轮对基础知识
轮对基本知识
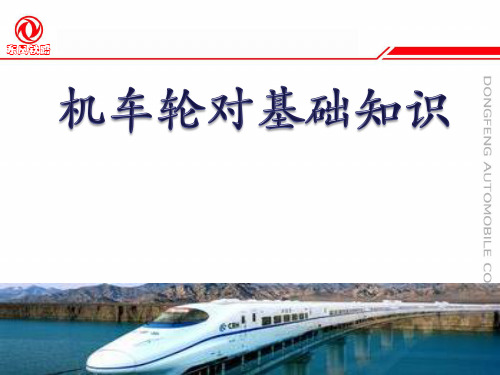
制造厂代号 制造年月 制造顺序号码 熔炼号码 轮型
3.2.2 车轴标记
东风铁路
轴对 类型
生产 厂家
车轴 标记
生产 序号
生产 日期
3.2.3 轮芯标记
东风铁路
系列 号
生产 日期
生产厂家
东风铁路
3.2.3 装配标记
组装 标记
检修 标记
东风铁路
不妥之处,请予指 正,谢谢大家!
东风铁路 3.1.1.2 轮对故障
东风铁路 3.1.1.3 轮对故障
1.3 轮缘垂直磨耗
10
轮缘垂直磨耗
不能小于23mm
3.1.1.4 轮对擦伤
东风铁路
轮芯 擦伤
轮对擦伤
踏面 擦伤
轮芯擦伤 踏面擦伤
3.1.1.5 踏面擦伤
东风铁路
轮箍踏面擦伤深
严 重
度不超过0.7
擦
毫米,且长度不
伤
得超过70mm.
较
严
重
踏面上的缺陷或
擦
剥离长度不超过
伤
40毫米,且深
一
般
度不超过1毫米。
擦
伤
东风铁路 3.1.1.6 轮对裂纹
轮箍裂纹 轮芯裂纹 车轴裂纹
3.1.1 轮对故障
东风铁路
透油
透锈
弛缓
轮对 故障
轮对在运用中如果发现有以上故障,必 须进行大修处理。
3.2 轮对标记
东风铁路
1
2 3 4
车箍标记 车轴标记 轮芯标记 装配标记
东风铁路
机车轮对 机车走行部中 最重要的部件 之一,机车全 部重量通过轴 颈、轮对支承 在钢轨上,轮 对滚动使机车 前进。
Байду номын сангаас
机车轮对
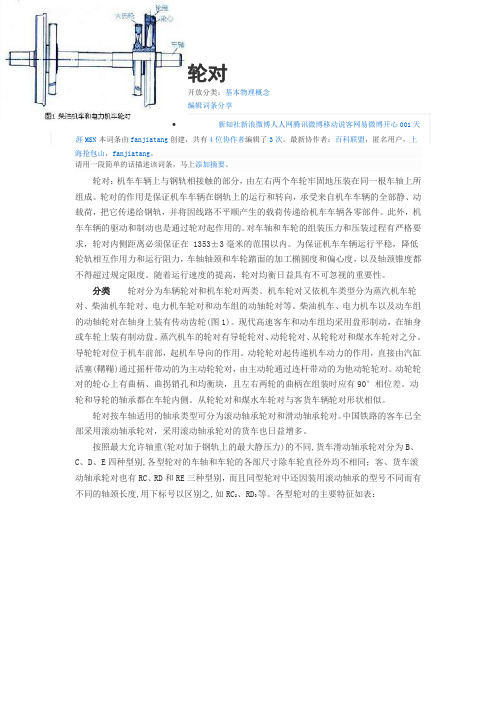
轮对开放分类:基本物理概念编辑词条分享•新知社新浪微博人人网腾讯微博移动说客网易微博开心001天涯MSN本词条由fanjiatang创建,共有4位协作者编辑了3次。
最新协作者:百科联盟,匿名用户,上海抢包山,fanjiatang。
请用一段简单的话描述该词条,马上添加摘要。
轮对:机车车辆上与钢轨相接触的部分,由左右两个车轮牢固地压装在同一根车轴上所组成。
轮对的作用是保证机车车辆在钢轨上的运行和转向,承受来自机车车辆的全部静、动载荷,把它传递给钢轨,并将因线路不平顺产生的载荷传递给机车车辆各零部件。
此外,机车车辆的驱动和制动也是通过轮对起作用的。
对车轴和车轮的组装压力和压装过程有严格要求,轮对内侧距离必须保证在 1353±3毫米的范围以内。
为保证机车车辆运行平稳,降低轮轨相互作用力和运行阻力,车轴轴颈和车轮踏面的加工椭圆度和偏心度,以及轴颈锥度都不得超过规定限度。
随着运行速度的提高,轮对均衡日益具有不可忽视的重要性。
分类轮对分为车辆轮对和机车轮对两类。
机车轮对又依机车类型分为蒸汽机车轮对、柴油机车轮对、电力机车轮对和动车组的动轴轮对等。
柴油机车、电力机车以及动车组的动轴轮对在轴身上装有传动齿轮(图1)。
现代高速客车和动车组均采用盘形制动,在轴身或车轮上装有制动盘。
蒸汽机车的轮对有导轮轮对、动轮轮对、从轮轮对和煤水车轮对之分。
导轮轮对位于机车前部,起机车导向的作用。
动轮轮对起传递机车动力的作用,直接由汽缸活塞(鞲鞴)通过摇杆带动的为主动轮轮对,由主动轮通过连杆带动的为他动轮轮对。
动轮轮对的轮心上有曲柄、曲拐销孔和均衡块,且左右两轮的曲柄在组装时应有90°相位差。
动轮和导轮的轴承都在车轮内侧。
从轮轮对和煤水车轮对与客货车辆轮对形状相似。
轮对按车轴适用的轴承类型可分为滚动轴承轮对和滑动轴承轮对。
中国铁路的客车已全部采用滚动轴承轮对,采用滚动轴承轮对的货车也日益增多。
按照最大允许轴重(轮对加于钢轨上的最大静压力)的不同,货车滑动轴承轮对分为B、C、D、E四种型别,各型轮对的车轴和车轮的各部尺寸除车轮直径外均不相同;客、货车滚动轴承轮对也有RC、RD和RE三种型别,而且同型轮对中还因装用滚动轴承的型号不同而有不同的轴颈长度,用下标号以区别之,如RC2、RD3等。
机车轮对
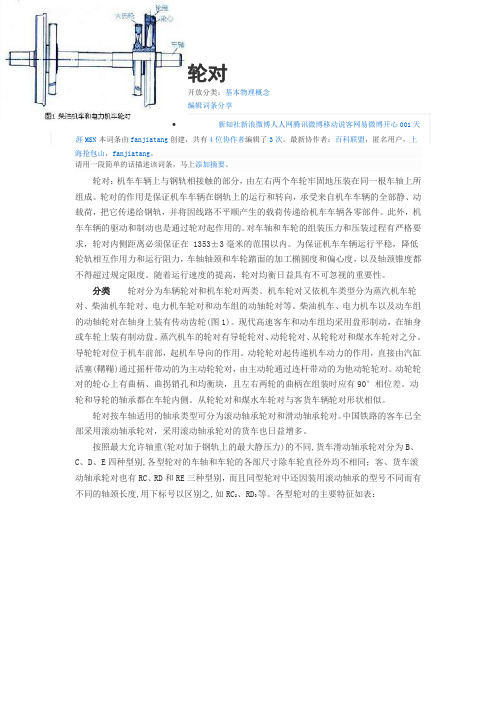
轮对开放分类:基本物理概念编辑词条分享•新知社新浪微博人人网腾讯微博移动说客网易微博开心001天涯MSN本词条由fanjiatang创建,共有4位协作者编辑了3次。
最新协作者:百科联盟,匿名用户,上海抢包山,fanjiatang。
请用一段简单的话描述该词条,马上添加摘要。
轮对:机车车辆上与钢轨相接触的部分,由左右两个车轮牢固地压装在同一根车轴上所组成。
轮对的作用是保证机车车辆在钢轨上的运行和转向,承受来自机车车辆的全部静、动载荷,把它传递给钢轨,并将因线路不平顺产生的载荷传递给机车车辆各零部件。
此外,机车车辆的驱动和制动也是通过轮对起作用的。
对车轴和车轮的组装压力和压装过程有严格要求,轮对内侧距离必须保证在 1353±3毫米的范围以内。
为保证机车车辆运行平稳,降低轮轨相互作用力和运行阻力,车轴轴颈和车轮踏面的加工椭圆度和偏心度,以及轴颈锥度都不得超过规定限度。
随着运行速度的提高,轮对均衡日益具有不可忽视的重要性。
分类轮对分为车辆轮对和机车轮对两类。
机车轮对又依机车类型分为蒸汽机车轮对、柴油机车轮对、电力机车轮对和动车组的动轴轮对等。
柴油机车、电力机车以及动车组的动轴轮对在轴身上装有传动齿轮(图1)。
现代高速客车和动车组均采用盘形制动,在轴身或车轮上装有制动盘。
蒸汽机车的轮对有导轮轮对、动轮轮对、从轮轮对和煤水车轮对之分。
导轮轮对位于机车前部,起机车导向的作用。
动轮轮对起传递机车动力的作用,直接由汽缸活塞(鞲鞴)通过摇杆带动的为主动轮轮对,由主动轮通过连杆带动的为他动轮轮对。
动轮轮对的轮心上有曲柄、曲拐销孔和均衡块,且左右两轮的曲柄在组装时应有90°相位差。
动轮和导轮的轴承都在车轮内侧。
从轮轮对和煤水车轮对与客货车辆轮对形状相似。
轮对按车轴适用的轴承类型可分为滚动轴承轮对和滑动轴承轮对。
中国铁路的客车已全部采用滚动轴承轮对,采用滚动轴承轮对的货车也日益增多。
按照最大允许轴重(轮对加于钢轨上的最大静压力)的不同,货车滑动轴承轮对分为B、C、D、E四种型别,各型轮对的车轴和车轮的各部尺寸除车轮直径外均不相同;客、货车滚动轴承轮对也有RC、RD和RE三种型别,而且同型轮对中还因装用滚动轴承的型号不同而有不同的轴颈长度,用下标号以区别之,如RC2、RD3等。
第二讲 轮对

二.超声波探伤:
基本原理: 向工件内发射超声波,遇缺陷受阻发射. 检测: 1)缺陷反射的超声波 2)超声波通过工件后衰减程度. 来发现缺陷
超声波探伤仪简介:脉冲反射式
思考题 1、画出车轴示意图并标出各部名称。
2、画出车轮示意图并标出各部名称。
3、名词解释:热切、冷切、电磁探伤、超声
第二讲 轮对
组成:一轴两轮(同型、同材)过盈配合
作用:
1)承受车全部重量(轮对自重除外) 2)负重下,引导车在轨上运行,传力。
要求:
1)足够强度。 2)一定弹性——减少轮轨间作用力、噪音。 3)强度足够,一定寿命前提下,重量要最小 耐磨性好。
第一节 车轴
整体辗钢轮: 强度髙,韧性好,适应重载、 髙速,寿命长,轮缘可焊修,踏面可旋修, 自重轻。 新型铸钢轮::比辗钢轮劳动力消耗少、生 产能耗低;尺寸精确、几何形狀好、内部组 织均匀、质量分布均匀、轮轨间动力作用相 对小;耐疲劳、抗热裂性的性能均优于辗钢 轮。 按辐板形狀:直辐板形轮 S形辐板轮
纹等故障,用专用探伤器进行探伤查— —磁探、超探。
一、 电磁探伤 基本原理:将铁磁材料的零件磁化,零件 缺陷处的磁阻增大,利用漏磁来发现缺陷。
电磁探伤器:
1、开合马蹄型电磁探伤器:
2、 TYC-3000型荧光磁粉探伤机:
车轴表面探伤专用设备,纵向、周向联 合磁化,磁悬液荧光磁粉显示,机械化 高,灵敏度高。
第三节
轮对的组装
轮轴压力配合,在常温下将车轴用轮轴顶压机 按一定的压力压入车轮的轮毂孔内,座与孔直径 之差称为过盈量。
1、过盈量的选择: 2、压力曲线:
压力曲线
轮辋宽度≥135 原型1353±2
轮对压配合时的压装与分解

轮对压配合时的压装与分解摘要:轮对是转向架的重要组成部分。
通过了解轮对压装的基本工艺的基础上,并进一步分析圆柱度,过盈量,压入速度和润滑剂等关键因素对轮对压装质量的影响。
通过分析关键因素的影响,有助于提高轮对压装质量,从而为转向架安全工作提供重要保障。
关键词:转向架;轮对压装;关键因素1前言轮对本身的结构并不复杂,但是由于它承担的任务多且重要,因此它的加工制造以及组装要求都非常高。
尤其是轮对的组装对于转向架的运行表现起到关键性的作用,组装稍有差错容易引发列车停车,甚至脱轨等重大事故。
通过对轮对组装过程的分析,可以更好地保证轮对正常使用,保障列车行驶安全。
2轮对压装工艺简介轮对本身结构较为简单,但是其对压装的要求却十分严格。
目前常见压装根据压装方式不同可以分为普通压装和注油压装两种方式。
其中普通压装根据压装温度不同可以分为热压装和冷压装。
热压装是将车轮内孔进行加热使其膨胀后再进行压装,其主要是针对过盈量较大的情况下使用。
热压装工艺设备一般较为复杂,一次投入成本较高,压装合格率较高,可提高车轴的使用寿命,止推试验效率低。
冷压装是直接通过压装机将车轮压到车轴上的方式,其主要是针对过盈量较小的情况下使用。
冷压装设备较为简单,一次性投入成本较低,但压装合格率一般,对操作要求较高,操作不当容易“戗轴”,对车轴寿命有一定影响,止推试验效率高。
而注油压装是在车轮上开注油孔,在压装过程中通过注入高压油,在车轮和车轴接触面之间形成一层油膜进行压装,其主要是针对车轴表面要求较高时使用。
注油压装设备较为复杂,操作难度较大,加工难度大,但压装过程允许停顿且不限时间,可以在一定范围内自由调整车轮位置。
这三种压装工艺目前都在使用,都有各个的优缺点。
这三种压装工艺的选择主要根据车轮和轮轴的结构以及压装的具体要求来决定的。
目前使用最为广泛使用的还是冷压装工艺。
3轮对压装影响因素在轮对冷压装过程中,影响压装效果主要包括过盈量,圆柱度,压入速度和润滑剂等因素。
火车轮结构基础知识
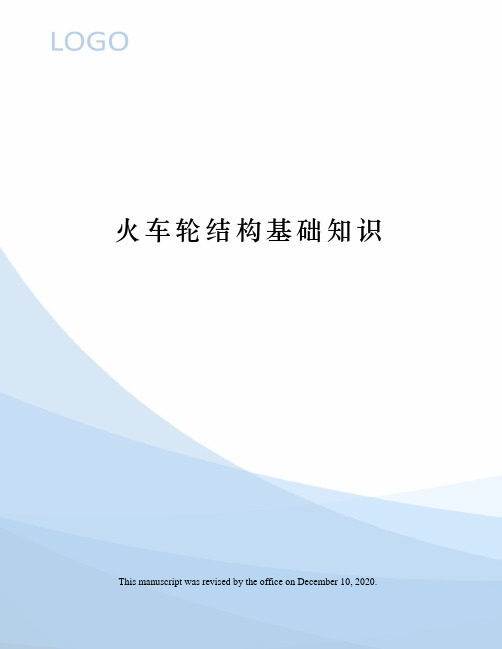
火车轮结构基础知识 This manuscript was revised by the office on December 10, 2020.车轮结构完全由车轮直径,轮辋,轮毂尺寸,毂辋距,辐板形状,轮缘踏面外形所决定。
每个尺寸或每部位形状都有其特殊意义。
一、直径车轮直径对其本身及整个车辆都有较大影响。
一方面车轮直径越大,车辆重心越高,车辆的动力性能越差。
另一方面,增大车轮直径,可以降低轮轨的接触应力,降低车轮磨耗速度,增加车轮的热容量,提高踏面制动热负荷的承受能力。
因此车轮直径大小应根据车辆情况综合确定。
但总的来说,车辆轴重越大,车轮直径应越大,以提高车轮的热容量和增加轮轨的接触面积,减少踏面损伤和磨耗。
另外,车轮直径的取值还应注意规格的标准化系列问题,以利于车轮制造和检修。
目前我过货车车轮直径大多为840mm,特殊货车车轮直径为915。
二、轮辋轮辋宽度尺寸主要取决于轮轨的搭载量。
当轮对运行在曲线上时,外侧车轮轮缘靠近钢轨,内侧轮缘远离钢轨。
只有内侧车轮踏面在钢轨上的搭载量足够,才能保证轮对不脱轨。
《铁路技术管理规程》规定,当曲线半径在300m以下时,轨距应加宽15mm。
因此,最大轨距为1435+15+6=1456mm(其中:名义轨距L为1435mm,最大公差为6mm)。
轮对最小内侧距为1354mm,轮缘最小厚度为23mm。
车轮踏面外侧倒角5mm,钢轨头部圆弧半径为R13mm,钢轨内侧磨耗2mm,轨枕弯曲、道钉松动等引起轨距扩大8mm,重车时车轴微弯引起轮对内侧距离减小2mm,轮轨安全搭载量按7mm考虑,根据上述数据算得轮辋最小宽度为120mm,考虑到车辆过驼峰时实施的制动,车轮外侧面磨损5mm,则轮辋最小宽度应为125mm。
目前我国铁路货车车轮轮辋宽度为135~140mm。
轮辋厚度通常指新轮辋厚度。
我国铁路对正常服役的车轮的判废依据是轮辋剩余厚度,当轮辋剩余厚度小于等于23mm时车轮报废。
铁路运输安全技术常识
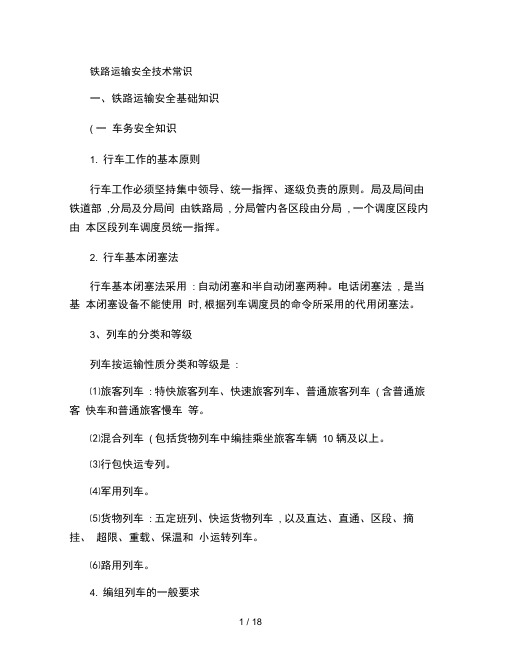
铁路运输安全技术常识一、铁路运输安全基础知识( 一车务安全知识1. 行车工作的基本原则行车工作必须坚持集中领导、统一指挥、逐级负责的原则。
局及局间由铁道部,分局及分局间由铁路局, 分局管内各区段由分局, 一个调度区段内由本区段列车调度员统一指挥。
2. 行车基本闭塞法行车基本闭塞法采用: 自动闭塞和半自动闭塞两种。
电话闭塞法, 是当基本闭塞设备不能使用时, 根据列车调度员的命令所采用的代用闭塞法。
3、列车的分类和等级列车按运输性质分类和等级是:⑴旅客列车: 特快旅客列车、快速旅客列车、普通旅客列车( 含普通旅客快车和普通旅客慢车等。
⑵混合列车( 包括货物列车中编挂乘坐旅客车辆10 辆及以上。
⑶行包快运专列。
⑷军用列车。
⑸货物列车: 五定班列、快运货物列车, 以及直达、直通、区段、摘挂、超限、重载、保温和小运转列车。
⑹路用列车。
4. 编组列车的一般要求列车应按《铁路技术管理规程》( 简称《技规》规定及列车编组计划和列车运行图规定的编挂条件、车组、重量或长度编组。
列车重量应根据机车牵引力、区段内线路状况及其设备条件确定; 列车长度应根据运行区段内各站到发线的有效长, 并须预留30m 的附加制动距离确定; 旅客列车按旅客列车编组表编组, 机车后第一位编挂一辆未搭乘旅客的车辆作为隔离车列车最后一辆的后端应有压力表、紧急制动阀和运转车长乘务室。
同时, 《技规》第175 条规定对9 种情况的车辆禁止编入列车。
5. 调车作业的有关规定车站的调车工作应按车站的技术作业过程及调车作业计划进行, 并要固定作业区域、线路使用、调车机车、人员、班次、交接班时间、交接班地点、工具数量及存放地点。
车站的调车工作由车站值班员( 调度员统一领导, 调车作业由调车长单一指挥。
调车领导人应正确及时编制、布置调车作业计划, 调车领导人及调车指挥人必须亲自交接计划, 调车指挥人必须亲自向司机及其他人员交递和传达计划。
调车作业时, 调车作业人员必须正确及时地显示信号, 机车乘务员要认真确认信号并鸣笛回示, 不足两人不准进行调车作业。
(完整word版)火车轮结构基础知识
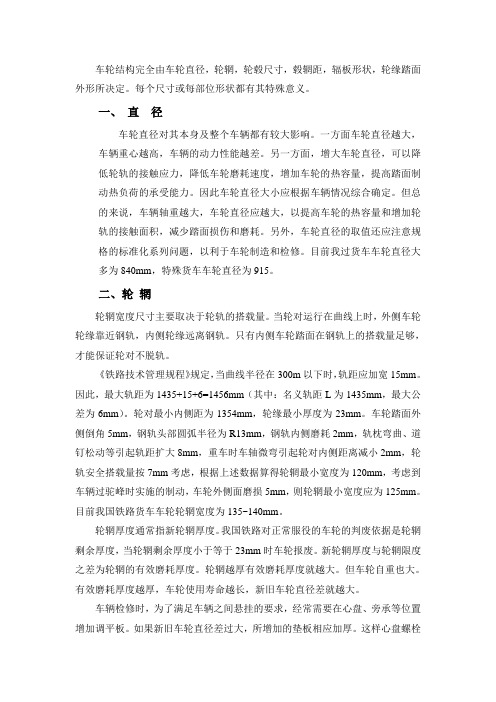
车轮结构完全由车轮直径,轮辋,轮毂尺寸,毂辋距,辐板形状,轮缘踏面外形所决定。
每个尺寸或每部位形状都有其特殊意义。
一、直径车轮直径对其本身及整个车辆都有较大影响。
一方面车轮直径越大,车辆重心越高,车辆的动力性能越差。
另一方面,增大车轮直径,可以降低轮轨的接触应力,降低车轮磨耗速度,增加车轮的热容量,提高踏面制动热负荷的承受能力。
因此车轮直径大小应根据车辆情况综合确定。
但总的来说,车辆轴重越大,车轮直径应越大,以提高车轮的热容量和增加轮轨的接触面积,减少踏面损伤和磨耗。
另外,车轮直径的取值还应注意规格的标准化系列问题,以利于车轮制造和检修。
目前我过货车车轮直径大多为840mm,特殊货车车轮直径为915。
二、轮辋轮辋宽度尺寸主要取决于轮轨的搭载量。
当轮对运行在曲线上时,外侧车轮轮缘靠近钢轨,内侧轮缘远离钢轨。
只有内侧车轮踏面在钢轨上的搭载量足够,才能保证轮对不脱轨。
《铁路技术管理规程》规定,当曲线半径在300m以下时,轨距应加宽15mm。
因此,最大轨距为1435+15+6=1456mm(其中:名义轨距L为1435mm,最大公差为6mm)。
轮对最小内侧距为1354mm,轮缘最小厚度为23mm。
车轮踏面外侧倒角5mm,钢轨头部圆弧半径为R13mm,钢轨内侧磨耗2mm,轨枕弯曲、道钉松动等引起轨距扩大8mm,重车时车轴微弯引起轮对内侧距离减小2mm,轮轨安全搭载量按7mm考虑,根据上述数据算得轮辋最小宽度为120mm,考虑到车辆过驼峰时实施的制动,车轮外侧面磨损5mm,则轮辋最小宽度应为125mm。
目前我国铁路货车车轮轮辋宽度为135~140mm。
轮辋厚度通常指新轮辋厚度。
我国铁路对正常服役的车轮的判废依据是轮辋剩余厚度,当轮辋剩余厚度小于等于23mm时车轮报废。
新轮辋厚度与轮辋限度之差为轮辋的有效磨耗厚度。
轮辋越厚有效磨耗厚度就越大。
但车轮自重也大。
有效磨耗厚度越厚,车轮使用寿命越长,新旧车轮直径差就越大。
轮对

轮对轮对的分类及其标记轮对的类型和名称,应根据车轮和车轴类型而定。
货车标准滑动轴承轮对型号与车轴、车轮三者型号完全一致;标准滚动轴承轮对型号与车轴型号一致,其车轮即为普通相应吨位的车轮。
客车滚动轴承轮对型号与车轴型号一致,车轮为相应吨位客车车轮。
非标准轮对型号的确定与标准轮对相似。
轮对的标记包括车轴标记、车轮标记和轮对标记三部分。
车轴的标记:车轴制成以后,在车轴一端的任意1/3圆内,刻打一“左”字做为始端并刻打制造标记,车轴的制造标记包括:制造工厂代号、熔炼号码、制造顺序号码(即轴号)、轴型标记、制造年月日。
车轮制造标记:车轮应在辗压成型后的炽热状态下,在其轮辋外侧面刻打制造厂代号、制造年月、制造顺序号码、熔炼号码、轮型等标记。
轮对责任钢印:凡轮对组装,车轴横裂纹处理等均应在轴端刻打责任钢印。
其刻打方法是:第一次责任钢印刻打在制造钢印旁,即按顺时针方向的第二个三角形面内,以后各项顺序刻打,一端用完可在另一端刻打,第六次刻打完时,应磨去第一次的责任钢印后继续刻打。
轮对的责任钢印内容应包括:责任厂或段代号、检查员钢印、验收员钢印、年月日,此外,根据具体修程内容应分别刻打专门钢印。
凡有轴型、轴号、“左”或表示横向裂纹标记“艹”代号者,均需永久保留,直至该车轴报废为止。
车轮踏面设计成斜度的理由及踏面磨耗的主要过程以往车轮外形成锥形,即踏面具有一定的斜度,主要是由于:1、当车辆通过曲线时,虽然外轨比内轨长,但因离心作用,轮对偏向外轮运行,外侧车轮在钢轨上滚动部分的直径较内侧车轮为大,使外侧车轮比内侧车轮滚动的距离大,利用此滚动部分的直径大小不同以适应内、外轨长短不同的特点,减小了车轮在轨面上的滑动,使车辆顺利地通过曲线。
2、由于踏面具有一定斜度,且靠轮缘处为1/20,靠车轮外侧有1/10的斜度。
踏面外侧制成1/10的斜度,这使车轮外侧直径更为减少,以便通过更小的曲线半径。
因为此段斜度仅在较小半径的曲线上运行时才会使用,故磨耗较小。
第二章轮对

2. 轮对的基本要求
应有足够的强度,以保证在容许的最高速度和最大载 荷下安全运行; 应在强度足够和保证一定使用寿命的前提下,使其重 量最小,并具有一定弹性,以减小轮轨之间的相互作 用力; 应具备阻力小和耐磨性好的优点,这样可以只需要较 少的牵引动力并能提高使用寿命; 应能适应车辆直线运行,同时又能顺利通过曲线,还 应具备必要的抵抗脱轨的安全性。
第二章 轮对
3. 轮箍轮 由轮箍、轮心和扣环组成,安全性差,已很少使用。
4. 高速轻型车轮 主要特点:轮辋、辐板、轮毂壁厚薄,优化的踏面和辐 板外形。 对车轮的加工精度及质量均衡性提出了更高的要求。
第二章 轮对
5. 弹性车轮 主要优点:可减小车辆簧下部分质量,降低轮轨力,缓 和冲击,提高列车运行平稳性,改善车轮与车轴的运 用条件,减小磨耗和噪声。
第二章 轮对
五、轮对内侧距离与轨道的关系
3.安全通过辙叉。《铁路技术管理规程》规 定,辙叉心作用面至护轮轨头部外侧的距 离不小于1391 mm,而辙叉翼轨作用面至护 轮轨头部外侧的距离不大于1348 mm。为此 要求:
(1) 轮对最大内侧距 离加上一个轮缘厚 度应小于或等于 1391 mm,如大于 1391 mm,车轮将骑 入辙叉的另一侧, 导致脱轨; (2) 轮对最小内侧距 离应大于1348 mm, 否则,轮缘内侧面 将被护轮轨挤压, 不能安全通过道岔。
拉伸强度:在拉伸试验中,试样直至断裂为止所受的最大 拉伸应力。
伸长率:即延伸率,指材料在拉伸断裂后,总伸长(伸长量)与 原始标距长度的百分比。
冲击值αk:表示材料在冲击载荷作用下抵抗变形和断裂的 能力。一般把αk值低的材料称为脆性材料, αk值高的材 料称为韧性材料。 第二章 轮对
火车轮结构基础知识

车轮结构完全由车轮直径,轮辋,轮毂尺寸,毂辋距,辐板形状,轮缘踏面外形所决定。
每个尺寸或每部位形状都有其特殊意义。
一、直径车轮直径对其本身及整个车辆都有较大影响。
一方面车轮直径越大,车辆重心越高,车辆的动力性能越差。
另一方面,增大车轮直径,可以降低轮轨的接触应力,降低车轮磨耗速度,增加车轮的热容量,提高踏面制动热负荷的承受能力。
因此车轮直径大小应根据车辆情况综合确定。
但总的来说,车辆轴重越大,车轮直径应越大,以提高车轮的热容量和增加轮轨的接触面积,减少踏面损伤和磨耗。
另外,车轮直径的取值还应注意规格的标准化系列问题,以利于车轮制造和检修。
目前我过货车车轮直径大多为840mm,特殊货车车轮直径为915。
二、轮辋轮辋宽度尺寸主要取决于轮轨的搭载量。
当轮对运行在曲线上时,外侧车轮轮缘靠近钢轨,内侧轮缘远离钢轨。
只有内侧车轮踏面在钢轨上的搭载量足够,才能保证轮对不脱轨。
《铁路技术管理规程》规定,当曲线半径在300m以下时,轨距应加宽15mm。
因此,最大轨距为1435+15+6=1456mm(其中:名义轨距L为1435mm,最大公差为6mm)。
轮对最小内侧距为1354mm,轮缘最小厚度为23mm。
车轮踏面外侧倒角5mm,钢轨头部圆弧半径为R13mm,钢轨内侧磨耗2mm,轨枕弯曲、道钉松动等引起轨距扩大8mm,重车时车轴微弯引起轮对内侧距离减小2mm,轮轨安全搭载量按7mm考虑,根据上述数据算得轮辋最小宽度为120mm,考虑到车辆过驼峰时实施的制动,车轮外侧面磨损5mm,则轮辋最小宽度应为125mm。
目前我国铁路货车车轮轮辋宽度为135~140mm。
轮辋厚度通常指新轮辋厚度。
我国铁路对正常服役的车轮的判废依据是轮辋剩余厚度,当轮辋剩余厚度小于等于23mm时车轮报废。
新轮辋厚度与轮辋限度之差为轮辋的有效磨耗厚度。
轮辋越厚有效磨耗厚度就越大。
但车轮自重也大。
有效磨耗厚度越厚,车轮使用寿命越长,新旧车轮直径差就越大。
轮对基础知识

第一章轮对基础知识1.1轮对的作用及组成轮对是转向架主要部件之一。
它的功能是最终承受车辆的自重与载重,并通过轮对在钢轨上滚动完成车辆的运行。
它的运用条件十分恶劣,经常发生擦伤、剥离、掉块、热裂和疲劳损坏等情况。
其性能的好坏,对行车安全具有十分重大的影响。
轮对是由一根车轴和两个相同的车轮组成,如图1-1所示,在轮轴接合部位采用过盈配合,使两者牢固地结合在一起,为保证安全,绝不允许有任何松动现象发生。
图1-1 轮对的构成1—车轴;2—车轮我国铁路车辆上主要采用的是碾钢整体车轮,简称碾钢轮,以碾钢轮为例,车轮各部分的名称及作用如图1-2所示。
(1)踏面:车轮与钢轨面相接触的外圆周面,具有一定的斜度。
踏面与轨面在一定的摩擦力下完成滚动运行。
(2)轮缘:车轮内侧面的径向圆周突起部分,称为轮缘。
其作用是防止轮对脱轨,保证车辆在直线和曲线上安全运行。
(3)轮辋:车轮具有完整踏面的径向厚度部分,以保证踏面内具有足够的强度,同时也便于加修踏面。
(4)轮毂:车轮中心圆周部分,固定在车轴轮座上,是整个车轮结构的主干与支承。
(5)轮毂孔:用于车轴的安装,该孔与车轴轮座部分直接固结在一起。
(6)轮辐板:连接轮辋与轮毂的部分,呈板状者称为辐板,辐板呈曲面状,使车轮具有一定弹性,使力在传递时较为缓和。
(7)辐板孔:为了便于加工和吊装轮对而设置,每个车轮上有两个辐板孔。
由于在辐板孔周围容易产生裂纹,同时还影响车轮的平衡性能,因此在S 形辐板的车轮上已取消辐板孔。
图1-2 整体轮的各部分组成1— 踏面 2—轮缘 3—轮辋 4—轮毂 5—轮毂孔 6—辐板 7—辐板孔1.2车轮的类型和轮对型号1.2.1车轮类型车轮按其构造可以分为带箍车轮和整体车轮,带箍车轮在我国铁道车辆上已经被整体车轮所取代。
车轮按其材质可以分为碾钢车轮和铸钢车轮。
碾钢轮最大的优点是强度高,韧性好,适应速度高的要求,其次是自重低,轮缘磨耗后可以堆焊,踏面磨耗后可以镟修,维修费用低,碾钢轮的缺点是制造技术较复杂,设备投资较大,踏面耐磨性较差等。
轮对(车辆构造与检修课件)

二、轮对的作用及结构
5
车轮
车轮分类:
➢ 按用途分类:客车车轮、货车车轮、机车车轮
➢ 按结构分类:整体轮(碾钢轮、铸钢轮)、轮毂 轮
➢ 新型车轮:弹性车轮、S型辐板轮
二、轮对的作用及结构
5
车轮
车轮分类:
➢ 1、碾钢整体轮
➢ 简称辗钢轮,是由钢锭或轮坯经加热碾轧而成 ,并经过淬火热处理。
➢ 优点:强度高、韧性、自重轻,能适应载重大 运行速度高的要求;维修费用低。
有一定的弹性——减少轮轨间作用力、噪音。 车轴与车轮结合牢固。 应具备阻力小和耐磨性好的优点,减少牵引力并
提高寿命。 适应车辆直线及曲线运行,并具备必要的抵抗脱
轨的安全性。
二、轮对的作用及结构 3 轮对组成结构
二、轮对的作用及结构 3 轮对组成结构
轮对是由1根车轴和2个车轮,通过过盈配合,采用冷压装连接 在一起的。(轮对压装)
轴颈
轴颈
二、轮对的作用及结构
4
车轴
轮座:安装车轮。受力最大、直径最大。
轮座
二、轮对的作用及结构
4
车轴
防尘板座: 防尘板座是车轴与防尘板配合的 部位,其直径比轴颈直径大、比轮座轴颈小, 是轴颈与轮座的中间过渡部位,以减少应力 集中。
防尘板座
防尘板座
轴身
二、轮对的作用及结构
4
车轴
二、轮对的作用及结构
A、失去标准轮廓、踏面锥度变大、蛇形运动频率增高——平稳 性降
B、过道岔,车轮由基本轨向尖轨过渡,产生上下跳动、易砸伤 尖轨,并引起脱轨
四、轮对的故障
2 车轮的故障
踏面故障:
(1)踏面圆周磨耗: ➢ 检修限度:
客:厂、段≤ 0.5 货:厂≤ 3、段≤ 5
轮对制图期末总结
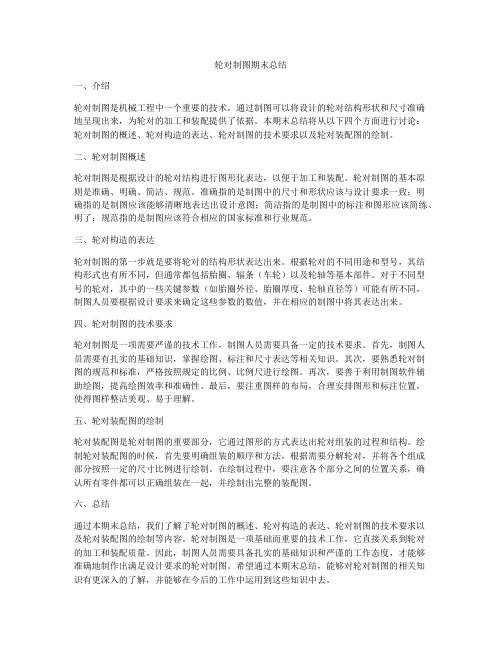
轮对制图期末总结一、介绍轮对制图是机械工程中一个重要的技术,通过制图可以将设计的轮对结构形状和尺寸准确地呈现出来,为轮对的加工和装配提供了依据。
本期末总结将从以下四个方面进行讨论:轮对制图的概述、轮对构造的表达、轮对制图的技术要求以及轮对装配图的绘制。
二、轮对制图概述轮对制图是根据设计的轮对结构进行图形化表达,以便于加工和装配。
轮对制图的基本原则是准确、明确、简洁、规范。
准确指的是制图中的尺寸和形状应该与设计要求一致;明确指的是制图应该能够清晰地表达出设计意图;简洁指的是制图中的标注和图形应该简练、明了;规范指的是制图应该符合相应的国家标准和行业规范。
三、轮对构造的表达轮对制图的第一步就是要将轮对的结构形状表达出来。
根据轮对的不同用途和型号,其结构形式也有所不同,但通常都包括胎圈、辐条(车轮)以及轮轴等基本部件。
对于不同型号的轮对,其中的一些关键参数(如胎圈外径、胎圈厚度、轮轴直径等)可能有所不同,制图人员要根据设计要求来确定这些参数的数值,并在相应的制图中将其表达出来。
四、轮对制图的技术要求轮对制图是一项需要严谨的技术工作,制图人员需要具备一定的技术要求。
首先,制图人员需要有扎实的基础知识,掌握绘图、标注和尺寸表达等相关知识。
其次,要熟悉轮对制图的规范和标准,严格按照规定的比例、比例尺进行绘图。
再次,要善于利用制图软件辅助绘图,提高绘图效率和准确性。
最后,要注重图样的布局,合理安排图形和标注位置,使得图样整洁美观、易于理解。
五、轮对装配图的绘制轮对装配图是轮对制图的重要部分,它通过图形的方式表达出轮对组装的过程和结构。
绘制轮对装配图的时候,首先要明确组装的顺序和方法,根据需要分解轮对,并将各个组成部分按照一定的尺寸比例进行绘制。
在绘制过程中,要注意各个部分之间的位置关系,确认所有零件都可以正确组装在一起,并绘制出完整的装配图。
六、总结通过本期末总结,我们了解了轮对制图的概述、轮对构造的表达、轮对制图的技术要求以及轮对装配图的绘制等内容。
轮对基础知识
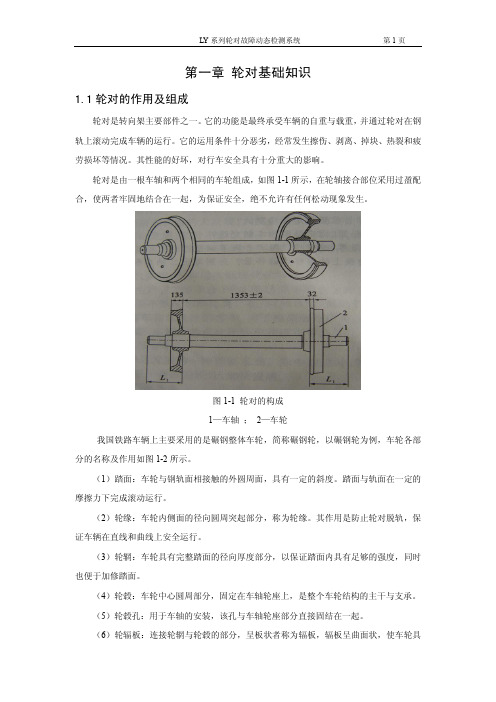
LY 系列轮对故障动态检测系统
第9页
化小,这对保证车辆运行平稳很有利。特别是高速车辆,如日本东海道新干线采用 1:40 锥 形外形,据此确定了悬挂参数,但 1:40 外形很快磨耗,为保证车辆平稳,必须每 3 万公里 就必须镟修踏面,增加了维修成本。欧洲的法国、德国、英国等国家的高速车辆都用磨耗型 踏面,毋须经常镟轮。近年来,日本开发的高速车也采用了磨耗型踏面。
950 mm。我国碾钢整体车轮形式和基本尺寸如图 1-3、图 1-4 和表 1-1、表 1-2 所示。
LY 系列轮对故障动态检测系统
第3页
图 1-3 碾钢整体车轮形式和基本尺寸 (GB 8601—1988)
表 1-1:铸钢整体车轮基本尺寸(GB 8601——1988) 规格型号 外 径D 轮 辋 内 侧 直 径 轮 毂 孔 径 轮 毂 外 径 毂 长 L 辋 宽 H 毂 辋 距 E R40 处 R50 处 辐板厚度 轮 毂 斜 度 轮 辋 斜 度 理论 重量 (kg)
LY 系列轮对故障动态检测系统
第7页
2、磨耗型踏面 在长期使用过程中发现,锥形踏面每次镟削后出现踏面外形与钢轨顶部断面形状不匹 配、运用初期磨耗较快、镟削时无益切销量大等问题。同时发现一个规律:不论车轮踏面初 始形状如何,经过运用磨耗后,将趋向一个“稳定形状” ,而在形状稳定之后,磨耗将减缓。 世界各国都对这种“稳定形状”的新型外形进行了研究,各国称呼不一,有的叫磨耗型,有 的叫圆弧形或曲形, 也有的叫凹形。 在认识了锥形踏面存在的问题和掌握了踏面磨耗规律后,
图 1-1 轮对的构成 1—车轴 ; 2—车轮 我国铁路车辆上主要采用的是碾钢整体车轮,简称碾钢轮,以碾钢轮为例,车轮各部 分的名称及作用如图 1-2 所示。 (1)踏面:车轮与钢轨面相接触的外圆周面,具有一定的斜度。踏面与轨面在一定的 摩擦力下完成滚动运行。 (2)轮缘:车轮内侧面的径向圆周突起部分,称为轮缘。其作用是防止轮对脱轨,保 证车辆在直线和曲线上安全运行。 (3)轮辋:车轮具有完整踏面的径向厚度部分,以保证踏面内具有足够的强度,同时 也便于加修踏面。 (4)轮毂:车轮中心圆周部分,固定在车轴轮座上,是整个车轮结构的主干与支承。 (5)轮毂孔:用于车轴的安装,该孔与车轴轮座部分直接固结在一起。 (6)轮辐板:连接轮辋与轮毂的部分,呈板状者称为辐板,辐板呈曲面状,使车轮具
轮对知识

这几种轴型的标准轴重见右列表 * 轴重:指每轴所承受的载重量。
其中: RD3、 RD4 型车轴既可用于客车,也可用于货车 —— 冷藏车。 RC4、 RD4 型为发电机传动车轴,在车轴的一端设有发电机皮带 轮的安装轴。
客车车轴的基本尺寸
客车车轴特别是盘形轮对车轴对尺寸的精确度要求都非常严 格。 作为基础培训,可参看《 铁道车辆技术》教材 P31 ~ P32 图、表中所列各项基本尺寸加以了解。 作为常识来讲,应主要熟悉车轴的轴颈尺寸、防尘板座尺 寸、轴颈中心距尺寸、车轴全长,以方便从外观上辩别不同类型 的车轴。(以 RD3 型车轴为例 —— 看下列图示)
货车车轴
因轴颈尺寸公差、形位公差要求严格,必须采用机加工和
磨削加工,而我国70年代还没有成型磨削设备,不得已采用
了轴颈根部卸荷槽这种型式。 1977年修订车轴标准时,因轴承已定型,轴颈规格不能改 动,仅将该型车轴的轮座增大到 194mm,轴身相应增大到 174mm,全加工。因当时国内仍无成型磨削设备,故仍采
过渡(一般采取圆滑过渡)。 为了提高车轴的疲劳强度 ,长期以来一直采用滚压强化加工法轴颈 、防
尘板 、轮座进行精加工。现已采用 成型磨 进行精加工。
为了便于在车床对车轴进行机加工,在车轴轴颈两端面均制有中心孔 。
圆滑过渡
* 滑动轴承车轴
滑动轴承车轴与滚动轴承车轴大体相似,但在外观上滑动轴承车轴的轴颈 两端 设有轴领 (如图示),其余各部的名称及作用与滚动轴承车轴基本相同。
●
货车车轴
因RE2 型车轴载荷中心距短,增加了转向架结
构的设计难度,加上早期设计的197730型轴承比
较笨重,所以该车轴仅进行了装车运用试验而未
大量推广使用。
货车车轴
轮对装置的名词解释

轮对装置的名词解释轮对装置是指在铁路车辆中,将车轮与车体连接起来的机械装置。
它是铁路运输中不可或缺的关键部件,承担着支撑车体重量、传递牵引力和制动力、减震缓冲等多项功能。
本文将对轮对装置的组成、作用以及相关技术进行解释。
轮对装置主要由车轮、轮轴、轴承和轮轴箱组成。
车轮是负责与铁轨接触以提供支撑和传递力的部件。
它由高强度钢材制成,通过热处理和机械加工等工艺获得所需的硬度和精度。
轮轴则是将车轮连接到车体的关键组件,负责承载车体重量和传递功率。
一般情况下,轮轴由碳素钢材制成,具有较高的强度和耐久性。
轴承在轮对装置中起到支撑和减少摩擦的作用。
它通常由滚子轴承或滑动轴承构成。
滚子轴承利用滚子在内外圈之间滚动,减小了接触面积,从而减少了滑动摩擦。
滑动轴承则利用润滑油或润滑脂来减小轴承与轮轴的摩擦,使其能够更顺畅地旋转。
轮轴箱是保护轮轴和轴承的重要部件。
它通常由铸铁或铸钢制成,具有较高的强度和刚度。
轮轴箱内包含轴承座,将轴承安装在其中,并通过密封装置保护轴承免受到外部灰尘和水分的侵入。
轮轴箱还具有导向轴承的作用,使轮轴旋转时能够保持正确的轴向位置。
轮对装置在铁路运输中发挥着至关重要的作用。
首先,它承担着支撑车体重量的任务。
当车辆行驶时,轮对装置通过车轮和轮轴将车体的重量传递到铁轨上。
同时,轮对装置还能传递动力和制动力。
通过牵引力传递装置(如牵引电机、传动装置等),车轮能够将机车或车厢的动力传递到铁轨上,从而推动车辆运行。
而在制动过程中,制动装置通过对车轮施加阻力,将车辆的动能转化为热能,实现制动效果。
此外,轮对装置还能起到一定的减震和缓冲效果。
当车辆通过不平的铁轨时,轮对装置可以减少车体受到的震动和冲击,提高乘坐舒适性。
为了进一步提高减震效果,一些轮对装置还采用了悬挂系统,通过弹簧和减震器来吸收冲击力,减少对车体和乘客的影响。
随着铁路技术的不断发展,轮对装置也在不断改进和创新。
例如,一些现代化的高速列车采用了空心轮轴和磁浮轮轴技术,使列车能够以更高的速度行驶,并提高了运行的平稳性和舒适性。
- 1、下载文档前请自行甄别文档内容的完整性,平台不提供额外的编辑、内容补充、找答案等附加服务。
- 2、"仅部分预览"的文档,不可在线预览部分如存在完整性等问题,可反馈申请退款(可完整预览的文档不适用该条件!)。
- 3、如文档侵犯您的权益,请联系客服反馈,我们会尽快为您处理(人工客服工作时间:9:00-18:30)。
第1页
第一章 轮对基础知识
1.1 轮对的作用及组成
轮对是转向架主要部件之一。 它的功能是最终承受车辆的自重与载重, 并通过轮对在钢 轨上滚动完成车辆的运行。它的运用条件十分恶劣,经常发生擦伤、剥离、掉块、热裂和疲 劳损坏等情况。其性能的好坏,对行车安全具有十分重大的影响。 轮对是由一根车轴和两个相同的车轮组成,如图 1-1 所示,在轮轴接合部位采用过盈配 合,使两者牢固地结合在一起,为保证安全,绝不允许有任何松动现象发生。
图 1-6 轮对在直线上运行 车辆在直线上运行时, 如果轮对中心线与线路中心线不一致时, 造成轮对的两个车轮一
LY 系列轮对故障动态检测系统
第6页
个导前,一个滞后,则导前车轮以踏面外侧小直径圆周滚动,滞后车轮以踏面内侧大直径圆 后滚动。因此,同样转数,导前车轮滚动距离短,滞后车轮滚动距离长,从而自动纠正两车 轮位置,使两车轮重新处于平行或前后变位,以减少轮缘磨耗,如图 1-6 所示。 车辆在曲线上运行时,由于离心力的作用,使外轨上的车轮轮缘紧靠钢轨,内轨上的车 轮轮缘则远离钢轨。 于是在外轨上的车轮以踏面内侧大直径圆周滚动, 在内轨上的车轮以踏 面外侧小直径圆周滚动。从而在相同转数内,外轨上的车轮滚动距离长,内轨上的车轮滚动 距离短,正好与曲线上外轨长内轨短相适应,可使两轮同时通过曲线,以减少车轮在钢轨上 滑行,如图 1-7 所示。
LY 系列轮对故障动态检测系统
第2页
有一定弹性,使力在传递时较为缓和。 (7)辐板孔:为了便于加工和吊装轮对而设置,每个车轮上有两个辐板孔。由于在辐 板孔周围容易产生裂纹,同时还影响车轮的平衡性能,因此在 S 形辐板的车轮上已取消辐 板孔。
图 1-2 整体轮的各部分组成 1— 踏面 2—轮缘 3—轮辋 4—轮毂 5—轮毂孔 6—辐板 7—辐板孔
950 mm。我国碾钢整体车轮形式和基本尺寸如图 1-3、图 1-4 和表 1-1、表 1-2 所示。
LY 系列轮对故障动态检测系统
第3页
图 1-3 碾钢整体车轮形式和基本尺寸 (GB 8601—1988)
表 1-1:铸钢整体车轮基本尺寸(GB 8601——1988) 规格型号 外 径D 轮 辋 内 侧 直 径 轮 毂 孔 径 轮 毂 外 径 毂 长 L 辋 宽 H 毂 辋 距 E R40 处 R50 处 辐板厚度 轮 毂 斜 度 轮 辋 斜 度 理论 重量 (kg)
1.2 车轮的类型和轮对型号
1.2.1 车轮类型
车轮按其构造可以分为带箍车轮和整体车轮, 带箍车轮在我国铁道车辆上已经被整体车 轮所取代。车轮按其材质可以分为碾钢车轮和铸钢车轮。碾钢轮最大的优点是强度高,韧性 好,适应速度高的要求,其次是自重低,轮缘磨耗后可以堆焊,踏面磨耗后可以镟修,维修 费用低,碾钢轮的缺点是制造技术较复杂,设备投资较大,踏面耐磨性较差等。因此,我国 现在又重新生产新型的铸钢车轮已解决使用整体碾钢轮所存在的不足。 车轮按踏面形状可分为锥形车轮踏面外形(TB 型)和磨耗性车轮踏面外形(LM 型) ,LM 型踏面已取代了 TB 型踏面。车轮按辐板形状可以分为直辐板车轮和 S 形辐板车轮,S 形辐 板车轮是我国近几年研制的新产品, 是新型车轮的发展方向。 我国铁路货车使用的车轮轮径 为 840 mm ,少量使用 915 mm 。我国铁路客车使用的车轮轮径为 915 mm ,少量使用
图 1-7 轮对在曲线上运行 车轮通过道岔时,由于车轮踏面外侧有 1:10 的坡度,当 1:20 的坡度的踏面磨耗后,踏 面外侧与基本轨或翼轨间尚有一定间隙,不至于互相接触而产生作用力,造成障碍,从而可 以安全通过道岔,如图 1-8 所示。
图 1-8 轮对通过道岔 1—翼轨 2—辙叉心 3—间隙 4—踏面磨耗后轮廓 5—踏面原型轮廓
LY 系列轮对故障动态检测系统
第9页
化小,这对保证车辆运行平稳很有利。特别是高速车辆,如日本东海道新干线采用 1:40 锥 形外形,据此确定了悬挂参数,但 1:40 外形很快磨耗,为保证车辆平稳,必须每 3 万公里 就必须镟修踏面,增加了维修成本。欧洲的法国、德国、英国等国家的高速车辆都用磨耗型 踏面,毋须经常镟轮。近年来,日本开发的高速车也采用了磨耗型踏面。
D1
d0
D3
241 273 279 273 105 110 178 135 110
S1
19
S2
25
12o
20o
344 351 353 394
840
HB HD HE
840
710
138 170 186
915
KD
915
785
170
LY 系列轮对故障动态检测系统
第4页
图 1-4 碾钢整体车轮(TB/T 2817—1997)
图 1-10 两种踏面轮轨接触点的位置 A—锥形踏面轮轨接触点位置 B—LM 型踏面轮轨接触点位置 (7)减少热轴、偏磨故障。 转向架、轮对加工中不可能没有误差,如对角线差、相对轴距差、相对轮径差等,若工 艺水平低或检验不严,过大的误差将造成燃(热)轴、轮缘偏磨等故障。弧形踏面等效斜度 大,而且位移越大,斜度上升的越快,从而可减少热轴、偏磨,提高了车辆运行安全性和经 济性。 (8)镟修时金属切削量小。 LM 系列外形与磨耗后的外形相近,镟轮时切削量小,使车轮实现了经济镟削,这已被 实践证明。 3、S 形辐板车轮 铁道部四方车辆研究所, 经过对运用车轮裂损情况的调查, 发现车轮的裂纹故障主要是 轮辋、辐板裂纹。其原因除因制造缺陷所致之外,主要是车轮结构不合理。据对现行客货车
LY 系列轮对故障动态检测系统
第7页
2、磨耗型踏面 在长期使用过程中发现,锥形踏面每次镟削后出现踏面外形与钢轨顶部断面形状不匹 配、运用初期磨耗较快、镟削时无益切销量大等问题。同时发现一Байду номын сангаас规律:不论车轮踏面初 始形状如何,经过运用磨耗后,将趋向一个“稳定形状” ,而在形状稳定之后,磨耗将减缓。 世界各国都对这种“稳定形状”的新型外形进行了研究,各国称呼不一,有的叫磨耗型,有 的叫圆弧形或曲形, 也有的叫凹形。 在认识了锥形踏面存在的问题和掌握了踏面磨耗规律后,
表 1-2:车轮基本尺寸(TB/T 2817——1997) 规格型号 外 径D 轮 辋 内 侧 直 径 轮 毂 孔 径 轮 毂 外 径 毂 长 L 辋 宽 H 毂 辋 距 E R40 处 R50 处 辐板厚度 轮 毂 斜 度 轮 辋 斜 度 理论 重量 (kg)
D1
d0
D3
235 274 274 68 178 135 68
图 1-1 轮对的构成 1—车轴 ; 2—车轮 我国铁路车辆上主要采用的是碾钢整体车轮,简称碾钢轮,以碾钢轮为例,车轮各部 分的名称及作用如图 1-2 所示。 (1)踏面:车轮与钢轨面相接触的外圆周面,具有一定的斜度。踏面与轨面在一定的 摩擦力下完成滚动运行。 (2)轮缘:车轮内侧面的径向圆周突起部分,称为轮缘。其作用是防止轮对脱轨,保 证车辆在直线和曲线上安全运行。 (3)轮辋:车轮具有完整踏面的径向厚度部分,以保证踏面内具有足够的强度,同时 也便于加修踏面。 (4)轮毂:车轮中心圆周部分,固定在车轴轮座上,是整个车轮结构的主干与支承。 (5)轮毂孔:用于车轴的安装,该孔与车轴轮座部分直接固结在一起。 (6)轮辐板:连接轮辋与轮毂的部分,呈板状者称为辐板,辐板呈曲面状,使车轮具
G 3 L3 、 SY10 、 SY30 、 我国 20 世纪 70 年代开始研究设计这种新型磨耗踏面, 先后研制有 SY、
SY50 等多种型号并进行了试验,1984 年对 SY30 型进行了部级鉴定,取名为 LM 型,其中 L
代表“辆”字的汉语拼音第一个字母,M 表示“磨”字的汉语拼音第一个字母意思,其含义 是磨耗型车辆车轮踏面。1985 年开始推广,1987 年上升为标准 TB1967-1987《机车车辆用 车轮磨耗型轮缘踏面外形》 。 磨耗型踏面外形如图 1-9 所示,其轮辋宽度、基准点、基准线及用途、轮缘顶点位置等 与锥形踏面相同,所不同的是踏面采用 R100mm 和 R500mm 及 R220mm 为半径的三段弧线,圆 滑连接成的一条曲线, 并和斜度为 1:8 的一段直线共同组成踏面外形。 轮缘高度是由过基准 点且与车轮内侧面的垂直线到轮缘顶点的距离,标准高度为 27mm。轮缘厚度是由过基准点 且与车轮内侧面的垂直线向轮缘顶点方向 12mm 作一水平线交轮缘内外侧两点之间的距离, 标准厚度为 32mm。
5
LY 系列轮对故障动态检测系统
第5页
48mm 处的点作车轮内侧面的垂直线称为测量线。 由测量线到轮缘顶点的距离称为轮缘高度, 标准高度为 25mm。由测量线向轮缘顶点方向 10mm 作一水平线交轮缘内、外侧两点之间的距 离称为轮缘厚度,标准厚度为 32mm。
图 1-5 锥形踏面外形 (2)踏面设置坡度的理由
S1
19
S2
25
12o
20o
342 348 391
840
HBS HDS
710 710 785
710 710 785
147 186 186
915
KD
1、锥形踏面 (1)锥形踏面基本外形 锥形踏面基本外形如图 1-5 所示。轮辋内、外侧面之间的距离称为轮辋宽度。标准轮辋 宽度为 1350 mm。由于车轮内侧面到踏面上 70mm 处的点叫基准点。由基准点组成的圆周线 叫基准线。基准线的用途是测量车轮直径、轮缘厚度和踏面圆周磨耗深度。车轮踏面由具有 一定坡度的两端直线组成,由车轮内侧面向外 48mm 和 100mm 之间的踏面为 1:20 的坡度, 由车轮内侧面向外 100—135mm 之间的踏面为 1:10 的坡度。 由车轮内侧面向外 16mm 与轮缘外表面的交点为轮缘顶点。由过车轮内侧面到踏面上
LY 系列轮对故障动态检测系统
第 10 页
直辐板车轮所进行的有限元强度计算结果表明,直辐板车轮应力不均,在所有计算工况下, 车轮辐板都出现严重的应力集中现象。 当轮辋磨耗到限时, 在辐板外侧向轮毂过渡处应力已 超过弹性极限,产生塑性变形,降低了车轮强度。辐板应力集中是导致运用中辐板疲劳裂纹 的主要原因之一,辐板孔周边应力集中也容易产生疲劳裂纹。由于直辐板车轮形状不合理, 在制动热负荷作用下还将产生过大的热应力,其数值约为机械应力的 4—6 倍,是运用中车 轮产生裂纹的主要原因。针对这些问题,四方车辆研究所经过分析研究,并借鉴国外先进经 验,设计了改善车轮应力的辐板形状——S 形辐板车轮,见图 1-11。