10钢球抗冲击实验记录
冲击实验报告

冲击实验报告一.实验目的1.掌握常温下金属冲击试验方法;2.了解冲击试验机结构、工作原理及正确使用方法。
二.实验设备JBW-300冲击试验机及20#钢试样和40Cr试样。
三.实验原理:冲击试验是根据许多机器零件在工作时受到冲击载荷作用提出来的。
冲击载荷是动载荷,它在短时间内产生较大的力,在这种情况下往往对材料的组织缺陷反映更敏感。
在冲击试验中,我们认为材料存在截面突变、即缺口,冲击动能在零件内的分布是不均匀的,在缺口处单位体积内将吸取较多的能量,从而使该处的应力、应变值增大。
因此,Ak或ak 值都是代表材料缺口敏感度。
冲击载荷与静拉伸的主要区别在于加载速度不同。
拉伸速度一般在10-4~10-2mm/s,而冲击速度为102~104mm/s,静载荷作用于构件,一般不考虑惯性力的影响,而冲击载荷作用下惯性的作用不可忽视。
四﹑试样的制备若冲击试样的类型和尺寸不同,则得出的实验结果不能直接比较和换算。
本次试验采用U型缺口冲击试样。
其尺寸及偏差应根据GB/T229-1994规定,见图1-2。
加工缺口试样时,应严格控制其形状﹑尺寸精度以及表面粗糙度。
试样缺口底部应光滑﹑无与缺口轴线平行的明显划痕。
五﹑实验原理冲击试验利用的是能量守恒原理,即冲击试样消耗的能量是摆锤试验前后的势能差。
试验时,把试样放在图1-2的B处,将摆锤举至高度为H的A处自由落下,冲断试样即可。
摆锤在A处所具有的势能为:E=GH=GL(1-cosα) (1-1)冲断试样后,摆锤在C处所具有的势能为:E1=Gh=GL(1-cosβ)。
(1-2)势能之差E-E1,即为冲断试样所消耗的冲击功A K:A K=E-E1=GL(cosβ-cosα) (1-3)式中,G为摆锤重力(N);L为摆长(摆轴到摆锤重心的距离)(mm);α为冲断试样前摆锤扬起的最大角度;β为冲断试样后摆锤扬起的最大角度。
图1-3冲击试验原理图六﹑实验步骤1. 测量试样的几何尺寸及缺口处的横截面尺寸。
材料冲击实验报告

材料冲击实验报告1. 引言材料的抗冲击性能是评估其在受到外界冲击载荷时能否保持完整性和功能性的重要指标。
为了研究材料的冲击性能,本实验通过对不同材料的冲击实验,评估材料的抗冲击能力,并分析材料的破坏机制。
本实验选取了三种常见的材料进行了冲击测试,包括金属材料 (铝合金),塑料材料 (聚丙烯)和弹性材料 (聚氨酯)。
2. 实验目的•评估不同材料的抗冲击性能;•分析不同材料的破坏机制;•探讨材料冲击性能与材料特性的关系。
3. 实验装置和材料3.1 实验装置本实验使用的实验装置包括:•冲击试验机:用于提供冲击载荷;•冲击台:固定试样并接受冲击载荷;•冲击传感器:用于测量冲击过程中的载荷;•计算机数据采集系统:用于记录和分析实验数据。
3.2 实验材料本实验选取的材料包括:1.铝合金:作为典型的金属材料,具有很高的强度和硬度。
2.聚丙烯:作为典型的塑料材料,具有良好的韧性和耐冲击性。
3.聚氨酯:作为典型的弹性材料,具有很高的延展性和回弹性。
4. 实验方法4.1 样品制备首先,将铝合金、聚丙烯和聚氨酯分别加工为具有一定尺寸的试样,保证每个试样的尺寸和几何形状一致。
4.2 实验步骤1.将制备好的铝合金试样固定在冲击台上,调整冲击试验机的参数 (如冲击速度、冲击角度等)。
2.使用计算机数据采集系统连接冲击传感器,并调试传感器使其正常工作。
3.进行铝合金试样的冲击实验。
记录冲击过程中的载荷变化,并实时通过计算机数据采集系统保存数据。
4.重复上述步骤,分别对聚丙烯和聚氨酯试样进行冲击实验。
5.对实验得到的数据进行处理和分析,评估不同材料的抗冲击性能。
5. 实验结果和讨论经过冲击实验,得到了铝合金、聚丙烯和聚氨酯试样在不同冲击载荷下的载荷变化曲线。
根据实验数据,可以得到以下结论:1.铝合金在冲击载荷下承受能力较高,其载荷变化曲线较为平缓,说明其具有较好的抗冲击性能。
2.聚丙烯在冲击载荷下表现出较好的韧性,载荷变化曲线相对平缓,但其承受能力相对铝合金较低。
冲击试验和疲劳强度实验
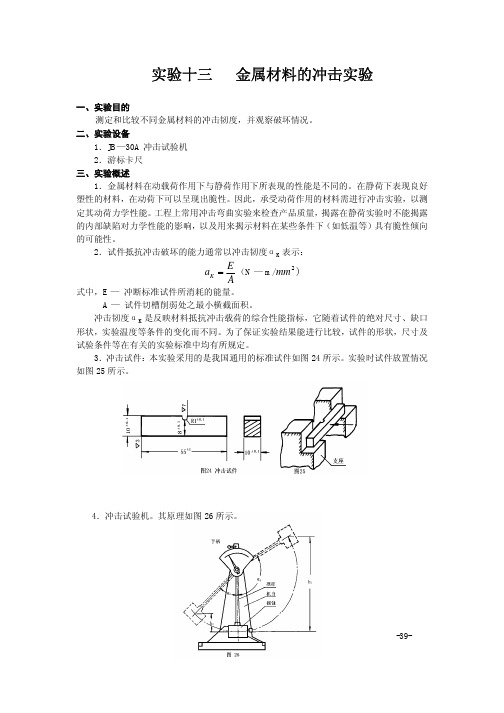
实验十三 金属材料的冲击实验一、实验目的测定和比较不同金属材料的冲击韧度,并观察破坏情况。
二、实验设备1.JB—30A 冲击试验机 2.游标卡尺 三、实验概述1.金属材料在动载荷作用下与静荷作用下所表现的性能是不同的。
在静荷下表现良好塑性的材料,在动荷下可以呈现出脆性。
因此,承受动荷作用的材料需进行冲击实验,以测定其动荷力学性能。
工程上常用冲击弯曲实验来检查产品质量,揭露在静荷实验时不能揭露的内部缺陷对力学性能的影响,以及用来揭示材料在某些条件下(如低温等)具有脆性倾向的可能性。
2.试件抵抗冲击破坏的能力通常以冲击韧度αK 表示:AE a K =(N — m/)2mm 式中,E — 冲断标准试件所消耗的能量。
A — 试件切槽削弱处之最小横截面积。
冲击韧度αK 是反映材料抵抗冲击载荷的综合性能指标,它随着试件的绝对尺寸、缺口形状,实验温度等条件的变化而不同。
为了保证实验结果能进行比较,试件的形状,尺寸及试验条件等在有关的实验标准中均有所规定。
3.冲击试件:本实验采用的是我国通用的标准试件如图24所示。
实验时试件放置情况如图25所示。
-39-4.冲击试验机。
其原理如图26所示。
绕水平轴转动的摆杆下部装有摆锤,摆锤中央凹口中装有冲击刀刃。
冲击前,装好试件,将摆锤按规定抬起一角度α1,当摆锤自由下落时,将试件冲断,由于冲断试件消耗了一部分能量,因此摆锤能继续向左运动摆起一个角度α2。
所以冲断试件的能量为)(21h h Q E −=)cos (cos 12a a Ql −=此能量E 可直接在机器的度盘上读出。
四.实验步骤1.记录室温。
2.测量试件尺寸。
3.检查机器,校正零点。
检查机器运动部分和钳口座等的固结情况。
校零点用空摆实验进行。
4.安装试件。
将摆锤拉起一角度,然后将试件放入钳口座,并用样板校正位置以对准刀刃。
5.将度盘上指示副针拨至度盘左端,准备实验。
6.冲击实验。
将电器控制盒拿在手中,操作者与观察者均远离试验机一米以上。
钢冲击实验报告
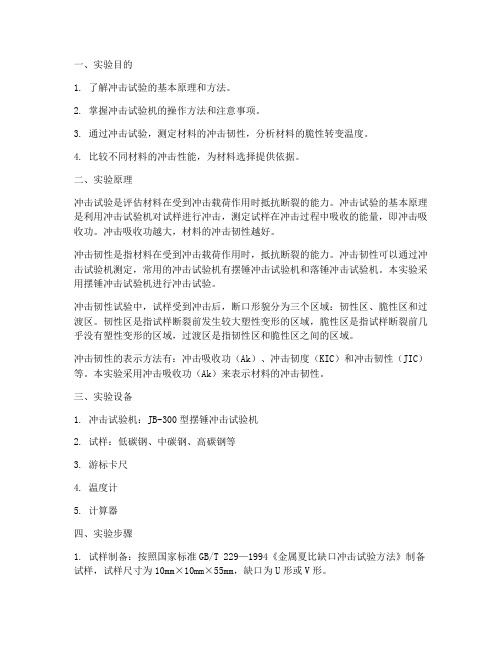
一、实验目的1. 了解冲击试验的基本原理和方法。
2. 掌握冲击试验机的操作方法和注意事项。
3. 通过冲击试验,测定材料的冲击韧性,分析材料的脆性转变温度。
4. 比较不同材料的冲击性能,为材料选择提供依据。
二、实验原理冲击试验是评估材料在受到冲击载荷作用时抵抗断裂的能力。
冲击试验的基本原理是利用冲击试验机对试样进行冲击,测定试样在冲击过程中吸收的能量,即冲击吸收功。
冲击吸收功越大,材料的冲击韧性越好。
冲击韧性是指材料在受到冲击载荷作用时,抵抗断裂的能力。
冲击韧性可以通过冲击试验机测定,常用的冲击试验机有摆锤冲击试验机和落锤冲击试验机。
本实验采用摆锤冲击试验机进行冲击试验。
冲击韧性试验中,试样受到冲击后,断口形貌分为三个区域:韧性区、脆性区和过渡区。
韧性区是指试样断裂前发生较大塑性变形的区域,脆性区是指试样断裂前几乎没有塑性变形的区域,过渡区是指韧性区和脆性区之间的区域。
冲击韧性的表示方法有:冲击吸收功(Ak)、冲击韧度(KIC)和冲击韧性(JIC)等。
本实验采用冲击吸收功(Ak)来表示材料的冲击韧性。
三、实验设备1. 冲击试验机:JB-300型摆锤冲击试验机2. 试样:低碳钢、中碳钢、高碳钢等3. 游标卡尺4. 温度计5. 计算器四、实验步骤1. 试样制备:按照国家标准GB/T 229—1994《金属夏比缺口冲击试验方法》制备试样,试样尺寸为10mm×10mm×55mm,缺口为U形或V形。
2. 试样测量:使用游标卡尺测量试样尺寸,精确到0.01mm。
3. 冲击试验:将试样放入冲击试验机的试样夹具中,调整试样位置,使缺口位于冲击方向。
4. 冲击试验机操作:打开冲击试验机电源,调整摆锤高度,使摆锤与试样距离为一定的距离。
按动冲击试验机按钮,使摆锤自由落下冲击试样。
5. 数据记录:记录冲击试验过程中冲击吸收功(Ak)、冲击韧度(KIC)等数据。
6. 冲击试验重复:对同一试样进行多次冲击试验,取平均值作为最终结果。
突起路标抗冲击性能、抗压荷载检测记录表

抗压最大力值
校核:计算:检验:
试样编号:
一、整体抗冲击性能:
要求:经质量1040g±10g的实心钢球,在突起路标上方1m的高度自由落下,突起路标上表面的中心处直径12mm的区域外不应有任何形式的破损。
试样编号
受冲击后破损情况
二、抗压荷载:
要求:以2.5mm/min的速率对突起路标进行加载,直到样品破坏或样品产生明显变形(大于3.3mm)为止,A1、A2类突起路标的最大力值应不小于160KN,A3类突起路标应不小于245KN。
试-X-XXX
XXX工程检测有限公司
突起路标抗冲击性能、抗压荷载检测记录表
记录编号:第页,共页
委托单编号:
检评规程:
委托方名称:
检测环境:温度:℃湿度: %
委托方地址:
检测日期:年日
工程名称:
检测仪器:突起路标耐冲击测定装置、0.5级电子万能材料试验机
工程部位:
仪器编号:
试样型号:
抽样人:
试样产地:
冲击实验报告总结

冲击实验报告总结
本次实验是一次关于冲击力的实验,旨在探究物体在受到不同冲击力作用下的反应。
在实验中,我们通过使用冲击力计对不同重量的物体进行了多次冲击实验,记录下了每次实验中物体受到的冲击力和位移等数据,并对数据进行了统计和分析。
通过实验,我们得出了以下几个结论:
1.物体在受到较大的冲击力作用下,会产生较大的位移。
2.不同重量的物体在受到相同的冲击力作用下,产生的位移和反应有所不同。
3.在实验中,使用冲击力计可以较为准确地记录下物体受到的冲击力和位移等数据。
通过本次实验,我们对物体在受到不同冲击力作用下的反应有了更深入的了解,并且掌握了一定的实验操作技能。
同时,我们也发现,在实验过程中需要注意安全,避免产生意外情况。
在今后的学习和科研中,我们将继续深入探究物体受力的规律和反应,为实际生产和应用提供更多的科学依据和技术支持。
- 1 -。
小球冲击测试数据收集
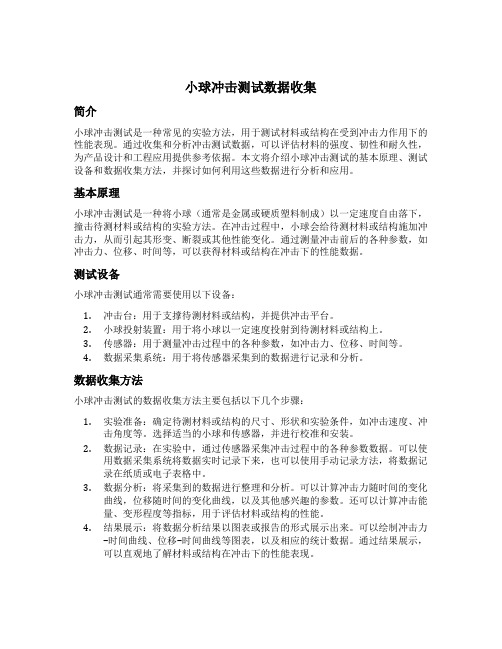
小球冲击测试数据收集简介小球冲击测试是一种常见的实验方法,用于测试材料或结构在受到冲击力作用下的性能表现。
通过收集和分析冲击测试数据,可以评估材料的强度、韧性和耐久性,为产品设计和工程应用提供参考依据。
本文将介绍小球冲击测试的基本原理、测试设备和数据收集方法,并探讨如何利用这些数据进行分析和应用。
基本原理小球冲击测试是一种将小球(通常是金属或硬质塑料制成)以一定速度自由落下,撞击待测材料或结构的实验方法。
在冲击过程中,小球会给待测材料或结构施加冲击力,从而引起其形变、断裂或其他性能变化。
通过测量冲击前后的各种参数,如冲击力、位移、时间等,可以获得材料或结构在冲击下的性能数据。
测试设备小球冲击测试通常需要使用以下设备:1.冲击台:用于支撑待测材料或结构,并提供冲击平台。
2.小球投射装置:用于将小球以一定速度投射到待测材料或结构上。
3.传感器:用于测量冲击过程中的各种参数,如冲击力、位移、时间等。
4.数据采集系统:用于将传感器采集到的数据进行记录和分析。
数据收集方法小球冲击测试的数据收集方法主要包括以下几个步骤:1.实验准备:确定待测材料或结构的尺寸、形状和实验条件,如冲击速度、冲击角度等。
选择适当的小球和传感器,并进行校准和安装。
2.数据记录:在实验中,通过传感器采集冲击过程中的各种参数数据。
可以使用数据采集系统将数据实时记录下来,也可以使用手动记录方法,将数据记录在纸质或电子表格中。
3.数据分析:将采集到的数据进行整理和分析。
可以计算冲击力随时间的变化曲线,位移随时间的变化曲线,以及其他感兴趣的参数。
还可以计算冲击能量、变形程度等指标,用于评估材料或结构的性能。
4.结果展示:将数据分析结果以图表或报告的形式展示出来。
可以绘制冲击力-时间曲线、位移-时间曲线等图表,以及相应的统计数据。
通过结果展示,可以直观地了解材料或结构在冲击下的性能表现。
数据分析与应用收集到的小球冲击测试数据可以用于以下方面的分析和应用:1.材料评估:通过分析冲击测试数据,可以评估材料的强度、韧性和耐久性。
冲击试验实验报告
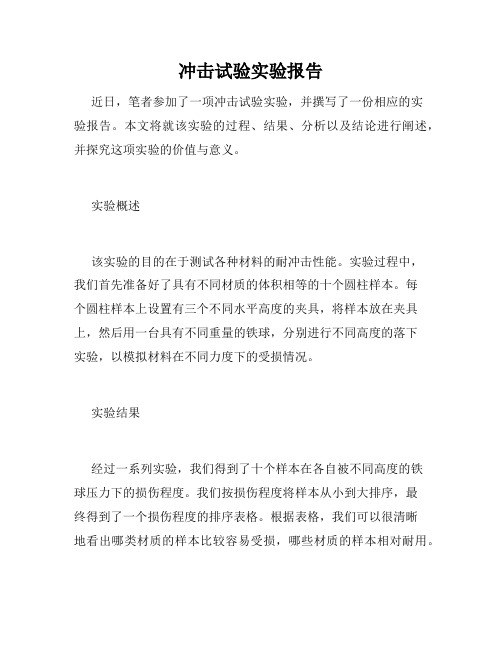
冲击试验实验报告近日,笔者参加了一项冲击试验实验,并撰写了一份相应的实验报告。
本文将就该实验的过程、结果、分析以及结论进行阐述,并探究这项实验的价值与意义。
实验概述该实验的目的在于测试各种材料的耐冲击性能。
实验过程中,我们首先准备好了具有不同材质的体积相等的十个圆柱样本。
每个圆柱样本上设置有三个不同水平高度的夹具,将样本放在夹具上,然后用一台具有不同重量的铁球,分别进行不同高度的落下实验,以模拟材料在不同力度下的受损情况。
实验结果经过一系列实验,我们得到了十个样本在各自被不同高度的铁球压力下的损伤程度。
我们按损伤程度将样本从小到大排序,最终得到了一个损伤程度的排序表格。
根据表格,我们可以很清晰地看出哪类材质的样本比较容易受损,哪些材质的样本相对耐用。
分析与讨论针对每个样本,我们还进行了详细的分析。
我们发现,当铁球以较小的高度(例如20厘米)落下时,多数样本没有显示出任何损伤,这是因为材质强度并不足以导致塑性变形。
但随着铁球落下高度的增加,样本之间的差异逐渐明显。
比如说,当铁球以60厘米的高度落下时,由铝制成的样本出现了明显的划伤和凹陷,而由碳纤维制成的样本却几乎没有受损。
这意味着在某些领域里,碳纤维可能比铝更适合用于制造耐久性产品。
结论本实验显示出了各种材料在不同力度下的耐冲击性能。
它提供了有关材料的重要信息,以指导工程师优化设计,改进材料选择和加强产品质量。
此外,该实验还提供了学生进行材料失效和破坏分析的机会,进而提升教学效果。
然而,本实验存在一定的局限性,例如未考虑材料与温度和湿度的相互作用等因素,仍需基于实际应用情景进一步研究。
因此,未来的探索和研究仍需要人们对实验方法和结果的不断探索和验证。
总之,本实验为我们展示了材料的耐久性和性能,并为工程师和研究人员提供了重要的信息,有助于设计更加优越的与产品。
同时,该实验还带来了许多教育上的益处,使我们更好地了解材料的特性和机制。
材料冲击演示实验
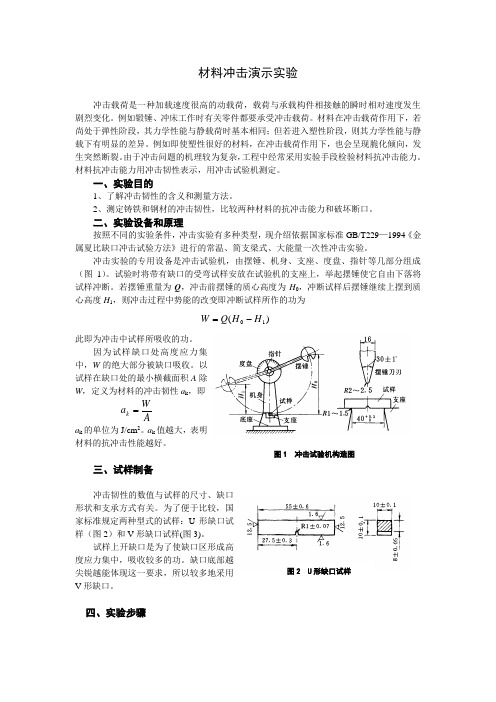
材料冲击演示实验冲击载荷是一种加载速度很高的动载荷,载荷与承载构件相接触的瞬时相对速度发生剧烈变化。
例如锻锤、冲床工作时有关零件都要承受冲击载荷。
材料在冲击载荷作用下,若尚处于弹性阶段,其力学性能与静载荷时基本相同;但若进入塑性阶段,则其力学性能与静载下有明显的差异。
例如即使塑性很好的材料,在冲击载荷作用下,也会呈现脆化倾向,发生突然断裂。
由于冲击问题的机理较为复杂,工程中经常采用实验手段检验材料抗冲击能力。
材料抗冲击能力用冲击韧性表示,用冲击试验机测定。
一、实验目的1、了解冲击韧性的含义和测量方法。
2、测定铸铁和钢材的冲击韧性,比较两种材料的抗冲击能力和破坏断口。
二、实验设备和原理按照不同的实验条件,冲击实验有多种类型,现介绍依据国家标准GB/T229—1994《金属夏比缺口冲击试验方法》进行的常温、简支梁式、大能量一次性冲击实验。
冲击实验的专用设备是冲击试验机,由摆锤、机身、支座、度盘、指针等几部分组成(图1)。
试验时将带有缺口的受弯试样安放在试验机的支座上,举起摆锤使它自由下落将试样冲断。
若摆锤重量为Q ,冲击前摆锤的质心高度为H 0,冲断试样后摆锤继续上摆到质心高度H 1,则冲击过程中势能的改变即冲断试样所作的功为)(10H H Q W -=此即为冲击中试样所吸收的功。
因为试样缺口处高度应力集中,W 的绝大部分被缺口吸收。
以试样在缺口处的最小横截面积A 除W ,定义为材料的冲击韧性a k ,即AW a k = a k 的单位为J/cm 2。
a k 值越大,表明材料的抗冲击性能越好。
三、试样制备冲击韧性的数值与试样的尺寸、缺口形状和支承方式有关。
为了便于比较,国家标准规定两种型式的试样:U 形缺口试样(图2)和V 形缺口试样(图3)。
试样上开缺口是为了使缺口区形成高度应力集中,吸收较多的功。
缺口底部越尖锐越能体现这一要求,所以较多地采用V 形缺口。
四、实验步骤1、 测量试样缺口处最小横截面积,选择试验机摆锤和刻度盘。
敲击测试的实验报告(3篇)

第1篇一、实验目的1. 了解敲击测试的基本原理和方法。
2. 通过敲击测试,评估材料的抗冲击性能。
3. 分析不同材料的敲击测试结果,找出其优缺点。
二、实验原理敲击测试是一种评估材料抗冲击性能的实验方法。
实验过程中,通过在材料表面施加一定的冲击力,观察材料在冲击作用下的破坏情况,从而判断其抗冲击性能。
实验原理如下:1. 根据冲击能量与材料破坏情况的关系,评估材料的抗冲击性能。
2. 通过对比不同材料的敲击测试结果,找出其优缺点。
三、实验材料与设备1. 实验材料:钢、铝、塑料、木材等。
2. 实验设备:冲击试验机、冲击试验样品、砝码、测量工具等。
四、实验步骤1. 准备实验材料,将材料切割成规定尺寸的样品。
2. 将样品放置在冲击试验机的试验台上。
3. 设置冲击试验机的冲击速度,确保实验过程中冲击力满足要求。
4. 在样品上施加一定的冲击力,记录冲击次数。
5. 观察样品在冲击作用下的破坏情况,记录破坏形态。
6. 重复实验,分析不同材料的敲击测试结果。
五、实验结果与分析1. 钢材样品:在冲击试验过程中,钢材样品在冲击次数达到50次后出现明显变形,但在100次冲击后仍保持完整。
这说明钢材具有良好的抗冲击性能。
2. 铝材样品:在冲击试验过程中,铝材样品在冲击次数达到20次后出现明显变形,但在50次冲击后出现断裂。
这说明铝材的抗冲击性能较钢材差。
3. 塑料样品:在冲击试验过程中,塑料样品在冲击次数达到5次后出现明显变形,但在10次冲击后出现断裂。
这说明塑料的抗冲击性能最差。
4. 木材样品:在冲击试验过程中,木材样品在冲击次数达到10次后出现明显变形,但在20次冲击后出现断裂。
这说明木材的抗冲击性能较铝材差。
六、结论1. 通过敲击测试,可以评估材料的抗冲击性能。
2. 钢材具有良好的抗冲击性能,其次是铝材和木材,塑料的抗冲击性能最差。
3. 在实际应用中,应根据材料的抗冲击性能选择合适的材料。
七、实验注意事项1. 实验过程中,确保实验设备运行正常,避免因设备故障导致实验结果不准确。
实验六 冲击实验
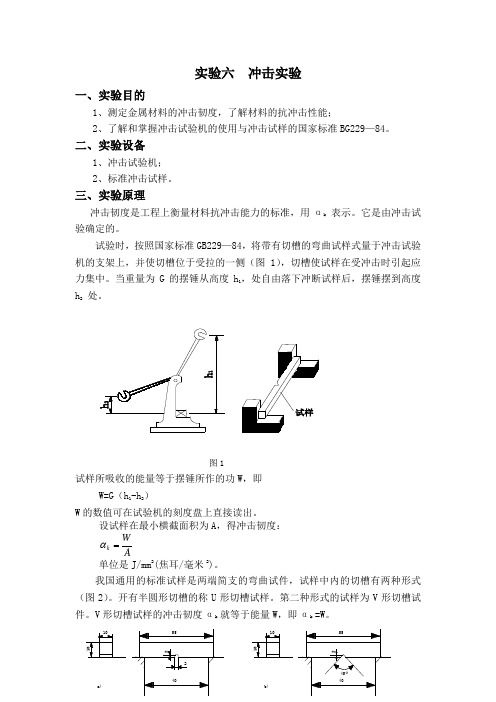
实验六 冲击实验一、实验目的1、测定金属材料的冲击韧度,了解材料的抗冲击性能;2、了解和掌握冲击试验机的使用与冲击试样的国家标准BG229—84。
二、实验设备1、冲击试验机;2、标准冲击试样。
三、实验原理冲击韧度是工程上衡量材料抗冲击能力的标准,用αk 表示。
它是由冲击试验确定的。
试验时,按照国家标准GB229—84,将带有切槽的弯曲试样式量于冲击试验机的支架上,并使切槽位于受拉的一侧(图1),切槽使试样在受冲击时引起应力集中。
当重量为G 的摆锤从高度h 1,处自由落下冲断试样后,摆锤摆到高度h 2 处。
图1试样所吸收的能量等于摆锤所作的功W ,即W=G (h 1-h 2)W 的数值可在试验机的刻度盘上直接读出。
设试样在最小横截面积为A ,得冲击韧度:AW k =α单位是J/mm 2(焦耳/毫米2)。
我国通用的标准试样是两端简支的弯曲试件,试样中内的切槽有两种形式(图2)。
开有半圆形切槽的称U 形切槽试样。
第二种形式的试样为V 形切槽试件。
V 形切槽试样的冲击韧度αk 就等于能量W ,即αk =W 。
试样a)b)图2四、实验步骤1、了解冲击试验机的操作方法和使用注意事项。
2、测量试样尺寸(如果用V形切槽试样,不作测量)。
3、不装试样,升起重摆空打一次,检验试验机读数刻度盘的零点。
如有初读数,应作记录。
4、试样靠紧支座放置好。
5、升起重摆,按下“冲击”钮,重摆下落冲击试样。
6、制动重摆,待重摆停稳后读取数据,观察试样断口形貌。
7、试验时每组试样不少于四根,以减小其所测结果的误差。
五、注意事项1、放置试样时,重摆应处于自然下垂位置。
2、重摆升起后,在重摆摆动范围内不得有人和障碍物。
3、特别注意人身安全。
六、思考题(一)低碳钢和铸铁试样受冲击破坏后的断口形貌有什么不同?有什么工程实际意义?(二)测量冲击韧击韧度αk附录五:冲击试验数据记录试样类型:。
冲击实验实验报告
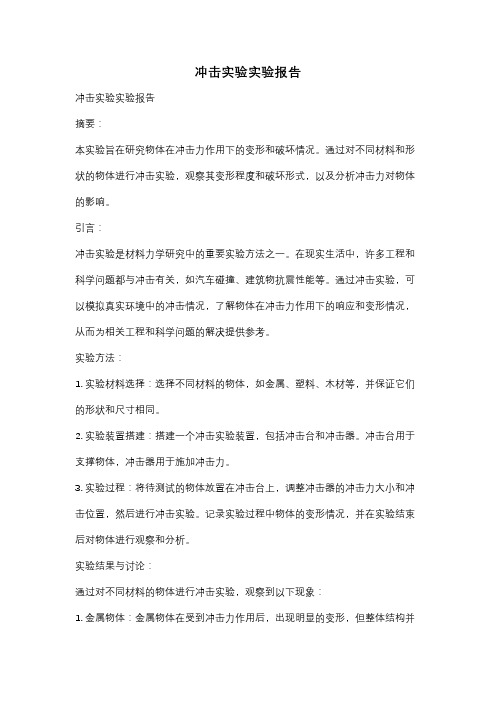
冲击实验实验报告冲击实验实验报告摘要:本实验旨在研究物体在冲击力作用下的变形和破坏情况。
通过对不同材料和形状的物体进行冲击实验,观察其变形程度和破坏形式,以及分析冲击力对物体的影响。
引言:冲击实验是材料力学研究中的重要实验方法之一。
在现实生活中,许多工程和科学问题都与冲击有关,如汽车碰撞、建筑物抗震性能等。
通过冲击实验,可以模拟真实环境中的冲击情况,了解物体在冲击力作用下的响应和变形情况,从而为相关工程和科学问题的解决提供参考。
实验方法:1. 实验材料选择:选择不同材料的物体,如金属、塑料、木材等,并保证它们的形状和尺寸相同。
2. 实验装置搭建:搭建一个冲击实验装置,包括冲击台和冲击器。
冲击台用于支撑物体,冲击器用于施加冲击力。
3. 实验过程:将待测试的物体放置在冲击台上,调整冲击器的冲击力大小和冲击位置,然后进行冲击实验。
记录实验过程中物体的变形情况,并在实验结束后对物体进行观察和分析。
实验结果与讨论:通过对不同材料的物体进行冲击实验,观察到以下现象:1. 金属物体:金属物体在受到冲击力作用后,出现明显的变形,但整体结构并未破坏。
这是因为金属具有较高的强度和韧性,能够承受较大的冲击力。
2. 塑料物体:塑料物体在受到冲击力作用后,变形程度较大,甚至出现破裂。
这是因为塑料的强度和韧性相对较低,不能很好地抵抗冲击力。
3. 木材物体:木材物体在受到冲击力作用后,出现较小的变形,但整体结构并未破坏。
这是因为木材具有一定的韧性,能够在一定程度上吸收冲击力。
通过对实验结果的分析,可以得出以下结论:1. 冲击力对物体的变形和破坏有重要影响。
冲击力越大,物体的变形程度和破坏形式越严重。
2. 材料的性质对物体的冲击响应有重要影响。
不同材料具有不同的强度和韧性,因此在受到冲击力作用时表现出不同的变形和破坏形式。
3. 物体的形状和尺寸对其冲击响应也有一定影响。
形状复杂、尺寸较大的物体在受到冲击力作用时可能更容易发生破坏。
抗冲击试验实验报告(3篇)
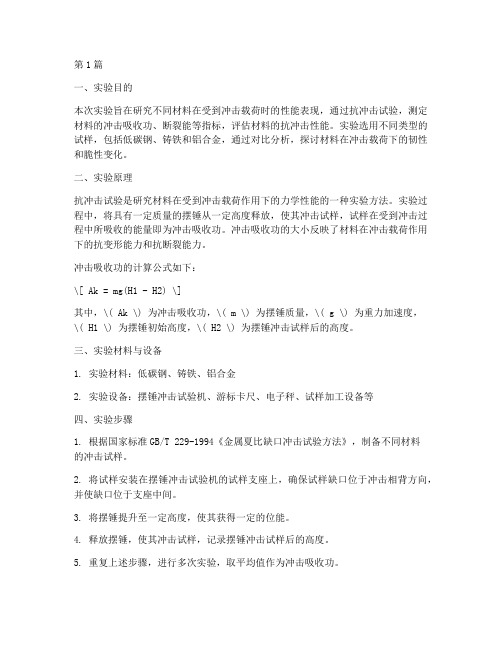
第1篇一、实验目的本次实验旨在研究不同材料在受到冲击载荷时的性能表现,通过抗冲击试验,测定材料的冲击吸收功、断裂能等指标,评估材料的抗冲击性能。
实验选用不同类型的试样,包括低碳钢、铸铁和铝合金,通过对比分析,探讨材料在冲击载荷下的韧性和脆性变化。
二、实验原理抗冲击试验是研究材料在受到冲击载荷作用下的力学性能的一种实验方法。
实验过程中,将具有一定质量的摆锤从一定高度释放,使其冲击试样,试样在受到冲击过程中所吸收的能量即为冲击吸收功。
冲击吸收功的大小反映了材料在冲击载荷作用下的抗变形能力和抗断裂能力。
冲击吸收功的计算公式如下:\[ Ak = mg(H1 - H2) \]其中,\( Ak \) 为冲击吸收功,\( m \) 为摆锤质量,\( g \) 为重力加速度,\( H1 \) 为摆锤初始高度,\( H2 \) 为摆锤冲击试样后的高度。
三、实验材料与设备1. 实验材料:低碳钢、铸铁、铝合金2. 实验设备:摆锤冲击试验机、游标卡尺、电子秤、试样加工设备等四、实验步骤1. 根据国家标准GB/T 229-1994《金属夏比缺口冲击试验方法》,制备不同材料的冲击试样。
2. 将试样安装在摆锤冲击试验机的试样支座上,确保试样缺口位于冲击相背方向,并使缺口位于支座中间。
3. 将摆锤提升至一定高度,使其获得一定的位能。
4. 释放摆锤,使其冲击试样,记录摆锤冲击试样后的高度。
5. 重复上述步骤,进行多次实验,取平均值作为冲击吸收功。
五、实验结果与分析1. 低碳钢试样:在冲击载荷作用下,低碳钢试样表现出较好的韧性,冲击吸收功较高,断裂能较大。
2. 铸铁试样:铸铁试样在冲击载荷作用下,表现出脆性断裂特征,冲击吸收功较低,断裂能较小。
3. 铝合金试样:铝合金试样在冲击载荷作用下,表现出较好的韧性和塑性,冲击吸收功较高,断裂能较大。
六、结论1. 低碳钢和铝合金在冲击载荷作用下,具有良好的抗冲击性能,适合用于承受较大冲击载荷的场合。
钢化玻璃落球冲击试验标准国标

钢化玻璃落球冲击试验标准国标
钢化玻璃是一种广泛应用于建筑、汽车及家居领域的新型材料,它具有高强度、高透光性和防爆性能等优点。
然而,在使用过程中,钢化玻璃可能会受到冲击力的影响,因此钢化玻璃的落球冲击试验标准国家标准就应运而生。
国家标准GB/T 9963-1998《建筑玻璃落球冲击试验方法》规定了钢化玻璃落球冲击试验的标准。
该标准分为两种试验方法:球直径为
45mm及球直径为50mm。
下面将对两种试验方法进行具体介绍。
第一种试验方法:球直径为45mm
试验流程:在平面钢化玻璃的中心位置,从高度为1.5m处落下一直径为45mm、质量为0.226kg的钢球,观察钢化玻璃是否破裂或出现明显的裂痕。
试验结果:若钢化玻璃未出现破裂或明显的裂痕,则试验合格;若钢化玻璃出现破裂或明显的裂痕,则试验不合格。
第二种试验方法:球直径为50mm
试验流程:在平面钢化玻璃的中心位置,从高度为2.0m处落下一直径为50mm、质量为0.24kg的钢球,观察钢化玻璃是否破裂或出现明显的裂痕。
试验结果:若钢化玻璃未出现破裂或明显的裂痕,则试验合格;若钢化玻璃出现破裂或明显的裂痕,则试验不合格。
在进行实验之前,需要对试验设备进行检查和校正,以确保实验结果的准确性和可靠性。
同时,在进行试验时,还需要注意现场安全,采取适当的措施确保人员和设备的安全。
总之,通过进行钢化玻璃落球冲击试验,可以检测钢化玻璃的耐冲击性能,确保其在使用过程中可以承受一定的冲击力而不破裂或出现明显的裂痕。
在实际生产和使用中,企业和个人均应遵守国家标准,对钢化玻璃进行严格的质量检验,以确保其质量合格、安全可靠。
冲击常数测定实验报告

冲击常数测定实验报告1. 引言冲击常数是一个用来描述物质的抗冲击性能的物理常数。
通过测定物质在受到外力冲击时的变形程度和残余变形程度,可以间接测定物质的冲击常数。
本实验旨在通过测定金属材料的冲击试验,以获得该材料的冲击常数,并进一步了解材料的抗冲击性能。
2. 实验方法2.1 实验器材和试样本实验所用的冲击试验机为Model XYZ,试样为直径30mm、高度60mm的金属柱。
2.2 实验步骤1. 准备实验器材,并将试样固定在冲击试验机上。
2. 设置冲击试验机的参数,如冲击力、冲击时间等。
3. 进行冲击试验,记录下冲击力施加后试样的变形程度。
4. 根据试样的变形程度,计算出试样的冲击常数。
2.3 数据处理根据实验结果,采用以下公式计算冲击常数:冲击常数= 施加的冲击力/ 试样的变形程度3. 实验结果经过多次实验,得到以下结果:实验次数冲击力(N)变形程度(mm)-1 100 5.22 120 6.33 110 5.8根据上表数据,我们可以得到:冲击常数= (100 + 120 + 110) / (5.2 + 6.3 + 5.8) ≈9.49 N/mm4. 结果分析通过上述实验结果,我们可以得到金属材料的冲击常数为9.49 N/mm。
这意味着施加1N的冲击力时,试样的变形程度为0.1059mm。
冲击常数是描述材料抗冲击性能的重要指标之一。
该指标越小,表示材料越抗冲击。
在实际应用中,我们可以根据不同的需求选择不同冲击常数的材料,以保证设备和结构在受到外力冲击时的安全性。
5. 结论本实验通过冲击试验测定了金属材料的冲击常数为9.49 N/mm。
根据该结果,我们可以评估该材料的抗冲击性能,并加以应用。
通过对冲击常数的测定,我们可以更好地了解和评估材料的抗冲击性能,并在工程设计和材料选择时进行合理的判断和决策。
落球冲击试验标准

落球冲击试验标准落球冲击试验是一种常用的材料力学性能测试方法,通常用于评估材料的抗冲击性能。
该试验通过让一个标准化的钢球自特定高度自由落下,以一定速度撞击被测试材料,从而评估材料的抗冲击能力。
落球冲击试验标准的制定对于确保产品质量、保障消费者安全具有重要意义。
首先,落球冲击试验标准的制定需要考虑到被测试材料的特性以及实际使用环境。
不同材料在不同环境下的抗冲击性能会有所差异,因此制定落球冲击试验标准需要考虑到这些因素。
标准化的测试方法能够确保测试结果的可比性和准确性,从而为产品设计和生产提供参考依据。
其次,落球冲击试验标准应当明确测试过程中的各项参数和要求。
包括落球的直径、重量、下落高度、撞击速度等参数都需要在标准中予以规定,以确保测试的一致性和可重复性。
此外,还需要规定测试样品的准备方法、测试设备的要求以及数据记录和分析的标准流程,以确保测试的科学性和规范性。
另外,落球冲击试验标准还需要考虑到不同行业和产品的特殊要求。
不同行业对于材料的抗冲击性能有着不同的要求,因此落球冲击试验标准需要根据具体的行业特点进行细化和完善。
例如,建筑材料、汽车零部件、电子产品等不同行业的产品对于抗冲击性能的要求各不相同,因此需要有针对性地制定相应的标准。
最后,落球冲击试验标准的制定需要考虑到国际化和标准化的趋势。
随着全球化的发展,越来越多的产品和材料在国际市场上流通和应用,因此落球冲击试验标准需要与国际接轨,以满足国际贸易和合作的需要。
同时,标准化的制定也有利于促进行业的技术进步和产品质量的提升。
总之,落球冲击试验标准的制定对于推动材料科学与工程技术的发展,促进产品质量和安全,具有重要的意义。
制定落球冲击试验标准需要考虑到材料特性、实际需求、行业要求以及国际标准化的趋势,以确保测试的科学性、规范性和可比性。
只有制定了科学合理的标准,才能够更好地保障产品质量和消费者的安全。
材料冲击实验报告
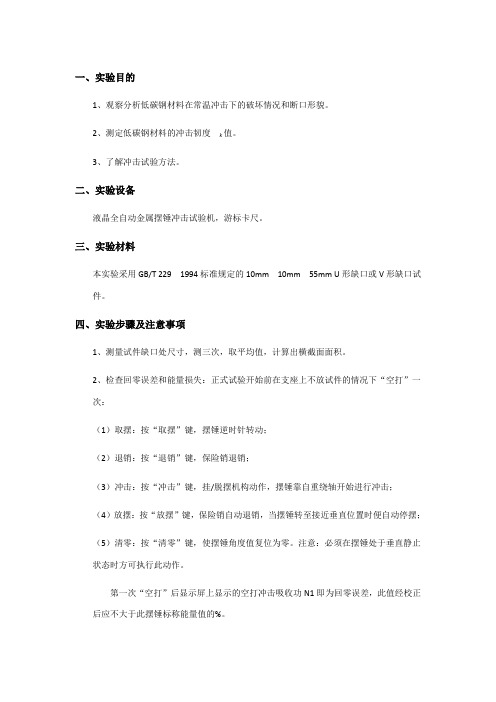
一、实验目的1、观察分析低碳钢材料在常温冲击下的破坏情况和断口形貌。
2、测定低碳钢材料的冲击韧度k值。
3、了解冲击试验方法。
二、实验设备液晶全自动金属摆锤冲击试验机,游标卡尺。
三、实验材料本实验采用GB/T 2291994标准规定的10mm10mm55mm U形缺口或V形缺口试件。
四、实验步骤及注意事项1、测量试件缺口处尺寸,测三次,取平均值,计算出横截面面积。
2、检查回零误差和能量损失:正式试验开始前在支座上不放试件的情况下“空打”一次:(1)取摆:按“取摆”键,摆锤逆时针转动;(2)退销:按“退销”键,保险销退销;(3)冲击:按“冲击”键,挂/脱摆机构动作,摆锤靠自重绕轴开始进行冲击;(4)放摆:按“放摆”键,保险销自动退销,当摆锤转至接近垂直位置时便自动停摆;(5)清零:按“清零”键,使摆锤角度值复位为零。
注意:必须在摆锤处于垂直静止状态时方可执行此动作。
第一次“空打”后显示屏上显示的空打冲击吸收功N1即为回零误差,此值经校正后应不大于此摆锤标称能量值的%。
继续“空打”五次,记下第六次空打冲击吸收功N6,则摆锤在摆动中由于空气和摩擦阻力造成的能量损失为:()16101N N e -=,此值应不大于此摆锤标称能量值的%。
3、正式试验:按“取摆”键,摆锤逆时针转动上扬,触动限位开关后由挂摆机构挂住,保险销弹出,此时可在支座上放置试件(注意试件缺口对中并位于受拉边)。
然后顺序执行以上 “取摆”、“退销”、“冲击”、“放摆”动作。
显示屏上将显示该试件的冲击吸收功和相应的冲击韧度。
4、摆锤抬起后,严禁在摆锤摆动范围内站立、行走和放置障碍物。
五、实验数据记录及结果处理冲击功W (Nm)冲击韧度AWk =α (Nm/cm 2)。
玻璃对比实验报告
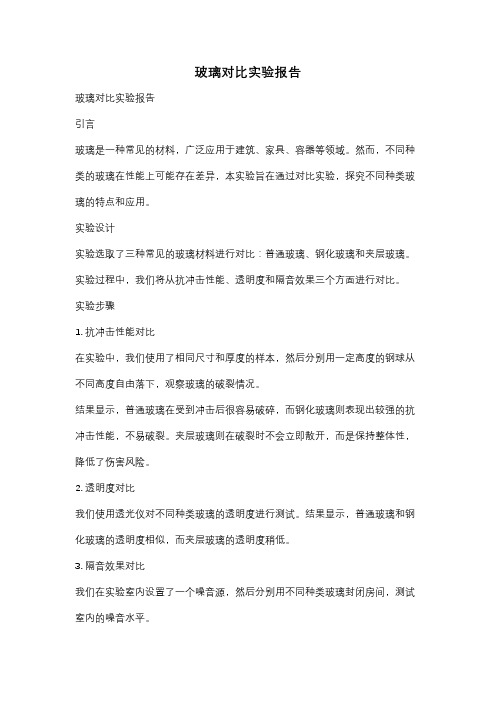
玻璃对比实验报告玻璃对比实验报告引言玻璃是一种常见的材料,广泛应用于建筑、家具、容器等领域。
然而,不同种类的玻璃在性能上可能存在差异,本实验旨在通过对比实验,探究不同种类玻璃的特点和应用。
实验设计实验选取了三种常见的玻璃材料进行对比:普通玻璃、钢化玻璃和夹层玻璃。
实验过程中,我们将从抗冲击性能、透明度和隔音效果三个方面进行对比。
实验步骤1. 抗冲击性能对比在实验中,我们使用了相同尺寸和厚度的样本,然后分别用一定高度的钢球从不同高度自由落下,观察玻璃的破裂情况。
结果显示,普通玻璃在受到冲击后很容易破碎,而钢化玻璃则表现出较强的抗冲击性能,不易破裂。
夹层玻璃则在破裂时不会立即散开,而是保持整体性,降低了伤害风险。
2. 透明度对比我们使用透光仪对不同种类玻璃的透明度进行测试。
结果显示,普通玻璃和钢化玻璃的透明度相似,而夹层玻璃的透明度稍低。
3. 隔音效果对比我们在实验室内设置了一个噪音源,然后分别用不同种类玻璃封闭房间,测试室内的噪音水平。
结果显示,普通玻璃对噪音的隔音效果较差,而钢化玻璃和夹层玻璃在隔音方面表现出较好的效果。
特别是夹层玻璃,其夹层中的隔音膜能有效吸收噪音,降低外界噪音对室内的干扰。
讨论通过对比实验,我们可以得出以下结论:1. 钢化玻璃在抗冲击性能方面表现出较好的特点,适合用于需要较高安全性的场所,如高层建筑、汽车等。
2. 夹层玻璃在抗冲击性能、隔音效果方面均表现出优异的特点,适合用于需要综合性能的场所,如住宅、商业建筑等。
3. 普通玻璃在透明度方面与其他两种玻璃相似,但在抗冲击性能和隔音效果方面相对较差。
结论通过本次实验,我们对比了普通玻璃、钢化玻璃和夹层玻璃在抗冲击性能、透明度和隔音效果方面的差异。
实验结果表明,不同种类的玻璃在性能上存在显著差异,应根据具体需求选择适合的玻璃材料。
这对于建筑设计和家具选择等领域具有重要意义,可以提供科学依据和参考。
未来的研究可以进一步探究不同种类玻璃的热传导性能、耐候性等方面的差异,以及如何通过技术手段改进玻璃的性能。