粒化高炉矿渣知识汇总
矿渣粉基本知识

矿渣粉基本知识1、什么是矿渣粉?矿渣,是高炉炼铁产生的水渣,矿渣粉是高炉水渣通过细磨后,达到相当细度且符合相当活性指数的粉体。
2、矿渣粉国家标准是什么?目前执行的国家标准是GB/T18046-2008《用于水泥和混凝土中的粒化高炉矿渣粉》。
3、什么是矿渣粉的活性指数?简言之:即用50%矿粉和50%水泥拌合制作标准砂浆试件测试的强度,与用100%水泥制作标准砂浆试件测试强度的百分比,就是矿粉的活性指数。
4、矿渣粉分几个等级?共分为S105、s95、S75三个级别,具体的意义是:如:S105-28天活性指数不小于105%。
也就是说:50%矿粉和50%水泥拌合制作试件测试的强度大于100%水泥制作试件测试强度的105%以上的矿粉才符合S105级的要求。
其他依此类推。
5、GB/T18046-2008矿渣粉的技术要求有哪几项?共10项:密度、比表面积、活性指数、流动度比、含水量、三氧化硫含量、氯离子含量、烧失量、玻璃体含量、放射性等,如下表:6、矿渣粉的作用及特点?(1)减少坍落度损失;(2)大大提高混凝土耐久性;(3)对混凝土的显著增强作用;(4)优良的碱骨料抑制剂y(5)增强混凝土的抗腐蚀性;(6)提高混凝土的可泵性;(7)减少混凝土泌水。
(8)改善了混凝土的微现结构使水泥浆体的空障率明显下降,强化了集料界面的粘结力,使得混凝土的物理力学性能大大提高(8)减少水泥用量节约成本8、如何确定矿粉(s95级)在混凝土中的掺量?“单掺”矿粉时,可按等量取代原则并根据以下方法确定矿粉的合适掺量(1)对于地上结构以及有较高早期强度要求的混凝土结构,掺量一般为2030%。
(2)对于地下结构、强度要求中等的混凝土结构,排量一般为30-50%°(3)对于大体积混凝土或有严格温升限制的混凝土结构,掺量一般为50-65%。
(4)对于有较高耐久性能更求的特殊混凝土结构(如海工防腐蚀结构、污水处理设施等),掺量可达50-70%。
粒化高炉矿渣粉

一、判断1、活性指数试验,到龄期的试体应在试验(破型)前30min从水中取出,并用湿布覆盖至破型。
(×)2、矿渣粉活性指数试验,试块在水中养护时可以水平放置,试块削平面应向上。
(√)3、 GB/T18046-2008《用于水泥中的粒化高炉矿渣粉》规定矿渣粉氯离子含量不小于0.02。
(×)4、矿渣粉比表面积检测时,上面的滤纸可以重复使用,而料层下面的不可以重复使用。
(×)5、使用立磨粉磨矿渣时,矿渣入磨不需烘干。
(√)6、当散装工具容量超过生产厂规定出厂编号吨数时,允许该编号数量超过出厂编号吨数。
(√)7、GB/T18046-2008《用于水泥中的粒化高炉矿渣粉》规定,矿渣粉磨时允许加入石膏。
(√)8、矿渣粉试体在水中养护期间,允许全部换水,需注意水温。
(×)9、矿渣粉密度按GB/T208进行,矿渣粉的体积等于它排开的液体体积,液体使用普通煤油。
(×)10、比表面积按规定称取样品,将样品倒入已预先放好一张滤纸的料桶内,上下晃动 2-3次,使料层平坦,然后再放一张滤纸。
(×)11、从试验样中取出,用于复验仲裁的一份称为封存样。
(×)12、分别测定试验样品和对比样品的抗折强度,两种样品同龄期的抗折强度之比即为活性指数。
(×)13、矿渣粉活性指数检验用试模,深度规定为40mm±0.10mm 。
( √ )14、矿渣粉活性指数检验,削平后,用防水墨汁或颜料笔对试体进行编号和做标记。
(×)15、矿渣粉活性指数检验,两个龄期以上试体,每个试模内三条试块为一个龄期。
(×)16、矿渣粉活性指数计算时,计算结果保留两位小数。
(×)17、矿渣的活性系数为矿渣中三氧化二铝与二氧化硅的比值。
(√)18、矿渣粉封存样保存期限为本批次样品发完后三个月。
(√)19、试体带模养护温度的养护箱温度为20士1℃,湿度大于90%。
混凝土原料-矿粉篇
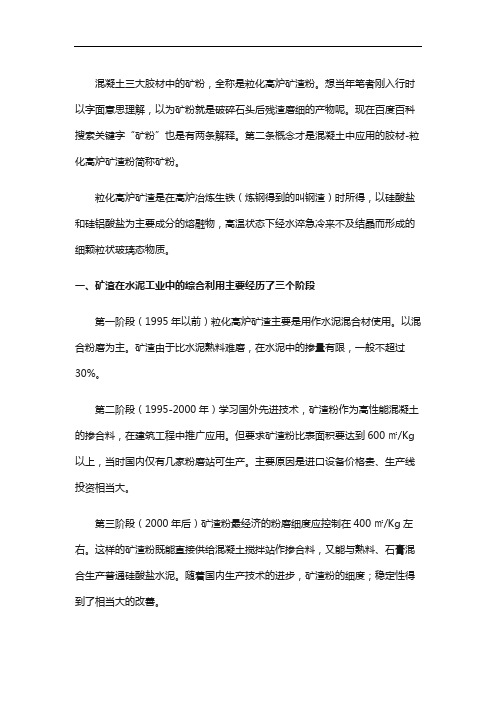
混凝土三大胶材中的矿粉,全称是粒化高炉矿渣粉。
想当年笔者刚入行时以字面意思理解,以为矿粉就是破碎石头后残渣磨细的产物呢。
现在百度百科搜索关键字“矿粉”也是有两条解释。
第二条概念才是混凝土中应用的胶材-粒化高炉矿渣粉简称矿粉。
粒化高炉矿渣是在高炉冶炼生铁(炼钢得到的叫钢渣)时所得,以硅酸盐和硅铝酸盐为主要成分的熔融物,高温状态下经水淬急冷来不及结晶而形成的细颗粒状玻璃态物质。
一、矿渣在水泥工业中的综合利用主要经历了三个阶段第一阶段(1995年以前)粒化高炉矿渣主要是用作水泥混合材使用。
以混合粉磨为主。
矿渣由于比水泥熟料难磨,在水泥中的掺量有限,一般不超过30%。
第二阶段(1995-2000年)学习国外先进技术,矿渣粉作为高性能混凝土的掺合料,在建筑工程中推广应用。
但要求矿渣粉比表面积要达到600㎡/Kg 以上,当时国内仅有几家粉磨站可生产。
主要原因是进口设备价格贵、生产线投资相当大。
第三阶段(2000年后)矿渣粉最经济的粉磨细度应控制在400㎡/Kg左右。
这样的矿渣粉既能直接供给混凝土搅拌站作掺合料,又能与熟料、石膏混合生产普通硅酸盐水泥。
随着国内生产技术的进步,矿渣粉的细度;稳定性得到了相当大的改善。
二、矿渣粉的生产过程在高炉炼铁过程中,出了铁矿石和燃料(焦炭)外,为了降低冶炼温度,还要加入适当数量的石灰石和白云石作为助溶剂。
它们在高炉内分解所得到的氧化钙、氧化镁和铁矿石中的废矿、以及焦炭中的灰份相熔化,生成了以硅酸盐和硅铝酸盐为主要成分的熔融物浮在铁水表面,定期从排渣口排出,经空气或水急冷处理,形成粒状颗粒物,这就是矿渣。
矿渣中含有95%以上的玻璃体和硅酸二钙,硅黄长石、硅灰石等矿物,与水泥成分接近。
如果未经淬水的矿渣,其矿物形态呈稳定型结晶体。
只有少部分的硅酸二钙具有一定水化活性。
这里可以理解为通过水淬急冷处理手段将一定的能量“封印”到矿渣中了。
这种“能量”(活性)可以在碱性条件下激发出来。
矿渣粉基本知识

矿渣粉基本知识1、什么是矿渣粉?6、矿渣粉的作用及特点?(1)减少坍落度损失;(2)大大提高混凝土耐久性;(3)对混凝土的显著增强作用;(4)优良的碱骨料抑制剂;(5)增强混凝土的抗腐蚀性;(6)提高混凝土的可泵性;(7)减少混凝土泌水。
(8)改善了混凝土的微观结构,使水泥浆体的空隙率明显下降,强化了集料界面的粘结力,使得混凝土的物理力学性能大大提高(8)减少水泥用量节约成本8、如何确定矿粉(S95级)在混凝土中的掺量?“单掺”矿粉时,可按等量取代原则并根据以下方法确定矿粉的合适掺量:(1) 对于地上结构以及有较高早期强度要求的混凝土结构,掺量一般为20-30%。
(2) 对于地下结构、强度要求中等的混凝土结构,掺量一般为30-50%。
(3) 对于大体积混凝土或有严格温升限制的混凝土结构,掺量一般为50-65%。
(4) 对于有较高耐久性能要求的特殊混凝土结构(如海工防腐蚀结构、污水处理设施等),掺量可达50-70%。
9、销售中客户重点关注哪些矿粉质量指标?(1)矿渣粉的7天活性指数:对于矿粉的28天活性指数一般都能够满足要求,而7天活性指标,就不容易达标了。
7天活性越高,混凝土里就可以多加矿粉,从而为混凝土企业增加利润。
S95级7天活性指数一般要大于75%。
(2)比表面积:代表矿渣粉的细度,一般为420㎡/㎏左右(3)45u筛余:代表矿粉颗粒的分布情况,筛余越小越好。
一般矿粉的筛余在2%以下。
这个指标在国家标准里未列入。
但一定程度放映了企业的质量管理水平,同样是客户关注的。
(4)氯离子含量:氯离子对钢筋有腐蚀作用,因此越小越好。
矿粉中的氯离子含量一般要小于0.06%。
10、我公司立磨生产矿粉的特点?我公司采用立磨矿渣粉生产线,属于自动化控制的先进矿渣粉磨工艺。
生产的矿粉,细度稳定在420-450m2/kg范围内,颗粒级配合理,质量稳定性好。
第五章高炉矿渣和矿渣水泥
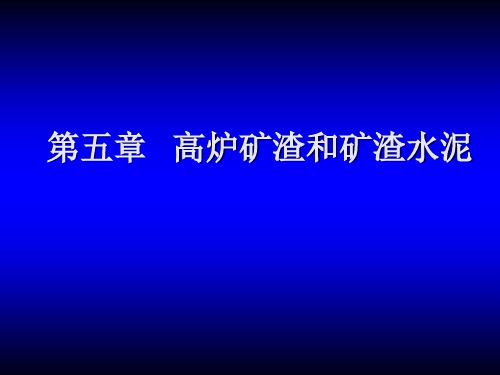
矿渣的矿物组成对其水化活性也有影响
13#、8#和11#主要矿物组成是黄长石 (C2AS),13#还含有C2S,11#还含 有C3S2 5#和9#主要是硅灰石(βCS)
C2S>C2AS>C3S2>CS
编号 矿物组成 28 的抗压强度析晶相组成源自强度的影响5 βCS 19.5
二、矿渣水泥的水化硬化过程
加水后,首先水泥熟料矿物水化,生成的Ca(OH)2 是矿渣的碱性激发剂,使玻璃体中的Ca 2+、Al2O3、 Al 3+、SiO44-离子进入溶液,生成水化硅酸钙、水化 铝酸钙。
由于部分Ca(OH)2与矿渣作用,使水化产物的碱度 要低一些。
由于矿渣水泥中,水泥熟料相对减少,使其早期硬 化较慢,表现出3d和7d强度较低。
--
1.56
9.03 1.06 0.16
--
1.99
9.43 1.97 0.67
--
2.10
7.77 0.97 0.20
--
1.58
10.54 2.21 0.36
--
2.90
10.20 0.75
--
--
1.93
5.65 -- 11.90 --
1.54
8.93 0.28 0.65 24.95
1.26
3-8 1.4-2.5 0.2-0.7 --
高炉炼铁是在高温下将氧化铁还原成金属铁,但是 在冶炼过程中,还需加入一定数量的溶剂矿物(如石灰 石),这些溶剂矿物分解出的CaO和MgO与铁矿石的 杂质和燃料中的灰分熔为一体,组成以硅酸盐和铝酸盐 为主的熔融体,然后以废渣的形式排出。
为了限制矿渣结晶并发生粒化,一般采取水等急冷措 施,如直接排放到水中。
混凝土用粒化高炉矿渣粉应用技术规程

混凝土用粒化高炉矿渣粉应用技术规程篇一:《混凝土用粒化高炉矿渣粉应用技术规程:我眼中的神奇“配方”》嗨,大家好!今天我要和大家讲一讲一个特别厉害的东西,就是混凝土用粒化高炉矿渣粉应用技术规程。
你可能会想,这听起来好复杂、好枯燥啊。
其实呀,一点也不呢!我先给你们讲个故事吧。
我爸爸是个建筑工人,他每天都在工地上忙忙碌碌的。
有一次,我跟着爸爸去了工地。
哇,那场面可壮观了,到处都是高高的架子和一堆堆的建筑材料。
我看到那些叔叔们在搅拌混凝土,我就好奇地问爸爸:“爸爸,这混凝土就这么简单地搅一搅就可以盖房子啦?”爸爸笑着说:“傻孩子,这里面学问可大着呢。
就像咱们做饭,不是随便把米和水放一起就行,得有合适的比例,混凝土也是。
”这时候,我就注意到旁边有一些灰色的粉末,和其他的沙子、石头不太一样。
我又问爸爸:“爸爸,那这个灰灰的东西是什么呀?”爸爸告诉我那就是粒化高炉矿渣粉。
我就更奇怪了,高炉里出来的东西怎么能用到混凝土里呢?爸爸说:“这个呀,就像是给混凝土加了一种神奇的调料。
”你看,混凝土就像一个大蛋糕,沙子、石头是蛋糕里的大块配料,水泥呢就像是把这些配料黏在一起的奶油。
那粒化高炉矿渣粉呢?它就像是蛋糕里的特殊香料,虽然放得不多,但是作用可大啦。
它能让混凝土变得更结实、更耐用。
就好比我们人,如果只是有强壮的肌肉(沙子、石头)和连接的组织(水泥)还不够,还得有一些特殊的营养元素(矿渣粉)来让我们的身体更好地发挥作用。
我又问爸爸:“那这个矿渣粉随便加多少都行吗?”爸爸说:“当然不行啦,这就得按照那个技术规程来。
”我想这技术规程就像是一本特别的食谱。
你想啊,如果做蛋糕的时候,香料放多了或者放少了,蛋糕的味道就不对了。
混凝土也是这样,如果矿渣粉的量不对,那混凝土可能就不那么结实,房子盖起来就可能有危险。
我在工地上还看到一个叔叔,他拿着一个本子在记录着什么。
我跑过去问他:“叔叔,你在写什么呀?”叔叔说:“我在记录我们用矿渣粉的情况呢,要严格按照技术规程来,这可关系到工程的质量啊。
矿渣知识简介
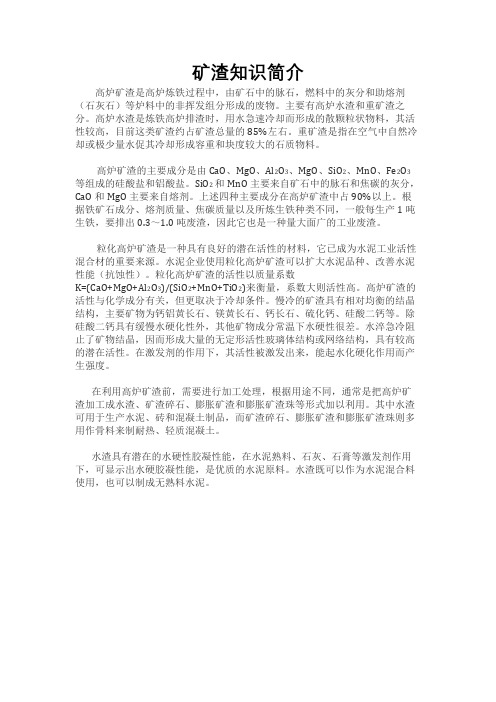
矿渣知识简介高炉矿渣是高炉炼铁过程中,由矿石中的脉石,燃料中的灰分和助熔剂(石灰石)等炉料中的非挥发组分形成的废物。
主要有高炉水渣和重矿渣之分。
高炉水渣是炼铁高炉排渣时,用水急速冷却而形成的散颗粒状物料,其活性较高,目前这类矿渣约占矿渣总量的85%左右。
重矿渣是指在空气中自然冷却或极少量水促其冷却形成容重和块度较大的石质物料。
高炉矿渣的主要成分是由CaO、MgO、Al2O3、MgO、SiO2、MnO、Fe2O3等组成的硅酸盐和铝酸盐。
SiO2和MnO主要来自矿石中的脉石和焦碳的灰分,CaO 和MgO主要来自熔剂。
上述四种主要成分在高炉矿渣中占90%以上。
根据铁矿石成分、熔剂质量、焦碳质量以及所炼生铁种类不同,一般每生产1吨生铁,要排出0.3~1.0吨废渣,因此它也是一种量大面广的工业废渣。
粒化高炉矿渣是一种具有良好的潜在活性的材料,它已成为水泥工业活性混合材的重要来源。
水泥企业使用粒化高炉矿渣可以扩大水泥品种、改善水泥性能(抗蚀性)。
粒化高炉矿渣的活性以质量系数K=(CaO+MgO+Al2O3)/(SiO2+MnO+TiO2)来衡量,系数大则活性高。
高炉矿渣的活性与化学成分有关,但更取决于冷却条件。
慢冷的矿渣具有相对均衡的结晶结构,主要矿物为钙铝黄长石、镁黄长石、钙长石、硫化钙、硅酸二钙等。
除硅酸二钙具有缓慢水硬化性外,其他矿物成分常温下水硬性很差。
水淬急冷阻止了矿物结晶,因而形成大量的无定形活性玻璃体结构或网络结构,具有较高的潜在活性。
在激发剂的作用下,其活性被激发出来,能起水化硬化作用而产生强度。
在利用高炉矿渣前,需要进行加工处理,根据用途不同,通常是把高炉矿渣加工成水渣、矿渣碎石、膨胀矿渣和膨胀矿渣珠等形式加以利用。
其中水渣可用于生产水泥、砖和混凝土制品,而矿渣碎石、膨胀矿渣和膨胀矿渣珠则多用作骨料来制耐热、轻质混凝土。
水渣具有潜在的水硬性胶凝性能,在水泥熟料、石灰、石膏等激发剂作用下,可显示出水硬胶凝性能,是优质的水泥原料。
用于水泥和混凝土中的粒化高炉矿渣

❖
❖ 式中:
A7 R7 100 ·················(A.1) R07
❖ A7—— 矿渣粉7d活性指数,%; ❖ R07——对比胶砂7d抗压强度,单位为兆帕(MPa); ❖ R7—— 试验胶砂7d抗压强度,单位为兆帕(MPa)。 ❖ 矿渣粉28d活性指数按式中(A.2)计算,计算结果保留至整数:
❖ 交货与验收
❖ 交货时矿渣粉的质量验收可抽取实物试样以其检验结果为依据,也可以生产者同 编号矿渣粉的检验报告为依据。
附录A (规范性附录)
矿渣粉活性指数及流动度比的测定
❖ A.1 范围 ❖ 本附录规定了粒化高炉矿渣粉活性指数及流动度比的检验方法。 ❖ A.2 方法原理 ❖ 1.测定试验样品和对比样品的抗压强度,采用两种样品同龄期的抗压强度之比评
❖ 判定规则
❖ 1.检验结果符合本标准中密度、比表面积、活性指数、流动度比、含水量、三氧 化硫等技术要求的为合格品。
❖ 2.检验结果不符合本标准中密度、比表面积、活性指数、流动度比、含水量、三 氧化硫等技术要求的为不合格晶。若其中任何一项不符合要求,应重新加倍取样, 对不合格的项目进行复检,评定经确认矿渣粉各项技术指标及包装符合要求时方可出厂。 ❖ 2.出厂检验项目为密度、比表面积、活性指数、流动度比、含水量、三氧化硫等
技术要求(如掺有石膏则出厂检验项目中还应增加烧失量)。
❖ 型式检验
❖ 1.型式检验项目为表一全部技术要求。 ❖ 2.有下列情况之一应进行型式检验: ❖ ——原料、工艺有较大改变,可能影响产品性能时 ❖ ——正常生产时,每年检验一次; ❖ ——产品长期停产后,恢复生产时; ❖ ——出厂检验结果与上次型式检验有较大差异时 ❖ ——国家质量监督机构提出型式检验要求时。
粒化高炉矿渣知识汇总
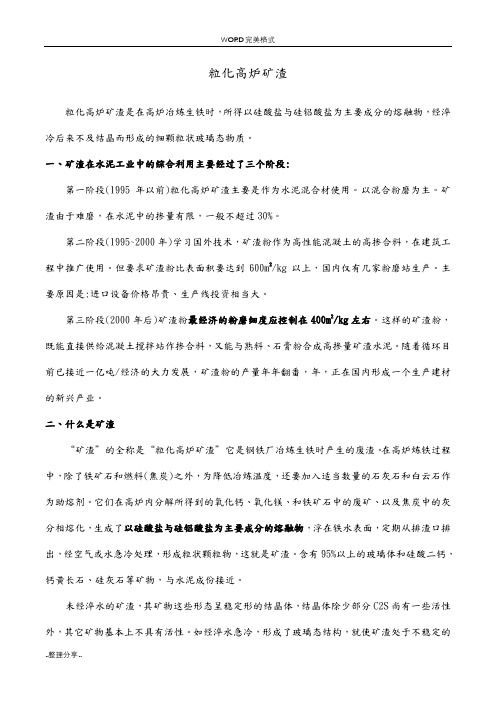
粒化高炉矿渣粒化高炉矿渣是在高炉冶炼生铁时,所得以硅酸盐与硅铝酸盐为主要成分的熔融物,经淬冷后来不及结晶而形成的细颗粒状玻璃态物质。
一、矿渣在水泥工业中的综合利用主要经过了三个阶段:第一阶段(1995年以前)粒化高炉矿渣主要是作为水泥混合材使用。
以混合粉磨为主。
矿渣由于难磨,在水泥中的掺量有限,一般不超过30%。
第二阶段(1995~2000年)学习国外技术,矿渣粉作为高性能混凝土的高掺合料,在建筑工程中推广使用。
但要求矿渣粉比表面积要达到600m2/kg以上,国内仅有几家粉磨站生产。
主要原因是:进口设备价格昂贵、生产线投资相当大。
第三阶段(2000年后)矿渣粉最经济的粉磨细度应控制在400m2/kg左右。
这样的矿渣粉,既能直接供给混凝土搅拌站作掺合料,又能与熟料、石膏粉合成高掺量矿渣水泥。
随着循环目前已接近一亿吨/经济的大力发展,矿渣粉的产量年年翻番,年,正在国内形成一个生产建材的新兴产业。
二、什么是矿渣“矿渣”的全称是“粒化高炉矿渣”它是钢铁厂冶炼生铁时产生的废渣。
在高炉炼铁过程中,除了铁矿石和燃料(焦炭)之外,为降低冶炼温度,还要加入适当数量的石灰石和白云石作为助熔剂。
它们在高炉内分解所得到的氧化钙、氧化镁、和铁矿石中的废矿、以及焦炭中的灰分相熔化,生成了以硅酸盐与硅铝酸盐为主要成分的熔融物,浮在铁水表面,定期从排渣口排出,经空气或水急冷处理,形成粒状颗粒物,这就是矿渣。
含有95%以上的玻璃体和硅酸二钙,钙黄长石、硅灰石等矿物,与水泥成份接近。
未经淬水的矿渣,其矿物这些形态呈稳定形的结晶体,结晶体除少部分C2S尚有一些活性外,其它矿物基本上不具有活性。
如经淬水急冷,形成了玻璃态结构,就使矿渣处于不稳定的状态。
因而具有较大的潜在化学能。
出渣温度愈高,冷却速度愈快,则矿渣玻璃化矿渣的潜在化学能程度愈高,愈大,活性也愈高。
因此,经水淬急冷的高炉矿渣的潜在活性较好。
每生产1吨生铁,要排出0.3-1吨矿渣。
矿渣控制介绍

矿渣又称粒化高炉矿渣,经过粉磨后细度和颗粒细小的矿渣就是矿渣微粉。
矿渣微粉的主要用途是作为水泥生产中的混合材料,或者用于预制和预拌混凝土中,等量替代或超量替代部分水泥,以改善混凝土和水泥制品的性能并降低生产成本和能耗,具有广泛的应用前景。
矿渣微粉控制的主要内容包括:高炉矿渣的输送控制;矿渣料场的堆料、取料控制;矿渣、钢渣、石膏料的入仓传送;混合料的配比、向立磨输料控制;立磨主机系统及立磨外循环系统;热风炉热风控制系统;引风收尘系统;成品矿粉输送和储存系统以及成品卸料系统。
1.高炉矿渣的输送控制是将高炉矿渣经过皮带、分料器等设备运送到料场前段。
2.矿渣料场的堆料控制是控制地面输送皮带、堆料机将来料堆放在矿渣料场;取料控制是通过取料机、地面输送皮带将矿渣输送到矿渣仓。
3.矿渣、钢渣、石膏料的入仓传送:控制运输皮带将矿渣、钢渣、石膏运输到矿渣、钢渣、石膏仓。
4.混合料的配比、向立磨输料控制:通过控制定量给料机、胶带输送机、永磁除铁器等设备的运行,将混合料输送至立磨。
5.立磨主机系统及立磨外循环系统:立磨主机系统由立磨主机、主电动机及润滑站、主减速机及润滑站、选粉机、密封风机、主辊液压站、辅辊液压站、物料入磨管道吹堵空气炮等组成。
立磨有3个主磨辊和 3个辅磨辊,辅辊负责对物料进行摊铺、排气、压实。
主辊对物料进行碾压。
碾压后的粉磨经选粉机进行分选,细粉随热气流排出磨机进入收尘器收集,再经输送设备送入矿渣粉库;粗颗粒则沿选粉机内壁返回磨盘同新入的物料一起粉磨;大颗粒物料和难磨物经立磨外循环系统再次进入立磨进行研磨。
6 热风炉系统(成套设备)提供物料烘干所需的热风源,经过热风炉出口调节阀、管路上冷风调节阀,控制入磨风温。
7引风收尘系统由离心通风机主排风机、低压长袋脉冲袋收尘器、通风管道等设备组成。
离心通风机保证系统生产过程中处于负压状态,减小粉尘排放,提供系统通风所需的负压源,保证磨内各部位合理的风速以使物料在磨内与热空气充分接触,完成换热烘干、风送和选粉工作,在收尘器内完成气料分离,成品通过灰斗收集后卸出,洁净空气通过排风机和烟囱排入大气或作为循环风重新入磨。
矿渣硅酸盐水泥中粒化高炉矿渣的掺量

矿渣硅酸盐水泥中粒化高炉矿渣的掺量
矿渣硅酸盐水泥是一种利用高炉矿渣和其他辅助材料制成的水泥。
其中,粒化高炉矿渣是高炉炉渣经过特殊处理形成的颗粒状物料。
粒化高炉矿渣可以用于替代部分水泥熟料,以降低水泥生产过程中的二氧化碳排放和降低能耗。
通常情况下,矿渣硅酸盐水泥中可掺入粒化高炉矿渣的掺量范围为20%到70%,这个范
围是根据不同的水泥标准和生产要求来设定的。
具体的掺量需要根据相关标准、水泥的强度、工程要求和使用环境等因素来确定。
在确定掺量时需要进行试验和验证,以保证水泥的性能和工程质量。
总的来说,矿渣硅酸盐水泥中粒化高炉矿渣的掺量可以根据需要在20%到70%之间进行调整,以满足工程要求和环保要求。
硅灰和粒化高炉矿渣粉材料知识

矿渣和硅灰材料知识矿渣又称粒化高炉矿渣,是由高炉炼铁熔融的矿渣骤冷时,来不及结晶而大部分形成的玻璃态物质。
其主要组分为氧化钙、氧化硅和氧化铝,共占总量的95%以上,它具有较高的潜在活性,在激发剂的作用下,与水化合可生成具有水硬性的胶凝材料。
磨细矿粉作为一个独立的产品出现在建筑市场,广泛应用于预制和预拌混凝土中,磨细矿粉在水泥或混凝土中的掺加量则可达20-70%。
一些欧洲国家甚至允许掺到85%。
磨细矿粉则通常采用“等量”取代水泥方式配制混凝土,其强度仍然可以满足设计要求。
主要特点:o减少坍落度损失o大大提高混凝土耐久性o对混凝土的显著增强作用o优良的碱骨料抑制剂o增强混凝土的抗腐蚀性o提高混凝土的可泵性o减少混凝土泌水硅灰是在冶炼硅铁合金和工业硅时产生的SiO2和Si气体与空气中的氧气迅速氧化并冷凝而形成的一种超细硅质粉体材料。
一、硅灰的物理化学性能:1、硅灰: 外观为灰白色粉末、耐火度>1600℃。
容重:200~250千克/立方米。
硅灰的化学成份见下表:项目 SiO2 Al2O3 Fe2O3 MgO CaO Na2O PH平均值 85~94% 1.0±0.2% 0.9±0.3% 0.7±0.1% 0.3±0.1%1.3±0.2% 中性2、硅灰的细度:硅灰中细度小于1μm的占80%以上,平均粒径在0.1~0.3μm,比表面积为:20~28m2/g。
其细度和比表面积约为水泥的80~100倍,粉煤灰的50~70倍。
3、颗粒形态与矿相结构:硅灰在形成过程中,因相变的过程中受表面张力的作用,形成了非结晶相无定形圆球状颗粒,且表面较为光滑,有些则是多个圆球颗粒粘在一起的团聚体。
它是一种比表面积很大,活性很高的火山灰物质。
掺有硅灰的物料,微小的球状体可以起到润滑的作用。
二、作用:硅灰能够填充水泥颗粒间的孔隙,同时与水化产物生成凝胶体,与碱性材料氧化镁反应生成凝胶体。
矿渣硅酸盐水泥中粒化高炉矿渣的掺量
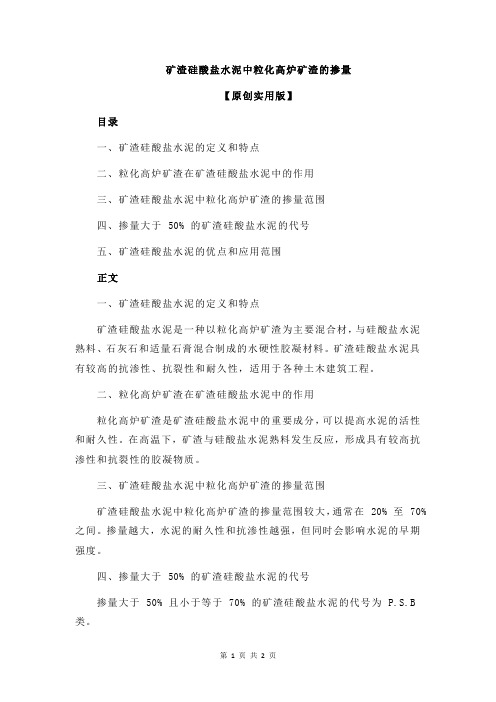
矿渣硅酸盐水泥中粒化高炉矿渣的掺量
【原创实用版】
目录
一、矿渣硅酸盐水泥的定义和特点
二、粒化高炉矿渣在矿渣硅酸盐水泥中的作用
三、矿渣硅酸盐水泥中粒化高炉矿渣的掺量范围
四、掺量大于 50% 的矿渣硅酸盐水泥的代号
五、矿渣硅酸盐水泥的优点和应用范围
正文
一、矿渣硅酸盐水泥的定义和特点
矿渣硅酸盐水泥是一种以粒化高炉矿渣为主要混合材,与硅酸盐水泥
熟料、石灰石和适量石膏混合制成的水硬性胶凝材料。
矿渣硅酸盐水泥具
有较高的抗渗性、抗裂性和耐久性,适用于各种土木建筑工程。
二、粒化高炉矿渣在矿渣硅酸盐水泥中的作用
粒化高炉矿渣是矿渣硅酸盐水泥中的重要成分,可以提高水泥的活性
和耐久性。
在高温下,矿渣与硅酸盐水泥熟料发生反应,形成具有较高抗
渗性和抗裂性的胶凝物质。
三、矿渣硅酸盐水泥中粒化高炉矿渣的掺量范围
矿渣硅酸盐水泥中粒化高炉矿渣的掺量范围较大,通常在 20% 至 70% 之间。
掺量越大,水泥的耐久性和抗渗性越强,但同时会影响水泥的早期
强度。
四、掺量大于 50% 的矿渣硅酸盐水泥的代号
掺量大于 50% 且小于等于 70% 的矿渣硅酸盐水泥的代号为 P.S.B 类。
五、矿渣硅酸盐水泥的优点和应用范围
矿渣硅酸盐水泥具有抗渗性、抗裂性和耐久性等优点,广泛应用于地下工程、隧道、桥梁、大坝等土木建筑工程。
矿渣微粉基本知识

精选课件
2
矿渣微粉的产生:由于矿渣易磨性差,与水泥熟料共同 粉磨时,细度往往偏粗而活性得不到有效发挥。如将矿 渣单独粉磨,粉磨到预定细度后掺人水泥中或在拌制混 凝土时掺人,则其活性可以得到充分的发挥。这种经过 粉磨细度和颗粒细小的矿渣就是矿渣微粉。矿渣微粉作 为一个独立的产品出现在建筑市场.广泛应用于预制和预 拌混凝土中。可以替代约50%水泥。
精选课件
7
七、矿渣粉的定义: 以粒化高炉矿渣为主要原料,可掺加少量石膏磨制成一
定细度的粉体,称粒化高炉矿渣粉,简称矿渣粉。
第二节 矿渣微粉的性能 一、技术要求:在GB/T 18046—2008中对矿渣微粉的质
量指标作如下规定:
抗压强度比
精选课件
8
上表中密度、氯离子含量、烧失量、三氧化硫含量、玻 璃体含量、放射性指标由矿渣和相关组分材料本身性质 决定。
精选课件
9
三、矿渣微粉的用途:
1、水泥生产中按一定比例直接掺入水泥中,是生产矿渣 硅酸盐水泥的组分材料。
2、在预拌混凝土和水泥制品中等量替代或超量替代部分 水泥,作为胶凝材料直接用于拌制混凝土和砂浆,改善 其工作性能。
精选课件
10
第二章矿渣微粉的生产方法及工艺
第一节 矿渣粉的生产过程
一、按生产主机设备和工艺分为三类:
精选课件
5
五、玻璃体:
粒化高炉矿渣中的非晶态固体称玻璃体。
玻璃体亦称为无定形体或非晶体。玻璃体的结构特征为 原子质点在空间上呈非周期性排列。 具有一定化学成分 的熔融物质,在急冷时,若质点来不及或因某些原因不 能按一定的规律排列,而凝固成固体,则得到玻璃体结 构的物质,玻璃体物质相对于晶体处于高能状态,处于 亚稳定状态,有向晶体转化的趋势,这种变化叫晶化或 脱玻化。要求矿渣微粉中玻璃体含量≥85%。
粒化高炉矿渣知识汇总

粒化高炉矿渣粒化高炉矿渣是在高炉冶炼生铁时,所得以硅酸盐与硅铝酸盐为主要成分的熔融物,经淬冷后来不及结晶而形成的细颗粒状玻璃态物质。
一、矿渣在水泥工业中的综合利用主要经过了三个阶段:第一阶段(1995年以前)粒化高炉矿渣主要是作为水泥混合材使用。
以混合粉磨为主。
矿渣由于难磨,在水泥中的掺量有限,一般不超过30%。
第二阶段(1995~2000年)学习国外技术,矿渣粉作为高性能混凝土的高掺合料,在建筑工程中推广使用。
但要求矿渣粉比表面积要达到600m2/kg以上,国内仅有几家粉磨站生产。
主要原因是:进口设备价格昂贵、生产线投资相当大。
第三阶段(2000年后)矿渣粉最经济的粉磨细度应控制在400m2/kg左右。
这样的矿渣粉,既能直接供给混凝土搅拌站作掺合料,又能与熟料、石膏粉合成高掺量矿渣水泥。
随着循环目前已接近一亿吨/经济的大力发展,矿渣粉的产量年年翻番,年,正在国内形成一个生产建材的新兴产业。
二、什么是矿渣“矿渣”的全称是“粒化高炉矿渣”它是钢铁厂冶炼生铁时产生的废渣。
在高炉炼铁过程中,除了铁矿石和燃料(焦炭)之外,为降低冶炼温度,还要加入适当数量的石灰石和白云石作为助熔剂。
它们在高炉内分解所得到的氧化钙、氧化镁、和铁矿石中的废矿、以及焦炭中的灰分相熔化,生成了以硅酸盐与硅铝酸盐为主要成分的熔融物,浮在铁水表面,定期从排渣口排出,经空气或水急冷处理,形成粒状颗粒物,这就是矿渣。
含有95%以上的玻璃体和硅酸二钙,钙黄长石、硅灰石等矿物,与水泥成份接近。
未经淬水的矿渣,其矿物这些形态呈稳定形的结晶体,结晶体除少部分C2S尚有一些活性外,其它矿物基本上不具有活性。
如经淬水急冷,形成了玻璃态结构,就使矿渣处于不稳定的状态。
因而具有较大的潜在化学能。
出渣温度愈高,冷却速度愈快,则矿渣玻璃化矿渣的潜在化学能程度愈高,愈大,活性也愈高。
因此,经水淬急冷的高炉矿渣的潜在活性较好。
每生产1吨生铁,要排出0.3-1吨矿渣。
什么是“矿渣粉”

膨胀高炉矿渣:用水或其他冷却质,如蒸汽或压缩空气,或两者兼用对熔融高炉炉渣进行急冷所获得的轻质蜂窝状材料。(膨胀高炉矿渣常用作轻骨料,本身不具备胶凝特性)
参考文献
1.ACI 116R-00,Cement and ConcreteTerminology, American Concrete Institute,Farmington Hills, Michigan, 2000.
2.ACI 233R-95,Ground Granulated Blast-Furnace Slag as a Cementitious Constituent inConcrete;American Concrete Institute,Farmington Hills, Michigan, 1995.
申明:和所有混凝土一样,必须进行多批次试验以验证混凝土的性能。除了其他方面之外,结果还可能因环境温度和混合物组分而有所不同。您应该咨询矿渣粉相关的专释为明示或暗示的担保或保证,包括任何适用于特定用途的担保。
铁水被输送到炼钢设备中,而熔渣则被输送到熔渣粒化系统。用水将熔融的矿渣快速冷却(该过程称为“造粒”)形成粒状原材料(水淬矿渣)。急冷能阻止熔渣结晶,从而形成玻璃态、非金属硅酸钙和铝硅酸钙等成分。
图三 高炉 图四 粒化器
(图片来源:https:///)
将这些颗粒干燥后磨至合适的细度,即可得到矿渣粉。除此之外,这些颗粒也可以作为复合硅酸盐的混合材。
(图片来源:https:///)
用矿渣粉代替混凝土中的部分硅酸盐水泥是一种使混凝土的性能更优异、更稳定的有效方法,可预见的性能提升包括:
矿渣微粉基本知识 PPT课件

第二节 矿渣微粉立磨生产系统
一、系统的组成和各子系统功能:
矿渣微粉立磨生产系统按功能由矿渣计量输送系统、立磨主 机系统、立磨外循环系统、热风炉系统、引风收尘系统、成 品矿粉输送和储存系统六大系统组成。
1、矿渣计量输送系统
组成:缓存仓(3)、棒阀(3)、定量给料机(3)、胶带 输送机(2)、永磁除铁器(2)、喷水设施(2)。
2012年1月
绪言
矿渣:又称粒化高炉矿渣,是由高炉炼铁熔融的矿物经水淬 骤冷时,来不及结晶而大部分形成的玻璃态物质。高炉 生 产 过程中,入炉的各种原、燃料经冶炼后,除获得铁水外 (炼钢生铁或铸造生铁)和副产品高炉煤气以外,铁矿石中的 脉石、燃料中的灰分和熔剂矿物融合就形成液态炉渣,其一 般温度为1450~1550℃,定时从渣口、铁口排出。高炉炉渣 的化学成分取决于原料成分、冶炼铁种、操作方法和冶炼过 程中的炉况变化。其主要组分由氧化钙,氧化镁,氧化硅和 氧化铝组成,共占总量的95%以上。矿渣是高炉炼铁的副产 品,它具有较高的潜在活性和水硬性,主要用途是作为水泥 生产中的混合材料,以改善水泥的性能并降低生产成本和能 耗。用水淬高炉矿渣作为水硬性混合材料,和硅酸盐水泥熟 料,适量石膏共同磨细混匀可制得矿渣硅酸盐水泥。矿渣硅 酸盐水泥中水渣的掺加量按重量计为20% -70%。
3、立磨和辊压机进行闭路粉磨。这种粉磨方式的优点是 集粉磨、烘干、选粉一体,系统简单、粉磨效率高、节 约能耗、单机台时产量高。由于立磨可以对矿渣的玻璃 体进行料层间挤压粉碎,因此能量利用率得到了较大的 提高,一般来说这种系统将矿渣粉磨到400~450㎡/kg比 表面积时的单位电耗为30一50kwh/t。其缺点在于投资规 模巨大。主机的维修费用昂贵,对生产管理要求很高;此 外立磨系统难以实现高等级的矿渣微粉生产,虽然在粒 度分布和颗粒形貌 (圆度系数)劣于前两种生产系统。 但基本可满足S95级矿渣微粉的生产要求。获得广泛的推 广。随大型立磨国产化,投资成本逐渐降低,目前我国 新建矿渣微粉项目以立磨系统为主。本厂即采用中信重 工LGMS5725矿渣立磨粉磨系统。
粒化高炉矿渣化学分析方法

粒化高炉矿渣化学分析方法D⒋1二氧化硅的测定D⒋⒈1分析步骤称取约0.5g(m)试样,精确至0.0001g,置于银坩埚中,在700℃的高温炉内预烧20min,取出稍冷,加入5g氢氧化钠,盖上坩锅盖(应留有较大缝隙),放入温度在400℃的高温炉中,继续升温至650~700℃的高温炉中熔融约20min 以上。
取出冷却,将坩锅放入盛有100mL热水的烧杯中,盖上表面皿于电热板适当加热。
待熔块完全被浸出后,立即取出坩锅,用水冲洗坩锅及盖,盖上表面皿,随即加入20mL盐酸,搅拌,再加入1mL硝酸。
再用少量热盐酸(1+5)和热水洗净坩锅和钙,将洗液合并于原烧杯中,将溶液加热至沸,得到澄清透明的溶液。
待溶液冷却后,移入250mL容量瓶中,并稀释至刻度,摇匀。
此溶液A供测定二氧化硅(见D⒋⒈1)、三氧化二铁(见D⒋⒉1)、三氧化二铝与二氧化钛(见D⒋⒊1)、氧化亚锰(见D⒋⒋1)、氧化钙(见D⒋⒌1)、氧化镁(见D⒋⒍1)用。
吸取D⒋⒈1试样溶液50.00mL于300mL的塑料烧杯中,加入10mL硝酸,冷却,加入10mL 氟化钾溶液(150g/L),搅拌,然后加入固体氯化钾,不断仔细搅拌至饱和并有少量氯化钾析出,再加入2g氯化钾。
冷却放置10min。
用快速滤纸过滤,用氯化钾溶液(50g/L)洗涤塑料杯与沉淀3次。
将滤纸连同沉淀一起置于原塑料杯中,沿杯壁加入10mL 氯化钾乙醇溶液(50g/L)及1mL酚酞指示剂溶液(10g/L),用[c(NaOH)=0.15mol/L ]氢氧化钠标准滴定溶液中和未洗净的酸,仔细搅动滤纸并随之擦洗杯壁,直至溶液呈红色。
向杯中加入200mL沸水(此沸水预先用氢氧化钠溶液中和酚酞呈微红色)。
用[c(NaOH)=0.15mol/L ]氢氧化钠标准滴定溶液滴定至微红色。
D⒋⒈2结果表示二氧化硅的百分含量X SiO2 按(D4.1)计算:T SiO2 ×V1 ×5X SiO2 =————————×100..............(D4.1)m×1000式中: X SiO2 —二氧化硅的质量百分数,%;T SiO2 —每毫升氢氧化钠标准溶液相当于二氧化硅的毫克数;V1 —滴定时消耗氢氧化钠标准滴定溶液的体积,mL;m—试料的质量,g。
- 1、下载文档前请自行甄别文档内容的完整性,平台不提供额外的编辑、内容补充、找答案等附加服务。
- 2、"仅部分预览"的文档,不可在线预览部分如存在完整性等问题,可反馈申请退款(可完整预览的文档不适用该条件!)。
- 3、如文档侵犯您的权益,请联系客服反馈,我们会尽快为您处理(人工客服工作时间:9:00-18:30)。
粒化高炉矿渣粒化高炉矿渣是在高炉冶炼生铁时,所得以硅酸盐与硅铝酸盐为主要成分的熔融物,经淬冷后来不及结晶而形成的细颗粒状玻璃态物质。
一、矿渣在水泥工业中的综合利用主要经过了三个阶段:第一阶段(1995年以前)粒化高炉矿渣主要是作为水泥混合材使用。
以混合粉磨为主。
矿渣由于难磨,在水泥中的掺量有限,一般不超过30%。
第二阶段(1995~2000年)学习国外技术,矿渣粉作为高性能混凝土的高掺合料,在建筑工程中推广使用。
但要求矿渣粉比表面积要达到600m2/kg以上,国内仅有几家粉磨站生产。
主要原因是:进口设备价格昂贵、生产线投资相当大。
第三阶段(2000年后)矿渣粉最经济的粉磨细度应控制在400m2/kg左右。
这样的矿渣粉,既能直接供给混凝土搅拌站作掺合料,又能与熟料、石膏粉合成高掺量矿渣水泥。
随着循环目前已接近一亿吨/经济的大力发展,矿渣粉的产量年年翻番,年,正在国内形成一个生产建材的新兴产业。
二、什么是矿渣“矿渣”的全称是“粒化高炉矿渣”它是钢铁厂冶炼生铁时产生的废渣。
在高炉炼铁过程中,除了铁矿石和燃料(焦炭)之外,为降低冶炼温度,还要加入适当数量的石灰石和白云石作为助熔剂。
它们在高炉内分解所得到的氧化钙、氧化镁、和铁矿石中的废矿、以及焦炭中的灰分相熔化,生成了以硅酸盐与硅铝酸盐为主要成分的熔融物,浮在铁水表面,定期从排渣口排出,经空气或水急冷处理,形成粒状颗粒物,这就是矿渣。
含有95%以上的玻璃体和硅酸二钙,钙黄长石、硅灰石等矿物,与水泥成份接近。
未经淬水的矿渣,其矿物这些形态呈稳定形的结晶体,结晶体除少部分C2S尚有一些活性外,其它矿物基本上不具有活性。
如经淬水急冷,形成了玻璃态结构,就使矿渣处于不稳定的状态。
因而具有较大的潜在化学能。
出渣温度愈高,冷却速度愈快,则矿渣玻璃化矿渣的潜在化学能程度愈高,愈大,活性也愈高。
因此,经水淬急冷的高炉矿渣的潜在活性较好。
每生产1吨生铁,要排出0.3-1吨矿渣。
表1我国部分钢铁厂的高炉矿渣化学成分三、矿渣微粉的应用通过将矿粉等工业废渣以等比例取代水泥的方式掺入到水泥中形成复合胶凝材料,能够产生例如“火山灰效应”和“微集料效应”等作用,从而使各个原材料在性能上产生互补作用。
因此,在倡导“低碳、环保”的今天,应在保证胶凝材料性能满足使用要求的前提下,尽可能多的将这类工业废渣、生物质灰循环利用,以达到节约水泥、保护环境的目的。
3.1 矿渣微粉的特性:1、矿渣微粉具有潜在水化活性。
当与水泥混凝土混合时,活性SiO2、A12O3与水泥中C3S 和C2S水化产生的Ca(OH)2反应,进一步形成水化硅酸钙产物,填充于水泥混凝土的孔隙中,大幅度提高水泥混凝土的致密度,同时将强度较低的Ca(OH)2晶体转化成强度较高的水化硅酸钙凝胶,显著发送了水泥和混凝土的一系列性能。
2、矿渣微粉具有潜在水硬性。
矿渣中含有硅酸盐、铝酸盐及大量含钙的玻璃质(如C2S、CAS2、C2AS、C3A、C2F和CaSO4等),具有独立的水硬性,在氧化钙与硫酸钙的激发作用下,遇到水就能硬化,通过细磨后,硬化过程大大加快。
3.2 矿渣化学成分对其活性的影响不同钢铁厂的矿渣的化学成分差异很大,同一钢铁厂不同时期排放的矿渣有时也不一样。
所以,要按进厂批次检测其化学成分的变化。
(1)氧化钙氧化钙属碱性氧化物,是矿渣的主要化学成分,一般占40%左右,他在矿渣中化合成具有活性的矿物,如:硅酸二钙等。
氧化钙是决定矿渣活性的主要因素,因此,其含量越高,矿渣活性越大。
(2)氧化铝氧化铝属酸性氧化物,是矿渣中较好的活性成分,他在矿渣中形成铝酸盐或铝硅酸钙等矿物,有熔融状态经水淬后形成玻璃体。
氧化铝含量一般为5%~15%,也有的高达30%;其含量越高,活性越大,越适合水泥使用。
(3)氧化硅氧化硅微酸性氧化物,在矿渣中含量较高,一般为30%~40%。
与氧化钙和氧化铝比较起来,它使矿渣活性降低。
(4)氧化镁氧化镁比氧化钙的活性要低,其含量一般在1%~18%,,在矿渣中呈稳定的化合物或玻璃体,不会产生安定性不良的现象。
因此,一般将氧化镁看成是矿渣的活性组份。
(5)氧化亚锰氧化亚锰对水泥的安定性无害,但对矿渣的活性有一定的影其含量一般应限制在1%~3%,如果超过4%~5%,矿渣活性响。
明显下降。
(6)硫矿渣中硫较多时,可使水泥强度损失较大;但硫化钙与水作用,生成氢氧化钙起碱性激发作用。
(7)氧化钛矿渣中的钛以钛钙石存在,使矿渣活性下降。
国家标准中规定矿渣中的二氧化钛含量不得超过10%。
3.3 矿渣微粉的用途:1、与硅酸盐水泥按比例混合,生产高性能矿渣水泥。
细度为400-450m2/kg的矿粉,可配制425,425R矿渣硅酸盐水泥;细度为400-450m2/kg的矿粉,可配制525,525R矿渣硅酸盐水泥。
2、作为混凝土掺和料,等量取代部分水泥(20%-70%),配制高强度、耐久性、高性能混凝土。
3.4 使用矿渣微粉的效果:1)可有效提高水泥混凝土的抗海水侵蚀性能,特别适合于抗海水工程。
2)可显著降低水泥混凝土的水化热,适于配制大体积混凝土。
3)可有效抑制水泥混凝土的碱骨料反应,提高混凝土的耐久性。
4)可显著减少水泥混凝土的泌水量,改善溺水混凝土的和易性。
5)可大幅度提高水泥混凝土的强度,轻而易举地配制超高强度水泥混凝土。
6)可显著增加水泥混凝土的致密度,改善水泥混凝土的抗渗性。
7)用于普通水泥混凝土可节省水泥用量,降低混凝土成本。
四、怎样评价矿渣质量的好坏4.1 质量评定方法1.化学分析法用化学成分分析来评定矿渣的质量是评定矿渣的主要方法.我国国家标准(GB/T203-2008)规定粒化高炉矿渣质量系数如下:式中:各氧化物表示其质量百分数含量。
质量系数K反映了矿渣中活性组份与低活性、非活性组份之间的比例关系,质量系数K 值越大,矿渣活性越高。
2.碱度经验法矿渣的活性组分含量之和与主要非活性组分的比值,称代号B为:碱度,碱度计算:式中:各氧化物表示其质量百分数含量。
B>1.6的矿渣属于活性矿渣,B越大潜在水硬性越好。
4.2 矿渣品质要求国家标准(GB/T203-2008)1.粒化高炉矿渣的质量系数K应不小于1.2。
2.粒化高炉矿渣中锰化合物的含量,以MnO计不得超过4%;锰铁合金粒化高炉矿渣的MnO允许放宽到15%;硫化物含量(以氟化物含量(以氟计)不得大于2%。
硫计)不得超过3%;3.粒化高炉矿渣的松散容重不大于1.2kg/L;矿渣颗粒直径不得超过50mm;210mm的颗粒含量不得超过8%。
4.粒化高炉矿渣不得混有外来夹杂物,铁尘泥、未经淬冷的块状矿渣等。
5.矿渣在未烘干前,其贮存期限,从淬冷成粒时算起,不宜超过3个月。
五、怎样激发矿渣的活性矿渣是一种具有“潜在水硬性”的材料,其单独存在时无水硬性。
但受到某些激发作用后,就呈现水硬性。
常用的激发方式有三大类,1.物理激发:也就是采用高细粉磨和超细粉磨的方法,用机械力使矿渣的热力学性质、结晶学性质、物理化学性质等都会发生规律性变化。
2.化学激发:采用对水泥或混凝土性能无害的化学物质,用化学反应激发矿渣水化的活性。
化学激发方式,可分为:碱激发、硫酸盐激发等多种激发形式。
3.复合助磨剂激发复合助磨剂激发简称:复合激发。
通常单独采用一种激活措施,不能显著地提高矿渣体系的活性,在实际应用时,需要综合各种物理和化学的激活方法,在粉磨矿渣的过程中,掺入“矿渣专用的复合助磨剂”,使磨细的矿渣粉在水化前具备激活的充分条件。
这是目前最广泛、最经济适用的复合激发方法。
矿渣专用复合助磨剂品种多样。
我们曾经用三乙醇胺、聚羧酸减水剂和氢氧化钙饱和溶经磁化装置活化处理的一种“多功能复合液,助磨剂”,既激发了矿渣的活性,又提高了矿渣粉的比表面积和磨机台时产量。
六、矿渣水泥生产工艺用于水泥工业的工业固体废弃物,一般细粉的水化速度比水泥慢得多,经测试表明:颗粒大小在80μm高炉矿(比表面积300m2/kg)时,渣水化90天左右才能产生与硅酸盐水泥熟料水化28天时相应的强度;粉煤灰则需150天左右才能达到相应的强度。
工业废渣粉磨到大部分在45μm(比表面积450m2/kg)时,扩大了水化反应时的表面积,可以较大幅度地提高它们的水化速度,使它们能在较短时间内产生较高的强度。
对粒化高炉矿渣采用高细粉磨并采用分别粉磨的形式,是目前综合利用中最适用的工艺流程。
工艺流程形式多样,可以是高细高产管磨机(尤其是滚动轴承球磨机)一级开路流程,也可以是普通球磨机、高效选粉机一级闭路流程;可以是立式磨一级闭路流程,也可以是辊压机与球磨机联合粉磨流程等等。
这些流程的共同点是:必须将矿渣粉磨成高细粉(统称:矿渣微粉),即矿渣微粉中的颗粒80%≤50μm、比表面积≥380m2/kg,其中,≤10μm的超细粉约占30~40%。
然后可以直接给混凝土搅拌站提供掺合料,或再与熟料粉合成不同强度等级的品种水泥。
图1球磨机分别粉磨合成水泥工艺流程辊压机与球磨机联合粉磨工艺流程如图2所示,配合料经过辊压机挤压粉碎之后,不能直接入磨;而是先经过打散分级机分选,细料(粒径≤2mm)送入球磨机水泥粉磨系统;粗料(粒径在2mm以上)返回辊压机再次挤压。
球磨机水泥粉磨系统可以是普通球磨机一级闭路流程,也可以是高细高产磨一级开路流程。
这种流程最大的特点是消除了辊压机的边缘效应,满足了辊压机过饱和喂料的要求;同时可以采用“低压大循环工艺”,减小辊压机的工作压力,延长辊套使用寿命,提高运转率;不必刻意追求辊压机出料中的合格细粉含量,充分发挥打散分级机的调控作用。
实践证明:该工艺流程比普通球磨机一级闭路流程增产60%以上,降低单产电耗15~20%,不仅经济效显著,而且运行费用降低、维修量大为减小。
图2辊压机与球磨机联合粉磨工艺流程图3立式磨水泥粉磨一级闭路流程七、矿渣粉磨工艺主要注意事项7.1 粉磨平衡一般来说,物料粉磨时间越长,出磨粒度越细。
但是,随着粉磨时间的延长,物料比表面积逐渐增大,其比表面能也增大,因而,微细颗粒相互聚集、结团的趋势也逐渐增强。
经过一段时间后,磨内会处于一个“粉磨↔团聚”的动态平衡过程,达到所谓的“粉磨极限”。
在这种状态下,即使再延长粉磨时间,物料也难粉磨得更细,有时甚至使粒度变粗。
同时,粉磨能耗成倍增加、粉磨效率降低。
这种现象在普通粉磨时并不明显,但在高细粉磨和超细粉磨中经常出现。
解决办法是:添加助磨剂。
它能形成物料颗粒表面的包裹薄膜,使表面达到饱和状态,不再互相吸引粘结成团,并通过裂纹形成和扩展过程中的防“闭合”和吸附,降低颗粒硬度、减弱强度,改善其易磨性。
助磨剂通过保持颗粒的分散,来阻止颗粒之间的聚结或团聚。
粉磨粒度越细,使用助磨剂的效果越显著。
7.2 矿渣质量检验与分选不同钢铁企业由于自己钢铁产品生产的需要,使其排放的高炉粒化矿渣化学成分不尽相同,加上冶炼环境、水淬条件不一样,同一工厂不同时段排放的矿渣,质量的差异有时也波动相当大。