甲醇制烯烃技术报告(非常好)
mto烯烃分离

mto烯烃分离
摘要:
1.介绍MTO 烯烃分离技术
2.MTO 烯烃分离技术的应用领域
3.MTO 烯烃分离技术的优势与不足
4.我国在MTO 烯烃分离技术方面的发展
正文:
MTO 烯烃分离技术,即甲醇制烯烃分离技术,是一种将甲醇转化为乙烯和丙烯等烯烃的先进技术。
这种技术广泛应用于石油化工、煤化工、精细化工等领域,为我国的石油替代和能源转型战略提供了重要支撑。
MTO 烯烃分离技术的应用领域主要体现在以下几个方面:一是石油替代,通过MTO 技术将甲醇转化为乙烯和丙烯,可以降低对石油资源的依赖;二是能源转型,MTO 技术可以将煤炭等非石油资源高效转化为烯烃,有助于实现能源结构的转型;三是精细化工,MTO 技术可以提供高纯度的烯烃,满足精细化工行业的需求。
MTO 烯烃分离技术虽然具有很多优势,但也存在一些不足。
首先,MTO 技术对甲醇的转化率较低,一般仅为50%-60%,存在较大的提升空间;其次,MTO 技术对催化剂的选择性要求较高,催化剂的研发和更换成本较高;最后,MTO 技术对设备的要求较高,设备的投入成本较大。
我国在MTO 烯烃分离技术方面的发展取得了一定的成绩。
我国已经成功研发出多种MTO 技术,包括传统的液相法和先进的气相法等,为我国的烯烃
供应提供了重要保障。
同时,我国在MTO 技术的催化剂研发、设备制造等方面也取得了重要进展,大大提高了MTO 技术的转化率和经济效益。
甲醇制烯烃生产工艺

甲醇制烯烃生产工艺甲醇制烯烃是将甲醇转化为烯烃的一种工艺。
烯烃是一类重要的有机化工原料,广泛应用于合成塑料、橡胶、纤维等领域。
以下将介绍甲醇制烯烃的生产工艺。
首先,甲醇制烯烃的关键步骤是通过甲醇脱氢反应生成烯烃。
脱氢反应通常在催化剂存在下进行。
常用的催化剂包括氧化铜-锌(Cu-Zn-O)催化剂、模型选区氧化镁(MOx)催化剂和氧化铝(Al2O3)载体上的甲醇蒸汽重整催化剂等。
甲醇脱氢反应的条件是高温和低压。
通常反应温度在400℃~600℃之间,反应压力在0.1~1.0 MPa之间。
在这些条件下,甲醇分子发生脱氢反应,生成一氧化碳和氢气,同时还会生成一系列的烯烃产物。
接下来,脱氢反应产生的一氧化碳和氢气需要进行增氢反应才能转化为烯烃。
增氢反应通常在氧化铝载体上的催化剂存在下进行。
常用的催化剂有氧化镁(MOx)和氧化铝(Al2O3)催化剂等。
增氢反应的条件是中温和中压。
一氧化碳和氢气在催化剂上发生增氢反应,生成了一系列的烯烃产品。
这些烯烃产品可通过分离和精馏等方式得到纯度较高的产物。
甲醇制烯烃最大的难点是选择合适的催化剂和控制反应条件。
对于不同类型的催化剂,需要探索合适的反应温度、压力和甲醇的进料速率等工艺参数,以达到最佳的反应效果和产物选择性。
甲醇制烯烃的生产工艺还面临着一些挑战。
首先,催化剂具有一定的寿命,需要进行周期性的再生和更换;其次,反应过程中会生成一些副产物,如甲烷、乙烷等,需要通过后续的处理步骤进行处理。
此外,甲醇制烯烃是一个高温、高压的反应过程,对设备和安全管理提出了更高的要求。
总之,甲醇制烯烃是一种重要的有机合成工艺,可以将甲醇转化为烯烃原料。
通过选择合适的催化剂和控制反应条件,可以实现高效、高选择性的烯烃产物得到。
这种工艺的应用在化工行业具有广阔的前景。
甲醇制烯烃技术分析

甲醇制烯烃技术分析发布时间:2021-08-24T16:45:48.730Z 来源:《建筑科技信息》2020年13期作者:宋垚[导读] 本文主要阐述了甲醇制低碳烯烃各个工艺的研究进展。
摘要:甲醇制低碳烯烃核心在于甲醇转化催化剂的研发,煤通过气化、净化、合成制得甲醇,以甲醇为原料,选取ZSM-5或者SAPO-34分子筛催化剂,在特定的反应器中反应制取低碳烯烃。
根据产物种类的不同,大致可以分为甲醇制乙烯(MTO)技术,甲醇制丙烯(MTP)技术以及甲醇制丁烯(CMTX)技术。
本文主要阐述了甲醇制低碳烯烃各个工艺的研究进展。
关键词:甲醇;制烯烃;技术一、甲醇制烯烃技术借助煤资源来获得低碳烯烃的过程如下:首先采取措施实现煤的气化,继而将其转化得到合成气。
事实上,甲醇就是借助以上操作得到的。
至于低碳烯烃的获取,就是由甲醇的提取转化得来的。
这种制作低碳烯烃的技术,在我国已经属于较为娴熟的技术工艺了。
然而其中的甲醇制烯烃技术正是其中的重要环节,但就这一技术而言我国的技术研发仍有待提升。
二、甲醇制乙烯技术2.1UOP/NorskHydro的MTO技术 UoP/NorskHydro的MTO工艺可以加工各种规格甲醇原料,以SAPO-34分子筛为催化剂,小试结果为甲醇转化率100%,双烯选择性大于80%,乙烯与丙烯比可在1.5—0.75内调节。
2.2中国科学院大连化学物理研究所DMTO技术 20世纪80年代,中国科学院大连化学物理研究所开始进行甲醇制低碳烯烃研究,最初采用中孔ZSM-5沸石催化剂完成年产300t装置固定床中试,鉴于固定床反应器催化剂的再生方式和取热等问题,90年代又开始了流化床技术的开发,以SAPO-34分子筛为催化剂,先后开发了合成气经二甲醚制低碳烯烃(SDTO)技术和甲醇经二甲醚中间产物制低碳烯烃(DMTO)技术。
2005年,中国科学院大连化学物理研究所、中国石化洛阳工程设计有限公司、陕西新兴煤化工科技有限公司开始进行万吨级DMTO工业化试验。
中科院科技成果——甲醇制取低碳烯烃(DMTO)技术
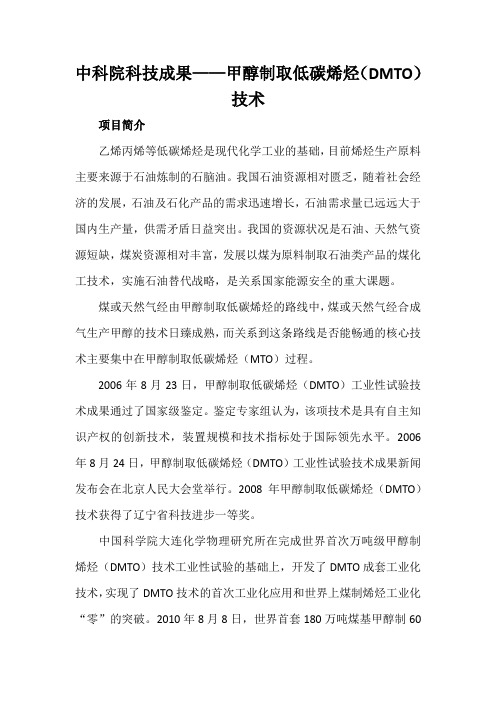
中科院科技成果——甲醇制取低碳烯烃(DMTO)技术项目简介乙烯丙烯等低碳烯烃是现代化学工业的基础,目前烯烃生产原料主要来源于石油炼制的石脑油。
我国石油资源相对匮乏,随着社会经济的发展,石油及石化产品的需求迅速增长,石油需求量已远远大于国内生产量,供需矛盾日益突出。
我国的资源状况是石油、天然气资源短缺,煤炭资源相对丰富,发展以煤为原料制取石油类产品的煤化工技术,实施石油替代战略,是关系国家能源安全的重大课题。
煤或天然气经由甲醇制取低碳烯烃的路线中,煤或天然气经合成气生产甲醇的技术日臻成熟,而关系到这条路线是否能畅通的核心技术主要集中在甲醇制取低碳烯烃(MTO)过程。
2006年8月23日,甲醇制取低碳烯烃(DMTO)工业性试验技术成果通过了国家级鉴定。
鉴定专家组认为,该项技术是具有自主知识产权的创新技术,装置规模和技术指标处于国际领先水平。
2006年8月24日,甲醇制取低碳烯烃(DMTO)工业性试验技术成果新闻发布会在北京人民大会堂举行。
2008年甲醇制取低碳烯烃(DMTO)技术获得了辽宁省科技进步一等奖。
中国科学院大连化学物理研究所在完成世界首次万吨级甲醇制烯烃(DMTO)技术工业性试验的基础上,开发了DMTO成套工业化技术,实现了DMTO技术的首次工业化应用和世界上煤制烯烃工业化“零”的突破。
2010年8月8日,世界首套180万吨煤基甲醇制60万吨烯烃装置投料试车一次成功,2011年1月进入商业化运营阶段,创造了巨大的经济效益和社会效益。
“十二五”期间,DMTO技术推广取得了显著成绩,技术已经许可20套工业化装置,烯烃产能1126万吨/年,预计拉动投资2500亿元。
截至目前,已有9套工业装置成功投产,烯烃产能达520万吨/年,新增产值约600亿元/年。
在成功开发甲醇制烯烃工业化技术的基础上,大连化物所又与合作伙伴联合进行了新一代甲醇制取低碳烯烃(DMTO-II)技术的研究开发。
DMTO-II技术是在DMTO技术的基础上将甲醇制烯烃产物中的C4+组分回炼,使乙烯、丙烯收率提高10%以上,实现多产烯烃的新一代工艺技术。
甲醇制烯烃技术进展及评价
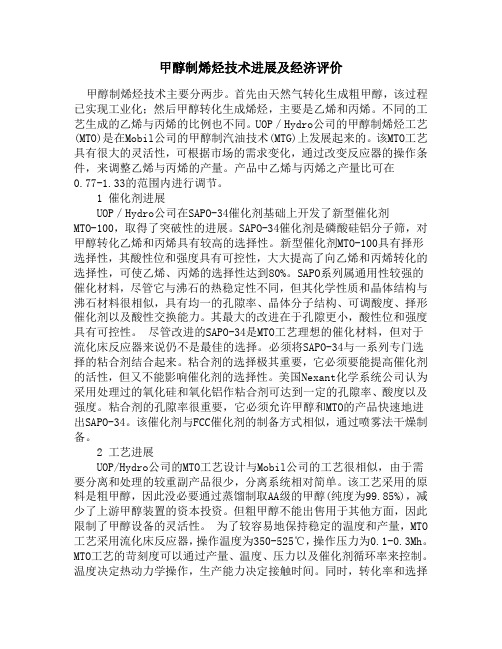
甲醇制烯烃技术进展及经济评价甲醇制烯烃技术主要分两步。
首先由天然气转化生成粗甲醇,该过程已实现工业化;然后甲醇转化生成烯烃,主要是乙烯和丙烯。
不同的工艺生成的乙烯与丙烯的比例也不同。
UOP/Hydro公司的甲醇制烯烃工艺(MTO)是在Mobil公司的甲醇制汽油技术(MTG)上发展起来的。
该MTO工艺具有很大的灵活性,可根据市场的需求变化,通过改变反应器的操作条件,来调整乙烯与丙烯的产量。
产品中乙烯与丙烯之产量比可在0.77-1.33的范围内进行调节。
1 催化剂进展UOP/Hydro公司在SAPO-34催化剂基础上开发了新型催化剂MTO-100,取得了突破性的进展。
SAPO-34催化剂是磷酸硅铝分子筛,对甲醇转化乙烯和丙烯具有较高的选择性。
新型催化剂MTO-100具有择形选择性,其酸性位和强度具有可控性,大大提高了向乙烯和丙烯转化的选择性,可使乙烯、丙烯的选择性达到80%。
SAPO系列属通用性较强的催化材料,尽管它与沸石的热稳定性不同,但其化学性质和晶体结构与沸石材料很相似,具有均一的孔隙率、晶体分子结构、可调酸度、择形催化剂以及酸性交换能力。
其最大的改进在于孔隙更小,酸性位和强度具有可控性。
尽管改进的SAPO-34是MTO工艺理想的催化材料,但对于流化床反应器来说仍不是最佳的选择。
必须将SAPO-34与一系列专门选择的粘合剂结合起来。
粘合剂的选择极其重要,它必须要能提高催化剂的活性,但又不能影响催化剂的选择性。
美国Nexant化学系统公司认为采用处理过的氧化硅和氧化铝作粘合剂可达到一定的孔隙率、酸度以及强度。
粘合剂的孔隙率很重要,它必须允许甲醇和MTO的产品快速地进出SAPO-34。
该催化剂与FCC催化剂的制备方式相似,通过喷雾法干燥制备。
2 工艺进展UOP/Hydro公司的MTO工艺设计与Mobil公司的工艺很相似,由于需要分离和处理的较重副产品很少,分离系统相对简单。
该工艺采用的原料是粗甲醇,因此没必要通过蒸馏制取AA级的甲醇(纯度为99.85%),减少了上游甲醇装置的资本投资。
甲醇制烯烃的几种技术分析

出 甲 醇 法 的 是 Mo b i l ( 美 孚) 公司, 接着埃克森公 司 、 巴斯 夫 公 司 、
烯、 丙烯 以及 乙烯 能 够 达 到 大约 9 7 %的选 择 性 [ 3 】 。 通 过 三 乙胺 和 艺 中, 丙烯 和 乙烯 所 占 的 比例 各有 不 同 。将 天 然 气用 来 生 成 烯 烃 氟 化 物 制 取 出 较 高活 性 的 S A P O -3 4类 型 的 催 化 剂 。 该 化 工 研 究 主要 包 含 了 3种 工艺 技 术 , 主 要 包 括 甲烷 氧 化 偶 联 法 、 费 一 托 合 所 利 用 相 关 的催 化 剂 能 够 确 保 在 循 环 流 化 床 进 行 超 过 两 千 小 时 成 法 以 及最 常使 用 的 甲 醇 法[ 1 1 。ቤተ መጻሕፍቲ ባይዱ甲醇 法 主 要 是 通 过将 合 成 气 与 的运 作 周 期 , 该工艺具有大于 8 0 % 的丙 烯 及 乙烯 的选 择 性 . 甲 醇 甲 醇作 用 生 成烯 烃 的 方法 ,这 一 技 术 为 当前 制 取 烯 烃 工 艺 中 最 保 持 了高 于 9 9 . 8 %的 转化 效 率 。 具 现代 化 条 件 的 技 术 之一 。 2 . 甲醇 制低 碳 烯 烃 ( DMT O1 的工 艺探 究
1 . 甲醇 制烯 烃( S MT O) 的 工 艺探 究
中石 化 工 集 团 中的 上 海 研 究 院 是 较 早 进 行 甲醇 制 烯 烃 工 艺 研 发 的部 门 之 一 。其 主要 是 通 过 晶 化液 内添 人 锌 盐 , 该 研 究 院 成 功制取 Z n S A P O 一 3 4的特 殊 类 型 催 化 剂 ,在 这 一 实 验 过 程 中 , 丁
甲醇制烯烃实习报告

一、实习背景随着我国经济的快速发展和化学工业的持续增长,对低碳烯烃的需求日益增加。
甲醇制烯烃(MTO/MTP)技术作为一种以煤或天然气合成的甲醇为原料,生产乙烯、丙烯等低碳烯烃的重要化工技术,在我国具有广阔的发展前景。
为了深入了解这一先进技术,我于2023年在某化工企业进行了为期一个月的实习。
二、实习内容1. 甲醇制烯烃技术简介甲醇制烯烃技术是指以甲醇为原料,通过催化反应生产乙烯、丙烯等低碳烯烃的过程。
该技术主要包括MTO(甲醇制乙烯)和MTP(甲醇制丙烯)两种工艺。
MTO工艺以煤或天然气合成的甲醇为原料,借助流化床反应形式生产乙烯;MTP工艺则以甲醇为原料,生产丙烯。
2. 实习过程(1)参观生产现场实习期间,我参观了甲醇制烯烃生产现场,了解了整个生产流程。
从甲醇的合成、储存、输送,到催化反应、烯烃的分离和提纯,每一个环节都给我留下了深刻的印象。
(2)学习催化反应原理在导师的指导下,我学习了甲醇制烯烃催化反应的原理。
了解到ZSM-5催化剂在MTO工艺中的重要作用,以及反应条件对产率和选择性的影响。
(3)操作模拟装置为了更好地掌握甲醇制烯烃工艺,我参与了模拟装置的操作。
通过模拟实验,我了解了反应过程中的温度、压力、空速等参数对反应的影响,以及如何调整参数以获得最佳产率。
(4)数据分析与处理在实习过程中,我收集了大量的生产数据,并对其进行了分析处理。
通过对比不同反应条件下的产率和选择性,我发现了一些规律,为生产优化提供了依据。
三、实习收获1. 理论知识与实践相结合通过这次实习,我将所学的理论知识与实际生产相结合,加深了对甲醇制烯烃技术的理解。
掌握了MTO/MTP工艺的基本原理、操作流程和影响因素。
2. 提高了动手能力在实习过程中,我参与了模拟装置的操作,锻炼了我的动手能力。
学会了如何调整反应条件、处理实验数据,为今后从事相关工作打下了基础。
3. 拓宽了视野通过参观生产现场和与工程师交流,我了解了甲醇制烯烃行业的发展现状和趋势,拓宽了视野。
甲醇制烯烃
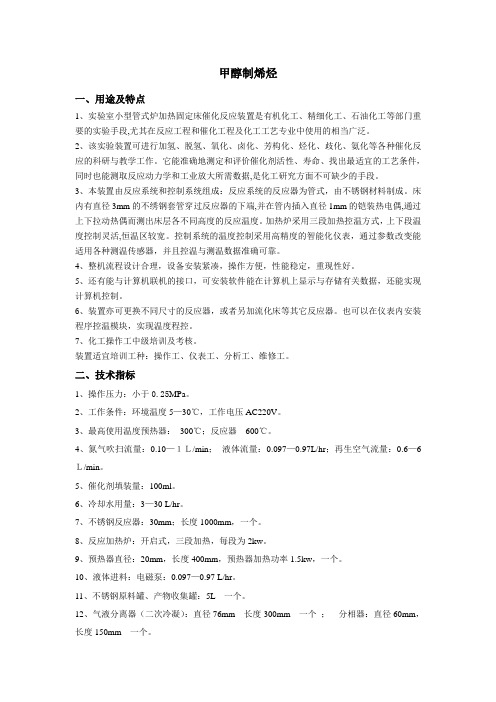
甲醇制烯烃一、用途及特点1、实验室小型管式炉加热固定床催化反应装置是有机化工、精细化工、石油化工等部门重要的实验手段,尤其在反应工程和催化工程及化工工艺专业中使用的相当广泛。
2、该实验装置可进行加氢、脱氢、氧化、卤化、芳构化、烃化、歧化、氨化等各种催化反应的科研与教学工作。
它能准确地测定和评价催化剂活性、寿命、找出最适宜的工艺条件,同时也能测取反应动力学和工业放大所需数据,是化工研究方面不可缺少的手段。
3、本装置由反应系统和控制系统组成:反应系统的反应器为管式,由不锈钢材料制成。
床内有直径3mm的不绣钢套管穿过反应器的下端,并在管内插入直径1mm的铠装热电偶,通过上下拉动热偶而测出床层各不同高度的反应温度。
加热炉采用三段加热控温方式,上下段温度控制灵活,恒温区较宽。
控制系统的温度控制采用高精度的智能化仪表,通过参数改变能适用各种测温传感器,并且控温与测温数据准确可靠。
4、整机流程设计合理,设备安装紧凑,操作方便,性能稳定,重现性好。
5、还有能与计算机联机的接口,可安装软件能在计算机上显示与存储有关数据,还能实现计算机控制。
6、装置亦可更换不同尺寸的反应器,或者另加流化床等其它反应器。
也可以在仪表内安装程序控温模块,实现温度程控。
7、化工操作工中级培训及考核。
装置适宜培训工种:操作工、仪表工、分析工、维修工。
二、技术指标1、操作压力:小于0.25MPa。
2、工作条件:环境温度5—30℃,工作电压AC220V。
3、最高使用温度预热器:300℃;反应器600℃。
4、氮气吹扫流量:0.10—1L/min;液体流量:0.097—0.97L/hr;再生空气流量:0.6—6L/min。
5、催化剂填装量:100ml。
6、冷却水用量:3—30 L/hr。
7、不锈钢反应器:30mm;长度1000mm,一个。
8、反应加热炉:开启式,三段加热,每段为2kw。
9、预热器直径:20mm,长度400mm,预热器加热功率1.5kw,一个。
甲醇制烯烃的总结
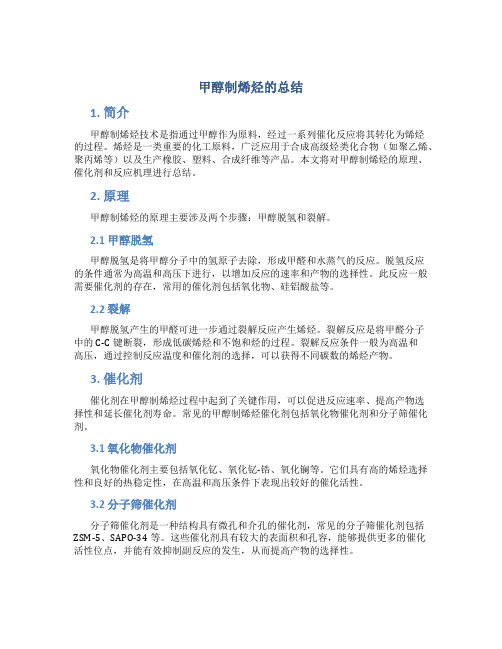
甲醇制烯烃的总结1. 简介甲醇制烯烃技术是指通过甲醇作为原料,经过一系列催化反应将其转化为烯烃的过程。
烯烃是一类重要的化工原料,广泛应用于合成高级烃类化合物(如聚乙烯、聚丙烯等)以及生产橡胶、塑料、合成纤维等产品。
本文将对甲醇制烯烃的原理、催化剂和反应机理进行总结。
2. 原理甲醇制烯烃的原理主要涉及两个步骤:甲醇脱氢和裂解。
2.1 甲醇脱氢甲醇脱氢是将甲醇分子中的氢原子去除,形成甲醛和水蒸气的反应。
脱氢反应的条件通常为高温和高压下进行,以增加反应的速率和产物的选择性。
此反应一般需要催化剂的存在,常用的催化剂包括氧化物、硅铝酸盐等。
2.2 裂解甲醇脱氢产生的甲醛可进一步通过裂解反应产生烯烃。
裂解反应是将甲醛分子中的C-C键断裂,形成低碳烯烃和不饱和烃的过程。
裂解反应条件一般为高温和高压,通过控制反应温度和催化剂的选择,可以获得不同碳数的烯烃产物。
3. 催化剂催化剂在甲醇制烯烃过程中起到了关键作用,可以促进反应速率、提高产物选择性和延长催化剂寿命。
常见的甲醇制烯烃催化剂包括氧化物催化剂和分子筛催化剂。
3.1 氧化物催化剂氧化物催化剂主要包括氧化钇、氧化钇-锆、氧化镧等。
它们具有高的烯烃选择性和良好的热稳定性,在高温和高压条件下表现出较好的催化活性。
3.2 分子筛催化剂分子筛催化剂是一种结构具有微孔和介孔的催化剂,常见的分子筛催化剂包括ZSM-5、SAPO-34等。
这些催化剂具有较大的表面积和孔容,能够提供更多的催化活性位点,并能有效抑制副反应的发生,从而提高产物的选择性。
4. 反应机理甲醇制烯烃反应机理是一个复杂的过程,涉及多个步骤和中间产物。
以下是一种常见的甲醇制烯烃反应机理:1.甲醇脱氢:甲醇在催化剂的作用下脱氢生成甲醛和水蒸气。
2.甲醛裂解:甲醛进一步通过裂解反应,形成C1至C4的低碳烯烃和不饱和烃。
3.低碳烯烃重排:低碳烯烃在催化剂的作用下发生重排反应,形成C5以上的高碳烯烃。
4.高碳烯烃裂解和重排:高碳烯烃在反应中会发生自身的裂解和重排反应,产生更高碳数的烯烃。
甲醇制烯烃调研报告

甲醇制烯烃调研报告
甲醇制烯烃是一种重要的烃类化工原料生产技术,具有较高的经济和环境效益。
本次调研报告主要针对甲醇制烯烃的工艺流程、市场需求和发展前景进行分析。
一、工艺流程
甲醇制烯烃的工艺主要包括甲醇脱水和烯烃合成两个步骤。
甲醇脱水通过高温反应将甲醇分解成甲烷、烯烃和水等组分,再通过分离纯化获得甲烷和烯烃。
烯烃合成主要采用催化剂将甲烷转化成乙烯、丙烯和丁烯等烯烃产品。
二、市场需求
烯烃是石化行业的重要原料,广泛应用于塑料、橡胶、纺织、农药、医药等领域。
随着全球经济的快速发展,对烯烃的需求不断增加。
目前,世界烯烃年需求量已接近1亿吨,市场潜力巨大。
三、发展前景
甲醇制烯烃技术具有成本低、资源丰富、生产效率高等优势,是当前开发利用天然气和煤炭资源的重要途径之一。
随着天然气和煤炭资源的广泛应用,甲醇制烯烃技术将有更广阔的发展空间。
四、面临的挑战
虽然甲醇制烯烃技术具有巨大发展潜力,但面临着一些挑战。
首先是原料选择的问题,目前主要是采用天然气和煤炭作为甲醇制烯烃的原料,但天然气和煤炭资源的可获得性和价格波动
性对生产造成一定影响。
其次是技术难题,包括甲醇脱水和烯烃合成的催化剂研发、反应条件优化、产品纯化等方面存在一定的技术难题。
五、发展建议
为了推动甲醇制烯烃技术的发展,应加强科研力量,加大对催化剂研发和工艺优化的支持。
此外,还应加强产学研合作,建立实验室和企业之间的紧密联系,加快科研成果的转化和应用。
另外,还应注重环保问题,加强废水、废气的处理和利用,实现资源的最大化利用。
甲醇制烯烃技术
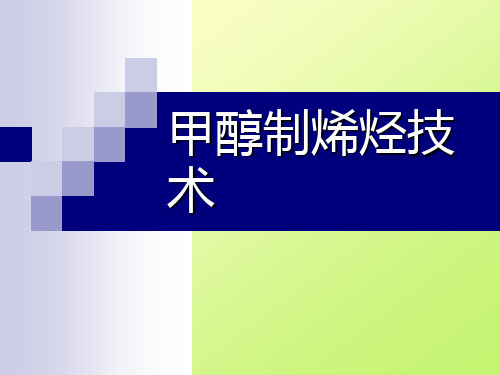
③再生空气和废气区 再生空气区由主风机、直接燃烧空气加热器和提升风机组 成。主风机提供的助燃空气经直接燃烧空气加热器后进入 再生器。直接燃烧空气加热器只在开工时使用,以将再生 器的温度提高到正常操作温度。 提升风机为再生催化剂 冷却器提供松动空气,还为待生催化剂从反应器转移到再 生器提供提升空气。提升空气需要助燃空气所需的较高压 力。通常认为用主风机提供松动风和提升空气的设计是不 经济的。然而,如果充足的工艺空气可以被利用来满足松 动风和提升风的需要,可以不用提升风机。 废气区由烟气冷却器,烟气过滤器和烟囱组成。来自再生 器的烟气在烟气冷却器发生高压蒸汽,回收热量。出冷却 器的烟气进入烟气过滤器,除去其中的催化剂颗粒。出过 滤器的烟气由烟囱排空。为了减少催化剂损失,从烟气过 滤器回收的物料进入废气精分离器。分离器将回收的催化 剂分为两类。较大的颗粒循环回 MTO 再生器。较小的颗 粒被处理掉。
④碱洗区 MTO 气相产品中的二氧化碳产物在碱洗塔中脱除。碱洗塔 有三股碱液回流和一股水回流来脱除残余的碱。碱洗区包括 补充碱和水的中间罐和注入泵。废碱脱气后送出界区处理。 二氧化碳脱除后,MTO 气相产品被冷却然后送入干燥区。 ⑤干燥区 MTO 的气体产物需干燥处理,为下游的低温工段做准备。 干燥区由两个 MTO 产品干燥器和再生设备组成。干燥器用 分子筛脱水。来自于 LORP 单元的轻质气体用于再生干燥 剂。再生设备由再生加热器,再生冷却器和再生分离罐组成。 脱水后,再生的气体混入燃料气系统。干燥后的反应气送入 分馏区的脱乙烷塔。脱乙烷塔的塔顶气压缩后送入乙炔转换 区。 ⑥乙炔转换区 脱乙烷塔顶气中包含 C2 和更轻的物料。物流中的副产物乙 炔被选择加氢转化为乙烯。乙炔转化是气相催化工艺。这个 区由两个乙炔转换塔和
甲醇制烯烃技术分析

甲醇制烯烃(MTO)技术国际领先的甲醇制烯烃工艺,主要有美国环球油品公司(UOP)和挪威海德鲁(NorskHydro)公司共同开发的UOP/HYDRO MTO工艺,中国科学院大连化学物理研究所的DMTO工艺,德国鲁奇(Lurgi)公司开发的MTP工艺¨。
J.其次,埃克森美孚(ExxonMobil)的MTO工艺、中国石化上海石油化工研究院的S—MTO工艺以及清华大学的FMTP工艺等也各有长处。
1、MTO是指甲醇直接转化为低碳烯烃(乙烯、丙烯)的技术。
最早提出MTO工艺的是美孚石油公司(Mo—bil),随后巴斯夫(BASF)、埃克森石油公司(Exxon)、环球石油公司(UOP)及海德鲁公司(Hydro)等相继投入开发。
具有代表性的MTO工艺技术主要是:UOP、UOP /Hydro、Exxon Mobil和国内中国大连化学物理研究所的DMTO、DMTO--II工艺技术。
2、MTO的反应机理是甲醇先脱水生成二甲醚(DME),然后DME与原料甲醇的平衡混合物脱水继续转化为乙烯、丙烯为主的低碳烯烃,少量的C2~C。
低碳烯烃进一步由环化、脱氢、氢转移、缩合、烷基化等反应,生成分子量不同的饱和烃、芳烃、C。
烯烃及焦炭。
3、MTO的工艺过程:MTO装置包括甲醇制烯烃(MTO)和轻烯烃回收(LORP)单元。
MTO 工艺采用气相进料、流化催化技术将甲醇转化为轻烯烃(主要是乙烯和丙烯)。
原料甲醇可采用精甲醇、粗甲醇或两者的混合物,粗甲醇是指来自甲醇合成装置还未被精制的甲醇,其中甲醇和水的质量分数约为80%和20%。
MTO单元主要由下列工序和系统构成:甲醇蒸发和产品激冷工序、反应和再生工序、空气系统和烟道气排放系统等。
轻烯烃回收单元(LORP)的主要功能是通过对气相反应产物进行压缩、冷凝、分离和提纯,得到有价值的轻烯烃(主要是乙烯和丙烯)。
LORP单元包括以下几个工序:压缩、DME回收、水洗、碱液洗涤、干燥、乙炔转化、分馏、丙烯制冷和氧化物回收工序(ORU)。
甲醇制烯烃调研报告

甲醇制烯烃调研报告《甲醇制烯烃调研报告》一、研究背景烯烃是一种重要的有机化合物,广泛应用于化工、医药、农业等多个领域。
传统上,烯烃的生产主要依靠石油和天然气等化石能源作为原料。
然而,随着环境保护和可持续发展理念的兴起,寻找替代原料生产烯烃的方法成为了重要课题。
甲醇是一种广泛应用于化工行业的化合物,其生产成本相对较低,且在生产过程中能够减少碳排放。
因此,利用甲醇制备烯烃成为了一种备受关注的新技术。
二、调研目的本次调研旨在了解甲醇制烯烃的生产工艺、市场应用情况以及发展前景,为相关企业和科研机构提供参考。
三、调研方法本次调研采用了文献资料收集、专家访谈和实地考察相结合的方法,以确保调研结果的客观性和准确性。
四、调研结果1.生产工艺:甲醇制烯烃的生产工艺主要分为催化转化和热裂解两种方法。
催化转化是利用特定催化剂将甲醇转化为烯烃的方法,而热裂解则是通过高温将甲醇分解成烯烃。
两种方法各有优劣,需根据实际情况选取合适的工艺路线。
2.市场应用情况:甲醇制烯烃技术已经在一些国家得到了广泛应用,特别是在亚洲地区。
烯烃产品主要用于化工领域的乙烯裂解和烯烃聚合等生产过程中。
3.发展前景:甲醇制烯烃技术因其成本低、环保等优势,有望成为未来烯烃生产的重要方法。
同时,随着技术的不断进步和工艺的改进,甲醇制烯烃的市场前景十分广阔。
五、结论甲醇制烯烃技术具有生产成本低、环保和可持续发展等优势,已经在一些国家得到了广泛应用。
未来,随着技术的不断进步和工艺的改进,甲醇制烯烃的市场前景将更加广阔,值得相关行业和科研机构进一步关注和研究。
六、建议应加大对甲醇制烯烃技术的研发投入,提高产业化的技术水平,加快产业化进程,推动技术的应用和推广。
同时,应加强政策支持,为甲醇制烯烃技术的发展创造更好的环境。
甲醇制烯烃研究报告结论

甲醇制烯烃研究报告结论
根据我们的研究结果,甲醇制烯烃是一种有效和可行的方法。
主要结论如下:
1. 甲醇制烯烃是一种相对比较简单和低成本的方法,可从廉价的甲醇中生产高附加值的烯烃产品。
2. 在甲醇制烯烃的过程中,催化剂的选择对产物分布和反应效率具有重要影响。
某些催化剂具有较高的烯烃选择性和活性,从而提高了反应的效果。
3. 温度、压力和催化剂负载等反应条件也对甲醇制烯烃的产物分布和产率产生影响。
适当调节这些反应条件可以优化烯烃产率。
4. 甲醇制烯烃过程中产生的副产品和废物也需要得到有效处置,以减少对环境的负面影响。
综上所述,甲醇制烯烃是一种有潜力的生产方法,可以为化工行业提供新的发展方向。
然而,进一步的研究和实验仍然需要进行,以进一步优化反应条件和探索其商业应用的可行性。
甲醇制烯烃

UOP开发的以SAPO-34为活性组分的MTO-100催化剂,其乙烯选择性明显优于ZSM-5,使MTO工艺取得突破性 进展。其乙烯和丙烯的选择性分别为43%~61.1%和27.4%~41.8%。
技术简介
技术简介
甲醇制烯烃(Methanol to Olefins,MTO)和甲醇制丙烯(Methanol to Propylene)是两个重要的C1化 工新工艺,是指以煤或天然气合成的甲醇为原料,借助类似催化裂化装置的流化床反应形式,生产低碳烯烃的化 工技术。
上世纪七十年代美国Mobil公司在研究甲醇使用ZSM-5催化剂转化为其它含氧化合物时,发现了甲醇制汽油 (Methanol to Gasoline,MTG)反应。1979年,新西兰政府利用天然气建成了全球首套MTG装置,其能力为75 万吨/年,1985年投入运行,后因经济原因停产。
从国外发表的专利看,MTO又做了一些新的改进。
1、以二甲醚(DME)作MTO中间步骤
水或水蒸气对催化剂有一定危害性,减少水还可节省投资和生产成本,生产相同量的轻质烯烃产生的水,甲 醇是二甲醚的两倍,所以装置设备尺寸可以减小,生产成本也可下降。
技术发展现状
技术发展现状
中科院大连化物所是国内最早从事MTO技术开发的研究单位。该所从上世纪八十年代便开展了由甲醇制烯烃 的工作。“六五”期间完成了实验室小试,“七五”期间完成了300吨/年(甲醇处理量)中试;采用中孔ZSM-5 沸石催化剂达到了当时国际先进水平。90年代初又在国际上首创“合成气经二甲醚制取低碳烯烃新工艺方法(简 称SDTO法)”,被列为国家“八五”重点科技攻关课题。该新工艺是由两段反应构成,第一段反应是合成气在以 金属-沸石双功能催化剂上高选择性地转化为二甲醚,第二段反应是二甲醚在SAPO-34分子筛催化剂上高选择性地 转化为乙烯、丙烯等低碳烯烃。
甲醇制烯烃技术研究
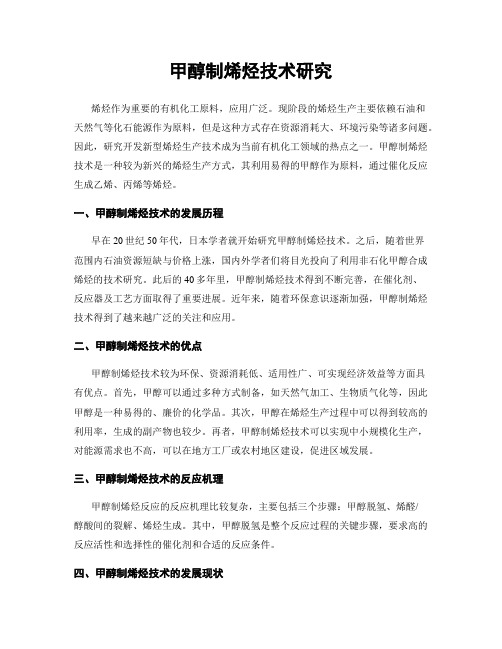
甲醇制烯烃技术研究烯烃作为重要的有机化工原料,应用广泛。
现阶段的烯烃生产主要依赖石油和天然气等化石能源作为原料,但是这种方式存在资源消耗大、环境污染等诸多问题。
因此,研究开发新型烯烃生产技术成为当前有机化工领域的热点之一。
甲醇制烯烃技术是一种较为新兴的烯烃生产方式,其利用易得的甲醇作为原料,通过催化反应生成乙烯、丙烯等烯烃。
一、甲醇制烯烃技术的发展历程早在20世纪50年代,日本学者就开始研究甲醇制烯烃技术。
之后,随着世界范围内石油资源短缺与价格上涨,国内外学者们将目光投向了利用非石化甲醇合成烯烃的技术研究。
此后的40多年里,甲醇制烯烃技术得到不断完善,在催化剂、反应器及工艺方面取得了重要进展。
近年来,随着环保意识逐渐加强,甲醇制烯烃技术得到了越来越广泛的关注和应用。
二、甲醇制烯烃技术的优点甲醇制烯烃技术较为环保、资源消耗低、适用性广、可实现经济效益等方面具有优点。
首先,甲醇可以通过多种方式制备,如天然气加工、生物质气化等,因此甲醇是一种易得的、廉价的化学品。
其次,甲醇在烯烃生产过程中可以得到较高的利用率,生成的副产物也较少。
再者,甲醇制烯烃技术可以实现中小规模化生产,对能源需求也不高,可以在地方工厂或农村地区建设,促进区域发展。
三、甲醇制烯烃技术的反应机理甲醇制烯烃反应的反应机理比较复杂,主要包括三个步骤:甲醇脱氢、烯醛/醇酸间的裂解、烯烃生成。
其中,甲醇脱氢是整个反应过程的关键步骤,要求高的反应活性和选择性的催化剂和合适的反应条件。
四、甲醇制烯烃技术的发展现状目前,甲醇制烯烃技术主要被广泛应用于乙烯、丙烯等烯烃生产,特别是乙烯产业。
相较于中国,欧美等国家已经建立起成熟的甲醇制烯烃产业链,具有规模化生产、成本优势等特点。
而在中国,甲醇制烯烃技术仍处于起步阶段,目前主要以技术开发研究为主,生产规模较小,工程应用受到一定限制。
五、甲醇制烯烃技术的未来展望甲醇制烯烃技术具有广阔的应用前景。
随着环境保护意识逐渐提高,烯烃生产中的石化原料的问题也现已越来越引起社会各界重视。
甲醇制烯烃技术

甲醇制烯烃技术甲醇制烯烃工艺是煤基烯烃产业链中的关键步骤,其工艺流程主要为在合适的操作条件下,以甲醇为原料,选取适宜的催化剂(ZSM-5沸石催化剂、SAPO-34分子筛等),在固定床或流化床反应器中通过甲醇脱水制取低碳烯烃。
根据目的产品的不同,甲醇制烯烃工艺分为甲醇制乙烯、丙烯(methanol-to-olefin ,MTO,甲醇制丙烯(methanol-to-propylene ,MTP。
MTC工艺的代表技术有环球石油公司(UOP)和海德鲁公司(Norsk Hydro)共同开发的UOP/Hydro MTOJ术,中国科学院大连化学物理研究所自主创新研发的DMTO 技术;MTP工艺的代表技术有鲁奇公司(Lurgi )开发的Lurgi MTP技术和我国清华大学自主研发的FMTP技术。
甲醇制烯烃的基本原理在一定条件(温度、压强和催化剂)下,甲醇蒸汽先脱水生成二甲醚,然后二甲醚与原料甲醇的平衡混合物气体脱水继续转化为以乙烯、丙烯为主的低碳烯烃;少量C2〜C5的低碳烯烃由于环化、脱氢、氢转移、缩合、烷基化等反应进一步生成分子量不同的饱和烃、芳烃、C6+烯烃及焦炭。
整个反应过程可分为两个阶段:脱水阶段、裂解反应阶段1、脱水阶段2CH3OH R CH3OCH3+ H2O + Q2、裂解反应阶段该反应过程主要是脱水反应产物二甲醚和少量未转化的原料甲醇进行的催化裂解反应,包括:(1)主反应(生成烯烃)n CH304 Cn H2n + nH20 + Qn CH30CH4 2CnH2n + nH20 + Qn = 2和3 (主要),4、5和6 (次要)以上各种烯烃产物均为气态。
(2)副反应(生成烷烃、芳烃、碳氧化物并结焦)(n+ 1)CH30F R CnH2n+ 2+ C+(n+ 1)H20 + Q(2n+ 1)CH30F R 2CnH2n+ 2+ C0^ 2nH20 + Q(3 n + 1)CH30F R3CnH2r+ 2+ C0+ (3n —1)H20 + Qn= 1 , 2 , 3 , 4 , 5 ...............n CH30CH4 CnH2n-6+ 3 H2 + n H20 + Qn= 6 ,7,8 .........以上产物有气态(C0 H2、H20 C02 CH4等烷烃、芳烃等)和固态(大分子量烃和焦炭)之分。
- 1、下载文档前请自行甄别文档内容的完整性,平台不提供额外的编辑、内容补充、找答案等附加服务。
- 2、"仅部分预览"的文档,不可在线预览部分如存在完整性等问题,可反馈申请退款(可完整预览的文档不适用该条件!)。
- 3、如文档侵犯您的权益,请联系客服反馈,我们会尽快为您处理(人工客服工作时间:9:00-18:30)。
1 甲醇制烯烃1.1 工艺技术方案的选择1.1.1 甲醇制烯烃工艺技术1.1.1.1 原料路线确定的原则和依据甲醇制乙烯、丙烯等低碳烯烃(Methanol-to-Olefin,简称MTO)是最有希望替代石脑油为原料制烯烃的工艺路线,目前工艺技术开发已趋于成熟。
该技术的工业化,开辟了由煤炭或天然气经气化生产基础有机化工原料的新工艺路线,有利于改变传统煤化工的产品格局,是实现煤化工向石油化工延伸发展的有效途径。
甲醇制烯烃的反应比较复杂,在高选择性催化剂上,MTO主要发生如下放热反应:2CH3OH CH3OCH3+H2O12CH3OH C2H4+ 2C3H6+ C4H8+12H2O6CH3OCH3C2H4+ 2C3H6+ C4H8+6H2O本项目采用煤炭气化制甲醇,甲醇制烯烃的生产路线。
1.1.1.2 国内、外工艺技术概况(1) 国外工艺技术概况二十世纪八十年代初,美国美孚(Mobil)公司在研究采用沸石催化剂利用甲醇制汽油(MTG)工艺的过程中发现并发展甲醇制烯烃(MTO)工艺。
Mobil对反应机理进行了细致的研究,优化催化剂,合成了针对MTO和MTG反应的新型沸石催化剂ZSM-5。
Mobil基于流化床的工艺示范装置自1982年底运行至1985年末,成功地证明了流化床反应系统可以应用于MTG和MTO过程。
Mobil甲醇制汽油技术的成功开发推动了甲醇制烯烃(MTO)、甲醇制丙烯(MTP)等工艺的开发。
目前,国外的工艺技术中,由※※※※/※※※※公司共同开发的MTO 工艺、由Lurgi公司开发的MTP工艺最具有产业化前景。
1986年UCC发现采用SAPO-34(磷酸硅铝分子筛)可以有效地将甲醇转化为低碳烯烃,而后UCC将相关技术转让给了※※※※公司。
1992年※※※※和Norsk※※※※合作开发了以多孔性MTO-100(主要活性组分为SAPO-34)为催化剂的※※※※/※※※※工艺,MTO-100催化剂具有更好稳定性和耐磨性。
1995年※※※※/※※※※公司在挪威建成了一套甲醇加工能力为0.75-1t/d的中试装置。
※※※※/※※※※中试装置使用流化床反应器,并配一台流化床再生器,采用自欧洲市场购买的AA级甲醇为原料,在0.1-0.3MPa(G)压力和400~450℃温度条件下,采用以磷酸铝分子筛SAPO-34为主要成分的MTO-100型催化剂,在连续运转期间,甲醇转化率始终大于99.8%,乙烯和丙烯收率达到约80%。
根据操作条件的不同,乙烯/丙烯可以在0.75-1.5之间调整,乙烯和丙烯产品可以达到聚合级。
低碳烯烃合成的关键技术是催化剂,20世纪80年代多使用ZSM-5及其改性产品,90年代以来,则倾向于磷酸硅铝分子筛(SAPO),尤其是具有强选择性和活性的8环通道的小孔SAPO-34倍受青睐。
※※※※公司推荐采用的催化剂是MTO-100催化剂,目前已经完成了MTO-100催化剂的扩大研究和测试,包括甲醇转化率、选择性、结焦、再生能力和长期稳定性。
同时也完成了商业化催化剂生产试验,在中试装置中经过数百次反应-再生循环,性能非常稳定,验证了商业化规模催化剂的强度和耐磨性可以达到预期目标,催化剂的物理强度和耐磨性超过FCC催化剂。
但MTO-100催化剂的价格较为昂贵,催化剂的寿命、选择性、耐磨性还有待于工业化的实践考验。
※※※※公司作为世界上最早的流化催化裂化技术专利商,在FCC领域和工程放大方面有着丰富的经验,MTO的反应、再生苛刻度均比FCC低,设备风险在可控范围内。
在MTO工艺方面,针对不同空速进行了很多试验,催化剂的选择性很强,实验结果表明空速对反应不是敏感参数。
流化床反应器在控制反应区的密度和空速调节上具有优势,因此设计的把握性更大。
轻烯烃回收部分与管式炉裂解制乙烯的分离流程基本相同,由于MTO工艺生成气中的甲烷、氢气和杂质含量要比轻油管式炉裂解生产乙烯工艺少得多,流程更简化。
因此,从工艺流程来看,MTO工艺工业化有很多成熟的经验可以借鉴,工业化的把握较大。
※※※※石化在比利时Feluy建设的10吨甲醇/天的MTO示范装置(包括OCP 单元)计划于2009年开车。
新加坡的欧洲化学公司正在尼日利亚建设1万吨甲醇/天的MTO装置(包括OCP单元),目前已完成基础设计。
(2) 国内工艺技术概况我国MTO工艺及催化剂的开发也有相当长的时间,中科院※※※※※※※※在20世纪80年代初开展MTO研究工作(该技术现简称为DMTO)。
上世纪八十年代完成了1.0吨/天(甲醇进料)中试,采用中孔ZSM-5沸石催化剂,固定床反应器,其结果达到同期国际先进水平。
20世纪90年代初开发了合成气经二甲醚制低碳烯烃的工艺路线(SDTO工艺),于1995年完成了中试装置的实验研究。
SDTO工艺包括2个阶段:第一阶段是在固定床中将合成气转化为二甲醚,采用金属酸双功能催化剂,连续平稳操作1000h,二甲醚选择性95%,CO单程转化率75%-78%。
第二阶段采用上流密相流化床反应器将二甲醚转化成低碳烯烃,日处理当量甲醇0.08-0.15吨(进料是二甲醚时,折算成甲醇的量),甲醇转化率始终大于98%,乙烯和丙烯收率达到81%。
催化剂为基于SAPO-34的DO123催化剂。
催化剂连续经历1500次左右的反应再生操作,反应性能未见明显变化,催化剂损耗与工业用流化催化裂化催化剂时相当。
2004年8月,※※※※※※※※与陕西新兴煤化工科技发展有限责任公司(现更名为新兴能源科技有限公司)、中国石化集团洛阳石油化工工程公司三方合作,启动建设世界上第一套万吨级工业性试验装置。
※※※※化物所提供DMTO催化剂制备技术,并提供实验室阶段得到的工艺数据,中石化洛阳石化工程公司承担DMTO 示范装置的工程设计工作,陕西新兴煤化工科技发展有限责任公司承担施工建设管理、投料运行和维护技术支持。
该试验装置的规模为50吨/天甲醇进料,建设方案仅为反应部分,不包括压缩、净化和产品气体分离部分。
该装置于2005年7月完成试验装置的建设、安装工作,2005年底完成了试验设备的调试工作。
2006年2月20日试验装置一次投料试车成功,经过2月21日~3月2日,4月21日~5月20日两个阶段,累计运行1102小时的工艺条件试验后,于2006年6月17日~20日中国石油化工协会组织相关单位和专家对该工业试验装置进行了72小时现场考核表明,试验装置运行平稳,达到设计预定的参数和目标,能够满足反应-再生系统温度、压力、循环量、取热和烧焦的要求,催化剂物化指标和粒度分布数据合理,水热稳定性良好,可满足大型化流化床工业装置的要求。
甲醇转化率近100%,乙烯+丙烯收率约为80%,乙烯/丙烯的比率在0.8-1.2范围内可调。
但也存在催化剂损失大等问题。
2006年8月,国家有关部门组织的技术鉴定专家组一致认为:甲醇制烯烃工业性试验取得了重大突破性进展,各项指标已达到世界领先水平。
同时,※※※※※※※※进行了DMTO专用催化剂的工业放大,2008年,年产2000吨的DMTO催化剂的商业化生产装置开工。
可以保证为MTO商业化装置连续供应催化剂。
DMTO技术的第一个商业化应用是※※※※煤化工项目,该项目于2006年12月获得国家发改委批准,目前采用DMTO技术的60万吨/年甲醇制烯烃装置进展顺利,正处于详细设计和建设阶段,计划于2010年开工。
此外,一些大型能源企业计划采用DMTO技术,正在积极争取国家核准。
1.1.2 利用C4+增产丙烯技术C4+是MTO工艺的副产品,在MTO装置中采用C4+利用技术可达到更高的甲醇进料利用率。
1.1.2.1 工艺路线介绍目前利用C4+增产丙烯技术研究主要集中在2个方面:(1) C4+烯烃裂解技术;(2) C4烯烃歧化技术;1.1.2.2 C4+烯烃裂解制丙烯国内外工艺技术概况C4+烯烃裂解是将C4-C8烯烃在催化剂作用下转化为丙烯和乙烯的技术,它不仅可以解决炼厂、石脑油裂解及煤制烯烃副产的C4-C8的出路问题,又可以增产高附加值的乙烯、丙烯产品,成为近年研究较为活跃的领域。
根据反应器的型式,可将C4—C8烯烃裂解制丙烯技术分为两类:一类是固定床工艺,目前国外较为成熟的技术主要有※※※※石化/※※※※公司的烯烃裂解工艺(OCP工艺)、Lurgi公司的Propylur工艺、日本旭化成公司Omega工艺,国内有中国石油化工股份有限公司上海石油化工研究院(简称上海石油化工研究院)开发的OCC工艺。
其中具有代表性的是※※※※石化/※※※※公司的OCP工艺;另一类是流化床工艺,国外主要有Arco/KBR公司的Superflex工艺、Mobil公司的MOI工艺,国内有※※※※※※※※的C4+催化裂解工艺。
下面是两种具有代表性的工艺技术概况。
(1) ※※※※石化/※※※※公司的OCP工艺※※※※石化和※※※※公司联合开发了OCP工艺。
该工艺的特点是原料中不加稀释气、空速高,因而反应器的体积小,设备投资少。
该工艺采用专用的沸石分子筛催化剂,在500-600℃、0.1-0.5MPa、较高空速的反应条件下,原料在固定床反应器中和催化剂接触发生催化裂化反应,丙烯选择性及收率都较高。
该工艺用于甲醇制烯烃(联合装置时)可在甲醇进料量不变的情况下,使乙烯和丙烯的总收率由80%提高到90%以上,丙烯收率由30%-50%提高到60%。
OCP的示范装置位于比利时的Antwerp。
该装置于1998年开始运行,处理量为0.7-1.7t/d的新鲜进料。
装置内包括两个反应器(一个运行模式,另一个则再生或备用),还有催化剂再生设施。
OCP示范装置的原料来自Antwerp炼厂FCC装置下游的MTBE装置。
※※※※石化在比利时Feluy建设的10吨甲醇/天的MTO示范装置(包括OCP单元)计划于2009年开车。
新加坡的欧洲化学公司正在尼日利亚建设1万吨甲醇/天的MTO装置(包括OCP单元),目前已完成基础设计。
(2) ※※※※※※※※(DICP)的C4+催化裂解工艺※※※※※※※※的C4+催化裂解工艺是基于DMTO示范装置发展起来的工艺技术,C4+催化裂解工艺技术采用密相流化床反应器,采用和DMTO工艺同一种催化剂。
C4+催化裂解工艺与DMTO工艺结合(DMTOⅡ)大大提高了乙烯与丙烯的收率。
P/E可以在更大范围内调整。
单位烯烃产品甲醇消耗降低。
C4+催化裂解反应温度为500-600℃,反应压力为0.1-0.3MPa。
在500-600℃。
该工艺充分利用MTO主反应及催化剂再生烧焦释放的热量,建立热能回收系统。
1.1.2.3 C4烯烃歧化制丙烯国内外工艺技术概况烯烃歧化技术多年以前已经开发成功,只是因为近年来一些地区丙烯价格逐步走高,这一技术又重新引起了人们的重视。