国外舰船先进制造技术_先进切割技术
船舶制造行业创新的造船技术

船舶制造行业创新的造船技术在当今全球化的经济环境下,船舶制造行业一直在不断寻求创新的方法来提高船舶的安全性、可靠性、效率和经济性。
造船技术是船舶制造过程中最为关键的环节之一,如何通过技术创新来提高造船效率和质量是该行业长期以来一直在探索的问题。
一、数字化制造技术在造船业的应用数字化制造技术是目前制造行业中最受关注的领域之一,它的应用已经从传统制造行业扩展到了船舶制造行业。
数字化制造技术的应用可以大大提高船舶的制造效率和质量。
数字化船舶制造技术包括计算机辅助设计(CAD)、计算机辅助制造(CAM)和计算机辅助工艺规划(CAPP)等领域。
通过数字化设计和生产,可以实现精细化的制造流程和质量控制,提高造船效率并减少成本。
例如使用数字化制造技术,可以通过模拟造船过程来优化船舶的设计和生产,从而达到更好的效果。
二、智能化创新技术在造船业的应用智能化创新技术是船舶制造业实现高效率和高质量制造的一个重要手段。
智能化制造涉及到人工智能、机器学习、自动化控制与机器人等学科的应用,可以大大提高船舶生产的效率和质量。
通过使用智能化创新技术,可以实现船舶制造的全自动化生产和物流管理。
例如,使用智能机器人和自动化技术可以大大提高制造效率和减少制造成本。
此外,智能化创新技术还可以提高制造过程中的安全性和可靠性,自动化控制和机器人技术可以避免意外事故的发生。
三、材料创新技术在造船业的应用材料创新技术是船舶制造行业中的另一个重要的技术领域。
船舶的结构材料通常是钢铁、铝和玻璃纤维等,这些材料经常用于制造船体、船舱和其他重要部分。
然而,这些材料在制造过程中存在某些缺陷,如焊接质量不稳定、脆性等等。
因此,船舶制造业需要不断探索新材料和新的制造技术。
在船舶制造行业中,新材料的应用可以大大提高船体的稳定性、质量和耐用性。
例如,使用新材料可以提高船体强度和硬度,并且减少船体质量,从而提高船舶的速度和能源效率。
此外,新材料还可以提高船舶的使用寿命和可靠性。
船舶制造工艺探索现代船舶建造的先进技术
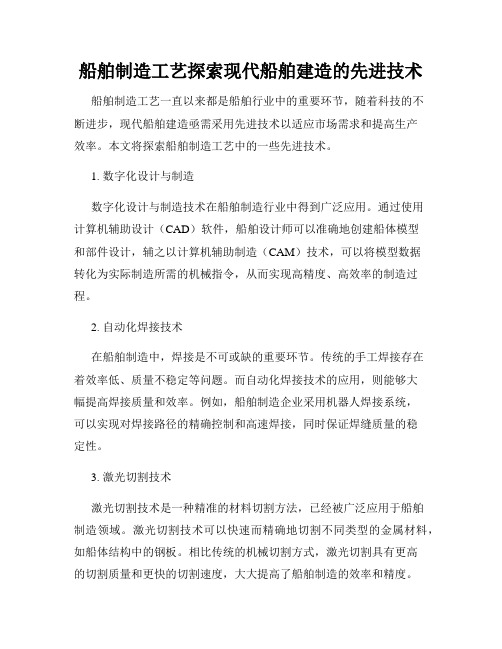
船舶制造工艺探索现代船舶建造的先进技术船舶制造工艺一直以来都是船舶行业中的重要环节,随着科技的不断进步,现代船舶建造亟需采用先进技术以适应市场需求和提高生产效率。
本文将探索船舶制造工艺中的一些先进技术。
1. 数字化设计与制造数字化设计与制造技术在船舶制造行业中得到广泛应用。
通过使用计算机辅助设计(CAD)软件,船舶设计师可以准确地创建船体模型和部件设计,辅之以计算机辅助制造(CAM)技术,可以将模型数据转化为实际制造所需的机械指令,从而实现高精度、高效率的制造过程。
2. 自动化焊接技术在船舶制造中,焊接是不可或缺的重要环节。
传统的手工焊接存在着效率低、质量不稳定等问题。
而自动化焊接技术的应用,则能够大幅提高焊接质量和效率。
例如,船舶制造企业采用机器人焊接系统,可以实现对焊接路径的精确控制和高速焊接,同时保证焊缝质量的稳定性。
3. 激光切割技术激光切割技术是一种精准的材料切割方法,已经被广泛应用于船舶制造领域。
激光切割技术可以快速而精确地切割不同类型的金属材料,如船体结构中的钢板。
相比传统的机械切割方式,激光切割具有更高的切割质量和更快的切割速度,大大提高了船舶制造的效率和精度。
4. 三维打印技术三维打印技术作为一项新兴的先进制造技术,也在船舶制造中得到了尝试。
船舶制造企业可以使用三维打印技术制造船舶组件,通过将材料逐层堆叠来实现船舶部件的快速制造。
利用三维打印技术,不仅可以减少制造成本和时间,而且可以实现更复杂和个性化的设计。
5. 船舶智能制造技术船舶智能制造技术涵盖了多个方面,如物联网、传感器技术、云计算等。
通过将多个智能设备和传感器应用于船舶制造过程中,可以实现生产数据、设备状态等的实时监控和分析。
这有助于船舶制造企业优化生产流程,提高生产效率和产品质量。
综上所述,船舶制造工艺中的先进技术对现代船舶建造具有重要意义。
数字化设计与制造、自动化焊接技术、激光切割技术、三维打印技术以及船舶智能制造技术,都为船舶制造业的发展提供了新的可能性。
船舶先进制造技术

造船企业CIMS的实施 造船企业CIMS的实施 造船C IMS 是运用先进的信息技术、网络技 术、智能技术建立船舶的数字化设计、制 造、管理环境,实现以设计为源头、信息流 为依据、物流控制为主线的 造船设计、制 造、管理一体化数字平台系统!, 对船舶的设 计、制造、管理等活动进行全过程、全系 统的最优控制, 使造船企业实现产品开发设 计、生产制造与过程控制以及管理与经营 决策数字化, 从而为现代造船模式的进一步 深化, 提高船舶企业综合素质和整体效率提 供技术支撑。
造船CIMS总体框架图 造船CIMS总体框架图
CIMS成功实施的主要因素 CIMS成功实施的主要因素
1)项目研制是企业发展自身的需求 2)领导必须直接参与项目的推进 3)正确处理整体和局部的关系 4)扎实的管理是项目推进的基础 5)抓好基础数据收集与分析 6)人员培训是项目实施的保证
造船CIMS的总体框架: 造船CIMS的总体框架: 的总体框架 主要由造船CAD / CAM 设计软件、基于 PDM(产品数据库管理系统)构架产品设计信 息集成系统、生产计划管理系统、劳动力 资源管理系统、船舶质量管理系统、人力 资源管理系统、造船物流管理系统、造船 财务管理系统、船舶成本管理系统、系统 集成和信息交换平台等10个功能部分组成, 参见图1。
先进制造技术是造船业发展的基础
类型和阶段分类,按”中间产品” 类型和阶段分类,按”中间产品”的概念组织造船 的流水和工位固定人员流动的虚拟流水生产。 4)80年代以来,电子计算机技术在造船中应用不 80年代以来, 断拓展,造船精度控制技术和船舶工程管理技术 日臻完善, 使造船业的社会技术的协同机制充分发 挥作用, 实现了以“ 空间分道、时间有序” 为特 征的“壳舾涂一体化” 。即造船的计算机集成制 造系统(CIMS)船厂成为信密集型企业, 是现代 造船的最高水平。
国外舰船先进制造技术_先进切割技术

1999 年俄罗斯海军在核潜艇建造过程的钛合金切 割中, 使用了高压水射流技术, 加工速度大大提高, 加 工精度良好, 减少了后期加工的工作量, 缩短了造船周 期, 已在俄海军造船领域广泛应用。
目前, 氧气等离子切割技术已达到了一个较高的 发展水平, 并普遍应用于国外船舶制造中。例如: 2000 年美国 Mare Island 海军船厂利用 Hyspeed HT2000 氧 离子切割机切割船用材料和电缆, 使得切割碳钢的速 度提高了 50% , 同时采用长寿命氧气等离子弧切割技 术和银正极电极技术, 其切割大多数厚碳钢板速度明 显 快 于 激 光 切 割 和 火 焰 切 割 。 图 1 为 Hypertherm 的 Hyspeed HT2000 氧气等离子切割机工作时的情况。
图 1 Hyspeed HT2000 正在切割示意图
2000 年英国著名的军船制造企业沃斯帕·桑尼克 罗夫特造船公司引进数控氧气等离子切割机, 在加工 厚 l6mm 的船体零件和建造用的各种样板时, 预涂底漆 的钢板割后漆膜无损坏, 且零件精度高, 非常平整。
2002 年美国某船舶修造有限公司将氧气等离子切 27
等离子切割除可切割碳钢外, 还可用于切割不锈钢、 铝、铜等金属。 1.3 氧气等离子切割技术特点
与传统的氧乙炔、等离子弧切割技术相比, 该技术 手段的优越性表现在: (1) 无挂渣, 切割速度快, 切割范 围大, 切口质量好; (2) 切缝狭窄, 切口窄面平整光洁, 热影响区小, 无表面氮化现象, 切割后的工件具有良好 的焊接和加工性能; (3) 工件变形度低, 切割厚、薄板均 不变形; (4) 相同电源功率下切割速度可提高 30% , 而 且具有显著的节能效果, 是目前较为理想的热切割设 备; (5) 操作简单, 容易掌握, 使用安全, 切割成本低。 1.4 氧气等离子切割技术的应用实例
船舶工业中的先进制造技术与工艺

船舶工业中的先进制造技术与工艺随着科技的不断发展与进步,船舶工业中也出现了越来越多的先进制造技术和工艺。
这些技术和工艺对于提高船舶制造效率、优化产品质量以及保证安全性都发挥了巨大的作用。
本文将就船舶工业中的先进制造技术与工艺进行详细的探讨。
1. 3D打印技术随着3D打印技术的日益成熟,其在船舶制造行业中已经得到了广泛的应用。
利用3D打印技术,可以实现零部件的快速制造,极大地提高了制造效率。
同时,该技术还可以减少零部件的重量,提高船舶的载重量。
此外,3D打印技术可以创建更加复杂的零部件,并且可以制造出更具创新性的设计。
2. 数控制造技术数控制造技术是船舶制造行业中一项非常重要的技术。
该技术可以实现复杂零部件的精密加工,提高了工作效率。
同时,数控技术可以保证零部件制造的精度,从而提高了产品质量。
此外,数控机床还具有自动化的特点,能够减少人工干预,提高了生产效率。
3. 脉冲功率激光焊接技术脉冲功率激光焊接技术是一项非常先进的船舶制造技术。
利用该技术可以实现高质量焊接,同时还可以减少对工件的影响,从而减轻了工件的变形程度。
此外,脉冲功率激光焊接技术还可以保证焊接的速度,从而提高了生产效率。
该技术在船舶制造行业中的应用已经越来越广泛。
4. 无损检测技术无损检测技术是船舶制造行业中非常重要的一项技术。
通过无损检测技术可以快速发现隐蔽的缺陷,保证产品的质量。
同时,该技术还可以避免对产品结构的影响,从而降低了零部件的损坏程度。
船舶制造行业中的无损检测技术已经得到了广泛的应用。
5. 氧化铝堆焊技术氧化铝堆焊技术是船舶制造行业中一项非常实用的技术。
利用该技术可以快速对船舶上的零部件进行堆焊,从而提高了产品的质量。
氧化铝堆焊技术还可以保证零部件之间的相互匹配,并且能够保证产品的密封性。
该技术的应用已经得到了船舶制造业的广泛认可。
6. 摩擦振动焊接技术摩擦振动焊接技术是船舶制造行业中的一项非常新颖的技术。
该技术可以实现高效、快速的焊接,同时还可以保证产品的质量。
国内外先进制造技术
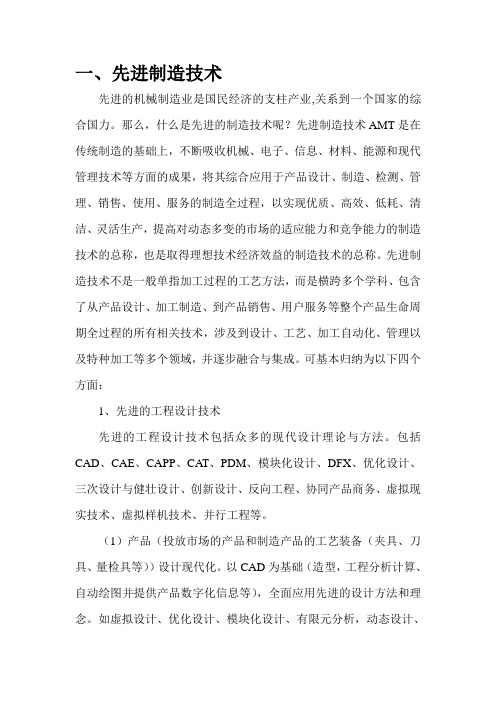
一、先进制造技术先进的机械制造业是国民经济的支柱产业,关系到一个国家的综合国力。
那么,什么是先进的制造技术呢?先进制造技术AMT是在传统制造的基础上,不断吸收机械、电子、信息、材料、能源和现代管理技术等方面的成果,将其综合应用于产品设计、制造、检测、管理、销售、使用、服务的制造全过程,以实现优质、高效、低耗、清洁、灵活生产,提高对动态多变的市场的适应能力和竞争能力的制造技术的总称,也是取得理想技术经济效益的制造技术的总称。
先进制造技术不是一般单指加工过程的工艺方法,而是横跨多个学科、包含了从产品设计、加工制造、到产品销售、用户服务等整个产品生命周期全过程的所有相关技术,涉及到设计、工艺、加工自动化、管理以及特种加工等多个领域,并逐步融合与集成。
可基本归纳为以下四个方面:1、先进的工程设计技术先进的工程设计技术包括众多的现代设计理论与方法。
包括CAD、CAE、CAPP、CAT、PDM、模块化设计、DFX、优化设计、三次设计与健壮设计、创新设计、反向工程、协同产品商务、虚拟现实技术、虚拟样机技术、并行工程等。
(1)产品(投放市场的产品和制造产品的工艺装备(夹具、刀具、量检具等))设计现代化。
以CAD为基础(造型,工程分析计算、自动绘图并提供产品数字化信息等),全面应用先进的设计方法和理念。
如虚拟设计、优化设计、模块化设计、有限元分析,动态设计、人机工程设计、美学设计、绿色设计等等;(2)先进的工艺规程设计技术与生产技术准备手段。
在信息集成环境下,采用计算机辅助工艺规程设计、即CAPP,数控机床、工业机器人、三坐标测量机等各种计算机自动控制设备设备的计算机辅助工作程序设计即CAM等。
2、先进制造工艺技术(1)高效精密、超精密加工技术,包括精密、超精密磨削、车削,细微加工技术,纳米加工技术。
超高速切削。
精密加工一般指加工精度在10~0.1μm(相当于IT5级精度和IT5级以上精度),表面粗糙度Ra值在0.1μm以下的加工方法,如金刚车、金刚镗、研磨、珩磨、超精研、砂带磨、镜面磨削和冷压加工等。
韩国先进造船技术

(Automatic Design & Engineering System )
z UAIS
(Universal Automatic Identification System)
z CSDD (Complete Set of
Data/Drawing/Document)
(意识变化、提高业务处理能力) ¾ 传授知识/经验
提高 生产量、 生产率,
缩短 纳期
5
增加 销售额,
节減 成本
2. GEO-PRO CIMS的目标
 为达成目标而要同时解决的课题
经
营
明确经营目标: 提出中长期设想,制订中长期计划
生产计划
建立计划体系: 总体规划,建立网络,先行中日程等
设备/装备 设施/装备的阶段别构筑: 新投资、固定设备、运营装备、各种胎架及工具
z 实时监控管理 (共享全公司信息,管理数据)
z 各模块的联系(设计、物资、生产) (实时联系)
z 缩短业务处理时间、分析容易
z 负荷平衡 (关键途径瓶颈)
z确保管理的客观性、透明性 (金额支付、库存、进度率、 外包管理等)
¾ 制订标准准则 ¾ 制订业务流程 ¾ 提高管理能力(运营、方法、目标) ¾ 业务推进指导( 咨询 ) ¾ 学习组织化
10
4. CIMS 的特点
GEO-PRO CIMS和其他ERP有什么不一样 ?
根据造船、海洋领域特点,特别开发的CIMS Package
包含韩国主要造船厂的造船管理理念和最佳的方法 灵活运用标准(船种等)数据,简化数据输入, 最少化键入工 作,使操作简单易行 使用符合造船业务特点的执行方法,使之在短时间内容 易应用 以3-Tier 体系结构处理大容量/复杂的数据 分散负荷 可容易设立编码体系 (运用GEOSM 标准编码体系和样品 数据)
造船焊接与切割技术-PPT课件

机器人切割可以提高切割效率、降低人工成本,同时提高切割精度和一致性。随 着机器人技术的不断发展,机器人切割的应用范围也将越来越广泛。
提高焊接与切割技术的安全性和环保性
安全防护措施
在焊接与切割过程中,应采取有效的 安全防护措施,如佩戴防护眼镜、手 套等,以保障操作人员的安全。
环保措施
焊接与切割过程中会产生烟尘、废气 等污染物,应采取有效的环保措施, 如安装烟尘净化器、废气处理装置等 ,以减少对环境的污染。
压力焊接
包括超声波焊、摩擦焊等,适用于金 属材料和部分非金属材料。
焊接工艺流程
2. 预热
根据材料和焊接方 法选择预热温度。
4. 后处理
清理焊缝、检查、 修整等。
准备
清理焊缝、装配、 固定等。
3. 焊接
按照工艺要求进行 焊接操作。
5. 质量检测
确保焊接质量符合 要求。
焊接质量检测与控制
01
02
铝合金
铝合金具有轻质、高强度等优点,在船舶制造中应用越来越 广泛,但铝合金的焊接与切割技术难度较大,需要解决铝合 金的氧化膜、热导率等问题。
智能化焊接与切割技术的发展趋势
自动化焊接
自动化焊接可以提高焊接效率、降低人工成本,同时减少人为因素对焊接质量的 影响。目前,自动化焊接已经在造船行业中得到了广泛应用。
03
04
外观检测
通过目视或放大镜对焊缝进行 外观检查。
无损检测
利用射线、超声波、磁粉等方 法检测焊缝内部缺陷。
力学性能检测
对焊接接头进行拉伸、弯曲、 冲击等试验,检测其力学性能
。
焊接工艺评定
根据产品要求和焊接工艺流程 ,对焊接接头进行综合评价,
船舶先进制造技术参考资料

一、现代造船模式的基本概念及原理(成组技术、产品导向型工程分解、区域舾装、管件族制造、中间产品、船体分道建造、区域涂装、壳舾涂一体化等)现代造船模式的涵义所谓现代造船模式,可理解为以统筹优化理论为指导,应用成组技术原理,以中间产品为导向,按区域组织生产,壳(船体建造)、舾、涂作业在空间上分道,时间上有序,实现设计、生产、管理一体化,均衡、连续地总装造船.现代造船模式形成的技术基础—成组技术与系统工程技术在造船中应用阐述如下:先进制造技术在现代造船模式中的应用(1)成组技术。
首先应用于机械制造业,利用零件的相似性来组织多品种小批量生产,以获得少品种大批量的生产效率。
成组技术被应用于船舶建造工程,导致了中间产品分类成组加工和管件族加工方法的产生,形成了船体分道建造生产线;成组技术中短间隔期、小批量的生产管理方法形成了船舶建造作业的托盘管理。
(2)产品导向型工程分解。
是按中间产品生产特征分解组织生产的形式,是按总系统、各分系统、系统/区域、区域/类型/阶段而成组,再把这些成组法分别用干基本设计,功能设计、转换设计和施工设计中。
这样可将不同系统的专业人员分配到专门负责某个产品级别的组里,以改善组里的横向关系、简化生产顺序、提高生产效率。
产品导向型工程分解既可用于设计和材料的选定,也可用干生产和控制。
实现壳舾涂一体化,指以“船体为基础,舾装为中心、涂装为重点”的管理思想,把壳(船体)、舾(舾装)、涂(涂装)不同性质的三大作业类型,建立在空间上分道、在时间上有序的立体优化排序。
(3)区域舾装。
新的舾装概念:把船壳视作载体,为造船厂生产主体,往船壳上安装的一切物件都叫作舾装件。
以后发展按区域划分进行舾装作业划分的,分为机舱舾装和除机舱以外的船体舾装、加上跟踪涂装和每阶段交工之前的精细整修等,确立了舾装的全新概念。
如上所述,按照区域划分进行舾装作业的舾装方法便称为区域舾装。
但是严格地说,区域舾装的定义是不够完整的,叫区划舾装更确切些,这里的“区划”是指除了空间要有划分外,在时间上也要有划分,才能使区域舾装的概念更加完整。
发达国家的造船工艺有哪些

发达国家的造船工艺有哪些发达国家的造船工艺包括多种先进技术和工程方法,下面将介绍其中一些主要的造船工艺。
1. 数字化设计和制造:发达国家采用计算机辅助设计(CAD)和计算机辅助制造(CAM)技术,实现船舶的数字化设计和制造。
这些技术可以提高设计的精度、减少错误,同时加快了制造过程,提高了生产效率。
2. 钣金加工:钣金加工是造船中的重要工艺,通过将金属板材切割、弯曲、焊接等工艺,可以制造出船体的各个部件。
发达国家采用先进的数控钣金设备和高精度的焊接技术,确保船体结构的强度和密封性。
3. 先进的船体建造技术:发达国家在船体建造方面有较高的技术水平。
例如,采用预应力混凝土技术可以提高船体的强度和耐久性;采用人造材料如复合材料可以减轻船体重量,并提高抗腐蚀性能。
4. 舾装技术:舾装是指安装机械设备、仪器仪表和管道等船舶辅助设备。
发达国家采用先进的舾装技术,包括模块化舾装和集中舾装等,在保证整体结构强度的基础上,提高了船舶的稳定性和安全性。
5. 平台安装技术:平台安装是指将飞机、直升机等飞行器安装在船上的技术。
发达国家的造船厂利用大型起重设备和自动化控制系统,将船体与船舶平台进行精确匹配,确保平台的安全和稳定。
6. 线缆布置和维护技术:船舶内部的线缆布置和维护是一个复杂而繁琐的过程。
发达国家的造船厂通过采用先进的电气布置设计软件和特殊的线缆槽道设计,提高了船体内线缆系统的可靠性和维护性。
7. 船舶试航与调试技术:船舶的试航与调试是确保船舶设计和制造质量的关键环节。
发达国家的造船厂采用先进的试航设备和技术,进行全面的试验和调试,包括性能测试、动力系统测试、控制系统测试等,确保船舶安全、可靠地投入运营。
8. 环境保护技术:发达国家在造船行业中注重环境保护,通过使用低排放材料,配置污染治理设备,实施循环利用等措施,减少船舶制造过程中的环境污染。
综上所述,发达国家的造船工艺采用了多种先进技术和工程方法,包括数字化设计和制造、钣金加工、先进的船体建造技术、舾装技术、平台安装技术、线缆布置和维护技术、船舶试航与调试技术以及环境保护技术。
船舶先进制造技术

CIMS的概念
CIMS是一种新型的生产模式。其目标在于寻找一 条使企业达到预定战略目标的有效途径。这就是, 从系统工程的整体优化观点出发,通盘考虑市场 需求,企业经营目标,技术支撑条件和人的因素, 利用现代信息技术,生产技术及两者的结合,对 生产过程涉及的各个局部系统进行有效的综合集 成以达到全局优化的目的。
造船CIMS总体框架图
CIMS成功实施的主要因素
1)项目研制是企业发展自身的需求 2)领导必须直接参与项目的推进 3)正确处理整体和局部的关系 4)扎实的管理是项目推进的基础 5)抓好基础数据收集与分析 6)人员培训是项目实施的保证
/10/29
.
9
船舶先进制造技术
CIMS在船舶制造中的应用
先进制造技术是造船业发展的基础
先进制造技术与造船业的发展
1)50年代前“铆接技术”在造船业中的应用,使 古老的木船建造发展为以钢船建造为主体的近代 造船。
2)60年代“焊接技术”的应用,使原来以功能分 类的“系统”导向的古代造船方法转变为以“区 域”导向。
3)70年代“成组技术”引入造船业,通过不同类 型船舶的建造过程相似性分析,以船舶区域,作 业
先进制造技术是造船业发展的基础
类型和阶段分类,按”中间产品”的概念组织造船 的流水和工位固定人员流动的虚拟流水生产。
4)80年代以来,电子计算机技术在造船中应用 不断拓展,造船精度控制技术和船舶工程管理技 术日臻完善, 使造船业的社会技术的协同机制充分 发挥作用, 实现了以“ 空间分道、时间有序” 为 特征的“壳舾涂一体化” 。即造船的计算机集成 制造系统(CIMS)船厂成为信密集型企业, 是现 代造船的最高水平。
造船企业CIMS的实施
高新切割技术在现代造船业中的应用

高新切割技术在现代造船业中的应用
随着人类社会的发展,造船业的发展正在不断提升,让人们欣喜不已。
近几年,现代造船业发展迅速,技术也不断更新。
其中,高新切割技术在现代造船业发挥了重要作用。
高新技术是一种利用电等物理力学原理将厚重材料切成薄片的
技术,常见的切割方式有水切,气切,激光切割等。
这些高新切割技术可以提供质量高、精度精细、速度快的切割效果,从而使整个制造流程更加高效率。
首先,高新切割技术使现代造船工艺能够更好地利用原料,从而提高了建造船只的效率。
采用高新切割技术可以减少原料的浪费,使建造船只的效率得到显著提高。
,这项技术的使用可以提高制造船只
的安全性。
减少材料的误差和错误是一种实现安全预警的重要一步。
对于一个新建的船只,安全性是最重要的考虑因素,因此,现代造船业利用高新切割技术在制造船只的过程中,能够更好地保证安全性,同时也可以有效地减少质量、效率等方面的问题。
此外,高新切割技术也可以有效地改善制造船只的质量。
从安装方面来看,使用高新切割技术进行加工可以减少零件接触的不稳定性,从而提高船只的防腐耐久性。
体现在制作过程中,高新切割技术可以让整个制造过程变得更加节省,从而提高了产品质量和工艺水平。
总之,高新切割技术在现代造船业中发挥了重要作用。
它可以帮助提高造船效率,提高船只的安全性,并且可以缩短制造周期,提高产品的质量和工艺水平。
而随着时间的发展,现代造船业将更加依赖
这项先进技术,从而使现代造船技术得到显著改进。
船舶先进制造技术作

先进制造技术
随着信息技术、新材料等 领域的突破,船舶制造技 术不断升级,向数字化、 智能化方向发展。
现代船舶制造技术的特点
数字化
自动化
利用计算机技术实现船舶设计的数字化建 模、仿真和优化,提高设计效率和精度。
采用机器人、自动化设备进行切割、焊接 、装配等作业,减少人工干预,提高生产 效率。
智能化
绿色环保
通过物联网、大数据等技术实现船舶制造 过程的智能化监控、预测和优化,提高生 产管理水平和产品质量。
注重环保和可持续发展,采用环保材料和 清洁能源,降低能耗和排放,提高船舶能 效和环保性能。
船舶制造技术的应用领域
民用船舶
包括货船、客船、游艇等 ,满足国内外航运市场需 求。
军用船舶
包括军舰、潜艇等,用于 国防建设和军事行动。
定制化、个性化制造
随着消费者需求的多样化,船舶制造 将更加注重定制化和个性化,以满足 不同客户的需求。
数字化、信息化技术的应用
数字化、信息化技术将广泛应用于船 舶制造中,实现生产过程的可视化和 可控化。
船舶先进制造技术对未来船舶工业的影响
提高船舶制造效率和质量
先进制造技术的应用将大幅提高船舶制 造的效率和质量,缩短产品研发周期,
THANKS
感谢观看
市场竞争激烈
船舶制造业市场竞争激烈,需要不断提高 产品质量和技术水平,以获得更大的市场 份额。
船舶先进制造技术的发展前景
智能化制造
随着人工智能、大数据等技术的发展 ,船舶制造将逐渐实现智能化,提高 制造效率和质量。
绿色制造技术
环保法规的日益严格,绿色制造技术 将在船舶制造中得到广泛应用,实现 环保和经济效益的双赢。
通过智能船舶制造技术,可以实现船舶设计和制造过程的自动化和智舶制造技术
国外造船术发展概况

第一级水平
第二级水平
第三级水平
第四级水平
第五级水平
系统导向
系统和区域导向
区域、类型和阶段(中间产品)导向
船台散装
分段建造
分段建造
壳舾涂
设计制造
码头舾装
预舾装
区域舾装
一体化
一体化
整船涂装
预涂装
区域涂装
劳动密集型
设备密集型
信息密集型
知识密集型
离散型生产过程
连续型生产过程
传统造船
现代造船
未来造船
日本、韩国、中国造船技术水平比较表
国度
设计技术 制造技术
管理技术
日本
100
100
100
韩国
85
Hale Waihona Puke 9090中国
65
65
55
3、开发研究目的
船舶集成制造技术的开发,旨在建立一种新的生产 函数,把一种关于生产要素和生产条件的新组织 引入生产关系。把成组技术、信息技术与我国的 船舶生产条件相结合,把先进的船舶设计、制造 技术与现代生产管理体制相结合,从而建立全厂 的船舶集成制造系统,实现船舶工程优质、高效 、安全、低耗的生产效果,促进造船模式从初级 阶段向高级阶段发展,使我国的造船技术水平达 到3--4级,相当于国际20世纪90年代初期水平, 实现现代化造船。
4、总体方案关键技术
4.1 总体方案 船舶集成制造技术是从研究开发“先进制造技
术”的角度,应用成组技术原理和统筹优化理论, 确立壳舾涂一体化的先进造船模式,按其建模原 则形式一套全新的生产作业体系。在船舶设计过 程中合理规划,并在规划中与制造策略、管理思 想和各项先进造船技术有机地结合,把设计、制 造、管理信息集成,做到船舶设计制造一体化, 从而实现造船工程优质、安全、高效、低耗的效 果. 4.2 关键技术 船舶集成制造技术包含四项关键技术,分别是 设计技术、制造技术、管理技术、计算机技术。 它们之间的相互关系,如图2所示。
国外飞机先进制造技术发展趋势

国外飞机先进制造技术发展趋势冷战时代的军备竞赛,刺激了军事工业,尤其是飞机制造业的发展。
为了研制高性能新型战机、大型军用运输机、特种军用飞机和武装直升机,各国政府和军方不断推出新的研究计划,投入巨额资金,开发先进制造技术及其专用设备,基本建立了飞机先进制造技术发展的基础。
随着世界经济较长时期的衰退,各国航空公司利润急剧下降,直接影响到飞机制造商。
因此,他们为了生存,降低飞机全寿命周期内的成本就成为了新一代民机研制的一个重要指标和先进制造技术的发展方向。
冷战结束后,各国大量削减国防经费,军方难以承受高性能武器装备的高昂采购费用,如F—22战斗机每架1.6亿美元。
如此高昂的采购费,限制了该飞机的生产数量,因此美国军方提出研制买得起的飞机——JSF联合攻击机(每架约6000万美元)作为相应的补充。
军机的研制生产也提出了高性能和全寿命周期低成本的双重目标。
计算机技术的不断发展,精益生产等许多新理念的诞生,使得飞机先进制造技术处于不断变革之中,传统技术不断精化,新材料、新结构加工、成形技术不断创新,集成的整体结构和数字化制造技术构筑了新一代飞机先进制造技术的主体框架。
为了进一步了解国外飞机先进制造技术发展的这一趋势,本文介绍几种主要制造技术。
1 树脂基复合材料构件制造技术树脂基复合材料具有高的比强度、比模量,抗疲劳、耐腐蚀、成形工艺性好以及可设计性强等特点,现已成为飞机结构中与铝合金、钛合金和钢并驾齐驱的四大结构材料之一。
国外的新一代军机和民用运输机已普遍采用这种材料,第四代战机复合材料用量占飞机结构重量的25%~40%,干线客机用量约15%,其应用水平成为飞机先进性的一个重要标志。
为满足飞机上扩大复合材料应用的需求,飞机制造商在不断地完善复合材料层压板真空袋—热压罐制造技术,并不断地开发高性能低成本的复合材料制造技术,如:纤维缝合技术、树脂转移模塑成形技术(RTM)、树脂膜渗透成形技术(RFI)、真空辅助树脂渗透成形技术(V ARI)、纤维铺放技术、电子束固化技术及膜片成形技术等。
美国海军采用的先进金属加工技术

美国海军采用的先进金属加工技术
吴始栋
【期刊名称】《国外舰船工程》
【年(卷),期】2002(000)007
【摘要】国家优秀金属加工技术中心为美国海军提供先进金属制造加工技术,由此可生产高性能舰船结构钢,大大降低采购成本并节省寿期成本.该中心还研究了焊接材料的最佳焊接程序,提高了焊接接头的可靠性;取消对锻件和铸件焊接时的预热;改进扫雷制冷和声呐用陶瓷;采用低成本的轻质非耐压壳体部件,改善潜艇的机动性,并增加有效载荷.此外,该中心还开发超导体制造技术,采用包铝超导丝,并研制新型热处理工具等,以满足海军的需要.
【总页数】4页(P22-25)
【作者】吴始栋
【作者单位】第七二五研究所
【正文语种】中文
【中图分类】U6
【相关文献】
1.美国海军采用的若干舰船控制先进技术 [J], 刘昭昆(译);惠佳(校)
2.美国海军金属加工先进技术 [J], 吴始栋
3.先进金属材料及特种成形加工技术创新团队 [J],
4.中石油采用UOP先进重油加工技术 [J], 郑文兰
5.美国海军首次采用超声加工技术降低潜艇建造成本 [J], 胡晓睿
因版权原因,仅展示原文概要,查看原文内容请购买。
船舶先进制造技术参考资料

一、现代造船模式的基本概念及原理(成组技术、产品导向型工程分解、区域舾装、管件族制造、中间产品、船体分道建造、区域涂装、壳舾涂一体化等)现代造船模式的涵义所谓现代造船模式,可理解为以统筹优化理论为指导,应用成组技术原理,以中间产品为导向,按区域组织生产,壳(船体建造)、舾、涂作业在空间上分道,时间上有序,实现设计、生产、管理一体化,均衡、连续地总装造船.现代造船模式形成的技术基础—成组技术与系统工程技术在造船中应用阐述如下:先进制造技术在现代造船模式中的应用(1)成组技术。
首先应用于机械制造业,利用零件的相似性来组织多品种小批量生产,以获得少品种大批量的生产效率。
成组技术被应用于船舶建造工程,导致了中间产品分类成组加工和管件族加工方法的产生,形成了船体分道建造生产线;成组技术中短间隔期、小批量的生产管理方法形成了船舶建造作业的托盘管理。
(2)产品导向型工程分解。
是按中间产品生产特征分解组织生产的形式,是按总系统、各分系统、系统/区域、区域/类型/阶段而成组,再把这些成组法分别用干基本设计,功能设计、转换设计和施工设计中。
这样可将不同系统的专业人员分配到专门负责某个产品级别的组里,以改善组里的横向关系、简化生产顺序、提高生产效率。
产品导向型工程分解既可用于设计和材料的选定,也可用干生产和控制。
实现壳舾涂一体化,指以“船体为基础,舾装为中心、涂装为重点”的管理思想,把壳(船体)、舾(舾装)、涂(涂装)不同性质的三大作业类型,建立在空间上分道、在时间上有序的立体优化排序。
(3)区域舾装。
新的舾装概念:把船壳视作载体,为造船厂生产主体,往船壳上安装的一切物件都叫作舾装件。
以后发展按区域划分进行舾装作业划分的,分为机舱舾装和除机舱以外的船体舾装、加上跟踪涂装和每阶段交工之前的精细整修等,确立了舾装的全新概念。
如上所述,按照区域划分进行舾装作业的舾装方法便称为区域舾装。
但是严格地说,区域舾装的定义是不够完整的,叫区划舾装更确切些,这里的“区划”是指除了空间要有划分外,在时间上也要有划分,才能使区域舾装的概念更加完整。
国际先进造船技术

2.4 现代造船模式的内涵
现代造船模式是一个完整生产体系,目标是贯彻以“中间产品”为 导向的建造策略,并主要由如下11项技术组成:
(l)质量控制循环活动:造船企业中的每个人都置身于各自业务的 “计划—实施—校核—改进—再计划”的无限循环和提高之中。
(2)船舶建造标准化:为达到有效的控制,实现一切与船舶生产有关 的活动的全面标准化,包括产品设计、加工、装配、安装、检验和 各项管理工作。
•模块导向的分形 产组合的动态耦
•造船和船舶运营 过程的瞬态监
•劳力密集
•劳力密集
•设备密集
船厂类型 •大型厂数万名 •大型厂员工万 •大型厂员工
员工
名左右
千人左右
•信息密集
•大型厂员工千人 以下
•知识密集
•大型厂员工数百 或百人左右
发展时序
传统船舶工业
现代船舶工业
未来船舶工业
关键技术 典型装备
•人工放样技术 •切割、成型、装配技术 •管子加工技术 •铸、锻、热处理和机加工 •机电设备和系统的安装调试
现代船舶工业
未来船舶工业
•定场地、设备、人员和指标,制 造某“中间产品”的多工种的生产 单元
•按区域的多专业的科室
•复合工种的生产工人
•多学科的科技人员
•快速组织的生产班组, 安装和调试各类模块
•智能化高素质的生产工 科技人员,能持续改进工 并适应灵捷的动态组合
2.3 现代造船模式的技术基础
现代造船模式形成的技术基础是成组技术与系统工程技术。
1.2 AMT的目标是全新概念的 T、Q、C、S
进入80年代,企业战略决策,由传统的以“标准化”为核心, 转变为以满足用户需要为核心。企业的一切生产活动以T、Q、C、 S的新概念为目标,以赢得竞争。 T——Time to market 商品以最短时间上市。 Q——Quality 运用完整和可靠的质量保证体系,把最完美的产品 送到用户手中。
- 1、下载文档前请自行甄别文档内容的完整性,平台不提供额外的编辑、内容补充、找答案等附加服务。
- 2、"仅部分预览"的文档,不可在线预览部分如存在完整性等问题,可反馈申请退款(可完整预览的文档不适用该条件!)。
- 3、如文档侵犯您的权益,请联系客服反馈,我们会尽快为您处理(人工客服工作时间:9:00-18:30)。
船舶设计与建造
国外舰船先进制造技术— ——先进切割技术
周方明, 陶永宏
( 江苏科技大学, 江苏 镇江 212003)
现 代 船 舶 的 建 造 会 用 到 大 量 的 板 材 、型 材 和 管 材 , 船 体 、甲 板 、船 舱 以 及 各 种 上 层 建 筑 和 管 道 都 是 由 切 割 成形的板材、型材和管材装配组合而成的。这些型材的 品种主要有: 球鼻钢、角钢、扁钢和 T 型钢等, 型材在成 形或焊接加工前还要切割各种形状的端头、中间孔和 焊接坡口, 并标识记号及加工装配用的线段, 因而切割 工作量大已成为船舶工业的一个显著特点。由于型材 品种和规格尺寸的多样性, 产生了多种多样的切割内 容和要求, 而原有技术加工效率低、切割精度低及切口 表面质量也难以保证, 使得传统的切割设备与切割方 法已不能满足其要求, 这些存在的问题促使先进切割 技术的发展, 同时也使船舶工业成为引入先进切割技 术最早、涵盖的切割技术面最广并紧随现代技术不断 发展的行业。
2002 年德国迈尔船厂在游船和客船上的非主结构 甲板和上层建筑平面分段的焊接中采用了高压水射流 切割技术, 切割后效果令人非常满意。 2.5 高压水切割技术的产业化发展概况
目前世界先进造船国家在高压水射流切割方面已 经达到了产业化应用, 主要用途和优势体现在陶瓷、硬
中外船舶科技 2008 年第 2 期
目前, 氧气等离子切割技术已达到了一个较高的 发展水平, 并普遍应用于国外船舶制造中。例如: 2000 年美国 Mare Island 海军船厂利用 Hyspeed HT2000 氧 离子切割机切割船用材料和电缆, 使得切割碳钢的速 度提高了 50% , 同时采用长寿命氧气等离子弧切割技 术和银正极电极技术, 其切割大多数厚碳钢板速度明 显 快 于 激 光 切 割 和 火 焰 切 割 。 图 1 为 Hypertherm 的 Hyspeed HT2000 氧气等离子切割机工作时的情况。
3 切割机器人技术
3.1 切割机器人技术背景 机器人技术是各国造船工业重点发展的领域, 其
中 焊 接 机 器 人 、切 割 机 器 人 、涂 装 机 器 人 等 是 发 展 的 热 点, 目前国外的型材切割机器人技术已经日益实用化, 成为了船舶加工流水线的重要组成部分。 3.2 切割机器人技术原理
自 20 世纪 80、90 年代起, 借助计算机、微电子、网 络和光、机、电一体化技术水平的迅速提高, 工业机器 人技术及其应用获得了前所未有的进展。切割机器人 历来在工业机器人应用领域中占据着相当重要的位 置, 随着全球制造业的复苏及新一轮的迅猛发展, 切割 的工作总量、复杂程度和技术要求都在不断提高, 而机 器人切割设备的成功应用也向世人充分展示了其在解 决 技 术 劳 动 力 不 足 、提 高 生 产 率 、改 进 产 品 质 量 和 降 低 生产成本方面的显著作用, 日益成为造船业在型材切 割 、三 维 曲 面 切 割 、柔 性 切 割 等 方 面 保 持 产 品 竞 争 能 力 的一支不可缺少的关键力量。
船舶设计与建造
质 合 金 、模 具 钢 、淬 火 钢 、白 口 铸 铁 、钨 钼 钴 合 金 、耐 热 合金、钛合金、耐蚀合金、FRM 或 FRP 等复合 材 料 、高 速钢( HRC30 以下) 等高、尖、难材料的切割上。在军船 方面, 高压水切割可用于巡洋舰上的硬质合金和核潜 艇上的钛合金等材料的切割。在民船方面, 高压水切割 可用于大型多功能化学品船舶耐蚀合金等材料的切 割。
2001 年 法 英 合 作 的 超 高 压 水 切 割 机 应 用 在 造 船 企业, 对 20 万吨以上的大型油船、10 万吨以上的大型 成品油船、大型多功能化学品船、5000TEU 以上的集装 箱船、大型汽车滚装船等大厚板的切割有着很大的优 势 , 最 大 的 钢 板 切 割 厚 度 为 70mm, 切 割 速 度 达 到 15mm/min;
1 氧气等离子弧切割技术
1.1 氧气等离子切割技术背景 常用材料的切割方法主要有氧乙炔切割和等离子
弧 切 割 。 氧 乙 炔 切 割 使 用 方 便 、切 割 成 本 低 、切 割 板 厚 度大, 但具有切缝宽、切口面不平整、不光洁、热影响区 较大、工件变形度大和只适用于碳钢等缺点。等离子弧 切割速度快, 精度高, 断面光滑, 适用于各种材料, 但切 割成本较高, 切割板厚较小。氧气等离子切割技术于 1983 年 由 美 国 Hypertherm 公 司 率 先 成 功 地 应 用 于 碳 钢的切割中, 它集成了氧乙炔燃烧的化学反应和等离 子弧高温的物理效应的优点, 大大提高了黑色金属的 切割厚度、速度和质量。 1.2 氧气等离子切割技术原理
( 3) 高压水切割的切 割 精 度 介 于 0.1mm~0.25mm 之间, 其切割精度取决于机器的精度、切割工件的尺寸 范围及切割工件的厚度和材质, 通常机器的系统定位 精度为 0.01mm 至 0.03mm。 2.4 高压水切割技术的应用实例
1999 年俄罗斯海军在核潜艇建造过程的钛合金切 割中, 使用了高压水射流技术, 加工速度大大提高, 加 工精度良好, 减少了后期加工的工作量, 缩短了造船周 期, 已在俄海军造船领域广泛应用。
28
者 的 结 合 正 使 得 其 在 切 割 材 料 时 犹 如 一 把 轴 向“ 锯 刀 ” 加工。磨料水射流技术切割材料时所使用的射流由压 力、速度都很高的水和磨料混合而形成。在材料被磨料 水射流去除的过程中, 单个固体颗粒的冲击是加工力 的基本作用单位。磨料水射流技术已被成功地用于多 种材料的切割, 特别是难加工材料方面。目前已有 3000 多 套 水 射 流 切 割 设 备 在 数 十 个 国 家 几 十 个 行 业 应用, 已可切割 500 余种材料, 其设备年增长率超过 20% 。 2.新型的热切割技术, 它的工作原理是以压缩氧气为工作气体, 并以在高温、 强 电 场 条 件 下 产 生 的 高 温( 20000℃) 高 速( 300m/s 以 上) 等离子弧为热源, 经机械压缩、热压缩和磁压缩, 使 弧柱电流密集、产生极高的温度和高速气流, 高温、高 速的等离子弧焰流将被切割的金属局部熔化, 并同时 用高速气流将已熔化的金属吹走, 形成狭窄切缝。由于 弧柱温度大大超过金属及其氧化物的熔点, 因此, 氧气
图 1 Hyspeed HT2000 正在切割示意图
2000 年英国著名的军船制造企业沃斯帕·桑尼克 罗夫特造船公司引进数控氧气等离子切割机, 在加工 厚 l6mm 的船体零件和建造用的各种样板时, 预涂底漆 的钢板割后漆膜无损坏, 且零件精度高, 非常平整。
2002 年美国某船舶修造有限公司将氧气等离子切 27
等离子切割除可切割碳钢外, 还可用于切割不锈钢、 铝、铜等金属。 1.3 氧气等离子切割技术特点
与传统的氧乙炔、等离子弧切割技术相比, 该技术 手段的优越性表现在: (1) 无挂渣, 切割速度快, 切割范 围大, 切口质量好; (2) 切缝狭窄, 切口窄面平整光洁, 热影响区小, 无表面氮化现象, 切割后的工件具有良好 的焊接和加工性能; (3) 工件变形度低, 切割厚、薄板均 不变形; (4) 相同电源功率下切割速度可提高 30% , 而 且具有显著的节能效果, 是目前较为理想的热切割设 备; (5) 操作简单, 容易掌握, 使用安全, 切割成本低。 1.4 氧气等离子切割技术的应用实例
2 高压水切割技术
2.1 高压水切割技术背景 二战期间, 飞机飞行中雷达舱被雨侵蚀破坏的现
象启发了人们利用高压水流的思维。高压水射流切割 技术最早源于前苏联, 但第一项切割技术专利却在美 国诞生; 然而, 作为一项独立而完整的切割技术, 高压 水射流(WJ)的产生还是最近四十年的事。在过去的 20 年中, 纯水射流已经得到了广泛的应用, 并为磨料水射 流技术奠定了基础。磨料水射流技术是 20 世纪 80 年 代中期英国流体力学研究协会 ( British Hydrodynamics Research Association) 首 次 提 出 的 , 其 应 用 已 遍 及 船 舶 工业生产的各个方面。目前工业中使用的高压水射流 技术主要有两种实现方法: 纯水射流和磨料水射流。 2.2 高压水切割技术原理
给切割机器人赋予位置和动作的执行程序信息, 切割 机器人现在常用的编程方法有直接示教和离线编程 2 种;
2002 年日本石川岛播磨的爱知船厂也引进了氧气 等离子切割机, 在对 8mm~30mm 中厚板切割后, 样板 具有良好的焊接和加工性能。 1.5 氧气等离子切割的产业化发展概况
造船业是应用氧气等离子弧切割技术最早、得 益 最大的行业。近年来, 国外大船厂纷纷引进配备氧气 等离子弧切割装置的大型数控等离子切割机, 并在钢 板 下 料 中 发 挥 着 无 可 替 代 的 主 力 军 作 用 。氧 气 等 离 子 弧 切 割 技 术 优 质 、高 速 、高 效 率 、低 成 本 的 优 越 性 已 在 造船生产实践中得到验证, 目前已达到产业化应用阶 段。
船舶设计与建造
中外船舶科技 2008 年第 2 期
割新工艺用于切割 50mm 厚的钢板, 在大约 l 秒钟内就 可 以 完 成 38mm 厚 钢 板 的 穿 孔 , 连 续 切 割 速 度 可 达 200mm/min, 割缝宽度仅有几毫米; 每切割一张钢板比 火焰切割可以平均节省时间 40 分钟, 使得作业成本更 经济; 而且割嘴离钢板的初始距离也可上升到 7mm, 较 常规切割的 0.5mm~2mm 增加了许多, 减少了切割穿 孔飞溅物对割嘴的损耗; 切割表面质量好, 热影响区 小, 获得了较高的切割精度, 省略了许多后续加工。
高压水射流本身具有较高的刚性, 在与靶物碰撞 时, 能产 生 极 高 的 冲 击 动 压(P=ρVC)和 涡 流 , 从 微 观 上 看相对于射流平均速度存在着超高速区和低速区 (有 时 可 能 为 负 值), 因 而 高 压 水 射 流 表 面 上 虽 为 圆 柱 模 型, 而内部实际上存在刚性高和刚性低的部分, 刚性高 的部分产生的冲击动压使传播时间减少, 增大了冲击 强度, 宏观上看起快速楔劈作用, 而低刚度部分相对于 高刚度部分形成了柔性空间 , 起吸屑、排屑作用, 这两