清洁验证合格限度计算
清洁验证淋洗水残留限度公式

清洁验证淋洗水残留限度公式在清洁验证中,淋洗水残留限度公式是一个重要的指标,用于确定在清洁过程中是否存在残留的淋洗水,并评估其数量是否符合规定的限度。
淋洗水是在清洁生产过程中使用的一种溶液,用来清洁和去除工艺设备和工作表面上的污垢、油脂、细菌等。
然而,假如这些淋洗水在清洁后仍然残留在设备表面上,可能对产品质量和生产过程的效率产生负面影响。
为了解决这个问题,制定了清洁验证淋洗水残留限度公式,用于判断淋洗水的残留是否在允许的范围内。
这个公式通常基于残留物质的最大容忍量和最终产品的使用要求来确定。
具体而言,清洁验证淋洗水残留限度公式可以根据以下步骤计算:1. 确定最大容忍量(MRC):MRC是指在清洁过程中允许残留在设备表面上的淋洗水的最大数量。
这个值通常取决于产品的特性和使用要求,可以通过相关标准和指南来确定。
2. 收集样品:在清洁后,从设备表面上收集淋洗水的样品。
这可以通过采用适当的试剂和工具,如棉签、洗涤剂溶液等来实现。
3. 测定淋洗水残留量:将收集到的样品送往实验室进行分析。
使用适当的分析方法,例如高效液相色谱法(HPLC)或质谱法,来测定淋洗水中特定物质的含量。
4. 计算残留水量:使用以下公式计算淋洗水残留量:淋洗水残留量 = (测定结果 / 设备表面积) x 100%5. 比较结果与MRC:将计算得到的淋洗水残留量与最大容忍量进行比较。
如果计算得到的残留量小于或等于MRC,则判定清洁过程合格。
如果计算得到的残留量大于MRC,则需要重新评估清洁过程或采取其他措施来降低淋洗水的残留量。
通过清洁验证淋洗水残留限度公式,生产企业可以确保清洁过程的有效性和产品质量的稳定性。
这有助于提高产品安全性和合规性,并保护消费者的权益。
因此,清洁验证淋洗水残留限度公式在生产过程中具有重要的作用,需要被严格遵守和执行。
设备清洁方法验证标准操作规程

文件制修订记录一、目的通过科学的方法采集足够的数据,以证明按规定方法(清洁规程)清洁后的设备,能始终如一地达到预定的清洁标准。
二、适用范围:所有工艺设备清洁方法的验证。
三、责任者:生产车间、质量保证部四、管理程序:清洁验证实际就是对清洗标准操作规程的验证,通过验证建立合适的设备清洁标准操作规程。
清洁验证的目的足证明所采用的清洁方法确能避免产品的交又污染,微生物污染以及清洁后残留的污染,使之达到可接受限度标准。
1、清洁验证的步骤1.1列出待进行清洁验证的设备所生产的一组产品。
1.2选择参照产品。
在所生产的一组产品中,选择最难清洁(即溶解度最小)的产品作参照产品。
相对于辅料而言,活性成分的残留物对下批产品的质量,疗效和安全性有更大的威胁,通常将残留物中的活性成分确定为最难清洁物质。
1.3选择设备最难清洗部位和取样点。
凡是死角、清洁剂不易接触的部位——如带密封垫圈的管道连接处,压力、流速迅速变化的部位如有歧管或岔管处,管径由小变大处,容易吸附残留物的部位如内表面不光滑处等,均应视为最难清洗部位。
取样点应包括各类最难清洗部位。
1.4选择最不利清洗条件的参数A=一组产品中最小NOEL=活性成分最小LAD/40(μg/60kg体重)其中:NOEL—活性成分的无显著影响值;LAD—每60kg体重最小有效剂量;40(即4×10)—总体安全系数;B—一组产品中最大口服日剂量(m1/g或mg/日)C—一组产品中最小批量(mg或m1)D—棉签取样面积(25cm2/每个棉签);E—设备内表面积(或与物料直接接触的总面积)(cm2)F—取样有效性(一般取50%,即假定棉签所取样品有50%的量被洗脱出来);G—冲洗溶剂的体积(m1)。
1.5化学验证及可接受标准限度。
清洗效果的最终评价根据是产品活性成分即主药及洗涤剂的残留量、微生物限度。
目前,企业界普遍接受的限度标准基于以下原则:(1)生物活性限度:任何产品不能受到前一品种带来的超过其0.001的日剂量的污染;(2)分析方法客观能达到的能力:污染不能超过10PPm。
清洁验证标准和可接受限度
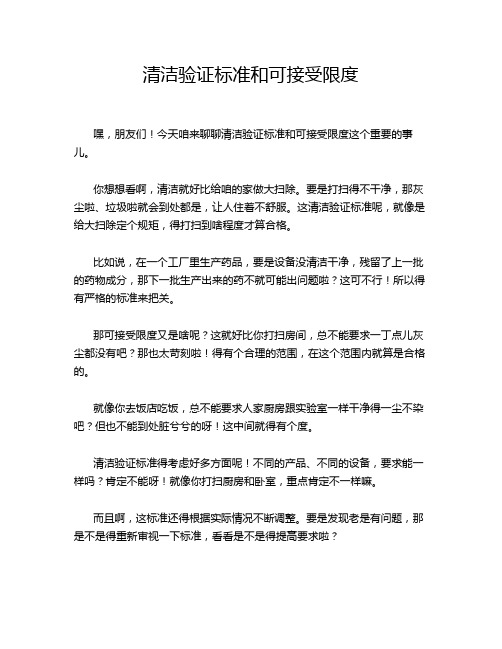
清洁验证标准和可接受限度嘿,朋友们!今天咱来聊聊清洁验证标准和可接受限度这个重要的事儿。
你想想看啊,清洁就好比给咱的家做大扫除。
要是打扫得不干净,那灰尘啦、垃圾啦就会到处都是,让人住着不舒服。
这清洁验证标准呢,就像是给大扫除定个规矩,得打扫到啥程度才算合格。
比如说,在一个工厂里生产药品,要是设备没清洁干净,残留了上一批的药物成分,那下一批生产出来的药不就可能出问题啦?这可不行!所以得有严格的标准来把关。
那可接受限度又是啥呢?这就好比你打扫房间,总不能要求一丁点儿灰尘都没有吧?那也太苛刻啦!得有个合理的范围,在这个范围内就算是合格的。
就像你去饭店吃饭,总不能要求人家厨房跟实验室一样干净得一尘不染吧?但也不能到处脏兮兮的呀!这中间就得有个度。
清洁验证标准得考虑好多方面呢!不同的产品、不同的设备,要求能一样吗?肯定不能呀!就像你打扫厨房和卧室,重点肯定不一样嘛。
而且啊,这标准还得根据实际情况不断调整。
要是发现老是有问题,那是不是得重新审视一下标准,看看是不是得提高要求啦?再说说可接受限度,这可不是随便定的。
得综合考虑各种因素,既要保证产品质量,又不能太不切实际,让人没法做到。
这就好比你跑马拉松,总不能要求每个人都像专业运动员一样跑那么快吧?得根据大多数人的能力来定个合理的目标。
咱平时生活中也一样,你洗个碗,也得有个差不多干净的标准吧,总不能还带着饭粒就说洗好了。
清洁验证标准和可接受限度就是为了确保一切都在可控范围内,让我们放心使用产品,不用担心有啥问题。
要是没有这些标准和限度,那不乱套啦?产品质量没法保证,我们的健康也可能受到威胁呀!所以说啊,这可真是太重要啦!大家可得重视起来,别不当回事儿。
只有严格按照标准和限度来做,才能生产出高质量的产品,让我们用得安心,吃得放心!这就是我想说的,大家觉得有没有道理呢?。
清洁验证之限度计算方法分析

清洁验证之限度计算方法分析目前最常用的化学残留限度计算方法主要有以下四种:1基于最低日治疗剂量的千分之一标准计算公式如下:R:单位面积残留MTDD:最低日治疗剂量SBS:下一产品最小批量SF:安全因子TDDnext:下一产品最大日服用量S:共用接触面积该计算方法通常适用于制剂产品。
对于原料药,如果明确其将来的制剂形式,也可以采用该方法计算化学残留限度。
该公式中有个计算陷阱,须格外注意。
分子中的MTDD指的是上一批产品的最低日治疗剂量,为每天服用的有效成分(API)的量。
分母中TDD指的是下一批产品的每天的服用量,该服用量包括有效成分和辅料。
(记忆小技巧:分子应尽量小,分母应尽量大,以得到更严格的限度标准。
)2基于浓度的10ppm标准计算公式如下:R:单位面积残留限度SBS:下批产品最小批量SF:安全因子S:共用接触面积该计算方法应用面非常广,适用于大多数药品的清洁残留限度计算。
3基于毒理的限度标准MACO:最大允许残留量,从上一产品带入下一产品的最大可接受量PDE :每日允许暴露量SBSnext:下一产品最小批量TDDnext:下一产品的最大日服用量NOAEL:无可见有害影响水平Weight adjustment:体重调节F1~F5:安全因子(安全因子F1到F5具体如何选择,也可以参考ICH Q3C的相关内容,限于篇幅,本文中不再做重复介绍。
)基于毒理的残留限度计算方法可以参考欧盟在其官方网站上公布的《在共用设施生产不同药品使用风险辨识建立健康暴露限度指南》,并结合APIC(原料药委员会)发布的《原料药工厂清洁验证指南》的部分内容可以得到上述公式。
该计算方法中每日允许暴露量(PDE)的计算公式中NOAEL的查找和确定将是面临的一个困难。
目前制药企业可能没有足够的时间和精力去摸索每一个原料药的NOAEL值,而对于NOAEL的检索应基于科学的方法并制定相应的策略。
检索策略、检索记录和结果均应该记录,并应由相关的主题专家(SME)进行审核,因此对NOAEL的准确性判断将非常关键。
清洁残留限度原理和计算公式解析

清洁残留限度原理和计算公式解析清洁验证在制药生产过程中起着重要作用, 其是防止药品污染和交叉污染的重要控制措施, 目的是确保共线生产产品之间不会产生交叉污染, 影响产品正常药理学作用。
01残留的举例要讲述药物残留,我想先以一个例子作为代入:芝麻炒饭我们都做过炒饭,假设炒饭需要加芝麻,我们把黑芝麻粒看作是炒锅的残留物,当我们加入米饭进行翻炒时,我们假设炒饭结束后,黑芝麻粒在炒饭操作的过程中被均匀分散到炒饭中。
这时我们需要将炒饭等量分给几份给顾客,但是这几个顾客都不太喜欢炒饭中有太多的芝麻,比如一碗米饭(假设是200g)不能有超过2g的芝麻粒,那么在下一次炒饭时,我们就需要根据顾客的数量以及米饭的数量,确定我一开始应该放多少g的芝麻才不会引起顾客的不适。
药物的残留限度也和以上举的例子是一样的道理,只是芝麻粒转变成了药物残留,炒锅转变成了生产设备,米饭转变成了拟生产的产品,顾客转变成了用药对象。
02药物残留原理和意义要想了解药物残留限度的计算公式,我们先了解药物在生产过程中残留的方式,以及其所产生的实际意义,可以帮助我们更好的理解计算公式和应用。
对于清洁验证中的残留限度,一般主要针对的是共用设备的直接接触设备内表面的活性药物残留。
1、A生产后残留于设备内表面所表达的是上一生产产品(A产品)生产结束后的活性药物残留,默认均匀的分布(考虑到清洁验证最差条件,实际以最难清洁部位,最大残留量的位置计)千生产过程中物料所接触的设备内表面。
2、A的所有残留全部被带入B中然后在下—产品(B产品)生产时,物料在接触与A产品共用的设备内表面,将A产品的API残留全部(实际可能不全部带入,但清洁验证按最差情况考虑)带入B产品的物料(按1批计)中,此时也是默认均匀的分散在B产品的物料中。
3、被带入B中的残留均匀分散通过生产成型均匀分布在每一个单位剂量的B产品中。
4、患者服用B时吸入A患者在服用B产品时,会将残留千B产品的A产品活性药物也同步吸收,如果A的活性残留量较大,B 产品的单位剂量中所残留的A产品活性残留也就越高。
清洁验证方案

一引言1 概述贝诺酯合成车间生产设备均为专用型设备,专门用于单一品种、同一规格原料药的生产,各类型设备均制定有具体、完善的设备清洁规程和清洁记录,在生产工艺过程中与成品质量关系密切的清洗过程涉及:氯化反映罐、酯化反映罐、离心机、板框压滤机、脱碳过滤系统、精制结晶罐、洁净区离心机、干燥箱、粉碎机、二维混合机等设备的清洗。
同时,对洁净区的清洁进行验证,确认洁净厂房的清洁效果。
本验证即针对以上关键环节的清洁规程和清洁效果进行清洁验证。
2 目的通过对反映罐、离心机、脱碳过滤系统、精制结晶罐、洁净区离心机、气流干燥、气流粉碎等设备清洗过程的检查和监测,证明已经制定的设备清洁规程切实可行,可以达成保证药品质量的目的,文献资料符合GMP的管理规定,并为设备清洁规程的进一步修改和完善提供资料和依据。
3验证类别本次验证为同步验证。
二参考资料本文献参考了以下标准和指南:1.中华人民共和国药典(2023版)2.GMP(2023年修订版)3.药品GMP指南4.药品生产验证指南(2023版)三验证准备1 验证人员及职责1.1 各部门的验证职责质量负责人:批准验证方案、验证报告。
生产负责人:审核验证方案、验证报告。
生产运营部职责:审核验证方案、验证报告。
提供公用系统保证。
提供设备维修保证。
针对不一致项界定解决办法。
负责测量仪器的校验,并提供校验证书。
生产车间职责:起草、审核验证方案、验证报告。
组织实行验证方案。
收集相关数据,编写相关的验证报告。
对参与验证的人员完毕必需的的培训。
指定操作人员,对生产设备进行操作,清洁和维护保养。
拟定最终的SOP。
质量管理部职责:负责审核验证方案。
负责监督严格按照验证方案及所依据文献规定方法和标准实行验证。
负责对验证过程中户县的偏差和变更评价和解决。
维护所有受控的文献符合法规。
负责制定相关的质量标准、检查规程和取样程序。
负责相关的取样及校验,并依据检查结果出具检查报告单。
审核验证结果、最终验证报告保证所有验收标准均得到满足。
清洁验证最全计算公式截止到2020年

ISPE 指南RISK-mapp (第1版2010年) ADE (mg/天)=NOAEL (mg/kg/天)×BW (kg )UFc (综合不确定因子)×MF (修正因子)×pk (药代动力学调节因子)EMA 指南(2014年)PDE (mg/天)=NOAEL (mg/kg/天)×BW (kg )F1(物种间推断因子)×F2(个体间差异因子)×F3(短期重复剂量毒性研究的因子)×F4(毒性如致癌致畸致毒情况下可能试用的因子)×F5(未建立无效水平应用的可变因子)ISPE 指南RISK-mapp (第2版2017年)PDE 或ADE (mg/天)=POD (mg/kg/天)×BW (kg )AFc (综合调整因子)×MF (修正因子)×pk (药代动力学调节因子)ASTM 组织E3219部HBEL 推导(2020年) ADE (mg/天)=POD (mg/kg/天)×BW (kg )Ft (综合调整因子)×PK-AF (累积因子)×α(接触途径的生物利用度)说明:POD 为人某途径给药最低剂量,且为成人则BW 不纳入。
◆ PK-AF 计算◆ A:适用于研究的给药时间表是间歇性的,或者研究的时间太短而无法达到稳态浓度,如果临床文档中未提供1、PK-AF=11-e-0.693/t 1/2*t :(e 自然对数,t 给药时间间隔;t 1/2为药物消除半衰期;药代动力学房室模型评估)2、PK-AF=1.44*t 1/2t3、凯尔方程假设一阶动力学,并提供一个修正因子来反映人类的代谢率,生物蓄积和正常的排泄机制4、还可以通过使用规定的剂量间隔(以天为单位)每日平均剂量来计算PK-AF 。
例如,如果每周一次给药,则PK-AF 为7 B 、 如果PoD 给药间隔达到稳态浓度,则通常不需要PK-AF ◆ α(PK-ABS )计算1、α=FHBEL /FPoDFPoD =研究中使用的给药途径的生物利用度分数(如口服0.2FHBEL =建立HBEL 的给药方式的生物利用度分数.(如IV 静脉为1.0),则α为5 2、如果已知人类口服生物利用度,则可以使用生物利用度范围的平均值。
清洁验证残留物计算公式(一)

清洁验证残留物计算公式(一)清洁验证残留物1. 简介清洁验证残留物是指在清洁过程完成后,可能残留在物体表面的污染物或化学物质。
为了确保清洁工作的有效性,需要对残留物进行验证。
本文将介绍清洁验证残留物的计算公式,并提供示例说明。
2. 计算公式残留物检测值(RWV)残留物检测值(Residue Detection Value,RDV)是一种测量残留物含量的指标。
它通常使用以下计算公式进行计算:RWV = (残留物质重量 / 清洁表面积) * 100其中,残留物质重量是指在清洁过程中收集的残留物质的重量,清洁表面积是指被清洁的表面的面积。
有效清洁度(CE)有效清洁度(Cleaning Effectiveness,CE)是指清洁过程的效果。
它可以使用以下计算公式进行评估:CE = (1 - (RWV后 - RWV前) / RWV前) * 100其中,RWV前是清洁前的残留物检测值,RWV后是清洁后的残留物检测值。
CE的值越高,表示清洁效果越好。
3. 示例说明以清洁工作中的一个常见案例为例,说明如何应用上述计算公式。
假设清洁前的残留物检测值RWV前为40,清洁后的残留物检测值RWV后为10。
根据计算公式,可以计算得到有效清洁度CE的值:CE = (1 - (10 - 40) / 40) * 100 = 75%根据计算结果可知,该清洁过程的有效清洁度为75%,说明清洁效果较好。
4. 结论清洁验证残留物的计算公式可以帮助评估清洁过程的有效性。
通过测量残留物检测值和计算有效清洁度,可以确保清洁工作的质量。
在实际应用中,可以根据特定情况进行公式的调整和优化,以适应不同的清洁需求。
注意:上述公式和示例仅供参考,对于具体情况仍需根据实际情况进行调整和确认。
关于清洁验证

清洁验证是指对设备或工具清洁工艺有效性的验证,其目的是证明所采用的清洁方法确能避免产品的交叉污染以及清洁剂残留的污染。
2 范围包括所用能够直接接触到产品、或接触产品的介质的设备以及部件的清洁。
新产品、新工艺、新设备在投入使用前清洁验证必须合格。
3 职责R&D:负责提供可选择的清洁剂种类及清洁后残留物(活性成分、有机溶剂、微生物、清洁剂、缓冲剂、润滑剂和设备磨损等)的检测方法和残留限度。
生产车间:负责制定清洁SOP,执行清洁操作以及对操作人员的培训和考核。
质量保证部:负责制定取样方法和执行取样,并对清洁验证的结果进行评价。
质量控制室:负责对R&D提供的检测方法进行分析方法的验证并制定检验规程,按照检验规程对样品进行检验和结果评价。
6 规程6.1 验证前的准备取样回收率试验及清洁剂的选择,要求取样回收率大于80%,取样回收率RSD﹤20%。
清洁剂的选择要考虑到是否对设备产生污染,最好的清洁剂是水、乙醇、异丙醇。
建立清洁验证的分析方法,并对分析方法进行验证。
6.2 验证方案内容验证方案内容包括:清洁方法,用于清洁的设备,清洁过程、次数,采用清洁剂的种类、浓度、用量,清洗顺序和时间,取样方法,取样部位图示,残留物测定的方法和限度,确定已清洁设备的存放条件和存放时限等,设备清洁后可存放的最长时间和存放条件应要求写在设备清洁程序中。
验证时考虑的最差情况为设备最难清洗的部位、最难清洗的产品以及主药的生物活性等。
6.3 可接受标准:1.概述根据清洗过程中的清洗时间,清洗部位,清洗程序,清洗液用量,洗涤剂各类数据及清洁结果对“清洁规程”的清洁效果进行验证。
3.验证使用的文件文件名称存放地点ZSL-A-3KW型真空上料机的标准清洁规程生产设备部档案柜存放1份4.验证范围:本设备清洁验证方案范围为:真空上料机、粉碎各岗位设备的清洁。
5 验证条件5.1 设备条件:能正常使用的完好设备。
5.2 清洁剂条件:为清洁规程中规定的清洁剂。
GMP清洁验证中的最大残留限值(MCL)计算

清洁验证中的最大残留限值(MCL)计算合格标准的Sievers推导合格标准的Sievers推导是一个多步计算,并将碳和API贡献系数应用到最终的合格标准结果上。
每一步骤的说明如下:1每日容许摄入量每日容许摄入量(ADI)被认为是安全水平,通常与毒性水平一起用于合格标准计算,以减少各批次之间的残留风险。
根据生产的产品,通过应用安全系数,从未观察到作用剂量NOEL(Non-observed Effect Level)值计算至ADI值。
2后续产品中的最大残留限值(MCL,Maximum Carryover Limit)可计算MCL以显示后续产品B中产品A浓度的绝对量。
此计算中的大多数系数可在法规档案、产品标签和公司规定的验证文件(如主计划、协议、认证或步骤)中非常容易找到。
以下修正的公式(原来由Foreman和Mullen 开发)给出允许的最大残留浓度。
其中:MCL = 最大残留限值(mg/L)ADI = 每日允许摄入量(mg)Bbatch = 后续产品B的批量(mg)Bmax dose = 产品B的最大剂量(mg)3单位表面积的绝对限值计算MCL之后,下一步是确定共用生产设备的表面积上可能污染含量的残留限值。
其中:MCL = 最大残留限值(mg/L)SSA = 用于生产产品A和B的设备的共用表面积(cm2)有时无法确定MCL计算中的某些系数。
例如,在开发阶段,确定产品A和B的剂量规定可能太早。
因此建议使用体积计算以确定正常运行时设备的处理容量。
其中:MCL = 最大残留限值(mg/L)ADI = 每日允许摄入量(mg)矩形设备的容积=长x 宽x 深(cm3)圆柱形设备的容积=圆形面积x 深(cm3)圆锥形设备(如V型混合器)的容积=圆形面积x 深/3(cm3)SSA = 用于生产产品A和B的设备的共用表面积(cm2)务必认识到此系数的推导,是假设所有产品残留体积均匀分布在设备的共用表面积。
推导的下一步提供一种解决方案,通过验证的TOC分析方法确定所分析的擦拭或漂洗样品中的限值。
4种残留限度计算方法

四种制药清洁限度算法详解在《药品共线生产质量管理指南(征求意见稿)》出台之前,制药企业常用的清洁限度的算法有最低日治疗剂量的1/1000、10ppm、半数致死量LD50,2021年11月,中国CFDI 出台了《药品共线生产质量管理指南(征求意见稿)》,提供了更具有科学性和优势的方法,即基于健康的暴露限度(ADE/PDE)。
本文就这四种清洁限度作一下论述1、最低日治疗剂量的1/1000定义:下批产品的最高日服用剂量中含有上批产品的量不超过上批产品的最低日治疗量的1/1000,以此标准来制定残留限度。
公式:MDDbUbBb MTDa L ⨯⨯=10001000/1解释:MTDa:清洁前产品(目标化合物)最小每日给药剂量中的活性成分含量(mg);Bb:清洁后产品的批量(支/瓶)Ub:清洁后产品的每支含量(mg)MDDb:清洁后产品(目标化合物)最大每日给药剂量中的活性成分含量(mg)解析:①a 品种专用MTDa 对特定品种a 是固定值,根据生产线所有品种,选择MDDbUbBb ⨯最小值,即为a 品种专用限度。
②全品种可用MDDUB MTD L ⨯⨯=10001000/1根据生产线所有品种,选择MTD 最小值,选择MDDUB ⨯最小值,即为该生产线全品种皆可用限度。
历史:[1/1000来源:对于一个产品,出现在另一种产品的最大每日剂量中量,不应超过其剂量的0.001(1/10x 1/10x 1/10)。
其中,第一个1/10系数:认为药物在剂量的1/10下是非活性的;第二个1/10系数:以确保清洁程序是稳健的;最后一个1/10系数:作为安全系数。
]2、残留物浓度10ppm来源:《药品生产验证指南》指出除高活性,高致敏性药品外,10ppm 是足够安全的,衍生出了以10ppm 为限度计算残留物浓度,即,将10ppm 简化为最终淋洗水中样品残留物浓度限值为10ppm。
公式:FppmBb L ppm 1010⨯=解释:Bb:清洁后产品的批量(kg);10ppm:10×10-6,即10mg/kg;F:为安全因子系数,根据风险评估,一般取2-10;根据生产线所有品种,选择最小批量进行计算,即为该生产线全品种皆可用限度。
揭密清洁验证中的最大残留限值(MCL)计算

揭密清洁验证中的最大残留限值(MCL)计算药品生产中清洗过程的主要目的之一,是去除产品或洗涤剂残留,以防止潜在污染转移到生产的下一产品中。
确保不会出现这种情况的一个必要程序,是建立经科学证明的合格标准限值。
本文专为使用TOC建立合格标准进行逐步讲解。
| 合格标准的Sievers推导 |合格标准的Sievers推导是一个多步计算,并将碳和API贡献系数应用到最终的合格标准结果上。
每一步骤的说明如下:1 |每日容许摄入量每日容许摄入量(ADI)被认为是安全水平,通常与毒性水平一起用于合格标准计算,以减少各批次之间的残留风险。
根据生产的产品,通过应用安全系数,从未观察到作用剂量NOEL (Non-observed Effect Level)值计算至ADI值。
2 |后续产品中的最大残留限值(MCL,Maximum Carryover Limit)可计算MCL以显示后续产品B中产品A浓度的绝对量。
此计算中的大多数系数可在法规档案、产品标签和公司规定的验证文件(如主计划、协议、认证或步骤)中非常容易找到。
以下修正的公式(原来由Foreman和Mullen开发)给出允许的最大残留浓度。
其中:MCL = 最大残留限值(mg/L)ADI = 每日允许摄入量(mg)Bbatch = 后续产品B的批量(mg)Bmax dose = 产品B的最大剂量(mg)3 |单位表面积的绝对限值计算MCL之后,下一步是确定共用生产设备的表面积上可能污染含量的残留限值。
其中:MCL = 最大残留限值(mg/L)SSA = 用于生产产品A和B的设备的共用表面积(cm2)有时无法确定MCL计算中的某些系数。
例如,在开发阶段,确定产品A和B的剂量规定可能太早。
因此建议使用体积计算以确定正常运行时设备的处理容量。
其中:MCL = 最大残留限值(mg/L)ADI = 每日允许摄入量(mg)矩形设备的容积=长x 宽x 深(cm3)圆柱形设备的容积=圆形面积x 深(cm3)圆锥形设备(如V型混合器)的容积=圆形面积x 深/3(cm3)SSA = 用于生产产品A和B的设备的共用表面积(cm2)务必认识到此系数的推导,是假设所有产品残留体积均匀分布在设备的共用表面积。
清洁验证要求

设备清洁后无可见残留(包括所有类别的外来物质:如水、试剂、溶剂、化学物质
等)。
•
活性成分残留水平
针对制剂产品
活性成分的接受标准应根据前一产品的药理活性、毒性以及其他的潜在污染因素确
定。常用的方法有以下3种:一般标准、基于日治疗量的计算标准、基于毒性数据的计算
标准。其中一般标准和基于日治疗量的计算标准较为常用,也可以采取从其中选择最严格
如果使用非专属性的测试方法如总有机碳法、电导率法或紫外吸收法,应证明结果与
专属方法的测试结果等效或者采用最差条件对结果进行评估(例如:使用总有机碳法测量
淋洗液中活性成分残留含量时,无法区分测试到的碳来自前一产品活性成分、辅料还是清
洁剂。这种情况下,最差条件意味着,测试出的总有机碳全部认为来自于前一产品的活性
取样和分析方法。
分析方法验证内容详见“质量控制系统指南”。
残留量[mg/m2]应按照下列公式进行修正计算:
RP x RF
X = ^ F ~
X
残留量(修正值)
AP
取样面积
RP
样品中检出的残留量(测量值)
RF
回收因子
( 7 )分组概念(Bracketing Concept)
3产品质量实现的要素
同一个清洁程序可能会应用在不同的产品、工艺和设备上。在清洁验证时不必针对每
验证的目的;
•
执行和批准验证的人员职责;
參对所使用的设备的描述;
•
生产结束至开始清洁的时间间隔(待清洁放置时间);
•
每个产品、每个生产系统或每个设备所使用的清洁规程;
拳需连续执行的清洁循环的数量;
•
常规监测的要求;
參取样规程,包括选择特定取样方法所依据的原则;
清洁验证限度计算及方法学验证

药物研发完成小试研究以后,进入预中试或者中试生产阶段,这一阶段通常需要在药厂完成,并遵守GMP关于设备的使用和清洁要求,清洁符合标准的基本原则是证明清洁方法能够去除污染物或将污染降低至可接受的水平。
当单品种单独生产线时,只要目视洁净就可以,当多产品共线生产时,则需要考虑上一品种在下一品种中的残留,因为这些残留可能产生副反应或者毒副作用。
所以在进行清洁验证前要计算允许残留限度(即检验清洁是否合格的标准),有三个比较常用的计算残留的方法,分别是基于毒理的限度、基于浓度的10ppm的限度和基于最低日治疗剂量的千分之一的限度。
1、基于毒理的限度标准2、基于浓度的10ppm的限度标准3、基于最低日治疗剂量的千分之一的限度标准在计算清洁限度的时候需要注意所讨论产品的日标准治疗剂量(有效成分)和下一产品的日标准治疗剂量(制剂)的区别,例如某制剂规格2ml:200mg,日治疗剂量20mg/kg,成年标准体重50kg,那么日标准治疗剂量(有效成分)为20mg/kg×50kg=1000mg,日标准治疗剂量(制剂)为1000mg÷200mg×2ml=10g。
清洁限度确定以后,进行清洁方法验证,可根据《化学药物质量控制分析方法验证技术指导原则》和《中国药典2020年版》9101 分析方法验证指导原则等制定验证内容,验证指标主要包括专属性、检测限、定量限、线性与范围、仪器精密度、重复性、中间精密度、准确度、溶液稳定性和耐用性。
1.溶液配制:1.1空白溶液:水1.2空白棉签溶液:取2个棉签放入具塞试管中,精密加入水10ml,密封,超声10分钟,取超声后溶液过滤即得。
1.3对照品溶液:精密称取xxxx对照品xxmg,置100ml量瓶中,加水溶解并稀释至刻度,摇匀,作为擦拭限度对照品溶液。
1.4供试品溶液:精密称取xxxx(含量约为100%)约xxmg,置于100ml量瓶中,加水溶解并稀释至刻度,摇匀,在10*10cm的区域均匀涂布0.5ml,待溶剂挥干后,用2个棉签擦拭,每个棉签分别先横向蛇形擦拭,再翻转棉签纵向蛇形擦拭,之后将2根擦拭棉签放入具塞试管中,精密加入水10ml,密封,超声10分钟,取超声后溶液过滤即得。
ASTM新发布指南:清洁验证限度计算

ASTM新发布指南:清洁验证限度计算今年5⽉,ASTM发布了E3219-20指南:基于健康的接触限值(HBEL)的推导,描述了如何计算基于健康的接触限值(HBEL),适⽤于确定清洁验证和清洁确认过程中API和其它物质的残留。
新发布指南中概述的程序,有望极⼤地帮助专业⼈⼠推导可接受的残留⽔平,结合使⽤ASTM E3106 :基于科学和基于风险的清洁⼯艺开发标准指南,可以系统性实现对清洁⼯艺进⾏风险评估和验证。
该指南的发布,反映了监管机构和⾏业对HBEL的系统性思考,让我们⼀起看看该指南诞⽣的故事:FDA 1996年对GMP的修订建议事情可以追溯到Barr Labs法院案件,该案件在1996年GMP中起着重要作⽤,推动Risk-MaPP指南的开发。
简单说,FDA对Barr Laboratories,Inc.的多次检查有很多共同的观察项,结果是双⽅诉诸于法庭。
阿尔弗雷德·沃林法官在判决中认为,FDA对Barr Laboratories的所有主张都是有根据的,并同意按照GMP要求,需要进⾏⼯艺验证和清洁验证。
Barr Labs案件的决定适⽤于整个⾏业。
但同时,沃林法官还批评了GMP含糊不清。
FDA回应了沃林法官的批评,在1996年提出了对先前建⽴的GMP进⾏变更的建议。
在这些拟议的变更中,FDA规定,除青霉素外,某些化合物,包括“细胞毒性剂或其他抗⽣素...”,也需要在专⽤设施中⽣产。
在提议的变更序⾔中,FDA指出:“FDA希望⽣产商识别出存在风险的任何药物。
FDA认识到,根据药品的不同,可以采取多种措施来消除交叉污染;但是,在某些情况下,可能只有专门的设施才能消除交叉污染。
”⾏业在满⾜潜在的专⽤设施要求⽅⾯,遇到了许多困难。
使这个问题更加复杂的是,许多公司已经发现,⽆法执⾏由Fourman和Mullen在1993年发表的清洁验证限值标准(即治疗剂量的1 / 1000,不超过10ppm)。
如果清洁程序⽆法减少残留,以满⾜这样的低限值,那么即使对于低风险产品,也可能需要考虑使⽤专⽤设备。
pde计算清洁验证限度公式

pde计算清洁验证限度公式PDE是数学中的一个重要分支,广泛应用于物理、工程、生物等领域的建模和计算中。
它描述了多个变量之间的关系以及其随时间和空间的变化规律。
在实际应用中,PDE常常需要通过数值方法进行求解,例如有限差分法、有限元法等。
在使用PDE进行计算时,为了保证计算结果的准确性,需要满足清洁验证限度公式。
这是因为PDE的求解过程中存在着离散误差和截断误差,而这些误差会对计算结果产生一定的影响。
为了控制这些误差,需要设定一定的限度条件,以保证计算结果的可靠性。
清洁验证限度公式通常包括以下几个方面的限度条件:1. 空间步长限度:空间步长是指在离散化求解PDE时,将空间进行划分的间隔大小。
较小的空间步长可以提高计算的精度,但也会增加计算的复杂度和计算时间。
因此,需要设定合适的空间步长限度,以确保计算结果的准确性和计算效率的平衡。
2. 时间步长限度:时间步长是指在离散化求解PDE时,将时间进行划分的间隔大小。
与空间步长类似,较小的时间步长可以提高计算的精度,但也会增加计算的复杂度和计算时间。
因此,需要设定合适的时间步长限度,以确保计算结果的准确性和计算效率的平衡。
3. 稳定性限度:稳定性是指在PDE的求解过程中,解的振荡是否会随时间的推进而不断增强。
如果解的振荡增强,会导致计算结果的不稳定性。
因此,需要设定一定的稳定性限度,以确保计算结果的稳定性。
4. 收敛性限度:收敛性是指在离散化求解PDE时,当空间步长和时间步长趋于无穷小时,数值解是否能够逼近真实解。
为了保证计算结果的准确性,需要设定一定的收敛性限度,以确保数值解能够逼近真实解。
通过设定合适的空间步长限度、时间步长限度、稳定性限度和收敛性限度,可以有效地控制离散误差和截断误差,从而保证PDE计算结果的准确性和可靠性。
此外,在具体应用中,还可以根据实际需求和计算资源的限制进行适当的调整,以达到最佳的计算效果。
PDE计算清洁验证限度公式是为了保证PDE计算结果的准确性和可靠性所设定的一定限度条件。
计算方法

清洁验证残留限度的计算
根据GMP 实施指南和相关要求,我们控制原料药(乙酰螺旋霉素)残留限度的计算依据如下:
计算方法:10ppm 法、日剂量的千分之一、下批批量的0.1%(基于低毒性原料的杂质限度标准)
1、10ppm 法:乙酰螺旋霉素批量为260kg ,因残留物浓度最高为10*10-6,即10mg/kg ,则残留物总量最大为:260*10*10-6=2600mg 。
则设备内表面残留物允许的限度为:
222600100010010%70%89.710000
g A cm m ⨯=⨯⨯⨯⨯残留限量(保险系数)(取样回收率) =20.31㎎/100㎝2
残留限度定为:20.31㎎/100㎝2/25ml=0.8124mg/ml 2、日剂量的千分之一:由于原料药生产清洁后用于生产药用辅料(醋酸钠),其为无活性物质,因此暂无法用此公式计算。
3、下批批量的0.1%(基于低毒性原料的杂质限度标准)
原料药(乙酰螺旋霉素)的最小批产量为260㎏,下批批量的0.1%,则乙酰螺旋霉素最大残留物为260g 。
擦拭测试:擦拭面积以10㎝×10㎝的区域计
(取样回收率)(保险系数)残留限量%70%1010010000
7.89100026022⨯⨯⨯⨯⨯=cm m g A =2.03㎎/100㎝2
残留限度定为:2.03㎎/100㎝2/25ml=0.081mg/ml
根据比较,上述计算方法限度最低的为计算方法3【下批批量的0.1%(基于低毒性原料的杂质限度标准)】,从清洁风险控制角度分析,我们以3的残留限度为可接受限度。
清洁验证合格限度计算

复方氨基酸注射液生产清洁验证残留限度推算以10 ppm为标准计算单位面积的残留量。
假设残留物均匀分布在设备内表面。
计算过程10 ppm =10 μg/ml ≅ 10 mg/kg某产品日常生产最小批量:2500L ≅ 2500kg 每批产品生产接触总面积S= 20m2,(配制系统 19 m2和灌封机1 m2)每批总残留量(产品中所有氨基酸组分残留到下批产品中的总量):=10 mg/kg x 2500 kg=25000 mg单位面积残留量限度:=25000 mg/20m2=1250 mg/m2=12.5 mg/100cm2取安全因子F=10,最后的残留限度=1.25 mg/100cm2氯雷他定片剂生产清洁验证残留限度推算以最低日治疗剂量的1/1000为标准计算单位面积的残留量。
假设残留物均匀分布在设备内表面。
最小批量:10kg最低日治疗剂量(MTDD)=每天最少给药片数x含量/片(mg)=1片x10mg/片=10mg每天最大服用量 (LDSD)=每天最多给药片数x重量/片(mg)=1片x87mg/片=87mg相关设备内表面积9制粒机:8000cm29烘干机:50000cm29整粒机:1000cm29V形终混机:10000cm29压片机:1000cm2设备总表面积:70000cm2计算过程产品残留允许的最低限度= MTDD (mg) x 1/1000 x 1/LDSD(mg) = 10x10-3(mg)/87(mg)换算成每公斤B产品中A产品残留量=10x10-3x106(mg)/87(kg)=104(mg)/87(kg)下批最小批量为10(kg),则活性物质总残留量=104(mg)/87(kg)*10(kg)=105/87(mg)因生产设备总面积为70000(cm2),则单位面积残留限度L =105/87(mg)/70000(cm2)=1.64mg/100cm2。
清洁验证及其残留限度计算培训 N

� 评分方式1:MACO值
MACO值 得分
10-99.9 4分
100-999.9 3分
1000-9999.9 2分
≥10000 1分
� 评分方式2: MACO值的倒数
� 适用于MACO值特别小时
MACO值或其倒数的取值范围: 根据各车间所有品种评估后 确定的,没有明确的规定具体
MACO值的倒数 1-999.9
S-----上批产品与下批产品共用设备累计接触面积,cm2
先生产A产品,再生产B产品
� 计算公式三 �3 S
� MBS NOEL � S TDD SF
�SBS kg kg g LD next �S�LDSD SF
R3---------单位面积上残留物允许限度,mg/cm2
• 溶解度
• 活性/毒性
同一台设备生产 不同品种的产品 同一清洁程序
� 评价标准
将各品种分别按三个评价项目进行评分�将三个数字相乘�清洁难 易程度、溶解度和MACO值或MACO值的倒数��乘积最大的产品就是要 验证的产品。
� 评估---多标准分析
� 清洁难易程度
• 每个产品按生产操作工在生产此类产品结束后�清洁使用过的设 备所遇到的困难程度分为4级�
SF----安全系数�一般取1000
S-----上批产品A与下批产品B共用设备累计接触面积,cm2
先生产A产品,再生产B产品
� 计算公式二、基于日治疗剂量的1/1000
R� 其中�
SBS L 2S
� �2 SBS D B A S SF�
��
min
/SBS
MTDD� �6
S LDSD SF
R2----单位面积上残留物允许限度,mg/cm2
- 1、下载文档前请自行甄别文档内容的完整性,平台不提供额外的编辑、内容补充、找答案等附加服务。
- 2、"仅部分预览"的文档,不可在线预览部分如存在完整性等问题,可反馈申请退款(可完整预览的文档不适用该条件!)。
- 3、如文档侵犯您的权益,请联系客服反馈,我们会尽快为您处理(人工客服工作时间:9:00-18:30)。
复方氨基酸注射液生产
清洁验证残留限度推算
以10 ppm为标准计算单位面积的残留量。
假设残留物均匀分布在设备内表面。
计算过程
10 ppm =10 μg/ml ≅ 10 mg/kg
某产品日常生产最小批量:2500L ≅ 2500kg 每批产品生产接触总面积S= 20m2,(配制系统 19 m2和灌封机1 m2)
每批总残留量(产品中所有氨基酸组分残留到下批产品中的总量):
=10 mg/kg x 2500 kg
=25000 mg
单位面积残留量限度:
=25000 mg/20m2
=1250 mg/m2
=12.5 mg/100cm2
取安全因子F=10,
最后的残留限度=1.25 mg/100cm2
氯雷他定片剂生产
清洁验证残留限度推算
以最低日治疗剂量的1/1000为标准计算单位面积的残留量。
假设残留物均匀分布在设备内表面。
最小批量:10kg
最低日治疗剂量(MTDD)
=每天最少给药片数x含量/片(mg)
=1片x10mg/片=10mg
每天最大服用量 (LDSD)
=每天最多给药片数x重量/片(mg)
=1片x87mg/片=87mg
相关设备内表面积
9制粒机:8000cm2
9烘干机:50000cm2
9整粒机:1000cm2
9V形终混机:10000cm2
9压片机:1000cm2
设备总表面积:70000cm2
计算过程
产品残留允许的最低限度
= MTDD (mg) x 1/1000 x 1/LDSD(mg) = 10x10-3(mg)/87(mg)
换算成每公斤B产品中A产品残留量=10x10-3x106(mg)/87(kg)
=104(mg)/87(kg)
下批最小批量为10(kg),
则活性物质总残留量
=104(mg)/87(kg)*10(kg)
=105/87(mg)
因生产设备总面积为70000(cm2),则单位面积残留限度
L =105/87(mg)/70000(cm2)
=1.64mg/100cm2。