自卸车检验标准
自卸车通用检验标准
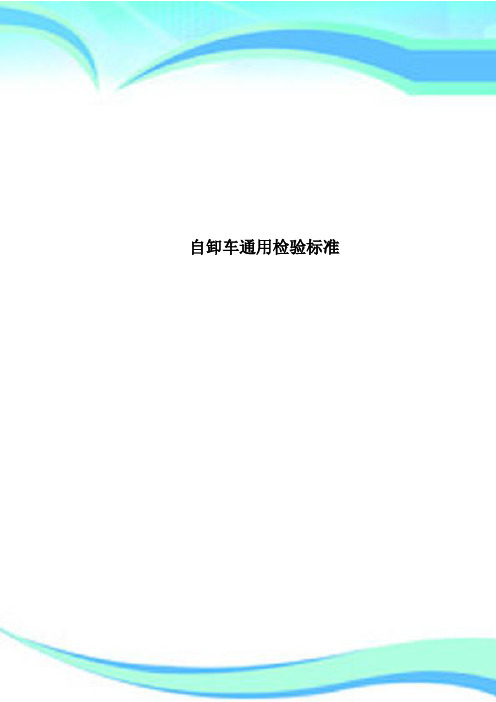
自卸车通用检验标准————————————————————————————————作者:————————————————————————————————日期:文件编号:受控状态发放号自卸车通用制造检验规范编制:审核:批准:2006年月日发布2006年月日实施前言自卸车通用制造检验规范1 范围本标准规定了自卸车的技术要求、制造检验规范,试验方法。
本标准适用于本公司生产的各种型号自卸车(上装)的制造及最终检验。
2 规范性引用文件下列文件中的条款通过本规范的引用而成为本规范的条款。
凡是注日期的引用文件,其随后所有的修改单(不包括勘误的内容)或修订版均不适用于本规范,然而,鼓励根据本规范达成协议的各方研究是否可使用这些文件的最新版本。
凡是不注日期的引用文件,其最新版本适用于本规范。
GB7258-2004 机动车运行安全技术条件GB1589-2004 道路车辆外廓尺寸、轴荷及质量限值GB/T 3766 液压系统通用技术条件QC/T 223-1997 自卸车性能试验方法QC/T 252-1998 专用汽车定型试验规程QC/T 319-1999 自卸汽车取力器技术条件QC/T 460-1999 自卸汽车液压缸技术条件QC/T 460-1999 自卸汽车栏板锁紧装置技术条件3 技术要求及检验规范3.1 整车要求3.1.1 自卸汽车整车必须符合本规范要求,并按照规定程序批准的图样及技术文件制造。
3.1.2 自卸汽车外廓尺寸应符合GB1589-2004《道路车辆外廓尺寸、轴荷及质量限值》的规定,货箱内部尺寸等必须符合产品公告和图纸要求。
3.1.3 自卸汽车上装按质心,轴荷设计要求计算,严格按图纸及公告尺寸施工。
3.1.4 照明及信号系统应符合GB4785-1998《汽车及挂车外部照明和信号装置的安装规定》的要求。
a)自卸车应安装两只红色后示廓灯,安装在后立柱上部;b)自卸车应安装两只红色前示廓灯,安装在前立柱上部;c)自卸车应安装侧标志灯和侧回复反射器,琥珀色,安装位置高度距地面不得小于900,不得大于1500,最好是车架边纵梁处,整车纵向位置是距前部小于3000,距后部小于900,两灯中间位置相距小于3000,最大不能超过3500;d)后转向灯、后位灯离地高度不得小于900,大于1200,后位灯距外廓侧面不得小于400;e)车辆后部必须安装一只红色后雾灯,不能与后位灯干涉,二者相距至少200;f)车辆后部必须安装后回复反射器,三角形红色2只,安装在保险杠上或后尾板上,距车辆左右侧不得小于400,并且对称安装。
自卸车检验指导书

1.生产过程检验1.1副车架总成检验规范1.1.1.检验项目及标准1.1.1.1车架长度公差±5mm,宽度公差负1-3毫米。
用钢卷尺测量。
1.1.1.2车架下平面平面度≤4mm。
1.1.1.3两纵梁直线度任意5米内≤4mm。
5-7米≤6mm。
7米以上≤8mm。
1.1.1.4翻转轴孔中心相对于纵梁底平面误差≤1mm。
1.1.1.5翻转轴孔轴向与总量垂直度≤1度。
1.1.1.6翻转轴套两端相对于两纵梁中心线对称度≤2mm。
1.1.1.7油缸支座中心与两纵梁中心左右偏差不大于2mm。
1.1.1.8油缸支座至后翻转轴套两端距离差不大于5mm。
1.1.1.9底架对角线差≤5mm。
1.1.1.10外观要求:平整;清洁;无焊丝头、氧化铁;无扭曲变形、锤痕、凹陷等外观缺陷。
焊缝应美观,洁净不得有焊瘤、咬边、气孔、夹渣、假焊、偏焊、漏焊,焊缝标准应达到厂标二级以上标准。
1.1.2.对以上检验项目的说明1.1.2.1以上检验项目由生产班组先进行自检,然后由检验员进行专检。
1.1.2.2以上检验项目的检查必须采用全检的方法.有一项不合格就不能进行下道工序。
1.1.2.3检验员必须做到认真检验,严格要求,并做好检验记录。
1.1.2.4以上检验项目用250×500mm直角弯尺;5米、20米钢卷尺。
1.2底架总成检验规范1.2.1.检验项目及标准1.2.1.1板材厚度符合国家GB/T1222-1989规定标准。
底架总长度±5mm,底板宽度±3mm。
两纵梁宽度公差负2-4mm。
1.2.1.2两纵梁纵向中心与底板纵向中心错移量≤3mm。
1.2.1.3底架总体6米以内平面度≤3mm。
6米以上平面度≤5mm。
1.2.1.4焊后变形允许有一定上拱,上拱高度≤2mm。
不允许下塌。
1.2.1.5两纵梁下端平面到底板两侧距离差≤5mm。
1.2.1.6底架对角线差≤5mm。
1.2.1.7主托架工作面距纵梁下表面距离±1mm。
金属非金属露天矿山在用矿用自卸汽车安全检验规范
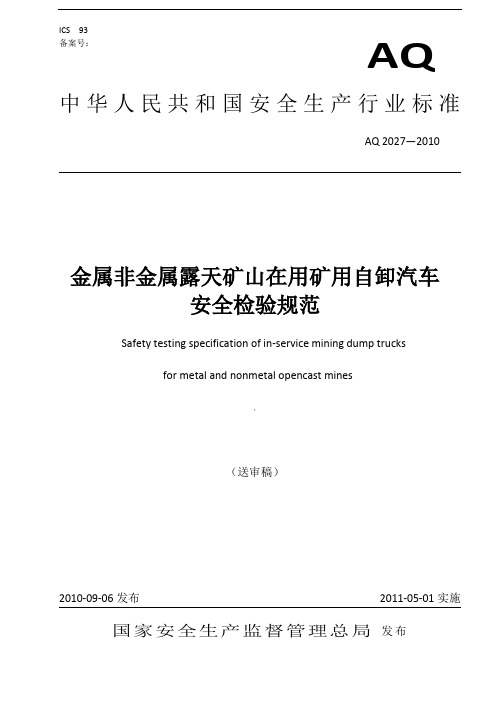
ICS 93 备案号:AQ金属非金属露天矿山在用矿用自卸汽车安全检验规范Safety testing specification of in-service mining dump trucksfor metal and nonmetal opencast mines:(送审稿)国家安全生产监督管理总局发布目次前言 (II)1范围 (1)2规范性引用文件 (1)3定义 (1)4检验基本要求 (2)5检验项目及技术要求 (2)6判定规则 (6)7检验方法及仪器 (8)8检验周期 (8)前言本标准为强制性标准。
本标准由国家安全生产监督管理总局提出。
本标准由全国安全生产标准化技术委员会非煤矿山安全分技术委员会归口。
本标准负责起草单位:国家安全生产长沙矿山机电检测检验中心。
本标准主要起草人:贺建国、翟守忠、李春娟、骆拓、袁乐安、龚文、周建、邓宇、周振华、王四现、季光洲、罗振兴。
本标准为首次发布。
金属非金属露天矿山在用矿用自卸汽车安全检验规范1范围本标准规定了金属非金属露天矿山在用矿用自卸汽车安全检验的项目、技术要求、检验方法、判定规则和检验周期。
本标准适用于金属非金属露天矿山在用矿用自卸汽车现场检验。
2规范性引用文件下列文件中的条款通过本标准的引用而成为本标准的条款。
凡是注日期的引用文件,其随后所有的修改单(不包括勘误的内容)或修订版均不适用于本标准,然而,鼓励根据本标准达成协议的各方研究是否可使用这些文件的最新版本。
凡是不注日期的引用文件,其最新版本适用于本标准。
GB 7258—2004 机动车运行安全技术条件GB 16423—2006 金属非金属矿山安全规程3术语和定义下列术语和定义适用于本标准。
3.1金属非金属露天矿山metal and nonmetal opencast mines在地表开挖区通过剥离围岩、表土或砾石,采出供建筑业、工业或加工业用的金属或非金属矿物的采矿场及其附属设施。
3.2矿用自卸汽车mining dump trucks矿山用载重10 t 以上,以柴油机为动力的自卸汽车,包括电传动矿用自卸汽车。
自卸车标准
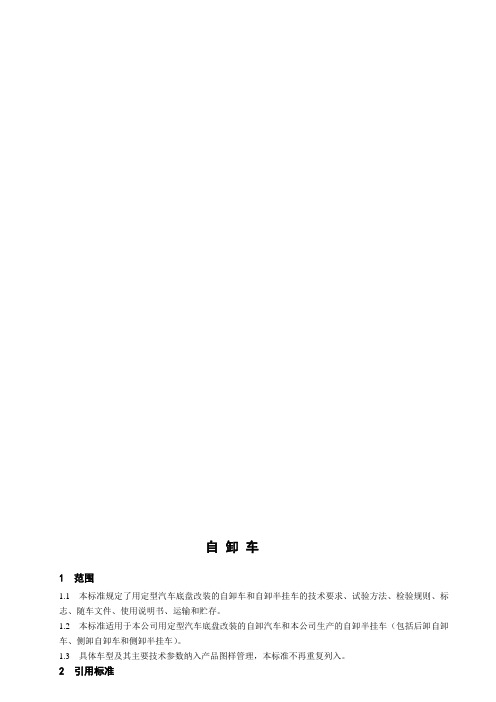
自卸车1 范围1.1 本标准规定了用定型汽车底盘改装的自卸车和自卸半挂车的技术要求、试验方法、检验规则、标志、随车文件、使用说明书、运输和贮存。
1.2 本标准适用于本公司用定型汽车底盘改装的自卸汽车和本公司生产的自卸半挂车(包括后卸自卸车、侧卸自卸车和侧卸半挂车)。
下列标准所包含的条文,通过在本标准中引用而构成为本标准的条文,所有标准都会被修定,使用本标准的各方应探讨使用下列标准最新版本的可能性。
GB 1589-2004 道路车辆外廓尺寸、轴荷及质量限值GB 3766-2001 液压系统通用技术条件GB 4785-1998 汽车及挂车外部照明和信号装置的安装GB 5920-1999 汽车及挂车前位灯、后位灯、示廓灯和制动灯配光性能GB 7258-2004 机动车运行安全技术条件GB 9969.1-1998 工业产品使用说明书总则GB 11554-1998 汽车与挂车之后雾灯配光性能GB 11564-1998 机动车回复反射器GB 11567.1-2001 汽车和挂车侧面防护要求GB 11567.2-2001 汽车和挂车后下部防护要求GB/T 12674-1990 整车质量(重量)参数测定方法GB 15741-1995 汽车和挂车号牌板(架)及其位置GB 17509-1998 汽车和挂车转向信号灯配光性能GB 18099-2000 汽车及挂车侧标志灯配光性能JB/T 5943-1991 工程机械焊接件通用技术条件GB 4019-1985 汽车驻车制动性能要求QC/T 222-1997 自卸汽车通用技术条件QC/T 223-1997 自卸汽车性能试验方法QC/T 252-1998 专用汽车定型试验规程QC/T 319-1999 自卸汽车取力器技术条件QC/T 460-1999 自卸汽车液压缸技术条件QC/T 461-1999 自卸汽车换向阀技术条件QC/T 559-1999 货车、客车行车制动性能要求QC/T 569-1999 汽车驻车制动试验方法QC/T 625-1999 汽车用涂镀层和化学处理层。
煤矿自卸汽车检测标准

煤矿自卸汽车检测标准一、外观检测1.车辆外观应整洁,无严重磨损、锈蚀、凹陷、变形等情况。
2.车身各部件(包括车灯、后视镜、门锁、车门气动杆等)应完整,无损坏。
3.车辆标识(包括车牌、车辆识别码、安全警示标志等)应清晰、完整。
二、尺寸检测1.车辆的长、宽、高应符合设计要求,允许偏差不超过±5%。
2.车辆的轴距、轮距应符合设计要求,允许偏差不超过±3%。
3.车辆的整备质量、满载质量应符合设计要求,允许偏差不超过±5%。
三、重量检测1.车辆的总重量应符合设计要求,允许偏差不超过±5%。
2.车辆的轴荷分布应符合设计要求,允许偏差不超过±3%。
四、载重检测1.车辆的最大载重应符合设计要求,允许偏差不超过±5%。
2.车辆的额定载重应符合设计要求,允许偏差不超过±3%。
3.车辆在额定载重下的行驶性能应稳定,无跑偏、飘逸等现象。
五、性能检测1.车辆的动力性能应符合设计要求,发动机功率、扭矩应达到额定值,加速性能良好。
2.车辆的制动性能应符合设计要求,制动距离、制动效能稳定可靠。
3.车辆的操控性能应符合设计要求,转向灵敏、稳定,无跑偏、振荡等现象。
4.车辆的通过性能应符合设计要求,对不同地形、路况的适应能力强。
5.车辆的燃油经济性能应符合设计要求,百公里油耗应达到较低水平。
六、安全性检测1.车辆的安全设施(如刹车防抱死系统、防滑系统、安全带、应急逃生门等)应工作正常,无故障。
2.车辆的稳定性应良好,在满载及复杂路况下应能保持稳定行驶。
3.车辆的灯光系统(包括前照灯、后尾灯、转向灯等)应工作正常,无故障。
4.车辆的安全警示标志(如危险品标志、放大号牌等)应清晰可见。
七、可靠性检测1.车辆的主要部件(如发动机、变速箱、车桥等)应工作正常,无异响、无泄漏。
2.车辆的电气系统(包括电源、用电设备等)应工作稳定,无故障。
3.车辆的液压系统(如液压倾卸机构)应工作稳定,无泄漏。
自卸车检验作业指导书1

自卸车检验作业指导书检验项目图片检验标准检验方法副车架总成检验车架长度公差±5mm,宽度公差负1-3mm 钢卷尺车架下平面平面度≤4mm 直角尺两纵梁直线度任意5M内≤4mm,5-7M≤6mm,7M以上≤8mm钢卷尺翻转轴孔中心相对于纵梁底平面误差≤1mm 钢卷尺翻转轴孔轴向与纵梁垂直度≤1度直角尺翻转轴套两端相对于两纵梁中心线对称度≤2mm 钢卷尺油缸支座中心与两纵梁中心摆布偏差≤2mm 钢卷尺油缸支座至后翻转轴套两短距离差≤5mm 钢卷尺底架对角线误差≤5mm 钢卷尺外观平整;清洁;无焊丝头、氧化铁;无扭曲变形、锤痕、凹陷等外观缺陷。
焊缝美观,不得有焊瘤、咬边、气孔、夹渣、假焊、偏焊、漏焊等,焊缝标准应达到相关标准。
目测编制校对标准化审核批准检验项目图片检验标准检验方法底架总成检验板材厚度符合国家GB/T1222-1989规定标准。
底架总长度±5mm,底板宽度±3mm,两纵梁宽度公差负2-4mm。
钢卷尺两纵梁纵向中心与底板纵向中心错移量≤3mm。
钢卷尺底架总体6米以内平面度≤3mm,6米以上平面度≤5mm。
钢卷尺焊后变形上拱高度≤2mm,不允许有下塌。
钢卷尺两纵梁下端平面到底板两侧距离差≤5mm。
钢卷尺底架对角线差≤5mm。
钢卷尺主托架工作面距纵梁下表面距离±1mm。
钢卷尺主托架中心道后翼梁距离±3mm。
钢卷尺主托架与纵梁焊接坚固、可靠。
目测底架纵梁、底架横梁与底板焊接角高度8mm、为100mm断续焊,其他部位焊角高6mm、全方位焊接。
钢卷尺、目测底架尾部横梁外侧打印字码,标记生产编号目测编制校对标准化审核批准检验项目图片检验标准检验方法底架总成检验外观平整;清洁;无焊丝头、氧化铁;无扭曲变形、锤痕、凹陷等外观缺陷。
焊缝美观,不得有焊瘤、咬边、气孔、夹渣、假焊、偏焊、漏焊等,焊缝标准应达到相关标准。
目测编制校对标准化审核批准检验项目图片检验标准检验方法货箱检验厢板宽(长)度方向误差允许负0-3mm,高度方向允许误差±3mm,板材厚度符合国家GB/T1222-1989规定标准。
AQ 2027—2010《《金属非金属露天矿山在用矿用自卸汽车安全检验规范》

在用自卸车
MT4400
MT4400
SF3102
3311E
MT4400
SF31904
TR-100
3307水车
同力841
SF33900
SF31904
MT4400 整机参数
(1) 额定载重量:220公吨。 (2) 驱动型式:交流-直流-交流 电传动方式 (3) 发动机功率(KW):1865 (4) 长× 宽× 高(m):14.1× 8× 7.1 (5) 最小转弯半径(m):15.2 (6) 轴距(m):6.4 (7) 轮距前轮(m):6.3 (8) 轮距后轮(m):7.6 (9) 箱斗举升时最大高度(m):12.8 (10) 箱斗举升最大角度(° ):45 (11) 装载高度(2:1堆装)(m):8.95 (12) 最大爬坡坡度%:14% (13) 最大速度km/h:64 (14)整车自重Kg:170975
现场组装
2.规范性引用文件
GB 7258—2004 机动车运行安全技术条件 GB 16423—2006 金属非金属矿山安全规 程
3.术语和定义
3.1矿用自卸汽车 矿山用载重10 t 以上,以柴油机为动力的自卸 汽车,包括电传动矿用自卸汽车。 3.2最小转弯直径 汽车前轮处于最大转角状态行驶时,车体离转 向中心最远点形成的轨迹圆直径。
5.检验项目及技术要求
ቤተ መጻሕፍቲ ባይዱ
液压转轮靠液压转向器转动改变方向:即液压动力式转向器 转向器 (也常称为转向机)是完成由旋转运动到直线运动(或近似直线动) 的一组齿轮机构,同时也是转向系中的减速传动装置。它是转 向系中最重要的部件。 它的作用是:增大转向盘传到转向传动 机构的力和改变力的传递方向。
3.3方向盘自由行程 转向轮在直线行驶位臵时,方向盘的空转角度。
自卸车出厂检验规范

编号:QMSW(8.2.4)质检06.1—2000自卸车出厂检验规范1.目的为了提高自卸半挂车系列产品质量,保证产品主要零部件结构的一致性,对采购、生产过程中的检验、出厂检验提供依据。
2.范围本规程适用于本公司半挂车系列产品的质量检验活动。
3.引用标准或文件JB/T4185-1986 半挂车通用技术条件QC/T223-2010 自卸车通用技术条件QMSW(8.2.4)质检06.1—2000 半挂车系列产品检验规程试验条件:自卸半挂车在空载状态下,停止在平坦、硬实场地上外观1.外廓尺寸符合图纸规定2.焊缝应无裂缝、焊坑、焊穿、焊渣、漏焊等现象3.所有外露的黑色金属件应采取防腐防锈处理,油漆色泽鲜艳,无皱皮、污痕4.所有管路排列平直、整齐,所有零件装配位置正确5.将上述情况目测记录性能要求1.标记、外观、车辆参数、一致性、反光标记、侧后防护、装配质量、电器、制动的检查参照:QMSW(8.2.4)质检06.1—2000《半挂车系列产品检验规程》2.耐压试验:1.5倍额定工作压力保压1min,不允许出现渗油、破裂、局部膨胀及接头脱开等现象。
液压油箱在50KPa压力下保压1min不应有渗漏现象。
3.车厢最大举升角不小于45°,车厢空载举升最大举升角的时间不小于20s,空载从最大举升角下降到副车架贴合的时间不大于20s。
车厢分别举升10°和20°,停留5min时车厢自降量不大于2.5°。
4.车厢在超重10%的状态下,分别举升到10°和°时停留5min车厢自降不超过3°。
5.空载时车厢纵梁与底架或垫铁之间应贴合,间隙不大于5mm。
6.车厢举升下降应平稳,不允许发生窜动、冲撞和卡滞现象。
车厢栏板应开关灵活,锁紧可靠,在行驶过程中,不得自动打开。
分配阀密封可靠,操纵灵活。
编制: 审核:批准:日期:2012.09.01。
自卸车验收表

自卸车验收表自卸车验收表工程名称:规格型号:序号检查项目检查内容1 操作人员自卸车的操作人员必须通过国家专门机构的培训和考试,持证上岗操作。
2 控制线路自卸车的控制线路必须稳定可靠,不得存在线路漏电或破皮等现象。
控制总闸必须灵敏可靠。
3 制动刹车自卸车的制动刹车必须齐全可靠。
4 方向自卸车的方向必须灵活,磨损不得超过规定要求,间隙不得过大。
5 仪器仪表自卸车的控制仪器仪表必须定期进行校验,确保仪表的准确可靠性。
6 保养自卸车必须定期进行维修保养,确保各活动部位的灵敏。
7 灯光自卸车的灯光必须能够满足行驶和夜间施工的要求。
8 四漏情况自卸车不得有漏油、漏电、漏气、漏水等情况发生。
注:删除了明显有问题的段落,并对每段话进行了小幅度的改写。
自卸车是建筑工地上常用的一种车辆,用于运输各种建筑材料。
为确保自卸车的安全运行,必须进行严格的验收。
本文提供了一份自卸车验收表,以供参考。
该表格包括了自卸车的各项检查内容,如操作人员、控制线路、制动刹车、方向、仪器仪表、保养、灯光和四漏情况等。
对于每一项检查内容,都有相应的要求和注意事项。
例如,自卸车的操作人员必须经过专门机构的培训和考试,持证上岗操作。
控制线路必须稳定可靠,不得存在线路漏电或破皮等现象。
制动刹车必须齐全可靠。
方向必须灵活,磨损不得超过规定要求,间隙不得过大。
仪器仪表必须定期进行校验,确保仪表的准确可靠性。
自卸车必须定期进行维修保养,确保各活动部位的灵敏。
自卸车的灯光必须能够满足行驶和夜间施工的要求。
自卸车不得有漏油、漏电、漏气、漏水等情况发生。
只有经过严格的验收,自卸车才能安全地运输建筑材料。
自卸车检验规范
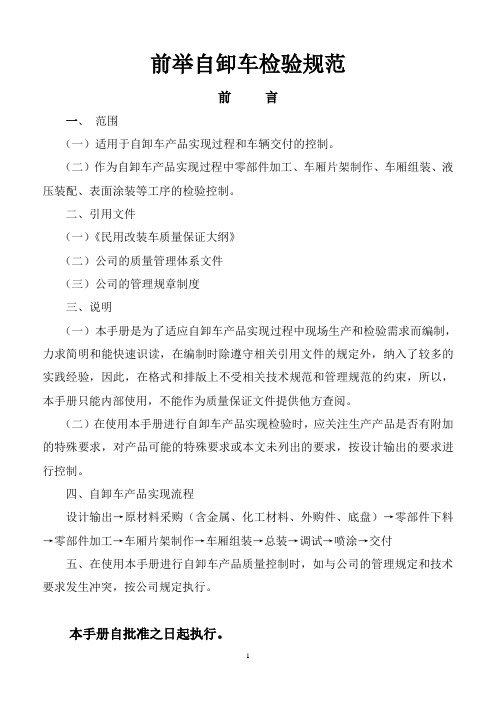
前举自卸车检验规范前言一、范围(一)适用于自卸车产品实现过程和车辆交付的控制。
(二)作为自卸车产品实现过程中零部件加工、车厢片架制作、车厢组装、液压装配、表面涂装等工序的检验控制。
二、引用文件(一)《民用改装车质量保证大纲》(二)公司的质量管理体系文件(三)公司的管理规章制度三、说明(一)本手册是为了适应自卸车产品实现过程中现场生产和检验需求而编制,力求简明和能快速识读,在编制时除遵守相关引用文件的规定外,纳入了较多的实践经验,因此,在格式和排版上不受相关技术规范和管理规范的约束,所以,本手册只能内部使用,不能作为质量保证文件提供他方查阅。
(二)在使用本手册进行自卸车产品实现检验时,应关注生产产品是否有附加的特殊要求,对产品可能的特殊要求或本文未列出的要求,按设计输出的要求进行控制。
四、自卸车产品实现流程设计输出→原材料采购(含金属、化工材料、外购件、底盘)→零部件下料→零部件加工→车厢片架制作→车厢组装→总装→调试→喷涂→交付五、在使用本手册进行自卸车产品质量控制时,如与公司的管理规定和技术要求发生冲突,按公司规定执行。
本手册自批准之日起执行。
目录一、自卸车底盘入厂、流转及车辆交付要求-----------------------4二、车厢片架制作及检验要求-----------------------------------------6三、前举自卸车副车架制作及上装检验要求-----------------------8四、车厢制作及检验要求---------------------------------------------10五、前举自卸车车厢及其附件上装检验要求-----------------------11六、前举自卸车液压系统上装及检验要求--------------------------14七、车厢涂装检验要求--------------------------------------------------18自卸车底盘入厂、流转及车辆交付要求一、自卸车底盘入厂验收及流转要求(一)底盘入厂验收1、按《自卸车底盘入厂复验细则》的规定执行,各职能部门按公司相关规定各负其责。
自卸车检验规程

章节号:1第1页 共12页版本/修订状态:A/0检验规程生效日期:2011年9月1.关键外购、外协件与原材料检验/验证规程1.1目的确保关键外购、外协件与主要原材料符合产品图和相关设计文件的要求,保证生产 产品的一致性要求。
1.2范围适用于本公司主要原材料与外购件、外协件的进货检验。
1.3检验规程序号进货名称检验/验证要求检验/验证方法抽样与判定周期或频次1底盘1)底盘型号是否与产品图及合同要求底盘型号一致;2)随车文件齐全;3)随车工具及备胎齐全4)整车外观检验 (面漆、紧固件、丢、缺、损件、轮胎划伤等) 5)三漏(电、汽、液)6)性能(启动、怠速、制动)7)底盘不允许歪斜,左右纵梁及高度差≤58)三液(齿轮油、柴油、防冻液)1)依据产品图、技术要求及合同2)装箱单3)装箱单4)目测 5)目测、听6)启车、行驶、制动试验7)目测、圈尺8)按技术文件全数查验、合格接收每批查验2泵、缸、阀1)缸、阀型号是否与产品图及合同要求型号一致;2)随机文件及合证3)外观质量(无脱漆、锈蚀、裂痕、划伤等)4)启动压力、密封、耐压试验 1)依据产品图、技术要求及合同2)装箱单3)目测4)依相关标准及技术条件(由供方提供)1、2、3项全数查验、合格接收4)由供方每半年提供一份相应项目检测报告每批查验3高压油管1)合格证、规格型号、外观质量、标识高压油管2)耐压试验1)依据产品图、技术要求及合同。
目测外观质量2)依相关标准及技术条件(由供方提供)1项全数查验2由供方每半年提供一份相应项目检测报告每批查验4后翻座1)合格证、规格型、外观质量、(有无锈蚀、裂痕、划伤等)2)几何尺寸1)依据产品图、技术要求及合同。
目测外观质量2)供方产品图1)全数查检2)抽样合格接收1)合格接收2)抽验50%, 一件不合格全验。
序号进货名称检验/验要求检验/验证方法抽样与判定周期或频次5灯具1、合格证、规格型号、外观质量2、出公司检验报告查验试验报告、合格证、规格型号、目测外观质量每20套抽查1套,手续齐全、外观质量合格接收,否则拒收每批查验6型钢及扳材1、产品质量证明书、规格型号外观质量(有无锈蚀、尺寸等)、进货数量查验质量证明书、查验规格型号、实测进货数量、目测外观质量全数查验、合格接收7电焊条(丝)1、合格证、规格型号、外观质量、包装标识、工业产品生产许可证查验检验报告、合格证、规格型号、包装标示、生产许可证编号、目测外观质量每10箱抽查1箱中的任一最小包装单元,手续齐全、包装标识、外观质量合格接收、否则拒收每批查验注: a)货物供应商如有质量体系认证证书或产品认证证书优先选择b)当进货检验由供应商完成时,就对供应商提出明确的检验要求,具体见《采购控制程序》。
自卸车技术检验标准
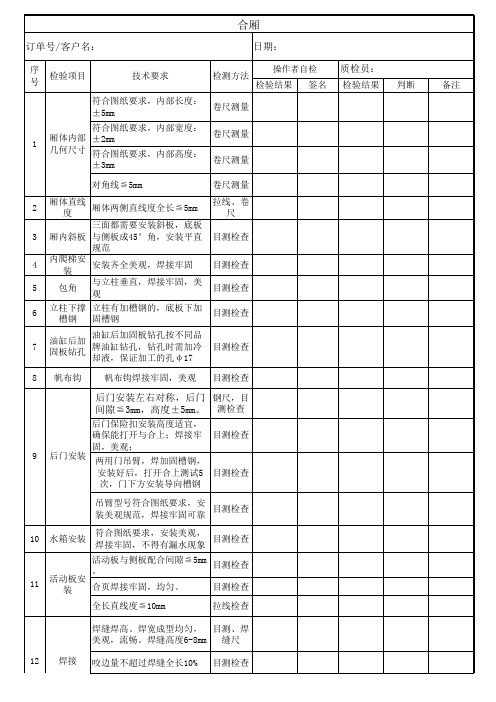
订单号/客户名:
序号 检验项目 技术要求 符合图纸要求,内部长度: ±5mm 1 符合图纸要求,内部宽度: 厢体内部 ±2mm 几何尺寸 符合图纸要求,内部高度: ±3mm 对角线≦5mm 2 3 4 5 6 厢体直线 厢体两侧直线度全长≦5mm 度 三面都需要安装斜板,底板 厢内斜板 与侧板成45°角,安装平直 规范 内爬梯安 安装齐全美观,焊接牢固 装 与立柱垂直,焊接牢固,美 包角 观 立柱下撑 立柱有加槽钢的,底板下加 槽钢 固槽钢 油缸后加固板钻孔按不同品 油缸后加 牌油缸钻孔,钻孔时需加冷 固板钻孔 却液,保证加工的孔φ 17 帆布钩 帆布钩焊接牢固,美观 检测方法 卷尺测量 卷尺测量 卷尺测量 卷尺测量 拉线、卷 尺 目测检查 目测检查 目测检查 目测检查
12
焊接 焊缝表面不得有裂纹、气孔 、弧坑、偏焊及未烧透等现 象。 目测检查 按图检查 目测检查
13 14
其他
按图纸技术要求
平整、清洁、无杂物(焊丝 外观检查 头、飞溅残渣)、无扭曲变 形。
日期:
操作者自检
质检员:
检验结果 判断 备注
检验结果
签名
7 8
目测检查 目测检查
后门安装左右对称,后门 钢尺,目 间隙≦3mm,高度±5mm。 测检查
后门保险扣安装高度适宜, 确保能打开与合上;焊接牢 固,美观; 9 后门安装 目测检查
两用门吊臂,焊加固槽钢, 安装好后,打开合上测试5 目测检查 次,门下方安装导向槽钢 吊臂型号符合图纸要求,安 目测检查 装美观规范,焊接牢固可靠
10
水箱安装
符合图纸要求,安装美观, 目测检查 焊接牢固,不得有漏水现象 活动板与侧板配合间隙≦5mm 目测检查 。 目测检查 拉线检查
自卸车检验标准
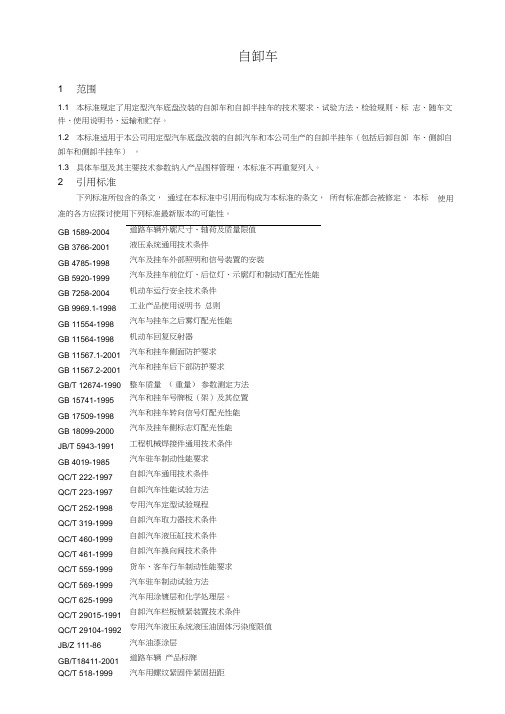
自卸车1 范围1.1 本标准规定了用定型汽车底盘改装的自卸车和自卸半挂车的技术要求、试验方法、检验规则、标志、随车文件、使用说明书、运输和贮存。
1.2 本标准适用于本公司用定型汽车底盘改装的自卸汽车和本公司生产的自卸半挂车(包括后卸自卸车、侧卸自卸车和侧卸半挂车)。
1.3 具体车型及其主要技术参数纳入产品图样管理,本标准不再重复列入。
2 引用标准下列标准所包含的条文,通过在本标准中引用而构成为本标准的条文,所有标准都会被修定,本标使用准的各方应探讨使用下列标准最新版本的可能性。
GB 1589-2004道路车辆外廓尺寸、轴荷及质量限值GB 3766-2001液压系统通用技术条件GB 4785-1998汽车及挂车外部照明和信号装置的安装GB 5920-1999汽车及挂车前位灯、后位灯、示廓灯和制动灯配光性能GB 7258-2004机动车运行安全技术条件GB 9969.1-1998工业产品使用说明书总则GB 11554-1998汽车与挂车之后雾灯配光性能GB 11564-1998机动车回复反射器GB 11567.1-2001汽车和挂车侧面防护要求GB 11567.2-2001汽车和挂车后下部防护要求GB/T 12674-1990整车质量(重量)参数测定方法GB 15741-1995汽车和挂车号牌板(架)及其位置GB 17509-1998汽车和挂车转向信号灯配光性能GB 18099-2000汽车及挂车侧标志灯配光性能JB/T 5943-1991工程机械焊接件通用技术条件GB 4019-1985汽车驻车制动性能要求QC/T 222-1997自卸汽车通用技术条件QC/T 223-1997自卸汽车性能试验方法QC/T 252-1998专用汽车定型试验规程QC/T 319-1999自卸汽车取力器技术条件QC/T 460-1999自卸汽车液压缸技术条件QC/T 461-1999自卸汽车换向阀技术条件QC/T 559-1999货车、客车行车制动性能要求QC/T 569-1999汽车驻车制动试验方法QC/T 625-1999汽车用涂镀层和化学处理层。
自卸车过程检验流程

自卸车过程检验流程一、检验前的准备。
咱得先让自己精神饱满地去做这个检验。
检验员得穿上合适的工作服,可不能穿个奇装异服就去了,这就像战士上战场得穿好军装一样。
然后要拿好各种检验工具,像卡尺啊,手电筒啊这些,要是没带齐工具,到时候发现问题却没法准确测量,那可就抓瞎啦。
而且呀,得对要检验的自卸车的基本信息有个大概的了解,是哪个型号的,大概生产批次之类的,这就好比要去见一个新朋友,先知道点基本情况才好打交道嘛。
二、外观检验。
三、车厢部分检验。
车厢可是自卸车的关键部分呢。
走进车厢,看看车厢的钢板有没有裂缝或者腐蚀的地方。
要是有裂缝,就像房子的墙裂了缝一样危险,装东西的时候可能就会出问题。
检查车厢的连接部位,螺丝有没有拧紧,要是螺丝松松垮垮的,那车厢可能就会晃来晃去,这可不好。
再看看车厢的举升装置,能不能正常工作呢?想象一下,如果举升装置坏了,车厢就像个不听话的孩子,不肯起来,那可怎么卸货呀。
四、底盘部分检验。
底盘就像是自卸车的脚一样重要。
趴在地上(当然要注意安全啦)看看底盘有没有漏油的地方,要是地上有一滩油,就像自卸车在偷偷地哭呢,肯定是哪里出问题了。
检查底盘的各个部件有没有松动或者损坏,像传动轴啊,悬架啊这些。
要是传动轴松了,就像人的腿关节松了一样,走路都不稳。
悬架要是坏了,那自卸车在路上跑起来就会颠颠簸簸的,像个喝醉酒的大汉。
五、动力系统检验。
动力系统就像是自卸车的心脏。
打开发动机舱,听听发动机的声音,要是发动机的声音像小猫打呼噜一样轻柔平稳,那还不错。
要是像个生病的老人一样咳嗽气喘,那肯定是有问题啦。
检查发动机的各种管路,有没有破损或者老化的,这就像人的血管一样,要是血管出问题了,身体肯定不健康。
还要看看变速箱,换挡是不是顺畅呢?要是换挡的时候像卡住了一样,那自卸车跑起来就会很不自在。
六、检验后的总结。
检验完了之后呢,要把所有发现的问题都记下来。
这就像写日记一样,把自卸车的小毛病都写得清清楚楚。
然后根据这些问题判断自卸车是不是合格,如果有小问题,要看看能不能简单修复,如果是大问题,那可就得好好研究研究怎么解决啦。
自卸车通用检验标准
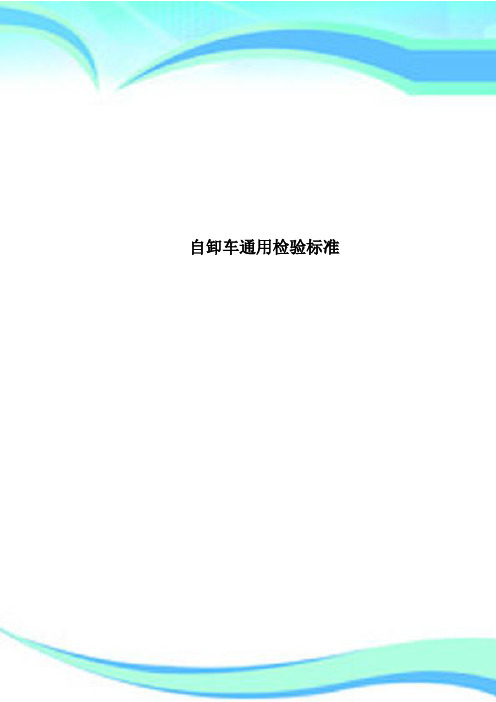
自卸车通用检验标准————————————————————————————————作者:————————————————————————————————日期:文件编号:受控状态发放号自卸车通用制造检验规范编制:审核:批准:2006年月日发布2006年月日实施前言自卸车通用制造检验规范1 范围本标准规定了自卸车的技术要求、制造检验规范,试验方法。
本标准适用于本公司生产的各种型号自卸车(上装)的制造及最终检验。
2 规范性引用文件下列文件中的条款通过本规范的引用而成为本规范的条款。
凡是注日期的引用文件,其随后所有的修改单(不包括勘误的内容)或修订版均不适用于本规范,然而,鼓励根据本规范达成协议的各方研究是否可使用这些文件的最新版本。
凡是不注日期的引用文件,其最新版本适用于本规范。
GB7258-2004 机动车运行安全技术条件GB1589-2004 道路车辆外廓尺寸、轴荷及质量限值GB/T 3766 液压系统通用技术条件QC/T 223-1997 自卸车性能试验方法QC/T 252-1998 专用汽车定型试验规程QC/T 319-1999 自卸汽车取力器技术条件QC/T 460-1999 自卸汽车液压缸技术条件QC/T 460-1999 自卸汽车栏板锁紧装置技术条件3 技术要求及检验规范3.1 整车要求3.1.1 自卸汽车整车必须符合本规范要求,并按照规定程序批准的图样及技术文件制造。
3.1.2 自卸汽车外廓尺寸应符合GB1589-2004《道路车辆外廓尺寸、轴荷及质量限值》的规定,货箱内部尺寸等必须符合产品公告和图纸要求。
3.1.3 自卸汽车上装按质心,轴荷设计要求计算,严格按图纸及公告尺寸施工。
3.1.4 照明及信号系统应符合GB4785-1998《汽车及挂车外部照明和信号装置的安装规定》的要求。
a)自卸车应安装两只红色后示廓灯,安装在后立柱上部;b)自卸车应安装两只红色前示廓灯,安装在前立柱上部;c)自卸车应安装侧标志灯和侧回复反射器,琥珀色,安装位置高度距地面不得小于900,不得大于1500,最好是车架边纵梁处,整车纵向位置是距前部小于3000,距后部小于900,两灯中间位置相距小于3000,最大不能超过3500;d)后转向灯、后位灯离地高度不得小于900,大于1200,后位灯距外廓侧面不得小于400;e)车辆后部必须安装一只红色后雾灯,不能与后位灯干涉,二者相距至少200;f)车辆后部必须安装后回复反射器,三角形红色2只,安装在保险杠上或后尾板上,距车辆左右侧不得小于400,并且对称安装。
- 1、下载文档前请自行甄别文档内容的完整性,平台不提供额外的编辑、内容补充、找答案等附加服务。
- 2、"仅部分预览"的文档,不可在线预览部分如存在完整性等问题,可反馈申请退款(可完整预览的文档不适用该条件!)。
- 3、如文档侵犯您的权益,请联系客服反馈,我们会尽快为您处理(人工客服工作时间:9:00-18:30)。
自卸车1 范围1.1 本标准规定了用定型汽车底盘改装的自卸车和自卸半挂车的技术要求、试验方法、检验规则、标志、随车文件、使用说明书、运输和贮存。
1.2 本标准适用于本公司用定型汽车底盘改装的自卸汽车和本公司生产的自卸半挂车(包括后卸自卸车、侧卸自卸车和侧卸半挂车)。
1.3 具体车型及其主要技术参数纳入产品图样管理,本标准不再重复列入。
2 引用标准下列标准所包含的条文,通过在本标准中引用而构成为本标准的条文,所有标准都会被修定,使用本标准的各方应探讨使用下列标准最新版本的可能性。
GB 1589-2004 道路车辆外廓尺寸、轴荷及质量限值GB 3766-2001 液压系统通用技术条件GB 4785-1998 汽车及挂车外部照明和信号装置的安装GB 5920-1999 汽车及挂车前位灯、后位灯、示廓灯和制动灯配光性能GB 7258-2004 机动车运行安全技术条件GB 9969.1-1998 工业产品使用说明书总则GB 11554-1998 汽车与挂车之后雾灯配光性能GB 11564-1998 机动车回复反射器GB 11567.1-2001 汽车和挂车侧面防护要求GB 11567.2-2001 汽车和挂车后下部防护要求GB/T 12674-1990 整车质量(重量)参数测定方法GB 15741-1995 汽车和挂车号牌板(架)及其位置GB 17509-1998 汽车和挂车转向信号灯配光性能GB 18099-2000 汽车及挂车侧标志灯配光性能JB/T 5943-1991 工程机械焊接件通用技术条件GB 4019-1985 汽车驻车制动性能要求QC/T 222-1997 自卸汽车通用技术条件QC/T 223-1997 自卸汽车性能试验方法QC/T 252-1998 专用汽车定型试验规程QC/T 319-1999 自卸汽车取力器技术条件QC/T 460-1999 自卸汽车液压缸技术条件QC/T 461-1999 自卸汽车换向阀技术条件QC/T 559-1999 货车、客车行车制动性能要求QC/T 569-1999 汽车驻车制动试验方法QC/T 625-1999 汽车用涂镀层和化学处理层。
QC/T 29015-1991 自卸汽车栏板锁紧装置技术条件QC/T 29104-1992 专用汽车液压系统液压油固体污染度限值JB/Z 111-86 汽车油漆涂层GB/T18411-2001 道路车辆产品标牌GB 16735-2004 道路车辆车辆识别代号(VIN)3要求3.1整车要求3.1.1 自卸车应符合本标准规定,并按经规定程序批准的图样及技术文件制造。
3.1.2 改装用的底盘、原材料、外购件、外协件应符合有关标准规定,并有制造厂的合格证明。
所有零、部件(包括自制件)应经检验合格后方能使用装配。
3.1.3 外观质量、装备的完整性及运行安全技术的一般要求,应符合GB 7258-2004的规定。
3.1.4 整车外廓尺寸应符合GB 1589-2004的规定。
3.1.5自卸车允许最大总质量和允许最大轴载质量不得超过原底盘车允许值的3% 。
3.1.6自卸汽车的动力性、操纵稳定性、地形通过性、燃料经济性等,应满足原底盘的规定。
3.1.7外部照明及信号装置的安装应符合GB 4785-1998。
3.1.8外部照明及信号装置的一般要求应符合GB 7258-2004。
3.1.9自卸汽车应装设后视镜,其安装要求应符合GB 15084-1994的规定。
3.1.10黑色金属外露表面应进行防腐处理。
油漆涂层应符合JB/Z 111-86的规定。
汽车用涂镀层和化学处理层应符合QC/T 625-1999的规定3.1.11底漆层厚度不低于15微米,面漆层厚度不低于30微米,漆膜外观要求光色均匀,允许有轻微“桔皮”。
但不允许有露底和严重的流痕。
3.1.12整车的漆膜应完整,不允许有露底(包括焊缝、封闭内腔)和碰伤的表面。
在总装后如有碰伤、划痕等应补漆。
3.1.13 焊接质量应符合JB/T 5943-1991的规定。
3.1.14 所有紧固件均应进行表面处理,联接必须牢固可靠,行驶中不得松脱。
轮胎螺栓紧固扭矩应在389-456(N·M)范围之内,板簧U型螺栓紧固扭矩应在243-285 (N·M)范围之内。
未注紧固扭矩应符合QC/T 518-1999的规定。
3.1.15 自卸汽车的制动性能应符合GB 7258-1997和GB 12676-1999、QC/T 559-1999的规定,驻车制动性能应符合JB 4019-1985的规定。
3.1.16 自卸汽车取力器应符合QC/T 319-1999的规定,安装后应转动灵活,无松旷、卡阻现象和无异常声响,取力器速比应保证油泵在额定工作转速时,发动机处于经济转速范围内。
3.1.17 自卸汽车的各相对运动关节,应装配油脂咀,各运动关节和摩擦面应加注和涂抹充足的、规定的润滑油或润滑脂。
3.1.18 车箱、车架的扭转变型不影响液压系统的正常工作。
扭转试验应符合QC/T 223-1997的规定。
3.1.19 自卸汽车和自卸半挂车应具有与定型汽车底盘、半挂牵引车一致的对环境、气候的适应能力,(寒冷地区按合同约定)。
3.1.20 汽车和挂车侧面和后下部防护装置应符合GB 11567.1-2001和GB 11567.2-2001的规定。
3.1.20.1 侧护网装置对于N2和N3类汽车:前缘应处在最靠近它的轮胎外切面之后295mm的范围之内;对于半挂车:前缘到转向中心销位于最后位置时的中心横截面中间的距离不能超过2.7m;对于全挂车:前缘应处在最靠近它的轮胎外切面之后495mm的范围之内。
3.1.20.2 侧护网的后缘应处在最靠近它的轮胎外切面之后295mm的范围之内;3.1.20.3 侧护网的下缘任何一点的离地高度不应大于495mm。
3.1.20.4 后护网装置在整个宽度上的下边缘离地高度不应大于495mm;宽度不可大于车辆后轴两侧车轮最外点之间的距离,并且任一端的最外缘与这一侧车辆最外端的横向水平距离不大于100mm。
3.2车厢3.2.1 车厢应有足够的强度和刚度。
3.2.2栏板锁紧装置应符合QC/T 29015-1991的规定,车厢栏板应开关灵活,锁紧可靠,在行驶过程中不得自行打开。
3.2.3 后开式车厢后栏板与车厢两侧板后端面之间,侧开式车箱栏板与立柱、底板之间应贴合,其最大间隙不大于4mm。
3.2.4 空载时车厢纵梁与副车架纵梁之间应贴合,最大间隙不大于5mm。
3.2.5 车厢纵梁与底架限位装置应贴合,两侧总间隙不大于2mm。
3.2.6 车箱底板对角线差不大于5mm。
3.2.7 自卸汽车车箱纵向中心平面与底盘纵向中心平面偏移量不大于5mm。
3.2.8 车箱应设置能防止车箱自降的维修用安全支撑装置。
3.3 液压举升倾卸机构3.3.1 液压系统应符合GB 3766-2001和下列要求:a) 液压系统应有限压装置;b) 液压油泵应符合GB 3766-2001的规定;c) 液压缸应符合QC/T 460-1999的规定;d) 换向阀应符合QC/T 461-1999的规定,在装配之前应清洗,所有密封件、防尘件在装配时应涂以机油或薄层润滑脂,并保证不损坏密封件;e) 开式液压系统应有空气滤清装置;f) 液压系统应进行1.5倍(额定工作压力≤15Mpa)或1.25倍(额定工作压力≥15Mpa)额定工作压力保持1min的耐压性能试验,不允许出现渗油、破裂、局部膨胀及接头脱开现象;g) 液压系统液压油固体污染度应符合QC/T 29104-1992的规定;g) 液压油箱在50KP气应下经1min密封性能试验不应有渗漏现象。
a3.3.2 液压油清洁度的控制与液压系统的清理。
3.3.2.1 按照自卸汽车技术文件的要求,选购规定牌号的液压油,储油的容器(油筒)必须清洁,并且专用。
3.3.2.2 液压油的储存,应放在具有防雨、防晒、防潮、通风和具有消防设备的库房内,严禁污物和水份进入。
3.3.2.3 液压管路、油箱等系统零部件应经严格的清理、清洗后方能装配使用(包括外购件和自制件)焊接管接头、油箱焊好后必须清渣、去毛刺、然后酸洗、磷化、除锈,最后用清水、煤油(或柴油)、液压油依次清洗干净,清洗后封口,加盖或包扎封存,或直接安装于液压系统中。
3.3.2.4 向液压系统加油时,应用高过滤精度的加油机(或专用装置),以保证油料和系统的清洁。
三缸的加油量为:40升,四缸的加油量为:50升。
3.3.3 各油、气管路和电线线路应布置合理,固定牢靠,安全整齐,不允许与其他零部件发生磨擦、碰撞,可动管路在运动中不应有干涉现象。
3.3.4 车厢最大举升角度:侧卸45°;后卸48°。
3.3.5 车厢最大举升角度与设计值的误差不超过±2°。
3.3.6 自卸车的举升和降落时间不超过20S。
3.3.7 车厢举升与下降应平稳不允许发生窜动、冲击和卡滞现象。
3.3.8 超载10%的状况下,车厢分别举升到10°和20°时,停留5min车厢自降量不超过2.5°。
3.3.9 自卸车在额定载荷状况下连续举升(举升到最大举升角度的一半,若超过30°,只举到30°),下降(不卸载,载荷不移动)3000次后应保证下述要求:a) 液压倾卸装置中各零部件不得出现任何损坏(不包括易损件);b) 车厢自降量应符合3.3.7的规定。
3.3.10 取力器应符合ZB/T T25001的规定。
4试验方法自卸汽车试验方法按GB/T 223-1997《自卸汽车性能试验方法》规定进行。
5检验规则5.1 过程检验为了确保产品质量,在产品质量形成过程中,应进行过程检验。
整车产品须经过程检验合格方能进行定型检验和出厂检验。
5.2 定型检验新产品定型,应进行定型检验。
定型检验应按QC/T 252-1998《专用汽车定型试验规程》规定执行。
5.3 出厂检验每辆车制造完成后应进行出厂检验,经质量检验部门检验合格并签发合格证后方能入库或出厂。
5.4 检验项目5.4.1 过程检验项目:按第3技术要求各项。
5.4.2 出厂检验项目见表1规定。
5.4.3 定型检验项目见表1规定。
表 1 检验(试验)项目和检验(试验)方法检验( 试验 ) 项目要求章条检验( 试验 ) 方法出厂检验定型检验整车要求图样符合性:a)图样文件符合性b)产品实物符合性3.1.1 核查图样文件按图样技术文件检验√√底盘、原材料、外购件、外协件、自制件质量3.1.2 按国家.行业标准、图样及技术文件检查,并核查有关合格证明√√外观质量、装备的完整性及运行安全一般要求3.1.3按图样及GB 7258-2004及技术文件规定进行√√外廓尺寸符合性 3.1.4 按GB 1589-2004规定进行√√质量参数 3.1.5 按GB 1589-2004规定进行√动力性、操纵稳定性、通过性、燃料经济性等应满足原底盘要求3.1.6 按国家行业有关标准规定进行√各操纵件、指示器及信号装置图形 3.1.7 按GB 4094-1999规定进行√√外部照明及信号装置的配光性能灯泡要求3.1.8按GB 5290-1999等6个标准规定进行按GB 15766.1-1995规定进行√外部照明及信号装置的安装要求 3.1.7 按GB 4785-1998规定进行√√外部照明及信号装置的一般要求 3.1.8 按GB 7285-2004的规定进行√√后视镜的安装要求 3.1.9 按GB 15084-1994规定进行√√汽车污染物排放 3.1.12按GB 3847-1999或GB 18352.1-2001规定进行√自卸汽车车外行驶噪声 3.1.13 按GB 1495-2002规定进行√防腐处理:a)油漆涂层b)涂镀层和化学处理层3.1.14按Q/01 JHK024规定进行按QC/T 625-1999规定进行√√焊接件质量检验 3.1.15 按GB 5943-1991规定进行√√螺纹紧固件扭矩 3.1.16按Q/01 JHK069及产品图样规定进行√√整车要求自卸车汽车的制动性能和驻车制动性能 3.1.17 按GB 12676-1999、GB 7258-1997、QC/T559-1999、JB/4019-1985规定进行√√自卸汽车的取力器 3.1.18 按QC/T 319-1999规定进行√自卸汽车的运动关节和摩擦面的润滑 3.1.19 √√灭火器安装牢固,取用方便 3.1.20 √√扭转变形试验 3.1.21 按QC/T 223-1997规定进行√对环境、气候的适应能力 3.1.22 对比试验或用户试用√侧面及后下部防护装置符合性 3.1.23 按GB 11567.1-2001和GB 11567.2-2001规定进行检查行驶试验50km 3.1.24 √可靠性行驶试验5000km 3.1.25 按QC/T 252-1998规定进行√车厢车厢有足够的强度和刚度 3.2.1 √√栏板锁紧装置 3.2.2 按QCn 29015-1991规定进行√车厢制造精度及安全支撑装置3.2.3~3.2.8√√液压举升液压系统要求 3.3.1 按GB 3766-2001、QC/T 460-1999、QC/T461-1999、QC/T 29104-1992、QC/T29105.1-1992、QC/T 29105.3-1992等规定进行√倾卸机构液压油清洁度的控制与液压系统的清理 3.3.2 √√油、气、电各路布置合理,整齐、牢固、运动部件无干涉现象3.3.3√√举升角度与设计值误差不超过±2° 3.3.4 按QC/T 223-1997中4.3.2规定进行√√举升与降落时间不超过20s 3.3.5 用秒表测量(精确到0.1S) √√举升与下落平稳 3.3.6 √√泄漏试验 3.3.7 按QC/T 223-1997中4.4规定进行√√倾卸(举升)作业可靠性试验 3.3.8 按QC/T 223-1997中4.6规定进行√自卸半挂车 3.4 按本标准和Q/ JHK035有关规定进行√√表2 可靠性行驶试验里程分配表 %平原公路山路坏路城市公路无路地段高速行驶常规行驶20 30 20 30 ---- ----注:高速行驶指平均车速不低于最高车速的80%。