中国液压舵机行业发展概述
我国液压工业与技术的发展现状与展望的战略思考_许仰曾
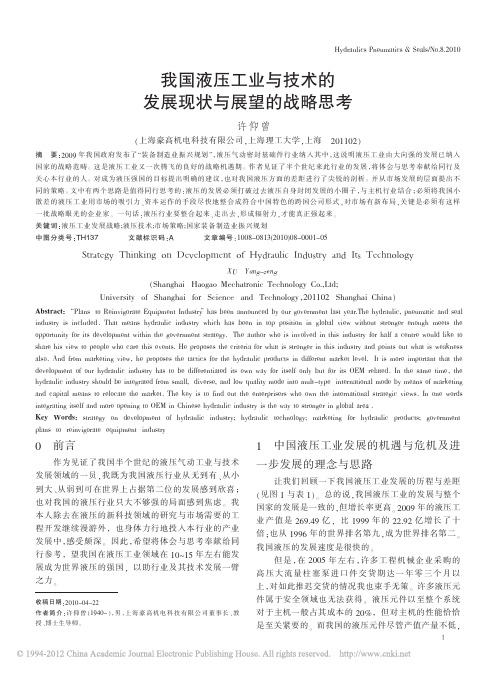
我国液压工业与技术的发展现状与展望的战略思考许仰曾(上海豪高机电科技有限公司,上海理工大学,上海201102)Strategy Thinking on Development of Hydraulic Industry and Its TechnologyXUYang-zeng(Shanghai Haogao Mechatronic Technology Co.,Ltd;University of Shanghai for Science and Technology ,201102Shanghai China )摘要:2009年我国政府发布了“装备制造业振兴规划”,液压气动密封基础件行业纳入其中,这说明液压工业由大向强的发展已纳入国家的战略范畴。
这是液压工业又一次腾飞的良好的战略机遇期。
作者见证了半个世纪来此行业的发展,将体会与思考奉献给同行及关心本行业的人。
对成为液压强国的目标提出明确的建议,也对我国液压方面的差距进行了尖锐的剖析。
并从市场发展的层面提出不同的策略。
文中有两个思路是值得同行思考的:液压的发展必须打破过去液压自身封闭发展的小圈子,与主机行业结合;必须将我国小散差的液压工业用市场的吸引力、资本运作的手段尽快地整合成符合中国特色的跨国公司形式,对市场有新布局,关键是必须有这样一批战略眼光的企业家。
一句话:液压行业要整合起来、走出去,形成辐射力,才能真正强起来。
关键词:液压工业发展战略;液压技术;市场策略;国家装备制造业振兴规划中图分类号:TH137文献标识码:A文章编号:1008-0813(2010)08-0001-05Abstract:“Plans to Reinvigorate Equipment Industry”has been announced by our government last year.The hydraulic,pneumatic and seal industry is included.That means hydraulic industry which has been in top position in global view without stronger enough meets the opportunity for its development within the government strategy.The author who is involved in this industry for half a centre would like to share his view to people who care this events.He proposes the criteria for what is stronger in this industry and points out what is weakness also.And from marketing view,he proposes the tactics for the hydraulic products in different market level.It is more important that the development of our hydraulic industry has to be differentiated its own way for itself only but for its OEM related.In the same time,the hydraulic industry should be integrated from small,diverse,and low quality mode into mult-type international mode by means of marketing and capital means to relocate the market.The key is to find out the enterprisers who own the international strategic views.In one words integrating itself and more opening to OEM in Chinese hydraulic industry is the way to stronger in global area ..Key Words:strategy on development of hydraulic industry;hydraulic technology;marketing for hydraulic products;government plans to reinvigorate equipment industry前言作为见证了我国半个世纪的液压气动工业与技术发展领域的一员,我既为我国液压行业从无到有、从小到大、从弱到可在世界上占据第二位的发展感到欣喜;也对我国的液压行业只大不够强的局面感到焦虑。
液压技术的发展现状和趋势
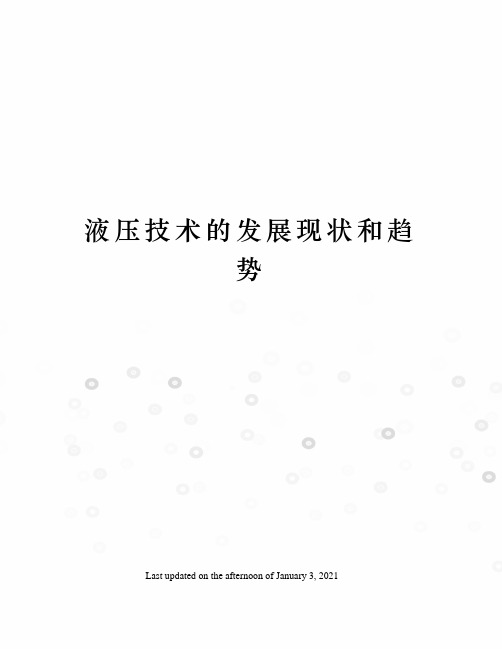
液压技术的发展现状和趋势Last updated on the afternoon of January 3, 2021内蒙古科技大学课程论文论文题目液压传动技术现状及趋势学生姓名刘颖学号专业班级机09-9班指导老师钟金豹液压技术的发展现状及趋势摘要:液压与气压传动相对于机械传动来说是一门新兴技术。
二十一世纪国内外的液压技术日渐走向成熟,但由于液压技术存在的一些优缺点,导致液压技术的发展速度受限。
本文介绍了液压传动技术的一些优缺点和国内外液压技术的一些发展状况和趋势。
关键词:液压技术发展趋势发展现状新兴技术国内外液压液压与气压传动相对于机械传动来说是一门新兴技术。
从1795年世界上第一台水压机诞生起,已有几百年的历史,液压传动技术被广泛采用和有较大幅度的发展是由19世纪崛起并蓬勃发展的石油工业推动起来的,最早实践成功的液压传动装置是舰船上的炮塔转位器,其后出现了液压六角车床和磨床,一些通用车床到20世纪30年代末才用上了液压传动。
第二次世界大战期间,在一些兵器上用上了功率大,反应快,动作准的液压传动和控制装置,大大提高了兵器的性能,也大大促进了液压技术的发展。
战后,液压技术迅速转向民用,并随着各种标准的不断制订和完善,各类元件的标准化,规格化,系列化而在机械制造,工程机械,材料科学,控制技术,农业机械,汽车制造等行业中推广开来。
由于军事及建设需要的刺激,液压技术日益成熟。
20世纪60年代后,原子能技术,空间技术,计算机技术等的发展再次将液压技术推向前进,使它发展成为包括传动,控制,检测在内的一门完整的自动化技术,在国民经济的各个方面都得到了应用。
如工程机械,数控加工中心,冶金自动线等。
液压传动在某些领域内甚至已占有压倒性优势。
液压传动是以流体作为工作介质对能量进行传动和控制的一种传动形式。
利用有压的液体经由一些机件控制之后来传递运动和动力。
因而在工程机械、冶金、军工、农机、汽车、轻纺、船舶、石油、航空和机床行业中,液压技术得到了普遍的应用。
全球液压行业竞争格局分析

全球液压行业竞争格局分析一、液压行业下游应用产品分类液压核心元件广泛应用于各行业的各类主机产品和技术装备,如农业机械、工程建筑机械、塑料机械、机床、汽车、船舶、轻纺医药机械等各类主机,以及航空航天、兵器装备、冶金矿山、石油化工、电力能源、信息电子、交通车辆等重大技术装备。
事实上,应用在不同领域的液压件在精度、智能化和价格方面存在较大差异。
通常来说,在农业机械等领域使用的液压件要求较低,而在航空航天、船舶制造等领域使用的液压件往往需要在精度、响应速度和可靠性方面具备优势。
二、液压行业发展现状液压产品的下游行业分布广泛,我国液压件市场的下游行业以工程机械、汽车、重型机械、机床工具为主,2019年工程机械行业在液压行业中的应用占比达40.5%,是液压产品最主要的应用行业,航空航天行业在液压行业的应用占比为8.7%,占比仅次于工程机械。
中国为全球液压行业第二大市场。
2019年液压件全球销售规模达316亿欧元,同比增长5.69%,全球液压工业已进入相对稳定、成熟阶段,液压件应用范围不断拓宽,未来液压行业市场前景向好。
液压行业的市场规模与一国经济总量和工业化水平高度相关,美国、中国、日本、德国、法国是全球液压销售的前五位国家,近几年来看,美国、中国、欧洲的液压市场呈现稳步扩张趋势。
2019年中国液压件市场规模达95.2亿欧元,同比增长4.9%,市场份额从2015年的27.7%迅速提升至2019年的30.2%,美国销售额占比为38%位居行业第一。
泵、阀、油缸、马达为液压系统的核心元件,产品技术难度大、价值量占比高。
在液压系统的5个部分中,泵、阀、油缸、马达的技术难度大、产品附加值高、价值占比高,是液压系统的核心元件。
国内液压市场中以油缸、泵、阀为代表的关键零部件比重较高,2019年合计占比达62.9%,油缸、泵、阀占比分别为34.4%、16.1%、12.4%。
三、液压行业竞争格局德、美、日液压产业全球领先,孕育行业巨头百年老店。
关于编制液压舵机项目可行性研究报告编制说明

液压舵机项目可行性研究报告编制单位:北京中投信德国际信息咨询有限公司编制时间:高级工程师:高建关于编制液压舵机项目可行性研究报告编制说明(模版型)【立项 批地 融资 招商】核心提示:1、本报告为液压舵机形式,客户下载后,可根据报告内容说明,自行修改,补充上自己项目的数据内容,即可完成属于自己,高水准的一份可研报告,从此写报告不在求人。
2、客户可联系我公司,协助编写完成可研报告,可行性研究报告大纲(具体可跟据客户要求进行调整)编制单位:北京中投信德国际信息咨询有限公司专业撰写节能评估报告资金申请报告项目建议书商业计划书可行性研究报告目录第一章总论 (1)1.1项目概要 (1)1.1.1项目名称 (1)1.1.2项目建设单位 (1)1.1.3项目建设性质 (1)1.1.4项目建设地点 (1)1.1.5项目主管部门 (1)1.1.6项目投资规模 (2)1.1.7项目建设规模 (2)1.1.8项目资金来源 (3)1.1.9项目建设期限 (3)1.2项目建设单位介绍 (3)1.3编制依据 (3)1.4编制原则 (4)1.5研究范围 (5)1.6主要经济技术指标 (5)1.7综合评价 (6)第二章项目背景及必要性可行性分析 (7)2.1项目提出背景 (7)2.2本次建设项目发起缘由 (7)2.3项目建设必要性分析 (7)2.3.1促进我国液压舵机产业快速发展的需要 (8)2.3.2加快当地高新技术产业发展的重要举措 (8)2.3.3满足我国的工业发展需求的需要 (8)2.3.4符合现行产业政策及清洁生产要求 (8)2.3.5提升企业竞争力水平,有助于企业长远战略发展的需要 (9)2.3.6增加就业带动相关产业链发展的需要 (9)2.3.7促进项目建设地经济发展进程的的需要 (10)2.4项目可行性分析 (10)2.4.1政策可行性 (10)2.4.2市场可行性 (10)2.4.3技术可行性 (11)2.4.4管理可行性 (11)2.4.5财务可行性 (11)2.5液压舵机项目发展概况 (12)2.5.1已进行的调查研究项目及其成果 (12)2.5.2试验试制工作情况 (12)2.5.3厂址初勘和初步测量工作情况 (13)2.5.4液压舵机项目建议书的编制、提出及审批过程 (13)2.6分析结论 (13)第三章行业市场分析 (15)3.1市场调查 (15)3.1.1拟建项目产出物用途调查 (15)3.1.2产品现有生产能力调查 (15)3.1.3产品产量及销售量调查 (16)3.1.4替代产品调查 (16)3.1.5产品价格调查 (16)3.1.6国外市场调查 (17)3.2市场预测 (17)3.2.1国内市场需求预测 (17)3.2.2产品出口或进口替代分析 (18)3.2.3价格预测 (18)3.3市场推销战略 (18)3.3.1推销方式 (19)3.3.2推销措施 (19)3.3.3促销价格制度 (19)3.3.4产品销售费用预测 (20)3.4产品方案和建设规模 (20)3.4.1产品方案 (20)3.4.2建设规模 (20)3.5产品销售收入预测 (21)3.6市场分析结论 (21)第四章项目建设条件 (22)4.1地理位置选择 (22)4.2区域投资环境 (23)4.2.1区域地理位置 (23)4.2.2区域概况 (23)4.2.3区域地理气候条件 (24)4.2.4区域交通运输条件 (24)4.2.5区域资源概况 (24)4.2.6区域经济建设 (25)4.3项目所在工业园区概况 (25)4.3.1基础设施建设 (25)4.3.2产业发展概况 (26)4.3.3园区发展方向 (27)4.4区域投资环境小结 (28)第五章总体建设方案 (29)5.1总图布置原则 (29)5.2土建方案 (29)5.2.1总体规划方案 (29)5.2.2土建工程方案 (30)5.3主要建设内容 (31)5.4工程管线布置方案 (32)5.4.1给排水 (32)5.4.2供电 (33)5.5道路设计 (35)5.6总图运输方案 (36)5.7土地利用情况 (36)5.7.1项目用地规划选址 (36)5.7.2用地规模及用地类型 (36)第六章产品方案 (38)6.1产品方案 (38)6.2产品性能优势 (38)6.3产品执行标准 (38)6.4产品生产规模确定 (38)6.5产品工艺流程 (39)6.5.1产品工艺方案选择 (39)6.5.2产品工艺流程 (39)6.6主要生产车间布置方案 (39)6.7总平面布置和运输 (40)6.7.1总平面布置原则 (40)6.7.2厂内外运输方案 (40)6.8仓储方案 (40)第七章原料供应及设备选型 (41)7.1主要原材料供应 (41)7.2主要设备选型 (41)7.2.1设备选型原则 (42)7.2.2主要设备明细 (43)第八章节约能源方案 (44)8.1本项目遵循的合理用能标准及节能设计规范 (44)8.2建设项目能源消耗种类和数量分析 (44)8.2.1能源消耗种类 (44)8.2.2能源消耗数量分析 (44)8.3项目所在地能源供应状况分析 (45)8.4主要能耗指标及分析 (45)8.4.1项目能耗分析 (45)8.4.2国家能耗指标 (46)8.5节能措施和节能效果分析 (46)8.5.1工业节能 (46)8.5.2电能计量及节能措施 (47)8.5.3节水措施 (47)8.5.4建筑节能 (48)8.5.5企业节能管理 (49)8.6结论 (49)第九章环境保护与消防措施 (50)9.1设计依据及原则 (50)9.1.1环境保护设计依据 (50)9.1.2设计原则 (50)9.2建设地环境条件 (51)9.3 项目建设和生产对环境的影响 (51)9.3.1 项目建设对环境的影响 (51)9.3.2 项目生产过程产生的污染物 (52)9.4 环境保护措施方案 (53)9.4.1 项目建设期环保措施 (53)9.4.2 项目运营期环保措施 (54)9.4.3环境管理与监测机构 (56)9.5绿化方案 (56)9.6消防措施 (56)9.6.1设计依据 (56)9.6.2防范措施 (57)9.6.3消防管理 (58)9.6.4消防设施及措施 (59)9.6.5消防措施的预期效果 (59)第十章劳动安全卫生 (60)10.1 编制依据 (60)10.2概况 (60)10.3 劳动安全 (60)10.3.1工程消防 (60)10.3.2防火防爆设计 (61)10.3.3电气安全与接地 (61)10.3.4设备防雷及接零保护 (61)10.3.5抗震设防措施 (62)10.4劳动卫生 (62)10.4.1工业卫生设施 (62)10.4.2防暑降温及冬季采暖 (63)10.4.3个人卫生 (63)10.4.4照明 (63)10.4.5噪声 (63)10.4.6防烫伤 (63)10.4.7个人防护 (64)10.4.8安全教育 (64)第十一章企业组织机构与劳动定员 (65)11.1组织机构 (65)11.2激励和约束机制 (65)11.3人力资源管理 (66)11.4劳动定员 (66)11.5福利待遇 (67)第十二章项目实施规划 (68)12.1建设工期的规划 (68)12.2 建设工期 (68)12.3实施进度安排 (68)第十三章投资估算与资金筹措 (69)13.1投资估算依据 (69)13.2建设投资估算 (69)13.3流动资金估算 (70)13.4资金筹措 (70)13.5项目投资总额 (70)13.6资金使用和管理 (73)第十四章财务及经济评价 (74)14.1总成本费用估算 (74)14.1.1基本数据的确立 (74)14.1.2产品成本 (75)14.1.3平均产品利润与销售税金 (76)14.2财务评价 (76)14.2.1项目投资回收期 (76)14.2.2项目投资利润率 (77)14.2.3不确定性分析 (77)14.3综合效益评价结论 (80)第十五章风险分析及规避 (82)15.1项目风险因素 (82)15.1.1不可抗力因素风险 (82)15.1.2技术风险 (82)15.1.3市场风险 (82)15.1.4资金管理风险 (83)15.2风险规避对策 (83)15.2.1不可抗力因素风险规避对策 (83)15.2.2技术风险规避对策 (83)15.2.3市场风险规避对策 (83)15.2.4资金管理风险规避对策 (84)第十六章招标方案 (85)16.1招标管理 (85)16.2招标依据 (85)16.3招标范围 (85)16.4招标方式 (86)16.5招标程序 (86)16.6评标程序 (87)16.7发放中标通知书 (87)16.8招投标书面情况报告备案 (87)16.9合同备案 (87)第十七章结论与建议 (89)17.1结论 (89)17.2建议 (89)附表 (90)附表1 销售收入预测表 (90)附表2 总成本表 (91)附表3 外购原材料表 (92)附表4 外购燃料及动力费表 (93)附表5 工资及福利表 (95)附表6 利润与利润分配表 (96)附表7 固定资产折旧费用表 (97)附表8 无形资产及递延资产摊销表 (98)附表9 流动资金估算表 (99)附表10 资产负债表 (101)附表11 资本金现金流量表 (102)附表12 财务计划现金流量表 (104)附表13 项目投资现金量表 (106)附表14 借款偿还计划表 (108) (112)第一章总论总论作为可行性研究报告的首章,要综合叙述研究报告中各章节的主要问题和研究结论,并对项目的可行与否提出最终建议,为可行性研究的审批提供方便。
中国液压气动工业的现状与展望探析

中国液压气动工业的现状与展望探析我国液压气动工业已经发展了将近半个世纪,其发展历程经历了从无到有、从小到大的过程,如今已经在世界上占有一席之地。
虽然我国的液压气动工业已经发展到可喜可贺的地步,但是其发展历程还不是完美无缺的,因此本文通过对液压气动工业的发展现状、存在问题等进行分析,提出行之有效的解决措施,并对未来的发展做出展望。
1 液压气动工业的发展现状1.1液压气动产品的类型我国液压气动工业经过半个世纪的努力逐渐形成一个系统化、专业化体系,已经具备了一定的技术水平和生产能力,可以基本上满足农业机械、工程机械、冶金、煤炭、矿山、机床、塑机、造船、纺织、兵器、轻工、航空、航天工业等行业的需求。
而且大型成套设备的配套率已经超过了60%。
到2013年统计发现,我国液压气动工业生产厂家已经超过了500家,从事液压技术研究的机构超过50多个,并且在30多所高校内部设置了机电一体化和流体传动课程。
在天津工程机械研究所、广州机械科学研究院、农业机械研究院等机构设置了液压质量检测中心。
改革开放以来,对液压气动产品进行了引进消化、科技攻关、创新等一系列举措,并取得了不错的效果,基本上满足了部分高端市场1/ 10和国产机电的需要。
不少产品如齿轮泵、柱塞泵和马达、高压阀门、叶片泵、滤油器等产品已经成为国家生产的主导产品,有些产品已经与国际化接轨,并出口到欧美等发达国家。
目前我国主要的液压气动产品种类比较多,主要包括以下几大类。
1.1.1齿轮泵目前我国能够生产的齿轮泵类型约有30多个系列,能够很好的满足我国农业机械、工程机械和车辆等行业需要。
其排量在0.6-200cc/r,压力分别为16、20、25、28MPa,其中CBN高压系列每年的产量就已经超过了200万台,并且在农业机械中得到了广泛的应用。
而中高压齿轮泵(压力在20、25MPa),一般采用径向平衡、间歇浮动补偿、DU润滑轴承等常用技术,壳体采用了高强度球墨铸铁和高强度合金2种材料,致使该类产品的性能已经达到了国际水准,并广泛应用于推土机、装载机、自装卸汽车和平地机等,能够很好的满足工程机械需要。
液压技术的发展现状与趋势

液压技术的发展现状与趋势液压技术是一种以液体为工作介质,通过液体传递能量和控制信号,实现机械运动的技术。
液压技术应用广泛,涉及工程机械、冶金设备、航空航天、汽车工业等各个领域。
近年来,随着科技的不断进步,液压技术也在不断发展壮大。
本文将探讨液压技术的发展现状,分析其趋势,并展望未来的发展方向。
一、液压技术的发展现状1. 技术应用方面液压技术作为一种高效、可靠的动力传输和控制方式,已广泛应用于航空航天、工程机械、冶金设备、船舶、汽车工业等领域。
在航空航天领域,液压技术被用于飞机的起落架、飞行控制系统等;在工程机械领域,液压技术被应用于挖掘机、起重机、装载机等设备的动力传输和控制系统中;在汽车工业领域,液压制动系统、悬挂系统等也是液压技术的应用范畴。
随着科技的发展,液压技术不断拓展应用领域,成为各行各业的不可或缺的技术手段。
2. 技术发展水平液压技术的核心在于液压元件的研发和制造。
目前,国内外液压元件制造商在液压泵、阀、缸、管路等方面技术水平已经相当成熟,各类液压元件的性能和质量得到了大幅提升。
智能化、高效化、节能化成为了液压技术发展的主要方向,新型的智能液压元件和系统不断涌现,为液压技术的推广应用提供了新的动力和支撑。
3. 技术瓶颈尽管液压技术目前已经取得了很大的进步,但在一些领域还存在着一些瓶颈问题。
传统液压系统存在能源消耗较大、噪音较高、维护成本较高等问题,这些问题制约了液压技术在一些领域的发展和应用。
液压技术在高温、低温、腐蚀等特殊环境下应用较为困难,需要更好的材料和密封技术加以解决。
二、液压技术的发展趋势1. 智能化随着人工智能、云计算、大数据等技术的发展,液压技术也将向智能化方向发展。
智能液压元件和系统将更好地满足工业自动化、智能制造的需求,实现设备的智能监测、诊断和维护,提高生产效率和降低能耗。
2. 高效化高效化是未来液压技术的一个重要趋势。
通过减小系统油路阻力、提高元件工作效率、优化系统控制策略等手段,实现液压系统的能源消耗降低,工作效率提高,从而降低生产成本、减少资源浪费。
2023年液压行业市场分析现状

2023年液压行业市场分析现状液压行业是指以液压原理为基础,利用液压油传递力量和控制运动的行业。
液压行业广泛应用于各个领域,如工程机械、冶金设备、矿山设备、航空航天、军工等。
目前,液压行业市场发展态势良好,呈现出以下几个特点:1. 市场需求稳定增长。
随着国民经济的快速发展和技术的不断进步,各个行业对液压技术的需求不断增加。
比如,工程机械行业对液压系统的需求量巨大,冶金设备行业对大型液压机的需求不断增加等。
液压行业市场潜力巨大。
2. 技术水平不断提高。
随着科技的进步,液压技术也在不断地发展和改进。
液压控制系统的自动化、数字化程度越来越高,使得液压设备的性能和效率得到了大幅提升。
同时,液压系统的设计和制造技术也在不断创新,提高了产品的可靠性和使用寿命。
3. 产品结构不断优化升级。
随着市场需求的变化和技术进步,液压产品的结构也在不断优化和升级。
传统的液压系统逐渐向集成化、小型化、模块化的方向发展,减小了体积和重量,提高了性能和效率。
同时,液压马达、液压缸等液压元件的设计也在不断创新,提高了产品的性能和可靠性。
4. 市场竞争激烈。
液压行业市场竞争激烈,液压产品的价格相对较高,技术门槛较高,进入市场的难度也相对较大。
但是,随着市场的扩大和技术的进步,液压行业市场的竞争将更加激烈。
企业需要通过提高产品质量、降低成本、不断创新等方式提升竞争力。
在液压行业市场分析的基础上,可以得出以下几点对市场前景的看法:1. 市场前景广阔。
随着国民经济的快速发展和技术的进步,各个行业对液压技术的需求不断增加。
特别是工程机械、冶金设备、矿山设备等行业的需求量巨大。
预计未来几年,液压行业市场将继续保持稳定增长。
2. 技术创新是市场发展的关键。
随着市场竞争的加剧,液压企业需要不断创新,提高产品的性能和可靠性。
同时,企业还需要加强与科研机构、高校等的合作,共同推动液压技术的创新和发展。
3. 环保节能成为市场发展的重要方向。
随着全球环保意识的逐渐增强,液压行业也面临着环保压力。
液压行业发展前景

液压行业发展前景液压技术是一种应用广泛的传动和控制技术,主要包括液压元件、液压传动、液压控制、液压系统等方面。
液压行业作为工程机械、航空航天、汽车车辆、冶金能源等各个领域的重要支持产业,其发展前景非常广阔。
首先,液压技术在工程机械领域有着广泛的应用前景。
随着我国基础设施建设的不断推进,工程机械市场需求持续增长。
液压技术在挖掘机、装载机、起重机等工程机械中发挥着重要作用,提高了机械的工作效率和准确性。
随着技术的进步和需求的增长,液压系统将进一步得到应用和发展。
其次,航空航天领域也是液压技术的重要应用方向。
航空航天领域对液压技术的要求非常高,要求系统工作稳定、可靠、高效。
液压技术在飞机起落架、飞行操纵系统、气动减震系统等方面发挥着至关重要的作用。
随着我国航空航天事业的快速发展,液压技术的需求将会持续增长。
此外,汽车车辆领域也是液压技术的重要应用领域。
液压制动系统、液压悬挂系统、液压转向系统等都是汽车车辆中广泛采用液压技术的部分。
随着汽车工业的不断发展和消费者对车辆安全性和舒适性的要求提高,液压技术在汽车行业中的应用前景将会更加广阔。
最后,冶金能源领域也是液压技术的重要应用领域。
在高炉、矿山、电力站等冶金工业和能源工业中,液压技术在各种设备和系统中发挥着重要作用。
液压系统可以实现对材料和能源的高效利用,提高生产效率和节能减排。
随着我国工业化进程的加快和能源领域的重点发展,液压技术在冶金能源领域的应用前景将会更加广泛。
综上所述,液压行业发展前景非常广阔。
随着我国经济的快速发展和工业化进程的加快,液压技术的需求将会持续增长。
同时,随着技术的进步和应用领域的拓展,液压技术将会得到更广泛的应用和发展。
因此,液压行业将会成为一个有着很大发展潜力和市场前景的行业。
2024-2030年中国舵机市场研究与市场运营趋势报告

2024-2030年中国舵机市场研究与市场运营趋势报告舵机,是指在自动驾驶仪中操纵飞机舵面(操纵面)转动的一种执行部件。
分有:①电动舵机,由电动机、传动部件和离合器组成。
接受自动驾驶仪的指令信号而工作,当人工驾驶飞机时,由于离合器保持脱开而传动部件不发生作用。
②液压舵机,由液压作动器和旁通活门组成。
当人工驾驶飞机时,旁通活门打开,由于作动器活塞两边的液压互相连通而不妨害人工操纵。
此外,还有电动液压舵机,简称“电液舵机”。
舵机的大小由外舾装按照船级社的规范决定,选型时主要考虑扭矩大小。
如何审慎地选择经济且合乎需求的舵机,也是一门不可轻忽的学问。
产业研究报告网发布的《2024-2030年中国舵机市场研究与市场运营趋势报告》共十四章。
首先介绍了舵机行业市场发展环境、舵机整体运行态势等,接着分析了舵机行业市场运行的现状,然后介绍了舵机市场竞争格局。
随后,报告对舵机做了重点企业经营状况分析,最后分析了舵机行业发展趋势与投资预测。
您若想对舵机产业有个系统的了解或者想投资舵机行业,本报告是您不可或缺的重要工具。
本研究报告数据主要采用国家统计数据,海关总署,问卷调查数据,商务部采集数据等数据库。
其中宏观经济数据主要来自国家统计局,部分行业统计数据主要来自国家统计局及市场调研数据,企业数据主要来自于国统计局规模企业统计数据库及证券交易所等,价格数据主要来自于各类市场监测数据库。
报告目录:第一章舵机行业发展综述1.1 舵机行业定义及分类1.1.1 行业定义1.1.2 行业主要产品分类1.1.3 行业主要商业模式1.2 舵机行业特征分析1.2.1 产业链分析1.2.2 舵机行业在国民经济中的地位1.2.3 舵机行业生命周期分析(1)行业生命周期理论基础(2)舵机行业生命周期1.3 最近3-5年中国舵机行业经济指标分析1.3.1 赢利性1.3.2 成长速度1.3.3 附加值的提升空间1.3.4 进入壁垒/退出机制1.3.5 风险性1.3.6 行业周期1.3.7 竞争激烈程度指标1.3.8 行业及其主要子行业成熟度分析第二章舵机行业运行环境分析2.1 舵机行业政治法律环境分析2.1.1 行业管理体制分析2.1.2 行业主要法律法规2.1.3 行业相关发展规划2.2 舵机行业经济环境分析2.2.1 国际宏观经济形势分析2.2.2 国内宏观经济形势分析2.2.3 产业宏观经济环境分析2.3 舵机行业社会环境分析2.3.1 舵机产业社会环境2.3.2 社会环境对行业的影响2.3.3 舵机产业发展对社会发展的影响2.4 舵机行业技术环境分析2.4.1 舵机技术分析2.4.2 舵机技术发展水平2.4.3 行业主要技术发展趋势第三章我国舵机所属行业运行分析3.1 我国舵机行业发展状况分析3.1.1 我国舵机行业发展阶段3.1.2 我国舵机行业发展总体概况3.1.3 我国舵机行业发展特点分析3.2 2017-2022年舵机行业发展现状3.2.1 2017-2022年我国舵机行业市场规模3.2.2 2017-2022年我国舵机行业发展分析3.2.3 2017-2022年中国舵机企业发展分析3.3 区域市场分析3.3.1 区域市场分布总体情况3.3.2 2017-2022年重点省市市场分析3.4 舵机细分产品/服务市场分析3.4.1 细分产品/服务特色3.4.2 2017-2022年细分产品/服务市场规模及增速3.4.3 重点细分产品/服务市场前景预测3.5 舵机产品/服务价格分析3.5.1 2017-2022年舵机价格走势3.5.2 影响舵机价格的关键因素分析(1)成本(2)供需情况(3)关联产品(4)其他3.5.3 2024-2030年舵机产品/服务价格变化趋势3.5.4 主要舵机企业价位及价格策略第四章我国舵机所属行业整体运行指标分析4.1 2017-2022年中国舵机所属行业总体规模分析4.1.1 企业数量结构分析4.1.2 人员规模状况分析4.1.3 行业资产规模分析4.1.4 行业市场规模分析4.2 2017-2022年中国舵机所属行业产销情况分析4.2.1 我国舵机所属行业工业总产值4.2.2 我国舵机所属行业工业销售产值4.2.3 我国舵机所属行业产销率4.3 2017-2022年中国舵机所属行业财务指标总体分析4.3.1 行业盈利能力分析4.3.2 行业偿债能力分析4.3.3 行业营运能力分析4.3.4 行业发展能力分析第五章我国舵机行业供需形势分析5.1 舵机行业供给分析5.1.1 2017-2022年舵机行业供给分析5.1.2 2024-2030年舵机行业供给变化趋势5.1.3 舵机行业区域供给分析5.2 2017-2022年我国舵机行业需求情况5.2.1 舵机行业需求市场5.2.2 舵机行业客户结构5.2.3 舵机行业需求的地区差异5.3 舵机市场应用及需求预测5.3.1 舵机应用市场总体需求分析(1)舵机应用市场需求特征(2)舵机应用市场需求总规模5.3.2 2024-2030年舵机行业领域需求量预测(1)2024-2030年舵机行业领域需求产品/服务功能预测(2)2024-2030年舵机行业领域需求产品/服务市场格局预测5.3.3 重点行业舵机产品/服务需求分析预测第六章舵机行业产业结构分析6.1 舵机产业结构分析6.1.1 市场细分充分程度分析6.1.2 各细分市场领先企业排名6.1.3 各细分市场占总市场的结构比例6.1.4 领先企业的结构分析(所有制结构)6.2 产业价值链条的结构分析及产业链条的整体竞争优势分析6.2.1 产业价值链条的构成6.2.2 产业链条的竞争优势与劣势分析6.3 产业结构发展预测6.3.1 产业结构调整指导政策分析6.3.2 产业结构调整中消费者需求的引导因素6.3.3 中国舵机行业参与国际竞争的战略市场定位6.3.4 产业结构调整方向分析第七章我国舵机行业产业链分析7.1 舵机行业产业链分析7.1.1 产业链结构分析7.1.2 主要环节的增值空间7.1.3 与上下游行业之间的关联性7.2 舵机上游行业分析7.2.1 舵机产品成本构成7.2.2 2017-2022年上游行业发展现状7.2.3 2024-2030年上游行业发展趋势7.2.4 上游供给对舵机行业的影响7.3 舵机下游行业分析7.3.1 舵机下游行业分布7.3.2 2017-2022年下游行业发展现状7.3.3 2024-2030年下游行业发展趋势7.3.4 下游需求对舵机行业的影响第八章我国舵机行业渠道分析及策略8.1 舵机行业渠道分析8.1.1 渠道形式及对比8.1.2 各类渠道对舵机行业的影响8.1.3 主要舵机企业渠道策略研究8.1.4 各区域主要代理商情况8.2 舵机行业用户分析8.2.1 用户认知程度分析8.2.2 用户需求特点分析8.2.3 用户购买途径分析8.3 舵机行业营销策略分析8.3.1 中国舵机营销概况8.3.2 舵机营销策略探讨8.3.3 舵机营销发展趋势第九章我国舵机行业竞争形势及策略9.1 行业总体市场竞争状况分析9.1.1 舵机行业竞争结构分析(1)现有企业间竞争(2)潜在进入者分析(3)替代品威胁分析(4)供应商议价能力(5)客户议价能力(6)竞争结构特点总结9.1.2 舵机行业企业间竞争格局分析9.1.3 舵机行业集中度分析9.1.4 舵机行业SWOT分析9.2 中国舵机行业竞争格局综述9.2.1 舵机行业竞争概况(1)中国舵机行业竞争格局(2)舵机行业未来竞争格局和特点(3)舵机市场进入及竞争对手分析9.2.2 中国舵机行业竞争力分析(1)我国舵机行业竞争力剖析(2)我国舵机企业市场竞争的优势(3)国内舵机企业竞争能力提升途径9.2.3 舵机市场竞争策略分析第十章舵机行业领先企业经营形势分析10.1 A公司10.1.1 企业概况10.1.2 企业优势分析10.1.3 产品/服务特色10.1.4 公司经营状况10.1.5 公司发展规划10.2 B公司10.2.1 企业概况10.2.2 企业优势分析10.2.3 产品/服务特色10.2.4 公司经营状况10.2.5 公司发展规划10.3 C公司10.3.1 企业概况10.3.2 企业优势分析10.3.3 产品/服务特色10.3.4 公司经营状况10.3.5 公司发展规划10.4 D公司10.4.1 企业概况10.4.2 企业优势分析10.4.3 产品/服务特色10.4.4 公司经营状况10.4.5 公司发展规划10.5 E公司10.5.1 企业概况10.5.2 企业优势分析10.5.3 产品/服务特色10.5.4 公司经营状况10.5.5 公司发展规划10.6 F公司10.6.1 企业概况10.6.2 企业优势分析10.6.3 产品/服务特色10.6.4 公司经营状况10.6.5 公司发展规划第十一章2024-2030年舵机行业投资前景11.1 2024-2030年舵机市场发展前景11.1.1 2024-2030年舵机市场发展潜力11.1.2 2024-2030年舵机市场发展前景展望11.1.3 2024-2030年舵机细分行业发展前景分析11.2 2024-2030年舵机市场发展趋势预测11.2.1 2024-2030年舵机行业发展趋势11.2.2 2024-2030年舵机市场规模预测11.2.3 2024-2030年舵机行业应用趋势预测11.2.4 2024-2030年细分市场发展趋势预测11.3 2024-2030年中国舵机行业供需预测11.3.1 2024-2030年中国舵机行业供给预测11.3.2 2024-2030年中国舵机行业需求预测11.3.3 2024-2030年中国舵机供需平衡预测11.4 影响企业生产与经营的关键趋势11.4.1 市场整合成长趋势11.4.2 需求变化趋势及新的商业机遇预测11.4.3 企业区域市场拓展的趋势11.4.4 科研开发趋势及替代技术进展11.4.5 影响企业销售与服务方式的关键趋势第十二章2024-2030年舵机行业投资机会与风险12.1 舵机行业投融资情况12.1.1 行业资金渠道分析12.1.2 固定资产投资分析12.1.3 兼并重组情况分析12.2 2024-2030年舵机行业投资机会12.2.1 产业链投资机会12.2.2 细分市场投资机会12.2.3 重点区域投资机会12.3 2024-2030年舵机行业投资风险及防范12.3.1 政策风险及防范12.3.2 技术风险及防范12.3.3 供求风险及防范12.3.4 宏观经济波动风险及防范12.3.5 关联产业风险及防范12.3.6 产品结构风险及防范12.3.7 其他风险及防范第十三章舵机行业投资战略研究13.1 舵机行业发展战略研究13.1.1 战略综合规划13.1.2 技术开发战略13.1.3 业务组合战略13.1.4 区域战略规划13.1.5 产业战略规划13.1.6 营销品牌战略13.1.7 竞争战略规划13.2 对我国舵机品牌的战略思考13.2.1 舵机品牌的重要性13.2.2 舵机实施品牌战略的意义13.2.3 舵机企业品牌的现状分析13.2.4 我国舵机企业的品牌战略13.2.5 舵机品牌战略管理的策略13.3 舵机经营策略分析13.3.1 舵机市场细分策略13.3.2 舵机市场创新策略13.3.3 品牌定位与品类规划13.3.4 舵机新产品差异化战略13.4 舵机行业投资战略研究13.4.1 2022年舵机行业投资战略13.4.2 2024-2030年舵机行业投资战略13.4.3 2024-2030年细分行业投资战略第十四章研究结论及投资建议14.1 舵机行业研究结论14.2 舵机行业投资价值评估()14.3 舵机行业投资建议14.3.1 行业发展策略建议14.3.2 行业投资方向建议14.3.3 行业投资方式建议。
液压控制技术及发展方向

液压控制技术及发展方向一、前言液压及控制技术是一种应用极为广泛的基础技术,在国民经济各领域中获得了极为广泛的应用。
我国的液压及控制技术长期落后于国外,严重制约了中国主机水平的提高和工业自动化的实现,因而迅速提高我国液压技术和控制技术的水平具有极为重要的经济意义和现实意义【1】。
在传统的液压传动中,是通过各种液压阀来控制普通油缸的运动方向、速度和位置的。
为了满足各种要求,液压先驱者们,经过近百年的不断努力,发明和生产了上百种规格的液压元件和产品。
但为了获得精确的控制,普通的液压元件已经不能满足要求【1】。
自二十世纪七十年代以来,随着以微电子技术为主导的信息技术、生物技术、新材料技术、新能源技术、空间技术、海洋开发技术等高技术群的蓬勃发展,在世界上逐步出现了机械电子工业、光电子工业、办公自动化设备、信息处理系统、电子医疗设备、现代生物制品、新材料、新能源等高技术产业。
流体传动与控制技术就是其中的机械电子技术产业中起重要作用的关键技术领域。
流体传动及控制包括液压传动及控制与气体传动与控制两个方面。
液压传动及控制技术应用于生产开始于十七世纪,经历了二百多年的徘徊,直到二十世纪四十年代,才进人了高速发展时期。
气动技术的应用历史虽然久远,但真正应用于生产是在十八世纪,其应用与研究则在二十世纪五十年代才开始被重视。
控制论的出现,特别是自动控制理论与技术的发展,使流体传动及控制技术取得了飞速的进步。
目前,流体传动及控制技术已经在冶金、煤炭、石油、化工、能源、航空、航天、国防等领域广泛应用,成为国民经济发展中不可缺少的支撑技术。
【2】二、液压技术的发展液压技术是以液体(主要是矿物油)为工作介质,实现能量传递、转换、分配及控制的一门技术。
液压技术的发展总是与当代的高新技术紧密结合在一起的。
二十世纪四十年代控制论的诞生,极大地促进了液压技术的快速发展,使其应用范围逐渐扩大,不仅在国防领域具有不可替代的地位,而且已经渗透到国民经济的各个行业,液压技术发展与应用的程度已成为衡量一个国家工业发展水平的重要标志。
液压技术简介与发展趋势

生物可降解环保型液压油是指既能满足液压系统 的要求,其耗损产物又对环境不造成危害的液压油。润滑 油的可生物降解特性是其特性中最主要的指标。可生物降 解性指物质被活性有机体通过生物作用分解为简单化合物 如CO2和H2O的能力。
30
环保型液压油的发展
环保型液压油的组成
环保型液压油的组成
船舶控制工程实验室在某型号收放式减摇鳍的随动系统中用 电液比例阀取代传统的电液伺服阀,设计了减摇鳍电液比例 控制系统,下图为之前的伺服控制和改进后的比例控制
39
电液比例技术
电液比例技术的应用:
1在冶金行业中的应用 冶金机械正在向大型化、连续化、高速化和自动化的方向发展。在电解极板加工 机组中运用电液比例技术后,其传动的可靠性、控制精度、稳定性和生产效率都 大幅提高,降低了生产成本;而运用电液比例控制系统设计的冶金冷却回路,提 高了系统元件的使用寿命,便于快速故障诊断和响应。 2在工程机械中的应用 利用电液比例阀代替布置在工程机械操控室的多路阀,提高了主机总体设计的柔 性,改善了操作特性。在汽车起重机中的起升机构、伸缩机构和防止二次起升下 滑机构的控制系统中,都运用了电液比例换向阀,保证了起重机作业的可靠性。 3在矿山机械中的应用 在带式输送机的自动张紧装置中,布置电液比例方向阀来控制张紧油缸的动作, 或用比例溢流阀控制液压马达的输出扭矩来实现张紧力的适时控制。
7
高压化
8
高压化
(2)液压挖掘机
现有的液压挖掘机基本上都是开回路的, 平均使用压力在28~35MPa之间。这是因为日本的液 压挖掘机可作多种用途,作业人员往往更重视挖掘 机的操作性能。认为高压化会引起操作性能的恶化 ,因此使用压力一直停顿在目前的水平上。但是, 今后如能与载荷传感器或电子控制器等相融合,那 即使压力升高,也不会降低操作性能,也就是说液 压挖掘机的油压可达到35~42MPa级水平。
中国舵轮行业发展现状
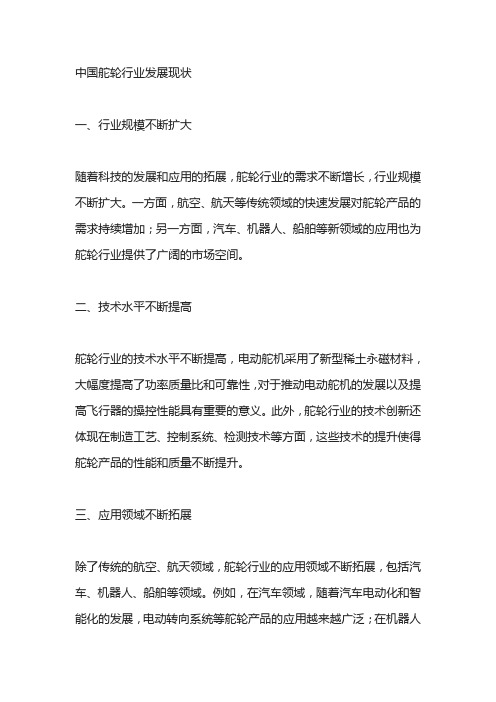
中国舵轮行业发展现状
一、行业规模不断扩大
随着科技的发展和应用的拓展,舵轮行业的需求不断增长,行业规模不断扩大。
一方面,航空、航天等传统领域的快速发展对舵轮产品的需求持续增加;另一方面,汽车、机器人、船舶等新领域的应用也为舵轮行业提供了广阔的市场空间。
二、技术水平不断提高
舵轮行业的技术水平不断提高,电动舵机采用了新型稀土永磁材料,大幅度提高了功率质量比和可靠性,对于推动电动舵机的发展以及提高飞行器的操控性能具有重要的意义。
此外,舵轮行业的技术创新还体现在制造工艺、控制系统、检测技术等方面,这些技术的提升使得舵轮产品的性能和质量不断提升。
三、应用领域不断拓展
除了传统的航空、航天领域,舵轮行业的应用领域不断拓展,包括汽车、机器人、船舶等领域。
例如,在汽车领域,随着汽车电动化和智能化的发展,电动转向系统等舵轮产品的应用越来越广泛;在机器人
领域,舵轮作为驱动器的重要组成部分,广泛应用于机器人的关节驱动系统中;在船舶领域,舵轮用于控制船舶航向和稳定性,对于提高船舶的操纵性能和安全性具有重要作用。
四、市场竞争日益激烈
随着市场规模的扩大,舵轮行业的竞争日益激烈,企业需要加强技术创新和产品质量提升,提高市场竞争力。
一方面,国内企业需要通过技术创新和产品质量提升来应对国际品牌的竞争;另一方面,国内企业也需要加强合作,通过资源整合和优势互补来提高整体竞争力。
综上所述,中国舵轮行业在规模、技术水平、应用领域和市场竞争力等方面都取得了长足的进步。
然而,面对未来的发展机遇和挑战,舵轮行业还需要进一步加强技术创新和产品质量提升,以适应不断变化的市场需求和应用场景。
- 1、下载文档前请自行甄别文档内容的完整性,平台不提供额外的编辑、内容补充、找答案等附加服务。
- 2、"仅部分预览"的文档,不可在线预览部分如存在完整性等问题,可反馈申请退款(可完整预览的文档不适用该条件!)。
- 3、如文档侵犯您的权益,请联系客服反馈,我们会尽快为您处理(人工客服工作时间:9:00-18:30)。
中国液压舵机行业发展概述
液压舵机是近代船舶工业的科技进步的体现,我们可以从八十年代开始追溯舵机以及液压舵机更新换代的十年发展过程。
引起这种更新的原因主要有二方面。
最直接的原因是:1978年装有22万吨轻厥油的美国油轮阿莫戈.卡迪兹号在途经法国西北海面对因舵机失灵而触礁,造成严重污染和重大经济损失。
为此,舵机在紧急情况下的可靠性引起了国际上的普遍关注。
经煞一段时间酝酿,1981年国际海事会议正式通过了对1974年SOLAS公约的修正案,其中对舵机的要求提出了重要的新条款。
修正案明确规定:1万总吨及以上的油轮(包括化学品船、液化气运输船)的舵机动力执行系统应符合“单项故障原则”,即除了舵柄(或舵扇)或舵执行器卡住外,任何其它部分发生单项故障,应能在45秒内恢复操舵能力。
这就要求舵机有二个独立的液压系统,或者能各自单独工作满足要求,或者平时共同工作,而任一系统液体流失时能自动检铡和自动隔离,使另一系统仍能保持工作,以保持50%的扭矩。
而1万总吨以上、十万载重吨以下的油轮采用单一的舵执行器时(倒如一般单缸体的转叶式油缸),如设计、材料和密封。
试验检查等符合严格的专门规定,可不对舵执行嚣提出单项故障的要求。
舵机更新的另一原因,是液压传动技术从七十年代以来一直在迅速发展,产品的高压化和集成化不断取得进展,逻辑阀、比例阀等新型液压元件开始应用于舵机和其它船用液压装置中,另外,舵机电气遥控系统的技术也更趋成熟,不仅淘汰了液压遥控系统,而且使传
统的浮动杆机械追随机构也显得陈旧。
进入八十年代以来,世界舵机主要制造厂家都开始认真检查其产品,并按1981年修正案的要求重新设计各自的舵机,力争在市场上保持较大的竞争优势。
新一代的液压舵机的性能和可靠性更趋完善。
归纳起来目前液压舵机变化动向如下:
1.普遍设置了油箱液位报警开关,并设置了两套液压系统的人工和自动隔离装置。
这种自动隔离装置具有代表性的是采用电液换向阀的装置。
生产转叶舵机相当长历史的挪威富利登渡公司认为上述方案使设备复杂化,产品价格较贵,而且某些阀正常工作时长期不动,紧急情况能否正常动怍使难于保证,因而又提出了一种仅采用二个主油路自动锁闭阁来隔离损坏的油路系统的方案。
这种方案仅适台于转叶式油缸,它在缸体内部设有油路连通相应油腔,但如果一对油腔密封损坏时,并不能使之与工作油路隔离。
显然,单缸体的转叶式油缸如发生故障(如密封损坏、动叶断裂等),是不能接单项故障原则迅速恢复工作的,因此它不能用于10万载重吨以上的油轮。
为此,日本三井一AEG公司提出了双油缸体转叶舵机的设计,它将二个转叶油缸迭置在同一舵杆上方,其二套油路系统之一可以被隔离和旁通,以适应10万载重吨以上油轮的要求
2.阀控型舵机的应用功率范围在扩大,性能也在改善。
阀控型舵机因稳舵时主油泵仍需全流量工作,虽然排出压力小,但仍要消耗一定的功率,故经济性较差,而且换向时液压冲击大,故
过去多用于功率较小的舵机。
现在随着阀控型舵机设计的改善,扭矩范围也有了显著提高。
例如西德哈特拉帕R系列阀控型舵机最大公称扭矩已达到1200KNM,完全能胜任一般数万吨级海船的需要。
阀控型舵机液压系统的发展趋向是取消辅泵。
这种舵机采用辅泵的主要用途是为电液换向阀提供控制油。
取消辅泵,由主泵本身为电液换向阀提供控制油,可以减少设备,提高可靠性。
但主泵在换向阀位于中位(稳航)时需要卸荷,即排油直通油箱,为了保持换向阀所需要的最低控制油压(一般不超过1 MPA),不得不在主泵回油管上增设背压阀,这就使稳舵时主泵功率损失增加。
哈特拉帕舵机稳舵时用先导溢流阀卸荷,较好地解决了这个问题。
挪威生产的闷控型转叶式舵机也采用了类似的卸荷方法。
这种舵机系统实际上属于半闭式系统。
3.半闭式系统有所增加
半闭式系统多用于液压起货机。
起货机液压系统采用闭式比开式经济性好得多,但由于起货机负荷大,筒式系统油液发热严重,为此设置了低压选择阔,使系统工作时从低压倒连续与油箱换油达总流量的三分之一左右,故称半闭式系统。
舵机因为大多数情况下轻载运行,发热不严重,除少数小型阀控型舵机用开式系统外,大多数采用闭式系统。
近年来半闭式系统增多主要不是解决油液发热的需要。
一种情况是前述阀控型舵机稳舵时采用了开式系统,转舵时用闭式系统,可称为半闭式,另一种情况是摆缸式转舵机构也占领了一部分市场,它采
用的双作用活塞两侧油腔进排泊流量不等,为此而采用了半闭式系统。
活塞式油缸即使采用双缸或四缸对称布置,将工作油腔分为有效工作面积相等的二组,转过任一舵角时二组油腔容积变化仍是不等的,这是因为转过任一舵角时二个对称的活塞移动距离并不相同。
因此,从容积变化较大的一侧吸油排向容积变化较小的一侧时,就会使活塞移动量增加,油泵吸油侧压力升高而阻碍活塞移动。
为了解决两组油腔进排流量不等的矛盾,泵控型系统可设置与超货机相同的低压选择阀连续更油,成为半闭式系统阀控型系统则可使定向定量主泵吸油侧管路与高置膨胀油箱相通。
如果只使用一对容积不太大的活塞式油缸,二侧的进排油流量差小于漏泄流量,也可以仍用普通闭式系统。
4.新型液压阀件得到应用
随着液压技术迅速进步,从60年代末开始,能根据电气信号的变化对液压油流向及压力、流量进行连续的按比倒的远程控制的比例迅速发展,70年代为解决大流量(200升/分以上)系统控制固集成化的困难,逻辑阀(又称二通插装阀)元件不仅开始在工程船液压传动装置中出现,也开始用于棱压舵机。
5.浮动杆机械反馈机构日渐被淘汰
在变量泵舵机中采用浮动杆机械反馈机构已有较长的历史。
但随着舵机电气遥控系统更趋成熟,浮动杆机构已显得落后,它表现出以下缺点:增加了机攘元件数量,也增加了安装调试的工作量I增加了维护保养的工作,也增加了故障发生的可能;增加了一次反馈环节,
降低了控制精度而且,浮动杆机构往往是双泵共用的,这样,备用泵变量机构也必须动作,其主油路也必须锁紧。
更重要的是万一一台泵变量机构卡死,则必须使之与浮动秆脱离,否则另一台泵也无法操纵(曾发生泵控制杆折断事故),这样显然不能满足万吨以上油轮在45秒内排除单项故障的原则,因此,新一代舵机采用伺服马达、比例阀等比例控制元件而取消机械反馈的日渐增多。