染色一次成功率
细菌简单染色法注意事项
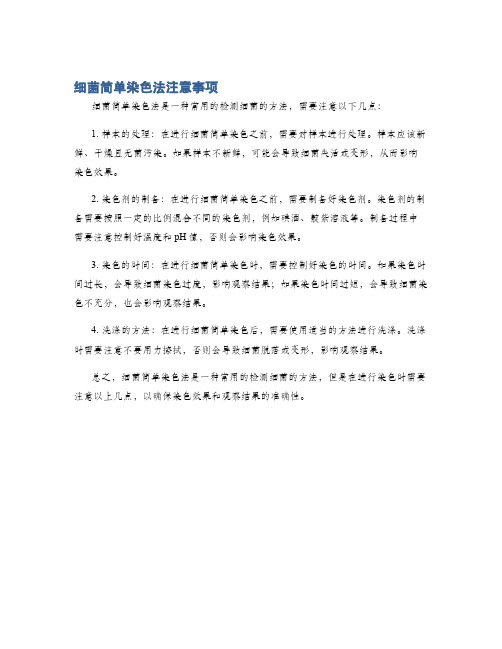
细菌简单染色法注意事项
细菌简单染色法是一种常用的检测细菌的方法,需要注意以下几点:
1. 样本的处理:在进行细菌简单染色之前,需要对样本进行处理。
样本应该新鲜、干燥且无菌污染。
如果样本不新鲜,可能会导致细菌失活或变形,从而影响染色效果。
2. 染色剂的制备:在进行细菌简单染色之前,需要制备好染色剂。
染色剂的制备需要按照一定的比例混合不同的染色剂,例如碘酒、靛紫溶液等。
制备过程中需要注意控制好温度和pH值,否则会影响染色效果。
3. 染色的时间:在进行细菌简单染色时,需要控制好染色的时间。
如果染色时间过长,会导致细菌染色过度,影响观察结果;如果染色时间过短,会导致细菌染色不充分,也会影响观察结果。
4. 洗涤的方法:在进行细菌简单染色后,需要使用适当的方法进行洗涤。
洗涤时需要注意不要用力擦拭,否则会导致细菌脱落或变形,影响观察结果。
总之,细菌简单染色法是一种常用的检测细菌的方法,但是在进行染色时需要注意以上几点,以确保染色效果和观察结果的准确性。
多段发一次性染色的原理知识美发师要想染好颜色必看

多段发一次性染色的原理知识美发师要想染好颜色必看多段色一次性释放就是不管它是一段色、两段色、三段色等都可以做到一次性释放,想要做到多段色一次性释放就要先了解到它的公式,与公式中每一种色膏的用量和运用。
公式是:目标色+目标色同度基色+目标色加强色+加强蓝+双氧。
首先我们先来了解一下目标色:目标色就是既顾客意向所需的颜色,以及最终呈现的一个颜色。
例:6/45、5/66等。
目标色的用量是根据客人头发的多少薄于厚来决定的。
目标色同度基色:基色即麦拉,它在公式中起到的作用是弥补双氧在提浅发色时所残缺的麦拉宁色素,给予头发光泽度、饱满度,使目标色更加完美的呈现。
例:2/0、3/0、4/0、5/0、6/0、7/0、8/0这些只有色度没有色调的都是基色。
基色的用量是根据头发最浅的位置和目标色相差的度数来决定的,一般分为3种,浅染深、同度染、深染浅。
深染浅或同度染加的同度基色都是为10%,浅染深相差一度加20%同度基色,相差2度加30%同度基色。
如果相差2度以上需要对最浅的位置打底,用目标色低一度染膏加9度奶加水,比例1:1:1,等15-20分钟,只需要涂抹发尾最浅的位置,不需要洗头,只需要吧对于的染膏刮掉就好。
目标色加强色:加强色它是一个只有色调没有色度的一个颜色,纯度非常高,一般不建议单独使用,因为它的覆盖率仅仅只有10%,它在公式中起到的作用是弥补双氧在提浅发色时目标色所流失的彩度,双氧浓度越高它所流失的色素就越多,在目标色中加入少量的加强色会使目标色更加纯正,也展现了更好的出彩率。
例:0/11、0/22、0/33、0/43、0/45、0/66、0/88国际代码:1灰、2紫、3黄、4橙、5褐、6红、7绿、8蓝国内代码:1灰、2绿、3黄、4铜、5红、6紫、7棕、8蓝这些只有色调没有色度的都叫加强色。
加强色的用量是根据双氧的浓度越高加的量越多,因为双氧里含的是二氧化氢,我们双氧浓度越高,它的养含量也就越大,目标色流失的色素也就越多,加的加强色越多。
怎样染色才能让丝光羊毛纱线一次成功或提高它的成功率

怎样染色才能让丝光羊毛纱线一次成功或提高它的成功率1丝光羊毛特性羊毛的丝光处理,即防缩处理,主要是通过对毛条或毛纱的特殊处理,提高羊毛产品的防缩性能,获得良好的尺寸稳定性和如蚕丝一般的光泽和手感。
目前宏其化工处理的方法主要有3类:化学降解法(氧化法),聚合物沉积法(树脂法),酶处理法。
氧化法指通过氧化剂的氧化作用,部分或全部剥蚀羊毛的鳞片层。
树脂法指在羊毛的表面施以高分子聚合物,使之沉积在羊毛纤维表面,限制和制约纤维的相对运动。
酶处理法指通过蛋白酶与羊毛鳞片层中蛋白质大分子作用,部分剥蚀羊毛的鳞片层。
无论是通过氧化法、树脂法、酶处理法或三者联合处理过的羊毛,与常规未处理的羊毛相比较,有5个特性:①防缩性能提高;②对染料的亲和力提高;③纤维的pH值降低;④羊毛的手感变滑,光泽变亮;⑤染色的色牢度降低。
2提高染色的砌玎系统工程经过丝光处理后的毛纱,对染料的吸附性能提高以及纤维pH值降低的特性,增大了染色色花的机率;由于丝光羊毛产品多数是机可洗产品,染色色牢度降低的特性使要满足国际羊毛局对机可洗产品的高色牢度要求变的更难。
要一次成功的生产出色泽均匀、色牢度良好、满足机可洗要求的染色产品,对于丝光毛纱的染色提出了更高的要求。
提高丝光羊毛纱线染色的RFT是一个系统工程,该工程包括纱线前处理、染色、后处理等与染色相关的工艺过程,以及所有参与人员和相应的全部物资资源如羊毛固色剂、羊毛匀染剂等。
要实现这个系统工程,正确仿样是前提,稳定生产是关键,二者的联结点是大小样的符样率。
3正确仿样客户确认和车间顺利生产是正确仿样的两大目的。
二者均要兼顾,不能偏重一面。
只求客户确认,不顾车间生产的可行性;只顾大生产的需要,而忽视客户的要求都是不可取的。
4客户确认为了得到客户的确认,要关注以下5点:①客户使用的对色光源。
客户一般不特别提出,通常使用D65光源;如果使用双光源,应特别注意灯光跳色现象,及时与客户沟通相关情况。
②客户对水洗、摩擦、耐氯、耐汗光等色牢度的要求和其他环保要求,尤其是针对特殊用途的产品对色牢度的不同要求。
染色车间一次成功率讨论

染色一次成功率讨论
染色一次成功率
ENTERPOINT管理系统是针对印染行业开发的管理系统。
其主要目的,为企业搭建一个信息管理平台,简化企业内部的管理流程,提高实际管理能力,加强各部门的沟通。
我们从几个方面讨论一下,ENTERPOINT是如何提高企业的染色一次成功率:
1.从原材料的质量上进行控制,我们对每一次染料和白坯的入库进行质量检验,当发
现质量问题时,及时进行反馈。
避免因原材料的质量问题而影响生产的成功。
最后需要反复回修才能达到预先的色泽要求。
2.进行虚拟库存管理,根据订单进行选纱,既每个订单的白坯领用只能选纱进行出库,
这样可以尽量避免在领纱时发生的混批现象,提高车间的一次成功率。
3.在车间实施计件工资和奖惩制度。
清晰的工资制度,提高员工的工作积极性和责任
心。
4.明确的交接班记录,避免交接不清,造成生产过失。
其目的为提高车间的生产成功
率。
5.提供半成品检验,既络筒完成后的质量检验。
尽量保证纱线入缸前达到质量要求,
从而提高生产一次成功率。
6.在车间内,有准确的生产质量报表,统计前段时间的质量情况,找出前段时间哪些
工序、染缸有严重质量问题的原因,方便以后的在那些环境做着重控制,提高生产一次成功率。
7.工艺处方方面,包括小样中样等。
大幅度提高活性染料染色一次成功率

随着社会的进步,生活水平的提高,人们对穿着的舒适性要求进一步提高,全棉、棉混纺、再生纤维素纤维及其混纺针织物越来越受到人们的青睐,其天然舒适亲肤、吸湿、排汗、防静电、可降解等优点深受人们喜欢,并呵护着人们的身体健康。
2021年这类面料占面料总用量的58.2%,并且还有进一步扩大的趋势。
随着国家节能环保、低碳生活的推进,结合目前面料市场的激烈竞争,我们自主研发了一种智能型全自动染色复板设备(型号RF6P600C ),配合专业的技术配套方案,有效地解决了(再生)纤维素纤维面料用活性染料染色一次成功率偏低的难题,配套染厂科学的管理系统,一次成功率能达到90%以上,基本可以实现“盲染”。
1活性染料的染色机理及影响因素活性染料(reactive dyes )又叫反应性染料,是分子中含有化学性活泼的基团,能在水溶液中与棉、毛等纤维反应形成共价键结合的染料,具有较高的耐洗色牢度。
活性染料由母体染料、连接基、活性基组成,使其在使用时能与纤维形成牢固的共价键结合。
1.1活性染料染色机理1.1.1活性染料的上染上染是指活性染料从染液中被吸附到纤维上,并在纤维上均匀扩散,纤维和溶液间的染料浓度达到平衡的过程。
活性染料在上染过程中,同样存在着大幅度提高活性染料染色一次成功率的设备及方法摘要:分析了活性染料染色一次成功率低的原因,并对相关影响因素进行了分析。
研究开发了相应的染色复板设备(型号RF6P600C ),并提供了相应的解决方案。
结果表明,严格按标准流程操作,一次成功率可以达到90%以上,基本可以实现“盲染”,大大提高生产效率,具有节能减排的作用。
关键词:活性染料;染色;一次成功率;复板设备中图分类号:TS193.5文献标志码:B 文章编号:1005-9350(2022)12-0020-04Abstract:The reasons for the low success rate of dyeing with reactive dyes are analyzed,and the relevant influenc⁃ing factors are analyzed,and the corresponding dyeing cladding equipment (model RF6P600C)is developed to provide a corresponding solution.The results show that the one-time success rate can reach more than 90%by strictly following the standard process,which can basically achieve “blind dyeing ”,greatly improve production efficiency,and play a role in en⁃ergy conservation and emission reduction.Key words:reactive dyes;dyeing;one-time success rate;cladding equipmentEquipment and method for greatly improving the dyeing one-time success rate of reactive dye收稿日期:2022-04-02作者简介:张新文(1969—),男,广东广州人,高级工程师,本科,研究方向为染整工艺技术,从事印染厂管理。
活性染料的配伍性

1.08
1.06 1.04
◆ ◆
1.02
■ ■
Integ 值
1.00 0.98
■◆ ◆ ■
0.96
■
0.94
◆
0.92
0.90
0.88
40
50
60
70
80
元明粉用量/(g·L-1)
1.10
◆
1.05
◆ ■
■
1.00
■◆
■
0.95
■
◆
Integ 值
0.90
◆
0.85
0.80
10
15
20
25
30
纯碱用量/(g·L-1)
染料
S值
E值
F值
R值
黄 3RS
79
95
79
59
红 3BS
69
92
75
51
深蓝 2GLN
78
93
77
65
黄 EDN
73
93
83
63
红 EDN
71
94
85
65
藏青 EDN
70
92
84
64
注:染料用量 1.0%(omf)。
2.3 温度 、时间 、浴比 、盐碱用量变化的影响[10] 以上两个工具基本可以选择出一组配伍性好的
Abstract The reactive dye matching dyeing of cellulose fiber, especially man-made cellulose fiber fabric, requires high compatibility of dyes. The dyestuffs with good compatibility can greatly improve the first pass rate and fabric quality of factory products, and ensure the reproducibility of products. In order to select the compatibility of three primary colors of reactive dyes, or to verify the compatibility of three primary colors, the dye uptake curve, S, E, R, F values of dyes, the sensitivity of dyes to temperature, time, bath ratio, sodium sulfate dosage, soda dosage and other factors in the dyeing process, and the color fastness of dyes were selected as indexes.
免疫组化染色常见问题及解释
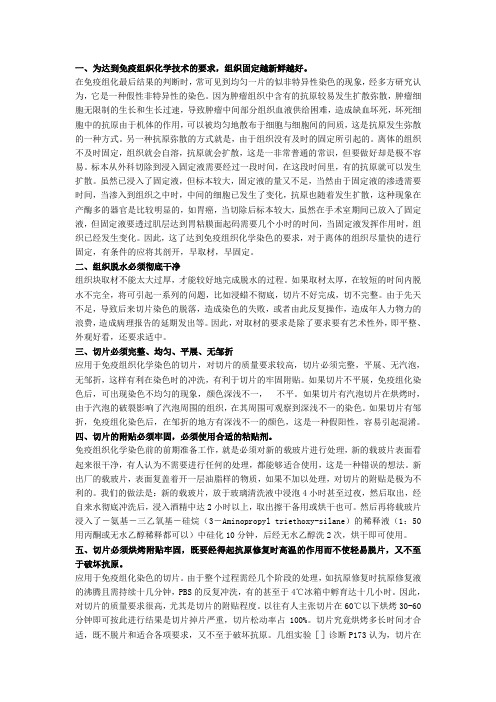
一、为达到免疫组织化学技术的要求,组织固定越新鲜越好。
在免疫组化最后结果的判断时,常可见到均匀一片的似非特异性染色的现象,经多方研究认为,它是一种假性非特异性的染色。
因为肿瘤组织中含有的抗原较易发生扩散弥散,肿瘤细胞无限制的生长和生长过速,导致肿瘤中间部分组织血液供给困难,造成缺血坏死,坏死细胞中的抗原由于机体的作用,可以被均匀地散布于细胞与细胞间的间质,这是抗原发生弥散的一种方式。
另一种抗原弥散的方式就是,由于组织没有及时的固定所引起的。
离体的组织不及时固定,组织就会自溶,抗原就会扩散,这是一非常普通的常识,但要做好却是极不容易。
标本从外科切除到浸入固定液需要经过一段时间,在这段时间里,有的抗原就可以发生扩散。
虽然已浸入了固定液,但标本较大,固定液的量又不足,当然由于固定液的渗透需要时间,当渗入到组织之中时,中间的细胞已发生了变化,抗原也随着发生扩散,这种现象在产酶多的器官是比较明显的,如胃癌,当切除后标本较大,虽然在手术室期间已放入了固定液,但固定液要透过肌层达到胃粘膜面起码需要几个小时的时间,当固定液发挥作用时,组织已经发生变化。
因此,这了达到免疫组织化学染色的要求,对于离体的组织尽量快的进行固定,有条件的应将其剖开,早取材,早固定。
二、组织脱水必须彻底干净组织块取材不能太大过厚,才能较好地完成脱水的过程。
如果取材太厚,在较短的时间内脱水不完全,将可引起一系列的问题,比如浸蜡不彻底,切片不好完成,切不完整。
由于先天不足,导致后来切片染色的脱落,造成染色的失败,或者由此反复操作,造成年人力物力的浪费,造成病理报告的延期发出等。
因此,对取材的要求是除了要求要有艺术性外,即平整、外观好看,还要求适中。
三、切片必须完整、均匀、平展、无邹折应用于免疫组织化学染色的切片,对切片的质量要求较高,切片必须完整,平展、无汽泡,无邹折,这样有利在染色时的冲洗,有利于切片的牢固附贴。
如果切片不平展,免疫组化染色后,可出现染色不均匀的现象,颜色深浅不一,不平。
从ITMA 2019看印染装备的发展
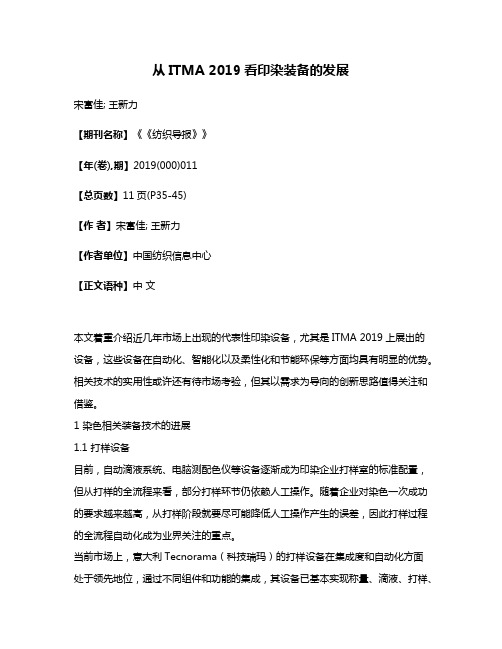
从ITMA 2019看印染装备的发展宋富佳; 王新力【期刊名称】《《纺织导报》》【年(卷),期】2019(000)011【总页数】11页(P35-45)【作者】宋富佳; 王新力【作者单位】中国纺织信息中心【正文语种】中文本文着重介绍近几年市场上出现的代表性印染设备,尤其是ITMA 2019上展出的设备,这些设备在自动化、智能化以及柔性化和节能环保等方面均具有明显的优势。
相关技术的实用性或许还有待市场考验,但其以需求为导向的创新思路值得关注和借鉴。
1 染色相关装备技术的进展1.1 打样设备目前,自动滴液系统、电脑测配色仪等设备逐渐成为印染企业打样室的标准配置,但从打样的全流程来看,部分打样环节仍依赖人工操作。
随着企业对染色一次成功的要求越来越高,从打样阶段就要尽可能降低人工操作产生的误差,因此打样过程的全流程自动化成为业界关注的重点。
当前市场上,意大利Tecnorama(科技瑞玛)的打样设备在集成度和自动化方面处于领先地位,通过不同组件和功能的集成,其设备已基本实现称量、滴液、打样、染色过程监控的自动化,另外,在产品的适用性方面也具有明显的优势。
科技瑞玛在ITMA 2019上展出的Dos&Dye® Compact化验室自动管理系统可用于制作生产所用的样本及相应配方。
该系统包括1台自动配料机和1台自动印色机,染色机配有多个染色单元,每个单元均可独立工作,执行不同的染色工艺。
该系统适用于机织物、针织物、筒纱、散纤维等的染色打样,适用范围非常广泛。
这种特殊的系统可以完成以下项目:用分装装置自动配置染液;自动更换和补充失效或用尽的染液和清洗瓶子;将染液直接分配到染缸中;采用机器手搬运瓶子、粉末分配罐和布料架。
这套系统在管理打样流程时不需要人工干预,可避免工作过程中的人为失误,且可以在无人情况下长时间持续工作。
数据显示,该机可提高打样效率50%,减少50%的打样成本,并且能够将大货重现性提高1倍,极大地提高染色一次成功率。
Freefit面料开发ok[1]
![Freefit面料开发ok[1]](https://img.taocdn.com/s3/m/7d043637a32d7375a4178022.png)
课题名称:Freefit面料开发开发背景:1.Freefit面料的手感柔软,弹性适中,吸湿、透气性好,穿着舒适。
是衬衫用弹性面料的上佳选择。
2.由于XLA的生产供应出现问题,Freefit面料作为XLA面料的替代品,使得我们对其研究与开发迫在眉睫。
与XLA面料的对比分析:1.弹性比较XLA弹力面料:15%~20%弹性FREEFIT面料:15%~25%弹性FREEFI面料为棉包氨纶丝的一种面料,其弹性较大,适合做高弹力产品。
2.表观对比棉包XLA与棉包氨纶丝的异同处:用手扯纱线棉包XLA表现出棉、丝同时断的现象而棉包氨纶则是棉断丝不断,氨纶丝表现出很大的弹性空间。
这一现象说明棉包氨纶纤维潜在弹性大,必须选定合适的工艺参数,既要能保证弹性损失在要求的范围内,又要保证筒子纱染色的质量,满足色织布面料的质量要求。
为了使面料的弹性在20%以上,纱线潜在弹性要控制在25%左右。
3..我们对原纱、增白纱、染色纱的潜在弹性分别做了测试对比,验证了纱线的潜在弹性与漂染的染色工艺的关系:通过测试:原纱的潜在弹性约为36%增白纱的潜在弹性约为35%、染色纱的潜在弹性约为20-25%。
从而我们得出了以下结论:即深浅色染色工艺对潜在弹性的影响不同,但可满足面料弹性的需求。
确定研究的关键点:纱线在漂染工序合理的生产流程和染色工艺是关键所在1.筒子纱的内外差及所需要挑疵纱的数量。
2.筒子纱的染色不匀问题3.大小样的重现性(染色一次合格率)4.界定纱线定型的方式,确定生产流程和染色工艺采取的措施:1、首先与技术研发中心配合,借鉴原料厂家提供的技术资料结合研发中心下发试验订单,采用预定型的工艺,提前对原纱进行定型,防止纱线在染色过程中出现大幅度收缩现象。
采用的定型工艺:135度*20分钟采用的生产流程:松式络筒→定型→烘干→松式络筒→前处理→染色(增白)2.同时与纱线事业部、研发中心一道试验了不同的蒸纱、煮纱工艺,验证纱线的定型程度与染色的一次成功率和筒子纱的内外质量的关系。
提高针织物绳状染色的一次性成功率
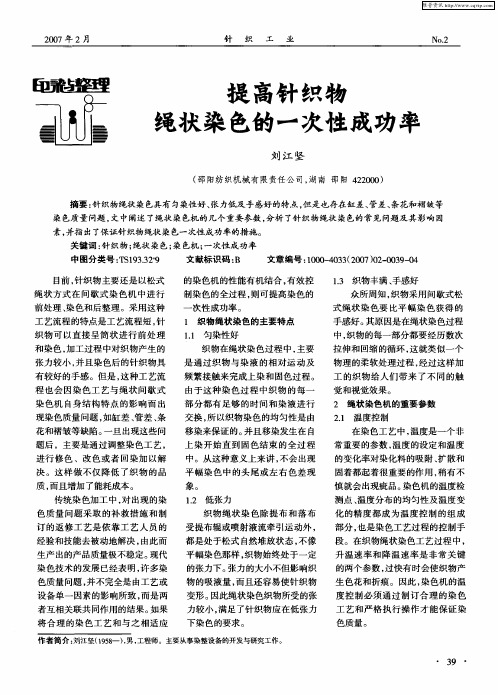
实 现分 时间 、 阶段 、 量 和注 人 分 计 速度控制 , 被染织物在最短 时间 让
内达到匀染 。 通常是将编好的程序
写人 到染色工艺 中去 , 由染 色机 的
相关控制 系统 自动完成 。
2 浴 比控制 I 4 浴 比是被 染 物 的重量 与 染液
短 的时 间内达 到一致 , 就成 为设 备
维普资讯
20 0 7年 2月
针 织 工 业
No2 .
提 高针 织物 绳状 柒 色的 一次性 成功 率
刘 江 坚
( 阳纺 织机械 有限责任 公司 , 邵 湖南 邵 阳 4 2 0 ) 2 00
摘要 : 针织物绳状染 色具有匀染性好 、 张力低及手感好 的特 点, 但是也存在缸 差、 管差、 条花和褶皱等
绳状 方式 在 间歇式 染 色机 中进 行
文献标 识码 : B
文章 编号 :0 0 4 3 (0 7 0 — 0 9 0 10 — 0 3 2 0 )2 0 3 —4 1 织 物丰满 、 - 3 手感好 众所周知 , 织物 采用间歇式松
式绳 状染 色要 比平 幅染 色 获得 的
的染色机 的性能有 机结 合 , 有效控 制染色 的全过程 , 可提高染 色的 则
上 染开 始直 到 固色结 束 的全 过程 中。从 这种意义上来讲 , 不会 出现
平 幅染 色 中数 , 温度 的设定 和温度 的变化率对染化料 的吸附 、 扩散 和
进行 修色 、改 色或 者 回染加 以解 决 。这 样 做不 仅降 低 了织 物 的品 质, 而且增加 了能耗成本 。
次性成功率 。
1 织物绳状染色的主要特点 1 匀染性好 . 1 织 物在 绳状染色过程 中 , 主要
提高纱线染色一次成功率
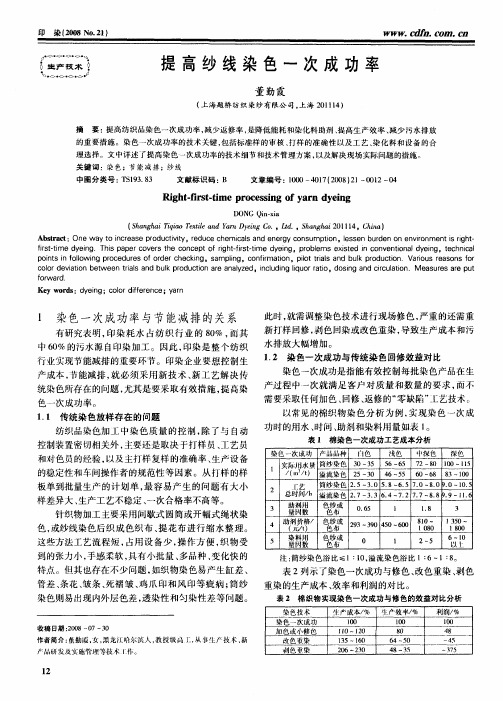
板单到批量生产 的计划单 , 最容易产 生的问题 有大小 样差异大 、 生产工艺不稳定 、 一次合格率不高等。
针 织物 加工 主要采 用 间歇式 圆筒 或开 幅式 绳 状染
2 5~3 0 5. . 8~6 5 . . 7 O~8 O 9 0~ l 5 . . 0. 』艺 筒纱染 色 . 二 总 时 间/ 溢流染色 . 3 3 6 4~ . . 8 899~l. h 2 7~ . . 7 2 7 7~ . . I6
印
染 (0 8N . 1 20 o2 )
WWW. . 0 0 珊. D C
≤ 差 圣圣 兰≥
提高纱线染色一次成功率
董 勤霞
( 上海题桥 纺织染纱有 限公 司, 上海 2 1 1 ) 0 14
摘 要 : 提高纺织 品染色一次成功率 , 减少返修率 , 是降低 能耗 和染化料助剂 、 提高生产效率 、 减少污水排放 的重要措施 。染色一 次成 功率的技术关键 , 括标 准样 的审核 、 包 打样的准确性 以及工艺 、 染化料 和设 备的合 理选择。文中详述了提高染色 一次成功率 的技术 细节 和技术管理方案 , 以及解决现场实际问题的措施
l 染色一次成功率与节能减排 的关系
此时 , 就需调 整染 色技 术进行 现场 修 色 , 重 的还需 重 严
剥 导致 生 产成 本 和污 有研究表明, 印染耗水 占纺织行业的 8 % , 0 而其 新 打样 回修 , 色 回染或 改 色重染 , 中 6 % 的污水 源 自印染 加 工 。 因此 , 0 印染 是 整 个 纺织 水排 放大 幅增加 。 12 染色一 次成 功与 传统染 色 回修效益对 比 . ห้องสมุดไป่ตู้业实现节能减排的重要环节。印染企业要想控制生 产成本 , 能减 排 , 必 须采 用 新 技 术 、 工 艺 解 决 传 节 就 新 染色 一次成功 是指 能有效 控制 每批 染 色产 品在 生 产过 程 中一次就 满 足 客 户对 质 量 和 数 量 的要 求 , 不 而
影响染色一次成功率的因素—前处理篇
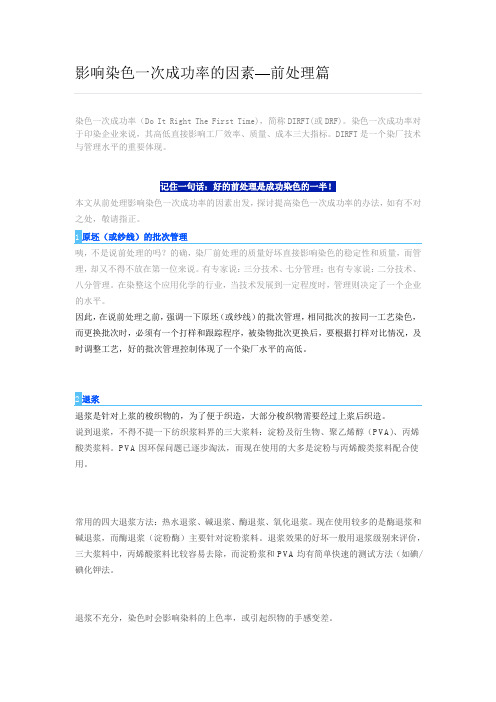
影响染色一次成功率的因素—前处理篇染色一次成功率(Do It Right The First Time),简称DIRFT(或DRF)。
染色一次成功率对于印染企业来说,其高低直接影响工厂效率、质量、成本三大指标。
DIRFT是一个染厂技术与管理水平的重要体现。
本文从前处理影响染色一次成功率的因素出发,探讨提高染色一次成功率的办法,如有不对之处,敬请指正。
1原坯(或纱线)的批次管理咦,不是说前处理的吗?的确,染厂前处理的质量好坏直接影响染色的稳定性和质量,而管理,却又不得不放在第一位来说。
有专家说:三分技术、七分管理;也有专家说:二分技术、八分管理。
在染整这个应用化学的行业,当技术发展到一定程度时,管理则决定了一个企业的水平。
因此,在说前处理之前,强调一下原坯(或纱线)的批次管理,相同批次的按同一工艺染色,而更换批次时,必须有一个打样和跟踪程序,被染物批次更换后,要根据打样对比情况,及时调整工艺,好的批次管理控制体现了一个染厂水平的高低。
2退浆退浆是针对上浆的梭织物的,为了便于织造,大部分梭织物需要经过上浆后织造。
说到退浆,不得不提一下纺织浆料界的三大浆料:淀粉及衍生物、聚乙烯醇(PVA)、丙烯酸类浆料。
PVA因环保问题已逐步淘汰,而现在使用的大多是淀粉与丙烯酸类浆料配合使用。
常用的四大退浆方法:热水退浆、碱退浆、酶退浆、氧化退浆。
现在使用较多的是酶退浆和碱退浆,而酶退浆(淀粉酶)主要针对淀粉浆料。
退浆效果的好坏一般用退浆级别来评价,三大浆料中,丙烯酸浆料比较容易去除,而淀粉浆和PVA均有简单快速的测试方法(如碘/碘化钾法。
退浆不充分,染色时会影响染料的上色率,或引起织物的手感变差。
3去油去油主要针对化纤类织物(或纱线),比如涤纶、锦纶等,去油不干净同样影响染料的上色和会造成油斑、色斑等问题。
去油一般在碱性条件下加去油剂高温进行,好的去油剂的选择有助有提高去油效果。
现在为了优化工艺流程,适用于化纤类的去油染色同浴也很多,选择的时候注意同浴去油剂的耐高温性能和分散性能。
提高丝光羊毛纱线染色的一次成功率
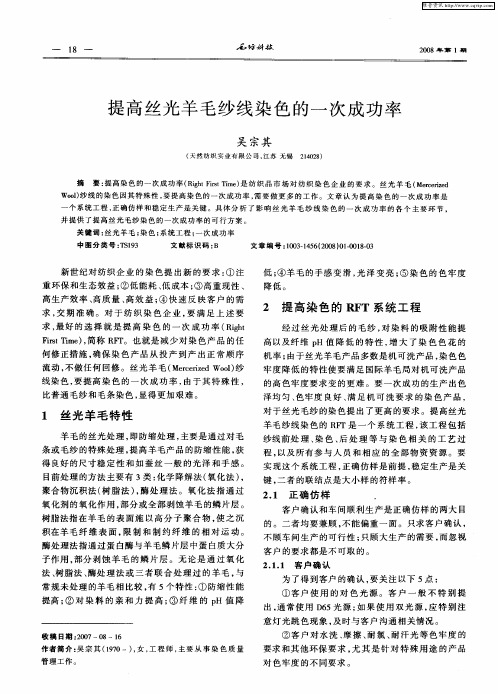
客户确 认 和车间顺 利生 产是正 确仿 样 的两 大 目 的 。二者均 要兼 顾 , 能偏重 一 面 。只求 客户 确认 , 不
不顾 车间 生产 的可行性 ; 只顾 大 生 产 的需 要 , 忽 视 而
1 丝 光 羊毛 特 性
羊 毛 的丝 光处理 , 防缩处理 , 即 主要是 通过 对毛 条 或毛纱 的特殊 处理 , 提高 羊毛产 品 的防缩性 能 , 获 得 良好 的尺寸稳 定 性 和如 蚕 丝 一般 的光 泽 和手 感 。 目前处理 的方法 主要 有 3类 : 化学 降解法 ( 氧化法 ) ,
聚合物沉 积法 ( 脂法 ) 酶 处 理法 。氧 化 法 指通 过 树 ,
氧 化剂 的氧化作 用 , 分或 全部剥 蚀羊 毛 的鳞 片层 。 部
2 1 正 确 仿 样 .
.
树脂 法指 在羊 毛 的表 面施 以高 分 子 聚合 物 , 之沉 使 积在 羊毛 纤 维 表 面 , 制 和 制 约 纤 维 的 相 对 运 动 。 限
并 提供 了提 高 丝 光 毛 纱 染 色 的 一 次 成功 率 的可 行 方 案 。
关键 词 : 光 羊 毛 ; 色 ; 统 工 程 ; 次 成 功 率 丝 染 系 一 中 图分 类 号 :S 9 T 13 文 献 标 识 码 : B 文 章 编 号 :0 3 15 I 0 8 0 .0 8 3 10 .4 6 2 0 ) 1 1. 0 0
客户 的要求 都是 不可取 的。
2 1 1 客 户 确 认 ..
法、 树脂 法 、 酶处 理 法或 三 者 联 合处 理 过 的 羊毛 , 与
影响染色一次成功率的因素——化验室篇

染整百科———您手机上的染整百科全书!染色一次成功率(Do It Right The First Time),简称DIRFT。
染色一次成功率对于印染企业来说,其高低直接影响工厂效率、质量、成本三大指标。
DIRFT 是一个染厂技术与管理水平的重要体现。
本文从化验室影响染色一次成功率的因素出发,探讨提高染色一次成功率的办法,如有不对之处,敬请指正:从管理角度讲,化验室打样的各种条件力求做到与车间大生产仿样,化验室打样工作是为车间服务的,不是要车间按照化验室的条件去生产,而是化验室在打样时要力求模仿车间的各种条件。
化验室做的再精密,不能有效的为车间提供数据和工艺支撑,那么化验室的价值也就无从体现。
作为染色三要素(温度、时间、水量)之一的温度,化验室在对温度的控制,表现在对大货生产的影响,主要有以下几点:1、小样机温度表与车间大生产温度表的统一与校正小样机的温度表一般对电阻传感器式,车间染色机温度表一般为双金属温度计,因小样机与车间染色机的生产厂家不同,需要对化验室温度计与车间进行统一与校正,这是化验室与车间仿样一致性的前提。
具体校正方法本文不再赘述。
2、皂煮、还原清洗等温度控制要模仿车间很多染厂化验室打样时,染色肯定是小样机控制,而皂煮、还原清洗等操作很多是在电炉或电磁炉上操作的,很多化验室打样员在皂煮时会有把水煮沸的习惯,认为煮沸了才是皂煮,笔者认为这一点是错误的,车间在皂煮或还原清洗时,温度一般设置为95℃,而化验室煮沸操作时,水温接近100℃,那么皂煮条件不同,得到的颜色肯定是有差异的。
比如,活性染料染浅色,按照化验室的工艺放样下去,车间老是染深,而且煮不下来,很多工艺主管会摸索出一个参数,下大货工艺时,下调10-20%的染料,而不去追查上缸染深的原因。
有条件的工厂,建议皂煮、还原清洗等,也在单独的小样机内操作,以达到小样与大样的温度统一。
1、化验室打样用的坯布一定要与车间大货需要染色的坯布一致,不同批次的坯布上色肯定存在差异。
2007年中国国际染整新技术暨染色一次成功率论坛成功召开

效 率 2 主题 , 国 际上 不 断更新 的环 保 染 整新 技 术 和企 业 急 需提 高的 染 色一 次 成功 率 技 术 个 对
进 行 交流 和研 讨 。
在 国际环保 染整 新技术 分 会场 , 内外专 家 针对今 年 6 1日起 执行 的 欧盟 R A H法 规 国 月 EC 的重 点和热 点 问题进 行分 析述 评 , 出 了 中国纺 织 企 业如 何 适 应 和应 对 国 际环 保 新 要 求 的方 提
支持。
代表们 对专 家 的报告 给予 了很 大 的关注 和肯 定 , 现场交 流 咨询 气氛热 烈 , 坛取 得 了圆满 论
法 和措 施 。为我 国纺 织染 整行业 运用 国际高新 技 术实 现高效 生 态 的染整 生产 提 出 了新 的发 展 思路 和实 现方法 。在 染色一 次 成功率 分 会场 中 , 自染 色 生产 企 业 的染 整专 家 , 对纺 织 品 、 来 针
针 织 品染 色 中的色变 、 花和 色牢度 问题 、 高染 色一 次成 功率 的生 产工艺 和 生 产管 理 问题 进 色 提
维普资讯 http:Байду номын сангаас/
・
18 ・ 0
统 [] 纺织 学 报 ,012 ( )3 —3 . J. 20 ,2 3 :0 1
纺织 学 报
国 纺织 出 版 社 ,0 5 8 9 . 20 : 4— 5
第2 8卷
[ 王 鸿 博 . 杆 织 机 实用 技 术 [ . 京 : 国 纺 织 出 版 2] 剑 M] 北 中
由 中国纺 织 工程 学 会 、 国纺 织信 息 中 心主 办 , 国纺 织工 程 学 会咨 询 部 、 国纺 织工 程 中 中 中 学 会染 整专 业 委员会 、 国印染 科 技信 息 中心 、 港 雅式 出版 有 限 公 司 承办 的 2 0 全 香 0 7年 中 国 国 际染 整新技 术 暨染 色一 次成 功 率论坛 5月 底在 杭州 圆满 落幕 。来 自国 内外 的纺 织染 整 行业 代 表 共 计 2 0名 出席 大会 , 7 中国纺 织工 程学 会毕 国典 常务 副理 事长 在会 上做 了重 要讲话 。
八大因素决定染色一次性成功率
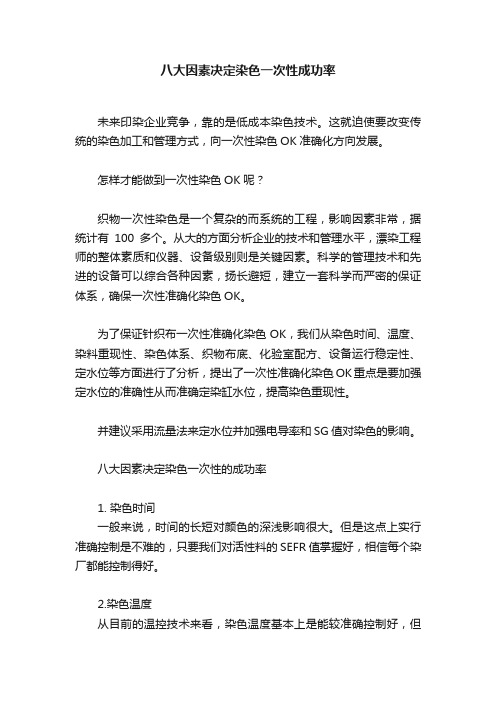
八大因素决定染色一次性成功率未来印染企业竞争,靠的是低成本染色技术。
这就迫使要改变传统的染色加工和管理方式,向一次性染色OK准确化方向发展。
怎样才能做到一次性染色OK呢?织物一次性染色是一个复杂的而系统的工程,影响因素非常,据统计有100多个。
从大的方面分析企业的技术和管理水平,漂染工程师的整体素质和仪器、设备级别则是关键因素。
科学的管理技术和先进的设备可以综合各种因素,扬长避短,建立一套科学而严密的保证体系,确保一次性准确化染色OK。
为了保证针织布一次性准确化染色OK,我们从染色时间、温度、染料重现性、染色体系、织物布底、化验室配方、设备运行稳定性、定水位等方面进行了分析,提出了一次性准确化染色OK重点是要加强定水位的准确性从而准确定染缸水位,提高染色重现性。
并建议采用流量法来定水位并加强电导率和SG值对染色的影响。
八大因素决定染色一次性的成功率1. 染色时间一般来说,时间的长短对颜色的深浅影响很大。
但是这点上实行准确控制是不难的,只要我们对活性料的SEFR值掌握好,相信每个染厂都能控制得好。
2.染色温度从目前的温控技术来看,染色温度基本上是能较准确控制好,但存在整体液体的温度是否平均问题,因为现在的染色普遍存在个“成本压力”;所以一般500P以下的缸都会在20min升到100℃左右,升温速率是如此之快.但热传递需要一定的时间才能完成的,基于这个问题在理论和实践中都容易把握好,因而在染色设备的设计上,这对矛盾是可以解决的。
3. 染料的稳定程度(即重现性的好坏)对于这个问题,我们在做染色直通时必须要考虑,它是我们一次性染色成功的重要参考因素,但我们只是作为参考染料重现性能的好坏,这点可以由染料公司研究解决,在这里就不作详细解说。
4. 色体系在活性料染色时,我们的染色体系中有大量的电解质、碱剂、各种类型表面活性剂等各种助剂在染色体系中的SG值(密度值)和电导率对一次性染色成功率影响很大。
但各类助剂的质量我们在收货时已经监控,只要是助剂质量的稳定性把关好,其它事宜应由助剂供应商来处理了。
毛料染色疵点分析与控制考核试卷
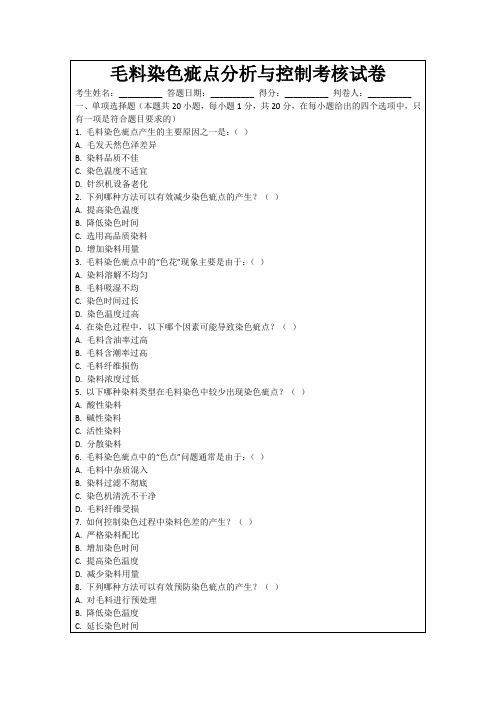
5.毛料染色疵点中的“色渍”主要是由于染色过程中染料在毛料上______造成的。
6.提高染色色牢度的方法包括:选用高色牢度染料、控制染色______和______、后处理等。
7.在染色前对毛料进行预处理,可以提高毛料的______和______,从而提高染色效果。
D.毛料纤维受损
14.在染色疵点的预防和控制中,以下哪些做法是有效的?()
A.对染料进行预溶解处理
B.保持染色设备的清洁
C.避免在染色过程中频繁开关染缸
D.选用适合的染料
15.以下哪些条件会影响毛料染色的均匀性?()
A.毛料的含潮率
B.染料的扩散性能
C.染色时间
D.染色温度
16.以下哪些方法可以用来检测毛料染色后的色牢度?()
毛料染色疵点分析与控制考核试卷
考生姓名:__________答题日期:__________得分:__________判卷人:__________
一、单项选择题(本题共20小题,每小题1分,共20分,在每小题给出的四个选项中,只有一项是符合题目要求的)
1.毛料染色疵点产生的主要原因之一是:()
A.毛发天然色泽差异
A.优化染料配方
B.改进染色工艺
C.使用助剂提高匀染性
D.减少染色过程中的机械操作
12.毛料染色疵点中,以下哪些属于色斑疵点的原因?()
A.毛料中的杂质
B.染料未能充分溶解
C.染色机清洗不彻底
D.毛料吸色不均匀
13.以下哪些因素可能导致染色后的毛料手感不佳?()
A.染料固色率过高
B.毛料含油率过低
C.染色过程中温度控制不当
- 1、下载文档前请自行甄别文档内容的完整性,平台不提供额外的编辑、内容补充、找答案等附加服务。
- 2、"仅部分预览"的文档,不可在线预览部分如存在完整性等问题,可反馈申请退款(可完整预览的文档不适用该条件!)。
- 3、如文档侵犯您的权益,请联系客服反馈,我们会尽快为您处理(人工客服工作时间:9:00-18:30)。
生产技术提高纱线染色一次成功率1染色一次成功率与节能减排的关系有研究表明,印染耗水占纺织行业的80%,而其中60%的污水源自印染加工。
因此,印染是整个纺织行业实现节能减排的重要环节。
印染企业要想控制生产成本,节能减排,就必须采用新技术、新工艺解决传统染色所存在的问题,尤其是要采取有效措施,提高染色一次成功率。
1.1传统染色放样存在的问题纺织品染色加工中染色质量的控制,除了与自动控制装置密切相关外,主要还是取决于打样员、工艺员和对色员的经验,以及主打样复样的准确率、生产设备的稳定性和车间操作者的规范性等因素。
从打样的样板单到批量生产的计划单,最容易产生的问题有大小样差异大、生产工艺不稳定、一次合格率不高等。
针织物加工主要采用间歇式圆筒或开幅式绳状染色,或纱线染色后织成色织布、提花布进行缩水整理。
这些方法工艺流程短,占用设备少,操作方便,织物受到的张力小,手感柔软,具有小批量、多品种、变化快的特点。
但其也存在不少问题,如织物染色易产生缸差、管差、条花、皱条、死褶皱、鸡爪印和风印等疵病;筒纱染色则易出现内外层色差,透染性和匀染性差等问题。
此时,就需调整染色技术进行现场修色,严重的还需重新打样回修,剥色回染或改色重染,导致生产成本和污水排放大幅增加。
1.2染色一次成功与传统染色回修效益对比染色一次成功是指能有效控制每批染色产品在生产过程中一次就满足客户对质量和数量的要求,而不需要采取任何加色、回修、返修的“零缺陷”工艺技术。
以常见的棉织物染色分析为例,实现染色一次成功时的用水、时间、助剂和染料用量如表1。
表2列示了染色一次成功与修色、改色重染、剥色重染的生产成本、效率和利润的对比。
注:以实现染色一次成功的经济技术指标为基准。
1.2.1不排液加色由表1、表2可知,与染色一次成功相比,不排液加色的总用水量和助剂用量基本不变,但染色总时间增加30~50 min,染料用量增加5%~20%。
1.2.2改色重染与染色一次成功相比,改色重染的总用水量、染料用量和耗时均增加2倍,助剂用量增加1.5 ~2.0倍。
此外,其还需要重新脱水烘干,造成能源、人工、设备效率的进一步浪费。
1.2.3剥色重染与染色一次成功相比,剥色重染的总用水量增加1.5~2.5倍,总时长增加1.5~3.0倍,染料用量增加2倍,助剂用量增加2.0~2.5倍,且其还需再重新脱水烘干,耗能耗时。
从以上分析可以看出,提高染色一次成功率,减少加色、修色,对于印染企业节能减排、降低生产成本、提高经济效益非常有效。
2染色一次成功率的技术关键实现染色一次成功,需要选择生产稳定、重现性好,适用的染料、助剂,并建立“零缺陷”的管理体系。
该体系包括建立完善的作业指导标准和染色工艺跟踪监督抽查方法;要求染色加工工艺所有参数在线管理记录;建立坯布、水、染色助剂、酸、碱、盐的控制核算方法,以及染色产品质量控制标准等。
现代化印染企业普遍使用电脑测配色系统、自动配料加料机和自动复样机,实现生产过程自动化和电脑管理现代化,为提高打样、复样、放样及生产染色一次合格率提供了充分的“硬件”条件。
然而,更重要的是,还必须提高工艺设计水平、员工素质、打样复样的准确性和生产放样一次成功率与在线重现性。
[pagebreak]2.1审单、打样及管理工作2.1.1标准样的审核标准样是指客户来样分析。
分析内容主要包括原料组分和色光评定的标准光源,织物的克重、规格,染色牢度有无特殊要求,强力、缩水率等物理指标要求,以及有无特殊后整理要求等。
必须仔细阅读客户来单要求,以充分了解客户需求,制定具体技术方案。
在审单中,对于常规品种,接单后可转入打色样程序。
对于特殊品种,如高支高密、轻薄型、新纤维产品和以前未做过的品种,必须进行先期生产小样试验,以确保各项物理指标基本符合客户要求,并验证大生产的可行性。
当幅宽、克重或单染的混纺产品不能满足客户要求时,应积极采取对应措施。
同时,还要主动与客户沟通,尽量满足客户需求,迅速好打手板样提供给客户。
对于明确提出技术要求的订单,应在满足客户要求的同时,考虑本企业的技术水平和生产能力。
无明确要求的单子,一般按照国家标准安排生产。
对于有特殊品质要求和功能整理要求的订单,在没有充分把握时,都必须做先锋生产试验,以确保产品品质的质量指标和交货期。
客户标样注意保存完好,不能直接见光和暴晒,也不能沾污变色。
对色光源要定期校正,统一采用标准光源箱的光源对色。
因为不同灯箱的内壁颜色不同,折射到样纱、样布上会引起对色不准;灯管中的荧光材料不同,对于同一块布的反射光谱也不同,从而显示出色光差异。
因此,无论化验室还是车间,都必须与客户的对色光源一致。
当客户只要求单一光源时,如CWF、TL84、D65等,最好也能在其它相关光源(日光灯、自然光等)下对色测试,以避免在不同光源下存在“跳灯”现象。
2.1.2确定生产工艺根据企业设备确定生产工艺。
打样时,按照大生产工艺设备,正确选择染化料和工艺流程。
打样条件尽可能与染色工艺生产条件保持一致;复样、放样与大生产所使用的染料、助剂和被染织物一定要一致;所确定的工艺流程、工艺条件不能随意改变;染料用量可根据大小样的实践经验及使用设备的特点规律进行微调。
2.1.3染料和助剂的选择根据客户标样对染色深度、色光偏向、色泽鲜艳度和染色牢度等要求,按照配伍性能选用染化料。
染料选择原则:(1)深、浓色选择高力分、高上染率、高湿摩擦牢度的染料。
(2)浅、中色选择高匀染性、高染色牢度的染料。
(3)耐汗渍牢度、耐氯漂牢度、耐日晒牢度要求高的,可选择进口的特殊染料。
(4)耐干洗牢度要求高的,选择耐有机溶剂染料。
(5)染后丝光的品种,选择耐碱染料。
(6)纱线染色,为防止色织产品搭色,应选择耐水洗牢度好的染料。
(7)染后需高温定形的色织面料,为防止“飞色”,应选择耐高温染料。
助剂选择原则:匀染性好、渗透性强,助染性好、不影响染色色光。
2.1.4打样操作的准确性(1)染化料称重与配液,采用高精度电子天平,减少染化料称重的系统误差。
(2)复样所用的染化料必须与大生产所使用的染化料批号一致,注意染料不要受潮。
(3)化料方法要保持一致,根据染料的性能采用不同的化料方法。
如X型活性染料于30℃温水化料,其它类型活性染料于50~60℃热水化料;分散染料用40~50℃水调浆,加入分散剂均匀分散后,再加水不断搅拌均匀;阳离子染料用HAc调成浆状,再用100℃热水冲至无沉淀为止;酸性染料用常温水调成浆状,再用沸水冲至充分溶解,加水后,染液应处于常温状态。
(4)吸料操作采用自动滴料机滴料准确性很高,没有条件的可采用吸管,但操作一定要正确。
对于配好的染液,用磁力棒不断搅拌,防止部分染料聚集或者沉淀。
为提高打样、复样的准确率,最好采用每天配制的新染液,以防止染料沉淀和空气氧化。
(5)打样操作被染物应准确称量。
注意染色时一定要湿进纱或布,严格按照工艺要求控制温度、时间。
皂洗应按照生产工艺和打样条件,确定快速皂洗的调整值。
(6)一般情况下,一定要经过复样后再大生产。
对于不再复样的小缸染色直开的配方和复样的配方,要注意打样被染物与生产被染物必须一致。
2.1.5对色目光的一致性(1)对打样员、复样员、对色员、调色员和质检员定期进行色彩敏感度检查和目光的对光培训,对于色盲、色弱、色不清、色不准的人员,应及时调整岗位。
(2)对存在阶段性、疲劳性色弱,及对黄色和红色阶段性疲劳的员工,应作适当调整。
2.2色样确认与不确认的问题分析2.2.1色样确认(1)首先进行手板样评价。
用灰色样卡对色,原样与小样之间要求达到4~5级以上。
(2)用电脑对色时,一般ΔE<1,考虑系统误差时,内控标准ΔE应在0.6以下。
对于要求高的客户,应将色相(ΔH)和色彩度(ΔC)考虑在内。
(3)正确理解客户对小样的确认意见。
为了使客户早日确认下单,当客户意见与实际自测情况不一致时,首先分析光源是否搞错,然后及时与客户沟通确认。
如果“跳灯”严重,应考虑调换染料予以改善。
平时要熟悉染料的“同色异谱”,积累经验,为挑选染料做好基础工作。
2.2.2色样不确认根据标样和客户要求,打好的小样通常需要经过客户确认。
在确认过程中,有时会出现多次不确认情况。
此时,技术人员一定要配合销售员与客户直接沟通,确定其原因。
复样与生产时,引起大小样色差的因素主要有:(1)原材料小样仿色后,需客户确认。
因为小样与打样不会在同一时期生产,将造成所用染化料、坯布批号的差异,必须重新复样后再生产。
(2)水质有些小企业采用软化水打样,而实际生产用自来水、地下水或未处理的河水,因水质硬度高,不符合染色要求。
(3)染色设备升温、保温、浴比和染液循环不稳定,而造成生产波动。
(4)工艺参数计量如温度、压力、扬程和循环流量等计量不准确。
2.3放样前的准确复样客户确认的处方未经复样不能投产,这是提高染色一次成功率的原则。
复样工作必须安排打样经验丰富、出样准确性高的复样员专人负责;不宜安排原来的打样员复样。
因为经过不同复样员复样,易出现染料配伍不当,助剂使用有误,打样方式方法不对,染色配方或记录误差等问题。
必须采用生产车间准备大生产投产的半制品进行复样。
复样所用染料和助剂等必须与生产车间一致,不能使用打样间库存料。
复样必须落实审核制度,复好的样和配方需经主管签字确认无差错,方能开单。
复样后,配方卡上除了要贴好客户确认样、复好的样,还需贴上复样时的留白样、单染样,以便放样员随时检查对照待染半制品与复样半制品的相符性,以确保放样的准确性。
2.4放样试生产生产配方一定是经过放样和复样主管签字确认的配方,否则车间可拒绝放样生产。
要严格按照设定的工艺曲线、时间、温度和加料方式放样。
3放样和大生产工艺技术管理措施3.1制定合理的工艺3.1.1染色温度控制温度在染色过程中是一个非常重要的参数。
升温速率、保温时间和降温速率直接影响染料的吸附、上染、扩散和固色,若控制不当,会产生色花、色差和褶痕等瑕疵。
同时,亦应检查染色设备温度的检测点是否合理,温度扩散是否均匀,温度变化是否灵敏等。
操作工严格执行工艺规定,才能保证染色合格率。
3.1.2染色时间控制染色时间需根据所选择染料的染色性能、配伍性能、织物品种以及染色温度而确定。
[pagebreak]3.1.3织物运行速度一般来说,染液与织物的交换次数越高,被染物匀染性越好。
但随着染液循环和织物速度提高,织物受到的张力加大,经向拉伸加大,导致缩水率和尺寸稳定性下降。
所以,织物运行速度控制要合理。
3.1.4浴比控制原则上,浴比越大,越不容易产生色花和褶皱,但染化料和水电汽的消耗量和排污量随之加大,与节能降耗原则相违背。
从成本考虑,实际生产中选择小浴比更合理。
只要采用合理的染色技术,使设备性能得到精确控制,小浴比染色是能够顺利进行的。