多晶铸锭生产工艺文件
多晶铸锭生产工艺文件
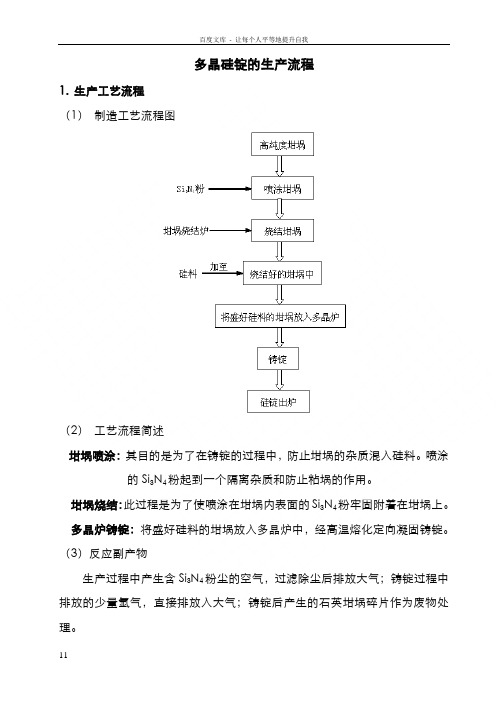
多晶硅锭的生产流程1.生产工艺流程(1)制造工艺流程图(2)工艺流程简述坩埚喷涂:其目的是为了在铸锭的过程中,防止坩埚的杂质混入硅料。
喷涂的Si3N4粉起到一个隔离杂质和防止粘埚的作用。
坩埚烧结:此过程是为了使喷涂在坩埚内表面的Si3N4粉牢固附着在坩埚上。
多晶炉铸锭:将盛好硅料的坩埚放入多晶炉中,经高温熔化定向凝固铸锭。
(3)反应副产物生产过程中产生含Si3N4粉尘的空气,过滤除尘后排放大气;铸锭过程中排放的少量氩气,直接排放入大气;铸锭后产生的石英坩埚碎片作为废物处理。
多晶铸锭操作流程1目的为了保证正确操作多晶硅铸锭炉,使铸锭过程规范、有效地进行,并确保铸锭成功。
2适用范围多晶铸锭车间3规范性引用文件无4职责生产部负责铸锭的整个过程。
工厂工程部负责整个外围设施条件,以保证多晶炉正常运行的环境条件要求。
5 术语和定义坩埚喷涂:在坩埚的内表面均匀喷涂Si3N4粉溶液,以防止在铸锭时坩埚和硅锭烧结在一起。
其目的是为了在铸锭过程中,防止坩埚内的杂质扩散入硅锭。
喷涂Si3N4粉起到了一个隔离杂质和防止粘埚的作用。
涂层烧结:此过程是为了使喷涂在坩埚内表面的Si3N4涂层牢固地附着在坩埚上。
多晶炉铸锭:将硅料放入坩埚,并一起放入多晶炉中,硅料经高温熔化、定向凝固成为硅锭。
定向凝固:在梯度热场中,液体朝一个方向凝固,固液界面近似于平面的凝固过程。
6 多晶炉工艺过程准备石英坩埚检查石英坩埚表面,不能有裂纹,内部不能有超过2mm的划痕、凹坑、突起。
6.1.1 用压缩空气和去离子水清洁坩埚的内表面。
6.1.2 坩埚喷涂:取250g的Si3N4粉末,用滤网筛滤。
然后取1000ml的去离子水,将Si3N4粉末溶解到去离子水中,用气动搅拌泵搅拌均匀。
喷涂时喷枪要距离坩埚内壁30cm左右,只喷涂坩埚底部和侧壁3/4的地方,要均匀不要使液体凝聚。
喷涂过程中要检测坩埚内表面的温度,应为80±5℃,不断用去油的压缩空气吹去掉落的颗粒。
多晶铸锭工艺流程
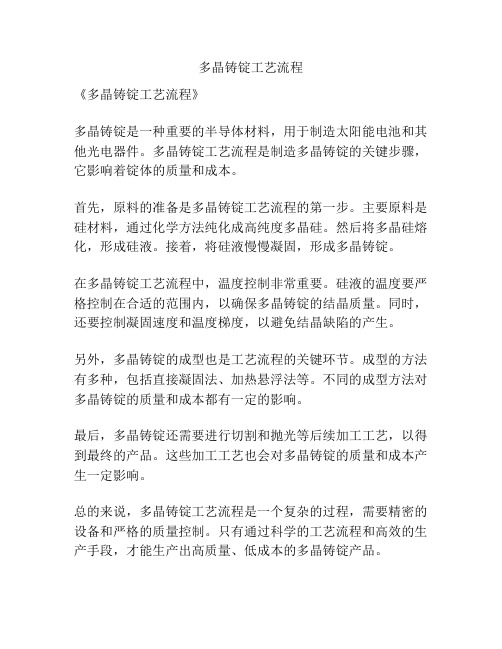
多晶铸锭工艺流程
《多晶铸锭工艺流程》
多晶铸锭是一种重要的半导体材料,用于制造太阳能电池和其他光电器件。
多晶铸锭工艺流程是制造多晶铸锭的关键步骤,它影响着锭体的质量和成本。
首先,原料的准备是多晶铸锭工艺流程的第一步。
主要原料是硅材料,通过化学方法纯化成高纯度多晶硅。
然后将多晶硅熔化,形成硅液。
接着,将硅液慢慢凝固,形成多晶铸锭。
在多晶铸锭工艺流程中,温度控制非常重要。
硅液的温度要严格控制在合适的范围内,以确保多晶铸锭的结晶质量。
同时,还要控制凝固速度和温度梯度,以避免结晶缺陷的产生。
另外,多晶铸锭的成型也是工艺流程的关键环节。
成型的方法有多种,包括直接凝固法、加热悬浮法等。
不同的成型方法对多晶铸锭的质量和成本都有一定的影响。
最后,多晶铸锭还需要进行切割和抛光等后续加工工艺,以得到最终的产品。
这些加工工艺也会对多晶铸锭的质量和成本产生一定影响。
总的来说,多晶铸锭工艺流程是一个复杂的过程,需要精密的设备和严格的质量控制。
只有通过科学的工艺流程和高效的生产手段,才能生产出高质量、低成本的多晶铸锭产品。
多晶铸锭工艺流程
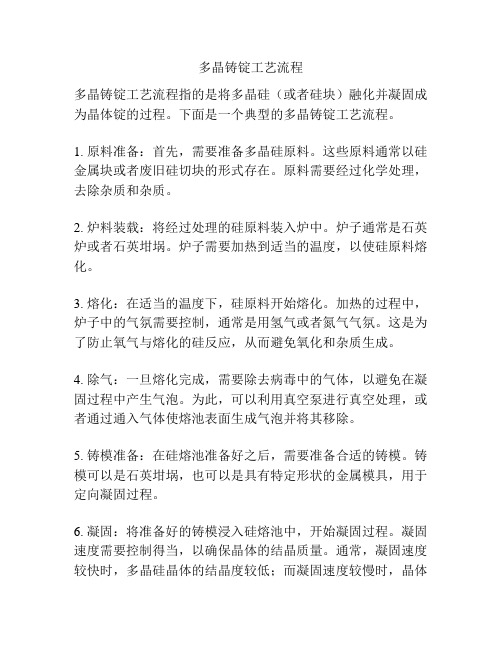
多晶铸锭工艺流程多晶铸锭工艺流程指的是将多晶硅(或者硅块)融化并凝固成为晶体锭的过程。
下面是一个典型的多晶铸锭工艺流程。
1. 原料准备:首先,需要准备多晶硅原料。
这些原料通常以硅金属块或者废旧硅切块的形式存在。
原料需要经过化学处理,去除杂质和杂质。
2. 炉料装载:将经过处理的硅原料装入炉中。
炉子通常是石英炉或者石英坩埚。
炉子需要加热到适当的温度,以使硅原料熔化。
3. 熔化:在适当的温度下,硅原料开始熔化。
加热的过程中,炉子中的气氛需要控制,通常是用氢气或者氮气气氛。
这是为了防止氧气与熔化的硅反应,从而避免氧化和杂质生成。
4. 除气:一旦熔化完成,需要除去病毒中的气体,以避免在凝固过程中产生气泡。
为此,可以利用真空泵进行真空处理,或者通过通入气体使熔池表面生成气泡并将其移除。
5. 铸模准备:在硅熔池准备好之后,需要准备合适的铸模。
铸模可以是石英坩埚,也可以是具有特定形状的金属模具,用于定向凝固过程。
6. 凝固:将准备好的铸模浸入硅熔池中,开始凝固过程。
凝固速度需要控制得当,以确保晶体的结晶质量。
通常,凝固速度较快时,多晶硅晶体的结晶度较低;而凝固速度较慢时,晶体的结晶度较高。
此外,凝固过程中,温度和气氛的控制也非常关键。
7. 破模:当多晶硅晶体完全凝固之后,需要将其从铸模中取出。
这通常需要用机械工具或者化学方法进行破模。
在破模过程中,需要小心操作,以避免对晶体造成损害。
8. 切割:一旦晶体从铸模中取出,需要将其切割成合适的尺寸。
这可以用钻石工具进行切割,切割后得到的是硅片。
硅片的尺寸和厚度可以根据需要进行调节。
9. 清洗:最后,需要对切割好的硅片进行清洗和去除杂质。
这是为了确保硅片的纯净度和表面平整度。
综上所述,多晶铸锭工艺流程是一个涉及熔化、除气、凝固、破模、切割和清洗等多个步骤的复杂过程。
不同的工艺参数和条件将直接影响到多晶硅晶体的质量和晶格结构。
因此,精确控制每个步骤是非常重要的,以确保最终产品的质量和性能。
多晶硅铸锭工艺流程

2、实验方法
图2-1高效晶硅铸锭工艺流程
➢铸锭:G 6型 810Kg ➢坩埚尺寸:890×890×480mm3 ➢母合金:硼
3、铸锭车间生产流程
3.1 涂层工序
1、准备石英坩埚 检查石英坩埚表面,应干净无污染且无裂纹,内部不能有
3.2装料工序
多晶硅块(chunk)料 碎块(fines)
硅颗粒
电阻率测试仪
硅粉
头料
边料
尾料
碎片 单晶边皮料 单晶头料
PN型测试仪
1、备料
对多晶硅的原硅料和回收料使用PN测试仪和电阻率进行分档 分类,直到达到配比质量,最后计算出需要的掺杂剂质量。
2、装料
a、选取边料垫于坩埚底部
b、将碎片置于边料之上
4、硅锭项目检测
电阻率
1.5
1.45
1.4
1.35
1.3
1.25
1.2 10%尾
20%
30%
40%
50%
60%
70%
80%
90%
典型的电阻率分布呈现出上述的变化趋势,尾高头 低。主要是因为所添加的母合金的分凝系数造成的, 检测硅锭中的电阻率是否出现异常。
少子寿命分布状况
检验硅方的边部和底部红区长度和硅锭整体的少子寿 命。
其作用与退火一样重要,直接影响硅锭的性能。
注意事项
在熔化和长晶阶段工会出现熔化、中间长晶和边部长晶 三次报警。在铸锭循环过程中,这两个阶段需予以密切关 注。
当炉内压力低于980mbar时,需要对炉子进行充气。回填 操作时炉内压力大于这一数值时没有自动停止,需自动停 止。
铸锭过程中根据炉内出现不同情况手动调整,如适当延 长长晶时间等。注意炉内的水电、气压。
多晶铸锭生产过程
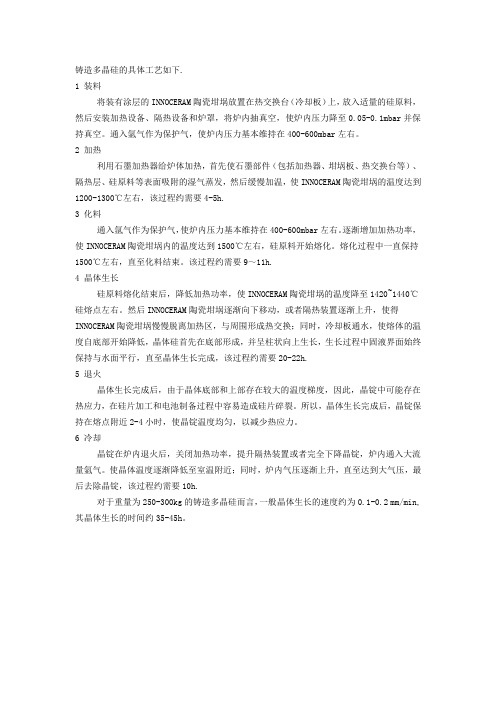
铸造多晶硅的具体工艺如下.1 装料将装有涂层的INNOCERAM陶瓷坩埚放置在热交换台(冷却板)上,放入适量的硅原料,然后安装加热设备、隔热设备和炉罩,将炉内抽真空,使炉内压力降至0.05-0.1mbar并保持真空。
通入氩气作为保护气,使炉内压力基本维持在400-600mbar左右。
2 加热利用石墨加热器给炉体加热,首先使石墨部件(包括加热器、坩埚板、热交换台等)、隔热层、硅原料等表面吸附的湿气蒸发,然后缓慢加温,使INNOCERAM陶瓷坩埚的温度达到1200-1300℃左右,该过程约需要4-5h.3 化料通入氩气作为保护气,使炉内压力基本维持在400-600mbar左右。
逐渐增加加热功率,使INNOCERAM陶瓷坩埚内的温度达到1500℃左右,硅原料开始熔化。
熔化过程中一直保持1500℃左右,直至化料结束。
该过程约需要9~11h.4 晶体生长硅原料熔化结束后,降低加热功率,使INNOCERAM陶瓷坩埚的温度降至1420~1440℃硅熔点左右。
然后INNOCERAM陶瓷坩埚逐渐向下移动,或者隔热装置逐渐上升,使得INNOCERAM 陶瓷坩埚慢慢脱离加热区,与周围形成热交换;同时,冷却板通水,使熔体的温度自底部开始降低,晶体硅首先在底部形成,并呈柱状向上生长,生长过程中固液界面始终保持与水面平行,直至晶体生长完成,该过程约需要20-22h.5 退火晶体生长完成后,由于晶体底部和上部存在较大的温度梯度,因此,晶锭中可能存在热应力,在硅片加工和电池制备过程中容易造成硅片碎裂。
所以,晶体生长完成后,晶锭保持在熔点附近2-4小时,使晶锭温度均匀,以减少热应力。
6 冷却晶锭在炉内退火后,关闭加热功率,提升隔热装置或者完全下降晶锭,炉内通入大流量氩气。
使晶体温度逐渐降低至室温附近;同时,炉内气压逐渐上升,直至达到大气压,最后去除晶锭,该过程约需要10h.对于重量为250-300kg的铸造多晶硅而言,一般晶体生长的速度约为0.1-0.2 mm/min,其晶体生长的时间约35-45h。
多晶铸锭工艺指导书

工艺指导书 NXRJ-MC450/500
3.4.4、热区检修与炉室清理:热区检修与炉室清理必需由专业人员操作。每 炉均需检修热区,清理炉室。准备好无尘纸、酒精、软刷、吸尘器及可能需 要的配件,如石黑螺栓、螺帽等。
① 专业检修人员检修热区:首先检测螺丝有无松动,螺栓有无断折,松 动的要及时扭紧,断的要及时更换;而后检测相应加热件的连接性以及其与 石墨纤板及炉体的电绝缘性,一般要求绝缘阻抗大于 2K 欧,最小不能低于 1 K 欧。若加热件上有颗粒物和脱落物以及其它杂物,需用吸尘器及时除去, 吸不去的先用软刷刷一刷,而后再用吸尘器吸;若隔热笼上有杂质,也应及 时用吸尘器除去,吸不去的先用软刷刷一刷,而后再用吸尘器吸。
⑥、用吸尘器对坩埚边缘的硅料粉尘进行清洁。
4.5 注意事项: 4.5.1、装料时,小心硅料的尖角划破手指,必须慢慢地平铺硅料,切勿将 - 13 -
工艺指导书 NXRJ-MC450/500
硅料扔投坩埚内。 4.5.2、安装石墨板时,注意石墨板与坩埚四周的间隙,应保持 2-3mm 的距 离,防止高温下坩埚膨胀导致石墨螺栓断裂。 5 进炉 5.1 目的:将装满原料的坩埚,准确、平稳的放置到炉内交换快上。 5.2 物料:装好料的坩埚、无尘纸、酒精、真空油脂。
③ 大块料放置于坩埚靠底部中间,但注意 这些硅料之间要存在空隙,要与坩埚内壁保持
- 12 -
工艺指导书 NXRJ-MC450/500
5-7cm 的间隙,且大块料不能放在坩埚四个角落, 避免发生膨胀时损坏坩埚;待平铺完一层硅料后 就用碎硅料填充大料之间的空隙;待碎硅料填充 完空隙后,又在上面平铺一层大块料,间隙再用 碎料填充,一层一层向上装料。
1.6.2、备料:准备好 400g Si3N4 粉末和 1600ml 纯水。Si3N4 粉末称好后,用细网(100 目) 进行过筛,将 Si3N4 粉末和纯水放入烘箱进行 烘烤,烘箱温度维持在 50℃左右,烘烤时间 15 分钟左右。
多晶硅锭制备-铸锭多晶硅工艺

铸锭多晶硅在光伏产业中的应用案例
总结词
铸锭多晶硅在光伏产业中得到了广泛应 用,其高效、低成本的优势为光伏产业 的发展提供了有力支持。
VS
详细描述
铸锭多晶硅作为一种高效的光伏材料,在 光伏产业中得到了广泛应用。其具有较高 的光电转换效率和稳定性,能够满足各种 应用场景的需求。同时,铸锭多晶硅的生 产成本相对较低,有利于降低光伏发电的 成本,促进光伏产业的可持续发展。
02
多晶硅锭制备的原料与设备
原料选择与准备
01
02
03
硅源
选择纯度高的工业硅作为 原料,确保硅锭的质量和 纯度。
清洗
对原料进行清洗,去除表 面的杂质和污染物,保证 硅锭的纯净度。
破碎与筛分
将大块工业硅破碎成小块, 并进行筛分,以便于后续 的熔炼和铸锭。
设备配置与使用
熔炼炉
熔炼炉是制备多晶硅锭的 核心设备,用于将破碎筛 分后的工业硅熔化成硅液。
定期保养
按照设备保养要求,对设备进行定期 保养,延长设备使用寿命。
03
多晶硅锭制备的工艺参数
温度控制
熔化温度
熔化温度是制备多晶硅锭的关键参数,它决定了硅材料的纯度和结晶质量。熔 化温度过高会导致硅材料氧化和杂质混入,而温度过低则会导致硅材料无法完 全熔化。
结晶温度
结晶温度是多晶硅锭制备过程中的重要参数,它决定了硅材料的结晶结构和晶 粒大小。结晶温度过低会导致晶粒过小,而温度过高则会导致晶粒过大,影响 多晶硅锭的质量。
06
多晶硅锭制备的案例分析
某公司多晶硅锭制备工艺流程优化案例
总结词
该公司通过对多晶硅锭制备工艺流程的优化,提高了生产效率和产品质量,降低了能耗和生产成本。
单晶多晶铸锭工艺流程

单晶多晶铸锭工艺流程下载温馨提示:该文档是我店铺精心编制而成,希望大家下载以后,能够帮助大家解决实际的问题。
文档下载后可定制随意修改,请根据实际需要进行相应的调整和使用,谢谢!并且,本店铺为大家提供各种各样类型的实用资料,如教育随笔、日记赏析、句子摘抄、古诗大全、经典美文、话题作文、工作总结、词语解析、文案摘录、其他资料等等,如想了解不同资料格式和写法,敬请关注!Download tips: This document is carefully compiled by theeditor. I hope that after you download them,they can help yousolve practical problems. The document can be customized andmodified after downloading,please adjust and use it according toactual needs, thank you!In addition, our shop provides you with various types ofpractical materials,such as educational essays, diaryappreciation,sentence excerpts,ancient poems,classic articles,topic composition,work summary,word parsing,copy excerpts,other materials and so on,want to know different data formats andwriting methods,please pay attention!单晶多晶铸锭工艺流程一、准备工作阶段在进行单晶多晶铸锭的工艺流程之前,需要进行一系列准备工作。
- 1、下载文档前请自行甄别文档内容的完整性,平台不提供额外的编辑、内容补充、找答案等附加服务。
- 2、"仅部分预览"的文档,不可在线预览部分如存在完整性等问题,可反馈申请退款(可完整预览的文档不适用该条件!)。
- 3、如文档侵犯您的权益,请联系客服反馈,我们会尽快为您处理(人工客服工作时间:9:00-18:30)。
多晶硅锭的生产流程1. 生产工艺流程(1) 制造工艺流程图(2) 工艺流程简述坩埚喷涂:其目的是为了在铸锭的过程中,防止坩埚的杂质混入硅料。
喷涂的Si 3N 4粉起到一个隔离杂质和防止粘埚的作用。
坩埚烧结:此过程是为了使喷涂在坩埚内表面的Si 3N 4粉牢固附着在坩埚上。
多晶炉铸锭:将盛好硅料的坩埚放入多晶炉中,经高温熔化定向凝固铸锭。
(3)反应副产物生产过程中产生含Si 3N 4粉尘的空气,过滤除尘后排放大气;铸锭过程中排放的少量氩气,直接排放入大气;铸锭后产生的石英坩埚碎片作为废物处理。
多晶铸锭操作流程1 目的为了保证正确操作多晶硅铸锭炉,使铸锭过程规范、有效地进行,并确保铸锭成功。
2 适用范围多晶铸锭车间3 规范性引用文件无4 职责4.1 生产部负责铸锭的整个过程。
4.2 工厂工程部负责整个外围设施条件,以保证多晶炉正常运行的环境条件要求。
5 术语和定义5.1 坩埚喷涂:在坩埚的内表面均匀喷涂Si 3N 4粉溶液,以防止在铸锭时坩埚和硅锭烧结在一起。
其目的是为了在铸锭过程中,防止坩埚内的杂质扩散入硅锭。
喷涂Si 3N 4粉起到了一个隔离杂质和防止粘埚的作用。
5.2 涂层烧结:此过程是为了使喷涂在坩埚内表面的Si 3N 4涂层牢固地附着在坩埚上。
5.3 多晶炉铸锭:将硅料放入坩埚,并一起放入多晶炉中,硅料经高温熔化、定向凝固成为硅锭。
5.4 定向凝固:在梯度热场中,液体朝一个方向凝固,固液界面近似于平面的凝固过程。
6 多晶炉工艺过程6.1 准备石英坩埚检查石英坩埚表面,不能有裂纹,内部不能有超过2mm 的划痕、凹坑、突起。
6.1.1 用压缩空气和去离子水清洁坩埚的内表面。
6.1.2 坩埚喷涂:取250g 的Si 3N 4粉末,用滤网筛滤。
然后取1000ml 的去离子水,将Si 3N 4粉末溶解到去离子水中,用气动搅拌泵搅拌均匀。
喷涂时喷枪要距离坩埚内壁30cm 左右,只喷涂坩埚底部和侧壁3/4的地方,要均匀不要使液体凝聚。
喷涂过程中要检测坩埚内表面的温度,应为80±5℃,不断用去油的压缩空气吹去掉落的颗粒。
6.1.3 将坩埚放在烧结炉中进行烘烤。
设定程序,用10分钟升到40℃,然后用6小时升到1000℃,在1070℃保温2∽3小时,然后等坩埚冷却后待用。
6.2 填料将坩埚放在石墨板上,并一起放在磅秤上称量(磅秤必须归零)。
要保证坩埚处于石墨板的中央,距石墨板周围4.3cm 左右,误差不得超过2mm 。
向坩埚中填料240kg 左右。
(特别注意:在填料的过程中尽量少走动,以免扬起灰尘)。
6.3 外围设施基本条件的准备6.3.1 启动设备前,检查水、电、气。
冷却水、气、电源检查没有问题后,方可进行。
6.3.2 密切监视室内的温度和湿度,冷却水进水温度25±1℃,室温下相对湿度不超过65%。
6.3.3 冷却水进水压力在0.3∽0.4MPa之间,冷却回水压力小于(冷却水进水压力-0.26MPa),冷却水的流量总和在120—140LPM,需经常检查水流量计的情况,以防有阻塞的情况发生。
6.3.4 进气压力范围为0.2±0.03MPa。
6.3.5 检查安全阀的位臵是否放正,避免安全阀漏气。
检查下炉腔的“O”型密封圈和表面是否清洁,不能有灰尘。
6.3.6 检查真空泵(含机械泵和罗茨泵),包括电源、泵油、运转情况等。
6.3.7 确认电控柜正常供电。
6.3.8 确定压缩空气的压力为0.5MPa,指针处于表的正中央位臵。
6.3.9 调节冷却回水的阀门,使8根冷却回水的流量分别为:F1:(14±2)LPM (电极1)F2:(14±2)LPM (电极2)F3:(14±2)LPM (电极3)F4:(16±2)LPM (炉体上腔体和顶盖)F5:(18±2)LPM (炉体侧壁)F6:(42±3)LPM (炉体下腔和上部)F7:(35±2)LPM (炉体下腔和下部)F8:(9±2)LPM (机械泵和总阀)6.4 开始铸锭6.4.1 将装有硅料的坩埚放到定向凝固块上:注意:坩埚的位臵要处于定向凝固块块的正中央,距定向凝固块块周围的距离4.1cm左右,误差不要超过2mm(特殊交代除外)。
对炉子进行手动抽真空检漏。
确定绝热笼的位臵,其位臵是以腔体下边沿为零点。
铸锭开始前,校准隔热笼的位臵。
一般在未关机的情况下,绝热笼的位臵不需要校准。
调入程序:首先从“模式”下选择所需工艺配方,点击“确定工艺”,接着点击“执行/下载修改工艺”,然后点击“自动运行”,此时,系统进入“初始检查窗口”,则程序开始自动运行,进入自动运行阶段。
如果是手动模式下抽真空,应首先确认真空模式,然后用鼠标点击机械泵开关,此时机械泵开启。
当压强降到10mbar以下,罗茨泵自动开启,将压强降到0.01mbar(这个过程的时间大约1小时)。
当压强降到0.01mbar后,关掉总阀V1,在前5分钟,压强增加值小于0.008mbar,并记录随后4分钟增大的压强变化量。
如果检查漏气,则要排查漏气孔。
6.4.2 铸锭整个过程所需时间大约为50小时,其间,将会出现3次正常报警:(1)中央熔化报警:此时需要确认熔体中央是否完全熔化。
具体操作为:点击“报警消声”,再点击“继续熔化”。
然后去上面检查是否彻底熔化。
报警会在4分钟后再次响起,处理方法同上。
当报警响过3次后,再次报警,点击“进入下一步”,同时记录此次的具体时间。
中央熔化确认报警至少3次以上,如果中央没有完全熔化,而此时“熔化”将要结束,此时点击“保持”保持这一状态直至完全熔化。
(2)中央凝固报警:及时观察中央是否凝固,如果能看到液体,则点击“取消”,继续进行凝固,这个报警要响3次以上才能通过完成。
(3)边缘凝固报警:一般将报警取消,点击“延时”,使其继续走完,确保边缘完全凝固。
铸锭过程中,隔热笼只在“长晶”和“冷却”时会升起,其余的步骤隔热笼总是封闭的。
铸锭过程中应特别注意炉体温度,室内湿度,千万避免炉体出现冷凝水。
试验结束后,待温度(TC2)降到300℃以下,才可降下炉腔体,取出硅锭。
坩埚会自然裂开,不能直接接触,以免烫伤。
6.5 试验记录试验过程中一般1小时记录1次外围数据,特殊情况每隔半小时记录1次数据,包括:步骤、时间、剩余时间、设定温度、当前温度(TC1、TC2)、绝热笼的位臵、加热电压、电流、即时最大功率、平均功率、时间、冷却进水压力及温度、冷却回水压力及温度、F1-F8的流量、进气气压及(储罐)瓶压。
注意:整个过程中冷却水的温度,F1-F8的流量,千万不能阻塞;温度、湿度也要密切注意,并注意观察1175℃的功率曲线。
具体见“铸锭炉运行数据记录表”。
多晶铸锭工艺文件1 坩埚喷涂1.1 准备坩埚坩埚需无可见破损,内壁不可有污迹和明显划痕,如有,要用白洁布用力擦去,同时用去油压缩空气吹干。
将坩埚放入坩埚加热器中。
操作时要穿洁净服,防止人体的产物掉到或擦到坩埚上,同时防止粉尘吸入肺部。
1.2 配制溶液配制溶液采用250g 的Si 3N 4粉末对1000ml 的去离子水,不使用其它粘接剂。
使用前为防止结块,Si 3N 4粉末需使用80目左右尼龙筛网过滤。
整个喷涂时须防止同一位臵停留过久而使液体凝聚,喷涂须均匀,以防止涂层脱落。
喷涂的温度应控制在80±5℃,温度过低涂层起皮脱落,温度过高Si 3N 4粉末也容易脱落。
溶液配制好后,需用气动搅拌器高速搅拌2分钟。
使粉末颗粒分布均匀,然后低速搅拌,准备开始喷涂。
1.3 坩埚喷涂喷涂过程中特别注意喷扫时两端边沿的停留时间不可过长,过长停留时间容易导致边沿液体凝聚。
喷涂速度要保证涂层适当干燥,不起皮。
如果起皮或液体凝聚,要用油石将涂层全部刮去,用白洁布处理表面后,重新喷涂。
2 坩埚烧结烧结前先在加热器中烘干15分钟,放入烧结炉。
10分钟升温到40℃,然后用6小时线性升温到1000℃,在1000℃恒温3∽4小时,然后等坩埚自然冷却后待用。
烧结后如发现起皮,要将涂层全部刮去,用白洁布处理表面后,重新喷涂。
3 装料3.1 清洁液装料时要保证洁净度,尽量防止灰尘落入,人员应穿洁净服。
3.2 保护涂层装料是要小心、轻放,防止破坏Si 3N 4涂层。
3.3 正确摆放装块状料时,最下层摆放要疏松,防止膨胀过程中坩埚胀裂。
3.4 装料到一半时,按照计算出的量加入高硼硅掺杂:掺杂剂使用前要酸洗表面并干燥。
酸洗可先用HF:HNO 3的体积比1:4的溶液稍微抛光,然后用去离子水冲洗干净并干燥,化学试剂推荐使用电子级纯度,如用分析纯,一定要用去离子水多次冲洗。
3.5 上料整个装料和上料过程中,要保证坩埚处于石墨板的中央,石墨板要处于定向凝固块中央,误差都不可以超过5mm ,建议误差不超过2mm 。
4 铸锭工艺铸锭工艺分为五个主要阶段4.1 加热隔热笼下降到最低,真空状态下让硅料升温排出石墨件和硅料吸附的水汽和其它气体。
该过程为功率控制模式,加热器按照设定功率加热。
4.2 熔化加热到1175℃时通入保护气体—氩气,进入熔化步骤,迅速升温到熔化点以上,熔化开始。
从熔化开始进入温度控制模式,加热器按照TC1的设定温度反馈控制加热。
完全熔化后,由TC2或功率斜率微分触发熔化完成报警。
4.3 长晶隔热笼开始提升,定向凝固块开始把热量辐射到下炉壁,形成温度梯度,定向凝固开始。
中央结晶完成由光学高温计触发,边沿结晶完成由功率斜率触发。
4.4退火完全凝固后,隔热笼重新下降,使整个硅锭达到相同温度(1250—1300℃),高温退火减少位错和应力。
4.5冷却加热器停止工作,隔热笼缓慢升起,TC2冷却到300℃时整个过程结束。
可以开炉取锭。
具体每个阶段的详细步骤设定和时间,按48所提供的240kg和270kg 锭标准工艺执行。