黑点杂质改善
白色或透明胶件黑点问题的控制措施
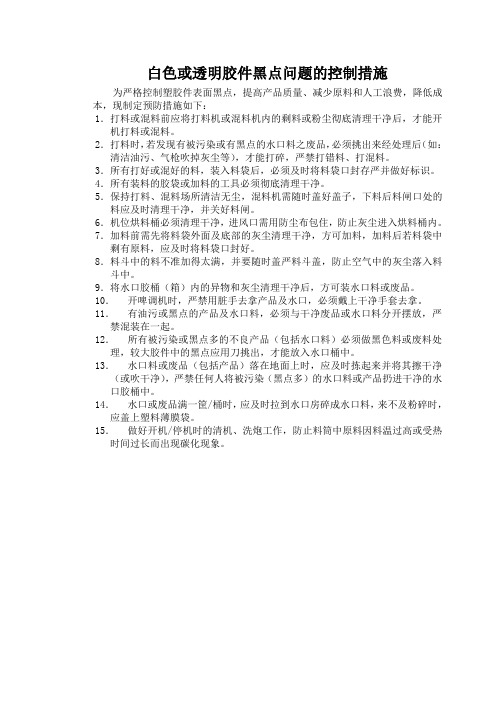
白色或透明胶件黑点问题的控制措施为严格控制塑胶件表面黑点,提高产品质量、减少原料和人工浪费,降低成本,现制定预防措施如下:1.打料或混料前应将打料机或混料机内的剩料或粉尘彻底清理干净后,才能开机打料或混料。
2.打料时,若发现有被污染或有黑点的水口料之废品,必须挑出来经处理后(如:清洁油污、气枪吹掉灰尘等),才能打碎,严禁打错料、打混料。
3.所有打好或混好的料,装入料袋后,必须及时将料袋口封存严并做好标识。
4.所有装料的胶袋或加料的工具必须彻底清理干净。
5.保持打料、混料场所清洁无尘,混料机需随时盖好盖子,下料后料闸口处的料应及时清理干净,并关好料闸。
6.机位烘料桶必须清理干净,进风口需用防尘布包住,防止灰尘进入烘料桶内。
7.加料前需先将料袋外面及底部的灰尘清理干净,方可加料,加料后若料袋中剩有原料,应及时将料袋口封好。
8.料斗中的料不准加得太满,并要随时盖严料斗盖,防止空气中的灰尘落入料斗中。
9.将水口胶桶(箱)内的异物和灰尘清理干净后,方可装水口料或废品。
10.开啤调机时,严禁用脏手去拿产品及水口,必须戴上干净手套去拿。
11.有油污或黑点的产品及水口料,必须与干净废品或水口料分开摆放,严禁混装在一起。
12.所有被污染或黑点多的不良产品(包括水口料)必须做黑色料或废料处理,较大胶件中的黑点应用刀挑出,才能放入水口桶中。
13.水口料或废品(包括产品)落在地面上时,应及时拣起来并将其擦干净(或吹干净),严禁任何人将被污染(黑点多)的水口料或产品扔进干净的水口胶桶中。
14.水口或废品满一筐/桶时,应及时拉到水口房碎成水口料,来不及粉碎时,应盖上塑料薄膜袋。
15.做好开机/停机时的清机、洗炮工作,防止料筒中原料因料温过高或受热时间过长而出现碳化现象。
黑点、杂质形成原因及改善对策

黑点、杂质形成原因分析及对策黑点、杂质的缺陷是在正常生产过程中产生废品率的最重要因素。
它主要是影响制品外观从而导致报废。
杂质和绝大多数黑点都是外来物质,和原料本身无关,而少部分黑点、杂质是由原料本身造成。
黑点、杂质特征是颗粒较小、呈黑褐色,一般不反光,颗粒大时杂质呈层状、脆、易碎、破碎后多孔,其分布有两大特性:1、有的整体性无规则零散分布,有的是局部无规则零散分布,有时则仅偶尔出现在某一局部区域;2、这类黑点、杂质有时仅出现在制品表层,有时则不论表里深浅都有,不过距表层较近的内部黑点比表层黑点来颜色要浅,更深层的黑点则根本看不到。
有意思的是将这两点联系起来会发现,仅出现在某局部区域的杂质必然是表层的黑点,而黑点分布不论表里深浅的必然是整体性无规则零散分布。
这是由于内部存在的杂质必然是成型前就存在的,而仅成型时才出现的杂质必然只分布在表面。
这样,杂质就分为成型前和成型时形成两大类:一、成型前黑点、杂质成因:1 原料加工时,由于种种原因,异物不干净而使原料出现黑点;2 造粒不纯造成黑点;3 原料混入色母或带斑点的粉碎料块、料屑;4 料不纯,低熔点料中混入了高熔点料粒;5 包装、运输、贮藏过程中可能出现杂质混入,它明显特征是原料开包后,仔细观察,可以看到在料颗粒表面有异物、杂质;6 加料过程中的杂质、异物如下图为吸引或上料器及料斗的简图;除了5、11不会直接对料斗料造成污染,其他部分均可能在上料过程式中污染原料,造成制品黑点、杂质。
污染源包括:空气中的灰尘、料状悬浮物、异料料屑、异料料粒、粉状色母、染色剂等。
为杜绝异物杂质造成黑点,必须加强管理,控制从原料进厂至加料各环节(包括回用过程)。
换料时,必须仔细清理可能原先料或屑滞留的部位,特别备料箱、料斗、漏斗、下摆夹扣紧处等。
正常生产时,要特别注意加料源——备料箱的清洁。
停止生产后,应将加料系统对外界环境暴露处——上料管的上料端口密封,以防污染,做到环环相扣,封闭管理。
生产中常见的问题和解决方法
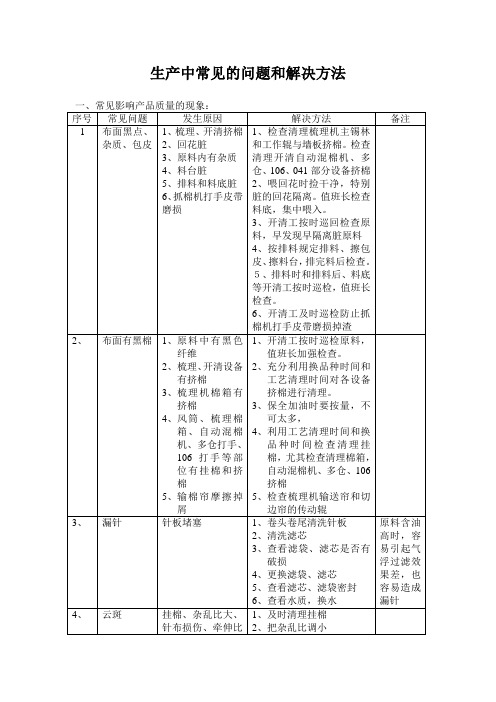
生产中常见的问题和解决方法
二、常见生产中影响生产的现象:
三、各工序操作时要遵循的原则
1、设备清理:先上后下,先里后外。
2、开清和梳理棉箱启动、停车原则:先开风机后开打手,先开打手后开给棉;先停给棉后停打手,先停打手后停风机。
3、水刺启动停止顺序:先开传动后开抽吸,先开抽吸后开供水;先停供水后停
风机,先停风机后停传动。
4、烘燥开停顺序:先开传动后开风机,先停风机后停传动。
烘燥内部温度低于50度后方可停传动。
四、影响原料消耗的原因:
1、开清落地棉多,开清设备漏棉多,要尽可能减少落地棉,挑拣喂入。
2、分切切边大,分切切边不大于5CM,在保证不薄边的情况下尽量减小切边。
3、开停车、分切换卷引头布太长,应尽量减少,不超过3米。
4、更换品种次数多,要根据订单情况尽量安排统一品种统一克重一起生产。
5、回潮低,根据检测情况,尽量降低烘燥温度和风机速度。
6、切边过小,利用水刺、烘燥、卷绕牵伸强拉,致使下卷时幅宽过大造成浪费
7、操作清理跟不上,梳理缠棉、停车次数多,废布多。
8、、布面脏,分切时引废布多。
各种不良硅片的表现形式及改善方法
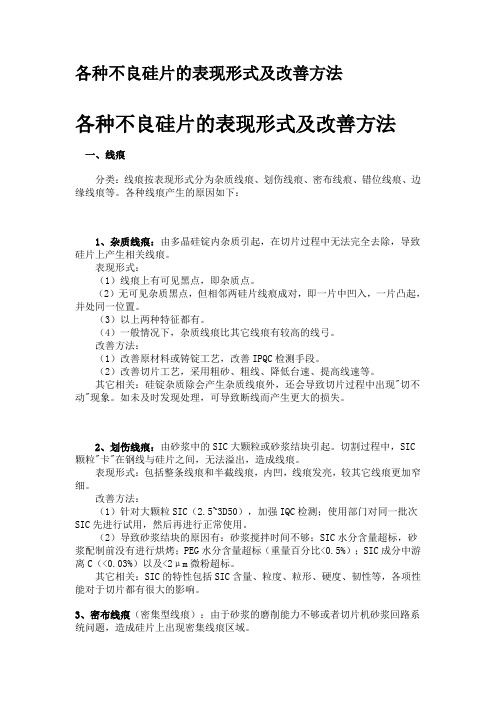
各种不良硅片的表现形式及改善方法各种不良硅片的表现形式及改善方法一、线痕分类:线痕按表现形式分为杂质线痕、划伤线痕、密布线痕、错位线痕、边缘线痕等。
各种线痕产生的原因如下:1、杂质线痕:由多晶硅锭内杂质引起,在切片过程中无法完全去除,导致硅片上产生相关线痕。
表现形式:(1)线痕上有可见黑点,即杂质点。
(2)无可见杂质黑点,但相邻两硅片线痕成对,即一片中凹入,一片凸起,并处同一位置。
(3)以上两种特征都有。
(4)一般情况下,杂质线痕比其它线痕有较高的线弓。
改善方法:(1)改善原材料或铸锭工艺,改善IPQC检测手段。
(2)改善切片工艺,采用粗砂、粗线、降低台速、提高线速等。
其它相关:硅锭杂质除会产生杂质线痕外,还会导致切片过程中出现"切不动"现象。
如未及时发现处理,可导致断线而产生更大的损失。
2、划伤线痕:由砂浆中的SIC大颗粒或砂浆结块引起。
切割过程中,SIC 颗粒"卡"在钢线与硅片之间,无法溢出,造成线痕。
表现形式:包括整条线痕和半截线痕,内凹,线痕发亮,较其它线痕更加窄细。
改善方法:(1)针对大颗粒SIC(2.5~3D50),加强IQC检测;使用部门对同一批次SIC先进行试用,然后再进行正常使用。
(2)导致砂浆结块的原因有:砂浆搅拌时间不够;SIC水分含量超标,砂浆配制前没有进行烘烤;PEG水分含量超标(重量百分比<0.5%);SIC成分中游离C(<0.03%)以及<2μm微粉超标。
其它相关:SIC的特性包括SIC含量、粒度、粒形、硬度、韧性等,各项性能对于切片都有很大的影响。
3、密布线痕(密集型线痕):由于砂浆的磨削能力不够或者切片机砂浆回路系统问题,造成硅片上出现密集线痕区域。
表现形式:(1)硅片整面密集线痕。
(2)硅片出线口端半片面积密集线痕。
(3)硅片部分区域贯穿硅片密集线痕。
(4)部分不规则区域密集线痕。
(5)硅块头部区域密布线痕。
喷涂涂料表面浮黑色小油点的解决方法

组分不同,在涂膜干燥过程中产生应力,导致在黑
色小油点四周的涂膜带有短小裂缝。
解决办法: 1)对于对于漂浮黑色小油点的成品喷涂涂料,
可以适当添加基材润湿剂和适量的乳化剂,使不槽
容的黑色小油点像颜料颗粒一样,吸附润湿剂后进
入喷涂涂料体系,不再影响喷涂涂料和涂膜外观。 2)加强对原材料的质量控制。
3)在喷涂涂料配方中,尽量引进疏水的分散
剂,可以预防此问题的发生。
Hale Waihona Puke 点。在 20 倍放大镜下,可见油点中心有白色细小
粉末物质。
分析:黑色小油点通常是由填充料带进来的油
污,更换一批原料,黑色小油点问题就消失了。漂
浮黑色小油点的成品喷涂涂料应用效果不好,由于
黑色小油点与喷涂涂料体系不相容,成膜后油点镶
嵌在涂膜中成为疵病。由于黑色小油点为油、粉混
合物,参与喷涂涂料成膜,其成分与喷涂涂料其他
喷涂涂料表面浮黑色小油点的解决方 法
f8e1k 吸音喷涂 无机纤维喷涂 保温喷涂
生产出的成品喷涂涂料在表面有漂浮黑点或
杂质。很多喷涂涂料生产技术人员遇到过类似的问
题,喷涂涂料生产过程中有“小气泡”或小黑点无
法消除。仔细检测这些“小气泡”其实是黑色小油
手机屏幕黑点消除方法
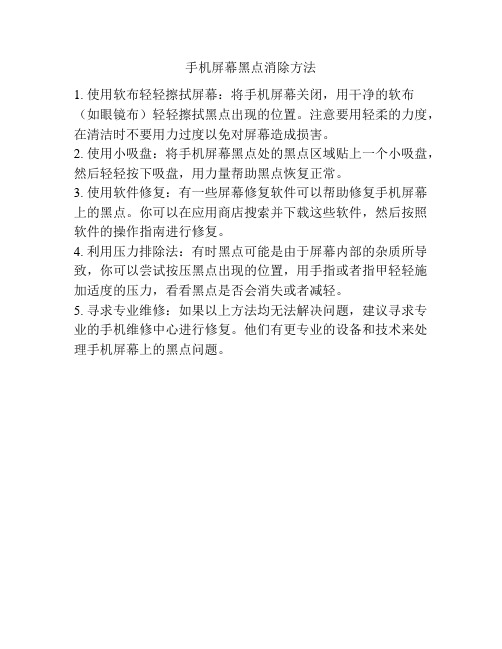
手机屏幕黑点消除方法
1. 使用软布轻轻擦拭屏幕:将手机屏幕关闭,用干净的软布(如眼镜布)轻轻擦拭黑点出现的位置。
注意要用轻柔的力度,在清洁时不要用力过度以免对屏幕造成损害。
2. 使用小吸盘:将手机屏幕黑点处的黑点区域贴上一个小吸盘,然后轻轻按下吸盘,用力量帮助黑点恢复正常。
3. 使用软件修复:有一些屏幕修复软件可以帮助修复手机屏幕上的黑点。
你可以在应用商店搜索并下载这些软件,然后按照软件的操作指南进行修复。
4. 利用压力排除法:有时黑点可能是由于屏幕内部的杂质所导致,你可以尝试按压黑点出现的位置,用手指或者指甲轻轻施加适度的压力,看看黑点是否会消失或者减轻。
5. 寻求专业维修:如果以上方法均无法解决问题,建议寻求专业的手机维修中心进行修复。
他们有更专业的设备和技术来处理手机屏幕上的黑点问题。
改变皮肤杂质的几种方法

改变皮肤杂质的几种方法去脸部角质在脸上撒少许白砂糖,然后用半个柠檬轻轻摩擦皮肤,可以去死皮和减轻阳光灼晒斑痕。
神奇指数:★★☆有效指数:★★★☆增长睫毛将喝剩的茶水晾凉,在睡前或隔天清晨,利用棉花棒沾湿眼睫毛,可达到增长睫毛的功效。
赶快试试吧,保证是最廉价又经济的睫毛增长液!神奇指数:★★★★有效指数:★★★★☆去身体角质手肘、膝盖、后脚跟部分用滑石轻轻磨去变老变黑的角质,严重时可涂上凡士林,用绷带覆盖一晚上。
神奇指数:★★有效指数:★★★☆去黑鼻头把生鸡蛋靠近蛋皮的那层薄膜整张撕下来,贴在鼻头上。
等干透之后揭下来,你会发现“草莓”上的小黑点全都不见了!神奇指数:★★★★☆有效指数:★★★★☆6个治疗雀斑的小偏方1、将鲜胡萝卜辟碎挤汁,取10-30毫升,每日早晚洗完脸后涂抹,待干后,洗净。
此外,每日喝一杯胡萝卜汁,可美白肌肤。
2、将柠檬汁搅汁,加糖水适量饮用。
柠檬中含有大量维生素C、钙、磷、铁等。
常饮柠檬汁不仅可美白肌肤,还能使黑色素沉淀,达到祛斑的作用。
3、每天喝一杯西红柿汁或常吃西红柿,对防止祛斑有较好的作用。
因为西红柿中含有丰富的谷胱甘肽,谷胱甘肽可抑制黑色素,从而使沉着的色素减退或消失。
4、洗脸时,在水中加1-2汤匙的食醋,有减轻色素沉着的作用。
6、用干净的茄子皮敷脸,一段时间后,小斑点就不那么明显了。
轻松拥有白皙皮肤9诀窍1、如果不是一定要外出,避免在早上10点至下午2点出去,因为此时阳光中的紫外线最强,对肌肤的伤害也最厉害。
2、每次曝晒于阳光下,应及时使用防晒产品,而且每隔2—3小时再擦一次。
此外,即使在水中一样会晒伤,所以喜欢戏水或潜水者,需使用防晒系数高且具防水效果的防晒品。
3、只要从事过户外活动,无论日晒的程度如何,回家后应先将全身冲洗干净。
以轻松的动作擦拭身体之后,以温水将泡沫冲洗干净,再以冷水冲淋,并可抹些身体的护肤品。
或用毛巾包裹冰块,冰镇在发热的肌肤上,减缓燥热不舒服的感觉。
pvc成型中黑点解决方法
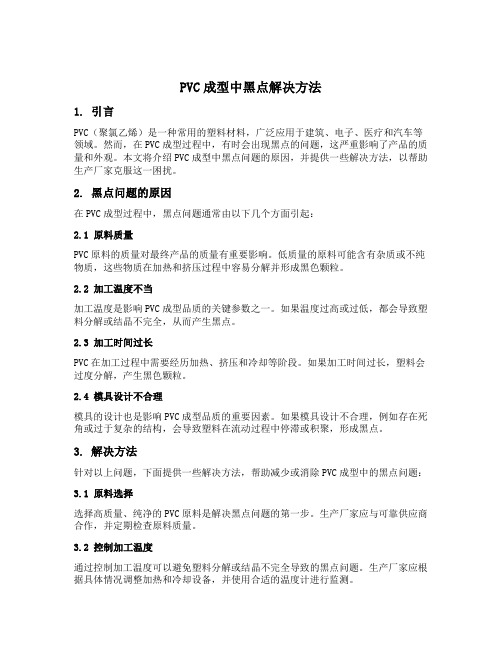
PVC成型中黑点解决方法1. 引言PVC(聚氯乙烯)是一种常用的塑料材料,广泛应用于建筑、电子、医疗和汽车等领域。
然而,在PVC成型过程中,有时会出现黑点的问题,这严重影响了产品的质量和外观。
本文将介绍PVC成型中黑点问题的原因,并提供一些解决方法,以帮助生产厂家克服这一困扰。
2. 黑点问题的原因在PVC成型过程中,黑点问题通常由以下几个方面引起:2.1 原料质量PVC原料的质量对最终产品的质量有重要影响。
低质量的原料可能含有杂质或不纯物质,这些物质在加热和挤压过程中容易分解并形成黑色颗粒。
2.2 加工温度不当加工温度是影响PVC成型品质的关键参数之一。
如果温度过高或过低,都会导致塑料分解或结晶不完全,从而产生黑点。
2.3 加工时间过长PVC在加工过程中需要经历加热、挤压和冷却等阶段。
如果加工时间过长,塑料会过度分解,产生黑色颗粒。
2.4 模具设计不合理模具的设计也是影响PVC成型品质的重要因素。
如果模具设计不合理,例如存在死角或过于复杂的结构,会导致塑料在流动过程中停滞或积聚,形成黑点。
3. 解决方法针对以上问题,下面提供一些解决方法,帮助减少或消除PVC成型中的黑点问题:3.1 原料选择选择高质量、纯净的PVC原料是解决黑点问题的第一步。
生产厂家应与可靠供应商合作,并定期检查原料质量。
3.2 控制加工温度通过控制加工温度可以避免塑料分解或结晶不完全导致的黑点问题。
生产厂家应根据具体情况调整加热和冷却设备,并使用合适的温度计进行监测。
3.3 控制加工时间严格控制加工时间可以防止PVC过度分解。
生产厂家应根据实际情况设置合理的加工时间,并定期检查设备运行情况,避免过长的加工时间。
3.4 合理设计模具合理设计模具可以减少塑料在流动过程中的停滞和积聚。
生产厂家应根据产品要求和工艺特点,选择合适的模具材料、结构和尺寸,并定期进行维护和清洁。
3.5 清洁设备和环境定期清洁加工设备和生产环境可以减少杂质对成型品质量的影响。
固体片剂“黑点”产生的原因分析及预防措施

固体片剂“黑点”产生的原因分析及预防措施固体片剂在生产过程中出现“黑点”是一个常见的问题,可能会影响产品质量和市场形象。
因此,对于这个问题的分析和预防措施是非常重要的。
首先,我们来分析“黑点”产生的原因。
主要原因如下:1.原材料问题:固体片剂生产过程中使用的原材料可能会受到污染或质量问题,例如颗粒物、杂质或化学物质。
这些污染物或质量问题可能会导致“黑点”的产生。
2.混合不均匀:固体片剂的生产过程中需要将各种原材料混合均匀。
如果混合过程不够均匀或时间不足,可能会导致部分原材料没有完全溶解或分散,形成“黑点”。
3.热处理问题:在片剂生产的过程中,热处理是一个必要的步骤。
如果温度不适宜或时间不足,可能会导致一些成分或原材料氧化或分解,产生“黑点”。
4.机械设备问题:生产过程中使用的设备,例如混合机、造粒机、压片机等,如果设备本身存在问题,例如表面腐蚀、粉尘积聚等,可能会导致“黑点”的产生。
针对这些原因,我们可以采取以下预防措施:1.优化原材料质量:严格控制原材料的采购渠道和质量标准,确保原材料没有污染和质量问题。
2.加强质量控制:建立严格的质量控制标准和流程,例如进行原材料的质量检验、加强混合过程的监控和调整等。
3.优化热处理条件:通过实验和工艺优化,确定最佳的热处理温度和时间,避免原材料的氧化和分解。
4.定期维护和检修设备:确保设备表面没有腐蚀和粉尘积聚,减少机械设备对产品质量的影响。
5.完善清洁制度:加强生产场所的清洁工作,减少杂质和颗粒物的污染。
另外,对于已经出现“黑点”的固体片剂,可以采取以下处理方法:1.分析原因:通过化学分析和检测,确定“黑点”产生的具体原因,找出问题所在。
2.改善工艺:根据问题的原因进行工艺调整和优化,避免类似问题再次发生。
3.控制质量:加强对“黑点”产品的质量控制,剔除不合格产品,确保优质产品出厂。
总之,固体片剂“黑点”的产生是一个影响产品质量和市场形象的重要问题。
通过分析产生原因并采取预防措施,可以减少“黑点”的发生,同时对已经出现的问题进行分析和处理,以提高产品质量和企业形象。
pvc成型中黑点解决方法
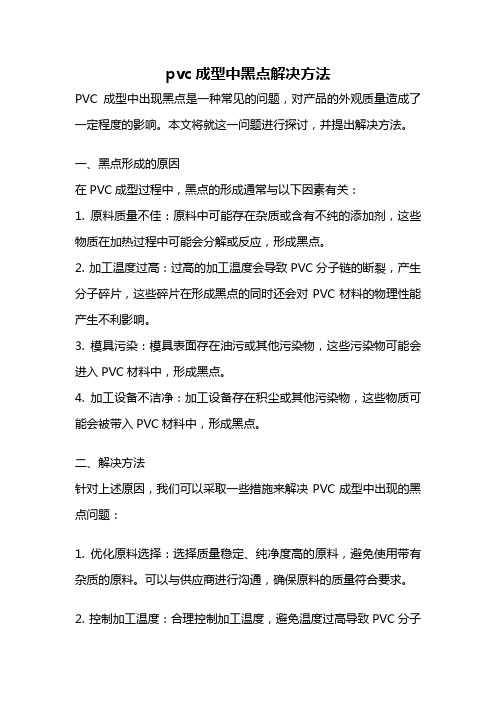
pvc成型中黑点解决方法PVC成型中出现黑点是一种常见的问题,对产品的外观质量造成了一定程度的影响。
本文将就这一问题进行探讨,并提出解决方法。
一、黑点形成的原因在PVC成型过程中,黑点的形成通常与以下因素有关:1. 原料质量不佳:原料中可能存在杂质或含有不纯的添加剂,这些物质在加热过程中可能会分解或反应,形成黑点。
2. 加工温度过高:过高的加工温度会导致PVC分子链的断裂,产生分子碎片,这些碎片在形成黑点的同时还会对PVC材料的物理性能产生不利影响。
3. 模具污染:模具表面存在油污或其他污染物,这些污染物可能会进入PVC材料中,形成黑点。
4. 加工设备不洁净:加工设备存在积尘或其他污染物,这些物质可能会被带入PVC材料中,形成黑点。
二、解决方法针对上述原因,我们可以采取一些措施来解决PVC成型中出现的黑点问题:1. 优化原料选择:选择质量稳定、纯净度高的原料,避免使用带有杂质的原料。
可以与供应商进行沟通,确保原料的质量符合要求。
2. 控制加工温度:合理控制加工温度,避免温度过高导致PVC分子链的断裂。
可以通过调整加工设备的温度控制系统来实现温度的控制。
3. 清洁模具表面:定期对模具进行清洁,防止油污或其他污染物进入PVC材料中。
可以使用专门的模具清洁剂进行清洁。
4. 维护加工设备:定期对加工设备进行清洁和维护,确保设备表面没有积尘或其他污染物。
可以制定设备维护计划,定期进行设备的检查和维护工作。
5. 加强质量控制:建立严格的质量控制体系,对原料、加工过程和成品进行全面监控。
可以采取抽样检验、检测仪器等手段,及时发现问题并进行处理。
6. 培训操作人员:加强对操作人员的培训,提高其对PVC成型工艺的理解和操作技能。
操作人员应具备良好的操作习惯,确保操作过程中的卫生和安全。
7. 定期检测:建立定期检测制度,对成品进行抽样检测,及时发现黑点等质量问题。
可以借助专业的检测机构进行检测,确保产品质量符合要求。
陶瓷密密麻麻的黑点的工艺
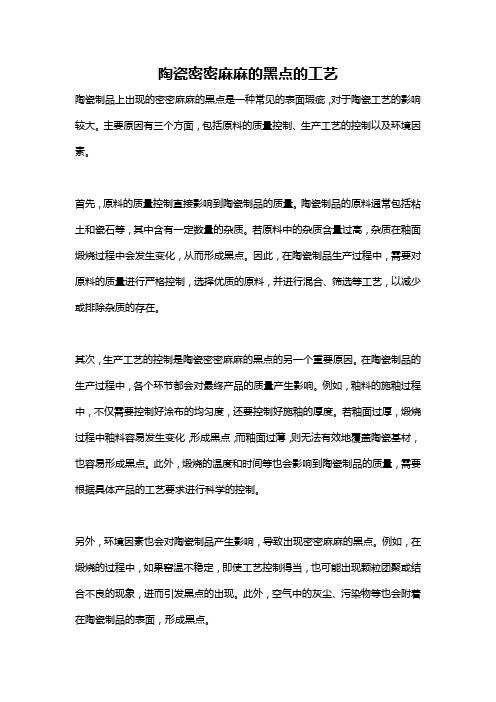
陶瓷密密麻麻的黑点的工艺陶瓷制品上出现的密密麻麻的黑点是一种常见的表面瑕疵,对于陶瓷工艺的影响较大。
主要原因有三个方面,包括原料的质量控制、生产工艺的控制以及环境因素。
首先,原料的质量控制直接影响到陶瓷制品的质量。
陶瓷制品的原料通常包括粘土和瓷石等,其中含有一定数量的杂质。
若原料中的杂质含量过高,杂质在釉面煅烧过程中会发生变化,从而形成黑点。
因此,在陶瓷制品生产过程中,需要对原料的质量进行严格控制,选择优质的原料,并进行混合、筛选等工艺,以减少或排除杂质的存在。
其次,生产工艺的控制是陶瓷密密麻麻的黑点的另一个重要原因。
在陶瓷制品的生产过程中,各个环节都会对最终产品的质量产生影响。
例如,釉料的施釉过程中,不仅需要控制好涂布的均匀度,还要控制好施釉的厚度。
若釉面过厚,煅烧过程中釉料容易发生变化,形成黑点;而釉面过薄,则无法有效地覆盖陶瓷基材,也容易形成黑点。
此外,煅烧的温度和时间等也会影响到陶瓷制品的质量,需要根据具体产品的工艺要求进行科学的控制。
另外,环境因素也会对陶瓷制品产生影响,导致出现密密麻麻的黑点。
例如,在煅烧的过程中,如果窑温不稳定,即使工艺控制得当,也可能出现颗粒团聚或结合不良的现象,进而引发黑点的出现。
此外,空气中的灰尘、污染物等也会附着在陶瓷制品的表面,形成黑点。
针对陶瓷制品上密密麻麻的黑点问题,可以从以下几个方面进行改进。
首先,在原料的质量控制上,需要加强选材,选择优质原料,并进行混合、筛选等步骤,以减少带入陶瓷制品生产过程的杂质含量。
其次,在生产工艺的控制上,需要严格控制每个环节的参数,如施釉的厚度、煅烧的温度和时间等,确保每个工艺步骤的质量。
另外,在环境控制上,需要保持生产车间的干净整洁,减少灰尘和污染物对陶瓷制品的影响。
同时,要确保煅烧的环境温度稳定,避免温度波动引起的问题。
最后,为了提高陶瓷制品的质量,还需要加强工艺人员的培训与技术水平的提升。
只有操作人员具备扎实的工艺知识和丰富的经验,才能够更好地掌控整个生产过程,从而减少黑点的产生。
PC透明产品烧黄黑点的防范和改善措施
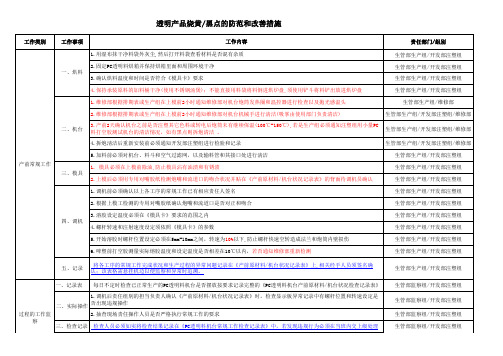
1.调机后责任组別的担当负责人确认《产前原材料/机台状况记录表》时,检查显示板异常记录中有螺杆位置和转速设定是 二、实际操作 否出现违规操作 过程的工作监 察 三、检查记录 2.抽查现场责任操作人员是否严格执行常规工作的要求 检查人员必须如实将检查结果记录在《PC透明料机台常规工作检查记录表》中,若发现违规行为必须在当班內交上级处 工作事项 四、异常检查 五、违规处理 工作内容 根据《生产机台一览表》或《停产单》反馈黑点/烧黄的不良内容进行分析并对相应的常规工作进行检查 对外部违规行为必须开出错报告与其部门负责人,对内部违规行为按照内部处罚条例对违规人员进行处罚 1.对模具行位进行淸洁(抹模) 2.检查产前常规工作是否执行到位 生产中异常对策 检测/改善 3.打空胶测量实际熔胶温度和设定温度是否相差在10℃以内,若超出该范围须通知维修部检测炮筒发热圈、温控器和感温头 4.打空胶查看烧黄/黑点是否从炮筒中出現,若是拆炮淸洁并检查炮筒螺杆及配件是否存在磨损并给予更换 5.开模打空胶查看烧黄/黑点是否经过前模热嘴后出現,若是开修模单检查或更换热嘴 责任部门/组别 生管部生产组/开发部注塑组 生管部监察组/开发部注塑组 生管部监察组/开发部注塑组 生管部生产组/开发部注塑组 生管部生产组/开发部注塑组 维修部/开发部注塑组 生管部生产组/开发部注塑组
透明产品烧黄/黑点的防范和改善措施
工作类別 工作事项 工作内容 1.用湿布抹干净料袋外灰尘,然后打开料袋查看材料是否混有杂质 2.固定PC透明料烘箱并保持烘箱里面和周围环境干净 一、烘料 3.确认烘料温度和时间是否符合《模具卡》要求 4.保持承装原料的加料桶干净(使用不锈钢汤煲);不能直接用料袋将料倒进烘炉盘,须使用铲斗将料铲出放进烘炉盘 1.维修部根据排期表或生产组在上模前2小时通知维修部对机台炮筒发热圈和温控器进行检查以及拋光感温头 2.维修部根据排期表或生产组在上模前2小时通知维修部对机台机械手进行淸洁(吸掌由使用部门负责清洁) 二、机台 3.产前2天确认机台之前是否注塑其它色料或转电后炮筒未有继续保温(100℃-150℃),若是生产组必须通知注塑组用小量PC 料打空胶测试机台的清洁情况,如有黑点则拆炮清洁 。 4.拆炮淸洁后重新安装前必须通知开发部注塑组进行检验和记录 5.加料前必须对机台、料斗和空气过滤网,以及输料管和其接口处进行淸洁 产前常规工作 三、模具 2.上模后必须用专用对嘴胶纸检测炮嘴和流道口的吻合状况并贴在《产前原材料/机台状况记录表》的背面待调机员确认 1.调机前必须确认以上各工序的常规工作已有相应责任人签名 2.根据上模工检测的专用对嘴胶纸确认炮嘴和流道口是否对正和吻合 3.溶胶设定温度必须在《模具卡》要求的范围之内 四、调机 4.螺杆转速和注射速度设定须依照《模具卡》的参数 5.开始溶胶时螺杆位置设定必须在5mm-10mm之间,转速为10%以下,防止螺杆快速空转造成法兰和炮筒内壁损伤 6.啤塑前打空胶测量实际熔胶温度和设定温度是否相差在10℃以内,若否通知维修部重新检测 五、记录 一、记录表 将各工序的常规工作完成状况和生产过程的异常问题记录在《产前原材料/机台状况记录表》上,相关经手人员须签名确 认;该表格需悬挂机边以便监察和异常时追溯。 每日不定时检查已正常生产的PC透明料机台是否摆放按要求记录完整的《PC透明料机台产前原材料/机台状况检查记录表》 生管部生产组/开发部注塑组 生管部生产组/开发部注塑组 生管部生产组/开发部注塑组 生管部生产组/开发部注塑组 生管部监察组/开发部注塑组 生管部监察组/开发部注塑组 生管部监察组/开发部注塑组 生管部监察组/开发部注塑组 生管部生产组/开发部注塑组 生管部生产组/开发部注塑组 生管部生产组/开发部注塑组 生管部生产组/开发部注塑组 1. 模具必须在上模前除油,防止模具沾有油渍和有锈渍 生管部生产组/开发部注塑组 生管部生产组/开发部注塑组 生管部生产组/维修部 生管部生产组/开发部注塑组/维修部 生管部生产组/开发部注塑组/维修部 生管部生产组/开发部注塑组/维修部 生管部生产组/开发部注塑组 生管部生产组/开发部注塑组 责任部门/组别 生管部生产组/开发部注塑组 生管部生产组/开发部注塑组
塑件黑点标准
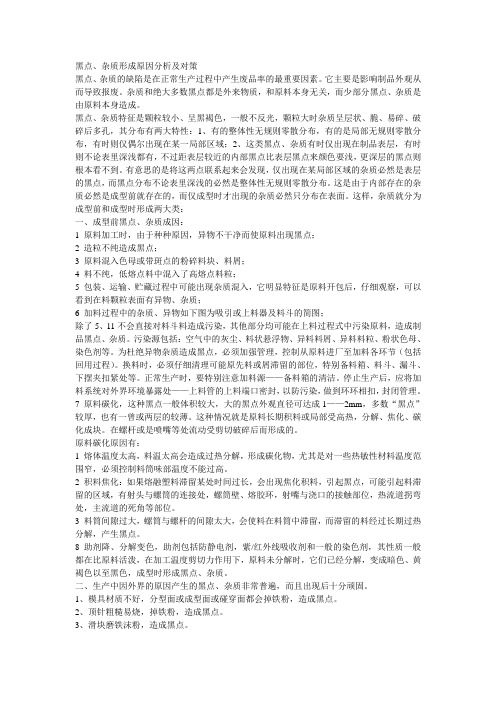
黑点、杂质形成原因分析及对策黑点、杂质的缺陷是在正常生产过程中产生废品率的最重要因素。
它主要是影响制品外观从而导致报废。
杂质和绝大多数黑点都是外来物质,和原料本身无关,而少部分黑点、杂质是由原料本身造成。
黑点、杂质特征是颗粒较小、呈黑褐色,一般不反光,颗粒大时杂质呈层状、脆、易碎、破碎后多孔,其分布有两大特性:1、有的整体性无规则零散分布,有的是局部无规则零散分布,有时则仅偶尔出现在某一局部区域;2、这类黑点、杂质有时仅出现在制品表层,有时则不论表里深浅都有,不过距表层较近的内部黑点比表层黑点来颜色要浅,更深层的黑点则根本看不到。
有意思的是将这两点联系起来会发现,仅出现在某局部区域的杂质必然是表层的黑点,而黑点分布不论表里深浅的必然是整体性无规则零散分布。
这是由于内部存在的杂质必然是成型前就存在的,而仅成型时才出现的杂质必然只分布在表面。
这样,杂质就分为成型前和成型时形成两大类:一、成型前黑点、杂质成因:1 原料加工时,由于种种原因,异物不干净而使原料出现黑点;2 造粒不纯造成黑点;3 原料混入色母或带斑点的粉碎料块、料屑;4 料不纯,低熔点料中混入了高熔点料粒;5 包装、运输、贮藏过程中可能出现杂质混入,它明显特征是原料开包后,仔细观察,可以看到在料颗粒表面有异物、杂质;6 加料过程中的杂质、异物如下图为吸引或上料器及料斗的简图;除了5、11不会直接对料斗料造成污染,其他部分均可能在上料过程式中污染原料,造成制品黑点、杂质。
污染源包括:空气中的灰尘、料状悬浮物、异料料屑、异料料粒、粉状色母、染色剂等。
为杜绝异物杂质造成黑点,必须加强管理,控制从原料进厂至加料各环节(包括回用过程)。
换料时,必须仔细清理可能原先料或屑滞留的部位,特别备料箱、料斗、漏斗、下摆夹扣紧处等。
正常生产时,要特别注意加料源——备料箱的清洁。
停止生产后,应将加料系统对外界环境暴露处——上料管的上料端口密封,以防污染,做到环环相扣,封闭管理。
黑点杂质改善
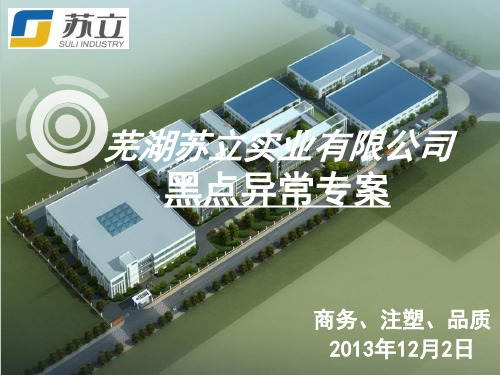
• 4.检查冷/热浇道的清洁度,清理塑料流动区域
四
原料
1.原料内含有的脏污,杂质 2.色母内含有的脏污,杂质 3.二次料清洁度不足 4.原料存放区域污染
对策------原料
• 1.品质对没批次原料粒子、色母进行检测, 确保生产领用料必须是合格品
黑点、杂质不良的专案
人员
机台
品质标准
螺杆损伤
加料时混入 换料时未清理干净
料温设定不当
机台停机时 间长
止逆环磨损
料管损伤 机台表面灰尘
模具表面灰尘
顶出活动 件脏污
色母脏污 模具钢材磨损
回料脏污
原料内脏污 原料存放污染
杂质、黑点 环境因素,空气灰尘
模具
原料
环境
一
人
1.加料时混入 2.换料时未清理干净 3.品质标准不明确 4.机台停机时间过长
对策------人
• 1.对加料人员进行培训,严格依照加料流程操 作。控制加料过程清洁度。
• 2.换料时,料桶内部清洁,包含送风电机防尘 罩,出风口防护
• 3.品质人员明确品质黑点、杂质标准。提供黑 点卡,悬挂在机台明显位置,以便比对
• 4.分析黑点、杂质现象布局并统计 • 5.各班长宣导机台操作员,半自动机台务必确
• 2.生产领用原物料时,须做记录(生产厂家, 批号,领用数量)
• 3.严控二次料回收破碎 存放 使用比例, 针对纯白大件,建议不加二次料
• 3.原料/色母存放区域5S,须保持清洁
五
环境
环境空气中漂浮的灰尘
对策------环境
• 1.每班次对车间环境进行清扫,车间通道用 湿拖把4H/次清洁
生产过程中黑点常见原因和解决办法 (1)
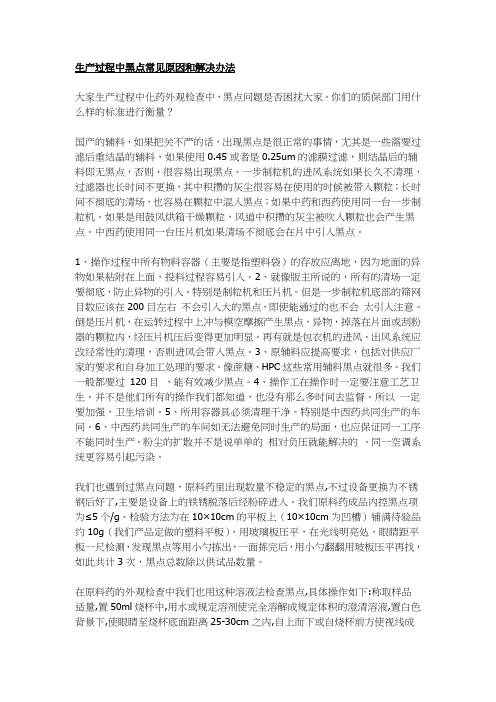
生产过程中黑点常见原因和解决办法大家生产过程中化药外观检查中,黑点问题是否困扰大家。
你们的质保部门用什么样的标准进行衡量?国产的辅料,如果把关不严的话,出现黑点是很正常的事情,尤其是一些需要过滤后重结晶的辅料,如果使用0.45或者是0.25um的滤膜过滤,则结晶后的辅料即无黑点,否则,很容易出现黑点。
一步制粒机的进风系统如果长久不清理,过滤器也长时间不更换,其中积攒的灰尘很容易在使用的时候被带入颗粒;长时间不彻底的清场,也容易在颗粒中混入黑点;如果中药和西药使用同一台一步制粒机。
如果是用鼓风烘箱干燥颗粒,风道中积攒的灰尘被吹入颗粒也会产生黑点。
中西药使用同一台压片机如果清场不彻底会在片中引入黑点。
1、操作过程中所有物料容器(主要是指塑料袋)的存放应离地,因为地面的异物如果粘附在上面,投料过程容易引入。
2、就像版主所说的,所有的清场一定要彻底,防止异物的引入。
特别是制粒机和压片机。
但是一步制粒机底部的筛网目数应该在200目左右不会引入大的黑点,即使能通过的也不会太引人注意。
倒是压片机,在运转过程中上冲与模空摩擦产生黑点,异物,掉落在片面或刮粉器的颗粒内,经压片机压后变得更加明显。
再有就是包衣机的进风、出风系统应改经常性的清理,否则进风会带入黑点。
3、原辅料应提高要求,包括对供应厂家的要求和自身加工处理的要求。
像蔗糖、HPC这些常用辅料黑点就很多。
我们一般都要过120目,能有效减少黑点。
4、操作工在操作时一定要注意工艺卫生。
并不是他们所有的操作我们都知道,也没有那么多时间去监督。
所以一定要加强,卫生培训。
5、所用容器具必须清理干净。
特别是中西药共同生产的车间。
6、中西药共同生产的车间如无法避免同时生产的局面,也应保证同一工序不能同时生产。
粉尘的扩散并不是说单单的相对负压就能解决的。
同一空调系统更容易引起污染。
我们也遇到过黑点问题,原料药里出现数量不稳定的黑点,不过设备更换为不锈钢后好了,主要是设备上的铁锈脱落后经粉碎进入。
杂质质量改善措施方案
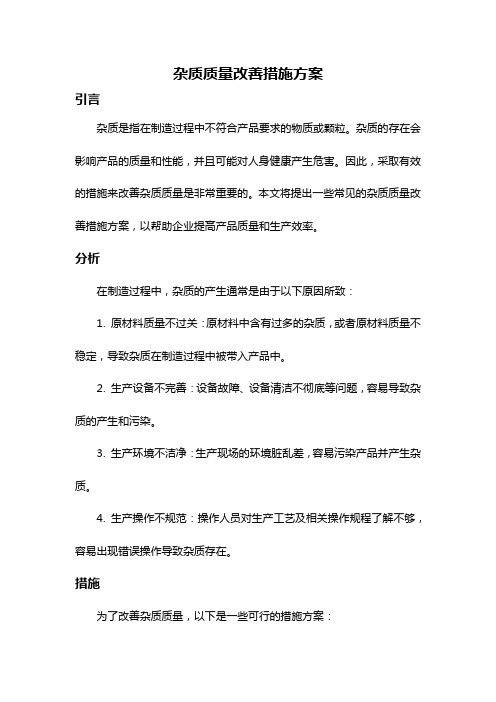
杂质质量改善措施方案引言杂质是指在制造过程中不符合产品要求的物质或颗粒。
杂质的存在会影响产品的质量和性能,并且可能对人身健康产生危害。
因此,采取有效的措施来改善杂质质量是非常重要的。
本文将提出一些常见的杂质质量改善措施方案,以帮助企业提高产品质量和生产效率。
分析在制造过程中,杂质的产生通常是由于以下原因所致:1. 原材料质量不过关:原材料中含有过多的杂质,或者原材料质量不稳定,导致杂质在制造过程中被带入产品中。
2. 生产设备不完善:设备故障、设备清洁不彻底等问题,容易导致杂质的产生和污染。
3. 生产环境不洁净:生产现场的环境脏乱差,容易污染产品并产生杂质。
4. 生产操作不规范:操作人员对生产工艺及相关操作规程了解不够,容易出现错误操作导致杂质存在。
措施为了改善杂质质量,以下是一些可行的措施方案:1. 严格选择优质原材料和供应商在采购过程中,应该与供应商建立长期稳定的合作关系,共同制定与杂质质量有关的标准,并定期进行原材料质量的评估和检测。
同时,通过合理的原材料筛选和检测程序,确保原材料的质量符合要求,并避免带入杂质。
2. 完善的设备维护和清洁计划设备在使用过程中容易受到磨损和杂质积累,因此,制定定期的设备维护和清洁计划至关重要。
维护和保养设备,确保设备的正常运行和性能稳定。
在使用过程中,要加强设备的清洁和消毒工作,确保产品的卫生和纯净度。
3. 建立严格的生产环境管理制度建立严格的生产环境管理制度,包括定期清洁、消毒和除尘工作。
在生产现场的设置和布局上,合理规划生产区域和仓储区域,减少杂质和污染的传播。
同时,要加强员工培训,提高员工的卫生意识和操作规范,降低环境污染和杂质污染的概率。
4. 加强质量控制和检测建立完善的质量控制和检测体系,制定严格的质量检测标准和流程。
在制造过程中,定期进行质量抽检,对产品中的杂质进行识别和分析。
同时,在产品质量监控的过程中,及时发现问题并采取相应的措施来解决。
5. 持续改进和管理优化持续改进和管理优化是改善杂质质量的关键。
聚酰亚胺碳化黑点
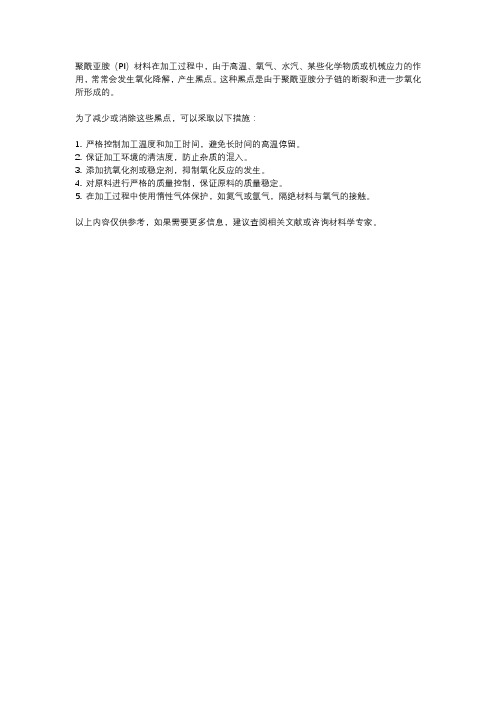
聚酰亚胺(PI)材料在加工过程中,由于高温、氧气、水汽、某些化学物质或机械应力的作用,常常会发生氧化降解,产生黑点。
这种黑点是由于聚酰亚胺分子链的断裂和进一步氧化所形成的。
为了减少或消除这些黑点,可以采取以下措施:
1. 严格控制加工温度和加工时间,避免长时间的高温停留。
2. 保证加工环境的清洁度,防止杂质的混入。
3. 添加抗氧化剂或稳定剂,抑制氧化反应的发生。
4. 对原料进行严格的质量控制,保证原料的质量稳定。
5. 在加工过程中使用惰性气体保护,如氮气或氩气,隔绝材料与氧气的接触。
以上内容仅供参考,如果需要更多信息,建议查阅相关文献或咨询材料学专家。
煮饭时如何去除谷中黑点——有关米饭的科学教案

煮饭是我们日常中必不可少的饮食环节,而米饭作为我们餐桌上的主食之一,也需要我们去注意一些细节,保障饭的质量和口感,其中去除谷中黑点就是其中的一部分。
以下是有关米饭的科学教案。
一、黑点来源米饭中的黑点有很多种来源,包括土壤、水源、胶质层残留等等。
而其中最主要的黑点来源则是因为米粒收割时未能及时去除空心部位导致,由于空腔会在米粒内部空气流通时形成,细菌也能轻而易举地进入米粒内部生长繁殖,导致米饭出现黑点。
二、处理方法如何去除谷中黑点呢?以下是几种常见的处理方法:1.清洗米饭:在烹饪米饭之前,先用清水将米饭浸泡30分钟或以上,倒掉浸泡过的水后再次冲洗,将多余的黑点和杂质冲走,这种方法适用于谷中黑点较轻的情况。
2.淘米:淘米是指用清水冲洗未煮的干米,让米饭表面的黑点和杂质被淘走。
方法是先用干净的手揉动米饭,使米纹的表面表现出一层白色的朦胧,然后将米放入清水中,把水倒出来,重复此操作数次后,黑点和杂质就会越来越少。
3.捞渣:在煮饭的过程中,用漏勺捞去米饭煮到下面的渣滓,这些渣滓包括胶质层残留,也是会导致黑点的来源之一。
4.选择优质的米:选择外观完好,米粒内无空腔和腐烂斑点的优质米,以此减少米饭中黑点出现的可能性。
三、科学原理为什么这些方法能去除谷中黑点呢?以下是科学原理的解释:1.清洗米饭:清水浸泡米饭是为了使杂质在水浸过程中容易将其浮出,这样就可以轻松地将黑点和其他杂质去掉。
2.淘米:淘米可以摩擦掉米饭得表面上的杂质和黑点,同时也能将部分营养物质的油脂和蛋白质去掉,让米饭更加嫩滑。
3.捞渣:捞渣可以去除米饭煮到最底下的渣滓和胶质层残留,在煮出精致的米饭的同时也能减少黑点的出现。
4.选择优质的米:优质米的煮饭质量远远好于普通米,由于没有空腔或腐烂斑点,所以黑点出现的可能性也就降低了。
四、小结去除谷中黑点是米饭烹饪过程中的一个重要环节,只有妥善地处理过黑点,才能保障米饭的品质和口感。
以上介绍了几种去除谷中黑点的方法,这也是科学的,严谨的烹饪方法。
浸胶纸黑点改善方案

浸胶纸黑点问题可能由多种因素引起,包括原材料问题、生产工艺问题、设备问题等。
为了解决这个问题,可以采取以下改善方案:
1.原材料控制:首先,对原材料的采购和使用进行严格把关。
确
保所使用的原材料符合质量要求,无杂质和污染。
同时,对原
材料进行定期检测,及时发现并处理潜在问题。
2.生产工艺优化:对生产工艺进行深入研究,找出可能导致黑点
产生的环节,并进行优化。
例如,调整浸胶液的配方,减少杂
质和气泡的产生;优化浸胶纸的干燥工艺,确保浸胶纸在干燥
过程中不会受到污染。
3.设备维护:定期对生产设备进行维护和保养,确保设备处于良
好的工作状态。
对于可能出现问题的设备,及时进行维修和更
换,避免设备故障对产品质量造成影响。
4.环境控制:对生产环境进行严格控制,确保生产环境的清洁和
卫生。
对于可能产生污染的因素,如灰尘、油污等,进行及时
清理和处理。
5.质量检测:加强产品质量检测,对每一批次的浸胶纸进行严格
的质量检查。
对于存在黑点等质量问题的产品,及时进行追溯
和处理,避免问题产品流入市场。
综上所述,针对浸胶纸黑点问题,可以从原材料控制、生产工艺优化、设备维护、环境控制以及质量检测等方面入手,全面提升产品质量和生产效率。
- 1、下载文档前请自行甄别文档内容的完整性,平台不提供额外的编辑、内容补充、找答案等附加服务。
- 2、"仅部分预览"的文档,不可在线预览部分如存在完整性等问题,可反馈申请退款(可完整预览的文档不适用该条件!)。
- 3、如文档侵犯您的权益,请联系客服反馈,我们会尽快为您处理(人工客服工作时间:9:00-18:30)。
对策------人
• 1.对加料人员进行培训,严格依照加料流程操 作。控制加料过程清洁度。 • 2.换料时,料桶内部清洁,包含送风电机防尘 罩,出风口防护 • 3.品质人员明确品质黑点、杂质标准。提供黑 点卡,悬挂在机台明显位置,以便比对 • 4.分析黑点、杂质现象布局并统计 • 5.各班长宣导机台操作员,半自动机台务必确 保机台周期稳定,非异常状态时,不得私自停 机、怠工
芜湖苏立实业有限公司 黑点异常专案
商务、注塑、品质 2013年12月2日
黑点、杂质不良的改善方案
次合格率
• 协作人员,配合单位
专案协作人员
一.注塑工艺员 二.模具工程师 三.项目工程师 四.品质工程师 五.设备维修组 六.物料组 七.注塑直接作业员
二
机台
1.料温设定不当 2.止逆环磨损 3.料管组损坏 4.机台表面灰尘
对策------机
• 1.合理设定注塑机台各段温度,包含料管、热 流道、烘料温度; • 2.检测机台止逆环磨损状态,防止因部件磨损 后的铁屑产生; • 3.每班次定时清理机台表面浮尘,确保在开合 模动作时产生空气流,吹动表面灰尘而落入模 具型腔表面 • 4.原料流通通道,有间隙导致灰尘进入。吸料 机过滤网内残留料屑,定期清理
四
原料
1.原料内含有的脏污,杂质 2.色母内含有的脏污,杂质 3.二次料清洁度不足 4.原料存放区域污染
对策------原料
• 1.品质对没批次原料粒子、色母进行检测, 确保生产领用料必须是合格品 • 2.生产领用原物料时,须做记录(生产厂家, 批号,领用数量) • 3.严控二次料回收破碎 存放 使用比例, 针对纯白大件,建议不加二次料 • 3.原料/色母存放区域5S,须保持清洁
三
模具
1.模具表面灰尘 2.顶出活动件脏污 3.模具钢材磨损,铁屑 4.流道脏污
对策------模具
• 1.每班次定期清理模具,包含PL面残留胶丝、 锈斑、模具外侧落尘 • 2.清理&保养模具顶出机构,保养后的顶针、 斜顶残留油污及时清理 • 3.定期保养顶出、配合块的润滑,确保不可有 活动机构件(模具、顶出、配合块)动作时产 生的铁屑 • 4.检查冷/热浇道的清洁度,清理塑料流动区域
五
环境
环境空气中漂浮的灰尘
对策------环境
• 1.每班次对车间环境进行清扫,车间通道用 湿拖把4H/次清洁 • 2.机台作业区,每2H/次清扫 • 3.模具每班1次保养
结 束 语
以上为检讨改善对策 请各单位相关人员协助处 理,并严格执行
诚恳邀请各位提出宝贵意见! 感谢!
黑点、杂质不良的专案
人员 品质标准 加料时混入 换料时未清理干净
模具表面灰尘 料温设定不当 机台停机时 间长
机台
螺杆损伤 料管损伤
止逆环磨损
机台表面灰尘 杂质、黑点 回料脏污
原料内脏污
色母脏污
顶出活动 件脏污
环境因素,空气灰尘
模具钢材磨损
原料存放污染
模具
原料
环境
一
人
1.加料时混入 2.换料时未清理干净 3.品质标准不明确 4.机台停机时间过长