煅烧温度和时间对熟料质量的影响
生料质量对水泥熟料煅烧的影响
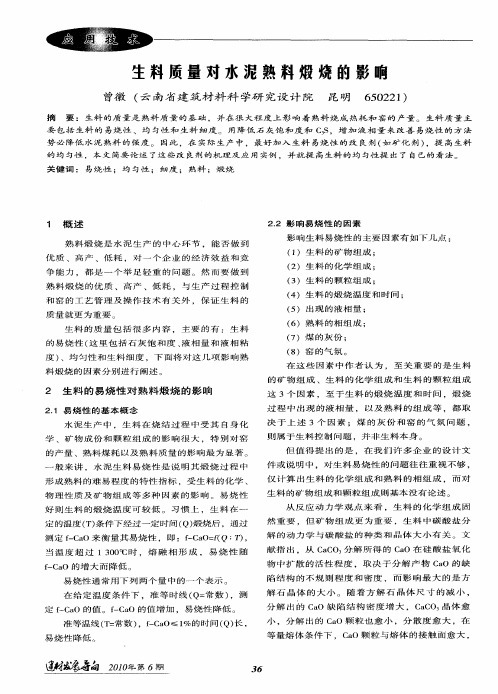
22 影 响 易 烧 性 的 因 素 .
影 响生 料 易烧性 的主 要 因素有 如 下几 点 : ( )生 料 的 矿 物 组 成 ; 1 ()生 料 的化 学组 成 ; 2
解 石 晶体 的 大小 。随 着 方 解 石 晶体 尺 寸 的减 小 , 分 解 出 的 C O 缺 陷 结 构 密 度 增 大 ,Ca a CO。 体 愈 晶
小 , 分 解 出 的 C O 颗 粒 也 愈 小 , 分 散 度 愈 大 ,在 a
易烧 性降 低 。
等 量 熔 体 条 件 下 .C O 颗 粒 与 熔 体 的 接 触 面 愈 大 , a
测 定 f c 0来 衡 量 其 易 烧 性 , 即 : fc 0: ( : ) _a . a ,Q T , 当 温 度 超 过 1 3 O【时 , 熔 融 相 形 成 , 易 烧 性 随 0c = f C 0 的增 大 而 降 低 。 - a
易烧性 通 常用 下 列两 个 量 中的一 个 表示 。
定 的 温度 ( 条 件 下 经 过 一 定 时 间 ( 煅 烧 后 ,通 过 T) Q)
仅 计 算 出 生 料 的 化 学 组 成 和 熟 料 的 相 组 成 , 而 对
生 料 的矿 物 组 成 和 颗 粒 组 成 则 基 本 没 有 论 述 。 从 反 应 动 力 学 观 点 来 看 , 生 料 的 化 学 组 成 固 然 重 要 。但 矿 物 组 成 更 为 重 要 , 生 料 中 碳 酸 盐 分 解 的 动 力 学 与 碳 酸 盐 的 种 类 和 晶 体 大 小 有 关 。 文
石灰回转窑煅烧参数
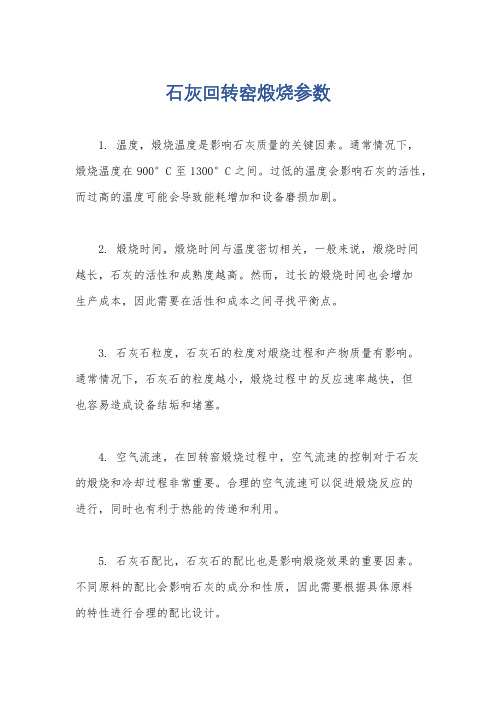
石灰回转窑煅烧参数
1. 温度,煅烧温度是影响石灰质量的关键因素。
通常情况下,
煅烧温度在900°C至1300°C之间。
过低的温度会影响石灰的活性,而过高的温度可能会导致能耗增加和设备磨损加剧。
2. 煅烧时间,煅烧时间与温度密切相关,一般来说,煅烧时间
越长,石灰的活性和成熟度越高。
然而,过长的煅烧时间也会增加
生产成本,因此需要在活性和成本之间寻找平衡点。
3. 石灰石粒度,石灰石的粒度对煅烧过程和产物质量有影响。
通常情况下,石灰石的粒度越小,煅烧过程中的反应速率越快,但
也容易造成设备结垢和堵塞。
4. 空气流速,在回转窑煅烧过程中,空气流速的控制对于石灰
的煅烧和冷却过程非常重要。
合理的空气流速可以促进煅烧反应的
进行,同时也有利于热能的传递和利用。
5. 石灰石配比,石灰石的配比也是影响煅烧效果的重要因素。
不同原料的配比会影响石灰的成分和性质,因此需要根据具体原料
的特性进行合理的配比设计。
除了上述参数外,还有其他一些影响石灰回转窑煅烧的因素,如燃料选择、窑速控制、窑体结构等。
综合考虑这些参数,可以优化石灰回转窑煅烧的生产工艺,提高石灰的质量和产量,降低能耗和生产成本。
原燃材料质量波动对熟料煅烧的影响

27 . 27 .5
27 .4
9 .8 95
9 . ’ l 97 37 6
6 中 国 水 泥 2 1 .0 0 11
项 目 铜 矿 渣 含铁 量 / % 熟 料 2 d强 度 /MP ) 8 ( a
Fl — 4. 02 53 8
F2 一 3- 94 5. 79
高 ,当然较用最理 想 的煤 粉仍然有 些差距 。分 析原 因 是 。 生料率值均 没有变化 的情况 下 , 在 煤的发热量 越低
的差异 和液 相性 的不 同 , 熟料 煅 烧温 度 和形成 晶体 反
应时 间 的不 同 .原燃 材料 质量 的波 动及 品位 的高 低 ,
耗煤就会 增加 , 熟料整个 预热 、 在 分解 、 烧过程 中 , 煅 因
A 灰 石 石
B 灰 石 石
4. 3 5
4. 1 9
0 0 3 0 1 5 . 36 _ . 4 34
12 1 6 05 5 . 3 . 4 0 26
1 . 6
1 . 8
9 . 08 6 28 1 2 O9 9 .9 . 2 4 . .8 4
(h t) /
l 11 2.
头 煤 l 尾 煤
69 . 99 .
合 计
l. 68
a O合 格 率/ %
9. 09
强 度/MP ) a 3 d 2d 8
3. 08 5. 88
B 煤
24 . 4
2. 05 5
2 72 4
4. 92 6
‘
∑ fO K S C H a M
9 .4 73 14 . 7 0 O8 .5 O8 1 .9 08 9 8
.
I M
浅谈水泥熟料微观结构及其质量性能

Cement production 水泥生产1浅谈水泥熟料微观结构及其质量性能李成恩(葛洲坝当阳水泥有限公司 444103)中图分类号:TQ172 文献标识码:B 文章编号1007-6344(2017)04-0001-01摘要:随着经济的发展,促使建筑行业也有了质的飞跃,然而在建筑中水泥的应用是必不可少的,水泥熟料的质量性能决定了建筑的安全性,对水泥熟料的微观结构进行有效的分析,进而加强其质量性能的确定。
关键词:水泥熟料;微观结构;质量性能引言:水泥熟料微观结构也就是其在显微镜下的形态,其会因原材料和工艺因素的不同而有显著的变化。
也就是熟料微观结构与原材料和工艺因素密切相关,并从本质上影响着熟料的性能。
这样,水泥熟料的微观结构不仅记录了矿物的形成和生长的全过程,也反映了全过程的工艺因素,以及因工艺因素不同而变化了的水泥熟料诸多物性。
1.水泥熟料的形成生料在窑内经过干燥、预热、分解、烧成及冷却等阶段形成熟料。
硅酸盐水泥熟料主要由硅酸三钙(C3S)、硅酸盐二钙(C2S)、铝酸三钙(C3A)、铁铝酸四钙(C4AF)等矿物所组成。
生料通常是用石灰石、黏土及少量铁矿石等按适当的比例配制而成。
石灰石的主要组成是碳酸钙(CaCO3)和少量的碳酸镁(MgCO3),黏土的主要矿物是高岭石(SiO2·2Al2O3·2H2O)及蒙脱石(Al,Mg)2[(OH)2|Si4O10](Na,Ca)x*nH2O 等,铁矿石的主要组成是氧化铁(Fe2O3)。
硅酸盐水泥熟料形成的过程,实际上是石灰石、黏土、铁矿石等主要原料经过加热发生一系列物理化学变化形成C3A、C4AF、C2S和C3S等 矿物的过程,不论窑型的变化如何,其过程是不变的。
2.水泥熟料的特征水泥熟料是以石灰石和粘土等作为原料在部份熔融状态下烧成的,通过固液相反应形成矿物。
因此它的成分是不均一的,是多种矿物的集合体。
我们用肉眼观察熟料,从外观可以看到颗粒大小、形状、表面状态、色泽等,把熟料颗粒打碎,还可看到内部的致密程度等。
煅烧温度和时间对熟料质量的影响

煅烧温度和时间对熟料质量的影响纯阅读作者:刘天振单位:淮海中联水泥有限公司来源:发布日期:2013—08-15影响熟料质量方面因素很多,但熟料在窑内煅烧是最重要环节之一.熟料矿物形成实际上是在液相量出现以后进行的.影响熟料质量方面因素很多,但熟料在窑内煅烧是最重要环节之一。
熟料矿物形成实际上是在液相量出现以后进行的.液相主要有氧化铁、氧化铝、氧化钙所组成(包括其他次要组分氧化镁、氧化钾、氧化钠等),在高温液相作用下,C2S逐渐溶解于液相中与f-cao化合成C3S,随着温度升高和时间延长,C3S晶核不断形成,小晶体逐渐长大,最终形成阿里特晶体.完成熟料的烧结过程。
实践证明,C3S的生成,如果熟料配料时三率值KH、N、P适当,生料成分稳定的条件下,主要取决于熟料煅烧温度、液相量、液相性质以及形成晶体反应时间。
本文重点介绍熟料煅烧温度和晶体反应时间对熟料强度的影响。
淮海中联水泥(287.08元/吨,0%)有限公司2#窑是由南京凯盛水泥设计院设计,2005年3月投产的5000t/d 熟料生产线,2007年8月公司利用现有1条日产5000t/d 熟料生产线的窑尾、窑头废气余热,配套建设了1*9MW的纯低温余热发电系统。
该厂3、6、7月份窑系统工艺参数平均台帐(一)6月与3月份工艺参数对比.CO平均值下降-44.12ppm。
二次风温上升+25。
2℃。
f—cao合格率上升+5.81%,在同等喂料量情况下窑速降低—0。
3rpm,主窑皮长度增加+3。
10m;由于窑皮厚度较3月份降低(见表五)。
窑内填充率下降窑功率同比降低—120A。
其它参数无明显变化。
熟料3天、7天、28天强度分别增加+1.38 Mpa、+5。
59 Mpa、+4.19Mpa,液相量略有增加+0.1%。
通过参数对比分析:CO平均值下降和二次风温以及f-cao合格率上升,都能说明窑系统通风状况较好,二、三次风比例合适,窑内煅烧温度同比较高;在同等喂料量情况下由于窑速降低和主窑皮长度增加,延长了熟料在窑内煅烧时间,使熟料矿物结晶更加完全,熟料强度提高明显。
153、煅烧温度对硫铝酸盐水泥熟料矿物组成及性能有何影响

煅烧温度对硫铝酸盐水泥熟料矿物组成及性能有何影响(1)烧成温度对熟料矿物组成的影响实验室煅烧试验结果表明,在1200~1400℃温度范围内都可以烧成以SAC34和C2S为主的硫铝酸盐水泥熟料。
但随着烧成温度的不同,熟料的矿物组成会有如下变化: 当烧成温度在1200℃时,除SAC34和C2S外,还有C2AS、2C2S·CaSO4及CaSO4存在,后三种矿物在1250℃还存在,说明在此温度下熟料的有用矿物还没有完全形成。
当烧成温度上升至1300℃时,2C2S·CaSO4和C2AS基本消失,温度在1300~1350℃范围内,熟料中主要矿物为SAC34和C2S,烧成温度若再升高,即当温度达1400℃时,SAC34部分分解,熟料中SAC34反而减少,出现C2AS和C12A7矿物,还有微量f-CaO存在。
对不同烧成温度下形成熟料中SO3和SAC34的测定结果表明,随着烧成温度的提高,熟料中SO3不断减少,在1200℃时,熟料中SO3为11.27%,此时CaSO4除生成有用矿物SAC34外,还与C2S反应生成复盐2C2S·CaSO4,即2C2S+CaSO4→2C2S·CaSO4。
当烧成温度在1400℃时,原已形成的SAC34部分分解,SO3则挥发逸出,熟料中SO3仅剩6.59%,熟料的SA/>3.82,SO3已不足与CaO和Al2O3完全形成C4A3S,故有其他矿物生成。
熟料中SAC34含量的变化开始时随烧成温度的升高而增多,在1300~1350℃时,SAC34的生成量最大,但烧成温度到1400℃后,熟料中SAC34明显减少。
对工厂熟料物相检定结果显示,煅烧温度较低的低烧熟料中同样含有2C2S·CaSO4和C2AS等矿物,这种熟料在窑内约在1200℃左右煅烧而成。
在1300~1350℃范围内烧成的正常熟料中主要含有C4A3S和C2S矿物。
而熔块料则在过烧情况下形成,估计烧成温度≥1400℃,发现有C2AS和C12A7及微量f-CaO存在。
水泥制造过程中的主要质量控制点是什么

水泥制造过程中的主要质量控制点是什么水泥作为建筑行业中不可或缺的重要材料,其质量的优劣直接关系到建筑物的安全性和耐久性。
要确保水泥的质量稳定可靠,就需要在制造过程中严格把控各个环节。
那么,水泥制造过程中的主要质量控制点究竟是什么呢?首先,原材料的选择和质量控制是至关重要的第一步。
水泥的主要原料包括石灰石、黏土、铁矿粉等。
这些原材料的化学成分、物理性质以及杂质含量都会对水泥的质量产生深远影响。
例如,石灰石中的碳酸钙含量要达到一定标准,黏土的塑性和黏性要适中,铁矿粉的含铁量要符合要求。
在采购原材料时,必须对其进行严格的检验和分析,确保其质量符合生产要求。
同时,还要注意原材料的储存和管理,避免受潮、混入杂质或者发生变质。
接下来是生料的制备过程。
生料是由原材料经过破碎、配料、粉磨等工艺制成的。
在这个环节中,配料的准确性是关键。
需要根据预定的水泥配方,精确控制各种原材料的比例。
如果配料不准确,就会导致生料成分的偏差,进而影响水泥的质量。
此外,粉磨的细度也会对生料的质量产生影响。
粉磨得过粗,生料反应不充分;粉磨得过细,不仅增加能耗,还可能导致生料的团聚和结块。
生料进入窑中进行煅烧是水泥制造的核心环节之一。
煅烧的温度、时间和气氛控制都极为重要。
温度过低或时间不足,生料无法完全反应,会产生大量的游离氧化钙等有害物质,影响水泥的安定性;温度过高或时间过长,则可能导致熟料的过烧,降低水泥的强度。
同时,窑内的气氛控制也很关键,要保证有足够的氧气参与反应,避免还原气氛的出现,以免影响熟料的质量。
熟料冷却也是一个不容忽视的环节。
快速冷却可以使熟料中的矿物形成细小均匀的晶体结构,提高熟料的质量和活性。
如果冷却速度过慢,熟料中的矿物会长大,晶体结构变得不均匀,从而降低水泥的强度和性能。
在水泥的粉磨过程中,粉磨的细度和均匀性是重点关注的方面。
粉磨细度直接影响水泥的水化反应速度和强度发展。
过粗的水泥颗粒难以充分水化,影响早期强度;过细的水泥颗粒则容易产生收缩裂缝,并且增加生产成本。
浅谈如何提高预分解窑熟料的质量

M O主要来 自砂岩和页岩 , g 我们控制进厂砂 岩和页
岩中 wM O< . ( g )2 %。 0 () O。 O 会使窑内熟料液相量增加 , 3 S S 煅烧温 度降低 ;另过剩的硫在窑中循环容易引起预热器结 皮堵塞和窑内结圈 .导致熟料质量下降及系统热工
质石英含量 ( 主要通过现场 目测 )并对原材料进行 , 合理有效的均化。 () g 。少量 的 M O存在能使生料易烧性和 2 MO g 熟料的色泽得到改善 ,超过一定范围后会使液相提 前出现并增加总的液相含量 , 使煅烧温度降低 , 导致 熟料质量下降。我公 司石灰石 品位较高 ,熟料 中
煅烧温 wf C O) (- a
度- / ℃
l350 140 0 150 0
3 抗 压强度 d
2 5 7. 2 6 9. 3 2 4. O 7. 6 2 4 4.
2 d抗压强度 8
54. 8 57. 2 64. 7 0 4. 4 1 0 8此 , 须对原 燃材 料加 强均 化措 施 。 必
质量下降。我们在 配料过程 中控制生料 中 (l c- )
≤ 0. 5 。 01 %
1 . 1原燃材料中微量组分对质量的影响及控制 原燃材料 中微量组分[ 主要包括 : 晶质 一 石英 、 M O S , ( N 2)氯 等] g 、O 、 K0,a 、 碱 0 对预分解 窑的熟料
注 意 这 些 组
分的影响。 ( ) 晶 1
质 一 石英 。
我 公 司 由 石
工薮磊根 据 X 荧光分析仪 岗位记录统计 , 中生料 的硫碱 比为 09 。 一 其 . 0
灰石和砂岩原料带人的晶质 O 石英结构致密 , 以 t 一 难 磨细 ,在煅烧 中不易与氧化钙化合 ,易导致熟料 fC O增加和熟料后期强度下降 。我们所采取的主 -a
影响回转窑操作的几个重要参数

影响回转窑操作的几个重要参数窑的任务就是煅烧熟料,而组成熟料的矿物都是通过固相反应形成的,因此要搞好窑的操作,就必须把握好影响熟料固相反应的因素。
这个道理大家都懂,在各种资料上也都有讲解,但在实际操作中却往往被忽视。
这里也只是把他们提炼出来,再次作一提醒,以引起操作者的重视。
一、生料细度不难理解,生料磨的越细,颗粒尺寸越小,比表面积越大,组分之间的接触面就越大,同时表面质点的自由能也越大,使得扩散和反应机会增多、能力增强,因此固相反应加快。
但是,生料磨的越细,其粉磨电耗就越高,细度磨到多少合适,应该根据各厂的实际情况,找一个最佳的平衡点。
就现在一般的分解窑来讲,对于烧成熟料,小于100um的方解石和小于55u m的粗粒石英是没有任何问题的,因此过细的粉磨没有意义,我们的重点应放在抓少数大颗粒上,做到既要能烧又要省电。
大多数水泥厂的生料细度以考核0.08mm筛余为主,而实际上起主要影响的却是0.2mm筛余,应该抓住这个重点。
按通常的经验:当0.2mm筛余≦1.5%时,0.08mm筛余以控制在12%以下为好;当0.2mm筛余控制≦1.0%时,0.08mm筛余可以放宽到15%;当0.2mm筛余控制≦0.5%时,0.08mm筛余可以放宽到18%;二、液相量水泥熟料的主要矿物硅酸三钙是通过液相烧结进行的。
在高温液相作用下,硅酸二钙和游离氧化钙都逐步溶解于液相中,以离子的形式发生反应,形成硅酸三钙,水泥熟料逐渐烧结,物料由疏松状态转变为色泽灰黑、结构致密的熟料。
在硅酸盐水泥熟料中,由于含有氧化镁、氧化钠、氧化钾、硫酐、氧化钛等易熔物,其最低共熔温度约为1250℃。
随着温度的升高和时间的延长,液相量会增加,液相黏度会减小,使参与反应的离子更易扩散和结合,也就是说液相在熟料的形成过程中起着非常重要的作用,而且受到水泥熟料化学成分和烧成温度的影响。
既然液相量与化学成分有关,那么在配料上将如何控制呢?根据以往的经验,先定义为1450℃下(比较接近于生产实际)的液相量,液相量按下式计算:L=3.0A+2.25F+M+R式中L、A、F、M、R分别表示水泥熟料的液相量、氧化铝、氧化铁、氧化镁、氧化钠和氧化钾的合量。
熟料质量控制及煅烧方面的影响因素

培训材料熟之三料质量控制及煅烧方面的影响因素一、熟料质量控制的重要性1、熟料质量是确保水泥质量的核心,熟料质量达不到要求,难以磨制优质的水泥产品。
其中配料和煅烧是决定熟料质量的关键。
2、从生料到熟料,是一个化学反应过程。
化学反应,最基本的核心就是要求参预化学反应的物质间的比例要满足理论要求。
参预化学反应的某一物质的量,不得过剩或者不足,否则,化学反应形成的结果,不是当初设计的结果。
因此,熟料生产过程实际上要求是很精细的,不是表面上的那种粗糙现象。
3、设计合理的熟料率值,通过良好的煅烧,才干生产出优质的水泥熟料。
1、原料磨工艺变化现代水泥企业,以节能高效为主要导向,装备和工艺流程日益简化和高效。
2、原料磨由过去的球磨机改为现代立磨,原料磨工艺装备的改变,对产品质量的影响。
3、球磨机的工艺特点,决定了生料细度更加均匀,900 孔细度小,只在 3.0%以内, 1800 孔细度在 12%以内。
立磨的生料细度粗, 900 孔细度在 6.0-8.0%, 1800 孔细度在 22%摆布。
由上看出,现代水泥工业改成立磨后,生料的颗粒级配产生了较大的变化,立磨的生料粗大颗粒占比例明显上升,中等颗粒的比例,也较球磨机增加了一倍。
4、现代水泥工业、细度标准的变化。
80 年代,国家旋窑管理规程对细度有控制要求,最开始的标准规定生料细度小于等于 10%,作为一次水泥工艺管理的标准来执行,其后更改为 12%。
后来随着先进水泥工艺发展,生料细度作为一次过程控制指标,再也不强制执行,由企业根据自身生产需要自行控制。
质量体系认证,也将细度标准作为企业自行制定来审核,细度标准被企业自身不断放松标准。
按照现行立磨的生产工艺,生料细度按 10%、12%、16% 等等标准,已经无法满足当前立磨工艺的要求,根据立磨的特点及与窑的产能关系,细度只能控制在 20-22%之间,即使控制较好的工厂细度也在 8 摆布。
但是 , 目前的细度控制指标,不表示细度粗对煅烧没有影响。
熟料煅烧质量的影响因素
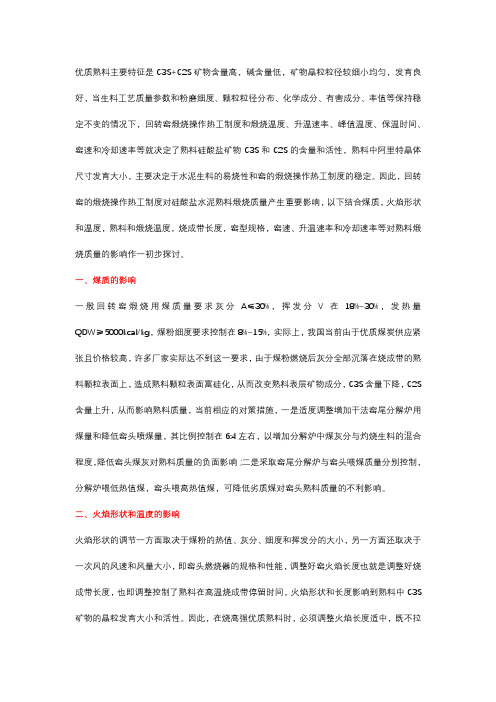
优质熟料主要特征是C3S+C2S矿物含量高,碱含量低,矿物晶粒粒径较细小均匀,发育良好,当生料工艺质量参数和粉磨细度、颗粒粒径分布、化学成分、有害成分、率值等保持稳定不变的情况下,回转窑煅烧操作热工制度和煅烧温度、升温速率、峰值温度、保温时间、窑速和冷却速率等就决定了熟料硅酸盐矿物C3S和C2S的含量和活性,熟料中阿里特晶体尺寸发育大小,主要决定于水泥生料的易烧性和窑的煅烧操作热工制度的稳定。
因此,回转窑的煅烧操作热工制度对硅酸盐水泥熟料煅烧质量产生重要影响,以下结合煤质,火焰形状和温度,熟料和煅烧温度,烧成带长度,窑型规格,窑速、升温速率和冷却速率等对熟料煅烧质量的影响作一初步探讨。
一、煤质的影响一般回转窑煅烧用煤质量要求灰分A≤30%,挥发分V在18%~30%,发热量QDW≥5000kcal/kg,煤粉细度要求控制在8%~15%,实际上,我国当前由于优质煤炭供应紧张且价格较高,许多厂家实际达不到这一要求,由于煤粉燃烧后灰分全部沉落在烧成带的熟料颗粒表面上,造成熟料颗粒表面富硅化,从而改变熟料表层矿物成分,C3S含量下降,C2S 含量上升,从而影响熟料质量,当前相应的对策措施,一是适度调整增加干法窑尾分解炉用煤量和降低窑头喷煤量,其比例控制在6:4左右,以增加分解炉中煤灰分与灼烧生料的混合程度,降低窑头煤灰对熟料质量的负面影响;二是采取窑尾分解炉与窑头喂煤质量分别控制,分解炉喂低热值煤,窑头喂高热值煤,可降低劣质煤对窑头熟料质量的不利影响。
二、火焰形状和温度的影响火焰形状的调节一方面取决于煤粉的热值、灰分、细度和挥发分的大小,另一方面还取决于一次风的风速和风量大小,即窑头燃烧器的规格和性能,调整好窑火焰长度也就是调整好烧成带长度,也即调整控制了熟料在高温烧成带停留时间,火焰形状和长度影响到熟料中C3S 矿物的晶粒发育大小和活性。
因此,在烧高强优质熟料时,必须调整火焰长度适中,既不拉长火焰使烧成带温度降低,也不缩短火焰使高温部分过于集中,从而烧垮窑皮和耐火砖而不利于窑的安全运转,回转窑内火焰形状粗细必须与窑断面积相适应,要求比较充满近料而不触料,正常形状保持其纵断面为正柳叶形状。
煅烧温度与煅烧时间对熟料fCaO的影响
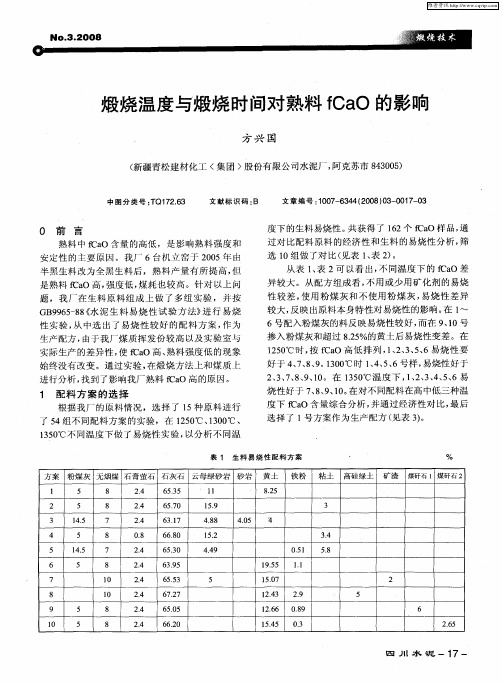
2 1 .3
28 .5 25 .3
o s。 SO5 s
| J
2
3. 8 9 9
3 .0 86
1. 1 4 7
l.1 17
32 . 5
35 .4
25 . O
27 .9
3 .6 8 7
3 .1 88
12 . 6
17 .4
1O . 1
11 .7
O9 . 5
09 .5
维普资讯
煅 烧温 度与煅烧 时间对 熟料 f a 的影 响 C O
方 兴 国
( 新疆 青松 建材 化 工 <集 团 > 份 有 限公 司水 泥厂 , 克苏 市 8 3 0 ) 股 阿 4 0 5
中 图分 类 号 : Q1 26 T 7 .3
文献 标 识 码 : B
2 3 7 8 9 1 。在 15 ℃温 度 下 , 、 、 、 、 、 、、 、、 、0 30 12 3 4 5 6易
题 ,我 厂 在 生料 原 料 组 成 上 做 了 多组 实验 , 并 按
GB 9 5 8 《 泥 生 料 易 烧 性 试 验 方 法》 行 易烧 96 - 8 水 进 性 实验 , 中选 出 了易烧 性较 好 的配 料 方 案 , 为 从 作 生产 配方 , 由于 我 厂煤 质挥 发 份 较 高 以及 实 验 室 与
1 43 2. 2. 9 5
2
9 1 0
5 5
8 8
24 . 24 .
6 .5 50 6 .0 62
1 .6 26 1 .5 54
08 .9 0_ 3
6 26 .5
四 jI I水 泥 一 1 — பைடு நூலகம் 7
维普资讯
水泥烧成工艺技术
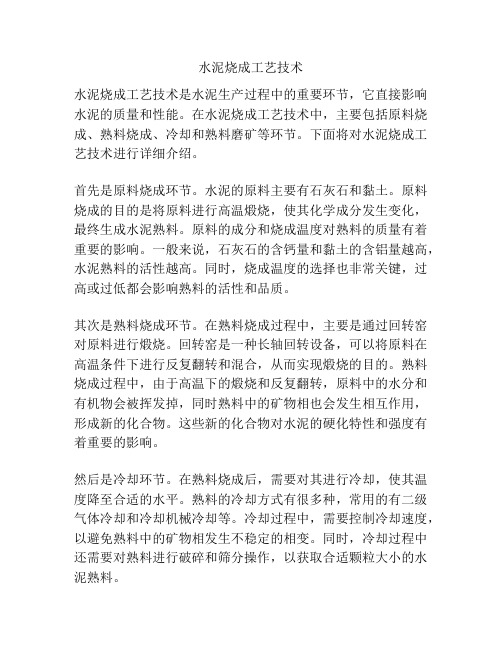
水泥烧成工艺技术水泥烧成工艺技术是水泥生产过程中的重要环节,它直接影响水泥的质量和性能。
在水泥烧成工艺技术中,主要包括原料烧成、熟料烧成、冷却和熟料磨矿等环节。
下面将对水泥烧成工艺技术进行详细介绍。
首先是原料烧成环节。
水泥的原料主要有石灰石和黏土。
原料烧成的目的是将原料进行高温煅烧,使其化学成分发生变化,最终生成水泥熟料。
原料的成分和烧成温度对熟料的质量有着重要的影响。
一般来说,石灰石的含钙量和黏土的含铝量越高,水泥熟料的活性越高。
同时,烧成温度的选择也非常关键,过高或过低都会影响熟料的活性和品质。
其次是熟料烧成环节。
在熟料烧成过程中,主要是通过回转窑对原料进行煅烧。
回转窑是一种长轴回转设备,可以将原料在高温条件下进行反复翻转和混合,从而实现煅烧的目的。
熟料烧成过程中,由于高温下的煅烧和反复翻转,原料中的水分和有机物会被挥发掉,同时熟料中的矿物相也会发生相互作用,形成新的化合物。
这些新的化合物对水泥的硬化特性和强度有着重要的影响。
然后是冷却环节。
在熟料烧成后,需要对其进行冷却,使其温度降至合适的水平。
熟料的冷却方式有很多种,常用的有二级气体冷却和冷却机械冷却等。
冷却过程中,需要控制冷却速度,以避免熟料中的矿物相发生不稳定的相变。
同时,冷却过程中还需要对熟料进行破碎和筛分操作,以获取合适颗粒大小的水泥熟料。
最后是熟料磨矿环节。
熟料磨矿是指对熟料进行机械粉磨,最终得到合适颗粒大小的水泥粉末。
熟料磨矿过程中,需要选择适当的磨矿设备和工艺参数。
常用的磨矿设备有球磨机和辊压机等。
磨矿的目的是将熟料中的矿物颗粒细化,增加其活性和反应速度,从而提高水泥的强度和硬化特性。
综上所述,水泥烧成工艺技术是水泥生产过程中的重要环节。
通过对原料烧成、熟料烧成、冷却和熟料磨矿等环节的控制和调节,可以获得高质量的水泥熟料,从而保证水泥的质量和性能。
熟料烧成工艺技术

熟料烧成工艺技术熟料烧成工艺技术是指将生料在高温条件下煅烧成熟料的一项工艺过程。
熟料是制造水泥的主要原料,熟料烧成工艺技术的优劣直接影响着水泥的质量和生产成本。
熟料烧成工艺技术主要包括熟料原料的准备、煅烧过程以及冷却等环节。
首先是熟料原料的选择和准备。
熟料原料主要包括石灰石、粘土、铁矿石等,这些原料的配比和质量直接影响着熟料的成分和性能。
在熟料原料准备过程中,需要进行粉碎、混合和均化等处理,以确保原料的均匀性和可操作性。
其次是熟料的煅烧过程。
煅烧是将原料在高温条件下加热,使之发生化学反应,生成熟料的过程。
煅烧过程需要控制熟料中CaO、SiO2、Al2O3、Fe2O3等成分的含量和比例,以确保熟料的硅酸盐和铝酸盐矿物分解得充分和合理。
同时,还需要控制煅烧过程中的温度、时间和气氛等因素,以确保煅烧过程的顺利进行和熟料的品质。
最后是熟料的冷却过程。
煅烧后的熟料需要进行冷却处理,以降低温度并稳定其组织结构。
冷却过程需要适应熟料的产量和质量要求,采取不同的冷却方式,如风冷、排热气、水冷等。
冷却过程中还需要注意熟料的收缩和裂纹等问题,以避免熟料的质量问题。
熟料烧成工艺技术在水泥生产中具有重要的意义。
一方面,熟料烧成工艺技术直接影响着水泥的质量。
熟料的成分和比例决定着水泥的性能,如强度、硬化时间、抗渗透性等。
合理控制熟料烧成工艺技术可以提高水泥的质量,并满足不同材料要求的工程建设需求。
另一方面,熟料烧成工艺技术还影响着水泥的生产成本。
高效、低能耗的熟料烧成工艺技术可以降低生产成本,提高企业的经济效益。
总之,熟料烧成工艺技术是水泥工业中不可或缺的一环,它直接影响着水泥的质量和生产成本。
合理选择熟料原料、控制煅烧过程和冷却过程,将有助于提高水泥的质量和降低生产成本,进一步推动水泥产业的可持续发展。
煅烧对熟料显微结构和质量的影响
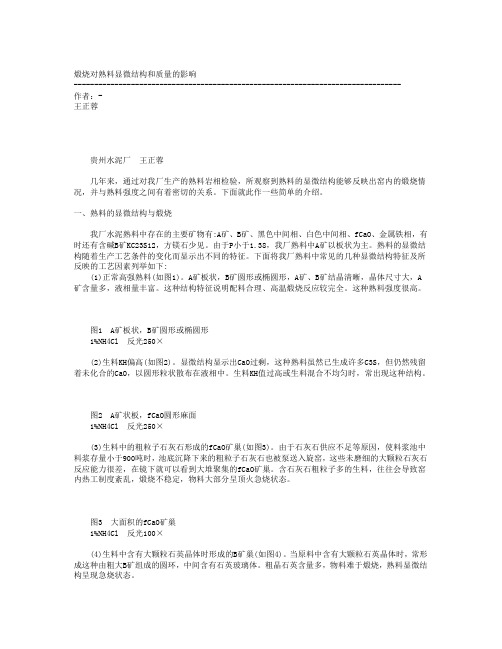
煅烧对熟料显微结构和质量的影响--------------------------------------------------------------------------------作者:-王正蓉贵州水泥厂王正蓉几年来,通过对我厂生产的熟料岩相检验,所观察到熟料的显微结构能够反映出窑内的煅烧情况,并与熟料强度之间有着密切的关系。
下面就此作一些简单的介绍。
一、熟料的显微结构与煅烧我厂水泥熟料中存在的主要矿物有:A矿、B矿、黑色中间相、白色中间相、fCaO、金属铁相,有时还有含碱B矿KC23S12,方镁石少见。
由于P小于1.38,我厂熟料中A矿以板状为主。
熟料的显微结构随着生产工艺条件的变化而显示出不同的特征。
下面将我厂熟料中常见的几种显微结构特征及所反映的工艺因素列举如下:(1)正常高强熟料(如图1)。
A矿板状,B矿圆形或椭圆形,A矿、B矿结晶清晰,晶体尺寸大,A 矿含量多,液相量丰富。
这种结构特征说明配料合理、高温煅烧反应较完全。
这种熟料强度很高。
图1 A矿板状,B矿圆形或椭圆形1%NH4Cl 反光250×(2)生料KH偏高(如图2)。
显微结构显示出CaO过剩,这种熟料虽然已生成许多C3S,但仍然残留着未化合的CaO,以圆形粒状散布在液相中。
生料KH值过高或生料混合不均匀时,常出现这种结构。
图2 A矿状板,fCaO圆形麻面1%NH4Cl 反光250×(3)生料中的粗粒子石灰石形成的fCaO矿巢(如图3)。
由于石灰石供应不足等原因,使料浆池中料浆存量小于900吨时,池底沉降下来的粗粒子石灰石也被泵送入旋窑,这些未磨细的大颗粒石灰石反应能力很差,在镜下就可以看到大堆聚集的fCaO矿巢。
含石灰石粗粒子多的生料,往往会导致窑内热工制度紊乱,煅烧不稳定,物料大部分呈顶火急烧状态。
图3 大面积的fCaO矿巢1%NH4Cl 反光100×(4)生料中含有大颗粒石英晶体时形成的B矿巢(如图4)。
硅酸盐水泥熟料的煅烧工艺

硅酸盐水泥熟料的煅烧工艺硅酸盐水泥熟料是一种重要的建筑材料,其主要成分是硅酸盐矿物质。
熟料的生产是通过对原料进行煅烧工艺来实现的。
以下是硅酸盐水泥熟料的煅烧工艺的详细步骤:1. 原料准备:硅酸盐水泥熟料的主要原料包括石灰石、黏土和其他辅助原料。
这些原料需要粉碎和混合以获得均匀的化学成分。
2. 煤粉燃烧:在水泥炉中,需要使用煤粉作为主要燃料。
煤粉经过燃烧反应产生高温和热量,为后续反应提供能量。
3. 干法预热:将经过预处理的原料送入水泥炉,通过高温烟气进行干法预热。
在预热过程中,原料中的水分逐渐蒸发,从而实现干燥和预热的目的。
4. 煅烧反应:在水泥炉中,原料经过预热后被加热至高温,从而引发一系列的化学反应。
其中,主要的反应是石灰石的分解反应,将石灰石中的钙碳酸钙分解为氧化钙和二氧化碳。
此外,还有一系列的矿物转化反应和固相反应发生。
5. 冷却:煅烧后的硅酸盐水泥熟料需要进行冷却。
这一过程通过烟气和新鲜空气流通来降低熟料的温度,避免过度煅烧。
6. 粉磨:冷却后的熟料被送入水泥磨进行粉磨处理。
通过磨破磨、分级破磨和分级等步骤,熟料被加工成细度符合要求的水泥产品。
硅酸盐水泥熟料的煅烧工艺是一个复杂的化学和物理变换的过程。
煅烧过程中,需要控制适当的温度、时间和燃烧条件,以确保熟料的质量。
同时,通过优化煅烧工艺,可以降低能耗和环境排放,实现节能减排的目的。
硅酸盐水泥熟料煅烧工艺的详细步骤:7. 烟气处理:在炉内煅烧过程中,产生大量的烟气、灰尘和废气。
这些废气含有有害物质,需要进行处理以减少对环境的影响。
常见的烟气处理方法包括电除尘、袋式除尘等,以去除烟气中的粉尘和固体颗粒,并通过喷淋洗涤等方式去除废气中的二氧化硫等有害物质。
8. 能源回收:在煅烧过程中,通过使用高温烟气作为热源,可以回收能量并用于干法预热等步骤。
这种能源回收措施不仅可以降低能源消耗,减少生产成本,还可以减少对自然资源的开采和环境的影响。
9. 质量控制:在整个煅烧工艺中,对煅烧过程的温度、时间和燃烧条件等进行严格控制,以确保熟料的质量。
矿渣粉烧失量s95

矿渣粉烧失量s95矿渣粉是一种常用的水泥混合材料,由矿渣经过粉碎和细度调节制得。
在水泥生产过程中,矿渣粉的应用可以有效提高水泥品质,并减少对天然石膏和熟料的需求。
然而,矿渣粉的烧失量对其性能和应用有着重要影响。
本文将探讨矿渣粉烧失量S95的相关问题。
一、矿渣粉烧失量的定义与影响因素烧失量是指矿渣粉在高温下的质量损失,一般以百分比表示。
矿渣粉烧失量的大小与其原料矿渣的化学成分、煅烧温度、煅烧时间及冷却方式等因素有关。
1. 原料矿渣的化学成分原料矿渣的化学成分对矿渣粉的烧失量有直接影响。
对于含有较高含铁量的矿渣,其烧失量往往较低;而含有较高氧化钙(CaO)含量的矿渣则烧失量较高。
2. 煅烧温度和煅烧时间煅烧温度和煅烧时间是烧失量的重要控制因素。
通常情况下,提高煅烧温度和延长煅烧时间会使矿渣粉的烧失量降低。
这是因为高温下矿渣中的有机物质和结晶水会更容易脱除。
3. 冷却方式冷却方式对矿渣粉的烧失量影响较小。
但是,当采用水淬冷却方式时,烧失量会略微增加。
这可能是由于冷却速度过快导致矿渣中剩余有机物难以完全挥发。
二、矿渣粉烧失量S95的特点与应用矿渣粉烧失量S95是指烧失量在5%以下的矿渣粉,其适用于制备高性能混凝土、高强度水泥及其他建筑材料。
相比于烧失量高的矿渣粉,S95具有以下特点和优势:1. 提高混凝土的工作性能矿渣粉S95具有良好的细度和活性,可以填补水泥颗粒之间的空隙,提高混凝土的流动性和可塑性。
同时,细腻的矿渣颗粒可以增加混凝土的内聚力,使其抗裂性和抗渗性得到明显提高。
2. 增强混凝土的力学性能适量添加矿渣粉S95可以显著改善混凝土的抗压强度、抗折强度和耐久性。
矿渣粉S95中的玻璃体颗粒可以与水泥水化产物反应,生成胶凝物质,填充水泥胶凝物和孔隙之间的缝隙,提高混凝土的致密性和力学性能。
3. 降低混凝土的热产烟毒和碱骨料反应矿渣粉S95中的活性硅酸盐和微量元素可以减缓混凝土的水化反应速度,降低热产烟毒。
水泥窑工况参数

水泥窑工况参数
水泥窑,作为水泥生产中的核心设备,其工况参数对于确保生产过程的顺利进行以及产品质量的稳定具有至关重要的作用。
以下将详细介绍水泥窑的一些关键工况参数。
首先,温度是水泥窑工况中最重要的参数之一。
水泥窑内的温度分布直接影响到熟料的形成和质量。
在煅烧过程中,需要严格控制窑内各区域的温度,以确保物料能够充分反应并生成高质量的熟料。
通常,水泥窑的煅烧温度可高达1400℃以上,这对窑体的耐高温性能和保温措施提出了较高的要求。
其次,窑内气氛也是水泥窑工况中的重要参数。
气氛主要影响到窑内的氧化还原反应,进而影响到熟料的矿物组成和性能。
通过调整窑内气氛,可以控制熟料中矿物相的形成,从而调整水泥的性能。
此外,物料在窑内的停留时间也是一个关键的工况参数。
物料在窑内的停留时间直接影响到其受热程度和反应程度。
过短的停留时间可能导致物料反应不充分,影响熟料质量;而过长的停留时间则可能导致熟料过烧,同样影响质量。
因此,需要根据物料性质和生产要求,合理控制物料在窑内的停留时间。
最后,窑的转速和斜度也是影响水泥窑工况的重要参数。
窑的转速和斜度决定了物料在窑内的运动状态和分布,进而影响到物料的混合和反应。
通过调整窑的转速和斜度,可以控制物料在窑内的运动轨迹,实现物料的均匀受热和充分反应。
综上所述,水泥窑的工况参数包括温度、气氛、物料停留时间、窑转速和斜度等。
这些参数之间相互关联、相互影响,共同决定了水泥窑的生产效率和产品质量。
熟料煅烧过程中的质量控制
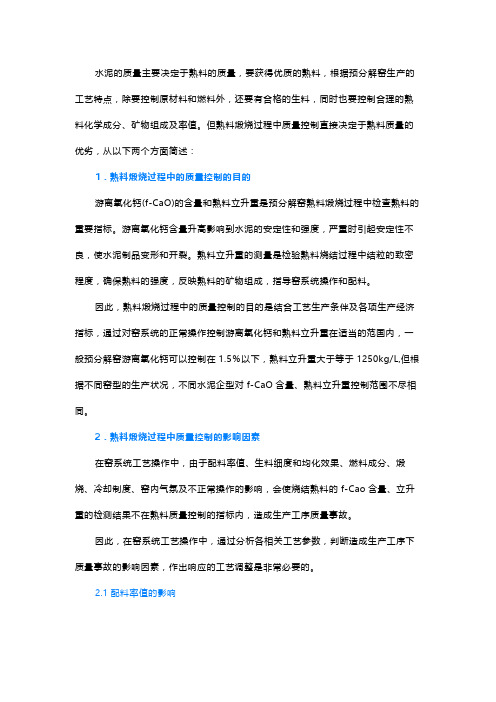
水泥的质量主要决定于熟料的质量,要获得优质的熟料,根据预分解窑生产的工艺特点,除要控制原材料和燃料外,还要有合格的生料,同时也要控制合理的熟料化学成分、矿物组成及率值。
但熟料煅烧过程中质量控制直接决定于熟料质量的优劣,从以下两个方面简述:1.熟料煅烧过程中的质量控制的目的游离氧化钙(f-CaO)的含量和熟料立升重是预分解窑熟料煅烧过程中检查熟料的重要指标。
游离氧化钙含量升高影响到水泥的安定性和强度,严重时引起安定性不良,使水泥制品变形和开裂。
熟料立升重的测量是检验熟料烧结过程中结粒的致密程度,确保熟料的强度,反映熟料的矿物组成,指导窑系统操作和配料。
因此,熟料煅烧过程中的质量控制的目的是结合工艺生产条伴及各项生产经济指标,通过对窑系统的正常操作控制游离氧化钙和熟料立升重在适当的范国内,一般预分解窑游离氧化钙可以控制在1.5%以下,熟料立升重大于等于1250kg/L,但根据不同窑型的生产状况,不同水泥企型对f-CaO含量、熟料立升重控制范围不尽相同。
2.熟料煅烧过程中质量控制的影响因素在窑系统工艺操作中,由于配料率值、生料细度和均化效果、燃料成分、煅烧、冷却制度、窑内气氛及不正常操作的影响,会使烧结熟料的f-Cao含量、立升重的检测结果不在熟料质量控制的指标内,造成生产工序质量事故。
因此,在窑系统工艺操作中,通过分析各相关工艺参数,判断造成生产工序下质量事故的影响因素,作出响应的工艺调整是非常必要的。
2.1配料率值的影响率值表明熟料各氧化物之间相对含量的系数,用来控制矿物组成,满足熟料的强度的控制;在窑系统操作中,常因生料的率值的波动而导致窑热工制度的破坏,一般生料的饱和比高,会导致生料很难烧,f-CaO偏高,操作员被迫增加喂煤,从而很容易烧坏窑皮;IM过低,会导烧结范围变窄,窑内容易结大蛋,严重破坏热工制度。
2.2生料细度和均化的影响生料细度和均化对熟料的烧成和熟料的质量均有重要意义,生料细度控制在12~15%(0.08mm方孔筛筛余),如采用立磨可放宽到16%。
- 1、下载文档前请自行甄别文档内容的完整性,平台不提供额外的编辑、内容补充、找答案等附加服务。
- 2、"仅部分预览"的文档,不可在线预览部分如存在完整性等问题,可反馈申请退款(可完整预览的文档不适用该条件!)。
- 3、如文档侵犯您的权益,请联系客服反馈,我们会尽快为您处理(人工客服工作时间:9:00-18:30)。
375.3 385.0 377.0
940 820 837
3.7 2.3
2.2
185.4 141.o 140.2
1020
l
176
l
—348 —313 —3II
94.2
8.2
3.9
23.O
30.4
56.4 60.6
58.7
26.3 26.4
26.3
1045 】030
199 198
328 333—4885来自—4791 —946月与7月相比,CO平均值持平,二次风温高 出15℃,fCaO合格率高出9.2%。在同等喂料量情况 下,窑速相同,主窑皮长度多出0.8m;窑皮厚度值持 平,其它参数无明显变化。熟料3d和28d强度分别高 出1.2MPa和1.9MPa,液相量略有增加(0.1%)。以上 参数也说明,6月份窑系统各项参数较好,通过适当延 长主窑皮长度,来延长熟料在窑内煅烧时间,熟料强 度会有所改善。
≤60
卜窑转速,r/min;
D广一窑衬内径,m;
|s——窑斜度,(o)。
表1中3种情况下物料在烧成带停留时间与窑 速、窑皮长度之间关系见表5。
表5物料在烧成带停留时间、窑速及窑皮长度和厚度
时间
3月 6月 7月
投料量
/(t/h) 375.3 385.0 377.0
窑速 /(dminl
3.9
窑皮长度
/m
节,尽量将每一个部位都恢复到初始状态;对设备进 行定期、定人巡检,保证系统风量与风压的均衡、稳 定;定期检查与检修设备,确保收尘系统的密封良好, 脉冲正常。 2)中控操作时,一定要稳定选粉机操作。在系统
万方数据
2010.No.2
季良平,等:煅烧温度和时间对熟料质量的影响
一33一
j彤。睡勰篱龋躺龋隳臻黼蛹嘲蛹鞠醴奠囊麟酾—翻■■—■霞■■■—磷阁■■■■瞳囊—————■■●———●———■—■—■■■——■●———●■■—————●—■●一 有利于C3S形成,我公司控制在25%一26.5%。6月份
,℃
332
项目
喂料量 窑功率 ,l【W /(t/h)
02 ,%
C0 /ppm
二次风 温度,℃
分解 炉出
口温
fCa0
煤粉 细度
/%
温度
/oC
压力
肫
压力
/Pa
—d744
度,℃
869
合格 率,%
水分
/%
1.7
主窑皮 窑速 长度 /(ffmin) /m
熟料 抗压 强度,‘MPa
3d 28d
液相鹾
,%
3月 6月 7月 6月和7月 比较 6月和3月 比较
万方数据
煅烧温度和时间对熟料质量的影响
作者: 作者单位: 刊名: 英文刊名: 年,卷(期): 季良平, 刘天振, 孙琳 淮海中联水泥有限公司,江苏,徐州,221168 水泥 CEMENT 2010(2)
本文链接:/Periodical_sn201002011.aspx
一32一
扣渗t'E,,IIB'1"
2010№N
2
■—●——■■■●————●●———●——————●———■———■————————■■■—■■翻嘲■嘲嘲麟鞠瞒嘲麟嘲略髓瓣端瓣穗糍端鲻搿势乒蹦≯j
煅烧温度和时间对熟料质量的影响
季良平,刘天振,孙琳
(淮海中联水泥有限公司,江苏徐州221168) 中图分类号:TQl72.622.26 文献标识码:B 文章编号:1002—9877(2010)02—0032—02
3
工况变化不大的情况下,尽量稳定选粉机的转速,以 使出磨矿粉的质量稳定;在系统工况稳定的前提下, 增加喂料量或提高质量必须注意加大研磨压力。同时 操作中应密切关注各工艺参数的变化及相互间的关 系,对故障和隐患做出准确的分析、判断,以利于及时
调整。 (编辑乔彬)
总结 1)设备检修与维护时,不能忽视每一个细小的环
表2煤的工业分析
3烧成时间
C3s形成不仅需要煅烧温度,还要有一定的时间 (一般在10~20min),熟料煅烧时间与合适的温度梯 度、烧成带长度、窑转速、窑衬内径及窑斜度等有关。 合适的温度梯度,即达到烧成温度l 300—1
450。C
后的火焰要有一定长度,没有明显的峰值出现。如果 熟料结粒正常,一般在20~30ram,但破开后外部裹有 一环致密坚硬的外壳,内部熟料颜色与外部一致,只 是密实度较外部差,这类熟料多数因为窑内温度较 高,但温度场分布不均所致,是明显的短焰急烧熟料。 质量方面表现为fCao较低,但熟料28d强度不高,长 时间存放容易出现粉化现象。 合理的窑皮长度、平整度是表明窑内温度梯度是 否合适的标志。 物料在正常情况下通过烧成带所用时间:
窑皮厚度
/nun
烧成带停留 时间/rain
9.09 10.95 lO.62
24.0 27.1 26.3
250 220 220
60—65 ≤65
3.6 3.6
注:煤粉水分<2.O%时,尽量降低出口温度。
从表5看出,3月份熟料在烧成带停留时间最短 仅9.09rain,与6月份相比平均缩短1.86min;7月与6 月相比平均缩短0.33min。综合表l和表5的数据,6 月份熟料在窑内的煅烧时间相对较长,使熟料矿物晶 体发育更加完全,在一定程度上提高了熟料强度,稳
窑系统二次风温和熟料fCaO合格率均较3月和7月 高,表明窑内煅烧温度的提高,对熟料质量有利。 我公司在保证窑内煅烧温度方面有以下措施: 1)控制煤粉质量。我公司使用的是国产燃烧器, 煤工业分析见表2。根据生产需要制定了煤粉水分与 细度对应关系见表3,缓解因煤粉水分上升带来的不 利影响。当Ad上升时,煤粉细度适当降低。
表4原煤挥发分和水分与磨机出口温度控制 挥发分,% 水分,%
≤10 <27 lO一12 ≥12 ≤lO 27—30 10~12 ≥12 ≤10 ≥30 lO一12 ≥12
1.4L/(n・n-S)
式中:
t——物料在烧成带停留时间,nfin: L——烧成带窑皮长度,m;
磨机出口温度,℃
≤65 65—70 65~75 ≤60 60—65 65~70
2熟料煅烧温度和液相量
在正常温度下,液相量一般控制在22%一26%。在 系统工况正常情况下,液相量可偏中上限控制,这样
-争・夺・・争・・争・÷・・争・争・专・夺—争・÷・夺・夺・{,・夺—}・专・专・寺-・—争・夺岭・夺・・争・÷・专・・{,・专・夺・争・毒・・幸・专t专・争・寺・—争・夺・夺・夺・毒,-争・夺・夺・牵岭・・{” 偏大问题得到彻底解决。
1.4
4.2
O.1
由表l可见,6月比3月CO平均值下降44.4ppm, 二次风温上升25℃,fCaO合格率上升5.8%。在喂料量 相近情况下,窑速降低0.3dmin,主窑皮长度增加 3.10m;由于窑皮厚度较3月份降低(分别为220mm 和250mm),窑内填充率下降,窑功率同比降 低120kW。其它参数无明显变化。熟料3d和28d抗 压强度分别增加1.4MPa和4.2MPa,液相量略有增加 (0.1%)。以上参数说明,6月份窑系统通风状况较好, 二、三次风比例合适,窑内煅烧温度同比较高。由于窑 速降低和主窑皮长度增加,延长了熟料在窑内煅烧时 间,使熟料矿物结晶更加完全,熟料强度提高明显。
实践证明,在熟料三率值KH、,l、P适当,生料成 分稳定的条件下,熟料质量取决于煅烧温度、液相性 质及形成晶体的反应时间。本文结合我公司5 000t/d
裘1
生产线,介绍煅烧温度和时间对熟料强度的影响。
1窑系统工艺参数分析
窑系统工艺参数月平均值见表1。
2009年3,6、7月份窑系统工艺参数月平均值
窑尾 C。出口 温度
863 865
100.O 90.8
9.6 9.9
I,9 2.6
3.6 3.6 0.O
26.1 25.3
31.8
30.6
1
8.O
-17
0.1
O.8
15
1
-3
-5
-2
9.2
-0.3
-0.7
O.8
1.2
1.9
0.1
9.7
—120
一1.4
—44.4
25
23
-35
--4
—14l
-6
5.8
1.4
O.2
一O.3
3.1
t=l
l肌。,% l 1.12.2.58
I I
‰,%
26.20一28.5
1
A.d,% 18.80~25.19
月%,%
49.40~52.20
‰,(MJ/l【曲I
23.3~25.2
l
%
I
表3煤粉水分与细度对应关系
l I
煤粉水分 细度
<1.5
≤12
l-5—2.O
≤10
≥2.O
≤8
在原煤水分超出设计要求时,为降低煤粉水分, 在保证磨机安全运行基础上,根据原煤挥发分适当提 高磨机出口温度(见表4)。
定了熟料质量。
2)保障总风量与料量合理配合,在窑系统达到或 超过设计产能后控制Cl出口:02含量为1.9%~2.5%, CO含量≤350ppm,温度≤330。C。 3)正常情况下,三次风闸板开度在50%-60%;一 般控制分解炉出口温度比C,下料管温度高10~20℃, 如果出现倒挂现象,说明煤粉在分解炉内燃烧不好, 这时可适当增加三次风量或控制煤粉质量。 4)控制窑头二次风温≥l 0300C,窑尾温度控制在
(1 150±50)qc,当发现尾温偏高或二次风温偏低时,适
4结论
正常结粒熟料的形成需要足够的熟料烧成温度 和时间,又与生料易烧性、煤粉质量、烧成带长度、厚 度以及窑速等有关。在正常生产运行中,应根据实际 生产工艺状况,及时调整系统有关工艺参数,以达到 稳定或提高熟料质量的目的。 (编辑顾志玲)