防腐层修复
管道防腐层修复及缺陷修复(补强)工程---施工方案.
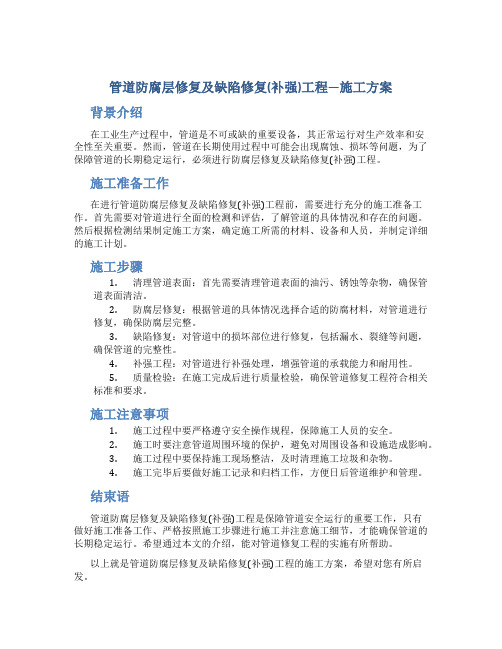
管道防腐层修复及缺陷修复(补强)工程—施工方案背景介绍在工业生产过程中,管道是不可或缺的重要设备,其正常运行对生产效率和安全性至关重要。
然而,管道在长期使用过程中可能会出现腐蚀、损坏等问题,为了保障管道的长期稳定运行,必须进行防腐层修复及缺陷修复(补强)工程。
施工准备工作在进行管道防腐层修复及缺陷修复(补强)工程前,需要进行充分的施工准备工作。
首先需要对管道进行全面的检测和评估,了解管道的具体情况和存在的问题。
然后根据检测结果制定施工方案,确定施工所需的材料、设备和人员,并制定详细的施工计划。
施工步骤1.清理管道表面:首先需要清理管道表面的油污、锈蚀等杂物,确保管道表面清洁。
2.防腐层修复:根据管道的具体情况选择合适的防腐材料,对管道进行修复,确保防腐层完整。
3.缺陷修复:对管道中的损坏部位进行修复,包括漏水、裂缝等问题,确保管道的完整性。
4.补强工程:对管道进行补强处理,增强管道的承载能力和耐用性。
5.质量检验:在施工完成后进行质量检验,确保管道修复工程符合相关标准和要求。
施工注意事项1.施工过程中要严格遵守安全操作规程,保障施工人员的安全。
2.施工时要注意管道周围环境的保护,避免对周围设备和设施造成影响。
3.施工过程中要保持施工现场整洁,及时清理施工垃圾和杂物。
4.施工完毕后要做好施工记录和归档工作,方便日后管道维护和管理。
结束语管道防腐层修复及缺陷修复(补强)工程是保障管道安全运行的重要工作,只有做好施工准备工作、严格按照施工步骤进行施工并注意施工细节,才能确保管道的长期稳定运行。
希望通过本文的介绍,能对管道修复工程的实施有所帮助。
以上就是管道防腐层修复及缺陷修复(补强)工程的施工方案,希望对您有所启发。
管线外防腐层破损原因及修复技术

管线外防腐层破损原因及修复技术
管线外防腐层破损可能是由于多种原因引起的,如外力破坏、腐蚀等。
修复技术主要包括修补和重涂两种方法。
管线外防腐层的破损原因主要包括以下几个方面:
1. 外物撞击:当管道位于地下或地面上容易受到外物的碰撞,如路面施工时的机械碰撞,杆路砂浆碰撞等,导致管道外防腐层破损。
2. 腐蚀:由于管道运行环境的气候湿度,介质条件等原因,使管道出现腐蚀现象,导致管道外防腐层脱落。
3. 温度变化:管道运行过程中,温度的变化会导致管道材料的膨胀和收缩,从而引起外防腐层的开裂或脱落。
根据不同的破损原因,可以采取以下修复技术:
1. 修补:修补是指在管道外防腐层破损处进行局部修复。
修补材料可以选择合适的环氧树脂或耐腐蚀性较强的聚合物,将其填充到破损处,并将其平整。
在填充之前,需要将破损处清洁干燥,并进行必要的融合处理,以保证修补部位的附着力。
2. 重涂:重涂是指将完全的撕去原有的外防腐层,然后重新进行涂层的喷涂。
该方法适用于破损较大的管道。
在进行重涂之前,需要彻底清洁管道表面,去除原有的外防腐层和腐蚀物,并进行必要的抛光和坑洞填补。
然后使用适当的喷涂材料,喷涂一定厚度的新的外防腐层,以保护管道。
无论是修补还是重涂,修复后的管道都需要进行严密的检测,以确保修复效果。
常用的检测方法包括涂层附着力测试、腐蚀检测和水密性检测等。
管线外防腐层破损的原因及修复技术多种多样,根据具体情况选择适当的修复方法,以延长管道的使用寿命,提高管道的安全性。
管道防腐层修复及缺陷修复(补强)工程---施工方案
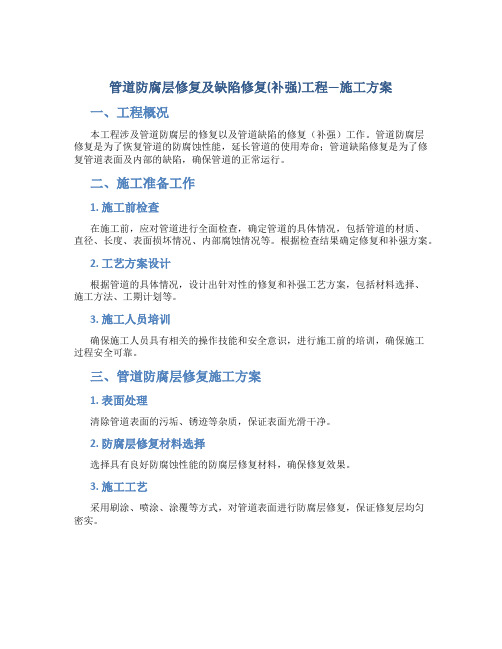
管道防腐层修复及缺陷修复(补强)工程—施工方案一、工程概况本工程涉及管道防腐层的修复以及管道缺陷的修复(补强)工作。
管道防腐层修复是为了恢复管道的防腐蚀性能,延长管道的使用寿命;管道缺陷修复是为了修复管道表面及内部的缺陷,确保管道的正常运行。
二、施工准备工作1. 施工前检查在施工前,应对管道进行全面检查,确定管道的具体情况,包括管道的材质、直径、长度、表面损坏情况、内部腐蚀情况等。
根据检查结果确定修复和补强方案。
2. 工艺方案设计根据管道的具体情况,设计出针对性的修复和补强工艺方案,包括材料选择、施工方法、工期计划等。
3. 施工人员培训确保施工人员具有相关的操作技能和安全意识,进行施工前的培训,确保施工过程安全可靠。
三、管道防腐层修复施工方案1. 表面处理清除管道表面的污垢、锈迹等杂质,保证表面光滑干净。
2. 防腐层修复材料选择选择具有良好防腐蚀性能的防腐层修复材料,确保修复效果。
3. 施工工艺采用刷涂、喷涂、涂覆等方式,对管道表面进行防腐层修复,保证修复层均匀密实。
四、管道缺陷修复(补强)施工方案1. 缺陷检修根据管道检查结果确定缺陷位置及缺陷类型,制定修复方案。
2. 修复材料选择根据缺陷类型选择适合的修复材料,包括涂料、补丁、套管等。
3. 施工工艺根据具体情况采用包裹法、补丁法等方式对管道缺陷进行修复,保证修复后的管道表面光滑、无漏洞。
五、施工安全与质量控制1. 安全措施施工过程严格遵守安全操作规程,保证施工人员安全。
2. 质量控制安排专人负责施工现场质量检查,确保施工质量达到要求。
六、总结通过管道防腐层修复及缺陷修复(补强)工程的施工方案设计和实施,可有效恢复管道的正常运行状态,延长管道的使用寿命,保障工程的安全运行。
管线外防腐层破损原因及修复技术

管线外防腐层破损原因及修复技术管线的外防腐层破损主要有以下几个原因:1. 材料老化:外防腐层的材料随着使用时间的增加会发生老化,失去原有的防腐效果。
材料老化可以是由于长期暴露在恶劣环境中,受到氧气、水分、紫外线等因素的侵蚀,也可以是由于材料的化学性质发生变化导致。
2. 外力作用:管线周围环境中存在各种外力作用,比如土壤运动、地震、机械碰撞等,这些外力作用会导致管线的外防腐层破损。
土壤运动可能是最主要的破坏原因,因为土壤中存在不规则的腐蚀体或者尖锐的岩石等物质,在地震或运动的情况下会对管道表面造成划伤或者冲击。
3. 腐蚀影响:管线外防腐层的破损也可能是由于内部腐蚀影响导致的。
管道内部的腐蚀反应会导致管道表面的薄弱点,进而容易受到外界环境的影响而出现脱落、破裂等破损问题。
以下是一些常用的管线外防腐层修复技术:1. 手工修复:对于小面积的破损,可以采用手工修复的方式。
首先清理并修整管道表面,然后使用防腐蚀材料进行涂抹,最后再涂上防腐蚀漆进行保护。
2. 点腐蚀修复:点腐蚀是管线外防腐层破损的一种常见类型,可以使用绝缘补丁或者冷补料来修复。
首先清理并修整破损部位,然后使用绝缘补丁或者冷补料粘贴在破损部位上,最后再涂上防腐蚀漆进行保护。
4. 热缩修复:热缩修复是一种比较常用的管线外防腐层破损修复技术。
首先清理并修整管道表面,然后将热缩修复带套在破损部位上,使用专用的热风枪加热使其收缩并与管道表面完全贴合,形成一层保护膜,最后再涂上防腐蚀漆进行保护。
热缩修复具有操作简便、修复效果好的特点。
管线外防腐层破损会给管道的使用寿命和安全性造成影响,因此及时修复是非常重要的。
选择合适的修复技术,可以有效地保护管道的外部防腐层,延长管道的使用寿命。
管线外防腐层破损原因及修复技术

管线外防腐层破损原因及修复技术管线外防腐层是保护管道的重要层,它能够防止管道受到腐蚀、磨损和机械损害,延长管道的使用寿命。
管线外防腐层破损却是一个常见的问题,因为管道运行环境复杂多变,破损原因多种多样。
为了保障管道的正常运行和安全,及时修复管线外防腐层就显得十分重要。
本文将分析管线外防腐层破损的原因,并介绍一些修复技术。
一、管线外防腐层破损原因1. 腐蚀腐蚀是管线外防腐层破损的主要原因之一。
管道长期处于恶劣环境中,比如潮湿、盐碱地带、酸碱环境等,容易受到腐蚀。
腐蚀不仅会损坏防腐层,也会损害管道本身的材质,导致管道渗漏、爆裂等问题。
2. 磨损管道在运行过程中会受到外界环境的影响,比如砂石的冲刷、机械设备的碰撞等,会导致管道防腐层的磨损。
磨损严重的管道会逐渐失去防腐作用,从而加速管道的老化损坏。
3. 温度变化管道在运行过程中,由于介质温度的变化,管道表面的温度也会发生变化,频繁的温度变化会导致管道外防腐层出现龟裂、剥落等现象。
4. 裂纹管道在运行中可能会出现裂纹,裂纹会导致管道外防腐层的损坏,进而影响管道的使用寿命和安全性。
5. 不良施工管道外防腐层在施工过程中,如果材料质量不过关、施工工艺不合理等原因,会导致管道外防腐层破损。
不良施工会直接影响到管道的使用寿命和安全性。
1. 补漆修复法补漆修复法是一种简单有效的修复技术,适用于管道外防腐层小面积损坏的情况。
首先需要将损坏部分的防腐漆清理干净,然后使用专用的防腐漆进行补漆修复。
这种修复技术操作简单,成本低廉,但只适用于小范围的修复。
2. 缠绕修复法缠绕修复法是指将聚酯带或玻璃钢带缠绕在损坏部分的管道上,然后涂上特制的环氧树脂胶水进行固化。
这种修复技术可以有效修复管道的防腐层破损,且具有耐腐蚀、耐磨损的特性,适用于各种管道的修复。
3. 喷涂修复法喷涂修复法是一种自动化程度高的修复技术,使用专用的设备将防腐涂料喷涂在管道表面,形成均匀的防腐层。
这种修复技术适用于管道大面积的防腐层修复,能够保证管道的防腐效果和美观度。
埋地管道腐蚀修补及防腐保温层修复技术
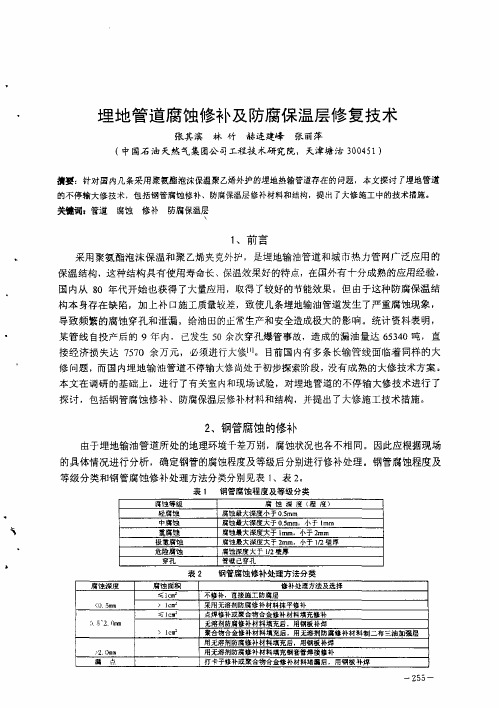
埋地管道腐蚀修补及防腐保温层修复技术张其滨林竹赫连建峰张丽萍(中国石油天然气集团公司工程技术研究院,天津塘沽300451)擅要:针对国内几条采用聚氨醢泡沫保温聚乙烯外护的埋地热输管道存在的问题,本文探讨,埋地管道的不停输大修技术.包括钢管腐蚀修补、防腐保温层修补材料和结构,提出了大修施工中的技术措施。
关键词t管道腐蚀修补防腐保温层1、前言采用聚氨酯泡沫保温和聚乙烯夹克外护,是埋地输油管道和城市热力管网广泛应用的保温结构,这种结构具有使用寿命长、保温效果好的特点,在国外有十分成熟的应用经验,国内从80年代开始也获得了大量应用,取得了较好的节能效果。
但由于这种防腐保温结构本身存在缺陷,加上补口施工质量较差,致使几条埋地输油管道发生了严重腐蚀现象,导致频繁的腐蚀穿孔和泄漏,给油田的正常生产和安全造成极大的影响。
统计资料表明,某管线自投产后的9年内,己发生50余次穿孔爆管事故,造成的漏油量达65340吨,直接经济损失达7570余万元,必须进行大修【I I。
目前国内有多条长输管线面临着同样的大修问题,而国内埋地输油管道不停输大修尚处于初步探索阶段,没有成熟的大修技术方案。
本文在调研的基础上,进行了有关室内和现场试验,对埋地管道的不停输大修技术进行了探讨,包括钢管腐蚀修补、防腐保温层修补材料和结构,并提出了大修施工技术措施。
2、钢管腐蚀的修补由于埋地输油管道所处的地理环境千差万别,腐蚀状况也各不相同。
因此应根据现场的具体情况进行分析,确定钢管的腐蚀程度及等级后分别进行修补处理。
钢管腐蚀程度及等级分类和钢管腐蚀修补处理方法分类分别见表1、表2。
表1钢管腐蚀程度及等级分类腐蚀等级腐蚀探度(程度)中腐蚀I腐蚀擐太_深度太于o 5m m.小于I m m极重腐蚀I腐蚀最大深度大于2mm,小于1/2壁厚危险腐蚀I腐蚀深度大于【,2壁厚表2铜管腐蚀修补处理方法分类腐蚀深度腐蚀面积1蕾补处理方法及选择不饪朴.直接施工防腐层采用无溶剂防腐修补材料捧平修扑c一电掉咎补戚聚台期合垒培补材料填充修补无溶剂防腐修补材料填充后.用钢板补焊聚台物台金任补材料填充后.用无溶剂防腐任补材料制二布三油加强层闩j无溶剂防腐修补材抖填充后.用钢板补焊用无溶剂防腐修补材料填充翻套管焊接修朴漏点打卡子恬补或聚合物音金恬补材科堵漏后,用铜板幸卜焊3、防腐层修复材料及结构防腐层是保护管道不受腐蚀的主要屏障。
管线外防腐层破损原因及修复技术

管线外防腐层破损原因及修复技术
管线的外防腐层是为了保护管道,延长其使用寿命而设置的一层防护层。
在使用过程中,外防腐层有可能出现破损,导致管道受到腐蚀,进而影响管道的正常运行。
本文将介绍管线外防腐层破损的原因以及修复技术。
管线外防腐层破损的原因主要有以下几点:
1.机械损伤:在施工、运输和安装过程中,管道可能会受到外力的作用,导致外防腐层破损。
管道被重物碰撞、划伤等。
2.化学腐蚀:一些腐蚀性物质如果和管道表面接触,会导致外防腐层破损。
化学品泄漏、腐蚀性土壤等都会对外防腐层产生损害。
3.电化学腐蚀:当管道与其他金属物或电解质接触时,会产生电化学反应,从而导致电流流过管道,引起外防腐层的破损。
针对不同的破损情况,可以采取不同的修复技术。
下面将介绍几种常见的修复技术:
1.喷涂修复技术:对于较小的破损区域,可以采用喷涂修复技术。
对破损区域进行清理和打磨,然后使用特殊的喷涂设备将修复剂喷涂在破损区域上。
修复剂可以填充破损处的孔洞,形成一层保护层。
3.环氧灌注修复技术:对于管道内壁的腐蚀和破损,可以采用环氧灌注修复技术。
通过清理和打磨管道内壁,去除腐蚀和破损的部分。
然后,将环氧树脂灌注至管道内壁,形成一层坚固的修复层。
4.局部更换修复技术:对于严重破损的管道,可能需要进行局部更换修复。
这种修复方式需要先将破损的部分切除,并通过焊接或其他连接方式将新的管道连接起来。
管线外防腐层破损会对管道的运行安全和寿命产生不利影响,因此及时发现和修复破损的部位是非常重要的。
通过采用适当的修复技术,可以保护管道不受腐蚀,延长其使用寿命。
自修复防腐涂层的研究现状
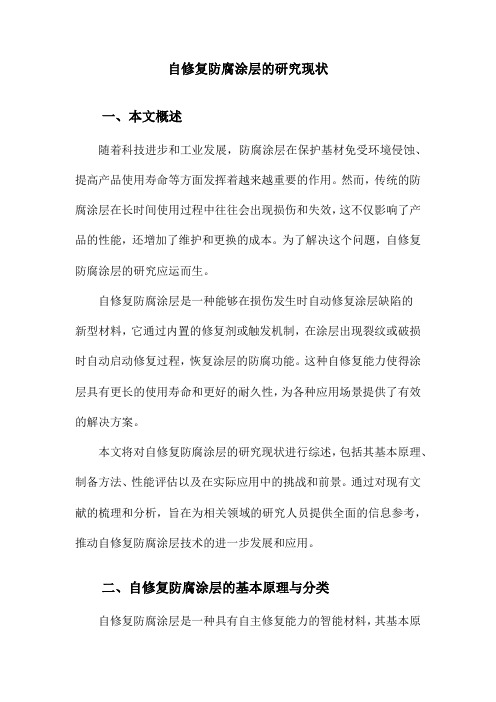
自修复防腐涂层的研究现状一、本文概述随着科技进步和工业发展,防腐涂层在保护基材免受环境侵蚀、提高产品使用寿命等方面发挥着越来越重要的作用。
然而,传统的防腐涂层在长时间使用过程中往往会出现损伤和失效,这不仅影响了产品的性能,还增加了维护和更换的成本。
为了解决这个问题,自修复防腐涂层的研究应运而生。
自修复防腐涂层是一种能够在损伤发生时自动修复涂层缺陷的新型材料,它通过内置的修复剂或触发机制,在涂层出现裂纹或破损时自动启动修复过程,恢复涂层的防腐功能。
这种自修复能力使得涂层具有更长的使用寿命和更好的耐久性,为各种应用场景提供了有效的解决方案。
本文将对自修复防腐涂层的研究现状进行综述,包括其基本原理、制备方法、性能评估以及在实际应用中的挑战和前景。
通过对现有文献的梳理和分析,旨在为相关领域的研究人员提供全面的信息参考,推动自修复防腐涂层技术的进一步发展和应用。
二、自修复防腐涂层的基本原理与分类自修复防腐涂层是一种具有自主修复能力的智能材料,其基本原理是在涂层受到损伤或破坏时,能够自动触发修复机制,恢复涂层的完整性和防腐功能。
这种自修复能力使得涂层在复杂多变的环境条件下具有更长的使用寿命和更好的保护效果。
自修复防腐涂层的分类可以根据其修复机制的不同来进行。
一种常见的分类方式是将其分为化学自修复和物理自修复两大类。
化学自修复涂层通过在涂层中添加特定的化学物质,如微胶囊、纳米容器等,这些物质在涂层受损时会释放出修复剂,与涂层中的成分发生化学反应,填补损伤并恢复涂层的防腐性能。
物理自修复涂层则依赖于涂层本身的物理性质,如弹性、粘性等,在涂层受到损伤时通过物理作用如流动、扩散等来填补损伤,恢复涂层的完整性。
除了上述分类方式,自修复防腐涂层还可以根据其修复触发方式的不同来进行分类。
例如,有些涂层需要在特定的环境条件下才能触发修复机制,如温度、光照、湿度等,这些被称为环境条件触发型自修复涂层。
而有些涂层则能够在涂层受到损伤时立即触发修复机制,这种被称为损伤触发型自修复涂层。
管道及防腐层修补技术规定

管道及防腐层修补技术规定(一)、管道修补技术规定:1、埋地和保温架空管道由手多种原因而造成局部腐蚀和点状腐蚀,威胁管道安全生产。
为此要求在管道防腐层修补和检查管道保温层时要注意这种情况,及时进行处理。
2、当管道腐蚀深度大于1毫米,腐蚀面积小手2cm2时,直接用电焊补焊。
要求焊缝饱满外表平滑。
当腐蚀面积大于2cm2,深度大于3毫米时,施行外加钢板补焊的办法。
3、管道腐蚀深度小于0.5毫米,面积小于10cm2,可以不补焊,做好防腐绝缘即可。
4、如果管道埋地时间不到几年而出现了大面积的腐蚀是不正常的情况,说明管道使用和检漏补漏工作存在问题。
主管部门应做调查并采取措施。
(二)管道防腐层修补技术规定:1、小型修补防腐层所用的原材料应和原防腐层材料一致,较大型的防腐层修补用其它材料时,应向公司管道科报告。
2、检漏挖出管道后,当漏点用眼晴不易发现时,应当用火花仪仔细检查,做出记号,以待修补。
3、凡修补过的防腐层均需做耐电压检查,电压一万伏不发生火花为合格。
4、修补过的防腐层表面要光滑,不得凸凹不平或折皱,厚度不小于8毫米,最外层要求贴上或包上塑料布。
5、当防腐层露铁面积小于1cm2,或者刀口划破长度小于30cm2 时,用喷灯烤化愿防腐层再用热沥青添满抹平。
6、露铁较大或者防腐层破损较大时,需按原来的结构进行修补,修补时削好接茬。
所用玻璃布要清洁干燥,修补过的防腐层厚度要够,粘接要牢。
7、修补防腐层需携带专用工具,不得将块状沥青放漏点烤化凑合施工,修补前露铁点要除锈,刷底漆,管道修补处必须干净干燥。
8、修补完成经自检合格后,要求站长进行验收,然后回填细土高于管顶30cm后方可大量回填,恢复地貌。
3pe防腐管防腐层补伤措施

3pe防腐管防腐层补伤措施3PE防腐管是一种常用的管道防腐材料,其具有优良的防腐性能和耐腐蚀性能。
然而,在使用过程中,由于各种原因,3PE防腐管的防腐层可能会发生损伤。
为了保证管道的防腐效果和使用寿命,需要采取相应的补伤措施。
对于3PE防腐管的补伤措施,我们需要了解什么是3PE防腐层。
3PE防腐层是由三层涂覆而成的,分别是底层的环氧粉末涂层、中间层的粘结层和外层的聚乙烯层。
这三层涂覆能够形成一个完整的防腐层,起到很好的防腐作用。
如果3PE防腐管的防腐层出现了损伤,我们需要对其进行补伤处理。
首先,需要对损伤部位进行清理,去除附着物和锈蚀物,使其表面光洁。
然后,使用砂布或砂纸对损伤部位进行打磨,使其表面粗糙,增加涂料的附着力。
接下来,需要在损伤部位上涂刷环氧底漆。
环氧底漆具有很好的附着力和抗腐蚀性能,能够有效地修补损伤部位。
在涂刷环氧底漆之前,需要将底漆充分搅拌均匀,然后使用刷子或滚筒将其均匀涂刷在损伤部位上,形成一层均匀的底漆。
底漆干燥后,需要进行中间层的涂覆。
中间层通常采用聚乙烯或胶带进行涂覆。
对于聚乙烯涂覆,需要将其预热至一定温度,然后将其包裹在管道上,使用压力机将其压紧,使其与管道表面紧密贴合。
对于胶带涂覆,需要将其粘贴在损伤部位上,然后用刮板将其压紧,确保其与管道表面紧密贴合。
需要对外层的聚乙烯层进行涂覆。
聚乙烯层的涂覆可以采用喷涂或滚涂的方式进行。
在涂覆之前,需要将聚乙烯涂料充分搅拌均匀,然后使用喷涂枪或滚筒将其均匀涂覆在管道表面上,形成一层均匀的聚乙烯层。
在涂覆完毕后,需要对其进行充分干燥,确保其防腐效果。
除了以上的补伤措施,我们还需要注意一些其他的细节。
例如,在进行补伤处理之前,需要对管道进行彻底的清洗,确保其表面没有油污和杂质。
另外,补伤处理过程中需要严格控制涂料的厚度和涂覆的质量,确保其达到标准要求。
此外,还需要对补伤部位进行定期检查和维护,及时修补和更换损伤的防腐层,以保证其持久的防腐效果。
管线外防腐层破损原因及修复技术
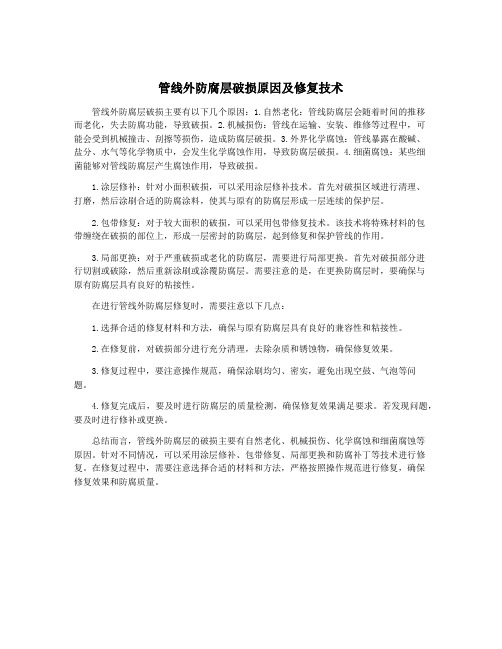
管线外防腐层破损原因及修复技术管线外防腐层破损主要有以下几个原因:1.自然老化:管线防腐层会随着时间的推移而老化,失去防腐功能,导致破损。
2.机械损伤:管线在运输、安装、维修等过程中,可能会受到机械撞击、刮擦等损伤,造成防腐层破损。
3.外界化学腐蚀:管线暴露在酸碱、盐分、水气等化学物质中,会发生化学腐蚀作用,导致防腐层破损。
4.细菌腐蚀:某些细菌能够对管线防腐层产生腐蚀作用,导致破损。
1.涂层修补:针对小面积破损,可以采用涂层修补技术。
首先对破损区域进行清理、打磨,然后涂刷合适的防腐涂料,使其与原有的防腐层形成一层连续的保护层。
2.包带修复:对于较大面积的破损,可以采用包带修复技术。
该技术将特殊材料的包带缠绕在破损的部位上,形成一层密封的防腐层,起到修复和保护管线的作用。
3.局部更换:对于严重破损或老化的防腐层,需要进行局部更换。
首先对破损部分进行切割或破除,然后重新涂刷或涂覆防腐层。
需要注意的是,在更换防腐层时,要确保与原有防腐层具有良好的粘接性。
在进行管线外防腐层修复时,需要注意以下几点:1.选择合适的修复材料和方法,确保与原有防腐层具有良好的兼容性和粘接性。
2.在修复前,对破损部分进行充分清理,去除杂质和锈蚀物,确保修复效果。
3.修复过程中,要注意操作规范,确保涂刷均匀、密实,避免出现空鼓、气泡等问题。
4.修复完成后,要及时进行防腐层的质量检测,确保修复效果满足要求。
若发现问题,要及时进行修补或更换。
总结而言,管线外防腐层的破损主要有自然老化、机械损伤、化学腐蚀和细菌腐蚀等原因。
针对不同情况,可以采用涂层修补、包带修复、局部更换和防腐补丁等技术进行修复。
在修复过程中,需要注意选择合适的材料和方法,严格按照操作规范进行修复,确保修复效果和防腐质量。
管线外防腐层破损原因及修复技术

管线外防腐层破损原因及修复技术管线外防腐层的破损可能是由多种因素引起的,包括机械破坏、腐蚀、温度变化、光照等。
当外防腐层破损时,会导致管线暴露在环境中,加速腐蚀的进程,最终可能导致管线的失效。
及时发现破损并进行修复是非常重要的。
机械破坏是导致管线外防腐层破损的常见原因之一。
机械破坏包括意外碰撞、挤压、刮擦等。
在施工过程中,如果管道暴露在机械碰撞的风险中,就需要采取预防措施,比如利用防护材料包覆管道或者进行异物堵塞。
如果发现了机械破坏导致的外防腐层破损,可以通过修复涂料或者补丁来修复破损的部分。
腐蚀是导致管线外防腐层破损的另一个重要原因。
腐蚀可以是由于管道材料自身的腐蚀性,也可以是由于管道周围环境的腐蚀性。
腐蚀性物质如化学物质、氧气、微生物等可能会导致管道表面发生腐蚀。
为了预防腐蚀引起的管道外防腐层破损,可以使用抗腐蚀材料来涂覆管道表面,例如涂层、被覆物等。
修复破损的外防腐层时,需要首先清除破损区域的腐蚀产物,然后使用适合的修复涂料进行修复。
温度的变化也可能导致管线外防腐层的破损。
温度变化会引起管道材料膨胀和收缩,从而导致外防腐层的开裂和脱落。
为了预防温度变化引起的外防腐层破损,可以使用具有良好防腐性和热稳定性的材料进行涂覆,以适应温度变化。
修复破损的外防腐层时,可以使用弹性修复材料填充裂缝或者修复膜来补充脱落的部分。
光照也可能引起外防腐层的破损。
长时间的紫外线照射会导致外防腐层老化和退化,使其变脆并易于破损。
为了预防光照引起的外防腐层破损,可以使用耐候性良好的抗紫外线涂层进行涂覆。
对于已经破损的外防腐层,可以通过刮削表面、清除老化层,然后重新涂刷防腐涂料进行修复。
管线外防腐层破损的原因包括机械破坏、腐蚀、温度变化和光照等。
针对不同原因导致的破损,可以采取不同的修复技术,如修复涂料、补丁、涂层和被覆物等。
在破损修复的过程中,需要对破损区域进行清理、刮削和补充,以确保修复效果。
通过及时发现破损并进行修复,可以延长管线的使用寿命,提高管道的安全性能。
燃气管道防腐层损伤的检测与修复
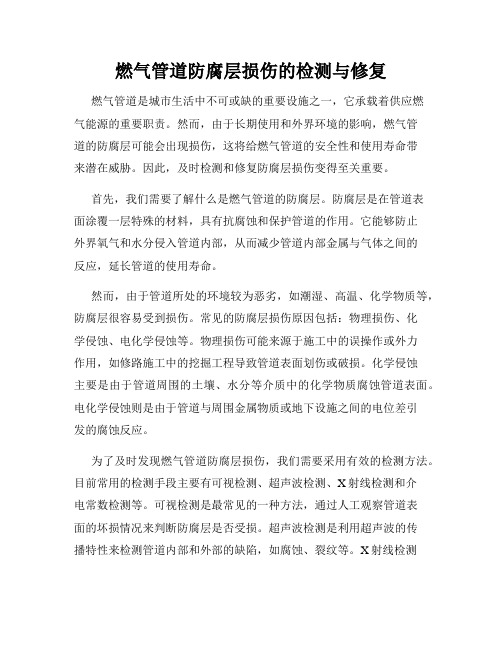
燃气管道防腐层损伤的检测与修复燃气管道是城市生活中不可或缺的重要设施之一,它承载着供应燃气能源的重要职责。
然而,由于长期使用和外界环境的影响,燃气管道的防腐层可能会出现损伤,这将给燃气管道的安全性和使用寿命带来潜在威胁。
因此,及时检测和修复防腐层损伤变得至关重要。
首先,我们需要了解什么是燃气管道的防腐层。
防腐层是在管道表面涂覆一层特殊的材料,具有抗腐蚀和保护管道的作用。
它能够防止外界氧气和水分侵入管道内部,从而减少管道内部金属与气体之间的反应,延长管道的使用寿命。
然而,由于管道所处的环境较为恶劣,如潮湿、高温、化学物质等,防腐层很容易受到损伤。
常见的防腐层损伤原因包括:物理损伤、化学侵蚀、电化学侵蚀等。
物理损伤可能来源于施工中的误操作或外力作用,如修路施工中的挖掘工程导致管道表面划伤或破损。
化学侵蚀主要是由于管道周围的土壤、水分等介质中的化学物质腐蚀管道表面。
电化学侵蚀则是由于管道与周围金属物质或地下设施之间的电位差引发的腐蚀反应。
为了及时发现燃气管道防腐层损伤,我们需要采用有效的检测方法。
目前常用的检测手段主要有可视检测、超声波检测、X射线检测和介电常数检测等。
可视检测是最常见的一种方法,通过人工观察管道表面的坏损情况来判断防腐层是否受损。
超声波检测是利用超声波的传播特性来检测管道内部和外部的缺陷,如腐蚀、裂纹等。
X射线检测则是通过X射线的透射和吸收特性来检测管道内的缺陷。
介电常数检测则是通过测量管道防腐层的电磁特性来判断其损伤程度。
一旦发现管道防腐层损伤,我们需要及时采取修复措施。
修复方法根据损伤程度的不同而有所区别。
对于小面积的表面划伤或破损,我们可以采用修补材料进行修复。
修补材料通常是一种具有较强附着力和耐腐蚀性能的防腐涂料,能够覆盖并修复防腐层上的损伤部位。
对于较大范围的腐蚀或破损,我们可能需要更换整段管道或进行焊接修复。
焊接修复是将损坏的管道切割下来,然后通过焊接技术将新的管道连接起来。
防腐层修补步骤

防腐层修补步骤一、3PE防腐层修补1、小于30mmx30mm,点、面、线状,单一3PE破损点修补技术要求(一)、除去损伤部位的污物,并将该处的聚乙烯层打毛。
(二)、将损伤部位的聚乙烯层修切圆滑,边缘应为钝角,在孔内填满与补伤片配套的胶黏剂,然后贴上补伤片。
补伤片的大小应保证其边缘距聚乙烯层的孔洞边缘不小于50mm。
(三)、贴补时应边加热边用辊子滚压或戴耐热手套用手挤压,排出空气,直至补伤片四周胶黏剂均匀溢出。
(四)、补伤片四周必须采用热熔胶进行加固固定。
2、大于30mmx30mm,3PE破损点此时应采用辐射交联聚乙烯热收缩带(套),选取的热收缩套应该按管径选用配套的规格,产品的基材边缘应平直,表面应平整、清洁、无气泡、裂口及分解变色。
热收缩带的周向收缩率不应小于百分之15;热收缩套的周向收缩率不应小于百分之50。
二、FBE防腐层修补1、小于或等于30mmx30mm,点、面、线状,单一FBE破损点修补技术要求(1)、固化剂与无溶剂环氧底漆原理1:2方式调和。
(2)、应采用硬的刷子或短毛辊筒用力,涂膜厚度控制在400um以内,以防流挂现象发生。
(3)、需要涂层2道。
第二道涂层在第一道涂层之上,并适当放大涂层面。
2、大于30mmx30mm,点、面、线状单一破损点,或者破损点密集区域。
(1)、管道金属表面处理方式:必须要对表面进行打磨,在施工前要除去全部的油脂及其他污物。
(2)、破损点周边防腐层处理要求:干净、无油脂和其他污物。
(挖出漏点附件的一段管道,用水清理表面泥土、用抹布擦净管道、用卫生纸擦干、用红笔圈出破损点的位置)(3)、要求周边环境相对湿度百分之80以上、温度5摄氏度以上。
(4)、修补结束后需要在外围涂上一层胶后最外层用冷缠带进行多圈缠绕带,其间必须要清楚缠绕带内空气。
三、修补处质量验收1、补伤后的外观应逐个检查,表面应平整、无皱折、无气泡、无烧焦碳化现象;补伤片四周应粘结密封良好,不合格的应重补。
管道防腐层修复情况汇报
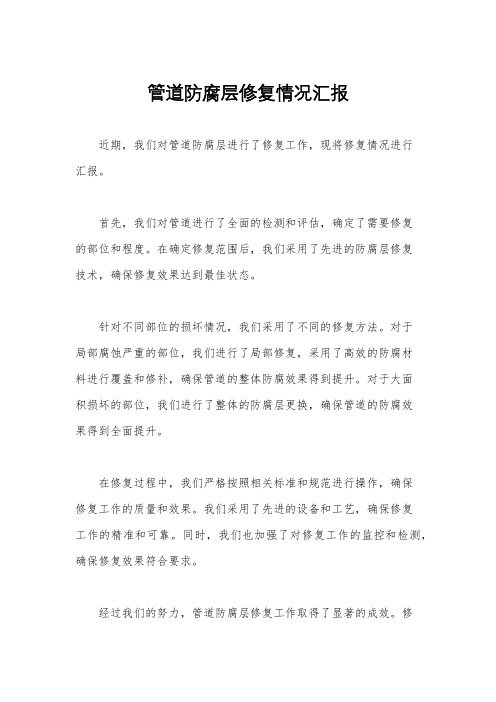
管道防腐层修复情况汇报
近期,我们对管道防腐层进行了修复工作,现将修复情况进行
汇报。
首先,我们对管道进行了全面的检测和评估,确定了需要修复
的部位和程度。
在确定修复范围后,我们采用了先进的防腐层修复
技术,确保修复效果达到最佳状态。
针对不同部位的损坏情况,我们采用了不同的修复方法。
对于
局部腐蚀严重的部位,我们进行了局部修复,采用了高效的防腐材
料进行覆盖和修补,确保管道的整体防腐效果得到提升。
对于大面
积损坏的部位,我们进行了整体的防腐层更换,确保管道的防腐效
果得到全面提升。
在修复过程中,我们严格按照相关标准和规范进行操作,确保
修复工作的质量和效果。
我们采用了先进的设备和工艺,确保修复
工作的精准和可靠。
同时,我们也加强了对修复工作的监控和检测,确保修复效果符合要求。
经过我们的努力,管道防腐层修复工作取得了显著的成效。
修
复后的管道防腐效果得到了明显提升,管道的使用寿命得到了有效延长,安全性和可靠性得到了进一步保障。
在未来的工作中,我们将继续加强对管道防腐层的监测和维护工作,确保管道的防腐效果始终保持在最佳状态。
同时,我们也将不断探索和引进更先进的防腐技术和工艺,为管道的安全运行提供更加可靠的保障。
总的来说,本次管道防腐层修复工作取得了显著成效,为管道的安全运行和可靠性提供了有力保障。
我们将继续努力,为管道的安全运行和稳定生产贡献力量。
管线外防腐层破损原因及修复技术
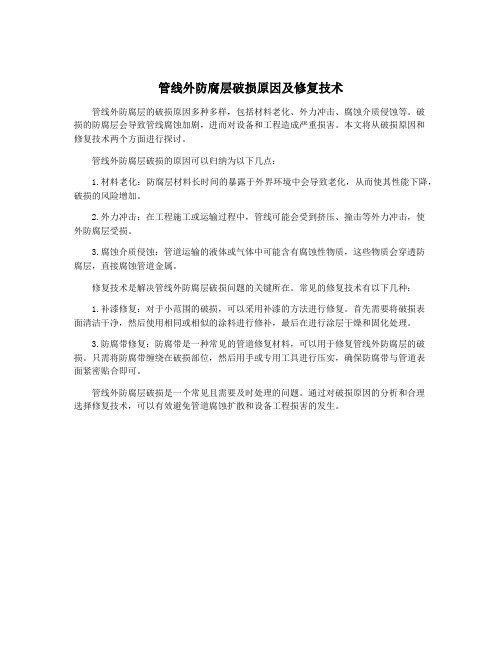
管线外防腐层破损原因及修复技术
管线外防腐层的破损原因多种多样,包括材料老化、外力冲击、腐蚀介质侵蚀等。
破
损的防腐层会导致管线腐蚀加剧,进而对设备和工程造成严重损害。
本文将从破损原因和
修复技术两个方面进行探讨。
管线外防腐层破损的原因可以归纳为以下几点:
1.材料老化:防腐层材料长时间的暴露于外界环境中会导致老化,从而使其性能下降,破损的风险增加。
2.外力冲击:在工程施工或运输过程中,管线可能会受到挤压、撞击等外力冲击,使
外防腐层受损。
3.腐蚀介质侵蚀:管道运输的液体或气体中可能含有腐蚀性物质,这些物质会穿透防
腐层,直接腐蚀管道金属。
修复技术是解决管线外防腐层破损问题的关键所在。
常见的修复技术有以下几种:
1.补漆修复:对于小范围的破损,可以采用补漆的方法进行修复。
首先需要将破损表
面清洁干净,然后使用相同或相似的涂料进行修补,最后在进行涂层干燥和固化处理。
3.防腐带修复:防腐带是一种常见的管道修复材料,可以用于修复管线外防腐层的破损。
只需将防腐带缠绕在破损部位,然后用手或专用工具进行压实,确保防腐带与管道表
面紧密贴合即可。
管线外防腐层破损是一个常见且需要及时处理的问题。
通过对破损原因的分析和合理
选择修复技术,可以有效避免管道腐蚀扩散和设备工程损害的发生。
管道防腐修复补强施工方案
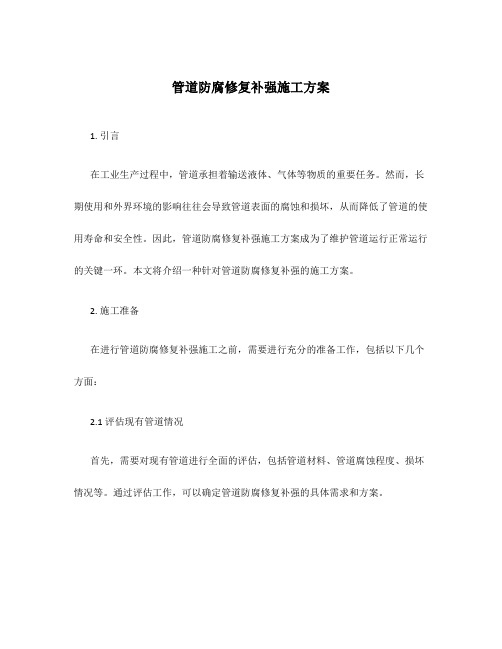
管道防腐修复补强施工方案1. 引言在工业生产过程中,管道承担着输送液体、气体等物质的重要任务。
然而,长期使用和外界环境的影响往往会导致管道表面的腐蚀和损坏,从而降低了管道的使用寿命和安全性。
因此,管道防腐修复补强施工方案成为了维护管道运行正常运行的关键一环。
本文将介绍一种针对管道防腐修复补强的施工方案。
2. 施工准备在进行管道防腐修复补强施工之前,需要进行充分的准备工作,包括以下几个方面:2.1 评估现有管道情况首先,需要对现有管道进行全面的评估,包括管道材料、管道腐蚀程度、损坏情况等。
通过评估工作,可以确定管道防腐修复补强的具体需求和方案。
2.2 选择合适的修复材料根据管道的材料和现有情况,选择合适的修复材料。
常见的修复材料包括环氧树脂、玻璃钢、不锈钢套管等。
2.3 准备施工设备和工具根据具体的施工方案,准备所需的施工设备和工具,包括各种刷子、刮刀、喷枪、滚筒等。
3. 施工步骤3.1 清洁管道表面首先,使用刮刀、刷子等工具清洁管道表面的杂质、尘土和锈迹。
确保管道表面干净,以便后续的修复施工。
3.2 修复管道腐蚀部位对于管道表面的腐蚀部位,可以使用环氧树脂等材料进行修复。
具体的修复方法包括:1.将环氧树脂涂料均匀涂刷在腐蚀部位上,形成一层保护膜。
2.使用刮刀等工具将环氧树脂涂料刮平,使其与管道表面平整结合。
3.等待环氧树脂涂料干燥固化,形成耐腐蚀的保护层。
3.3 加固管道结构对于管道的损坏部位,需要进行加固,以增强管道的结构强度。
常见的加固方法包括:1.使用不锈钢套管对管道进行包裹,以增加管道的强度。
2.玻璃钢加固是一种常见的方法,使用玻璃钢布和环氧树脂进行包裹,形成坚固的加固层。
3.4 防腐层施工在完成管道的修复和加固工作后,需要进行防腐层的施工,以保护管道不受腐蚀。
常见的防腐层材料包括环氧涂料、聚氨酯涂料等。
施工步骤如下:1.将防腐涂料涂刷在管道表面,形成一层防护膜。
2.使用刷子或滚筒等工具均匀涂刷防腐涂料,确保涂层厚度均匀一致。
管道防腐层修复施工流程

管道防腐层修复施工流程
朋友!今天跟您唠唠管道防腐层修复施工这档子事儿。
咱先说说为啥要搞这个修复啊,那是因为管道要是防腐层坏了,可不得了!就像人的皮肤破了容易生病一样,管道也容易出大问题。
要说这施工流程,第一步啊,得先把那坏的地方找出来。
这可不容易,有时候得一点点排查,我记得有一次,找了老半天,累得我哟!
找到坏的地方后,就得清理干净。
这清理工作可不能马虎,得把那些锈啊、脏东西啊都弄干净,不然新的防腐层可贴不牢。
然后呢,准备好修复的材料。
这材料可得选好,不然白费功夫。
我当初刚开始干这活的时候,就因为材料没选对,白忙活一场,唉!
接下来就是涂防腐材料啦。
这一步可得仔细,涂得均匀才行。
我跟您说,涂的时候那味道,可不好闻呐!
涂完还不算完,得检查检查有没有漏洞。
这要是没检查好,前面的功夫可就都白费啦!
嗯……我好像还有啥没说,哦对!在施工的时候,一定得注意安全,别磕着碰着了。
我这脑子,说不定还有些细节没讲到,您多担待。
要是您在实际操作中有啥问题,随时跟我交流。
对了,我跟您说个行业里的趣事儿。
有一次,有个新手把材料弄混了,结果那场面,简直不忍直视!哈哈!
反正啊,这管道防腐层修复施工,说简单也不简单,说难也不难,就得多练多琢磨。
希望您能顺顺利利地完成工作!。
- 1、下载文档前请自行甄别文档内容的完整性,平台不提供额外的编辑、内容补充、找答案等附加服务。
- 2、"仅部分预览"的文档,不可在线预览部分如存在完整性等问题,可反馈申请退款(可完整预览的文档不适用该条件!)。
- 3、如文档侵犯您的权益,请联系客服反馈,我们会尽快为您处理(人工客服工作时间:9:00-18:30)。
埋地管道外防腐层修复方案
一、修复规定
1、直径不大于30mm的损伤(包括针孔),采用热熔胶粘剂+聚乙烯补伤片。
2、直径大于30mm的损伤,采用粘弹体防腐胶带+ 环包双层聚丙烯增强纤维胶带。
二、表面处理
1、清除暴露管段上的泥土,使防腐层缺陷完全露出,测量并记录缺陷尺寸及位置,对缺陷处进行拍照。
2、对缺陷处的防腐层进行修整,将已剥离的防腐层除去(如发现3PE外防腐层大面积整体剥离则应立即报告业主,以便考虑适宜的处理实施),应使产生锈蚀的管体完全裸露;
3、对已裸露的管体表面进行处理,将腐蚀产物清理干净,等级应达到St2级;
4、将缺陷四周10mm范围及需要环包的防腐层表面的污物清理干净,缺陷防腐层边缘修成钝角坡口,防腐层缺陷处管体表面进行手工除锈,采用热熔胶填充,补伤片贴敷修复外防腐层缺陷时,应将聚乙烯表面打毛。
三、缺陷修复
1、直径不大于30mm损伤的修补
①对处理过的管体表面和周边防腐层进行预热,将熔融状的热熔胶涂敷在管体表面,填充至周边聚乙烯防腐层厚度为止,然后马上贴敷聚乙烯补伤片;
②聚乙烯补伤片的大小应保证其边缘距聚乙烯层涂层边缘不小于100mm,并将四角剪成圆角;
③贴补时,应先将补伤片的热熔胶烘烤至熔融,然后覆盖在已填充热熔胶的防腐层缺陷表面,边加热边用辊子辊压,排出空气,保证热熔胶充分熔融直至补伤片四周胶黏剂均匀溢出。
2、直径大于30mm损伤的修补
①粘弹体防腐胶带施工前,应保证补伤处干燥;
②将粘弹体防腐胶带依次贴敷,同时碾压排除空气;
③粘弹体防腐胶带搭接宽度不低于1cm,施工时可沿胶带内侧搭接线进行搭接;粘弹体防腐胶带与缺陷四周管体聚乙烯层涂层的搭接宽度至少为100mm,粘弹体防腐胶带始末端搭接长度不小于100mm;
④粘弹体防腐胶带施工完成后立即进行外观和漏点检测;
⑤粘弹体防腐胶带层合格后,采用聚丙烯增强纤维胶带(外带)环包缠绕在粘弹体防腐胶带外层。
聚丙烯增强纤维胶带具体施工方法是:从一端开始先原位缠绕一周,留出约3mm宽的粘弹体胶带不缠绕外带,然后进行螺旋缠绕,缠绕外带时应保持一定张力,胶带搭接宽度为50%~55%,直至另一端,在结束部位原位缠绕一周,留出3mm宽的粘弹体胶带不缠绕外带。
四、检查验收
1、补伤处外观应100%目测,表面平整、无皱折、无气泡及烧焦碳化现象,不合格应重新补伤;
2、补伤处应100%电火花检漏,检漏电压为15Kv,无漏点为合格。
五、修复报价
500元/处,报价中不包含开挖费用和管体补强费用。