陶瓷工业机械设备第十二章-干压成形机械(8)
陶瓷干压成型工艺精选全文完整版

陶瓷⼲压成型⼯艺陶瓷常⽤的成型⽅法有⼲压、流延以及注射,其中⼲压成型是应⽤最⼴泛的⼀种成型⼯艺,也是⼿机陶瓷背板主流的成型⼯艺之⼀,今天,我们就来详细了解⼀下陶瓷⼲压成型⼯艺。
陶瓷⼲压成型⼯艺⼀、⼲压成型⼲压成型⼜称模压成型,是最常⽤的成型⽅法之⼀。
⼲压成型是将经过造粒后流动性好,颗粒级配合适的粉料,装⼊⾦属模腔内,通过压头施加压⼒,压头在模腔内位移,传递压⼒,使模腔内粉体颗粒重排变形⽽被压实,形成具有⼀定强度和形状的陶瓷素坯。
陶瓷⼲压成型⼯艺⼆、⼲压成型的⼯艺原理和影响因素1. ⼯艺原理⼲压成型的实质是在外⼒作⽤下,颗粒在模具内相互靠近,并借助内摩擦⼒牢固地把各颗粒联系起来,保持⼀定形状。
这种内摩擦⼒作⽤在相互靠近的颗粒外围结合剂薄层上。
随着压⼒增⼤,坯料将改变外形,相互滑动,间隙减少,逐步加⼤接触,相互贴紧。
由于颗粒进⼀步靠近,使胶体分⼦与颗粒间的作⽤⼒加强因⽽坯体具有⼀定的机械强度。
2. 影响因素影响⼲压成型的主要因素有:•粉体性质:粒度、粒度分布、流动性、含⽔率等;•粉体性质:粒度、粒度分布、流动性、含⽔率等;•粘结剂和润滑剂的选择;•模具设计;•压制过程中压制⼒、加压⽅式、加压速度与保压时间。
综上,如果坯料颗粒级配合适,结合剂使⽤正确,加压⽅式合理,⼲压法也可以得到⽐较理想的坯体密度。
陶瓷⼲压成型⼯艺三、⼲压成型的分类根据压头和模腔运动⽅式的不同,⼲压成型可以为以下⼏种:•单向加压,即模腔和下压头固定,上压头移动;•双向加压,即模腔固定,上压头和下压头移动;•可动压模,下压头固定,模腔和上压头移动,即压头和模腔的运动是同步的,使⽤液压控制时,在某⼀设定压⼒下压头停⽌移动。
⽽双⾯加压⼜分为双⾯同时加压和双⾯先后加压,其中双⾯先后加压是指两⾯的压⼒先后加上,由于先后分别加压,压⼒传递⽐较彻底,有利于⽓体排出,作⽤时间较长,故其坯体密度⽐前⾯两种均匀。
陶瓷⼲压成型⼯艺四、⼲压成型的特点1. ⼲压成型的优点:•⼯艺简单,操作⽅便,周期短,效率⾼,便于实⾏⾃动化⽣产。
陶瓷滚压成型机总分配轴及滚压头系统设计

陶瓷滚压成型机总分配轴及滚压头系统作者姓名专业指导教师姓名专业技术职务教授目录摘要 (1)第一章陶瓷滚压成型机滚压系统和分配轴设计简介1.1陶瓷滚压成型机简介 (1)1.2陶瓷工艺及市场状况 (1)1.3滚压系统介绍 (2)1.4分配轴介绍 (3)第二章设计内容 (3)2.1 技术参数 (4)2.2 滚压系统的设计 (4)2.3 分配轴的设计 (11)2.4 其他零件的设计 (16)参考文献 (18)致谢 (18)本科生毕业设计(论文)摘要本文综述了陶瓷市场的现状及发展,阐述了陶瓷滚压成型机设计的工作原理及其主要工作系统的设计工作,特别是滚压系统和分配轴的设计。
最后结合零部件的设计过程并运用AUTOU CAD软件实现图纸设计。
滚压成型较刀压成型机有很多优点,滚压成型的工具是滚头。
成型时,滚头与泥料之间除了有相对滑动之外,主要还有相对滚动,且滚压成型的坯体质量好,操作简单。
关键词:滚压成型机分配轴滚压轴计算机辅助绘图ABSTRACTT his article provides an overview of the current status and development of ceramic markets, expounded ceramic rollers shaped aircraft design work systems and its main operating principles of the design work, especially the flow system and the distribution of axle design. Finally with the help of AUTOU CAD, the paper was finished.Bamboo shaped knife pressed shaped machine a lot more advantages, bamboo shaped tool is the first roll. Shaped, roll between the first and mud materials, in addition to the relative sliding, there is also the relatively rolling, and the accompanying flow shaped body of good quality, simple operation.Key word s: bamboo shaped plane; distribution axle; roller axle; AUTOU CAD第一章陶瓷滚压成型机滚压系统和分配轴设计简介1.1 陶瓷滚压成型机简介滚压成型的工具是滚头,滚头是一个回转体,滚头回转体的母线与坯体成型表面的母线相同。
陶瓷成型机械-滚压成型机

一些产品的主轴转速范围:
盘类 <7英寸(18cm)
500-800 rpm
> 7英寸(18cm) 300-600 rpm 碗类 杯类 500-800 rpm 700-1300 rpm
8
滚头倾角
9
滚压成型时泥料的运动
10
单头固定式
山东博山 陶瓷机械厂
11
转盘式滚压成型机
Байду номын сангаас
日本新荣机工 株式会社
12
4
5
6
主轴转速
1-由工作循环可知:主轴作间歇转动,与滚压头保持 一定的转速比。 2-石膏模有一定的吸水性,如坯泥在模中时间长,靠 近模型一侧坯体失水,坯体内水分不均,影响成型 效果。因此希望主轴转速快,加速成型过程。 3-主轴转速快,单位时间内滚头对坯泥压延次数多, 坯体表面致密光滑;如保持压延次数则能缩短单件 坯体成型时间,提高产量。 4-每成型一件坯体主轴要启动及制动一次,转速高, 制动阻力大,产生振动,同时会增大离合器摩擦片 的磨损。 5-转速过快,由于加工精度有限而发生振动,传给模 型,成型时坯体上会形成波纹及其它缺陷。 7 6-转速过快由于离心作用会使坯泥飞出。
1
1-成型坯体密度高,强度大,不易变形。
2-坯体规格一致,生产效率高,减轻劳动强度。 3-不需很高的操作技术,便于组成半自动化生产 线。
2
阳模成型
阴模成型
3
1-主电动机 2-凸轮轴 3-主轴离合器凸轮 4-滚头升降凸轮 5-滚头架 6-滚头电动机 7-滚头轴 8-滚头 9-模座 10-主轴 11-摩擦离合器 12-活动连轴器 13-蜗杆轴 14-蜗杆
双头固定式 滚压成型机
唐山轻工机械厂
13
日本新荣 特大型滚压成型机(产品直径400-700mm)
陶瓷粉末压制成型过程数值模拟的研究

geometry size in die pressing were simulated respectively.珊lat is more,the
powder grain’S flow rule and the friorion between the powder and the die wall were taken into consideration.Then,nle distribution of relative density and the changes of both axial size and radial size of the ZI'02 ceramic plunger in the wet isostatie pressing process were analyzed precisely.Tllis paper also did some research on the
caused.
Keywords:Finite element simulation method;Die pressing;Wh isostatic pressing; Optimization ofmold design
独创性声明
本人声明所呈交的学位论文是本人在导师指导下进行的研究工作和取得 的研究成果,除了文中特别加以标注和致谢之处外,论文中不包含其他人已经
the fields of metallurgy,mechanical engineering,national defence and aviation.Die pressing process and cold isostatie pressing process are the important methods of making ceramic parts.Die pressing method is mainly used to produce thin ceramic components.However,the structure of the compact produced by die pressing process is obviously inhomogeneous as the applied pressure is restricted in the axial Orientafion.Many Large and complicated components Call be made by cold isostatic pressing process,and the dens畸of the compact is more uniform than the one obtained by die pressing.Finite element simulation of the pressing process is the effective method to optimize the rubber mould design process,improve the product quality,heighten the e佑ciency and reduce the number of increasing trial and error cycles used in current industrial practice.
陶瓷机械技术装备行业发展探讨
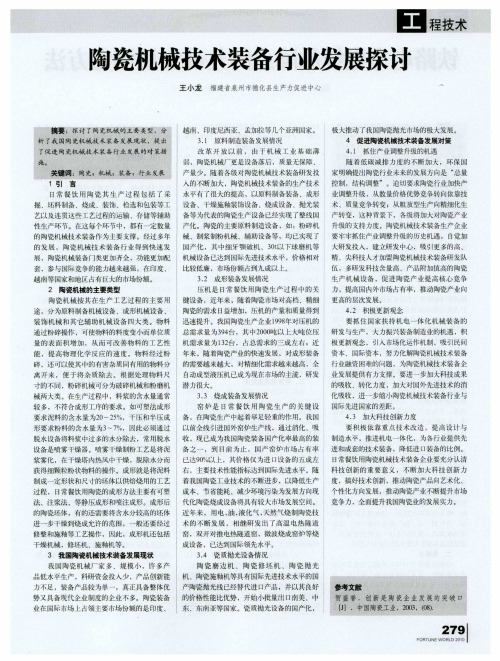
掘 、坯料 制备、烧 成 、装饰 、检选和包装 等工 设备 、干燥施釉装 饰设 备、烧 成设备 、抛光装 术 、质量竞 争转变 ;从粗 放型生 产向精 细化生
艺以 及连 贯这些工艺过程的运输 、存储 等辅助 备等为代表的陶瓷生产 设备已经实现 了整线国 产转变 ,这 种背景 下,各级将 加大对 陶瓷产业
33 烧成装备 发展情 况 . 备,在陶瓷生产中起着举足轻重的作用 。我国 以前 全线引进国外窑炉生产线 ,通过消化 、吸
窑 炉 是 日常 餐 饮 用 陶 瓷 生 产 的关 键 设 国际先进国家的差距。
脱水设备将料浆 中过 多的 水分除去 ,常用脱水 j收 ,现 已成为我国陶瓷装备 国产化率最 高的 装 制造水平 ,推进机 电一体化 ,为各行业提供先
1引 言
产量少。随着各级 对陶瓷机械技 术装备研发投 家 明确提 出陶瓷行业未 来的发展方向是 “ 量 总 入的不断加大 ,陶瓷机械技 术装备的生产技术 控制 ,结构 调整”。迫 切要求 陶瓷行 业加快 产
日常 餐饮 用 陶 瓷 其 生 产 过 程 包 括 了采 水平有 了很大的提 高,以原料 制备装备 、成形 业调 整升级 ,从数量价格 优势 竞争转 向依靠技
弱 ,陶瓷机械厂更是 设备落后 ,质量无保障 、
极 大推 动了我国陶瓷抛光 市场的极大发展 。
4 促进陶瓷机 械技 术装备 发展对策
4 1 抓 住产业调整升级的机遇 . 随 着 低碳减 排力 度的 不断加 大 ,环保 国
了促 进陶 瓷机械技术装备行业 发展 的对 蓑措
㈠
施。
关键调:陶瓷;机械I装备;行业发 展
我 国陶瓷机 械 厂家 多 、规 模 小 ,许 多产 f
品低水平生产 ,科研资金投 入少,产品创新能 机 、陶瓷施釉机等具 有国际先进技术水平的 国 力不足 ,装备产品较为单一 ,真正具 备整体优 产陶瓷抛光线 已经替代进 口产品 ,并以其 良好 : 1 势 又具 备现代企业制度的 业不 多。陶瓷装备 的价格性能 比优势 ,开始小批量出 t南美 、中
陶瓷成型机械-滚压成型机
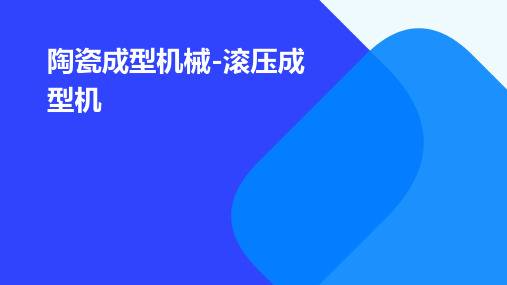
02
滚压成型机在陶瓷行业 的应用
滚压成型机在陶瓷行业的适用范围
适用于各种陶瓷制品 的成型,如餐具、厨 具、卫生洁具等。
适用于大规模生产, 提高生产效率和降低 成本。
可生产各种规格和形 状的陶瓷制品,满足 不同市场需求。
滚压成型机在陶瓷行业的应用优势
滚压成型机采用先进的滚压技术,可 实现高精度、高效率的陶瓷制品成型。
滚压成型机的售后服务及维修保养
厂家A
提供全面的售后服务,包括设备 安装、调试、培训和维修保养等, 确保客户使用无忧。
厂家B
重视客户体验,提供24小时在线 客服和免费的技术支持,定期回 访客户了解使用情况。
厂家C
提供专业的维修保养服务,定期 对设备进行全面检查和保养,确 保设备长期稳定运行。
滚压成型机的价格及性价比分析
价格对比
不同厂家的滚压成型机价格存在 差异,其中厂家A和厂家C的价格 相对较高,而厂家B的价格较为亲 民。
性价比分析
综合考虑产品品质、售后服务和 价格等方面,厂家A和厂家C的滚 压成型机性价比较高,而厂家B的 产品在价格和性能上相对均衡。
THANKS FOR WATCHING
感谢您的观看
电机功率:55KW
最大压力:2000KN 适用模具直径:300-1200mm
滚压成型机的操作和维护
操作注意事项
开机前检查各部件是否正常,确保机 器在良好状态下运行;操作过程中严 禁超负荷运行;定期检查油路、油位 及密封件,及时处理异常情况。
维护保养
定期清洗油箱、更换润滑油;检查主 轴轴承、曲轴及各运动副的磨损情况 ,及时维修或更换;定期检查电气元 件,确保电气系统正常工作。
滚压成型机可大幅减少材料浪费,降 低生产成本,同时减少环境污染。
陶瓷材料成型方法

陶瓷材料成型方法
陶瓷材料的成型方法有多种,以下是三种主要的方法:
1. 可塑法成型:在外力作用下,使具有可塑性的坯料发生塑性变形而制成坯体的方法。
具体分为手工成形和机械成形两大类。
手工成形如雕塑、印坯、拉坯、手捏等,多用于艺术陶瓷的制造。
而机械成形如旋压和滚压成形,则多用于盘、碗、杯碟等制品的生产。
此外,还有其他陶瓷工业中采用的挤制、车坯、压制、轧膜等可塑成形方法。
2. 注浆法成型:利用多孔模型的吸水性,将泥浆注入其中而成形的方法。
这种成形方法适应性强,凡是形状复杂,不规则的薄壁、厚胎、体积较大且尺寸要求不严的制品都可用注浆法成型。
例如日用陶瓷中的花瓶、汤碗、椭圆形盘、茶壶手柄等都可采用注浆法成型。
3. 压制法成型:利用压力将置于模具内的粉料压紧至结构紧密,成为具有一定形状和尺寸的坯体的成形方法。
此外,还有其他的成型方法,如干压成型、等静压成型等,可以根据不同的需求选择合适的成型方法。
工艺学实验报告 - 干压成型制作陶瓷片
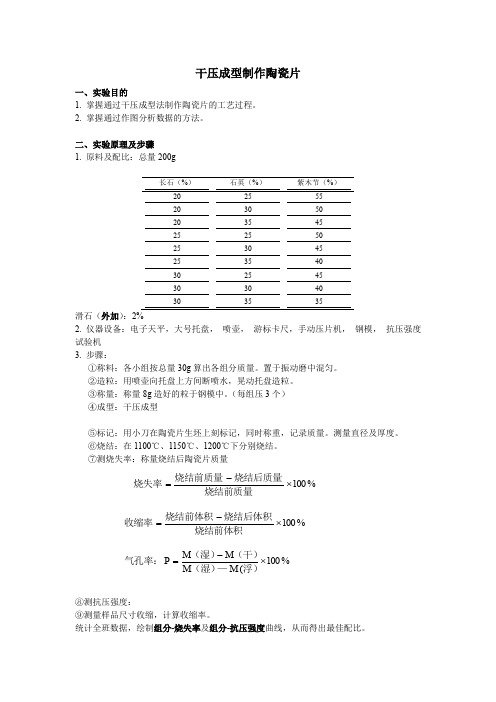
干压成型制作陶瓷片一、实验目的1. 掌握通过干压成型法制作陶瓷片的工艺过程。
2. 掌握通过作图分析数据的方法。
二、实验原理及步骤1. 原料及配比:总量200g长石(%)石英(%) 紫木节(%) 20 25 55 20 30 50 20 35 45 25 25 50 25 30 45 25 35 40 30 25 45 30 30 40 滑石(外加):2%2. 仪器设备:电子天平,大号托盘, 喷壶, 游标卡尺,手动压片机, 钢模, 抗压强度试验机3. 步骤:①称料:各小组按总量30g 算出各组分质量。
置于振动磨中混匀。
②造粒:用喷壶向托盘上方间断喷水,晃动托盘造粒。
③称量:称量8g 造好的粒于钢模中。
(每组压3个)④成型:干压成型⑤标记:用小刀在陶瓷片生坯上刻标记,同时称重,记录质量。
测量直径及厚度。
⑥烧结:在1100℃、1150℃、1200℃下分别烧结。
⑦测烧失率:称量烧结后陶瓷片质量%100⨯-=烧结前质量烧结后质量烧结前质量烧失率 %100⨯-=烧结前体积烧结后体积烧结前体积收缩率 %100(⨯-=浮)—(湿)(干)(湿)气孔率:M M M M P⑧测抗压强度:⑨测量样品尺寸收缩,计算收缩率。
统计全班数据,绘制组分-烧失率及组分-抗压强度曲线,从而得出最佳配比。
三、实验总结实验数据记录如下:在1000℃下烧结得到的数据及图形在1150℃下烧结的数据及图形在1200℃下烧结的数据及图形结论:通过以上数据分析可得出:当在1000摄氏度时,8—1配比下所得的样品抗压强度较好,烧失率和收缩率比较低;在1150摄氏度下,5—2配比时所得的配比好;在1200摄氏度时,7—3下配比好。
误差分析:(1)由于在制料的过程中操作错误而导致误差(2)在烧结的过程中由于不同温度下导致受热不均匀程度不同导致误差(3)在称量读数时不准确导致误差体会:本次试验中,通过干压成型法制作陶瓷片加深了我对这一制作工艺流程了解与认识,在实验过程中,经历了配料、造粒、成型和烧结这几个步骤,每个步骤都需要仔细准确操作,对于不懂的地方时刻向学长请教,其中,喷水量的多少一定要掌握好,否则,对成型颗粒结果影响很大;除此之外,在压片过程中也要把我好压力适度,压力过大或者过小都会影响成形结果,当压好从模具里脱模时也要小心,因为陶瓷片还没经过烧结,强度很低,不小心就容易损坏;最后,我明白了要作为一个合格的研究科研人员,必须具备细心、耐心等态度,对待科学是需要严谨的,只有这样才能在将来的学术上出很好的成果。
陶瓷材料成型
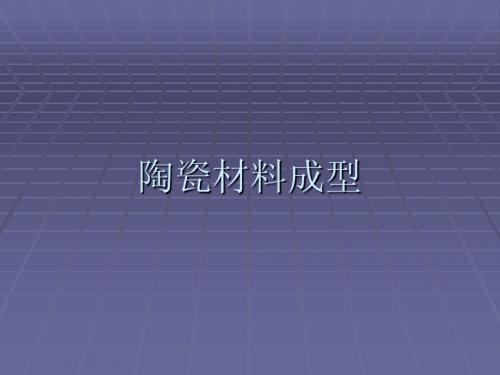
干燥基本理论知识
干燥基本原理 干燥定义:排出坯体中水分的工艺过程称为干燥。 坯体中所含水分的类型及其结合形式 1、化学结合水:物料矿物分子组成内的水分。又 称结构水。干燥过程中不能除去。 2、吸附水:物料内存在很多毛细管,存在其内的 即为吸附水。 3、自由水:存在于物料表面的润湿水分以及孔隙 中的水分。
排除吸附水时,不发生收缩,不产生应力。
干燥基本理论知识
干燥的过程 干燥可以分为四个阶段: 升温阶段:含水率下降、干燥速度上升、坯体表
面温度上升。 等速干燥阶段:含水率下降、干燥速度不变、坯 体表面温度不变。 降速干燥阶段:含水率下降、干燥速度下降、坯 体表面温度上升。 平衡阶段:含水率不变、干燥速度为零。
一车间压制工段部分技术参数
1、粉料过筛:10目 2、粉料水分:6.3~6.8% 两个仓以上混合使用 3、压制参数 3.1平面立体:凹凸面 坯重:1160±20g 厚度:8.1~8.2 mm 压力:280bar 3.2文化石: 坯重:1420±20g 厚度:5.5 mm 压力:250bar 3.3树皮纹: 坯重:1500±20g 厚度:10.3~10.颗粒之间以及颗粒与模壁 之间产生摩擦力,摩擦力的不均匀分布导致坯体 中压力分布不均匀。
陶瓷材料成型
影响坯体致密度的因素
一、成型压力 施加于粉料上的压力主要消耗在克服粉料的阻 力以及克服颗粒对模壁的摩擦力,所以成型压力 的确定要依据粉料的组成和性质以及坯体的大小 和形状。 二、加压方式 2.1 加压有单面加压、双面同时加压、双面先后 加压和六面加压等几种方式。在墙地砖生产中应 用前三种方式。
坯体强度的变化
在坯体压制过程中坯体强度与压制力呈现规 律变化。压制力较小会使坯体强度不够,压制力 过大会造成动力浪费。
干压成型

6.干压成型坯体性能的影响因素 干压成型坯体性能的影响因素
1. 粉体的性质,包括粒度、粒度分布、形状、含水 率等。 2. 添加剂特性及使用效果。好的添加剂可以提高粉 体的流动性、填充密度和分布的均匀程度,从而提 高坯体的成型性能。 3. 压制过程中的压力、加压方式和加压速度,一般 地说,压力越大坯体密度越大,双向加压性能优于 单向加压,同时加压速度、保压时间、卸压速度等 都对坯体性能也有较大影响。
2.干压成型基本原理
首先,通过加入一定量的表面活性剂, 改变粉体表面性质,包括改变颗粒表面吸附 性能,改变粉体颗粒形状,从而减少超细粉 的团聚效应,使之均匀分布;加入润滑剂减 少颗粒之间及颗粒与模具表面的摩擦;加入 黏合剂增强粉料的粘结强度。将粉体进行上 述预处理后装入模具,用压机或专用干压成 型机以一定压力和压制方式使粉料成为致密 坯体。
3.干压成型的添加剂
在干压成型的粉末中,往往要加入一定种类和数量的 添加物,促进成型过程顺利进行,提高坯体的密度和强度, 减少密度分布不均的现象。添加物有如下几个作用: 1)减少粉料颗粒之间及粉料与模壁间的摩擦,因此所加入的添 加剂又叫润滑剂 2)增加粉料颗粒之间的粘结作用,这类添加剂又叫粘合剂 3)促进粉料颗粒吸附、湿润或变形,这类添加剂属表面活性物 质 在干压成型中采用的添加剂,最好是在烧成过程中尽可 能地烧掉,故不会影响产品的性能;添加剂与粉粒最好不发 生化学反应;添加剂的分散性要好,少量使用便能得到良好 的效果。
1.干压成型简介
干压成型又称模压成型,是将粉料填充 到模具内部后,通过单向或双向加压,将粉 料压成所需形状。这种方法这种方法操作简 便,生产效率高,易于自动化,是常用的方 法之一,但干压成型时粉料容易团聚,坯体 厚度大时内部密度不均匀,制品形状可控精 度差,且对模具质量要求高,复杂形状的部 件模具设计较困难。
陶瓷生产工艺设备
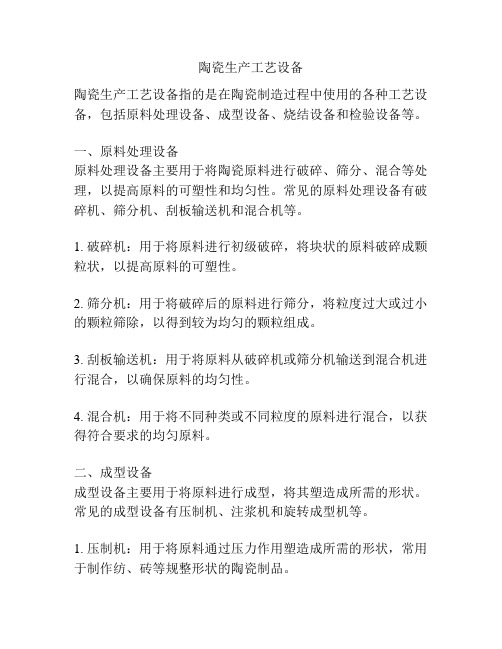
陶瓷生产工艺设备陶瓷生产工艺设备指的是在陶瓷制造过程中使用的各种工艺设备,包括原料处理设备、成型设备、烧结设备和检验设备等。
一、原料处理设备原料处理设备主要用于将陶瓷原料进行破碎、筛分、混合等处理,以提高原料的可塑性和均匀性。
常见的原料处理设备有破碎机、筛分机、刮板输送机和混合机等。
1. 破碎机:用于将原料进行初级破碎,将块状的原料破碎成颗粒状,以提高原料的可塑性。
2. 筛分机:用于将破碎后的原料进行筛分,将粒度过大或过小的颗粒筛除,以得到较为均匀的颗粒组成。
3. 刮板输送机:用于将原料从破碎机或筛分机输送到混合机进行混合,以确保原料的均匀性。
4. 混合机:用于将不同种类或不同粒度的原料进行混合,以获得符合要求的均匀原料。
二、成型设备成型设备主要用于将原料进行成型,将其塑造成所需的形状。
常见的成型设备有压制机、注浆机和旋转成型机等。
1. 压制机:用于将原料通过压力作用塑造成所需的形状,常用于制作纺、砖等规整形状的陶瓷制品。
2. 注浆机:将原料制成浆料后,通过注入浆料到模具中,使其在模具中形成所需的形状,常用于制作瓷砖等平面形状的陶瓷制品。
3. 旋转成型机:将原料制成浆料后,将浆料注入旋转成型机中的模具中,通过旋转使浆料均匀分布,并在模具内形成所需的形状,常用于制作坯体较大的陶瓷制品,如盆、碗等。
三、烧结设备烧结设备主要用于将成型后的陶瓷制品进行高温烧结,使其形成致密的结构。
常见的烧结设备有窑炉、烧结炉和烧结机等。
1. 窑炉:用于将成型后的陶瓷制品进行整体烧结,常用于陶瓷制品的初次烧结。
2. 烧结炉:用于将初次烧结的陶瓷制品进行二次烧结,以提高其致密度和耐火性能。
3. 烧结机:用于将陶瓷颗粒进行快速烧结,并使其形成致密的结构,常用于制作陶瓷砖等小型陶瓷制品。
四、检验设备检验设备主要用于对成品进行质量检验,以确保产品符合质量要求。
常见的检验设备有压力试验机、硬度计、显微镜等。
1. 压力试验机:用于对陶瓷制品进行压力或弯曲强度的测试,以评估其力学性能。
陶瓷成型工艺

陶瓷成型工艺一、干压成型干压成型又称模压成型,是最常用的成型方法之一,也是手机陶瓷背板主流的成型工艺之一,小米MIX系列的陶瓷后盖都是干压成型的。
干压成型是将经过造粒、流动性好,颗粒级配合适的粉料,装入金属模腔内,通过压头施加压力,压头在模腔内位移,传递压力,使模腔内粉体颗粒重排变形而被压实,形成具有一定强度和形状的陶瓷素坯。
图单向和双向加压时压坯密度沿高度的分布,(a)单向加压,(b)双向加压二、流延成型流延成型(tepe-casting)又称为刮刀成型。
它的基本原理是将具有合适黏度和良好分散性的陶瓷浆料从流延机浆料槽刀口处流至基带上,通过基带与刮刀的相对运动使浆料铺展,在表面张力的作用下形成具有光滑上表面的坯膜,坯膜的厚度主要由刮刀与基带之间间隙来调控。
坯膜随基带进入烘干室,溶剂蒸发有机黏结剂在陶瓷颗粒间形成网络结构,形成具有一定强度和柔韧性的坯片,干燥的坯片与基带剥离后卷轴待用。
然后可安所需形状切割,冲片或打孔,最后经过烧结得到成品。
流延成型工艺可以分为非水基流延成型、水基流延成型、凝胶流延成型等。
流延成型制备陶瓷基片工艺包括浆料制备、流延成型、干燥、脱脂、烧结等工序,其中最关键的是浆料的制备和流延工艺的控制。
图流延成型法制备陶瓷基片的工艺流程图三、注射成型陶瓷注射成型(ceramic injection molding,CIM),是将聚合物注射成型方法与陶瓷制备工艺相结合而发展起来的一种制备陶瓷零部件的新工艺。
陶瓷注射成型的制造过程主要包括四个环节:(1)注射喂料的制备:将合适的有机载体与陶瓷粉末在一定温度下混炼、干燥、造粒,得到注射用喂料;(2)注射成型:混炼后的注射混合料于注射成型机内被加热转变为粘稠性熔体,在一定的温度和压力下高速注入金属模具内,冷却固化为所需形状的坯体,然后脱模;(3)脱脂:通过加热或其它物理化学方法,将注射成型坯体内的有机物排除;(4)烧结:将脱脂后的陶瓷素坯在高温下致密化烧结,获得所需外观形状、尺寸精度和显微结构的致密陶瓷部件。
陶瓷PPT课件

陶瓷的典型组织结构:晶体相、玻璃相和气相
陶瓷的组织示意图
陶瓷材料的相组成
晶体相
晶体相是陶瓷材料最主要的组成相,主要是某些固溶体 或化合物,其结构、形态、数量及分布决定了陶瓷材料 的特性和应用。晶体相又分为主晶相、次晶相和第三相。 陶瓷中晶体相主要有含氧酸盐(硅酸盐、钛酸盐等)、氧 化物(MgO、Al2O3)、非氧化物(SiC,Si3N4)等。
彩陶双连壶
仰韶文化时期陶器 1972年河南省郑州市大河村出土
山东历城县龙山镇出现了“黑陶”。所以这个时期称为“龙山文化”时 期,又称“黑陶文化”。龙山黑陶在烧制技术上有了显著进步,它广泛采用 了轮制技术,因此,器形浑圆端正,器壁薄而均匀,将黑陶制品表面打磨光 滑,乌黑发亮,薄如蛋壳,厚度仅1mm,人称“蛋壳陶”。
中国陶瓷珍品之清青花
景德镇传统名瓷之一的薄胎瓷
景德镇传统名瓷之一的雕塑瓷
景德镇传统名瓷之 一的粉彩瓷
景德镇传统名瓷 景德镇传统名瓷
之一的玲珑瓷
之一的青花瓷
我国的陶瓷发展经历了三个阶段,取得三个重大突破: 三个阶段:a. 陶器
b. 原始瓷器(过渡阶段) c. 瓷器 三个重大突破:a. 原料的选择和精制
再次,陶瓷又是一个原料来源丰富,传统技艺悠久,具有坚硬、 耐用及一系列优良性质的材料,在建筑、电力、电子、化学、冶金 工业等,甚至农业和农产品加工中都大量应用。
最后,随着现代科学技术的飞速发展,使得具有优良性能的特 种陶瓷得到了广泛应用。
一、 陶瓷的分类
2.1 陶瓷材料的分类和制备工 艺
1.按陶瓷概念和用途来分类
• 泥浆稳定性表示在不搅拌时,泥浆长时间保持 稳定,不产生沉淀或分层的性能。
• 配料就是按陶瓷材料的组成,将所需各种原料 进行称量。
陶瓷粉体干压成型中坯体开裂问题
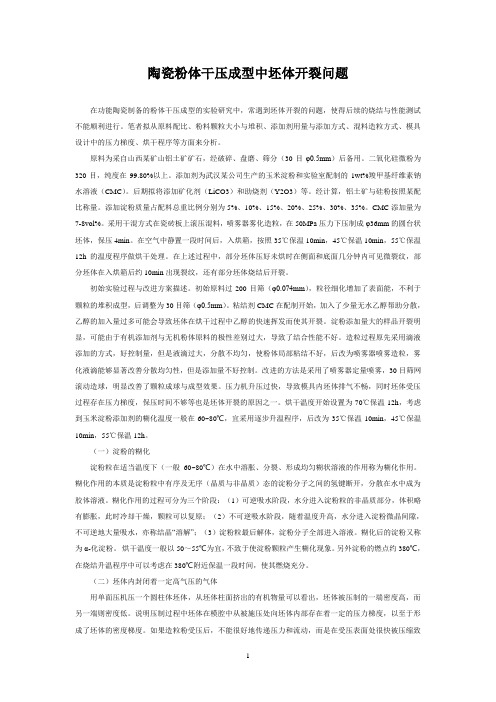
陶瓷粉体干压成型中坯体开裂问题在功能陶瓷制备的粉体干压成型的实验研究中,常遇到坯体开裂的问题,使得后续的烧结与性能测试不能顺利进行。
笔者拟从原料配比、粉料颗粒大小与堆积、添加剂用量与添加方式、混料造粒方式、模具设计中的压力梯度、烘干程序等方面来分析。
原料为采自山西某矿山铝土矿矿石,经破碎、盘磨、筛分(30目φ0.5mm)后备用。
二氧化硅微粉为320目,纯度在99.80%以上。
添加剂为武汉某公司生产的玉米淀粉和实验室配制的1wt%羧甲基纤维素钠水溶液(CMC)。
后期拟将添加矿化剂(LiCO3)和助烧剂(Y2O3)等。
经计算,铝土矿与硅粉按照某配比称量。
添加淀粉质量占配料总重比例分别为5%、10%、15%、20%、25%、30%、35%。
CMC添加量为7-8vol%。
采用干混方式在瓷砖板上滚压混料,喷雾器雾化造粒,在50MPa压力下压制成φ36mm的圆台状坯体,保压4min。
在空气中静置一段时间后,入烘箱,按照35℃保温10min,45℃保温10min,55℃保温12h的温度程序做烘干处理。
在上述过程中,部分坯体压好未烘时在侧面和底面几分钟内可见微裂纹,部分坯体在入烘箱后约10min出现裂纹,还有部分坯体烧结后开裂。
初始实验过程与改进方案描述。
初始原料过200目筛(φ0.074mm),粒径细化增加了表面能,不利于颗粒的堆积成型,后调整为30目筛(φ0.5mm)。
粘结剂CMC在配制开始,加入了少量无水乙醇帮助分散,乙醇的加入量过多可能会导致坯体在烘干过程中乙醇的快速挥发而使其开裂。
淀粉添加量大的样品开裂明显,可能由于有机添加剂与无机粉体原料的极性差别过大,导致了结合性能不好。
造粒过程原先采用滴液添加的方式,好控制量,但是液滴过大,分散不均匀,使粉体局部粘结不好,后改为喷雾器喷雾造粒,雾化液滴能够显著改善分散均匀性,但是添加量不好控制。
改进的方法是采用了喷雾器定量喷雾,30目筛网滚动造球,明显改善了颗粒成球与成型效果。
陶瓷设备习题

陶瓷设备习题绪论1-我国陶瓷机械设备发展分为哪三个阶段?(1)传统作坊式⽣产时期:古代---20世纪40到60年代.特点:简单\⼿⼯操作.(2)近代⽣产时期:60到80年代;特点:机械化、单机为主、简单连动⽣产线。
(3)现代⽣产时期:80年代到现在;特点:系列引进国外先进⽣产机械、并国产化。
特点:机械化、⾃动化⽔平⾼。
2-现代陶瓷机械设备有什么特点?(1)⼴泛采⽤现代科技成果;(2)具有很强的⼯艺适应性:(3)具有⾼的耐磨性、耐久性、可靠性、可调性。
(4)随着产品增多、⼯艺过程的复杂,机械设备种类繁多,品种及规格逐渐趋于标准化、系列化。
(5)随机械化、⾃动化程度的提⾼,机械设备成为陶瓷企业投资的主体,直接影响企业效益。
3-简述陶瓷⽣产的⼯艺流程。
第⼀章粉碎机械1-什么叫粉碎?⽤机械的⽅法克服固体物料内部凝聚⼒⽽将其分裂的操作称为粉碎。
2-粉碎⼜可细分为⼏种?这是根据什么标准分的?粉碎分为破碎、粉磨。
破碎分为粗碎、中碎、细碎。
粉磨分为粗磨、细磨、超细磨。
按粉碎后物料的尺⼨范围来划分。
3-对陶瓷⼯业来说,粉碎有什么意义?(1)使物料的粒度变⼩、体表⾯积增加,改善⽆聊的⼯艺性能;(2)对不同组分的物料,混合的均匀程度增加;(3)有利于除杂。
4-机械粉碎⽅法有哪⼏种?挤压、碰击、研磨、劈裂。
1-⼲压成型的条件是什么?1)具有封闭空间(不是密闭)的模型模腔;2)此空间可在外⼒的作⽤下改变容积;3)此空间可提供粉料填⼊,空⽓排出及坯体移出的通道;4)有⾜够的成型压⼒。
1-在压制过程中物料结构发⽣了哪些变化?1)假颗粒变成真颗粒,弹性变形到塑性变形,颗粒相互移动靠拢;2)真颗粒由弹性到塑性变形是致密的过程,⽓体继续排出,颗粒移动变形,⽓孔率进⼀步降低。
7-分析压制成型坯体中致密度不均匀的原因。
原因:坯体中的压⼒消耗不同,表现在四个⽅⾯:1)克服颗粒间的摩擦⼒:2)克服颗粒于模型内壁间的摩擦⼒:3)变形;4)空⽓阻⼒。
陶瓷成型工艺原理及方法
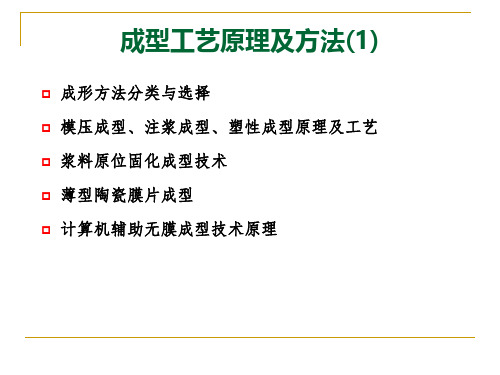
干压成型设备
注浆成型
(1)石膏模注浆成型 利用石膏吸水性的一种成形方法。其过程: (水+粉料)倒入事先制作
好、吸水性很强的石膏模中,浆料中之水分向石膏模壁渗透,因而浆料 便沿石膏模壁固化。到一定厚度后,可倾出剩余浆料。
对注浆成型所用的料浆,必须具备以下性能: 流动性和稳定性好(不易分层和沉淀)、触变性要小、含水量尽
加压方式与压力分布
单向加压 一端加压,受压面密度大,未加压端密度小
双向加压:坯体两边受压,两端密度大,中间密度小 改进的双向加压:
(1) 先上加压,后下加压 (2) 加润滑剂并造粒
模压成型工艺参数控制及特点
➢ 成型压力 取决于坯体的形状、高度、粘合剂种类与用量、粉体的流动性、
坯体的致密度 ➢ 加压速度与保压时间
从工艺上来讲,根据坯料的性能和含水量的不同,陶瓷的成型方 法可分为三类:注浆成型、可塑成型和压制成型
成型 方法
成型方法分类
注浆成型法
热法(热压铸法):钢模
冷法
常压冷法注浆 加压冷法注浆 抽真空冷法注浆
石膏模
坯料含水量 30%~40%
有模 可塑成型法 无模
坯料含水量18%~26%
干压成型法:使用钢模,坯料含水量6%~8% 等静压成型法:使用橡皮模,坯料含水量1.5%~3%
4. 加热装置
5.9阀门
6. 活塞
7. 模具
8. 温度计
10.脚控踏板 11. 压缩空气进口
蜡浆制备
熟瓷粉 石蜡 硬脂酸
预热
60~80℃
熔化
12成腊饼存放
要点1: 热压铸成型必须用熟料,目的: (1) 保证铸浆有良好的 流动性;(2) 减少坯体的收缩率和变形。 要点2: 石蜡是亲油而憎水的, 而瓷粉与油之间缺乏很大的亲和 力,需加入硬脂酸或油酸一类两性物质。
陶瓷压机工作原理

陶瓷压机工作原理
陶瓷压机是一种用于陶瓷制品成型的机械设备,其工作原理基本可分为两个阶段:填充料料的装填及压制成形。
首先,在填充料料的装填阶段,陶瓷压机将粉状的陶瓷料填充至特定位置的料仓或模具中。
填充料通常是由陶瓷粉末和其他添加剂组成的混合物。
填充料的填充过程中,通常会使用辅助设备如料斗、输送带等辅助装置来实现自动化装填或者手工装填。
接着,在压制成形阶段,陶瓷压机会施加一定的压力来将填充料压制成所需形状。
常见的压制方式包括静压和动压两种。
静压是指通过施加持续的压力,使填充料在模具内静止不动,从而实现成形。
动压则是在静压的基础上,通过模具或制件的运动来加速成形过程。
一旦完成了压制成形过程,模具就会打开,成型的陶瓷制品可以取出,经过后续的烧结等工艺步骤进行加工和处理。
需要注意的是,陶瓷压机的工作原理可能根据具体的设备和应用而有所不同。
例如,一些陶瓷压机可能采用液压或气动系统来提供压力,而其他可能采用机械手臂或自动化控制系统来实现更高效的生产。
因此,在实际操作中,会根据具体的工艺要求来选择不同的陶瓷压机,以满足不同制品的成型需求。
08陶瓷成型工艺

第21章陶瓷成型工艺成型方法的选择,首先取决于原料的性质,其次取决于制品的形状和大小。
陶瓷粉末首先经过预处理,然后再成型。
§21.1 预处理21.1.1 配料配料是陶瓷工艺中一道最基本的工序,必须认真对待。
有两个地方需要配料,其一是在原料烧块合成之前,其二是在成形之前。
21.1.2 混合一、加料次序问题二、加料方法问题三、湿磨瓷料的分层问题四、球磨筒专用的问题21.1.3 造粒所谓造粒,就是将已经磨得很细的粉料,混和进粘结剂后,做成流动性好的较祖的粒子(这个粒子还是很小的,约20~80目)。
为了区别于粉料的原始粒子,我们把它叫做团粒。
这道工序对批量生产来说是非常重要的。
造粒的方法,目前常用的有三种,即普通造粒法,加压造粒法与喷雾干燥法。
所谓团粒的质量,最基本的是团粒的体积密度和堆集密度。
21.1.4 塑化一、塑化剂所谓可塑性就是指瓷料在外力作用下发生形变,但又不出现裂纹,当外力去除后,瓷料维持既得的形状的能力。
使瓷料具有这种能力的物质也就叫做塑化剂。
塑化剂共分两大类:一类是无机的(粘土类矿物),一类是有机的(高分子化合物)。
1.聚乙烯醇2.聚醋酸乙烯酯3.羧甲基纤维素4.石蜡二、塑化工艺有机塑化剂是一种水溶液(当然,也有不含水的,如石蜡),它是由粘结剂、增塑剂和溶剂组成的,在使用前先要配制。
粘结剂的作用是把粉料粘结在一起,通常用有机高分子化合物,如前面提到的聚乙烯醇、聚醋酸乙烯酯、羧甲基纤维素、糊精等。
它们都是粉末状的,要溶解后才能使用。
增塑剂是对水有良好的亲和力并能溶于水的有机化合物。
它的作用是插入线性的高分子之间,增大高分子间的距离,以降低它的粘度。
常用的为甘油。
溶剂是用来溶解上面两种有机化合物的,分子结构应与它们相似。
常用的有水、无水酒精(乙醇)、丙酮、苯等。
有机塑化剂的调配要在加热的情况下进行,同时还要不断搅拌使充分溶解。
这里以聚乙烯醇塑化剂的调配为例,说明如下:以压电瓷料的配方为例。
实验 陶瓷坯体的干压成形
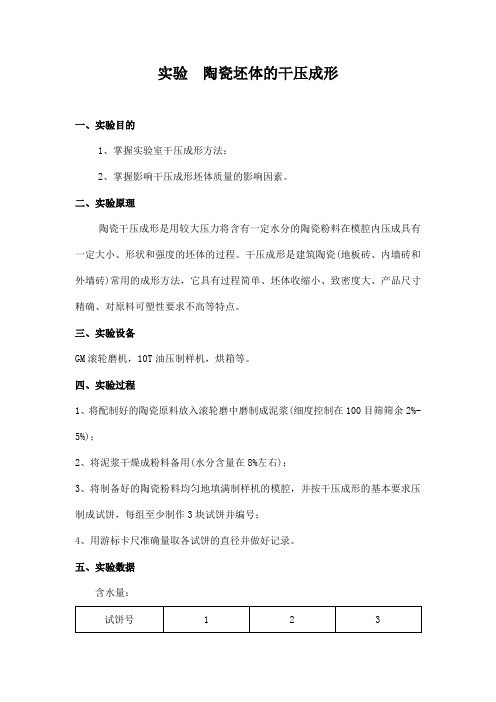
实验陶瓷坯体的干压成形
一、实验目的
1、掌握实验室干压成形方法;
2、掌握影响干压成形坯体质量的影响因素。
二、实验原理
陶瓷干压成形是用较大压力将含有一定水分的陶瓷粉料在模腔内压成具有一定大小、形状和强度的坯体的过程。
干压成形是建筑陶瓷(地板砖、内墙砖和外墙砖)常用的成形方法,它具有过程简单、坯体收缩小、致密度大、产品尺寸精确、对原料可塑性要求不高等特点。
三、实验设备
GM滚轮磨机,10T油压制样机,烘箱等。
四、实验过程
1、将配制好的陶瓷原料放入滚轮磨中磨制成泥浆(细度控制在100目筛筛余2%-5%);
2、将泥浆干燥成粉料备用(水分含量在8%左右);
3、将制备好的陶瓷粉料均匀地填满制样机的模腔,并按干压成形的基本要求压制成试饼,每组至少制作3块试饼并编号;
4、用游标卡尺准确量取各试饼的直径并做好记录。
五、实验数据
含水量:
六、实验分析
讨论分析影响陶瓷干压成形坯体性质的因素。