b113中温变换催化剂
一氧化碳的变换

一氧化碳变换时半水煤气借助于催化剂的作用,在一定温度下,水蒸气反应,生成二氧化碳和氢的工艺过程。
通过变换即除去了一氧化碳,又得到了合成氨的原料气氢和氨加工的原料气二氧化碳。
近年来,变换工段由于采用了低温高活性的催化剂和高串低,高-低-低(俗称“中串低”、“中-低-低”),全低变等多种新工艺流程,加强了热量回收利用,工段面貌发生了很大变化。
1、一氧化碳变换反应的基本原理时什么?其反应的特点时怎么样的?一氧化碳变换反应是在一定条件下,半水煤气中的一氧化碳和水蒸气反应生成氢气和二氧化塔的工艺过程。
CO + H2O <==> CO2 +H2+41kj/mol这是一个可逆放热反应,从化学平衡来看,降低反应温度,增加水蒸气用量,有利于上述可逆反应向二氧化碳和氢气的方向移动,提高平衡变换率。
但是水蒸气增加到一定值后,变换率增加幅度会变小。
温度对变化反应的速度影响较大,而且对正逆反应速度的影响不一样。
温度升高,放热反应即上述变换反应速度增加的慢,逆反应(吸热反应)速度增加得快。
因此,当变换反应开始时,反应物浓度大,提高温度,可加快变换反应,在反应的后一段,二氧化碳和氢的浓度增加,逆反应速度加快,因此,需降低反应温度,使逆反应速度减慢,这样可得到较高的变换率。
提高变化压力,分子间的有效碰撞次数,可以加快变换反应速度,提高催化剂的生产能力。
2“高串低”工艺与传统的高温变换工艺主要有什么不同?有何优点?传统的高温变换工艺,变换炉入口温度一般控制在320~340℃。
在流程设置上一般是一个变换炉,炉内装填铁-铬系催化剂,分两段或三段,半水煤气从上到下一次通过各段催化此后即完成变换过程。
“高串低”工艺与创痛的高温变换工艺主要不同之处是在原高变炉之后,又串联了一个装有钴-钼系列耐硫宽温催化剂的低变炉,形成高变串低变的工艺流程。
耐硫宽温变换催化剂在“高串低”工艺中被利用做低变催化剂。
低变炉入口气体温度一般可控制在210~230℃。
制氢三剂性能及种类

制氢三剂性能及种类制氢过程使用的催化剂有:钴-钼加氢脱硫催化剂、脱氯催化剂、氧化锌脱硫剂、烃类-水蒸汽转化催化剂、中温变换催化剂、低温变换催化剂。
还有PSA吸附剂及磷酸三钠化学助剂。
1.1 钴-钼加氢转化催化剂1.1.1 作用制氢原料中含有不同数量的有机硫和无机硫,这些硫化物的存在,会增加原料气体对设备的腐蚀,尤其重要的是制氢过程所使用的含镍、含铜的催化剂极容易被硫中毒,失去活性,严重影响生产的顺利进行。
但是,有机硫化物性能稳定,不容易被脱除,只有在钴-钼催化剂的作用下,与氢气快速反应生成硫化氢,才能被脱除。
1.1.2 特点钴-钼加氢转化催化剂必须在有氢气存在的条件下,才能将有机硫转化无机硫,否则,将无法起作用。
1.1.3 物理化学特性(T205)外观:灰蓝色条状物几何尺寸:Φ3~3.5×3~10mm堆密度:0.65~0.8kg/L比表面:180~220m2/g1.1.4 化学组成C O O:2~4%M O O3:10~13%载体:TiO2、AL2O31.2 氧化锌脱硫剂(T306)1.2.1 作用氧化锌与硫化氢作用生成难于解离的硫化锌,以此脱除制氢原料气中的硫化氢,一般用于精脱硫过程。
1.2.2 特点氧化锌脱硫剂能脱除无机硫和一些简单的有机硫,硫容较高,能使原料中的硫含量降至0.2~0.02×10-6。
反应温度范围较宽(180~400℃),是一种比较理想的脱硫剂,在较高温度(350~400℃)条件下使用效果更好。
1.2.3 物理化学特性外观:白色条状几何尺寸:Φ5mm×5~10堆密度: 1.16kg/L比表面:45.88m2/g总孔容积:0.28ml/g穿透硫容:>10%1.2.4 化学组成ZnO:≥ 85%1.3 烃类-水蒸汽转化催化剂(Z402、Z405)1.3.1 作用在高温的条件下,烃类和水蒸汽在转化催化剂的作用下,烃类发生裂解,生成甲烷、氢气、一氧化碳和二氧化碳。
国内外耐硫变换催化剂的研究进展

提高催化剂对水蒸气及硫化氢的吸附性能,加速反 应物及产物在催化剂表面的吸附与解离,提高催化 剂的 ’> 变换活性,特别是中温变换活性,并能有 效 地 阻 止 09C.! >$ 在 特 定 条 件 下 发 生 相 变 的 可 能 性,提高催化剂的强度及强度稳定性。 赫崇衡研究了制备方法对 09C.!>$ 载体水热稳 定性的影响,指出各种制备方法对载体的水热稳定 性的影响 。
(+ ) 还原性能随着 ()*! 含量的增加而增大。 钛对硫 化性能的影响。研究结果表明,()*! 的加入促进了 催化剂低温下物理吸附 ,! - 的能力,并且低温下吸 附的 ,! - 有一部分转化为化学吸附,随着催化剂中 化学吸附量增加。 的 ()*! 含量的增加, !" # 镧对催化剂的影响 谢筱帆对镧的研究指出, 催化剂加入氧化镧后 其活性与含量和处理温度有关, 含有 ./ 01 % #/ .1 氧化镧的催化剂和载体经 "..2 处理活性和耐热性 最高, 活性下降低, 活性恢复快。 34- 测定结果发现 镧助化的催化剂在反应时, 56 可以保持较好的分散 "7 和较少形成无活性的 56 。
・!"・
刘伟华等
国内外耐硫变换催化剂的研究进展
综
述
钛主要用在加氢制备中,近几年来引用到耐硫 (#) 变换催化剂中。张新堂等研究了 钛对耐硫变换 。 ()*! 对催化剂的变换活性 有明显的促进作用, 特别是对低温变换活性; 随 ()*! (! ) 催化剂的 含量的增加, 催化剂的变换活性增加。 催化剂活性的影响
$ #! % #& ’
度升高, 使催化剂烧结。 还会使催化剂的活性组分硫 酸盐化从而失去活性。 当加氢功能不全时, 未被加氢 的氧易与催化剂上的硫发生反应生成 -*! , 使催化 剂的活性降低。 因此新开发耐硫变换催化剂必须具 有较高的抗氧性能。 (9) 增加耐低硫能力。 为防止硫化氢对下游工艺 和设备的影响, 很多化肥厂在变换工段前预脱硫, 进 入变换工段的工艺气中的硫化氢的含量为:. ; #. < ", (催化剂的水解 很多工业耐硫变换催化剂因反硫化 反应) 而失活, 因此新开发的耐硫变换催化剂必须具 有较强的耐低硫能力。
中温变换催化剂总结

中温变换催化剂1、研究进展早期的变换催化剂的研究工作在于提高活性,降低活行温度下限,抑制生成碳黑、甲烷的副反应,也就是提高催化剂的选择性。
后来在以Fe2O为主体的基础上,对添加Cr、Al、Cu、Zn、CO、Ni、Mn和K的氧化物进行了大量研究工作,从而发现它们可以提高催化剂的活性、改善催化剂耐热及抗毒性能。
最后确定了以Fe2O3为主体,Cr2O3为主要添加剂的Fe-Cr系催化剂,一般含Fe2O380~90%,含Cr2O37~14%,并含有K2O、Al2O3等成分。
国内主要的中变催化剂:B107、B109、B112、B113、B114、B115、B116、B117、WB-2、WB-3、DGB、B118、B121等,其特性见下表:铁的氧化物是中变催化剂的活性组分,但纯Fe3O4的活性温度范围很窄,而且在低汽气比条件下有可能发生过度还原而变为FeO,甚至还原到铁,从而引起CO的甲烷化和歧化反应。
工业上用的中变催化剂都是添加Cr2O3的,它起稳定剂的作用,可以防止和延缓催化剂因高温烧结而使晶粒长大和表面积减小,当Fe2O3还原成Fe3O4时,Cr2O3可提高活性相Fe3O4的分散度,增大比表面积。
导致催化剂活性增加。
铬的氧化物还起另外一个作用,在一般条件下,从Cr3+转变为Cr是非常困难的,而Fe3+还原为Fe是比较容易的,因而在反应条件下Cr3+可以防止铁氧化物的过度还原。
2、物理结构与活性和强度的关系中变催化剂中的Fe2O3需经还原成Fe3O4后才具有活性,但在还原过程中铁的氧化物或盐类都会发生变化,并对最终催化剂的活性和强度有很大的影响。
研究表明,催化剂活性随Cr2O3的量增至14%而达到最大值,一般在实际生产中,工业上中变催化剂的Cr2O3含量都小于14%。
另外Cr2O3进入了Fe3O4的晶格以后,形成了固溶体。
这种Fe3O4-Cr2O3与Fe3O4相比,具有较高的分散度和比表面积以防止Fe3O4的再结晶。
一氧化碳变换催化剂的特性与选用(上)

Page 2
LOGO
一氧化碳变换催化剂的性能与特点
工业上使用较为广泛的Fe3o4为主相的铁系催化剂、cu为主相的铜系催化剂和 MoS2为主相的钼系催化剂一氧化碳变换催化剂.通常为了改善催化剂的某些缺 陷或强化某项特点,而引入一些助催化剂使得即使是同一类催化剂亦各具特色。 2.1 铁系催化剂 以Fe 3o 4为主相的铁系催化剂因为单纯的Fe 3o 4在操作温度(温度区间300~470℃, 常称为中温或高温)下, 由于结晶颗粒的长大而很快失活, 因此在催化主相中加 入一定的(结构性)助催化剂。工业上较为成功的助催化剂主要有CrO3 , 因此铁系 催化剂也称为铁铬中(高)变催化剂。
Page 5LOGO Nhomakorabea一氧化碳变换催化剂的性能与特点
2 l 5 低水汽比铁铬中变催化剂 为了改善铁铬中变催化荆对水汽比的适应-肚,特别是节能型烃娄蒸汽转化流程 (水碳比小于2.75) 通过添加锢促进剂.改善了铁铬中变催化剂对低水汽比条件 的适应性, 主要型号有:B113-2等。 2.1.6 本体低硫铁铬中变催化剂 催化剂本体硫含量的高低.直接影响催化剂使用前的放硫时间,本体岔硫量低的 催化剂有利于保护后续的对硫非常敏感的催化剂.如铜锌低变催化剂等 主要型 号有:B110-2、B113等。
Page 3
LOGO
一氧化碳变换催化剂的性能与特点
2.1.1 铁铬中变催化剂 传统的铁铬中变催化剂的结构性助催化剂CrO3 的含量一般为7%~12%,
此外为了改善催化剂的催化活性还添加调变性助催化剂如K+ 等。 2.1.2 低铬型铁铬中变催化剂 由于CrO 3对于人体和环境具有毒害作用. 为了减少CrO 3对于人体和
Page 8
LOGO
一氧化碳变换催化剂的性能与特点
10万吨年合成氨厂两段中间间接换热式变换炉的最佳工艺设计 毕业设计
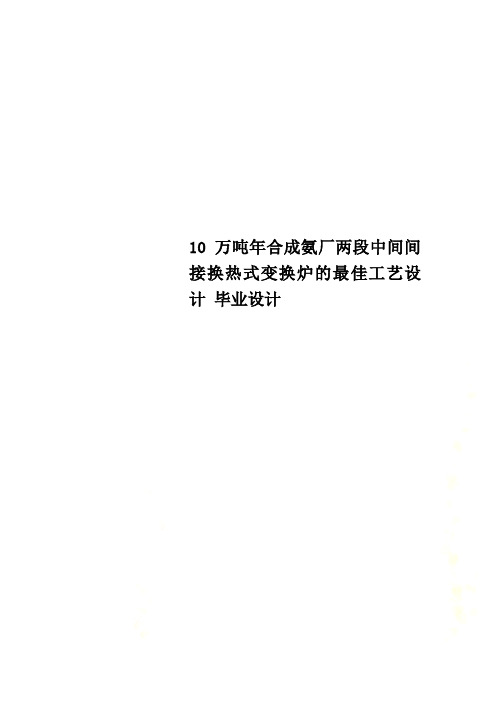
10万吨年合成氨厂两段中间间接换热式变换炉的最佳工艺设计毕业设计10万吨/年合成氨厂两段中间间接换热式变换炉的最佳工艺设计学院:化学化工学院班级:20101331班学号:2010133108姓名:姚正贤指导老师:王智娟完成时间:2013年8月30日目录绪论 (6)一、合成氨原料 (6)1、合成氨生产工艺 (6)2、 氨的用途 (6)二、合成氨的生产现状 (7)1、世界合成氨生产现状 (7)2、我国合成氨生产现状 (7)三、合成氨技术的发展趋势 (8)设计条件 (9)一、最佳设计条件式的建立 (9)二、最佳温度变换率分配方案和接触时间的计算 (10)1、已知条件 (10)2、在T~x 图上标绘出平衡曲线和最佳温度曲线 (12)3、由条件式I 确定第一段出口状态和第二段入口状态。
(13)(1)绝热操作线方程及绝热温升的确定 (13)4.用条件式2T ∏确定二段出口状态 (16)三、催化剂用量的计算 (19)1、第一段11001V C R υτ= .................................................................. 19 2、第二段20022V C V T R ∴= ................................................................... 19 3、总用量3+13.5310.4214.95m 12V V V RT R R ==+= ....................... 19 四、变换炉工艺尺寸的确定 .. (19)五、 附录 (22)1、正负面积求变化率: (22)2、求接触时间 (23)10万吨/年合成氨厂两段中间间接换热式变换炉的最佳工艺设计摘要本设计根据效益最好的原则,以变换炉催化剂体积最小为目标函数,导出了间接换热式变换炉最佳设计的条件式,并通过计算机求解,得出年产十万吨合成氨厂变换炉所需B113型催化剂的理论体积,可供有关设计部门和生产单位参考。
耐硫变换催化剂使用、硫化中出现的问题及建议

耐硫变换催化剂使用、硫化中出现的问题及建议王立群【摘要】介绍4.0 MPa和6.5 MPa气化系统变换工段的情况.结合生产实际,建议中温变换采用耐硫变换催化剂,还推荐了补硫方法.【期刊名称】《化工设计通讯》【年(卷),期】2011(037)005【总页数】4页(P12-15)【关键词】变换催化剂;使用;硫化;问题;补硫【作者】王立群【作者单位】黑龙江龙煤东化有限公司,黑龙江伊春 154111【正文语种】中文【中图分类】TQ113.26+4.2耐硫变换催化剂近几年在化工行业得到广泛应用,无论是合成氨变换还是甲醇变换都逐渐放弃铁系催化剂,尤其是设计压力较高的系统,耐硫变换催化剂更具优势。
因其制作强度高、不易粉碎、变换效率高、使用时间长等特点深受使用者的青睐。
但是耐硫变换催化剂也有不足之处,在原料气硫含量低、水汽比大的情况下,耐硫变换催化剂极易出现反硫化现象,催化剂使用寿命缩短,尤其是硫含量不稳定,使催化剂在硫化与反硫化之间波动时,更易造成催化剂快速失活。
为此,笔者总结多年的生产实践经验,对耐硫变换催化剂的硫化过程及使用情况阐述一下自己的看法。
1 催化剂的选择近几年国内外催化剂生产厂家生产出一系列耐硫变换催化剂,使用业绩较好的有K811、QCS-01、QCS-04、QDB-04几种型号的催化剂。
国内产品尤其以青岛联信和齐鲁科力两家产品使用较多,使用效果也是说法不一,尤其是在原料气低硫环境下使用的情况差别较大。
由于我公司是以煤为原料生产合成氨的厂家,所采用的工艺是水煤浆气化工艺(设计压力有4.0MPa和6.5MPa两个压力等级)。
6.5 MPa等级采用西北化工研究院多元料浆气化技术,气化装置出口原料气水汽比1.45,温度237℃。
变换入口原料气硫含量500×10-6。
变换采用中低温变换,催化剂采用耐硫变换催化剂,入口硫含量低、水汽比大,对耐硫变换催化剂有着极高的要求,否则就要发生反硫化现象。
青岛联信的催化剂,使用时要求硫含量不低于1 200×10-6;齐鲁科力要求硫含量不能低于400×10-6。
一氧化碳变换

一氧化碳变换概述一氧化碳的变换是指煤气借助于催化剂的作用,在一定温度下,与水蒸气反应,一氧化碳生成二氧化碳和氢气的过程。
通过变换反应既除去了煤气中的一氧化碳,又得到了制取甲醇的有效气体氢气。
因此,变化工段既是转化工序,又是净化工序。
前工段来的煤气中,一氧化碳含量高,通过变换反应以后,要求达到工艺气体中的CO/H2约为2.05~2.1的关系,以满足甲醇合成的要求。
一氧化碳变换反应是在催化剂存在的条件下进行的,是一个典型的气固相催化反应。
60年代以前,变换催化剂普遍采用Fe-Gr催化剂,使用温度范围为350~550℃,60年代以后,开发了钴钼加氢转化催化剂和氧化锌脱硫剂,这种催化剂的操作温度为200~280℃,为了区别这两种操作温度不同的变换过程,习惯上将前者称为“中温变换”,后者称为“低温变换”。
按照回收热量的方法不同,变换又可分为激冷流程和废锅流程,冷激流程中,冷激后的粗原料气已被水蒸气饱和,在未经冷却和脱硫情况下直接进行变换,因此,两种流程按照工艺条件的不同选用不同的催化剂,激冷流程采用Co-Mo耐硫变换催化剂,废锅流程采用Fe-Cr 变换催化剂。
第一节变换反应原理变换过程为含有C、H、O三种元素的CO和H2O共存的系统,在CO变换的催化反应过程中,除了主要反应CO+H2O=CO2+H2以外,在某种条件下会发生CO分解等其他副反应,分别如下:2CO=C+CO22CO+2H2=CH4+CO2CO+3H2=CH4+H2OCO2+4H2=CH4+2H2O这些副反应都消耗了原料气中的有效气体,生成有害的游离碳及无用的甲烷,避免副反应的最好方法就是使用选择性好的变换催化剂。
一、变换反应的热效应一氧化碳变换反应是一个放热反应,CO+H2O=CO2+H2+41kJ/gmol反应的热效应视H2O的状态而定,若为液态水,则是微吸热反应,若是水蒸气,则为放热反应。
变换反应的反应热随温度的升高而降低,具体反应热列表如下:表1 CO+H2O=CO2+H2的反应热压力对变换反应的反应热影响较小,一般不做考虑。
NB113中变催化剂的还原与使用
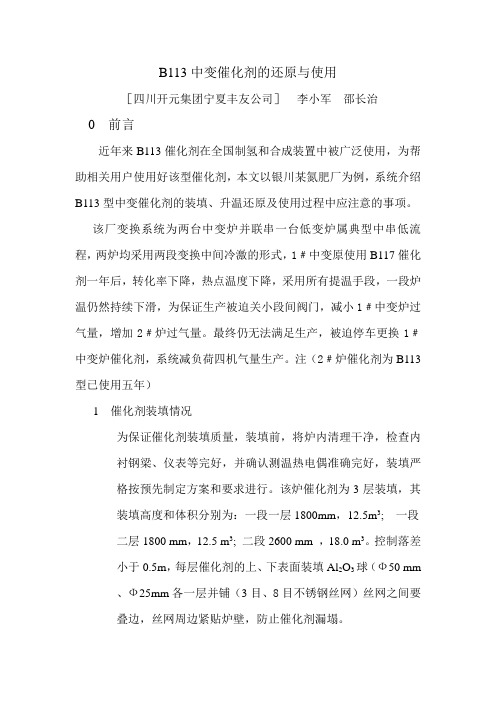
B113中变催化剂的还原与使用[四川开元集团宁夏丰友公司]李小军邵长治0 前言近年来B113催化剂在全国制氢和合成装置中被广泛使用,为帮助相关用户使用好该型催化剂,本文以银川某氮肥厂为例,系统介绍B113型中变催化剂的装填、升温还原及使用过程中应注意的事项。
该厂变换系统为两台中变炉并联串一台低变炉属典型中串低流程,两炉均采用两段变换中间冷激的形式,1﹟中变原使用B117催化剂一年后,转化率下降,热点温度下降,采用所有提温手段,一段炉温仍然持续下滑,为保证生产被迫关小段间阀门,减小1﹟中变炉过气量,增加2﹟炉过气量。
最终仍无法满足生产,被迫停车更换1﹟中变炉催化剂,系统减负荷四机气量生产。
注(2﹟炉催化剂为B113型已使用五年)1催化剂装填情况为保证催化剂装填质量,装填前,将炉内清理干净,检查内衬钢梁、仪表等完好,并确认测温热电偶准确完好,装填严格按预先制定方案和要求进行。
该炉催化剂为3层装填,其装填高度和体积分别为:一段一层1800mm,12.5m3; 一段二层1800 mm,12.5 m3; 二段2600 mm ,18.0 m3。
控制落差小于0.5m,每层催化剂的上、下表面装填Al2O3球(Ф50 mm、Ф25mm各一层并铺(3目、8目不锈钢丝网)丝网之间要叠边,丝网周边紧贴炉壁,防止催化剂漏塌。
2 催化剂的升温还原中变催化剂的主要活性组份为Fe2O3 ,它本身没有催化活性,只有在一定条件下被还原成Fe3O4才具有活性。
催化剂升温还原质量好坏,直接影响到今后催化剂的使用效果。
2.1升温B113中变催化剂升温流程如图1,具体升温过程如下。
1 升温阶段:基点--120℃:以空气做为载热体进行升温,操作时注意以下几点:⑴空气入炉前仔细检查煤气风机管线阀门,升温管线与煤气总管盲板是否加好,防止升温期间煤气漏入。
⑵空气升温期间尽可能加大空气量,入炉空气温度用电炉调节。
⑶升温前期120℃催化剂有脱水过程,此阶段升温速度缓慢进行。
B113中变催化剂使用说明

B113中变催化剂使用说明产品简介B113型CO高温变换催化剂系采用先进工艺生产的无硫型高温变换催化剂。
该催化剂以-Fe2O3为活性组成分,Cr2O3为助剂,并含有有少量活性添加剂的高活性宽温变换催化剂,适用于合成氨装置制氢装城市煤气甲烷等CO变换工艺。
变换反应如下:CO+H2O=CO2+H2+41.19KJ/molB113型催化剂的活性组成是γ-Fe2O3,其晶相结构及活化能都优于a-Fe2O3,因此,该催化剂的低温活性及使用强度均高于其它同类产品。
本企业采用特殊工艺制作的B113型催化剂还具有抗蒸汽冷凝(即抗水煮)的特点,因而提高了使用的抗风险能力。
该催化剂的本体含硫一般都低于250ppmm,开车时不需安排专门的放硫时间。
在当今国内外合成氨装置向低温节能型发展的同时,辽河牌B113型催化剂是一种非常理想的低温高性耐毒耐热长寿命节能型催化剂。
产品的物化性质物理性质化学组成适用条件B113型催化剂使用压力0.1-5.0Mpa,使用温度300-500℃,运行空速500-5000h,使用寿命预计三年以上。
B113型催化剂的突出特点是具有良好的抗蒸汽冷性能,在事故状态下,用工艺气干燥处理后,催化剂强度不减,床层阻力不增加,催化剂仍能保证事故状态前的活性。
装填催化剂的装填质量直接关系到反应器床层的气流分布阻力降及催化剂性能的发挥,因而要十分重视装填工作。
(1)为了保证装填质量,要选择晴朗的天气,并避开油污灰尘及化学毒物的污染。
(2)装填前,首先确认中变反应器质量合格,器内干燥,无其它杂物,并在内壁标出耐火球铁丝网篦子板和催化剂的装填线。
(3)催化剂装填前,要用4×4mm的筛网仔细过筛,除去运输过程中产生的粉尘。
(4)首先向中变反应器装25的瓷球12mm瓷球100-200mm,铺一层不锈钢丝网,然后再装催化剂。
(5)将催化剂慢慢吊至于器顶,缓慢的倒入接有帆布口袋的漏斗或溜槽中,催化剂从帆布袋口流入器内,器内需有人手握帆布袋口不断移动下料口位置,使催化剂按水平面上升,不得采用集堆后耙平的做法。
制氢装置工艺原理催化剂及助剂

制氢装置工艺原理催化剂及助剂制氢过程可分为几个反应步骤:钴-钼加氢脱硫反应、脱氯反应、氧化锌脱硫反应、烃类-水蒸汽转化反应、一氧化碳变换反应及氢气提纯部分(本装置用PSA)。
为了分离出部分加氢干气中的氢气,在干气压缩机与加氢加热炉之间增加膜分离单元。
1 钴─钼加氢脱硫反应1.1 反应原理制氢原料油、气中含有各种有机硫,在一定的温度(一般为260~400℃)及有H2存在的条件下,钴─钼加氢脱硫催化剂能使有机硫转化成无机硫,无机硫再由其它脱硫剂(如ZnO)吸收,原料中含有的烯烃也能被加氢饱和,有机氯化物被加氢生成HCL。
反应式如下:(1)硫醇加氢反应式:R-SH +H2→ RH +H2S(2)二硫醚加氢反应式:R-S-S-R'+3H2→ RH +2H2S +R'H(3)硫醚加氢反应式:2R-S-R'H +5H2→ 2RH +2R'H2+2H2S(4) 二硫化碳加氢反应式:CS2+4H2→ CH4+2H2S(5) 硫氧化碳加氢反应式:COS +H2→ H2S +CO(6) 烯烃加氢反应式:RCH=CHR' +H2→ RCH2-CH2R'(7) 有机氯化物加氢反应式:R-CL +H2→ R-H +HCL(反应式中:R、R’代表烷基)1.2 影响因素(1)温度钴-钼催化剂进行加氢脱硫时,操作温度通常控制在260~400℃范围内,当温度低于220℃,加氢效果明显下降,温度高于420℃以上催化剂表面聚合和结碳现象增加。
(2)压力由于有机硫化物在轻油中的含量不高,故压力对氢解反应影响不大,压力由整个工艺流程的要求决定,通常控制在3.0~4.0MPa。
(3)空速单位时间(h),通过单位催化剂体积(m3)的气体(折合为标准状态下)体积数量,称为空速,单位为m3/h.m3,可简写为h-1。
有些反应,水蒸汽参与反应过程,但计算空速时不计算水蒸汽的体积,这时的空速称为干气空速。
催化剂基础标准与通用方法
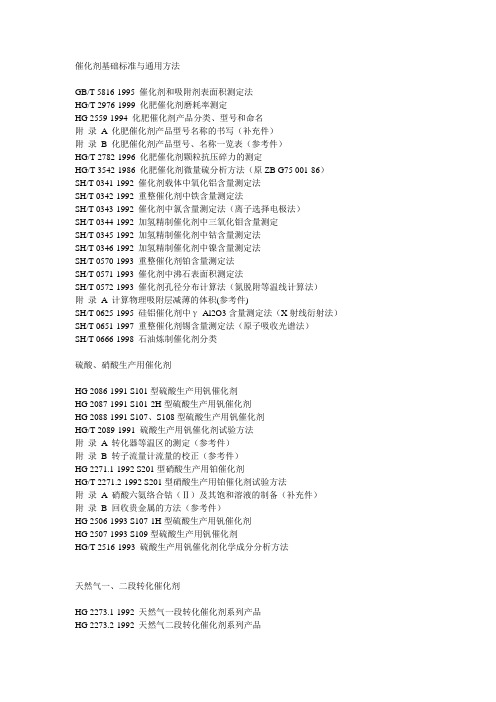
催化剂基础标准与通用方法GB/T 5816-1995 催化剂和吸附剂表面积测定法HG/T 2976-1999 化肥催化剂磨耗率测定HG 2559-1994 化肥催化剂产品分类、型号和命名附录A 化肥催化剂产品型号名称的书写(补充件)附录B 化肥催化剂产品型号、名称一览表(参考件)HG/T 2782-1996 化肥催化剂颗粒抗压碎力的测定HG/T 3542-1986 化肥催化剂微量硫分析方法(原ZB G75 001-86)SH/T 0341-1992 催化剂载体中氧化铝含量测定法SH/T 0342-1992 重整催化剂中铁含量测定法SH/T 0343-1992 催化剂中氯含量测定法(离子选择电极法)SH/T 0344-1992 加氢精制催化剂中三氧化钼含量测定SH/T 0345-1992 加氢精制催化剂中钴含量测定法SH/T 0346-1992 加氢精制催化剂中镍含量测定法SH/T 0570-1993 重整催化剂铂含量测定法SH/T 0571-1993 催化剂中沸石表面积测定法SH/T 0572-1993 催化剂孔径分布计算法(氮脱附等温线计算法)附录A 计算物理吸附层减薄的体积(参考件)SH/T 0625-1995 硅铝催化剂中γ-Al2O3含量测定法(X射线衍射法)SH/T 0651-1997 重整催化剂锡含量测定法(原子吸收光谱法)SH/T 0666-1998 石油炼制催化剂分类硫酸、硝酸生产用催化剂HG 2086-1991 S101型硫酸生产用钒催化剂HG 2087-1991 S101-2H型硫酸生产用钒催化剂HG 2088-1991 S107、S108型硫酸生产用钒催化剂HG/T 2089-1991 硫酸生产用钒催化剂试验方法附录A 转化器等温区的测定(参考件)附录B 转子流量计流量的校正(参考件)HG 2271.1-1992 S201型硝酸生产用铂催化剂HG/T 2271.2-1992 S201型硝酸生产用铂催化剂试验方法附录A 硝酸六氨络合钴(Ⅱ)及其饱和溶液的制备(补充件)附录B 回收贵金属的方法(参考件)HG 2506-1993 S107-1H型硫酸生产用钒催化剂HG 2507-1993 S109型硫酸生产用钒催化剂HG/T 2516-1993 硫酸生产用钒催化剂化学成分分析方法天然气一、二段转化催化剂HG 2273.1-1992 天然气一段转化催化剂系列产品HG 2273.2-1992 天然气二段转化催化剂系列产品HG 2273.3-1992 天然气二段转化热保护剂HG/T 2273.4-1992 天然气一、二段转化催化剂试验方法附录A 反应器等温区的测定(参考件)附录B 水碳比的测定(参考件)附录C 转子流量计流量校正(参考件)附录D EDTA标准滴定溶液对稀土氧化物的滴定度的测定(补充件)HG/T 3543-1988 天然气转化催化剂化学成分分析方法(原ZB G75 005-88)一氧化碳变换催化剂HG 2090-1991 B113型一氧化碳中温变换催化剂HG/T 2693-1995 一氧化碳高温变换催化剂化学成分的测定HG 2779-1996 一氧化碳耐硫变换催化剂HG/T 2780-1996 一氧化碳耐硫变换催化剂试验方法附录A(提示的附录)转化器等温区的测定附录B(提示的附录)气体流量的校正HG/T 2781-1996 一氧化碳耐硫变换催化剂中钴钼含量的测定HG/T 3544-1989 一氧化碳中温变换催化剂试验方法(原ZB G74 001-89)附录A 反应器等温区的测定(参考件)附录B 水蒸气与原料气之比测定(参考件)附录C 转子流量计流量校正(参考件)附录D 催化剂堆积密度的测定(参考件)附录E 气体分析和温度控制(参考件)HG 3546-1989 B110-2型一氧化碳中温变换催化剂(原ZB G75 006-89)HG 3547-1989 B111型一氧化碳中温变换催化剂(原ZB G75 007-89)HG 3548-1989 B112型一氧化碳中温变换催化剂(原ZB G75 008-89)HG 3549-1989 B107,B107-1,B108,B109型一氧化碳中温变换催化剂(原ZB G 75 009-89)甲烷化催化剂HG 2509-1993 甲烷化催化剂HG/T 2510-1993 甲烷化催化剂试验方法附录A 反应器等温区测定(参考件)附录B 催化剂堆密度的测定(参考件)附录C 流量校正(参考件)HG/T 2511-1993 甲烷化催化剂化学成分分析方法附录A EDTA标准滴定溶液对稀土氧化物滴定度的测定(补充件)氨合成催化剂HG 2772-1992 A201型氨合成催化剂附录A 氧化钴含量的测定亚硝基红盐比色法(补充件)HG/T 3545-1990 氨合成催化剂试验方法(原ZB G74 002-90)附录A 五槽反应器等温区的测定(补充件)附录B 催化剂堆密度的测定(补充件))附录C 附录C (参考件)HG 3550-1990 A110型系列氨合成催化剂(原ZB G75 010-90)HG 3551-1990 A109型氨合成催化剂(原ZB G75-011-90)HG 3552-1990 A106型氨合成催化剂(原ZB G75-012-90)HG/T 3554-1981 氨合成催化剂化学成分分析方法(原HG 1-1430-81)附录A 标准溶液的制备(补充件)氧化锌脱硫剂HG 2508-1993 氧化锌脱硫剂HG/T 2512-1993 氧化锌脱硫剂化学成分分析方法附录A 溶液的配制(补充件)HG/T 2513-1993 氧化锌脱硫剂试验方法附录A 硫容分析--燃烧中和法(补充件)附录B 气体中硫离子的分析--汞量法(补充件)附录C 硫化氢的发生及原料气的配制(参考件)附录D 附录D 反应炉等温区的测定(参考件)附录E 水蒸气与原料气比例的测定(参考件)附录F 转子流量计流量校正(参考件)有机硫加氢催化剂HG 2505-1993 有机硫加氢催化剂HG/T 2514-1993 有机硫加氢催化剂试验方法附录A 色谱柱的制备(补充件)附录B 盐浴的制备(参考件)附录C 反应炉温度控制及盐浴等温区的测定(参考件)附录D 转子流量计流量的校正(参考件)HG/T 2515-1993 有机硫加氢催化剂活性组分分析方法其他催化剂HG/T 3553-1981 联醇及低温变换催化剂化学成分分析方法(原HG 1-1428-81)附录A 标准溶液的制备(补充件)HG/T 3555-1984 轻油蒸气转化催化剂化学成分分析方法(原HG/T 1-1546-84)附录A 标准溶液的配制(补充件)HG 3556-1980 B202型低温变换催化剂(原HG 1-1315-80)附录A 反应器温度控制及等温层的测定(参考件)附录B 水蒸气与原料气之比测定及饱和水气温度的计算(参考件)附录C 锐孔流量计的校正(参考件)附录D 气体分析方法(参考件)分子筛GB/T 6286-1986 分子筛堆积密度测定方法附录A 堆积密度测定仪的说明(参考件)GB/T 6287-1986 分子筛静态水吸附测定方法GB/T 6288-1986 粒状分子筛粒度测定方法附录A 样品板的选用(补充件)附录B 标准筛的说明(参考件)GB/T 8770-1988 分子筛动态水吸附测定方法GB/T 10504-1989 3A分子筛GB/T 10505.1-1989 3A分子筛抗压碎强度测定方法GB/T 10505.2-1989 3A分子筛磨耗率测定方法GB/T 10505.3-1989 3A分子筛静态乙烯和氮气吸附测定方法GB/T 10505.4-1989 3A分子筛包装品含水量测定方法GB/T 13550-1992 5A分子筛及其试验方法HG/T 2524-1993 4A分子筛HG/T 2690-1995 13X分子筛HG/T 2691-1995 沸石分子筛动态二氧化碳吸附的测定HG/T 2783-1996 分子筛抗压碎力试验方法SH/T0339-1992 NaY分子筛晶胞参数测定法SH/T 0340-1992 NaY分子筛结晶度测定法。
CO变换在合成氨系统中的应用与注意事项

图1-1无饱和热水塔的简单工艺流程
:
压缩低压机四出半水煤气→丝网过滤器(下进上出)→除油剂炉(下进上出) →前热交壳程(下进上出)→后热交管程(上进下出)→变换炉一段(上进下出)→二段增湿器(上进下出)→变换炉二段(上进下出)→三段增湿器(上进下出)→变换炉三段(上进下出)→后热交壳程(下进上出)→前热交管程(上进下出)→水加热器管程(上进下出)→冷却器管程(上进下出)→气液分离器(上进侧出)→二脱
c进行变换炉的物料衡算和能量衡算;
d根据所用催化剂的宏观动力学方程及变换炉x-t图,计算每一段催化剂用量;
e绘制所用系统工艺流程简图、变换炉计算物料表。
2.21.2.2变换炉段间的降温方法
变换反应是剧烈的放热反应,随着反应的进行气体温度不断升高,但最适宜反应温度则是随着变换率的增高而逐步降低的。因此,为了提高变换率,使反应能在最适宜温度下进行,必须不断移走反应热,使温度随反应进行不断降低。其次,催化剂本身耐热性有一定限度,为防止催化剂层超温也必须及时移走反应热。
变换系统变换炉工艺设计主要内容
a根据合成氨生产原料确定初始气体成分、根据所采用的流程确定汽气比等,选定变换炉段数以及段间降温方法。根据所用催化剂确定变换炉进口温度;
b根据选定的初始气体成分、汽气比、所用催化剂参数等,计算变换炉每一段的平衡曲线、最适宜温度曲线。计算变换炉每一段的操作线,根据每段最适宜温度曲线调整该段的进出口温度以及各段变换率,直至合理为止。据此绘制变换炉x-t图;
一氧化碳变换的发展一般分为几个阶段:90年代以前一般为中温变换,目前常见的为全低变。中温变换即变换温度在400℃左右的变换,全低变为变换温度在200℃-340℃之间的变换。
变换反应为:
微型反应器中温变换催化剂性能测试

实验三 微型反应器中温变换催化剂性能测试一.实验目的:1.了解微分反应器的性质特点,微分与积分反应器的区别与联系,各自的优缺点;2.深刻认识催化剂活性,中毒,热稳定性,机械强度等有关固体催化剂的评价性能指标、物理意义,活性与反应动力学的关系,反应动力学参数的关系;3.掌握实验中测取催化剂反应的本征反应区与宏观反应区范围,掌握测取本征与宏观动力学的实验方法及计算反应速率的方法,学会计算反应动力学参数的数学方法; 4.学会设计评定催化剂性能、测取催化剂动力学参数的实验方案。
二.实验原理在合成氨生产中,无论采用哪一种原料和何种造气方法所制得的原料气,除有用成分氮和氢外,尚含有不同数量的硫化氢、有机硫化合物、二氧化碳、一氧化碳以及其它气体,这些气体如不预先加以清除,不仅增加压缩这些气体的动力消耗,而且对氨的生产有着极大的危害性,例如,原料气中的一氧化碳,对于合成氨催化剂有严重的毒害。
因此,为使生产得以正常进行,确保各种催化剂的安全使用,同时避免不必要的动力消耗,就必须按照合成氨生产过程的工艺条件要求,在原料气进入合成氨系统以前,应将原料气中的一氧化碳杂质除去。
除去的方法是将一氧化碳与水蒸气在适当的温度与催化剂的存在下进行反应,生成氢气和二氧化碳。
该反应称作一氧化碳的变换反应。
变换后的气体称变换气,CO 变换反应化学方程式为:CO(g)+H 2O(g)═CO 2(g)+H 2(g)+Q变换反应具有可逆、放热、体积不变的特点。
根据这些特点,可选择适当的操作条件,促使平衡向右移动。
经过变换反应,增加了合成氨原料气中氢的含量,由于二氧化碳的除去比一氧化碳要容易得多,这样简化了原料气的精制过程。
同时,二氧化碳经过回收以后,可以作为生产尿素、纯碱或碳酸氢钠的原料。
因此,一氧化碳变换反应在合成氨工业中具有重要的意义。
变换反应必须在催化剂存在的条件下进行。
本实验采用铁基催化剂,反应温度为350~500℃。
设反应前气体混合物中各组分干基摩尔分率为oco y 、o co y 2、o H y 2、oN y 2;初始汽-气比为R o ;反应后气体混合物中各组分干基摩尔分率为co y 、2co y 、2H y 、O H y 2;一氧化碳的变换程度通常用变换率α来表示。
B113中变催化剂使用说明
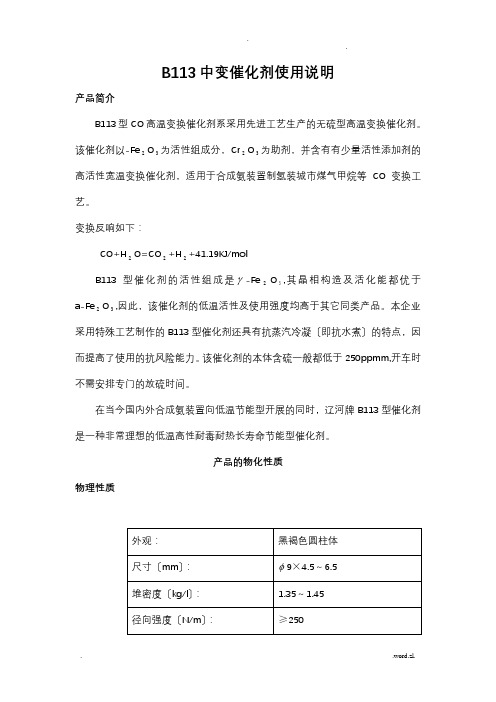
B113中变催化剂使用说明产品简介B113型CO高温变换催化剂系采用先进工艺生产的无硫型高温变换催化剂。
该催化剂以-Fe2O3为活性组成分,Cr2O3为助剂,并含有有少量活性添加剂的高活性宽温变换催化剂,适用于合成氨装置制氢装城市煤气甲烷等CO变换工艺。
变换反响如下:CO+H2O=CO2+H2+41.19KJ/molB113型催化剂的活性组成是γ-Fe2O3,其晶相构造及活化能都优于a-Fe2O3,因此,该催化剂的低温活性及使用强度均高于其它同类产品。
本企业采用特殊工艺制作的B113型催化剂还具有抗蒸汽冷凝〔即抗水煮〕的特点,因而提高了使用的抗风险能力。
该催化剂的本体含硫一般都低于250ppmm,开车时不需安排专门的放硫时间。
在当今国内外合成氨装置向低温节能型开展的同时,辽河牌B113型催化剂是一种非常理想的低温高性耐毒耐热长寿命节能型催化剂。
产品的物化性质物理性质化学组成产品质量指标产品的使用适用条件B113型催化剂使用压力0.1-5.0Mpa,使用温度300-500℃,运行空速500-5000h,使用寿命预计三年以上。
B113型催化剂的突出特点是具有良好的抗蒸汽冷性能,在事故状态下,用工艺气枯燥处理后,催化剂强度不减,床层阻力不增加,催化剂仍能保证事故状态前的活性。
装填催化剂的装填质量直接关系到反响器床层的气流分布阻力降及催化剂性能的发挥,因而要十分重视装填工作。
(1)为了保证装填质量,要选择晴朗的天气,并避开油污灰尘及化学毒物的污染。
(2)装填前,首先确认中变反响器质量合格,器内枯燥,无其它杂物,并在内壁标出耐火球铁丝网篦子板和催化剂的装填线。
(3)催化剂装填前,要用4×4mm的筛网仔细过筛,除去运输过程中产生的粉尘。
(4)首先向中变反响器装25的瓷球12mm瓷球100-200mm,铺一层不锈钢丝网,然后再装催化剂。
(5)将催化剂慢慢吊至于器顶,缓慢的倒入接有帆布口袋的漏斗或溜槽中,催化剂从帆布袋口流入器内,器内需有人手握帆布袋口不断移动下料口位置,使催化剂按水平面上升,不得采用集堆后耙平的做法。