JBT 6061 焊缝磁粉检测方法和缺陷迹痕的分级
焊接标准大全-焊接国家标准汇总
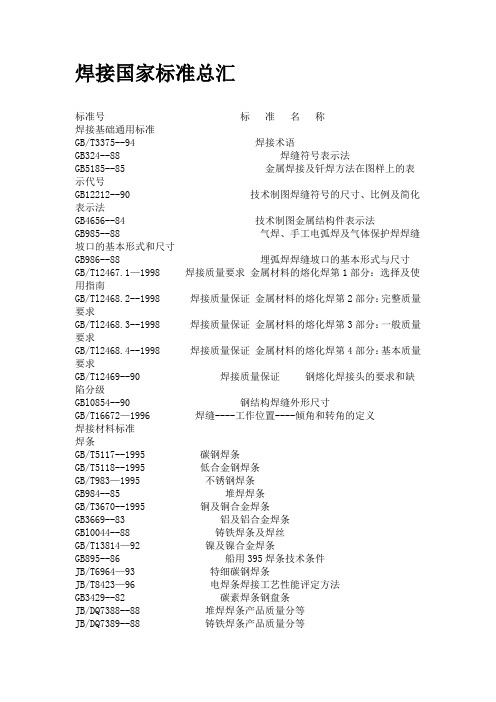
焊接国家标准总汇标准号标准名称焊接基础通用标准GB/T3375--94 焊接术语GB324--88 焊缝符号表示法GB5185--85 金属焊接及钎焊方法在图样上的表示代号GB12212--90 技术制图焊缝符号的尺寸、比例及简化表示法GB4656--84 技术制图金属结构件表示法GB985--88 气焊、手工电弧焊及气体保护焊焊缝坡口的基本形式和尺寸GB986--88 埋弧焊焊缝坡口的基本形式与尺寸GB/T12467.1—1998 焊接质量要求金属材料的熔化焊第1部分:选择及使用指南GB/Tl2468.2--1998 焊接质量保证金属材料的熔化焊第2部分:完整质量要求GB/Tl2468.3--1998 焊接质量保证金属材料的熔化焊第3部分:一般质量要求GB/Tl2468.4--1998 焊接质量保证金属材料的熔化焊第4部分:基本质量要求GB/T12469--90 焊接质量保证钢熔化焊接头的要求和缺陷分级GBl0854--90 钢结构焊缝外形尺寸GB/T16672—1996 焊缝----工作位置----倾角和转角的定义焊接材料标准焊条GB/T5117--1995 碳钢焊条GB/T5118--1995 低合金钢焊条GB/T983—1995 不锈钢焊条GB984--85 堆焊焊条GB/T3670--1995 铜及铜合金焊条GB3669--83 铝及铝合金焊条GBl0044--88 铸铁焊条及焊丝GB/T13814—92 镍及镍合金焊条GB895--86 船用395焊条技术条件JB/T6964—93 特细碳钢焊条JB/T8423—96 电焊条焊接工艺性能评定方法GB3429--82 碳素焊条钢盘条JB/DQ7388--88 堆焊焊条产品质量分等JB/DQ7389--88 铸铁焊条产品质量分等JB/DQ7390--88 碳钢、低合金钢、不锈钢焊条产品质量分等JB/T3223--96 焊接材料质量管理规程焊丝GB/T14957—94 熔化焊用钢丝GB/T14958--94 气体保护焊用钢丝GB/T8110--95 气体保护电弧焊用碳钢、低合金钢焊丝GBl0045--88 碳钢药芯焊丝GB9460--83 铜及铜合金焊丝GBl0858--89 铝及铝合金焊丝GB4242--84 焊接用不锈钢丝GB/T15620--1995 镍及镍合金焊丝JB/DQ7387--88 铜及铜合金焊丝产品质量分等焊剂GB5293--85 碳素钢埋弧焊用焊剂GBl2470--90 低合金钢埋弧焊焊剂钎料、钎剂GB/T6208--1995 钎料型号表示方法GBl0859---89 镍基钎料GBl0046--88 银基钎料GB/T6418--93 铜基钎料GB/T13815--92 铝基钎料GB/T13679--92 锰基钎料JB/T6045--92 硬钎焊用钎剂GB4906--85 电子器件用金、银及其合金钎焊料GB3131--88 锡铅焊料GB8012--87 铸造锡铅焊料焊接用气体GB6052--85 工业液体二氧化碳GB4842--84 氩气GB4844--84 氮气GB7445--87 氢气GB3863--83 工业用气态氧GB3864--83 工业用气态氮GB6819--86 溶解乙炔GBlll74--89 液化石油气GBl0624--89 高纯氩GBl0665--89 电石其它GB12174--90 碳弧气刨用碳棒焊接质量试验及检验标准钢材试验GBl954--80 镍铬奥氏体不锈钢铁素体含量测定方法GB6803--86 铁素体钢的无塑性转变温度落锤试验方法G132971--82 碳素钢和低合金钢断口试验方法焊接性试验GB4675.1--84 焊接性试验斜Y型坡口焊接裂纹试验方法GB4675.2—84 焊接性试验搭接接头(CTS)焊接裂纹试验方法GB4675.3--84 焊接性试验T型接头焊接裂纹试验方法GB4675.4--84 焊接性试验压板对接(FISCO)焊接裂纹试验方法GB4675.5—84 焊接热影响区最高硬度试验方法GB9447--88 焊接接头疲劳裂纹扩展速率试验方法GB/T13817--92 对接接头刚性拘束焊接裂纹试验方法GB2358--80 裂纹张开位移(COD)试验方法GB7032--86 T型角焊接头弯曲试验方法GB9446--88 焊接用插销冷裂纹试验方法GB4909.12—85 裸电线试验方法镀层可焊性试验焊球法GB2424.17--82 电工电子产品基本环境试验规程锡焊导则GB4074.26—83 漆包线试验方法焊锡试验JB/ZQ3690 钢板可焊性试验方法SJl798--81 印制板可焊性测试方法力学性能试验GB2649--89 焊接接头机械性能试验取样方法GB2650--89 焊接接头冲击试验方法GB2651—89 焊接接头拉伸试验方法GB2652—89 焊缝及熔敷金属拉伸试验方法GB2653--89 焊接接头弯曲及压扁试验方法GB2654--89 焊接接头及堆焊金属硬度试验方法GB2655--89 焊接接头应变时敏感性试验方法GB2656--81 焊接接头和焊缝金属的疲劳试验方法焊接材料试验GB3731--83 涂料焊条效率、金属回收率和熔敷系数的测定GB/T3965--1995 熔敷金属中扩散氢测定方法焊接检验GB/T12604.1--90 无损检测术语超声检测GB/T12604.2--90 无损检测术语射线检测GB/T12604.3--90 无损检测术语渗透检测GB/T12604.4--90 无损检测术语声发射检测GB/T12604.5--90 无损检测术语磁粉检测GB/T12604.6--90 无损检测术语涡流检测GB5618--85 线型象质计GB3323--87 钢熔化焊对接接头射线照相和质量分级GB/T12605--90 钢管环缝熔化焊对接接头射线透照工艺和质量分级GB/T14693--93 焊缝无损检测符号GBll343--89 接触式超声斜射探伤方法GBll345--89 钢焊缝手工超声波探伤方法和探伤结果的分级GBll344--89 接触式超声波脉冲回波法测厚GB2970--82 中厚钢板超声波探伤方法JBll52--81 锅炉和钢制压力容器对接焊缝超声波探伤GB/T15830—1995 钢制管道对接环缝超声波探伤方法和检验结果的分级GB827--80 船体焊缝超声波探伤GBl0866--89 锅炉受压元件焊接接头金相和断口检验方法GBll809---89 核燃料棒焊缝金相检验JB/T9215--1999 控制射线照相图像质量的方法JB/T9216--1999 控制渗透探伤材料质量的方法JB/T9217--1999 射线照相探伤方法JB/T9218--1999 渗透探伤方法JB3965--85 钢制压力容器磁粉探伤EJ187--80 磁粉探伤标准JB/T6061--92 焊缝磁粉检验方法和缺陷磁痕的分级JB/T6062--92 焊缝渗透检验方法和缺陷迹痕的分缀EJl86---80 着色探伤标准JB/ZQ3692 焊接熔透量的钻孔检验方法JB/ZQ3693 钢焊缝内部缺陷的破断试验方法GBll373--89 热喷涂涂层厚度的无损检测方法EJ188--80 焊缝真空盒检漏操作规程JBl612--82 锅炉水压试验技术条件GB9251--88 气瓶水压试验方法GB9252--88 气瓶疲劳试验方法GBl2135---89 气瓶定期检查站技术条件GBl2137--89 气瓶密封性试验方法GBll639--89 溶解乙炔气瓶多孔填料技术指标测定方法GB7446--87 氢气检验方法GB4843--84 氩气检验方法GB4845--84 氮气检验方法JB4730—94 压力容器无损检测DL/T820-2002 管道焊接接头超声波检验技术规程DL/T821-2002 钢制承压管道对接焊接接头射线检验技术规程DL/T541-94 钢熔化焊角焊缝射线照相方法和质量分级JB4744—2000 钢制压力容器产品焊接试板的力学性能检验焊接质量GB6416--86 影响钢熔化焊接头质量的技术因素GB6417--86 金属熔化焊焊缝缺陷分类及说明TJl2.1--81 建筑机械焊接质量规定JB/T6043--92 金属电阻焊接接头缺陷分类JB/ZQ3679 焊接部位的质量JB/ZQ3680 焊缝外观质量JB/TQ330--83 通风机焊接质量检验GB999--82 船体焊缝表面质量检验方法A-4 焊接方法及工艺标准GBl2219--90 钢筋气压焊GBll373--89 热喷涂金属件表面预处理通则JB/Z261--86 钨极惰性气体保护焊工艺方法JB/Z286--87 二氧化碳气体保护焊工艺规程JB/ZQ3687 手工电弧焊的焊接规范SDZ019--85 焊接通用技术条件J134251—86 摩擦焊通用技术条件ZBJ59002.1--88 热切割方法和分类ZBJ59002.2--88 热切割术语和定义ZBJ59002.3--88 热切割气割质量和尺寸偏差ZBJ59002.4—88 热切割等离子弧切割质量和尺寸偏差ZBJ59002.5--88 热切割气割表面质量样板JB/ZQ3688 钢板的自动切割ZBK540339--90 汽轮机铸钢件补焊技术条件NJ431—86 灰铸铁件缺陷焊补技术条件GBll630--89 三级铸钢锚链补焊技术条件GB/Z66--87 铜极金属极电弧焊JB/TQ368—84 泵用铸钢件焊补JB/TQ369---84 泵用铸铁件焊补HB/Z5l34--79 结构钢和不锈钢熔焊工艺JB/T6963—93 钢制件熔化焊工艺评定JB4708--2000 钢制压力容器焊接工艺评定JB4709—2000 钢制压力容器焊接规程DL/T752-2001 火力发电厂异种钢焊接技术规程DL/T819-2002 火力发电厂焊接热处理技术规程DL/T868-2004 焊接工艺评定规程DL/T869—2004 火力发电厂焊接技术规程焊接设备标准GB2900-22--85 电工名词术语电焊机GB8118--87 电弧焊机通用技术条件GB8366--87 电阻焊机通用技术条件GBl0249--88 电焊机型号编制方法GBl0977--89 摩擦焊机GB/T13164--91 埋弧焊机ZBJ64001--87 TIG焊焊炬技术条件ZBJ64003--87 弧焊整流器ZBJ64004188 MIG/MAG弧焊机ZBJ64005--88 电阻焊机控制器通用技术条件ZBJ64006--88 弧焊变压器ZBJ64008--88 电阻焊机变压器通用技术条件ZBJ64009--88 钨极惰性气体保护弧焊机(TIG焊机)技术条件ZBJ64016--89 MIG/MAG焊枪技术条件ZBJ64021—89 送丝装置技术条件ZBJ64022--89 引弧装置技术条件ZBJ64023--89 固定式点凸焊机JB5249--91 移动式点焊机JB5250--91 缝焊机ZBJ33002--90 焊接变位机ZBJ33003--90 焊接滚轮架JB5251--91 固定式对焊机JB685--92 直流弧焊发电机JB/DQ5593.1—90 电焊机产品质量分等总则JB/DQ5593.2--90 电焊机产品质量分等弧焊变压器.JB/DQ5593.3--90 电焊机产品质量分等便携式弧焊变压器JB/DQ5593.4--90 电焊机产品质量分等弧焊整流器JB/DQ5593.5--90 电焊机产品质量分等MIG/MAG弧焊机JB/DQ5593.6--90 电焊机产品质量分等TIG焊机JB/DQ5593.7--90 电焊机产品质量分等原动机弧焊发电机组JB/DQ5593.8--90 电焊机产品质量分等TIG焊焊炬JB/DQ5593.9--90 电焊机产品质量分等电焊机冷却用风机JB/DQ5593.10-90 电焊机产品质量分等MIG/MAG焊焊枪JB/DQ5593.11-90 电焊机产品质量分等电阻焊机控制器JB/DQ5593.12-90 电焊机产品质量分等摩擦焊机JB/Z152--81 电焊机系列型谱JB2751--80 等离子弧切割机JBJ33001—87 小车式火焰切割机JBl0860--89 快速割嘴GB5110--85 射吸式割炬JB/T5102--91 坐标式气割机JB5101--91 气割机用割炬JB6104--92 摇臂仿形气割机GB5107--85 焊接和气割用软管接头焊接安全与卫生标准GB9448—88 焊接与切割安全GBl0235--88 弧焊变压器防触电装置GB8197--87 防护屏安全要求GBl2011--89 绝缘皮鞋焊工培训与考试标准GB6419--86 潜水焊工考试规则JJl2.2--87 焊工技术考试规程EJ/Z3--78 焊工培训及考试规程DL/T679--1999 焊工技术考核规程JB/TQ338--84 通风机电焊工考核标准GB/T15169--94 钢熔化焊手焊工资格考试方法SDZ009--84 手工电弧焊及埋弧焊焊工考试规则JBll52--88 机械部焊工技术等级标准国家质量监督检验检疫总局锅炉压力容器压力管道焊工考试与管理规则(船舶)焊工考试规则冶金建设工程焊工考试规则。
JBT6062--92焊缝渗透检验方法和缺陷迹痕的分级

JB/T 6062--92 焊缝渗透检验方法和缺陷迹痕的分级中华人民共和国机械行业标准JB/T6062--92焊缝渗透检验方法和缺陷迹痕的分级──────────────────────────────────1 主题内容与适用范围本标准规定了焊缝及其邻近母材表面开口缺陷的渗透检验方法(着色检验和荧光检验)和缺陷迹痕的分级。
本标准适用于下述金属焊缝的表面开口缺陷检验:(1) 用非磁性材料焊接的焊缝;(2) 磁性材料的角焊缝以及磁粉探伤有困难或者检验效果不好的焊缝,例如对接双面焊焊缝清根过程中的检验等。
2 引用标准GB/T 12604.3无损检测术语渗透检测ZBJ04 005 渗透探伤方法ZBJ04 003 控制渗透探伤材料质量的方法ZBH24 002 渗透探伤用A型灵敏度对比试块JB/T xxxx 渗透探伤用镀铬试块技术条件GB388 石油产品硫含量测定法ZBE30 002 石油产品中氯含量测定法(烧瓶燃烧法)3 检验人员3.1 焊缝渗透检验人员应按有关规程的规定经过严格培训和考核,并持有相应考核组织颂发的等级资格证书。
3.2 焊缝渗透检验人员的视力应每年检查一次,校正视力不得低于1.0,无色盲和色弱。
4 探伤液4.1 探伤液包括渗透剂、乳化剂、清洗剂和显像剂,应对被检焊缝及其母材无腐蚀作用。
4.2 当检验镍合金焊缝时,每种探伤液的硫含量均不应超过用GB388标准分析所得的残留物重量的1%;当检验奥氏体不锈钢或钛合金焊缝时,每种探伤液氯和氟含量之和不应超过用ZBE30002和附录A分析所得的残留物重量的1%。
4.3 应使用同一家生产的同一系列配套探伤液,不允许将不同种类的探伤液混合使用。
4.4 用着色法检验后的焊缝,如果需要进行荧光检验,则荧光检验必须在彻底清理之后才能进行。
4.5 为了控制渗透探伤液质量的需要,可根据ZBJ04003标准的规定,使用符合ZB H24 002或者JB/Txxxx要求的铝合金试块或镀铬试块。
JBT6061焊缝磁粉检测方法和缺陷迹痕的分级

JBT 6061 焊缝磁粉检测方法和缺陷迹痕的分级目次前言 (II)1 范畴 (1)2 规范性引用文件 (1)3 检测人员 (1)4 检测设备 (1)5 磁粉材料 (2)6 磁悬液的配制和选用 (2)7 表面预备 (3)8 磁化方式与磁化规范 (3)9 标准试片和试块 (4)10 检测 (6)11 磁粉的施加 (8)12 磁痕评定与记录 (8)13 复验 (8)14 验收标准 (8)15 报告 (8)图1 周向磁化. (4)图2 纵向磁化. (4)图3 磁场强度指示器. (6)图4 焊缝检测触头的配置 (7)表1 标准试片的类型、规格和图形 (4)表2 磁痕显示的验收等级 (8)请注意本标准的某些内容有可能涉及专利。
本标准的公布机构不应承担识别这些专利的责任。
本标准代替JB/T 6061 —1992《焊缝磁粉检验方法和缺陷磁痕的分级》。
本标准与JB/T 6061 —1992 相比要紧变化如下:——修改了⋯。
本标准由中国机械工业联合会提出。
本标准由全国无损检测标准化技术委员会( SAC/TC 56)归口。
本标准起草单位:哈尔滨锅炉厂有限责任公司。
本标准所代替标准的历次版本公布情形为:——JB/T 6061 —1992。
无损检测焊缝磁粉检测方法和缺陷迹痕的分级1 范畴本标准适用于铁磁性材料金属材料制成的焊缝磁粉检测和缺陷磁痕等级分类方法。
磁粉检测是能够检测焊缝表面和近表面裂缝以及其它不连续性的一种无损检测方法。
要紧检测的典型不连续性有裂缝、未熔合、未焊透、夹杂和气孔等。
磁粉检测采纳周向磁化(直截了当通电法、触头法)和纵向磁化法(线圈法、电磁轭)。
磁粉检测分为干磁粉和湿磁粉检测技术。
2 规范性引用文件下列文件中的条款通过本标准的引用而成为本标准的条款。
凡是注日期的引用文件,其随后所有的修改单(不包括勘误的内容)或修订版均不适用于本标准,然而,鼓舞按照本标准达成协议的各方研究是否可使用这些文件的最新版本。
JBT6062--92焊缝渗透检验方法和缺陷迹痕的分级

JB/T 6062--92 焊缝渗透检验方法和缺陷迹痕的分级中华人民共和国机械行业标准JB/T6062--92焊缝渗透检验方法和缺陷迹痕的分级──────────────────────────────────1 主题内容与适用范围本标准规定了焊缝及其邻近母材表面开口缺陷的渗透检验方法(着色检验和荧光检验)和缺陷迹痕的分级。
本标准适用于下述金属焊缝的表面开口缺陷检验:(1) 用非磁性材料焊接的焊缝;(2) 磁性材料的角焊缝以及磁粉探伤有困难或者检验效果不好的焊缝,例如对接双面焊焊缝清根过程中的检验等。
2 引用标准GB/T 12604.3无损检测术语渗透检测ZBJ04 005 渗透探伤方法ZBJ04 003 控制渗透探伤材料质量的方法ZBH24 002 渗透探伤用A型灵敏度对比试块JB/T xxxx 渗透探伤用镀铬试块技术条件GB388 石油产品硫含量测定法ZBE30 002 石油产品中氯含量测定法(烧瓶燃烧法)3 检验人员3.1 焊缝渗透检验人员应按有关规程的规定经过严格培训和考核,并持有相应考核组织颂发的等级资格证书。
3.2 焊缝渗透检验人员的视力应每年检查一次,校正视力不得低于1.0,无色盲和色弱。
4 探伤液4.1 探伤液包括渗透剂、乳化剂、清洗剂和显像剂,应对被检焊缝及其母材无腐蚀作用。
4.2 当检验镍合金焊缝时,每种探伤液的硫含量均不应超过用GB388标准分析所得的残留物重量的1%;当检验奥氏体不锈钢或钛合金焊缝时,每种探伤液氯和氟含量之和不应超过用ZBE30002和附录A分析所得的残留物重量的1%。
4.3 应使用同一家生产的同一系列配套探伤液,不允许将不同种类的探伤液混合使用。
4.4 用着色法检验后的焊缝,如果需要进行荧光检验,则荧光检验必须在彻底清理之后才能进行。
4.5 为了控制渗透探伤液质量的需要,可根据ZBJ04003标准的规定,使用符合ZB H24 002或者JB/Txxxx要求的铝合金试块或镀铬试块。
焊缝磁粉探伤评定
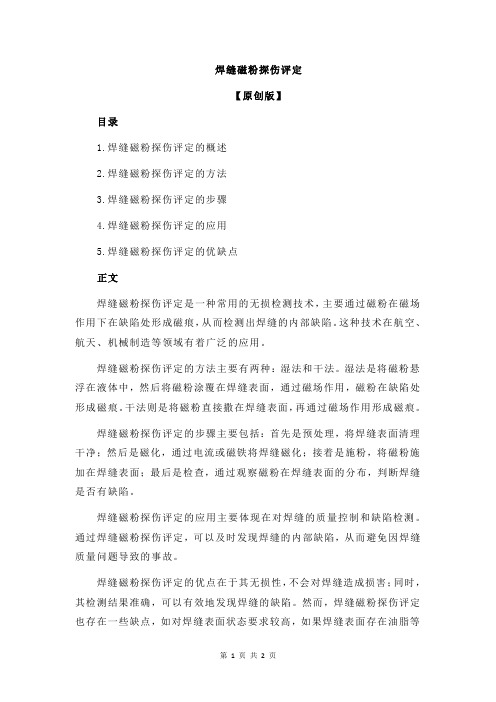
焊缝磁粉探伤评定
【原创版】
目录
1.焊缝磁粉探伤评定的概述
2.焊缝磁粉探伤评定的方法
3.焊缝磁粉探伤评定的步骤
4.焊缝磁粉探伤评定的应用
5.焊缝磁粉探伤评定的优缺点
正文
焊缝磁粉探伤评定是一种常用的无损检测技术,主要通过磁粉在磁场作用下在缺陷处形成磁痕,从而检测出焊缝的内部缺陷。
这种技术在航空、航天、机械制造等领域有着广泛的应用。
焊缝磁粉探伤评定的方法主要有两种:湿法和干法。
湿法是将磁粉悬浮在液体中,然后将磁粉涂覆在焊缝表面,通过磁场作用,磁粉在缺陷处形成磁痕。
干法则是将磁粉直接撒在焊缝表面,再通过磁场作用形成磁痕。
焊缝磁粉探伤评定的步骤主要包括:首先是预处理,将焊缝表面清理干净;然后是磁化,通过电流或磁铁将焊缝磁化;接着是施粉,将磁粉施加在焊缝表面;最后是检查,通过观察磁粉在焊缝表面的分布,判断焊缝是否有缺陷。
焊缝磁粉探伤评定的应用主要体现在对焊缝的质量控制和缺陷检测。
通过焊缝磁粉探伤评定,可以及时发现焊缝的内部缺陷,从而避免因焊缝质量问题导致的事故。
焊缝磁粉探伤评定的优点在于其无损性,不会对焊缝造成损害;同时,其检测结果准确,可以有效地发现焊缝的缺陷。
然而,焊缝磁粉探伤评定也存在一些缺点,如对焊缝表面状态要求较高,如果焊缝表面存在油脂等
物质,可能会影响检测结果。
磁粉探伤检验规范

编号:SHZ—056版次:第一版磁粉探伤检验规范共 4 页(连封面)编制:审核:批准:2020-12-27发布 2020-12-28 实施磁粉探伤检验规范1.零件名称:2.零件图号:3.检测设备:磁轭4.检测方法:连续法5.磁化速度:移动速度应不大于2m/min.6.磁粉:湿黄色磁粉7.磁粉浓度:3-5g/L8.检测规范:JB/T6061-19929.仪器型号:Y-7AC/DC10.验收标准:JB/T6061-1992 I级11.适用范围:焊缝表面及近表面质量的检验和评定.12.磁痕的观察:非荧光磁粉的磁痕应当在白光照射下进行观察,白光强度不小于1000lx.荧光磁粉的磁痕应当在白光强度不大于20lx的阴暗环境下用紫外线灯进行观察,紫外线灯的发光亮度不低于1500uW/cm.13.检测要求:对焊缝表面及近表面缺陷的检验,评定,记录.14.检验人员资格:a.检验人员应按GB 9445的规定取证,经过有关部门考试合格方可从事操作,签发检验报告者必须持有磁粉检验二级以上资格证书.b.检验人员应了解产品焊接中常出现的缺陷类型,部位,方向,并掌握可使重要缺陷不漏检的试验方法.c. 检验人员的校正视力应不低于1.0,并且没有色盲.15.检验方法及要求:a.每班工作前需进行磁悬液度检测及用A试片验证系统灵敏度.b.磁轭的磁极间距在75-200mm,此磁化区域每次应有不少于15mm的重叠.c.对不合格区域用彩色记号笔做出明显的标记.d.在检测角向焊缝时需调节相应的角度.16.操作步骤:a.预处理:检查工作表面.b.磁化:工件(试片).c.施加磁悬液:在磁化过程中用喷嘴喷淋磁悬液(水+磁粉).d.检测:按规定的顺序进行检测并记录.e.缺陷评定:不允许存在任何裂纹和夹渣及所有的线性缺陷.f.统记缺陷.17.磁轭提升的力校定:每半年对磁轭进行提升力校定,交流电磁轭≥44N,直流电磁轭≥117N.18.质量评定和返修后的检验:a.焊缝磁粉检验的质量评定原则上根据缺陷磁痕的类型,长度,间距以及缺陷性质分为四个等级,I级质量最高,IV级质量最低.b.出现在同一条焊缝上不同类型或者不同性质的缺陷,可以选用相同的等级进行评定.c.评定为不合格的缺陷,在不违背焊接工艺规定的情况下,允许进行返修.返修后的检验和质量评定与返修前相同.19.检验报告:检验报告应至少包括下列内容:a.委托单位,报告编号.b.焊接件名称及编号.c.技术蓝图和被检部位.d.焊接件状况(材料,热处理情况,尺寸).e.焊缝情况(焊接方法,焊缝长度,焊缝所在部位).f.检验设备(型号,名称).g.磁粉种类和施加方法.h.磁方法,磁化电流值或磁场强度值.i.人工试片或试块.j.质量评定结果.k.检验日期和报告日期.l.检验者和审核者签名.缺陷磁痕分级表磁粉探伤操作流程1、3-4工作日对磁轭进行提升力检测。
焊缝的无损检测要求及等级分类解释
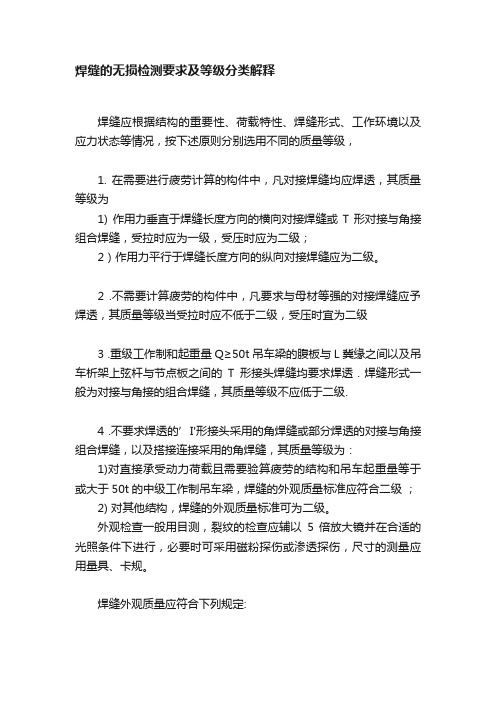
焊缝的无损检测要求及等级分类解释焊缝应根据结构的重要性、荷载特性、焊缝形式、工作环境以及应力状态等情况,按下述原则分别选用不同的质量等级,1. 在需要进行疲劳计算的构件中,凡对接焊缝均应焊透,其质量等级为1) 作用力垂直于焊缝长度方向的横向对接焊缝或T形对接与角接组合焊缝,受拉时应为一级,受压时应为二级;2)作用力平行于焊缝长度方向的纵向对接焊缝应为二级。
2 .不需要计算疲劳的构件中,凡要求与母材等强的对接焊缝应予焊透,其质量等级当受拉时应不低于二级,受压时宜为二级3 .重级工作制和起重量Q≥50t吊车梁的腹板与L冀缘之间以及吊车析架上弦杆与节点板之间的T形接头焊缝均要求焊透.焊缝形式一般为对接与角接的组合焊缝,其质量等级不应低于二级.4 .不要求焊透的’I'形接头采用的角焊缝或部分焊透的对接与角接组合焊缝,以及搭接连接采用的角焊缝,其质量等级为:1)对直接承受动力荷载且需要验算疲劳的结构和吊车起重量等于或大于50t的中级工作制吊车梁,焊缝的外观质量标准应符合二级;2) 对其他结构,焊缝的外观质量标准可为二级。
外观检查一般用目测,裂纹的检查应辅以5 倍放大镜并在合适的光照条件下进行,必要时可采用磁粉探伤或渗透探伤,尺寸的测量应用量具、卡规。
焊缝外观质量应符合下列规定:1 一级焊缝不得存在未焊满、根部收缩、咬边和接头不良等缺陷,一级焊缝和二级焊缝不得存在表面气孔、夹渣、裂纹和电弧擦伤等缺陷;2 二级焊缝的外观质量除应符合本条第一款的要求外,尚应满足下表的有关规定;3 三级焊缝的外观质量应符合下表有关规定焊缝质量等级检测项目二级三级未焊满≤0.2+0.02t 且≤1mm,每100mm长度焊缝内未焊满累积长度≤25mm≤0.2+0.04t且≤2mm,每100mm 长度焊缝内未焊满累积长度≤25mm根部收缩≤0.2+0.02t 且≤1mm,长度不限≤0.2+0.04t且≤2mm,长度不限咬边≤0.05t 且≤0.5mm,连续长度≤100mm,且焊缝两侧咬边总长≤10%焊缝全长≤0.1t 且≤1mm,长度不限裂纹不允许允许存在长度≤5mm 的弧坑裂纹电弧擦伤不允许允许存在个别电弧擦伤接头不良缺口深度≤0.05t 且≤ 0.5mm,每1000mm 长度焊缝内不得超过1 处缺口深度≤0.1t且≤1mm,每1000mm 长度焊缝内不得超过1 处表面气孔不允许每50mm 长度焊缝内允许存在直径≤0.4t 且≤3mm 的气孔 2 个;孔距应≥6倍孔径表面夹渣不允许深≤0.2t,长≤0.5t 且≤ 20mm设计要求全焊透的焊缝,其内部缺陷的检验应符合下列要求:1 一级焊缝应进行100%的检验,其合格等级应为现行国家标准《钢焊缝手工超声波探伤方法及质量分级法》(GB 11345)B 级检验的Ⅱ级及Ⅱ级以上;2 二级焊缝应进行抽检,抽检比例应不小于20%,其合格等级应为现行国家标准《钢焊缝手工超声波探伤方法及质量分级法》(GB 11345)B级检验的Ⅲ级及Ⅲ级以上;3 全焊透的三级焊缝可不进行无损检测。
磁粉探伤评判标准
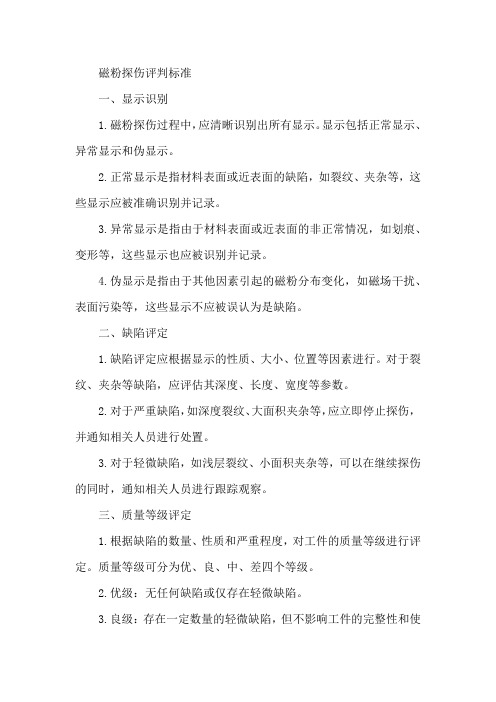
磁粉探伤评判标准一、显示识别1.磁粉探伤过程中,应清晰识别出所有显示。
显示包括正常显示、异常显示和伪显示。
2.正常显示是指材料表面或近表面的缺陷,如裂纹、夹杂等,这些显示应被准确识别并记录。
3.异常显示是指由于材料表面或近表面的非正常情况,如划痕、变形等,这些显示也应被识别并记录。
4.伪显示是指由于其他因素引起的磁粉分布变化,如磁场干扰、表面污染等,这些显示不应被误认为是缺陷。
二、缺陷评定1.缺陷评定应根据显示的性质、大小、位置等因素进行。
对于裂纹、夹杂等缺陷,应评估其深度、长度、宽度等参数。
2.对于严重缺陷,如深度裂纹、大面积夹杂等,应立即停止探伤,并通知相关人员进行处置。
3.对于轻微缺陷,如浅层裂纹、小面积夹杂等,可以在继续探伤的同时,通知相关人员进行跟踪观察。
三、质量等级评定1.根据缺陷的数量、性质和严重程度,对工件的质量等级进行评定。
质量等级可分为优、良、中、差四个等级。
2.优级:无任何缺陷或仅存在轻微缺陷。
3.良级:存在一定数量的轻微缺陷,但不影响工件的完整性和使用性能。
4.中级:存在一定数量的中等缺陷,可能会对工件的完整性和使用性能产生一定影响。
5.差级:存在大量严重缺陷,严重影响工件的完整性和使用性能。
四、报告和记录1.探伤结束后,应编写探伤报告,详细记录探伤过程、显示识别、缺陷评定和质量等级评定等信息。
2.探伤报告应提交给相关部门和人员,以便及时采取相应的处置措施。
3.对于重要的探伤结果,应进行拍照或录像记录,以便后续分析和追溯。
4.所有报告和记录应妥善保存,以便在需要时进行查阅和验证。
磁粉检测技术:磁痕显示验收要求与质量分级
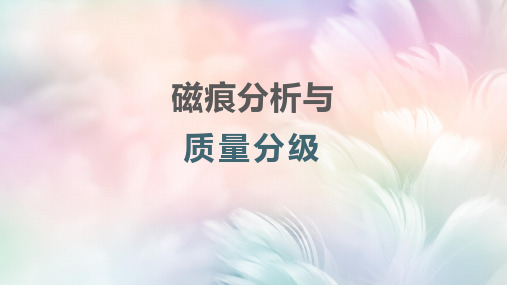
I
L≤1.5
d≤2.0,且在评定框内不大于1个
II
大于I级
注:l表示线性缺陷磁痕长度,单位为mm;d表示圆形缺陷磁痕长径, 单位为mm。
二、磁粉检测质量分级
3)其他部件的质量分级
等级
线性缺陷磁痕
圆形缺陷磁痕 (评定框尺寸为2500mm2,其中一条矩形
边长最大为150mm)
I
不允许
d≤2.0,且在评定框内不大于1个
二、磁粉检测质量分级
磁粉检测质量分为 四个级别,其中Ⅰ级为质量最高级,Ⅳ级为质量最低 级。 1)不允许存在的缺陷 下列缺陷在磁粉检测时不允许存在,否则视为不合格。
不允许任何裂纹显示; 紧固件和轴类零件不允许存在任何横向缺陷。
二、磁粉检测质量分级
2)焊接接头的磁粉检测质量分级
等级 线性缺陷磁痕
圆形缺陷磁痕 (评定框尺寸为35mm×100mm)
II
L≤4.0
d≤4.0,且在评定框内不大于2个
III
L≤6.0
d≤6.0,且在评定框内不大于4个
IV
大于III级
注:l表示线性缺陷磁痕长度,单位为mm;d表示圆形缺陷磁痕长径, 单位为mm。
磁痕分析与 质量分级
Байду номын сангаас
磁痕显示验收 要求与质量分级
一、验收要求(NB/T47013.4-2015)
磁痕的分类与处理
1)长度与宽度之比大于3的缺陷磁痕,按线性磁痕处理;长度与宽度之 比不大于3的缺陷磁痕,按圆形磁痕处理。 2)长度小于0.5mm的磁痕不计。
3)两条或两条以上缺陷磁痕在同一直线上且间距不大于2mm时,按一 条磁痕处理,其长度为两条磁痕之和加间距。 4)缺陷磁痕长轴方向与工件(轴类或管类)轴线或母线的夹角大于或等 于30°时,按横向缺陷处理,其他按纵向缺陷处理。
磁轭检测作业指导书

磁粉检测作业指导书1.适用范围文件适用于磁轭法检测铁磁性材料焊缝(包括热影响区)表面或近表面缺陷的检测方法及质量分级要求。
不适用于非铁磁性材料的检验。
2.术语和定义2.1相关显示:磁粉检测时由缺陷产生的漏磁场吸附磁粉而形成的磁痕显示,一般也称为缺陷显示。
2.2非相关显示:磁粉检测时由截面变化或材料磁导率改变等产生的漏磁场吸附磁粉而形成的磁痕显示。
2.3伪显示:不是由漏磁场吸附磁粉形成的磁痕显示。
2.4纵、横向缺陷:缺陷磁痕长轴方向与工件(轴类或管类)轴线或母线的夹角大于或等于30°时,按横向缺陷处理;其他按纵向缺陷处理。
2.5线状显示:长度大于三倍宽度的显示。
2.6非线装显示:长度小于或等于三倍宽度的显示。
3.检测标准JB/T6061-2007无损检测焊缝磁粉检测4.检测人员资质要求4.1磁粉检测及最终验收结果的评定应由有资格和能力的人员来完成,并取得相关门类等级资格鉴定。
4.2无损检测人员资格级别分为Ⅰ级(初级)、Ⅱ级(中级)和Ⅲ级(高级)。
取得不同无损检测方法不同资格级别的人员,只能从事与该方法和该资格级别相应的无损检测工作。
4.3检测人员的未经矫正或经矫正的近(小数)视力和远(距)视力应不低于5.0(小数记录值为1.0),并一年检查一次,不得有色盲。
5.仪器和校准5.1使用仪器:1CDX-Ⅰ型多功能磁粉探伤仪磁粉检测设备应符合GB/T8290的规定。
5.2提升力校验:磁轭最大间距时,交流电磁轭提升力至少应有45N(4.5Kg),直流电磁轭至少应有177N(18Kg)的提升力。
用于核查提升力的试块重量应进行校准;使用保管过程中发生损坏,应重新进行校准。
电磁轭的提升力至少半年核查一次;磁轭损伤修复后应重新核查。
6.灵敏度试片6.1灵敏度试片主要用于检验磁粉检测设备和磁悬液的综合性能,显示被检工件表面具有足够的有效磁场强度和方向、有效检测区以及磁化方法是否正确。
试片有A1型、C型、D型和M1型。
介绍磁粉检测技术中的缺陷评定和等级划分方法

介绍磁粉检测技术中的缺陷评定和等级划分方法磁粉检测技术是一种常用于金属材料表面缺陷检测的非破坏性检测方法。
它基于磁性材料的磁阻效应,通过施加磁场和施加磁粉,可以有效地检测出材料表面的细小裂纹、毛刺、气孔等缺陷。
在实际应用中,对于检测结果的评定和等级划分非常重要。
缺陷评定是磁粉检测中的关键步骤之一。
通过评定,可以判断出检测结果中的缺陷是否符合相关标准和规范,并进行合理的划分措施。
缺陷评定一般包括对缺陷的类型、位置、尺寸和数量等进行详细描述,并根据检测对象的材料特性和应用要求,确定相应的评定标准。
在磁粉检测中,常用的缺陷评定方法包括定性评定和定量评定。
定性评定主要通过观察和判断缺陷形态、尺寸和位置等特征,对缺陷进行描述和分类。
通过比对评定标准,将缺陷确定为可接受缺陷、不可接受缺陷或重要缺陷等不同等级。
定性评定不需要使用具体的数值,主要依靠检测人员经验和专业知识。
它的优点是简单直观,适用于对一些重要部位缺陷的初步评估。
定量评定是基于检测结果的具体数值进行的评定方法。
它通过测量和计算,对缺陷的尺寸、形状和密度等进行精确确定。
常见的定量评定方法包括缺陷长度评定、缺陷深度评定和缺陷密度评定等。
在这些评定方法中,常用的评定标准有国际标准、行业标准或企业内部标准等。
定量评定的优势是具备更高的准确性和可重复性,适用于对缺陷尺寸和密度有明确要求的应用场景。
等级划分是根据缺陷评定的结果,将检测对象的缺陷按照一定的等级分级。
等级划分是保证磁粉检测结果的可靠性和一致性的重要环节。
在等级划分中,通常将缺陷分为可接受缺陷、不可接受缺陷和重要缺陷三个等级。
其中,可接受缺陷是指对于材料特性和应用要求影响较小的缺陷,可以在一定程度上容忍或修复;不可接受缺陷是指对于材料特性和应用要求影响较大的缺陷,需要进行更严格的处理和修复;重要缺陷是指对材料安全和使用寿命产生重大影响的缺陷,需要立即采取措施进行修复或淘汰。
等级划分的目的是为了帮助用户根据检测结果,确定后续的处理方式和决策。
磁粉检测质量分级

磁粉检测质量分级
1.1不允许任何裂纹显示;紧固件和轴类零件不允许任何横
向缺陷显示。
1.2焊接接头的质量分级按表6进行。
表6 焊接接头的质量分级
等级线性缺陷磁痕圆形缺陷磁痕(评定框尺寸为
35mm×100mm)
Ⅰl≤1.5d≤2.0,且在评定框内不大于1
个
Ⅱ大于Ⅰ级
注:l 表示线性缺陷磁痕长度,单位为mm;d 表示圆形缺陷磁痕长径,单位为mm。
1.3 其他部件的质量分级按表7进行。
表7 其他部件的质量分级
等级线性缺陷磁痕
圆形缺陷磁痕
(评定框尺寸为2500mm2其中一条矩形边长最大为150mm)
Ⅰ不允许d≤2.0,且在评定框内不大于1个Ⅱl≤4.0d≤4.0,且在评定框内不大于2个Ⅲl≤6.0d≤6.0,且在评定框内不大于4个Ⅳ大于Ⅲ级
注:l 表示线性缺陷磁痕长度,单位为mm;d 表示圆形缺陷磁痕长径,单位为mm。
10 在用承压设备的磁粉检测
对在用承压设备进行磁粉检测时,其内壁宜采用荧光磁
粉检测方法进行检测。
制造时采用高强度钢以及对裂纹(包
括冷裂纹、热裂纹、再热裂纹)敏感的材料,或长期工作在
腐蚀介质环境下有可能发生应力腐蚀裂纹的承压设备,其内
壁应采用荧光磁粉检测方法进行检测。
检测现场环境应符合
6.2.2的要求。
焊缝、边缘及其他表面缺陷部位的处理等级
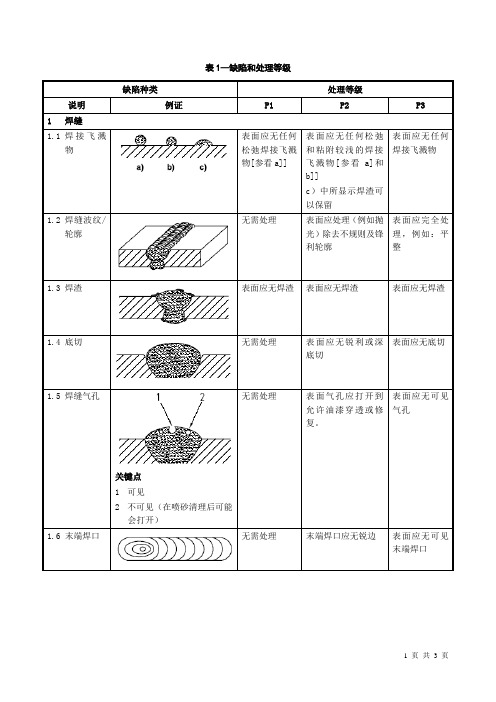
P3
2边缘
2.1卷边
无需处理
无需处理
边缘应带圆,半径不少于2mm
(参看ISO 12944-3)
2.2边缘由冲孔、剪切、锯或钻形成
主要原因
1冲孔
2剪切
边缘任何部分不可锐利;边缘应无毛边。
边缘任何部分不可锐利;边缘应无毛边。
边缘应是带圆,半径不少于2mm
(参看ISO12944-3)
2.3热切边
表面应无夹渣和疏松的氧化皮
1.3焊渣
表面应无焊渣
表面应无焊渣
表面应无焊渣
1.4底切
无需处理
表面应无锐利或深底切
表面应无底切
1.5焊缝气孔
关键点
1可见
2不可见(在喷砂清理后可能会打开)
无需处理
表面气孔应打开到允许油漆穿透或修复。
表面应无可见气孔
1.6末端焊口
无需处理
末端焊口应无锐边
表面应无可见末端焊口
缺陷种类
处理等级
说明
例证
P1
边缘任何部份应无不规则外形。
应去除切面,边缘应带圆,半径不少于2mm
(参看ISO 12944-3)
3一般表面
3.1麻点和焊口
麻点和焊口应足够地打开,允许油漆穿透
麻点和焊口应足够地打开,允许油漆穿透
表面应无麻点和焊口
3.2结疤
注释:英语中“毛刺”和“锯齿形缺陷”也用以描述这类缺陷。
表面应无翘起材料
表面应无可见结疤
3.6压痕和辊印
无需处理
压痕和辊印应平滑
表面应无压痕和辊印
表面应无可见结疤
3.3滚压筛渣/滚压分层/切削分层
表面应无翘起材料
表面应无可见滚压-筛渣/分层
- 1、下载文档前请自行甄别文档内容的完整性,平台不提供额外的编辑、内容补充、找答案等附加服务。
- 2、"仅部分预览"的文档,不可在线预览部分如存在完整性等问题,可反馈申请退款(可完整预览的文档不适用该条件!)。
- 3、如文档侵犯您的权益,请联系客服反馈,我们会尽快为您处理(人工客服工作时间:9:00-18:30)。
JBT 6061 焊缝磁粉检测方法和缺陷迹痕的分级目次前言 (II)1 范畴 (1)2 规范性引用文件 (1)3 检测人员 (1)4 检测设备 (1)5 磁粉材料 (2)6 磁悬液的配制和选用 (2)7 表面预备 (3)8 磁化方式与磁化规范 (3)9 标准试片和试块 (4)10 检测 (6)11 磁粉的施加 (8)12 磁痕评定与记录 (8)13 复验 (8)14 验收标准 (8)15 报告 (8)图1 周向磁化 (4)图2 纵向磁化 (4)图3 磁场强度指示器 (6)图4 焊缝检测触头的配置 (7)表1 标准试片的类型、规格和图形 (4)表2 磁痕显示的验收等级 (8)前言请注意本标准的某些内容有可能涉及专利。
本标准的公布机构不应承担识别这些专利的责任。
本标准代替 JB/T 6061—1992《焊缝磁粉检验方法和缺陷磁痕的分级》。
本标准与 JB/T 6061—1992 相比要紧变化如下:——修改了…。
本标准由中国机械工业联合会提出。
本标准由全国无损检测标准化技术委员会(SAC/TC 56)归口。
本标准起草单位:哈尔滨锅炉厂有限责任公司。
本标准所代替标准的历次版本公布情形为:——J B/T 6061—1992。
无损检测焊缝磁粉检测方法和缺陷迹痕的分级1 范畴本标准适用于铁磁性材料金属材料制成的焊缝磁粉检测和缺陷磁痕等级分类方法。
磁粉检测是能够检测焊缝表面和近表面裂缝以及其它不连续性的一种无损检测方法。
要紧检测的典型不连续性有裂缝、未熔合、未焊透、夹杂和气孔等。
磁粉检测采纳周向磁化(直截了当通电法、触头法)和纵向磁化法(线圈法、电磁轭)。
磁粉检测分为干磁粉和湿磁粉检测技术。
2 规范性引用文件下列文件中的条款通过本标准的引用而成为本标准的条款。
凡是注日期的引用文件,其随后所有的修改单(不包括勘误的内容)或修订版均不适用于本标准,然而,鼓舞按照本标准达成协议的各方研究是否可使用这些文件的最新版本。
凡是不注日期的引用文件,其最新版本适用于本标准。
GB 9445 无损检测人员技术资格鉴定通则JB 4730 压力容器无损检测(磁粉检测部分)JB/T 6063 磁粉探伤用磁粉技术条件JB/T 6065 无损检测磁粉检测用试片JB/T 8290 磁粉探伤机3 检测人员3.1 凡从事磁粉检测的无损检测人员应按照GB 9445进行考核,取得相应的资格证书方可从事相应方法的检测工作。
签发检测报告者必须持有磁粉检测Ⅱ级及Ⅱ级以上资格证书。
3.2 检测人员应了解焊接工艺,熟悉焊缝中可能显现的缺陷类型、部位及方向,并把握典型焊缝的检测方法。
3.3 从事磁粉检测的人员,不得有色盲、色弱。
3.4 从事磁粉检测的人员,校正视力不得低于1.0,并一年检查一次。
4 检测设备4.1 焊缝磁粉检测设备必须符合JB/T 8209中的有关规定。
4.2 电流表4.2.1 磁化设备上用以指示磁化电流的电流表应至少每年校准一次,设备进行定期电气修理或损害修复后必须进行校准。
设备停止使用一年或更长时刻,则应在第一次使用前进行校准。
4.2.2 在电流表指示的量程范畴内,其校准点应许多于3个。
设备上的电流表读数与标准电流表读数之间的误差应不超过满量程的10%。
4.2.3 校准电流表使用的计量外表和器具都必须具有计量合格证书。
4.3 触头式检测设备:触头式检测设备通常用于局部磁化,如图1(b)所示。
接触工件的触头应是铝、铜编织物,而不是实心铜。
用实心铜触头时,触头安置或移动会引起电弧和过热,从而造成工件表面渗铜,进而可能会引起金属软化、硬化或开裂等。
开路电压不超过25V。
4.4 磁轭式检测设备:交流及直流磁轭通常是П字形的电磁铁,如图2(a)所示。
焊缝检测用便携式磁轭应配有活络关节的磁极,以便有利于与圆弧形表面或有一定夹角的两个表面的良好接触。
4.5 磁轭的提升力4.5.1 磁轭的提升力至少每年校验一次。
如果磁轭已一年或一年以上没有使用,或刚刚修过第一次使用前应校验提升力。
4.5.2 当使用磁轭最大间距时,交流电磁轭至少应有大于4.5kg(44N)的提升力。
直流电磁轭的提升力至少应有大于18.1kg(177N)。
4.6 用于施加干磁粉的喷粉器应能平均地喷洒出雾状的干燥磁粉,并产生足够的压缩气流,用以吹掉被检表面上没有形成磁痕的磁粉。
喷粉器应定期检查,发生故障应及时修复。
4.7 设备的校验和修复情形都应有文字记录,并作为设备档案妥善保管。
5 磁粉材料5.1 磁粉类型:用于焊缝检测的磁粉应是细小弥散的铁磁性材料。
磁粉类型按其观看条件可分为荧光磁粉和非荧光磁粉,按载体不同可分为干粉和湿粉;按其颜色又可分为黑色、红色、白色、灰色等。
5.1.1 荧光磁粉:在紫外光照耀下观看磁痕显示的磁粉称为荧光磁粉。
荧光磁粉是以磁性氧化铁粉、工业纯铁粉或铁基粉为核心,在别处用树脂粘附一层荧光染料而制成的。
由于荧光磁粉在紫外光照耀下,能发出波长范畴在510~550nm为人眼同意最敏锐的色泽鲜艳的黄绿色荧光,因此荧光磁粉的可见度以及与工件表面的对比度都专门高。
荧光磁粉一样只适用于湿法。
5.1.2 非荧光磁粉:在可见光下观看磁痕显示的磁粉称为非荧光磁粉。
常用的非荧光磁粉能够是黑色、红色或灰色等,选用的磁粉颜色应对被检测表面有适当的对比度,必要时还可在被检部位喷刷一层反差增强剂,关心提升对比度,然而喷刷的厚度应尽量小,否则会降低检测灵敏度。
5.1.3 识别度:是指磁粉的光学性能,包括磁粉的颜色、荧光亮度及工件表面颜色的对比度。
关于非荧光磁粉,只有磁粉的颜色与工件表面的颜色形成专门大对比度时,磁痕才容易观看到,缺陷才容易被发觉;关于荧光磁粉,在紫外光下观看时,工件表面出现紫色,只有柔弱的可见光本底,磁痕呈黄绿色,色泽鲜艳,能够提供最大的对比度和亮度。
5.1.4 干粉:干法磁粉是将磁粉在空气中吹成雾状喷洒到工件表面的磁粉。
常用的黑磁粉和红磁粉既适用于湿粉,也适用于干粉;用粘合剂包覆制成的白磁粉或其它颜色的磁粉,一样只用于干粉。
5.1.5 湿粉:湿粉是将磁粉悬浮在油或水载液中喷洒到工件表面的磁粉。
5.2 磁粉性能:磁粉应具有高的导磁率、低的顽磁性与较好的分散力。
磁粉的粒度应平均。
其形状应便于流淌。
磁粉应是无毒、无锈、无油脂和污垢等,以免干扰其使用,磁粉各性能指标应符合JB/T 6063的规定。
5.3 磁粉储存:磁粉应置于密封容器内,并在干燥环境中贮存,或者配置成磁膏备用。
否则,使用前应将磁粉在60~80℃下烘干1h。
必要时还应当重新进行研磨和选择,然而此法不适用于荧光磁粉。
5.4 选择磁粉:在白炽光强烈照耀的室内以及有自然光强烈照耀的野外场所检测焊缝时,宜采纳非荧光磁粉。
在检测场所比较阴暗或夜间或检测灵敏度要求较高时,宜采纳荧光磁粉。
在需要实现自动化检测的部门,更应当采纳荧光磁粉。
6 磁悬液的配制和选用6.1 用于配制磁悬液的载体可分为油剂和水基两种。
常用的油剂载体为变压器油、煤油、或变压器油和煤油的混合液,举荐使用无味煤油。
常用的水剂载液为含有添加剂的水。
6.2 在水中加入添加剂的目的是为了改善水剂载体的性能,使得载体对磁粉具有良好的分散作用和保质作用,加入载液的磁粉能被平均地分散开来,并在磁悬液的规定贮存期内性能不变;当磁悬液施加到焊缝表面时,使其具有良好的润湿、消泡、防锈作用。
6.3 配制磁悬液时,第一应把磁粉或磁膏用少量载液调成平均的糊状,然后在连续搅拌中缓慢加入所需的载液,直至磁粉和载液之间达到规定比例为止。
6.4 在用油剂载液配制荧光磁粉的磁悬液时,应优先选用无味煤油。
在用水剂载液配制荧光磁粉的磁悬液时,应尽可能使用磁粉制造厂举荐的载液,防止荧光磁粉在载液中显现结团、溶解等现象。
6.5 磁悬液浓度应按照磁粉种类、粒度及载液类型和施加方法确定。
新配置的非荧光水基磁悬液,磁粉浓度一样为10~25g/L,荧光磁粉浓度0.5~3g/L。
6.6 磁悬液性能及浓度的验证6.6.1 磁悬液浓度可采纳磁悬液浓度验定管测定其沉淀进行验证,在取样前,将新配制的磁悬液充分搅拌至少30min后,取100ml磁悬液注入验定管,静止30min后,观看验定管底部沉积的体积即表示磁悬液浓度。
对非荧光磁粉的沉淀体积每100ml磁悬液应为1.2~2.4ml;荧光磁粉每100ml磁悬液是0.1~0.4ml。
6.6.2 采纳带有已知人工缺陷的工件或灵敏度试片对检测用磁悬液性能进行验证,按标准举荐的磁化规范,对工件磁化可验证的磁悬液,将得到的磁痕显示与性能已认可磁悬液花纹的磁痕显示作对比,以便确定磁悬液性能。
参考磁痕为实际磁痕、磁痕照片和磁痕复制品等。
6.7 选用:检测表面涂刷过油类物质或被油类物质污染过的焊缝,宜用油剂载液配制的磁悬液。
对表面比较潮湿的焊缝以及有防火要求的焊缝检测,一样不承诺有油污染,宜用水剂载液配制的磁悬液。
触头法检测中也最好使用由水剂载液配制的磁悬液。
7 表面预备7.1 一样情形下焊缝及其邻近母材表面已能满足检测要求,但若表面凸凹不平以致能掩盖缺陷显示时,应采纳砂轮打磨或机械加工来制备表面。
被检工件表面粗糙度Ra应不大于12.5µm。
7.2 在磁粉检测前,被检测表面及所有邻近至少25mm的区域内应是干燥的,同时没有任何污垢、油脂、纤维屑、锈皮、焊剂、焊接飞溅或者其他阻碍检测的外来物。
7.3 被检表面必须通过表面目视检查合格后,才能进行磁粉检测。
7.4 反差增强剂是氧化锌等白色粉末与易挥发的有机溶剂等组成的悬浮液。
要紧用来增强被检工件表面与磁粉或和磁悬液之间的对比度。
使用反差增强剂,需在磁化工件前在其被检表面喷涂一层极薄的(25~45微米)反差增强剂,待其干燥后形成白色薄膜就能够磁化工件并施加磁粉或磁悬液,不但增强了对比度而且提升了磁痕显示,易于观看磁痕和评定磁痕。
8 磁化方式与磁化规范8.1 焊缝磁粉检测采纳的磁化方式要紧有:周向磁化和纵向磁化。
8.1.1 周向磁化:通电法和触头法,如图1所示。
8.1.2 纵向磁化:线圈法和磁轭法,如图2所示。
8.2 用于焊缝磁粉检测的磁化电流有:直流电和全波整流电、半波整流电和交流电。
常用的是半波整流电和交流电。
为了检测埋藏深度较大的缺陷,应使用直流电或全波整流电。
当焊缝位于形状复杂、尺寸变化大的焊接件上时,应使用交流电或半波整流电。
在干法检测中及检测后需退磁的焊缝检测中,也可使用交流电或者半波整流电。
a)通电法 b)触头法图1 周向磁化a)线圈法 b)磁轭法图2 纵向磁化8.3 在剩磁法检测中,如果需要使用交流电或半波整流电,应加断电相位操纵器,把断电时刻操纵在π/2~π和3π/2~2π之间。
8.4 用通电法进行焊缝的整体磁化时,磁化电流值可用式(1)求得:I=HD/0.32 (1)式中:I——磁化电流值,A;D——焊接件的等效直径,m;H——磁场强度,可在2400~4800A/m之间选用。