价值流培训课件(最终版)
价值流分析培训课件

绘制价值流图:根据收集的数据,绘制出产品或服务的 整个价值流图,包括原材料采购、生产、物流、销售等 环节。
步骤4
分析价值流:对绘制的价值流图进行分析,找出浪费的 环节和瓶颈,提出改进方案。
步骤5
制定并实施改进计划:根据分析结果,制定改进计划并 实施,以消除浪费、提高效率。
步骤6
监控与评估:对改进计划实施情况进行监控与评估,以 确保改进目标的实现。
03
价值流瓶颈分析
瓶颈识别与确认
1 2
收集数据
收集生产过程中的各种数据,包括但不限于物 料、人力、设备、能源等的使用情况。
数据分析
对收集的数据进行深入分析,找出可能导致价 值流瓶颈的因素。
3
现场确认
到生产现场进行实地观察和调查,确认瓶颈的 存在。
瓶颈分析与优化建议
原因分析
对已确认的瓶颈进行深入分析,找出导致瓶颈的 具体原因。
优化方案制定
根据原因分析结果,制定相应的优化方案,如改 进生产工艺、提高设备精度、优化物料管理等。
方案评估与选择
对所有优化方案进行评估,选择最合适的方案进 行实施。
瓶颈解决方案的实施与跟踪
实施方案
按照所选方案进行实施,确保 方案的执行力度和效果。
跟踪监测
在方案实施过程中,对实施效果 进行实时跟踪和监测,及时发现 并解决可能出现的问题。
效果评估
在方案实施完成后,对实施效果进 行评估,确认是否已解决价值流瓶 颈问题。
04
价值流持续改进
持续改进的思路与方法
定义价值流
分析价值流
制定改进计划
实施改进
评估改进效果
识别产品或服务的全部 活动,包括从需求收集 到产品交付的各个环节 。
价值流图分析步骤PPT培训课件
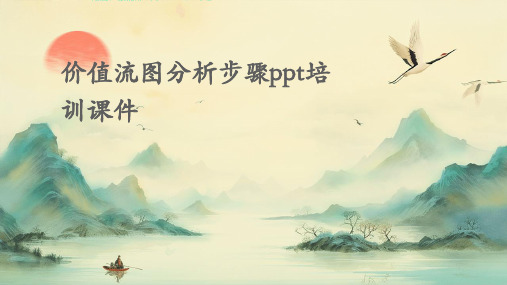
案例二:物流行业价值流图分析
总结词
物流行业是价值流图分析的重要应用领域,通过分析物流过程中的各个环节,优化物流运作,降低成 本并提高客户满意度。
详细描述
在物流行业中,价值流图分析可以帮助企业识别物流过程中的瓶颈和浪费,进而优化物流运作。通过 分析运输、仓储、装卸和配送等环节,企业可以发现潜在的改进空间,例如提高运输效率、降低仓储 成本、优化装卸作业等。这些优化措施可以降低成本并提高客户满意度。
THANKS
感谢观看
3
促进跨部门协作
价值流图分析需要各部门的参与和协作,有助于 打破部门壁垒,促进跨部门沟通与合作。
价值流图分析的步骤概述
确定分析对象
选择要分析的产品或过程,明确分析的目标 和范围。
数据收集
收集相关数据,包括各阶段的时间、数量、成 本等信息。
绘制价值流图
根据收集的数据,绘制产品从原材料到最终消费 者的整个过程的价值流图。
总结词
生产制造行业是价值流图分析的重要应用领域,通过分析生产过程中的物流、信息流和资金流,优化生产流程, 提高生产效率。
详细描述
在生产制造行业中,价值流图分析可以帮助企业识别生产过程中的瓶颈和浪费,进而优化生产流程,提高生产效 率。通过分析原材料的采购、加工、组装和配送等环节,企业可以发现潜在的改进空间,例如减少库存、降低运 输成本、提高设备利用率等。
02
它通过图形表示各个活动之间的 关系和时间顺序,帮助企业了解 产品在生产过程中的流动情况, 发现瓶颈、浪费和低效问题。
价值流图分析的意义
1 2
识别生产过程中的瓶颈和浪费
价值流图分析可以清晰地展示生产过程中的各个 环节,帮助企业发现瓶颈和浪费,如等待时间、 运输、库存等。
价值流培训教材课件_1

机床事业部CA36系列工厂级价值流现状分析
节拍时间:25.7 分钟 制造周期:62.7天 增值比例:2.9% 成品库存:0.83亿(7
1.8天) 在制品:0.61亿
21
四、为什么采用价值流分析
目视
• 整体流程目视化,而不仅仅是单个流程 • 从顾客角度看待流程(外部顾客) • 上游对下游工序的影响 (内部顾客) • 便于识别流程中浪费 • 显示物料和信息流之间的联系 • 将不同部门或职能的问题联系在一起
7
价值流图是一个基本工具
分析价值
关注整个
流的现状
生
系统的流动
系统地
产
发现问题
流
识别和消除 系统
和流程中的 浪费
是讨论生 产过程的 共通语言
信 息 流
8
可借助衡量指数来了解制 造过程绩效及改善目标
实施改善计划的基础
实施精益制造的蓝图
价值流图是一个基本工具
是一个量化的工具
显示信息流、工艺流、材料流的
I
2700P 1440NP
4.1D
53
步骤6 时间线填充
填入作业周期时间
Assembly
45,000pcs/mo - 5,400 P
过程的改善
过程改善就是在生产现 场的小组层级消除浪费, 以人员和工艺流程为焦 点。
26
无先、后与高、低之分 一个的改进可以促进另一个的改进. 两者需要互相促进.
27
绘制价值流的目的
价值流图是精益制造的工具,完整的绘制出价值流图后,引入目视化 能看到整个制造系统;
1
问题的解决 过程的了解与培训 减少缺陷
面向生产线— 一线员工
流程改 善(价值流推进) 焦点在物流和信息流
价值流分析培训教材PPT(共 52张)

第三章
如何绘制价值流 (how)
16
“ 究 竟 咋 画 的 呢 ? ? ? ”
17
价值流图析图标
物流图标
ASSEMBLY
内部工艺工程
XYZ Corporation
外部资源
C/T = 45 sec C/O = 30 mins 3 Shifts 2% Scrap
数据筐
I
300 pieces 1 Day
Overall Process Lead Time = 10,400 seconds
Lead Time 1 = 10,100 s
Lead Time 2= 200 s
Lead Time 3 = 100s
Supplier
90 S 10 s
CT = 100s VA % = 10% NVA% = 90%
100 units
31
VSM识别: • 理解价值 • 清晰识别价值实现的每个过程的始点、终点 • 识别增值的过程操作
– 只承认直接使价值实现成为可能的绝对有必要的步骤
• 把增值步骤链接起来
32
价值流现状图分析
• 几个重要的参数:
– 增值时间/周期时间 – 平均库存数量
n 整体改进而不是局部优化 n 观察并了解物流与信息流 n 憧憬“未来状态”
1.定义价值
n给输出物命名 n确定输出物的接收者 n对输出物进行描述 n与输出物的接收者共同去确定输出物的规格及标准
22
客户眼中的增值 客户认为:
我需要,并愿意支付的; 产品、服务发生了有形变化的; 正确的时间一次做好交付给我;
以上三点必须同时具备才会被认为是增值。。。。。。
23
价值过程
商务功能 确认客户
2024版精益价值流程VSM培训PPT
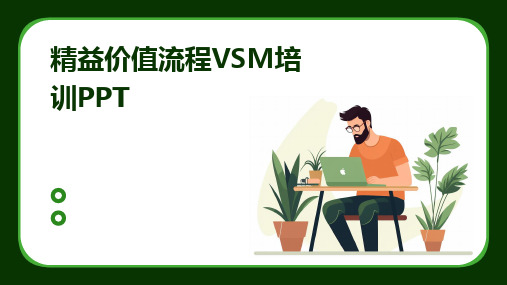
精益价值流程VSM培训PPT•精益价值流程VSM概述•精益价值流程VSM核心原理•精益价值流程VSM实施步骤•精益价值流程VSM在制造业应用案例目录•精益价值流程VSM在服务业应用案例•精益价值流程VSM培训总结与展望01精益价值流程VSM概述精益思想与VSM关系精益思想强调消除浪费,持续改进,追求卓越。
VSM 作为精益思想的重要工具,通过可视化价值流,识别浪费,推动流程优化。
精益思想与VSM相互补充,共同推动组织实现高效、灵活、优质的生产与服务。
VSM(Value Stream Mapping,价值流图)是一种可视化工具,用于描述产品或服务的整个价值流。
VSM通过识别价值流中的浪费,帮助组织优化流程,提高生产效率,降低成本。
VSM的作用包括:识别浪费、优化流程、提高生产效率、降低成本、增强组织竞争力。
VSM定义及作用010204 VSM发展历程VSM起源于丰田生产方式(TPS),是精益生产的重要工具之一。
随着精益生产的普及,VSM逐渐在制造业中得到广泛应用。
近年来,VSM的应用范围不断扩展,已经渗透到服务业、医疗、教育等领域。
未来,随着数字化、智能化技术的发展,VSM的应用将更加便捷、高效。
0302精益价值流程VSM核心原理选择具有代表性的产品族,明确其生产流程,包括从原材料到成品的所有环节。
确定产品族和生产流程收集数据绘制价值流图识别浪费收集各环节的生产数据,如生产周期、在制品数量、设备利用率等。
运用专业的绘图工具,将生产流程以图形化方式展现出来,包括物料流、信息流等。
在价值流图中标注出存在的浪费现象,如等待、运输、不良品等。
价值流图绘制方法识别浪费制定消除策略实施改进措施持续监控与改进浪费识别与消除策略持续改进文化培养树立持续改进观念建立改进机制培养员工能力营造改进氛围03精益价值流程VSM实施步骤现状调研与数据收集01020304明确调研目标收集现场数据了解客户需求分析现状价值流图绘制及分析确定价值流图的范围分析浪费和瓶颈A B C D绘制当前状态的价值流图制定改进目标改进方案制定与实施实施方案制定改进方案调整方案监控实施过程对实施过程进行监控,确保改进方案的顺利执行。
价值流分析培训课程

生产周期=存货数量X生产节拍 存货数量=原材料数量X在制品数量=15+100=115(个) 生产节拍=10(秒/个) 生产周期=115X10=1150(秒)
第38页,共77页。
第二节 现状图绘制的十大步骤
步骤4 完成数据表
1x
Daily
发运:
• 每天1卡车 • 作业周期时间OCT 120 秒 • 5 个作业员工 • 20 电机/箱 • 2 箱/货盘 • 30 “P” 型 货盘/天 • 15 “NP” 型 货盘/天 • 库存:
要求实现
第5页,共77页。
库存增加了产品的价值吗?
早餐只有干粮,没有牛奶的损失是什么?
案例:冰箱的价值是什么?
一次吃不完的食物放坏了的损失是什么?
拓展知识点:
库存的实际价值是在恰当的地点,恰当的时间拥有合适的产品。所以,库存为 公司走向成功提供了必要的地点和时间的效用。
第6页,共77页。
第三节 价值流分析 – 作用
• 而识别价值流的工具,就是价值流图---Value Stream Mapping
第4页,共77页。
第二节 价值流的组成特点
增值
顾客愿意付费的 能改变形状和功能的活动
浪费
任何消耗资源但不增加价值的活动
典型浪费包括“七种浪费”+ 能源、空间、安全和
环境的浪费
浪费 增值
顾客需求
流程 从客户的角度看待工作
3.识别关键指标
4.完成数据筐
5.绘制等待天数
6.填充时间线 7.计算增值比例 8.绘制原材料供应 9.绘制信息流 10.识别改善项目
第24页,共77页。
第二节 现状图绘制的十大步骤
步骤1:选择价值流
《价值流培训》课件

《价值流培训》
17
《价值流培训》
18
《价值流培训》
19
《价值流培训》
20
《价值流培训》
21
《价值流培训》
22
《价值流培训》
23
《价值流培训》
24
《价值流培训》
25
《价值流培训》
26
《价值流培训》
27
《价值流培训》
28
《价值流培训》
29
《价值流培训》
30
《价值流培训》
31
《价值流培训》
47
《价值流培训》
48
《价值流培训》
49
《价值流培训》
50
《价值流培训》
51
《价值流培训》
52
《价值流培训》
53
《价值流培训》
54
《价值流培训》
55
《价值流培训》
56
《价值流培训》
57
《价值流培训》
58
《价值流培训》
59
《价值流培训》
60
《价值流培训》
61
《价值流培训》
62
《价值流培训》
63
《价值流培训》
1
《价值流培训》
2
《价值流培训》
3
《价值流培训》
4
《价值流培训》
5
《价值流培训》
6
《价值流培训》
7
《价值流培训》
8
《价值流培训》
9
《价值流培训》
10
《价值流培训》
11
《价值流培训》
12
《价值流培训》
13
《价值流培训》
14
《价值流培训》
价值流图技术PPT课件

I
I
I
I
3500
1500
1850
2300
I
200t
仓库
3.2.4识别价值流中的增值与非增值时间
增值活动(VA)
无效活动(NVA)
定义:任何符合客户需求的动作、服务、材料变化
定义:任何不符合客户需求的工作、服务、材料变化。所有可以被取消、简化、降低、合并的动作。
先进先出料道
Max 80 pcs.
5.2规划将来状况应考虑的要点
5.2.5 在所有工序中,瓶颈在什么地方?选定何处作为生产控制节拍?
1.2价值流图分析的作用
分析系统整体存在的问题,具有看到宏观生产流程的能力 帮助发现浪费源 展示了信息流与物流之间的联系 广泛沟通的工具 确定优先次序 结合精益的概念与技术…避免“只挑容易的” 来改进难 形成实施计划的基础 建立起确定改善目标的数据基础
组装1
C/T:35S C/O:0min Oper:1 Uptime:100% Shifts:25,600s 2%Scrap
发货
I
I
I
I
3500
1500
1850
2300
I
200t
天
35S
25.8天
天
天
2.0
8.3
148S
48S
60S
天
3.5
5S
天
4.5
7.5
仓库
3.2.7当前状况图示
XX钢铁厂
每种产品都应有价值流图---全面了解浪费情况
小批多品种绘减值流图较难---运用产品分族矩阵分类
3.1.1产品分族矩阵
工艺顺序、关键设备或工序
工序1
价值流分析培训PPT精品文档40页

4
Value Stream Mapping
Value Stream - All steps, value added and non value added, required to bring the product from raw material to customer.
CI-GT-015 REV. 0
use this symbol to represent a "supermarket" (first-in-first-out)
CI-GT-015 REV. 0
15
Typical Process Data
• Cycle time • Changeover time • Production batch sizes • Number of product variations • Number of operators • Pack size • Working time (minus breaks) • Scrap rate • On-demand machine time
• Information flow another flow associated with production that tells each process what to make or do next
CI-GT-015 REV. 0
11
Value Stream Mapping Steps
CI-GT-015 REV. 0
13
Product Family
CI-GT-015 REV. 0
14
Gather Data
Manufacturing
T rig g e r: D one: M a n u a l C y c le T im e : A u to C y c le T im e : T a k t T im e : N u m b e r o f P e o p le : W IP P ie c e s : C /O T im e : D is ta n c e Ite m T ra v e ls : % R ew o rk: T o p 3 D e fe c ts : 1. 2. 3.
- 1、下载文档前请自行甄别文档内容的完整性,平台不提供额外的编辑、内容补充、找答案等附加服务。
- 2、"仅部分预览"的文档,不可在线预览部分如存在完整性等问题,可反馈申请退款(可完整预览的文档不适用该条件!)。
- 3、如文档侵犯您的权益,请联系客服反馈,我们会尽快为您处理(人工客服工作时间:9:00-18:30)。
图析顾客数据
图析顾客数据
计算节拍时间
节拍时间定义
根据销售的速度, 要满足顾客的需求, 应该隔多久生产一个零件
计算
可用工作时间/顾客需求
27000秒/1500件外壳=18秒
MME实例
1班x8小时=28800秒 2段15分钟的休息时间/班=-1800秒
可用的工作时间=27000秒 顾客需求/月=30000件外壳
图析过程
图析过程
图析过程
图析库存水平
案例研究实例: Mike’s Metal Enclosures(MME)
图析供应商数据
案例研究实例: Mike’s Metal Enclosures(MME)
计算每个过程的加工时间
加工时间和OCT相等时: 在没有平行作业(例如多名操作
工),而且在过程中的任何时间 内只有1个“价值对象”时 冲压:15秒 成形:20秒
提供识别改 进机会的基 础和方向
价值流 特征
用常用制图 语言的形象
展示
力量存在于 该计划中
清楚识别关键的端对 端制造和业务过程中
目的
的浪费,
并创建可执行的改造
计划
现状价值流
图
优点
关注有限的资源 确定预期绩效改善的时
间线 避免在浪费的大海中出
现成功的孤岛 使每个人对目前状态和
未来远景有共同的了解
将会对节拍时间产生怎样的影响?你的策略是什么? • 如果你的生产线换型时间是30分钟或更多,将会对
生产线有何影响?对节拍时间产生怎样的影响?
• 准则一:计算节拍时间 • 准则二:连续流
– 在能夠连续流动的地方做连续流 – 沒有连续流动时,工程之间会变成每一個小孤
岛 – 连续流动之后,几个工程会变成大岛 – 不要勉強变成连续流
• 1953年丰田公司在丰田市总厂的机械车间里,第一次設置 了庫存超市。
• 丰田的执行官从美國超市的照片中,看到他們把貨物按照 明确的位置摆放到貨架上,供顧客提取,從中受到启发而 产生了这种观念。
• 准则一:计算节拍时间
• 准则二:连超市来控制生产。
目录
1
价值流理论概述
2
价值流图析
3
理想价值流
4
问询价值流图
5
未来价值流图
Customer
• 客户声音(VOC:Voice of Customer)-客戶對於 你的產品及流程需求和看 法。
• 流程声音(VOB:Voice of Business)-用於描述你的企 業在生產產品或執行流程過程 中的需求。
将每个过程的加工时间和交付时间加在一起,得到价值流的总时间
案例研究实例: Mike’s Metal Enclosures(MME)
图析信息流
案例研究实例: Mike’s Metal Enclosures(MME)
询问目前状态价值流图
• 准则一:计算节拍时间
– 节拍时间是要用什么速度來生产一个零件或在 制品。
• 准则一:计算节拍时间
• 准则二:连续流
• 准则三:在连续流无法向上游扩展时,使用超市 来控制生产。
• 准则四:选择基准节拍工程
• 准则五:在基准节拍工程,要平均分配各品种的 生产时间。即种类平准化生产。在此也必須同時 考虑数量平准化。
• 准则六:对极准节拍工程发出生产指示或 領取一定的产品以产生「启动的拉力」,亦 即运用平均生产量的概念。
Heijunka 平准化
• 在固定的生产周期內,平衡产品的类型与数量。這樣可以在避免大量生产的同 時,有效的滿足顾客的需求,最終帶來整條价值流中的最优化的库存、投資成 本、人力資源以及产品交付期。
• 举例說明“按照客戶需求的产品数量來均衡生产”:假設一個制造商每周都收到 500個产品的訂單,但是每天收到的訂單的产品數量卻有著显著的差別:周一 要运送200個,周二100個,周三50個,周四100個,周五再运送50個。為了平 衡产量,制造商可能會把少量的已經完工的产品储存在装运处,作為一種缓存 來滿足周一的高需求量,並按照每天生產100個产品的產量,來平衡整個一周 的生产。通過在价值流終點庫存少量成品,制造商可以平衡顾客的需求,同時, 更有效地利用整條价值流的資源。
• 连续流动是指每生产一件产品,然後此产 品立即从这一工程传到下一工程,在工程 之間沒有停滯,也沒有任何浪费产生。连 续流是效率最高的生产方式。
• 准则一:计算节拍时间 • 准则二:连续流 • 准则三:在连续流无法向上游扩展时,使用超市来控制生
产。
– 有些工程的 C/T 很长或是很短,而且需要進行换模來切換不同 产品。
– 在节拍时间内对问题做出最快反应 – 消除意外故障因素 – 减少下游工程和装配工程的換模時間
节拍时间计算
节拍 =
可用的工作时间 平均需求
TAKT =
Available Work Time Average Demand
你必須考虑的事情
• 高节拍对你的生产线重要吗?为什么? • 高节拍,低节拍的影响是什么? • 如果你的生产线机器正常工作时间只有70%或更少,
20天/月x1班=20 每天需生产的外壳=1500件外壳
计算节拍时间
制程间隔时间(DOI)(产出率)
DOI观察
DOI定义
单件产品或服务在一个过程 结束时“制成”的频率
Process time=120分钟周期x60秒 批量=60x5=300个
DOI=7200/300=24秒
DOI注释
最理想的情况是观察得到DOI,而 不是计算得到
过程步骤1 现场评估
价值流图析成功路线图
过程步骤2
VSM活动 准备
针对每个已识别的价值流重复一次
过程步骤3
进行 VSM活动
过程步骤4
执行 VSM计划
重复 循环
选择产品 创建目前 询问目前 创建未来 制定价值
或服务族 状态图
状态
状态图
流计划
价值流图析阶段日程
• 把目前状态过程走一遍
选择产品 或服务族
• 标识目前状态图上的过程框
创建目前 • 有完整数据的目前状态图
状态图
• 向管理层提交的目前状态报告
询问目前 状态
• 完成的有标记目前状态图
创建未来 • 完成的未来状态图和价值计划
状态图
制定价值 • 向管理层提交的最终报告
流计划
确定和选择产品族
1、产 品族
2、产 品族矩
阵
3、记 录信息
下游生产过程有相似加工步骤/使用共同设备的一组产品。
• 举例說明“按照产品類型來平衡产量”:請看圖示,假設一家衬衫公司為人們提 供A,B,C,D四種樣式的衬衫,而顾客每周對這些衬衫的需求量為5件A型,3件B 型,以及C型和D型各兩件。對於追求規模经济性,希望尽可能減少換模的大 批量制造商而言,他們很可能會按照AAAAABBBCCDD這樣的生产次序來制造 产品。然而,一個精益制造商,可能會考慮按照AABCDAABCDAB的次序來生 产产品,并通过适当的系統改進,減少換模時間。同時根据顾客订单需求的变 化,对生产次序进行周期性的调整。
价值流 组成
价值流改进 计划
未来价值流 图
价值流(VSM)是什么?
一种用特定符号形式呈现整 个生产制造过程并从宏观角 度引导管理者发现问题的精 益工具
它需要多部门通力合作完成
V
价值流改进计划 非常重要
S M
T 可以帮助管理者 确定改善方向及 问题改进的优先 级
它使每个人对目 前状态和未来远 景有共同的了解
计算价值流的总需求
产品族中所有产品的合计需求将被用来计算价值流的节拍时间
创建目前状态图的方法
小组路线1: 过程识别
小组路线2: 收集数据
图的创建
重要特征
每个人一开始应该创建他们自己的图 首先走过整个流程,记录过程流 在终点开始,逆流而上 用铅笔和纸画出过程图
确定每个过程要收集什么数据 再次逆流而上,收集数据和信息流 只要可能,就使用真实和观察到的数据 尽可能使用最小的时间单位——前后一致
外部客户 VOC
內部客户 VOB
把价值量化
最终客户
(把产品值用掉的人 )
中间客户
(购买产品,增加附加值再卖出去)
Key performance indicator 可量化
上游
(上司、股东)
平行单位
(与你平行的单位如产销单位)
VOC
KPI
轉換
Voice of customer 不可量化
下游
(制作流程在你后面的单位)
计算每个过程的加工时间
加工时间和DOI不同时: 如果多名操作工同时执行相同(或相
似)的职能 多个“价值对象”同时通过价值流 在图中反映的就是单个操作工加工
“价值对象”所需的时间
案例研究实例: Mike’s Metal Enclosures(MME)
计算每个过程的交付时间
计算总时间
有時候1個VOC要多個KPI來衡量。 有時候1個KPI可以衡量多個VOC。
• 大多数流程体系的目标:
– 让流程有效地生产期望的结果,来自客户的观点 – 让流程有效率,使我們尽可能地节约資源
VOC:有效的
准时 高品质 低价格
VOB:有效率的
快速 低成本 最少的資源
VSM是使产品或服务通过主材料和信息流所需的所有创造价值和不创造价值行动的快照。
• 准则四:选择基准节拍工程
– 只将客户订单下发给基准节拍工程点 – 基准节拍点之后必须是连续流动,或是小批量
连续流
• 准则一:计算节拍时间
• 准则二:连续流
• 准则三:在连续流无法向上游扩展时,使 用超市来控制生产。
• 准则四:选择基准节拍工程