铝板带轧制常见故障分析及处理PPT课件
铝板带轧制过程 ppt课件

板材 热轧坯料 9.5*10001300mm 6.07.0*1100mm -1300mm 1#/2#清洗 (厚度>3.2mm 卷材切边,板 材切边至成品 宽度)
1#/2#/3#横 切 2#拉矫 (拉伸+ 矫直+切 边)
冷
>2.5mm卷材
纵剪
ppt课件
18
厚度>2mm 本厂3004 合金热轧 坯料 9.5mm*100 0~1460mm
ppt课件 8
热轧卷工艺流程
热轧卷工艺流程一般为:铸锭——铣面、铣 边——加热——热轧(开坯轧制)——热精轧 (卷取轧制)——卸卷 铣面是为了便于热轧加工,因表面有氧化皮、 铸造细密组织等,后续加工容易造成裂边、表 面质量差等缺陷 加热的目的是为了方便后续热轧加工,提供一 个软化组织,加热一般在470℃~520℃之间, 加热时间在10~15h,不超过35h,否则可能过 烧,出现粗大组织
21
变形过程示意图
ppt课件
22
冷轧机各部件简述
开卷机:料卷上在开卷机卷轴上 工作辊:生产过程中与铝箔直接接触的辊 支撑辊:为工作辊提供压力,保持工作辊辊缝 X射线测厚仪:穿透铝箔,通过衰减来计算铝箔实 际厚度 板形仪:通过压力感应控制铝箔板形 卷取机:铝箔轧后缠卷在卷轴上面 轧制油:冷却与润滑作用 过滤系统:将使用后的轧制油过滤后重新使用(无 纺布、硅藻土、白土) 灭火系统:防止断带起火
ppt课件 9
热轧机示意图
ppt课件
10
热轧机
ppt课件
11
热轧生产注意事项
硬合金与软合金轧制道次不一样,硬合金轧制 道次要多于软合金,从15道次到20道次不等 需要严格控制终轧温度,终轧温度直接影响后 续加工,以及成品理化性能 生产过程中应合金种类一般需要辊边 需要把头尾浇口铸口咬合部分切除 乳液为水包油系,水起冷却作用,油起润滑作 用,需要常年保温在65℃左右 热轧速度一般在200m/min左右
铝箔轧制缺陷产生的原因和解决措施

第七章铝箔轧制缺陷产生的原因和解决措施主讲人:马文宏1、夹渣产生的原因• 铝熔体铸造前过滤、除气除渣不彻底,Al2O3 、炉渣等夹渣物被带入铝熔体中,最终带入坯料中。
• 更换过滤片时Al2O3 、炉渣等夹渣物被带入铝熔体中。
• 铝熔体纯净度太差,非金属异物太多,除气除渣无法彻底。
解决措施• 采取更有效的过滤、除渣方式(如Ar+Cl2两级精练, 高吸附能力的泡沫陶瓷双级过滤)。
• 改变过滤片的更换方式。
• 选择良好的原铝和废料。
2、气道产生的原因• 铝溶体氢气含量高,铸轧嘴前沿结渣,铝溶体向前流动时受阻,在结渣处的后面形成负压,铝溶体中的氢气析出,在铸轧板中形成通长的气孔叫气道,当铝箔轧制到比较薄时,由于此处的铝是两层的,延伸性能差,被轧裂。
气道一般只发生在亨特(倾斜式)铸轧机上。
解决措施• 加强精练,降低氢气含量和渣含量,氢含量应控制在0.15ml/100gAl以下。
3、氧化产生的原因• 铝和水发生化学反应生成Al2O3(开始颜色发白,随着时间的延长逐渐变黑)。
• 水的来源:— 轧制油含有游离水。
— 蚊虫带入轧辊。
— 候湿热、坯料、铝箔放置时间太长。
2Al+3H2O ═ Al2O3+3H2↑解决措施• 轧制油含水量应小于150PPm。
• 灭蚊虫。
• 铝产品应放置在通风干燥的区域,如果放置在密闭区间,应有足量的干燥剂。
• 放置时间越短越好。
非金属压入非金属异物在铝材生产过程中带入变形区后压入铝基体中,形成非金属压入物。
这些非金属压入物大多数会在后来的轧制中脱落,在铝箔表面留下痕迹,最终可能产生针孔、孔洞或颜色不均。
产生原因• 环境卫生差,空气中灰尘多。
• 生产设备、使用的吊具等工具脏。
• 过滤纸克重小或厚度不均,造成过滤土泄漏,再通过油喷嘴喷入轧制变形区。
• 轧制油过滤精度不够,轧制油中有非金属颗粒。
解决措施• 加强5S管理,改善环境清洁度。
•久置的铝材应扒去外层。
• 控制好轧制油的过滤质量。
废料(断带)产生原因•断带后碎铝箔未处理干净,附在机架内,轧制时入口侧的碎铝箔掉下,被带入轧制变形区,造成该区域铝箔变形不均而压裂(正常区域只有两层铝箔,有废料的区域至少三层),产生断带现象。
铝压铸件工序不良汇总与分析PPT课件
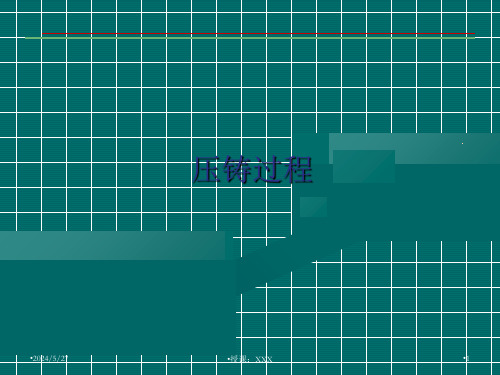
DPD机箱---航空头车偏原因分析
不良原因
纠正措施 预防措施
1、产品装夹定位 孔偏;
2、装夹到位;
不良品报废
1、控制上 工序装夹;
2、操作人 员装夹时注 意装夹到位。
•授课:XXX
•23
氧化过程
•2024/5/27
•授课:XXX
•24
不良图片
DPD机箱---牙纹孔水印、泛酸 分析
不良原因
纠正措施 预防措施
1、过程防护不到 位,导致产品碰 伤;
不良品报废
1、提升操 作人员质量 意识;
2、按规范 要求防护搬 运;
•2024/5/27
•授课:XXX
•13
机加工过程 机加工过程
•2024/5/27
•授课:XXX
•14
DPD机箱---牙纹孔断丝攻分析
不良图片
不良原因
纠正措施 预防措施
不良描述: DPD机箱牙纹孔断丝攻。
以下。
1、严格控 制机加工前 的整形工艺, 单个机箱必 须控制在 0.5mm之 内。
•授课:XXX
•35
不良图片
•2024/5/27
1、产品内部有砂 孔;
2、丝攻达到加工 极限;
1、保证产 品的致密性, 减少气孔存 不良品电火花后 在; 加钢丝螺套返修; 2、施行刀 具管理,严 格控制刀具 寿命。
•授课:XXX
•15
不良图片
DPD机箱---牙纹孔偏浅分析
不良原因
纠正措施 预防措施
不良描述: DPD机箱牙纹孔偏浅。
1、不良品补漆 返修;
1、增加喷 涂工的技能 培训,预防 不良发生。
•2024/5/27
•授课:XXX
铝箔轧制过程产生的原因及控制方法

铝箔轧制常见缺陷的一般特征、原因及措施
铝箔作为一种极限加工,其生产工序多、加工技术难度大、厚度最薄的生产特点决定了其产生缺陷的几率要比其他压力加工高许多倍,其生产的可能性、稳定性除非设备有重大问题,否则绝大部分与缺陷有关,努力减少和消除轧制缺陷是实现安全、优质、高效、低耗生产的关键之一。
本资料主要以我厂在实际生产中遇到的一些问题为研究对象进行编制,旨在通过机台操作人员的学习来提升他们的基础知识和专业水平,更好地为顾客提供具有竞争力的产品。
* 表示该问题的原因尝不确定。
铝轧机板形等质量问题分析及采取措施

铝轧机板形等质量问题分析及采取措施一、板形不良.1、冷轧机:(1)每三个月由钳工检查一次喷杆梁的减振喉是否损坏.及时更换(2)每两个月由操作手和电工一起检查喷嘴是否有堵塞或者在轧制时,操作手发现板形明显不良或者喷嘴喷油异常时,马上对喷嘴进行测试检查.(3)针对不同宽度,不同厚度,操作手及质检作好记录,并及时通知设备部进行一起分析,是否需要对板形目标曲线进行更改及试验(不同的板形目标曲线会对喷淋产生一定的影响). (4) 有些薄板,建议操作手可以进行手动喷淋干预,总结分析板形不良原因.(5)所有辊系检测每季度一次,由技术组完成,水平度及平行度。
2、粗轧机:(1)建议要求厂家增加手动调节喷淋功能(因为粗轧机不能对局部喷油进行手动干预,其不良板形只能通过弯辊,倾斜等手段进行辊型控制).(2)定期检查压平辊平行及水平度.1次/季度。
(3)每两个月由操作手和电工一起检查喷嘴是否有堵塞或者在轧制时,操作手发现板形明显不良或者喷嘴喷油异常时,马上对喷嘴进行测试检查.(4)工艺道次合理安排,张力合理使用,轧辊凸度建议尝试支承辊凸度0.02mm;工作辊凸度0.05-0.07mm.3、精轧机:(1)定期检查喷杆梁喷嘴.(2)定期检查压平辊平行及水平度.1次/季度(3)喷射梁及板型仪备品备件要尽快订货,因为膜片及滤芯都是消耗品需定期更换。
(4)工艺道次合理安排,张力合理使用,轧辊凸度建议尝试支承辊凸度0.02mm;工作辊凸度0.05-0.07mm.针对以上情况,将对三台轧机定期作以下的检查和测试:(1)定期对入口张紧辊进行检查辊系.(2)定期对板形辊平行度,水平度进行检查.(3)定期对工作辊辊隙进行检查.(4)定期对轧制线进行检查.(5)对薄板的局部板形不良,操作手是否可以采用手动调节喷淋,对相同的铝卷进行持续跟踪和比较.二、打底印.1、目前对部分变形的套筒进行车削,保证套筒的外圆一致。
2. 生产要加强套筒管理严格区分退火用套筒和非退火用套筒,决不能混用3、合理使用张力速度,匹配要合理.三、铝粉堆积1、入口可增加板面清洗装置.2,加强板式过滤器维护,确保过滤能力满足生产需求3,定期换纸,严格执行硅藻土及白土纤维素的添加工艺,搅拌箱内不能吸空4,每班要对轧制油透光率进行检测设备部2017-4-18。
《铝板带轧制过程》课件

3 轧制参数控制
轧制参数的控制对于铝 板带轧制的成功至关重 要,因为轧制参数可以 控制铝板带的厚度、表 面光洁度等重要性能。
铝板带轧制的需求
生产率
生产率是铝板带轧制过程中 的重要指标,高生产率意味 着更快的加工速度和更高的 经济效益。
制品质量
制品质量是铝板带轧制最重 要的指标之一,高品质的制 品能够满足用户的需求,获 得更多的市场份额。
预轧
用预轧机进行预轧,把厚铝板带压成 薄铝板带。
冷却
冷却刚刚轧好的铝板带,以保证其质 量。
铝板带轧制的关键环节
1 热轧温度
热轧温度过高,易导致 铝板带的表面粗糙,且 塑性不易控制;热轧温 度过低,难以满足轧制 强度和韧性要求。
2 润滑剂
润滑剂在铝板带的轧制 过程中起到关键作用, 它可以降低轧制力,减 小摩擦阻力,进而提高 铝板带的表面质量。
《铝板带轧制过程》PPT 课件
这份PPT课件将会向大家介绍铝板带轧制的过程和应用,希望大家能够加深 对这个领域的理解。
铝板带轧制简介
定义
将铝板带材料通过加热和轧制,加工成所需 要的形状和厚度的一种重要加工方式。
应用领域
铝板带轧制应用广泛,可用于航空、航天、 船舶、汽车、建筑等领域。
历史
铝板带轧制的历史可以追溯到19世纪,当时 铝及其合金为人们所熟知。
环保要求
铝板带轧制过程中需要使用 润滑剂等影响环境的物质, 因此环保要求也是一个需求 方面的重要方面。
铝板带轧制的未来展望
技术创新
目前,铝板带轧制技术正朝着 高精度、低损耗、绿色化的方 向不断发展。
应用拓展
随着航空、航天、军工等行业 的快速发展,对于铝板带轧制 技术的应用场景也将会持续拓 宽。
铝板带热轧支承辊常见失效案例

多 的应 力 , 引发 裂纹 和潜 在疲 劳剥 落 。
4 . 3 预 防
点, 且 表 皮下 的最 大 瞬时 剪切应 力 显著 增加 。
3 . 3 预 防措 施
( 1 ) 合 理控 制轧 制乳 液浓 度 尽量 避 免 出现 工 作辊 打滑 现象 ;
4 滑 痕
4 . 1 特 征
滑 痕是 工 作 辊 和 支 承辊 间 的 相 对 滑 动 。 由于 多
数工作辊辊身比支承辊辊身长 , 损伤通常扩展到整个
支承 辊 辊 面或 最 后 在 支 承 辊 上 有 所 减 轻 。如 果 工 作 辊严 重 磨 损 成 一 个 凹 坑 , 损 伤 将 会 在 支 承 辊 辊 端 结 束 。两 种情 况下 会 出现 损伤 , 当打滑 产 生 高 温 或 由于 改变 原 始结 构导 致微 结 构损 坏 时就 会 出 现严 重 裂 纹 。 较大 的摩 擦 滑 动 , 称 为打滑 , 先 由摩 擦 热 损 坏 轧 辊 微 结构 , 然 后在 局部 弱化 区域 引发疲 劳失 效 和剥 落 。
( 8 ) 减 少 辊 身 凸度 量 , 以便 减 少 辊 身 中心 处 的最 大 瞬时剪 切应 力 。
足 或轧 辊磨 损 产 生 裂 纹 而 引 起 的剥 落 。多 数 肩 部 剥 落 与工 作辊 磨损 有关 , 小 块 边 部 剥落 则 与 倒 角不 够 有 关 。滑 动机 理 和 可 变 的线 接 触 压 力 都 有 助 于 控 制 支 承 辊表 面碎 片磨 损 。热 轧 机 中 , 来 自工 作 辊 的 氧化 物 碎 片侵 蚀 支 承 辊 材 料 , 导 致 形 成 凹面 中心 。然 后 , 不
铝冷轧板带缺陷教程

16 滑移线
• 2.16.1 缺陷定义及特征 • 拉伸板表面,与拉伸方向呈450角左右的有规律的发暗
• c) 冷轧时张力不当,开卷时产生层间错动而产生擦伤; • d) 精整验收和包装操作不当产生板间滑动而造成擦伤。
5 碰伤(凹陷)
• 5.1 缺陷定义与特征
• 铝板、铝卷与其他物体 碰撞后在板、带表面或端 面产生的伤痕。
• 该缺陷发生在铝板、铝 卷的表面或端面,且大多 数在凹陷边际有被挤出的 金属存在。
入。
3 划伤
• 3.1 缺陷定义及特征
• 凡因尖锐的东西(如板 角、金属屑或设备上的尖 锐物等)与板面接触,在相 对滑动时所造成的呈单条 状分布的伤痕叫做划伤。
• 3.2 产生原因
• a) 热轧机辊道、导板上粘铝使板、带划伤; • b) 冷轧机导板、压平辊等有突出的尖锐物; • c) 精整时板角划伤; • d) 涂油包装时油中有金属屑带到涂油辊或毛毡上而划伤
• 腐蚀板、带失去金属光 泽、严重时在表面产生灰 白色的腐蚀产物。
• 11.2 产生原因
• a) 淬火洗涤后、板材表面残留有酸、碱、硝盐痕迹; • b) 板、带放置保管不当,由于气候潮湿或水滴浸入表面
引起腐蚀; • c) 生产过程中的工艺润滑剂中含有水分或呈碱性而腐蚀
板、带; • d) 储运过程中,包装防腐层破坏了,引起腐蚀。
12 硝盐痕
• 12.1 缺陷定义及特征 • 热处理硝盐介质残留在板材表面而产生的斑痕。 • 硝盐痕呈不规则的白色斑块,表面粗糙,无金属光泽。
• 12.2 产生原因 • a) 淬火后洗涤不彻底; • b) 压光前板面没有擦干净; • c) 板片表面残留有硝盐。
13 油斑
• .1 缺陷定义及特征 • 残留在板带上的油污,经退火后形成的黄褐色程度不同
铝板常见的问题以及产生原因

1.表面气泡2.贯穿气孔熔铸品质不好。
铸锭含氢量高组织疏松;铸锭表面凸凹不平的地方有脏东面,装炉前没有擦净;蚀洗后,铸块与包铝板表面有蚀洗残留痕迹;加热时间过长或温度过高,铸块表面氧化;第一道焊合轧制时,乳液咀没有闭严,乳液流到包铝板下面。
3.铸块开裂热轧时压下量过大,从铸锭端头开裂;铸块加热温度过高或过低。
4.力学性能不合格没有正确执行热处理制度或热处理设备不正常,石家庄铝板经销空气循环不好;淬火时装料量大,盐浴槽温度不够时装炉,保温时间不足,没有达到规定温度即出炉;试验室采用的热处理制度或试验方法不正确;试样规格形状不正确,试样表面被破坏。
5.铸锭夹渣熔铸品质不好,板片内夹有金属或非金属残渣。
6.撕裂润滑油成分不合格或乳液太浓,板片与轧辊间产生滑动,金属变形不均匀;没有控制好轧制率,压下量过大;轧制速度过大;卷筒张力调整得不正确,张力不稳定;退火品质不好;金属塑性不够;辊型控制不正确,使金属内应力过大;热轧卷筒裂边;轧制时润滑不好,板带与轧辊摩擦过大;送卷不正,带板一边产生拉应力,一边产生压应力,使边沿产生小裂口,经多次轧制后,从裂口处继续扩大,以至撕裂;精整时拉伸机钳口夹持不正或不均,或板片有裂边,拉伸时就会造成撕裂;淬火时,兜链兜得不好或过紧,使板片压裂,拉伸矫直时造成撕裂。
7.过薄压下量调整不正确;测厚仪出现故障或使用不当;辊型控制不正确。
8.压折(折叠)辊型不正确,如压光机轴承发热,使轧辊两端胀大,结果压出的板片中间厚两边薄;压光前板片波浪太大,使压光量过大,从而产生压折;薄板压光时送入不正容易产生压折;板片两边厚差大,易产生压折。
9.非金属压入热轧机的轧辊、辊道、剪刀机等不清洁,加工过程中脏物掉在板车带上,经轧制而形成;冷轧机的轧辊、导辊、三辊矫直机、卷取机等接触带板的部分不清洁,将脏物压入;轧制油喷咀堵塞或压力低,带板表面上粘附的非金属脏物冲洗不掉;乳液更换不及时,铝粉冲洗不净及乳液槽未洗刷干净。
铝板带轧制常见故障分析及处理

2012-6-6
11
• b、原因分析 • ①、产生厚度中心点飘移的原因:出口测厚 仪测量数据不真实和操作人员对厚度中心点 设定不恰当所致。 影响出口测厚仪测量准确性的因素有:校 核测厚仪的标准板厚度不准确引起厚度中心 点设定不准确,测厚仪厚度补偿系数不准确 ;放射源发出的射线被其他物件所挡;测厚 仪自动清零功能不稳定。
2012-6-6
9
b、厚度控制
①FF-AGC:Feed-forward Automatic Gauge Control ②MF-AGC : Mass Flow - Automatic Gauge Control ③MV-AGC : Multi-Variable - Automatic Gauge Control ④MN-AGC : MoNitor - Automatic Gauge Control ⑤TLC : Tension Limit Control ⑥RE-AGC : Roll Eccentricity - Automatic Gauge Control
2012-6-6
24
1.3.6 自动板形控制
• 自动板形控制过程如下图
板形辊
分区冷却
弯辊控制
倾辊控制 板形检测 一次板形 二次板形 高次板形
板 形 控 制 调 节 器
目标板型
图1.
2012-6-6
自动板形控制系统过程图
25
1.3.7 板形问题案例
• 断带原因分析
2012-6-6
26
1.4 表面质量
• 出现板形不良的直接原因是轧件宽向上延 伸不均。
2012-6-6
20
• 出现板形不良的根本原因是:轧件在轧 制过程中,轧辊产生了有害变形,致使 辊缝形状不平直,从而产生波浪。
铝材常见不良原因分析

19.过短 剪切时定尺不当或设备出现故障。
20.镰刀形 热轧机轧辊两端辊缝值不同;导尺送带板不正,带板两边延伸不同;热轧机轧辊预热不好,辊形不正确;乳液喷射不均或喷咀有堵塞;压光机轧制时板片未对中。
打开 DVD光盘制作助手免费版——添加文件——在打开的界面里找到刚转换的文件后——点击——打开——有提示就点确认或打叉——开始生成——(有提示就点确认或打叉——如果有还会有提示是否覆盖?你就打x——浏览——改变储存位置——确认——开始生成)——有提示就点确认或打叉——等转换好——有提示就点确认或打叉——打x——打X。
铝板带材工艺废品种类及产生原因
1.贯穿气孔 熔铸品质不好。
2.表面气泡 铸锭含氢量高组织疏松;铸锭表面凸凹不平的地方有脏东面,装炉前没有擦净;蚀洗后,铸块与包铝板表面有蚀洗残留痕迹;加热时间过长或温度过高,铸块表面氧化;第一道焊合轧制时,乳液咀没有闭严,乳液流到包铝板下面。
3.铸块开裂 热轧时压下量过大,从铸锭端头开裂;铸块加热温度过高或过低。
4.力学性能不合格 没有正确执行热处理制度或热处理设备不正常,空气循环不好;淬火时装料量大,盐浴槽温度不够时装炉,保温时间不足,没有达到规定温度即出炉;试验室采用的热处理制度或试验方法不正确;试样规格形状不正确,试样表面被破坏。
5.铸锭夹渣 熔铸品质不好,板片内夹有金属或非金属残渣。
21.裂频——MPG——输出配置——SVCD-NTSC或PAL
——确认——添加文件——点击文件——打开——确认——开始。
此默认转换参数为;《(视频屏幕大小——NTSC制式480x480或PAL制式480x576—
铝板卷常见质量缺陷及原因实图讲解

铝板卷常见质量缺陷及原因实图讲解一个月的铝锭带你快速致富:上月你订10吨恭喜你夫妻双双欧美游;上月你订50吨,恭喜老板哈弗H6包牌带回家;上月订100吨,4S店奥迪A4提回家;上月订200吨,宝马5系相中哪款带回家!上个月订1000吨,郊区别墅是你家……上个月你对他爱搭不理,这个月铝价让你高攀不起!虽是玩笑之意,但也传达着市场的情绪。
铝价这种上涨的趋势,使下游很多企业都在观望。
闲暇之余,适合来点干货。
距离上次为大家推送《怎样分辨铝箔好坏?史上最全铝箔质量缺陷集锦 | 实图讲解》已有些时日,今天,小慧带着“涨姿势”系列继续归来,为大家带来的是铝板卷常见的缺陷及原因,赶紧收起来吧!1.复合层脱落定义:复合材料包铝层离开基体并脱落形成的不规则缺陷。
主要原因:包铝层与基体金属之间有异物,导致包铝层无法焊合,并进一步产生包铝层脱落。
2.压花由于带材折皱、断带等原因导致轧辊辊面不规则色差在轧制过程中周期性地印到带材表面的色差现象。
3.波浪边部波浪和中间波浪示意图二肋波浪和碎浪示意图定义:板、带材由于不均匀变形而形成的各种不同的不平整现象的总称。
板、带边部产生的波浪称为边部波浪,中间产生的波浪称为中间波浪,在中间和边部之间的既不在中间又不在两边的波浪称为二肋波浪,尺寸较小且通常呈圆形的波浪称为碎浪。
主要产生原因:a. 辊缝调整不平衡,辊型控制不合理;b. 润滑冷却不均,使板、带变形不均;c. 道次压下量分配不合理;d. 来料板型不良;e. 卷取张力使用不均。
4.翘边定义:经轧制或剪切后,带材边部翘起。
主要产生原因:a. 轧制时压下量过大;b. 轧制时润滑油分布不均匀;c. 剪切时剪刃调整不当。
5.侧边弯曲定义:板、带的纵向侧边呈现向某一侧弯曲的非平直状态。
主要产生原因:a. 轧机两端压下量不一样;b. 轧机送料不正;c. 板、带来料两侧厚度不一致;d. 轧辊预热不良或乳液流量控制不当;e. 工艺润滑剂浓度过高,产生打滑;f. 剪切前带材存在波浪,经剪切后波浪展开。
变形铝及铝合金板带材缺陷_PPT课件

破坏了氧化膜, 对抗蚀性有影 响
A B
滑动;
e) 卷材松卷。
顾客反馈 最终产品质量
所有产品
区别于划伤
二、表面质量缺陷
划伤【★★★★★】
定义及特征
主要产生原因
影响
缺陷分级 涉及方面 主要影响产品
备注
因尖锐的物体(如板角、金属屑或 设备上的尖锐物等)与板面接触, 在相对滑动时所造成的呈单条状分 布的伤痕
则的水渍痕迹。
残留水份;
美观
A
c) 淋雨/停机等原因造成板、带材表
面残留水份,未及时处理干净。
顾客反馈
所有产品
及时烘干后不会进 一步腐蚀
二、表面质量缺陷
黑点/条【★★★☆☆】
定义及特征
主要产生原因
影响
缺陷分级 涉及方面 主要影响产品
备注
a) 工艺润滑不良;
b) 工艺润滑剂不干净;
c) 板、带表面有擦划伤;
板、带材表面沿轧制方向分布的黑 色点/线条状缺陷
d) 板、带通过的导路不干净; e) 铸轧带表面偏析或热轧用铸块铣面 不彻底; f) 金属中有夹杂;
降低材料的抗 蚀性能,也影 响美观
B
g) 开坯轧制时,产生大量氧化铝粉,
并压入金属,进一步轧制产生黑条。
外观
外观件(主要 主要靠阳极氧化检
是阳极氧化件)
铝及铝合金板带材缺陷
质量改善课程
1
产品缺陷分类
2
表面质量缺陷
3
板形质量缺陷
4
外观质量缺陷
一、产品缺陷分类
铝板带产品主要技术要求
① 化学成分——化学成分一般由熔铸工序按技术标准控制。 ② 机械性能——一般产品只要求抗拉强度、屈服强度和延伸率。有的产品还要求硬
铝板常见的问题以及产生原因

1.表面气泡2.贯穿气孔熔铸品质不好。
铸锭含氢量高组织疏松;铸锭表面凸凹不平的地方有脏东面,装炉前没有擦净;蚀洗后,铸块与包铝板表面有蚀洗残留痕迹;加热时间过长或温度过高,铸块表面氧化;第一道焊合轧制时,乳液咀没有闭严,乳液流到包铝板下面。
3.铸块开裂热轧时压下量过大,从铸锭端头开裂;铸块加热温度过高或过低。
4.力学性能不合格没有正确执行热处理制度或热处理设备不正常,石家庄铝板经销空气循环不好;淬火时装料量大,盐浴槽温度不够时装炉,保温时间不足,没有达到规定温度即出炉;试验室采用的热处理制度或试验方法不正确;试样规格形状不正确,试样表面被破坏。
5.铸锭夹渣熔铸品质不好,板片内夹有金属或非金属残渣。
6.撕裂润滑油成分不合格或乳液太浓,板片与轧辊间产生滑动,金属变形不均匀;没有控制好轧制率,压下量过大;轧制速度过大;卷筒张力调整得不正确,张力不稳定;退火品质不好;金属塑性不够;辊型控制不正确,使金属内应力过大;热轧卷筒裂边;轧制时润滑不好,板带与轧辊摩擦过大;送卷不正,带板一边产生拉应力,一边产生压应力,使边沿产生小裂口,经多次轧制后,从裂口处继续扩大,以至撕裂;精整时拉伸机钳口夹持不正或不均,或板片有裂边,拉伸时就会造成撕裂;淬火时,兜链兜得不好或过紧,使板片压裂,拉伸矫直时造成撕裂。
7.过薄压下量调整不正确;测厚仪出现故障或使用不当;辊型控制不正确。
8.压折(折叠)辊型不正确,如压光机轴承发热,使轧辊两端胀大,结果压出的板片中间厚两边薄;压光前板片波浪太大,使压光量过大,从而产生压折;薄板压光时送入不正容易产生压折;板片两边厚差大,易产生压折。
9.非金属压入热轧机的轧辊、辊道、剪刀机等不清洁,加工过程中脏物掉在板车带上,经轧制而形成;冷轧机的轧辊、导辊、三辊矫直机、卷取机等接触带板的部分不清洁,将脏物压入;轧制油喷咀堵塞或压力低,带板表面上粘附的非金属脏物冲洗不掉;乳液更换不及时,铝粉冲洗不净及乳液槽未洗刷干净。
铸轧铝卷缺陷及解决措施

外观:
名称:通条横裂纹
外观:
名称:通条划沟
外观:
名称:热带
外观:
名称:气道
的核质点。
外观:
名称:粗大晶粒
外观:
名称:晶粒不均外观:
名称:粘辊
外观:
名称:裂边
外观:
名称:飞边
名称:缩边
名称:横向细纹
名称:晶内偏析
外观:
名称:
非金属压入
铸轧
非金属压入物呈点状、长条状或不规则形状,颜色随压入物不同而不同
(1) “小飞行物” : 每当夏季时 ,车间里的蚊子、飞蛾较多 ,当它们撞在热态铸轧板上时 ,立即被烫死并被卷入板中 ,形成压入物。
名称:白条
名称:晶粒带
名称:纵向条纹
名称:凉铝
名称:塔形
名称:
名称:松层
化学成分不合格
)不同牌号的回炉冷料混用
)合金添加量计算有误
)对回炉冷料进行分类管理 ,并对重量进行核实。
)在进完铝液之后充分进行搅拌 , 确保熔体成份均匀。
- 1、下载文档前请自行甄别文档内容的完整性,平台不提供额外的编辑、内容补充、找答案等附加服务。
- 2、"仅部分预览"的文档,不可在线预览部分如存在完整性等问题,可反馈申请退款(可完整预览的文档不适用该条件!)。
- 3、如文档侵犯您的权益,请联系客服反馈,我们会尽快为您处理(人工客服工作时间:9:00-18:30)。
2020/9/24
24
1.3.6 自动板形控制
• 自动板形控制过程如下图
分区冷却
弯辊控制
倾辊控制
2020/9/24
一次板形 二次板形 高次板形
图1.
板 形 控 制 调 节 器
自动板形控制系统过程图
板形辊
板形检测 目标板型
25
1.3.7 板形问题案例
• 断带原因分析
2020/9/24
26
1.4 表面质量
无规律的波动: 1.来料厚板波动大,性能不均匀。 2.频繁的加减速及相关的工艺参数 变化。 3.厚度控制机构的周期性振荡。 4.测厚仪相关部件产生了故障。
2020/9/24
13
1.2.4 厚度不合格解决办法及预防
认真检查及设 定目标厚度及
轧制参数
定期对测厚仪进行 标定、修正及维护 提高精度及准确度
定期对压上系统, 传感器,轴承间隙
等设备进行检查
提高磨削精度
2020/9/24
14
1.2.5 案例分析
• 厚度偏薄?
2020/9/24
15
1.3 板形
1.3.1什么是板形? • 板带材的板形是指板带材横向各部位是否
产生波浪和瓢曲,它决定于延伸率沿宽度 方向是否相等。实质指的是带材内部残余 应力的分布。
⑥RE-AGC : Roll Eccentricity - Automatic Gauge Control
厚度自动控制
FF-AGC 前馈厚度
控制
MF-AGC 质量流厚 度控制
MV-AGC 多元可变 厚度控制
MN-AGC 反馈厚度
控制
TLC 张力控制
RE-AGC 轧辊偏心
补偿
其中②目前只使用在S1、S2机架,③未投入使用。Leabharlann 2020/9/2410
1.2.3 厚度不合格现象及分析
a、厚度不合格现象 ①厚度中心点漂移:整体偏薄或偏厚。 ②厚度波动:有规律的周期性波动及无规 律的上下波动。
2020/9/24
11
• b、原因分析
• ①、产生厚度中心点飘移的原因:出口测厚 仪测量数据不真实和操作人员对厚度中心点 设定不恰当所致。
▲结构:放射源、检测器、
标准块盒。
2020/9/24
9
b、厚度控制
①FF-AGC:Feed-forward Automatic Gauge Control ②MF-AGC : Mass Flow - Automatic Gauge Control ③MV-AGC : Multi-Variable - Automatic Gauge Control ④MN-AGC : MoNitor - Automatic Gauge Control ⑤TLC : Tension Limit Control
2020/9/24
23
(6)张力对板形的影响
张力对板形的影响体现在几个方面。
①、张力改变对轧辊热凸度产生影响。
②、张力对轧制压力产生影响,而轧制力变化导致轧辊弹性 变形发生变化。
③、张力分布对金属横向流动产生影响。
(7)轧辊接触状态对板形的影响
工作辊和支撑辊的接触状态对板形的影响。
在轧制过程中,在轧制力的作用下,工作辊与支持辊之间形 成接触压力,在板宽以外的区域,辊间压力形成一个有害弯 矩,它使轧辊发生多余的弯曲。为抵消这个有害弯矩引起的 轧辊变形,可以改变轧辊的初始凸度,也可以使用液压弯辊 。
2020/9/24
7
• 方法2:称重法。
• 根据质量m与体积V的关系 m=ρV
• 将铝板切成单位面积a的圆片。V=aH
• H=m/ρa
ρ-该合金的密度。
冲压单位面积 的圆片
使用高精度电 子称称重
计算得出厚度值
2020/9/24
8
1.2.2 在线测量与厚度控制
A X射线测厚仪
▲原理:基于射线穿过被测材料时,射线的强度因被 材料吸收而减少,其射线剂量的减少又与材料的厚 度由一定的函数关系,通过转换测量出材料的厚度 。
22
(2)轧制力变化对板形的影响。
使轧辊挠曲变形,使辊缝形状变化。
(3)热凸度变化对板形的影响。 (4)初始轧辊凸度对板形的影响 (5)板宽变化对板形的影响
横刚度是指造成板中心和边部单位厚差所需要的轧制力, 单位是kN/mm。轧机的横刚度是相对一定板宽而言的,当 板宽变化时,轧机的横刚度发生变化。
影响出口测厚仪测量准确性的因素有:校 核测厚仪的标准板厚度不准确引起厚度中心 点设定不准确,测厚仪厚度补偿系数不准确 ;放射源发出的射线被其他物件所挡;测厚 仪自动清零功能不稳定。
2020/9/24
12
②、产生厚度波动的原因
•。
厚度波动的主要原因
有规律周期 性波动: 轧辊的磨削 精度不高圆 度不够。
• 出现板形不良的直接原因是轧件宽向上延 伸不均。
2020/9/24
20
• 出现板形不良的根本原因是:轧件在轧 制过程中,轧辊产生了有害变形,致使 辊缝形状不平直,从而产生波浪。
2020/9/24
21
1.3.5 影响板形的因素
(1)来料板形对出口板形的影响 来料截面积与辊形不匹配。
2020/9/24
• 表面质量时衡量产品优劣的重要指标,是 客户对产品评价的直观因素。
。 • 详见《铝板带轧制表面质量缺陷及形因》
2020/9/24
27
1.5 性能
A 加工硬化 金属在变形过程中随着变形程度的增加,强度和硬 度明显增加,塑性迅速下降的现象称为~ 。
铝带轧制常见故障 分析及处理
2020/9/24
1
目录
111 生产故障 操作及设备故障
22
2020/9/24
2
1.生产故障
1.1怎样才是合格的铝板带产品?
板形良好
性能稳定
优质的产品
表面无缺陷
厚度精确
2020/9/24
3
1.2 铝板厚度
• 达到目标板厚的步骤
根据订单确认目标 厚度
根据目标厚度确定来 料厚度及压下制度
2020/9/24
16
1.3.2 板形的种类
• 理想板形 • 潜在板形 • 表观板形 • 混合板形
2020/9/24
17
1.3.3 表观板形的种类
A、侧弯 B、中浪 C、边浪 D、二肋浪
2020/9/24
18
E、小边浪 F、小中浪 G、复合浪 H、斜浪
2020/9/24
19
1.3.4 板形不良的根本原因
应用相应的压下制度 进行轧制
NO
查找厚度偏差原因 并整改
YES
离线检测厚度 是否准确
精确的在线测量与 厚度控制
2020/9/24
4
如图示例为 我公司的销 售生产订单
2020/9/24
5
如图为生产计划单
2020/9/24
6
1.2.1 离线测量板厚
• 方法1:千分尺直测法。 • 使用方法:正确使用千分尺测量的方法。 • 测量位置:多点测量,注意边部减薄。