生产线平衡-电子产品装配线案例
线平衡改善及案例分析

提升生产速度﹐维持人手不变
缩短生产节拍
工
将工序2里一
作 时 间
改
改 善
善 前
后
部分可抽调的 时间转至工序 3里﹐以缩减 整体的生产节
拍
工序 1 2 3 4 5
生产线平衡-例2﹕减少人手(1人) 减少人员,维持生产速度不变
工 作 時 間 工序 1 2 3 4 5
减少人手(1)
將工序3里的工作时 间分配至工序2﹑4及 5之內﹐从而工序3里 的人手可调配其它生 产线去
18
1
打室内外线10
2 打线2 打电源线 16
16
1
打室内外线
插室 PCB外观 15
3
温管 插室温管温7
温 打胶水
2
24
1
4
插线 插变压器线7
37
1
插线
30
插线
20
5
功能 功能检验 16
检 拆线
5
45
2
贴断电标贴4
外观检验 8
6
外观 检 贴条码
2
包装
6
16
1
生产线平衡的改善实例
电子电装7人柔性线,改善前各工位的作业时间如下所示:
降低线体速度,减少生产产量
工 作 時 間 工序 1 2 3 4 5
减少人手(2)
因生产需求量降低而 可降低线体速度
将工序3﹑4的工作时 间分配至工序 1﹑2﹑5里﹐从而工 序3﹑4工作岗位的人 手可调配至其它生产 线去。
降低线体速度,减少生产产量
工 作 時 間 工序 1 2 3 4 5
减少人手(2)
100.00% 80.00% 60.00% 40.00% 20.00% 0.00%
生产线平衡率实例

Nt
=
11.35 mins/台 4.2 mins/台
=
2.702,
or 3
(5)根据排程排产
2
1
1
A
B
G
1.4
H
C
D
E
F
3.25
1.2
.5
1
任务 A C D B E F G H
工位 1
工位2
后续任务 6 4 3 2 2 1 1 0
时间 (Mins) 2
3.25 1.2 1 0.5 1 1 1.4
工位 3
流水线平衡
1.4 H
F 1
任务
A C D B E F G H
工位2
后续任务
6 4 3 2 2 1 1 0
时间 (Mins) 2
3.25 1.2 1 0.5 1 1 1.4
工位 3
C (4.2-3.25)=0.95
Idle=0.2
流水线平衡
2
1
1
A
B
G
C
D
E
3.25
1.2
.5
工位 1
A (4.2-2=2.2) B (2.2-1=1.2) G (1.2-1= 0.2)
Idle=0.2
Idle =0.95
2
1
1
A
B
G
C
D
E
3.25
1.2
.5
工位 1
A (4.2-2=2.2) B (2.2-1=1.2) G (1.2-1=0.2)
流水线平衡
1.4 H
F 1
任务 A C D B E F G H
工位2
后续任务 6 4 3 2 2 1 1 0
生产线平衡案例分析过程

生产线平衡案例分析过程1. 引言生产线平衡是一种优化生产过程的方法,旨在确保生产线上的工作站之间的工作负载均衡,以提高生产效率和产品质量。
本文将以一个实际案例为例,分析生产线平衡的过程。
2. 案例背景假设某公司生产手机,并且生产线上有三个关键工作站:组装、测试和包装。
每个工作站的工人数量不同,导致工作负载不均衡,组装工作站负责最多的工作量,而测试和包装工作站的工作负载较少。
3. 数据收集为了分析生产线平衡的问题,首先需要收集一些关键数据。
包括每个工作站的工作时间、工人数量以及每个工作站的工作量。
工作站工作时间(分钟)工人数量工作量(数量)组装工作站30 3 200测试工作站25 2 150包装工作站20 2 100通过收集这些数据,可以计算出每个工作站的单位时间工作量,即每分钟能完成的工作量。
根据上表数据,可以得出以下结果:•组装工作站的单位时间工作量为6.67件/分钟(200件/30分钟)•测试工作站的单位时间工作量为6件/分钟(150件/25分钟)•包装工作站的单位时间工作量为5件/分钟(100件/20分钟)4. 分析和优化通过计算每个工作站的单位时间工作量,可以判断哪个工作站是生产线上的瓶颈工作站。
在这个案例中,组装工作站的工作量最大,成为瓶颈,会导致生产线的工作负载不平衡。
为了平衡工作负载,可以采取以下优化措施:•调整工人数量:增加组装工作站的工人数量,以减轻其工作负荷。
•优化工作时间:分析工作时间,寻找减少生产时间的方法,例如改进工艺或引入自动化设备。
•转移工作量:将部分组装工作转移到其他工作站,以平衡各工作站的负载。
5. 优化结果评估经过优化措施的实施后,重新计算每个工作站的单位时间工作量,以评估结果。
工作站工作时间(分钟)工人数量工作量(数量)单位时间工作量(件/分钟)组装工作站30 4 200 5测试工作站25 2 150 6包装工作站20 2 100 5通过调整组装工作站的工人数量,将其增加到4人,重新计算单位时间工作量之后,可以看到组装和包装工作站的工作量现在已经达到了平衡,测试工作站的工作量仍然保持不变。
生产能力平衡案例ppt课件
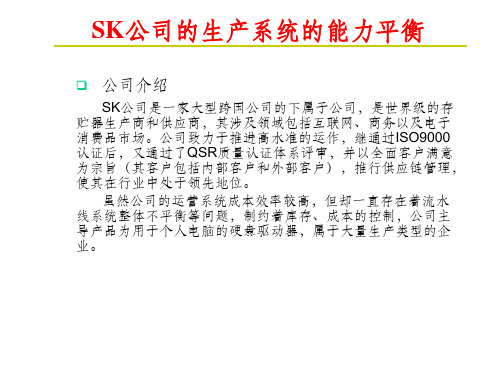
SK公司的生产系统的能力平衡
测试区
第四个工作中心为测试区,它是一种混合式的工作中心。在老化 测试阶段,老化炉采用机群式组织方式布置于测试区,一个老化炉 能同时老化256个产品,整个老化测试过程长达数小时,工艺专业化 是必然的选择;紧跟其后的一个工位是标签工位,完全自动化作业, 加工对象平行移动,属典型的流水生产线对象专业化作业;再后的 接口测试则类似于老化测试,一台测试设备能同时检测120个硬盘驱 动器,测试完一批次后,再测试另一批次,测试时间比老化测试时 间稍短。
可以看出,产量增加了1/3 。
工序6的负荷= 9 0.74 12.2
SK公司的生产系统的能力平衡
第二个工作中心具有合理的流程,生产周期短,生产效率高。但分 工很细,设备种类不同,常因一台设备有问题导致整条流水线停顿,为 解决此问题,通常在一些关键工位保留一些安全库存。
伺服刻写
第三个工作中心为伺服刻写,即用机器在硬盘上写上磁道和相关信
综述
综上所述,四个工作中心都按照实际情况选择不同的空间组织、 对象专业化原则或工艺专业化原则以适应不同的情况需求,但各个 环节生产能力的平衡一直存在问题。
SK公司的生产系统的能力平衡
思考题
1. 第二个工作中心的流水线目前平衡率很低,系统不稳定, 安全库存过高,是否应在瓶颈工序增加设备?
2. 如果按上述分析中的改进,可以提高三分之一的产量,但 这样一来后两个工作中心的能力需要调整,增加设备投入(以第 三个工作中心讨论为例),是否可行?
SK公司的生产系统的能力平衡
清洗区
第一个工作中心为清洗区。硬盘驱动器的一部分机械组件包括 螺钉等,在去离子水中进行成批清洗、烘干。此工作中心属工艺专 业化工作中心,不同产品(螺钉)的清洗、烘干流程相同,使用的 清洗设备相同,工人的技术工种也相同,可对各种部件进行清洗操 作。其特点是有非常好的适应能力,能对标准件和各种差异件在标 识明确的情况下进行混合清洗,其最小单位为一篮。
生产线平衡分析改善案例

生产线平衡分析改善案例引言生产线平衡是指在生产过程中,通过合理分配各个工序的工作量,使得各个工序的产能能够实现平衡,从而提高生产效率、降低成本,并确保产品质量。
本文将以一个实际案例为例,介绍生产线平衡分析和改善的具体过程。
案例背景某电子产品制造公司拥有一条生产线,生产一种电子产品,该产品的组装工序分为A、B、C、D四个子工序。
在目前的生产线上,工序A的生产能力远超其他三个工序,导致A工序成为瓶颈工序,无法满足后续工序的需求,从而影响了整个生产线的效率和产量。
因此,公司决定进行生产线平衡分析,并制定改善方案,以提高生产线的平衡度。
生产线平衡分析1. 数据收集首先,需要收集工序A、B、C、D的工作时间数据,包括每个工序的加工时间、准备时间和等待时间。
这些数据将作为分析的基础。
2. 流程图绘制根据数据收集到的各个工序的时间,并结合实际生产情况,可以绘制出生产线的流程图。
流程图可以清晰地展示每个工序的工作时间和流程顺序,有助于进一步分析。
3. 生产线平衡计算根据流程图,可以计算出每个工序的工作时间总和。
然后,根据目标产量,计算出每个工序的标准工作时间,即每个工序应该占用的时间比例。
通过比较实际工作时间和标准工作时间,可以评估生产线的平衡度。
4. 分析结果根据生产线平衡计算的结果,可以看出工序A的工作时间远超其他工序,导致生产线的不平衡。
这也解释了为什么A工序成为瓶颈工序。
改善方案1. 调整工序A的产能由于工序A是瓶颈工序,可以考虑通过增加设备或优化工艺,提高工序A的产能,以满足后续工序的需求。
这可以通过增加工序A的设备数量、提高工段效率或优化工艺流程等手段实现。
2. 优化其他工序除了调整工序A的产能外,还可以进一步优化其他工序的流程,减少每个工序的工作时间。
例如,可以通过流程改进、工艺优化、培训员工等方式,提高其他工序的效率,从而平衡整个生产线。
3. 调整生产计划根据生产线平衡分析的结果,可以对生产计划进行合理调整。
生产线平衡案例

实施平衡措施后,生产线平衡率得到显著提高, 在制品数量减少,设备故障率降低,整体生产效 率提升。
案例二:电子产品生产线平衡
生产线现状分析
针对电子产品生产线,发现其存在工序繁多、作业时间不稳定、 物料供应不及时等问题。
平衡措施实施
通过作业测定对工序进行重新组合与排序,实现作业时间的均衡化; 加强物料计划与调度管理,确保物料供应的稳定性。
稳定性。
降低生产成本和浪费
减少因生产线不平衡而产生的在制品库存和成品 库存,降低库存成本。
通过优化生产计划和调度,减少生产过程中的停 机、换模等浪费,降低生产成本。
提高设备利用率和员工工作效率,减少人力和物 力的浪费。
增强企业竞争力和可持续发展能力
• 生产线平衡有利于企业实现精益生产和敏捷制造,快速响应市场需求变 化。
优化资源配置
通过生产线平衡,合理配置人力、 物力和财力资源,使生产过程更加 顺畅,提高企业的整体运营水平。
生产线平衡的定义和意义
定义
提升生产效率
降低成本
提高产品质量
增强企业竞争力
生产线平衡是对生产线 上各个工序进行作业时 间分析和调整,使各工 序的作业时间尽可能相 等或接近,以达到提高 生产效率、降低成本的 目的。
编制方法
根据工艺流程图提供的基础数据,计算各工序的生产能力、负荷率等 指标,并按照一定的格式编制成表格。
瓶颈分析和改善
定义
瓶颈分析是指通过分析生产线上各工序的生产能力和负荷 情况,找出制约生产线整体效率的瓶颈工序,并制定相应 的改善措施。
作用
通过瓶颈分析,可以针对生产线上的瓶颈工序进行改善, 提高生产线的整体效率,降低成本,提高产品质量。
即每个产品需要在多长时间内完成生产。
装配生产线改善案例

装配生产线改善案例01.装配部部门简介装配部,作为车模生产的最后一道工序,肩负着车模成品的组装和包装的全部生产过程。
装配部现有六条生产线和一条样办组装线。
常用的设备有:钻床,电批,手啤机,风批,烙铁,高周波,封口机等。
为了更好的完成生产任务,装配部引入了精益生产工艺流程。
精益生产是目前工业界公认最佳的一种生产组织体系和方式。
通过合理的排拉,达到合理生产,提高效率和质量的目的。
02.例子(一):DCP1/25货车,按流程标准可分成:车身半品( 10人),车身组合(16人),内座组合(4人),车底组合(11人),成品组装(7人)和包装(9人)共六个小组(57人)来完成。
每个小组会有一次或以上的自检。
(二):YTB002 1/42莱茵之星单层客车,按流程标准可分成:内座组装(12人),车底组装(9人),车身组装(20人),成品包装(6人)共四个小组(47人)来完成,在其中也加入了多次的自检。
03.装配车间平面分布图04.装配生产线平衡改善过程•了解产品组装工艺•对U型拉进行工时测定,得到统计数据•从统计数据分析U型拉平衡状况•识别瓶颈工位,找出不平衡的原因•运用平衡改善法则(ECRS法则)、动作经济原则等方法制定改善方案•将改善方案告知组长或装配主任,实施现场改善•改善效果分析总结05.平衡改善法则-ECRS法则简介以上ECRS法则,具体可通过下列图片来说明生产中如何运用改善:06.装配线平衡典型案例•U拉序号:U24、U25•产品编号:53072(太空车)•组装部分:成品和包装改善前各工位组装工艺此款产品的装配线由U25、U24两个U型拉组成,工位分布如下图所示:平衡率=各工序的作业时间/(瓶颈工位时间*人数)=(9.5+11+6+13+8+8+8+6+9+10+6+8)/(13*12)=65.71% 平衡损失率=1-平衡率=34.29%改善前装配线工位平衡图改善措施从统计数据分析这条装配线,可以发现瓶颈工位是工位4。
生产线平衡(实例版)
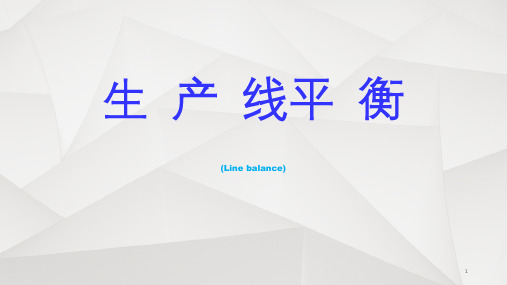
1﹑生产线平衡的相关概念
1.2工站及周期时间
时间
T2
T1
T3
T4
T5
工站
S1
S2
S3
S4
S5
CycleTime ﹕每工站中1个循环的作业所需的标
准工时(如图中所示﹕T1,T2,T3,T4,T5)
8
1﹑生产线平衡的相关概念
1.3瓶颈时间
时间
T2
瓶颈时间
T1
T3
T4
T5
工站
S1
S2
S3
S4
S5
瓶颈工时﹕生产线作业工时最长的工站的
生产单位:协助生产单位拟定及推动改善方案. 制工单位:改善前/后之工时测量,山积表制作﹑分析及改善方案之实施,
跟踪方案效果评估及各种相关文件修订及系统窗体发行﹔ 品管单位:负责改善前/后产品质量评估﹔ 工务单位:主导及其它改善事项协助﹐设备改善﹔ IE﹑经管﹑企划:改善前后产线效益评估及跟进.
50
THE END!
时间
S1
S2
S3
S4
S5
增加可供时 间
还有什么 方法 平均时间T CT
工站
41
Steps4:山积表平衡
3.平衡的步骤
若T略小于CT:将CT设为上限,消除瓶颈
时间
CT 平均时间T
S1
S2
S3
S4
S5
工站
42
Steps4:山积表平衡
3.平衡的步骤
若T严重小于CT:将CT设为上限,重排 消除瓶颈
时间
所有工站时间之和 平衡率= 瓶颈工站时间*工站总数
100%
16
1﹑生产线平衡的相关概念
1.6平衡率﹐平衡损失及其计算
- 1、下载文档前请自行甄别文档内容的完整性,平台不提供额外的编辑、内容补充、找答案等附加服务。
- 2、"仅部分预览"的文档,不可在线预览部分如存在完整性等问题,可反馈申请退款(可完整预览的文档不适用该条件!)。
- 3、如文档侵犯您的权益,请联系客服反馈,我们会尽快为您处理(人工客服工作时间:9:00-18:30)。
MPM
Screen Printer
AOI system
High-speed Chip shooter
Multi-purpose Chip shooter
Reflow oven
制程缺点 50% ~70% 修护成本/缺点
SMT 生产线布置
結束
FUJI
MPM
LOADER
MPM UP2000
GL-541
FCP-642
2 3
计算闲置时间百分比
結束
=
(N)(CT)
生产线平衡的规则
一些启发式 (直觉式) 规则: 依照后续作业数最多者先指派 依照最大阶位者先指派
�
結束
阶位,是各个作业时间与其所有后续作业时间的加 总
例题 2
結束
0.2
0.2
0.3
a
0.8
b
0.6
e
c
d
f
1.0
g
0.4
h
0.3
例题2的解答
結束
站1
站2
SMT生产线影像-1
結束
SMT生产线影像-2
結束
手焊与修检站
結束
人工插件生产线
結束
电子构装类型
TYPE I
Solder paste SMT Complex FPT Simple
PLCC Chip Components SOIC
結束
TYPE II
Solder paste
PLCC
Chip Components
結束
ACM FILE CONTENT Device No. Part NO X- axis Y-axis Orientation
37,CRS1011J1M,R17,-6827,5732,90, 57,CTRRMPP01M,Q4, 195,12410,90, 21,CICA07474M,U1,-8338,12641,
結束
作业指导书内容
作业指导书乃依据产品设计图 /零件尺寸 /零件特性/组合公差 /生产线资源配置 /组装方式/循环时间考量下之产物。 作业指导书之目的在于正确无误与兼顾质量下组装产品并 需符合生产率之需求。 作业指导书内容须包含:
� 文件编号、产品料号、发行部门、制程别、、、 � 组装加工顺序 � 组装图 � 使用工具 (治夹具) � 使用材料列表 � 工具使用参数 (例如电动起子之扭力设定) � 注意事项
結束
电子产品
結束
PCB 基板 (Printed Circuit Board)
結束
SMT 电子零件
結束
电子构装织模型
結束
表面黏着制程 (Surface Mount Technology)
电子产品生产制程 (PCBA)
• Final ass’s – 产品组装作业 • Final test – 产品测试(功能性) • Packing – 产品包装作业
結束
•拒收(Rejected) (1) 焊锡未全部充满于零件接着面与焊垫上, 且零件50%以上脚宽超出焊垫范围。
SMT 检验标准
結束
Preferred
Acceptable
SMT制程控制流程
結束
表面黏着制造流程 表面黏着制造流程
•制程变异监控 •修正措施施行
SMT制程缺点与修护成本趋势
結束
FUJI
Speed: 1.65 ~ 2.00 sec/pcs
SMT 生产程序
Jobname: 18193r3/18193r3
Side: TOP Units: 10 Micro-meters CD PN OR X Y BX BY SD MT -----------------------------------------------------------------------------------------------------------------------------------------------------R17 2 90 -6827 5732 -6727 5732 TOP S Q4 3 90 195 12410 195 12410 TOP S U1 16 180 -8338 12641 -8338 12641 TOP S . . . Date: Fri Aug 8
FINAL TEST
PACK ING
SHIP
FORM ING
SUB ASS'Y
HANDLING C BOARD (OPTIONAL) INST. W/S
POST SOLDER
SMT
FORM ING
Terms: • SMT – 表面黏着技术(制程) • Forming – 零件成型 • INST. – 人工插件 (Insertion) • W/S - 波焊制程 (Wave soldering) • Post solder – 接接后作业 (Such as touch-up, rework) • B/I – 烧机测试 (Burn-in)
将前一页所显示的作业,安排到工作站之中
� 采用1.0分钟的周期时间 � 依照后续工作数最多者,依序安排作业
結束
例题1的解答
工作站 1 剩餘時間 1.0 .9 .2 1.0 0 1.0 .5 .3 有資格 的 a c 無 b 無 d e 指派工作 閒置時間 a c b d e -
結束
.2 0 .3 .5
电子构装生产线/ 作业指导书制作/生产线平衡
Prepared by: Dr. Tsung-Nan Tsai
电子产品与制程趋势
多重应用功能(Multi-purpose Applications) 携带式与缩小化 (Portable and Miniature)
. Mobile phone . PDA . Notebook …
結束
作业指导书制作流程图
了解产品电子 /机构 产品/雏型拆解纪录 (设计图/照片) 了解BOM结构 了解产品结构 (爆炸图) 了解生产线编制 / 能力/产品族群
結束
BOM SMT PTH
经由DCC编号 发行 Yes 各类制程 W/I齐备 No
TESTING
标准工时
了解各种作业/ 标准工时 人工编辑/软件协助 编辑
站3
站4
a c
b
e f d g h
平行工作站
30/小时 30/小时 30/小时 30/小时
結束
1 分钟
1 分钟
2 分钟
1 分钟
Bottleneck
30/小时 1 分钟 60/小时 1 分钟 30/小时 1 分钟. 30/小时 1 分钟 30/小时 1 分钟 60/小时
平行工作站
結束
决定所需工作站的最少数目
結束
N=
(D)( ∑ t) OT
∑t =
先行图 (Precedence diagram)
先行图: 用来平衡生产线的工具,以显示单元的作 业和顺序需求
0.1 分钟
第1个作业
結束
1.0 分钟
简单的先行图例
a c
b d
0.5分钟
e
0.2 分钟
0.7 分钟
例题 1: 装配线的平衡
作业指导书 (Working Instruction)
作业指导书类型
作业指导书乃用于指导作业员从事加工 /组装作业程序之文 件,作业员须依据此文件进行作业。 电子业作业指导书一般包含:
� 机器加工方式/组装指导书 � 零件/銲点修护指导书 � 人工插件指导书 (Manual Insertion) � 次组件组装指导书 (Sub-assembly) � 测试指导书 � 品检指导书 � 烧机指导书 (Burn-in) � 原物料取用与储存环境指导书 � 包装指导书 � 最后组装指导书 (Final assembly)
結束
可制性(Manufacturability) 构装自动化 (Automation in Assembly Process) 重复性与再现性 (Repeatability and Reliability) 生产力与及时供货能力 (Time to Market) 效率(Efficiency)
电子产品与制程趋势
a. 所有先行任务皆以分配 b. 作业时间未超过工作站剩余时间 c. 假若找部到合适任务则移至下一个工作站
結束
4. 当每个任务分配后应确认该工作站周期时间减掉 已指派作业时间之总和,以找出剩余时间。
生产线平衡步骤
5. 产生中断时则以下列规则处理之:
a. 分配最长作业时间之任务 b. 分配后续作业最多之任务 c. 如果能处于打结状态,责任选一个任务指派
零件黏贴
Ball screw
結束
基版
传感器 送料器
取置头
焊性检验标准 (IPC STANDARDS)
•标准(Preferred) (1) 零件脚位于焊垫中央。 (2) 零件端点与焊垫间皆充满足够的焊锡, 且呈平滑圆弧形。 (3) 零件脚与焊接面平贴于焊垫上。 •允收(Acceptable) (1) 零件接着面在焊垫范围内,且50%以上 脚宽位于锡垫范围内。
SOIC
DIP
Glue dot
Chip Components DIPs
TYPE III
Chip Components
SMT 生产作业网络
結束
SMT 生产线布置
結束
結束
High Speed Chip Shooter - Fuji
Speed: 0.09 ~ 0.45 sec/pcs
結束
Multi-purple chip shooter - Fuji
結束
组 装 爆 炸 图
PCB
产品组装爆炸图
結束
作业指导书格式