优化酸洗工艺降低黑斑缺陷(1)
酸洗板表面质量控制和常见缺陷应对措施
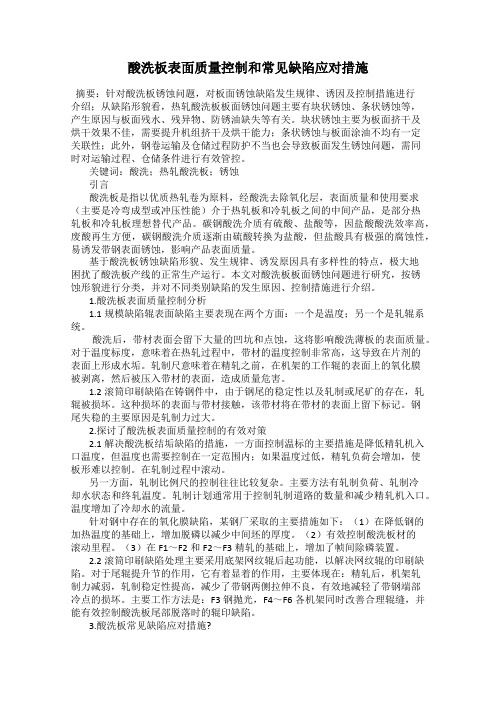
酸洗板表面质量控制和常见缺陷应对措施摘要:针对酸洗板锈蚀问题,对板面锈蚀缺陷发生规律、诱因及控制措施进行介绍;从缺陷形貌看,热轧酸洗板板面锈蚀问题主要有块状锈蚀、条状锈蚀等,产生原因与板面残水、残异物、防锈油缺失等有关。
块状锈蚀主要为板面挤干及烘干效果不佳,需要提升机组挤干及烘干能力;条状锈蚀与板面涂油不均有一定关联性;此外,钢卷运输及仓储过程防护不当也会导致板面发生锈蚀问题,需同时对运输过程、仓储条件进行有效管控。
关键词:酸洗;热轧酸洗板;锈蚀引言酸洗板是指以优质热轧卷为原料,经酸洗去除氧化层,表面质量和使用要求(主要是冷弯成型或冲压性能)介于热轧板和冷轧板之间的中间产品,是部分热轧板和冷轧板理想替代产品。
碳钢酸洗介质有硫酸、盐酸等,因盐酸酸洗效率高,废酸再生方便,碳钢酸洗介质逐渐由硫酸转换为盐酸,但盐酸具有极强的腐蚀性,易诱发带钢表面锈蚀,影响产品表面质量。
基于酸洗板锈蚀缺陷形貌、发生规律、诱发原因具有多样性的特点,极大地困扰了酸洗板产线的正常生产运行。
本文对酸洗板板面锈蚀问题进行研究,按锈蚀形貌进行分类,并对不同类别缺陷的发生原因、控制措施进行介绍。
1.酸洗板表面质量控制分析1.1规模缺陷辊表面缺陷主要表现在两个方面:一个是温度;另一个是轧辊系统。
酸洗后,带材表面会留下大量的凹坑和点蚀,这将影响酸洗薄板的表面质量。
对于温度标度,意味着在热轧过程中,带材的温度控制非常高,这导致在片剂的表面上形成水垢。
轧制尺意味着在精轧之前,在机架的工作辊的表面上的氧化膜被剥离,然后被压入带材的表面,造成质量危害。
1.2滚筒印刷缺陷在铸钢件中,由于钢尾的稳定性以及轧制或尾矿的存在,轧辊被损坏。
这种损坏的表面与带材接触,该带材将在带材的表面上留下标记。
钢尾失稳的主要原因是轧制力过大。
2.探讨了酸洗板表面质量控制的有效对策2.1解决酸洗板结垢缺陷的措施,一方面控制温标的主要措施是降低精轧机入口温度,但温度也需要控制在一定范围内;如果温度过低,精轧负荷会增加,使板形难以控制。
冷轧带钢表面黑斑缺陷的控制实践

冷轧带钢表面黑斑缺陷的控制实践摘要:介绍了冷轧碳素带钢的常见缺陷—压入型、氧化型黑斑的形貌特征及成因机理,泰钢冷轧薄板厂在2 a的生产实践中,通过提高酸洗板质量、合理优化轧机道次变形量,对乳化液温度、浓度、压力、流量及清洁度的有效控制,较好地控制了黑斑缺陷。
关键词:带钢;黑斑缺陷;酸洗质量;轧制道次;乳化液中图分类号:TG335.12 文献标识码:B 文章编号:1004-4620(2008)03-0038-02 Practice of Controlling Black Spot Defects in Cold Rolling Steel Strip SurfaceLIU Jin-yuan(The Cold Rolling Sheet Plant of Shandong Taishan Iron and Steel Group Corporation, Laiwu271100, China)Abstract: This article introduces the usual flaw of carbon cold rolling steel strip surface that is pressing and oxidizing black spot defects characteristic and cause of its formation. During two years’practice, the cold-rolling plant of Taishan steel controls black spot defects better by improving quality of pickled sheet and rolling degree of deformation in pass, and by controlling the temperature, thickness, pressure, outflow and cleanness of emulsion.Key words: steel strip; black spot defects; quality of pickling; rolling pass; emulsion1 前言冷轧碳素带钢“黑斑”是在轧制过程中产生的一种常见缺陷。
酸洗钝化处理工艺的好处
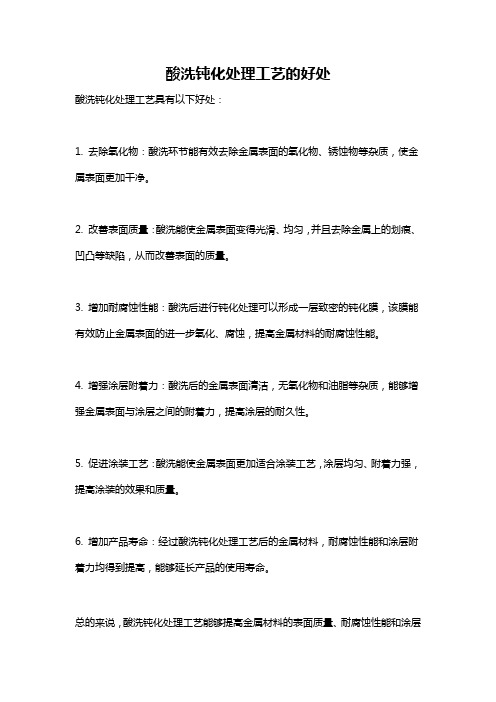
酸洗钝化处理工艺的好处
酸洗钝化处理工艺具有以下好处:
1. 去除氧化物:酸洗环节能有效去除金属表面的氧化物、锈蚀物等杂质,使金属表面更加干净。
2. 改善表面质量:酸洗能使金属表面变得光滑、均匀,并且去除金属上的划痕、凹凸等缺陷,从而改善表面的质量。
3. 增加耐腐蚀性能:酸洗后进行钝化处理可以形成一层致密的钝化膜,该膜能有效防止金属表面的进一步氧化、腐蚀,提高金属材料的耐腐蚀性能。
4. 增强涂层附着力:酸洗后的金属表面清洁,无氧化物和油脂等杂质,能够增强金属表面与涂层之间的附着力,提高涂层的耐久性。
5. 促进涂装工艺:酸洗能使金属表面更加适合涂装工艺,涂层均匀、附着力强,提高涂装的效果和质量。
6. 增加产品寿命:经过酸洗钝化处理工艺后的金属材料,耐腐蚀性能和涂层附着力均得到提高,能够延长产品的使用寿命。
总的来说,酸洗钝化处理工艺能够提高金属材料的表面质量、耐腐蚀性能和涂层
附着力,从而增加产品的使用寿命,保证产品的品质和可靠性。
酸洗缺陷分析

酸洗缺陷分析在冷轧带钢生产中的酸洗工序,有时因酸洗条件不理想,操作不当或某些设备不良,可能会造成各种酸洗缺陷,归结起来,大致有以下几种:1、酸洗不均带钢表面个别或局部地方残留着未被酸洗掉的氧化铁皮斑点。
产生原因:①带钢在酸洗前没有松卷或松卷不均,表面有相互贴紧现象,酸液不易与其反应。
②酸洗前,带钢表面上有油污等未被清除干净,而阻碍了带钢与酸反应,③酸洗中,未将带钢反复提升或充分揽动酸液也会产生酸洗不匀的情况。
2、酸洗不足带钢表面残留着未被酸洗掉的氧化皮,用手抹有黑灰。
产生原因:①酸液的温度低,浓度不够,或带钢在酸液中的停留时间不够,②剥壳处理未达到预先要求,酸洗不足的带钢,轻者轧制后带钢表面颜色发暗,严重者氧化铁皮被轧入呈黑斑,氧化铁皮也可能粘在轧辊表面上,大块的氧化铁皮使带钢轧制时不延伸,而造成轧制后带钢出现浪形等缺陷。
解决方法是重新进行酸洗。
3、点状腐蚀带钢表面上产生点或带状的凹坑。
产生原因:①酸液温度过高、浓度过高;②酸洗时间过长,③酸洗缓蚀剂量不足,至使带钢表面逐渐变粗糙成麻面。
点状腐蚀的带钢,延伸性大大降低,在轧制过程中很容易断裂或破碎,坯料上的细微点状腐蚀一般可通过冷轧得到清除,而成品带钢的点状腐蚀是一种不可清除的缺陷。
4、酸渍、水渍带钢酸洗后,表面被锈蚀,呈黄色。
产生原因:①带钢表面经清洗后还残存着少量的酸质,中和不完全,②带钢表面没有完全干燥而与空气中氧发生反应而锈蚀。
解决方法:清洗槽尽量采用活水,提高中和槽中碱的含量和温度,或增加烘干工序,也可采用钝化处理。
5、氢脆带钢表面呈现外观为条状的小鼓泡,鼓泡破裂后呈黑色细小裂缝,没有破裂的经轧制后便破裂或裂缝延伸、扩大。
并且是无规律的,它直接影响带钢的韧性和塑性。
产生原因:带钢吸收酸洗过程中所析出的氢。
解决方法:严格按酸洗工艺制度进行酸洗,采用缓蚀剂,酸洗后,采用烘干或将带钢置于空气或清水中若干时间。
6、黑斑带钢表面呈现形状不同的黑色或成片的黑印。
冷轧带钢酸洗工艺缺陷及对策分析探讨
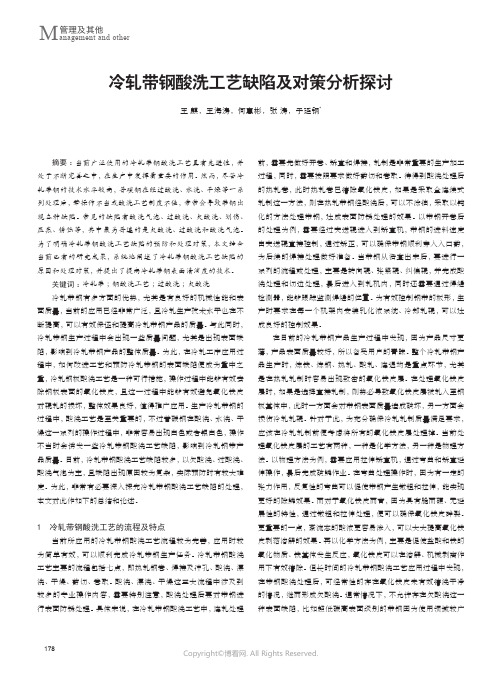
管理及其他M anagement and other冷轧带钢酸洗工艺缺陷及对策分析探讨王 麒,王海涛,何惠彬,张 涛,于延钢*摘要:当前广泛使用的冷轧带钢酸洗工艺具有先进性,并处于不断完善之中,在生产中发挥着重要的作用。
然而,尽管冷轧带钢的技术水平较高,普碳钢在经过酸洗、水洗、干燥等一系列处理后,若操作不当或酸洗工艺制度不佳,常常会导致带钢出现各种缺陷。
常见的缺陷有酸洗气泡、过酸洗、欠酸洗、划伤、压痕、锈蚀等,其中最为普遍的是欠酸洗、过酸洗和酸洗气泡。
为了明确冷轧带钢酸洗工艺缺陷的预防和处理对策,本文结合当前已有的研究成果,系统地阐述了冷轧带钢酸洗工艺缺陷的原因和处理对策,并提出了提高冷轧带钢表面清洁度的技术。
关键词:冷轧带;钢酸洗工艺;过酸洗;欠酸洗冷轧带钢有多方面的优势,尤其是有良好的机械性能和表面质量,当前的应用已经非常广泛,且冷轧生产技术水平也在不断提高,可以有效保证和提高冷轧带钢产品的质量。
与此同时,冷轧带钢生产过程中会出现一些质量问题,尤其是出现表面缺陷,影响到冷轧带钢产品的整体质量。
为此,在冷轧工序应用过程中,如何改进工艺和预防冷轧带钢的表面缺陷便成为重中之重,冷轧钢板酸洗工艺是一种可行措施,操作过程中能够有效去除钢板表面的氧化铁皮,且这一过程中能够有效避免氧化铁皮对辊轧的损坏,整体效果良好,值得推广应用。
生产冷轧带钢的过程中,酸洗工艺是至关重要的,不过普碳钢在酸洗、水洗、干燥这一系列的操作过程中,非常容易出现白色或者银白色,操作不当时会诱发一些冷轧带钢酸洗工艺缺陷,影响到冷轧钢带产品质量。
目前,冷轧带钢酸洗工艺缺陷较多,以欠酸洗、过酸洗、酸洗气泡为主,且缺陷出现原因较为复杂,实际预防时有较大难度。
为此,非常有必要深入探究冷轧带钢酸洗工艺缺陷的处理,本文对此作如下的总结和论述。
1 冷轧带钢酸洗工艺的流程及特点当前所应用的冷轧带钢酸洗工艺流程较为完善,应用时较为简单有效,可以顺利完成冷轧带钢生产任务。
优化酸洗工艺降低黑斑缺陷(1)

294
314
296
课题成立时,黑斑缺陷有逐月增多趋势,月平均值在300吨左右。以厂部制定
的废次降硬性指标作为攻关目标,即产量的0.01%约为170~180吨每月,小组通过
讨论,觉得有能力将黑斑缺陷降低至100吨每月以下,因此将目标定制在100吨/
月。
300吨
100吨
攻关前黑斑重量/月 攻关后黑斑重量/月
针对这一情况我们重新制定了破鳞机使用 参数以及挤干辊更换周期,从现在来看效果 较好。已经固话写入技术规程。
七、改善对策
破鳞机参数:
厚度
1#矫直机啮合量 2#矫直机啮合量
防横弯啮合量
h≤2.5 2.5<h≤3.5
10-15mm 8-15mm
10-15mm 8-15mm
10-15mm 8-15mm
3.5<h≤4.5
否
合工艺要求,同时充分考虑成本影响,酸浓度不做
要因。
通过观察生产实际,目前制定的酸洗速度
5
酸洗速度的影 响
240m/min时常造成带钢板面欠酸洗,同时由于速 度过快造成入口活套量不足,造成酸洗速度
(20m/min以下)过慢,会造成板面发黑,产生过
是
酸洗,罩退重卷后产生黑斑。
6
换辊等停车影 由于换辊原因造成的酸洗段停车,产生的停车斑在 是
5Y95670
5Y97064
黑斑
黑斑
黑斑 黑斑 停车 斑
4*1524
4*1219
3.5*121 9
3.5*125 0
4*1250
SPCC1
SPCC1
SPCC1
TYH
SPCC1
大量块状黑斑
纠偏报警,酸洗工艺段 停车2分
常见酸洗缺陷及对策

(4)锈蚀 ) 酸洗后表面重新出现锈层的现象称为锈蚀 锈蚀形成的原因是 锈层的现象称为锈蚀。 形成的原因是: 原料酸洗后表面重新出现锈层的现象称为锈蚀。锈蚀形成的原因是: 带钢(钢板)酸洗后表面残留少许的酸溶液,或带钢清 少许的酸溶液 带钢(钢板)酸洗后表面残留少许的酸溶液,或带钢清洗后没有达到 完全干燥而使表面重新 干燥而使表面重 此外,带钢在酸洗后于高温的清 于高温的 完全干燥而使表面重新生锈。此外,带钢在酸洗后于高温的清洗水中 停留时间过长, 产生锈蚀现象。 锈蚀现象 停留时间过长,也会产生锈蚀现象。 带钢锈蚀处的钢板表面在轧制之后呈暗色 使成品在库存 库存时 带钢锈蚀处的钢板表面在轧制之后呈暗色,它促使成品在库存时再次 锈蚀处的钢板表面在轧制之后呈暗色, 锈蚀, 降低成品材的表面质 严重时使产品报 锈蚀,从而降低成品材的表面质量,严重时使产品报废。 防止锈蚀的措施是严格执行酸洗、清洗操作规程,及时给表面涂油, 及时给表面涂油 涂油, 防止锈蚀的措施是严格 行酸洗、 洗操作规 锈蚀的措施是严格执 并应堆放 干燥的地 堆放在 的地方 并应堆放在干燥的地方。 (5)夹杂 ) 带钢在酸洗后表面出现深陷的星罗棋布的黑点疵病称为夹杂。它是由 星罗棋布的黑点疵病称为夹杂 带钢在酸洗后表面出现深陷的星罗棋布的黑点疵病称为夹杂。它是由 于热轧时氧化铁皮被压入 形成的。这样的缺陷不可能采取酸洗 轧时氧化铁皮被压入所 的缺陷不可能采取酸洗法除 于热轧时氧化铁皮被压入所形成的。这样的缺陷不可能采取酸洗法除 轧后, 点便扩 延伸呈黑色条 去。当它经过冷轧后,黑点便扩展延伸呈黑色条状,大大降低了成品 钢板的冲击性能。 冲击性能 钢板的冲击性能。
6. 酸洗段经常出现的缺陷
(1)酸洗气泡 ) 酸洗气泡产生的机理是:金属和酸产生化学反应时, 酸洗气泡产生的机理是:金属和酸产生化学反应时,生成了部分氢 原子,它渗透到金属的结晶格子中,并使其变形, 原子,它渗透到金属的结晶格子中,并使其变形,变形后使氢更向 金属内扩散,其中一部分氢原子穿过金属并分子化,从酸液中逸出, 金属内扩散,其中一部分氢原子穿过金属并分子化,从酸液中逸出, 部分氢原子的分子化在晶格变形产生的“显微空孔”边界上, 部分氢原子的分子化在晶格变形产生的“显微空孔”边界上,或金 属的夹杂及孔隙中进行,氢在空孔中的压力可达到很大值( 属的夹杂及孔隙中进行,氢在空孔中的压力可达到很大值(几十兆 使金属中产生了引起氢脆的内应力。 帕),使金属中产生了引起氢脆的内应力。 防止产生气泡的措施是:调整酸液的浓度; 防止产生气泡的措施是:调整酸液的浓度;控制酸洗时溶液的温度 和带钢表面平直状态等。 和带钢表面平直状态等。
冷轧酸洗钢板表面黑斑缺陷分析

spot of ST13 hot rolled Biblioteka nd ST13 cold rolled
pickled steel sheet
S Tl3 热轧原板表面氧化铁皮其主要成分为 Fe3 O4 和 FeO ,生产现场的 S Tl3 冷轧酸洗板的黑斑缺陷 其主要成分为 Fe3 O4 和 FeO ;冷却试验后的 S Tl3 试 样空白 板 表 面 氧 化 铁 皮 其 主 要 成 分 为 Fe3 O4 和 FeO 。Q195 与 S Tl3 试样有相同的规律 。
Analysis of Surface Black Spots on Cold Rolled Pickled Steel Sheets
HUAN G Xian2qiu , L U Ying , YAN G Da2ke , C H EN Liang
( Technology Center of Wuhan Iro n and Steel Group Co rp . , Wuhan 430080 , China)
·74 ·
钢 铁
第 40 卷
图 2 冷却试验后的 STl3 试样空白板 表面氧化铁皮相组成
Fig. 2 Phase composition of surface oxide scale of ST13 black specimen after cooling
见表 3 。图 2 、表 3 中试样编号所对应的钢种及试验 条件见表 4 。
© 1994-2006 China Academic Journal Electronic Publishing House. All rights reserved.
电镀中酸洗工艺改进措施

电镀中酸洗工艺改进措施电镀产业链上,多道工序需要酸洗,酸洗在不同阶段其目的是不一样的,有的是为了去除氧化皮,有的是为了提高工件表面活性,有的是为了缩小尺寸等。
传统的酸洗工艺繁琐、流程长、成本高、能耗大、污染严重、劳动条件差等,更为可怕的是对钢材内在质量产生很大的危害—氢脆。
为此,改进酸洗工艺,采取防渗氢措施,已成为人们关注的问题。
一、酸洗工艺的改进钢铁表面的锈蚀主要是铁的氧化物和氢氧化物等,清除这些锈蚀主要是酸类组分借助表面活性剂等的协同作用来完成的,其作用过程大致是溶解和剥落。
为克服酸洗带来的缺点,作如下改进:(1)首先降低酸浓度。
一般钢铁件采用30%~35%HC1(质量分数),除去氧化皮的速度快,但耗量大,酸雾重,对基体的过腐蚀也强,难以保证产品质量。
如用低浓度酸洗工艺对降低酸液消耗,改善环境,提高工件表面质量有明显的经济效益和社会效益。
该工艺利用氧化皮的多孔性,在润湿剂的作用下使酸液迅速渗透到基体与氧化皮的界面上发生Fe+2HCl=2FeCl2+H2↑化学反应,利用氢气的机械剥落作用,达到除去氧化皮清洁表面的作用。
由于氧化物在稀酸中的反应缓慢,DS857酸性除垢剂对裸露基体的吸附力强,防止了过腐蚀,降低了酸的无用消耗,同时亦减轻了工件渗氢数量。
(2)其次,利用混合酸液的综合特性。
生产上常用盐酸或硫酸液除锈,但两者的性能各异,若将盐酸与硫酸按适当比例配制成混合液,能兼有两者的功能,既能提高除锈速度,又降低了操作温度。
(3)再次,采用多功能的高效除油除锈剂。
如多功能酸洗除油粉及活化盐等,这是钢铁酸洗工艺的进步。
(4)最后,采用特殊的酸洗工艺。
针对不同工件的形状、用途、采取不同的酸洗工艺,就是说酸洗工艺也应该个性化。
二、防止氢脆的措施酸洗过程的渗氢是一个相当复杂的过程,即涉及腐蚀的共轭步骤,又涉及氢在金属表吸附和析出的以及浸入金属内部的并、串联步骤,还涉及到应力腐蚀的深层次问题。
研究表明,在酸洗条件下,直接进行渗氢的电化学测量是研究酸洗过程渗氢行为的可行方法。
冷轧带钢酸洗工艺缺陷及应对措施分析

冷轧带钢酸洗工艺缺陷及应对措施分析发表时间:2020-04-08T09:01:13.237Z 来源:《基层建设》2019年第31期作者:吴新奇[导读] 摘要:在当下的机械供应生产中将冷轧钢板进行酸洗的主要目的是为了去除冷轧有害原料在钢板表面所存留的氧化铁皮,从而避免由于氧化皮造成生产中轧辊受到一定的影响,来保护冷轧钢板的质量。
日照钢铁有限公司 276800摘要:在当下的机械供应生产中将冷轧钢板进行酸洗的主要目的是为了去除冷轧有害原料在钢板表面所存留的氧化铁皮,从而避免由于氧化皮造成生产中轧辊受到一定的影响,来保护冷轧钢板的质量。
在实际的冷轧带钢生产过程中进行酸洗是非常重要的工序之一,普通的碳钢在通过酸洗、水洗和干燥过后,碳钢表面变会生成银白色或者是灰白色的附着物,这样就会致使在酸洗过程中会由于操作人员的疏忽或者是设备的不良造成冷轧带钢在酸洗过程中出现缺陷。
本文中首先分析了冷轧钢带三洗工艺中存在的缺陷和应对措施,然后对完善冷轧带钢表面酸洗工艺缺陷的新技术进行阐述,来为冷轧带钢酸洗工艺提供一些参考意见。
关键词:冷轧带钢;酸洗工艺;工艺缺陷;应对措施引言:在工业生产中带钢是指对宽度和厚度具有严格限制的钢制品,带钢在常温条件下经过冷轧压制后便会产生塑性变形的效果,同时这种效果在带钢结晶温度下也会出现,通常我们称这种效果为冷轧带钢。
在工业生产中冷轧带钢的生产过程具有简便灵活、少投资、高回报、低风险等特点。
因此在我国目前的经济环境背景下,提高冷轧带钢的生产技术水平可以进一步的促进当前我国工业领域的发展。
但冷轧带钢在酸洗工艺中,可能会由于酸洗工艺制度不完善、设备操作不当等原因造成冷轧带钢出现不同类型的缺陷,通常这些缺陷主要包括酸洗气泡、过酸洗现象、欠酸洗现象、冷轧带钢表面出现锈蚀、冷轧带钢表面出现夹杂等一系列问题。
一、冷轧钢带酸洗工艺中存在的缺陷及对策(1)酸洗工艺中易出现酸洗气泡冷轧带钢在酸洗工艺中最容易出现酸洗气泡,出现这一现象的主要原因是由于在酸洗过程中带钢表面的金属裸露在酸性液体中,这时金属便会与酸性液体发生化学反应从而生成氢气。
电泳漆酸洗法优缺点

电泳漆酸洗法优缺点第一篇:电泳漆酸洗法优缺点电泳漆酸洗法优缺点酸洗是指利用酸溶液去除钢铁表面上的氧化皮和锈蚀物的方法。
一般将制件浸入硫酸等的水溶液,以除去金属表面的氧化物等薄膜。
那么酸洗法有什么优点和缺点呢?优点酸洗后所获得的表面较为平整,光滑,人仅可以降低涂料单耗,而且可以提高对表面平整度要求较高的电泳涂装的外观质量;酸洗时洗液浸透到工件的每个角落,使锈鉵、油污得到比较全面和彻底的清洗,只要选择好了洗液及其相关参数得到良好的控制,处理质量就比较容易获得保证。
一般酸洗液价格都不算很贵,对降低处理成本有利。
酸洗法对电泳涂装属于“湿对湿“处理,可以实现流水作业,这对提高涂装线的机械自动化有生产率极为有利。
不同酸洗液的处理质量受到工件材质及其表面状态的很大影响,如果选择不当,不仅处理质量得不到保证,而且处理成本高,环境污染大;酸洗要求后道水洗很严格,因为酸洗液常用的酸是硫酸或盐酸,酸洗后如清洗不干净,硫酸的残酸,盐酸残留下的氯离子均有很强的腐蚀性,对涂件或设备都留下隐患。
酸洗尾渣PH仍很低,如不经过很好的中和处理就废气,将造成严重的环境污染。
显然,采用酸洗法不仅在处理质量方面还是在提高电泳涂装的质量方面,与物理法比,均具有一定的优势,但也仍存在一些实际问题,需在应用中不断的探索和改进。
本文摘自变宝网-废金属_废塑料_废纸_废品回收_再生资源B2B交易平台网站;第二篇:各类清洗法优缺点的详解各类清洗法优缺点的详解磷化液1.物理清洗法2.化学清洗法3.电子清洗法(电子除垢、防垢)4.静电清洗法(静电防垢、除垢)磷化液物理清洗法是借助于手工工具和机械对各种污类施加外力清除,脱脂剂而不改变污类组分的清洗方法。
即不改变原来的化学分子组分的方法。
①机械清洗法:清洗剂清扫器和刮刀清理法、钻管清洗法、喷丸清洗法。
②水利清洗法:低压水力清洗(低压清洗的压力为196-686千帕,脱脂剂大约2-7公斤力/平方厘米,等于0.2-0.7Mpa)。
酸洗板常见缺陷及控制措施

酸洗板常见缺陷及控制措施1、酸洗产品概述酸洗板带是以热轧钢卷带为原料,经酸洗后,表面质量和使用要求介于热轧板和冷轧板之间的中间产品。
与热轧板相比,酸洗板的优势主要在于:表面质量好、尺寸精度高、表面光洁度的提高、外观效果的增强以及减少用户分散酸洗造成的环境污染。
另外酸洗产品跟热轧产品相比较,由于表面氧化铁皮已经去除,因而焊接较容易,也利于涂油、上漆等表面处理。
一般热轧产品的表面质量等级是FA,酸洗产品是FB,冷轧产品是FB/FC/FD。
酸洗产品可以代替冷轧产品做一些结构件,也就是以热代冷。
2、酸洗板常见缺陷酸洗板在其生产过程中常见的缺陷主要有:氧化铁皮压入、氧斑(表面山水画)、腰折(横折印)、擦划伤、黄斑、欠酸洗、过酸洗等。
(注:缺陷是和标准或协议要求挂钩的,不符合的才叫缺陷,这里为了方便表达,用缺陷来代之某一类形貌。
)2.1 氧化铁皮压入氧化铁皮压入是热轧轧制过程中形成的一种表面缺陷。
经酸洗后,往往呈黑色点状、长条状压入,表面粗糙,一般有手感,且零星或密集出现。
氧化铁皮产生的原因,与多方面因素有关,主要的有以下几个方面:加热炉加热、除鳞过程、轧制工艺、轧辊材质及状态、辊道状态及轧制计划等。
控制措施:优化加热工艺,增加除鳞道次,定期检查维护辊道及轧辊,使轧制线保持良好的状态。
2.2 氧斑(表面山水画缺陷)氧斑缺陷是指热卷表面氧化铁皮洗掉后,留下的点状、线状或凹坑状形貌,目视呈无规律色差斑迹,由于形状类似山水画,所以也叫山水画缺陷。
目视像高低起伏的山峰状深色图案,在带钢板面呈现整体或者局部分布。
其本质上是氧化铁皮斑迹,氧化铁皮斑迹是浮在表面的一层东西,没有手感,可能颜色会深一点、浅一点。
深色部位相对粗糙,电泳后对外观有一定影响,但是不影响使用性能。
氧斑(山水画缺陷)产生原因:该缺陷本质是热轧带钢表面的氧化铁皮未被除净,经随后的轧制被压入基体,在酸洗后凸显出来。
氧斑的控制措施:降低加热炉出钢温度,增加粗轧除鳞道次,同时优化精轧冷却水工艺。
酸洗碳钢软钢氧斑缺陷控制技术

酸洗碳钢软钢氧斑缺陷控制技术潘世华【期刊名称】《金属世界》【年(卷),期】2015(000)006【总页数】4页(P10-13)【作者】潘世华【作者单位】宝钢不锈钢有限公司,上海 200431【正文语种】中文氧化铁皮斑迹(简称氧斑)缺陷俗称“山水画”,也就是带钢在酸洗之后表面出现的类似“山水画”状的斑迹,没有手感,但影响外观。
2011年以前,该缺陷一直为酸洗软钢的主要质量缺陷,通过2011年攻关,采取了控制在炉时间以及确保粗轧除鳞等措施,取得了显著控制效果。
然而,2013年8月份氧斑缺陷突然再次爆发,缺陷率高达18%,并且连续几个月一直居高不下,2013年8—12月,氧斑缺陷发生率平均就高达10%,造成酸洗软钢降级近5000 t,造成了极大的损失,同时还发生了5起以上的质量异议。
通过质量分析排查发现,大批量板坯出现了超标砷(As)元素,于是将氧斑缺陷样板进行检测,发现缺陷处有明显的砷(As)富集现象。
显然,现在的氧斑与以前的氧斑产生原因不同,以前的氧斑仅仅是表面氧化皮没有除尽,现在的氧斑是表面砷(As)元素富集造成。
由于板坯中砷(As)元素的来源与废钢原料关系密切,但目前无法做到全面控制,因此本文将从热轧角度对由于砷(As)元素导致的氧斑缺陷进行解决改善。
含砷氧斑产生的机理解析典型的严重程度含砷氧斑缺陷形貌如图1所示。
从图1可以看出,“As 斑”缺陷部位比较粗糙。
从EDS 能谱分析来看,突出部位的As 含量较高,达2%以上,如图2所示。
以往发现的氧斑缺陷,其产生原因是由于一次氧化铁皮残留、二次氧化铁皮甚至是比较严重的三次氧化铁皮压入带钢表面,经过轧制延伸之后在带钢表面形成的“山水画”状斑迹。
一次氧化铁皮残留导致的氧化铁皮斑迹缺陷相对严重,主要表现为板面条带状或整面发黑的斑迹;二次氧化铁皮残留导致的氧化铁皮斑迹往往表现为整面的、颜色相对较浅的斑迹;严重的三次氧化铁皮残留导致氧化铁皮斑迹类似于二次氧化铁皮残留的状况,但程度较轻,一般用户都能接受。
SWRH82B盘条酸洗黑膜产生原因及解决措施_杨桂瑜

· 14·
金 表2 Table 2
属
制
品
第 39 卷
试验方案和结果
Test program and results 酸洗 酸洗后表面质量 表面辊缝处约 20% 的氧化铁皮未洗净, 表面黑膜较少 表面辊缝处约 20% 的氧化铁皮未洗净, 表面黑膜较少 表面辊缝处约 10% 的氧化铁皮未洗净, 表面黑膜颜色较浅 50% 的氧化铁皮未洗掉, 表面有黑膜, 表面发黑 10% 氧化铁皮没洗掉, 表面有轻微黑膜, 表面灰黑 15% 氧化铁皮没洗掉, 表面有轻微黑膜, 表面灰 25% 氧化铁皮没洗掉, 表面较重黑膜, 表面发黑 表面严重黑膜, 氧化铁皮 20% 未洗净, 表面发黑 表面黑膜严重, 氧化铁皮 30% 未洗净, 表面发黑 J] . Iron and Steel, 2005 ( 5 ) :72 - 74. steel plate[ 评分 3 2 1 5 6 4 7 8 9
试样 1 2 3 4 5 6 7 8 9
ρ( H2 SO4 ) / ( g·L 60 90 120 60 90 120 60 90 120
-1
ρ( FeSO4 ) / ( g·L - 1 ) 70 70 70 140 140 140 200 200 200
酸洗 温度 / ℃ 60 40 50 50 60 40 40 50 60
SWRH82B 盘条酸洗后表面产生的黑膜导致润滑失效, 钢丝直径频繁超差。 从盘条表面氧化铁皮和酸洗
工艺 2 方面进行分析, 给出原因及解决措施:( 1 ) 盘条氧化铁皮组织异常 。把吐丝温度降低到 900 ℃ , 保证相变终 了时的冷却速度, 避免盘条在 570 ℃ 以上停留, 可以消除盘条氧化铁皮缺陷 。( 2 ) 采用正交试验法优化酸洗工艺: H2 SO4 质量浓度 90 ~ 120 g / L, FeSO4 质量浓度不高于 140 g / L, 温度 40 ~ 50 ℃ , 时间 25 ~ 35 min。采用以上措施, 酸 洗后盘条表面黑膜明显减轻, 磷化润滑质量提高, 模具消耗下降。 关键词 SWRH82B 盘条;表面处理;酸洗工艺;氧化铁皮;金相分析;正交优化;控制措施 TG178 中图分类号
分析冷轧酸洗钢板表面黑斑缺陷

分析冷轧酸洗钢板表面黑斑缺陷陈㊀朋(本钢板材股份有限公司冷轧厂㊀辽宁㊀本溪㊀117000)摘㊀要:表面黑斑缺陷是冷轧钢板材料在接受酸洗加工处理过程中极易出现的技术缺陷问题之一,在全面分析现有的生产技术工艺流程,以及技术限制条件前提下,制定和运用适当策略对表面黑斑缺陷问题展开预防和处置干预,能支持冷轧酸洗钢板生产加工技术活动在具体开展过程中,顺利获取到优质且良好的质量控制效果.本文将会围绕冷轧酸洗钢板表面黑斑缺陷论题,展开简要的阐释分析.关键词:冷轧酸洗钢板;表面黑斑缺陷;处理思路;研究分析ʌ中图分类号ɔT G 335.5+6㊀㊀㊀㊀㊀ʌ文献标识码ɔB ㊀㊀㊀㊀㊀ʌ文章编号ɔ1674-3733(2020)04-0211-01㊀㊀运用盐酸针对冷轧钢板材料开展酸洗处理,主要目的在于全面清除覆盖在钢板材料表面的氧化铁皮层,但是在实际化生产加工活动开展过程中,有数量众多的冷轧钢板材料在经由酸洗处理之后,会在外部表面形成黑斑缺陷现象,且这一现象的出现,标志着冷轧钢板材料表面分布的氧化铁皮层厚度较大,继而在接受后续开展的轧机轧制加工处理环节过程中,极易出现氧化铁皮层压入冷轧钢板材料基体的不良结果.因此,在针对冷轧钢板材料开展的酸洗加工过程中,做好对可能发生的材料表面黑斑缺陷问题的预防,以及处置干预工作,是相关技术人员应当致力于完成的基本工作任务之一.1㊀冷轧酸洗钢板表面黑斑缺陷问题的引致原因从材料特性角度展开阐释分析,冷轧原料钢板材料表面通常会分布有一层氧化铁皮结构,其物质成分包含氧化亚铁㊁四氧化三铁,以及三氧化二铁,从物质分布状态角度展开阐释分析,在氧化铁皮结构之中,富氏体仅在靠近冷轧原料钢板材料表面的区域分布,而处在氧化铁皮结构外层位置的四氧化三铁物质和三氧化二铁物质在一般浓度的盐酸溶液之中都具备难溶性特点,与此同时,氧化铁皮结构之中广泛分布着一定数量的裂缝和气孔,盐酸溶液能够经由气孔和裂缝到达冷轧原料钢板材料的富氏体分布层,以及金属材料层表面,继而在富氏体和金属物质逐渐被盐酸溶解处理条件下,降低氧化铁皮结构与冷轧原料钢板材料之间的相互附着力,并且在盐酸溶液与金属材料发生置换反应生成释放氢气条件下,氧化铁皮结构与冷轧原料钢板材料会发生相互分离结果,与此同时,难以被盐酸溶液溶解的四氧化三铁物质和三氧化二铁物质还会被逐渐还原处理成氧化亚铁物质,继而支持氧化铁皮结构成功实现剥离过程.从实际开展的冷轧钢板材料生产加工活动过程角度展开分析,盐酸溶液浓度水平对冷轧钢板材料酸洗加工过程的具体实施程度具备决定性作用.如果在实际开展的酸洗加工技术活动过程中使用的盐酸溶液浓度水平过高,通常会诱导盐酸对冷轧钢板材料的本体部分造成一定程度的腐蚀破坏作用,而如果在实际开展的酸洗加工技术活动过程中使用的盐酸溶液浓度水平过低,则通常会诱导覆盖在冷轧钢板材料表面的氧化铁皮结构,以及富氏体无法实现充分剔除,继而诱导冷轧钢板材料发生以表面黑斑为代表的技术缺陷问题.从冷轧钢板材料酸洗加工环节的具体实施过程角度展开阐释分析,冷轧钢板材料的运行速度对酸洗加工处理过程实际获取的质量水平具备深刻的影响制约作用,在酸洗加工过程中运用的盐酸溶液浓度保持不变条件下,如果冷轧钢板材料的运行速度参数过快,则势必会诱导分布在冷轧钢板材料表面的氧化亚铁物资㊁四氧化三铁物质,以及三氧化二铁物质,无法实现与盐酸溶液中有效物质成分的充分接触.反之,如果冷轧钢板材料的运行速度参数过慢,则势必会对冷轧钢板材料的本体部分造成一定程度的腐蚀破坏作用,继而产生以表面黑斑为代表的种类多样的技术缺陷问题.2㊀冷轧酸洗钢板表面黑斑缺陷的处置干预措施第一,关注破鳞机设备对冷轧钢板材料可洗性的影响干预作用.在破鳞机设备实际运行使用过程中,伴随着带钢张紧力参数和辊子压下量参数的持续加大,冷轧钢板材料在接受拉伸应力因素和弯曲应力因素同时作用条件下,其表面分布的氧化铁皮层结构将会不再保持原有的致密均匀状态,而是会有数量越来越多的氧化物质以块状的形式逐渐从冷轧钢板材料的表面发生脱落现象,继而诱导实际对外暴露的铁基体结构部分的总面积持续加大,且通过增大压下量比参数的方式,能有效促进分布在冷轧钢板材料表面的氧化铁皮层结构实现更加充分的脱落过程.第二,合理控制酸洗加工处理过程中的温度参数.通过对现有的冷轧钢板材料酸洗加工技术工艺展开研究分析,不难发现,伴随着盐酸溶液温度参数水平的持续升高,冷轧钢板材料在接受酸洗加工处理过程中的持续时间,将会呈现出持续缩短的变化趋势.实验室数据测算结果显示,对于质量分数为18.00%的盐酸溶液而言,在其温度参数从45.00ħ提升到80.00ħ条件下,其酸洗加工处理过程的持续时间,将会从39.20s 逐渐缩短到22.80s ,其缩短幅度高达58.20%.与此同时,受盐酸物质本身具备的物理特性角度展开分析,伴随着温度参数的持续提升,其挥发程度也会逐渐提升,继而产生大量酸雾,在一定程度上给生产工人的身体健康水平造成不良影响.因此,想要在针对冷轧钢板材料开展的酸洗加工生产活动过程中顺利获取到优质且良好的生产质量和生产效率控制效果,必须在合理设置盐酸溶液的浓度水平前提下,将其温度参数控制在75.00-80.00ħ之间.结束语:表面黑斑缺陷是冷轧酸洗钢板在接受酸洗处理之后最为常见的技术缺陷类型之一,在全面考量分析冷轧酸洗钢板材料的生产加工工艺流程,以及技术性限制条件前提下,制定和运用适当措施对冷轧酸洗钢板表面黑斑缺陷问题展开预防,以及处置干预,能获取较好效果,支持冷轧酸洗钢板材料在生产加工制备过程中获取到最优化的质量控制状态.参考文献[1]㊀周鹏,崔珊.430不锈钢1.8mm 冷轧退火酸洗板折弯开裂的原因分析及工艺改进[J ].特殊钢,2019,40(06):51-54.[2]㊀李玉峰,阮强,陈安忠,潘吉祥.退火工艺对C r -M n -N i -N 奥氏体不锈钢组织和力学性能的影响[J ].热加工工艺,2019,48(22):155-158.[3]㊀李娜,刘船行,赵有明,刘天纬.冷轧硅钢浅槽紊流酸洗工艺改进及质量控制[J ].江西冶金,2018,38(06):23-26.[4]㊀周鹏,苗高蕾,惠恺,臧涛.双相钢冷轧酸洗板表面黑色条带缺陷成因分析[J ].铸造技术,2018,39(12):2869-2872.[5]㊀刘传鹏,颜廷洲,白雪,李亮亮,郑利元,齐杰斌.冷轧硅钢热处理线酸洗控制系统设计[J ].冶金设备,2018(05):37-39+57.112 2020年1月㊀第4期写真地理科学与技术。
冷轧厂酸洗工艺段常见表面缺陷及预防

冷轧厂酸洗工艺段常见表面缺陷及预防摘要:冷轧钢板酸洗的目的是为了去除带钢在生产过程中表面产生的氧化铁皮。
防止在后续加工工艺中氧化铁皮对轧件造成的损坏。
如果未将氧化铁皮清洗干净,则会造成一系列的工艺段表面缺陷,本文简要介绍了酸洗板产生的表面缺陷产生的原因以及如何纠正预防缺陷的发生。
关键词:酸洗线;酸洗;缺陷引言目前,为了提高国内钢材生产企业的生产能力,国内生产基地都采用酸洗-冷轧联合机组的设计,联合机组的采用能使工厂年产量达到百万吨以上。
其中酸洗阶段的主要任务是洗掉带钢表面的氧化铁,为冷轧工艺阶段提供合适的加工材料。
所以,维护好酸洗工艺段的设备对于整个加工过程都有重要意义。
1.酸洗工艺质量缺陷酸洗工艺缺陷主要包括:(1)工艺控制不当造成的缺陷:欠酸洗、过酸洗、停车斑;(2)机械作用造成的缺陷:擦划伤、边丝和毛边、卷边、折皱、缝合;(3)其它水印、边锈、漏涂等。
2.工艺控制不当造成的缺陷及预防纠正措施2.1欠酸洗欠酸洗是带钢表面氧化铁皮与盐酸反应不充分仍残留在带钢表面,其主要成分是Fe304,Fe0。
缺陷特征及判定方法:带钢表面有条纹状或鳞片状黑印.用纸巾擦拭有粘附现象。
多出现于带钢的边部和头尾部,严重时遍布整个带钢表面。
造成的主要原因:酸液的浓度、温度低,酸洗速度过快,或Fe2+浓度过高;另外原料板形、热轧卷取温度等因素也可产生欠酸洗。
边部欠酸洗的产生原因有两方面:1.热轧时带钢边部冷却较快达到570℃以下:Fe0-4Fe304+Fe并能长时间保持在400-500℃,形成致密的Fe304保护层,给酸洗造成了较大的困难。
2.板形不好导致峰部与酸接触时间短,出现欠酸洗。
头尾部欠酸洗是因为带刚尾部在酸槽垂度太小,酸洗时间不够。
纠正预防措施:首先降低运行速度,到出口活套坑处跟踪观察质量;其次适当将6#槽酸液温度升高1-2℃;进一步查看各酸槽自由酸浓度和Fe2+浓度,如有必要,修改注酸系数,增加注酸量。
另外操作工要及时按产品的不同规格控制酸洗时间。
【解决方案】镀镍层常出现“暗黑斑点”
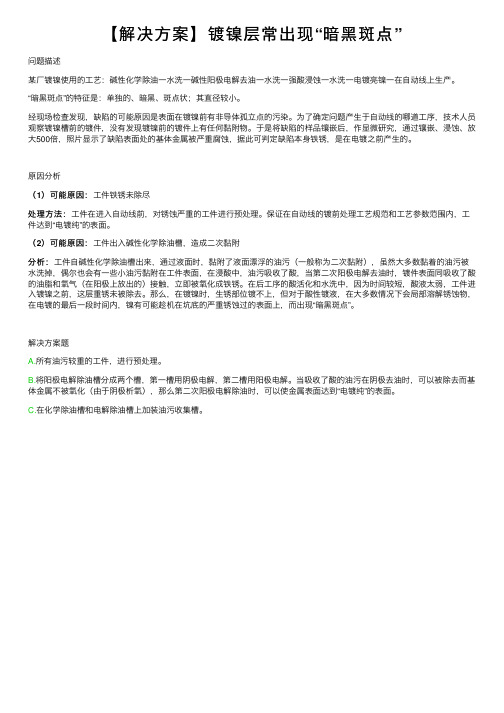
【解决⽅案】镀镍层常出现“暗⿊斑点”问题描述某⼚镀镍使⽤的⼯艺:碱性化学除油⼀⽔洗⼀碱性阳极电解去油⼀⽔洗⼀强酸浸蚀⼀⽔洗⼀电镀亮镍⼀在⾃动线上⽣产。
“暗⿊斑点”的特征是:单独的、暗⿊、斑点状;其直径较⼩。
经现场检查发现,缺陷的可能原因是表⾯在镀镍前有⾮导体孤⽴点的污染。
为了确定问题产⽣于⾃动线的哪道⼯序,技术⼈员观察镀镍槽前的镀件,没有发现镀镍前的镀件上有任何黏附物。
于是将缺陷的样品镶嵌后,作显微研究,通过镶嵌、浸蚀、放⼤500倍,照⽚显⽰了缺陷表⾯处的基体⾦属被严重腐蚀,据此可判定缺陷本⾝铁锈,是在电镀之前产⽣的。
原因分析)可能原因:⼯件铁锈未除尽(1)可能原因:处理⽅法:⼯件在进⼊⾃动线前,对锈蚀严重的⼯件进⾏预处理。
保证在⾃动线的镀前处理⼯艺规范和⼯艺参数范围内,⼯处理⽅法:件达到“电镀纯”的表⾯。
(2)可能原因:)可能原因:⼯件出⼊碱性化学除油槽,造成⼆次黏附分析:⼯件⾃碱性化学除油槽出来,通过液⾯时,黏附了液⾯漂浮的油污(⼀般称为⼆次黏附),虽然⼤多数黏着的油污被分析:⽔洗掉,偶尔也会有⼀些⼩油污黏附在⼯件表⾯,在浸酸中,油污吸收了酸,当第⼆次阳极电解去油时,镀件表⾯同吸收了酸的油脂和氧⽓(在阳极上放出的)接触,⽴即被氧化成铁锈。
在后⼯序的酸活化和⽔洗中,因为时间较短,酸液太弱,⼯件进⼊镀镍之前,这层重锈未被除去。
那么,在镀镍时,⽣锈部位镀不上,但对于酸性镀液,在⼤多数情况下会局部溶解锈蚀物,在电镀的最后⼀段时间内,镍有可能趁机在坑底的严重锈蚀过的表⾯上,⽽出现“暗⿊斑点”。
解决⽅案题A.所有油污较重的⼯件,进⾏预处理。
B.将阳极电解除油槽分成两个槽,第⼀槽⽤阴极电解,第⼆槽⽤阳极电解。
当吸收了酸的油污在阴极去油时,可以被除去⽽基体⾦属不被氧化(由于阴极析氧),那么第⼆次阳极电解除油时,可以使⾦属表⾯达到“电镀纯”的表⾯。
C.在化学除油槽和电解除油槽上加装油污收集槽。
- 1、下载文档前请自行甄别文档内容的完整性,平台不提供额外的编辑、内容补充、找答案等附加服务。
- 2、"仅部分预览"的文档,不可在线预览部分如存在完整性等问题,可反馈申请退款(可完整预览的文档不适用该条件!)。
- 3、如文档侵犯您的权益,请联系客服反馈,我们会尽快为您处理(人工客服工作时间:9:00-18:30)。
是
8
是
9
否
六、要因确认
纠偏影响
设备因素
活套影响
设备因素
破鳞机、挤干辊 的使用
酸洗工艺影响
酸洗速度
酸槽内洁净程度
换辊等原因造成 的停车
七、改善对策
要因1、活套、纠偏的影响 对策 由于生产宽度1500mm以上规格,纠偏报警
生产宽规格 添加缓蚀剂
频繁,导致酸洗工艺段频繁降速、停车,酸
洗后带钢表面质量无法得到保证,产生大量 的停车斑。为减少此情况造成的影响,我们
通过统计,发现黑斑处粗糙度明显高于停车斑缺陷。
三、现状调查
在确认了黑斑产生机理后,我们对2015年12月份后工序反馈回来的 黑斑缺陷与酸轧生产实际进行了一一对应(部分缺陷带钢):
缺陷 名称 5Y9763 停车 0 斑 钢卷号 5Y9663 黑斑 4
√ √ 200 220
七、改善对策
要因5:破鳞机、挤干辊使用不规范
通长结构的氧化铁皮经破碎者较未经破碎
对策
者的酸洗时间缩短了40%。破鳞机使用不当, 造成带钢表面氧化铁皮疏松情况不好,影响
破鳞机与 挤干辊使 用规范
酸洗效果。挤干辊若挤干效果不好,不但会
造成酸液、漂洗水串液,破坏酸循环区域成 分,而且会造成带钢出干燥风机后带液,造
300吨
100吨
攻关前黑斑重量/月
攻关后黑斑重量/月
四、目标设定
可行性分析
为验证我们制定的目标的合理性,我们对比了邯钢与马钢罩退产 品,每月黑斑重量及所占比例: 企业 唐钢 邯钢 马钢 罩退黑斑每月重量 300 80 110 占缺陷比例 88% 42% 65%
通过对比发现其余钢厂在黑斑缺陷控制上要好于我 们。在设备情况差不多的情况下,我们认为我们也有能力 实现黑斑缺陷月均100吨以下的目标。
6Y03880
3*1267
否
七、改善对策
对比添加缓蚀剂前后酸洗工艺段速度10m/min的板面效 果:
未添加缓蚀剂
成本计算:
添加缓蚀剂
7-11月共计生产宽度1500mm以上规格19.60万吨,缓蚀剂消耗
7000kg,吨钢成本2.2元。
七、改善对策
要因2:酸洗工艺段停车斑 对策
通过分析入口、中间活套大小,以及酸洗
一、选题背景
281 吨 294 吨 314 吨
提升酸洗后带钢 表面质量,减少 因酸洗原因产生 的黑斑缺陷
2015.10
2015.11
2015.12
8.43
8.82
9.42
2015.10
2015.11
2015.12
课题选择
二、小组简介
小组名称 课题名称 活动周期 成员 组长 姓名 王俊伟 性别 男 黑斑缺陷攻关小组 降低因酸洗原因产生的黑 斑缺陷 小组类型 成立时间 攻关型 2015年12月
固定入口活套地表螺丝, 酸洗工艺段速度 带钢板面黑斑 10~20m/min,短暂停车 轧机断带
带钢正反两面 黑斑 3.5*125 TYH 0 有大面积黑带 停车 SPCC5Y97064 斑 4*1250 带钢表面停车斑 1
来料变宽度,切边剪调 整宽度
通过柏拉图可以得出酸轧黑斑主要由过酸洗、酸洗后可见黑斑、点
是
是
六、要因确认
序号
末端因素
确认过程
是否要因
7
二酸洗通过清洗酸罐内油泥,带钢表面的点状黑斑 酸槽内油泥影 明显减少,一酸酸罐内油泥也较多,因此认为清理 响 油泥对减少带钢表面点状黑斑有显著效果。
带钢在酸洗之前往往经过破磷机反复弯曲变形,消 弱了氧化铁皮与金属本体铁的附着力和完整程度, 破鳞机、挤干 将有许多碎粒从金属表面上破碎脱落下来,从而加 辊影响 速了酸洗过程。因此破鳞机对提升酸洗效果有着显 著影响。挤干辊对酸液浓度稳定、减少带液有着极 为重要的作用。 操作工操作因 虽然4个班组在操作习惯上存在一定差距,但是对 素 酸洗工艺影响较小
工艺段长度,制定了酸洗工艺段停车倒车要
酸洗工艺 段停车后 需倒车
求:停车前必须保证中间活套套量充裕,使
得起车前酸洗段能够有15%以上套量进行倒
车,保证酸洗槽内所有带钢都可以倒离酸洗 段,通过二次酸洗停车斑缺陷来减弱停车斑
造成的影响。
同时,如果原料厚度、长度允许,尽量使 停车斑存在于带钢的头尾,后道工序方便切
决定在生产宽度1500mm以上规格时添加缓蚀
剂。添加方式为生产宽度1500mm以上规格前6 小时开始添加,缓蚀剂添加计量泵开度70%。
七、改善对策
1.21日添加缓蚀剂后带钢生产情况
钢卷号 6Y03240 生产 时间 6分 规格 过酸洗 欠酸洗 否 备注 轧机换辊停车卷
3*1524 过酸洗 轻微过 酸洗 否
状黑斑、换辊停车斑构成。
四、目标设定
月份 项目 2015.10 2015.11 2015.12 平均值
后工序反馈的黑斑缺陷量(吨)
281
294
314
296
课题成立时,黑斑缺陷有逐月增多趋势,月平均值在300吨左右。以厂部制定 的废次降硬性指标作为攻关目标,即产量的0.01%约为170~180吨每月,小组通过 讨论,觉得有能力将黑斑缺陷降低至100吨每月以下,因此将目标定制在100吨/月。
钢卷号 生 产 时 间 20 分 规格 过酸洗 带钢表面 发黑,产 生停车斑 欠酸洗 备注
6Y03864
3*1267
否
轧机断带,酸洗工艺段降速至 10~20m/min,后短暂停车
6Y03870
11 分
4分
3*1267
较严重停 车斑
否
否
轧机换辊,酸洗工艺段停车
正常生产未降速,酸洗工艺段 240m/min
二、小组简介
活
1月1日-1 月15日 1月15日1月31日
时间 步骤 确定目标 P 现状调查 要因确认
动
2月
日
3月
程
3-11月 12月
制定对策
D C A 对策实施 效果检验
巩固措施
活动总结
三、现状调查
对酸轧2015.10-12月废次降进行统计: 黑斑 黑斑 9-11月(吨) 占比 889 88.19%
6Y03262
14分
3*1524
否
纠偏报警,酸洗工艺段停车2分 正常生产未降速,酸洗工艺段 200m/min 固定入口活套地表螺丝,酸洗工艺 段速度10~20m/min,短暂停车
6Y03264
5分
3*1524
否
6Y03285
10分
3*1524
否
否
七、改善对策
2016.1.22日未添加缓蚀剂带钢过酸洗欠酸洗生产情况
否
5
6
通过观察生产实际,目前制定的酸洗速度 240m/min时常造成带钢板面欠酸洗,同时由于速 酸洗速度的影 度过快造成入口活套量不足,造成酸洗速度 响 (20m/min以下)过慢,会造成板面发黑,产生过 酸洗,罩退重卷后产生黑斑。 换辊等停车影 由于换辊原因造成的酸洗段停车,产生的停车斑在 响 经过罩退平整后,会产生黑斑缺陷。
及对带钢表面进行粗糙度测试。
三、现状调查
1、电镜分析。 通过电镜分析,带钢中间或边部黑斑得出了确切结论。下图为电镜扫描结果。
扫描电镜图片
三、现状调查
黑斑电镜扫描能普图
三、现状调查
2、粗糙度检测。 下表为我们对整板面黑斑进行的粗糙度测试结果。 钢卷号 5Y97630 5Y97630 5Y97630 5Y97630 5Y98213 黑斑处粗糙度 1.12 1.23 1.18 1.15 1.20 同卷板面正常处 粗糙度 0.83 0.81 0.92 0.87 0.90 两者比较(正常 与黑斑处差值) 0.29 0.42 0.26 0.28 0.30
现是由于酸槽内油泥过多导致,因此提议对
一酸酸槽内油泥也进行定期清理。 课题组讨论决定以检修为清理周期,清理
酸罐内油泥,2月11日的清理中,发现油泥的
确非常严重,打开酸槽盖时发现带钢表面已 经被污染。
七、改善对策
2016.1.21日清理前
2016.10.23酸轧检修打开槽盖
通过对比,可以清楚的发现,在实施清洁生产项后,酸洗槽内带钢表 面油泥明显减少。现在我们已经将清洁生产项纳入操作规程,以检修为周 期对酸槽内油泥进行清理。
七、改善对策
要因4:酸洗工艺段速度不合理 对策
通关对比精整黑斑与酸洗工艺,我们发现当酸
规范酸洗 速度
洗工艺段速度降低至20m/min以下时,带钢表面会 发生过酸洗现象,在重卷会出现黑斑。 小组认为现行的酸洗速度过快,导致入口活套 量不足,造成酸洗工艺速度波动过大,经常有速度 过低的情况发生。针对这一情况,我们对酸洗工艺 速度进行了规范,从实施来看,效果较好,酸洗速
2006年1~12月 行政职务 冷轧部技术员 文化程度 本科
组员
小 组 成 员 组员 组员 组员 组员 组员 组员
吴旻
黄超 郭世忠 于海涛 王瑛琳 马德刚 王蕾
男
男 男 男 男 男 男
冷轧部技术员
冷轧部技术员 酸轧作业区作业长 酸轧作业区见习作业长 冷轧厂技术员 酸轧作业区主操 冷轧部技术员
本科
本科 本科 本科 本科 本科 本科
7%
各类缺陷占比 切边不净 切边不净 辊印 64 2%
3%
辊印 尺寸超差 34 3.37%
尺寸超差 21 2.08%
7.2%
88%
通过图表统计,可以清晰的反映出黑斑缺陷是酸轧作业区产生 的最主要的缺陷。
三、现状调查
精整作业区反馈黑斑主要有以下两种形貌:
板面中间或边部黑斑
整板面黑斑,板面发污
为调查黑斑产生机理,我们先后对黑斑进行取样电镜分析以