OEE记录表格(设备综合效率)
设备综合效率(OEE)计算表

#D I#VD I#VD I#VD I#VD I#VD IV 0
#D I#VD I#VD I#VD I#VD I#VD IV 0
#D I#VD I#VD I#VD I#VD I#VD IV 0
#D I#VD I#VD I#VD I#VD I#VD IV 0
#D I#VD I#VD I#VD I#VD I#VD IV 0
#D I#VD I#VD I#VD I#VD I#VD IV 0
#D I#VD I#VD I#VD I#VD I#VD IV 0
#D I#VD I#VD I#VD I#VD I#VD IV 0
#D I#VD I#VD I#VD I#VD I#VD IV 0
#D I#VD I#VD I#VD I#VD I#VD IV 0
XXXX 有限
设 备 效 率(OEE) 计 算 表
设备编号: 日期
总工作时间
设备名称:
日 期:
年
月
1
2
3
4
5
6
7
8
9
10
11
12
13
14
15
16
17
18
19
20
21
22
23
24
25
26
27
28
29
30
31
全月总 计
0
点检保养
0
计划 工间休息
0
停止
时间 计划维修
0
停产调整
0
负荷时间
0000000000000000000000000000000 0
实际生产周期
######
时间运行效率
速度运行效率
设备综合效率oee计算表 (1)
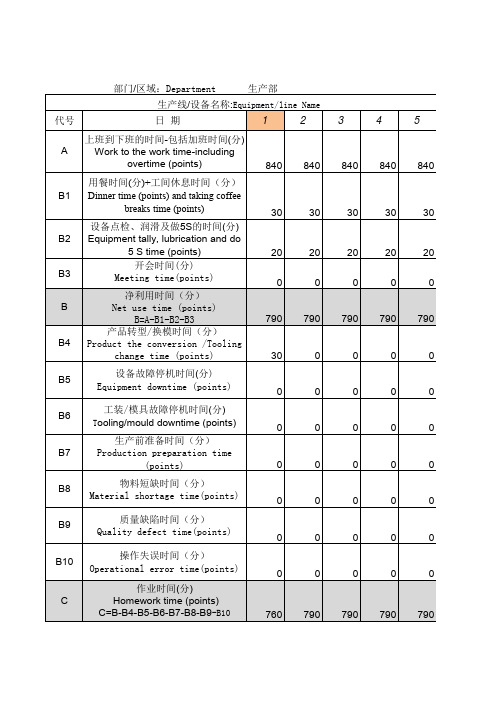
11600 12900
5000
0 14800 18900 7500 17560 16500 17500
0.057 0.045
0.062
0 0.075 0.07 0.097 0.07 0.07 0.07
72.7% 92.1% 96.9% #DIV/0! 86.7% 95.9% 90.9% 96.0% 90.2% 95.7%
320
0 1280 1400 800 1280 1280 1280
0
0
0
0
0
20
0
0
0
0
0
0
0
0
0
0
0
0
0
0
0
0
0
0
0
0
0
0
0
0
0
0
0
0
0
0
0
0
0
0
0
0
0
0
0
0
0
0
0
0
0
0
0
0
0
0
0
0
0
0
0
0
0
0
0
0
0
0
0
0
910 630
320
0 1280 1380 800 1280 1280 1280
100.0% 100.0% 100.0% #DIV/0! 100.0% 98.6% 100.0% 100.0% 100.0% 100.0%
26
27
28
29
30
6月 31 综合
1320 1320 1320 1320 1320
0 30540
OEE怎么算看完这篇文章你就明白了~附OEE计算表格
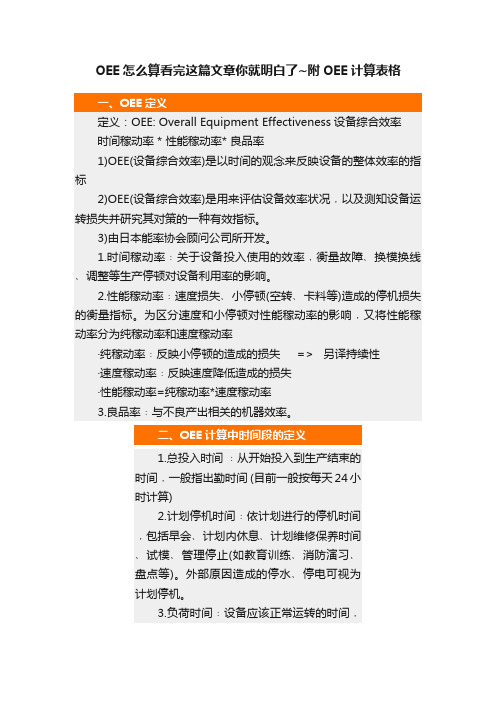
OEE怎么算看完这篇文章你就明白了~附OEE计算表格定义:OEE: Overall Equipment Effectiveness设备综合效率时间稼动率 * 性能稼动率* 良品率1)OEE(设备综合效率)是以时间的观念来反映设备的整体效率的指标2)OEE(设备综合效率)是用来评估设备效率状况﹐以及测知设备运转损失并研究其对策的一种有效指标。
3)由日本能率协会顾问公司所开发。
1.时间稼动率﹕关于设备投入使用的效率﹐衡量故障﹑换模换线﹑调整等生产停顿对设备利用率的影响。
2.性能稼动率﹕速度损失﹑小停顿(空转﹑卡料等)造成的停机损失的衡量指标。
为区分速度和小停顿对性能稼动率的影响﹐又将性能稼动率分为纯稼动率和速度稼动率·纯稼动率﹕反映小停顿的造成的损失 => 另译持续性·速度稼动率﹕反映速度降低造成的损失·性能稼动率=纯稼动率*速度稼动率3.良品率﹕与不良产出相关的机器效率。
1.总投入时间﹕从开始投入到生产结束的时间﹐一般指出勤时间 (目前一般按每天24小时计算)2.计划停机时间﹕依计划进行的停机时间﹐包括早会﹑计划内休息﹑计划维修保养时间﹑试模﹑管理停止(如教育训练﹑消防演习﹑盘点等)。
外部原因造成的停水﹑停电可视为计划停机。
3.负荷时间﹕设备应该正常运转的时间﹐为总投入时间减去计划停机时间 (计算OEE 的分母)4.当机时间﹕指由于设备故障﹑模具故障﹑换模换线﹑暖机﹑换料等造成的生产停止时间。
1)设备故障时间﹕因设备故障造成机器停机的总时间。
包含维修时间和调试时间﹐直至可正常生产2)换线损失时间﹕机器因切换不同产品或为达成产品最终特性而进行调整的总时间﹐包括从前一个产品停止到新产品第一个良品产出所花费所有的时间3)模具故障时间﹕因模具原因造成的停机的总时间4)暖机时间﹕暖机时间是指﹐要开始生产时﹐启动﹑调整运转﹑直至加工条件安定前所需要的时间5.稼动时间﹕设备实际用于生产的时间﹐等于负荷时间减去当机时间6.净稼动时间﹕稼动时间中扣除速度损失﹑小停顿损失后的产出时间。
设备综合效率(OEE)

Level 3
1
计划保修体制的确立
1
Level 4 状态 保修体制的确立
故
2
事后保修 >预防保修
2
事后保修 =预防保修
2
事后保修 < 预防保修
2
预防保修
障
L
3 故障LOSS有多大没有统计 3 发生故障 LOSS1%以上 3
故障LOSS 1%以下
3
故障LOSS 0.1%~0
O
4 自主保修体制的不完备 4 自主保修体制正在完备中 4 开展自主保修体制的活动 4 自主保修体制的维持和改善
TPM “三全”理念和OEE
全 效 率 全 过 程 全 员
目标 对象/范围 基础
设备的六大损失
1. 设备停机时间损失 2. 设置与调整损失 3. 空转与短暂停机损失 4. 速度降低损失 5. 残次品损失 6. 产量损失(从安装到稳定生产、或班次
)
六大损失定义
1. 停机:未预料到的大于10分钟的设备停机,丧失原有功 能或需要更换零部件的时间。
① 故障
设备1台当故障频度 10分以上 – 1回以下
②
准备 调整
准备调整时间 / 回 10分以下
空转 ③ 瞬间
停止
空转,瞬间停止频度 10分以下-3回/月以下
理论 CYCLE TIME实现 ④ 速度
回转数 10%以上 UP
⑤
工程 不良
工程别不良率(修理 包含) 0.1以下
⑥
初期 收率
初期收率 LOT SIZE 的 90%以上
案例:单台设备综 合 设 备 效 率 (OEE)计算
例题:
❖ 假设有一工厂某设备某班某天工作时间为8小时,其 中用餐、休息时间为1小时,在上线和收工之前的开 会、点检、清扫需费时30分钟,因突发故障而停机时 间为20分钟,而且每天必须换线2次,每次15分钟, 每天必须更换刀具1次,费时10分钟;生产线生产周 期为0.4分钟,当天生产数量为750个产品,其中不 合格品为50个。请计算其总设备效率。
设备综合效率OEE统计表(使用)

6600
64.25
150
6600
70.83 42.83
%
%
100.0 0%
30.3 4%
00
#DIV/0!
#DIV/ 0!
#DIV/ 0!
#DIV/ 0!
#DIV/ 0!
#DIV /0!
00
#DIV/0!
#DIV/ 0!
#DIV/ 0!
#DIV/ 0!
#DIV/ 0!
#DIV /0!
00
#DIV/0!
#DIV /0!
#DIV/0!
#DIV/ 0!
#DIV/ 0!
#DIV/ 0!
#DIV/ 0!
#DIV /0!
#DIV/0!
#DIV/ 0!
#DIV/ 0!
#DIV/ 0!
#DIV/ 0!
#DIV /0!
#DIV/0!
#DIV/ 0!
#DIV/ 0!
#DIV/ 0!
#DIV/ 0!
#DIV /0!
#DIV/ 0!
#DIV /0!
00
#DIV/0!
#DIV/ 0!
#DIV/ 0!
#DIV/ 0!
#DIV/ 0!
#DIV /0!Biblioteka 00#DIV/0!
#DIV/ 0!
#DIV/ 0!
#DIV/ 0!
#DIV/ 0!
#DIV /0!
00
#DIV/0!
#DIV/ 0!
#DIV/ 0!
#DIV/ 0!
#DIV/ 0!
计划停机时间
生产 总数
不合 格数
计划 保养
休息
调机
培训
会议
OEE统计表

F—设备故障/维修
G—工装故障/维修
E—检验
~ ~ ~ ~ ~ ~ ~ ~ ~ ~ ~ ~ ~ ~ ~ ~ ~ ~ ~
: : : : : : : : : : : : : : : : : : : 产出 合计
作业内容:A—正常生产 B—更换工装/模具 C—韧磨/更换刀具 D—待料/待单 H—设备更换调试 I—品质异常及处理 J—5S/休息 K—其它(在备注栏注明)
四川绵阳三力股份有限公司
设备综合效率(OEE)统计表
车间: 日期 班次 员工姓名 工段: 产品型号 名称 批次号 计划 数量 设备名称/型号: 工序名称 标准时间 (秒/件) 公司编号: 起止时间 生产 状态 良品 数量 不良 数量 备注
: : : : : : = 时间开动率×性能开动率×合格品率 =合格产品的理论加工总时间÷负荷时间 设备综合效率(OEE)
OEE记录表格(设备综合效率)
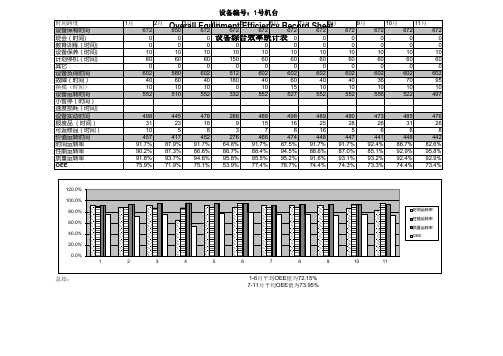
498 31 10 457 91.7% 90.2% 91.8% 75.9%
445 23 5 417 87.9% 87.3% 93.7% 71.9%
478 18 8 452 91.7% 8பைடு நூலகம்.6% 94.6% 75.1%
288 9 3 276 64.8% 86.7% 95.8% 53.9%
488 15 7 466 91.7% 88.4% 95.5% 77.4%
设备编号:1号机台
时间跨度 设备保有时间 班会(时间) 教育训练(时间) 设备保养(时间) 计划停机(时间) 其它 设备负荷时间 故障(时间) 换模(时间) 设备运转时间 小暂停(时间) 速度损耗(时间) 设备实动时间 报废品 (时间) 可返修品(时间) 价值运转时间 时间运转率 性能运转率 质量运转率 OEE 1月 672 0 0 10 60 0 602 40 10 552 2月 3月 4月 5月 6月 7月 8月 Overall Equipment Efficiency Record Sheet 650 672 672 672 672 672 0 0 设备综合效率统计表 0 0 0 0 0 10 60 0 580 60 10 510 0 10 60 0 602 40 10 552 0 10 150 0 512 180 0 332 0 10 60 0 602 40 10 552 0 10 60 0 602 60 15 527 0 10 60 0 602 40 10 552 9月 672 0 0 10 60 0 602 40 10 552 672 0 0 10 60 0 602 36 10 556 10月 672 0 0 10 60 0 602 70 10 522 11月 672 0 0 10 60 0 602 95 10 497
设备综合效率OEE统计表
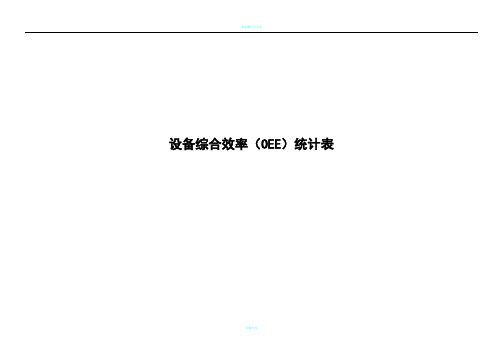
白班
中班
零班
全天
A
交接班/班前准备
B
模具部件安装/消毒
C
设备调整、试车、预热
D
生产
E
日常维护/清洁
F
设备故障-待修
G
设备故障-维修
H
非常规清洁
I
任务完成后计划停机
累加
设备名称
设备型号
设备最大生产能力
OEE统计
月计划生产时间 =min
月净生产时间 =min
产品/批次:___________________
数量:_______________________
组长签名:___________________
5
10
15
20
25
30
35
40
45
50
55
60
5
10
15
20
25
30
35
40
45
50
55
60
5
10
15
20
25
30
35
40
45
50
55
60
5
10
15
20
25
30
35
40
45
50
55
60
04:00 05:00 06:00 07:00 08:00
5
10
15
20
25
30
35
40
45
50
55
60
5
10
15
20
25
30
设备综合效率OEE统计表
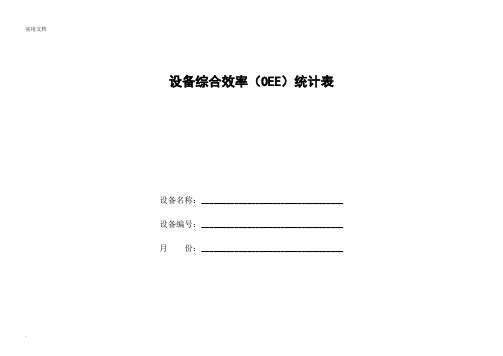
当天班次总时间=min
计划生产时间=当天班次总时间-计划停机时间=当天班次总时间- A - I =min
净生产时间=计划生产时间-非计划停机时间=计划生产时间- B - C - E - F - G -H =min
OEE =时间开动率×性能开动率×合格品率
=【净生产时间/计划生产时间】×【净开动率×速度开动率】×【合格品数量/总产量】
25
30
35
40
45
50
55
60
12:00 13:00 14:00 15:00 16:00
5
10
15
20
25
30
35
40
45
50
55
60
5
10
15
20
25
30
35
40
45
50
55
60
5
10
15
20
25
30
35
40
45
50
55
60
5
10
15
20
25
30
35
40
45
50
55
60
中班
16:00 17:00 18:00 19:00 20:00
25
30
35
40
45
50
55
60
04:00 05:00 06:00 07:00 08:00
5
10
15
20
25
30
35
40
45
50
55
60
5
10
15
20
OEE设备综合效率统计表
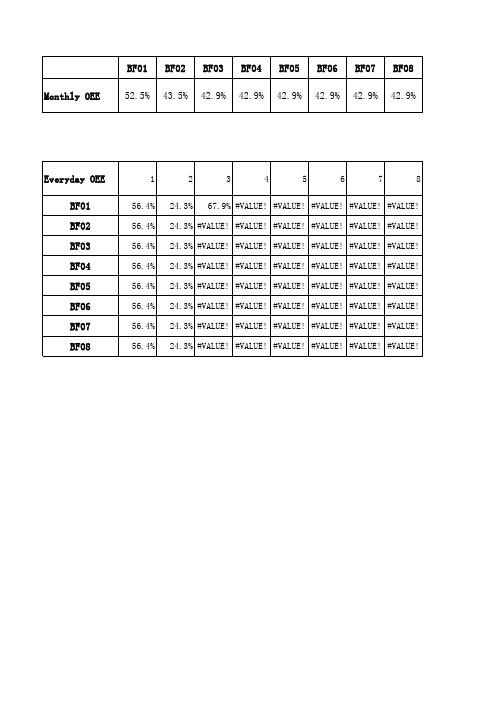
26 #VALUE! #VALUE! #VALUE! #VALUE! #VALUE! #VALUE! #VALUE! #VALUE!
#VALUE! #VALUE! #VALUE! #VALUE! #VALUE! #VALUE! #VALUE! #VALUE! #VALUE! #VALUE! #VALUE! #VALUE! #VALUE! #VALUE! #VALUE! #VALUE!
28
29
30
31
#VALUE! #VALUE! #VALUE! #VALUE! #VALUE! #VALUE! #VALUE! #VALUE! #VALUE! #VALUE! #VALUE! #VALUE! #VALUE! #VALUE! #VALUE! #VALUE!
#VALUE! #VALUE! #VALUE! #VALUE! #VALUE! #VALUE! #VALUE! #VALUE! #VALUE! #VALUE! #VALUE! #VALUE! #VALUE! #VALUE! #VALUE! #VALUE!
16 #VALUE! #VALUE! #VALUE! #VALUE! #VALUE! #VALUE! #VALUE! #VALUE!
17 #VALUE! #VALUE! #VALUE! #VALUE! #VALUE! #VALUE! #VALUE! #VALUE!
#VALUE! #VALUE! #VALUE! #VALUE! #VALUE! #VALUE! #VALUE! #VALUE! #VALUE! #VALUE! #VALUE! #VALUE! #VALUE! #VALUE! #VALUE! #VALUE!
9 #VALUE! #VALUE! #VALUE! #VALUE! #VALUE! #VALUE! #VALUE! #VALUE!
设备效率统计表
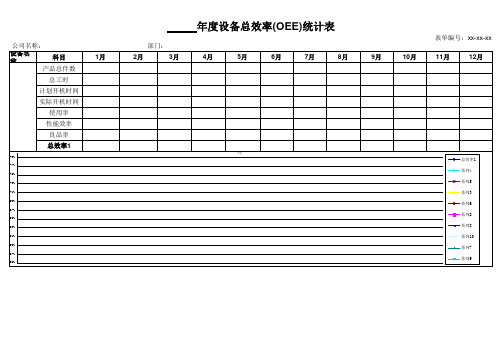
12月
月份
总效率1 系列4 系列5 系列3 系列6 系列2 系列8 系列10 系列7 系列9
OEE是Overall Equipment Effectiveness(全局设备效率)的缩写;OEE=使用率X 性能效率 X良品率。 其中: 使用率=操作时间 / 计划工作时间 它是用来考虑停工所带来的损失,包括引起计划生产发生停工的任何事件,例如设备故障,原料短缺以及生产方法的改变等) 性能效率=(总产量/操作时间)/理想周期时间=(总产量 / 操作时间)/ 生产速率 (性能效率考虑生产速度上的损失。包括任何导致生产不能以最大速度运行的因 素,例如设备的磨损,材料的不合格以及操作人员的失误等) 良品率=良品/总产量 (质量指数考虑质量的损失,它用来反映没有满足质量要求的产品(包括返工的产品)) 利用OEE的一个最重要目的就是减少一般制造业所存在的六大损失:停机损失、换装调试损失、暂停机损失、减速损失、启动过程次品损失和生产正常运行时产 生的次品损失。
公司名称:
设备名 称
科目
产品总件数
总工时
计划开机时间
实际开机时间
使用率
性能效率
良品率
总效率1
79% 77% 75% 73% 71% 69% 67% 65% 63% 61% 59% 57% 55%
1月
部门:
2月
3月
年度设备总效率(OEE)统计表
4月
5月
6月
7月
8月Βιβλιοθήκη 表单编号:xx-xx-xx
9月
10月
11月
OEE统计表
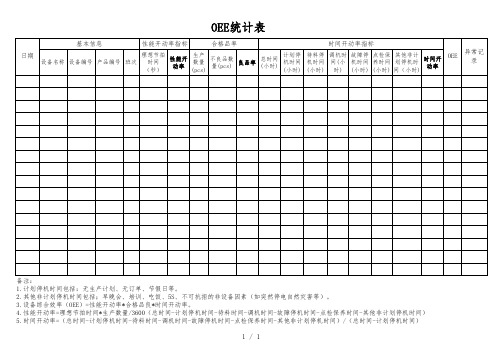
OEE统计表
备注:
1.计划停机时间包括:无生产计划、无订单、节假日等。
2.其他非计划停机时间包括;早晚会、培训、吃饭、5S、不可抗拒的非设备因素(如突然停电自然灾害等)。
3.设备综合效率(OEE)=性能开动率*合格品良*时间开动率。
4.性能开动率=理想节拍时间*生产数量/3600(总时间-计划停机时间-待料时间-调机时间-故障停机时间-点检保养时间-其他非计划停机时间)
5.时间开动率=(总时间-计划停机时间-待料时间-调机时间-故障停机时间-点检保养时间-其他非计划停机时间)/(总时间-计划停机时间)
1 / 1。
设备综合效率OEE计算(附计算表格)

OEE(设备综合效率)
OEE计算(文末附计算表格)
1、OEE=时间开动率x性能开动率x合格率
2、时间开动率=实际操作时间/计划工作时间
计划工作时间=总可用时间-计划停机时间
(计划停机时间为员工休息、吃饭时间,计划保养时间)
实际操作时间=计划工作时间-计划外停机时间
(计划外停机时间为计划工作时间中设备故障、设备调整、设备紧急换型等非计划性时间)
3、性能开动率=实际产量/(实际操作时间/理想节拍时间)
4、合格率=良品数量/实际总产量
例如:某设备1天工作时间为24h,员工用餐、休息时间90min,班中计划保养停机60min,故障停机20min,生产中工艺调整30min,产品的理论加工周期为1.2min/件,一天加工产品1000件,有100件废品,求这台设备的设备综合效率OEE
备注:浅绿色为需要输入数据。
(精品)OEE记录表格(设备综合效率)

理论节拍时间:
400次/min
实际节拍时间:
320次/min
合格产品数量:
70048pcs
报废产品数量:
11352pcs
可返工产品数量:
0
质量问题描述:
产品 #2 KC0154 400次/min 420次/min 67125
0 12225
产品 #3
模具或设备故障描述
1
2
3
4
5
6
问题原因初步判定和措施
设备运行状况统计表
设备编号:
生产日期/班:
组长确认:
班长确认:
8:00
9:00
时间
(10分钟/ 格)
原因
时间
(10分钟/ 格)1Leabharlann :0014:00原因
10:00 15:00
11:00 16:00
12:00 17:00
13:00
操作工:
18:00
注: 每格为5分钟
产品 #1
零件号/名称:
KA 0051
可疑品处理
1
KA:孔未冲出
冲针断,换下模具维修
筛选
2
KC:毛刺大
新模不稳定
筛选,返工
3
4
符号:
P 设备保养 D 无生产计划
C 架模(需注明下一产品号) T 模具或设备故障(需注明故障名称)
R 休息 W 待料
A 调试新模具 O 其它
维修和处理结果及验证 最终解决方案和验证
设备运行状况统计表
19'40
表格模板-设备综合利用率统计表 精品
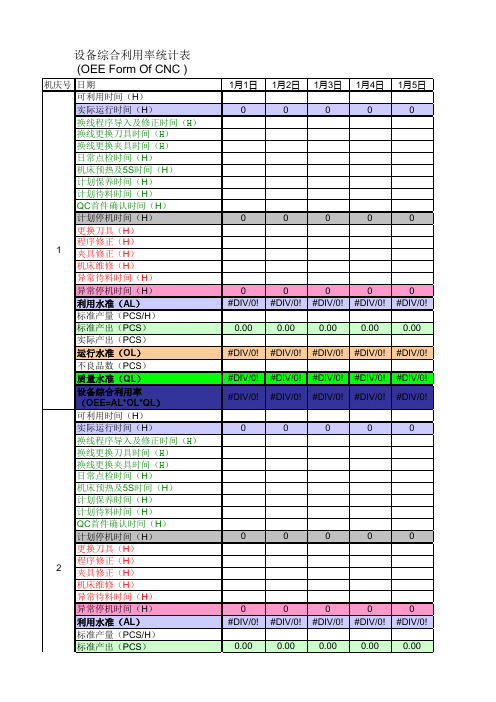
(OEE Form Of CNC )
机庆号 日期 可利用时间(H) 实际运行时间(H) 换线程序导入及修正时间(H) 换线更换刀具时间(H) 换线更换夹具时间(H) 日常点检时间(H) 机床预热及5S时间(H) 计划保养时间(H) 计划待料时间(H) QC首件确认时间(H) 计划停机时间(H) 更换刀具(H) 程序修正(H)
0.00
0.00
0.00
0.00
0.00
#DIV/0! #DIV/0! #DIV/0! #DIV/0! #DIV/0!
#DIV/0! #DIV/0! #DIV/0! #DIV/0! #DIV/0! #DIV/0! #DIV/0! #DIV/0! #DIV/0! #DIV/0!
0
0
0
0
0
0
0
0
0
0
0
0
0
0
0
0
0
0
0
0
0
0
0
0
0
0
0
#DIV/0! #DIV/0! #DIV/0! #DIV/0! #DIV/0!
0.00
0.00
0.00
0.00
0.00
实际产出(PCS) 运行水准(OL) 不良品数(PCS) 质量水准(QL)
设备综合利用率 (OEE=AL*OL*QL) 可利用时间(H) 实际运行时间(H) 换线程序导入及修正时间(H) 换线更换刀具时间(H) 换线更换夹具时间(H) 日常点检时间(H) 机床预热及5S时间(H) 计划保养时间(H) 计划待料时间(H) QC首件确认时间(H) 计划停机时间(H) 更换刀具(H) 程序修正(H) 3 夹具修正(H) 机床维修(H) 异常待料时间(H) 异常停机时间(H) 利用水准(AL) 标准产量(PCS/H) 标准产出(PCS) 实际产出(PCS) 运行水准(OL) 不良品数(PCS) 质量水准(QL)
设备综合效率(OEE)

型号
A B C D
产能(个/分 ) 63 60 60 79
生产数量
12600 12000 15000 13790
不良品
180 160 150 188
设备 LOSS的构造和指标
设备
6大 LOSS
管理指标
作业时间
负荷时间
计划 维持
开动时 间
停止 LOSS
纯开动时间
速度 LOSS
价 值 不良 加动时间 LOSS
通过8大损失计算TEEP
设备
八大损失
利用率计算
负荷时间
计划停机 外部因素
设备 利用率
=
工作时间 开动时间
停
开动时间
机 损
失
净开动
速
时间
度
损
失
设备故障 安装调整
空转短暂 停机 速度降低
时间 开动率
=
性能 开动率
=
有价 废 值开 品 动时 损 间失
加工废品
初期未 达产
合格 品率
=
产能利用率TEEP=设备利用率×OEE
间
管理损失
运作损失
生产线管理损失
后勤和运输
测量和调节损失
能源损失
成
备品备件损失
原材料损失
本
联合利华世界500强在经过近10年的OEE的管理,2010年 才从12大损失向16大损失迈进。
其中它是先做6大损失到9大损失到12大损失不断的摸索中 才有今天的成绩。数据显示联合利华洗衣粉的产量从2004年 日产260T/D到2010年日产近1000T/D。其中生产机器只增加 了50%。在OEE的数据支撑下结合一些优良的管理方法再 加上公司员工的群策群力下设备的效率平均提高了48.6%。
设备综合效率OEE统计表(使用)
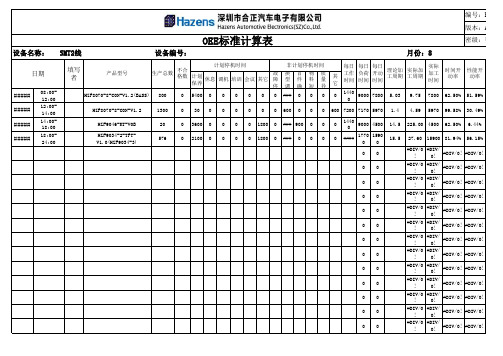
HZF8070-8-CON-V1.2(BASS) 800
0 5400 0 0 0 0 0 0 ### 0 0 0
其 它
每日 工作 时间
每日 每日 负荷 开动 时间 时间
理论加 工周期
实际加 工周期
实际 加工 时间
0
1440 0
9000
7800
5.03
#DIV/0! #DIV/0! #DIV/0! #DIV/0! #DIV/0! #DIV/0! #DIV/0! #DIV/0! #DIV/0! #DIV/0! #DIV/0! #DIV/0! #DIV/0! #DIV/0! #DIV/0! #DIV/0! #DIV/0! #DIV/0!
00
#DIV/0 !
#DIV/ 0!
#DIV/0!
#DIV/0!
00
#DIV/0 !
#DIV/ 0!
#DIV/0!
#DIV/0!
00
#DIV/0 !
#DIV/ 0!
#DIV/0!
#DIV/0!
00
#DIV/0 !
#DIV/ 0!
#DIV/0!
#DIV/0!
00
#DIV/0 !
#DIV/ 0!
#DIV/0!
#DIV/ 0!
#DIV/0!
#DIV/0!
00
#DIV/0 !
#DIV/ 0!
#DIV/0!
#DIV/0!
00
#DIV/0 !
#DIV/ 0!
#DIV/0!
#DIV/0!
00
#DIV/0 !
#DIV/ 0!
#DIV/0!
#DIV/0!
00
#DIV/0 !
- 1、下载文档前请自行甄别文档内容的完整性,平台不提供额外的编辑、内容补充、找答案等附加服务。
- 2、"仅部分预览"的文档,不可在线预览部分如存在完整性等问题,可反馈申请退款(可完整预览的文档不适用该条件!)。
- 3、如文档侵犯您的权益,请联系客服反馈,我们会尽快为您处理(人工客服工作时间:9:00-18:30)。
设备编号:
日期/班: 设备保有时间 班会(时间) 教育训练(时间) 设备保养(时间) 计划停机(时间) 其它 设备负荷时间 故障(时间) 换模(时间) 设备运转时间 小暂停(时间) 速度损耗(时间) 设备实动时间 报废品 (时间) 可返修品(时间) 价值运转时间 时间运转率 性能运转率 质量运转率 OEE 1440 0 0 10 720 0 710 50 90 570
0 #DIV/0! #DIV/0! #DIV/0! #DIV/0!
0 #DIV/0! #DIV/0! #DIV/0! #DIV/0!
0 #DIV/0! #DIV/0! #DIV/0! #DIV/0!
0 #DIV/0! #DIV/0! #DIV/0! #DIV/0!
0 #DIV/0! #DIV/0! #DIV/0! #DIV/0!
0 #DIV/0! #DIV/0! #DIV/0! #DIV/0!
0 #DIV/0! #DIV/0! #DIV/0! #DIV/0!
0
100.0% 90.0% 80.0% 70.0% 60.0% 50.0% 40.0% 30.0% 20.0% 10.0% 0.0% 1 2 3 4 5 6 7 8 9 10 11
0
0
000源自0000
0
0
0
0
0
0
0
0
0
0
0
396.87 28.38 30.56 342.93 80.3% 69.6% 86.4% 48.3%
0 #DIV/0! #DIV/0! #DIV/0! #DIV/0! #DIV/0! #DIV/0! #DIV/0! #DIV/0!
0 #DIV/0! #DIV/0! #DIV/0! #DIV/0!
时间运转率 性能运转率 质量运转率
OEE
Overall Equipment Efficiency Record Sheet 设备综合效率统计表