高光蒸汽注塑成型技术如何发挥优势
高光无痕注塑技术介绍

热变温急冷急热高光无痕注塑RHCM技术优势★ 消除产品表面熔接线;★ 增强原料流动填充效果,提高生产效率★ 提高产品表面光洁度,使之达到镜面效果;★ 产品无需后序喷漆加工处理;;★ 解决加纤产品所产生的浮纤现象。
热变温急冷急热高光无痕注塑RHCM技术分类①蒸汽高光无痕辅助成型技术该工艺加热介质为高温高压的饱和蒸汽,在蒸汽热效控制器的作用下,高温高压蒸汽,冷却水以及压缩空气按顺序输入至模具,使模具相应部位的温度急速升高及降低,从而使塑料制品获得良好表面。
该技术适合于大型热变温无痕注塑成型产品,如大型平板类显示器或相似产品,系当前最为广泛使用的热变温高光无痕注塑系统技术。
高温高压蒸汽通常来自于市政、电厂等机构的商品化管道蒸汽或企业外购的工业蒸汽燃气锅炉自制蒸汽,目前很多企业通过加装小型电加热环保蒸汽发生器自制蒸汽。
蒸汽压力和温度越高,生产效率越高,同时生产的稳定性以及产品的表面高光效果越好。
目前工业化生产中,当饱和蒸汽压力达到2.2MPa时,可以适配任何高光材料的温度要求。
②电热辅助成型技术既在多功能电热控制的作用下,将内置在模具中的加热元件迅速通电加温,使模具相应部位的温度升高及降低,从而使塑料制品获得良好表面质量的成型方法。
适合于小型热变温无痕注塑成型产品,如小尺寸平板类显示器或相似产品,但其模具技术较为复杂,模具冷却问题难度较大,且模具内置电加热部件的损耗寿命问题不太稳定,目前其应用领域和普及程度比蒸汽辅助技术还有差距。
③过热水辅助成型技术在过热水热效控制器的作用下,将热水机产生的高温热水(110-120度),冷却水以及压缩空气进行顺序切换输入至模具水路,从而达到使模具相应部位的温度升高及降低的整套设备。
④热油辅助成型技术设备在热油热效控制器的作用下,将热油机产生的高温热油与常温冷油进行顺序切换输入至模具油路,从而达到使用模具相应部位的温度升高及降低的整套设备。
在上述技术设备中,蒸汽辅助成型技术和电热辅助成型技术系当前主流的高光无痕技术方向,蒸汽辅助成型技术主要针对大中型产品;电热辅助成型技术则面向小型产品,该两项技术由于其高光效果完美、加热效率高、工艺稳定性高、良品率高等显著特点,在实际生产中已几乎涵盖了目前所有批量生产的高光无痕产品。
阐述塑料成型工艺中注塑成型的基本原理和优点

阐述塑料成型工艺中注塑成型的基本原理和优点1. 注塑成型的基本原理注塑成型,简单来说,就是把塑料颗粒加热融化,然后像打针一样,把它们注入一个模具中,等它冷却后,就变成我们想要的形状了。
这个过程其实就像我们小时候玩黏土,先把黏土捏软,再压成各种各样的形状,最后等它干掉就能拿去玩了。
不过,注塑成型用的材料是塑料,不是黏土,听起来是不是很酷?1.1 融化的过程首先,塑料颗粒在加热炉里受热,逐渐融化。
这时候,塑料就像变魔术一样,从固态变成了液态。
想象一下,你把冰淇淋放在阳光下,过了一会儿,它就融化成了一滩。
这个融化的过程可是很关键哦,因为只有这样,塑料才能顺利流进模具里。
1.2 注入的过程接下来,融化的塑料会通过一个很厉害的机械装置,被迅速注入到模具里。
这就像我们用注射器打针一样,速度快得惊人,几乎一瞬间就完成了。
模具里面的空间就像是个塑料的“家”,一旦塑料流进去,待会儿就能安家落户,变成各种各样的产品。
1.3 冷却与成型最后一步是冷却。
液态塑料在模具里待着,慢慢变得坚硬。
这时候,可以想象成一颗冰淇淋球在冰箱里冷却,慢慢定型。
等到冷却完成,我们打开模具,哇!一件全新的塑料制品就诞生啦!就这样,注塑成型的神奇过程完成了,简直是科技的结晶。
2. 注塑成型的优点接下来说说注塑成型的优点,真是一堆好处让人眼前一亮啊!2.1 生产效率高首先,注塑成型的生产效率可是杠杠的。
一次可以生产出很多件产品,尤其适合大规模生产。
想想看,咱们日常生活中见到的各种塑料瓶、玩具,都是通过这种方法快速造出来的,真是让人赞叹不已。
2.2 复杂形状也能做其次,注塑成型可以做出复杂的形状,这一点简直是太神奇了!比如说,咱们见到的那些精致的小玩具,形状各异,五花八门,都是这种工艺的功劳。
可以说,只要模具设计得好,几乎没有什么不可以的。
2.3 成本低再来就是,虽然初期模具的制作成本稍微高点,但一旦模具做好了,后续的生产成本就降下来了,简直就是物美价廉的代表。
蒸汽注塑技术的一些事儿

蒸汽注塑技术的一些事儿如何生产出无熔痕、无流痕、无流线、无缩痕,表面高光的外壳产品,对于平板电视机、电脑液晶显示器、空调、汽车内饰件来说尤为重要。
使用高光注塑技术就可以很好地解决此问题。
高光注塑的工艺原理在合模前及合模过程中对模具进行加温、合模完成后,温度达到设定条件即进行注射。
注射过程中模具继续维持高温,这样可以使胶料注射时在模具内保持很好的流动性。
注射完成,在保压冷却时,则对模具进行降温处理,又可以大大缩短制品的冷却时间,从而提高生产效率。
蒸汽无痕高光注塑技术目前在国内尚属于一项先进的生产工艺。
由于这一技术大大改善了制品的表面质量和表面强度,并可取消后续的喷涂或喷漆等工艺、既保护了环境和操作人员的人身健康,又因减少工艺流程,省去了昂贵的二次加工费用,在大幅度降低生产成本的同时,节省能源与材料。
传统工艺传统的做法是采用模温机对模具进行加温,但这种方法的不足之处如下:①无法满足高光注塑中快速升温及快速降温的需要;②升温幅度较小,制品表面的熔接痕只能得到减轻而无法消除;③由于塑料硬度越高,流动性越差。
因此采用此种工艺制品表面的硬度只能达到HB级无法满足实际使用需要;④模具升温时受热膨胀,降温时又会收缩,使锁模力很不稳定。
容易造成制品打不满,烧焦,内应力大等各种缺陷。
高光注塑技术在传统工艺基础上发展而来的蒸汽高光注塑技术则针对以上缺陷分别做了改进:①此技术在模具中开水管,需要升温时通蒸汽,需要降温时通冷水,冷却完毕后则用压缩空气将残留水分吹出,以确保能实现快速升温、降温;②以最大程度地消除熔接痕夹、水纹缺胶等各种制品故障;③由于升温幅度较大,宜使用H甚至2H硬度级别的塑料,使制品表面硬度大大提高;④由于在模具内部开设管道时,只对模具内表面进行升温或降温,模具的整体膨胀较小,因此减少了由于锁模力的不稳定而带来的各种制品缺陷。
高光注塑怎么做?这7个方法一定要记牢

高光注塑怎么做?这7个方法一定要记牢高光注塑技术又称快速热循环注塑技术,使用此技术可以很好地复制模具表面的任何形状,使制品件表面无熔痕,表面高光达到镜面效果;提高塑件强度和表面硬度;使薄壁成型提高注塑流动性,提高产品品质和强度;使厚壁成型注塑周期可降低60%以上;无需后续环境污染严重喷涂工艺,可减少工艺流程,节省能源与材料。
直接降低塑料制品的成本,保护环境和操作人员的人身健康。
接下来,我们为大家整理了做高光注塑时,需要注意一些什么?1、高温油传热的油温机模具内部设计均匀的加热或冷却管道,通过油加热系统达到模具预热的功效,同时在注射过程有冷却的作用。
最高温度可达350℃。
由于油的热传导系数低,效率较低,而且产生的油气影响高光成型质量,但效果比较不理想。
但目前企业油温机比较普遍,使用经验丰富。
2、高温高压水传热的高压水温机模具内部设计均衡的管道,不同阶段使用不同温度的水。
加热时通入高温过热水,冷却时切换为低温冷却水,实现模具表面的加热或冷却。
如将水加压,温升还可达140~180℃,升温很快。
高温高压的水温控制系统的制造厂商有:如奥德的GWS系统,由于热水可循环利用,运行成本较低,是目前国内市场上使用较多的一种,也是代替蒸汽的最佳选择。
3、蒸汽传热的蒸汽模温机同高压水温机作用原理相似,模具内部设计均衡的管道,加热时通入蒸汽,冷却时切换为低温水,实现模具表面的加热或冷却(蒸汽加热前一般还需要用压缩空气将管道吹干)。
高温高压蒸汽加热系统可使模具表面最高温度达到160℃。
由于蒸汽相对于水,其热容较小,相对升温时间较长。
达到150℃模具表面温度需要300℃左右的蒸汽。
但由于生产过程中蒸汽不可循环利用,需要安装锅炉设备和铺设管道等,致使其运行成本偏高。
4、电热管传热的电热模温机采取电阻加热元件(电热板,电热框,电热圈等)作为热源,其中电热管应用较多,它以金属管为外壳(包括不锈钢、紫铜管),沿管内中心轴向均布螺旋电热合金丝(镍铬、铁铬合金),其空隙填充压实具有良好绝缘导热性能的氧化镁砂,管口两端用硅胶密封。
蒸汽模高光注塑技术(急冷急热模)-应用探讨

三、3.1蒸塑件汽结构模的技优化术设计中的关键技术
蒸汽模成型技术作为高光无熔痕成型技 术之一,其塑件的结构设计与普通塑件不同, 即需要根据高光无熔痕模具的成型特点对塑 件进行优化设计,如制件的脱模斜度、圆角 过渡、螺钉柱固定结构等都需要调整,以满 足高光无熔痕注塑成型的工艺要求。
三、3.2蒸成型汽过模程模技拟和术浇注中系统的优化关键技术
二、2.2蒸模具汽温度模控技制系术统 所涉及的设备
模具温度控制系统包括: 冷却塔、蒸汽锅炉、 压缩机、高光温度控制柜等生产设备。该温 度控制系统有时也可用高光蒸汽模温机代替。 高光温度控制柜是系统非常关键的一部分, 它根据模具上的温度传感器反馈的温度控制 着高温蒸汽和冷却水的切换,并与注塑机控 制系统实时互换信号,从而进行熔体的注射、 保压以及开模顶出动作,以完成整个注塑过 程!整个注塑成型。
前后的对比。 从图3(a)可以看出,制件在Z轴方向的变形比较严重,翘曲现象
明显。从图3(b)可以看出,在Moldflow软件进行优化以后,Z 轴方向设置术与优中化 的关键技术
由于蒸汽管道和冷却管道是共用的,因此正确设置管道尤 型技术对蒸汽管道的排布讲究合理性和有效性。合理的排 提高注塑效率,而且起到使塑件受热和冷却更加均匀,减 的作用。其设计原则是:根据塑件形状特征来设计模具的 的随形冷却管道,实现模腔内部熔体温度的动态控制,使 动达到最佳状态。
蒸汽高光注塑技术 应用探讨
蒸1汽模技术的基本原理 蒸2汽模技术所涉及的设备
目录 蒸3汽模技术中的关键技术
蒸4汽模技术的优势 蒸汽5 模成型的主要影响因素
一蒸、汽模蒸成型汽技术模的技成型术工艺的过程基是: 本原理
模具合模后,首先在加热冷却管道内通入高 温蒸汽,把模具温度提高到一个高的设定值, 然后注射塑料熔体,在保压转入冷却后,用 气压吹走通道内的残留蒸汽,开始注入冷水, 使模具温度快速下降到一个设定值,再向加 热冷却管道内通入空气,把冷水完全吹走, 开模取制件,然后进入下一次注塑循环。
注塑模具设计中常见的优化思路与挑战

注塑模具设计中常见的优化思路与挑战注塑模具设计是制造注塑成型零件的关键步骤之一。
在实际的设计过程中,常常会遇到各种优化思路与挑战。
本文将介绍注塑模具设计中常见的优化思路与挑战,并提供相应的解决方案。
一、优化思路1. 减少制造成本:在注塑模具设计过程中,需要考虑如何降低成本,提高效率。
可以通过优化零件结构、减少模具制造工序、选择合适的材料等方式实现成本的控制。
2. 提高产品质量:注塑模具设计中,要考虑如何提高产品的外观质量、尺寸精度等方面的要求。
可以通过优化模具结构、选择合适的冷却系统、控制塑料流动等方式来提高产品质量。
3. 增加模具寿命:模具是一个昂贵的投资,因此延长模具的使用寿命对于生产企业来说非常重要。
在注塑模具设计中,可以优化模具结构、加强模具的冷却系统、提高模具材料的硬度等以延长模具的使用寿命。
4. 提高生产效率:在注塑模具设计中,可以通过优化模具结构、提高注塑机的性能、控制塑料的流动速度等方式提高生产效率。
5. 降低能源消耗:节能减排是当前社会的一个重要目标。
在注塑模具设计中,可以通过优化模具结构、控制塑料的流动速度、合理设计冷却系统等方式降低能源消耗。
二、挑战与解决方案1. 塑料流动性问题:塑料在注塑过程中的流动性会影响产品的质量和成型效果。
要解决这一挑战,可以通过优化模具结构、调整注射压力、控制塑料温度等方式来改善塑料的流动性。
2. 部件尺寸精度问题:注塑产品的尺寸精度是制造和测量过程中的一个关键问题。
要解决这一挑战,可以通过优化模具结构、控制注射速度、选择合适的冷却系统等方式来提高产品的尺寸精度。
3. 模具结构设计问题:在注塑模具设计中,模具的结构设计是一个重要的环节。
要解决这一挑战,可以采用模具流动分析、结构强度分析等技术手段,对模具的结构进行优化和改进。
4. 冷却系统设计问题:模具的冷却系统对于产品质量和生产效率都有重要影响。
要解决这一挑战,可以通过优化冷却系统的布局、选择合适的冷却介质、调整冷却时间等方式提高冷却效果。
注塑车间的效率提升手段
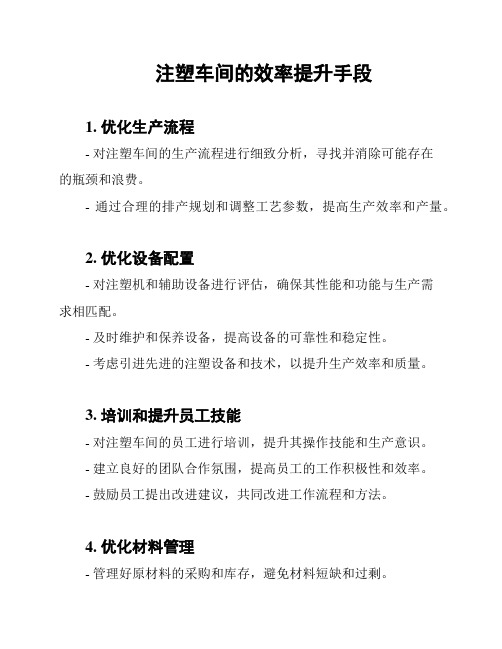
注塑车间的效率提升手段
1. 优化生产流程
- 对注塑车间的生产流程进行细致分析,寻找并消除可能存在
的瓶颈和浪费。
- 通过合理的排产规划和调整工艺参数,提高生产效率和产量。
2. 优化设备配置
- 对注塑机和辅助设备进行评估,确保其性能和功能与生产需
求相匹配。
- 及时维护和保养设备,提高设备的可靠性和稳定性。
- 考虑引进先进的注塑设备和技术,以提升生产效率和质量。
3. 培训和提升员工技能
- 对注塑车间的员工进行培训,提升其操作技能和生产意识。
- 建立良好的团队合作氛围,提高员工的工作积极性和效率。
- 鼓励员工提出改进建议,共同改进工作流程和方法。
4. 优化材料管理
- 管理好原材料的采购和库存,避免材料短缺和过剩。
- 优化物料配送和储存方式,减少搬运和等待时间。
- 加强对材料质量的控制和检测,确保生产过程中的一致性和
稳定性。
5. 引入自动化和信息化技术
- 引入自动化设备和生产线,减少人工操作,提高生产效率和
精度。
- 建立信息化系统,实时监控生产数据和设备状态,及时发现
和解决问题。
- 利用数据分析和优化算法,提高生产计划的准确性和可执行性。
以上是提升注塑车间效率的一些手段,通过优化生产流程、设
备配置、员工技能、材料管理和引入自动化技术,可以达到提高生
产效率和质量的目标。
同时,持续改进和创新也是提升效率的关键,注塑车间应不断探索新的方法和策略,以适应市场需求的变化。
注塑工艺写自己的优势

注塑工艺写自己的优势
作为注塑工艺的专业从业者,我具备以下优势:
1. 丰富的经验:我在注塑工艺领域拥有多年的从业经验,通过参与各类项目和工作,积累了丰富的实践经验和解决问题的能力。
2. 深刻的理论知识:我具备深入的注塑工艺的理论知识,掌握了塑料材料的性质和特点、注塑机的原理和操作方法,能够准确理解并分析注塑工艺中的各个环节。
3. 熟练的操作技能:我熟悉各种注塑设备的操作和维护,能够熟练掌握注塑工艺的各项操作步骤,确保生产过程的安全和高效。
4. 优秀的问题解决能力:在注塑过程中,常常会遇到各种问题,如产品质量不合格、设备故障等,我通过多年的实践经验和学习,具备了快速分析问题和解决问题的能力。
5. 结果导向的工作态度:我注重效率和质量,努力追求优秀的工作结果。
在注塑工艺中,我注重细节,并且能够根据需求灵活调整工艺参数,确保生产的产品质量达到客户的要求。
总之,我在注塑工艺方面积累了丰富的经验和知识,具备优秀的操作技能和问题
解决能力,并以结果导向的工作态度为目标,为满足客户需求提供高质量的注塑工艺服务。
提高注塑生产效率的方法
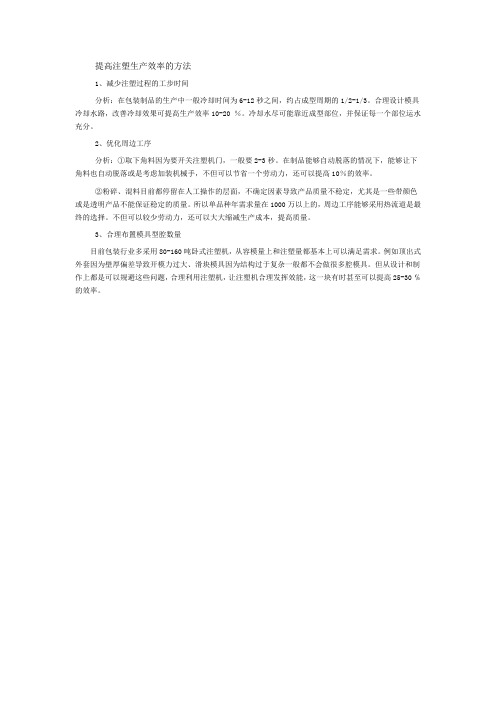
提高注塑生产效率的方法
1、减少注塑过程的工步时间
分析:在包装制品的生产中一般冷却时间为6-12秒之间,约占成型周期的1/2-1/3。
合理设计模具冷却水路,改善冷却效果可提高生产效率10-20 %。
冷却水尽可能靠近成型部位,并保证每一个部位运水充分。
2、优化周边工序
分析:①取下角料因为要开关注塑机门,一般要2-3秒。
在制品能够自动脱落的情况下,能够让下角料也自动脱落或是考虑加装机械手,不但可以节省一个劳动力,还可以提高10%的效率。
②粉碎、混料目前都停留在人工操作的层面,不确定因素导致产品质量不稳定,尤其是一些带颜色或是透明产品不能保证稳定的质量。
所以单品种年需求量在1000万以上的,周边工序能够采用热流道是最终的选择。
不但可以较少劳动力,还可以大大缩减生产成本,提高质量。
3、合理布置模具型腔数量
目前包装行业多采用80-160吨卧式注塑机,从容模量上和注塑量都基本上可以满足需求。
例如顶出式外套因为壁厚偏差导致开模力过大、滑块模具因为结构过于复杂一般都不会做很多腔模具。
但从设计和制作上都是可以规避这些问题,合理利用注塑机,让注塑机合理发挥效能,这一块有时甚至可以提高25-30 ℅的效率。
注塑解决方案

注塑解决方案
《注塑解决方案:优化生产效率,降低成本》
注塑是一种常见的塑料制造工艺,也是许多行业中常用的生产方法。
然而,注塑过程中可能会遇到一些问题,如产品质量不稳定、生产效率低、耗材浪费等。
因此,寻找注塑解决方案是许多企业面临的挑战。
为了优化生产效率和降低成本,企业需要寻找适合自己的注塑解决方案。
首先,企业可以考虑使用先进的注塑设备,如高速注塑机、多螺杆注塑机等,这些设备可以提高生产效率和降低能耗。
另外,企业还可以采用智能化的注塑生产管理系统,实现生产过程的自动化和智能化,从而进一步提高生产效率。
除了设备和系统的升级外,注塑解决方案还需要关注产品设计和模具制造。
通过优化产品设计和模具制造工艺,可以降低产品成本、缩短生产周期,并且提高产品质量。
同时,企业还可以采用高性能的注塑材料,如工程塑料、特种塑料等,来提升产品的性能和品质。
在实施注塑解决方案的过程中,企业需要综合考虑生产成本、产品质量、生产效率等多方面因素,并根据自身的实际情况进行调整和优化。
通过寻找合适的注塑解决方案,企业可以实现生产效率的提升和成本的降低,从而在激烈的市场竞争中获得更大的优势。
高光注塑技术的原理及应用
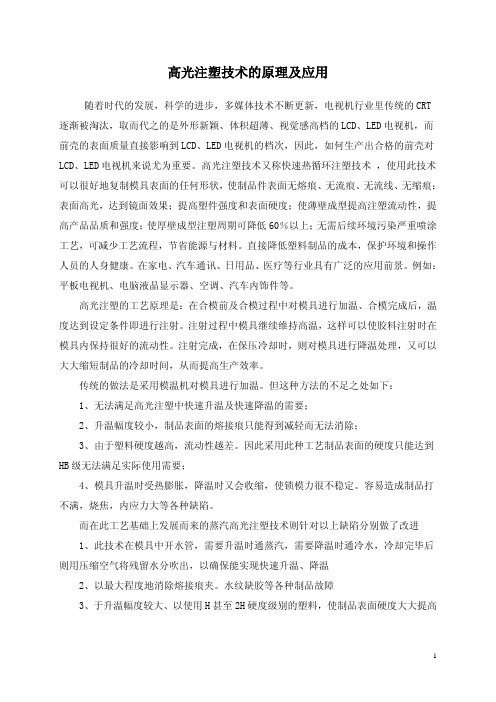
高光注塑技术的原理及应用随着时代的发展,科学的进步,多媒体技术不断更新,电视机行业里传统的CRT 逐渐被淘汰,取而代之的是外形新颖、体积超薄、视觉感高档的LCD、LED电视机,而前壳的表面质量直接影响到LCD、LED电视机的档次,因此,如何生产出合格的前壳对LCD、LED电视机来说尤为重要。
高光注塑技术又称快速热循环注塑技术,使用此技术可以很好地复制模具表面的任何形状,使制品件表面无熔痕、无流痕、无流线、无缩痕;表面高光,达到镜面效果;提高塑件强度和表面硬度;使薄壁成型提高注塑流动性,提高产品品质和强度;使厚壁成型注塑周期可降低60%以上;无需后续环境污染严重喷涂工艺,可减少工艺流程,节省能源与材料。
直接降低塑料制品的成本,保护环境和操作人员的人身健康。
在家电、汽车通讯、日用品、医疗等行业具有广泛的应用前景。
例如:平板电视机、电脑液晶显示器、空调、汽车内饰件等。
高光注塑的工艺原理是:在合模前及合模过程中对模具进行加温、合模完成后,温度达到设定条件即进行注射。
注射过程中模具继续维持高温,这样可以使胶料注射时在模具内保持很好的流动性。
注射完成,在保压冷却时,则对模具进行降温处理,又可以大大缩短制品的冷却时间,从而提高生产效率。
传统的做法是采用模温机对模具进行加温。
但这种方法的不足之处如下:1、无法满足高光注塑中快速升温及快速降温的需要;2、升温幅度较小,制品表面的熔接痕只能得到减轻而无法消除;3、由于塑料硬度越高,流动性越差。
因此采用此种工艺制品表面的硬度只能达到HB级无法满足实际使用需要;4、模具升温时受热膨胀,降温时又会收缩,使锁模力很不稳定。
容易造成制品打不满,烧焦,内应力大等各种缺陷。
而在此工艺基础上发展而来的蒸汽高光注塑技术则针对以上缺陷分别做了改进1、此技术在模具中开水管,需要升温时通蒸汽,需要降温时通冷水,冷却完毕后则用压缩空气将残留水分吹出,以确保能实现快速升温、降温2、以最大程度地消除熔接痕夹。
注塑工厂节约成本、提升效率的10个方法
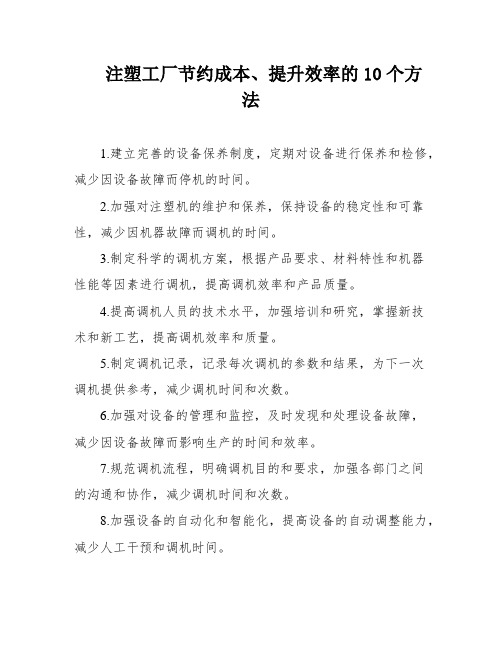
注塑工厂节约成本、提升效率的10个方法1.建立完善的设备保养制度,定期对设备进行保养和检修,减少因设备故障而停机的时间。
2.加强对注塑机的维护和保养,保持设备的稳定性和可靠性,减少因机器故障而调机的时间。
3.制定科学的调机方案,根据产品要求、材料特性和机器性能等因素进行调机,提高调机效率和产品质量。
4.提高调机人员的技术水平,加强培训和研究,掌握新技术和新工艺,提高调机效率和质量。
5.制定调机记录,记录每次调机的参数和结果,为下一次调机提供参考,减少调机时间和次数。
6.加强对设备的管理和监控,及时发现和处理设备故障,减少因设备故障而影响生产的时间和效率。
7.规范调机流程,明确调机目的和要求,加强各部门之间的沟通和协作,减少调机时间和次数。
8.加强设备的自动化和智能化,提高设备的自动调整能力,减少人工干预和调机时间。
9.对设备进行优化和改进,提高设备的性能和稳定性,减少设备故障和调机时间。
10.加强对设备的监控和预警,及时发现和处理设备故障,减少因设备故障而影响生产的时间和效率。
2.在指定区域按机台摆放需要填加的材料,并为每台机的材料标记明确的标识,以避免加错料。
3.使用机边自动吸料机代替人工上料。
4.采用中央供料系统和色母比例阀,实现自动供料。
5.改良盛料桶,降低加料频率,以减少加料人员。
1.在碎料房增加碎料机,按原料种类和颜色分机台碎料,减少清理碎料机的工作量。
2.制作胶箱支架,减少碎料员取拿水口的时间及降低劳动强度。
3.使用自动化传输带碎料机,减少碎料员的工作量(一个人可使用两台同是碎料)。
4.将碎料机摆放区域隔离开,以免交叉污染。
严格控制机位水口料的纯净度,减少碎料员清理水口料中的异物时间。
5.通过提高模具质量、注塑技术和管理水平,控制不良品和水口料量,减少碎料员的工作量。
6.采用热流道系统的模具,减少水口料,减少碎料量。
7.使用机边碎料机,实现自动化、无人化碎料。
8.碎料机停用时,盖上防尘罩,减少清理碎料机的工作量。
科技成果——高光快速注塑成型技术

科技成果——高光快速注塑成型技术
不少于1500字
摘要:随着科学技术的发展,注塑成型技术作为一种重要的成型技术,已经被广泛应用在各行各业里,特别是当前工业的发展处于快速增长阶段,注塑成型技术必将发挥重要的作用。
高光快速注塑成型技术就是在传统注
塑成型技术的基础上,使用射频高光技术(RFID),用新材料,新技术制
造出精细耐用的成型产品。
本文结合实例对该技术进行介绍,并对它的优点、缺点及可能的作用进行讨论,以印证这一先进的技术成果在工业上的
发展前景及应用前景。
关键词:高光快速注塑成型技术、射频高光、新材料、新技术
Introduction
随着科学技术的发展,注塑成型技术作为一种重要的成型技术,已经
被广泛应用在各行各业里,以较快的速度生产出精细耐用的产品。
然而,
在传统的注塑成型技术中,以塑胶为原材料,生产时的口穴和外观尚存在
粗糙度和复杂程度等问题,因而影响成垁的效果。
针对这样的情况,科学
家们在传统注塑成型技术的基础上,于2024年推出了一款全新的成型技术,高光快速注塑成型技术。
Overview of the Technology。
如何优化注塑成型生产

如何优化注塑成型生产注塑成型生产是现代工业生产中常见的一种生产工艺,优化注塑成型生产可以提高生产效率和产品质量。
以下是几种优化注塑成型生产的方法:1.优化原材料选择:-选择合适的原材料,根据产品要求选择适合的塑料类型和牌号,确保原材料质量稳定,避免出现不均匀溶解、熔断、气泡等问题。
-避免回料使用过多,回料使用过多可能会影响产品的物理性能和外观质量。
-进行材料配方优化,通过调整不同原料的比例,可以提高产品的性能和成本效益。
2.优化模具设计和制造:- 设计合理的注塑模具,减少产品缺陷的可能性。
合理设计产品形状、壁厚、流道等参数,防止模具内部出现气泡、短-shot等问题。
-优化模具材质,选择高强度、高耐磨、高导热的材料,延长模具寿命,减少维护与更换的频率。
-使用先进的模具加工设备,如CNC机床、电火花等,提高模具制造的精度和效率。
3.优化注塑工艺参数:-合理设置注塑机的温度、压力、速度等参数,以保证塑料的熔融、流动、充实和冷却等过程的顺利进行,避免产品缺陷的产生。
-优化冷却系统,确保注塑件在注射后能迅速降温固化,快速脱模,提高生产效率。
-确定合适的注射时间和保压时间,以提高产品的密实性和抗拉强度。
4.优化生产管理:-采用先进的生产管理系统,对注塑成型生产过程进行实时监控和数据分析,及时发现问题和异常,进行调整和改进。
-通过对生产设备的定期维护和保养,保证设备的正常运转和稳定性,减少生产故障和停机时间。
-建立完善的质量管理体系,通过严格的质量控制和检验,确保产品的质量稳定,减少次品率。
-增强员工的培训和技能提升,提高操作人员的技术水平,增强团队协作能力和问题解决能力。
5.推广绿色生产:-推广节能、环保的注塑成型生产工艺和设备,减少资源消耗和排放,降低对环境的污染。
-优化产品设计,减少使用材料和能源的数量,降低产品的包装和运输成本。
-建立可持续发展的生产模式,鼓励循环再利用和废弃物的再处理,减少对自然环境的负面影响。
注塑工作亮点总结范文

一、前言在过去的一年里,我司注塑车间全体员工在公司的正确领导下,紧紧围绕公司发展目标,积极投身于注塑生产工作。
在此,我对本年度注塑工作的亮点进行总结,以期在今后的工作中更好地发扬优势,改进不足。
二、工作亮点1. 机台保养方面本年度,注塑车间在机台保养方面取得了显著成效。
我们严格执行保养计划,定期对机台进行清洁、润滑、检查和维修,确保了设备的高效运行。
通过实施保养,设备故障率同比下降了30%,生产效率提高了15%。
2. 调模具的效率和质量在调模具方面,我们注重效率与质量的提升。
通过优化调模流程,缩短了调模时间,提高了模具的合格率。
例如,在调模过程中,我们采用了先进的自动化设备,将调模时间缩短了20%,同时,模具合格率达到了98%。
3. 二次料使用在原材料成本控制方面,我们积极推广二次料的使用。
通过优化工艺参数,降低了二次料的损耗,同时保证了产品质量。
据统计,本年度二次料的使用节省了约10%的原材料成本。
4. 产品质量提升在产品质量方面,我们加大了品管力度。
通过严格把控生产过程中的每一个环节,注塑出来的产品毛刺、缺边、飞边等不良品率降低了40%,产品质量得到了明显提升。
以下是几个典型案例:- 产品A:通过优化模具设计,提高了产品的尺寸精度,合格率从90%提升至95%。
- 产品B:针对产品C在生产过程中出现的变形问题,我们调整了生产工艺,使得产品C的变形率降低了50%。
5. 产能和机台利用率提升在产能和机台利用率方面,我们通过优化生产计划,合理安排生产任务,使得产能提高了15%,机台利用率达到了90%。
6. 员工思想教育在员工思想教育方面,我们注重提高员工的安全意识和责任感。
通过开展安全培训、技能竞赛等活动,员工的安全意识和技能水平得到了显著提高。
此外,我们还建立了完善的绩效考核制度,激发了员工的工作积极性。
三、总结总之,过去一年,注塑车间在机台保养、调模效率、二次料使用、产品质量、产能和机台利用率以及员工思想教育等方面取得了显著成果。
RHCM“蒸汽无痕高光注塑”技术的优越性

RHCM“蒸汽无痕高光注塑”技术的优越性蒸汽无痕高光注塑技术是透过运用蒸汽将模具表面快速升温,令成型模腔表面温度达到树脂塑料的玻璃转移温度(TgGlassTransitionTemperature)以上,然后开始进行射出成型,当完成模腔填充过程后,立刻利用水作为冷却媒体使模具表面温度急速下降,从而更改塑料产品表面特性。
RHCM“蒸汽无痕高光注塑”技术进展至今已近4年之多,由2023年德国K—Show中正式开始公布,直到2023年中国电视生产商才开始使用在生产液晶平板电视外壳上。
其实早在2023年韩国Samsung(三星)公司已开始使用RHCM“蒸汽无痕高光注塑”技术生产LCD液晶平板电视外壳,其中重要优点是可以使树脂塑料产品外壳拥有高光泽度;除去了传统注塑成型工艺存在的熔接痕问题,并省却了产品二次加工的必要和有关的成本RHCM注塑成型技术与传统注塑成型工艺相比之下,能大大改善产品表面光泽度,解决产品表面熔接痕问题,并对提升产品表面硬度也有肯定帮忙.另外,RHCM注塑成型技术也可以应用到添加纤维的工程塑料中,能够有效解决产品表面浮纤的问题。
熔接痕的形成是由两股或以上的融熔塑料在射出成型的填充过程中,融熔塑料流的波形前端在模腔中相遇会合,假如模腔表面温度不足或流体遇合压力不足,便会造成合流端无法*熔合,形成产品表面显现熔接痕缺陷;另外,如塑料中含有添加物(例如:色母),在熔合位置更会显现较为明显的颜色差异。
然而,运用RHCM注塑技术,让我们可以在每次开始进行射出成型过程之前,把模腔表面温度快速提升至树脂塑料的热变形温度以上(HDT),从而大大加添融熔塑料在模腔内的流动性,减低融熔塑料与模腔表面之间的磨擦阻力,显著地除去传统注塑工艺产品表面的熔接痕问题。
除此之外,RHCM搭配特别工程塑料更可生产出无痕高光泽度的树脂产品,省却产品因表面外观要求,而进行的二次加工RHCM技术另一项优点是,能够显著除去添加纤维的改性工程塑料产品表面纤维外露的问题。
蒸汽高光注塑的应用探讨
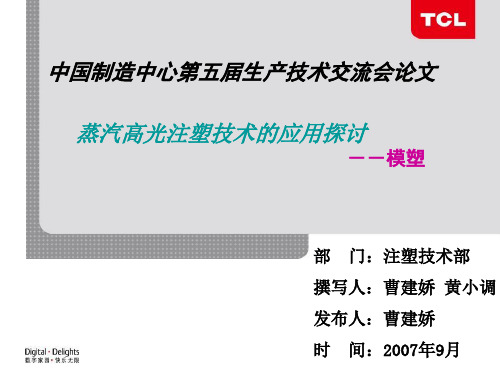
五.我们为什么要选择蒸汽注塑及其工作原理:
我们现阶段的高光注塑面临的问题: (1)由于高光产品的市场需求越来越大,那么用先 进的成型工艺技术稳定的进行高光注塑就势在必行 (2)高光产品计划的紧张,产品交期的完全可控需 要稳定的生产来保障 (3)制造成本的压力,产品不良率的偏高也急待解 决 (4)行业内的技术竞争,率先掌握先进的工艺技术 是我们的产品竞争力提升的标志之一
Page 4
四.传统高光注塑的缺点及原因分析:
1.夹水线 夹水线不能完全消除,用时间控制器顺序进胶以后,至少还会有一 条夹水线,影响产品外观
Page 5
夹水线
2. 料花 由于要防止夹水线的产生需控制每个浇口的开启及 关闭的时间,一般精确到0.1秒,但由于不同部位 的溶胶的流速会有差异,时间不易控制精确,经常 会导致在浇口的下方产生料花,有料花的产品肯定 是不良品
Page 21
欢迎您的批评,指正;期待与您沟通,交流!
谢谢
Date: 2007.05.09 Page 22
Page 6
料花易产 生部位
3.缩水 由于产品采用了气辅成型,产品结构及充气的不稳 定因素会导致产品筋位或柱位的时常缩水,并有类 似缩水的气道印
Page 7
废品主要类型
模具 名称 报废品类型 良品 废品 报废 数 料花 气纹 油点 模花 气爆 缩水 夹水纹 走胶 白印 其他 数 率 126 273 610 906 73 86 35 349 79 463 178 520 22 720 792 774 252 1818 203 732 68 1003 53 148 51 252 95 202 33 330 66 3737 22.1%
中国制造中心第五届生产技术交流会论文
RHCM工艺介绍
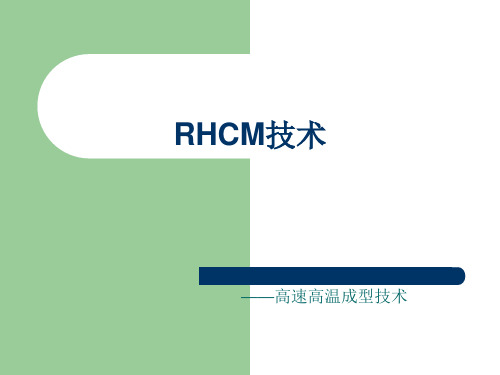
RHCM与传统制程的模具温度差异
优点
1、消除溶接线、溶接痕、波纹、银丝纹。
使用RHCM技术
使用常规技术
2、解决浮纤现象;
3、提高薄壁成型注塑流动性;
使用RHCM技术
使用常规技术
4、彻底解决表面缩水现象;
使用传统技术
使用RHCM技术
5、可省略喷漆加工,提高成品率; 6、使表面光洁度可达到镜面; 7、降低厚壁成型注塑周期。
技术要求
模具表面质量。良好的抛光性、耐腐蚀性、热 强度和热膨胀系数。 模具内部管道。水路的设计分层设置 。 模具零件。运动配合部分的隔热、密封、配合 良好 。 模温控制。热传递+热辐射。
缺点
模具维护复杂。 良率不高,80%左右 。 成本较高. 表面硬度仍旧不高 (Rapid Heat Cycle Molding):高速高温成
型技术,又称为高光无熔接痕注塑技术、蒸汽模具技 术。
原理
当合模后吹入高温蒸气或高温热水,首先把模 具温度提高,然后开始给模腔注射塑胶,在注塑 机完成保压转入冷却后,开始注入冷水,模具温 度很快下降,再向模具吹入空气把冷水完全吹 走,完成整个注塑过程。
- 1、下载文档前请自行甄别文档内容的完整性,平台不提供额外的编辑、内容补充、找答案等附加服务。
- 2、"仅部分预览"的文档,不可在线预览部分如存在完整性等问题,可反馈申请退款(可完整预览的文档不适用该条件!)。
- 3、如文档侵犯您的权益,请联系客服反馈,我们会尽快为您处理(人工客服工作时间:9:00-18:30)。
首先,注射前通过喷射蒸汽,使模具的温度达到超过树脂热变形的温度,然后注射熔融树脂,就会形成没有汇线、表面品质良好的成型品。
熔融树脂注射完成后,便开始冷却工序。
用冷却水使模具温度迅速下降到树脂热变形的温度以下。
这样,可以通过加快树脂的固化速度,来缩短成型周期,解决翘曲、下陷等问题。
高光蒸汽注塑可消除产品表面溶接线、溶接痕、波纹及银丝纹,彻底解决塑料产品的表面缩水现象,并使产品表面光洁度达到镜面水平。
产品不需要喷涂的后续加工,有效降低成本,缩短交货时间。
此外,高光注塑还可解决加纤产品所产生的浮纤现象,从而使产品品质更加完美。
在薄壁成型中,高光注塑有助于提高注塑流动性,提高产品质量与强度。
它也可使厚壁成型注塑周期降低70%以上。
奥德的高光急冷急热模温机具有8寸液晶真彩西门子LCD显示,触摸式中文数子输入,全中文界面,操作简单。
全闭环系统控制输入输出温度的检测,以模具实际温度反馈PLC,数彩图变化显示,确保输出准确稳定。
蒸汽、冷水、及模具温度显示,用时间和动作与注塑机信号互锁。
高光蒸气注塑应用目前用于液晶电视机,电脑液晶显示器,汽车液晶显示器,车灯和光学仪器等行业。
来源:模温机转载注明。