汽车灯罩外壳注塑件模流分析
零件盖模流分析和注塑模具设计

零件盖模流分析和注塑模具设计摘要:以汽车零件盖为例,零件盖模具设计采用三维绘图软件UGNX制作。
可以全面实行智能化全3D模具设计。
通过使用Moldflow软件,可以预先分析模具溶液的流动、固化过程及冷却时间等情况,以确认方案的可行性,并利用UG三维软件全3D把模具设计出来,再次利用UG软件导出二维功能转二维图纸的功能,使用二维计算机软件CAD绘制出所需要的图纸,使得模具制造、调试及返工的时间大大减少,从而提高产品的质量。
关键词:Moldflow;注塑成型;模流分析;翘曲变形模具行业是走在各个行业前列的行业,同时重视经验的产业,随着工业的迅速发展,塑料制品也日益被广泛应用。
而现在,企业不仅仅只依赖于人工经验来设计模具,更多地采用注塑模流分析技术,以更好的预先分析模具的设计合理性,减少试模次数,加快产品研发,提升企业效率。
Moldflow这款专业的模拟注塑过程的软件,可模拟整个注塑过程。
为了优化塑料产品的设计、生产和质量,我们将对影响进行分析、评估和优化,从而在模具制造前提供有效的解决方案,以帮助技术人员完成整个流程中的关键点优化工作。
本文以汽车零件盖结构特点,通过CAE软件以Moldflow为载体,对产品的浇注系统,冷却系统的成型过程,进行分析优化。
并在此基础上,利用UG 软件完成产品的模具设计。
1 产品模具与结构分析汽车零件盖为汽车零件中常见的塑料件,采用UG NX软件三维建模,如图1、图2所示,还未设置材料收缩的零件外形尺寸是30mm×30mm×15 mm,2mm是产品零件的平均厚度,1.5mm 和 0.3 mm分别是最大和最小厚度,产品结构较为简易,经测试评估后可采取顶杆顶出推出。
产品为零件上盖,注塑零件表面的质量要求很高,产品外表颜色需要均匀,绝对不允许有任何的披风、刺毛、局部塌陷等现象,材料为ABS材料,这种材料的收缩率是1.006。
采用一模两腔布置模腔。
(a)反面(b)正面图1汽车零件盖2 Moldflow 模流分析在Moldflow中进行产品优化分析的过程中,前处理十分重要,为了确保分析的准确性,模型的质量也十分重要。
汽车内外饰高光注塑件产品分析

制品表面高光免喷涂, 无溶解线,流痕等缺陷
3. 产品初步分析说明
2021/8/7
目标产品高光分析
* 目标产品描述 * PMMA+ASA材料属于高温材料材料范畴 * 1模1穴
2021/8/7
1.
10.
0
0
2021/8/7
筋位分布厚薄不均,材料流动保压均需较大 压力,部分区域会出现保压不足缺陷,建议 多浇口射出,减小材料流长
2. 前端格栅产品重点是网孔多.壁厚不均.弧面结构.高低不平----难点是怎 样让冷热交变温度恒定/均匀/持续到达模具高光表面。 3. 蒸汽设备与注塑机的安装调试匹配相当重要。
4. 蒸汽设备与模具蒸汽通道/模具结构设置是否合理,是关乎项目成功的 关键。前期的模流分析至关重要,分析时必须带入材料/水道等精确 判断后期产品结构导致的问题,避免后期更改造成被动。
注:此项目的开发具有一定难度且风险,但如果各环节把控好是相对可控的
2021/8/7
注:鉴于产品结构与模具要求高,前期必须开一套产品比例缩小3倍左 右的实验模具(软模),验证交表温度/溶解痕等结果,以决定最佳温 度与模具蒸汽通道位置大小后等,然后正式开硬模。
2021/8/7
。
一、模具钢材的选用:
通过对该产品的分析,需要选用较好的易切削性和抗腐蚀性,抛光性极 佳,采用特殊溶解方法,得到极高洁净度,及优良的镜面效果。另需要承 受模具温度长期冷热交表而不出现任何变形,裂纹等要求的钢材,预硬高 达HCR40,无须再热处理,能够降低模具制作周期。单从钢材本身来讲它 的价格高于其他钢材的价格,但是从长远的角度来看能降低多项成本。
2021/8/7
三.水路蒸汽示意图:
Φ8mm
Moldflow DOE分析车灯案例分享

Conclusion and suggestions(结论及建议)
结论:
通过DOE分析可以看到,产品变形随着保压时间和压力增大 有明显下降,变形有明显的改善,因此建议试模人员在设置 参数时注意这两项的设置。
建议:
注塑时适当使用较大的保压压力和保压时间, 另外从流动模式看中间有滞流,建议调整壁厚
PLASTICS LABS
背景介绍(正交)
现已知有3个工艺参数(注塑时间-A,融料温度-B,冷却时间-C),会对制品 翘曲(优化目标)有影响,如何安排实验以确定工艺参数对翘曲的影响程 度并优化参数设置减少翘曲。 --设A,B,C均有3个水平,即试验中可取(A1,A2,A3,B1,B2,B3,C1,C2, C3)
PLASTICS LABS
实际产品设变情况
增加壁厚,从1.6mm到2.0mm
PLASTICS LABS
Moldflow DOE(Design of experiments ) 在优化成型参数方面应用
PLASTICS LABS
CASE1:后向回复反射器灯体
PLASTICS LABS
数据状态:模具设计完成
Specification:说明
产品平均壁厚2.7mm,带RR花纹
PLASTICS LABS
Material Data(材料参数)
Family name: 材料名称
General:
PMMA Plexiglas 8N
PLASTICS LABS
确认可变壁厚,将其设置为DOE变量之一
按DOE推荐条件设置
将底部壁厚改为DOE推荐值1.5mm(1+30%)=2.0mm
PLASTICS LABS
灯罩注塑工艺分析与模具设计

灯罩注塑工艺分析与模具设计摘要塑料工业是当今世界上增长最为迅速的工业之一,而注塑模具是其中发展较快的种类,因此,研究注塑模具对于了解塑料产品的生产过程和提高产品质量有很大的意义。
本文设计了对接型销双向斜抽芯推杆内抽芯灯罩注塑模,既满足了制品的成型和抽芯要求,又省去了斜抽芯和水平抽芯机构,大大简化了模具结构,脱型可靠,成型塑件质量好。
本模具设计过程中分析了灯罩制件的工艺特性,并介绍了ABS材料的成型工艺特点;通过对塑件的形状、尺寸及其精度的要求来进行注射成型工艺的可行性分析。
塑件的成型工艺性主要包括塑件的壁厚,脱模斜度和圆角以及是否有侧向抽芯机构。
通过以上的分析来确定模具分型面、型腔数目、浇口形式、位置大小;其中最重要的是确定型芯和型腔的结构,以及它们的定位和紧固方式。
在模具结构设计过程中提出了不同成型的方案并进行了比较,采取了最佳的成型方案;此外还分析了模具受力,脱模机构的设计,模具推出机构设计,合模导向机构的设计,冷却系统的设计等。
同时,详细地分析了模具结构与计算。
最后还对模具的成型零件进行了加工工艺的分析和设备的校核;还说明了模具的工作原理,对模具的装配还作了简单的介绍。
最后绘制完整的模具装配总图和主要的模具非标准零件图。
最后介绍了当今世界上最为普及的三维CAD/CAM系统标准软件的PROGRAM模块,对导柱和导套进行了参数化设计。
还可以使用PRO/ENGNEER中的塑料顾问来确定浇口位置和分析浇注过程。
通过本设计,可以对注塑模具有一个初步的认识,注意到设计中的某些细节问题,了解模具结构及工作原理,通过对PROGRAM的学习,可以建立较简单的零件库,从而有效的提高工作效率。
关键词:塑料模具;参数化;镶件;分型面AbstractPlastic industry is in the world grows now one of quickest industry classes,but casts the mold is development quick type,therefore,the research casts the mold to understand the plastic product the production process and improves the product quality to have the very big significance.This paper designs the docking type pin two-way inclined core-pulling rod inside core-pulling chimney injection mold, not only satisfy the molding and core products, and save the inclined core-drawing and horizontal core-pulling mechanism, greatly simplifying the mould structure, reliable, plastic molding of good quality.The mould design process are analyzed in the process characteristics. Chimney,And introduces the characteristics of the forming process of ABS material.Based on the shape and size of plastic parts and precision requirements for injection molding process of feasibility analysis.Plastic molding process including plastic parts of wall thickness, draft and rounded and whether any side core-pulling mechanism.Through the above analysis to determine the mold parting surface, cavity number, gate location, size and form, One of the most important is to determine the core and the mold structure, and their location and tighten.In the process of mould design scheme of different shape and comparison, the best solution to the molding, In addition, the stress analysis of the mould design demoulding mechanism, mould design, mould design of steering mechanism, the cooling system design, etc.At the same time, the detailed analysis and calculation, the die structure. Finally the molding parts of mould processing equipment and analysis of checking, Also explains the working principle of die mold assembly is introduced. Finally the generalassembly drawing complete mold and die non-standard parts graph.Finally introduced now in the world the most popular three dimensional CAD/CAM system standard software PRO/ENGNEER's PROGRAM module, and led the wrap to the guide pillar to carry on the parametrization design.we can use the plastic consultant to determine the runner gating processes and analysis.Through this design, may to cast the mold to have a preliminary understanding, notes in the design certain detail question, understands the mold structure and the principle of work; Through to the PROGRAM study, may establish the simple components the components storehouse, thus effective enhancement working efficiency.Key words:The plastic mold;the parametrization; inlays;divides the profile.目录引言 (1)1 注塑件的设计 (5)1.1 功能设计 (5)1.2 材料选择 (5)1.3 结构设计 (6)1.3.1塑件工艺分析 (7)1.3.2 壁厚 (7)1.3.3 脱模斜度 (8)1.3.4 圆角 (8)1.4 塑件的尺寸精度及表面质量 (8)1.4.1尺寸精度 (8)1.4.2使用性能、制件技术要求和生产要求 (9)1.4.3塑件的表面质量 (9)2 注塑成型的准备 (10)2.1 注塑成型工艺简介 (10)2.2 注塑成型工艺条件 (11)2.3注塑机的选择 (12)2.3.1 注塑机简介 (12)2.3.2 注塑机基本参数 (13)2.3.3选择注塑机 (13)2.4 注射机的校核 (14)2.4.1 最大注塑量的校核 (14)2.4.2 锁模力的核校 (14)2.4.3 塑化能力的校核 (15)2.4.4 喷嘴尺寸校核 (15)2.4.5 定位圈尺寸校核 (15)2.4.6 模具外形尺寸校核 (15)2.4.7 模具厚度校核 (16)2.4.8 模具安装尺寸校核 (16)2.4.9 开模行程校核 (16)3 浇注系统设计 (17)3.1 型腔数目的确定 (17)3.2 浇口确定 (17)3.3 浇注系统设计 (19)3.3.1主流道 (19)3.3.2分流道 (19)3.3.3冷料穴 (20)3.3.4浇口深度 (21)3.3.5剪切速率的校核 (22)4 成型零件结构设计 (23)4.1 成型零件 (23)4.2分型时型销与塑件干涉分析 (25) 4.3 分型定距机构 (26)5推出机构及复位机构设计 (27)5.1脱模力的计算 (27)5.2推杆脱模机构 (28)6 模具设计 (30)6.1模具材料的选择 (30)6.2 模架的确定 (30)6.2.1型腔壁厚和底板厚度计算 (30) 6.2.2模架的选用 (31)6.3 导向与定位机构 (33)6.4 排气设计 (33)6.4.1排气设计原则 (33)6.4.2推杆、镶件排气功能的证明 (34) 6.5 温度调节系统设计 (35)6.5.1温度调节对塑件质量的影响 (35) 6.5.2对温度调节系统的要求 (35)6.5.3冷却系统设计 (35)7 参数化设计 (38)7.1 PROGRAM简介 (38)7.2导柱的参数化设计 (38)7.3灯罩模塑工艺卡 (39)7.4模具工作过程 (39)8 结论 (41)谢辞 (42)参考文献 (43)。
2021汽车前灯罩注塑成型模具的结构设计范文2
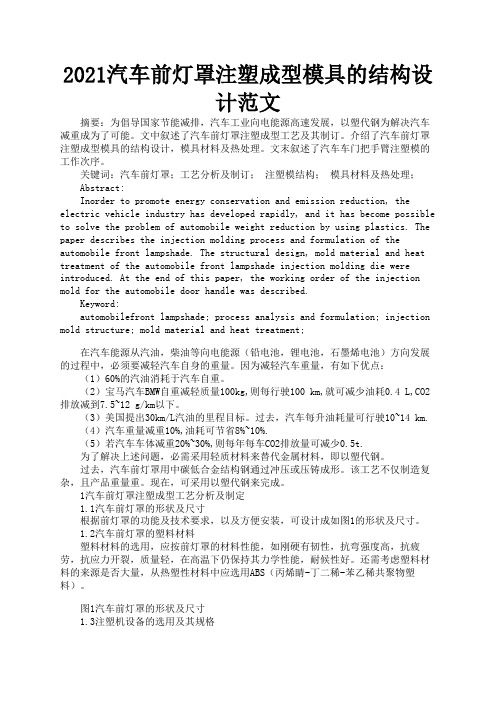
2021汽车前灯罩注塑成型模具的结构设计范文 摘要:为倡导国家节能减排,汽车工业向电能源高速发展,以塑代钢为解决汽车减重成为了可能。
文中叙述了汽车前灯罩注塑成型工艺及其制订。
介绍了汽车前灯罩注塑成型模具的结构设计,模具材料及热处理。
文末叙述了汽车车门把手臂注塑模的工作次序。
关键词:汽车前灯罩;工艺分析及制订;注塑模结构;模具材料及热处理; Abstract: Inorder to promote energy conservation and emission reduction, the electric vehicle industry has developed rapidly, and it has become possible to solve the problem of automobile weight reduction by using plastics. The paper describes the injection molding process and formulation of the automobile front lampshade. The structural design, mold material and heat treatment of the automobile front lampshade injection molding die were introduced. At the end of this paper, the working order of the injection mold for the automobile door handle was described. Keyword: automobilefront lampshade; process analysis and formulation; injection mold structure; mold material and heat treatment; 在汽车能源从汽油,柴油等向电能源(铅电池,锂电池,石墨烯电池)方向发展的过程中,必须要减轻汽车自身的重量。
汽车灯饰面盖零件热流道双色注塑模具设计

汽车灯饰面盖零件热流道双色注塑模具设计摘要:随着汽车工业的迅猛发展和消费者对汽车外观和功能的不断追求,汽车灯饰面盖在汽车外部设计中扮演着关键的角色。
汽车灯饰面盖既要满足美观和时尚的外观需求,又需要具备良好的照明效果和信号传递功能。
注塑成型技术已经成为制造汽车灯饰面盖的主要方法之一,而注塑模具的设计和制造对产品的质量和效率有着重要影响。
本文旨在设计一种用于汽车灯饰面盖的热流道双色注塑模具。
通过深入研究汽车灯饰面盖的设计要求和注塑模具的制造原理,结合现有的技术和工艺,提出了一种创新的双色注塑模具设计方案。
该设计方案不仅考虑了产品质量和生产效率,还兼顾了模具的可制造性和成本效益。
通过该设计方案,可以实现高质量、高效率的汽车灯饰面盖生产,提升产品竞争力和市场占有率。
关键词:汽车灯饰面盖;热流道;双色注塑模具;设计引言:随着汽车工业的快速发展,汽车灯饰面盖作为汽车外部设计的重要组成部分,对于车辆的外观美观和行车安全起着重要的作用。
而在汽车灯饰面盖的生产中,注塑成型技术被广泛应用,其制造过程中的模具设计和制造则是关键因素之一。
传统的注塑模具设计方法存在一些问题,如模具结构复杂、制造周期长、生产效率低下等。
而热流道双色注塑模具则是一种新型的设计方案,通过在模具中加入热流道系统,实现了两种不同颜色的塑料材料同时注入,使产品具有丰富的色彩和外观效果。
因此,热流道双色注塑模具在汽车灯饰面盖的生产中具有广阔的应用前景。
1. 汽车灯饰面盖的设计要求汽车灯饰面盖作为汽车外部设计的重要组成部分,对其设计要求较高。
首先,它必须具有良好的外观质量,以符合汽车品牌的形象和设计风格,为车辆增添美感。
灯饰面盖应具备流线型的外形设计,与整车的造型和比例相协调,从而提升整体的审美效果。
其次,汽车灯饰面盖需要具备优异的光学性能。
灯饰面盖作为汽车照明系统的重要部分,必须能够提供清晰明确的照明效果,确保车辆在夜间行驶时具备良好的可见性。
同时,它还需要具备良好的信号传递功能,确保车辆的转向信号、制动信号等能够准确传达给其他车辆和行人,保障行车安全。
汽车前照灯后壳大型注塑模具设计

汽车前照灯后壳大型注塑模具设计刘安林;黄瑶;周甫芝;杨雪【摘要】According to the structure characteristics of car headlight,a large and precision injection mold is designed by using composite and time-lapse core pulling mechanism and double stripping mechanism.The molding parts,side pulling mechanism,the gating system,the temperature control system,oriented positioning mechanism and stripping mechanism are introduced in detail.The design of mold structure is reasonable,and the action is safe and reliable,and obtained molding effect is satisfactory.%针对汽车前照灯后壳的结构特点,采用复合延时抽芯机构、双脱模机构,设计了一副大型精密注塑模具.详细介绍了该模具的成型零部件、侧向抽芯机构、浇注系统、温度控制系统、导向定位机构和脱模机构.该模具结构设计合理,动作安全可靠,获得了满意的成型效果.【期刊名称】《现代塑料加工应用》【年(卷),期】2018(030)002【总页数】4页(P48-51)【关键词】汽车前照灯后壳;大型注塑模;复合及延时抽芯;双脱模机构【作者】刘安林;黄瑶;周甫芝;杨雪【作者单位】江苏大学材料科学与工程学院,江苏镇江,212013;江苏大学材料科学与工程学院,江苏镇江,212013;江苏立德精密模具有限公司,江苏镇江,212132;江苏大学材料科学与工程学院,江苏镇江,212013【正文语种】中文车灯是汽车外饰件的重要组成部分之一,它给汽车的安全行驶提供了重要保障。
车灯支架注塑模设计与分析

车灯支架注塑模设计与分析作者:王敬艳来源:《CAD/CAM与制造业信息化》2013年第04期本文利用Moldflow软件对车灯支架进行工艺分析,检验和修改网格状态,选择成型材料,确定最佳浇口位置和工艺参数,并运用NX MoldWizard模块来设计车灯支架注塑模,从而将模具设计与分析结合起来,使设计出的模具最佳化。
车灯支架形状复杂,如图1所示,特征众多,厚度不均匀,故其模具型结构及尺寸也比较复杂。
该塑件材料为ABS,由其用途来看,塑件的表面光洁度要求较高,不允许有飞边,色泽均匀,不能出现凹陷、裂纹、波浪痕等缺陷。
一、车灯支架网格处理在进行一个塑件的CAE分析时,网格的质量是影响分析准确性的重要因素,因此,网格划分和网格修复是车灯支架模具设计的重点工作之一。
1.车灯支架的网格划分首先将三维模型转化为STL格式并在Moldflow软件中读取,采用三角形单元实现网格划分,通常制件的网格数目在几千到几万不等,甚至更多。
随着模型尺寸变大,复杂程度增加和网格密度增大,网格数目也相应增大。
本模型划分得到的网格单元数为7 184个,如图2所示。
2.车灯支架的网格优化网格划分好以后,接下来的工作就是网格信息统计,从统计信息不难发现,主要是纵横比问题较大,其他如重叠单元、配向、自由边、厚度和双层面等方面均良好。
为此,只要进行自动修复纵横比即可,其修复结果如图3所示。
二、车灯支架注塑模设计1.分型面分型面排位直接影响模具的使用、制造及塑件的形状、外观和精度,因此,必须选择合理的分型面。
分型面选择一般应遵循以下原则:确保塑件尺寸精度;尽可能减小塑件在分型面上的投影面积;合理安排浇注系统,特别是浇口位置;分型面是曲面时,应满足模具锁紧要求;尽量使模具结构简单、方便使用和制造容易。
车灯支架的侧向有凸台,需要侧向成型块来侧向成型,以便侧向顶离脱模。
在利用NX MoldWizard模块创建分型面时,首先进行侧面分型设计,以方便进行侧面抽芯;同时,利用分型功能识别塑件的分型边缘或最大轮廓线,并选择“条带曲面”的方式,选择合适的延伸距离,创建分型面如图4所示。
moldflow 注塑成型分析 模流分析报告

1. 熔体密度 2.实体密度 3.顶出温度 4.推荐模具温度 5.推荐熔料温度 6.材料失效温度
0.88 g/cu.cm 1.06 g/cu.cm
119 deg.C 45 deg.C 225 deg.C 290 deg.C
7. 熔料温度下限 8. 熔料温度上限 9. 模具温度上限 10.模具温度下限 11.最大剪切速率 12.最大剪切应力
Page 8
体积收缩
体积收缩结果用来判断产 品各处的体积收缩情况,收 缩不均匀会造成翘曲变形, 收缩较大则造成缩痕。 由图可见产品内部收缩较小, 且比较均匀。出现缩痕风险 小。
Page 9
困气位置
1
Air traps可提供模具的困气位 置。air traps产生在填充末端包 括高rib和boss柱位置、结合线、 流动包封位置。故而在这些位置 一般需要开设排入槽或排气入子。 另外在熔体温降较大处也应增加 排气,提高流动性。
pagepage1919尾部分子剪切作用较高故而分子取向度高并且分子结晶度高取向诱导结晶在取向方向上收缩较大故而收缩应力导致产品尾部收拉力而张开变形
Moldflow注塑成型分析
For
滨海
Reporter : 孟栋梁 sduan@
2010-07-16
分析描述
▪ 产品描述 此是汽车用产品,使用热浇道系统注射成型。
200.0 deg.C 250.0 deg.C 30.0 deg.C 60.0 deg.C 100000.0 1/s
0.25 Mpa
PVT Plow材料数据库
Page 3
工艺条件
注塑机设定:
最大锁模力:
未限定
最大注塑压力:
未限定
最大注射速度:
结合线
车灯常见注塑成型缺陷的机制分析及解决方法
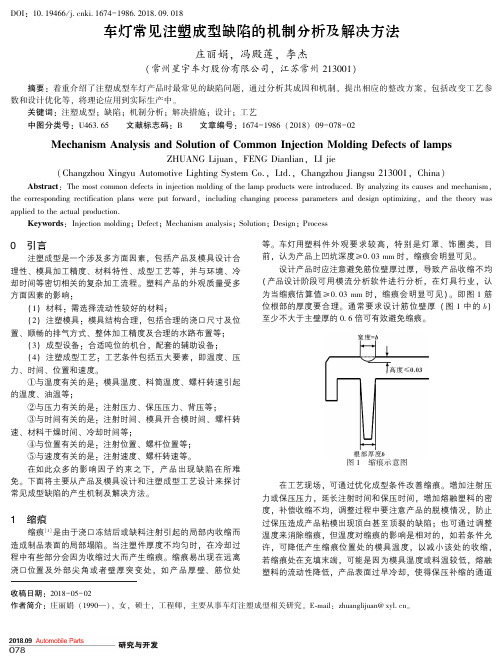
收稿日期:2018-05-02作者简介:庄丽娟(1990 ),女,硕士,工程师,主要从事车灯注塑成型相关研究㊂E⁃mail:zhuanglijuan@xyl cn㊂DOI:10 19466/j cnki 1674-1986 2018 09 018车灯常见注塑成型缺陷的机制分析及解决方法庄丽娟,冯殿莲,李杰(常州星宇车灯股份有限公司,江苏常州213001)摘要:着重介绍了注塑成型车灯产品时最常见的缺陷问题,通过分析其成因和机制,提出相应的整改方案,包括改变工艺参数和设计优化等,将理论应用到实际生产中㊂关键词:注塑成型;缺陷;机制分析;解决措施;设计;工艺中图分类号:U463 65㊀㊀文献标志码:B㊀㊀文章编号:1674-1986(2018)09-078-02MechanismAnalysisandSolutionofCommonInjectionMoldingDefectsoflampsZHUANGLijuan,FENGDianlian,LIjie(ChangzhouXingyuAutomotiveLightingSystemCo.,Ltd.,ChangzhouJiangsu213001,China)Abstract:Themostcommondefectsininjectionmoldingofthelampproductswereintroduced.Byanalyzingitscausesandmechanism,thecorrespondingrectificationplanswereputforward,includingchangingprocessparametersanddesignoptimizing,andthetheorywasappliedtotheactualproduction.Keywords:Injectionmolding;Defect;Mechanismanalysis;Solution;Design;Process0㊀引言注塑成型是一个涉及多方面因素,包括产品及模具设计合理性㊁模具加工精度㊁材料特性㊁成型工艺等,并与环境㊁冷却时间等密切相关的复杂加工流程㊂塑料产品的外观质量受多方面因素的影响:(1)材料:需选择流动性较好的材料;(2)注塑模具:模具结构合理,包括合理的浇口尺寸及位置㊁顺畅的排气方式㊁整体加工精度及合理的水路布置等;(3)成型设备:合适吨位的机台,配套的辅助设备;(4)注塑成型工艺:工艺条件包括五大要素,即温度㊁压力㊁时间㊁位置和速度㊂①与温度有关的是:模具温度㊁料筒温度㊁螺杆转速引起的温度㊁油温等;②与压力有关的是:注射压力㊁保压压力㊁背压等;③与时间有关的是:注射时间㊁模具开合模时间㊁螺杆转速㊁材料干燥时间㊁冷却时间等;④与位置有关的是:注射位置㊁螺杆位置等;⑤与速度有关的是:注射速度㊁螺杆转速等㊂在如此众多的影响因子约束之下,产品出现缺陷在所难免㊂下面将主要从产品及模具设计和注塑成型工艺设计来探讨常见成型缺陷的产生机制及解决方法㊂1㊀缩痕缩痕[1]是由于浇口冻结后或缺料注射引起的局部内收缩而造成制品表面的局部塌陷㊂当注塑件厚度不均匀时,在冷却过程中有些部分会因为收缩过大而产生缩痕㊂缩痕易出现在远离浇口位置及外部尖角或者壁厚突变处,如产品厚壁㊁筋位处等㊂车灯用塑料件外观要求较高,特别是灯罩㊁饰圈类,目前,认为产品上凹坑深度ȡ0 03mm时,缩痕会明显可见㊂设计产品时应注意避免筋位壁厚过厚,导致产品收缩不均(产品设计阶段可用模流分析软件进行分析,在灯具行业,认为当缩痕估算值ȡ0 03mm时,缩痕会明显可见)㊂即图1筋位根部的厚度要合理㊂通常要求设计筋位壁厚(图1中的b)至少不大于主壁厚的0 6倍可有效避免缩痕㊂图1㊀缩痕示意图在工艺现场,可通过优化成型条件改善缩痕㊂增加注射压力或保压压力,延长注射时间和保压时间,增加熔融塑料的密度,补偿收缩不均,调整过程中要注意产品的脱模情况,防止过保压造成产品粘模出现顶白甚至顶裂的缺陷;也可通过调整温度来消除缩痕,但温度对缩痕的影响是相对的,如若条件允许,可降低产生缩痕位置处的模具温度,以减小该处的收缩,若缩痕处在充填末端,可能是因为模具温度或料温较低,熔融塑料的流动性降低,产品表面过早冷却,使得保压补缩的通道变窄,造成产品末端产生缩痕;或者,在补缩通道冻结之前进行有效的保压,可提高注射速度等㊂当工艺无法优化时,可通过优化模具结构来调整缩痕㊂如,通过扩大浇口或流道截面尺寸以减小压力降;或者更改浇口位置,将浇口靠近缩痕处进行补缩㊂2㊀困气困气是指合模注射时,熔融塑料在型腔内流动挤压并压缩型腔内的空气,因无有效排气系统,导致气体困在熔融塑料内的现象㊂产品拐角处,因壁厚设计不合理易出现该缺陷,如图2(a)所示㊂工艺上可通过提高料温和注射压力,降低缺陷处注射速度的方法来改善该缺陷,旨在能将拐角的气体 溶解 到熔融塑料中㊂注塑生产不能完全指望通过工艺稳定产品质量,易造成报废较多㊁不能稳定生产且调试窗口较小㊂所以在前期设计时,应注意将产品拐角处的壁厚调整至与主壁厚相等,使得熔融材料可顺利通过拐角,避免将气体滞留在拐角处,优化方案如图2(b)所示㊂也可通过改变浇口数量或位置,改变熔体流动方向,避免流动 死角㊂图2㊀困气示意图及整改方案3㊀窜色窜色是指多色成型时,产品出现颜色不均匀的现象㊂如图3所示,第一射成型红片,第二射覆盖成型白片时,白片料流经过时会融化一部分红片带入白片之中,造成白片外观颜色不均匀㊂图3㊀窜色示意图工艺上可通过降低成型红片模具定模的温度来临时改善该缺陷;模具上,可通过减小非覆盖区域白片的厚度(即白片模具加铁)来改善(车灯透明灯罩通常建议减小0 5mm),如图4所示㊂另外,也可以更改浇口位置,如将浇口位置置于非覆盖区域,或者改变成型顺序,如先成型红片后成型白片来改善此类缺陷㊂图4㊀窜色整改方案示意图4㊀黑点黑点主要是由于塑料材料过热分解引起的㊂一方面可能是因为料筒温度异常导致材料过热分解,另外,螺杆转速太快㊁背压过高㊁注塑速率太快均可能造成材料过热分解,这需要工艺上按材料的物性要求去设定温度㊂另一方面,产品较小,但料管选择过大,原料或色母停留在料管中的时间过长,被储料时的高剪切作用降解,也会形成黑点,这要求产品克重为料管的最大计量容量的20% 80%(25% 75%更佳)㊂在设备方面,还要考虑 设备死角 问题,如若工艺参数均在合理范围之内,对空注射材料就有变色现象,即需找出 设备死角 ,如螺杆死角㊁热流道喷嘴死角等,需要通过清洗㊁修补㊁抛光 死角 加以解决㊂若一开机就有黑点,则考虑与料管存料有关,须注意操作方法㊂如果是因为加工过程中,因维修或其他原因暂时停机,时间较久导致料过热分解,下次生产仍为同一种原料,要用新料在低于成型温度20ħ下对空注射3-4次,直至无黑料㊂为避免上述情况,若临时中止生产,需按照保温规定对料筒进行设定,对PP㊁PBT㊁ABS㊁PMMA设定材料设置150ħ,PC㊁PC+ABS㊁PC⁃HT㊁PEI材料设定170ħ对料筒进行保温(注:透明材料需保持满料筒保温)㊂如果所存料为其他料,可用所存料的回料在成型温度下先清洗一遍,再将未烘干的新料原料在低于成型温度20ħ下清洗,最后用新料在成型温度下彻底清洗一遍,即可正常进行加工㊂另外,还要注意环境的清洁,保证模具和材料不被污染[2]㊂5㊀结论塑料成型是一个涵盖多方面因素的复杂加工过程,因此,塑料产品的外观质量受多方面因素的制约㊂文中主要从注塑成型工艺及模具设计方面来探讨产品成型缺陷的产生机制及解决办法,具有一定的实践指导意义㊂参考文献:[1]饶启琛,黄建军.注塑成型异常分析及处理(二)[J].橡塑技术与装备,2006,32(4):57.RAOQC,HUANGJJ.UnnormalAnalysisandTreatmentofInjectionMolding(PartⅡ)[J].ChinaRubber/PlasticsTechnologyandEquipment,2006,32(4):57.[2]董钜潮,周颖南,黄建军,等.PC注塑制品常见缺陷分析及解决方法[J].工程塑料应用,2003,31(9):23-27.DONGJC,ZHOUYN,HUANGJJ,etal.AnalysisofCommonDefectsintheInjectedPCProductsandtheirSolvingMethods[J].EngineeringPlasticsApplication,2003,31(9):23-27.。
汽车注塑件缺陷分析解读

不良缺陷注塑不满、凹陷、熔合缝、料流纹、光泽不好、气孔、黑点、溢边、翘曲变形、银文、脱模不好、云彩、冲孔粗糙、马蹄形、中心孔小、中心孔大、基片太厚、基片太薄、双折射大、双折射小、基片破裂、流道断裂、径向条纹、唱片沟纹、光环、麻点气、体烧焦、冷料、喷射纹、银纹、压花不均匀、滑痕、飞边、须状斑纹、表面剥离、气泡、变色、空洞、波纹、模垢、拉丝、裂纹、浇口切割不良、计量不良、注射量不稳定、主流道粘模、流涎、流线等以上缺陷成因:模具温度,冲孔刀、流道温度,注射速度、注射压力,保压力、保压时间,转换点,锁模力、冷却时间,炮筒温度、塑化时间、塑化速度,背压等制品缺陷及产生的原因克服方法注塑成型各种缺陷的现象及解决方法:(一)熔接痕(Weld line)熔接痕是由于来自不同方向的熔融树脂前端部分被冷却、在结合处未能完全融合而产生的。
熔合出现在树脂合流之处。
两股树脂流相遇时便会出现熔合。
此时,两者的温度越低,熔合就越明显。
由于熔合处的两股树脂流并不会相互混合(因为在喷流中一边半固化一边前进),因此如果温度偏低,表层就会变厚,纹路很明显,而且强度也会降低。
这是因为两者的粘合力变弱所致。
相反,如果两股树脂流的温度较高,粘合力便会增强,外观也就变得不很明显。
在熔合处,两种熔化了的树脂受到挤压,此处的粘合状况取决于施加在该处的压力。
保压越低,熔合就越明显,强度也就越低。
如果不仅要考虑保压的设定,而且要考虑实际施加在熔合处的压力会降低这一条件,则上述(i)~(iv)都几乎同样适用。
这是因为随着固化的进行,压力传递会变得更加困难。
此外,如果浇口尺寸变小,浇口位置变差的话,则熔合的外观和强度都会恶化。
熔合是树脂的合流点,同时也可能是流动末端。
此时,如果不在熔合处很好地设置一个排气口来排出气体,则会使熔合的外观和强度恶化。
一般情况下,主要影响外观,对涂装、电镀产生影响。
严重时,对制品强度产生影响(特别是在纤维增强树脂时,尤为严重)。
汽车车灯灯壳注塑模具设计

本科毕业设计设计题目:汽车车灯灯壳注塑模具设计2011年6月22日毕业设计独创声明本人郑重声明:所呈交的毕业设计,是本人在指导老师的指导下,独立进行研究工作所取得的成果,成果不存在知识产权争议。
尽我所知,除文中已经注明引用的内容外,本设计不含任何其他个人或集体已经发表或撰写过的作品成果。
对本文的研究做出重要贡献的个人和集体均已在文中以明确方式标明。
此声明的法律后果由本人承担。
作者(签名):毕业设计使用授权声明本人完全了解鲁东大学关于收集、保存、使用毕业设计的规定。
本人愿意按照学校要求提交设计的印刷本和电子版,同意学校保存设计的印刷本和电子版,或采用影印、数字化或其它复制手段保存设计;同意学校在不以营利为目的的前提下,建立目录检索与阅览服务系统,公布设计的部分或全部内容,允许他人依法合理使用。
(保密设计在解密后遵守此规定)作者(签名):毕业设计选题报告汽车车灯灯壳注塑模具设计王盼(交通学院机械制造及其自动化专业 2008级交通本0804班 20082814125)摘要:(内容为楷体,五号,左右两边各缩进2cm或2个字的位置)关键词:(楷体,五号,分号分隔,最后一个不用标点)Study of Surface Nan crystallization on Metal MaterialsWang Pan(School of Transportation, Communications and Transportation,Jiaotongben0401 Grade2004, 0428…..)Abstract:Increasing interests have been focused on nanocrystalline (nc) materialsduring the past decade with the anticipation that their properties will be different from,and often superior to those of conventional coarse-grained materials. The applicationand the recent research progress of surface nanocrystallization of metal materials havebeen summarized.Key Words: surface nanocrstallization; surface mechanical treatment; surfacemodification1 引言(第一层标题,三号黑体,行距:段前1行,段后1行)随着汽车工业的飞速发展,对汽车车灯照明性能的要求也越来越高,其中既有自由曲面组成的配光反射器壳体,它具有车灯高度低、光源利用率高及空气动力性能好等优点,又有结构更完善的衬匡,更有线条流畅美观大方的面罩,以上每一项的设计和造型,最终决定了该车型车灯的完美与否。
汽车前大灯灯壳注塑模设计

汽车前大灯灯壳注塑模设计汽车车灯主要是用做照明,可以说是汽车的眼睛,车灯是对所有汽车照明系统的统称。
汽车车灯外观要求高,几个重要零件都是透明件,电镀件等,可以说汽车外观要求最高的零件就是车灯,因而对模具设计与制造要求极高。
一般汽车的主要灯饰件就是前后大灯。
车灯不同的车系有不同的配置,同一车系依据高低配置也不尽相同。
组成汽车前后灯的主要零件有:左右透镜.左右装饰框.左右灯壳.左右反射镜等。
汽车车灯的外观要求极为严格,本文选取某名牌汽车前大灯模具进行介绍。
本文详细介绍汽车车灯注塑模具的设计经验和要点,以某品牌汽车的一款汽车的前大灯作为案例来分析。
汽车前大灯组装效果如图1所示:图1 汽车前大灯组装效果图图1所示零件为某品牌汽车的前大灯组装图,本章以汽车前大灯灯壳零件为例,详细介绍汽车灯壳注塑模具的设计要点与技术总结。
汽车灯壳零件如图2所示:图2 汽车前大灯灯壳零件图1 塑件外观要求与结构分析图2所示为某品牌汽车前大灯灯壳零件图,材料为PP+TD20,其中PP为灯壳外罩的基体,TD20是材料中加入20%的滑石粉,主要是提高灯壳外罩的刚性。
非外观件,属内部功能件。
塑件尺寸为:475.3*355.6*291.4mm。
塑件特点如下:(1)非外观件,塑件外观面不允许有斑点,收缩凹陷.熔接痕.飞边等缺陷(外观缩痕要求不是很高)。
(2)塑件为内部功能件,灯头孔.后盖孔等装配要求高。
(3)塑件外形复杂,塑件外侧面有6处倒扣,灯壳除了灯头孔非左右镜像外,其余特征都是左右镜像。
(4)塑件外侧面共有6处倒扣,需采用侧向抽芯结构。
(5)根据塑件特征,灯壳塑件有粘定模风险,塑件设计需预防粘定模。
2 模具结构分析根据汽车灯壳的结构特点与外观要求,模具优先采用热流道注塑模结构。
经模流分析结果与技术讨论,最终采用2点开放式热流道直接进胶。
本模具S1,S2,S3,S4,S5,S6由于在塑件外侧,倒扣面积大,因此优先采用动模“斜导柱+滑块”的抽芯结构。
浅析注塑成型车灯产品时常见缺陷及应对措施陈贝明

浅析注塑成型车灯产品时常见缺陷及应对措施陈贝明发布时间:2023-05-30T23:35:00.952Z 来源:《科技新时代》2023年6期作者:陈贝明[导读] 在汽车工业飞速发展的今天,人们对车灯的照明品质和外观设计也越来越关注。
车灯对车辆的安全运行起着非常重要的作用,它为车辆的安全运行提供了很好的照明和信号。
车灯的设计对车辆的外观和安全性有很大的影响。
身份证号码:33900519860512xxxx 摘要:在汽车工业飞速发展的今天,人们对车灯的照明品质和外观设计也越来越关注。
车灯对车辆的安全运行起着非常重要的作用,它为车辆的安全运行提供了很好的照明和信号。
车灯的设计对车辆的外观和安全性有很大的影响。
大多数的车辆设计规则都是为大灯而设计的。
因此,大灯是保证行车安全的重要部件。
如今,人们对车灯的需求已经不仅仅只是为了起到照明的作用,他们还想要有一个更完美的车灯外形,还有一个更酷炫的光照效果。
由于车灯是装在汽车的车身上,所以车灯与车身之间要有一个非常好的结合,这样才能更好地体现出流线的美,所以,车灯的设计也会变得越来越复杂。
当前,国内车灯设计及其模具制造主要依靠经验,许多设计理论知识和方法并不完善,因此,许多的核心技术还需要不断地去摸索与创新。
本文从车灯塑料件的注塑成型工艺以及车灯光学零件模具加工工艺这两方面的进展展开讨论,对车灯注塑成型中的主要工艺参数以及工艺优化过程进行了分析,并对未来的研究方向展开了展望。
关键词:浅析注塑成型;车灯产品;缺陷;应对措施1车灯塑料件的注射成型工艺注射成型是一门需要熟练掌握的技术。
注塑工艺参数的配合,也是为了更好地塑化塑料,然后一步一步地冲模,冷却,再定型,有一套完善的流程,才能生产出优质的产品。
目前,由于汽车品牌的迅猛发展,各种型号的车灯产品越来越多,各种型号的车灯产品往往会出现各种缺陷,因此,寻找适合车灯生产的最佳工艺参数,已成为国内外学者关注的焦点。
在某些较旧的注塑工艺中,通常都是由设计人员按照自己的生产经验和设计手册,先将车灯模具的图纸大纲设计出来,然后在下一步的工序中进行加工,如果在试模的时候出了什么问题,那么就需要对注射的参数进行重新设置,或者是对图纸进行修改,这样会在一定程度上加大人力成本,同时还会影响到生产的效率,从而造成不必要的损失。
注塑模流分析报告
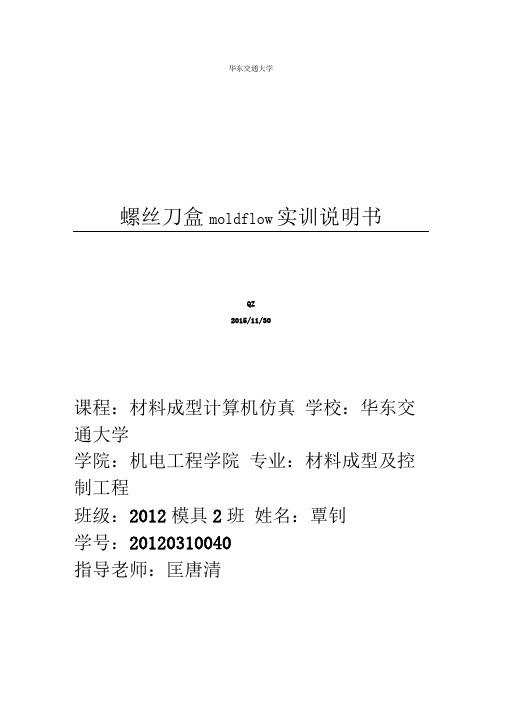
华东交通大学螺丝刀盒moldflow实训说明书QZ2015/11/30课程:材料成型计算机仿真学校:华东交通大学学院:机电工程学院专业:材料成型及控制工程班级:2012模具2班姓名:覃钊学号:20120310040指导老师:匡唐清1、三维造型利用UG8.0设计出模型如下图 1.1、1.2 表示<1图1.1 实物图图1.2三维图模型参数长宽高为143*85*19.5,主壁厚为1.5mm。
二维图如图1.3佩图1.3二维图壁厚均匀,但在盖钩和挂孔处厚度和壁厚相差较大,体积收缩率在这两个地方应该会出现一些问题。
主分型面在上表面,侧面有卡勾及圆孔,需要做侧抽芯。
材料选用普通PP材料。
模型建好之后导出为IGES格式。
2、模型修复与简化打开CAD Doctor后导入IGES模型,检查并修复,直到所有错误都为0,修复完成之后将模型导出,格式为udm格式。
3、moldflow模流分析3.1网格划分(1)新建工程,输入工程名称,导入模型,在导入窗口选择双层面。
(2)网格划分,网格变长取壁厚的3倍,为4.5m m,合并容差默认为0.1,启用弦高控制0.1mm,立即划分网格,划分之后打开网格统计,看到网格的基本情况,不存在自由边和多个连通区域的问题后进行下一步。
一般来说初始划分的网格纵横比都比较大,所以要进行修复。
纵横比诊断结果如图 3.1.1 :最大纵横比达到了45.57。
图3.1.1初次纵横比诊断3.2网格诊断与修复点击【网格】一一【网格修复向导】,前进到选择目标纵横比,输入6,点击修复。
之后在进行手动修复,通过合并节点移动节点等方式进行,直到得到满意的结果。
如下图3.2.1 :9.*387,319L II A^rbodedr■iM I.qiTg [eV ; k| I J■草(1WI «R(图321修改后的纵横比诊断修复后的纵横比为13.68,只出现少数,可以接受。
修复后的网格统计如下图 3.2.2:1^108纵横比:最大13.7平均2.71性角形30.S393 cn*3三元单:一兀S-节单童嬰全点相完交图3.2.2网格统计面积:表面面和;^5.432 cm A2边边边LBBUE■-TnnT^二互卄元单的确正:不百升比相互百亦比由统计结果知,匹配率都达到了 91%以上,合理。
汽车仪表罩模流分析报告
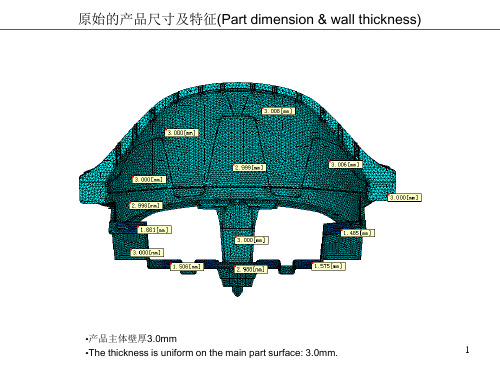
Volumetric shrinkage at ejection
17
Deflection
Deflection picture, all effects: Deflection
产品总的变形如上图所示,以上变形量包括产品的收缩, 产品尺寸450*235*228。
18
Deflection
Deflection picture, all effects: X Component
Pressure at V/P switchover
Pressure distribution
•The V/P switchover time is at 2.82s, when the part volume is filled at 99% •The V/P pressure is 65.02MPa. •It is suitable for molding.
原始的产品尺寸及特征(Part dimension & wall thickness)
•产品主体壁厚3.0mm •The thickness is uniform on the main part surface: 3.0mm.
1
Preprocess and mesh statistics
网格统计 Mesh statistics
Fill time Fill time (contour) Weld Lines Location Air Traps Location Pressure at V/P switchover Pressure at the end of fill Flow Front Temp Shear Rate Pressure at injection location Clamp Force Volumetric shrinkage at ejection Deflection (all deflection cause) Conclusions and suggestions
注塑车灯用塑料产品常见水丝缺陷分析及解决措施

注塑车灯用塑料产品常见水丝缺陷分析及解决措施摘要:汽车行业的发展速度不断加快,对汽车灯具的要求越来越高。
灯具的各项性能指标要符合规定,有较高的安全性,还要保证外观质量。
由于塑料有很多的优点,即质量轻,具有很好的耐腐蚀性、导热低、具有良好的机械性能且容易成型等等。
当前车灯的多数零部件均为注塑成型,包括反射镜、壳体、灯罩以及饰圈等等,在这个动态化加工过程中需要多种因素相互作用,比如,模具结构、模具材料、模具设备以及有关工艺参数等等,任何一个因素存在问题,都会影响产品质量。
本文着重于研究车灯用塑料产品常见水丝缺陷分析及解决措施。
关键词:注塑车灯;塑料产品;常见水丝缺陷;原因;解决措施引言:在对车灯进行注塑成型的过程中应用CAE软件,能够对每个环节进行模拟,包括充填环节、保压环节、冷却环节以及翘曲环节等等,可以预测注塑结构,对于产品可能产生的缺陷提前分析,基于此对模具结构进行优化处理,使得试模成功率有所提高[1]。
但是,在操作的过程中会受到诸多因素的影响,应用CAE软件进行模拟的时候很难获得等同于真实注塑过程的结果,当进行实际注塑生产的时候,需要从实际调试的具体情况出发,对所存在的缺陷以及原因进行分析,将相应的解决对策提出来,根据实际需要对工艺参数重新调整,还可以对模具结构进行修改,以使产品的外观要求得到满足。
一、注塑车灯生产中容易出现的问题当注塑车灯进入到实际生产过程中,从产品外观上来看,很容易产生一些问题,主要为水丝、开裂、欠注、色差、黑点以及缩痕等等,其中比较常见的是水丝,容易导致产品报废,甚至质量不合格。
水丝是在塑料充模的时候产生银纹或者气纹,在气体的干扰下,表面熔料方向很容易出现这种缺陷。
在气体的成分中包括有多种气体,主要为空气、水汽以及分解气等等。
如果气体已经突破了限度,当注射成型之后,模腔就会失去压力,此时在接近制品表面之处就会冒出气体,沿着料流的方向刻蚀之后,形成有泡点,而且连接成串,在阳光的照射下闪烁,这就是气纹,也被称为印纹[2]。
注塑车灯用塑料产品常见水丝缺陷分析及解决措施

注塑车灯用塑料产品常见水丝缺陷分析及解决措施摘要:车灯是汽车建造过程中最基础的部分,在进行注塑成型车灯产品过程中较为常见问题是水丝缺陷。
针对以上问题,本文对该现象的原因进行分析,提出相关的改革措施,应用于汽车车灯生产过程中,从而促进注塑车灯发展和进步。
关键词:注塑成型;表面质量;水丝;原因分析;解决措施引言汽车工业随着我国经济的迅速发展得到了良好的发展机会,人们对于汽车灯的质量要求也越来越高,因为汽车灯具的质量对行车安全有着重要的影响,灯具一定要符合国家的相关标准制定。
不仅是在质量上还有在车灯的外观上也有显著的要求,塑料的特点是方便运输,具有一定的抗压能力,易于成型等优点,车灯的大部分是需要塑料来进行注塑成型的。
注塑成型是一个动态的过程,对于模具结构、材料、设备、工艺参数都会产生一定的影响。
1水丝的类别1.1材料含水量高在进行水丝的注塑成型过程中,把未烘干的塑料粒子放入料筒。
在高温过程中,可以对水分进行速溶。
模具因为水汽的塑料与魔枪内壁会产生剧烈的摩擦,从而造成水汽的拉长产生丝状的现象(图1)图1材料含水量高产生的水丝如图所示,该水丝前端呈圆形状,可以从交口以扇形方式来进行扩散,并且形状较大会影响外观。
产品质量不高无法进行生产工作,所以在进行注塑过程中需要对原材料进行烘干。
1.2由热分解产生的水丝注塑成型的原理是指塑料在注塑机的料桶中进行加热,然后通过柱塞将容体到模具中进行成型。
根据调查,70%来源于螺杆的剪切热而30%来源于料筒的加热丝。
在进行高分子塑料受热过程中,会产生过分的分解就会产生图2所示的水丝。
注塑成型是指塑料先在注塑机的料筒中受热熔融。
之后由螺杆(或柱塞)将熔体推挤到模具中成型的一种方法。
通常认为,塑料受热的来源70%来自螺杆的剪切热,30%来自料筒加热丝。
高分子塑料受热会过度分解,产生如图2所示的水丝。
图2热分解产生的水丝该水丝比较密集并且是根根分明的,针对以上情况,来进行相关成因的分析,并且提出解决方案。
微车后灯外罩注塑工艺优化
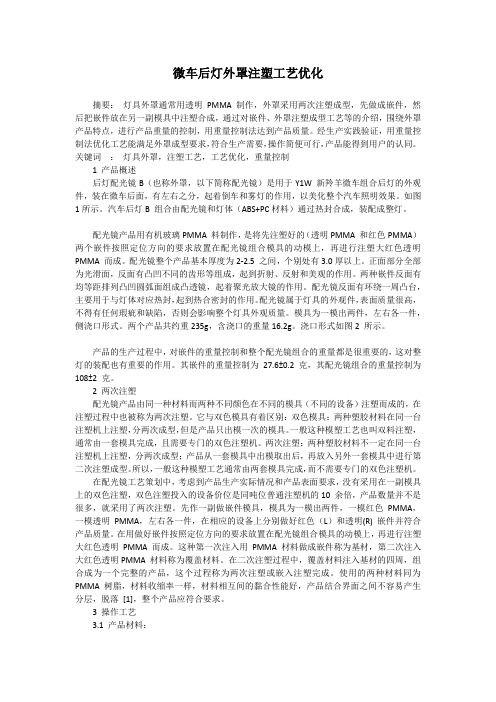
微车后灯外罩注塑工艺优化摘要:灯具外罩通常用透明PMMA 制作,外罩采用两次注塑成型,先做成嵌件,然后把嵌件放在另一副模具中注塑合成,通过对嵌件、外罩注塑成型工艺等的介绍,围绕外罩产品特点,进行产品重量的控制,用重量控制法达到产品质量。
经生产实践验证,用重量控制法优化工艺能满足外罩成型要求,符合生产需要,操作简便可行,产品能得到用户的认同。
关键词:灯具外罩,注塑工艺,工艺优化,重量控制1 产品概述后灯配光镜B(也称外罩,以下简称配光镜)是用于Y1W 新羚羊微车组合后灯的外观件,装在微车后面,有左右之分,起着倒车和雾灯的作用,以美化整个汽车照明效果。
如图1所示。
汽车后灯B 组合由配光镜和灯体(ABS+PC材料)通过热封合成,装配成整灯。
配光镜产品用有机玻璃PMMA 料制作,是将先注塑好的(透明PMMA 和红色PMMA)两个嵌件按照定位方向的要求放置在配光镜组合模具的动模上,再进行注塑大红色透明PMMA 而成。
配光镜整个产品基本厚度为2-2.5 之间,个别处有3.0厚以上。
正面部分全部为光滑面,反面有凸凹不同的齿形等组成,起到折射、反射和美观的作用。
两种嵌件反面有均等距排列凸凹圆弧面组成凸透镜,起着聚光放大镜的作用。
配光镜反面有环绕一周凸台,主要用于与灯体对应热封,起到热合密封的作用。
配光镜属于灯具的外观件,表面质量很高,不得有任何瑕疵和缺陷,否则会影响整个灯具外观质量。
模具为一模出两件,左右各一件,侧浇口形式。
两个产品共约重235g,含浇口的重量16.2g。
浇口形式如图2 所示。
产品的生产过程中,对嵌件的重量控制和整个配光镜组合的重量都是很重要的,这对整灯的装配也有重要的作用。
其嵌件的重量控制为27.6±0.2克,其配光镜组合的重量控制为108±2 克。
2 两次注塑配光镜产品由同一种材料而两种不同颜色在不同的模具(不同的设备)注塑而成的,在注塑过程中也被称为两次注塑。
它与双色模具有着区别:双色模具:两种塑胶材料在同一台注塑机上注塑,分两次成型,但是产品只出模一次的模具。
- 1、下载文档前请自行甄别文档内容的完整性,平台不提供额外的编辑、内容补充、找答案等附加服务。
- 2、"仅部分预览"的文档,不可在线预览部分如存在完整性等问题,可反馈申请退款(可完整预览的文档不适用该条件!)。
- 3、如文档侵犯您的权益,请联系客服反馈,我们会尽快为您处理(人工客服工作时间:9:00-18:30)。
汽车灯罩外壳注塑件模流分析摘要:本论文主要针对汽车灯罩外壳注塑件的生产过程进行研究,在研究中结合Moldflow技术以及有限元分析的方法,对汽车灯罩外壳注塑件进行三维建模并进行数值模拟,主要针对模型中的缺陷开展分析工作,对所建立模型的正确性进行验证。
本论文主要利用 Moldflow软件对汽车灯罩外壳注塑件成型过程中发生的缺陷进行了仿真分析,主要包括产品结构尺寸及质量的变化、内部流道温度分布以及产品各流道之间温度差等。
通过这些计算仿真得到了产品质量出现缺陷时对应点的曲线。
并利用 CAE技术对上述预测曲线作进一步分析和研究。
对于汽车灯罩外壳注塑过程中模具温度场分布及内部温度分布等方面也做了相关研究工作。
通过Moldflow软件仿真分析对上述预测的结果进行了验证,得到的预测结果与实际情况相符,从而证明了仿真模型在实际生产过程中可以作为一种有效的质量评定手段,同时也为模具设计提供了有效工具,为模具结构优化和改进提供了依据。
关键词:注塑成型;Moldflow;模流分析;翘曲变形1.绪论随着汽车行业的不断进步,汽车产品的性能和性能都在不断提高,除了具有高品质外,外观造型也是一个重要的性能指标。
而对于传统汽车生产企业而言,需要生产出质量合格有竞争力的产品以满足客户需求,为了保证生产的顺利进行,必须采取行之有效的措施。
在如今这个充满了激烈竞争的市场中,为了能更好地满足消费者要求以及使企业获得稳定、持续发展的能力,提高企业综合竞争力,在进行生产设计时需要考虑更多新事物、新技术和新材料。
本文结合注塑成型过程仿真分析及有限元分析技术对汽车灯罩外壳注塑件成型过程进行研究及分析。
2.产品分析汽车灯罩外壳主要由两部分组成,分别为前盖、后盖,其中前盖上有一个凹陷结构,后盖上有一个凸台结构。
本文以后盖为例进行注塑成型过程仿真分析及有限元分析。
汽车灯罩后盖是一种薄壁型塑料制品,平均壁厚2毫米。
该塑件使用的是聚碳酸酯和聚丙烯精 ABS+PC[1],将 ABS的可成型性与 PC的机械性能、冲击强度、抗高温、抗紫外线等优良性能有机地结合起来。
同时,该复合材料具有无毒、无味、可再生、可循环使用等特点,其环境保护特性已经获得了国际、国内有关部门的认可。
因为塑料材料具有热胀冷缩的特性,因此,在进行三维建模之后,在进行模具设计的时候,都需要提前对产品塑件的整体尺寸进行缩水。
聚碳酸酯和聚丙烯精材料具有在0.5%至0.8%之间的平均收缩率[2]。
本文对于这种塑料制品,采用的是0.5%的收缩率,所以,整个模型的放大倍数是1.005,灯罩外壳塑料制品的三维造型,如图1所示。
图1灯罩外壳三维建模(后壳)2.1网格划分此次分析选择双层面(Dualplane)划分网格,本次分析要求模型三角形网格单元任意纵横比不能超过6[3],产品塑件网格匹配率越高,计算结果越精确,并且网格匹配率百分比应大于85%在 Moldflow软件中建立双层面(Dualplane),得到了24691个单元,其中最小纵横比为1.157、最大纵横比为6.0、平均纵横比1.76、匹配率94.3%以上,符合分析的需要,并具有很高的精度,能够完成对模型的全面分析。
通过对网格进行诊断、修复等预处理,最终获得一个基于网格的有限元模型。
2.2产品模型(壁厚分析)通过 Moldflow仿真分析网格厚度诊断表明,产品壁厚与产品结构位置有关。
未设置收缩的零件外形尺寸为7x252π平均厚度为1.5mm,网格最大厚度为2.06mm,网格最小厚度为0.7131mm。
这种产品的构造比较复杂,在其边沿部位有3个向外的扣件设计,壁厚均在1.5mm以下,最薄处在0.8mm以下,在注射成形中,制品容易产生翘曲变形,熔接痕,缺料,气孔等缺陷。
2.3浇口分析在注塑成型的过程中,浇注系统的设定是模具设计的一个重要环节,其中,浇口位置的选择是首要的问题,它会对后续的排气的开设、脱模机构的布置等产生影响;在进行了模拟分析之后,本产品的浇口位置应当选择分析结果所示的蓝色区域,在这个区域内,与之匹配度最高,且流动阻力最低,是本产品的最佳浇口位置[4]。
常见浇口分为直接浇口、侧浇口、点浇口、潜浇口等类型,而小型注塑产品的浇口应设在模具分型面上,所以通常选择侧浇口。
侧浇口,又称边缘浇口,是当前应用最为广泛的浇口形式。
侧面浇口是主要用于多型腔注塑模具,但也适用于较小截面尺寸注塑件。
本次研究的产品浇注系统采用侧浇口,圆形流道,浇口设置于产品的中心处,出口为1mm下潜角度45°,分流道直径4mm,为了更好地提高物料流动的温度和提高物料的流动性,采用了直线形分流道。
2.4流动结果分析Moldflow仿真结果中充填动态分析结果表示,产品塑件充填所需要的时间和浇口所处位置有关系。
需填充区域距离浇口位置越远,需要的充填时间越长,卡扣末端最后充填,容易产生翘曲等缺陷;经过分析,产品塑件在填充时所需要的时间为0.6892s,充填时间比较短,有利于型腔充满,通过Moldflow仿真结果中发现,填充没有发现填充不满的现象,即欠注现象。
如果存在欠注现象,则模型将会出现灰色区域;考虑到红色部位为最后填充部位,所以在设计模具时,排气槽可以设计在红色部位的附近,更加利于实际与模拟的切实性。
流动前沿温度分析结果表明,熔体流动前沿温度相差3.3℃,最高温度278.2℃,三个卡扣设计所在的位置与其他位置温度有很大的不同,该位置所在区域填充的塑料溶体温度要高于附近区域的温度,该位置很有可能产生翘曲变形,或者出现熔接痕;注射位置处压力曲线分析表示,在充填的初始阶段,型腔内部中不存在压力,当型腔被料流填满时,进料压力快速升高,并达到最大值[5]。
由Moldflow仿真分析结果可知,当0.6788s型腔充满时,其注入压力最高达到61.48MPa,之后在49MPa持续很长一段时间,这对于该产品的材质和尺寸来说,是比较适合的。
锁模力的计算是为了让生产达到更精准的作业标准,它的正确使用可以减少器具的磨损和维护正常的生产。
在现实生产中,市场上大多数的注塑机都是按照锁模力吨数来设定等级的,而吨数大多为整数。
很明显,这样的设置是为了方便生产商在计算锁模力后,更直观、精准地选择适合的注塑机。
对产品的锁模力的仿真分析结果,在1.099s时,模具锁定力的最大值是17.64吨,需要选取一个锁模力20吨的注塑机,以达到产品的注塑成型要求。
2.5外观分析结果2.5.1熔接线产品在注塑过程中,熔接痕迹是由于两个塑料熔体的前锋相交而形成的,当熔接痕的汇合角越大时,熔接痕性能越好,分析结果中熔接痕的角度在33.75~101.3 deg之间,位于产品边缘,相对性能一般。
2.5.2气穴气穴通常是由于型腔中的气体以及混合在注塑熔体中的气体无法顺畅地排放而产生的[5]。
分析结果中,空泡主要发生在产品的内部的折角上,而在产品的表面几乎没有。
在设计模具的时候,合理的设计出的排气槽将会降低气穴的出现。
2.6缩印分析产品在经过冷却成型之后,往往会存在一些微小的凹陷,不仅影响产品的外观,而且对产品的性能也可能存在影响。
分析结果表示,产品收缩幅度小于0.0468mm,这是一个很小的数值。
2.7冷却结果分析在注塑过程中,塑料以高温度的熔体状态下充填并保持压力,为了加速制品的注射过程,冷却系统需要进行迅速冷却,让产品达到顶出温度。
经过仿真分析得出了结果,入口和出口的温度差为0.42℃,比5℃小,冷却系统设计较为合理,满足了设计的需要[6]。
2.8翘曲分析结果产品在成型后会产生翘曲变形,注塑件造成翘曲的原因有很多,如不均匀的冷却、不均匀的收缩以及不均匀的分子定向内作用力等。
分析结果中,由于本产品中有较宽的薄壁并且在卡扣处,壁厚是不均匀的,所以主要的翘曲变形是由于收缩不均匀造成的。
本章小结在这一章中,使用UG8.0建模软件,以实际的产品为例,建立了一个3D模型,再使用 Moldflow软件对注射过程进行了仿真数据分析(1)浇口设计采用侧浇口,并对其浇注系统以及冷却系统的结构进行了构造,并对其进行了仿真分析,结果表示设计的注射系统可以使用(2)通过仿真注射成型,以检验该模具设计的可行性,并进一步提高了工作效率。
(3)注塑成形时,由于制品壁厚度不均匀,会导致产品成形时的收缩不均而产生变形,同时,冷却系统的合理设计也会使制品的成型时间大大减少。
3模具3D设计本章对模具进行结构分析和设计,其中,分模平面的选择、型腔的布置、浇注系统的设计、流道的设计、冷却系统的设计以及推出机构的设计都是其中的一个重要组成部分。
3.1分型面的选择在进行模具设计的过程中,对分型面的选择是非常重要的,分型面是将模具取出塑件和浇注系统凝料的可分离的接触面,它也是将工件或模具零件划分为特定模块的分割面[7]。
选择分型面的原则:(1)分型面应该设置在注塑产品的的最大投影点边缘部分,符合塑件基本脱模要求。
(2)将较大的注塑区域放置于动、定模的闭合区域,将较小的区域放置于侧面的分模区域,以达到锁定的目的。
(3)将塑料制品尽可能地放置在动模一侧,这样便于顶出,顶出的痕迹不会暴露在外部表面上[8]。
3.2型腔布置设计本次模具的型腔布局数量选择根据该产品的尺寸以及模具的结构设计的加工难易程度,考虑到倒扣比较多,为了节约模具设计制造的成本,并根据模流分析过程中的型腔布局,选定一模两腔的型腔布局。
3.3模具结构尺寸设计型腔是模具直接用于塑料制品成型的空腔部分。
设计模仁大小时,考虑产品为小件的产品,产品之间的距离是15~20mm。
当不是平面分型时,每个单独的产品需要8~10mm的封胶。
考虑浇口为侧浇口,分流道是直线,所以产品之间取16mm,产品到模仁边的距离也取8mm,缩小模仁大小的同时能满足强度要求。
6总结(1)本章利用UG8.0软件进行了模具结构的设计,并且完成了整套模具的装配。
(2)对汽车灯盖外壳塑件结构分析,确定模具型腔布局和分型面的选取。
(3)完成其他部件的设计,调用了模架,完成了整体模具的装配。
参考文献[1]郑道友. Moldflow塑料模具分析及项目实践[M]. 浙江大学出版社, 2014.8[2]叶久新, 王群. 塑料成型工艺及模具设计[M]. 北京: 机械工业出版社, 2007.[3]韩瑞云. MoldFlow分析在模具设计中的应用[J]. 今日科苑, 2015(11): 63.简介:沈雯(2001-),女,汉族,广西贺州,本科,研究方向:材料成型及控制工程项目:百色学院2022年大学生创新创业训练计划项目,名称:基于MoldFlow软件的注塑成型过程与工艺优化研究,编号:202210609172。