汽车零件磷化过程
汽车零件的磷化膜质量及磷化发展趋势

( .h mia En ie r g 1C e c l gn ei Colg , ih u n le e Guzo Unv ri Guy n Guz o 5 0 0 C ia; .&D C ne , AW Gru ie t s y, ia g ih u 5 0 3, hn 2R e trF op
维普资讯
汽 车 工 艺与 材 料
・
专题综述 ・
AUT oM oBI LE TECHNOL OGY & M ATERI AL
文章 编 号 : 0 3 8 1 ( 0 6 0 - 0 9 0 10 — 87 2 0 )7 0 0 — 3
汽车零件的磷化 膜质 量及磷化 发展趋 势
态, 当被磷 化金 属 ( 例如 钢铁 ) 投人磷 化 液后 , 被处 理
C roain o hn C a g h n Jl 10 1 , hn ) op rt fC ia, h n c u in 3 0 C ia o i l
Ab t a t T e q a i a d f au e f p o p ae i m u l y n i e e t a tmo ie p r r n r d c d n r f sr c : h u l y n e t r s o h s h t l q ai o df r n u o t a t a e i t u e i b e , t f t f v s o i te h me h ns o h s h t l a t n s ic s e c re p n i g nl e c n a tr ae u c a im f p o p ae f m c i i i o d s u s d, o r s o d n if n i g f co s r s mma z d, n c re t u i r e a d u r n
轿车车身铝件的磷化工艺设计

轿车车身铝件的磷化工艺设计刘柏山(神龙汽车有限公司,武汉 430056)摘要:介绍了轿车车身前处理生产线中铝件的磷化工艺和设备设计选型原则。
详细阐述了渣泥产量的计算方法,以及磷化槽液的搅拌、渣泥的过滤系统、槽液的换热系统和游离氟加料系统的设计要点。
关键词:铝件;磷化;轿车车身中图分类号:TQ 639.1 文献标识码:A 文章编号:1009-1696(2009)09-0022-030 引言随着现代制造技术的发展,采用新材料减轻轿车车体质量的趋势越来越明显。
使用铝材是重要途径之一,除汽缸体、散热管、车轮等部件外,铝材目前已普遍使用在国内外中高档轿车车身上(如发动机罩、前吸能块等)。
为提高涂层间的附着力和防腐性能,使磷化车身电泳后获得厚度一致、光泽相同的涂层,必须考虑以钢板为主体材料的车身引入铝件后的磷化工艺设计问题。
铝材的涂装前表面处理工艺主要有以下几种:化学氧化膜法(碱性溶液氧化法)、铬酸盐膜法(黄膜铬酸盐法)、磷酸铬酸盐膜(绿膜铬酸盐法)、非铬膜、磷酸盐膜法。
铝件的单独前处理,以铬酸盐膜法为主,不过由于铬的环保问题,正在转向研究非铬膜法。
铝材作为车身的一部分被使用时,通常是将适用于钢板的磷化工艺作适当变动,采用磷酸盐膜法,直接将铝材和钢板组成的车身进入涂装前处理生产线进行磷化处理。
1 车身铝件的磷化工艺车身中的铝件进行磷化时,膜的生成原理同钢材相类似,晶体形貌也相似。
其生成膜的化学组成主要是磷酸锌,与钢材上的大致相同。
只不过为了能渗透铝件表面的氧化层,磷化槽液中要添加氟化物,比如氟硅酸盐、氟硼酸盐。
这就是针对铝材的改性锌盐磷化工艺。
铝材在磷化液中首先溶解出铝离子:2Al + 6HF→2AlF3 + 3H2[收稿日期] 2009-05-25在磷化过程中,铝的溶解量约为1.2 g/m3。
这些溶解的铝离子不仅妨碍铝材本身磷化,而且对随同的钢材磷化也带来很坏的影响。
据实验表明,当磷化液中铝离子含量高于700 mg/kg后,不能生成磷化膜。
磷酸化热处理
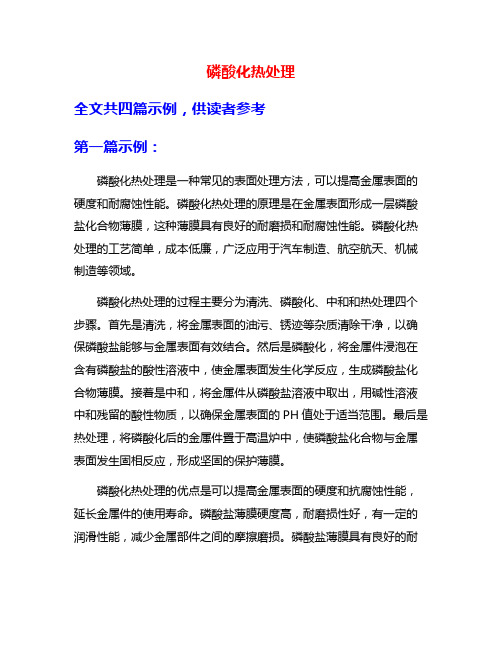
磷酸化热处理全文共四篇示例,供读者参考第一篇示例:磷酸化热处理是一种常见的表面处理方法,可以提高金属表面的硬度和耐腐蚀性能。
磷酸化热处理的原理是在金属表面形成一层磷酸盐化合物薄膜,这种薄膜具有良好的耐磨损和耐腐蚀性能。
磷酸化热处理的工艺简单,成本低廉,广泛应用于汽车制造、航空航天、机械制造等领域。
磷酸化热处理的过程主要分为清洗、磷酸化、中和和热处理四个步骤。
首先是清洗,将金属表面的油污、锈迹等杂质清除干净,以确保磷酸盐能够与金属表面有效结合。
然后是磷酸化,将金属件浸泡在含有磷酸盐的酸性溶液中,使金属表面发生化学反应,生成磷酸盐化合物薄膜。
接着是中和,将金属件从磷酸盐溶液中取出,用碱性溶液中和残留的酸性物质,以确保金属表面的PH值处于适当范围。
最后是热处理,将磷酸化后的金属件置于高温炉中,使磷酸盐化合物与金属表面发生固相反应,形成坚固的保护薄膜。
磷酸化热处理的优点是可以提高金属表面的硬度和抗腐蚀性能,延长金属件的使用寿命。
磷酸盐薄膜硬度高,耐磨损性好,有一定的润滑性能,减少金属部件之间的摩擦磨损。
磷酸盐薄膜具有良好的耐腐蚀性能,可以在恶劣的工作环境下保护金属表面免受腐蚀侵蚀。
磷酸盐薄膜的颜色稳定,不易褪色,能够提升金属表面的美观度。
磷酸化热处理的应用范围广泛,特别在汽车制造、航空航天、机械制造等领域得到了广泛应用。
在汽车制造中,发动机零部件、汽车底盘、车身构件等金属件经过磷酸化热处理后,可以提高抗疲劳性能和抗腐蚀性能,延长汽车的使用寿命。
在航空航天领域,飞机发动机零部件、飞行控制系统等关键金属件经过磷酸化热处理后,可以提高耐高温性能和耐腐蚀性能,保障飞机的安全飞行。
在机械制造领域,工业机床、模具、轴承等金属件经过磷酸化热处理后,可以提高耐磨损性能和耐腐蚀性能,延长设备的使用寿命。
磷酸化热处理是一种简单、经济、有效的表面处理方法,可以提高金属表面的硬度和耐腐蚀性能,广泛应用于各个领域。
随着技术的不断进步,磷酸化热处理的工艺将会更加完善,应用范围将会更加广泛,为金属制品的生产和应用带来更多的便利和效益。
21世纪的汽车车身用锌盐磷化处理技术

21世纪的汽车车身用锌盐磷化处理技术松下忠(日本帕卡濑精公司综合技术研究所)王锡春译1.前言现今,锌盐化处理在全世界被采用作为汽车车身的涂装前处理。
在20世纪,汽车车身要求的防锈性能靠车身结构•底材•锌盐磷化处理•涂装•防锈辅助材料等的综合技术来满足,其中锌盐磷化处理起到非常重要的作用。
锌盐磷化处理工艺包括除去附着在车身上的防锈油•冲压润滑油•切屑•或各种污物的洗净工艺,和溶解底材的化学反应,同时在车身金属表面上形成不导电的均一的锌盐磷化膜的磷化处理工艺。
锌盐磷化的膜能提高在下工序涂装的电泳膜与金属的附着力,特别能提高汽车车身的防蚀性能。
21世纪,与汽车有关的社会状况是迎来了以环境保护为中心的大的变革期。
特别是随着汽车车身的轻量化,轻量化金属材料多样化。
还有强力要求降低由锌盐磷化处理工序排出的磷化渣和排水,提高生产性和降低生产成本。
在本稿中介绍适应汽车厂最近的要求新的锌盐磷化处理技术,还有21世纪的锌盐磷化处理的动向。
2. 20世纪的锌盐磷化处理技术的变迁锌盐磷化处理工业化以来,以处理温度的低温化和缩短处理时间为中心进行探讨。
例如,当初不是锌盐磷化处理,而是铁系磷化处理,处理时间为2小时,而且温度接近沸点。
而后,添加锌,开发了锌盐磷化处理,从1930年前后开始改良。
改良事例如下表1所示。
在汽车车身斜处理得到部分实际应用。
还有,在处理时间缩短化方面,在钢铁厂的在线(in-line)处理中作为镀锌材质的涂装底层用途,进行数秒钟的锌盐磷化处理。
可是,供汽车车身用,作为电泳涂装的底层,适用构成车身的各种底材及其高要求的性能,这些技术未被采用。
`现今,汽车车身的锌盐磷化处理全世界采用浸渍型Zn-Ni-Mn(三阳离子)系,在日本国内已出现了处理温度为35℃,处理时间最短为70秒为条件的生产线。
约经一个世纪,处理时间·处理温度有着非常大的改良,在提高汽车车身的涂装性能、生产性方面作出了大的贡献。
3. 21世纪的锌盐磷化处理技术21世纪的锌盐磷化处理技术的可能性(处理温度低温化•处理时间缩短•环保技术)描述如下:3.1处理温度的低温化锌盐磷化处理反应速度取决于槽液温度•浓度•搅拌,三者越高,反应速度越快。
磷化工艺及技巧
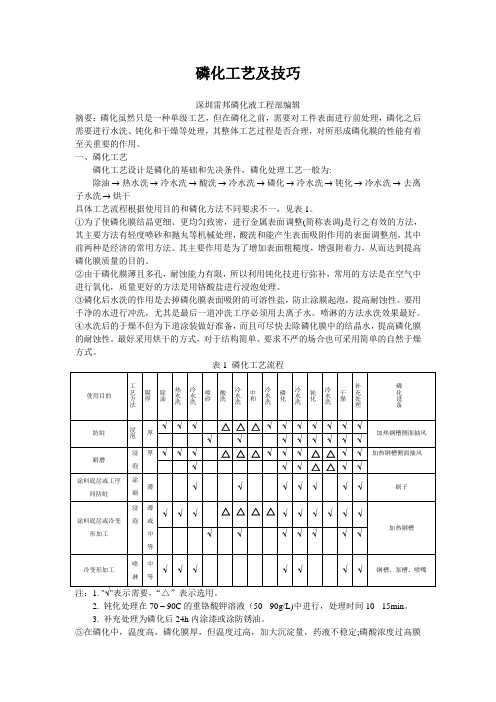
磷化工艺及技巧深圳雷邦磷化液工程部编辑摘要:磷化虽然只是一种单级工艺,但在磷化之前,需要对工件表面进行前处理,磷化之后需要进行水洗、钝化和干燥等处理,其整体工艺过程是否合理,对所形成磷化膜的性能有着至关重要的作用。
一、磷化工艺磷化工艺设计是磷化的基础和先决条件,磷化处理工艺一般为:除油→热水洗→冷水洗→酸洗→冷水洗→磷化→冷水洗→钝化→冷水洗→去离子水洗→烘干具体工艺流程根据使用目的和磷化方法不同要求不一,见表1。
①为了使磷化膜结晶更细、更均匀致密,进行金属表面调整(简称表调)是行之有效的方法,其主要方法有轻度喷砂和抛丸等机械处理,酸洗和能产生表面吸附作用的表面调整剂。
其中前两种是经济的常用方法。
其主要作用是为了增加表面粗糙度,增强附着力,从而达到提高磷化膜质量的目的。
②由于磷化膜薄且多孔,耐蚀能力有限,所以利用钝化技进行弥补,常用的方法是在空气中进行氧化,质量更好的方法是用铬酸盐进行浸泡处理。
③磷化后水洗的作用是去掉磷化膜表面吸附的可溶性盐,防止涂膜起泡,提高耐蚀性。
要用千净的水进行冲洗,尤其是最后一道冲洗工序必须用去离子水。
喷淋的方法水洗效果最好。
④水洗后的于燥不但为下道涂装做好准备,而且可尽快去除磷化膜中的结晶水,提高磷化膜的耐蚀性。
最好采用烘干的方式,对于结构简单、要求不严的场合也可采用简单的自然于燥方式。
表1 磷化工艺流程注:1. "√"表示需要,“△”表示选用。
2. 钝化处理在70 – 90C的重铬酸钾溶液(50 - 90g/L)中进行,处理时间10 - 15min。
3. 补充处理为磷化后24h内涂漆或涂防锈油。
⑤在磷化中,温度高,磷化膜厚,但温度过高,加大沉淀量,药液不稳定;磷酸浓度过高膜层疏松,过低难以成膜;溶液中Fe2+飞作用是提高磷化膜厚度和耐蚀性,但含量过高会导致膜层疏松,Zn2+的作用是加快磷化速度,提高致密性,但含量过高会导致脆性大,晶粒粗;Mn2+的作用是提高硬度、结合力和耐蚀性,但含量过高,磷化膜影响膜的形成;NO3-的作用是加快磷化速度,降低磷化温度,但含量过高会导致磷化膜粗而薄,易出现白点;NO3-的作用是加快磷化速度,减少空隙,提高耐蚀性,但含量过高易出现白点。
常见汽车级机床用零件机加热处理工艺路线
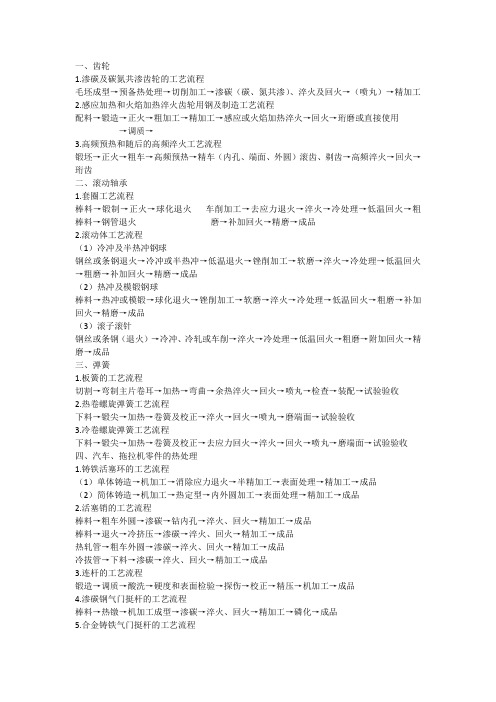
一、齿轮1.渗碳及碳氮共渗齿轮的工艺流程毛坯成型→预备热处理→切削加工→渗碳(碳、氮共渗)、淬火及回火→(喷丸)→精加工2.感应加热和火焰加热淬火齿轮用钢及制造工艺流程配料→锻造→正火→粗加工→精加工→感应或火焰加热淬火→回火→珩磨或直接使用→调质→3.高频预热和随后的高频淬火工艺流程锻坯→正火→粗车→高频预热→精车(内孔、端面、外圆)滚齿、剃齿→高频淬火→回火→珩齿二、滚动轴承1.套圈工艺流程棒料→锻制→正火→球化退火车削加工→去应力退火→淬火→冷处理→低温回火→粗棒料→钢管退火磨→补加回火→精磨→成品2.滚动体工艺流程(1)冷冲及半热冲钢球钢丝或条钢退火→冷冲或半热冲→低温退火→锉削加工→软磨→淬火→冷处理→低温回火→粗磨→补加回火→精磨→成品(2)热冲及模锻钢球棒料→热冲或模锻→球化退火→锉削加工→软磨→淬火→冷处理→低温回火→粗磨→补加回火→精磨→成品(3)滚子滚针钢丝或条钢(退火)→冷冲、冷轧或车削→淬火→冷处理→低温回火→粗磨→附加回火→精磨→成品三、弹簧1.板簧的工艺流程切割→弯制主片卷耳→加热→弯曲→余热淬火→回火→喷丸→检查→装配→试验验收2.热卷螺旋弹簧工艺流程下料→锻尖→加热→卷簧及校正→淬火→回火→喷丸→磨端面→试验验收3.冷卷螺旋弹簧工艺流程下料→锻尖→加热→卷簧及校正→去应力回火→淬火→回火→喷丸→磨端面→试验验收四、汽车、拖拉机零件的热处理1.铸铁活塞环的工艺流程(1)单体铸造→机加工→消除应力退火→半精加工→表面处理→精加工→成品(2)简体铸造→机加工→热定型→内外圆加工→表面处理→精加工→成品2.活塞销的工艺流程棒料→粗车外圆→渗碳→钻内孔→淬火、回火→精加工→成品棒料→退火→冷挤压→渗碳→淬火、回火→精加工→成品热轧管→粗车外圆→渗碳→淬火、回火→精加工→成品冷拔管→下料→渗碳→淬火、回火→精加工→成品3.连杆的工艺流程锻造→调质→酸洗→硬度和表面检验→探伤→校正→精压→机加工→成品4.渗碳钢气门挺杆的工艺流程棒料→热镦→机加工成型→渗碳→淬火、回火→精加工→磷化→成品5.合金铸铁气门挺杆的工艺流程合金铸铁整体铸造(间接端部冷激)→机械加工→淬火、回火→精加工→表面处理→成品合金铸铁整体铸造(端部冷激)→机械加工→消除应力退火→精加工→表面处理→成品钢制杆体→堆焊端部(冷激)→回火→精加工→成品钢制杆体→对焊→热处理→精加工→表面处理→成品6.马氏体型耐热钢排气阀的工艺流程马氏体耐热钢棒料→锻造成型→调质→校直→机加工→尾部淬火→抛光→成品7.半马氏体半奥氏体型耐热钢(Gr13Ni7Si2)排气阀的工艺流程棒料→顶锻→精压→热处理→精加工→成品8.奥氏体耐热钢排气阀的工艺流程棒料→顶锻→精压→阀面和尾部堆焊耐热合金→热处理→杆部滚压或软氮化→精加工→成品9.半轴调质的工艺流程合金结构钢棒料→锻造成形→正火或退火→机械加工→调质→校直→精加工→成品10.半轴的表面淬火的工艺流程棒料→锻造成形→预先热处理→校直→机械加工→表面淬火→校直→精加工→成品11.柱塞副和喷油嘴偶件的工艺流程热扎退火棒料→自动机加工成型→热处理→精加工→时效→成品12.拖拉机履带板(1)40SiMn2履带板的热处理热轧成形→下料→机加工→热处理→成品(2)ZGMn13履带板的热处理铸造成型→热处理→成品五、金属切削机床零件的热处理1.机床导轨(1)MM7125平面磨床立柱镶钢导轨锻造→正火→机加工→消除应力退火→机加工→淬火→回火→磨(2)M9025工具曲线磨床镶钢导轨锻造→退火→机加工→淬火→回火→磨(3)S788轴承磨床镶钢导轨机加工→消除应力退火→机加工→渗碳→淬火→回火→磨→时效(4)MZ208轴承磨床镶钢导轨锻造→退火→机加工→消除应力退火→机加工→淬火→冰冷处理→回火→磨→时效2.机床主轴(1)CA6104车窗主轴(45钢)下料→粗加工→正火→机加工→高频淬火→回火→磨(2)T68、T611镗床的镗杆及MGB132磨床的主轴(35CrMoAlA钢)下料→粗车→调质→精车→消除应力处理→粗磨→渗氮→粗磨(3)SGC630精密丝杠车床主轴(12CrNi3A)锻造→正火→机加工→渗碳→正火→校直→消除应力→机加工→头部淬火→颈部淬火→回火→磨→时效(4)X62W万能升降台铣床主轴(球墨铸铁QT60-2)铸造→机加工→淬火→回火(5)M1040无心磨床主轴(球墨铸铁QT60-2)铸造→机加工→正火→机加工3.丝杠(1)7级或7级精度一下的一般丝杠(45钢)下料→正火或调质→校直→消除应力处理→机加工(2)6级或6级以上精密不淬硬丝杠(T10或T12钢)球化退火→机加工→消除应力处理→机加工→时效→精加工(3)中大型精密淬硬丝杠(CrWMn)锻造→球化退火→机加工→消除应力→机加工→消除应力→机加工→淬火、回火→冰冷处理→回火→探伤→机加工→时效→精加工→时效→精加工(4)中小型精密淬硬丝杠(9Mn2V)锻造→球化退火→机加工→消除应力→机加工→淬硬淬火→回火→冰冷处理→回火、探伤→机加工→时效→精加工→时效→精加工(5)滚珠丝杠(GCr15,GCr15SiMn)4.弹簧卡头(1)卧式多轴自动车床夹料卡头(9SiCr)锻造→退火→机加工→淬火→回火→机加工→磨开口→胀大定型(2)卧式多轴自动车床送料卡头(T8A钢)锻造→退火→机加工→淬火→回火→磨(3)仪表机床小型专用卡头(60Si2)退火→机加工→淬火→回火→磨(4)磨阀辨机床专用卡头(65Mn)锻造→正火→高温→回火→机加工→淬火→回火→机加工5.摩擦片(1)X62W万能升降台铣床摩擦片(A3)机加工→渗碳→淬火→回火→机加工→回火(2)DLMO电磁离合器摩擦片(65Mn)冲片→淬火→回火→磨(3)电磁离合器摩擦片(6SiMnV)锻造→退火→切片→淬火→回火→磨6.FW250万能分度头主轴(45)锻造→正火→机加工→淬火→回火→机加工7.万能分度头蜗杆(20Cr)正火→机加工→渗碳→机加工→淬火→回火→机加工8.三爪卡盘卡爪(45)正火→机加工→淬火→回火→高频淬火→回火→法蓝→磨加工9.三爪卡盘丝(45)锻造→正火→机加工→淬火→回火→法蓝→磨六、活塞1.20CrMnMo钢制活塞的热处理锻造→正火→检验→机加工→渗碳→检验→正火→淬火→清洗→回火→检验→喷砂→磨削2.钒钢活塞的热处理下料→锻造→检验→预先淬火→球化退火→检验→机加工→淬火→回火→检验→磨削七、凿岩机钎尾锻造→退火→检验→渗碳→检验→淬火→回火→清洗→检验→磨削。
汽车涂装磷化工艺守则

共4页金杯系列车型涂装磷化工艺守则编号:GZTZ-03编制:审核:标准化:会签:批准:沈阳华晨金杯汽车有限公司重庆分公司1 范围本工艺守则规定了前处理工段磷化及三水洗、四水洗、纯水洗等工序的建槽方法、槽液参数检测及调整方法。
本工艺守则适用于重庆分公司金杯系列汽车的涂装磷化工艺要求。
2 用语解释磷化:用含有磷酸、磷酸盐等化学药品的水溶液处理金属。
在其表面发生化学反应,形成完整的、具有一定防腐蚀作用的不溶性磷酸盐膜的过程。
磷化剂:用于磷化工序的酸性药剂。
促进剂:即氧化剂,加速金属的溶解,加速H+的消耗,从而加速磷化成膜。
中和剂:用来控制磷化过程中游离酸的点数,使其在工艺要求范围内的一种药剂。
总酸度:磷化液中所有酸性物质的浓度总和,通常指磷酸二氢锌。
游离酸度:磷化液中以游离状态存在的酸的浓度,通常指磷酸。
总酸度(TA)点数:取磷化液,酚酞作指示剂,用0.1mol/LNaOH标准溶液滴定,所消耗NaOH标准溶液的毫升数来表示总酸度。
每消耗1毫升标准溶液为1点,称1Pt。
游离酸度(FA)点数:取磷化液,溴酚蓝作指示剂,用0.1mol/LNaOH标准溶液滴定,所消耗的NaOH标准溶液的毫升数来表示游离酸度。
每消耗1毫升标准溶液为1点,称1Pt。
3 磷化槽、管路及沉降塔总容量:46m34 药剂明细磷化剂:SURFDINE A Make-up (建浴剂);添加剂:STARTER 21(建浴添加剂);补加剂:SURFDINE SD2000MZ;中和剂:PRIMER 40;促进剂:TONER 30H。
NP CINDITIONER1、NP CINDITIONER2、NP CINDITIONER19。
5 建槽方法(以1000L计)编制标准化审核标记处数更改文件号签字日期标记处数更改文件号签字日期会签5.1先向磷化槽内加入槽容积4/5的工业水;5.2 在循环泵运转的状态下,加入下列药剂SURFDINE A Make-up: 25.7kg, STARTER 21:4.3kg, SURFDINE SD2000MZ:13.5kg,;5.3然后把PRIMER 40 中和剂约23kg缓慢滴加到槽液中;搅拌均匀;加入NP CINDITIONER1:2.7kg、NP CINDITIONER2:2.3kg、NP CINDITIONER19:0.5kg。
磷化处理
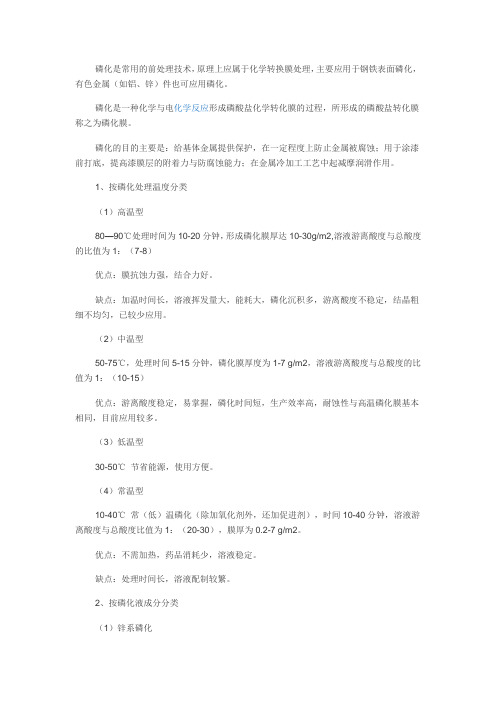
磷化是常用的前处理技术,原理上应属于化学转换膜处理,主要应用于钢铁表面磷化,有色金属(如铝、锌)件也可应用磷化。
磷化是一种化学与电化学反应形成磷酸盐化学转化膜的过程,所形成的磷酸盐转化膜称之为磷化膜。
磷化的目的主要是:给基体金属提供保护,在一定程度上防止金属被腐蚀;用于涂漆前打底,提高漆膜层的附着力与防腐蚀能力;在金属冷加工工艺中起减摩润滑作用。
1、按磷化处理温度分类(1)高温型80—90℃处理时间为10-20分钟,形成磷化膜厚达10-30g/m2,溶液游离酸度与总酸度的比值为1:(7-8)优点:膜抗蚀力强,结合力好。
缺点:加温时间长,溶液挥发量大,能耗大,磷化沉积多,游离酸度不稳定,结晶粗细不均匀,已较少应用。
(2)中温型50-75℃,处理时间5-15分钟,磷化膜厚度为1-7 g/m2,溶液游离酸度与总酸度的比值为1:(10-15)优点:游离酸度稳定,易掌握,磷化时间短,生产效率高,耐蚀性与高温磷化膜基本相同,目前应用较多。
(3)低温型30-50℃节省能源,使用方便。
(4)常温型10-40℃常(低)温磷化(除加氧化剂外,还加促进剂),时间10-40分钟,溶液游离酸度与总酸度比值为1:(20-30),膜厚为0.2-7 g/m2。
优点:不需加热,药品消耗少,溶液稳定。
缺点:处理时间长,溶液配制较繁。
2、按磷化液成分分类(1)锌系磷化(2)锌钙系磷化(3)铁系磷化(4)锰系磷化(5)复合磷化磷化液由锌、铁、钙、镍、锰等元素组成。
3、按磷化处理方法分类(1)化学磷化将工件浸入磷化液中,依靠化学反应来实现磷化,目前应用广泛。
(2)电化学磷化在磷化液中,工件接正极,钢铁接负极进行磷化。
4、按磷化膜质量分类(1)重量级(厚膜磷化)膜重7.5 g/m2以上。
(2)次重量级(中膜磷化)膜重4.6-7.5 g/m2。
(3)轻量级(薄膜磷化)膜重1.1-4.5 g/m2。
(4)次轻量级(特薄膜磷化)膜重0.2-1.0 g/m2。
酸洗磷化工艺流程
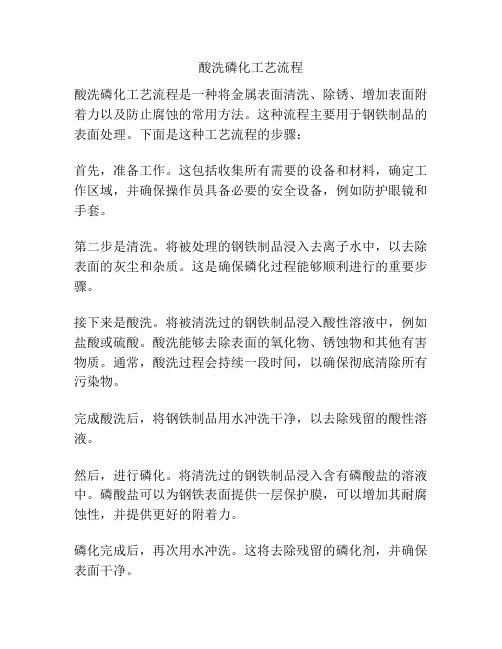
酸洗磷化工艺流程
酸洗磷化工艺流程是一种将金属表面清洗、除锈、增加表面附着力以及防止腐蚀的常用方法。
这种流程主要用于钢铁制品的表面处理。
下面是这种工艺流程的步骤:
首先,准备工作。
这包括收集所有需要的设备和材料,确定工作区域,并确保操作员具备必要的安全设备,例如防护眼镜和手套。
第二步是清洗。
将被处理的钢铁制品浸入去离子水中,以去除表面的灰尘和杂质。
这是确保磷化过程能够顺利进行的重要步骤。
接下来是酸洗。
将被清洗过的钢铁制品浸入酸性溶液中,例如盐酸或硫酸。
酸洗能够去除表面的氧化物、锈蚀物和其他有害物质。
通常,酸洗过程会持续一段时间,以确保彻底清除所有污染物。
完成酸洗后,将钢铁制品用水冲洗干净,以去除残留的酸性溶液。
然后,进行磷化。
将清洗过的钢铁制品浸入含有磷酸盐的溶液中。
磷酸盐可以为钢铁表面提供一层保护膜,可以增加其耐腐蚀性,并提供更好的附着力。
磷化完成后,再次用水冲洗。
这将去除残留的磷化剂,并确保表面干净。
最后,通过干燥钢铁制品结束整个工艺流程。
可以使用热风干燥或自然风干的方法,将水分从表面去除。
整个酸洗磷化工艺流程旨在为钢铁制品提供更好的耐腐蚀性和附着力。
它可以用于各种应用,例如汽车制造、建筑工程和家具制造等。
然而,需要注意的是,在进行酸洗磷化工艺时,操作员必须严格遵守安全规定,以确保他们的安全。
总体而言,酸洗磷化工艺流程是一种常用的方法,可以改善钢铁制品的表面性能。
通过正确执行这些步骤,可以加强钢铁制品的耐腐蚀性,并提高其在各种应用中的使用寿命。
磷化处理及工艺

磷化目录总述原理及应用磷化基础知识1. 一、磷化原理2. 二、磷化分类3. 三、磷化作用及用途4. 四、磷化膜组成及性质5. 五、磷化工艺流程6. 六、影响因素7. 七、磷化后处理8. 八、磷化渣9. 九、磷化膜质量检验10. 十、游离酸度及总酸度的测定11. 十一、有色金属磷化总述原理及应用磷化基础知识总述磷化(phosphorization)是一种化学与电化学反应形成磷酸盐化学转化膜的过程,所形成的磷酸盐转化膜称之为磷化膜。
磷化的目的主要是:给基体金属提供保护,在一定程度上防止金属被腐蚀;用于涂漆前打底,提高漆膜层的附着力与防腐蚀能力;在金属冷加工工艺中起减摩润滑使用。
磷化处理工艺应用于工业己有90多年的历史,大致可以分为三个时期:奠定磷化技术基础时期、磷化技术迅速发展时期和广泛应用时期。
磷化膜用作钢铁的防腐蚀保护膜,最早的可靠记载是英国Charles Ross于186 9年获得的专利(B.P.No.3119)。
从此,磷化工艺应用于工业生产。
在近一个世纪的漫长岁月中,磷化处理技术积累了丰富的经验,有了许多重大的发现。
一战期间,磷化技术的发展中心由英国转移至美国。
1909年美国T.W.Coslet将锌、氧化锌或磷酸锌盐溶于磷酸中制成了第一个锌系磷化液。
这一研究成果大大促进了磷化工艺的发展,拓宽了磷化工艺的发展前途。
Parker防锈公司研究开发的Parco Power配制磷化液,克服T许多缺点,将磷化处理时间提高到lho 1929年Bonderizing磷化工艺将磷化时间缩短至10min, 1934年磷化处理技术在工业上取得了革命性的发展,即采用了将磷化液喷射到工件上的方法。
二战结束以后,磷化技术很少有突破性进展,只是稳步的发展和完善。
磷化广泛应用于防蚀技术,金属冷变形加工工业。
这个时期磷化处理技术重要改进主要有:低温磷化、各种控制磷化膜膜重的方法、连续钢带高速磷化。
当前,磷化技术领域的研究方向主要是围绕提高质量、减少环境污染、节省能源进行。
汽车生产涂装车间前处理磷化工艺全

汽车生产涂装车间前处理磷化工艺磷化所谓磷化处理是指金属表面与含磷酸二氢盐的酸性溶液接触,发生化学反应而在金属表面生成稳定的不溶性的无机化合物膜层的一种表面化学处理方法,所生成的膜称为磷化膜。
具有微孔结构,在通常大气条件下比较稳定,具有一定的防锈能力,用作漆膜的底层,可以显著地提高涂层的附着力和耐蚀性能。
磷化膜作为电泳涂漆之底层,在汽车行业中得到几乎百分之百的应用。
磷化处理分类磷化处理有很多分类方法,工业上较通用的有如下几种:(1) .根据组成磷化液的磷酸盐分类,有磷酸锌系、磷酸镒系、磷酸铁系。
此外,还有在磷酸锌盐中加钙的锌钙系,在磷酸锌系中加银、加镒的所谓〃三元体系〃磷化等。
(2) .根据磷化温度分类,有高温磷化(80。
C以上)、中温磷化(50~70℃)和低温磷化(40。
C以下)。
(3) .按磷化施工方法分类,有喷淋式磷化、浸渍式磷化、喷浸结合式磷化、涂刷型磷化。
(3).按磷化膜的质量分类,有重量型(7.5g∕m2以上)、中量型(4.3g∕m2〜7.5g∕m2)、轻量型(1.1g∕m2~4.3g∕m2)和特轻量型(0.3g∕m2〜1.1g∕m2)o磷酸锌系,磷酸锌钙系,磷酸铁系磷化膜适用于涂装底层,其中以磷酸锌系磷化膜应用最为广泛。
磷酸镒系磷化膜,主要用于满足润滑性和耐磨性的要求。
磷化膜的组成和成膜机理磷化膜的组成钢铁在不同磷化液中形成的膜层的组成如表所示。
钢铁磷化膜的组成及外观类型溶液主要成分膜层主要成分膜层外观锌磷酸Zn2+,磷酸锌浅灰,深灰,黑灰色系锌系磷酸Zn2+,磷酸锌钙锌钙Ca2+,系磷酸Zn2+,磷酸锌镒锌锦Mn2+,系磷酸锦系Mn2+,磷酸锌浅灰,深灰,黑灰色磷酸铁系Fe2+,磷酸铁深灰色Me①,磷酸铁及铁的氧化物膜层为(0.1~1)g∕m2时呈彩虹色,大于1g∕m2时呈深灰色13.2.2磷化膜成膜的机理比如我们锌系磷化为例来说明磷化膜成膜机理,磷酸锌系处理溶液,通常含有磷酸、磷酸二氢锌、氧化剂和促进剂等成分,其磷化基本反应如下:Fe+2H3PO4——>Fe(H2PO4)2+2H+(基体)(磷化液)2H++02——>H20(氧化剂)Fe(H2PO4)2+02——»FeP04+H3PO4+H20(氧化剂)(沉淀)当铁与磷化液接触时,铁不断溶解,H3PO4不断消耗,并放出氢,这时铁与磷化液接触的界面处的酸度下降,PH值上升,处理液中成分发生下列反应:3Zn(H2PO4)2+4H2O——>Zn3(PO4)2∙4H20+4H3PO4(磷化液)(膜的成分)Fe+2Zn(H2PO4)2+4H2O+02——>Z∩2Fe(PO4)2∙4H20+2H3PO4+H20 (磷化液)(膜的成分)生成的不溶于水的Zn3(PO4)2∙4H20及Zn2Fe(PO4)2∙4H20覆盖在金属表面上即形成了磷化膜。
磷化处理工艺

磷化处理工艺关于磷化处理工艺1 防锈磷化工艺磷化工艺的早期应用是防锈,钢铁件经磷化处理形成一层磷化膜,起到防锈作用。
经过磷化防锈处理的工件防锈期可达几个月甚至几年(对涂油工件而言),广泛用于工序间、运输、包装贮存及使用过程中的防锈,防锈磷化主要有铁系磷化、锌系磷化、锰系磷化三大品种。
铁系磷化的主体槽液成分是磷酸亚铁溶液,不含氧化类促进剂,并且有高游离酸度。
这种铁系磷化处理温度高于9 5℃,处理时间长达30min以上,磷化膜重大于10g/m2,并且有除锈和磷化双重功能。
这种高温铁系磷化由于磷化速度太慢,现在应用很少。
锰系磷化用作防锈磷化具有最佳性能,磷化膜微观结构呈颗粒密堆集状,是应用最为广泛的防锈磷化。
加与不加促进剂均可,如果加入硝酸盐或硝基胍促进剂可加快磷化成膜速度。
通常处理温度80~100℃,处理时间10~20min,膜重在7.5克/m2以上。
锌系磷化也是广泛应用的一种防锈磷化,通常采用硝酸盐作为促进剂,处理温度80~90℃,处理时间10~15min,磷化膜重大于7.5g/m2,磷化膜微观结构一般是针片紧密堆集型。
防锈磷化一般工艺流程:除油除锈——水清洗——表面调整活化——磷化——水清洗——铬酸盐处理——烘干——涂油脂或染色处理通过强碱强酸处理过的工件会导致磷化膜粗化现象,采用表面调整活化可细化晶粒。
锌系磷化可采用草酸、胶体钛表调。
锰系磷化可采用不溶性磷酸锰悬浮液活化。
铁系磷化一般不需要调整活化处理。
磷化后的工件经铬酸盐封闭可大幅度提高防锈性,如再经过涂油或染色处理可将防锈性提高几位甚至几十倍,见表1。
表1 磷化膜与涂油复合对耐蚀性的影响出现锈蚀时间(h)(盐雾你发的这个词被禁止发行B117-64)材料 出现锈蚀时间(0.5 裸钢 0.5 15.0 钢+涂油 15.0 4.0 钢+16g/m2锌磷化 4.0 550.0 钢+锌磷化+涂油 550.0 摘自Freeman D B.Phosphating and Metal Pretreatment Woodhead-Faukner,1986. 2 耐磨减摩润滑磷化工艺对于发动机活塞环、齿轮、制冷压缩机一类工件,它不仅承受一次载荷,而且还有运动摩擦,要求工件能减摩、耐摩。
磷化线的介绍

磷化线的介绍全文共四篇示例,供读者参考第一篇示例:磷化线是一种常用的冶金工艺,在金属表面对磷进行热处理,使其与金属表面反应生成合金化合物,从而提高金属的表面硬度、耐磨性和耐腐蚀性的一种工艺。
磷化线的工艺过程简单,成本低廉,广泛应用于汽车、航空航天、电子、机械制造等领域。
磷化线的工艺流程包括清洗、脱脂、酸洗、磷化、中和和干燥等步骤。
待磷化的金属件需要经过清洗和脱脂处理,去除表面的油污和杂质,以保证磷化效果。
然后将金属件放入酸洗槽中进行酸洗处理,去除金属表面的氧化物和锈蚀层。
接着,将金属件浸入磷化槽中,与含磷化剂的溶液进行反应,生成磷化层。
磷化过程中,金属表面的铁原子与磷元素形成化合物,提高了金属的表面硬度和耐腐蚀性。
磷化完成后,金属件需要经过中和和干燥处理,最终得到具有优良性能的磷化金属件。
磷化线处理后的金属件表面光泽度高,颜色均匀,具有较好的抗氧化性和耐酸碱性。
磷化层可以有效防止金属表面的腐蚀和磨损,延长金属件的使用寿命。
磷化线处理后的金属件还具有良好的润滑性能,适用于需要经常移动或摩擦的零件。
磷化线广泛应用于汽车制造领域,如发动机缸套、连杆、曲轴、传动轴等零部件的表面处理。
磷化后的汽车零部件表面硬度高,耐磨性好,可有效减少零部件在使用过程中的磨损和损坏,提高汽车的整体性能和可靠性。
磷化线还用于航空航天领域的航空发动机零部件、轴承、涡轮叶片等的表面处理,提高零部件的耐高温、耐腐蚀性能,确保航空器的安全性和可靠性。
磷化线是一种简单、经济实用的金属表面处理工艺,具有显著的提高金属表面性能和使用寿命的优势。
随着科技的发展和工业的进步,磷化线的应用领域将不断扩大,为各行业的发展提供更多的可能性和保障。
第二篇示例:磷化线是一种常见的材料表面处理技术,通过在金属表面形成一层富含磷的化合物,以提高金属件的耐腐蚀性、耐磨性和耐热性等性能。
磷化线广泛应用于汽车、航空航天、机械制造等领域,其工艺简单、成本低廉,效果显著,受到广泛关注和应用。
酸洗磷化工艺
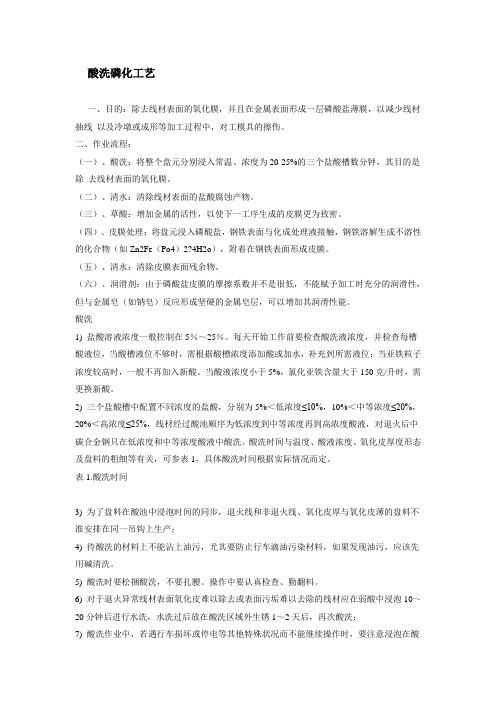
酸洗磷化工艺一、目的:除去线材表面的氧化膜,并且在金属表面形成一层磷酸盐薄膜,以减少线材抽线以及冷墩或成形等加工过程中,对工模具的擦伤。
二、作业流程:(一)、酸洗:将整个盘元分别浸入常温、浓度为20-25%的三个盐酸槽数分钟,其目的是除去线材表面的氧化膜。
(二)、清水:清除线材表面的盐酸腐蚀产物。
(三)、草酸:增加金属的活性,以使下一工序生成的皮膜更为致密。
(四)、皮膜处理:将盘元浸入磷酸盐,钢铁表面与化成处理液接触,钢铁溶解生成不溶性的化合物(如Zn2Fe(Po4)2?4H2o),附着在钢铁表面形成皮膜。
(五)、清水:清除皮膜表面残余物。
(六)、润滑剂:由于磷酸盐皮膜的摩擦系数并不是很低,不能赋予加工时充分的润滑性,但与金属皂(如钠皂)反应形成坚硬的金属皂层,可以增加其润滑性能。
酸洗1) 盐酸溶液浓度一般控制在5%~25%。
每天开始工作前要检查酸洗液浓度,并检查每槽酸液位,当酸槽液位不够时,需根据酸槽浓度添加酸或加水,补充到所需液位;当亚铁粒子浓度较高时,一般不再加入新酸。
当酸液浓度小于5%,氯化亚铁含量大于150克/升时,需更换新酸。
2) 三个盐酸槽中配置不同浓度的盐酸,分别为5%<低浓度≤10%,10%<中等浓度≤20%,20%<高浓度≤25%,线材经过酸池顺序为低浓度到中等浓度再到高浓度酸液,对退火后中碳合金钢只在低浓度和中等浓度酸液中酸洗。
酸洗时间与温度、酸液浓度、氧化皮厚度形态及盘料的粗细等有关,可参表1,具体酸洗时间根据实际情况而定。
表1.酸洗时间3) 为了盘料在酸池中浸泡时间的同步,退火线和非退火线、氧化皮厚与氧化皮薄的盘料不准安排在同一吊钩上生产;4) 待酸洗的材料上不能沾上油污,尤其要防止行车滴油污染材料,如果发现油污,应该先用碱清洗。
5) 酸洗时要松捆酸洗,不要扎腰。
操作中要认真检查、勤翻料。
6) 对于退火异常线材表面氧化皮难以除去或表面污垢难以去除的线材应在弱酸中浸泡10~20分钟后进行水洗,水洗过后放在酸洗区域外生锈1~2天后,再次酸洗;7) 酸洗作业中,若遇行车损坏或停电等其他特殊状况而不能继续操作时,要注意浸泡在酸中线材的品质,并向主管反映处理。
磷化工艺流程

总述:磷化是一种化学与电化学反应形成磷酸盐化学转化膜的过程,所形成的磷酸盐转化膜称之为磷化膜。
磷化的目的主要是:给基体金属提供保护,在一定程度上防止金属被腐蚀;用于涂漆前打底,提高漆膜层的附着力与防腐蚀能力;在金属冷加工工艺中起减摩润滑使用。
磷化处理工艺应用于工业己有90多年的历史,大致可以分为三个时期:奠定磷化技术基础时期、磷化技术迅速发展时期和广泛应用时期。
(二)磷化是常用的前处理技术,原理上应属于化学转换膜处理,主要应用于钢铁表面磷化,有色金属(如铝、锌)件也可应用磷化。
(三)磷化基础知识磷化原理1、磷化工件(钢铁或铝、锌件)浸入磷化液(某些酸式磷酸盐为主的溶液),在表面沉积形成一层不溶于水的结晶型磷酸盐转换膜的过程,称之为磷化。
磷化分类1、按磷化处理温度分类(1)高温型80—90℃处理时间为10-20分钟,形成磷化膜厚达10-30g/m2,溶液游离酸度与总酸度的比值为1:(7-8)优点:膜抗蚀力强,结合力好。
缺点:加温时间长,溶液挥发量大,能耗大,磷化沉积多,游离酸度不稳定,结晶粗细不均匀,已较少应用。
(2)中温型50-75℃,处理时间5-15分钟,磷化膜厚度为1-7 g/m2,溶液游离酸度与总酸度的比值为1:(10-15)优点:游离酸度稳定,易掌握,磷化时间短,生产效率高,耐蚀性与高温磷化膜基本相同,目前应用较多。
(3)低温型30-50℃节省能源,使用方便。
(4)常温型10-40℃常(低)温磷化(除加氧化剂外,还加促进剂),时间10-40分钟,溶液游离酸度与总酸度比值为1:(20-30),膜厚为0.2-7 g/m2。
优点:不需加热,药品消耗少,溶液稳定。
缺点:处理时间长,溶液配制较繁。
3、按磷化处理方法分类(1)化学磷化将工件浸入磷化液中,依靠化学反应来实现磷化,目前应用广泛。
(2)电化学磷化在磷化液中,工件接正极,钢铁接负极进行磷化。
5、按施工方法分类(1)浸渍磷化适用于高、中、低温磷化特点:设备简单,仅需加热槽和相应加热设备,最好用不锈钢或橡胶衬里的槽子,不锈钢加热管道应放在槽两侧。
磷化处理的作用和原理

磷化处理的作用和原理
磷化处理是一种金属表面处理工艺,具有增强表面耐磨抗腐蚀、增加表面硬度、改善
表面光洁度以及增加表面润滑性的效果,广泛应用于冶金、机械、家用电器、汽车及航空
航天等行业。
磷化处理的原理:基于工艺腐蚀原理,通过溶解磷化剂中含磷盐或酸和其他复合磷化剂,将磷元素直接均匀地扩散到金属表面,形成化学而又坚韧的亚氧化磷层,形成抗腐蚀、耐磨、防锈的静电屏蔽层,这就是磷化处理的原理。
1、改善表面形貌:磷化处理可以改善表面的粗糙度、细腻度和硬度,使表面变得更
光滑,从而使表面变得更加美观,而且表面颜色也变得更加鲜艳。
2、增强表面耐磨性:磷化处理可以形成致密的、耐磨的磷化层,由于表面的硬度升高,可以增加金属面在磨损作用下的抗磨性。
3、抗腐蚀性:磷化处理能够形成密闭的磷化层,可以阻止外界污染物进入金属表面,从而大大增强金属表面的耐腐蚀性能。
4、改善润滑性能:磷化熔融润滑性能,可以使成形件的表面光滑,增加润滑剂的粘
附力和滑动性,减少零部件之间的相对运动阻力。
此外,磷化处理还可以抑制金属材料表面氧化,延长金属材料的使用寿命,提高表面
的着色能力等。
纯锰磷化技术原理及应用介绍
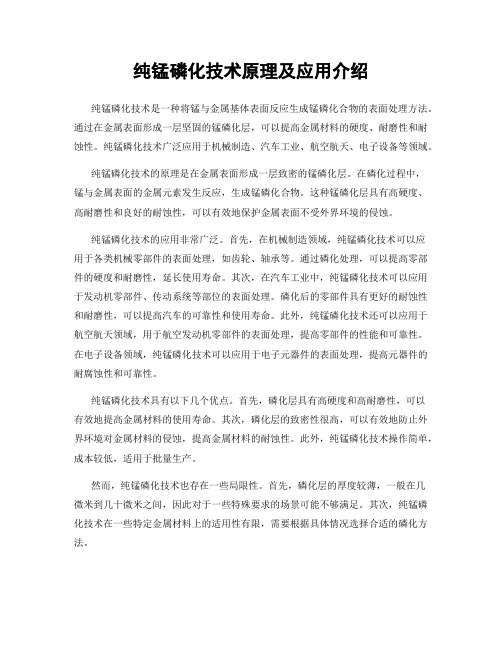
纯锰磷化技术原理及应用介绍纯锰磷化技术是一种将锰与金属基体表面反应生成锰磷化合物的表面处理方法。
通过在金属表面形成一层坚固的锰磷化层,可以提高金属材料的硬度、耐磨性和耐蚀性。
纯锰磷化技术广泛应用于机械制造、汽车工业、航空航天、电子设备等领域。
纯锰磷化技术的原理是在金属表面形成一层致密的锰磷化层。
在磷化过程中,锰与金属表面的金属元素发生反应,生成锰磷化合物。
这种锰磷化层具有高硬度、高耐磨性和良好的耐蚀性,可以有效地保护金属表面不受外界环境的侵蚀。
纯锰磷化技术的应用非常广泛。
首先,在机械制造领域,纯锰磷化技术可以应用于各类机械零部件的表面处理,如齿轮、轴承等。
通过磷化处理,可以提高零部件的硬度和耐磨性,延长使用寿命。
其次,在汽车工业中,纯锰磷化技术可以应用于发动机零部件、传动系统等部位的表面处理。
磷化后的零部件具有更好的耐蚀性和耐磨性,可以提高汽车的可靠性和使用寿命。
此外,纯锰磷化技术还可以应用于航空航天领域,用于航空发动机零部件的表面处理,提高零部件的性能和可靠性。
在电子设备领域,纯锰磷化技术可以应用于电子元器件的表面处理,提高元器件的耐腐蚀性和可靠性。
纯锰磷化技术具有以下几个优点。
首先,磷化层具有高硬度和高耐磨性,可以有效地提高金属材料的使用寿命。
其次,磷化层的致密性很高,可以有效地防止外界环境对金属材料的侵蚀,提高金属材料的耐蚀性。
此外,纯锰磷化技术操作简单,成本较低,适用于批量生产。
然而,纯锰磷化技术也存在一些局限性。
首先,磷化层的厚度较薄,一般在几微米到几十微米之间,因此对于一些特殊要求的场景可能不够满足。
其次,纯锰磷化技术在一些特定金属材料上的适用性有限,需要根据具体情况选择合适的磷化方法。
总结起来,纯锰磷化技术是一种通过在金属表面形成锰磷化层来提高金属材料性能的表面处理方法。
它在机械制造、汽车工业、航空航天、电子设备等领域都有广泛的应用。
纯锰磷化技术具有高硬度、高耐磨性和良好的耐蚀性等优点,但也存在一些局限性。
浅析凸轮轴磷化工艺

将钢铁零件在含有锰、铁、锌的磷酸盐溶液中进行化学处理,使其表面生成一层难溶于水的磷酸盐保护膜的方法称为磷化处理。
磷化处理方法有高温、中温和低温。
中温和低温磷化形成的磷化膜较薄,达不到对在严酷环境下工作的发动机零部件的指标要求,且减摩性、耐热性和结合力也差,而高温磷化能获得耐蚀性、耐磨性、耐热性、结合力及硬度均较高的磷化膜,本文中介绍的凸轮轴磷化方法即为高温磷化。
我公司在发动机下线磨合过程中发现,凸轮轴的凸轮存在严重早期磨损,需要重新更换凸轮轴,严重影响了发动机的交付,并造成了成本的增加。
借鉴其他发动机工厂的经验,在凸轮轴加工工艺中增加磨削后磷化工艺,在凸轮表面形成一层磷化膜,该磷化膜能够防止摩擦部位表面的金属之间的接触,减小与其他摩擦副的摩擦力,并能够储存润滑油,形成油膜,改善磨合性能。
1磷化溶液的配制1.1脱脂液(按1000L计)①加清水至处理槽的80%,加温至约40℃;慢慢加入20kg FC-4423T,边搅拌边溶解;加入清水至1000L;加热至规定的处理温度,再确认游离碱度。
②处理条件:碱度:11.0-13.0pt温度:45-55℃时间:2min以上③碱度测定:取10ml工作液放入三角烧杯中,加3~5滴酚酞,用0.1N H2SO4滴定,至粉红色消失为止,此时消耗酸的ml数即碱度pt数。
④补充和调整:(1000L)由于连续处理过程中浓度不断变化,需要定期测定浓度,使其保持在规定范围内。
一般为了使游离碱度上升1pt,补加1.8kg FC-4423T。
处理液经过长时间使用,液体就会变脏,最终脱脂能力降低,以至变为老化状态,即使补充新脱脂剂,也不会起到预期脱脂效果,这就需要废弃老化的处理液,更换新液。
1.2表面调整液(1000L)①将清水加到处理槽的八成,温度升到所定温度;将3kgPL-VMB先溶于60L40℃温水中添加处理槽;然后将3kgPL-VMA剂溶于60L40℃温水后添加处理槽;加水至1000L,彻底搅拌混合均匀。
磷化表面处理
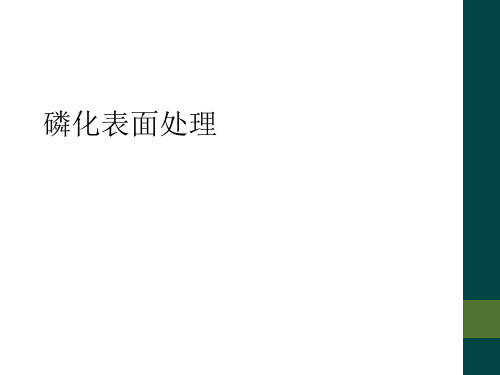
汽车涂装工艺
涂装前表面处理工艺 表面处理是防锈涂装的重要工序之一。工程机械防锈涂装质量在很大程度上取决于表面处理的方式好坏。
据英国帝国化学公司介绍 , 涂层寿命受 3 方面因素制约 : 表面处理 , 占 60%; 涂装施工 , 占 25%; 涂料本身质量 , 占 15% 。 工程机械行业 , 不同零部件的表面处理方式。 机械清理可有效去除工件上的铁锈、焊渣、氧化皮 , 消除焊 接应力 , 增加防锈涂膜与金属基体的结合力 , 从而大大提高工程机械零部件的防锈质量。机械清理标准要求达到 的Sa2 . 5 级。表面粗糙度要达到防锈涂层厚度的 1 /3 。喷、抛丸所用钢丸要达到 GB6484 要求。 薄板冲压件的表 面处理称一般用化学表面处理。
磷化表面处理
汽车涂装工艺
汽车涂装工艺,一般可分为两大部分:一是涂装前金属的表面处理,也叫前处理技术;二是涂装的施工工艺。 表面处理主要包括清除工件表面的油污、尘土、锈蚀、以及进行修补作业时旧涂料层的清除等,以改善工件的 表面状态。包括根据各种具体情况对工件表面进行机械加工和化学处理,如磷化、氧化和钝化处理。
磷化后处理
为了提高磷化膜的防护能力,磷化后应对磷化膜进行填充和封闭处理。填充处理的工艺是: 重铬酸钾 30~50 g/L 碳酸钠 2~4 g/L 温度 90~98 ℃ 时间 5~10 min
填充后,可以根据需要在锭子油、防锈油或润滑油中进行封闭。如需涂漆,应在钝化处理干燥后进行, 工序间隔不超过24小时。
汽车涂装-磷化处理 涂装前锌盐磷化处理中添加Ni和Mn。添加Ni能使磷化膜结晶细化,提高附着力,提高耐腐蚀性能。
谢谢大家!
磷化处理
四 影响磷化的因素 1 游离酸度 游离酸度是指溶液中磷酸二氢盐水解后产生游离磷酸的浓度。游离酸度过高时,氢气析出量大,晶核生 成困难,膜的晶粒粗大,疏松多孔,耐蚀性差;反之,生成的磷化膜较薄,甚至得不到磷化膜。游离酸度 高时,可加氧化锌或氧化锰调整;当低时,可加磷酸二氢锰铁盐,磷酸二氢锌或磷酸来调整。 2 总酸度 总酸度来源于磷酸盐,硝酸盐和酸的总和。总酸度高时磷化反应快,获得的膜层晶粒细致,但膜层较薄, 耐蚀性降低;总酸度低时,磷化速度慢,膜层厚且粗糙。总酸度高时可加水稀释,低时可加磷酸二氢锰铁 盐,磷酸二氢锌或硝酸锌,硝酸锰来调整。
- 1、下载文档前请自行甄别文档内容的完整性,平台不提供额外的编辑、内容补充、找答案等附加服务。
- 2、"仅部分预览"的文档,不可在线预览部分如存在完整性等问题,可反馈申请退款(可完整预览的文档不适用该条件!)。
- 3、如文档侵犯您的权益,请联系客服反馈,我们会尽快为您处理(人工客服工作时间:9:00-18:30)。
中国制造上汽乘用车临港工厂油漆车间
2013年06月13日 06:54来源:凤凰汽车作者:张佳栋1人参与 1条评论
凤凰汽车特别策划中国自主品牌现在的发展状况如何?如何应对合资品牌的压力?凤凰汽车《中国制造》栏目将走访国内主要的自主品牌汽车制造商,一探它们的生产、生存状况。
上汽乘用车是我们此次走访的第一站,我们的探访,就从上汽乘用车的临港制造基地开始。
上一期由我的同时介绍了上汽临港工厂的车身车间(点击查看),今天将由我继续向大家介绍上汽乘用车临港生产基地的油漆车间,油漆车间最主要执行的就是汽车生产四大工艺中的喷漆工艺,在车身车间完成的车体一系列的清洗、密封以及喷漆工序,为车辆最终的总装打好基础,车辆的颜色在油漆车间也就已经确定了。
上海汽车乘用车公司临港油漆车间,从2006年8月28日打下第一根桩,开始土建。
车间总占地面积为42000平方米,项目共投资5.2亿元,由机械工业第四设计院完成设计、施工。
设计最大产能为单班40件/小时,单班年产量8万余辆。
2008年12月实现第一阶段的27件/小时产能要求,2009年8月达到40件/小时的产能要求,2010年2月开始两班生产。
目前主要生产的车型为荣威550、MG6、MG3以及荣威950。
油漆车间是整个工厂中最洁净的地方,拥有大量密封进行自动化操作的工段,车间内的工作地点均具有良好的空气循环,各工位对烟雾、粉尘和其它污秽空气的控制都有极高的要求,必要时随时进行净化处理。
在进入车间是必须穿着专业防护服装并经过除尘、除静电通道,在人工操作区域都保证了充足的照明。
采用天然光照明时,不允许太阳光直接照射工作空间,在室内照度不足的情况下则采用与整体光源色调相一致的局部照明,光线保证均匀且亮度一直,从而保证车辆的细节都可完整、真实地呈现。
随时对员工通道进行清洁,进一步防止外界粉尘被带入施工地段。
一方面避免或减少人身伤害和增强职业危害防护,同时也最大限度地保证了车辆喷漆的质量和效果。
电泳、磷化、中涂、色漆喷涂以及清漆喷涂等每一道工序都对车辆防腐、车身保护以及最终车漆的呈现效果有至关重要的影响。
上汽油漆车间的工艺流程完整,不会因控制成本等
原因而在生产流程上有丝毫简化,最大限度为最终提供更消费者的车辆保证了扎实的基
在车身车间完成焊接的车体经白车身车体分配中心分配,从通道进入油漆车间。
首先进行预处理,对车辆进行清洁,为正式的油漆工序做准备。
使用热水清洗车身的效果比常温水更好,脱脂水洗是采用碱性溶液或有机溶剂等靠皂化、乳化作用或浸透溶解除去金属工件表面的油污,常见的脱脂方法有碱液清洗、有机溶剂
脱脂、表面活性剂、乳化剂脱脂、电化学除油。
经过洗涤和脱脂并烘干后,对车体进行表调。
该工段表调的目的是促使磷化形成晶粒细致密实的磷化膜以及提高磷化反应速度。
钢铁件在含有锌、锰、铁的磷酸盐溶液中经过化学处理,在其表面形成一层难溶于水的磷酸盐保护膜,这个化学处理过程称为磷化。
磷化的目的主要是给基体金属提供保护,在一定程度上防止金属被腐蚀,用于涂装前打底,提高漆膜层的附着力和防腐蚀能力。
磷化处理方式有喷淋式、浸渍式和喷浸结合式三种。
喷淋处理方式所得磷化膜的磷酸锌的含量高、结晶成针状且粗;浸渍处理方式所得的磷酸二锌铁含量高、结晶成粒状其致密,其耐蚀性和涂膜附着力好。
上汽油漆车间采用的是喷浸结合式的处理工序,效果最佳。
电泳涂装是把工件和对应的电极放入水溶性涂料中,接上电源后依靠电场所产生的物理化学作用,使涂料中的树脂、颜填料在以被涂物为电极的表面上均匀析出沉积形成不溶于水的漆膜的一种涂装方法。
上汽采用水溶、无铅电泳,无铬钝化工艺,减少重金属的排放,在环保方面起到了重要作用。
电泳涂装具有很多一般涂装工序所不具备的优势:采用水溶性涂料,以水为溶解介质,节省了大量有机溶剂,大大降低了大气污染和环境危害,安全卫生,同时避免了火灾的隐患;
涂装效率高、涂料损失小,涂料的利用率可达90%-95%;涂膜厚度均匀、附着力强、涂装质量好,工件各个部位如内层、凹陷、焊缝等处都能获得均匀、平滑的漆膜,解决了其他涂装方法对复杂形状工件的涂装难题;生产效率高、施工可实现自动化连续生产、大大提高劳动效率。
底部密封涂胶是目前部分厂商或车型由于种种原因而略过的环节,由于该工序主要在车底实施,一般消费者在选车时也容易被忽略。
上汽所有车型的生产都将该工序完整保留。
底部密封涂胶的作用:提高车身底板的耐腐蚀性;对外来冲击具有缓冲作用;防止由发动机、路面接触和车身振动产生的噪音;绝热作用;对焊接和铆接处间隙和凹坑起到密封胶的作用等。
底部密封涂胶一般涂在车身的挡泥板内部、车轮罩内部、发动机罩内部底板、下纵梁等部位,上汽采用底部密封机器人自动喷涂,由于该工序在总装前完成,覆盖率及喷涂效果远比购车后的底盘装甲施工要全面得多。
密封胶涂于车身须防止水渗入的部位,主要功能是防止焊缝渗水透气、提高车身的耐腐蚀性和密封性。
密封胶烘干后应具有弹性和良好的附着力,使其受振动时不开裂或脱落。
中涂能够填充电泳漆表面,改善被涂物表面平整度和光滑度,以提高涂膜的丰满度和鲜映性。
由于中涂的漆面厚度较大,还可以达到防石击的作用,同时具有一定的耐热和紫外线隔绝性,也在一定程度上保护了电泳底漆。
常用的有手工喷涂、自动喷涂或静电喷涂等工艺方法。
中涂能够填充电泳漆表面,改善被涂物表面平整度和光滑度,以提高涂膜的丰满度和鲜映性。
由于中涂的漆面厚度较大,还可以达到防石击的作用,同时具有一定的耐热和紫外线
隔绝性,也在一定程度上保护了电泳底漆。
经过中涂、烘干后还需进行中涂大漠,在去除前道工序产生的颗粒、流挂、缩孔等缺陷后,还可提升涂层间的附着力,为接下来的面漆喷涂做准备。
面漆涂装是对车体外板的装饰和保护。
装饰性赋予汽车更漂亮、更豪华、更庄重的外观;而保护性则是需要面漆膜不仅对中涂层和电泳底漆膜保护作用,而且本身也具有保色性、耐候性、耐污染性、抗划伤性、耐酸雨性等高功能性,才能保护自身。
在色漆喷涂完成后,还会经过表面清漆喷涂,一方面在色漆上增加了保护层,另一方面也进一步提升了车漆的光泽感,提升了车辆的品质和档次。
最终经过车漆的精饰后进入报交流程,在专业的观察车间经检测人员对车辆漆面的平整度、光泽度、均匀度等细节完成验收后,不合格的产品会下线进行调整,而合格的车身则会经过注蜡处理,通过油漆车身车体分配中心送往总装车间。
在后续的文章中,我会为大家详细介绍上汽总装车间的生产流程。