纺纱原理与设备的后加工工序.
纺织工程中的纺纱工艺流程

纺织工程中的纺纱工艺流程一、纱线的定义和分类在纺织工程中,纱线是制成织物的基本原材料。
根据生产用途和规格不同,可以将纱线分为棉纱、毛纱、化纤纱和混纺纱等多种类型。
其中,棉纱是最为普遍的一种纱线。
二、棉纱的生产流程1. 筛选棉花棉纱的生产首先需要筛选棉花,这一步是确保生产质量的关键环节。
选购的棉花需要杂质较少,纤维细长饱满,色泽均匀,手感柔软。
2. 梳棉梳棉是纺织工程中的一个重要工艺,主要是使粗糙的棉纤维经过梳理之后,变得柔软光滑。
经过梳棉后,棉纤维变得整齐,方便后续的制作工序。
3. 纤维成条经过梳棉之后,棉纤维需要进行成条,这一步是为了使纤维在后续加工中能够顺畅地被拉伸。
成条的过程需要将梳理过的棉纤维进行整形,使其形成带状状的纱条。
4. 纱条拉伸纱条拉伸是棉纱生产中的重要环节,其目的是使成条的棉纤维变得更为细长、柔软,便于后续加工。
拉伸过程需要使用细钢丝将纱条挂在纺机上,慢慢地通过细钢丝拉动纱条,使之逐渐变细。
5. 纱锭纺纱纱锭纺纱是棉纱生产中的最后一步工序,也是将成品纺织面料所需的纱线制成的关键工艺。
纺纱工序通常采用纱锭纺法,通过对细长的棉纤维进行拉伸、捻合操作,使其形成一根长长的纱线。
三、棉纱的质量控制棉纱生产过程中需要严格控制产品的质量,确保其符合生产要求。
其中,棉纱质量的控制可以从以下几个方面进行考虑:1. 原料的选购:棉花成分、纤维长度、强度等都会影响制成的纱线的质量,因此在选购原料时需要严格把关。
2. 工艺的控制:每个生产环节都需要控制好温度、湿度等参数,严格遵守纺织工艺规范。
3. 质量检测:对于每批生产出来的棉纱都需要进行质量检测,确保其符合标准,避免产品质量问题对后续生产所带来的影响。
四、纱线的应用范围棉纱作为纺织品的基本原材料,广泛应用于制作各种面料、服装、家居用品等。
在日常生活中,我们可以看到很多纯棉面料的衣物、被套、床单等。
此外,棉纱还可用于制作纺织工业中的各种绳索和索具等。
纺纱原理及设备和后加工工序共41页

16、自己选择的路、跪着也要把它走 完。 17、一般情况下)不想三年以后的事, 只想现 在的事 。现在 有成就 ,以后 才能更 辉煌。
18、敢于向黑暗宣战的人,心里必须 充满光 明。 19、学习的关键--重复。
20、懦弱的人只会裹足不前,莽撞的 人只能 引为烧 身,只 有真正 勇敢的 人才能 所向披 靡。
41、学问是异常珍贵的东西,从任何源泉吸 收都不可耻。——阿卜·日·法拉兹
42、只有在人群中间,才能认识自 己。——德国
43、重复别人所说的话,只需要教育; 而要挑战别人所说的话,则需要头脑。—— 玛丽·佩蒂博恩·普尔
44、卓越的人一大优点是:在不利与艰 难的遭遇里百折不饶。——贝多芬
45、自己的饭量自己知道。——苏联
பைடு நூலகம்
纺纱学简要回顾。doc

第一章绪论1、纺纱基本原理(松解、集合、开松、梳理、牵伸、加捻、除杂、精梳、混和、卷绕)P1~2页及PPT教案。
2、纺纱工程包含的工序①初步加工工序:原棉的轧棉;原毛开洗烘及含草多时炭化;麻类纤维脱胶;绢纺中的精练以去除丝胶、油脂等。
②梳理前准备工序:棉纺即开清棉工程,制成棉卷(定量单位为克/米)或均匀的棉流。
使用机台为开清棉联合机。
毛纺即和毛。
使用机台即和毛机。
麻纺即精干麻→机械软麻→给湿加油→分磅堆仓→开松③梳理工序:棉纺盖板梳理机,制成生条(定量单位克/5米);毛、麻、绢纺用罗拉梳理机。
④精梳工序:对棉纺而言,是精梳前准备工序(制精梳小卷)+精梳机(制精梳棉条)的统称。
⑤并条(针梳)工序:制半熟条、熟条。
涉及并合原理、牵伸原理、混和原理(涤棉混纺纱采用棉条混和)。
⑥粗纱工序:制粗纱(定量单位为克/10米)。
⑦细纱工序:制细纱(定量单位为克/100米)。
⑧后加工工序:络筒、并纱、捻线、烧毛、上蜡、丝光等。
3、棉纺纺纱系统(普梳系统、精梳系统、废纺系统:与普梳系统相比,无并条工序)化纤与棉混纺系统(精梳系统:棉要经过精梳、涤要经过预并、然后三道混并普梳系统:棉不需精梳但要经过预并、涤要经过预并、然后三道混并)第二章纤维原料初加工与选配1、轧棉机分类、轧棉质量判断(三观察:外观变化、长度变化、皮辊棉黄根的多少及锯齿棉疵点的多少)。
2、棉包质量的标识方法(P9页。
类型代号、品级代号、长度代号、马克隆值代号)。
3、“三丝”定义,三丝含量分档(“无、低、中、高”四档)。
4、含糖棉的处理方法。
5、乳化洗毛原理及工艺流程。
(P12~13页)6、炭化原理。
7、麻纤维脱胶基本原理(微生物脱胶、化学脱胶)。
Chapter3 原料的选配与混合配棉定义:棉纺厂将几种唛头、地区或批号的原棉,按比例搭配使用的方法。
1.配棉目的或意义(能满足不同纱线的质量要求、能保持生产过程和成纱质量的相对稳定、多唛混纺,混和批量大,混和棉的性能差异也较单一品种间的原棉性能差异为小,因而采用混和棉纺纱既可增加投产批量,又能在较长时期内保持原棉性能的稳定,确保生产过程和成纱质量的相对稳定、能节约原棉和降低成本)3.原棉主要性能(长度、短绒、细度等)与成纱强力、条干间关系。
新大纺纱学讲义第9章 后加工

第九章后加工第一节概述用原棉和各种化纤作原料经多道工序纺成的细纱,还需要经过后加工工序,以满足对成纱各品种不同的要求。
后加工工序包括络筒、并纱、捻线、烧毛、摇纱、成包等加工过程。
根据需要可选用部分或全部加工工序。
一、后加工工序的任务1.改善产品的外观质量细纱机纺成的不同品种管纱中,仍含有一定的疵点、杂质、粗细节等,后加工工序可以清除较大的疵点、杂质、粗细节等。
为使股线光滑、圆润,有的捻线机上装有水槽还可进行湿捻加工。
有的高级股线还要经过烧毛除去表面毛羽,改善纱线光泽。
对纱线要求光滑的产品可进行上蜡处理。
2.改善产品的内在性能股线加工能改变纱线结构,从而改变其内在性能。
不同的单纱经一次或两次合股加捻,采用不同生产工艺过程,可达到改善纱线物理性能的目的,如强力、耐磨性、条干、光泽、手感等。
花式捻线还能使纱线结构、形式发生改变,形成环、圈、结、点、节以及不同颜色、不同粗细等具有特殊效果的异形纱线。
3.稳定产品结构状态经过不同的后加工工序,可以达到稳定纱线的捻回和均匀股线中单纱张力。
如纱线捻回不稳定,易引起“扭结”、“小辫子”、“纬缩”等疵点。
对捻回稳定性要求高或高捻的纱线,有时要经过湿热定型。
如股线中各根单纱张力不匀,会引起股线的“包芯”结构,导致股线强力、弹性和伸长率下降。
4.制成适当的卷装形式为了满足后道工序加工的需要,要将纱线制成不同的卷装形式。
卷装形式必须满足卷装容量大,易于高速退绕,且适合后续加工,便于贮存和运输。
二、后加工的工艺流程根据产品要求、用途不同,有不同的后加工工序。
1.单纱的工艺流程筒子包管纱→络筒摇纱→成包2.股纱的工艺流程管纱直接并纱并纱→线筒→摇纱→成包3.较高档股线的工艺流程管纱→络筒→并纱→捻线→线筒→烧毛→摇纱→成包根据需要,可进行一次烧毛或两次烧毛。
需定型时,一般在单纱络筒后或股线线筒后进行。
4.缆线的工艺流程所谓“缆线”是经过一次以上并捻的多股线。
第一次捻线工序称为初捻,第二次捻线工序称为复捻。
纺纱工程八个工序的总结

纺纱工程八个工序的总结要将纺织原料纺成符合一定性能要求的纱,除了以上述纺纱原理为基础外,还需要应用各种相应的技术手段,并经过一系列加工过程才能实现。
把纺织纤维制成纱线的过程称为纺纱工程,它由下列若干子工程或工序组成,而上述的纺纱原理就贯穿于这些工序之中。
1.初步加工工序纺织原料特别是天然纺织原料,因为自然环境、生产条件、收集方式和原料种类本身的特点,除可纺纤维外还含有多类杂质,而这些杂质必须在纺纱前加以去除,这个过程即为初步加工工程。
各种纺织原料初步加工工程随原料不同而异。
(1)从棉田中采摘下来的棉铃除了棉纤维外,还含有棉籽及其他杂质,在进行下道加工前必须用轧棉机排除棉籽,制成无籽的皮棉,故棉的初步加工称为轧棉。
轧棉在轧棉厂里完成,轧下来的皮棉(原棉)经检验打成紧包后,运输到棉纺厂进行后续加工。
(2)毛纺工厂使用的原料是从羊身上剪下来的羊毛(原毛)。
原毛含有油脂、汗液、粪尿以及草刺、沙土等杂质,必须在原毛初步加工(俗称开洗烘工程)中清除。
除杂时,首先将压得很紧的纤维进行开松,去除原毛中易于除去的杂质如砂土、羊粪等,然后用机械和化学相结合的方法去除羊毛中的油脂、羊汗及黏附的杂质。
有的羊毛如散毛含草杂较多时,还需经过炭化,即利用化学和机械方法除去净毛中所含的植物性杂质,所用的设备为开洗烘联合机和散毛炭化联合机,得到的半制品分别为洗净毛、炭净毛。
(3)从茎秆上剥下来的麻皮(又称原麻)中除含有纤维素外,还含有一些胶质和杂质,它们大多包围在纤维表面,使纤维粘在一起,为了确保纺纱过程的顺利和纱线质量,这些非纤维杂质必须在成纱前全部或部分除去,这部分初步加工在麻纺厂称为脱胶。
苎麻原麻经过脱胶后得到的半制品叫做精干麻。
(4)绢丝原料是养蚕、制丝和丝织业的疵茧和废丝,其中含有丝胶,油脂,泥沙污杂物和其他杂质。
这些杂质必须在纺纱前用化学、生物等方法去除,这种初步加工在绢纺中称为精练工程,制得较为洁净疏松的半制品叫做精干绵。
纺纱的原理

纺纱是将天然纤维或化学纤维通过机械或化学方法加工成纱线的过程。
纺纱原理主要是通过机械力或化学力将纤维材料拉伸、变形、交织,使其成为连续的纱线。
纺纱的原理可以简单概括为以下几个步骤:
1. 纤维材料的准备:将天然纤维或化学纤维进行处理,使其变得柔软、均匀、有弹性,以便后续处理。
2. 开清:将纤维材料切成小块,去除杂质和短纤维,使其更加均匀。
3. 加捻:将纤维材料通过加捻机进行加捻,使其形成一个长条状的纤维束,以便后续的拉伸和变形。
4. 拉伸:将纤维束通过拉伸机进行拉伸,使其长度增加,同时纤维的直径变细,从而提高纱线的强度和密度。
5. 并合:将拉伸后的纤维束通过并合机进行并合,使其形成一个更加均匀的纱线。
6. 梳理:将并合后的纱线通过梳理机进行梳理,使其纤维排列更加整齐,同时去除杂质和短纤维,使纱线更加纯净。
7. 纺纱:最后,将梳理后的纱线通过纺纱机进行纺纱,形成连续的纱线。
以上是纺纱的基本原理,不同的纤维材料和纱线类型可能需要不同的加工方法和设备,但总体原理是相似的。
纺纱工艺设计
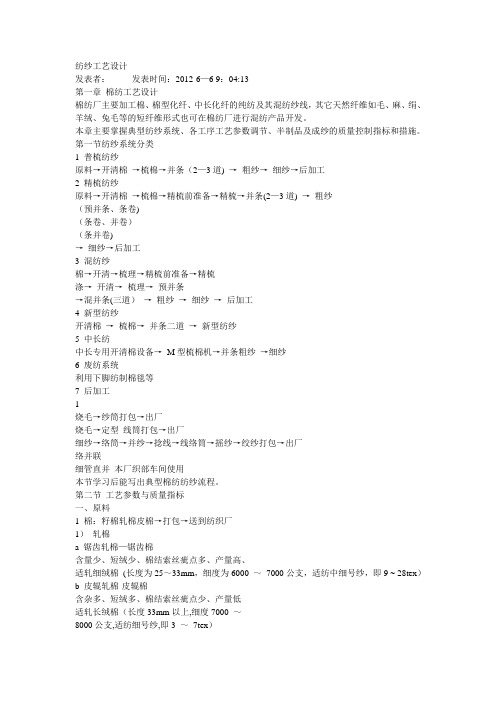
纺纱工艺设计发表者:发表时间:2012-6—6 9:04:13第一章棉纺工艺设计棉纺厂主要加工棉、棉型化纤、中长化纤的纯纺及其混纺纱线,其它天然纤维如毛、麻、绢、羊绒、兔毛等的短纤维形式也可在棉纺厂进行混纺产品开发。
本章主要掌握典型纺纱系统、各工序工艺参数调节、半制品及成纱的质量控制指标和措施。
第一节纺纱系统分类1 普梳纺纱原料→开清棉→梳棉→并条(2—3道) →粗纱→细纱→后加工2 精梳纺纱原料→开清棉→梳棉→精梳前准备→精梳→并条(2—3道) →粗纱(预并条、条卷)(条卷、并卷)(条并卷)→细纱→后加工3 混纺纱棉→开清→梳理→精梳前准备→精梳涤→开清→梳理→预并条→混并条(三道)→粗纱→细纱→后加工4 新型纺纱开清棉→梳棉→并条二道→新型纺纱5 中长纺中长专用开清棉设备→M型梳棉机→并条粗纱→细纱6 废纺系统利用下脚纺制棉毯等7 后加工1烧毛→纱筒打包→出厂烧毛→定型线筒打包→出厂细纱→络筒→并纱→捻线→线络筒→摇纱→绞纱打包→出厂络并联细管直并本厂织部车间使用本节学习后能写出典型棉纺纺纱流程。
第二节工艺参数与质量指标一、原料1 棉:籽棉轧棉皮棉→打包→送到纺织厂1)轧棉a 锯齿轧棉—锯齿棉含量少、短绒少、棉结索丝疵点多、产量高、适轧细绒棉(长度为25~33mm,细度为6000 ~7000公支,适纺中细号纱,即9 ~ 28tex)b 皮辊轧棉-皮辊棉含杂多、短绒多、棉结索丝疵点少、产量低适轧长绒棉(长度33mm以上,细度7000 ~8000公支,适纺细号纱,即3 ~7tex)2)打包规格:例国内包100*42*60cm 体积v=0.25m³密度300 ~ 360kg/m³G=75 ~90kg2、化纤1)品种粘胶莫代尔丽赛天丝2涤纶腈纶锦纶维纶丙纶)芳纶聚乳酸等2)型式长度(mm)细度(旦)棉型33—38 1。
2—1.5中长型51—76 2-3毛型76-102 3-5生产经验公式:L/D=1 L-英寸,D-旦3)分等及质量指标分等按内在质量和外观疵点分:内在质量:断裂强度、断裂伸长、细度偏差、长度偏差以及超长纤维、倍长纤维等. 外观疵点:粗丝、并丝、异状丝、油污纤维二、配棉简介1、不同种类纱线与原棉性状关系1)棉纱号数细号与中粗号的差别。
纺纱厂工艺流程

纺纱厂工艺流程
《纺纱厂工艺流程》
纺纱工艺流程是指将原料棉花、毛线或化纤纤维经过一系列的加工处理,最终变成纺纱产品的整个生产过程。
下面将介绍一下典型的纺纱厂工艺流程。
1. 纺前工序:这一阶段包括开松、梳理和精梳等工序。
开松是将原料纤维解开,梳理是将纤维进行整理和清理,而精梳则是通过一系列的络纱、成条和拉伸工序,排除杂质和短纤维,使纤维更加纯净和牢固。
2. 纺纱工序:在这一阶段,经过纺纱机的加工,将经过梳理的纤维进行纺成纱线。
纺纱机是一种设备,可以将纤维拉伸并形成细长的纱线,同时也可以通过捻合的方式增加纱线的强度和牢固性。
3. 纺后工序:包括加弹、浸纺、印染等工序。
加弹是指通过热处理或化学处理使纱线具有一定的弹性和柔软性,浸纺则是将纱线浸入染料中进行染色,而印染是在纱线上印上各种花纹和图案。
4. 最后是成品包装工序,将加工好的纱线进行包装,并进行质检和出厂。
纺纱工艺流程中,每一个环节都非常重要,只有各个环节都得到严格的执行和把关,最终才能生产出质量好、性能优越的纺
织品。
在工艺流程中,还需要充分运用科技手段和先进设备,以提高产量、节约能源,保护环境。
希望通过这篇文章,可以对纺纱的工艺流程有一定的了解。
纺纱的基本流程

纺纱的基本流程纺纱原就属于一项非常古老的活动,自史前时代以起,人类便懂得将一些较短的纤维纺成长纱,然后再将其织成布。
纺纱:用物理或机械的方法将纺织纤维纺成纱线的过程。
纺纱的基本原理01开清棉(清花)△直行式抓棉机主要任务开松——将压紧的化纤包中的块状纤维开松成小块或小纤维束。
除杂——除去原料中的部分杂质。
混和——将各种性质的纤维均匀混和。
成卷——制成均匀的化纤卷供梳棉工序使用。
02梳棉将棉卷喂入梳棉机,经梳理后获得棉条。
△开清工序产生的棉卷喂入到梳棉机主要任务梳理——获得单纤维除杂——清除杂疵、短绒混和——进行单纤维间的混和成条——制成均匀的棉条03并条为改善条子的均匀度,将6~8根条子并合喂入并条机,经罗拉牵伸获得1根条子。
主要任务匀整——改善棉条的条干均匀度,以便得到更均匀一致的纱线;平行——力求棉条内的纤维更加伸直与平行;混合——将各种纤维按要求混合;成条——按要求成条状盛装在棉条桶内,以便下道工序生产。
04粗纱主要任务牵伸——将条子抽长拉细成为粗纱。
加捻——给粗纱加上一定的捻度,提高粗纱强力。
卷绕——将加捻后的粗纱卷绕在筒管上。
05细纱主要任务牵伸——将粗纱牵伸到所要求的特数。
加捻——给牵伸后的纱条加上一定的捻度,使之具有一定的强力、弹性和光泽。
卷绕——卷绕成管纱,便于运输和后加工。
06后加工(络筒、并纱、捻线)主要任务改善产品的外观质量通过烧毛、上蜡、络筒等去除纱疵和棉结杂质,改善条干均匀度和光洁度等。
改变产品的内在性能通过并纱、捻线等提高成纱的强力。
稳定产品的结构状态主要稳定纱线捻回制成适当的卷装形式便于运输、储存和进一步加工,如制成筒子纱、绞纱或打成大包、小包等。
▲络筒:1. 接长纱线,以增加纱线的卷装容量,提高后续工序的生产效率。
2. 清除纱线上的疵点、杂质,改善纱线的品质和强力。
▲并纱:两根或两根以上的单纱并在一起。
▲捻线:并合在一起纱,加上一定捻度,加工成股线。
纺纱工艺系统为了获得具有不同品质标准的纱线,对于不同的纤维材料,应采取不同的纺纱方法和纺纱系统。
纺纱工艺流程

纺纱工艺流程纺纱是指将棉、麻、毛、丝等原料经过预处理、精梳、粗纱、细纱等多个工序,最终制成纱线的过程。
下面是一个700字的纺纱工艺流程。
纺纱工艺流程主要分为下述几个步骤:第一步:原料准备纺纱的原料可以是棉、麻、毛、丝等天然纤维,也可以是化纤和混纺纤维。
首先需要将原料进行清理,去除杂质,然后对其进行湿化处理,提高纤维的柔软度。
第二步:预浸染为了增加纺纱后纱线的色牢度和均匀度,需要将原料进行预浸染。
预浸染主要是将纤维浸泡在染料中,以染色剂顺利渗入纤维内部,并提高染色均匀度。
第三步:精梳首先将纤维进行打劫、解胶、组织和分离等处理,然后通过精梳工序进行纤维的梳理。
梳理的目的是将纤维的杂质、短纤维等分离出来,保留长纤维并使纤维平行排列。
第四步:粗纱经过精梳后的纤维可以进行粗纱工序,即将梳理后的长纤维进行初步细纱。
这一过程主要是通过轧制和延伸,使纤维拉长,形成粗纱。
第五步:细纱粗纱经过延伸、牵伸和细化等工序,形成细纱。
这个过程主要是通过调整纺纱机器的速度,控制纤维的伸长度和细度,使纤维成为合适的纱线。
第六步:加捻细纱经过一些特殊加工和捻度控制工序,形成终端纱。
这个过程会对纱线进行捻合,增加纱线的结实度和耐磨性。
第七步:织造纱线进行织造工序,由织布机或织机将纱线按照设计的格局和规格,进行织造成布料或纺织品。
织造工序要注重纱线的强度和密度的控制,以保证织成的布料质量。
第八步:整理经过织造的布料还需要进行整理工序,即去除其表面的污染物和误差。
整理工序包括漂白、染色、印花、涂层等步骤,使布料达到所需的颜色和外观效果。
第九步:后整理经过整理后的布料还需要进行后整理工序,即对其进行熨烫、定型、起毛等处理,以改善布料的外观效果和手感。
纺纱工艺流程涉及多个环节和复杂的技术操作,每个环节都需要严格控制纤维的质量和纺纱机器的运行参数,才能保证最终产品的质量和性能。
纺纱工艺的提高和发展,可以提高纺织品的品质和附加值,促进纺织产业的发展。
涡流纺纱机的工作过程及其成纱原理

涡流纺纱机的工作过程及其成纱原理涡流纺纱机的工作过程及其成纱原理涡流纺纱机的工作过程及其成纱原理.1.ST纱sT纱由1根或2根以上纤维条组成,各根纤维条的名义线密度与设计捻度相同。
sT纱明显存在s捻和z捻,并带有无捻区交替出现的股线。
这种纱不能承受与综筘的摩擦和制造开口时的张力变化,因此只能供纬纱或针织使用。
自捻纱结构的周期性导致其在机织物上易形成条纹,即使用做纬纱也易显现菱形纹路,如通过特殊浆纱处理,也会随机地形成径向条影,因此用此纱织造时需要选择隐蔽条纹的织物,如色纱织物、隐条织物、提花织物、花呢织物、异色经纬交织织物以及起绒织物。
2STT纱S1Yr自捻股线是将ST纱的某一捻向(S向或Z向)追加捻度,最终形成自捻股线。
这种股线的捻度分布还有一定的周期性团体广告服装,如ST纱的捻度过高,追加捻度必然随之加大,则STT纱强捻与弱捻段捻差会增大,从而影响织物的光泽和手感。
如ST 纱捻度较低,由此制得的S1Yr纱能获得较好的织物外观与手感。
这种纱可用做机织纱,虽然其捻度不匀较环锭纱大,但是其成本却比环锭纱低。
(2)无捻区:在捻向交替变化的过渡区内,无捻或者少捻。
自捻单纱和自捻纱都有无捻区。
当两根有捻单纱条汇合时,如两者的捻向相同的各片断完全重合时(即s捻与S捻、z捻与z捻,无捻区与无捻区重合),这样形成的自捻纱称为同相白捻纱,如图837(a)所示。
同相自捻纱由于其无捻区正好是两根单纱的无捻区重叠的地方,因此突出了自捻纱的弱点,其会影响到成纱的条干和强力,从而使纱的断头率高,质量差。
当两根有捻单纱汇合时,使两者捻向相同的各片段相互错开一段距离时所形成的自捻纱称为相差自捻纱空白POLO衫。
即一根单纱对另一根单纱的相对位置比同相自捻纱移过一段长度,也即两根单纱的周期性相对位置即“相位”错开,其错开距离的大小称为相位差,如图837(c)所示。
相差自捻纱的无捻区不再和单纱的无捻区相重合,而是把原有的两根单纱无捻区的薄弱点分散开来,避免了单纱无捻区与自捻纱无捻区的重叠,从而消除了成纱的薄弱环节,因此相差自捻纱的成纱质量和可纺性有所提高。
纺纱学

纺纱学
棉型纺纱系统
普梳系统 初加工→(原棉)配棉→开清棉→梳棉→并条→粗纱 →细纱→后加工 精梳系统 初加工→(原棉)配棉→开清棉→梳棉→精梳前准备 →精梳→并条→粗纱→细纱→后加工
纺纱原理
纺纱的概念
纱线:由一定长度的短纤维或长丝集聚而成具有一定 强力,能制成纺织品的细长体。 纺纱:把棉、毛、麻、丝和化纤切断纤维制成纱线的 工艺过程。
精梳
目的
1,排除不符合纺纱要求的短纤维; 2,梳理纤维进一步伸直、平行、分离; 3,较为彻底地清除条子中的杂质和纤维结粒; 4,原料进一步混和; 5,制成符合要求的精梳条。
精梳
精梳前准备
1,提高条子中纤维平行伸直度; 2,根据喂入的需要,制成均匀的小卷。
精梳
条卷机
精梳
条卷机
精梳
纺纱原理
纺纱的原理
大量而紊乱的纤维―――纤维集合体―――纱
初加工 选配 开松(除杂、混合) 梳理 分粗梳和精梳 牵伸 并合 加捻 卷绕
纤维原料的初加工
棉纤维的初加工
轧棉: 锯齿轧棉 皮辊轧棉
纤维原料的初加工
毛纤维的初加工
洗工
精梳机
牵伸与并和
目的
1,抽长拉细纱条; 2,提高纤维的平行伸直度; 3,降低纱条不匀率。
牵伸与并和
并条机
牵伸和并和
牵伸机构
粗纱
粗纱机
细纱
细纱机
加捻
目的
1,使纤维须条成纱或使纱捻合成股线; 2,使纤维、单纱、单丝在纱、线中获得一定的结构 形态,使制品具有一定的物理机械性能和外观结构。
脱胶
纤维原料的初加工
绢丝纤维的初加工
粗纱机的原理及工作过程解析
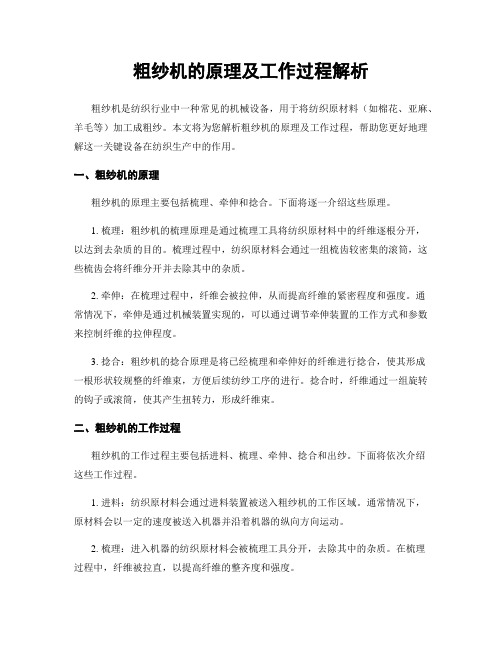
粗纱机的原理及工作过程解析粗纱机是纺织行业中一种常见的机械设备,用于将纺织原材料(如棉花、亚麻、羊毛等)加工成粗纱。
本文将为您解析粗纱机的原理及工作过程,帮助您更好地理解这一关键设备在纺织生产中的作用。
一、粗纱机的原理粗纱机的原理主要包括梳理、牵伸和捻合。
下面将逐一介绍这些原理。
1. 梳理:粗纱机的梳理原理是通过梳理工具将纺织原材料中的纤维逐根分开,以达到去杂质的目的。
梳理过程中,纺织原材料会通过一组梳齿较密集的滚筒,这些梳齿会将纤维分开并去除其中的杂质。
2. 牵伸:在梳理过程中,纤维会被拉伸,从而提高纤维的紧密程度和强度。
通常情况下,牵伸是通过机械装置实现的,可以通过调节牵伸装置的工作方式和参数来控制纤维的拉伸程度。
3. 捻合:粗纱机的捻合原理是将已经梳理和牵伸好的纤维进行捻合,使其形成一根形状较规整的纤维束,方便后续纺纱工序的进行。
捻合时,纤维通过一组旋转的钩子或滚筒,使其产生扭转力,形成纤维束。
二、粗纱机的工作过程粗纱机的工作过程主要包括进料、梳理、牵伸、捻合和出纱。
下面将依次介绍这些工作过程。
1. 进料:纺织原材料会通过进料装置被送入粗纱机的工作区域。
通常情况下,原材料会以一定的速度被送入机器并沿着机器的纵向方向运动。
2. 梳理:进入机器的纺织原材料会被梳理工具分开,去除其中的杂质。
在梳理过程中,纤维被拉直,以提高纤维的整齐度和强度。
3. 牵伸:经过梳理的纤维会通过牵伸装置,被拉伸以改变纤维的长度和形态。
牵伸装置通常由运动部件和张力控制装置组成,可以根据需要调整纤维的拉伸程度。
4. 捻合:经过梳理和牵伸的纤维会进一步被捻合,形成纤维束。
捻合的方式可以是通过旋转的钩子、滚筒或其他设备实现的,以产生纤维束的扭转力。
5. 出纱:经过捻合后的纤维束会通过排纱装置,被带出机器并卷绕成纱线。
排纱装置通常由一个或多个滚筒组成,通过调整滚筒的运动和张力,可以控制纱线的粗细和均匀度。
需要注意的是,粗纱机的工作过程在实际生产中可能会略有差异,具体的工作方式和参数会根据纺织原材料的不同以及生产要求的不同而有所变化。
纺纱原理与设备的精梳工序(六)
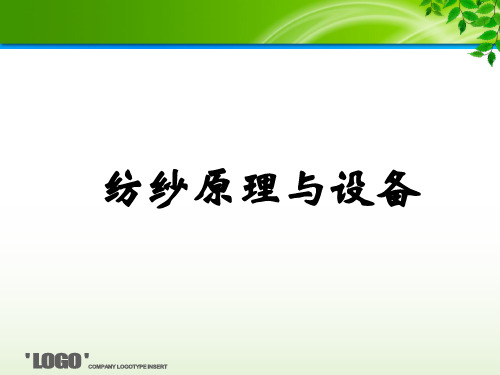
第七节 其他部分 一、车面输出部分
从棉网输出到进入牵伸 装置的部分称为车面部 分。 分离须丛叠合处常有厚 薄不匀,棉网在托盘上 集合时有一定的均匀混 合作用;车面上八根棉 条并合可改善周期性的 接合不匀;棉网松弛区 可改善精梳条的结构和 均匀度。
二、牵伸机构 (一)三上五下牵伸型式 后牵伸倍数为固定的 1.33倍,前区牵伸倍 数在6.5-14.7倍之间, 总牵伸倍数在8.6-19.6 (二)三上三下压力帮牵 伸型式
7.前段倒转量 (1)定义-锡林末排梳针通过 锡林与分离罗拉最紧点时 分离罗拉的倒转量。 (2)不能太大
8.分离罗拉顺转定时及开始顺转量 (1)分离罗拉顺转定时-分离罗拉由倒转结束开始顺转时, 分度盘指针指示的分度数。 (2)要求: a.分离罗拉顺转定时的确定应保证开始分离时分离罗拉的顺 转速度大于钳板的前摆速度。 b.分离罗拉顺转定时确定应保证分离罗拉倒入机内的棉网不 被锡林末排梳针抓走。 (3)分离机构的运动量决定于分离罗拉的总顺转量和总倒转 量,而有效输出长度即为总顺转量与总倒转量的差值。
第八节 精梳工序质量评价
一、精梳棉条质量 重量不匀率、条干不匀率、精梳棉条短绒率、棉结杂质清除 率 二、提高精梳棉条质量的主要措施 1.精梳落棉率控制 2.精梳条质量不匀率控制 3.精梳条条干CV值控制 4.精梳条棉结杂质的控制
• 作业10:
1.精梳锡林和顶梳的作用?梳理特点是什么? 2.分离接合部分和车面输出部分的作用? 3.分离罗拉顺转定时及开始顺转量的改变对分离接合的纤维 网质量有何影响? 4.如何控制精梳落棉率? 6.名词解释:分离丛长度、有效输出长度、接合率、继续顺 转量、前段倒转量。
纺纱原理与设备
3.分离接合开始定时 被锡林梳理过棉丛的头端到达分离钳口。 4.分离接合结束定时 钳板到达最前位置,再没有纤维进入分离 钳口。
1-纺纱基本原理与棉纺纺纱系统和流程
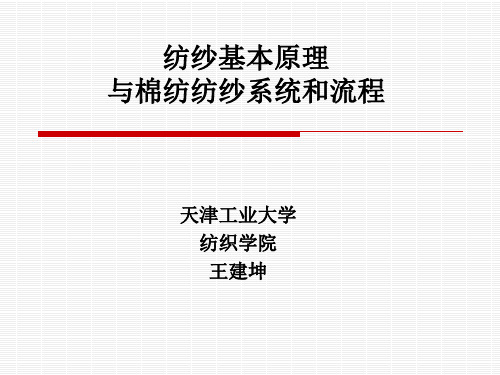
纤维的松解、集合
经过初步加工的原料呈大的块状,纤维间有 紧密的横向联系,纤维间的排列也是杂乱无 章的,并且仍然夹带有一定的杂质。 如何将杂乱无章、横向紧密联系的纤维加工 成纵向顺序排列,而且具有一定要求的光洁 纱线,需要将块状纤维变成单根纤维状态, 彻底解除纤维原料存在的横向联系,并且建 立起牢固的首尾衔接的纵向联系。前者称为 纤维的松解,后者称为纤维的集合。
加捻(完成集合、赋予纱线物理机械性能)
经过牵伸的纱条越来越细,截面内的纤维根 数越来越少,相互之间更加平行顺直,但轴 向联系越来越弱,强力降低,容易引起纤维 集合体(须条)的意外伸长,甚至断头。因 此,需要施加一定的捻度,增加纤维之间的 横向抱合,提高其强力 加捻是将须条绕其本身轴线加以扭转,使平 行于须条轴向的纤维呈螺旋状,从而产生经 向压力使纤维间的纵向联系固定下来
由于纤维原料的种类繁多,性能各异,在集 合体内的分布又呈现出很大的离散性。 纤维原料往往又受周围温度、湿度等环境的 影响很大,这些都给纺纱加工带来某些不确 定因素。 所以,在描述纺纱规律和表示产品性能时常 常带有统计学性质。
纺纱基本原理
纱线除了由很长的连续单丝捻合而成的外, 一般都是由许多长度不等的短纤维通过捻 接的方法制成的。 纺纱就是采用一定的系统、流程、设备和 工艺技术将纺织短纤维加工成满足一定要 求的纱线的过程。这个过程要对纤维进行 松解和集合。
精梳(除短纤维、伸直平行)
梳理后的条子中含有较多的短纤维和纤维的结粒杂 质,纤维的平行伸值度较差 当加工特数细、要求高或者有特殊用途的纱时,还 需要经过精梳机或者复精梳机的加工才能保证成纱 质量 精梳机的梳理作用是利用梳针对纤维的两端分别进 行握持状态下的更为细致的梳理 精梳机加工能够排除一定长度以下的短纤维和细小 杂疵,促使纤维更加平行、顺直 化学纤维因其长度整齐,杂质少,伸直平行状态好, 一般不经过精梳机的加工
简述纺纱的基本原理及应用

简述纺纱的基本原理及应用1. 纺纱的基本原理纺纱是将纤维材料经过一系列加工过程,转化为线状物的过程。
它的基本原理包括:•纤维处理:将原料纤维经过清洁、柔化等处理,去除杂质,使纤维更加适合后续加工;•纤维拉伸:将纤维进行拉伸,使其在长度方向上变细、变长,提高它的物理性能;•纤维旋绕:通过纺纱机械设备,将拉伸后的纤维进行旋转和定向排列,形成线状物。
2. 纺纱的应用领域纺纱作为纤维加工的重要环节,广泛应用于各个领域。
以下是纺纱的主要应用领域的简要介绍:2.1 纺织行业纺纱在纺织行业中起着至关重要的作用。
纺纱后的线状物可以用于织造各种织物,包括服装、家居用品、装饰品等。
不同纺纱工艺可以赋予纤维不同的特性,如强度、软度、弹性等,以满足不同织品的需求。
2.2 医疗行业纺纱的应用也延伸到医疗领域。
由于纺纱后的线状物具有较好的血液渗透性和透气性,可以用于医疗用品如敷料、医用绷带等的制作。
纺纱技术的发展还使得纺纱产生了一些具有功能性纤维,如抗菌纤维、吸湿排汗纤维等,这些纤维可以应用于保健和医疗领域。
2.3 工业行业在工业领域中,纺纱被用于制作各种工业纱线。
这些纱线可以用于制作绝缘材料、过滤材料、增强材料等,广泛应用于汽车、航空航天、电子等领域。
纺纱工艺可以根据不同工业需求,调整纱线的拉伸度、粗细程度等参数,以满足各种工业应用的要求。
2.4 传统工艺品另外,纺纱在传统工艺品的制作中也扮演着重要的角色。
在中国等一些传统文化底蕴深厚的国家,纺纱技术被用于制作各种手工艺品,如刺绣、织锦等。
通过纺纱,精细的纤维线可以用于表达各种精美的图纹,传承并展示着丰富的文化内涵。
3. 结语纺纱作为纤维加工的重要环节,以其基本原理和广泛应用的领域,对人类社会生活和工业发展产生了深远的影响。
随着科技的进步和纺纱技术的不断创新,纺纱行业将继续发展,为各行业提供更加优质的纺织品和材料,推动经济的繁荣和文化的交流。
转杯纺纱机纺纱原理及适纺原料

转杯纺纱机纺纱原理及适纺原料转杯纺纱机纺纱原理及适纺原料来源:中国纺机网发布时间:2011年05月13日转杯纺纱机纺纱原理及适纺原料一、纺纱原理转杯纺纱机无论是自排风式还是抽气式,其纺纱原理均为内离心式,即纺杯高速旋转,纺杯内便产生离心力,离心力可使从分梳腔转移到纺杯内的棉纤维产生凝聚而成为纤维环(须条),须条被加捻以后便成为纱条,纱条被引出纺杯后,棉纤维又在纺杯凝聚形成新的纤维环,以达到连续纺纱的目的。
自排风式纺纱原理如图1—13所示,抽气式纺纱原理如图1—14所示。
目前,我国运转生产的转杯纺纱机绝大多数为自排风式机型,纺纱机上配置的多为CEⅡ型纺纱器或是在CEⅡ型纺纱器基础上改进的D型纺纱器,这两种型号的纺纱器基本一样,只是在密封橡胶圈和输棉通道结构上略有区别。
CEⅡ型纺纱器的构造如图1—15所示,其工艺原理如图1—16所示。
喂入的棉条经给棉喇叭集束以后便进入给棉板与给棉罗拉的握持区,在压簧的作用下对给棉板产生26.5N的压力。
这时由给棉罗拉把棉条按牵伸倍数需要均匀地向前输送至高速旋转的分梳辊的抓取范围。
分梳辊对棉条进行开松并分解成单根纤维(单纤化过程),由于附面作用棉纤维便紧紧地附着在分梳辊齿端。
当分梳辊对棉条进行分解时,原来夹裹在棉纤维中的杂质,由于质量较大(较重),其离心力亦较大,便从棉条中分离出来,如图1—16所示。
杂质被分离出来后,在进入分梳腔排杂区时,借助排杂负压气流的吸引作用,通过纺纱器的排杂通道和排杂玻璃管被排到机身中部的总排杂管道中。
在自排风式转杯纺纱机中,由于高速旋转的纺杯把杯中原有的空气从底部的排气孔排出以后,纺杯内便产生负压(真空度),因纺杯的直径有大小之分,转速有快慢差别,并且又受纺纱器密封性能好坏的影响,因此,纺杯内负压高低存在着较大的差别。
图1—17所示为自排风式及抽气式纺杯内的负压值。
气压为了达到平衡,纺杯内原有的空气被排出后,外界的空气通过分梳腔和引纱玻璃管两个渠道源源不断地向纺杯内补充。
气流纺生产工艺

气流纺生产工艺气流纺是一种较新的纺纱工艺,相比传统的锭子纺、环锭纺等工艺,具有生产效率高、成本低、纤维质量好等优点。
下面将从纺纱原理、设备构成和生产工艺流程三个方面介绍气流纺的生产工艺。
一、纺纱原理气流纺利用高速的气流使纤维悬浮在空气中,并将悬浮的纤维拉伸、扭转成纱线。
在气流纺纺纱过程中,纤维经过剑刺或钳口的牵引而进入气流,纺纱时纤维沿气流的方向进行拉伸、扭转,最终形成纱线。
其纺纱原理是利用气流的动能、摩擦力和表面张力等作用于纤维上,使纤维产生捻度、撑直、扩散,从而形成纱线。
二、设备构成气流纺纺纱机主要由纤维缸、气流缸、引纱器、驱动装置等组成。
其中,纤维缸是纺纱机的核心部分,负责将纤维进给到气流缸中,经过加热并添加接枝剂等预处理;气流缸则是气流纺纺纱机中最关键的部分,通过喷射气流、卷辊速度的控制等手段,将纤维牵引、伸长、扭转,形成纱线;引纱器是将纱线引入传感器或层架的装置;驱动装置则是驱动气流缸和引纱器等组件工作的动力来源。
三、生产工艺流程气流纺生产工艺的主要流程包括:预处理、纤维进给、纺纱和整理。
预处理阶段主要是对纤维进行处理,包括清洗、张力调整、加湿、加热等工序。
其中,清洗是将原料纤维中的杂质去除,以保证纤维的纯净度;张力调整则是通过调整预处理设备的张力,降低纤维的弹性和扭曲度,以便于后续的纺纱工序进行;加湿和加热则是为了提高纤维的柔软性和伸长性,使其更易于纺制成纱线。
纤维进给阶段是将经过预处理的纤维送入纺纱机内部。
通常情况下,纤维以卷轴的形式放在纤维缸中,通过张力辊、优化纤维台等装置将纤维送入气流缸中。
纤维进入气流缸后,由高速的气流将纤维牵引、伸长、扭转,形成纱线。
纺纱阶段是气流纺的核心工序,也是整个生产工艺中最关键的环节。
在纺纱过程中,纤维不断接受气流的力量,得到拉伸、扭转和沉重力的作用,最终形成纱线。
纺纱速度、接送张力、压力等参数的控制对于纱线质量、纺纱效率等都有重要影响。
整理阶段是对纱线进行整形,主要包括卷绕、拉伸、整理等工序。
- 1、下载文档前请自行甄别文档内容的完整性,平台不提供额外的编辑、内容补充、找答案等附加服务。
- 2、"仅部分预览"的文档,不可在线预览部分如存在完整性等问题,可反馈申请退款(可完整预览的文档不适用该条件!)。
- 3、如文档侵犯您的权益,请联系客服反馈,我们会尽快为您处理(人工客服工作时间:9:00-18:30)。
二、合股加捻后股线性质的变化
1.改善条干不匀 – 按并合原理,n根单纱并合后条干不匀率可降 低。 – 部分粗节或细节隐藏在芯腔里,外观不易察觉。
2.增加强力 – n根单纱并合后的强力一般达不到原来单纱强 力的n倍。因各股单纱伸长率不一致,伸长率 小的应力较集中。 – 股线的强力常超过单纱强力的总和,一般双股 线中的单纱平均强力是普通单纱强力1.2~1.5 倍,三股线的1.5~1.7倍。
二、对络筒工序的要求
• 不损伤纱线原有的物理机械性质 • 做成筒子容量要大,结构坚实,便于贮存 和运输 • 纱线的接头要小而坚固
三、络筒机的工艺过程
四、 络筒张力与张力装置 (一)络筒张力
1、张力大小对卷绕及质量的影响
• 张力过小 筒子容量小、卷绕不良 在退绕时易生脱圈与断头 • 张力过大纱线受到的拉伸过大纱线的强力、弹性下降。
纺纱原理与设备
第九章 后加工
本章知识要点:
1.掌握后加工工序的任务和工艺流程。 2.了解络筒工序的任务、要求、工艺过程。掌 握络筒机的结构和工艺。 3.了解并纱的任务、工艺过程。 4.掌握捻线的任务、工艺过程,股线股数、捻 向及捻系数的选择。 5.了解摇纱和成包的任务。
第一节 概述
纺部品种较多,成纱后要进一步加工
二、 后加工的工艺流程 1、单纱的工艺流程
2、股线的工艺流程
3、缆线的加工工艺流程 • 缆线:经过两次并捻的多股线,第一次捻 线工序称为初捻,第二次捻线工序称为复 捻。 • 工业用线如轮胎帘子布用线、多股缝纫线 等需要进行复捻。
第二节 络 筒
一、络筒工序的任务
• 接长纱线,以增加纱线的卷装容量,提高后续工 序的生产效率。 • 清除纱线上的疵点。杂质,改善纱线的品质和强 力。
• 纱筒插杆→单纱筒子→导纱钩→张力垫圈 装置→落针→导纱罗拉→槽筒→筒子。
三、并纱机的断头自停机构
1、作用:保证并合根数,当某一纱管用完 时,使筒子与槽筒脱开。 2、断头自停机构的数量:等于单纱的根数。
第四节 捻线
一、捻线的任务 • 单纱经过并合后得到的股线。 • 捻线实质,就是以改善纱线中纤维所受应 力的分布状态的方法来提高纱线的品质。
– 原料有棉及化纤; – 成品有单纱及各种股线; – 卷装形式有管纱、筒子纱、绞纱及大小包;
– 加工要求有的需要定型,有的高档和特殊要求的产品要烧毛。
• 细纱工序后的各种加工统称为后加工
一、后加工的任务
1.改善产品外观质量 – 清纱装置:清除纱线的疵点、杂质。 – 捻线机上装水槽进行湿捻加工:使股线表面光滑圆润。 – 有的高级股线经过烧毛,除去表面毛羽、纤维环以增进光泽,上 蜡表面光滑。 2.改变产品内在性能 – 不同品质的单纱经一次或两次合股加捻,配不同股数、 捻向、捻 系数。 – 提高条干均匀度和强力;增加弹性、耐磨、耐疲劳;改善光泽与 手感,使截面更圆整,或使结构松紧起变化。花式捻线能使结构 形态多样化,产生环、圈、结、点节等异样花式。
3、圆盘式张力装置 • 种类:按加压方式不同可分为垫圈加压式、重锤加压式和弹簧加压 式三种;以垫圈加压式为最多。 • 垫圈加压式张力装置的结构:上、下张力盘,轴芯,毛毡垫圈,张 力垫圈及控制圈组成。 • 加压原理:纱线从上下张力盘之间通过时,张力盘和轴芯对纱线产 生摩擦,使纱线产生张力。 • 张力垫圈重量的选择 考虑因素:筒子的外形、纱线的强力(纱线的 粗细)等。对不同特数的加压重量见下表:
•
纱特 隔距/mm 38 0.48-0.6 29 0.4-0.5 25 0.38-0.48 18 0.33-0.4 15.3 0.28-0.38
•
特点:调整方便、适用于高速;但不能清除细节疵点、清纱板处易积尘 屑、清除效率低、易刮毛纱线。
4、电子清纱器 • 种类:光电式和电容式两种。 • 光电式电子清纱器的工作原理:由检测装 置、转换与放大装置、鉴别系统、驱动装 置组成。 • 电容式电子清纱器工作原理:与光电式相 比,其检测装置不同。
3.稳定产品结构状态 – 主要稳定纱线捻回,改善股线强力、弹性、伸长等性能,减少捻 线机上的断头。 – 单纱捻回不稳定,易“扭结”或“纬缩”。 – 股线中各股纱张力均匀,可避免“包芯”结构, – 在并纱机上装张力装置控制张力,使股线张力均匀。 4.制成适当的卷装形式 – 将容量较小,不宜高速退绕的管纱,在络筒机(包括并纱机)上 改绕成容量大并适宜于高速退绕的筒子。 – 有的纱线需要染色或其它处理,可摇成松散绞纱。为便于长期贮 存或远距离运输,可以将绞纱打成紧密的大包。
六、卷绕装置
1、组成:槽筒、筒管。 2、卷绕方式:全动程螺旋式卷绕。 3、卷绕过程:
槽筒转动 • 筒管转动 纱线沿筒管周向卷绕 纱线沿螺旋沟槽轴向移动
第三节 并 纱
一、并纱的任务 • 将两根以上的单并合在一起; • 清除纱上的杂质与疵点; • 做成张力均匀一致的筒子。
二、 并纱机的工艺流程
特数 重量(克)
58-36 19-15
36-24 17-12
21-18 11.5-9
16-14 9.5-8.5
11.7以下 8-4
五、清纱器
1.作用:清除纱线表面的疵点,如粗节、杂物等。 2.清纱器 • 结构:前盖板、固定清纱板、活动清纱板、后盖板、紧压弹簧、螺丝等 组成。 • 清纱原理:疵点在通过清纱器的缝隙时除去。 • 清纱板隔:它是清纱器的一个重要参数,过大时则粗节和纱圈漏过,过 小时纱线易被刮毛,断头多;一般清纱隔距为纱线直径的1.5-2.5倍。 清纱隔距与纱线密度的关系见下表:
2、络筒张力的主要来源
• 纱线退绕时,由于气圈的作用所产生的张力 • 由于张力装置的作用所附加的张力 • 导纱机件对纱线的阻力
3、络筒张力控制
• 对于棉纱:络筒张力≤纱线强力×15%~20%
(二)张力装置 1.张力装置的作用:增加纱线张力,以使筒子卷绕 成形良好。 2.对张力装置的要求: • 产生的附加张力要均匀(对时间稳定) • 与纱线的接触表面在光滑,不产生乱毛纱线 • 结构简单,便于调节,以适应不同粗细的纱线 • 便于清洁