OEE产能分析培训教程.pptx
合集下载
整体设备效率OEE培训课件
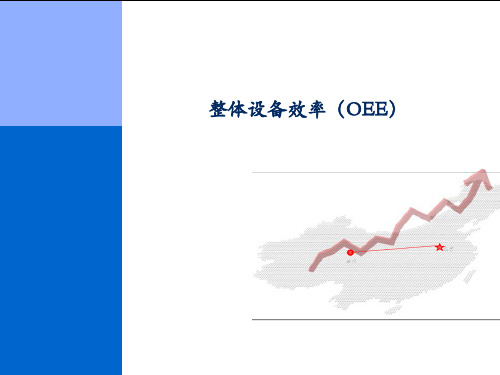
整体设备效率(OEE)
兰州
北京
目录
▪ OEE的作用及定义 ▪ 计算方法 ▪ 减少亏损 ▪ 其它计算举例 ▪ 总结及要点
1
OEE的作用及定义
作用
显示设备和流程的效能,作为改善措施的基础工具, 支援业务目标的实现。
定义
OEE(整体设备效率)作为一个独立的测量工具,它 用来表现实际的生产能力相对于理论产能的比率。它由可 用性、性能和质量指数三个关键因素组成。计算方式如下:
小停机 速度损失
性能损失
不 关 检通闭查、畅不产的到品生位在产等线流流程通;受导阻轨;传清感洁器、一需要般维指护停人机员5分介钟入以的下停,机并不
低于设计产能运行;设备磨损; 任何阻止设备达到设计产能的
员工失误等
因素
废品 返工
质量损失
报废;重工;指标不达标;不合 设备预热、调节等生产正式运
理装配等
行之前产生的次品
及时准确)
▪ 可靠、快捷的生产率 ▪ 闲置时间和废品率的减少可
以确保生产计划的按时执行
成本
▪ 库存
▪ 生产率
▪ 资本支出
▪ 要降低废品率就必须减少在
制品(WIP)
▪ 由于闲置时间缩短,有更多
时间利用资源创造附加值
▪ 释出潜在产能
3
世界级OEE 世界级的OEE指数的渴望值如下所示: 可用性=90.0% 性能=95.0% 质量指数=99.9% OEE=85.0% 经过调查显示:目前世界制造业的平均OEE指数为60%,这就表明了在工 业界还有许多可以改善的空间。
SMED法的三个基本要点
SMED法的5个步骤:
(1)区分“内变换操作”和“外变换操作”。前者是 第一步:观察当前的流程,
兰州
北京
目录
▪ OEE的作用及定义 ▪ 计算方法 ▪ 减少亏损 ▪ 其它计算举例 ▪ 总结及要点
1
OEE的作用及定义
作用
显示设备和流程的效能,作为改善措施的基础工具, 支援业务目标的实现。
定义
OEE(整体设备效率)作为一个独立的测量工具,它 用来表现实际的生产能力相对于理论产能的比率。它由可 用性、性能和质量指数三个关键因素组成。计算方式如下:
小停机 速度损失
性能损失
不 关 检通闭查、畅不产的到品生位在产等线流流程通;受导阻轨;传清感洁器、一需要般维指护停人机员5分介钟入以的下停,机并不
低于设计产能运行;设备磨损; 任何阻止设备达到设计产能的
员工失误等
因素
废品 返工
质量损失
报废;重工;指标不达标;不合 设备预热、调节等生产正式运
理装配等
行之前产生的次品
及时准确)
▪ 可靠、快捷的生产率 ▪ 闲置时间和废品率的减少可
以确保生产计划的按时执行
成本
▪ 库存
▪ 生产率
▪ 资本支出
▪ 要降低废品率就必须减少在
制品(WIP)
▪ 由于闲置时间缩短,有更多
时间利用资源创造附加值
▪ 释出潜在产能
3
世界级OEE 世界级的OEE指数的渴望值如下所示: 可用性=90.0% 性能=95.0% 质量指数=99.9% OEE=85.0% 经过调查显示:目前世界制造业的平均OEE指数为60%,这就表明了在工 业界还有许多可以改善的空间。
SMED法的三个基本要点
SMED法的5个步骤:
(1)区分“内变换操作”和“外变换操作”。前者是 第一步:观察当前的流程,
2019年设备OEE培训课件
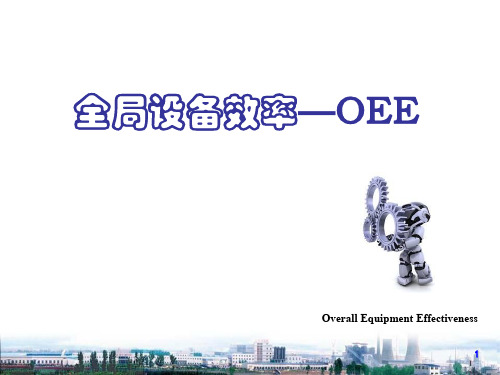
1100
汇报结束 谢谢大家
每日工作充分计划 每日工作详细记录 每日工作认真反省 每日工作努力提高 11
世界范围的研究表明,目前 制造业的平均OEE为60% 。全球工业的OEE平均渴 望值应该为85%(世界级 OEE指数)或者更高。显 而易见,目前的OEE指数 还有许多可以提高的余地。
5
六大损失与OEE的关系
六大损失类别 停机损失
OEE损失类别
注释
有效率
表示设备因为一些大的故障,或者突发事件所引 起的停工。
理想速度*实际运行时间=1/0.6 x 410=683 表现性=450/683=0.658(65.8%) 质量指数=(450—20)/450=0.955(95.5%) OEE=有效率x表现性x质量指数=55.4%
根据上述OEE系统测算所提供的数据,我们可以得知
案
生产效率低与产品合格率对该设备OEE指标干扰较
数三个关键要素组成。
OEE=可用率×表现性×质量指数
设备OEE = 时间开动率×性能开动率×合格品率
33
OEE 三要素
三个关键要素
要素表现
可用率=
操作时间 计划工作时间
它是用来考虑停工所带来的损失,包括引起计划生 产发生停工的任何事件,例如设备故障,原料短缺 以及生产方法的改变等。
表现性=(总产量 / 操作时间) 表现性考虑生产速度上的损失。包括任何导致生产
全局设备效率—OEE
Overall Equipment Effectiveness
1
目录
1、OEE的定义 2、OEE的三要素 3、OEE测算的目的 4、六大损失与OEE的关系 5、OEE案例分析 6、OEE数据的采集注意事项
2
OEE 的定义
汇报结束 谢谢大家
每日工作充分计划 每日工作详细记录 每日工作认真反省 每日工作努力提高 11
世界范围的研究表明,目前 制造业的平均OEE为60% 。全球工业的OEE平均渴 望值应该为85%(世界级 OEE指数)或者更高。显 而易见,目前的OEE指数 还有许多可以提高的余地。
5
六大损失与OEE的关系
六大损失类别 停机损失
OEE损失类别
注释
有效率
表示设备因为一些大的故障,或者突发事件所引 起的停工。
理想速度*实际运行时间=1/0.6 x 410=683 表现性=450/683=0.658(65.8%) 质量指数=(450—20)/450=0.955(95.5%) OEE=有效率x表现性x质量指数=55.4%
根据上述OEE系统测算所提供的数据,我们可以得知
案
生产效率低与产品合格率对该设备OEE指标干扰较
数三个关键要素组成。
OEE=可用率×表现性×质量指数
设备OEE = 时间开动率×性能开动率×合格品率
33
OEE 三要素
三个关键要素
要素表现
可用率=
操作时间 计划工作时间
它是用来考虑停工所带来的损失,包括引起计划生 产发生停工的任何事件,例如设备故障,原料短缺 以及生产方法的改变等。
表现性=(总产量 / 操作时间) 表现性考虑生产速度上的损失。包括任何导致生产
全局设备效率—OEE
Overall Equipment Effectiveness
1
目录
1、OEE的定义 2、OEE的三要素 3、OEE测算的目的 4、六大损失与OEE的关系 5、OEE案例分析 6、OEE数据的采集注意事项
2
OEE 的定义
OEE产能分析课件(PPT 36张)

14000*12=168000
满足
案例B
生产能力分析报告
供应商:XX公司
产品名称及图号:XX轴
项
目
工
序
磨外径
该工序加工
设备
时间(分钟,计划月 含辅助时间)台套② 次数/月
①
磨床
2件/分钟 24000
月调机时间③
时间/每次 (分钟)
总计时间分 钟(品种*次 数/月*时间/
次)
月设备维 修及停工 待料时间 (分钟)
专线和共线的产能分析,区别在于“产能分配百分比”的计 算,其它分析方法一致
28
产能分析问题交流
对以上内容有任何问题 或您在这方面有更深的体会请提出
共同参与交流
29
钓鱼
1、钓鱼方式 2、赢
30
分享共赢 钓鱼方式
传统钓
矶钓
海钓
冰钓
路亚钓
31
分享共赢 鱼竿种类
•
15、只有登上山顶,才能看到那边的风光。
•
16只会幻想而不行动的人,永远也体会不到收获果实时的喜悦。
•
17、勤奋是你生命的密码,能译出你一部壮丽的史诗。
•
1 8.成功,往往住在失败的隔壁!
•
1 9 生命不是要超越别人,而是要超越自己.
•
2 0.命运是那些懦弱和认命的人发明的!
•
21.人生最大的喜悦是每个人都说你做不到,你却完成它了!
•
3、当你还不能对自己说今天学到了什么东西时,你就不要去睡觉。 ——利希顿堡
•
4、人天天都学到一点东西,而往往所学到的是发现昨日学到的是错的。 ——B.V
•
5、学到很多东西的诀窍,就是一下子不要学很多。 ——洛 克
经典OEE培训教材

• 应对措施
– 了解损坏的原因及发生的时间和地点,然后运用根源问题解决 办法来解决
– 使用SMED技术来减少甚至消除设置调整的必要,并实现标准 化的第一轮通过流程
– 如果因为进线部件和原材料的变化而导致损坏,从而需要进行
调整来补偿就要建立部件质量拒收的限制,并使供应商质量管
理也参与到此管理流程
12
6. 质量缺陷
16
质量缺陷
计划外停 机
机器故障
速度下降
换线
损坏
4
OEE计算 – 模型
可编辑
六种重大损失降低机器效能说明
一班总工作时
可使用总工时
操作时间(停工时间 损失)
机器运转时间 (速度损失)
增值 (缺陷损失)
* 计划内停工排除在OEE计算之外
计划内停工*
机器故障 换线 计划外停工 速度降低 损坏 质量缺陷
可用时间 = (可使用总工时) - (窝工时间损失) (可使用总工时)
• 由PLC控制器衡量
• 应对措施 – 明确实际设计速度,最大速度,以及造成速度受限的物理原因 – 请工程人员进行程序检查并进行修改 – 应用Machine Kaizen来查找低速的原因并对设计速度提出质 疑
11
5. 损坏
可编辑
• 定义:工艺处理流程中,即“线上”即被查出的部件
• 由手写废品记录登记测量(注:假设每个部件的损坏造成生产该 部件全部时间的损失,从而将损坏部件数量转化为时间损失)
• 除机器故障或换线的所有计划 管理 外的停产 • 问题根源解决方法
• 由于机器运行速度较设计速度 慢而造成的时间损失 • 问题根源解决方法
• 在组装或调整中的损坏部件 • 问题根源解决方法
oee培训ppt课件
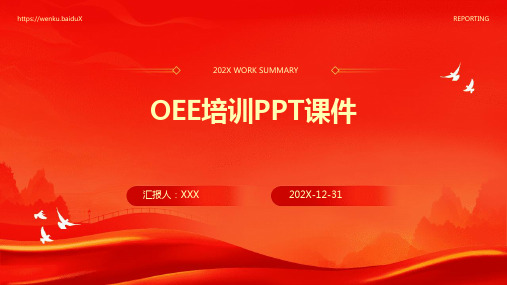
RY
OEE培训PPT课件
汇报人:XXX
202X-12-31
REPORTING
目录
• OEE基本概念 • OEE的重要性和影响 • 如何提高OEE • OEE的监控与改进 • OEE的未来人和时间节点,确保措施的 有效执行。
对改进措施进行风险评估和经 济效益分析,确保措施的公道 性和可行性。
跟踪改进效果
实施改进措施后,持 续监测OEE数据的变 化情况,评估改进效 果。
根据跟踪结果,及时 调整和优化改进措施 ,持续提高OEE水平 。
对改进效果进行统计 分析和可视化展示, 便于团队成员了解改 进成果。
下落生产成本
提高装备效率可以下落生产成本,因为装备效率的提高意味 着生产进程中所需的人力和物力资源更少,能源消耗更低, 从而下落了生产成本。
OEE培训可以帮助员工更好地掌握成本控制的方法和技能, 通过优化生产流程、减少浪费等措施,进一步下落生产成本 。
提升产品质量
01
装备效率的提高可以提升产品质 量,因为装备的稳定高效运行可 以减少产品缺陷和不良品率。
PART 04
OEE的监控与改进
OEE数据收集与整理
确定数据收集的指标
根据装备特点和生产要求,确定需要收集的OEE指标,如开机率 、故障率、准备时间等。
制定数据收集计划
确定数据收集的时间间隔、采集人员和采集方式,确保数据的准确 性和实时性。
数据整理与存储
对收集到的数据进行整理、分类和存储,便于后续的分析和查询。
备用装备
配备备用装备,在主装备故障时,能 够迅速切换到备用装备,保证生产连 续性。
提高操作员技能
培训教育
定期对操作员进行技能培训和安 全教育,提高操作员的专业素养
OEE培训PPT课件
汇报人:XXX
202X-12-31
REPORTING
目录
• OEE基本概念 • OEE的重要性和影响 • 如何提高OEE • OEE的监控与改进 • OEE的未来人和时间节点,确保措施的 有效执行。
对改进措施进行风险评估和经 济效益分析,确保措施的公道 性和可行性。
跟踪改进效果
实施改进措施后,持 续监测OEE数据的变 化情况,评估改进效 果。
根据跟踪结果,及时 调整和优化改进措施 ,持续提高OEE水平 。
对改进效果进行统计 分析和可视化展示, 便于团队成员了解改 进成果。
下落生产成本
提高装备效率可以下落生产成本,因为装备效率的提高意味 着生产进程中所需的人力和物力资源更少,能源消耗更低, 从而下落了生产成本。
OEE培训可以帮助员工更好地掌握成本控制的方法和技能, 通过优化生产流程、减少浪费等措施,进一步下落生产成本 。
提升产品质量
01
装备效率的提高可以提升产品质 量,因为装备的稳定高效运行可 以减少产品缺陷和不良品率。
PART 04
OEE的监控与改进
OEE数据收集与整理
确定数据收集的指标
根据装备特点和生产要求,确定需要收集的OEE指标,如开机率 、故障率、准备时间等。
制定数据收集计划
确定数据收集的时间间隔、采集人员和采集方式,确保数据的准确 性和实时性。
数据整理与存储
对收集到的数据进行整理、分类和存储,便于后续的分析和查询。
备用装备
配备备用装备,在主装备故障时,能 够迅速切换到备用装备,保证生产连 续性。
提高操作员技能
培训教育
定期对操作员进行技能培训和安 全教育,提高操作员的专业素养
OEE培训资料ppt课件
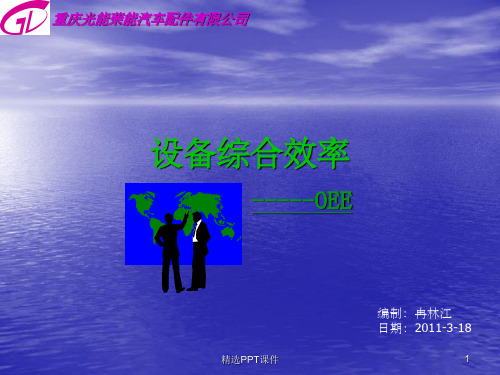
精选PPT课件
15
重庆光能荣能汽车配件有限公司
谢 谢 大 家!
精选PPT课件
16
1. 停工和故障的损失 设备失效需要执行维护操作。其原因有:
–机器过载 –螺钉和螺帽松开 –过渡磨损 –缺少润滑油 –污染物
4. 降低速度的损失
设备在低于其标准设计速度运行导致的 损失。其原因有:
–机器磨损 –人为干扰 –工具磨损 –机器过载
2. 换装和调试的损失
从一种产品到另一种产品换产的时间损 失,或运行时对设置的改动。其原因有:
2. 设备效率损失的分类
大分类 计划损失 停止损失 性能损失 不良损失
中分类 交班时间/就餐/休息/生产中断/预防维修 设备故障/动力事故/换产/流量不足 流量调节/资材短缺/品质问题
瞬间停止/速度降低/空转
不良/再作业
Hale Waihona Puke 公司认可的损失影响OEE 的损失
精选PPT课件
7
重庆光能荣能汽车配件有限公司
影响OEE的六大损失
重庆光能荣能汽车配件有限公司
设备综合效率
-----OEE
精选PPT课件
编制:冉林江 日期:2011-3-18
1
重庆光能荣能汽车配件有限公司
OEE(设备综合效率)
01.设备综合效率的定义 02. 设备效率损失的分类 03. 设备综合效率的计算
精选PPT课件
2
重庆光能荣能汽车配件有限公司
1.设备综合效率的定义
多数企业的OEE标准
世界级企业的OEE标准
废品/返工8%
准备时间10%
设备OEE 50%
停机13%
小中断19%
精选PPT课件
5%
OEE(设备综合效率)分析与管理ppt课件

运行缓慢
库存水平
最新课件
OEE衡量的是礁 石的大小,说明 应该先从哪块暗 礁着手处理。
24
8.OEE可带来的管理效益
1.企业规划: A、可以为企业规划提供客观科學的決策依据。 B、可以为企业提供很多的增值意見和建议。
2.生产管理: A、现场实时数据的收集,建立监控管理系统。 B、对OEE数据分析,规避潜在风险,降低设备六大损失,挖
掘设备最大潜能。 C、为企业精益生产管理提供可视化的生产報告。
最新课件
25
三、OEE的计算方法
2012-8-22
最新课件
26
1.一般企业的时间分类
最新课件
27
1.一般企业的时间分类
最新课件
28
1.一般企业的时间分类
最新课件
29
2.OEE时间分析
最新课件
30
3.设备的六大损失和OEE的关系
最新课件
9
设备运转过快容易造成故障
最新课件
10
您是不是正在制造一个不合格产品
最新课件
11
早晨机器的启动需要花去一定的时间
最新课件
12
二、OEE的定义及开展目的
最新课件
13
1.OEE是什么?
• OEE代表整体设备效能; • 这是一种严格的机器总体性能的衡量手段,揭示时间浪费存
在于哪里,统计各种时间浪费,目的在于实现改进。
最新课件
48
故障是冰山的一角
“如果我们问一问为什么会发生这样的情况——为什么、为什 么、—— 我们通常能找出问题,以及解决问题的方法。
最新课件
49
故障是冰山的一角
故故障障
•灰•灰尘尘、、污污垢垢、、原原料料粘粘附附 •磨•磨损损、、偏偏斜斜、、松松动动、、泄泄露露 •腐•腐蚀蚀、、变变形形、、伤伤痕痕、、裂裂纹纹 •温•温度度、、震震动动、、声声音音等等异异常常
OEE培训教材(ppt44张)

时
间
5大人力损失
11 12 13 14
3大原材料与能源损失
成
15 16
本
我们的近邻联合利华世界500强在经过近10年的OE 的管理,2010年才从12大损失向16大损失迈进。
其中它是先做6大损失到9大损失到12大损失不断的摸索 才有今天的成绩。数据显示联合利华洗衣粉的产量从2004 日产260T/D到2010年日产近1000T/D。其中生产机器只增 了50%。在OEE的数据支撑下结合一些优良的管理方法再 加上公司员工的群策群力下设备的效率平均提高了48.6%
…
OEE 表格
原来 修改制作 在修改的
你会选择那种表?
中国员工的画像
海尔总裁张瑞敏关于人的品质有一段精彩的论述; “如果训练一个日本人,让他每天擦六遍桌子,他一定 会这样做;而一个中国人开始会擦六遍,慢慢觉得五遍 四遍也可以,最后索性不擦了”,“中国人坐事最大毛 是不认真,做事不到位,每天工作欠缺一点,天长地久 成为落后的顽症”。
OEE表的填写标准
上班第一时间填写OEE表上的日期、班次 、机器号、包装机、设定速度 开班清理、点检、润滑后填写开停车时间 开机至机器正常运行时填写试车时间 运行过程中出现如故障、小停机调整等填 写相应项,吃饭停机后要填写吃饭时间 不得提前填写或推迟填写
【OEE】要注意的问题
设备综合效率 = 时间利用率 * 设备性能率 * 产品合格率
1. 时间利用率 = (负荷时间 - 停机损失) / 负荷时间 * 100%
2. 设备性能率 = 生产产品数 / (利用时间 * 设计速度) * 100
3. 质量缺陷率 = (生产产品数 - 不合格品) / 生产产品数 * 1
TPM与PAMCO OEE的差别
设备OEE培训PPT课件
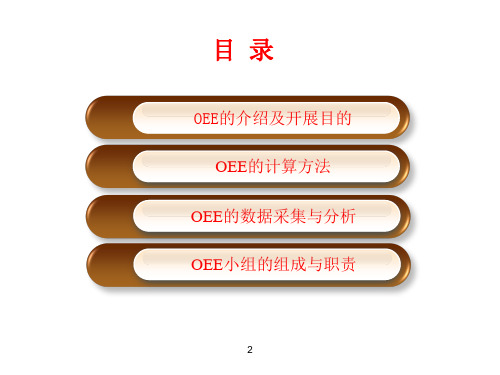
一工厂金工 OEE组长:黄元林
项目责任人 胡楚平
二工厂金工 OEE组长:宋秋阳
一工厂检包 OEE组长:金钱有
19
二工厂检包 OEE组长:刘银火
OEE车间小组结构图
OEE副组长 车间副主任
OEE专员
OEE组员 工程师、领班
1.组长负责整个OEE工作落 实
2.副组长、主管工程师负责 工艺分析与改进方案实施
2.每周进行数据汇总, 分析时间利用率、设 备性能率、产品合格 率指数,找出对应设 备损失
提升步骤
3.针对各项损失做出 改进方案,及时落实 工作
17
四、OEE小组的组成与职责
万丰摩轮设备OEE项目组织结构图
一工厂综合 OEE组长:徐亚忠
一工厂熔铸 OEE组长:张剑辉
二工厂熔铸 OEE组长:陈国云
时间开动率=
* 100%
负荷时间
停
可利用时间
止 损
失 2.空转、间
速
歇停顿
真正利用时间
度 损
失
1.废品、返工
创造价值的
不 良
2.启动、开机
运转时间 损
失
理论循环时间*加工数量
性能开动率=
利用时间
* 100%
加工数量-不合格数量
合格率 =
* 100%
加工数量
10
OEE案例
设某设备某天工作时间为8h, 班前计划停机15min, 故 障停机30min,工装调整25min, 产品的理论加工周期 为0.6 min/件, 一天共加工产品450件, 有20件不合格, 求这台设备的OEE? 根据上面可知: 计划运行时间 =8 x 60 -15 =465 (min) 实际运行时间 =465-30-25=410 (min) 时间开动率 =(410/465)*100%=88.1% 性能开动率 =(450*0.6)/410*100%=65.8% 合格品率 =(450—20)/450*100%=95.5% OEE = 时间开动率x性能开动率x合格品率=55.4%
OEE经典解析ppt课件
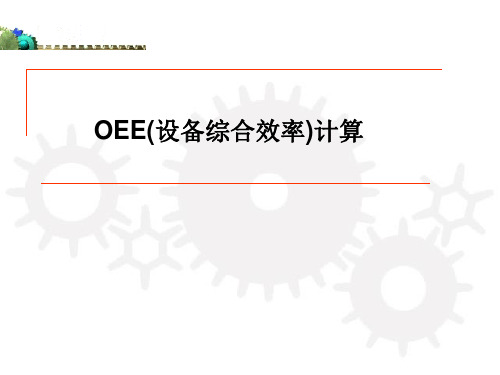
• 设某设备某天工作时间为8小时,班前计划停机10 分钟,故障停机30分钟,设备调整35分钟, 产品 的理论加工周期为1min/件,一天共加工产品400 件,有20件废品,求这台设备的OEE。
①OEE=时间稼动率*性能稼动率*合格率 =86%*98%*95% =80%
②OEE=380/(8*60-10) =80%
一、为什么要实施TPM
丰田等企业为什么会成功
追求精细化管理,维护管理工具
丰田公司数十年如一日的不断追求精细化管理,追求 零库存、零缺陷、低成本和零损耗等。丰田公司有效地运 用了各种各样的管理工具,如5S活动,TQC、TPM、IE、 JIT等,为企业的管理提升服务。这些管理工具在丰田都 能得到有效的坚持,这是它获得成功的必要条件之一。
=(F-T)/F =O / N =L / K =U x V x W
Process 1 Process 2 Process 3 Process 4 Process 5
Capacity analysis Y. Planned uptime (hours/day) Z. Planned uptime (days/week) AA. Planned rate of production (parts/minute) AB. Theoretical production capacity per day AC. Theoretical production capacity per week AD. Weekly Demand AE. Weekly Parts Available for Shipment AF. Daily Demand (DPV) AG. Daily Parts Available for Shipment AH. Percent above/below DPV
①OEE=时间稼动率*性能稼动率*合格率 =86%*98%*95% =80%
②OEE=380/(8*60-10) =80%
一、为什么要实施TPM
丰田等企业为什么会成功
追求精细化管理,维护管理工具
丰田公司数十年如一日的不断追求精细化管理,追求 零库存、零缺陷、低成本和零损耗等。丰田公司有效地运 用了各种各样的管理工具,如5S活动,TQC、TPM、IE、 JIT等,为企业的管理提升服务。这些管理工具在丰田都 能得到有效的坚持,这是它获得成功的必要条件之一。
=(F-T)/F =O / N =L / K =U x V x W
Process 1 Process 2 Process 3 Process 4 Process 5
Capacity analysis Y. Planned uptime (hours/day) Z. Planned uptime (days/week) AA. Planned rate of production (parts/minute) AB. Theoretical production capacity per day AC. Theoretical production capacity per week AD. Weekly Demand AE. Weekly Parts Available for Shipment AF. Daily Demand (DPV) AG. Daily Parts Available for Shipment AH. Percent above/below DPV
OEE培训PPT课件
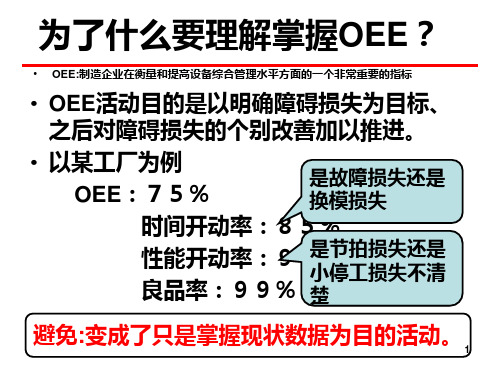
・・・ 23,000分
理论生产时间=∑(计划节拍×生产量)
8
为什么对以手工作业为主体的装配线 参考 应用OEE是不合适的呢?
手工作业为主体的装配线,比方说即使装配设备在 工序内存在,但装配线的频颈还是人的工作,工作的标 准时间成为了理论节拍。
在1个作业周期内,由于作业的次序和熟练度的不 同、作业速度的偏差,存在物品的取放、行走、搬运、 目测监视、修正调整、停工待料等的低附加值作业的损 失、以及由于各作业工序间的作业节拍不同,而产生的 生产线平衡损失(组成效率)等。
休息时间80min,设备故障、工艺调试停机30min。生产线
各工位周期如下表,本班生产了550个,报废2个,维修品数
4个。 OEE?
1
螺钉机
2
旋入机
0.95min 0.9min
3
布胶机
0.8min
4
配光机
0.76min
负荷时间-停止时间
*时间开动率=
负荷时间 =
630min-30min 630min
換)
首先来看看「作业分析」!
例)59厂 UX101自动线ンC9
动力头换模 1 工具准备 2 拆卸外套
拆卸装配螺栓 3 (寻找不够的工具) 4 拆卸动力头 5 清扫拆卸下的动力头
4’43” 34”
8’24” (2’17”)
2’05” 3’15”
有没有徒劳 无用的作业?
作业的顺序 合适吗?
标准化
6 清扫新的动力头
设备故障损失・准备调整损失・小 设备故障损失・准备调整损失・节
停工损失・速度低下损失・质量损 拍低下损失・作业充实度・质量损
失・・
失・・
OEE(设备综合效率)
OEE对人的 作业效率
理论生产时间=∑(计划节拍×生产量)
8
为什么对以手工作业为主体的装配线 参考 应用OEE是不合适的呢?
手工作业为主体的装配线,比方说即使装配设备在 工序内存在,但装配线的频颈还是人的工作,工作的标 准时间成为了理论节拍。
在1个作业周期内,由于作业的次序和熟练度的不 同、作业速度的偏差,存在物品的取放、行走、搬运、 目测监视、修正调整、停工待料等的低附加值作业的损 失、以及由于各作业工序间的作业节拍不同,而产生的 生产线平衡损失(组成效率)等。
休息时间80min,设备故障、工艺调试停机30min。生产线
各工位周期如下表,本班生产了550个,报废2个,维修品数
4个。 OEE?
1
螺钉机
2
旋入机
0.95min 0.9min
3
布胶机
0.8min
4
配光机
0.76min
负荷时间-停止时间
*时间开动率=
负荷时间 =
630min-30min 630min
換)
首先来看看「作业分析」!
例)59厂 UX101自动线ンC9
动力头换模 1 工具准备 2 拆卸外套
拆卸装配螺栓 3 (寻找不够的工具) 4 拆卸动力头 5 清扫拆卸下的动力头
4’43” 34”
8’24” (2’17”)
2’05” 3’15”
有没有徒劳 无用的作业?
作业的顺序 合适吗?
标准化
6 清扫新的动力头
设备故障损失・准备调整损失・小 设备故障损失・准备调整损失・节
停工损失・速度低下损失・质量损 拍低下损失・作业充实度・质量损
失・・
失・・
OEE(设备综合效率)
OEE对人的 作业效率
OEE培训材料ppt课件
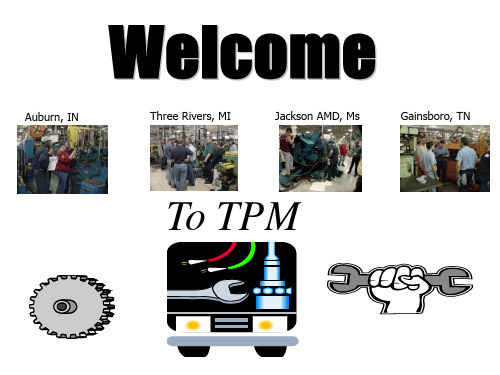
Auburn, IN
Three Rivers, MI
Jackson AMD, Ms
Gainsboro, TN
To TPM
六种损失对设备可生产时间的影响
8 小时
总机器可用时间
设备可用性角 度衡量
总可操作时间
6小时
停机损失
剩余操作时间
4.8小时
生产效率角度衡 量
速度损失
最终可操作时间 不良损失
3.2 小时
2. Observe proper "Lockout/Tagout" procedures when shutting down your equipment
for cleaning.
3. Systematically clean each part of the equipment using the checklist on the next
TPM Services
美国工厂 平均水平
30-45% OEE
55-70%
损失
隐藏的工厂
最大产
85% OEE 15%
损失
能
世界级
TPM Services
OEE
如何计算OEE
设备有效性 X 生产效率 X 质量结果
停机 换型 & 调整 其他
等待 & 微小停机 速度减缓
制程不良 开机或换型不良
提醒: OEE 衡量制造过程中的六种损失
page.
Note: An "abnormal condition" is defined as any condition within, or around the machine that affects the appearance and performance of the machine or production cell. a "normal condition" is defined as a condition in which the machine's appearance and performance is in "like new" condition and no waste is generated in time, resources, or materials. An abnormal condition can be a broken bolt, a leak, a worn or damaged part, it can also be a dirty part. As you document these conditions on your "Abnormality Summary Sheet" try and discover the reasons for them. Ask yourself the following questions:
Three Rivers, MI
Jackson AMD, Ms
Gainsboro, TN
To TPM
六种损失对设备可生产时间的影响
8 小时
总机器可用时间
设备可用性角 度衡量
总可操作时间
6小时
停机损失
剩余操作时间
4.8小时
生产效率角度衡 量
速度损失
最终可操作时间 不良损失
3.2 小时
2. Observe proper "Lockout/Tagout" procedures when shutting down your equipment
for cleaning.
3. Systematically clean each part of the equipment using the checklist on the next
TPM Services
美国工厂 平均水平
30-45% OEE
55-70%
损失
隐藏的工厂
最大产
85% OEE 15%
损失
能
世界级
TPM Services
OEE
如何计算OEE
设备有效性 X 生产效率 X 质量结果
停机 换型 & 调整 其他
等待 & 微小停机 速度减缓
制程不良 开机或换型不良
提醒: OEE 衡量制造过程中的六种损失
page.
Note: An "abnormal condition" is defined as any condition within, or around the machine that affects the appearance and performance of the machine or production cell. a "normal condition" is defined as a condition in which the machine's appearance and performance is in "like new" condition and no waste is generated in time, resources, or materials. An abnormal condition can be a broken bolt, a leak, a worn or damaged part, it can also be a dirty part. As you document these conditions on your "Abnormality Summary Sheet" try and discover the reasons for them. Ask yourself the following questions:
OEE Training分析PPT课件

设备负荷时间 设备开动时间
Planned Production Time(计划生产时间)(ex: 2x8shifts/230 days per year)
Not working hours 非工作时间
Operating Time(操作时间) (计划生产时间—计划测试及欠单停班时间)
清洁,点检 - -预防性维护- -周期性维护 - -会议,休息,培训
12
OEE定义
1,Overall Equipment Effectiveness (设备综合效率)的缩写,
2,由 时间开动率 、性能开动率 以及合格品率 三个关键要素组成
11/14/2020 Title of presentation
13
休息时间
11/14/2020 Title of presentation
生产出的2个 1个合格,一个不良
时间开动率=50%
性能开动率=50% 合格品率=50%
OEE = 50% X 50% X 50% = 12.5%
1 / 8 = 12.5 %
假设效率全部为1,实际开动2小时,4/小时,全部是合格品 合格品=?
11/14/2020 Title of presentation
时间损失
3. 空转和瞬间停机的损失 由于小问题引起的短暂中断。其原因有: -零件卡在滑道里 -清除碎屑 -感应器不工作 -软件程序出错
性能损失
11/14/2020 Title of presentation
4. 降低速度的损失 设备在低于其标准设计速度运行导致的损失。其原
因有: –机器磨损 –人为干扰 –工具磨损 –机器过载
14
OEE定义
1,Overall Equipment Effectiveness (设备综合效率)的缩写,
OEE培训教材

产品缺陷分类的目的
让全体员工都可以去识别我们生产出来产 品是否合格,以及产品缺陷的严重类别指数 。
我们可以通过什么方法达到我们要的效果和目 的?
培训
现场VCS
一点课程
现场活动
OEE 的时间利用表示图
720
690 660
总时间
操作时间
计划停 产时间
负荷时间 利用时间
净利用时间 有价值时间
不合格质量 停产时间 效率停 产时间 停产时 间
TPM与PAMCO OEE的差别
TPM OEE 基于由设备本身所带来的6大损失 ,强调负荷时间 PAMCO OEE 基于工厂业务/管理,前后工序 和设备本身等所带来的损失,强调总时间 PAMCO OEE < TPM OEE
PAMCO 设备效能指标
效率:
–生产效率PE –操作效率OE (E/P) (E/O)
产品合格率
6大损失的形象化
100% 速度损失
生产能力
时间
开车
小停车
质量 缺陷
故障
切换
停机
设备综合效率
设备综合效率 = 时间利用率 * 设备性能率 * 产品合格率
1. 时间利用率 = (负荷时间 - 停机损失) / 负荷时间 * 100% 2. 设备性能率 = 生产产品数 / (利用时间 * 设计速度) * 100% 3. 质量缺陷率 = (生产产品数 - 不合格品) / 生产产品数 * 100%
时
间
5大人力损失
11 12 13 14
成
3大原材料与能源损失
15 16
本
我们的近邻联合利华世界500强在经过近10年的OEE 的管理,2010年才从12大损失向16大损失迈进。 其中它是先做6大损失到9大损失到12大损失不断的摸索中 才有今天的成绩。数据显示联合利华洗衣粉的产量从2004年 日产260T/D到2010年日产近1000T/D。其中生产机器只增加 了50%。在OEE的数据支撑下结合一些优良的管理方法再 加上公司员工的群策群力下设备的效率平均提高了48.6%。 OEE对洽洽是一个陌生的管理方法,对我们来说OEE的 引进是对洽洽百利无一害的。同时联合利华给了我们一个很 好的启示和带头作用。
- 1、下载文档前请自行甄别文档内容的完整性,平台不提供额外的编辑、内容补充、找答案等附加服务。
- 2、"仅部分预览"的文档,不可在线预览部分如存在完整性等问题,可反馈申请退款(可完整预览的文档不适用该条件!)。
- 3、如文档侵犯您的权益,请联系客服反馈,我们会尽快为您处理(人工客服工作时间:9:00-18:30)。
• 2、Our destiny offers not only the cup of despair, but the chalice of opportunity. (Richard Nixon, American President )命运给予我们的不是失望之酒,而是机会之杯。二〇二〇年八月五日2020年8月5 日星期三
10
11
世界制造业OEE指数
12
13
OEE六大损失
质量缺陷
机器故障 速度损失
开停机
切换
小停机
14
什么是六大损失
15
你不可能在设备故障停机时生产出产品
16
设置和调整占用了太多的时间
17
一个微小的问题就会造成设备的停机
18
设备运转过快容易造成故障
19
您是不是正在制造一个不合格产品
20
OEE-产能分析-培训教程
2014-12-26
手机请打到静音 会议上不要接电话
培训前确认事项
您清楚供应商的生产过程 您准备了笔记本电脑
3
OEE的定义 _ 设备综合效率
4
OEE是什么?(看看来源!)
5
OEE是什么?(来看看损失的构成!)
在负荷时间中多大程度 上尽可能没有浪费、而
生产出好产品呢?
专线和共线的产能分析,区别在于“产能分配百分比”的计 算,其它分析方法一致
28
产能分析问题交流
对以上内容有任何问题 或您在这方面有更深的体会请提出
共同参与交流
29
钓鱼
1、钓鱼方式 2、鱼竿种类 3、鱼竿的组成 4、钓鱼的好处
分享共赢
30
分享共赢 钓鱼方式
传统钓
矶钓
海钓
冰钓
路亚钓
31
分享共赢 鱼竿种类
34
考试
填写一份产能分析报告(阶段3)
解答: 1、请验证各工序实际OEE? 2、产能是否满足客户要求? 3、如果不满足,您是公司总经理,你会如何改善?
35
Thank you for your attention!
谢谢!
• 1、Genius only means hard-working all one's life. (Mendeleyer, Russian Chemist) 天才只意味着终身不懈的努力。20.8.58.5.202011:0311:03:10Aug-2011:03
• 3、Patience is bitter, but its fruit is sweet. (Jean Jacques Rousseau , French thinker)忍耐是痛苦的,但它的果实是甜蜜的。11:038.5.202011:038.5.202011:0311:03:108.5.202011:038.5.2020
• 4、All that you do, do with your might; things done by halves are never done right. ----R.H. Stoddard, American poet做一切事都应尽力而为,半途而废永远不行 8.5.20208.5.202011:0311:0311:03:1011:03:10
PPAP阶段3(产能验证) --完成时机:量产爬坡阶段。固定时间,计算产出,满足客 户订单为目的
27
产能分析两种因素
专线设备生产 共线设备生产
专用设备: 指该设备仅用于本工作表中分析的那个零件。
共享设备: 指在该设备上会制造很多不同的零件,且具有更长的工具切换时间
举例: ·冲压设备 ·压铸机 ·热处理设备
100%
负荷时间 价值开动时间
多少%
OEE是什么?(来看看组成!)
7
OEE如何计算?
OEE(设备综合效率) =时间开动率×性能开动率×良品率
负荷时间-停止时间 时间开动效率=
负荷时间
*负荷时间=日历工作时间-计划停机时间
性能开动效率=
计划节拍×产量 开动时间
*开动时间=负荷时间-停止时间
产量-不良数 良品率=
产量
*不良数=废品+返修数
名词:开动率=稼动率=运行效率=Run
OEE计算案例
9
案例:5分钟测试题
工作时间:8h, 班前计划停机:20min, 故障停机:20min, 安装工夹时间:20min, 调整设备时间:20min。
零件加工总数:400件, 单件 理论加工周期为0.5min, 单件实际加工周期为0.8min, 合格品率为98% ;
④
需设备 数(台 /月)
⑤
生产其 他产品 占用该 设备台
数⑥
现有该 设备富 工序加 有台数 工设备 ⑧=⑦-
数⑦ ⑤-⑥
瓶颈工序
5
推荐使用的产能分析表
26
产能分析的三个阶段
产能规划阶段 --完成时机:报价阶段。零件未生产,处于规划阶段
PPAP阶段0(节拍生产) --完成时机:CP/IPSW阶段。固定数量,以计算节拍为目的
14000*12=168000
满足
案例B
生产能力分析报告
供应商:XX公司
产品名称及图号:XX轴
项
目
工
序
磨外径
该工序加工
设备
时间(分钟,计划月 含辅助时间)台套② 次数/月
①
磨床
2件/分钟 24000
月调机时间③
时间/每次 (分钟)
总计时间分 钟(品种*次 数/月*时间/
次)
月设备维 修及停工 待料时间 (分钟)
• 5、You have to believe in yourself. That's the secret of success. ----Charles Chaplin人必须相信自己,这是成功的秘诀。-Wednesday, August 5, 2020August 20Wednesday, August 5, 20208/5/2020
手竿
抛竿
矶竿
路亚竿
32
分享共赢
鱼竿的组成:鱼竿、鱼线、鱼钩、鱼坠、鱼漂、钓饵、钓线
33
分享共赢 钓鱼的好处
1、钓鱼可以修心养性,陶冶情操; 2、钓鱼时水面开阔,空气清新,有益身体健康; 3、钓鱼可以缓解情绪,适于放松工作压力。 4、可以锻炼自己的耐心。 5、鱼儿上钩时的兴奋,可以使自己有一个好心情。 6、享受新鲜的美味。
早晨机器的启动需要花去一定的时间
21
22
23
产能分析最佳时机
工装样件节拍生产时 PSW产能验证时 工艺、设备改进后
24
您可能见过的产能分析报告
案例A
供应商:XX有限公司
生产能力分析报告
产品图号名称 年需求量 瓶颈工序
班产量
月产量
年需求量
结论Байду номын сангаас
AA
150000
磨外圆
500
500*28=14000