中温变换催化剂的升温还原原操作说明
甲烷转化催化剂升温还原技术要求

转化催化剂升温还原技术要求(换热转化)四川天一科技股份有限公司2012年2月转化催化剂升温还原技术要求“技术要求”是根据转化催化剂的实际要求编写的,不涉及工厂具体的操作步骤及操作细节如阀门的动作等。
操作应以工程设计文本为准。
“技术要求”所叙述的是工厂在转化工段进行催化剂装填、烘炉、用惰性气体置换系统后所进行的转化催化剂的升温、还原、放硫等化工单元操作要点。
“技术要求”中所列的升温速度是根据装置在原始开车时耐火材料及设备的要求而制定的。
转化催化剂对升温速度无特殊要求。
重复开车时,可采用快速升温还原方案。
一、一、转化催化剂的升温1.1. 空气升温一、二段转化催化剂升温可采用氮气和空气作为介质。
当采用空气作为加热介质时,应注意控制升温速度及终点温度。
在转化系统通入空气后、缓慢地将催化剂床层由常温提高到200℃。
不得超过200℃。
转化催化剂是以金属镍为活性组分的。
因为镍再氧化时放出的热量会使催化剂的温度升高到足以使催化剂熔融或使容器损坏的程度。
因为镍催化剂不得在200℃以上温度与空气接触。
原始开车时已处于氧化状态的转化催化剂采用空气升温,终点可为200℃。
2. 蒸汽升温(1)(1)目的以蒸汽为介质,将一、二段转化催化剂床层温度升高到650℃~700℃左右,同时将一、二段炉顶部和上部温度升高,为二段炉导入空气创造条件。
(2)(2)升温速度催化剂床层从200℃—500℃ 30℃/小时500℃—700℃ 50℃/小时(3)(3)蒸汽升温注意事项①需待转化炉出口温度高于当时压力下蒸汽露点30℃,才能将空气升温切换为蒸汽升温,防止因蒸汽冷凝而损坏催化剂。
②蒸汽已作为加热介质后,需注意系统低点导淋及时排除冷凝水。
③在切换过程中,要减少温度和压力波动,以保持蒸汽不冷凝。
④在蒸汽升温过程中,如原料气供应不具备或因任何原因引起的工程不能进入转化催化剂还原阶段,则升温速度要减慢、控制转化出口温度不超过500℃。
避免因在高温、水蒸汽条件下停留时间过长引起催化剂床层局部超温而使催化剂部分失活。
中温变换催化剂的升温还原及生产维

中温变换催化剂的升温还原及生产维中温变换催化剂的升温还原,听起来复杂,但其实就像一个精妙的舞蹈。
在这场舞蹈中,催化剂就是主角,温度则是舞台。
我们一起来探讨这个过程,看看它如何影响生产维,如何在工业中发挥重要作用。
催化剂的升温还原,首先得明白它的作用。
催化剂就像那位高明的教练,能加速反应但自身不被消耗。
在中温变换反应中,催化剂的选择直接关系到反应的效率和产物的质量。
想象一下,如果没有催化剂,反应就像在泥潭里挣扎,进展缓慢,效率低下。
而有了它,反应迅速推进,犹如风驰电掣。
升温还原,顾名思义,就是在一定温度下,通过还原剂将催化剂表面的一些物质还原成其活性状态。
这个过程其实相当关键。
温度升高,反应活性增强,催化剂表面的化学状态改变,使得反应更易进行。
常见的还原剂如氢气、一氧化碳等,都是重要的角色。
它们不仅帮助催化剂恢复活性,还能提高反应的选择性。
在这个过程中,温度控制至关重要。
太高,催化剂可能失去活性,太低又无法达到预期效果。
这里的“温度”不只是一个数字,它背后关乎的是整个反应的动态平衡。
合理的温度调控,犹如为舞者找到最佳节奏,让每一步都稳健而有力。
中温变换反应一般在200到400摄氏度之间进行。
此时,催化剂的活性发挥到极致。
比如,常见的铂、钯等贵金属催化剂,它们在这个温度范围内表现出色。
想象一下,铂如同一位优雅的舞者,在这个温度的舞台上翩翩起舞,能够高效地完成反应,生成理想的产品。
生产维的提高,也离不开催化剂的出色表现。
在工业生产中,催化剂的使用效率直接影响着生产成本和资源利用率。
提升催化剂的性能,意味着在同样的时间内可以产出更多的产品,降低能耗和废物排放。
这就好比在同样的时间里,做更多的事情,效率倍增。
在许多化工企业,催化剂的选择和使用已经成为一门艺术。
企业如同一个个小国家,催化剂就是他们的“国宝”。
每个国家都有自己的特殊需求和技术背景,因此在催化剂的选择上,不同的企业各显神通。
有的企业偏爱传统的催化剂,有的则勇于尝试新材料,如金属有机框架(MOFs)和纳米催化剂。
变换催化剂硫化升温步骤及注意事项

变换催化剂硫化升温步骤及注意事项升温步骤及注意事项用氮气(也可用半水煤气,但控制速率,注意安全)对整个CO变换系统进行置换,置换至O2含量≤0.5%(体积分数)。
然后按制定的升温流程对催化剂进行升温,升温速率控制在15-25℃/h,当催化济床层温度升至80℃时,向升温载气中配入H2;在催化剂床层温度达120℃时,恒温约4h,以利催化剂吸附水的排放及吸附氧的释放、燃烧。
升温过程注意以下几点:一、根据实际情况制定升温流程,管线盲板倒换正确;二、用载气的温度将升温速率控制在安全范围内;三、配氢时,注意分析升温载气中的O2含量,严格控制载气中的O2含量≤0.5%(体积分数),超标时用放空进行调整;四、保持升温系统压力≤0.2Mpa。
变换催化剂硫化注意事项一、在升温、降温期间,采用大空速,要求电炉功率要大(用CS2硫化时,1m3催化剂的电炉功率为30kW,用固体硫化剂时,1m3催化剂的电炉功率要≥50kW,宜分为多组控制),以满足大负荷需要。
二、硫化期间,保持硫化载气中的H2含量≥25%,可采用部分放空和添加新鲜煤气的措施保证循环气中的H2浓度达标。
三、用CS2的加入量及硫化载气温度和流量控制催化剂床层的升温速率及热点温度,必要时可切气通蒸汽降温后再导气硫化,严禁床层温度暴涨、急降,进行强制硫化时,床层温度应控制在450-480℃,最高不得超过500℃。
四、在H2S穿透前,CS2量不可加入过多,否则会把催化剂中COO 直接还原为金属CO,CO有甲烷催化作用,不仅加剧超温,而且使硫化无法继续进行,同时损害催化剂的活性。
五、硫化系统压力应保持在0.2-0.3 Mpa。
六、因湿气硫化会使CO-MO系催化剂丧失部分活性,尤其是丧失低温活性,因此,系统保压、补氢时须用干气,并及时排放冷凝水,严禁冷凝水进入催化剂床层。
七、煤气中O2含量每升高0.1%,系统绝热温升约15℃。
O2会将催化剂中的活性组分氧化成硫酸盐,降低催化剂的活性,因此,在硫化全过程中,须严格控制煤气中O2含量<0.5%,当煤气中O2含量高时,必须迅速切气源,待O2浓度降至合格后再通气硫化。
转化催化剂升温还原技术要求

转化催化剂升温复原技术要求西南化工研究设计院四川天一科技股份2007.10转化催化剂升温复原技术要求“技术要求”是转化催化剂在投入工业运转过程中的技术要点,用以协助操作人员使催化剂到达理想的效果,不涉及工厂具体的操作步骤及操作细节如阀门等。
操作应以工程设计文件标准为准。
“技术要求”所表达的是工厂在一、二段转化设备进行催化剂装填、烘炉,用惰性气体置换系统后所进行的转化催化剂的升温、复原、放硫、投运等化工单元操作。
“技术要求”中所列的升温速度是根据装置在进行原始开车时耐火材料及设备的要求而制定的。
转化催化剂本身的升温速度无特殊要求。
重复开车时,可以采用快速升温复原方案。
一、转化催化剂的氮气升温1.氮气升温的目的以氮气为介质将催化剂床层温度加热到当时压力下水蒸汽露点以上。
2.氮气升温的条件与控制(1)升温条件氮气循环量:工厂初始给定的氮气量比较小,在循环阶段应逐渐加大氮气流量;MPa;终点温度:~300℃〔或高于露点温度50℃上〕;(2)氮气升温控制要点①在建立氮气循环前系统需充压。
当系统与原料气压缩机出口均压后,再打开系统出口阀,启动原料气压缩机,进行氮气循环。
②当热氮气升温速度减慢时,根据升温情况均匀增点转化炉顶部烧咀〔或侧壁烧咀〕。
③氮气升温阶段催化剂床层压差不允许超过设计值。
④氮气循环运行时,除保证本系统用氮外,应保证其余的氮气支路不要受到损害。
⑤氮气升温曲线二、催化剂蒸汽升温MPa的蒸汽为介质,在外加热条件下,将转化炉催化剂床层温度提高到650~760℃。
(1)升温条件蒸汽流量:设计蒸汽流量的30%~50%;MPa;终点温度:650℃〔~760℃〕;(2)蒸汽升温速度控制以30~50℃/时速度将转化炉催化剂床层由300℃升到650℃〔~760℃〕,为便于废热锅炉建立循环,当废锅入口升到约500℃时,升温速度应适当减慢。
初始引入的工艺蒸汽量约为设计蒸汽量的10%,然后逐渐加大流量。
〔1〕需待转化炉出口温度高于当时压力下蒸汽露点温度50℃以上,才能将氮气升温切换为蒸汽升温。
高温变换催化剂使用操作手册

高温变换催化剂使用操作说明书For personal use only in study and research; not forcommercial useFor personal use only in study and research; not forcommercial useFor personal use only in study and research; not forcommercial useFor personal use only in study and research; not forcommercial useFor personal use only in study and research; not forcommercial use中国石化集团南京化学工业有限公司催化剂厂二〇〇二年七月目录1.概述2.物化性能及工业使用条件3.催化剂装填4 催化剂升温还原5.催化剂的正常使用6.催化剂使用中应该注意的问题7.停车8. 开车9. 催化剂的卸出10.产品的包装、运输和保管:附件:高温变换催化剂空气升温阶段的超温现象及防范措施中国石化集团南京化学工业有限公司催化剂厂是我国最早生产催化剂的企业,也是催化剂行业第一家通过质量体系认证(ISO9002)的专业生产厂。
目前能够生产40多个品种、90多个型号的化肥、石油化工、有机化工催化剂。
化肥催化剂是传统的优势产品,广泛用于国内大、中、小型各类高低压工艺制氨装置,并出口多个国家和地区。
高温变换催化剂使用目的是为了制备后续生产要使用的氢气。
通过催化反应过程来实现快速、连续。
催化剂的使用,包括从催化剂的选型开始,到催化剂的装填、升温还原、正常操作、维护保养等一系列过程。
催化剂的性能只有通过工业化应用才能得以体现。
催化剂使用水平的高低影响着催化剂性能的发挥。
为了您更好的使用好催化剂,在使用高温变换催化剂前,敬请阅读本手册高温变换催化剂使用操作说明书1.概述:1.1 在高温条件下,铁铬系高温变换催化剂能促进一氧化碳和水蒸汽的变换反应制取H2。
一氧化碳高温变换催化剂使用说明-图片版[1]
![一氧化碳高温变换催化剂使用说明-图片版[1]](https://img.taocdn.com/s3/m/310e8e95dd88d0d233d46ae2.png)
一氧化碳高温变换催化剂使用说明一、变换反应原理一氧化碳变换反应是指一氧化碳与水蒸汽作用生成二氧化碳和氢气的反应,反应如下:C O+H2O H2+C O2+41.19k J/m o l上式是一个典型的气固相反应,它在合成氨,合成甲醇,制氢气、羰基合成气、城市煤气工业中得到了广泛的应用。
一氧化碳变换反应是可逆放热反应,该反应在一般条件下进行得非常缓慢,远不能满足工业生产的需要。
在变换催化剂作用下,可显著提高变换反应的速度,并可防止和减少副反应。
根据化学平衡原理,反应温度越高,变换反应的平衡转化率越低。
在绝热的变换反应器中,为了获得较高的CO变换率,就需要尽可降低催化剂床层入口温度,以使床层出口温度尽可能低,这就要求催化剂具有良好的低温活性。
为了保证变换催化剂不被过度还原,必须在超过化学计量的汽气比下操作。
催化剂使用温度越高,必需采用的汽气比也越高。
如果使用低温活性好的催化剂,整个催化剂床层可在较低的温度下操作,则可以降低变换系统的操作汽气比,节省蒸汽消耗。
二、催化剂的装填催化剂的装填非常重要,将直接影响床层的压力降和气流分布,进而影响催化剂效能的正常发挥。
催化剂的装填方案应认真讨论,可装单一型号的催化剂,也可采用混装法。
如果要使用部分筛过的、比较完好的旧催化剂,应该在一段上部装三分之二的低温活性好的新催化剂;第三段应全装新催化剂;而在一段剩下的三分之一和二段温度较高的部位可装填部分旧催化剂。
这样装填既能发挥新催化剂的低温活性又能合理利用旧催化剂的剩余活性。
推荐装填高度比,二段式1:0.8,三段式1:1:1。
如此装填的目的在于保证一段在较高温度下加快变换反应的速度,而在变换炉最末端温度较低的条件下获得较高的变换率,在装填总量相等的情况下,变换率最高,或变换率一定的情况下蒸汽消耗最低。
1.催化剂装填之前要清除变换炉内杂物,并根据各段的催化剂装量,在炉内标出催化剂装填的高度。
2.炉篦上面要铺一层耐火球和金属网。
中温变换催化剂的升温还原及生产维

中温变换催化剂的升温还原及生产维修过程分析中温变换催化剂(TWHR)是一种广泛应用于工业生产中的催化剂。
其在一定温度范围内具有高效活性,能够催化有机物的氧化或还原反应。
在工业领域中,TWHR常用于催化剂的升温还原和生产维修过程。
一、TWHR的升温还原过程升温还原是指将催化剂经过一定时间的加热,使其达到还原状态的过程。
TWHR的升温还原过程主要包括以下几个步骤:1. 温度升高:在还原过程中,首先需要将催化剂的温度逐渐提高。
这需要控制加热速度,以避免因温度升高过快而造成的催化剂热分解或其它不可逆变化。
适当的加热速度可以保证催化剂内的活性组分得到最佳还原效果。
2. 活性组分的还原:随着温度的升高,催化剂中的活性组分逐渐得到还原。
在还原过程中,一些氧化物会被逐步还原为更活性的金属或金属氧化物。
这些还原过程往往需要在特定温度范围内进行,以保证最佳的还原效果。
3. 温度保持:在TWHR的升温还原过程中,通常需要在一定温度范围内保持一段时间,以使还原反应达到平衡。
这个温度范围是根据具体催化剂的特性和还原反应的需求来确定的。
在这个过程中,一些反应产生的不稳定中间产物会进一步转化为较稳定的物种,从而提高催化剂的还原效果。
二、TWHR的生产维修过程生产维修是指对已经使用一段时间的催化剂进行维护和修复的工序。
TWHR的生产维修主要包括以下几个步骤:1. 催化剂的取下:首先需要将催化剂从反应器中取下。
在这个过程中,需要避免催化剂的损坏,以免影响后续的修复和再利用。
2. 清洗和预处理:在取下催化剂后,需要对催化剂进行清洗和预处理。
清洗可以去除催化剂表面的积垢和污染物,预处理可以进一步恢复催化剂的性能和活性。
3. 检查和修复:清洗和预处理完成后,需要对催化剂进行检查和修复。
检查可以发现催化剂中的损坏和老化情况,修复可以修补损坏的活性组分或替换已经失效的部分。
4. 再利用或更换:修复完成后,可以将催化剂重新安装到反应器中,继续使用。
中温变换催化剂的升温还原及生产维

关于中变催化剂的升温还原及生产维护姓名:(云南解化集团有限公司云南开远 661600)摘要:针对CO中温变换催化剂使用周期远低于合理使用期,采取改善催化剂装填、升温、还原方案,优化工艺运行,加强催化的日常生产维护管理,极大地延长了中变催化剂的运行周期,取得了良好运行效果。
关键词:中变催化剂装填升温还原维护前言:我公司以褐煤为原料通过鲁奇炉制气生产合成氨,其中煤气中的CO中温变换催化剂在不同的时期采用过B104、B109、B113三种型号的催化剂,其使用寿命从开始的1年一更换,到2年、3年到现在的5~6年才更换一次,催化剂的使用寿命不断被延长,节汽更加显著,生产成本明显降低。
一方面是得益于科学技术的不断进步,生产工艺不断优化,新型低温活性较好的催化剂不断被研制运用;另一方面工程技术人员及操作人员对催化剂的认识逐步深刻,对催化剂使用、生产管理更加规范、科学、深入细致。
1、中变催化剂的装填装填工作首先在思想上要高度重视,装填工作如有失误会使整个计划更换期的时间内使生产受到损失,不能把这一重要的工作承包给毫无经验的临时工,而装填时又缺乏严格的现场管理。
催化剂装填首先应将催化剂过筛,因在运输或包装过程中,由于桷擦、滚、碰、撞等都会产生少量粉末或碎片,它们会在床层中形成局部堵塞而导致气流分布不均。
在直径较大而装填工作人员必须进入变换炉的情况下,工作人员不可直接踩在催化剂上,而应垫上木板,使身体重量分散在木板上。
催化剂床按气流进程的第一反应段上部的1/2或1/3部位,一定要放新的催化剂而不可放用过的旧的催化剂(即使是在第三段低温条件下使用过的旧催化剂也不能放在一段上部),这样,开车后才能有较低的进气温度,较高的变换率。
催化剂装填好后,上部应铺一层(约50~100mm)耐火球。
有一种想法是不妥当的,认为耐火球无催化活性,而用“高强度”的旧催化剂来代替耐火球。
但是即使是用足也采不破的“高强度”旧催化剂,在高温下碰上液态水,仍要粉化。
触媒还原操作规程
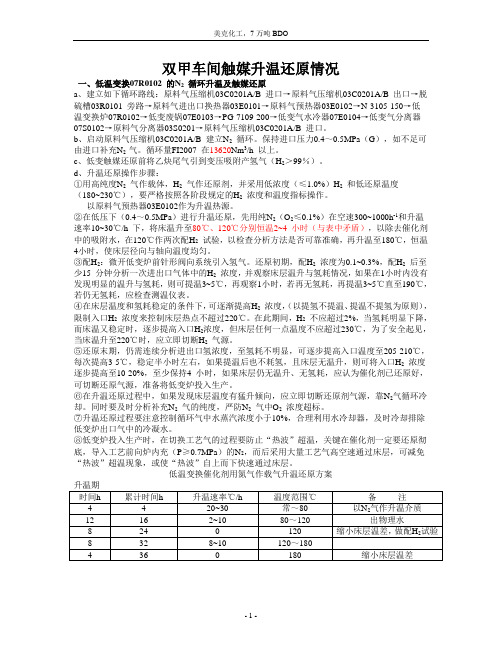
双甲车间触媒升温还原情况一、低温变换07R0102 的N2循环升温及触媒还原a、建立如下循环路线:原料气压缩机03C0201A/B 进口→原料气压缩机03C0201A/B 出口→脱硫槽03R0101 旁路→原料气进出口换热器03E0101→原料气预热器03E0102→N-3105-150→低温变换炉07R0102→低变废锅07E0103→PG-7109-200→低变气水冷器07E0104→低变气分离器07S0102→原料气分离器03S0201→原料气压缩机03C0201A/B 进口。
b、启动原料气压缩机03C0201A/B 建立N2循环。
保持进口压力0.4~0.5MPa(G),如不足可由进口补充N2 气。
循环量FI2007 在13620Nm3/h 以上。
c、低变触媒还原前将乙炔尾气引到变压吸附产氢气(H2>99%)。
d、升温还原操作步骤:①用高纯度N2气作载体,H2气作还原剂,并采用低浓度(≤1.0%)H2和低还原温度(180~230℃),要严格按照各阶段规定的H2浓度和温度指标操作。
以原料气预热器03E0102作为升温热源。
②在低压下(0.4~0.5MPa)进行升温还原,先用纯N2(O2≤0.1%)在空速300~1000h-1和升温速率10~30℃/h 下,将床温升至80℃、120℃分别恒温2~4 小时(与表中矛盾),以除去催化剂中的吸附水,在120℃作两次配H2试验,以检查分析方法是否可靠准确,再升温至180℃,恒温4小时,使床层径向与轴向温度均匀。
③配H2:微开低变炉前针形阀向系统引入氢气。
还原初期,配H2浓度为0.1~0.3%,配H2后至少15 分钟分析一次进出口气体中的H2浓度,并观察床层温升与氢耗情况,如果在1小时内没有发现明显的温升与氢耗,则可提温3~5℃,再观察1小时,若再无氢耗,再提温3~5℃直至190℃,若仍无氢耗,应检查测温仪表。
④在床层温度和氢耗稳定的条件下,可逐渐提高H2浓度,(以提氢不提温、提温不提氢为原则),限制入口H2浓度来控制床层热点不超过220℃。
精脱硫系统催化剂与转化催化剂的升温与还原复件

精脱硫转化系统开车方案及操作规程第一节精脱硫转化系统生产原理及流程一、原理1、精脱硫原理通过铁钼触媒及镍钼触媒将焦炉气中的硫醇(RSR,噻吩(GH4S)、二硫化碳(CS)、硫氧化碳(COS等有机硫加氢转化成无机硫HS、不饱和烃加氢转化为饱和烃;再利用铁锰脱硫剂及氧化锌脱硫剂,除去HS,使焦炉气硫含量w O.lppm。
(1)加氢反应RSH+2+RH+2S+Q;RSR ' +H二RH+R H+HS+QCHS+4H=GH0+HS+Q; CS 2+4H二CH+2HS+QCOS+24CO+H5+Q C 2H+H二GH+Q生产中铁钼触媒在进行上述反应的同时还存在以下副反应:CO+32+CH+HO+Q(甲烷化反应)2 H+O=2HO+Q(燃烧反应)C2H二C+CH+Q(析碳反应)2CO二C+C+Q(析碳反应)生产中加氢反应及副反应均为放热反应,在操作中应控制好触媒层温度。
铁钼触媒主要的副反应是甲烷化反应,因此操作中要注意原料气中CO 含量的变化。
(2)脱硫反应①铁锰脱硫剂对H2S的吸收反应:FeS+HS二FeS+HMnO+HB二MnS+HOMn S+2S= MnS+H2②氧化锌脱硫剂对硫的吸收反应:Zn O+bS=Z nS+bO2、转化原理在焦炉气中加入水蒸汽,在一定压力及温度下,通过催化剂作用,生成合成甲醇有用的H2、CO及CQ。
转化反应:CH+H2C= CO+3出QCO+ H 20= CQ+H2+QCH 4 = C+2H— Q二、流程1、精脱硫转化系统流程叙述来自焦炉气压缩机(C201)的焦炉气含H b S< 20mg/Nm有机硫250mg/Nm其压力为2.5MPa温度100〜110C。
焦炉气通过两台并联的脱油剂槽(D106a、b)脱除掉焦炉气中的油水之后进入冷热交换器(E104),被来自铁锰脱硫槽D103a D103b的一级脱硫气第一次加热;然后进入原料气第一预热器(E101)被来自转化气废热锅炉(E105)的转化气第二次加热;再经原料气第二预热器(E102)被来自气气换热器(E103)的转化气第三次加热;最后进入加热炉B101被第四次加热。
浅谈中变B112催化剂升温还原

关 键 词 : 变 炉 ; 12催 化 剂 ; 热 炉 中 B1 加
中 图 分 类 号 :Ql 3.6 T 1 2 文 献 标 识 码 : 文 章 编 号 :0 5—8 7 (0 2 0 B 10 3 0 2 0 )5—2 4—0 3
造 气 车 间 净 化 系 统 是 已有 2 0多 年 历 史 的 生 产 系 统 , 特 点 : 备 多 , 产 流程 长 , 艺 复 杂 。 中 变 其 设 生 工 装 置 只是 净化 系 统 中 的 一 个 组 成 部 分 , 且 又 是 极 而
中 变 炉采 用 的是 两 段 式 结 构 , 三 层 催 化 剂 , 装 有 效直 径 为 25 m, 效 容 积 为 6 3催 化 剂 体 积 70m 有 2m , 中变 催 化 剂 升 温 还 原 质 量 , 接 影 响 到 今 后 生 直 产 负 荷 高低 , 用 周 期 的 延 长 和 催 化 剂 利 用 率 的 提 使 高 , 减 小 对 后 工 序 的影 响 。 因此 , 据 生 产 的条 件 并 根
反 应 的热 点 温 度 由 4 0 逐 步 提 高 到 50 左 8℃ 2℃
在整个 装 填 过 程 中 , 终有 专 人 负责 检 查 、 始 落
实, 严格 把 关 不 出 差 错 。 并 根 据 实 际 情 况 把 催 化 剂 的装 量 作 了调 整 , 段 多 装 1 催 化 剂 , 对 今 后 的 上 吨 这 生 产是 非 常有 利 的 。
上 , 了 充 分 的修 改 和完 善 , 定 了相 应 的升 温 还 原 做 制 方案 。
4. 升 温 过 程 1
温情 况缓慢 增加并 进行严 格 的分 析 、 测 , 监 防止 C O 含量过 高或积 累 , 成床温猛涨或超温 。 造
中温变换催化剂的升温还原原操作说明
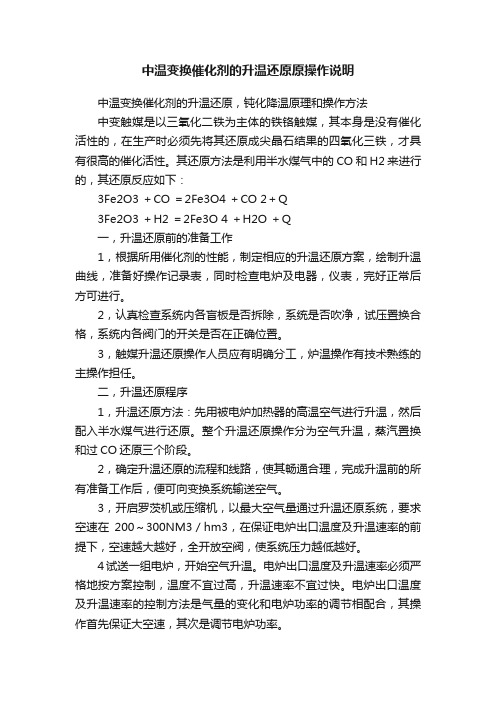
中温变换催化剂的升温还原原操作说明中温变换催化剂的升温还原,钝化降温原理和操作方法中变触媒是以三氧化二铁为主体的铁铬触媒,其本身是没有催化活性的,在生产时必须先将其还原成尖晶石结果的四氧化三铁,才具有很高的催化活性。
其还原方法是利用半水煤气中的CO和H2来进行的,其还原反应如下:3Fe2O3 +CO =2Fe3O4 +CO 2+Q3Fe2O3 +H2 =2Fe3O 4 +H2O +Q一,升温还原前的准备工作1,根据所用催化剂的性能,制定相应的升温还原方案,绘制升温曲线,准备好操作记录表,同时检查电炉及电器,仪表,完好正常后方可进行。
2,认真检查系统内各盲板是否拆除,系统是否吹净,试压置换合格,系统内各阀门的开关是否在正确位置。
3,触媒升温还原操作人员应有明确分工,炉温操作有技术熟练的主操作担任。
二,升温还原程序1,升温还原方法:先用被电炉加热器的高温空气进行升温,然后配入半水煤气进行还原。
整个升温还原操作分为空气升温,蒸汽置换和过CO还原三个阶段。
2,确定升温还原的流程和线路,使其畅通合理,完成升温前的所有准备工作后,便可向变换系统输送空气。
3,开启罗茨机或压缩机,以最大空气量通过升温还原系统,要求空速在200~300NM3/hm3,在保证电炉出口温度及升温速率的前提下,空速越大越好,全开放空阀,使系统压力越低越好。
4试送一组电炉,开始空气升温。
电炉出口温度及升温速率必须严格地按方案控制,温度不宜过高,升温速率不宜过快。
电炉出口温度及升温速率的控制方法是气量的变化和电炉功率的调节相配合,其操作首先保证大空速,其次是调节电炉功率。
5,尽可能地缩小触媒层的轴向温差,温差以50~80℃为妥。
120℃恒温主要是缩小触媒层轴向温差,有得于游离水缓慢地蒸发,以保证触媒的平稳温升和保护触媒的强度。
200℃恒温应将触媒层最低温度提至高于蒸汽漏点温度20℃以上,在系统压力为0.05~0.1MPa时,触媒最低温度应在120~130℃以上,为蒸汽置换作好温度上的准备。
中压变换升温还原总结

中压变换升温还原总结张峰,李媛媛(河南心连心化肥有限公司,河南新乡453731)摘要:介绍了中压变换炉的工艺流程及变换催化剂的硫化机理,详细讲述了硫化过程包括的升温期、硫化期、强化期、降温置换期等4个阶段,各阶段的运行时间、空速、床层温度和CS2加入量等,指出了CS2连接管断开、发生甲烷化反应、2#变换一段热点温度升至390 T等问题。
此次利用中修停车机会对变换催化剂进行了更换,自2017年5月31日开始升温至6月4日降温置换,一段、二段、三段温度均达到要求,标志着变换催化剂整体硫化工作结束。
关键词:中压变换;升温还原)催化剂中图分类号:TQ223. 12 [1文献标识码:B文章编号#2096-3548(2018#03-0022-02河南心连心化肥有限公司(以下简称心连心 化肥)化肥生产流程主要采用的是联醇生产技术[1],使用中压变换系统,生产运行压力为2. 0 MPa。
此次利用中修停车机会对变换催化剂 进行了更换,自2017年5月31日开始升温至 2017年6月4日降温置换,一段、二段、三段温度 均达到要求,标志着变换催化剂整体硫化工作结 束,6月5日并入系统开始正常生产。
1工艺流程变换炉催化剂装填量:一段装填抗毒剂20 m3,催化剂30 m3*二段装填催化剂32 m3*三 段装填催化剂47 @。
本次变换催化剂采用循环 升温硫化法,硫化与强化全部采用串联模式。
降 温置换合格后并入系统前使用2#变换气充压与 提温。
循环升温硫化路线$4#低压机来的合格的 半水煤气!1#变换硫化进气!硫化回气回4#低压机[2_3]。
2硫化机理变换系统采用B303Q型催化剂,其中活性成 分主要为氧化钴、三氧化钼,使用前须将其转化为 硫化态才具有活性。
此次硫化过程采用外加硫化 剂(CS2#方法进行,其反应方程式为:CS2 +4H2 =2H2S+CH4 -240 k\m〇1M〇03 +2H2S+ H2= M〇S2 +3H20-48.1k J/m〇1C〇0+ H2S= CoS+ H20-13.6 kJ/m〇1上述反应都是放热反应,特别是CS2的氢解 是很剧烈的放热反应。
B113中变催化剂使用说明

B113中变催化剂使用说明产品简介B113型CO高温变换催化剂系采用先进工艺生产的无硫型高温变换催化剂。
该催化剂以-Fe2O3为活性组成分,Cr2O3为助剂,并含有有少量活性添加剂的高活性宽温变换催化剂,适用于合成氨装置制氢装城市煤气甲烷等CO变换工艺。
变换反应如下:CO+H2O=CO2+H2+41.19KJ/molB113型催化剂的活性组成是γ-Fe2O3,其晶相结构及活化能都优于a-Fe2O3,因此,该催化剂的低温活性及使用强度均高于其它同类产品。
本企业采用特殊工艺制作的B113型催化剂还具有抗蒸汽冷凝(即抗水煮)的特点,因而提高了使用的抗风险能力。
该催化剂的本体含硫一般都低于250ppmm,开车时不需安排专门的放硫时间。
在当今国内外合成氨装置向低温节能型发展的同时,辽河牌B113型催化剂是一种非常理想的低温高性耐毒耐热长寿命节能型催化剂。
产品的物化性质物理性质化学组成适用条件B113型催化剂使用压力0.1-5.0Mpa,使用温度300-500℃,运行空速500-5000h,使用寿命预计三年以上。
B113型催化剂的突出特点是具有良好的抗蒸汽冷性能,在事故状态下,用工艺气干燥处理后,催化剂强度不减,床层阻力不增加,催化剂仍能保证事故状态前的活性。
装填催化剂的装填质量直接关系到反应器床层的气流分布阻力降及催化剂性能的发挥,因而要十分重视装填工作。
(1)为了保证装填质量,要选择晴朗的天气,并避开油污灰尘及化学毒物的污染。
(2)装填前,首先确认中变反应器质量合格,器内干燥,无其它杂物,并在内壁标出耐火球铁丝网篦子板和催化剂的装填线。
(3)催化剂装填前,要用4×4mm的筛网仔细过筛,除去运输过程中产生的粉尘。
(4)首先向中变反应器装25的瓷球12mm瓷球100-200mm,铺一层不锈钢丝网,然后再装催化剂。
(5)将催化剂慢慢吊至于器顶,缓慢的倒入接有帆布口袋的漏斗或溜槽中,催化剂从帆布袋口流入器内,器内需有人手握帆布袋口不断移动下料口位置,使催化剂按水平面上升,不得采用集堆后耙平的做法。
NB113型中温变换催化剂的升温还原及使用

NB113型中温变换催化剂的升温还原及使用
赵建安;任天河
【期刊名称】《中氮肥》
【年(卷),期】2008(000)002
【摘要】近年来,NB113型中温变换催化剂在全国各制氢和合成氨装置中得到广泛应用,为帮助相关用户进一步使用好该催化剂,本文以中原某氮肥厂为例,系统介绍NB113型中变催化剂的装填、升温还原及使用过程中应注意的事项。
【总页数】3页(P14-16)
【作者】赵建安;任天河
【作者单位】甘肃刘化(集团)有限责任公司,甘肃,永靖,731603;甘肃刘化(集团)有限责任公司,甘肃,永靖,731603
【正文语种】中文
【中图分类】TQ113.26+4.2
【相关文献】
1.IC171—1型和B113型变换催化剂的升温还原及生产使用小结 [J], 武利平;徐其胜
2.NB113型中温变换催化剂的延期使用 [J], 李晓波
3.IC171—1和B113型变换催化剂的升温还原及生产使用 [J], 武利平;徐其胜
4.低温型中温变换催化剂使用中几个问题的探讨 [J], 丁家灏
5.DGB型中温变换催化剂使用简介及节能效益 [J], 王国仁;李星孔
因版权原因,仅展示原文概要,查看原文内容请购买。
- 1、下载文档前请自行甄别文档内容的完整性,平台不提供额外的编辑、内容补充、找答案等附加服务。
- 2、"仅部分预览"的文档,不可在线预览部分如存在完整性等问题,可反馈申请退款(可完整预览的文档不适用该条件!)。
- 3、如文档侵犯您的权益,请联系客服反馈,我们会尽快为您处理(人工客服工作时间:9:00-18:30)。
中温变换催化剂的升温还原,钝化降温原理和操作方法中变触媒是以三氧化二铁为主体的铁铬触媒,其本身是没有催化活性的,在生产时必须先将其还原成尖晶石结果的四氧化三铁,才具有很高的催化活性。
其还原方法是利用半水煤气中的CO和H2来进行的,其还原反应如下:3Fe2O3 +CO =2Fe3O4 +CO 2+Q3Fe2O3 +H2 =2Fe3O 4 +H2O +Q一,升温还原前的准备工作1,根据所用催化剂的性能,制定相应的升温还原方案,绘制升温曲线,准备好操作记录表,同时检查电炉及电器,仪表,完好正常后方可进行。
2,认真检查系统内各盲板是否拆除,系统是否吹净,试压置换合格,系统内各阀门的开关是否在正确位置。
3,触媒升温还原操作人员应有明确分工,炉温操作有技术熟练的主操作担任。
二,升温还原程序1,升温还原方法:先用被电炉加热器的高温空气进行升温,然后配入半水煤气进行还原。
整个升温还原操作分为空气升温,蒸汽置换和过CO还原三个阶段。
2,确定升温还原的流程和线路,使其畅通合理,完成升温前的所有准备工作后,便可向变换系统输送空气。
3,开启罗茨机或压缩机,以最大空气量通过升温还原系统,要求空速在200~300NM3/hm3,在保证电炉出口温度及升温速率的前提下,空速越大越好,全开放空阀,使系统压力越低越好。
4试送一组电炉,开始空气升温。
电炉出口温度及升温速率必须严格地按方案控制,温度不宜过高,升温速率不宜过快。
电炉出口温度及升温速率的控制方法是气量的变化和电炉功率的调节相配合,其操作首先保证大空速,其次是调节电炉功率。
5,尽可能地缩小触媒层的轴向温差,温差以50~80℃为妥。
120℃恒温主要是缩小触媒层轴向温差,有得于游离水缓慢地蒸发,以保证触媒的平稳温升和保护触媒的强度。
200℃恒温应将触媒层最低温度提至高于蒸汽漏点温度20℃以上,在系统压力为0.05~0.1MPa时,触媒最低温度应在120~130℃以上,为蒸汽置换作好温度上的准备。
恒温操作首先保证大蒸汽量。
其次是适当地调节电炉功率,其电炉出口温度必须严格稳定在方案所要求的范围内,一般不应采用过高地提高电炉出口温度来提高触媒最低温度的方法。
6.在触媒层最低温度高于蒸汽露点后,可转为蒸汽置换升温。
在转空气升温为蒸汽置换升温的过程中,应注意保护好电炉,保证温升的平稳,保证罗茨机和压缩机的安全正常运行。
严禁系统压力过高,严禁带水进系统,尤其是触媒层。
在保证电炉出口温度及升温速率的前提下,在兼顾系统压力尽可能低的情况下,蒸汽量低些好。
蒸汽应将升温还原系统的所有设备和管线里的空气彻底置换干净(包括副线及设备的底部等死角)。
如需走倒流程置换应注意变化电炉,保证电炉出口温度温升的平稳,应避免变换气体的倒流。
要经常排放系统各处冷凝水。
7,蒸汽置换升温结束,当温度平稳,系统氧含量≦0.5%后,可转入触媒还原阶段。
宜采用打气量小的压缩机向系统送半水煤气,一般压缩机二出压力约0.05~0.1MPa,若采用罗茨机送为气还原,在保证罗茨机安全运行的前提下,压力尽可能高些,以保证还原煤气能进入升温还原系统。
如通煤气还原的阀门太大,可考虑设置管线小的近路来比较准确地调节还原煤气量。
8,应在大蒸汽比例的情况下,配入极少量的煤气。
开始触媒的还原,操作者应十分认真和慎重,应避免还原煤气量过大造成还原速度过快,温度过高。
触媒还原时间应长,应大于30分钟。
在多中手段都可以增加的煤气量的情况下,以每次只采用其中一种较稳妥,还原初期,蒸汽/煤气比应大于5:1。
在触媒升温还原过程中,如遇到触媒温度猛升,应酌情及时采用减小煤气量,加大蒸汽量。
换进口温度及使用煤气副线降低其它各段进口温度的方法来控制触媒层的猛升。
有条件的情况下可以适当采用相关蒸汽副线及**增湿的降温方法,来控制触媒的猛升。
触媒还原阶段配入过量的蒸汽以保证变换反应的正常进行,以控制触媒的还原温度和速度过高过快,以避免触媒的过度还原及减少副反应的发生。
9,还原阶段应将电炉出口温度缓缓地升至300℃,并稳定在300±10℃,避免因电炉出口温度的波动造成触媒温度的大起大落。
10,在触媒升温还原期间,应避免升温介质部分地走近路,直接进入第二,三层触媒。
11,保证半水煤气中O2≦0.5%,进入还原阶段应加强中变炉进出口气体成分的分析。
12,还原终点温度应略低于正常操作温度450℃,当催化剂层温度接近450℃时,应恒温4小时,等待触媒层温度平稳,放空气体中CO含量符合正常生产的工艺指标时,还原工作即告结束。
此后逐渐增加原料气和蒸汽,转入正常生产。
钝化降温的原理和操作方法钝化:①催化剂在使用期间,主要成分以Fe3O4存在,且具有很高的反应活性。
在系统停车检修时,要先将其表层缓慢氧化形成一层Fe2O3保护膜后才能与空气接触,这一过程称为钝化,反应方程式如下4Fe3O4+O2﹦6Fe2O3+Q②,钝化降温的操作方法,最常用的钝化降温方法是直接钝化降温,其操作方法如下。
停车前加大蒸汽,降低催化剂层温度。
停车后,切断与外工段联系,放空卸压,用蒸汽继续降温,待温度将到200℃左右,系统内通空气。
开始空气量要小,严防氧化激烈烧坏催化剂。
根据温度变化情况,调节罗茨机近路和出口阀控制空气,蒸汽加入量,力求温升速率不超过50℃/h,催化剂层温度最高不超过400℃,每次待温度将到200℃左右时,再适量增加空气量,这样经过数次的反复,分析变换炉出口气氧含量达20%,炉温基本上不在上升,切断蒸汽,全部用空气降温,150℃以下停热水泵,待炉温继续将到60℃以下停罗茨机,钝化降温结束。
低变触媒再硫化的目的及方案低变触媒呈现反硫化后,其部分活性组分失活,以氧化态存在,必需经高温充分硫化,使其转化为硫化物,方能恢复其高活性。
再硫化时采用气体一次通过法:即用含H2的干气体(变换气)作载气,经电炉加热后配以适量的CS2,通过触媒层,炉后放空,常压进行。
硫化的反应方程式:CS2+4H2=2H2S +CH4+240KJCoO +H2S =CoS +H2O +13.4KJMoO3 +H2S =MoS2 +3H2O +48.5KJ以上反应均为放热反应,半水煤气中每1gCS2/Mg氢解温升近3℃,因此再硫化时需密切注意床层温度,防止暴涨。
因此再硫化分三段进行,确认一段硫化结束后,方可进行二段强制硫化,二段硫化结束后方可对三段进行强制硫化。
硫化结束标志:(1)触媒层各点温度都应≧425℃并保持6小时(可在动态二小时后采用闷炉静硫化)(2)连续三次(每半小时一次)分析低变炉进,出口气体H2S含量相进且15g/Mg以上。
二、再硫化前准备工作;:1严格检查硫化系统各密封点的试漏工作确保无泄露.2检查硫化系统气体进口阀,放空阀,近路阀,排污阀的开关灵活性,确保好用,无泄露.3检查CS2储罐压力表准确度,液位计气,液相是否畅通,氮气瓶减压阀是否好用,CS2出口阀是否内漏,最好用闸阀.4,请电工,仪表工检查电炉,仪表的完好情况。
三、具体再硫化升温步骤1将CS2加如储罐,然后用钢瓶中的氮气将储罐压力绳至0.1~0.15MPa备用。
2开启低变炉后放空阀,用氮气置换电炉及低变系统至O2≦%3打开升温管线变换气进口阀及电炉出口阀,由炉出口放空阀放空。
4开电炉,触媒开始升温。
5当低变进口温度达200℃且触媒上段温度达180℃时,稍开CS2储罐出口阀,控制CS2流量在5~61/h,与电炉出口变换气混合进入低变炉。
6根据方案逐渐提高触媒温度及H2S浓度,直至400℃时进行深度硫化,当触媒进,出口H2S浓度几乎无变化且出口H2S≧15g/M3时,方可为在硫化结束。
7触媒温度升至300℃时,每小时分析一次出气H2S,升至350℃以上时每半小时分析一次,以掌握S穿透。
8 硫化结束后切电炉开始降温,在降至300℃以前仍应继续加入CS,以防反硫化。
9温度降至300℃切CS2,并加大放空量排硫,当出气H2S将至≦0.15g/M3时并如系统。
三、再硫化操作要求:此次硫化为触媒反硫化后的重新硫化,尤其一项技术性很强的工作。
再硫化后效果的好坏对今后的生产,能耗有着重要的影响,如控制得好,再硫化后效果的好坏对今后的生产,能耗有着重要的影响,如控制的好,低变触媒能恢复大部分活性。
1温度控制:初期提湿较容易,在中,后期要及时调整空速,电炉功率及CS2加入量,以确保湿度按要求提升至硫化最终温度。
2 CS2加如量的控制初期可适当减少,后期适当增加,充分利用氢解反应热。
如初期CS2加入量过大,容易引起床层温度暴涨。
3操作调节:气量(空速),电炉及CS2加入量为硫化操作的三个手段。
在实际应用中应尽量不采用多元素操作,应稳定CS2加入量(稳定CS2储罐压力),以控制压力为主。
适当调节功率。
四,再硫化操作注意事项:1.低变触媒再硫化应与原始硫化一样精心对待,硫化速率不能过快,时间不能过短。
2再硫化过程是使每一温升阶段让低变触媒吸硫“吃饱状态”,然后再升温进入下一阶段,其判断依据:一是低变触媒吸硫时各温度温升明显,当该温度状态吸硫达到饱和后,各点温度逐步拉平接近,二是低变进,出口H2S浓度趋于平衡。
3再硫化时触媒温度不得超过500℃,否则MoS2易在高温条件下升华,使触媒永久失活。
因此,在发现触媒温度暴涨时,应立即停加C2S,停电炉,并加大变换气流量,使温度下降,趋于平衡。
然后查清原因,重新硫化。
4严禁水蒸汽带入低变炉内。
5硫化结束降温吹排保持一定空速,否则容易因温度高H2S不足而反硫化,影响活性。