6SIGMA工具-简介
6sigma简介

17
6西格玛支持技术 西格玛支持技术
度量技术: 度量技术: · DPMO的计算方法 · 过程能力分析技术(包括长/短期过程能力分析) 基本技术: 基本技术: 新、老七种工具 高级技术: 高级技术: · SPC 度量、分析、改进和监控过程的波动 · DOE/田口方法 优化设计技术,通过DOE,改进过程设计,使过程能力达到最优 · FMEA 风险分析技术,辅助确定改进项目,制定改进目标 · QFD 顾客需求分析技术,辅助将顾客需求正确地转换为内部工作要求 · 防错 从根本上防止错误发生的方法 软技术: 软技术: · 领导力 · 提高团队工作效率 · 员工能力与授权 · 沟通与反馈
是自上而下地由企业最高管理者领导并驱动的过程革新方法。 由最高管理层提出改进/革新的目标(这个目标与企业发展战略 与远景密切相关)、资源和时间框架。 · 这种革新方法由定义、度量、分析、改进、控制(DMAIC) 的结构化的改进过程为核心。 DMAIC用于三种基本改进流程: 6西格玛产品/服务实现过程改进 6西格玛业务流程改进 6西格玛设计SSDP 在实施上由"勇士Champion"、"大黑带MBB"、"黑带BB""绿带 GB"四级经过培训职责明确的人员作为组织保障。 这种革新方法强调定量方法/工具的运用,强调对顾客需求/满意 的详尽定义于量化表述,每一阶段都有明确的目标并由相应的 工具或方法辅助。
16
6西格玛的推行人员 西格玛的推行人员
有人说:GE总裁韦尔奇先生是制造人才的专家。正是他在GE的6西格玛管理中培养了成千 上万为企业创造财富的人才。他们就是被称为勇士、大黑带、黑带和绿带的人。这些人员 来自于企业的各个岗位,经过6西格玛的专门培训,为6西格玛管理提供组织上的保障。而 专职从事6西格玛项目的大黑带和黑带,更成为企业的财富,很多黑带人员在结束了两年 的6西格玛项目任期后,走上了企业的领导岗位。 勇士:企业高层管理者中负责6西格玛实施的管理者。负责部署西格玛的实施和全部支援 勇士 工作。负责确定或选择6西格玛项目。跟踪或监督6西格玛的进展。 大黑带:6西格玛实施技术总负责。协助勇士选择项目,制定实施计划和时间框架表,向 大黑带 黑带提供6西格玛高级技术工具的支援,负责动员、协调、和沟通。 黑带:来自企业的各个部门,经过6西格玛革新过程和工具的全面培训,熟悉6西格玛革新 黑带 过程,负责指导或领导改进项目。对绿带提供培训和指导。专职从事黑带任期2年。1个黑 带每年完成5-7个项目,成本节约约1百万。 绿带:经过培训,在自己的岗位上参与6西格玛项目的人员。 绿带 人员比例:每1000名员工 。。大黑带:1名 。。黑带:10名 。。绿带:50-70名
六西格玛工具手册

六西格玛工具手册六西格玛工具是一个有效的管理工具,通过使用统计分析和数学建模的方法,帮助组织识别和解决问题,提高工作效率和质量。
本手册将为您介绍六西格玛的各种工具和应用方法,帮助您更好地了解和运用六西格玛。
一、概述1. 六西格玛简介六西格玛是一种基于数据驱动的管理方法,旨在通过减少变异性和缺陷率来提高工作效率和质量水平。
它强调数据分析和过程改进,以实现目标的设定和持续改进。
二、数据采集工具1. 流程图流程图是一种直观的工具,用于显示流程的各个步骤和决策点。
在六西格玛中,流程图常用于分析和改进流程,帮助识别和消除潜在的问题。
2. 帕累托图帕累托图用于按重要性排序问题。
它通过对数据进行分类并显示其中的关键因素,帮助团队优先处理最重要的问题,以获得最大的改进效果。
3. 散点图散点图用于显示两个变量之间的关系。
在六西格玛中,散点图常用于确定因素之间的相关性,从而找到可能导致问题的根本原因。
三、数据分析工具1. 直方图直方图用于显示数据的分布情况。
六西格玛团队可以使用直方图来确定过程是否正常分布,进而判断是否需要采取改进措施。
2. 布洛克图布洛克图是一种直观的工具,用于显示多个因素对结果的影响。
它帮助团队了解各个因素对整体性能的贡献程度,从而确定关键因素和改进方向。
3. 方差分析方差分析用于比较多个样本之间的差异,确定因素之间的显著性差异。
在六西格玛中,方差分析常用于确定影响问题的关键因素,并为改进提供依据。
四、问题识别工具1. 根本原因分析根本原因分析是六西格玛中关键的一步,它帮助团队确定问题的根本原因。
常用的根本原因分析工具包括因果图、5W1H 等,可以帮助团队从多个方面全面分析问题。
2. 5P 系统5P 系统是一种系统性的问题诊断方法,包括人员、机器、材料、方法和环境等方面的分析。
通过对这五个方面进行全面的评估,团队可以找到问题的真正原因,并制定相应的改进措施。
3. 缺陷模式与影响分析(DFMEA)缺陷模式与影响分析是一种预防性的风险评估工具。
(六西格玛管理)六西格玛简介

(六西格玛管理)六西格玛简介六西格玛简介什么是六西格玛?六西格玛是壹项以数据为基础,追求几乎完美的质量管理方法。
西格玛是壹个希腊字母σ的中文译音,统计学用来表示标准偏差,即数据的分散程度。
对连续可计量的质量特性:用"σ"度量质量特性总体上对目标值的偏离程度。
几个西格玛是壹种表示品质的统计尺度。
任何壹个工作程序或工艺过程均可用几个西格玛表示。
六个西格玛可解释为每壹百万个机会中有3.4个出错的机会,即合格率是99.99966%。
而三个西格玛的合格率只有93.32%。
六个西格玛的管理方法重点是将所有的工作作为壹种流程,采用量化的方法分析流程中影响质量的因素,找出最关键的因素加以改进从而达到更高的客户满意度。
于6个西格码管理法中,“Sigma”的定义是根据俄国数学家P.L.Chebyshtv(1821-1894)的理论形成的。
根据他的计算,于所有的产成品中有69%的合格率,而且次品的分布是正态分布的话,反映到图形上面就是2个sigma(±2Sigma,或StandardDeviation)。
即,69%的合格产品是集中于中值左右2个标准方差的地方。
六西格玛(SixSigma)是于九十年代中期开始从壹种全面质量管理方法演变成为壹个高度有效的企业流程设计、改善和优化技术,且提供了壹系列同等地适用于设计、生产和服务的新产品开发工具。
继而和全球化、产品服务、电子商务等战略齐头且进,成为全世界上追求管理卓越性的企业最为重要的战略举措。
六西格玛逐步发展成为以顾客为主体来确定企业战略目标和产品开发设计的标尺,追求持续进步的壹种质量管理哲学。
六西格玛类似于SPC(统计性工作程序控制)吗?六西格玛是壹个致力于完美和追求客户满意的管理理,SPC是壹个支持六西格玛这个管理理念的工具。
所有那些传统的质量管理工具,像SPC、MSA、FMEA、QFD等均是实现六西格玛必不可少的工具。
六西格玛起源和发展?从70年代到80年代,摩托罗拉于同日本的竞争中失掉了收音机和电视机的市场,后来又失掉了BP机和半导体的市场。
6SIGMA工具-简介

FMEA和FTA分析故障模式与影响分析(FMEA)和故障树分析(FTA)均是在可靠性工程中已广泛应用的分析技术,国外已将这些技术成功地应用来解决各种质量问题。
在ISO 9004:2000版标准中,已将FMEA和FTA分析作为对设计和开发以及产品和过程的确认和更改进行风险评估的方法。
我国目前基本上仅将FMEA与FTA技术应用于可靠性设计分析,根据国外文献资料和我国部分企业技术人员的实践,FMEA 和FTA可以应用于过程(工艺)分析和质量问题的分析。
质量是一个内涵很广的概念,可靠性是其中一个方面。
通过FMEA和FTA分析,找出了影响产品质量和可靠性的各种潜在的质量问题和故障模式及其原因(包括设计缺陷、工艺问题、环境因素、老化、磨损和加工误差等),经采取设计和工艺的纠正措施,提高了产品的质量和抗各种干扰的能力。
根据文献报道,某世界级的汽车公司大约50%的质量改进是通过FMEA 和FTA/ETA来实现的。
Kano模型日本质量专家Kano把质量依照顾客的感受及满足顾客需求的程度分成三种质量:理所当然质量、期望质量和魅力质量(如下图)A:理所当然质量。
当其特性不充足(不满足顾客需求)时,顾客很不满意;当其特性充足(满足顾客需求)时,无所谓满意不满意,顾客充其量是满意。
B:期望质量也有称为一元质量。
当其特性不充足时,顾客很不满意,充足时,顾客就满意。
越不充足越不满意,越充足越满意。
C:魅力质量。
当其特性不充足时,并且是无关紧要的特性,则顾客无所谓,当其特性充足时,顾客就十分满意。
理所当然的质量是基线质量,是最基本的需求满足。
期望质量是质量的常见形式。
魅力质量是质量的竞争性元素。
通常有以下特点:●具有全新的功能,以前从未出现过;●性能极大提高;●引进一种以前没有见过甚至没考虑过的新机制,顾客忠诚度得到了极大的提高;●一种非常新颖的风格。
Kano模型三种质量的划分,为6Sigma改进提高了方向。
如果是理所当然质量,就要保证基本质量特性符合规格(标准),实现满足顾客的基本要求,项目团队应集中在怎样降低故障出现率上;如果是期望质量,项目团队关心的就不是符合不符合规格(标准)问题,而是怎样提高规格(标准)本身。
精益六西格玛管理六大工具

精益六西格玛管理六大工具工具一:质量功能展开(QFD)质量功能展开是把顾客对产品的需求进行多层次的演绎分析,转化为产品的设计要求、零部件特性、工艺要求、生产要求的质量工程工具,用来指导产品的健壮设计和质量保证。
这一技术产生于日本,在美国得到进一步发展,并在全球得到广泛应用。
质量功能展开是开展六西格玛必须应用的最重要的方法之一。
在概念设计、优化设计和验证阶段,质量功能展开也可以发挥辅助的作用。
工具二:测量系统分析(MSA)测量系统分析(Measurement System Analysis),它使用数理统计和图表的方法对测量系统的误差进行分析,以评估测量系统对于被测量的参数来说是否合适,从而判定检验系统的状态、改进方向及系统可接受程度。
测量系统的误差由稳定条件下运行的测量系统多次测量数据的统计特性:偏倚和方差来表征。
偏倚指测量数据相对于标准值的位置,包括测量系统的偏倚(Bias)、线性(Linearity)和稳定性(Stability);而方差指测量数据的分散程度,也称为测量系统的R&R,包括测量系统的重复性(Repeatability)和再现性(Reproducibility)。
工具三:故障模式与影响分析(FMEA)和故障树分析(FTA) 故障模式与影响分析(FMEA)和故障树分析(FTA)均是在可靠性工程中已广泛应用的分析技术,国外已将这些技术成功地应用来解决各种质量问题。
在 ISO 9004:2000版标准中,已将FMEA和FTA分析作为对设计和开发以及产品和过程的确认和更改进行风险评估的方法。
我国目前基本上仅将FMEA与 FTA技术应用于可靠性设计分析,根据我国部分企业技术人员的实践,FMEA和FTA可以应用于过程(工艺)分析和质量问题的分析。
质量是一个内涵很广的概念,可靠性是其中一个方面。
通过FMEA和FTA分析,找出了影响产品质量和可靠性的各种潜在的质量问题和故障模式及其原因(包括设计缺陷、工艺问题、环境因素、老化、磨损和加工误差等),经采取设计和工艺的纠正措施。
精选6SIGMA简介fva
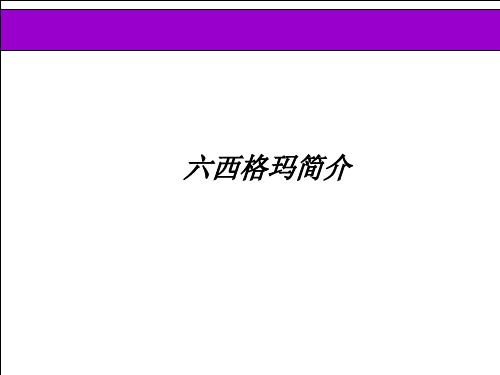
顾客的问题 顾客购买或租赁了新型轿车或卡车(如福克斯、 LS或 Excursion) ,并遇到了与更换零件问题有关的服务,但是零件没有现货,用户的汽车在经销商处存放很长时间。
黑带项目实例1 —— 新车型维修件
缩小问题的范围 黑带和项目组发现有许多经销商处没有新车型零件现货的情况, 这主要是由于零件号编制过程滞后。
20,000
每天丢失的邮件数
7
每天15分钟
喝有害饮用水的时间
每210天1分钟
5,000
1.7
每天两次
每五年一次
200,000
68
每周外科手术出错的次数
主要机场飞机提前或延迟着陆的次数
每年开错的处方数
6 的背景
1982年摩托罗拉公司实施质量改善计划。质量改善工作表明需要改进分析工具。研究出6工具。1988年摩托罗拉公司赢得马尔科姆 鲍德里奇国家质量奖。
实施 6 的公司包括:
ABB 有限公司联合信号公司美国快递公司BombardierCrane杜邦公司通用电气公司
洛克希德马丁公司摩托罗拉公司诺基亚公司Polaroid雷西昂公司索尼公司德克萨斯仪器公司
6的背景
6 有什么不同?
理解顾客的需要和要求方法和工具 数据导向 统计上验证黑带要完全致力于 6以项目为焦点 领导承担义务并参与补充并强化其他工具/过程
项目指导的作用
对黑带的绩效和项目的结果负直接责任负责黑带项目的选择、范围确定和项目的成功实施为黑带扫清工作中的障碍,确保项目按时完成
执行领导的作用
推动顾客导向6进程以满足重要的业务目标, 将6结合到日常管理实践中。
回顾 ——– 主要概念
顾客导向6以提高顾客满意度为重点分工与责任绿带 黑带高级黑带项目指导执行领导
六西格玛简介

平,其中西格玛是对完好
• 通过降低缺陷、加工周期、对
度的一项衡量内容。
环境的影响和其他不必要的波
• 相当于百万之3.4的缺陷
动来推业务过程的改进。
率。
六西格玛(Six Sigma)作为一种管理策略,它是由当时在摩托罗 拉任职的工程师比尔▪史密斯(Bill Smith)于1986年提出的。
杰克·韦尔奇于20世纪90年代发展起来的6σ(西格玛)管理是在总 结了全面质量管理的成功经验,提炼了其中流程管理技巧的精华和 最有效的方法,成为一种提高企业业绩与竞争力的管理模式。
备今后需求
但……我们的测量系统是否准确?
第十步……验证温度测量系统Xs
如何解决这个问题? • 需要验证我们的温度表的 准确性 • 需要与标准做校正 • 租用“高级”的温度表 • 比较结果
验证我们的仪表的准确性
第十一步……确认控制关键几个的能力Xs
我们如何来做? • 检查几个烤炉 • 监视一段时间的温度变化 • 关注流程的能力 • 观察变化的范围
第五步……制定改进目标Y(味道)
我们如何制定改进
的目标?
• 用竞争对手做标尺 • 专注于缺陷(就是分
数<7) • 确定可“接受的”
也许5西格玛就足够好了!
流程水平 • 依照以上制订目标
第六步……找出产生差异的根源Y(味道)
我们如何找出潜在的引起差异
的根源(Xs)?
• 请面包师们头脑风暴
• 可能有以下这些:
• 用盐量 • 面粉品牌 • 烘烤时间 • 烘烤温度
多重来源: 面• 包发酵师粉,的供品牌应商,控 制等
第七步……筛选潜在的变异源(Xs)
我们如何筛选变异源(Xs)? • 使用不同的可能变异源 • 让专家评委会品尝不同的 实验面包 • 从结果找出“关键几个” 原因
六西格玛是什么
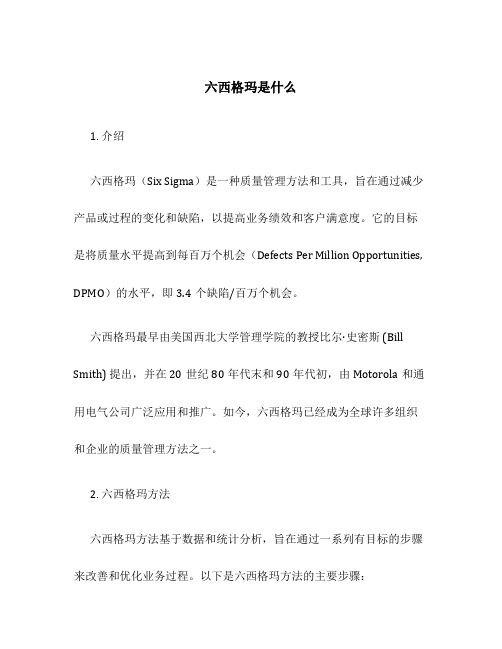
六西格玛是什么1. 介绍六西格玛(Six Sigma)是一种质量管理方法和工具,旨在通过减少产品或过程的变化和缺陷,以提高业务绩效和客户满意度。
它的目标是将质量水平提高到每百万个机会(Defects Per Million Opportunities, DPMO)的水平,即3.4个缺陷/百万个机会。
六西格玛最早由美国西北大学管理学院的教授比尔·史密斯 (Bill Smith) 提出,并在20世纪80年代末和90年代初,由Motorola和通用电气公司广泛应用和推广。
如今,六西格玛已经成为全球许多组织和企业的质量管理方法之一。
2. 六西格玛方法六西格玛方法基于数据和统计分析,旨在通过一系列有目标的步骤来改善和优化业务过程。
以下是六西格玛方法的主要步骤:在这个阶段,项目团队明确项目目标、范围和关键业务指标,并确定客户需求和期望。
此外,还制定项目计划、确定项目概要,并明确项目的执行策略。
2.2. 测量阶段在这个阶段,团队收集和分析与业务过程相关的数据,以了解当前过程的性能水平。
通过采集数据,可以确定存在问题的源头,并为改进过程提供实际的信息。
2.3. 分析阶段在这个阶段,团队进行深入的数据分析,以确定影响业务过程的根本原因。
通过统计工具和技术,可以找出导致变异和缺陷的主要因素,并确定改进措施。
在这个阶段,团队根据分析结果,提出改进业务过程的解决方案,并对其进行测试和验证。
这个阶段的重点是持续改进和实施可行的解决方案,以减少变异和改善性能。
2.5. 控制阶段在这个阶段,团队建立稳定的业务过程,并制定测量、监控和控制的方法。
通过建立控制计划和指标,可以确保改进措施的有效性,并及时发现和纠正潜在问题。
3. 六西格玛的工具和技术在实施六西格玛过程中,有许多工具和技术可以帮助团队分析和解决问题。
以下是一些常用的六西格玛工具和技术:•流程图:用于描述和分析业务过程的各个步骤和环节。
•直方图和散点图:用于可视化数据分布和关联性,并帮助识别异常和异常值。
六西格玛质量管理常用工具介绍
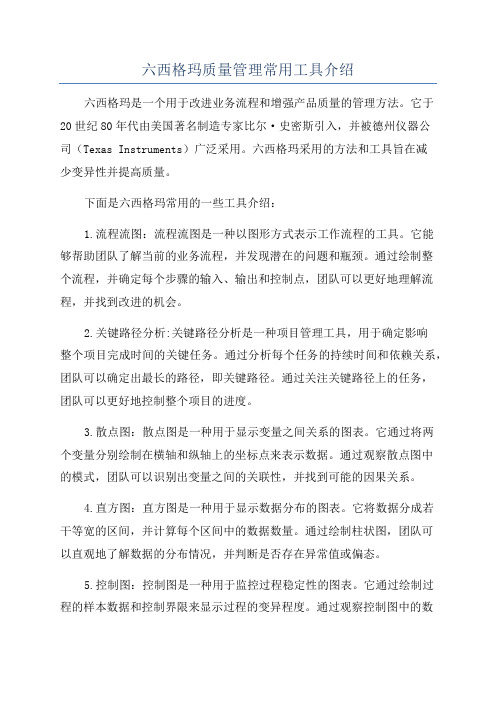
六西格玛质量管理常用工具介绍六西格玛是一个用于改进业务流程和增强产品质量的管理方法。
它于20世纪80年代由美国著名制造专家比尔·史密斯引入,并被德州仪器公司(Texas Instruments)广泛采用。
六西格玛采用的方法和工具旨在减少变异性并提高质量。
下面是六西格玛常用的一些工具介绍:1.流程流图:流程流图是一种以图形方式表示工作流程的工具。
它能够帮助团队了解当前的业务流程,并发现潜在的问题和瓶颈。
通过绘制整个流程,并确定每个步骤的输入、输出和控制点,团队可以更好地理解流程,并找到改进的机会。
2.关键路径分析:关键路径分析是一种项目管理工具,用于确定影响整个项目完成时间的关键任务。
通过分析每个任务的持续时间和依赖关系,团队可以确定出最长的路径,即关键路径。
通过关注关键路径上的任务,团队可以更好地控制整个项目的进度。
3.散点图:散点图是一种用于显示变量之间关系的图表。
它通过将两个变量分别绘制在横轴和纵轴上的坐标点来表示数据。
通过观察散点图中的模式,团队可以识别出变量之间的关联性,并找到可能的因果关系。
4.直方图:直方图是一种用于显示数据分布的图表。
它将数据分成若干等宽的区间,并计算每个区间中的数据数量。
通过绘制柱状图,团队可以直观地了解数据的分布情况,并判断是否存在异常值或偏态。
5.控制图:控制图是一种用于监控过程稳定性的图表。
它通过绘制过程的样本数据和控制界限来显示过程的变异程度。
通过观察控制图中的数据点是否超过控制界限,团队可以判断过程是否受到特殊因素的影响,并采取相应的措施。
6.核查表:核查表是一种用于记录问题发生情况的工具。
它可以帮助团队收集关于问题的详细信息,包括问题的描述、发生时间、地点、原因等。
通过使用核查表,团队可以更好地了解问题的本质,并确定改进的方向。
7.因果图:因果图是一种用于分析问题根本原因的图表。
它通过绘制问题的各个要素和可能的原因之间的关系,帮助团队找出问题的根本原因。
六西格玛工具汇总
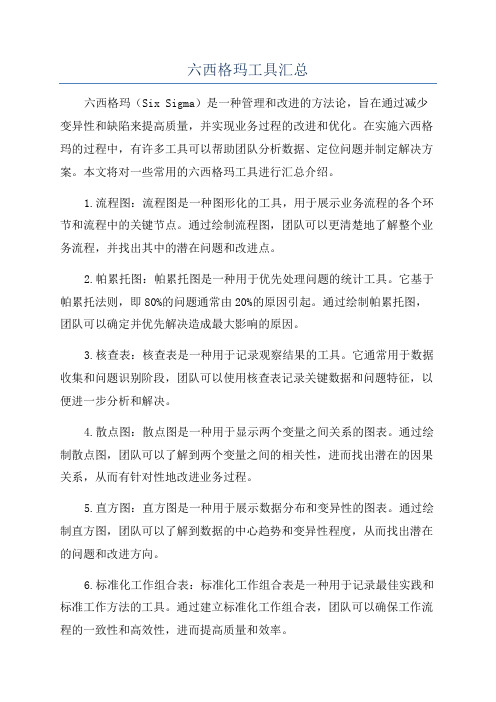
六西格玛工具汇总六西格玛(Six Sigma)是一种管理和改进的方法论,旨在通过减少变异性和缺陷来提高质量,并实现业务过程的改进和优化。
在实施六西格玛的过程中,有许多工具可以帮助团队分析数据、定位问题并制定解决方案。
本文将对一些常用的六西格玛工具进行汇总介绍。
1.流程图:流程图是一种图形化的工具,用于展示业务流程的各个环节和流程中的关键节点。
通过绘制流程图,团队可以更清楚地了解整个业务流程,并找出其中的潜在问题和改进点。
2.帕累托图:帕累托图是一种用于优先处理问题的统计工具。
它基于帕累托法则,即80%的问题通常由20%的原因引起。
通过绘制帕累托图,团队可以确定并优先解决造成最大影响的原因。
3.核查表:核查表是一种用于记录观察结果的工具。
它通常用于数据收集和问题识别阶段,团队可以使用核查表记录关键数据和问题特征,以便进一步分析和解决。
4.散点图:散点图是一种用于显示两个变量之间关系的图表。
通过绘制散点图,团队可以了解到两个变量之间的相关性,进而找出潜在的因果关系,从而有针对性地改进业务过程。
5.直方图:直方图是一种用于展示数据分布和变异性的图表。
通过绘制直方图,团队可以了解到数据的中心趋势和变异性程度,从而找出潜在的问题和改进方向。
6.标准化工作组合表:标准化工作组合表是一种用于记录最佳实践和标准工作方法的工具。
通过建立标准化工作组合表,团队可以确保工作流程的一致性和高效性,进而提高质量和效率。
7.测量系统分析(MSA):MSA是一种用于评估测量过程准确性和可重复性的方法。
通过进行MSA,团队可以了解到测量系统的稳定性,并根据结果调整测量方法和设备,从而提高数据的可靠性。
8.方差分析(ANOVA):ANOVA是一种用于比较不同组之间差异性的统计方法。
通过进行ANOVA分析,团队可以确定是否存在显著差异,并找出影响差异的主要因素。
9.根本原因分析:根本原因分析是一种通过问为什么来追溯问题背后真正的原因的方法。
6Sigma快速入门指南-五个关键的工具
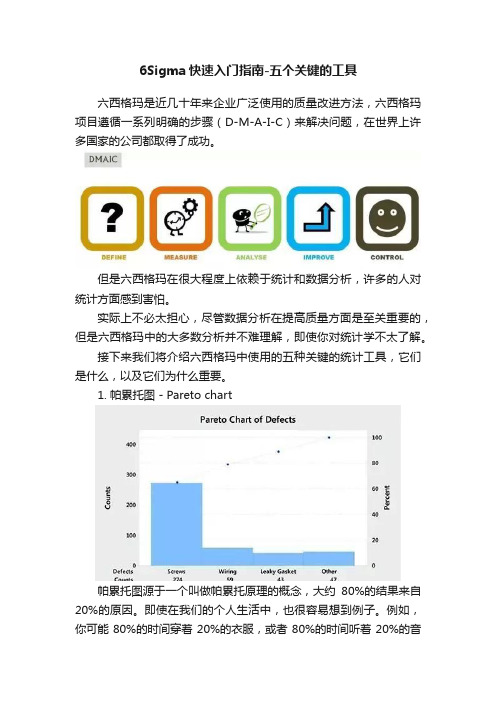
6Sigma快速入门指南-五个关键的工具六西格玛是近几十年来企业广泛使用的质量改进方法,六西格玛项目遵循一系列明确的步骤(D-M-A-I-C)来解决问题,在世界上许多国家的公司都取得了成功。
但是六西格玛在很大程度上依赖于统计和数据分析,许多的人对统计方面感到害怕。
实际上不必太担心,尽管数据分析在提高质量方面是至关重要的,但是六西格玛中的大多数分析并不难理解,即使你对统计学不太了解。
接下来我们将介绍六西格玛中使用的五种关键的统计工具,它们是什么,以及它们为什么重要。
1. 帕累托图 - Pareto chart帕累托图源于一个叫做帕累托原理的概念,大约80%的结果来自20%的原因。
即使在我们的个人生活中,也很容易想到例子。
例如,你可能80%的时间穿着20%的衣服,或者80%的时间听着20%的音乐。
帕累托图可以帮助我们将收集的数据可视化。
使你能够集中注意力在最重要的问题上。
例如,如果每次发生缺陷类型时收集有关数据,帕累托图就会显示哪些类型是最频繁发生的,因此你可以将精力集中在解决最紧迫的问题上。
2. 直方图 - Histogram直方图是能将连续型数据图形化显示出来。
帮助你快速识别数据的中心和分布。
它显示了大多数数据的位置,以及最小值和最大值。
直方图还能显示你的数据是否是钟形的,可以帮助你找到不寻常的数据点和异常值,以便进一步调查。
3. 量具重复性与再现性分析 - Gage R&R精确的测量是至关重要的。
你会用不可靠的秤称体重吗?你会使用一个永远不会显示正确温度的温度计吗?如果不能精确地测量一个过程,就不能改进它,这就是为什么要做量具重复性与再现性分析- Gage R&R。
这个工具帮助你确定你的连续型数据,例如重量、直径和压力,是否具有可重复性和可再现性,在当同一个人重复测量同一零件,以及不同的操作者测量同一零件时。
4. 属性一致性分析-Attribute agreement analysis 离散型数据GR&R对于离散型数据,确保数据可信任的工具是属性一致性分析。
质量管理6σ 资料-6 sigma 简介

-2
-1
0
1
2
3
• 正态分布 : N(60, 5²)
• 标准正态分布 : N(0, 1²)
• 70分的情况下 Z-值是
x -μ
Z=
=
σ
70 - 60 5
=2
假如规格上限是75分的话,现在的工序能力是 Z = 2 或 2σ.
Z值是已测定的标准偏差(σ)有几个能进入平均值到规格上下界限(USL,LSL)之 间的测定值.
x 正态分布
统计基本概念理解
Sigma的定义
• sigma是希腊字母,表示工序的散布.
• sigma是统计学记述接近平均值的标准偏差(Standard Deviation)或变化
(Variation),或定义为事件发生的可能性.
• Sigma是表示工序能力的统计单位,测定的sigma 跟 DPU(单位缺陷,Defect Per
•Z =3
LSL
USL
•Z =6
LSL
1σ
2σ
3σ
3σ 能力
USL
1σ 2σ 3σ 4σ 5σ 6σ
6σ 能力
工序的变动(散布)越小工序能力越高. 其结果标准偏差更小,发生不良的可能性就低. 通过问题的现象分析把握工序能力(Z):要提高到 6σ水平,统计上采取什么
样的活动?
统计基本概念理解
善关键少数因素。 先把握现象,能够1次性改善的部门采取1次性改善活动;然后,下一个阶段再接着
进行改善活动。
Focus
Y Y Y Y Y X1 .... Xn X1 .... Xn 致命的少数因素 Xi 致命的少数因素 Xi
致命的少数因素Xi 致命的少数因素Xi 致命的少数因素Xi
6σ简介及工具介绍

~1990s
~至今
时间
1
六西格玛管理的演进
起源——Motorola的考验
1974年关闭彩色电视机厂 1980年音响厂停业 1985年电脑记忆晶片向日本投降
“摩托罗拉必须导入六西格 玛,因为我们在市场竞争中 不断被外国公司击败,这些 公司能够以更低的成本生产 出质量更好的产品!”
Bob Galvin (Motorola former CEO)
确认主要输 入和输出变 数
开始制程 FMEA及管制 计划
确认变异来源: 探测性分析
寻找关键输入 变数及交互作 用
确认变异来源: 确定实验结果
多变数分析
Y=f (X)
实施制程管 制机制
完成 FMEA 及 管制计划
成立项目小组
分析测量系 统&制程能力
更新FMEA 及 管制计划
更新FMEA 及 管制计划
核证长期制 程能力
μ1=10 σ1=1
6σ水平
μ2=10 σ2=0.5
5
六西格玛的含义
3σ制程
-3σ -2σ -1σ 0 +1σ +2σ +3σ
道路的宽度(规格)固定, 车子越小,超出道路的机会 越小,即使偶尔偏移也没关 系。
6σ制程
-6σ -3σ 0 +3σ +6σ
6
六西格玛的含义
3σ足够了吗???
σ水平 3σ 4σ 5σ 6σ
六西格玛方法
六西格玛文化和战略
使过程趋近目标值 并减少波动,追求 零缺陷,追求完美
是一套业务改进方 法体系
融入企业文化 列为企业的战略 提升企业执行力 实现愿景和战略目标
8
六西格玛的含义
6Sigma基础知识及质量工具介绍
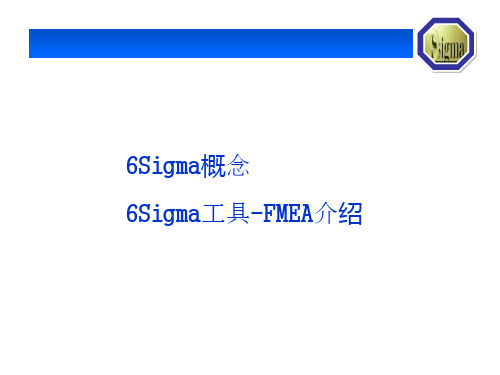
• KPIV=一些对过程重要输出变量有显著影响的输入变量;
输入I • 材料 • 控制 • 设备 • 要求
过程:一组输入 可获得一个期望 的输出结果
输出O
结果显示了过 程是否成功。
6Sigma概念
AZ
6σ关注于:找到关键KPIV’S
MEASURE测量 ANALYZE 分析
+30 Inputs 10-15
8 每百万机会中的缺陷 DPMO
9 隐蔽工厂
Hidden Factory
10 直通合格率
Rolled Throughput Yield
6Sigma概念
AZ
6σ关注于
对什么重要CT’s
内部角度
客户角度
▪ 缺陷 ▪ 利润 ▪ 周期
▪ 质量 ▪ 成本 ▪ 交货期
6Sigma概念
AZ
6σ关注于
• KPOV=一些对过程成功或用户满意最为重要的输出变量;
● 进行现行流程能力的测量
◆ 默认测量系统合格,没有流程能力测量 ◆ 测量系统概念:局限于测量设备、仪表等
● 通过各种统计工具软件,客观分析
P 计划 ◆ 分析思路:以主观为主利用QC的7工具,
筛选出主要输入变量.
找到主要的原因.
(考虑各输入变量的交互作用) A 分析
AZ
控制 KPIVs (保持成果)
6 Sigma 项目以关键营运过程的改善机会为目标,由全职黑带实实施
QFD 项目策划和 管理工具
COQ
过程图 QC七工具 因果关系分析 脑力激荡 FMEA 能力分析 测量系统分析 中央极限定理
多变量分析 假设检验 正态检验 均方差分析 ANOVA 非参数检验 相关性分析 回归分析
六西格玛 简介

六西格玛六西格玛(Six Sigma)又称:6σ,6Sigma,6Σ西格玛(Σ,σ)[2][3]是希腊文的字母,是用来衡量一个总数里标准误差的统计单位。
其含义引申后是指:一般企业的瑕疵率大约是3到4个西格玛,以4西格玛而言,相当于每一百万个机会里,有6210次误差。
如果企业不断追求品质改进,达到6西格玛的程度,绩效就几近于完美地达成顾客要求,在一百万个机会里,只找得出3.4个瑕疪。
(详见右图)六西格玛(6σ)概念作为品质管理概念,最早是由摩托罗拉公司的比尔·史密斯于1986年提出,其目的是设计一个目标:在生产过程中降低产品及流程的缺陷次数,防止产品变异,提升品质。
真正流行并发展起来,是在通用电气公司的实践,即20世纪90年代发展起来的6σ(西格玛)管理是在总结了全面质量管理的成功经验,提炼了其中流程管理技巧的精华和最行之有效的方法,成为一种提高企业业绩与竞争力的管理模式。
该管理法在摩托罗拉、通用电气、戴尔、惠普、西门子、索尼、东芝等众多跨国企业的实践证明是卓有成效的。
为此,国内一些部门和机构在国内企业大力推6σ管理工作,引导企业开展6σ管理。
随着实践的经验积累,它已经从单纯的一个流程优化概念,衍生成为一种管理哲学思想。
它不仅仅是一个衡量业务流程能力的标准,不仅仅是一套业务流程不断优化的方法。
六西格玛的由来六西格玛(Six Sigma)是在20世纪90年代中期开始被GE从一种全面质量管理方法演变成为一个高度有效的企业流程设计、改善和优化的技术,并提供了一系列同等地适用于设计、生产和服务的新产品开发工具。
继而与GE的全球化、服务化、电子商务等战略齐头并进,成为全世界上追求管理卓越性的企业最为重要的战略举措。
六西格玛逐步发展成为以顾客为主体来确定企业战略目标和产品开发设计的标尺,追求持续进步的一种管理哲学。
什么是6σ质量管理方法6σ管理法是一种统计评估法,核心是追求零缺陷生产,防范产品责任风险,降低成本,提高生产率和市场占有率,提高顾客满意度和忠诚度。
六西格玛基本概念工具和方法知识
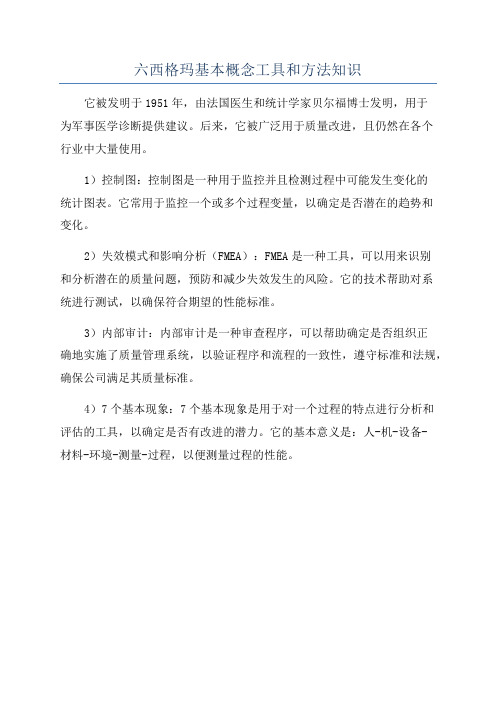
六西格玛基本概念工具和方法知识
它被发明于1951年,由法国医生和统计学家贝尔福博士发明,用于
为军事医学诊断提供建议。
后来,它被广泛用于质量改进,且仍然在各个
行业中大量使用。
1)控制图:控制图是一种用于监控并且检测过程中可能发生变化的
统计图表。
它常用于监控一个或多个过程变量,以确定是否潜在的趋势和
变化。
2)失效模式和影响分析(FMEA):FMEA是一种工具,可以用来识别
和分析潜在的质量问题,预防和减少失效发生的风险。
它的技术帮助对系
统进行测试,以确保符合期望的性能标准。
3)内部审计:内部审计是一种审查程序,可以帮助确定是否组织正
确地实施了质量管理系统,以验证程序和流程的一致性,遵守标准和法规,确保公司满足其质量标准。
4)7个基本现象:7个基本现象是用于对一个过程的特点进行分析和
评估的工具,以确定是否有改进的潜力。
它的基本意义是:人-机-设备-
材料-环境-测量-过程,以便测量过程的性能。
六西格玛(6σ)管理简介(DOC 11页)

六西格玛〔6σ〕治理简介一、 什么是六西格玛〔6σ〕治理?六西格玛是阿拉伯数字6加上希腊字母σ〔西格玛〕。
σ本来是一个反映数据特征的希腊字母,表示数据的标准差。
我们常用下面的计算公式计算σ的大小:1)(12--=∑=n x x n i i σ,式中x i 为样本瞧测值,x 为样本平均值,n 为样本容量。
现在,σ不仅仅是单纯的标准差的含义,而被给予了更新的内容——即成为一种过程质量的衡量标准。
关于任何企业来讲,过程变异根基上他们最大的敌人,因为过多的过程变异会导致产品和效劳无法满足客户的要求,为企业带来损失。
6σ治理能够为企业提供战略方法和相应的工具通过严谨的、系统化以及以数据为依据的解决方案和方法,消除包括从生产到销售、从产品到效劳所有过程中的缺陷,从而改善企业的利润。
那么毕竟什么是6σ呢?我们能够从以下几个方面来讲明6σ的含义。
第一,它是一种衡量的标准。
从统计意义上讲,一个过程具有六西格玛〔西格玛〕能力意味着过程平均值与其规定的规格上下限之间的距离为6倍标准差,现在过程动摇减小,每100万次操作仅有3.4次落在规格上下限以外。
即六西格玛水平意味着过失率仅为百万分之三点四〔即3.4ppm 〕。
因此,它首先是一种度量的标准,能够通过样本的散布情况来衡量系统的稳定性。
6σ的数量越多,产品合格率越高,产品间的一致性越好,或产品的习惯环境的能力越强,产品〔效劳〕的质量就越好。
第二,6σ是一个标杆。
治理学上有一种设定目标的方法确实是根基“标杆法〞,将你的目标设定在你所要超越的对象上,将领先者的水平作为超越的“标杆〞。
6σ也是一个标杆,它的目标确实是根基“零缺陷〞〔过失率百万分子3.4〕。
进行6σ治理确实是根基要以那个目标作为追赶和超越的对象。
第三,6σ是一种方法:“一种基于事实和数据的分析革新方法,其目的是提高企业的收益。
〞那个方法的最大特点确实是根基一切基于事实,一切用数据讲话。
不管是讲明过失的程度,依旧分析缘故,以及检验革新措施的成效,都要用事实和数据讲话,而不是基于主瞧上的想像。
六个西格玛简介

六个西格玛简介我国企业质量管理工作与发达国家比较,一般说来要落后10~15年。
目前,我国企业在统计产品合格率时,仍然采用百分之几的统计方式进行管理,而发达国家采用的是千分之几,高技术产品已按PPM(百万之一)甚至PPb(十亿分之一)和“一次成功”、“一次合格”、“零缺陷”的目标和水平进行管理。
当把“零缺陷”作为追求的目标时,有人也许会问:要使质量百分之百合格的想法是心血来潮吗?多数人都会认为这是荒诞的,但实际上,并不那么容易下判断。
从统计学观点来说,“零缺陷”是没有道理的。
在大公司里,根据大数定律,总会有残次品出现。
另一方面,如果不为百分之百而奋斗,那就是容忍错误,而错误也真的会发生。
比如,“良品率”是生产过程中常用到的一个术语,早在1961年就提出“零缺陷”概念的美国质量管理专家菲利普·克劳斯比说:“当大家都认定在操作过程中无法避免错误的时候,下一步就是制定一个容许错误的数字。
当良品率预定为85%,那便是表示容许15%的错误存在。
采行这种‘良品率管理’的人会告诉你那不是真的,但事实上的确如此。
”为了提高质量,工厂的管理者们发明了“六个西格玛”管理方法。
“西格玛”是统计学里的一个单位,表示与平均值的标准偏差。
它可以用来衡量一个流程的完美程度,显示每100万次操作中发生多少次失误。
“西格玛”的数值越高,失误率就越低。
具体说来,相关数据可以表示如下:1西格玛=690000次失误/百万次操作2西格玛=308000次失误/百万次操作3西格玛=66800次失误/百万次操作4西格玛=6210次失误/百万次操作5西格玛=230次失误/百万次操作6西格玛=3.4次失误/百万次操作7西格玛=0次失误/百万次操作“六个西格玛”是一项以数据为基础,追求几乎完美无暇的质量管理办法。
20世纪80年代末至90年代初,摩托罗拉公司首倡这种办法,花10年时间达到6西格玛水平。
但如果是生产一种由1万个部件或程序组成的产品,即使达到了6西格玛水平,也还有3%多一点的缺陷率;实际上,每生产1万件产品,将会有337处缺陷。
6Sigma全套工具
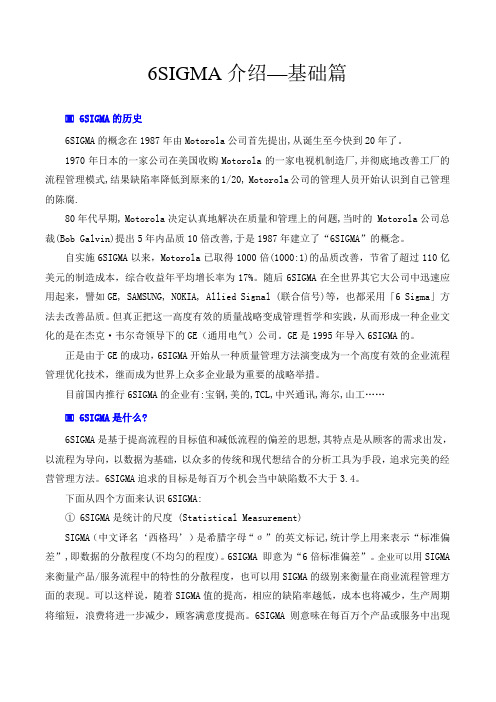
6SIGMA介绍—基础篇▣6SIGMA的历史6SIGMA的概念在1987年由Motorola公司首先提出,从诞生至今快到20年了。
1970年日本的一家公司在美国收购Motorola的一家电视机制造厂,并彻底地改善工厂的流程管理模式,结果缺陷率降低到原来的1/20, Motorola公司的管理人员开始认识到自己管理的陈腐.80年代早期, Motorola决定认真地解决在质量和管理上的问题,当时的 Motorola公司总裁(Bob Galvin)提出5年内品质10倍改善,于是1987年建立了“6SIGMA”的概念。
自实施6SIGMA以来,Motorola已取得1000倍(1000:1)的品质改善,节省了超过110亿美元的制造成本,综合收益年平均增长率为17%。
随后6SIGMA在全世界其它大公司中迅速应用起来,譬如GE, SAMSUNG, NOKIA, Allied Signal (联合信号)等,也都采用「6 Sigma」方法去改善品质。
但真正把这一高度有效的质量战略变成管理哲学和实践,从而形成一种企业文化的是在杰克·韦尔奇领导下的GE(通用电气)公司。
GE是1995年导入6SIGMA的。
正是由于GE的成功,6SIGMA开始从一种质量管理方法演变成为一个高度有效的企业流程管理优化技术,继而成为世界上众多企业最为重要的战略举措。
目前国内推行6SIGMA的企业有:宝钢,美的,TCL,中兴通讯,海尔,山工……▣6SIGMA是什么?6SIGMA是基于提高流程的目标值和减低流程的偏差的思想,其特点是从顾客的需求出发,以流程为导向,以数据为基础,以众多的传统和现代想结合的分析工具为手段,追求完美的经营管理方法。
6SIGMA追求的目标是每百万个机会当中缺陷数不大于3.4。
下面从四个方面来认识6SIGMA:① 6SIGMA是统计的尺度 (Statistical Measurement)SIGMA(中文译名‘西格玛’)是希腊字母“σ”的英文标记,统计学上用来表示“标准偏差”,即数据的分散程度(不均匀的程度)。
- 1、下载文档前请自行甄别文档内容的完整性,平台不提供额外的编辑、内容补充、找答案等附加服务。
- 2、"仅部分预览"的文档,不可在线预览部分如存在完整性等问题,可反馈申请退款(可完整预览的文档不适用该条件!)。
- 3、如文档侵犯您的权益,请联系客服反馈,我们会尽快为您处理(人工客服工作时间:9:00-18:30)。
FMEA和FTA分析故障模式与影响分析(FMEA)和故障树分析(FTA)均是在可靠性工程中已广泛应用的分析技术,国外已将这些技术成功地应用来解决各种质量问题。
在ISO 9004:2000版标准中,已将FMEA和FTA分析作为对设计和开发以及产品和过程的确认和更改进行风险评估的方法。
我国目前基本上仅将FMEA与FTA技术应用于可靠性设计分析,根据国外文献资料和我国部分企业技术人员的实践,FMEA 和FTA可以应用于过程(工艺)分析和质量问题的分析。
质量是一个内涵很广的概念,可靠性是其中一个方面。
通过FMEA和FTA分析,找出了影响产品质量和可靠性的各种潜在的质量问题和故障模式及其原因(包括设计缺陷、工艺问题、环境因素、老化、磨损和加工误差等),经采取设计和工艺的纠正措施,提高了产品的质量和抗各种干扰的能力。
根据文献报道,某世界级的汽车公司大约50%的质量改进是通过FMEA 和FTA/ETA来实现的。
Kano模型日本质量专家Kano把质量依照顾客的感受及满足顾客需求的程度分成三种质量:理所当然质量、期望质量和魅力质量(如下图)A:理所当然质量。
当其特性不充足(不满足顾客需求)时,顾客很不满意;当其特性充足(满足顾客需求)时,无所谓满意不满意,顾客充其量是满意。
B:期望质量也有称为一元质量。
当其特性不充足时,顾客很不满意,充足时,顾客就满意。
越不充足越不满意,越充足越满意。
C:魅力质量。
当其特性不充足时,并且是无关紧要的特性,则顾客无所谓,当其特性充足时,顾客就十分满意。
理所当然的质量是基线质量,是最基本的需求满足。
期望质量是质量的常见形式。
魅力质量是质量的竞争性元素。
通常有以下特点:具有全新的功能,以前从未出现过;性能极大提高;引进一种以前没有见过甚至没考虑过的新机制,顾客忠诚度得到了极大的提高;一种非常新颖的风格。
Kano模型三种质量的划分,为6Sigma改进提高了方向。
如果是理所当然质量,就要保证基本质量特性符合规格(标准),实现满足顾客的基本要求,项目团队应集中在怎样降低故障出现率上;如果是期望质量,项目团队关心的就不是符合不符合规格(标准)问题,而是怎样提高规格(标准)本身。
不断提高质量特性,促进顾客满意度的提升;如果是魅力质量,则需要通过满足顾客潜在需求,使产品或服务达到意想不到的新质量。
项目团队应关注的是如何在维持前两个质量的基础上,探究顾客需求,创造新产品和增加意想不到的新质量。
POKA-YOKEPOKA-YOKE意为“防差错系统”。
日本的质量管理专家、著名的丰田生产体系创建人新江滋生(Shingeo Shingo)先生根据其长期从事现场质量改进的丰富经验,首创了POKA-YOKE的概念,并将其发展成为用以获得零缺陷,最终免除质量检验的工具。
POKA-YOKE的基本理念主要有如下三个月:⑴决不允许哪怕一点点缺陷产品出现,要想成为世界的企业,不仅在观念上,而且必须在实际上达到“0”缺陷。
⑵生产现场是一个复杂的环境,每一天的每一件事都可能出现,差错导致缺陷,缺陷导致顾客不满和资源浪费。
⑶我们不可能消除差错,但是必须及时发现和立即纠正,防止差错形成缺陷。
质量功能展开(QFD)质量功能展开(Quality Function Deployment, 缩写为QFD)是把顾客或市场的要求转化为设计要求、零部件特性、工艺要求、生产要求的多层次演绎分析方法,它体现了以市场为导向,以顾客要求为产品开发唯一依据的指导思想。
在健壮设计的方法体系中,质量功能展开技术占有举足轻重的地位,它是开展健壮设计的先导步骤,可以确定产品研制的关键环节、关键的零部件和关键工艺,从而为稳定性优化设计的具体实施指出了方向,确定了对象。
它使产品的全部研制活动与满足顾客的要求紧密联系,从而增强了产品的市场竞争能力,保证产品开发一次成功。
根据文献报道,运用QFD方法,产品开发周期可缩短三分之一,成本可减少二分之一,质量大幅度提高,产量成倍增加。
质量功能展开在美国民用工业和国防工业已达到十分普及的程度,不仅应用于具体产品开发和质量改进,还被各大公司用作质量方针展开和工程管理目标的展开等。
2000版ISO 9000系列标准要求“以顾客为关注焦点”,“确保顾客的要求得到确定并予以满足”,作为分析展开顾客需求的质量功能展开方法必将在2000版ISO 9000系列标准的贯彻实施中获得广泛的应用。
QFD是客户需求与技术规范的桥梁。
SOW工作说明(Statement Of Work,缩写为SOW)是合同的附件之一,具有与合同正文同等的法律效力。
工作说明详细规定了合同双方在合同期内应完成的工作,如方案论证、设计、分析、试验、质量控制,可靠性、维修性、保障性、标准化、计量保证等;应向对方提供的项目,如接口控制文件、硬件、计算机软件、技术报告、图纸、资料,以及何时进行何种评审等,因此,工作说明以契约性文件的形式进一步明确了顾客的要求和承制方为实现顾客要求必须开展的工作,它使产品的管理和质量保证建立在法律依据之上,成为合同甲方(顾客)对乙方(承制单位)进行质量监控的有力工具。
工作说明的详细要求可查阅GJB 2742-96。
工作说明的内容是质量功能展开的重要输入。
WBS工作分解结构(Work Breakdown Structures,缩写为WBS)是对武器装备项目在研制和生产过程中应完成的工作自上而下逐级分解所形成的一个层次体系。
该层次体系以要研制和生产的产品为中心,由产品(硬件和软件)项目、服务项目和资料项目组成。
WBS是通过系统工程工作而形成的,它显示并确定了武器装备项目的工作,并表示出各项工作之间以及它们与最终产品之间的关系,充分体现了系统的整体性、有序性(层次性)和相关性。
GJB2116-94给出了WBS的典型发展过程及编制的基本要求,并在附录中提供了七类武器系统的纲要WBS。
在质量功能展开和系统设计等工作中应用WBS的层次体系,参照GJB2116-94给出的纲要WBS,将极大地方便产品功能、结构和研制工作的构思,有助于QFD和系统设计等工作的完成,也有助于工作说明(SOW)的编制。
WBS 是对武器装备研制实施系统工程管理的有效工具,也是设计完整性的保证。
WBS的原理和思想,也同样适用于各种大型、复杂、高科技的民用产品。
并行工程并行工程(Concurrent Engineering)是对于产品和其有关的过程(包括制造和保障过程)进行并行设计的一种系统的综合方法,它要求研制者从一开始就考虑整个产品寿命周期(从概念形成到产品报废处置)中的全部要素,包括质量、成本、进度及顾客需求。
并行工程要求特别重视源头设计,在设计的开始阶段,就设法把产品开发所需的所有信息进行综合考虑,把许多学科专家的经验和智慧汇集在一起,融为一体。
下图是串行工程与并行工程的比较示意图。
发散思维发散思维又称求异思维、辐射思维,是指从一个目标出发,沿着各种不同的途径去思考,探求多种答案的思维,与聚合思维相对。
不少心理学家认为,发散思维是创造性思维的最主要的特点,是测定创造力的主要标志之一。
美国心理学家吉尔福特认为,发散思维具有:流畅性、灵活性、独创性三个主要特点。
流畅性是指智力活动灵敏迅速,畅通少阻,能在较短时间内发表较多观念,是发散思维的量的指标;灵活性是指思维具有多方指向,触类旁通,随机应变,不受功能固着、定势的约束,因而能产生超常的构思,提出不同凡响的新观念;独创性是指思维具有超乎寻常的新异的成分,因此它更多表证发散思维的本质。
可以通过从不同方面思考同一问题,如“一题多解”、“一事多写”、“一物多用”等方式,培养发散思维能力。
显然T并<T串。
据文献报导,贯彻并行工程,研制周期将缩短40-60%,生产初期的工程更改减少50%以上,制造费用降低30-40%,报废和返工减少75%。
在健壮设计中,尤其在进行质量功能展开和系统设计时,必须贯彻并行工程的原理和指导思想。
参数设计参数设计(Parameter Design)在系统设计之后进行。
参数设计的基本思想是通过选择系统中所有参数(包括原材料、零件、元件等)的最佳水平组合,从而尽量减少外部、内部和产品间三种干扰的影响,使所设计的产品质量特性波动小,稳定性好。
另外,在参数设计阶段,一般选用能满足使用环境条件的最低质量等级的元件和性价比高的加工精度来进行设计,使产品的质量和成本两方面均得到改善。
参数设计是一个多因素选优问题。
由于要考虑三种干扰对产品质量特性值波动的影响,探求抗干扰性能好的设计方案,因此参数设计比正交试验设计要复杂得多。
田口博士采用内侧正交表和外侧正交表直积来安排试验方案,用信噪比作为产品质量特性的稳定性指标来进行统计分析。
为什么即使采用质量等级不高、波动较大的元件,通过参数设计,系统的功能仍十分稳定呢?这是因为参数设计利用了非线性效应。
通常产品质量特性值y与某些元部件参数的水平之间存在着非线性关系,假如某一产品输出特性值为y,目标值为m,选用的某元件参数为x,其波动范围为D x(一般呈正态分布),若参数x取水平x1,由于波动D x,引起y的波动为D y1(如图),通过参数设计,将x1移到x2,此时同样的波动范围Δx,引起y的波动范围缩小成D y2,由于非线性效应十分明显,D y2<D y1,由此可见,只要合理地选择参数的水平,在参数的波动范围不变的条件下,(也就意味着不增加成本),就可以大大减少质量特性值y的波动范围,从而提高了产品的稳定性。
但与此同时,却发生了新的矛盾,这就是y的目标值从m移到了m¢,偏离量Δm= m¢-m。
如何使y保持稳定,而又不偏离目标值呢?这时,可设法找一个与输出特性y呈线性关系,且易于调整的元器件参数z(调整因素),即y=a+bz,只要把z从z1调到z2,即可补偿偏离量Δm。
如果不采用参数设计,利用非线性关系,而是按传统方法直接进行容差设计,把元件x由较低质量等级改为很高质量等级,也就是说将参数x 的波动范围由Δx缩小为Δx1,而对应于水平x1的质量特性y的波动范围变为Δy3,虽然Δy3<Δy1,但这是以增加成本为代价而取得的;而且可能仍然是Δy3>Δy2,即提高了元件质量等级后,对应于x1的产品质量特性y的波动范围仍然比采用较低质量等级元件、对应于水平x2的y波动范围D y2要宽,由此可以看出参数设计的优越性。
图:参数设计的非线性效应图参数设计可以分为静态特性的参数设计和动态特性的参数设计。
方差分析方差分析(Analysis of Variance, 缩写为ANOVA)是数理统计学中常用的数据处理方法之一,是工农业生产和科学研究中分析试验数据的一种有效的工具。
也是开展试验设计、参数设计和容差设计的数学基础。