国内外合成氨原料气精制工艺技术发展
国内外合成氨原料气精制工艺技术发展

国内外合成氨原料气精制工艺技术发展南京国昌化工科技有限公司1.引言在合成氨工业中,经过脱碳工艺处理后的合成氨原料气中仍含有0.5~3% CO和0.5%~1%CO2,必须进一步处理将其降低至10ppm左右,以保护氨合成催剂,这一原料气精制工艺过程俗称“精炼”,目前合成氨厂脱除微量CO、CO2的方法大体分为热法和冷法两类。
冷法工艺即液氮洗涤法,近年来国内外新建的大型氨厂大多采用此法;而热法工艺门类较多,包括传统的醋酸铜氨液洗涤法(铜洗法)、低压甲烷化法、甲醇甲烷化法和分子筛变压吸附法等。
总体上讲冷法工艺技术先进、净化度很高,但投资巨大;而热法工艺技术相对简单成熟、投资低,但在净化度方面不及冷法。
热法中的铜洗工艺更因其能耗高、净化度低、污染大等诸多缺点而逐渐被其他先进的工艺方法所替代。
2. 国外合成氨原料气精制工艺发展2.1 铜洗法醋酸铜氨液洗涤法(简称铜洗)是最古老的方法。
早在1913年就开始应用,迄今有近一百年的历史,操作压力为15Mpa。
铜洗法以其工艺成熟、操作弹性大,长期在中小型合成氨厂占据主导地位。
随着技术的进步,铜洗法精制原料气与其它方法相比,缺点越来越突出。
主要表现在运行、维修、操作费用高,物料消耗大(消耗铜、醋酸、液氨、蒸汽)、根据国内氨厂实际情况测算,吨氨需要增加成本在50~80元,而且精制度低,一般净化后的CO+CO≥25ppm,然而其最致命2的缺陷还在于环境污染严重。
由于铜洗再生气经水洗涤产生铜洗稀氨水,其浓度视所采用的洗涤技术不同而不同,一般在1~3%左右。
中型氮肥厂每小时约产生,所以采用一般的提浓方法都由于10吨废水,这股废水除含有氨外,还含有CO2容易生成碳铵引起管道堵塞而无法处理,为此要么采用铜洗再生氨直接放空,要么就是铜洗稀氨水排放。
这不但浪费了宝贵的资源,也引起了大气或水环境的严重污染。
此外生产过程中经常出现严重的铜液泄漏,这些弊端与现代化高效、洁净的生产理念极不相适应。
合成氨工艺发展

③Braun公司的深冷净化工艺 针对传统天然气合 成氨流程中,燃料天然气消耗过大的问题,布朗
工艺采用了减少一段炉负荷、增大二段转化炉的
负荷的办法。由于二段炉采用绝热式催化反应器,
热效率高于一段转化炉效率,因此可以节省一段
转化炉的燃,必须添加过量空气以满足自热重整的需
后来在我国的川化和泽普的20万t/a装置上 使用,其工艺流程与经典的二段蒸汽转化
工艺相近。该工艺的特点是通过提高造气
转化压力,平衡一、二段转化炉负荷,改
进换热和冷量利用,减少合成回路循环比
和完善蒸汽系统等措施,使燃料消耗下降 50%,动力消耗降低23%,[wiki]冷却 [/wiki]水循环量下降37%,综合能耗下降 到28.4-30.0GJ/t。② Topsoe公司的低能 耗工艺 与凯洛格工艺不同,该工艺流程采
合成氨工艺发展
一:以煤为原料的[wiki]合成氨[/wiki]工艺。 各种工艺流程的区别主要在煤气化过程。典型 的大型煤气[wiki]化工[/wiki]艺主要包括固定 床碎煤加压气化工艺、德士古水煤浆加压气化 工艺以及壳牌干煤粉加压气化工艺。①固定床 碎煤气化 固定床碎煤加压气化,以鲁奇炉为代 表,是指一定粒度范围(5。50mm)的碎煤, 在1.0。3.0MPa的压力下与气化剂逆流气化的 反应过程。碎煤加压气化最先由德国 鲁奇公司
LCA工艺 1988年英国ICI公司提出了技术概念上 领先的合成氨工艺(LCA)。其主要特点是采用新 型的催化剂,一段转化水碳比为2.5。采用转化器 (GHR)代替结构复杂、体积庞大以[wiki]辐射 [/wiki]传热为主的一段转化炉,在转化器中,二 段转化气返回一段转化炉的表程提供一段转化炉 所需热量。采用水冷列管式变换炉代替传统流程 高、低变换炉。采用分子筛变压吸附工艺脱除过 量的氮以及[wiki]二氧化碳[/wiki]、一氧化碳、 甲烷及氩,流程中采用较少的传动设备,用电机 驱动机[wiki]泵[/wiki]。
合成氨的生产工艺的现状及发展趋势的探讨

合成氨的生产工艺的现状及发展趋势的探讨摘要:本文通过对合成氨的工艺流程和发展情况对合成氨的生产工艺的现状及发展趋势进行阐述。
关键词:合成氨生产工艺现状发展合成氨指由氮和氢在高温高压和催化剂存在下直接合成的氨。
别名氨气,生产合成氨的主要原料有天然气、石脑油、重质油和煤(或焦炭)等。
随着科学技术的发展和能源危机的加重,合成氨得到了迅猛的发展。
如今,我国的合成氨量已跃居世界首位,合成氨有着巨大的发展空间。
因此,合成氨的生产工艺也在不断的发展和更新,如今的合成氨生产工艺已经完全脱离了传统的模式,氨合成装置向着单系列、大型化、节能型方向发展,装置和合成工艺技术及流程的改进大大提高了氨合成转化率。
一、我国合成氨的生产工艺的现状目前我国是世界上合成氨量最大的国家,拥有大型氮肥装置共计三十四套,有十七套以天燃气为原料,六套以轻油为原料,九套以重油为原料,还有两套以煤为原料。
这三十四套大型氨肥装置每年可以生产大约一千万吨氨肥,其下游产品主要包括了硝酸磷肥和尿素。
除此之外,我国还有五十五套中型合成氨装置,包括三十四套以煤和焦油为原料的装置,九套以渣油为原料和十二套以气为原料的装置。
这五十五套中型合成氨装置年生产能力约为五百万吨,下游产品主要是尿素和硝酸铵,我国还有一百一十二套经过改造生产尿素,原料以煤,焦炭为主的氨合成装置。
其中以煤,焦炭为原料的占96%,以气为原料的仅占4%。
二、合成氨的生产工艺的流程不同的生产原料采用不同的生产工艺,比如以煤和天燃气为原料的氨合成,通常是采用原料气制备将原料制成含氢和氮的粗原料气。
对以煤和焦炭等固体原料的氨合成,通常采用气化的方法制取合成气;对于以渣油为原料的氨合成一般采用非催化部分氧化的方法;对气态烃类和石脑油,工业中一般采用二段蒸汽转化法。
合成氨原料气制备完成后一般要进行净化处理,净化处理的主要目的是除去氢气和氮气以外的杂质,主要包括变换过程、脱硫脱碳过程以及气体精制过程;净化首先包括进行一氧化碳变换,因为在合成氨的过程中不论采用哪种方式都会产生一氧化碳,这是合成氨中多余的成分,因此要对其清除。
浅谈合成氨原料气精制工艺的发展
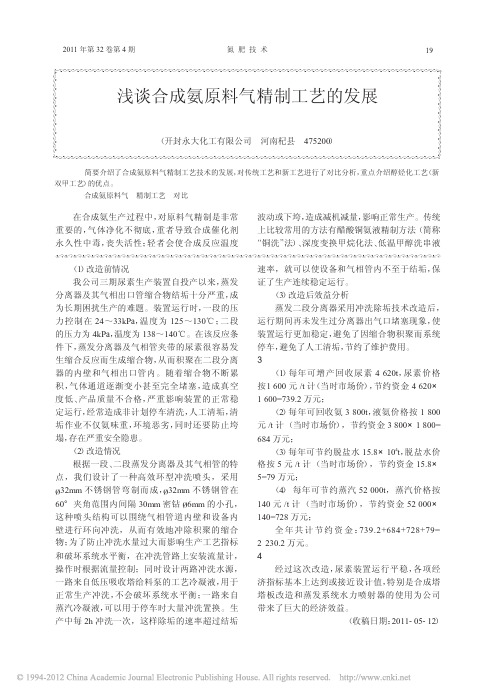
25.0
原料气精制后含 CO 的体积分数 (×10-6) 6.0 以下
原料气精制后含 CO2 的体积分数 (×10-6) 0.017 以下
蒸汽冷凝液,可以用于停车时大量冲洗置换。生 带来了巨大的经济效益。
产中每 2h 冲洗一次,这样除垢的速率超过结垢
(收稿日期:2011- 05- 12)
20
氮肥技术
2011 年第 32 卷
氮洗涤净化精制法(适应于粉煤制气和水煤浆制 气工艺)等。随着科技的不断发展,合成氨原料气 精制工艺也在不断地改进和提高,其中双甲工艺 和醇烃化工艺(也称新双甲工艺)取代传统的精 制工艺并得到了广泛的应用和发展,新工艺具有 降 低 消 耗 、节 约 成 本 、稳 定 操 作 、净 化 彻 底 的 特 点。 1 合成氨原料气传统精制工艺 1.1 醋酸铜氨液精制方法
双甲工艺的主要反应方程式: 甲醇化反应 CO+2H2=CH3OH+Q CO2+3H2=CH3OH+H2O+Q 甲醇化反应主要以 CO、CO2 与 H2 合成反应 生成甲醇产品,并去除了原料气中的一定量的 (CO+CO2),这是双甲工艺的第一步净化反应的功
合成氨原料气醇烃化净化精制新工艺技术

合成氨原料气醇烃化净化精制新工艺技术合成氨是一种重要的化学原料,在农业、化肥生产以及其他领域有广泛的应用。
合成氨的生产过程中,醇烃化是一个关键的步骤,它将醇类原料氧化成氨气。
然而,该过程中也存在着一些问题,如氨气纯度不高、能耗大和废水处理困难等。
为了解决这些问题,研究人员提出了一种新的工艺技术,通过气醇烃化净化和精制的方法来改进合成氨的生产过程。
新工艺技术的主要步骤包括以下几个方面:首先,选择高纯度的醇类原料作为氨气的来源。
一般来说,乙醇和丙醇是合成氨生产中常用的原料,它们具有较高的氨气产率。
在这一步中,可以采用蒸馏等方法从原料中提取纯度较高的醇类化合物。
其次,将醇类化合物经过催化氧化反应得到氨气。
这个步骤的关键在于选择适当的催化剂和反应条件,以提高氨气的产率和纯度。
同时,还需控制反应中的温度、压力和氧化剂的使用量,以减少能耗和废水产生。
接下来,对产生的氨气进行净化处理。
在这一步中,可以采用吸附剂、膜分离或冷凝等方法去除气相中的杂质,如水、氧气和碳氧化物等。
通过这些净化手段,可以提高氨气的纯度,并减少对后续工艺步骤的影响。
最后,对净化后的氨气进行精制处理。
在这一步中,可以利用洗涤和吸附等方法去除氨气中的杂质,如硫化氢和二氧化碳等。
通过精制处理,可以进一步提高合成氨的纯度,并保证其达到工业生产的要求。
总的来说,合成氨原料气醇烃化净化精制新工艺技术为合成氨的生产过程提供了一种可行的改进方法。
该工艺技术通过选择高纯度的醇类化合物原料、优化催化氧化反应条件以及采用净化和精制手段,可以提高氨气的产率、纯度和质量,降低能耗并减少废水处理难题,从而实现合成氨生产过程的可持续发展。
合成氨是一种广泛用于农业、化肥生产和其他领域的化学原料。
目前,最常用的方法是通过醇烃化将醇类原料氧化成氨气。
然而,传统的合成氨工艺存在一些问题,如氨气纯度低、废水处理难题以及能耗较高。
为了解决这些问题,研究人员提出了一种新的合成氨原料气醇烃化净化精制工艺技术。
合成氨原料气醇烃化净化精制新工艺

合成氨原料气醇烃化净化精制新工艺1. 醇烃化工艺开发简况合成氨原料气醇烃化净化精制工艺,即在用甲醇化、烃化(或甲烷化)反应的方法来净化精制合成氨原料气,使合成氨原料气进入氨合成工段之前的气体中CO、CO2(俗称气体中的“微量”指标)总量小于10ppm。
此工艺还可联产甲醇,用此工艺取代传统的“醋酸铜氨液洗涤法(俗称铜洗法)”的净化精制合成氨原料气的方法。
工艺简称醇烃化工艺(或双甲工艺)。
合成氨原料气醇烃化净化工艺是双甲工艺的升级技术,双甲工艺是湖南安淳高新技术有限公司开发成功的技术,该技术于上世纪1990年提出,1991年进行工业化实施,1992年9月第一套工业化装置在湖南衡阳市氮肥厂投产成功,国际上属于首先提出,最先进行工业化生产。
1993年4月获国家发明专利权,相继又申请了可调节氨醇比的醇烃化工艺专利,美、英等权威化学文摘均作了报道。
1994年元月通过化工部科技鉴定,1994年6月国家科委将该项目列入《国家重大科技成果推广计划》项目。
第一套装置至今已正常运行13年,目前净化精制能力达到了总氨8万吨/年,副产1万吨甲醇/年,取得了很好的效益。
目前,推广的工艺最大处理合成氨能力为40万吨,在全国中、小合成氨厂推广达15家,目前正在进行工程设计的有5家。
湖南郴州桥口氮肥厂的双甲工艺工程被评为国家优秀创新工程,双甲工艺技术于2000年被授予湖南省科技进步一等奖。
双甲工艺评为1995年度原化学工业部十二大重大科技成果之一,给予重点推广。
2003年醇烃化工艺获得国家科技进步二等奖。
此工艺开发和发展可分为三个阶段,历时十多年的开发创新和竭力推广,有着超乎寻常的辛劳可谓十年磨一剑。
技术发展的第一阶段——确认了国产的甲烷化催化剂在高压条件下的运行条件。
技术发展之初,当有双甲净化这个工艺创意时,当时国内的很多厂家已经有了联醇工段,一般为联醇后再串铜洗工段进行净化精制方法,由于联醇出口的CO和CO2的指标与传统的甲烷化进口的气体成份指标不一样,且压力等级也不一样,要将铜洗去掉用甲烷化来替代必须首先解决进甲烷化炉的进口气体的气体成份问题——一定要使醇后气中的CO+CO2总量不超过0.7%,且较低为好。
合成氨原料气的精制陈诚
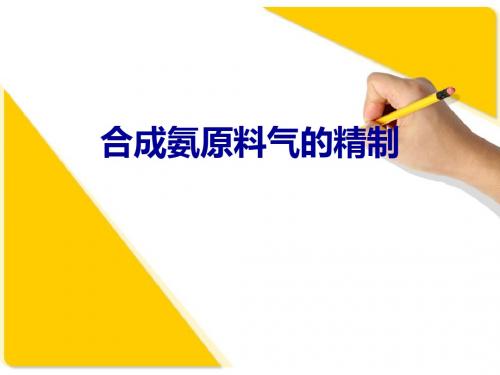
常规甲烷化工艺具有如下特点: 原料气中CO+CO2含量较低,一般不超过0.7%;
反应放热量少,热点温度不超过350℃ ;
反应空速为3000-6000h-1; 反应器为单绝热床; 催化剂为镍系,采用浸渍法或共沉淀法制备; 产品气中CO+CO2含量<2ppm。
二.催化剂主要活性组分
二.工艺流程
变换气经压缩机压缩,用水(或热钾碱溶液等)除去其中大部分CO2 后,再由压缩机加压到12~13MPa送至铜氨液洗涤系统。 气体自铜 氨液洗涤塔(简称铜洗塔)的底部进入,自下而上与塔顶喷淋下来的 铜氨液逆流接触,气体中CO、CO2、H2O和O2等即为铜氨液吸收。 如果洗涤后气体中CO+CO2〈10ml/m3,即可加压后送往氨合成系 统。倘若出铜洗塔气体中的CO2含量较高时,还要经过碱洗塔用氨水 或碱液吸收CO2后,才能达到净化要求。 吸收气体中CO等杂质后 的铜氨液,自铜液塔底部经减压至0.15MPa自动流到铜氨液再生系统 的回流塔3的顶部,与再生器4逸出的气体相遇,捕集其中氨及部分 CO2后,由回流塔底部流至还原器7中。还原器的上下两段均上设有 蒸汽加热管,底部有空气加入管 ,中部有旁通管线(即副线)。铜 氨液首先经过下加热器6加热,随即向上流,经还原器内几层有孔折 板后进入上加热器5。在必要时,可开用旁通管,使部分铜氨液不经 下加热器而直接进入上加热器。铜氨液经还原
金属的甲烷化活性顺序: Ru>Ir>Rh>Ni>Co>Os>Pt>Fe>Mo>Pd>Ag
从原料来源、成本和活性进行综合分析,认为Ni是最适 宜的甲烷化催化剂;
优点 缺点
镍系催化剂
钴系催化剂 钼系催化剂 铁系催化剂
活性高、选择性好
合成氨工艺技术的现状及发展趋势
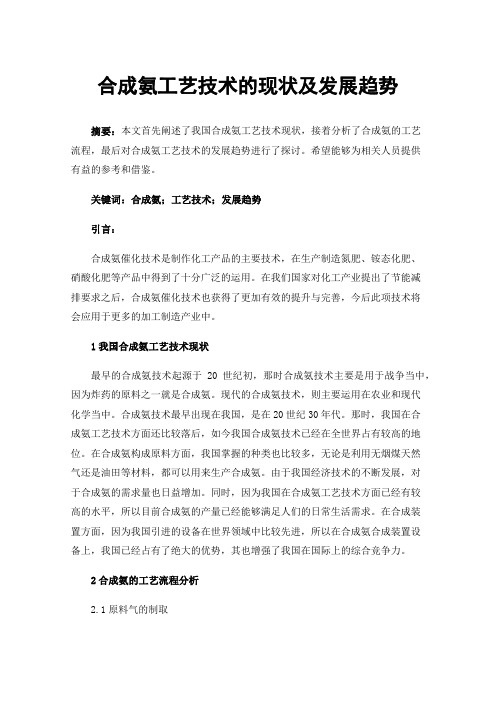
合成氨工艺技术的现状及发展趋势摘要:本文首先阐述了我国合成氨工艺技术现状,接着分析了合成氨的工艺流程,最后对合成氨工艺技术的发展趋势进行了探讨。
希望能够为相关人员提供有益的参考和借鉴。
关键词:合成氨;工艺技术;发展趋势引言:合成氨催化技术是制作化工产品的主要技术,在生产制造氮肥、铵态化肥、硝酸化肥等产品中得到了十分广泛的运用。
在我们国家对化工产业提出了节能减排要求之后,合成氨催化技术也获得了更加有效的提升与完善,今后此项技术将会应用于更多的加工制造产业中。
1我国合成氨工艺技术现状最早的合成氨技术起源于20世纪初,那时合成氨技术主要是用于战争当中,因为炸药的原料之一就是合成氨。
现代的合成氨技术,则主要运用在农业和现代化学当中。
合成氨技术最早出现在我国,是在20世纪30年代。
那时,我国在合成氨工艺技术方面还比较落后,如今我国合成氨技术已经在全世界占有较高的地位。
在合成氨构成原料方面,我国掌握的种类也比较多,无论是利用无烟煤天然气还是油田等材料,都可以用来生产合成氨。
由于我国经济技术的不断发展,对于合成氨的需求量也日益增加。
同时,因为我国在合成氨工艺技术方面已经有较高的水平,所以目前合成氨的产量已经能够满足人们的日常生活需求。
在合成装置方面,因为我国引进的设备在世界领域中比较先进,所以在合成氨合成装置设备上,我国已经占有了绝大的优势,其也增强了我国在国际上的综合竞争力。
2合成氨的工艺流程分析2.1原料气的制取制作合成氨的原材料主要是天然气、重油、石脑油等。
不管是哪一种原材料都可以用来代表。
这些原材料在水蒸气和高温下形成将一氧化碳与氢作为主体的合成氨原材料气。
我们国家制作合成氨原料气的主要方式为煤气化法。
这种方法主要是利用氧、蒸汽以及其他汽化剂高温处理煤,促使其转变成一氧化碳和氢等可以燃烧的气体。
对气态烃类,工业中通常使用二段蒸汽转化法加工制造合成气。
重油部分的氧化法主要是将重油作为原材料,而气态烃类主要是不完全燃烧氧气,促使烃类在高温的作用下出现燃烧和裂解现象,出现的二氧化碳和水蒸气在高温的作用下和甲烷发生转化反应,进而取得将氧化碳和氢气作为主要原料的合成气。
近年国内外合成氨生产发展综述

近年国内外合成氨生产发展综述
随着全球经济的快速发展和人口的增长,人们对食品、能源和化
学原料的需求不断上升。
而合成氨作为一种重要的化学原料,具有广
泛的用途,如农业肥料、工业原料和能源消耗品等。
因此,开发高效
的合成氨生产技术具有重要的意义。
国内方面,我国是世界上最大的化肥消费国和生产国之一,对合
成氨的需求量巨大。
目前,我国主要采用哈贝–博斯奥克(Haber-Bosch)法生产合成氨,该方法虽然具有高效、可靠、成熟的优点,但
也存在着能源消耗量大、生产成本高等问题。
为此,我国在探索新的
生产技术上下了很大的功夫,如采用新型催化剂、高温高压技术、废
气回收等技术来提高氨的生产效率和降低生产成本,这些技术已经逐
渐成为我国合成氨生产的新趋势。
国外方面,随着技术的不断进步,一些新型的合成氨生产技术也
在不断涌现。
如以水为介质的氨合成技术、光电化学合成氨技术、电
化学合成氨技术等,在降低生产成本、减少能源消耗等方面都具有较
大的潜力。
同时,相关国家还在探索生态、可持续的生产方式,如采
用太阳能和风能等清洁能源进行合成氨生产,以实现低碳环保的目标。
综上所述,合成氨生产技术的发展取得了较大的进展,各种技术
在中国和国际上得到了广泛的研究和应用。
未来,随着人们对环保、
可持续发展的要求越来越高,合成氨生产技术将会不断创新和优化,
以适应未来经济和社会的发展需求。
合成氨工业发展现状及重要性
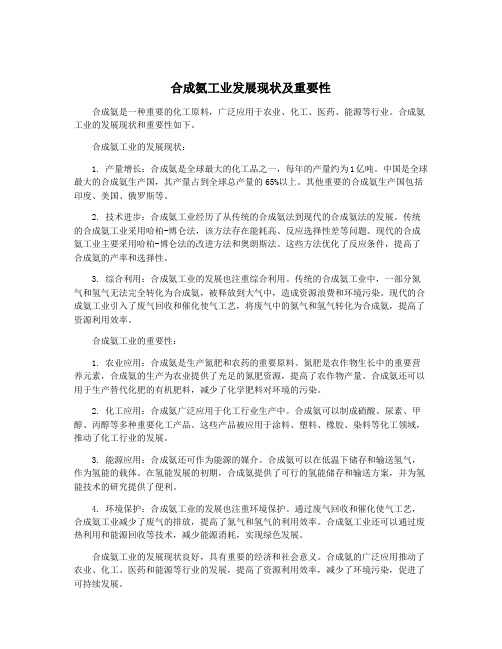
合成氨工业发展现状及重要性合成氨是一种重要的化工原料,广泛应用于农业、化工、医药、能源等行业。
合成氨工业的发展现状和重要性如下。
合成氨工业的发展现状:1. 产量增长:合成氨是全球最大的化工品之一,每年的产量约为1亿吨。
中国是全球最大的合成氨生产国,其产量占到全球总产量的65%以上。
其他重要的合成氨生产国包括印度、美国、俄罗斯等。
2. 技术进步:合成氨工业经历了从传统的合成氨法到现代的合成氨法的发展。
传统的合成氨工业采用哈柏-博仑法,该方法存在能耗高、反应选择性差等问题。
现代的合成氨工业主要采用哈柏-博仑法的改进方法和奥朗斯法。
这些方法优化了反应条件,提高了合成氨的产率和选择性。
3. 综合利用:合成氨工业的发展也注重综合利用。
传统的合成氨工业中,一部分氮气和氢气无法完全转化为合成氨,被释放到大气中,造成资源浪费和环境污染。
现代的合成氨工业引入了废气回收和催化使气工艺,将废气中的氮气和氢气转化为合成氨,提高了资源利用效率。
合成氨工业的重要性:1. 农业应用:合成氨是生产氮肥和农药的重要原料。
氮肥是农作物生长中的重要营养元素,合成氨的生产为农业提供了充足的氮肥资源,提高了农作物产量。
合成氨还可以用于生产替代化肥的有机肥料,减少了化学肥料对环境的污染。
2. 化工应用:合成氨广泛应用于化工行业生产中。
合成氨可以制成硝酸、尿素、甲醇、丙醇等多种重要化工产品。
这些产品被应用于涂料、塑料、橡胶、染料等化工领域,推动了化工行业的发展。
3. 能源应用:合成氨还可作为能源的媒介。
合成氨可以在低温下储存和输送氢气,作为氢能的载体。
在氢能发展的初期,合成氨提供了可行的氢能储存和输送方案,并为氢能技术的研究提供了便利。
4. 环境保护:合成氨工业的发展也注重环境保护。
通过废气回收和催化使气工艺,合成氨工业减少了废气的排放,提高了氮气和氢气的利用效率。
合成氨工业还可以通过废热利用和能源回收等技术,减少能源消耗,实现绿色发展。
合成氨工业的发展现状良好,具有重要的经济和社会意义。
合成氨国内外综述
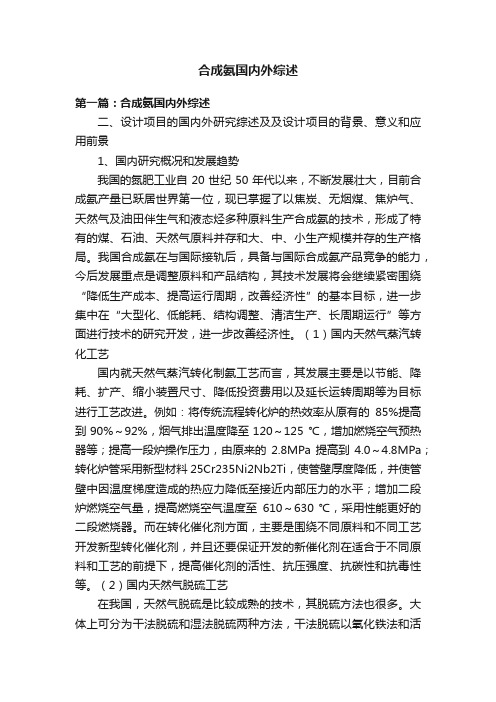
合成氨国内外综述第一篇:合成氨国内外综述二、设计项目的国内外研究综述及及设计项目的背景、意义和应用前景1、国内研究概况和发展趋势我国的氮肥工业自20世纪50年代以来,不断发展壮大,目前合成氨产量已跃居世界第一位,现已掌握了以焦炭、无烟煤、焦炉气、天然气及油田伴生气和液态烃多种原料生产合成氨的技术,形成了特有的煤、石油、天然气原料并存和大、中、小生产规模并存的生产格局。
我国合成氨在与国际接轨后,具备与国际合成氨产品竞争的能力,今后发展重点是调整原料和产品结构,其技术发展将会继续紧密围绕“降低生产成本、提高运行周期,改善经济性”的基本目标,进一步集中在“大型化、低能耗、结构调整、清洁生产、长周期运行”等方面进行技术的研究开发,进一步改善经济性。
(1)国内天然气蒸汽转化工艺国内就天然气蒸汽转化制氨工艺而言,其发展主要是以节能、降耗、扩产、缩小装置尺寸、降低投资费用以及延长运转周期等为目标进行工艺改进。
例如:将传统流程转化炉的热效率从原有的85%提高到90%~92%,烟气排出温度降至120~125 ℃,增加燃烧空气预热器等;提高一段炉操作压力,由原来的2.8MPa提高到4.0~4.8MPa;转化炉管采用新型材料25Cr235Ni2Nb2Ti,使管壁厚度降低,并使管壁中因温度梯度造成的热应力降低至接近内部压力的水平;增加二段炉燃烧空气量,提高燃烧空气温度至610~630 ℃,采用性能更好的二段燃烧器。
而在转化催化剂方面,主要是围绕不同原料和不同工艺开发新型转化催化剂,并且还要保证开发的新催化剂在适合于不同原料和工艺的前提下,提高催化剂的活性、抗压强度、抗碳性和抗毒性等。
(2)国内天然气脱硫工艺在我国,天然气脱硫是比较成熟的技术,其脱硫方法也很多。
大体上可分为干法脱硫和湿法脱硫两种方法,干法脱硫以氧化铁法和活性炭法应用较广,而湿法脱硫以砷碱法、ADA、改良ADA和栲胶法颇具代表性。
干法脱硫技术最早应用于煤气脱硫。
国内外合成氨工艺技术现状及其发展
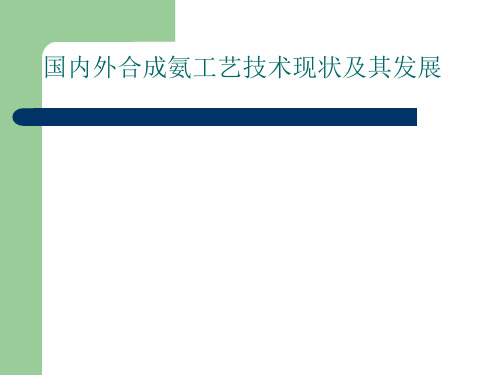
较先进的技术。
上世纪七八十年代引进的装置,经过节能和增产技术改造,产能、消
耗、质量、环保等仍处于国内领先水平;主要技术经济指标仍可跟踪 上世界先进工艺技术的水平。
以油为原料的装置在结构调整中,引入洁净煤气化技术提升了原料多
元化进的技术水平。
大型合成氨生产技术荟萃了当今世界上主要的先进工艺技术,是世界
2584.88
201
3954.67
321
1094.84
522
5049.51
占全国 (%)
9.16 29.45 51.19 78.32 21.68 100.00
1.4 原料以煤为主,适合中国资源特点
合成氨原料结构占产能的比例(%)
年份
2000
2006
2007
2008
天然气
14
21.3
20.2
20.1
2007
ቤተ መጻሕፍቲ ባይዱ
年份
2008
全球总计 中国总计 大型装置
1.1 产能快速增长
中国现有合成氨生产企业 522个,2008年合成氨总产能约5700万吨,2009年 底预计达到6000万吨以上。
产能增加主要是新建装置和部分装置扩能改造的贡献。
近年国内外合成氨生产发展综述

近年国内外合成氨生产发展综述
近年来,合成氨作为重要的化工原料和肥料,在全球范围内得到了广泛应用和开发。
国内合成氨生产行业也随着国内经济的不断发展而迅速壮大。
本文将对近年来国内外合成氨生产的发展情况进行综述。
在国外,欧洲的合成氨生产一直处于领先地位。
随着全球化的不断推进,国际化的生产模式成为了合成氨生产的趋势。
近年来,欧洲和南美洲先后投资兴建了多个大型合成氨生产厂,这些新兴厂家在技术和设备上的不断提升,也进一步推动了合成氨生产技术的进步。
在国内,合成氨生产发展也取得了很大的进展。
自20世纪70年代末到80年代初,我国合成氨生产技术实现了快速转型,从小型厂
家向大型化、集中化方向转变。
目前,我国的合成氨生产能力已经达到了世界领先水平。
同时,在技术上,我国也在不断探索新的生产工艺和设备,例如采用催化剂的高效合成氨工艺,以及数控自动化的生产设备等。
总的来说,合成氨生产行业在近年来取得了显著的发展成果,未来还将继续向着更加高效、智能化和节能环保化的方向发展。
- 1 -。
合成氨工艺技术的现状及其发展趋势
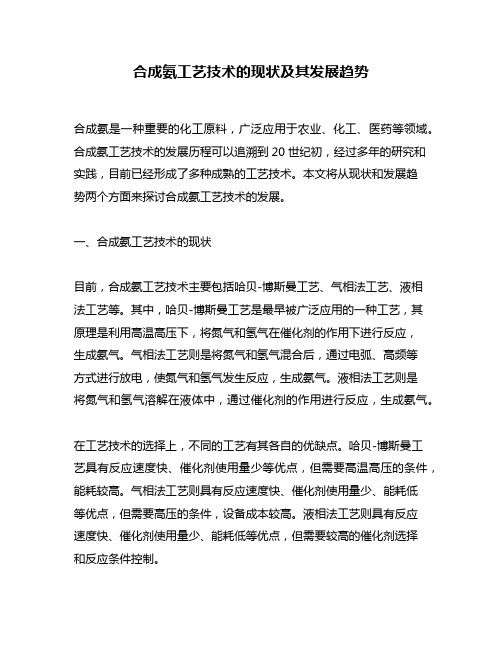
合成氨工艺技术的现状及其发展趋势合成氨是一种重要的化工原料,广泛应用于农业、化工、医药等领域。
合成氨工艺技术的发展历程可以追溯到20世纪初,经过多年的研究和实践,目前已经形成了多种成熟的工艺技术。
本文将从现状和发展趋势两个方面来探讨合成氨工艺技术的发展。
一、合成氨工艺技术的现状目前,合成氨工艺技术主要包括哈贝-博斯曼工艺、气相法工艺、液相法工艺等。
其中,哈贝-博斯曼工艺是最早被广泛应用的一种工艺,其原理是利用高温高压下,将氮气和氢气在催化剂的作用下进行反应,生成氨气。
气相法工艺则是将氮气和氢气混合后,通过电弧、高频等方式进行放电,使氮气和氢气发生反应,生成氨气。
液相法工艺则是将氮气和氢气溶解在液体中,通过催化剂的作用进行反应,生成氨气。
在工艺技术的选择上,不同的工艺有其各自的优缺点。
哈贝-博斯曼工艺具有反应速度快、催化剂使用量少等优点,但需要高温高压的条件,能耗较高。
气相法工艺则具有反应速度快、催化剂使用量少、能耗低等优点,但需要高压的条件,设备成本较高。
液相法工艺则具有反应速度快、催化剂使用量少、能耗低等优点,但需要较高的催化剂选择和反应条件控制。
二、合成氨工艺技术的发展趋势随着科技的不断发展,合成氨工艺技术也在不断地创新和改进。
未来,合成氨工艺技术的发展趋势主要有以下几个方面:1. 绿色化发展随着环保意识的不断提高,绿色化发展已经成为了合成氨工艺技术的重要发展方向。
未来,合成氨工艺技术将更加注重环保和可持续发展,采用更加环保的催化剂和反应条件,减少对环境的污染。
2. 低能耗化发展合成氨工艺技术的能耗一直是制约其发展的重要因素之一。
未来,合成氨工艺技术将更加注重能耗的降低,采用更加节能的反应条件和设备,减少能源的消耗。
3. 高效化发展合成氨工艺技术的效率一直是制约其发展的重要因素之一。
未来,合成氨工艺技术将更加注重效率的提高,采用更加高效的催化剂和反应条件,提高反应速度和产量。
4. 多元化发展合成氨工艺技术的应用领域非常广泛,未来,合成氨工艺技术将更加注重多元化的发展,开发更多的应用领域,满足不同领域的需求。
合成氨
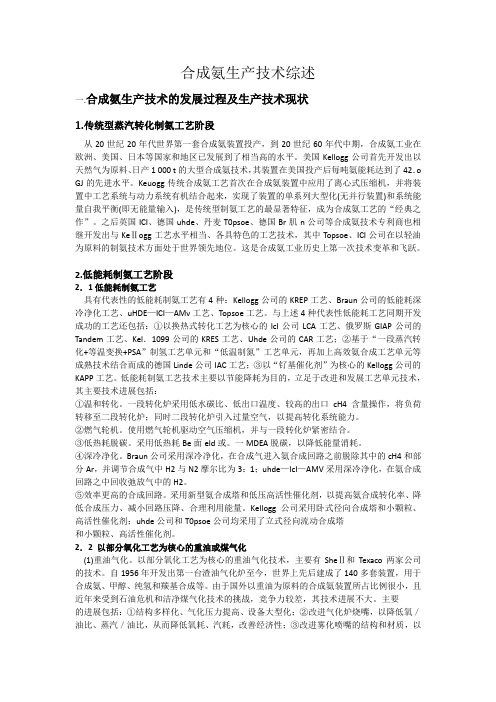
合成氨生产技术综述一.合成氨生产技术的发展过程及生产技术现状1.传统型蒸汽转化制氨工艺阶段从20世纪20年代世界第一套合成氨装置投产,到20世纪60年代中期,合成氨工业在欧洲、美国、日本等国家和地区已发展到了相当高的水平。
美国Kellogg公司首先开发出以天然气为原料、日产1 000 t的大型合成氨技术,其装置在美国投产后每吨氨能耗达到了42.o GJ的先进水平。
Keuogg传统合成氨工艺首次在合成氨装置中应用了离心式压缩机,并将装置中工艺系统与动力系统有机结合起来,实现了装置的单系列大型化(无并行装置)和系统能量自我平衡(即无能量输入),是传统型制氨工艺的最显著特征,成为合成氨工艺的“经典之作”。
之后英国ICI、德国uhde、丹麦T0psoe、德国Br肌n公司等合成氨技术专利商也相继开发出与KeⅡogg工艺水平相当、各具特色的工艺技术,其中Topsoe、ICI公司在以轻油为原料的制氨技术方面处于世界领先地位。
这是合成氨工业历史上第一次技术变革和飞跃。
2.低能耗制氨工艺阶段2.1低能耗制氨工艺具有代表性的低能耗制氨工艺有4种:Kellogg公司的KREP工艺、Braun公司的低能耗深冷净化工艺、uHDE—ICI—AMv工艺、Topsoe工艺。
与上述4种代表性低能耗工艺同期开发成功的工艺还包括:①以换热式转化工艺为核心的IcI公司LCA工艺、俄罗斯GIAP公司的Tandem工艺、Kel.1099公司的KRES工艺、Uhde公司的CAR工艺;②基于“一段蒸汽转化+等温变换+PSA”制氢工艺单元和“低温制氮”工艺单元,再加上高效氨合成工艺单元等成熟技术结合而成的德国Linde公司IAC工艺;③以“钌基催化剂”为核心的Kellogg公司的KAPP工艺。
低能耗制氨工艺技术主要以节能降耗为目的,立足于改进和发展工艺单元技术,其主要技术进展包括:①温和转化。
一段转化炉采用低水碳比、低出口温度、较高的出口cH4含量操作,将负荷转移至二段转化炉;同时二段转化炉引入过量空气,以提高转化系统能力。
合成氨催化技术与工艺发展探究

合成氨催化技术与工艺发展探究合成氨是工业上重要的化工产品之一,也是农业上主要的氮肥。
合成氨催化技术的发展对于化工行业和农业生产具有重要意义。
本文将探究合成氨催化技术与工艺的发展历程,分析其现状和未来发展趋势。
一、合成氨催化技术的历史合成氨的制备历史可以追溯到19世纪,当时科学家们开始尝试使用化学方法制备氨气。
而后,德国化学家哈勃发现了通过高温、高压条件下将氢气和氮气催化反应合成氨气的方法,这一方法被称为哈勃过程,也成为了工业合成氨的基础技术。
随后,人们又相继提出了费舍尔-特罗普希氏法、考夫曼法等制氨技术。
这些技术改善了合成氨的生产效率和质量,推动了工业合成氨的大规模生产。
工业上主要的合成氨催化技术路线有哈勃过程、费舍尔-特罗普希氏法和考夫曼法。
哈勃过程是通过将氢气和氮气在铁催化剂的存在下,经高压高温条件进行气相反应制备氨气。
费舍尔-特罗普希氏法则是在中温、高压的条件下,利用铁-铝催化剂进行氢气和氮气的合成。
而考夫曼法是将氨和水进行催化裂解,得到氢气和氮气,再行合成氨气。
目前,合成氨催化技术在工业生产中得到广泛应用。
尤其是哈勃过程,已成为工业上主要的制氨技术路线,因其操作简便、反应条件温和等优点而受到青睐。
随着科技的进步,合成氨催化剂也发生了革新,新型的合成氨催化剂不仅提高了合成氨的生产效率,还减少了对环境的影响,具有更好的发展前景。
在未来,合成氨催化技术的发展将会朝着高效、节能、环保的方向发展。
催化剂的研究将会成为重点,新型高效的合成氨催化剂将被不断开发,以提高合成氨的产率和质量,减少能源消耗和环境污染。
催化技术将会向着低温低压方向发展,以降低制氨过程的能耗和成本。
合成氨催化技术将和新材料、新能源等领域相结合,推动整个制氨工艺的创新和改进。
智能化制造和自动化控制将会成为合成氨生产的新趋势,提高生产效率的保障产品质量和生产安全。
合成氨催化技术与工艺的发展对于工业生产和农业发展具有重要意义。
随着科技的不断进步和创新,合成氨催化技术将会迎来更好的发展前景,为人类创造出更多的价值和福祉。
合成氨国际工艺技术

合成氨国际工艺技术合成氨是一种重要的化工原料,在农业和工业中有广泛的应用。
其生产工艺技术在国际上得到了长时间的研究和不断的改进。
目前,国际上主要采用的合成氨工艺技术包括哈伯–博仑斯(Haber-Bosch)法和贝礼法(Kellogg-Bel)法。
哈伯–博仑斯法是合成氨的传统工艺技术,也是目前最主要的工艺技术。
它是由德国化学家哈伯和博仑斯于20世纪初提出的。
该法是将氮气和氢气以高温高压的条件下通过络合剂进行反应,生成合成氨。
该法工艺相对简单,反应条件可调控性强,反应效率高。
然而,该法的能耗较高,对催化剂的要求较高,催化剂的失活也较快。
贝礼法是一种新型的合成氨工艺技术,也是目前工业化规模较大的工艺技术之一。
贝礼法是由美国化学家贝礼于20世纪30年代提出的。
该法与哈伯–博仑斯法相比,在合成氨的催化剂和工艺上有所不同。
贝礼法采用高压催化剂床,催化剂采用铁/铬复合氧化物。
该法具有催化剂活性高、催化剂失活慢、反应温度低等优点,能耗较哈伯–博仑斯法低。
在国际上,对于合成氨工艺技术的研究重点主要集中在提高反应效率、降低能耗和催化剂失活的问题上。
近年来,一些新型的催化剂和反应工艺被提出和采用,以期能更好地解决这些问题。
例如,一种基于银催化剂的工艺技术被提出,该技术能在相对较低的温度下实现高效的合成氨反应。
另外,一些研究者还尝试使用非传统的反应介质,如离子液体和超临界流体,以提高反应速率和效果。
总体而言,合成氨的国际工艺技术在不断发展和改进。
尽管哈伯–博仑斯法和贝礼法是目前应用最广的工艺技术,但随着科技的进步和对资源和环境的要求的不断提高,未来合成氨工艺技术的发展方向可能会更加多样化和绿色化。
相信随着技术的不断突破和创新,合成氨的生产将越来越高效、环保。
合成氨原料气精制工艺技术的发展

合成氨原料⽓精制⼯艺技术的发展在合成氨的⽣产过程中,经过⼀氧化碳变换和⼆氧化碳脱除后的原料⽓尚含有少量残余的CO和CO2。
这些微量CO和CO2的存在,对氨合成的触媒有着相当⼤的毒害作⽤,故要求进⼊氨合成塔原料⽓中的CO+CO2含氧化合物总含量⼩于10×10-6。
合成氨原料⽓精制⼯艺技术总体可归纳为湿法和⼲法2种。
湿法主要指以有选择性的溶液洗涤或吸收原料⽓中的CO和CO2,使原料⽓中的CO和CO2得到脱除。
⼲法则是以固体触媒催化使CO和CO2转化成对氨合成触媒⽆毒害作⽤的物质。
这些物质或从原料⽓中分离⽽使CO和CO2脱除,或继续保留在原料⽓中。
湿法⼯艺技术分为物理吸收⽅法和化学吸收⽅法。
应⽤年代较早的、适⽤于中⼩型合成氨装置的铜氨液吸收法,属于化学吸收⽅法。
应⽤年代较晚、适⽤于⼤型合成氨装置的液氮洗涤法,则属于物理吸收⽅法。
甲烷化⼯艺则是⼲法精制⼯艺。
随着⼈们节能降耗和环境保护意识的提⾼,合成氨原料⽓精制⼯艺技术中的物理吸收⽅法和⼲法精制⼯艺被⼴泛地采⽤和推⼴。
我国在甲烷化精制⼯艺基础上研究开发的、具有⾃主知识产权的、适⽤于我国⽬前中⼩规模合成氨装置的“全⾃热⾮等压醇烷化净化⼯艺”、“合成氨原料⽓双甲精制新⼯艺”就是这种发展趋势的范例。
笔者拟针对不同精制⼯艺的技术特点进⾏论述和⽐较。
1 铜氨液吸收⼯艺1.1 ⼯艺原理铜氨液是铜离⼦、酸根及氨组成的⽔溶液。
以铜离⼦、醋酸、液氨组成的醋酸铜氨液是铜氨液的代表。
铜氨液吸收CO和CO2的化学反应如下。
Cu(NH3)2++CO+NH3→Cu[(NH3)3CO]++QNH4OH+CO2==(NH4)2CO3+H2O+Q该吸收过程存在⽓液相的相平衡和液相的化学平衡,是⼀个⽐较复杂的化学反应。
⾸先,铜氨液中以Cu(NH3)2+形式存在的低价铜离⼦是吸收CO的有效成分,⽽以Cu(NH3)42+形式存在的⾼价铜离⼦是⽆吸收CO能⼒的,但它的存在可以保证有效的Cu(NH3)2+的存在。
- 1、下载文档前请自行甄别文档内容的完整性,平台不提供额外的编辑、内容补充、找答案等附加服务。
- 2、"仅部分预览"的文档,不可在线预览部分如存在完整性等问题,可反馈申请退款(可完整预览的文档不适用该条件!)。
- 3、如文档侵犯您的权益,请联系客服反馈,我们会尽快为您处理(人工客服工作时间:9:00-18:30)。
国内外合成氨原料气精制工艺技术发展南京国昌化工科技有限公司1.引言在合成氨工业中,经过脱碳工艺处理后的合成氨原料气中仍含有0.5~3% CO和0.5%~1%CO2,必须进一步处理将其降低至10ppm左右,以保护氨合成催剂,这一原料气精制工艺过程俗称“精炼”,目前合成氨厂脱除微量CO、CO2的方法大体分为热法和冷法两类。
冷法工艺即液氮洗涤法,近年来国内外新建的大型氨厂大多采用此法;而热法工艺门类较多,包括传统的醋酸铜氨液洗涤法(铜洗法)、低压甲烷化法、甲醇甲烷化法和分子筛变压吸附法等。
总体上讲冷法工艺技术先进、净化度很高,但投资巨大;而热法工艺技术相对简单成熟、投资低,但在净化度方面不及冷法。
热法中的铜洗工艺更因其能耗高、净化度低、污染大等诸多缺点而逐渐被其他先进的工艺方法所替代。
2. 国外合成氨原料气精制工艺发展2.1 铜洗法醋酸铜氨液洗涤法(简称铜洗)是最古老的方法。
早在1913年就开始应用,迄今有近一百年的历史,操作压力为15Mpa。
铜洗法以其工艺成熟、操作弹性大,长期在中小型合成氨厂占据主导地位。
随着技术的进步,铜洗法精制原料气与其它方法相比,缺点越来越突出。
主要表现在运行、维修、操作费用高,物料消耗大(消耗铜、醋酸、液氨、蒸汽)、根据国内氨厂实际情况测算,吨氨需要增加成本在50~80元,而且精制度低,一般净化后的CO+CO2≥25ppm,然而其最致命的缺陷还在于环境污染严重。
由于铜洗再生气经水洗涤产生铜洗稀氨水,其浓度视所采用的洗涤技术不同而不同,一般在1~3%左右。
中型氮肥厂每小时约产生10吨废水,这股废水除含有氨外,还含有CO2,所以采用一般的提浓方法都由于容易生成碳铵引起管道堵塞而无法处理,为此要么采用铜洗再生氨直接放空,要么就是铜洗稀氨水排放。
这不但浪费了宝贵的资源,也引起了大气或水环境的严重污染。
此外生产过程中经常出现严重的铜液泄漏,这些弊端与现代化高效、洁净的生产理念极不相适应。
国外早在60年代就逐步淘汰这种落后的工艺,之后新建氨厂几乎全用甲烷化法和液氮洗法代替铜洗。
2.2 低压甲烷化法与铜洗法比,用甲烷化脱除原料气中的CO+CO2可大幅度简化生产流程,降低建设和操作费用,操作也较平稳,运行费用不足铜洗的20%。
占地面积也较铜洗装置要少,低压甲烷化法其操作压力为1~6MPa。
1965年以后国外新建氨厂大多采用该工艺。
但该法也存在以下不足之处,由于CO和 CO2被除去的同时,不仅要消耗掉数倍于CO和 CO2的H2,而且甲烷化后甲烷含量增加,造成氨合成放空量增大,因此该工艺仅适用于经深度低变,原料气中含CO和 CO2极少(一般CO+CO2<0.7%,)的合成氨厂,即便如此,由甲烷化反应:CO+3H2 = CH4+H2OCO2+4H2 = CH4+2H2O可见进口气中每增加0.1% CO,相当于多消耗0.3%H2和0.1%的•CO,总共为0.4%(CO可转化为H2),同时合成气中增加0.1%CH4。
经测算,如有0.7%的CO+CO2进行甲烷化,以上二项累计增加原料气耗约10%,足见其耗量之大。
2.3 布朗深冷净化工艺深冷净化技术是通过深度冷冻混合气中部分组分液化分离,基于等熵膨胀原理。
甲烷化后的混合气干燥后经等熵膨胀,再经循环冷却,将温度降至-185℃~-175℃。
在该温度下,可将合成气中的全部CH4、残余的CO和大部分Ar和过量的氮液化分离掉,获得纯净、干燥(3:1)氢氮合成气,达到深度净化的目的。
而且合成系统少量的弛放气可以回到系统加以回收。
因此可以认为布朗深冷净化工艺在一定程度上弥补了甲烷化工艺的不足。
2.4 液氮洗涤法该工艺由联邦德国林德公司开发,与甲烷化工艺几乎同期问世,同样在大型合成氨厂得到广泛的应用。
70年代末我国先后共引进9套以渣油为原料制造合成氨的大型装置,变换后气体均采用低温甲醇洗脱硫,脱碳和液氮洗精制工艺。
其原料气先采用甲醇为物理溶剂的气体净化法即低温甲醇洗工艺脱除二氧化碳和硫化物。
为了防止气体结冰,在原料气进入原料气冷却器前,注人少量甲醇,在原料气冷却器中被冷却到-9℃,经分离器后送人甲醇洗涤塔。
从甲醇洗涤塔顶出来净化气含二氧化碳≤20ppm,硫化氢≤1 ppm,送往液氮洗工序。
离开甲醇洗涤塔的原料气,通过分子筛吸附器除去微量甲醇和二氧化碳及水分,然后进入氮洗冷箱内的低温区。
在原料气/氮气冷却器中被氮洗气和一氧化碳馏分冷却至-188℃后,进入液氮洗涤塔。
在液氮洗涤塔中,气体中的一氧化碳、甲烷和大部分Ar等杂质被液氮洗去。
净化后氢氮气含CO<5ppm,Ar十CH4<45ppm,充分显示该工艺净化度高的优点。
但其缺点是要消耗冷量,需要大型的空气冷冻分离装置,投资大。
一般用在大型装置,用纯氧制取原料气且与低温甲醇洗工艺相配套,才比较经济合理。
2.5.甲醇甲烷化法丹麦托普索公司于90年代初开发了一种新的气体净化工艺。
与传统工艺相比,这种新工艺更具吸引力。
该工艺由两部分组成,在甲醇合成之后,再是传统的甲烷化工艺工序。
在甲醇化工艺中,CO和CO2按下面反应转化为甲醇:CO+2H2 = CH3 O HCO2+3H2 = CH3 O H +H2O甲醇化是在高活性的铜基催化剂上进行的,由于原料气中的氢分压很高,CO 和甲醇的分压很低,加上操作温度较低,生成的副产物极为有限。
因此,甲醇化工艺可以得到纯度很高的甲醇。
该工艺1993年在埃及SEMACOT氨厂首先采用,其合成压缩机有22Mpa和45Mpa两个等级段,原来是22Mpa下采用铜洗精制CO、CO2,45Mpa氨合成。
托普索公司将其甲醇化技术应用于在22Mpa压力等级下,生产甲醇同时串接甲烷化,精制CO、CO2至10ppm,再加压至45Mpa进行氨合成。
图1.托普索公司甲醇甲烷化精制工艺3.国内合成氨原料气精制工艺发展3.1.我国化肥行业深度净化的现状我国化肥行业以煤(焦)制氨仍占主要地位,而且从我国的能源结构,储量,供应和消耗情况来看,油制氨将逐步为煤制氨所取代。
七十年代引进的大型合成氨厂也纷纷改变了原料路线,研究煤制氨厂的节能、减污、清洁生产技术是非常必要的。
据有关机构对34家不同规模的合成氨厂统计,脱除CO的技术主要有铜洗、甲烷化和液氮洗等技术。
如表1所示表1除引进的大型氨厂以外,目前国内绝大多数中小型化肥厂采用的仍然是传统的铜洗法。
3.2.甲烷化法在中小型合成氨厂的应用我国中小型合成氨厂一直以铜洗法精制原料气,直到铜系低温变换催化剂的研制成功、并在以天然气为原料的小合成氨厂采用中温变换串低温变换流程以后,原料气中的碳氧化物大幅度降低。
从此甲烷化净化方法才得以在以天然气为原料的小合成氨厂代替铜洗法。
而以煤焦为原料的厂采用甲烷化法者为数极少,究其原因可能有以下两点:一是我国中小型合成氨厂多以间歇法制得的半水煤气中水蒸汽含量少,不象国外以天然气重油制气,有大量饱和水蒸气,故变换蒸汽耗量大,深度变换的不仅成本增加,而且会导致全厂中压蒸汽难以平衡。
再者原料气中硫含量较高,普通低变催化剂难以承受,直到钴钼系耐硫低温变换催化剂的出现,才有很少的厂家开始尝试采用甲烷化取代铜洗流程,但深度低变同时,消耗蒸汽量也将成倍增加。
3.3.深冷净化技术在我国的应用液氮洗精制工艺主要集中在我国引进的大型装置中,中型氨厂也仅有云南解放军化肥厂等少数几家采用空分、富氧煤气化的流程中使用该项技术。
3.4.分子筛变压吸附净化技术的开发国内这些年正在研究吸附法脱除微量CO、CO2的工艺。
北京大学谢有畅教授等研究了第一床层装13X分子筛,第二床层装PU-1吸附剂的两床层变温吸附法,可将原料气中H2O除去,CO与CO2总体积分数≤10ppm。
南京工业大学居沈贵,用自己开发的吸附剂进行了三塔变压吸附的工业性侧线试验。
结果表明:吸附净化法的能耗只占甲烷化的20%,且分离出的CO、CO2可以返回系统重新使用。
当吨氨消耗原料气2800m3(标准状态)、H2+N2气中CO体积分数为3%~4%时,吨氨吸附净化的能耗为3.6×105~4.8×105kJ;当N2+H2气中CO体积分数为1%~1.5%时,吨氨吸附净化的能耗为2.4×105kJ目前“联醇”工艺中醇后气中CO与CO2总体积分数≤0.5%,吸附净化法能耗将会更小。
该法不仅脱除微量CO和CO2,且可以脱除其中的H2O。
这一潜在的优点,可使目前中小化肥厂新鲜原料气不加入氨冷器前,而直接加入合成塔进口或循环机入口,这样既节省了能耗,又可使装置能力有所提高。
若这一成果能实现工业化,将是合成氨工艺的一项新突破3.5.甲醇甲烷化法自上世纪90年代以来人们从“联醇”工艺的操作中发现,当入甲醇合成塔的气体中CO体积分数为2%~3%、CO2体积分数约0.5%,醇后气中CO与CO2总的体积分数≤0.5%时,醇后气再进行甲烷化,就能达到减少CH4生成量的目的。
同时可以使甲烷化工艺过程中H2损失减少。
它与上面提到的三种方法相比,既可以副产有价值的甲醇,还可减少消耗,一举两得。
因此一种以联醇工艺(甲醇化)配合甲烷化工艺的合成氨原料气净化方法“双甲”工艺应运而生。
所谓“双甲”工艺,实际上就是合成氨厂将联醇、甲烷化技术引入原料气净化系统,从而省去落后的铜洗再生工艺,从技术本身来说并不是一个新的领域,然而就甲醇化来说,它又不同于以往的联醇生产,必须兼顾到产醇和净化两个互相矛盾而又依存的目标。
对于甲烷化,却又存在反应率和热平衡相互抵触的问题,反应率高,热平衡好,但CH4生成量大,对氨合成不利;反之则热平衡又难以维系。
要作到甲醇化、甲烷化二者的和谐统一,有很多工程技术难题,为此,国内外众多商家和工程技术人员经过十多年不懈的努力,开发出各具特色的流程,在不断总结成功与失败、经验与教训的基础上。
使得以甲醇甲烷化净化技术日趋完善提高,形成多种形式竞争发展的态势。
目前,国内外已有的甲醇甲烷化工艺按醇化压力等级区分大体可以分为三类,中压双甲工艺、等高压双甲工艺和非等压醇烷化工艺。
按甲烷化所使用的镍系或铁系催化剂又可分为醇烷化和醇烃化两种工艺路线。
4.国内甲醇甲烷化净化工艺发展从技术层面上看,氨厂联产甲醇早已有之,氨厂用甲烷化精制原料气国内外也早已有之,两者的结合形成醇烷化即双甲净化工艺是水到渠成的事情。
但是在实现这一工艺技术的方法上,不同的商家和研究者有着不同的观点。
其中在国内较有影响的有湖南安淳公司中压双甲及醇烃化净化工艺、河南省化肥公司公司高压深度净化工艺、杭州林达公司等高压双甲净化工艺以及南京国昌公司全自热非等压醇烷化净化工艺。
4.1.中低压脱硫甲醇甲烷化净化工艺这是安淳公司在90年提出92年12月获得授权的发明专利(专利申请号:90105545.X)。
由于技术上的原因,至今尚未工业化,该发明是“一种合成氨原料气精制工艺,它特别适用于以煤为原料,采用空气、蒸汽造气的中小型氮肥厂原料气得精制,原料气经变换、脱碳以后,在5.0-15Mpa条件下,在同一个分段装有脱硫催化剂,甲醇催化剂,甲烷催化剂的精制塔内,依次、分别、连续进行脱硫反应,与H2生成甲醇、甲烷反应使原料气精制。