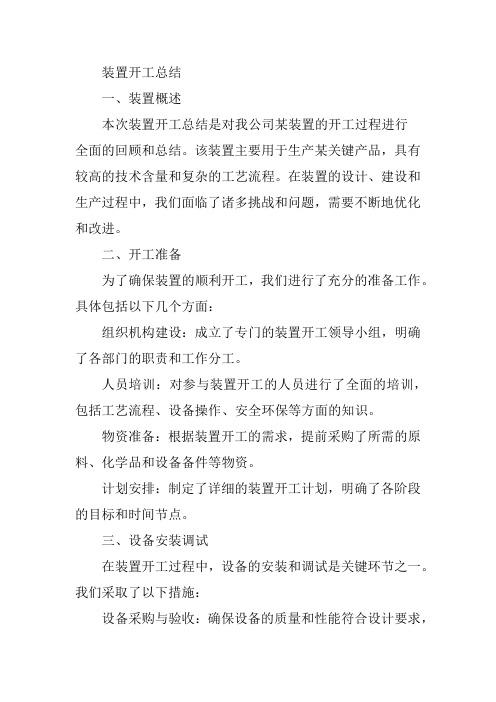
装置开工总结一、装置概述本次装置开工总结是对我公司某装置的开工过程进行全面的回顾和总结。
该装置主要用于生产某关键产品,具有较高的技术含量和复杂的工艺流程。
在装置的设计、建设和生产过程中,我们面临了诸多挑战和问题,需要不断地优化和改进。
二、开工准备为了确保装置的顺利开工,我们进行了充分的准备工作。
具体包括以下几个方面:组织机构建设:成立了专门的装置开工领导小组,明确了各部门的职责和工作分工。
人员培训:对参与装置开工的人员进行了全面的培训,包括工艺流程、设备操作、安全环保等方面的知识。
物资准备:根据装置开工的需求,提前采购了所需的原料、化学品和设备备件等物资。
计划安排:制定了详细的装置开工计划,明确了各阶段的目标和时间节点。
三、设备安装调试在装置开工过程中,设备的安装和调试是关键环节之一。
我们采取了以下措施:设备采购与验收:确保设备的质量和性能符合设计要求,并对设备进行了严格的验收。
安装施工:按照设计图纸和施工规范进行设备的安装施工,确保设备的安装精度和稳定性。
调试与试运行:对安装完成的设备进行了严格的调试和试运行,确保设备的正常运行和性能达标。
四、人员培训与考核为了提高装置开工的效率和安全性,我们进行了以下人员培训与考核工作:培训形式:采取了集中培训、现场培训和在线培训等多种形式,以满足不同人员的培训需求。
考核方式:对参与装置开工的人员进行了理论考核和实践操作考核,确保他们具备相应的技能和知识。
培训效果评估:对培训效果进行了评估,并根据评估结果对培训内容和方式进行了优化和改进。
五、安全环保措施在装置开工过程中,我们采取了以下安全环保措施:安全管理制度:制定了严格的安全管理制度和操作规程,确保人员的安全操作。
环保措施:对装置产生的废气、废水、废渣等污染物进行了有效的治理和处置,确保符合环保要求。
加氢装置年度工作总结会

加氢装置年度工作总结会概述根据公司要求,我们对加氢装置的年度工作进行了总结和评估。
首先,感谢各位同事一年来的辛勤工作和付出。
在大家的共同努力下,加氢装置顺利运行,达到了预期的目标。
以下是今年加氢装置的工作总结和反思。
一、工作回顾1. 运行情况加氢装置在过去一年中保持了稳定和高效的运转状态。
主要指标如下:- 加氢装置达到了设备额定处理量,并保持稳定的运行状态。
- 运行周期和维修时间得到有效控制,减少了设备停机和维修所导致的生产损失。
- 装置的产品质量达到了国家相关标准,并在用户中获得了良好的声誉。
2. 安全生产加氢装置的安全生产一直是我们的首要任务。
通过以下措施,我们保证了安全工作的顺利进行:- 严格执行安全操作规程,加强现场巡检,及时处理异常情况。
- 定期组织安全培训和演练,提高员工的安全防范意识。
- 强化设备的维护保养,确保设备的可靠性和安全性。
- 加强与相关部门的沟通合作,共同推动安全生产工作。
3. 技术改进为提高加氢装置的生产效率和产品质量,我们积极采取了一些技术改进措施:- 优化操作参数,提高了产品收率和质量。
- 引进了先进的控制系统,提升了装置的自动化程度和生产效率。
- 加强了对催化剂的研究和开发,提高了加氢装置的催化效果。
4. 能源消耗加氢装置的能源消耗一直是我们关注的重要指标。
通过以下措施,我们取得了一定的成效:- 优化装置流程,减少了能源的浪费。
- 定期检查和维护设备,保持设备的良好状态,减少能源的损耗。
- 加强员工的能源意识,提高节约用能的自觉性。
二、存在的问题与改进方向在工作总结中,我们也明确了一些存在的问题和需要改进的方向:1. 人员管理加氢装置的人员管理需要进一步完善。
当前存在的问题主要有:- 人员队伍需要进行专业技能培训,提高员工的工作效率和质量。
- 加强人员的岗位职责和分工,明确责任和任务,提高工作效率。
- 搭建有效的沟通渠道,增强员工间的协作和沟通能力。
2. 设备维护设备维护是保证加氢装置长期稳定运行的关键。
加氢装置个人年终总结
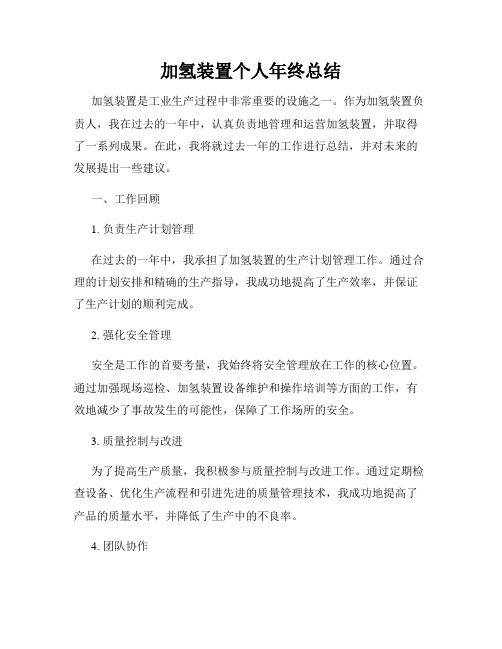
加氢装置个人年终总结加氢装置是工业生产过程中非常重要的设施之一。
作为加氢装置负责人,我在过去的一年中,认真负责地管理和运营加氢装置,并取得了一系列成果。
在此,我将就过去一年的工作进行总结,并对未来的发展提出一些建议。
一、工作回顾1. 负责生产计划管理在过去的一年中,我承担了加氢装置的生产计划管理工作。
通过合理的计划安排和精确的生产指导,我成功地提高了生产效率,并保证了生产计划的顺利完成。
2. 强化安全管理安全是工作的首要考量,我始终将安全管理放在工作的核心位置。
通过加强现场巡检、加氢装置设备维护和操作培训等方面的工作,有效地减少了事故发生的可能性,保障了工作场所的安全。
3. 质量控制与改进为了提高生产质量,我积极参与质量控制与改进工作。
通过定期检查设备、优化生产流程和引进先进的质量管理技术,我成功地提高了产品的质量水平,并降低了生产中的不良率。
4. 团队协作作为加氢装置的负责人,我加强了与团队成员的沟通和协作。
通过定期召开工作会议、分享技术经验和共同制定工作目标,我们建立了一个相互信任、互相支持的团队,提高了工作效率和合作意识。
二、取得成果1. 提高生产效率通过合理的计划管理和优化生产流程,我成功地提高了加氢装置的生产效率。
在过去的一年中,生产能力得到了显著提升,实现了更高效的生产运营。
2. 降低生产成本通过优化设备运行管理和精确的材料控制,我成功地降低了生产成本。
在过去的一年中,加氢装置的运营成本得到了有效控制,为企业节约了大量成本。
3. 提高产品质量通过加强质量控制与改进工作,我成功地提高了产品的质量水平。
在过去的一年中,产品的不良率明显下降,提升了客户对产品的满意度。
4. 加强团队合作通过加强团队沟通和协作,我成功地提高了团队的合作意识和工作效率。
在过去的一年中,团队的凝聚力得到了增强,为企业的发展奠定了坚实的基础。
三、未来发展建议1. 进一步提高安全管理水平安全是工作的核心,我们应进一步加强加氢装置的安全管理。
加氢装置操作工报告

加氢装置操作工报告
报告内容分为三个部分,加氢装置操作工的工作内容、工作中遇到的问题以及解决方案、工作中的改进建议。
第一部分,加氢装置操作工的工作内容包括但不限于:
1. 熟悉加氢装置的操作流程和相关设备的使用方法;
2. 确保加氢装置设备的正常运行,监控设备运行状态;
3. 配合其他部门进行设备维护和维修;
4. 遵守相关安全操作规程,确保操作过程中的安全;
5. 参与设备的日常检查和维护工作;
6. 协助上级主管完成其他工作任务。
第二部分,工作中遇到的问题以及解决方案:
在操作加氢装置的过程中,可能会遇到设备故障、操作失误、安全隐患等问题。
在遇到问题时,操作工需要及时报告,并根据实际情况采取相应的解决措施。
例如,如果发现设备出现故障,需要及时停机并通知维修人员进行处理;如果发现操作失误导致安全隐患,需要立即采取措施消除隐患,并报告相关负责人。
第三部分,工作中的改进建议:
在实际操作中,操作工可能会发现一些设备运行不畅、操作流程不够高效等问题,可以提出改进建议,以提高工作效率和设备运行稳定性。
例如,针对设备运行不畅的问题,可以提出设备维护周期的调整或设备更新换代的建议;针对操作流程不够高效的问题,可以提出操作流程的优化建议,提高操作效率。
总结,加氢装置操作工的工作报告需要全面反映工作内容、遇到的问题以及解决方案、工作中的改进建议,以便及时总结经验、改进工作。
- 1、下载文档前请自行甄别文档内容的完整性,平台不提供额外的编辑、内容补充、找答案等附加服务。
- 2、"仅部分预览"的文档,不可在线预览部分如存在完整性等问题,可反馈申请退款(可完整预览的文档不适用该条件!)。
- 3、如文档侵犯您的权益,请联系客服反馈,我们会尽快为您处理(人工客服工作时间:9:00-18:30)。
40万吨/年汽油加氢脱硫装置开工运行总结
张超群崔昕宇
重整加氢车间
一、装置概况
中国石油玉门油田公司炼油化工总厂40万吨/年汽油加氢装置,采用中国石油化工研究院研发的DSO技术,运用低压固定床工艺,以催化汽油为原料,对催化汽油进行预加氢、加氢精制和加氢改质,以改善汽油产品质量,满足全厂调和生产国Ⅳ汽油产品的需求,并为满足全厂调和生产国Ⅴ汽油产品打下基础。
根据玉门炼化总厂催化汽油的生产情况,本装置预加氢部分设计规模为40万吨/年,操作弹性为60%~110%,设计年开工时间8400h。
玉门炼化总厂40万吨/年汽油加氢装置由中国石油华东勘察设计院EPC项目总承包,于2013年9月28日装置建成中交,炼化总厂从9月29日开始组织装置投料试车。
二、开工情况
1、非临氢系统主要开工过程:
9月29日至10月4日进行分馏、稳定系统吹扫;10月5日至7日原料脱砷、分馏、稳定系统试压;10月8日至9日单机试运后水联运;10月10日至11日冷油联运;10月12日热油联运,带分馏塔底循环加热炉烘炉。
10月16日分馏系统冲压至操作压力0.7MPa、稳定系统冲压至操作压力0.9MPa,气密结束。
10月18日E-1205密封面整改完毕,稳定塔冲压做气密。
10月19日分馏塔底再沸炉烘炉完毕。
10月22日18:00装置广播对讲系统调试完毕。
10月23日至30日进行非临氢系统检查,并对发现问题及时整改。
2、临氢系统主要开工过程:
9月28日至10月2日临氢系统爆破吹扫;10月3日至5日临氢氮气置换,系统1.0MPa氮气气密、试压、整改漏点,并进行新氢压缩机、循环氢压缩机试运;10月6日至9日临氢系统2.2MPa 氮气气密、试压、整改漏点;10月9日至13日加氢脱硫产物加热炉烘炉、反应系统升温干燥;10月13日至15日,各反应器催化剂的装填完毕;10月16日脱砷剂装填完毕。
10月17日20:00启动循环氢压缩机,预加氢催化剂、加氢脱硫催化剂开始干燥;10月20日19:50,预加氢催化剂和加氢脱硫催化剂干燥结束;10月21日8:20,开始干燥后处理催化剂;10月22日22:30,后处理催化剂干燥结束;10月23日8:30,开始脱砷剂干燥;10月24日15:30 脱砷剂干燥结束;10月25日至28日,装置所有工艺联锁逻辑回路调试完毕。
11月6日至9日,预加氢催化剂、加氢脱硫催化剂、后处理催化剂硫化结束,20:10导通开工正向流程。
21:10预加氢反应器开始充液。
11月10日4:50切进催化汽油原料,调整操作参数。
11月11日20:00,R-1101入口温度升至80℃,R-1201入口升至215℃,R-1202入口温度升至260℃,汽油产品总硫降至48.95ppm,硫醇硫2ppm,辛烷值损失小于1,产品质量达到设计值,标志着40万吨/年催化汽油加氢脱硫装置一次开车成功。
三、运行数据
装置开工成功后运行主要工艺参数如表-1、表-2所示。
化验分析数据如表-3所示。
表-1反应系统主要工艺参数
表-2 分馏系统主要运行工艺参数
表-3 化验分析数据
四、装置优化调整情况
1、往复式压缩机(新氢压缩机和循环氢压缩机)共4台进出口增加旁路设计,解决了压缩机“0”负荷开车时入口负压、出口正压压力不平衡的可靠性和安全性问题;
2、稳定塔设计和施工建设均没有补压线,塔压低时无补压手段,开工过程中新增稳定塔顶补压线,解决稳定塔压力过低时无法补压控制的问题,目前稳定塔压力控制平稳;
3、在压缩机试运行过程中,新氢压缩机振动偏大,经过厂家沟通维修,压缩机振动问题已经解决;在循环氢压缩机试运行过程中,循环氢压缩机进出口管线振动较大,通过增加管线支撑,解决压缩机进出口管线振动问题;
4、装置运行初期系统压力控制不稳,无法实现自动控制,手动控制调节频繁,而且压力波动较大,将反应系统压力与补充新氢流量串级控制改为反应系统压力与循环氢压缩机入口分液罐顶废氢外排流量串级控制后,系统压力实现自动控制,而且一直稳定在设计压力1.5Mpa。
5、由于施工过程中没有单独设置产品不合格线,开工过程中新增污油出装置至50万吨/年柴油加氢改质装置流程,本装置污油打至柴油加氢装置经过加氢后进入重整原料,同时,催化剂硫化后硫化油也可以通过该流程退至柴油加氢装置,解决了催化剂硫化后硫化油的退油问题。
五、目前装置存在的问题
1、装置工艺联锁繁多,部分工艺联锁不具备投用条件,具体如下:
(1)加热炉入炉空气压力联锁,由于各加热炉入炉压力表引线安装位置距离二次风门太近,加热炉处于负压操作,导致仪表引线处为负压值,而加热炉供风压力联锁值为≤100Pa,因此该联锁投用时直接就会导致加热炉联锁自保。
(2)由于装置所有仪表伴热施工不到位,仪表引线过长,全部仪表表头均无伴热,在玉门所处地理环境,冬季仪表极易低温失灵,在近期气温较低的天气已经出现过仪表大面积失灵现象,因此,部分流量低低、液位低低联锁投用后容易因低温天气仪表失灵导致联锁,影响装置的长周期平稳运行。
2、装置伴热系统不完善,影响装置的安全平稳运行。
(1)汽油加氢装置伴热管线混乱,一根蒸汽引出同时给不同工艺管线或仪表伴热后又回到不同的凝结水线,经常发生伴热不过现象,遇到低温天气,仪表由于伴热不过经常失灵。
(2)由于本装置所有伴热采用蒸汽,温度太高,部分仪表伴热引线内介质汽化严重,导致仪表测量值误差较大,如果停用又容易发生冻凝。
3、分馏塔压控阀选型太小,塔压控制波动较大。
分馏塔塔压采用分程控制,压力低时由新氢补压,压力高时排至低压瓦斯系统。
但是由于瓦斯气外排阀芯偏小,经常出现塔压偏高气体外排不畅现象。
同时导致装置液收损失较大,经化验分析,分馏塔顶回流罐气体中C4、C5含量有将近40%,因此建议将分馏塔顶回流罐D-1103外排瓦斯气通过新增管线引进稳定塔C-1202进料后进塔进行再吸收,这样可以进一步提高装置总液收率。
4、分馏塔底循环热油泵冲洗油冷却器循环水管线负荷不够。
分馏塔低循环泵冲洗油通过循环水冷却,但是由于循环水进出冷却器管线太细,循环进水和回水压差较小,循环水进冷却器后极易汽化或气阻,导致循环水不畅,通过更换管线,冷却水常压排放近期能平稳运行,但是循环水消耗太大,装置能耗也将增大。
5、分馏塔顶轻汽油硫含量在线分析仪不准确。
为了实施监控分馏塔顶轻汽油硫含量,实现切割塔切割点自动控制,分馏塔顶轻汽油设计有一硫含量在线分析仪表,该仪表也是本装置关键性仪表,通过对轻汽油的硫含量的实时监测,可以准确控制分馏塔的切割点,准确控制切割比,该表对加氢脱硫部分影响较大,但自开工以来一直不准确,分析数据与化验室结果偏差较大,而且没有规律,轻汽油硫含量只能通过化验分析检测中心定时取样分析,分析频次较低,装置调整相对滞后,不利于装置轻重汽油切割的精确控制,不利于产品质量的稳定。
希望仪表车间尽快和厂家沟通,争取使该表能够正常平稳运行。
6、拔头油改进汽油加氢装置后的影响。
为了提高全厂汽油组分产量,自12月2日将重整装置拔头油通过开工石脑油线改进汽油加氢装置,拔头油流量由最初的2t/h提至5t/h,装置进料轻重组分比例较设计值变化较大,导致分馏塔C-1101负荷增大,又由于目前装置处于开炼初期,预加氢反应器温度较低,进塔温度偏低,分馏塔热负荷全靠塔底再沸炉提供,塔底温度提高至230℃(设计值210℃),塔底雾沫夹带量大,塔顶回流量升高,轻重汽油切割不完全,重汽油烯烃含量升高,最终导致加氢脱硫反应温升增加,装置辛烷值损失增加。
建议通过增加管线将拔头油直接改进加氢脱硫进料部分,这样既可以减小汽油辛烷值损失,又可以将拔头油转化为高效产品。
7、产品辛烷值损失偏大。
由于玉门炼厂烯烃含量高达50%,同时开炼初期,分馏塔进料温度偏低,导致轻重汽油切割不完全,加氢重汽油烯烃含量偏高,导致产品辛烷值损失偏高,平均在1.5个单位,有时辛烷值损失甚至高达2个单位,高于设计值(辛烷值损失不大于1),有待于进一步的调整优化分馏塔的操作,降低切割重汽油中的烯烃含量,降低装置的辛烷值损失。
六、结论
总结了40万吨汽油加氢装置开工过程,通过开工后近两个月运行数据情况看,DSO工艺能够达到设计指标,生产出硫含量小于70μg/g、硫醇硫含量小于10μg/g的低硫汽油调和组分,有了该装置,玉门炼厂所产汽油能够满足国Ⅳ标准要求,但是装置在运行过程中也暴露出一些问题,有待
于在装置的下一步优化调整中进一步整改。