简述抗滑桩施工工艺及要求
抗滑桩施工工艺原理及流程简介
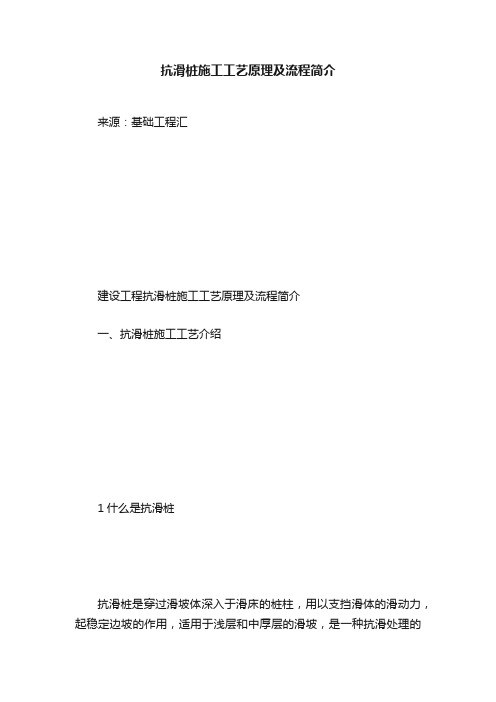
抗滑桩施工工艺原理及流程简介来源:基础工程汇建设工程抗滑桩施工工艺原理及流程简介一、抗滑桩施工工艺介绍1什么是抗滑桩抗滑桩是穿过滑坡体深入于滑床的桩柱,用以支挡滑体的滑动力,起稳定边坡的作用,适用于浅层和中厚层的滑坡,是一种抗滑处理的主要措施。
使用抗滑桩,土方量小,施工需有配套机械设备,工期短,是广泛采用的一种抗滑措施。
2抗滑桩的作用抗滑桩对滑坡体的作用是利用抗滑桩插入滑动面以下的稳定地层对桩的抗力(锚固力)平衡滑动体的推力,增加其稳定性。
当滑坡体下滑时受到抗滑桩的阻抗,使桩前滑体达到稳定状态。
根据滑体的厚薄、推力大小、防水要求及施工条件等选用木桩、钢桩、混凝土及钢筋混凝土桩。
抗滑桩埋入地层以下深度,按一般经验,软质岩层中锚固深度为设计桩长的三分之一;硬质岩中为设计桩长的四分之一;土质滑床中为设计桩长的二分之一。
当土层沿基岩面滑动时,锚固深度也有采用桩径的2~5倍。
抗滑桩的布置形式有相互连接的桩排,互相间隔的桩排,下部间隔、顶部连接的桩排,互相间隔的锚固桩等。
桩柱间距一般取桩径的3~5倍,以保证滑动土体不在桩间滑出为原则。
二、抗滑桩施工工艺流程1旋挖桩施工工艺流程图2施工现场准备工作(1)、施工平台填筑后,通过导线控制点,用全站仪坐标放样法来确定桩位,埋设护桩。
护桩埋设在钻孔桩纵、横轴方向,护桩距护筒边200㎝。
施工测量按铁路施工测量等有关要求执行,施工测量必须有两人相互校核并作出测量和校核记录。
(2)、钢护筒埋设,桩位放样完成后开挖基坑、埋设护筒,护筒周围用粘土夯填,护筒平面偏位控制在5cm,护筒底端的埋置深度为1.5m,护筒顶面高出地面0.4m。
护筒埋设时由护桩校核护筒位置,并严格控制护筒垂直度,垂直度为0.5%。
(3)、钻机就位,护筒埋设结束后进行钻机就位,钻机摆放平稳,钻机摆放就位后,要对机具及机座稳固性等进行全面检查,用水平尺检查钻机摆放是否水平,在钻锥下悬挂垂球,并利用交叉护桩检查钻机摆放是否正确。
抗滑桩工程施工工法规定

抗滑桩工程施工工法规定一、引言抗滑桩是指为了防止基础结构在地震、风、浪等自然因素作用下发生倾覆或滑动,而设置的一种工程结构。
抗滑桩主要用于桥梁、隧道、港口、码头、水利工程等基础工程中,以增加基础结构的稳定性和安全性。
以下将介绍抗滑桩工程的施工工法。
二、施工前准备1. 工程测量:施工前应进行精确的测量,确定抗滑桩的位置、深度和尺寸。
2. 基坑开挖:根据设计要求,开挖抗滑桩基坑,并清除基坑内的杂物和泥土,保持基坑干燥。
3. 材料准备:准备好所需的抗滑桩材料,如钢筋、混凝土、支撑材料等。
4. 安全措施:在施工现场设置必要的安全警示标识和安全防护设施,确保施工人员和周围环境的安全。
三、抗滑桩施工工法1. 钻孔首先,在基坑内布置好辅助桩承台,根据设计要求确定抗滑桩的位置和数量,采用旋挖钻机或冲击器进行钻孔。
在钻孔过程中,要及时清除孔内泥浆,确保孔壁的平整和清洁。
根据设计要求设置好孔径和孔深。
2. 筋笼安装将预先制作好的抗滑桩筋笼通过吊装设备放入钻孔中,保证筋笼的中心线与孔中心线一致,并用支撑设备固定筋笼。
然后,再在筋笼内灌入混凝土,并采取合适的振捣措施确保混凝土的密实性。
3. 抗滑桩外露部分处理当混凝土固化后,进行外露部分的处理,根据设计要求进行锥削、加固或防腐等处理,以保证抗滑桩的使用寿命和稳定性。
4. 支撑材料清除待抗滑桩完全固化后,清除基坑内的支撑材料和其他杂物,将基坑整理干净,并按设计要求对基坑进行防水和排水处理。
四、施工质量控制1. 材料质量:抗滑桩材料应符合国家标准和设计要求,各类材料应经过质量检测合格后方可使用。
2. 施工工艺:施工过程应按照设计要求和规范操作,及时清理基坑内的泥浆和杂物,并确保孔壁的平整和清洁。
3. 安全防护:施工现场应设置必要的安全警示标识和防护设施,严格执行安全操作规程,确保施工人员和周围环境的安全。
4. 施工记录:施工过程应认真记录各项施工数据和质量验收结果,形成完整的施工记录,以备将来查阅。
抗滑桩实施细则

抗滑桩实施细则一、引言抗滑桩是一种用于增加土体抗滑稳定性的地基处理方法。
本文将详细介绍抗滑桩的实施细则,包括设计要求、施工步骤、质量控制等方面的内容。
二、设计要求1. 抗滑桩的设计应符合相关国家规范和标准,确保工程的安全可靠。
2. 设计人员应充分考虑地质条件、荷载特点等因素,确定合适的桩径、桩长和桩间距。
3. 抗滑桩的布置应满足土体稳定性要求,确保抗滑桩的整体效果。
三、施工步骤1. 前期准备a. 确定施工范围,并进行现场勘察,了解地质情况和地下设施。
b. 制定详细的施工方案,包括施工方法、设备选用、安全措施等。
c. 聘请合格的施工队伍,并进行必要的培训。
2. 施工准备a. 按照设计要求,准备好所需的材料和设备。
b. 清理施工现场,确保施工区域的平整和清洁。
c. 搭建必要的施工临时设施,如施工平台、安全围栏等。
3. 桩基施工a. 根据设计要求,选用合适的施工方法,如钻孔灌注桩、钻孔钢筋混凝土桩等。
b. 进行桩基的钻孔或挖掘工作。
c. 在钻孔或挖掘中及时检查土层情况,确保桩基施工的质量。
d. 在钻孔或挖掘完成后,根据设计要求进行桩基灌注或钢筋布置。
4. 桩身处理a. 对已完成的桩基进行必要的处理,如打磨、修整等。
b. 检查桩身的垂直度和水平度,确保符合设计要求。
5. 质量控制a. 在施工过程中,进行必要的质量检查和监控,如桩基质量、桩身垂直度等。
b. 对施工过程中出现的问题及时处理,确保施工质量。
6. 施工记录和验收a. 记录施工过程中的关键节点和重要数据。
b. 完成施工后,进行抗滑桩的验收工作,确保符合设计要求和规范标准。
四、安全措施1. 施工现场应设置明显的警示标志,并配备必要的安全设施,如安全帽、安全绳等。
2. 施工人员应接受必要的安全培训,并遵守相关安全规定。
3. 施工过程中应注意土方坍塌、设备故障等安全风险,并及时采取措施进行防范和应对。
五、总结抗滑桩的实施细则包括设计要求、施工步骤、质量控制和安全措施等方面的内容。
抗滑桩施工工艺

抗滑桩施工工艺抗滑桩是防治滑坡的一种工程建筑物,是六十年代后铁路建设逐步采用和发展起来的一项防治滑坡的重大技术革新,该技术具有施工简便,效果突出的特点。
1 工艺特点(1)施工工艺比较简单。
(2)可操作性较强。
(3)机械装备程度较底。
(4)技术含量要求不高等特点。
2 实用范围(1)实用于铁路工程、公路工程、水利工程滑坡、古滑坡的病害整治。
(2)自然灾害(地震、泥石流、暴雨)所造成的山体滑坡的病害整治工程。
3 工艺原理及设计要求3。
1 工艺原理抗滑桩通常为钢筋混凝土或钢轨混凝土桩体,抗滑桩的分类根据滑坡体的规模大小分为单排抗滑桩及多排抗滑桩,单排抗滑桩通常设置于滑坡前沿且与桩间墙相连接形成整体,桩间墙通常为两种,一种是预制钢筋混凝土板,另一种是浆砌片石挡土墙.作用机理:抗滑桩由锚固段及抗滑段组成,锚固段是保证桩体的自身稳定性,抗滑段主要承担滑坡土体的下滑力,它的作用是阻止滑坡体沿着一定的软弱结构面(带)产生剪切位移而整体地向斜坡下方移动,承担滑坡体的整体下滑力,从而达到增强山体滑坡的稳定性及滑坡整治加固的目的.3。
2 工艺设计要求3。
2。
1 抗滑桩的设计原则上要满足以下几点:(1)桩间土体在下滑力作用下,不能从桩间挤出去,通过控制桩间的距离来进行控制,处理措施通常为桩间钢筋混凝土挡土板或桩间浆砌片石挡土墙两种。
(2)桩后土体在下滑力作用下不能产生新滑面自桩顶滑出,要进行越顶检算,通过桩高来控制.(3)桩身要有足够的稳定度,在下滑力的作用下不会倾覆,通过锚固桩深度来控制。
(4)桩身要有足够的强度,在下滑力的作用下不会破坏,对桩进行配筋来满足。
3.2。
2 抗滑桩的直径和间距抗滑桩水平截面长(a)、宽(b)和间距(d):抗滑桩通常设计为矩形,抗滑桩的间距通常为抗滑面边长的2倍,其水平截面长、宽和间距取值见表1。
表1 抗滑桩水平截面长、宽和间距取值注:抗滑桩水平截面长(a)、宽(b)和间距(d)的取值与滑坡体的地质情况有关。
简述抗滑桩施工工艺及要求
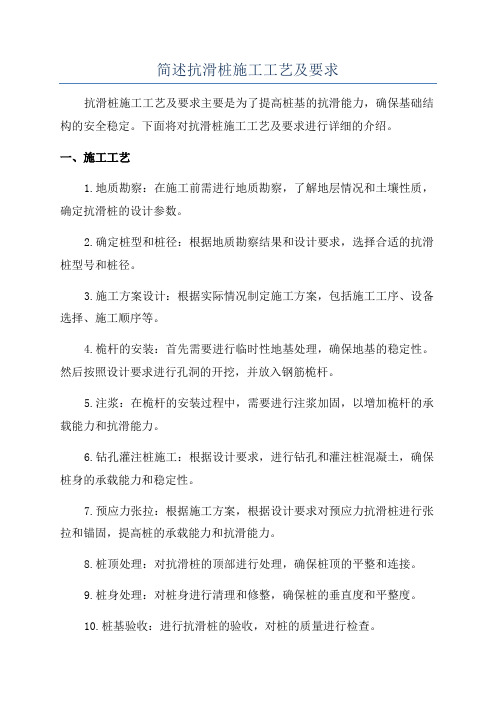
简述抗滑桩施工工艺及要求抗滑桩施工工艺及要求主要是为了提高桩基的抗滑能力,确保基础结构的安全稳定。
下面将对抗滑桩施工工艺及要求进行详细的介绍。
一、施工工艺1.地质勘察:在施工前需进行地质勘察,了解地层情况和土壤性质,确定抗滑桩的设计参数。
2.确定桩型和桩径:根据地质勘察结果和设计要求,选择合适的抗滑桩型号和桩径。
3.施工方案设计:根据实际情况制定施工方案,包括施工工序、设备选择、施工顺序等。
4.桅杆的安装:首先需要进行临时性地基处理,确保地基的稳定性。
然后按照设计要求进行孔洞的开挖,并放入钢筋桅杆。
5.注浆:在桅杆的安装过程中,需要进行注浆加固,以增加桅杆的承载能力和抗滑能力。
6.钻孔灌注桩施工:根据设计要求,进行钻孔和灌注桩混凝土,确保桩身的承载能力和稳定性。
7.预应力张拉:根据施工方案,根据设计要求对预应力抗滑桩进行张拉和锚固,提高桩的承载能力和抗滑能力。
8.桩顶处理:对抗滑桩的顶部进行处理,确保桩顶的平整和连接。
9.桩身处理:对桩身进行清理和修整,确保桩的垂直度和平整度。
10.桩基验收:进行抗滑桩的验收,对桩的质量进行检查。
二、施工要求1.施工计划:根据工程进度和施工条件制定合理的施工计划。
2.施工记录:详细记录施工过程中的关键数据和质量控制数据,以备后期检查和评定。
3.施工现场管理:严格按照规定的施工顺序进行操作,严禁违规操作。
4.施工设备和材料:选择合适的施工设备和材料,确保施工质量。
5.施工人员:施工人员应具备相关岗位的工作经验和技术资格证书,按照规定进行操作。
6.质量控制:进行严格的质量控制,检测桩的垂直度、平整度和承载能力等指标。
7.环境保护:施工过程中应注意环境保护,避免土壤和水体的污染。
8.安全措施:施工过程中应严格遵守安全规章制度,做好安全防护工作。
9.预应力设施:预应力抗滑桩施工前需检查预应力设施的安装情况,确保正常运转。
10.桩基检测:施工完成后需对抗滑桩进行检测,确保桩基的质量和稳定性。
抗滑桩实施细则

抗滑桩实施细则一、背景介绍抗滑桩是一种用于加固土壤、提高地基承载力的工程技术。
在建筑和土木工程中,抗滑桩的应用非常广泛,特别是在软土地区或需要加固边坡、挡土墙等结构时。
本文将详细介绍抗滑桩实施的细则,包括设计要求、施工方案、材料要求等内容。
二、设计要求1. 工程地质勘察:在进行抗滑桩实施前,必须进行详细的工程地质勘察,了解地质条件、土壤性质、地下水位等信息,以便确定合适的抗滑桩方案。
2. 荷载计算:根据工程的荷载要求,计算出所需的桩长、桩径和桩间距等参数,确保抗滑桩能够承受设计荷载。
3. 施工工艺:根据设计要求,确定抗滑桩的施工工艺,包括桩身的钻孔、灌注桩混凝土、桩顶的护筒等。
三、施工方案1. 桩基础施工:根据设计要求,选择合适的施工方法,如钻孔灌注桩、静压灌注桩等。
在施工过程中,必须确保桩孔的垂直度和直径的准确度,避免桩身出现变形或偏斜。
2. 混凝土灌注:在桩孔完成后,进行混凝土灌注。
混凝土的配合比应符合相关标准,并在灌注过程中保持连续性和均匀性,确保桩体的强度和稳定性。
3. 桩顶处理:根据设计要求,在桩顶设置护筒或连接板,以便与上部结构连接。
护筒或连接板的安装应牢固可靠,确保桩顶的稳定性。
四、材料要求1. 钢筋:采用符合国家标准的高强度钢筋,具有良好的抗拉强度和耐腐蚀性能。
2. 混凝土:采用符合国家标准的混凝土材料,具有合适的强度和流动性,以确保桩体的稳定性和耐久性。
3. 护筒或连接板:采用符合国家标准的钢材或混凝土材料制作,具有足够的强度和刚度,能够承受上部结构的荷载。
五、施工质量控制1. 施工现场管理:确保施工现场的整洁有序,材料的储存和使用符合规范,施工人员必须按照施工方案进行操作,严禁违章施工。
2. 施工质量检测:对抗滑桩的施工质量进行检测,包括桩孔的垂直度、直径的准确度、混凝土的强度等。
必要时,可委托第三方进行质量检测。
3. 施工记录和档案:对抗滑桩的施工过程进行详细记录,包括施工日期、施工人员、材料使用情况等,并建立相应的施工档案,以备后续参考和追溯。
抗滑桩施工工艺
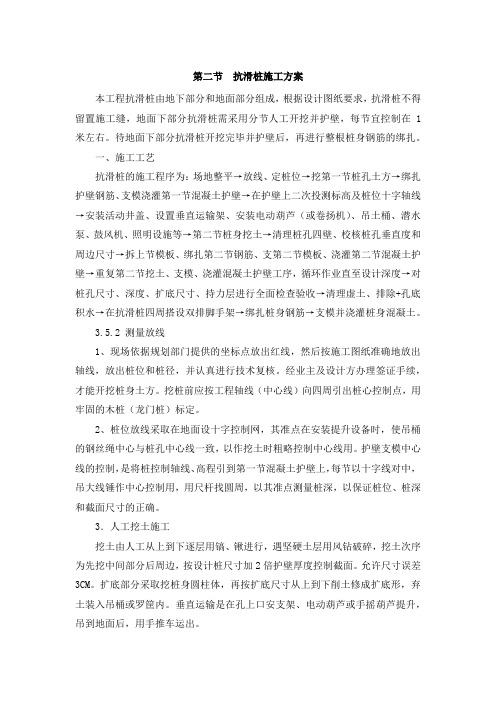
第二节抗滑桩施工方案本工程抗滑桩由地下部分和地面部分组成,根据设计图纸要求,抗滑桩不得留置施工缝,地面下部分抗滑桩需采用分节人工开挖并护壁,每节宜控制在1米左右。
待地面下部分抗滑桩开挖完毕并护壁后,再进行整根桩身钢筋的绑扎。
一、施工工艺抗滑桩的施工程序为:场地整平→放线、定桩位→挖第一节桩孔土方→绑扎护壁钢筋、支模浇灌第一节混凝土护壁→在护壁上二次投测标高及桩位十字轴线→安装活动井盖、设置垂直运输架、安装电动葫芦(或卷扬机)、吊土桶、潜水泵、鼓风机、照明设施等→第二节桩身挖土→清理桩孔四壁、校核桩孔垂直度和周边尺寸→拆上节模板、绑扎第二节钢筋、支第二节模板、浇灌第二节混凝土护壁→重复第二节挖土、支模、浇灌混凝土护壁工序,循环作业直至设计深度→对桩孔尺寸、深度、扩底尺寸、持力层进行全面检查验收→清理虚土、排除+孔底积水→在抗滑桩四周搭设双排脚手架→绑扎桩身钢筋→支模并浇灌桩身混凝土。
3.5.2 测量放线1、现场依据规划部门提供的坐标点放出红线,然后按施工图纸准确地放出轴线,放出桩位和桩径,并认真进行技术复核。
经业主及设计方办理签证手续,才能开挖桩身土方。
挖桩前应按工程轴线(中心线)向四周引出桩心控制点,用牢固的木桩(龙门桩)标定。
2、桩位放线采取在地面设十字控制网,其准点在安装提升设备时,使吊桶的钢丝绳中心与桩孔中心线一致,以作挖土时粗略控制中心线用。
护壁支模中心线的控制,是将桩控制轴线、高程引到第一节混凝土护壁上,每节以十字线对中,吊大线锤作中心控制用,用尺杆找圆周,以其准点测量桩深,以保证桩位、桩深和截面尺寸的正确。
3.人工挖土施工挖土由人工从上到下逐层用镐、锹进行,遇坚硬土层用风钻破碎,挖土次序为先挖中间部分后周边,按设计桩尺寸加2倍护壁厚度控制截面。
允许尺寸误差3CM。
扩底部分采取挖桩身圆柱体,再按扩底尺寸从上到下削土修成扩底形,弃土装入吊桶或罗筐内。
垂直运输是在孔上口安支架、电动葫芦或手摇葫芦提升,吊到地面后,用手推车运出。
抗滑桩施工工艺

一、抗滑桩施工抗滑桩施工时应隔桩开挖,作好护壁,杜绝爆破。
尽量选在旱季施工,作好地表排水工作。
抗滑桩的成孔方法和要求如下:1、开挖过程中及时进行地质编录,以利于反馈设计。
2、抗滑桩施工工序:施工准备→桩孔开挖→地下水处理→护壁→钢筋笼制作与安装→混凝土灌注→混凝土养护3、施工准备应按下列要求进行:⑴、按工程要求备料,选用材料的型号、规格符合设计要求,有产品合格证和质检单;⑵、钢筋应专门建库堆放,避免污染和锈蚀;⑶、使用普通硅酸盐水泥;⑷、砂石料的杂质和有机质的含量应符合《混凝土结构工程施工验收规程》〔GB50204-92〕的有关规定。
4、成孔采用人工开挖,并按下列原则进行:⑴、开挖前应平整孔口,并做好施工区的地表截、排水及防渗工作。
雨季施工时,孔口应加筑适当高度的围堰。
⑵、采用间隔式开挖,每次间隔1~2孔。
⑶、按由浅到深、由两侧向中间的顺序施工。
⑷、松散段原则上以人工开挖为主,孔口做锁口处理,桩身作护壁处理。
基岩或坚硬孤石段可采用少药量、多炮眼的松动爆破方式,但每次剥离厚度不宜大于30cm。
开挖基本成型后再人工刻凿孔壁至设计尺寸。
⑸、根据岩土体的自稳性、可能日生产进度和摸板高度,经过计算确定一次开挖深度。
一般自稳性较好的可塑-硬塑状粘性土、稍密以上的碎石土或基岩中为 1.0~1.2m;软弱的粘性土或松散的、易垮塌的碎石土层为0.5~0.6m;垮塌严重段宜先注浆后开挖。
⑹、每开挖一段及时进行岩性编录,仔细滑面(带)情况,综合分析研究,如实际位置与设计有较大出入时,应将发现异常及时向建设单位和设计单位报告,及时变更设计。
实挖桩底高程应会同设计、勘查等单位现场确定。
⑺、弃渣可用卷扬机吊起。
吊斗的活门应有双套防开保险装置。
吊出后应立即运走,不得堆放在边坡上,防止诱发次灾害。
5、桩孔开挖过程中应及时排除孔内积水。
6、桩孔开挖过程中应及时进行钢筋混凝土护壁,宜采用C20砼。
护壁的单次高度根据一次最大开挖深度确定,一般每开挖1.0~1.5m,护壁一节。
- 1、下载文档前请自行甄别文档内容的完整性,平台不提供额外的编辑、内容补充、找答案等附加服务。
- 2、"仅部分预览"的文档,不可在线预览部分如存在完整性等问题,可反馈申请退款(可完整预览的文档不适用该条件!)。
- 3、如文档侵犯您的权益,请联系客服反馈,我们会尽快为您处理(人工客服工作时间:9:00-18:30)。
简述抗滑桩施工工艺及要求作者:孙兵单位:中铁二十局集团第二工程有限公司一、工程概述:该滑坡位于拟建高速公路(K8+226~K8+280)段所通过的黄土沟壑地貌区。
该滑坡体长182 米,宽242 米,钻探揭露厚度约11.5~17.8 米,体积约58 万立方,属于大型滑坡,滑坡物质主要由黄土状构成,属牵引式黄土滑坡。
据勘察资料及现场情况,以“安全、耐久、节约、和谐”的原则,经综合考虑,采用综合措施治理,布置抗滑桩。
该抗滑桩布置于一级平台,共计5根。
桩径采用2.0*1.5m,桩长为17m,桩身采用C25钢筋混凝土。
二、施工顺序:1 、设置滑坡地表位移检测系统;2、夯实滑坡体裂缝;3、测量布置抗滑桩桩位;4、坡脚回填反压,以确保抗滑桩施工期间坡体稳定;5、清除松散滑体,并分段开挖坡面;6、坡顶截水沟施工,坡面绿化。
三、施工流程:平整场地、桩位放样、首次孔桩开挖1 米深、护壁钢筋、模型安装、灌注护壁混凝土、护壁混凝土强度》5MPa护壁模型拆除、向孔中注入新鲜空气、孔桩开挖每1米浇筑护壁混凝土、完成开挖、安制桩身钢筋、浇筑桩身混凝土、养护四、施工方法:1、先按设计图放出桩背坡度宽度、坡率、及平台位置,用挖掘机配合汽车对该段边坡进行开挖,开挖面内高外低,以便排水;2、挖至桩顶平台时,对抗滑桩场地进行平整,定出桩开挖区域、堆料场、钢筋加工场、施工便道,进行架电作业,搞好电线布置;3、人工挖孔及护壁施工:①测量定位:施工人员必须按图施工,工程开工前根据设计提供的现场坐标点测放轴线,放出的定位线测放所有的桩位,同时做好各轴线的控制桩,桩位的放样允许偏差为10mm经监理复核验收并办理有关手续后,方可进行开挖;②标定中点:挖孔前,以放好的桩位中心点向桩的四周按轴线方向,弓I出桩心控制点,待锁口浇筑好后,将中心控制点标定在锁口上,以后每放一节都用大线锤吊中,找桩中心及轴线控制点,在开挖桩工作面定出桩轴线,确保桩径不小于设计要求,桩轴线偏差不大于规范值;每浇筑完三节护壁,需校核垂直度一次,垂直度偏差不小于0.5 ,并做好记录;③挖桩:在填土层、淤泥层、黏土层用短柄铁锹、锄头挖土施工;进入砂岩层用风镐施工;如遇坚石风镐难以施工的,采用钻爆施工。
④运输:每孔桩原地面挖下150cm后,即在桩孔上架立垂直运输支架,用卷扬机作为运土设备;⑤护壁施工:护壁混凝土采用人工浇筑、人工振捣的方法,塌落度控制在8-10cm,原地面下第一节灌注锁口,其下挖深1米就灌注C20钢筋混凝土护壁一节,往下施工以每一节为一施工循环,护壁厚度为0.25m,在节与节之间插竖直钢筋(入下节25cm),护壁模板采用拆上节、支下节重复周转使用,模板之间用卡具、扣件连接固定,在上下端各设一道圆弧形的角钢作为内侧支撑。
护壁混凝土浇筑8小时后方可进行拆模工作,灌注混凝土未达到设计强度的80%前,不得拆除模板顶撑,每节最后收口时要在四周模板顶部留一缺口,待拆模后用干硬砼填塞抹平。
⑥夜间施工时要保证用电,施工场地周围架好照明灯,孔内照明用电采用36V安全电压,孔内照明灯泡采用专用灯罩防护,以防止其碰撞时破裂;⑦第一节锁口钢筋砼高出原地面20cm,孔口上搭设防护棚,孔口周围设防护栏,挖排水沟。
⑧检查:成孔后对桩身尺寸、孔底标高、桩位中线、井型垂直度进行全面测定,做好施工记录,经监理及有关质检人员共同检查鉴定,符合设计要求并验收合格后,再制作、吊放钢筋笼、浇筑砼。
⑨当遇到流泥、流砂时,护壁施工按下列方法:a,做到快速施工,并减少护壁高度(50cm~100cn),采用上述方法仍无法施工时,应迅速用砂回填桩孔到能控制塌孔为止,并通报有关设计、监理、质检及现场技术部门研究处理;b,对易塌方施工段应即挖、即验收、即浇筑护壁混凝土;⑩孔桩护壁须满足下列要求:a, 护壁的厚度,搭接筋的配备,砼必须符合设计要求;b, 孔桩开孔后,应尽快浇筑护壁砼,且当天需一次性浇筑完毕;c,发现护壁有蜂窝、漏水现象,应及时加以堵塞或导流。
4、抗滑桩孔内爆破:为确保施工安全,孔内爆破应注意:①导火线起爆须有工人迅速离孔的设备,导火线应做燃烧速度试验,据以决定导火线所需长度,孔深超过10米时采用电引爆;②必须打炮眼放炮,严禁裸露药包,对于软岩石炮眼深度不得超过0.8 米,对于硬岩石炮眼深度不超过0.5 米,炮眼数目、位置和斜插方向,应按岩层断面方向来定,中间一组集中掏心,四周斜插挖边;③严格控制药量,以松动为主,一般中间炮眼装硝铵炸药1/2 节,边眼装药1/3~1/4 节;④有水眼孔要用防水炸药,尽量避免瞎炮,如有瞎炮要按安全规程办理⑤炮眼附件的支撑应加固,以免支撑炸坏引起塌孔;⑥孔内放炮后须迅速排烟,可采用电动鼓风机放入孔底吹风等措施;⑦终孔检查处理:挖孔达到设计标高后,应进行孔底处理,必须做到平整、无松渣、污泥及沉渣,嵌入岩层深度应符合设计要求,开挖过程中应经常检查了解地质情况,如与设计资料不符,应提出变更设计;⑧抗滑桩炮眼布置根据实际情况。
5、钢筋笼制作:①施工前确保使用的设备机具状态良好,所使用钢筋材料必须有试验报告;②钢筋加工时主筋搭接位置应错开。
35d且不小于500mm范围内接头数目不得超过总受力钢筋面积的50%主筋焊接必须保证搭接长度不小于规范值,纵向主筋在桩顶以下2m内不设接头,水平加力筋必须和纵筋点焊成牢固钢筋笼,保证钢筋笼不变形、不扭转;③箍筋与主筋间采用22号铁丝全部进行绑扎,绑扎需牢固,适当加以点焊;④根据工期及现场实际情况,采用孔外人工绑扎钢筋笼。
钢筋笼数量、规格、尺寸及绑扎等按设计及规范施工,施工完毕后报监理单位验收,待验收合格后方可进行混凝土灌注;⑤钢筋在加工场地加工好后用人工搬运、安放至孔内。
由钢筋工按设计图定位,控制各钢筋笼间距、数量、长度,绑好保护层垫块,确保保护层厚度,然后进行绑扎焊接,成型后采取有效措施,固定好钢筋笼。
在同一圈可用3~5个300~500mm长$ 18钢筋,一端焊接在加力筋上,一端顶在护壁上,以防钢筋笼在灌注过程中发生位置偏移现象。
6、桩身混凝土灌注:①严格按设计要求施工,挖至设计标高,桩基成孔后,认真清理浮渣,抽净积水,经自检合格后请监理单位验收,验收合格后方可进行灌注混凝土;②桩身砼灌注前,落实现场各作业班组、质检员、值班人员职责,并做好桩身混凝土灌注记录;③浇筑前认真检查机具工作状态,所用处理符合要求;④浇筑采用干式浇筑法:在砼浇筑过程中,采用串筒。
保证串筒端部距离砼的浇筑面不大于2m,防止粗骨料与水泥砂浆离散,出现离析现象。
桩身砼每下料0.5米左右,用插入式振动器振捣一次,保证砼的密实度;⑤浇筑过程中,扩大部分每1 米振捣一次,振动棒振点间距0.4~0.5m ,每点振捣时间不少于20 秒,振动棒插入砼面不小于1 米,桩身部分每1.2 米振捣一次。
振捣程度以砼面不再明显沉落和无气泡溢出为限。
振捣由专业人员穿、戴安全防护品并有二人在孔口护送下孔进行作业;⑥桩身砼必须连续浇筑,不得留设施工缝。
浇筑完成后,24 小时内用水养护,灌注砼时,做好砼试块,认真养护,达到龄期后送检。
五、质量保证措施:1、技术措施:①施工过程中的系统检查、签证工作是工程质量的保证,签证前要认真进行自检,合格后方可填写检查证并报请监理工程师会同检查签认;②桩孔采用人工挖孔,抗滑桩应由两侧向中间靠,跳桩开挖施工;③精确测定桩位,根据桩位中心十字交叉放出护桩;④检查桩孔净空尺寸和平面位置,使孔的中线误差、截面尺寸、孔口平面位置满足设计要求;⑤上下节护壁的搭接长度不得小于50mm每节护壁均应在当日连续施工完毕。
护壁砼必须保证密实,根据土层渗水情况使用速凝剂,护壁拆模宜在24h 后进行。
桩身钢筋的接头,按钢筋设计图进行;⑥孔内砼一次性连续浇筑,不得中途停顿。
桩孔灌注完成后及时进行桩顶砼养护;⑦人工挖孔桩挖出的弃土,应堆砌在指定地点,挖桩弃土在抗滑桩施工完成前不应外运; ⑧严格控制钢筋的加工质量, 加强对加工后的钢筋的存放管理, 保证钢筋的绑 扎和焊接质量。
2、管理措施:①实行三级质检责任制和质量奖罚制;②施工过程中实行全工序控制,严格监理程序; ③优化施工方案, 使施工作业程序化和标准化; ④通过合理的组织与正确的 施工方法, 尽快形成生产能力, 提高施工进度, 保持稳定生产, 使施工作业程序化和标准化。
六、安全、文明及环保措施:1、安全措施:①安全管理实行三级检查责任制,即:现场安全员自查自纠、 行监督检查,随时整改,安全工程师实行巡视监督、检查、验收;②施工现场应有明显的安全标志,危险地区必须悬挂“危险”、“禁止通行” “严禁烟火”等标志,夜间设红灯示警;③ 施工所用机具和劳动保护用品定期进行检查和必要的试验, 态,不合格的机具设备和劳动保护用品严禁使用; ④ 孔内必须设置应急软梯,供人员上下井,使用的电葫芦、吊笼等安全可靠,并配有自 动卡保险装置,不得使用麻绳和尼龙绳吊挂或脚踏井壁凸缘上下,电葫芦宜用按钮式开关, 使用前必须检验其安全起吊能力;⑤ 用吊斗出土时,应设有信号指挥,土斗上应栓溜绳,装土或卸土后应将斗门关好,吊机扒杆和土斗下面严禁站人;⑥ 孔口四周必须设置护栏,一般加 0.8米高围栏围护,挖出的土石方应及时运离孔口,不得堆放在孔口四周 1 米范围内,机动车辆的通行,不得对井壁的安全造成影响;⑦ 混凝土灌注平台的减速漏斗, 应以吊具固定在平台方木或钢件上, 不得用扒钉或铁丝 栓挂,减速漏斗外边的缝隙,应以木板封闭,漏斗串筒之挂钩、吊环均应牢固可靠,悬挂之 串筒应有保险钢丝绳;⑧ 施工现场所有电设备, 除作保护接零外, 必须在设备负荷线的首端处加设两极漏电保 护装置,遇到跳闸时,应查明原因,排除故障后再进行合闸;⑨ 每个操作平台应悬挂安全操作规程,操作人员必须严格按程序操作, 道路出入口、 重要安全装置等处要悬挂安全警告标志;⑩ 配电箱开关要分开设置, 必须坚持一机一闸用电, 并采用两极漏电保护装置; 配电箱、 开关箱必须安装牢固,电具齐全完好,注意防尘、防湿; (11)各种电器应配有专用开关, 室外使用的开关、插座应外装防水箱并加锁, 在操作处加 设绝缘垫层; (12)各种电气设备的检查维修, 一般应停电作业;如必须带电作业时,应有可靠的安全措施并派专人监护; (13) 每个操作平台应悬挂安全操作规程, 操作人员必须严格按程序操专职安全员跟班旁站,实 保证其经常处于良好的状作。
道路出入口、重要安全装置等处要悬挂安全警告标志;(14) 清除一切可能造成的火灾、爆炸事故的根源,严格控制火源、易燃、易爆和助燃物;(15) 工地现场、料场派专人24小时轮班看守,防止生活物品、材料被盗及其他事故的发生。
2、环境保护措施:①施工中采取一切可靠合理措施,保护施工现场内外的环境,避免由于施工机械操作等引起的粉尘、有害气体、噪音等对环境的污染;②采用可靠的措施,保护原有交通的正常通行和维持沿线村镇的居民饮水、农田灌溉、生产生活用电及通讯管线的正常使用。