轧钢高线设备
高线生产简介

高速线材生产设备
二、轧机
高线厂15#~28#均为旋臂式轧机,15#~18#轧机布置 形式为平立交替式,传动方式为单独传动。19#~28#布置形 式为顶角45度,传动方式为集体传动。各架次轧机规格如下:
架次 规格 15#~18# φ285 19#~23# φ228 24#~28# φ170
(3)加热质量好。完全消除了粘钢、翻炉的限制,很大程度上消除了 钢坯黑印,坯料下表面也不会造成划伤
(4)能耗低。由于采用蓄热式,废气排放时经过蓄热式,蓄热体将高 温废气的热量留下给换向后的空气和煤气预热,大大降低了能耗损失。
高速线材生产设备
一、加热炉
高速线材生产设备
二、轧机
高线厂1#~14#均为短应线轧机,轧机布置形式为平立 交替式。短应力线轧机和闭口式轧机相比具有投资少,刚度 大、更换方便的特点。各架次轧机规格如下:
(1)尽量实现钢坯热送。
(2)避免强制加热,加热能力不足时可适当待温。
(3)轧制节奏允许时加大步距,减少钢坯在炉内停 留时间。
高速线材生产工艺
二、加热
4、钢坯除鳞 国内线材生产线钢坯高 压水除鳞是近几年才投入使 用的,因为以前国内线材产 品大多为建筑用材,对表面 质量要求不严格,而且线材 粗轧都有几架箱型孔,有较 好的去除氧化铁皮的效果。 随着线材产品的不断升级, 对线材产品表面质量的要求 不断提高,国内新投产的生 产线都配备了高压水除鳞设 备。
高速线材生产工艺
二、加热
1、原料
线材的原料为小方坯,一般为150*150或 160*160的连铸小方坯,单支重量一般在2~2.5吨。 由于一部分冷墩钢和硬线拉丝用线材需要有较高的 致密度,所以有些钢厂也开始采用初轧坯来做高线 的原料。
利用国产设备完成棒材、高线材轧制生产线设计
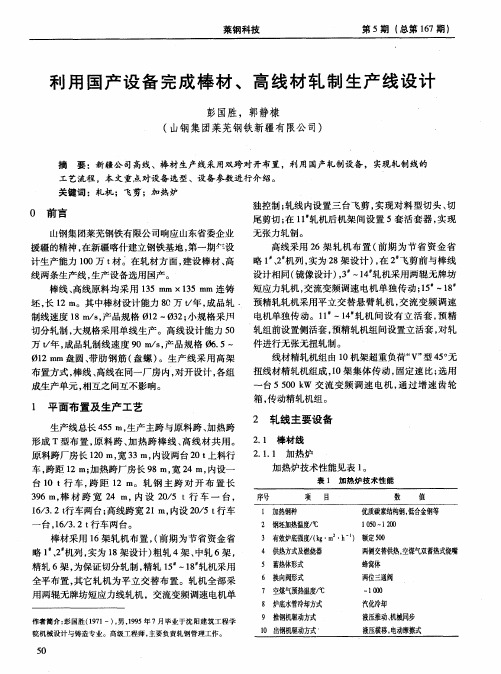
不供热利用热量辐射的保温段 , 节省能源投入; 炉底
采 用气 化冷 却技 术 。 加 热炉 有效 长度 2 5 m, 内宽 1 2 . 8 m, 采 用 高 炉 煤气 , 冷坯加热能力 1 5 0 t / h , 热装坯热装 温度大于
2 . 1 . 4 冷 床
6 0 0℃ , 热装率大于 7 0 %, 单位能耗 ≤1 . 1 G J / t ( 冷 装) 。
车, 跨距 1 2 I n ; 加热跨 厂房 长 9 8 r l l , 宽2 4 m, 内设 一 台1 0 t 行车, 跨距 1 2 I n 。轧 钢 主 跨 对 开 布 置 长 3 9 6 i n , 棒材跨 宽 2 4 i n , 内设 2 0 / 5 t行 车 一 台 , 1 6 / 3 . 2 t 行 车 两台 ; 高线跨 宽 2 1 m, 内设 2 0 / 5 t 行 车
山钢集 团莱 芜钢铁 有 限公 司响应 山东省 委企业
无张 力轧制 。
援疆的精神 , 在新疆喀什建立钢铁基地 , 第一期 : 设
计 生产能 力 1 0 0万 t 材 在 轧材 方 面 , 建设 棒 材 、 高 线 两条生 产线 , 生产 设备选 用 国产 。 棒线 、 高线 原料 均 采 用 1 3 5 m m ×1 3 5 m m 连 铸
棒 材采 用 1 6架 轧机 布 置 , ( 前期 为 节 省 资金 省
有效炉底强度 / ( k g ・ m 2 ・ h - 1 ) 额 定5 0 0 供热方式及燃烧器
略1 、 2 机列 , 实为 1 8 架设计) 粗轧 4 架、 中轧 6 架,
精 轧 6架 , 为保 证切 分轧 制 , 精轧 1 5 一1 8 轧机 采用 全 平布 置 , 其 它 轧机 为 平 立 交替 布 置 。轧 机 全 部采 用 两辊 无牌 坊短应 力 线轧机 ,交 流变频 调速 电机单
高线工艺及设备选用
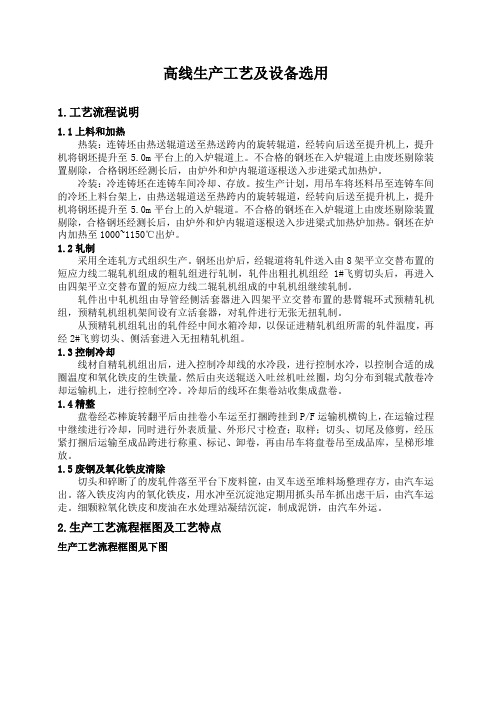
高线生产工艺及设备选用1.工艺流程说明1.1上料和加热热装:连铸坯由热送辊道送至热送跨内的旋转辊道,经转向后送至提升机上,提升机将钢坯提升至5.0m平台上的入炉辊道上。
不合格的钢坯在入炉辊道上由废坯剔除装置剔除,合格钢坯经测长后,由炉外和炉内辊道逐根送入步进梁式加热炉。
冷装:冷连铸坯在连铸车间冷却、存放。
按生产计划,用吊车将坯料吊至连铸车间的冷坯上料台架上,由热送辊道送至热跨内的旋转辊道,经转向后送至提升机上,提升机将钢坯提升至5.0m平台上的入炉辊道。
不合格的钢坯在入炉辊道上由废坯剔除装置剔除,合格钢坯经测长后,由炉外和炉内辊道逐根送入步进梁式加热炉加热。
钢坯在炉内加热至1000~1150℃出炉。
1.2轧制采用全连轧方式组织生产。
钢坯出炉后,经辊道将轧件送入由8架平立交替布置的短应力线二辊轧机组成的粗轧组进行轧制,轧件出粗扎机组经1#飞剪切头后,再进入由四架平立交替布置的短应力线二辊轧机组成的中轧机组继续轧制。
轧件出中轧机组由导管经侧活套器进入四架平立交替布置的悬臂辊环式预精轧机组,预精轧机组机架间设有立活套器,对轧件进行无张无扭轧制。
从预精轧机组轧出的轧件经中间水箱冷却,以保证进精轧机组所需的轧件温度,再经2#飞剪切头、侧活套进入无扭精轧机组。
1.3控制冷却线材自精轧机组出后,进入控制冷却线的水冷段,进行控制水冷,以控制合适的成圈温度和氧化铁皮的生铁量。
然后由夹送辊送入吐丝机吐丝圈,均匀分布到辊式散卷冷却运输机上,进行控制空冷。
冷却后的线环在集卷站收集成盘卷。
1.4精整盘卷经芯棒旋转翻平后由挂卷小车运至打捆跨挂到P/F运输机横钩上,在运输过程中继续进行冷却,同时进行外表质量、外形尺寸检查;取样;切头、切尾及修剪,经压紧打捆后运输至成品跨进行称重、标记、卸卷,再由吊车将盘卷吊至成品库,呈梯形堆放。
1.5废钢及氧化铁皮清除切头和碎断了的废轧件落至平台下废料筐,由叉车送至堆料场整理存方,由汽车运出。
精轧机说明书.(DOC)

高速线材精轧机组安装使用说明书制造单位:哈尔滨广旺机电设备制造有限公司设备图号: ZJF90d00使用客户:出厂日期:目录第一章、技术说明 (2)第二章、设备安装调整 (4)第三章、设备的使用维护与更换 (7)第四章、常见故障及排除 (13)第五章、附件 (14)精轧机组是高速线材车间的重要设备,为了保证精轧机组正常运转,用户须了解机组的性能、安装、运行与日常维护等基本常识。
本说明书就以上几个方面作了简单的介绍,用户在安装、使用机组前请先阅读本手册。
本说明书供武安文煜高线专用。
第一章技术说明一、设备用途本精轧机组为摩根五代顶交45°无扭重载高速线材精轧机组,图纸由国内设计转化完成。
本机组通过10机架连续微张力轧制,将上游轧机输送的轧件,轧制成φ5.5-φ20mm的成品线材。
二、设备主要性能参数1. 工艺参数:●来料规格:φ17—φ22mm●来料温度:>900℃●成品规格: φ5.5-φ20mm●主要钢种:碳钢、优质碳素钢、低合金钢、合金钢、焊条钢、冷镦钢等●第10架出口速度:≤95m/s(轧制φ6.5规格时)2. 设备参数:●机组组成:∅230轧机(5架)、∅170轧机(5架)、增速箱、大底座、挡水板与防水槽、缓冲箱、保护罩、联轴器、精轧机组配管等。
●机架数量: 10架(1-5架为∅230轧机,6-10架为∅170轧机同种规格的轧辊箱可以互换)●布置方式:顶交45°,10机架集中传动●辊环尺寸:∅230轧机:∅228.3/∅205×72mm∅170轧机:∅170.66/∅153×57.35/70mm ●传动电机: AC同步变频电机,功率: 5500kW●振动值:≤4.5 mm/s●噪音:≤80dB(距轧机1.5米处)●机组总速比(电机速度/装辊转速)见下表:●机组润滑方式:稀油集中润滑油压: 0.35MPa(点压力)总耗量:1200L/min油品: Mobil 525清洁度:10μ供油温度:38°C -42°C●保护罩液压系统:工作压力:15MPa系统流量:20 l/min●装辊工作压力:高压45 MPa -49.5MPa,低压22 MPa -25 MPa●卸辊工作压力:最大70MPa第二章设备安装调整一、安装调整顺序●将机组底座、增速箱、和主电机初步就位。
高线立式轧机安装技术

高线立式轧机的安装技术摘要:某精品高速线材设备安装工程,全线采用全连续式无扭转轧制工艺,轧机分为水平轧机和立式轧机。
立式轧机底座安装在立式基础上,底座垂直于地面,不仅给垫板座浆带来了施工难度,同时对底座的安装找正也带来了难度;万向接轴是重要的力矩传输装置位于减速机与轧机中间且垂直于地面不利于吊装。
我单位通过以往的施工经验及现场实际的情况,总结经验勇于实践,验证了一套比较好的安装立式轧机的施工方法。
关键词:设备安装;立式轧机;安装技术中图分类号: tg333.51 文献标识码: a 文章编号:1 工程概况某精品高速线材工程是设计能力为两条年产50万吨的高速线材加工项目,第一条生产线共有30架轧机,第二条生产线共计32架轧机。
该工程中的粗中轧区域内的轧机分为水平轧机和立式轧机。
2 施工方案根据轧机底座垂直于基础面,制定垫板反顺序进行安装;由于轧机单套机组与多套机组都存在着一定联系,确定设备安装的先后顺序;根据实际情况确定如何能够提高安装效率的方法,制作相应的辅助工具。
根据确定好的安装方案再进行设备基础与土建进行交接及验收,对整个轧线进行总体的测量控制并布置控制网、标高点、中心标板。
3 操作要点3.1基础验收根据基础中交验收单进行基础验收,验收标准如下:标高误差为: 0~-20mm预埋地脚螺栓中心偏差:±2mm螺栓顶部标高误差: 0~+20mm3.2建立测量控制网、标高及中心标板的埋设1)高速线材生产线为连续生产线,对轧机机组的纵向中心的直线度要求精度较高。
因此在需要建立一个测量控制网来控制整个轧线设备的安装,以保证整条线的安装精度要求。
选定粗轧第一台轧机内侧建立一个基准点,整条线的中心标板及表高点均以此点进行反设,以消除累计误差确保安装质量。
2)根据建立的测量控制网在安装前应进行永久性中心标板及标高基准点的埋设工作,中心标板埋设在轧制中心线上的设备空隙处,间隔为30—40米。
横向则埋设在各个立式轧机机架的横向中心上,基准点设置在机组旁易于检测的位置。
青特钢二三高线工艺设备简介

轧 速度 , 配合 T MB双模 块 轧 机 时 , 最 大轧 制 速度 可 达1 4 0 m / s ( 设 计 最 大 轧制 速 度 可 达 1 7 0 m / s ) , 大 幅
尺度大 , 总压下量大 , 故采用脱头辊道 。轧线设计
( 青 岛特殊钢铁有限公司 , 山东 青 岛 2 6 6 o o o )
摘
要: 介绍 了青岛特殊钢铁二 三高线的生产工艺 , 重 点介绍采用 的达涅利双模块轧机 、 双 管吐丝机和轮廓仪 等新工艺装
备特点 , 生产线可稳定生产 5 . 0 ~ 7 . 0 m i l l 的帘线钢 、 冷镦 钢等线材产品。 关键词 : 高速线材 ; 双模块轧机 ; 双管吐丝机 ; 轮廓仪
中图分类号 : T G3 3 8 文献标识码 : B 文章编 号: 1 0 0 4 — 4 6 2 0 ( 2 0 1 6 ) 0 6 — 0 1 0 1 — 0 1
1 前
言
青 岛特 殊 钢 铁 有 限公 司根 据 国家 环保 搬 迁 政 策要求 , 在黄岛西海岸新区建设两条新的高速线材
齿 隙 的止 推轴 承 , 可有 效 降低轧 制 载荷 对设 备 的变
形, 提 升 线 材 产 品 的加 工精 度 , 对于 5 . 0 m m和 5 . 5
低 了主 电机功率 , 节能降耗 , 也为后期生产 中减低
电单 耗 和降低 吨钢生产成 本奠定 了坚 实基础 n 。
m m高精度 帘线钢 用母材有 重要 意义 。
青 特钢 双模块 T MB采用 一椭 三 圆的孔 型系统 ,
3 新技 术及设 备
3 . 1 D WB 精 轧机/ T MB双模 块轧机
高线无扭线材精轧机组(BGV)精密维修实践

高线无扭线材精轧机组(BGV)精密维修实践摘要宝钢集团八钢股份有限责任公司棒线轧钢厂高线机组,高速无扭线材精轧机组维修实践进行了总结,对装配技术要点进行了论述,阐述了螺旋锥齿轮、油膜轴承、锥箱、辊箱、圆柱斜齿轮、轴向密封及轧辊装配的技术要求,对精轧机维修工作具有指导作用。
关键词高速线材;精轧机;装配调整中图分类号TG335 文献标识码 A 文章编号1673-9671-(2012)071-0158-011 概述宝钢集团八钢股份有限责任公司棒线轧钢厂高线机组建成于2000年,设计产量40万吨,2003年顺利达产,现年产量达到72万t。
其主线设备采用意大利达涅利公司研制的侧交45°无扭高速轧机(BGV)及减定径机(TMB)8+4机组,现成品线速度为115 m/s。
2 精轧机结构特点与工作原理45°无扭高速线材精轧机组由8个机架组成。
其结构为悬臂小辊径,轧辊直径1~4架Φ200mm,5~8架Φ165 mm。
每对轧辊轴线与水平成45°角布置。
相邻机架两对轧辊轴线互成90°交角,轧件在轧制中为无扭轧制。
3 锥齿轮的装配调整纵轴锥齿轮靠增减两端轴承端盖的垫片来调节它的位置,使螺旋锥齿轮副的齿侧间隙满足以保证齿侧间隙0.12 mm~0.22 mm,齿接触面积高度方向和长度方向均不少于70%。
这里要注意在装配时,一般通过研磨图一中7222轴承间的隔圈,让装有纵轴锥齿轮的纵轴朝锥齿轮小头方向(与轧制方向相同)留有0.108 mm~0.132 mm的间隙量,以减缓轧制咬钢时的瞬时冲击力。
4 油膜轴承及滚动轴承的安装4.1 油膜轴承安装①转轴和轧辊齿轮轴主要的径向力在动压油膜轴承上,其轴向力由滚动轴承支承。
在压力作用下,油膜轴承可能发生折皱现象,还可能在轴承外表面和偏心套内孔之间发生粘连,为了减少这种现象的发生,在装配前可通过加热偏心套、冷冻油膜轴承来减少过盈量。
安装油膜轴承时应用特殊的安装工具将偏心套加热120℃,同时将轴瓦置于干冰或液态氮中冷却至-80℃。
高线精轧机知识

高线精轧机知识一、高线精轧机概述高线精轧机是一种用于轧制金属线材的设备,广泛应用于钢铁、有色金属等行业。
其主要作用是通过连续轧制和塑性变形,将粗线材逐步压制成细线材,并达到一定的尺寸精度和表面质量要求。
高线精轧机通常由多个轧机组成,每个轧机都具有一对辊子,通过转动辊子来完成轧制过程。
二、高线精轧机的工作原理高线精轧机的工作原理是通过辊子的转动和线材的通过,使得线材在辊子之间受到挤压和塑性变形,从而达到减小线材直径和提高线材表面质量的目的。
整个过程中,线材在不同轧机之间经过多次轧制,逐渐减小直径,直至达到目标尺寸。
三、高线精轧机的主要部件1. 轧机辊子:是高线精轧机的核心部件,承担着线材的挤压和塑性变形任务。
辊子通常由优质的合金钢制成,具有高强度和耐磨性能。
辊子的表面经过精细抛光和硬化处理,以确保线材的表面质量。
2. 传动系统:用于驱动辊子的转动。
传动系统通常采用电机和减速器的组合,通过齿轮传动或皮带传动将动力传递给辊子。
3. 卷取系统:用于将轧制好的线材卷取起来。
卷取系统通常由卷取机构和张力控制系统组成,能够保证线材卷取的紧密度和稳定性。
4. 控制系统:用于对高线精轧机进行全面的控制和监测。
控制系统通常包括电气控制系统和液压控制系统,能够实现轧机的启停、速度调节、张力控制等功能,并对轧制过程进行实时监测和数据记录。
四、高线精轧机的应用领域高线精轧机广泛应用于钢铁、有色金属等行业。
在钢铁行业中,高线精轧机主要用于生产各种钢丝、钢绞线、钢绞线等产品。
在有色金属行业中,高线精轧机主要用于生产铝线、铜线等产品。
这些产品在建筑、交通、电力、通信等领域中都有广泛的应用。
五、高线精轧机的优势和发展趋势1. 高线精轧机能够实现线材直径的精确控制,提供高精度的线材产品,满足不同行业的需求。
2. 高线精轧机具有高效率和高自动化程度,能够实现连续生产和自动化控制,提高生产效率和产品质量。
3. 高线精轧机具有较小的占地面积和能耗,能够节约生产成本,提高经济效益。
轧钢高线主控台操作注意事项

主控台操作与注意事项一、速度调节及活套调节(1)速度调节:以精轧机为基准机架从1#轧机开始全线轧机为逆调:夹送辊、吐丝机与精轧机之间为顺调,以精轧机的速度为基准。
当精轧变速时,夹送辊、吐线机必须同步按比例调速。
级联逆调设有快速、慢速二种变速方式,调整量分别为:慢速=额定值0.25%/s,快速=额定值1%/s。
——单动单调:设备单独启车,调整至设定转速,必要时进行单独微调,不影响其它轧线设备转速。
――联动单调:在线联调模式下,对设备转速进行单独调整。
――联动单调:在线联调模式下,可以以任意机架为基准,对该轧机及其上游设备进行级联调节。
①在功能键盘上选择调整方式键(单调或联调)。
②选择调速键(快升、快降、慢升、慢降四选一)③选择所需变速机架的地址键,对照速度显示画面,即可按所需进行调节。
(2)活套调节:活套调节方式为全线级联逆调,按比例积分方式进行调节。
正常轧钢过程中,活套的调节是由活套扫描器自动进行的,通过分别改变对应各机架的速度来达到符合设定套高的目的。
(1)活套的成套过程活套扫描器检测到轧件头部并达到设定延时时间,推套器推出,同时活套扫描器投入使用,上游机架级联升速。
(2)收套过程前一个活套扫描器检测到轧件尾部,推套器收回、活套扫描器退出调节,活套退出同时上游机架级联降速。
(3)活套的调节方法①1#立活套设置为150~250mm的范围内。
(该设备已拆除)②预精轧立套量一般设置为100-200mm,可由操作工根据情况进行适当调整,正常情况下,由3#、4#、5#扫描器来分别控制各架预精轧机的速度以保证活套量。
异常时可由操作工分别调节预精轧的给定速度来保证立套量。
③水平套量设为340-450mm,可由操作工根据情况进行适当调整,正常情况下,由扫描器来控制预精轧机的速度以保证活套量。
二、停机操作与注意事项(1)接到调度停机指令后,联系加热炉出钢室(电话:5781670)留空位,烧小料。
(2)将自动出钢停止,单个按钮转换到单组,各组选择任意一架,将中粗轧水压报警关闭。
高线

φ10
45
1#飞剪投入状态
1#飞剪切头超前系数 1#飞剪切头长度 2#飞剪投入状态 2#飞剪切头超前系数 2#飞剪切头长度 2#飞剪切尾滞后系数 2#飞剪切尾长度 3#飞剪投入状态 mm mm mm
切头,不切尾
1.10-1.25 ≤150 切头,切尾 1.10-1.15 ≤200 0.85-0.90 ≤300 切头,不切尾
原料到成品的延伸变形整个过程。 轧制过程中需要控制的主要工艺参数就是轧制速度 和料型。 这里说的速度与前面讲过的速度是不同的,这里所 说的速度是各架轧机的速度,也就是各架轧机间的 速度匹配关系,也就是我们常说的张力关系
生产工艺-轧制
轧制速度与轧制料型:之所以把轧制速度和料型放在一起来
说,是因为生产过程中速度与料型的控制是相辅相成的。前 面讲过,高速线材轧机有一个特点就是连轧,而形成连轧的 条件就是秒流量相等,即FV=C(常数),用语言表述就是单 位时间内流经每一架轧机的金属体积相等。 实现良好的速度和料型调整是有前提的:首先要有稳定的设 备;再者要有良好的孔型设计,也就是说要有一套完备孔型 系统(后面介绍);最后要确保孔槽的加工精度和安装精度。 只有具备了上述条件,才能通过速度与料型的调整,使生产 连续、稳定。
高速无扭精轧
高速无扭精轧工艺是现代线材生产的核心技
术之一,它是针对以往各种线材轧机存在诸 多问题,综合解决产品多品种规格、高断面 尺寸精度、大盘卷和高生产率的有效手段。 唯精轧高速度才能有高生产率。才能解决大 盘重线材轧制过程的温降问题。精轧的高速 度要求轧制过程中轧件无扭转,否则事故频 发,轧制根本无法进行。因此,高速无扭精 轧是高速线材轧机的一个基本特点。
微张力轧制,粗中轧机组作用是以较大的压 下量实现大的变形和延伸,为预精轧机组输 送合适尺寸的轧件。
1#高线设备台帐
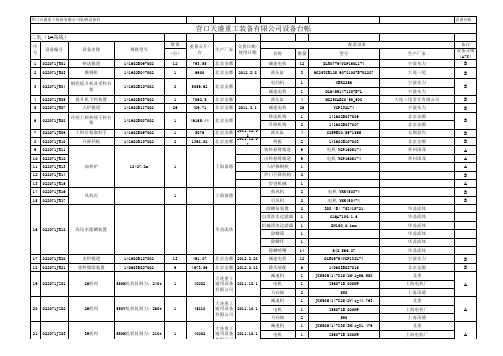
哈尔滨哈飞工业机电设备制造公司 哈尔滨哈飞工业机电设备制造公司 哈尔滨哈飞工业机电设备制造公司 哈尔滨哈飞工业机电设备制造公司 哈尔滨哈飞工业机电设备制造公司 哈尔滨哈飞工业机电设备制造公司 哈尔滨哈飞工业机电设备制造公司 哈尔滨哈飞工业机电设备制造公司 哈尔滨哈飞工业机电设备制造公司 哈尔滨哈飞工业机电设备制造公司 上海电机厂 哈尔滨哈飞工业机电设备制造公司 哈尔滨哈飞工业机电设备制造公司 上海电机厂 哈尔滨哈飞工业机电设备制造公司 哈尔滨哈飞工业机电设备制造公司 哈尔滨哈飞工业机电设备制造公司 哈尔滨哈飞工业机电设备制造公司 济南南方 济南南方 济南南方 南通宏大 济南南方 济南南方 济南南方 南通宏大 济南南方 济南南方
022071JZ44
2#飞剪 侧活套 卡断剪 预精轧机间立活套 预精轧机(平式) 预精轧机(立式)
Z4247.00TL DC12878-2 DC16362-2 DC16686-2 Φ 285水平轧机 Φ 285立式轧机
2 2 2 6 4 4
9371.3 3210
气缸 2011.12.17 2011.10.10 2011.10.10 上导辊装配 起套辊装配 预精轧安全罩 减速器 碎断剪
B B B B B B B B A A A B A B B
022071JR04 钢坯提升机及受料台架 022071JR05 022071JR07 提升机下料装置 入炉辊道
022071JR08 冷坯上料热坯下料台架 022071JR09 022071JR10 022071JR11 022071JR12 022071JR13 022071JR14 022071JR15 022071JR16 022071JR17 上料台架取料手 升降挡板
35
022071JZ18
轧钢高线主控台操作注意事项

轧钢高线主控台操作注意事项(总5页)本页仅作为文档封面,使用时可以删除This document is for reference only-rar21year.March主控台操作与注意事项一、速度调节及活套调节(1)速度调节:以精轧机为基准机架从1#轧机开始全线轧机为逆调:夹送辊、吐丝机与精轧机之间为顺调,以精轧机的速度为基准。
当精轧变速时,夹送辊、吐线机必须同步按比例调速。
级联逆调设有快速、慢速二种变速方式,调整量分别为:慢速=额定值%/s,快速=额定值1%/s。
——单动单调:设备单独启车,调整至设定转速,必要时进行单独微调,不影响其它轧线设备转速。
――联动单调:在线联调模式下,对设备转速进行单独调整。
――联动单调:在线联调模式下,可以以任意机架为基准,对该轧机及其上游设备进行级联调节。
①在功能键盘上选择调整方式键(单调或联调)。
②选择调速键(快升、快降、慢升、慢降四选一)③选择所需变速机架的地址键,对照速度显示画面,即可按所需进行调节。
(2)活套调节:活套调节方式为全线级联逆调,按比例积分方式进行调节。
正常轧钢过程中,活套的调节是由活套扫描器自动进行的,通过分别改变对应各机架的速度来达到符合设定套高的目的。
(1)活套的成套过程活套扫描器检测到轧件头部并达到设定延时时间,推套器推出,同时活套扫描器投入使用,上游机架级联升速。
(2)收套过程前一个活套扫描器检测到轧件尾部,推套器收回、活套扫描器退出调节,活套退出同时上游机架级联降速。
(3)活套的调节方法①1#立活套设置为150~250mm的范围内。
(该设备已拆除)②预精轧立套量一般设置为100-200mm,可由操作工根据情况进行适当调整,正常情况下,由3#、4#、5#扫描器来分别控制各架预精轧机的速度以保证活套量。
异常时可由操作工分别调节预精轧的给定速度来保证立套量。
③水平套量设为340-450mm,可由操作工根据情况进行适当调整,正常情况下,由扫描器来控制预精轧机的速度以保证活套量。
高线生产简介

(2)避免强制加热,加热能力不足时可适当待温。
(3)轧制节奏允许时加大步距,减少钢坯在炉内停 留时间。
高速线材生产工艺
二、加热
4、钢坯除鳞 国内线材生产线钢坯高 压水除鳞是近几年才投入使 用的,因为以前国内线材产 品大多为建筑用材,对表面 质量要求不严格,而且线材 粗轧都有几架箱型孔,有较 好的去除氧化铁皮的效果。 随着线材产品的不断升级, 对线材产品表面质量的要求 不断提高,国内新投产的生 产线都配备了高压水除鳞设 备。
高速线材生产工艺
线材生产特点
线材是热轧产品中断面面积最小,成品长度最大且成 卷交货的产品。其生产特点可概括为连续、高速、无扭、 控冷。其产品特点是大盘重、高精度、性能优良。
高速线材生产工艺
一、工艺流程
加热上料辊道 →提升机上料→ 辊道入炉→ 蓄热式步进加热炉→ 出钢辊道出炉→ 粗轧六架轧 制→ 1#飞剪切头(事故碎断)→ 中轧六架轧制→ 2#飞剪切头尾(事故碎断) →预精轧六架轧制 (中间设立活套) → 1#水箱→ 3 #飞剪切头(事 故碎断) →侧活套 →精轧机轧制 → 2#、3#水箱 → (双模块轧制) → 4#、5#水箱→夹送辊→吐 丝机→散卷冷却→集卷收集→ PF链运输 →检查质 量、取样、检除头尾→打包→称重→卸卷入库→成 品运出
高速线材生产工艺
二、加热
1、原料
高速线材生产工艺
二、加热
2、钢坯输送
连铸钢坯大部分可以实现热装热送,热送温度在600~ 750℃,个别的可以达到850℃。高线生产平台一般在离地 平面5m的平台上,钢坯要经过提升机提升或天车吊运到平 台上面,放在入炉辊道上入炉。 提升机提升和入炉时对钢 坯的弯曲度有一定的要求,否则会发生生产或设备事故。
高线车间平面布置图

高线车间平面布置图宝钢高速线材车间设计简介杨晓明摘要:描述了具有当今世界一流水平的宝钢高速线材车间的工艺、设备情况及主要技术参数,并对其拥有的处于世界领先水平的线材TEKISUN减定径机、电气传动全交流化、优质高碳钢步进梁式加热炉、探伤测径装置、闭环冷却控温系统等技术及设备进行了进一步阐述。
关键词:高速线材轧机;工艺特点;设备特点中图分类号:TG335.6 文献标识码:AIntroduction on high-speed wire mill of BaosteelYANG Xiao-ming(Chongqing Iron & Steel Designing Institute, Chongqing 400013, China) Abstract:The paper introduced the process, equipment and main technology parameters of high-speed wire mill of Baosteel, which is the one of the best advanced mills in the world, and described the TEKISUN reducing/sizing mill, the complete AC electrical driving, walking-beam furnace of high carbon steel, the flaw detector and diameter gauge, the close loop cooling control system, etc.Key words:high-speed wire mill; technology characteristics; equipment characteristics1 概况宝钢高速线材车间为当前世界最高水平的高速线材车间,全线连续无扭轧制,主要生产钢帘线、预应力钢丝钢绞线、冷镦钢等制品用线材,规格为Φ5~Φ25mm,设计年产量40万t,最高保证速度110m/s。
高压设备配置
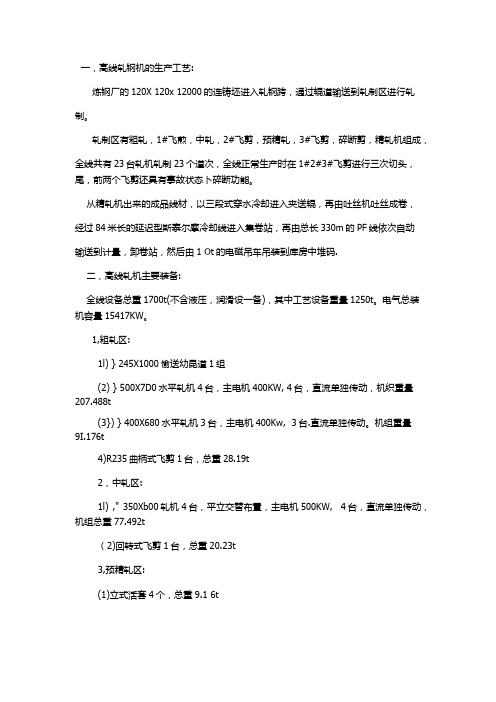
一,高线轧钢机的生产工艺:炼钢厂的120X 120x 12000的连铸坯进入轧钢跨,通过辊道输送到轧制区进行轧制。
轧制区有粗轧,1#飞煎,中轧,2#飞剪,预精轧,3#飞剪,碎断剪,精轧机组成,全线共有23台轧机轧制23个道次,全线正常生产时在1#2#3#飞剪进行三次切头,尾,前两个飞剪还具有事故状态卜碎断功能。
从精轧机出来的成品线材,以三段式穿水冷却进入夹送辊,再由吐丝机吐丝成卷,经过84米长的延迟型斯泰尔摩冷却线进入集卷站,再由总长330m的PF线依次自动输送到计量,卸卷站,然后由1 Ot的电磁吊车吊装到库房中堆码.二,高线轧机主要装备:全线设备总重1700t(不含液压,润滑设一备),其中工艺设备重量1250t。
电气总装机容量15417KW。
1,粗轧区:1l) } 245X1000愉送幼昆道1组(2) } 500X7D0水平轧机4台,主电机400KW, 4台,直流单独传动,机织重量207.488t(3}) } 400X680水平轧机3台,主电机400Kw, 3台.直流单独传动。
机组重量9I.176t4)R235曲柄式飞剪1台,总重28.19t2,中轧区:1l) ," 350Xb00轧机4台,平立交替布置,主电机500KW, 4台,直流单独传动,机组总重77.492t(2)回转式飞剪1台,总重20.23t3,预精轧区:(1)立式活套4个,总重9.1 6tt2) } 300X600轧机4台,平立交替布置,主电机500KW, 4台,直流单独传动,机组总重73.63t3})轧件输送导槽组4,精轧区:1l)回转式飞剪1台,自动回转式转撤器1台,总重6.94t}2)带夹送辊的碎断剪1台,总重2.79t3)水平活套1个(4) } 21 x72高速无扭精轧机组,共8台,有二台1250KW直流电机串联集体传动,机组总重92:05t5,精整区1})3组水冷箱总长38米,总重14.31t(2)带夹送辊的吐丝机1台,总重10.50t}3)带保温罩延迟型斯泰尔摩冷却线1条,长度84.645rn,总重366t(4)全自动集卷站一个,包括集卷筒1个,双臂芯轴1套,运卷小车1台t5)PF线,全长350m,共有50个C型钩,总重120t(6)液压式半自动打捆机2台t7)盘卷称量装置1套}8)卸卷机1套6,液压与润滑设备:[1)粗轧与中轧液压,润滑站各一套[2)预精轧及中轧液压,润滑站各一套(3)集卷,打捆,称量卸卷,加热液压站各一套7,水处理[1)旋流沉渣池1座,平流池2座[2)净循环水处理系统1套(3)浊循环水处理系统1套8,装各水平全线设备中,钢坯电磁吊为全国先进水平,精轧机所用油膜轴承为国外进口,精整线装各为国内一流.总体装备为国内九十年代先进水平.二、设备报价。
- 1、下载文档前请自行甄别文档内容的完整性,平台不提供额外的编辑、内容补充、找答案等附加服务。
- 2、"仅部分预览"的文档,不可在线预览部分如存在完整性等问题,可反馈申请退款(可完整预览的文档不适用该条件!)。
- 3、如文档侵犯您的权益,请联系客服反馈,我们会尽快为您处理(人工客服工作时间:9:00-18:30)。
加热炉加热炉步进机构分为步进梁和步进机械。
步进梁包括固定梁和活动梁,并采用步进梁交叉技术,即在装料端设固定梁4根,出料端设固定梁5根,炉内通长设置活动梁4根,9根梁分段并交叉布置,能实现梁与钢坯接触位置的不停倒换,有效消除“黑印”现象。
步进机械为双层框架式结构,上层框架为平移框架,下层框架为升降框架,在升降框架的上部和下部各安装有5组10个轮子完成升降和平移动作。
在平移框架和升降框架上各安装有2组8个防止跑偏的导轮。
步进机械采用全液压传动,平移框架和升降框架由钢梁制成。
步进梁随着步进框架的运动作上升、前进、下降、后退等的周期运动,设计最短周期为36s。
夹送辊位置:粗轧机组前卡断剪前,将钢坯夹持,送入1#粗轧机。
辊面线速度:0~2m/s上辊汽缸横移及汽缸夹紧。
粗轧机组前卡断剪位置:1#粗轧机前功能:事故时切断钢坯剪切端面:155×155mm剪切温度:≦900℃传动方式:气动轧机及主传动系统型式:水平二辊闭口式,机架横移,轧制线固定更换:小车换辊,上辊弹性阻尼体减震器平衡轴承:滚动轴承轧辊尺寸:Φ610/520×800mm电机:直流电机传动2高线采用的是短应力线轧机功能:根据工艺要求,将钢坯轧制成所需的断面形状设备组成:轧机机芯、轧机底座、轧机轨座、接轴托架、万向接轴、复合减速机、主传动电机等。
特点:由于取消了轧机牌坊,应力线通过拉杆和轴承座内置丝母连接,缩短了应力线长度,缩小了轧机的弹跳。
拉杆联结的轴承座使轧辊轴承的受力状态更合理,提高了轴承的承载能力和延长了轴承的使用寿命。
短应力线轧机提高了轧机的刚度,同时使轧辊轴承稳定运行,从而提高了轧制精度。
为了避免轧辊的径向跳动,上下辊轴承座内设置弹簧平衡装置。
为了防止轧辊的轴向窜动,上下轧辊均在操作侧设置了轴向固定装置。
为了精确地将上下辊的孔槽对准,上辊轴承座内置轧辊轴向调节装置。
通过手动蜗杆使既带蜗轮又带螺纹的套旋转,带动止推轴承和四列圆柱滚子轴承的内套和轧辊轴向移动,从而进行轴向调整;为消除螺纹间隙和防松,增设了对顶螺纹套。
辊缝调节装置:由液压马达、传动轴、传动侧和操作侧蜗杆蜗轮箱等组成。
轧机底座:用于安装轧机机芯,轧机机芯通过螺栓(液压螺母)联结到轧机底座上,组成轧机本体。
轧机主传动:轧机主电机采用交流变频调速电机,减速机齿轮采用硬齿面,两个输出轴通过SWC十字万向联轴器分别驱动上下轧辊。
轧机轨座:轧机本体和接轴托架安装在同一个轧机轨座上。
轨座为钢结构焊接件,上面衬有耐磨板。
轧机轨座上还装配了轧机横移装置和轧机锁紧装置。
轧机横移采用液压缸驱动。
多用在换槽,换卡盘!悬臂式预精轧机数量:4列型式:平立交替布置悬臂辊环式传动:直流单独传动辊缝调整:手动调整作用:通过4机架无扭无张力连续轧制,将坯料轧制成满足精轧机组要求的断面尺寸及精度。
结构:机组由4架 285悬臂式轧机组成,平立交替布置,机架间设有立式活套。
特点:①轧机为轧辊箱插入式机构。
②水平机架的齿轮箱内由输入轴和同步轴共两根带有齿轮的传动轴组成,机架可由一标准减速器调整速比。
③立式机架齿轮箱内的传动系统比水平机架多一对螺旋伞齿轮,用来改变传动方向和调整速比,其余部分与水平机架相同预精轧间立式活套数量:3个位置:位于悬臂式预精轧机组各机架之间。
作用:使预精轧机组实现无张力轧制,以提高轧件精度。
结构:气动立式活套,焊接结构,活套扫描器控制套量。
技术参数:活套高度:正常:~100 mm最大:~400 mm控制方式:活套扫描器控制套量气缸控制起套辊水冷段及导槽功能:冷却轧件,控制进入精轧机的轧件温度。
设备组成:水箱和导槽。
结构特点:水箱内集管上安装有便于更换的开口式喷咀装置。
各喷咀装置形成一个环形孔板可使轧件充分冷却。
喷咀孔规格相同。
参数:水箱长:~6.1m(2个)冷却喷咀:5450L/min,0.6MPa喷咀空气压力:0.4~0.6MPa喷咀空气流量:105m3/h最大冷却温降:150℃喷咀材质:不锈钢剪型式为3种第一种:型式:曲柄飞剪,启停工作制。
功能:轧后切掉轧件头、尾部,利于轧件进入中轧机组轧制,事故时用于轧件碎断。
设备组成:电机驱动装置、齿轮箱、曲柄连杆刀座、剪刀等。
结构特点:电机为启停工作制,直接驱动带减速级的齿轮箱。
齿轮箱的双输出轴为曲轴,分别带动装配上下剪刀的连杆机构。
剪刀刀座作圆周运动,剪刀作平动,剪刀面在剪切瞬间基本与轧件垂直,并与轧件速度基本一致,在轧件运动中将其剪断。
上下曲轴之间为齿轮传动,两曲轴间速比为1:1,电动机通过一减速机驱动下曲轴,使上下曲轴同时转动,带动剪刃进行剪切。
主要件材质:刀轴40CrMnMo,齿轮为锻件(齿圈20CrMnMo,其余Q235),剪刃4Cr5WMoVSi。
第二种:型式:回转式飞剪,启停工作制。
设备组成:电机驱动装置、齿轮箱、回转臂、剪刀等。
结构特点:电机为启停工作制,直接驱动带减速级的齿轮箱。
齿轮箱的双输出轴装配回转臂,分别装配上下剪刀。
剪刀作圆周运动,其水平速度与轧件速度基本一致,在轧件运动中将其剪断。
每个回转臂设置双剪刃,以便使碎断件变短。
剪机出轴密封采用聚丙烯酸脂橡胶密封圈。
主要件材质:刀轴42CrMoA,齿轮为锻件(齿圈20CrMnMo,其余Q235),剪刃4Cr5WMoVSi。
第三种:倍尺飞剪说明:该组合飞剪将与八钢型材厂小型机组现用倍尺飞剪交换,其剪切参数需满足型材厂剪切弹簧扁钢等产品的需要。
八钢提供有关资料,飞剪底座制作考虑小型机组飞剪原安装尺寸。
功能:将棒材按倍尺长度分段剪切。
型式:启停制回转/曲柄组合剪。
设备组成:电机驱动装置、飞轮、齿轮箱、曲柄连杆刀座和剪刀、回转臂和剪刀等。
结构特点:电机为起停工作制,直接驱动带减速级的齿轮箱。
齿轮箱的双输出轴为曲轴,分别带动装配上下剪刀的连杆机构,此时剪机为曲柄剪。
剪刀刀座作圆周运动,剪刀作平动,剪刀面在剪切瞬间基本与棒材垂直,并与棒材速度基本一致,在轧件运动中将其剪断。
在剪切高速小规格棒材时,将齿轮箱的双输出轴上的连杆机构取下旁置,再装配回转臂,剪机被改装成回转剪。
剪刀作圆周运动,其水平速度与棒材速度基本一致,在棒材运动中将其剪断。
在剪切低速大规格棒材时,使用曲柄剪,同时将飞轮投入使用。
飞轮装配在电机和齿轮箱之间的传动轴上,通过离合器与之相联。
在电动机和减速机之间的联轴器处装有制动器,剪切制动后锁住驱动装置,使剪刀停位预定的位置。
主要参数:剪切速度:1.5~18m/s剪刃宽度:180mm剪切钢种:60Si2Mn、42CrMoA、60Si2Cr、45钢、20CrMnTi;剪切温度:≥600℃剪切断面:2600mm2精轧机功能:轧制成品线材。
型式:45°顶交悬臂辊式轧机。
组成:传动装置,增速器,10机架辊箱。
安全罩,空过套管,专用工具等。
特点:轧机采用45 顶交布置,无扭轧制;10架轧机由1台电机集中传动;辊缝由装在每个机架辊轴上的偏心套对称轧制线调整,使轧制线固定;由于辊环精确地固定在辊轴上,因此不要求轧辊进行轴向调节;辊轴由油膜轴承径向支撑,由滚动轴承承受轴向负荷;在辊轴工作侧的油膜轴承设有热电阻,以监视轴承温度,并自动报警。
各个辊轴上设有特殊双口密封接触旋转抛油环,防止水进入辊箱或者油从辊箱中外泄。
辊环喷水冷却。
设有安全罩,安全罩由液压缸打开。
配置辊环装拆工具,用来在线快速换辊。
主要参数:辊环尺寸:Φ228/Φ205×72 (5架)Φ170/Φ155×72 (5架)辊环材质:碳化钨电机功率:6000kW,交流变频调速辊环更换:液压工具,用于辊环更换。
棒材穿水冷却装置在精轧机组出口与3#剪之间设置了水冷装置,出精轧机的带肋钢筋棒材立即进入水冷装置进行在线余热淬火处理,也就是将轧件经过水冷装置强制水冷,使其表面温度急剧降低至350℃左右,形成马氏体组织。
出水冷箱后,轧件芯部的热量散出,对表面马氏体组织进行回火,最终获得表面为回火马氏体组织、芯部为细粒珠光体组织。
这种组织的产品具有较高的抗拉强度,可使带肋钢筋强度提高一个等级。
根据不同钢种、规格的产品要求,对水冷装置的使用段数、水量等进行人工设定,以便使轧件上冷床时达到要求的轧件温度。
功能:对轧件强制冷却,达到细化晶粒,提高钢材的力学性能、改善轧件表面质量的目的。
设备组成:单线穿水冷却总成;双线穿水冷却总成;三线、四线穿水冷却总成;旁通辊道等共计4条通道。
都安装在横移小车上。
横移小车采用液压驱动。
穿水线出口设置压缩空气吹扫,横移小车将需要的通道横移对准轧制线,满足不同的生产工艺。
主要参数:型式:4个水冷段组成,分段驱动。
水系统压力:≥2.0MPa流量:≥800m3/h。
旁通辊道:辊子速度:3.5~20.0 m/s上床温度控制:≤900℃吐丝机•卧式低惯量吐丝机,具有线材头部定位控制功能,保证线环的头部以最佳方位落到斯太尔摩线上,以避免运输过程的事故,消除生产损失;还具有速度周期波动控制功能,以改善线环直径,提高线材集卷密实度。
•倾斜角度:20°(15 °)•线环平均直径:Φ1075mm•吐丝速度:(最大设备能力)150m/s•传动方式:直流电机传动,功率250kW一.风冷线功能:布置在吐丝机之后。
将线圈输送到集卷站。
通过“延迟”冷却或“标准”冷却方式,得到钢种需要的冶金机械性能。
延迟冷却时输送机以低速运行,以形成密实的线圈,保温罩关闭,风机停转;标准冷却时辊道以较高的速度运行,线材线圈形成敞开型式,保温罩打开,采用强制风冷。
特点:运输机分为8个基本的运输机段,加入口倾斜段和出口段。
各段的辊子由交流变频电机链式传动,每段可独立进行速度控制;运输机速度可调,以获得最佳冷却效果;跌落段设在每段末端,以便分开线圈,改善线材的冷却,由此改善拉伸强度的均匀性和改变运输机段的速度;主要参数:总长:86.149m保温罩长:~60m辊道共分:10段入口段1段,长~3.8m冷却段8段,9.25m/段;出口段1段,长~4.4m运输速度:0.1~2.0 m/s辊子规格:Φ120 mm(入口段Φ125 mm)辊子长:1540mm辊子材质:耐热球墨铸铁辊子间距:130/200/250 mm落差的位置2、3、4、5段的尾部落差高度:60mm大落差的位置6~8段的尾部落差高度:200~250mm出口段横移距离:300mm辊子传动电机:AC15kW 变频调速,10台风机电机:前6台为250kW变频调速电机,后8台为200kW电机风机空气流量:前6台19万m /h,后8台15万m /h。
静压力:3000Pa二.集卷筒功能:将散卷收集成卷,并使轧机以正常节奏轧制时,作为一个缓冲存贮空间。
参数:集卷筒内径:Φ850mm集卷筒外径:Φ1250mm鼻锥升降行程:50 mm临时托卷臂;6个三.双芯棒装置功能:位于集卷筒的下方。