油脂精炼2
油脂的精炼(Oil Refining)讲解
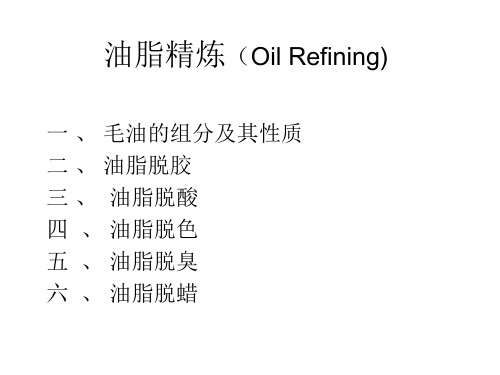
油脂加工的基本过程
毛油 脱胶 脱酸 脱色 脱臭 脱蜡
四级油 三级油 Crude oil bleaching
二级油 一级油 (高烹油)(色拉油) degumming deacidify deodorization dewaxing
第一节 毛油的组分及其性质
毛油定义:(粗油或原油Crude oil) 从天然油料中用压榨、浸出等方法提取的没经过处理的油脂。 其主要成分: 一、悬浮杂质 1、无机杂质:如:泥、沙、铁屑等。 2、有机杂质:如:饼或粕屑、草杆纤维等。 3、分离方法:A、重力沉降;B、离心分离; C、过滤分离; 二、水分 1、水的存在:在工艺中产生 2、水的危害:油脂透明度差,易导致油品酸败。 3、去水方法:减压干燥,成品油<0.05%。
4、非水化磷脂有组分: 主要形式为磷脂酸和溶血磷脂的钙镁盐。如肌醇 磷 酸 ( 2% ) 、 甘 油 磷 酸 ( 15% ) 、 溶 血 磷 脂 酸 (28%)、磷脂酸(55%)。 5、非水化磷脂转移水化磷脂方法: A、酸化处理;磷酸、乙酸酐; B、钝化磷脂酶: C、活性化处理:柠檬酸活化两性物质。 (二)蛋白质、糖类、黏液质 1、蛋白质及其水解产物; 2、糖及其聚合物质;
• E、蛋白质、糖类降解后生成新的结合物 (如胺基糖)是一种棕黑色色素;用一 般吸附剂对其脱色无效。 • F、蛋白质分解为氨基酸,多糖分解为单 糖,经过一系列反应而生成黑色素。在 制油过程中应避免形成新色素。 (3)色素的危害: 油中色素影响油品外观和使用性能, 不同色素对油品安定性有不同影响。 应 脱除色素。
水化脱胶工艺
1、间歇式水化脱胶工艺 软水 ↓ 过滤毛油→预热→水化→静置沉降→分离→含
水脱胶油→干燥(脱溶)→脱胶油 回收油←油脚处理←富油油脚
第六章.油脂精炼2

(四)碱炼脱酸工艺
1、间歇式碱炼脱酸工艺 、
碱液 软水 ↓ ↓ 过滤毛油→前处理 中和→静置沉降 前处理→中和 静置沉降→含皂脱酸油 过滤毛油 前处理 中和 静置沉降 含皂脱酸油 ↓ ↑ 油脚处理← 富油油脚 回收油 ← 油脚处理 →水洗 静置沉降 含水脱酸油 →干燥(脱溶)→ 水洗→静置沉降 干燥( 水洗 静置沉降→含水脱酸油 干燥 脱溶) 过滤→脱酸油 过滤 脱酸油
3、碱炼脱酸过程
(1)非均态界面反应: 非均态界面反应: 脂肪酸与碱液接触时 与碱液接触时, 脂肪酸与碱液接触时,脂肪酸亲水基团定向围包 在碱滴的表面,进行界面反应。 在碱滴的表面,进行界面反应。 (2)扩散作用: 扩散作用: 界面反应使油-碱滴界面形成皂膜。皂膜里的碱滴 界面反应使油-碱滴界面形成皂膜。 使油 界面形成皂膜 由于浓度差 不断扩散到皂膜外层, 浓度差, 由于浓度差,不断扩散到皂膜外层,逐渐形成较稳 定的胶态离子膜。 定的胶态离子膜。 (3)皂膜絮凝: 皂膜絮凝: 结构松散的皂粒吸附粗油中的胶质色素等杂质, 的皂粒吸附粗油中的胶质色素等杂质 结构松散的皂粒吸附粗油中的胶质色素等杂质, 并在电解质、温度及搅拌作用下, 并在电解质、温度及搅拌作用下,相互吸引絮凝成 大的胶团 胶团即 皂脚” 大的胶团即“皂脚”。
6、杂质的影响 胶溶性杂质、羟基化合物、色素等, 胶溶性杂质 、 羟基化合物、色素等,对碱炼效果有 重要影响,促使碱炼产生持久乳化; 重要影响 ,促使碱炼产生持久乳化; 其他色素增加用 碱量,造成中性油皂化机率。 碱量,造成中性油皂化机率。 碱液中的杂质影响碱的准确用量,其中的钙、 碱液中的杂质影响碱的准确用量 ,其中的钙、镁盐 在中和时产生水不溶性的钙皂或镁皂, 在中和时产生水不溶性的钙皂或镁皂 ,给洗涤操作增 加困难。配制碱溶液应使用软水。 加困难。配制碱溶液应使用软水。 7、分离 皂分离效果取决于皂脚的絮凝情况、 油-皂分离效果取决于皂脚的絮凝情况、皂脚稠度、 皂分离效果取决于皂脚的絮凝情况 皂脚稠度、 分离温度和沉降时间等。在连续-皂分离 效果还受分离机性能、物料流量、 效果还受分离机性能、 物料流量 、进料压力以及轻相 出口压力或重相出口口径等影响。 (油)出口压力或重相出口口径等影响。
油脂精炼详细介绍
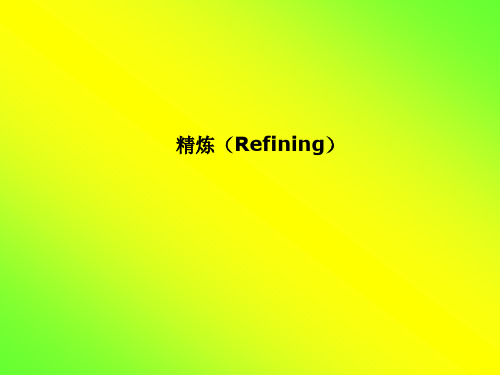
脱色
中和油
白土
真空系统
蒸汽入口 冷凝物出口
过滤 废白土
脱色油
脱臭
在真空及高温下清除油中挥发性旳臭味物质(volatile odoriferous material)和游离脂肪酸(free fatty acids) 环节 (真空下) - 油加热 - 蒸汽汽提除去挥发物和游离脂肪酸 - 油冷却至常温
脱臭
蒸汽
脱色油
脱酸、脱色、 脱臭精炼油
. .
.
.
. .
....
.... .
.
. .
.
. .. .
. .
除臭剂
.
脱臭馏出物 (FAD)
真空系统
FAD 冷却器
物理精炼
- 脱胶 - 脱色 - 脱臭
毛油
废白土 汽提蒸汽
脱胶
脱色 过滤 脱臭 脱酸、脱臭、脱色精炼油
白土 脱臭馏出物 (FAD)
脱蜡
中和油
脱胶
混合罐
脱胶油
毛油
酸溶液
胶质
从毛油中清除磷脂物(Phosphatides)和粘液(Mucilaginous material)(如胶质 gums) 等物
脱胶类型 - 水化脱胶 - 酸法脱胶 (磷酸 phosphoric/柠檬酸 citric acid 溶液)
中和
除去脱胶油中旳游离脂肪酸
环节如下: • 油经过碱液(Caustic solution) 如氢氧化钠 (NaOH) 处理形
product)
• 氧化物 (Oxidized product)
• 发色体(Colour bodies)
•水 • 溶剂 (Solvents)
精炼旳分类
- 化学精炼 - 物理精炼
(粮油加工课件)油脂精炼
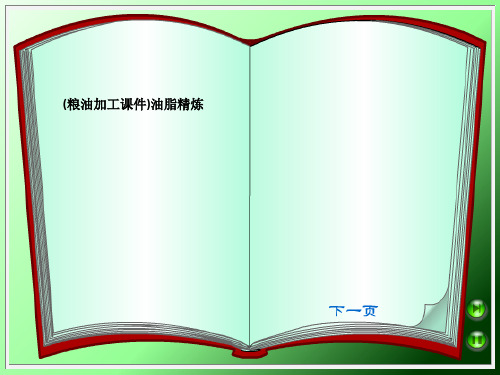
• 2.表面活性剂脱酸——海尔沃本法 • 此法是1963年由瑞典人发明的,海尔沃
本是一种易溶于水,对酸和碱都很稳定 的表面活性剂,学名为二甲基苯磺酸钠, 白色粉末或片状固体。 • 海尔沃本溶液对碱炼时生成的皂脚比对 中性油有更大的溶解能力,因此,在碱 炼时可优先溶解皂脚,减少了中性油的 损失,此法对精炼高酸价油尤为有利。
毛油酸价 >3 3~5
碱液浓度 10 11 (°Be)
5~7 7 ~10 10
1214 ຫໍສະໝຸດ 62020/7/22• ①低温浓碱法 (以棉籽油为例) • 先将毛油泵入锅中,调整温度至
20~30℃,通常加入量不超过锅容量的2/3, 取样化验酸价确定加碱量,然后将 20~25°Be的碱液在5~10分钟内加完,并 在60转/分条件下搅拌20~60分钟,当皂粒 形成时,开始升温(1℃/分),并减速搅 拌(30转/分),当温度达60℃时,静置 10~16小时,放出有脚,将油冷却到 20~25℃,经过滤后得脱酸油。
2020/7/22
(三)脱酸
• 脱酸即脱去油里所含的游离脂肪酸。但 脱酸工序中还能脱去一部分色素,全部 脱去油中的残留胶质,并能脱掉一部分 残留农药、黄曲霉毒素和硫,这对提高 油的食用品质大有益处。
• 脱酸的方法有很多种:碱炼法、蒸馏脱 酸法、泽尼斯脱酸法、海尔沃本法和混 合油脱酸法等。
2020/7/22
2020/7/22
二、油脂精炼的方法及原理
• 油脂精炼的方法大体上可分为机械法、 化学法和物理化学法三大类。
• 具体可分为除机械杂质、脱胶、脱酸、 脱色、脱臭、脱蜡及冬化等工序 。
2020/7/22
• 1 .除机械杂质:利用机械法,用过滤 或离心法使机械杂质与油分离。
油脂的精炼
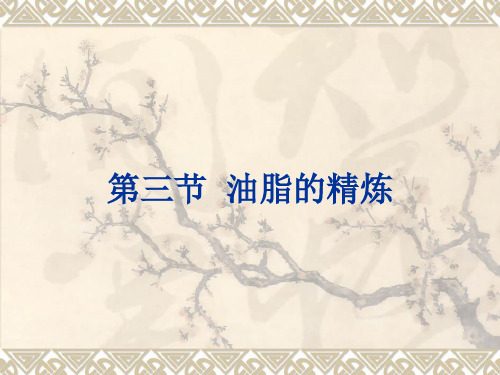
(一)脱蜡
蜡与油脂的熔点差及蜡在油脂中的 溶解度随温度降低而变小的物性,通 过冷却析出晶体蜡
工艺条件:蜡在40 ℃溶于油脂,20~25 ℃, 48~50h,使蜡质结晶析出。
经脱胶、脱酸、脱色、脱臭、脱蜡的植物油称为五脱油
(二)脱脂
0~10 ℃,养晶36~48h,过滤分离。 色拉油(六脱油)
第四节 油脂加工
起酥油的种类
1、按原料种类分类
植物性 动物性 动植物混合型
2、按制造方法分类
全氢化型 混合型 酯交换型
3、按使用添加剂的不同分类
乳化型 非乳化型
4、按性能分类
通用型 乳化型 高稳定型
5、按性状分类
可塑性起酥油 液体起酥油
粉末起酥油
起酥油的加工特性
1、可塑性 2、起酥性
在外力作用下可以改变其形状 烘焙糕点具有酥脆易碎的性质
四、脱酸 ❖ 碱炼脱酸 ❖ 蒸馏脱酸
(一)碱炼脱酸
基本原理
利用加碱中和油脂中的游离脂肪酸, 生成脂肪酸盐(肥皂)和水,肥皂吸附 部分杂质从油中沉降析出。
间隙式碱炼工艺
碱液 过滤毛油 精炼 中和 静置沉降 含皂脱酸油
皂脚 回收油 皂脚处理 富油皂脚
干燥
净油 静置沉降
洗涤
脱酸油
废水
废水
影响碱炼的因素
第三节 油脂的精炼
一、毛油中的杂质种类
毛油又称粗油,一般是指经压榨或浸出 法得到的、未经精炼的植物油脂。
❖ 混合脂肪酸甘油三酯 ❖ 非甘油三酯成分
(一)机械杂质
泥沙、料坯粉末、饼渣、纤维、 草屑及其他固态杂质 过滤、沉降
(二)水分
使油脂颜色较深,产生异味,促进酸败 加热法
(三)胶溶性杂质
第六章 油脂精炼2PPT课件
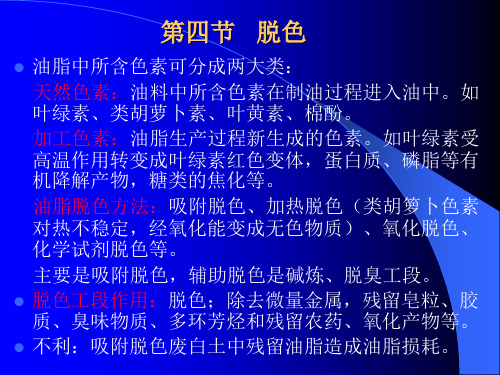
定度和品质。
一、油脂脱臭理论
(一)水蒸汽蒸馏理论
相同条件下,油脂中臭味物质的蒸汽压远大于甘三酯 的蒸汽压。因此,可利用高温、高真空、水蒸汽蒸馏 脱除臭味组分。
如:在250℃工业油脂脱臭条件下,高碳链脂肪酸蒸汽压为 26.66~2.67kPa,而高碳链脂肪酸相应的甘三脂的蒸汽压为 1.33×10-3~1.33×10-4kPa,两者的相对挥发度达20000。
吸附剂分离:叶片式过滤机
BLEACHING
Vessels
Spent earth
二、其他脱色法
(一)光能脱色法 油脂中的天然色素(类胡萝卜素、叶绿素等)能吸
收可见光或近紫外光的能量,双键氧化,发色基团 的结构破坏而裉色。但伴有油脂的光氧化从而促进 油脂的氧化酸败。 (二)热能脱色法 油脂中的某些热敏性色素受热分解褪色。需要在减 压下进行,操作温度为140℃左右,色泽退变后应及 时冷却,以减缓油脂的热氧化。 (三)空气脱色法 (四)试剂脱色法 (五)其他脱色法
(4)操作温度
吸附脱色的操作温度决定于油脂品种、操作压力以及 吸附剂品种。如脱除红色较脱除黄色所需温度高;常 压脱色及活性度低的吸附剂脱色温度较高。
一般105℃-110℃脱色。过高会造成回色,酸价升高。
图6-31 脱色时间对豆油脱色程度的影响
黄色度
80
温度
95
oC
60
白土添加量
2%
绝对压力
60mmHg
主要是吸附脱色,辅助脱色是碱炼、脱臭工段。
脱色工段作用:脱色;除去微量金属,残留皂粒、胶 质、臭味物质、多环芳烃和残留农药、氧化产物等。
油脂精炼步骤
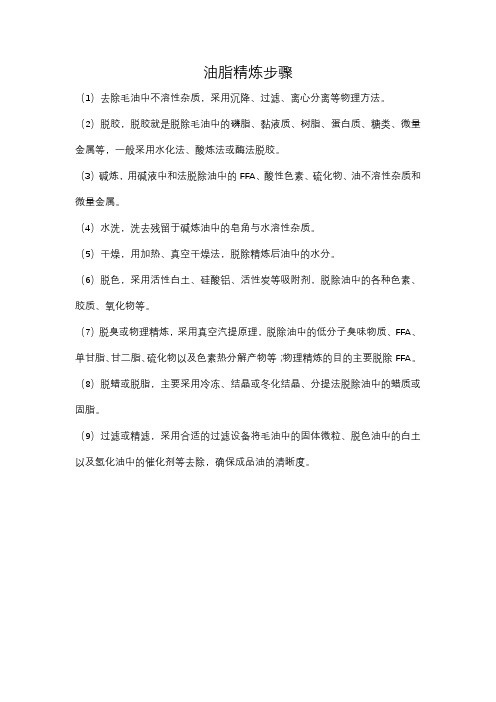
油脂精炼步骤
(1)去除毛油中不溶性杂质,采用沉降、过滤、离心分离等物理方法。
(2)脱胶,脱胶就是脱除毛油中的磷脂、黏液质、树脂、蛋白质、糖类、微量金属等,一般采用水化法、酸炼法或酶法脱胶。
(3)碱炼,用碱液中和法脱除油中的FFA、酸性色素、硫化物、油不溶性杂质和微量金属。
(4)水洗,洗去残留于碱炼油中的皂角与水溶性杂质。
(5)干燥,用加热、真空干燥法,脱除精炼后油中的水分。
(6)脱色,采用活性白土、硅酸铝、活性炭等吸附剂,脱除油中的各种色素、胶质、氧化物等。
(7)脱臭或物理精炼,采用真空汽提原理,脱除油中的低分子臭味物质、FFA、单甘脂、甘二脂、硫化物以及色素热分解产物等;物理精炼的目的主要脱除FFA。
(8)脱蜡或脱脂,主要采用冷冻、结晶或冬化结晶、分提法脱除油中的蜡质或固脂。
(9)过滤或精滤,采用合适的过滤设备将毛油中的固体微粒、脱色油中的白土以及氢化油中的催化剂等去除,确保成品油的清晰度。
油脂精炼——精选推荐
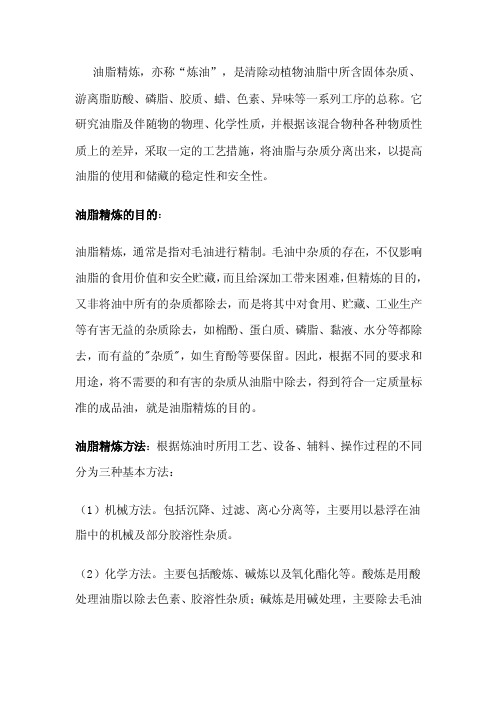
油脂精炼,亦称“炼油”,是清除动植物油脂中所含固体杂质、游离脂肪酸、磷脂、胶质、蜡、色素、异味等一系列工序的总称。
它研究油脂及伴随物的物理、化学性质,并根据该混合物种各种物质性质上的差异,采取一定的工艺措施,将油脂与杂质分离出来,以提高油脂的使用和储藏的稳定性和安全性。
油脂精炼的目的:油脂精炼,通常是指对毛油进行精制。
毛油中杂质的存在,不仅影响油脂的食用价值和安全贮藏,而且给深加工带来困难,但精炼的目的,又非将油中所有的杂质都除去,而是将其中对食用、贮藏、工业生产等有害无益的杂质除去,如棉酚、蛋白质、磷脂、黏液、水分等都除去,而有益的"杂质",如生育酚等要保留。
因此,根据不同的要求和用途,将不需要的和有害的杂质从油脂中除去,得到符合一定质量标准的成品油,就是油脂精炼的目的。
油脂精炼方法:根据炼油时所用工艺、设备、辅料、操作过程的不同分为三种基本方法:(1)机械方法。
包括沉降、过滤、离心分离等,主要用以悬浮在油脂中的机械及部分胶溶性杂质。
(2)化学方法。
主要包括酸炼、碱炼以及氧化酯化等。
酸炼是用酸处理油脂以除去色素、胶溶性杂质;碱炼是用碱处理,主要除去毛油中的游离脂肪酸;氧化主要用于脱色;酯化主要是通过添加甘油使油脂中的游离脂肪酸生成甘油三酸酯,从而降低游离脂肪酸含量。
(3)物理化学方法。
主要包括水化、吸附、水蒸气蒸馏及液---液萃取法。
水化主要用于除去毛油中的磷脂等杂质;吸附主要用于除去油中的色素;水蒸气蒸馏用于脱除臭味物质和游离脂肪酸;液---液萃取法适合于高酸值深色油脂的脱酸。
毛油的组成:毛油的主要成分是甘油三脂肪酸酯的混合物(俗称中性油)。
除中性油外,毛油中还含有非甘油酯物质(统称杂质)。
毛油中杂质的种类:(1)悬浮杂质。
主要包括制油或储运过程中混入的泥沙、料呸粉末、饼粕、纤维、草屑及其他固体杂质。
(2)水分(3)胶溶性杂质。
主要包括磷脂、和蛋白质、糖类、粘液质等(4)脂溶性杂质。
油脂精炼

油脂精炼(fats and oils refining)1、关于精炼精炼油是我国居民主要的食用油品种,精炼是从油料到食用油的加工链上的最后一个工段,油脂二次产品对精炼的特别要求。
1.1、油脂精炼目的1.1.1、增强油脂储藏稳定性1.1.2、改善油脂风味1.1.3、改善油脂色泽1.1.4、为油脂深加工制品提供原料1.1.5、去杂质,前提是低消耗、高保留,得到高价值的副产品。
1.2、精炼工序1.2.1、脱胶、脱酸、脱色、脱臭1.2.2、物理精炼:脱胶—→白土吸附—→脱酸/脱臭—→成品油1.2.3、化学精炼:脱胶—→碱炼—→白土吸附—→脱臭—→成品油有各自的特点。
在工艺上共同点很多,设备也基本相同,引进的成套精炼设备都可进行化学精炼和物理精炼。
1.2.4、化学精炼:碱炼工段可以去除:磷脂,FFA,金属,色素;脱色工段可以去除:氧化产物,残磷残皂,金属,色素;脱臭工段可以去除:FFA,异味,色素。
1.2.5、物理精炼:予处理可以去除:磷脂,金属;脱色工段可以去除:氧化产物,残磷残皂,金属,色素;脱臭工段可以去除:FFA,异味,色素。
1.3、精炼技术关键:降低炼耗,二部分1.3.1、不可避免炼耗:类脂物、伴随物,1一3%1.3.2、可控制损耗:油脚、皂脚、白土夹带,因操作不当被皂化、乳化和真空吸出1.3.3、可控制损耗往往占较大的比例,其高低反映了操作水平及工艺的先进与否,在发生操作故障时,应及时采取补救措施,设法降低可控制损耗,如油脚中夹带的过多中性油,破坏乳化等。
2、原油(Crude oil)组成成分原油中绝大部分为混酸甘三酯(≥95%)的混合物,即油脂,只含有极少量的杂质。
这些杂质虽然量小,但在影响油脂品质和稳定性上却“功不可没”。
按其在油脂中的存在状态可分为:2.1、悬浮杂质:①泥沙②料胚粉末③饼渣④草屑根据该类型杂质在大小和比重上与油有差异,去除方法可用过滤,沉降。
2.2、水分。
根据水在100℃(当然,在真空下这个温度会低一些)时为气态的特性,去除可选用热脱水。
油脂精炼车间精益生产管理研究2篇

油脂精炼车间精益生产管理研究 (2)油脂精炼车间精益生产管理研究 (2)精选2篇(一)油脂精炼车间的精益消费管理研究旨在优化消费过程,进步消费效率和质量,降低本钱。
以下是可能涉及的研究方向和方法:1. 流程分析和价值流分析:通过对消费流程的深化分析,找出各个环节的瓶颈和浪费,针对性地进展改良。
价值流分析可以帮助确定降低消费时间和产出的潜在时机。
2. 质量管理和质量改良:开展质量控制和质量改良活动,包括设置关键质量指标和制定操作标准,以确保产品满足质量要求并减少次品率。
3. 供给链管理:与供给商建立严密合作,确保原材料及时供给,减少库存和等待时间,优化供给链物流布局。
4. 绩效管理和鼓励机制:建立有效的绩效考核和鼓励机制,激发员工积极性和主动性,进步工作效率和产能。
5. 自动化和信息化技术应用:引入自动化设备和信息化系统,进步消费线的自动化程度和管理程度,实现数据的即时监测和分析,便于决策和改良。
6. 人员培训和技能提升:通过培训和技能提升方案,进步员工的技术程度和操作才能,降低操作失误和工作事故率。
7. 持续改良和创新:建立持续改良的机制,鼓励员工提出改良建议和创新想法,推动车间消费管理的不断优化。
对于详细的研究方法,可以采用实证研究、案例分析、模型建立和仿真等方法,结合实际情况进展分析和探究,找出合适该车间的精益消费管理方法和策略。
油脂精炼车间精益生产管理研究 (2)精选2篇(二)精益消费管理是一种以减少浪费和进步效率为目的的管理方法。
在油脂精炼车间中,可以应用精益消费管理的原那么和方法来改良消费效率和产品质量。
首先,通过价值流图分析,理解消费过程中的价值流动和非价值流动,找出存在的浪费和瓶颈,制定针对性的改良措施。
例如,可以通过优化物料流动和设备布局来减少等待时间和运输时间,进步消费效率。
其次,采用流水线消费方式,减少消费批次,减少库存和库存占用的空间,进步消费效率和消费才能利用率。
同时,通过标准化工作流程和工作指导书,确保每个员工都能按照标准进展操作,减少人为因素对消费质量的影响。
油脂的精炼与深加工技术
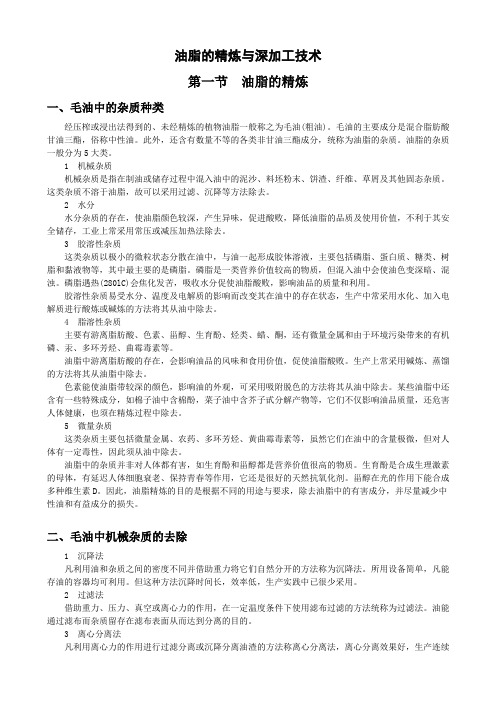
油脂的精炼与深加工技术第一节油脂的精炼一、毛油中的杂质种类经压榨或浸出法得到的、未经精炼的植物油脂一般称之为毛油(粗油)。
毛油的主要成分是混合脂肪酸甘油三酯,俗称中性油。
此外,还含有数量不等的各类非甘油三酯成分,统称为油脂的杂质。
油脂的杂质一般分为5大类。
1 机械杂质机械杂质是指在制油或储存过程中混入油中的泥沙、料坯粉末、饼渣、纤维、草屑及其他固态杂质。
这类杂质不溶于油脂,故可以采用过滤、沉降等方法除去。
2 水分水分杂质的存在,使油脂颜色较深,产生异味,促进酸败,降低油脂的品质及使用价值,不利于其安全储存,工业上常采用常压或减压加热法除去。
3 胶溶性杂质这类杂质以极小的微粒状态分散在油中,与油一起形成胶体溶液,主要包括磷脂、蛋白质、糖类、树脂和黏液物等,其中最主要的是磷脂。
磷脂是一类营养价值较高的物质,但混入油中会使油色变深暗、混浊。
磷脂遇热(280lC)会焦化发苦,吸收水分促使油脂酸败,影响油品的质量和利用。
胶溶性杂质易受水分、温度及电解质的影响而改变其在油中的存在状态,生产中常采用水化、加入电解质进行酸炼或碱炼的方法将其从油中除去。
4 脂溶性杂质主要有游离脂肪酸、色素、甾醇、生育酚、烃类、蜡、酮,还有微量金属和由于环境污染带来的有机磷、汞、多环芳烃、曲霉毒素等。
油脂中游离脂肪酸的存在,会影响油品的风味和食用价值,促使油脂酸败。
生产上常采用碱炼、蒸馏的方法将其从油脂中除去。
色素能使油脂带较深的颜色,影响油的外观,可采用吸附脱色的方法将其从油中除去。
某些油脂中还含有一些特殊成分,如棉子油中含棉酚,菜子油中含芥子甙分解产物等,它们不仅影响油品质量,还危害人体健康,也须在精炼过程中除去。
5 微量杂质这类杂质主要包括微量金属、农药、多环芳烃、黄曲霉毒素等,虽然它们在油中的含量极微,但对人体有一定毒性,因此须从油中除去。
油脂中的杂质并非对人体都有害,如生育酚和甾醇都是营养价值很高的物质。
生育酚是合成生理激素的母体,有延迟人体细胞衰老、保持青春等作用,它还是很好的天然抗氧化剂。
油脂精炼的目的与方法
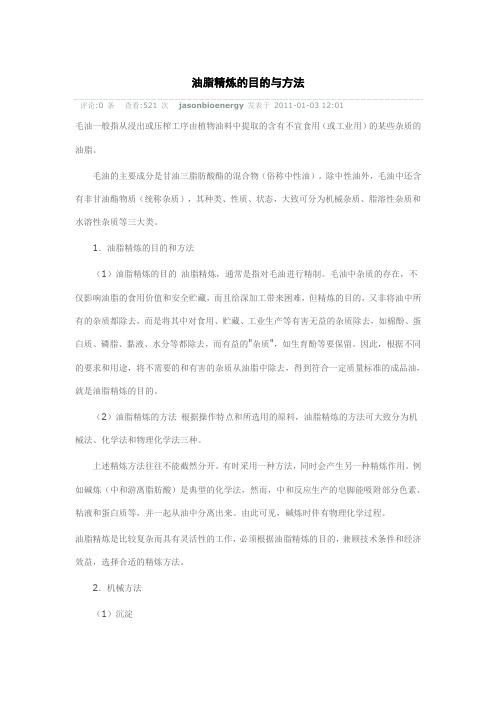
油脂精炼的目的与方法评论:0 条查看:521 次jasonbioenergy发表于2011-01-03 12:01毛油一般指从浸出或压榨工序由植物油料中提取的含有不宜食用(或工业用)的某些杂质的油脂。
毛油的主要成分是甘油三脂肪酸酯的混合物(俗称中性油)。
除中性油外,毛油中还含有非甘油酯物质(统称杂质),其种类、性质、状态,大致可分为机械杂质、脂溶性杂质和水溶性杂质等三大类。
1.油脂精炼的目的和方法(1)油脂精炼的目的油脂精炼,通常是指对毛油进行精制。
毛油中杂质的存在,不仅影响油脂的食用价值和安全贮藏,而且给深加工带来困难,但精炼的目的,又非将油中所有的杂质都除去,而是将其中对食用、贮藏、工业生产等有害无益的杂质除去,如棉酚、蛋白质、磷脂、黏液、水分等都除去,而有益的"杂质",如生育酚等要保留。
因此,根据不同的要求和用途,将不需要的和有害的杂质从油脂中除去,得到符合一定质量标准的成品油,就是油脂精炼的目的。
(2)油脂精炼的方法根据操作特点和所选用的原料,油脂精炼的方法可大致分为机械法、化学法和物理化学法三种。
上述精炼方法往往不能截然分开。
有时采用一种方法,同时会产生另一种精炼作用。
例如碱炼(中和游离脂肪酸)是典型的化学法,然而,中和反应生产的皂脚能吸附部分色素、粘液和蛋白质等,并一起从油中分离出来。
由此可见,碱炼时伴有物理化学过程。
油脂精炼是比较复杂而具有灵活性的工作,必须根据油脂精炼的目的,兼顾技术条件和经济效益,选择合适的精炼方法。
2.机械方法(1)沉淀①沉淀原理沉淀是利用油和杂质的不同比重,借助重力的作用,达到自然分离二者的一种方法。
②沉淀设备沉淀设备有油池、油槽、油罐、油箱和油桶等容器。
③沉淀方法沉淀时,将毛油置于沉淀设备内,一般在20~30℃温度下静止,使之自然沉淀。
由于很多杂质的颗粒较小,与油的比重差别不大。
因此,杂质的自然沉淀速度很慢。
另外,因油脂的粘度随着温度升高而降低,所以提高油的温度,可加快某些杂质的沉淀速度。
油脂精炼操作规程

油脂精炼操作规程
一、引言
油脂精炼是指通过一系列加工步骤,去除油脂中的杂质、气味和颜色,以提高其质量和纯度的过程。
本操作规程旨在规范油脂精炼操作,确保产品的质量和安全性。
二、适用范围
本操作规程适用于各类油脂精炼生产过程,包括但不限于植物油、动物油和合成油的精炼。
三、工艺流程
1. 原料接收与储存
a. 检查原料的质量与标识,确保符合相关标准和要求。
b. 将原料储存在干燥、阴凉、通风良好的储存室内,避免与有害物质接触。
2. 预处理
a. 对原料进行预处理,如去除杂质、根茎、叶子和细菌等。
b. 如果原料中含有过多的酸性物质,可以采取碱中和等方法进行处理。
3. 脱色
a. 将预处理后的原料加入脱色釜或脱色槽中,并加入适量的脱色剂。
b. 根据不同的产品需求,在特定的温度和时间条件下进行脱色处理。
c. 确保脱色后的产品色泽符合标准要求。
4. 脱臭
a. 脱色后的油脂需要进行脱臭处理,以去除其中的异味。
b. 采用蒸馏或蒸汽冲洗等方法进行脱臭,确保产品的气味符合标准要求。
5. 精炼
a. 对脱臭后的油脂进行进一步精炼和提纯,以去除其中的杂质和有害物质。
油脂精炼的方法
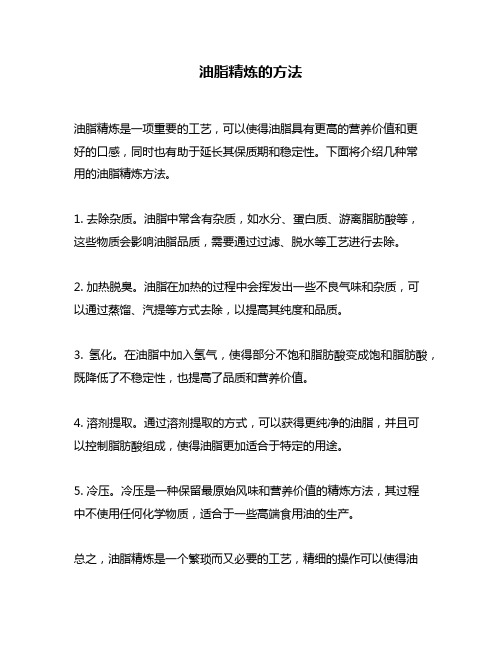
油脂精炼的方法
油脂精炼是一项重要的工艺,可以使得油脂具有更高的营养价值和更
好的口感,同时也有助于延长其保质期和稳定性。
下面将介绍几种常
用的油脂精炼方法。
1. 去除杂质。
油脂中常含有杂质,如水分、蛋白质、游离脂肪酸等,
这些物质会影响油脂品质,需要通过过滤、脱水等工艺进行去除。
2. 加热脱臭。
油脂在加热的过程中会挥发出一些不良气味和杂质,可
以通过蒸馏、汽提等方式去除,以提高其纯度和品质。
3. 氢化。
在油脂中加入氢气,使得部分不饱和脂肪酸变成饱和脂肪酸,既降低了不稳定性,也提高了品质和营养价值。
4. 溶剂提取。
通过溶剂提取的方式,可以获得更纯净的油脂,并且可
以控制脂肪酸组成,使得油脂更加适合于特定的用途。
5. 冷压。
冷压是一种保留最原始风味和营养价值的精炼方法,其过程
中不使用任何化学物质,适合于一些高端食用油的生产。
总之,油脂精炼是一个繁琐而又必要的工艺,精细的操作可以使得油
脂拥有更好的口感、营养价值和稳定性。
各种不同的精炼方法可以根据不同的需求进行选择和组合,以获得最佳的效果。
油脂精炼操作方法
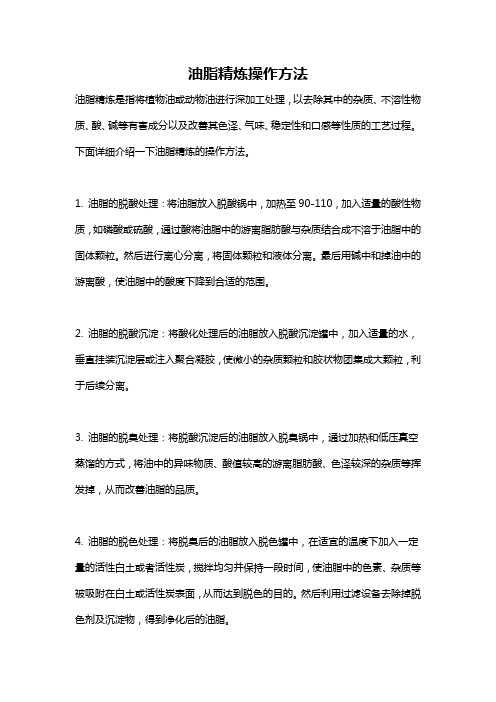
油脂精炼操作方法油脂精炼是指将植物油或动物油进行深加工处理,以去除其中的杂质、不溶性物质、酸、碱等有害成分以及改善其色泽、气味、稳定性和口感等性质的工艺过程。
下面详细介绍一下油脂精炼的操作方法。
1. 油脂的脱酸处理:将油脂放入脱酸锅中,加热至90-110,加入适量的酸性物质,如磷酸或硫酸,通过酸将油脂中的游离脂肪酸与杂质结合成不溶于油脂中的固体颗粒。
然后进行离心分离,将固体颗粒和液体分离。
最后用碱中和掉油中的游离酸,使油脂中的酸度下降到合适的范围。
2. 油脂的脱酸沉淀:将酸化处理后的油脂放入脱酸沉淀罐中,加入适量的水,垂直挂装沉淀层或注入聚合凝胶,使微小的杂质颗粒和胶状物团集成大颗粒,利于后续分离。
3. 油脂的脱臭处理:将脱酸沉淀后的油脂放入脱臭锅中,通过加热和低压真空蒸馏的方式,将油中的异味物质、酸值较高的游离脂肪酸、色泽较深的杂质等挥发掉,从而改善油脂的品质。
4. 油脂的脱色处理:将脱臭后的油脂放入脱色罐中,在适宜的温度下加入一定量的活性白土或者活性炭,搅拌均匀并保持一段时间,使油脂中的色素、杂质等被吸附在白土或活性炭表面,从而达到脱色的目的。
然后利用过滤设备去除掉脱色剂及沉淀物,得到净化后的油脂。
5. 油脂的脱水处理:将脱色后的油脂放入脱水罐中,通过低温、真空脱水的方式,将油脂中的水分蒸发掉,以提高油脂的保存质量和抗氧化能力。
6. 油脂的脱蜡处理:将脱水后的油脂放入脱蜡罐中,加热融化油脂中的结晶蜡,然后进行离心分离,将蜡沉淀分离出来,得到不含蜡的油脂。
7. 油脂的冷却和贮存:将脱蜡后的油脂冷却至适宜的温度,然后储存在密闭的容器中,避免光照和氧气的作用,以保持油脂的新鲜度和品质。
油脂精炼操作方法根据油脂的不同种类、原料的质量和使用的设备等因素而有所差异,但总体上可以分为脱酸、脱酸沉淀、脱臭、脱色、脱水、脱蜡和冷却贮存等步骤。
通过这些步骤,可以去除油脂中的杂质、不溶性物质、酸、碱等有害成分,改善其口感、稳定性、气味、色泽等性质,从而提高油脂的品质和市场竞争力。
油脂的精炼(Oil Refining)讲解
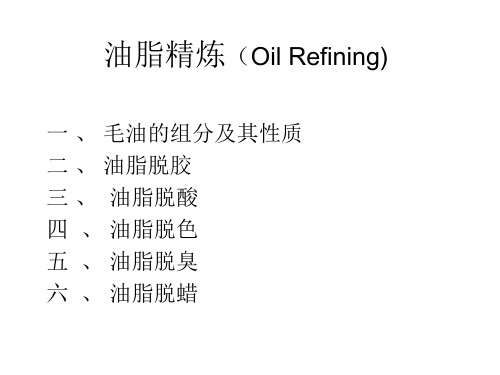
一 、 毛油的组分及其性质 二 、 油脂脱胶 三 、 油脂脱酸 四 、 油脂脱色 五 、 油脂脱臭 六 、 油脂脱蜡
概论
1、油脂精炼的目的: A、除去杂质;B、提高产品质量;C、利于安全储存。 2、油脂精炼要求: A、确定油脂精炼深度; B、组合精炼工艺合理; C、减少中性油和有益成分的损失; D、有利于副产物的综合利用; E、降低能量消耗; 3、油脂精炼方法: A、物化方法;B、化学方法;C、物理方法;
结晶塔
养晶塔
连续长混碱炼工艺流程
离心机工作原理图
Alfa Laval PX离心机碟片
第四节 脱色 (bleaching)
一、吸附脱色 二、工艺与设备
1、色素的成份
(1)天然色素: 油料中所含色素在制油过程进入油中。如叶绿 (黄)素、类胡萝卜素、棉酚。 (2)加工色素: 油脂生产中新生成的色素。 A、叶绿素受高温作用转变成叶绿素红色变体; B、游离脂肪酸与铁离子作用生成深色的铁皂; C、蛋白质、磷脂等有机降解产物; D、糖类的焦化,色原体氧化后呈现出颜色等;
2、油脂脱色方法
(1)吸附脱色;
(2)加热脱色:(类胡箩卜色素对热不稳定,经氧 化能变成无色物质)
(3)化学试剂脱色;
3、脱色工段作用
(1)脱除色素;
(2)脱除微量金属离子; (3)脱除残留皂粒、胶质; (4)脱除部分臭味物质; (5)脱除有毒物质;多环芳烃和残留农药、氧化产 物等。
4.吸附剂
水化脱胶工艺
1、间歇式水化脱胶工艺 软水 ↓ 过滤毛油→预热→水化→静置沉降→分离→含
水脱胶油→干燥(脱溶)→脱胶油 回收油←油脚处理←富油油脚
连续水化脱胶工艺流程
第三节 油脂脱酸(Oil deacidify)
油脂精炼的方法

油脂精炼的方法
油脂精炼是一种将原始油脂经过多次加工处理,去除杂质和不纯物质,提高油脂的纯度和质量的方法。
油脂精炼的目的是为了使油脂更加适合人们的食用和工业生产需求。
油脂精炼的过程通常包括以下几个步骤:去除杂质、脱色、脱臭和脱酸。
首先,原始油脂需要经过筛选和过滤,去除其中的杂质和不纯物质。
然后,油脂需要进行脱色处理,以去除其中的色素和其他杂质。
接着,油脂需要进行脱臭处理,以去除其中的异味和不良气味。
最后,油脂需要进行脱酸处理,以降低其中的酸度和提高其稳定性。
油脂精炼的方法有很多种,其中比较常见的包括物理精炼、化学精炼和混合精炼。
物理精炼是通过高温高压的物理处理方法,去除油脂中的杂质和不纯物质。
化学精炼则是通过添加化学剂,如酸、碱、蒸汽等,来去除油脂中的杂质和不纯物质。
混合精炼则是将物理精炼和化学精炼相结合,以达到更好的精炼效果。
油脂精炼的好处是显而易见的。
首先,精炼后的油脂更加纯净,更加适合人们的食用和工业生产需求。
其次,精炼后的油脂更加稳定,不易变质,可以更长时间地保存和使用。
最后,精炼后的油脂更加健康,不含有害物质,对人体健康更加有益。
油脂精炼是一种非常重要的加工方法,可以提高油脂的纯度和质量,
使其更加适合人们的食用和工业生产需求。
在未来,随着科技的不断进步和人们对健康的不断追求,油脂精炼的技术和方法也将不断发展和完善。
F 油脂精炼-脱蜡

一次结晶过滤工艺
脱臭米糠油在50℃以上送入冷却装置,在慢速搅拌、 常压下充分冷透至25℃。冷却结晶时间48h,然后过滤分离 油、蜡。过滤压强维持在0.3-0.35MPa,过滤后及时用压缩 空气吹出蜡中余油。
两次结晶过滤工艺
脱臭米糠油充分冷透至30℃,冷却结晶时间24h,过滤 除去大部分蜡,滤机压强不超过0.35MPa。滤出油第二次冷 却至25℃以下,冷却结晶24h,再过滤除去蜡质。滤出油即 为脱蜡油。
三、表面活性剂法工艺
在蜡晶析出过程中添加表面活性剂,强化结晶,改善油 -蜡分离效果。不同工艺目的添加表面活性剂种类及数量各 异。
四、中和冬化法工艺
将脱胶、脱酸和脱蜡组合在化学精炼工艺中的连续脱蜡 方法。
五、其他脱蜡法工艺
1.稀碱法;2.添加凝聚剂法;3.脲包脱蜡法
食工071、072、073
loozii0633
食工071、072、073
loozii0633
7
(二)结晶时间
足够的时间 = 缓慢结晶时间 + 持续养晶时间 养晶:熟成或老化
(三)搅拌速度 传热(冷却)均匀(放热过程,降温应均匀)
作用 提高晶体成长速度(单靠布朗运动结晶太慢) 减少晶簇的形成(晶簇包油,炼耗增大)
结晶、养晶过程应采用持续慢速搅拌,有利于 晶体成长,且不易形成晶簇:n=10-13r/min
食工071、072、073
loozii0633
12
一次结晶过滤法
脱臭米糠油
预热(搅拌)
冷却罐(搅拌)
过滤
脱蜡成品油
T≥50℃ n=60r/min
两次结晶过滤法
T=25℃ n=10-13r/min
t=48h
脱臭米糠油
- 1、下载文档前请自行甄别文档内容的完整性,平台不提供额外的编辑、内容补充、找答案等附加服务。
- 2、"仅部分预览"的文档,不可在线预览部分如存在完整性等问题,可反馈申请退款(可完整预览的文档不适用该条件!)。
- 3、如文档侵犯您的权益,请联系客服反馈,我们会尽快为您处理(人工客服工作时间:9:00-18:30)。
脱色吸附等温线
x/m 实 际 是 吸 附剂浓度(每100 份油取1份吸附剂 为单位重量)。 K是吸附剂活 性或脱色总能力。 n是吸附剂本 身吸附特性。
每1%白土除去的色度(罗维朋红色单位)
10 9 8 7 6 5 4 3 2
1 1 2 3 4 5 6 7 8 9 10 残留的色度(罗维朋红色单位)
1.油的品质及前处理:
(1)油脂中色素的成分; (2)残留胶质及悬浮杂质量。
2.吸附剂的质量和用量:
(1)吸附剂的种类; (2)吸附剂用量; (3)吸附剂的含水量。
3.操作压力:
(1)脱色伴有热氧化副反应; (2)不同操作压力下呈现出不同的脱色效果; (3)饱和程度低的油脂适宜在减压状态下脱色; (4)活性度较低的吸附剂宜在常压下脱色。
形式很多,主要有层板式、填料式、水平浅盘式脱臭 塔等。 为防止油流短路,有的采用折流隔板强制导向装置、 蒙马泵等。
(一)间歇式脱臭工艺及设备 间 歇 式 脱 臭 系 统
(二)半连续式脱臭工艺
双壳体塔
半连续 式 脱 臭 系 统
单壳体塔半连续式脱臭工艺
第四节
脱色 (bleaching)
主要内容 一、吸附脱色 二、其他脱色
1.色素的成份
(1)天然色素:
油料中所含色素在制油过程进入油中。如叶绿 (黄)素、类胡萝卜素、棉酚。
(2)加工色素:
油脂生产中新生成的色素。 A、叶绿素受高温作用转变成叶绿素红色变体; B、游离脂肪酸与铁离子作用生成深色的铁皂; C、蛋白质、磷脂等有机降解产物; D、糖类的焦化,色原体氧化后呈现出颜色等。
(2)化学吸附:
靠吸附剂表面自由能,吸附物和吸附剂之间 发生电子转移或形成共用电子,有选择性,高温 下进行。
2.吸附等温线
吸附是表面现象,取决于溶质与吸附剂之间特殊的 亲和力。在一定温度下剩余溶质浓度相关的吸附数学公 式由费兰德里胥导出如下 x/m=Kcn X-吸附物的量, m-吸附剂的量, c-残留物质量, K、n常数 也可以写成对数形式,在对数坐标上作x/m对c的 图,产生一条斜率为n的直线,即吸附等温线。
(四)吸附脱色工艺
1.间歇式脱色工艺:
(1)待脱色油的前处理:脱胶、脱酸; (2)油脂除氧及脱水; (3)添加吸附剂:真空吸入,避免吸入空气; (4)脱色; (5)分离吸附剂:进油量由小到大,以便形成好的滤 饼结构而保证过滤速率。过滤结束后。
间歇脱色罐及脱色工艺
1.待脱色油储罐 2.脱色罐 3.吸附剂罐 4.过滤机 5.油脂储槽
三、脱臭工艺及设备
1.间歇式脱臭:
时间长(8h)、耗蒸汽量大、热能利用率低。 蒸馏釜形式,高径比为2,油层下部有直接蒸汽盘管; 中央循环管,蒸汽从中央循环管上部喷出,强制循环。
2.半连续脱臭:
相当于多层间歇脱臭器重叠组成而成,脱臭过程被分 割为若干个独立的单元,每层的液层降低。层叠式如图642。
3.连续式脱臭:
(六)脱臭设备结构:
浅油层(200mm~250mm)、薄膜油层;防飞溅、防蒸馏液 回流;不锈钢材料; 脱臭系统的设备、管道、阀门、泵的严格密封,避免造 成真空度下降及油脂氧化。
(七)脱臭系统运行条件:
1.真空系统运行: (1)所需真空度、抽汽量、供汽压力等合理选型真空泵。 (2)动力蒸汽的量及压力稳定;冷凝水温度低。 (3)合理操作-设置止逆阀;真空装置终止运行前,以保 证安全运行(否则,冷凝水会倒吸)。 2.脂肪酸捕集: 脱臭馏出物要尽量回收,脂肪酸循环温度为60℃左 右。 3.热量回收: 脱臭成品油温240℃,可经过两次冷热油交换。 4.冷却过滤: 油温降至约40℃,安全过滤,成品油及时添加抗 氧化剂。
4.操作温度:
(1)操作温度取决于油脂品种,脱红色较脱黄色温度高。 (2)操作温度取决于操作压力。 (3)操作温度取决于吸附剂品种。 (4)温度高会造成油脂回色及酸价升高。
5.脱色时间:
(1)在最高温度下的脱色时间决定于吸附剂与色素间的吸 附平衡; (2)过长的时间,脱色速度明显缓慢甚至造成回色,共轭 化,油脂带异味等。 (3)正常时间:10-15min可满足脱色的要求。
一、油脂脱臭理论
(一)水蒸汽蒸馏理论:
1.油脂中臭味物质的蒸汽压大于甘三酯的蒸汽压。
Eg:250℃,高碳链脂肪酸蒸汽压为26.66~ 2.67kPa, 高碳链脂肪酸相应的甘三脂的蒸汽压为 1.33×10-3~1.33×10-4kPa。
2.油脂中其他臭味组分的蒸汽压比脂肪酸还要高。
油脂脱臭是液-气传质过程,汽-液表面相接触, 水蒸汽被挥发的臭味组分所饱和,并按其分压的比率 逸出,从而达到脱除臭味组分的目的。
2.飞溅损耗:
汽提蒸汽的机械作用而引起油脂飞溅损耗。
二、影响脱臭效果的因素
(一)温度:
1.温度升高,游离脂肪酸及臭味组分的蒸汽压力随之高。 2.蒸馏温度由177℃增加到204℃时,游离脂肪酸的汽化速率 可以增加3倍,温度增至232℃时,又可增加3倍。 3.过高温度会引起油脂分解、共轭化、反式酸,影响产品的 稳定性能并增加油脂的损耗。一般为230-270℃。
(1)脂肪酸和臭味组分的蒸汽压等于其在纯粹状态下的蒸汽压 乘上它在油脂中的浓度。 (2)脱臭塔的蒸发效率与设备的操作温度、压力、水蒸汽量/ 油量(S/O)三个主要参数有关: 在一定压力下,随着操作温度升高,臭味组分的蒸汽 压增大,使脱臭油中臭味组分的最终浓度降低。 固定脱臭深度,离塔脂肪酸的组分定为脱臭成品油的 质量指标,若操作温度保持不变, (S/O)将随着系统内 压力P的降低而减小,若操作压力接近真空,则水蒸汽用 量将会大幅度降低。由此,应最大限度负压操作。
脱色时间对豆油脱色程度的影响
80 温度 60 白土添加量 绝对压力 40 20 搅拌 2% 60mmHg 充分
95 C
o
黄色度
15
30
45
60
80
时间(min)
6.混合程度:
(1)固液非均匀反应要充分; (2)不能引起油脂飞溅以减少油脂氧。
7.脱色工艺:
(1)油脂与脱色剂逆流 、多次吸附平衡效果好。 (2)多层隔板脱色塔,管道式连续脱色器,此外,脱 色前的干燥、析气除氧等。
1.油脂臭味的来源
(1)油料含有的类脂物等在制油过程转入油脂。 (2)油脂制取、储藏过程中分解的物质。 如低分子醛、酮、酸、含硫化合物等。 (3)在制油和加工产生的工艺性气味: 如焦糊味、溶剂味,肥皂味、漂土味、氢化异味等。 (4)天然油脂中臭味组分:含量很低:为0.1-1.0%。 (5)油脂中臭味组分与游离脂肪酸含量降低相关: 当游离脂肪酸降至0.01~0.03%(过氧化值为0)时, 气味即消除。因此,脱臭的深度常用游离脂肪酸含量的降 低来衡量。 (6)油脂脱臭作用改善油脂风味,提高油脂烟点。
E、蛋白质、糖类降解后生成新的结合物(如胺基 糖)是一种棕黑色色素;用一般吸附剂对其脱 色无效。 F、蛋白质分解为氨基酸,多糖分解为单糖,经过 一系列反应而生成黑色素。在制油过程中应避 免形成新色素。
(3)色素的危害:
油中色素影响油品外观和使用性能,不同色 素对油品安定性有不同影响。 应脱除色素。
(1)改善油脂色泽;
(2)使油脂达到不同产品等级的要求;
(3)力求最低的油脂损耗,最低的副反应。
一、吸附脱色
(一)吸附剂 (二)吸附脱色机理 (三)影响吸附脱色的因素 (四)吸附脱色工艺
(一)吸附剂
1.吸附剂的种类:
(1)天然漂土:
又膨润土。主要组分Al4Si8O20(OH)4·nH2O,还 混有少量Ca、Mg、Fe、Na、K等成分。pH值为5~ 6,呈酸性,故又称酸性白土。因其脱色系数较 低,吸油率较高,逐渐为活性白土所代替。
色度(罗维朋红色单位)
6 5 4 3 2 1
B C
0
1
2
3
4 5 漂土量%
6
7
8
9
10
曲线说明:一般情况下,都要求K值大的吸附剂;在不降低K值的情 况下,n值愈大愈好。 B是符合要求K值大的吸附剂;当要求脱色降至2.1单位色度之前, 吸附剂C要比B有效,但如低于2.1单位色度, B优于 C。
(三)影响吸附脱色的因素
(四)待脱臭油和成品油质量:
脱臭前的油脂要很好的除去胶质、色素、微量金属后才 能得到优质的成品油;脱臭前进行脱氧析气(真空度与脱臭 相同,温度70℃以下) 。 极度酸败的油脂、胶杂、色素、微量金属含量高的油脂 难以精炼成高品质的油脂。
(五)直接蒸汽质量:
干燥脱氧的蒸汽,锅炉给水除氧,进塔前需进行严格的汽 水分离。
(二)热能脱色法:
油脂中的某些热敏性色素受热分解褪色。需要在 减压下进行,操作温度为140℃左右,色泽退变后应及 时冷却,以减缓油脂的热氧化。
(三)空气脱色法 (四)试剂脱色法:双氧水。 (五)其他脱色法
第五节
油脂脱臭(deodorization)
主要内容
一、脱臭理论 二、影响脱臭的因素 三、脱臭工艺 四、脱臭设备
(二)脱臭损耗:
先进工艺及合理操作条件下,脱臭最小损耗一般为 0.2~0.4%,再加上脱臭原料油中FFA含量的1.05~1.2倍。
1.蒸馏损耗:
(1)易蒸馏的低分子醛、酮及游离脂肪酸 (2)少部分油脂水解生成脂肪酸: 当FFA含量降低至0.015-0.03%时,游离脂肪酸的脱 除速率与油脂水解生成游离脂肪酸的速率达到平衡。而 实际上中性油的蒸馏损耗可认为甘三酯水解生成的甘二 酯和脂肪酸被蒸馏而损耗。 (3)难以蒸馏的甾醇及其他不皂化物
2.吸附剂的选择依据
取决于成本、活性、油脂残留三个因素的平衡
油脂工业吸附剂应具备条件:
(1)对色素吸附力强 (2)吸油少 (3)化学性质稳定,不对油脂产生不良作用 (4)方便使用,易与油脂分离 (5)来源广、价廉、使用经济
(二)吸附脱色机理