过程成本与质量损失
过程成本与质量损失

过程成本与质量损失The document was prepared on January 2, 2021过程成本和质量损失质量管理的过程监控原理告诉我们:所有的质量工作都是通过过程来完成的质量体系的基本构成单元就是过程.任何组织都要通过过程网来创造、改进和提供持续稳定的产品质量.因此,核算和分析过程成本,降低质量损失是研究质量管理经济效益必须重视的一个问题.一、过程成本1.什么是过程成本过程成本由符合性成本和非符合性成本构成,任何过程都存在符合性成本和非符合性成本.见GB/T 19004· 1-ISO9004· 1 质量管理和质量体系要素第一部分指南第6.2.2条.符合性成本是在现行过程无故障情况下,完成所有规定的和指定的顾客要求所支付的费用.如某客车制造厂为生产社会需求的客车所支付的正常生产成本费用,即原材料费、工资与福利费、设备折旧费、电费、辅助生产费等等.非符合性成本是由于现行过程的故障造成的费用.如生产过程中产生的废次品损失费,设备故障而导致的停工损失费,设备维修费等.显然,质量管理中核算过程成本的根本目的是要不断降低非符合性成本.2.降低不良品损失是降低非符合性成本的主要途径不良品损失是指产品生产经营过程中,因产品不符合顾客要求的质量标准或合同规定的质量要求而造成的损失.不良品,包括废品、次品、返修品和回用品,直接造成原材料、能源、人员和设备使用等方面的浪费和损失;它们是非符合性成本的主要组成部分.据一些工业化国家的报道,每年不良品给企业造成的经济损失占企业增值的15%~18%,如法国质量协会AFQ在80年代初的调查估计,法国不良品损失大约是增值的15%左右,大约损失额达2700亿法郎.我国的工业不良品损失,据有关方面调查,高达工业产值的10%~15%.如天津市经委80年代中期对52家企业实测,关键工序一次合格率平均为64%,这意味着整个生产过程的不良品率高达36%.因此,不良品损失是一座有待挖掘的金山,开采这座金山,即降低不良品损失是降低非符合性成本的重要途径.它对提高质量管理经济效益有巨大作用.具体来说,体现在下列三个方面:l保证产品质量,提高产品质量等级品率如某化工厂对聚氯乙烯树脂产品生产过程中对影响聚氯乙烯残留单体含量指标的三道关键工序过程进行工艺改进,加强设备管理,实行质量奖惩后,产品合格率由%提高到%;一级品率由10%以下显着上升到%,获得显着经济效益.2促进文明均衡生产,即保证质量也增加产量某洗衣机厂原洗衣机生产线,因返修量大,导致生产线流动不畅,生产均衡性差,工人每天生产九小时,也只能完成设计能力的55%.尔后,该厂通过过程成本分析,装配过程的一次合格率仅43%,非符合性成本较大.为此,该厂认真开展岗位培训,加强工艺监督,降低返修率,不仅提高了产品质量,而且实现了文明均衡生产,日产量也提高到设计能力,取得良好经济效益.3降低物耗、能耗,实现扭亏转盈某味精厂,因原材料价格大幅度上升,面临亏损.该厂经过过程质量分析,对发酵、提取和精制过程确定新的收得率质量目标,然后从抓基础管理入手,加强原材料管理,健全计量工作,狠抓工艺实施与监督,并实行质量否决权,使每吨味精产品消耗原材料从原来11吨多下降到吨,还节约了能源,很快就实现扭亏转盈.3.提高关键工序一次合格率是降低非符合性成本的有效方法企业生产经营过程由许多大大小小的过程所构成,其中主干过程往往起到关键性的作用.因此,降低非符合性成本和不良品损失,最有成效的方法就是提高关键工序过程的一次合格率.90年代初,我国各地开展的提高关键工序一次合格率活动实践,充分证明其有见效快、成效大的优点.一般来说,提高关键工序一次合格率有下列六道步骤:1实测准备实测准备包括技术性准备和管理性准备两个方面.技术性准备是要做好以下四项准备工作:①确定产品对象一般应是主导产品;②明确产品生产工艺或流程;③确定关键工序;④提出关键工序或再制品、中间品的质量指标项目,确定抽样检测方案等.管理性准备是指作好人员、仪器工具和时间计划等方面的准备工作.2实测关键工序的一次合格率按照准备好的方案和方法实测预定质量指标的一次合格率,如合格率、成材率、收得率等,并作好实测记录.3分析、计算、攻关,采取纠正措施对关键工序一次合格率的实测记录进行分析和计算,寻找非符合性成本大的过程及因素,运用统计技术和专业知识分析原因,并制定和采取相应的纠正措施,实施质量改进.4复测关键工序一次合格率在实行质量改进后,再用同样的方法对关键工序一次合格率进行测试与计算,并作好复测记录.5评价成效对提高关键工序一次合格率的投人和产出也就是过程质量改进的成效进行评价和总结.既要定量地计算获得的经济效果,也要定性地总结取得的经济效益.6巩固成绩,继续改进提高关键工序一次合格率的有效措施和方法应纳入相应的标准、规程、规范等程序文件,以巩固已取得的成绩.同时,寻找新的质量改进对象,即可提高过程质量的新工序过程,转入新的关键工序一次合格率提高活动中去.据天津市42家企业统计,在提高关键工序一次合格率活动中,平均提高一次合格率13.6%,采取的纠正措施中,有78%是管理性措施,技术性措施仅占22%,其中38家企业取得年经济效果3348万元.可见,提高关键工序一次合格率确实是一项降低非符合性成本,提高质量管理效益的捷径.二、质量损失1.什么是质量损失告诉我们:质量损失是“由于质量低劣造成的内部损失和外部损失,并分为有形和无形损失两类”见GB/T -ISO 质量管理和质量体系要素第一部分指南的第6章.质量损失的构成如下图所示.1外部无形损失“典型的外部无形损失是由于顾客不满意而造成的进一步销售损失.”“要考虑有缺陷的产品能导致形象和信誉损失,丧失市场,意见、索赔、责任和人力财力资源的浪费等风险.”见GB/T —ISO这就是说,由于顾客不满意而造成的形象和信誉损失,以及由此导致的丧失市场是最大的外部无形损失.市场经济条件下,企业间的剧烈竞争不仅是产品质量与价格的竞争,也是企业人才和组织质量的竞争,企业形象与信誉的竞争.企业形象并不是简单的企业外在表现,而是企业在产品质量、设备水平、科技进步、管理艺术,经济实力,员工素质等各方面质量的综合表现.企业信誉,首先也是其质量信誉.它们绝不只是靠广告、促销、新闻发布等宣传出来的,而是依赖其卓越而持久的产品质量和组织质量,在顾客心中逐步树立起来的.比如,你无论走到世界何地,只要看到深红色的衬底托出金黄色的M形拱门,就知道这里是麦当劳餐店,就会想到里面装饰一致、干净优雅的饮食环境,着装统一、服务规范、笑脸相迎的服务人员,还有那质量、口味、规格一致的“汉堡包”.这就是说“麦当劳”已在各国顾客心目中树立了良好的企业形象和信誉.名牌产品,驰名商标,荣获美国波多里奇奖1987年创立、日本戴明奖1951年创立和欧州质量奖1991年创立等荣誉的企业都是企业形象和信誉的良好表现.相反,伪劣产品、冒牌商标等都是有损企业形象和信誉的不正当行为,势必因引起顾客不满意而丧失市场,甚至导致企业衰亡.2内部无形损失GB/T —ISO 中明确指出:“典型的内部无形损失是由于返工、低效的人机控制,丢失机会等低工作效率引起的.”这就是说,企业生产经营过程中故障多,返工多,人流、物流与信息流不畅等引起的劳动生产率低下是内部无形损失的主要表现形式.高质量,必然产生高效率,也就带来高效益.我国现代化钢铁企业——宝钢,建设一流队伍,培养一流作风,掌握一流技术,实行一流管理,生产一流产品,成为一流企业.其劳动生产率也是我国同类企业中最高的,到2000年,全员实物劳动生产率可达到80G吨/人·年,居世界一流水平.相反,劳动生产率低的企业也必定是一个质量低劣、效益差的企业,迟早会被淘汰.因此,我们要十分重视工作效率即劳动生产率问题,减少和避免这种无形的质量损失.3有形损失有形的质量损失是指那些可以定量计算或可以用货币衡量的质量损失.GB/T —ISO 第六章中明确地指出:“有形的损失是内部和外部故障费用”.也就是说,内部有形损失即内部故障费用,如废次品损失费、返工和复检费、质量故障处理费、质量降级损失费等等;外部有形损失即外部故障费用,如索赔费、退货或降等降级损失费返修费等等.2.质量损失的核算和控制尽管无形的质量损失不能定量核算,但却是首先应该控制和预防的,凡是企业形象和信誉好的企业都十分重视和做好这一点.如法国是世界上最大的矿泉水生产国,皮里耶集团公司的矿泉水更是行销天下,在美国矿泉水市场处于“霸主”地位.但是,有一年,美国卫生部下属的食品与药品管理局FDA通知皮里耶公司产并公布在北卡罗来州市场上销售的皮里g/L,这一指标虽然所在欧洲市场耶矿泉水中,有13瓶中含苯量达到10~17μg/L标准.的食品卫生标准之内,但却超过美国FDA规定的5μ法国皮里耶公司毅然决定把在世界120个国家和地区行销的亿瓶皮里耶矿泉水全部撤下市场,并就地销毁;直接经济损失2亿多法郎.同时,由皮里耶公司总裁等主要领导人举行记者招待会,宣布公司三项决定.的工①宣布皮里耶矿泉水有些产品中含有苯成分是由于在矿泉水充入CO2序中,过滤器没有按规定定期更换而造成,该工序负责人已被革职.同时经由各方专家反复检验,使里耶矿泉水绝对安全可靠.②邀请两位在国际上享有较高知名度的法国医学院院士,毒理学家和癌症g/L的含苯量几乎与人站在离吸烟者一米远处闻专家,由他们解释:10~17μ吸烟者吸一支烟的含苯量相等,如在30年内每天饮用半升皮里耶矿泉水,也只会增中1%的致癌可能性.③向广大消费者宣布:即使皮里耶矿泉水含毒度微乎其微,仍决定把过滤器事故发生之前的全部矿泉水撤下市场,是因为不愿意看到公司一向追求尽善尽美的产品质量会受到丝毫怀疑,为此,不惜付出任何代价.皮里耶公司的上述处理立即引起巨大的反响和效应,成为法、英、美等国许多大报的头版重要新闻;皮里耶公司股市行情立即刹住下跌势头,而且回升%,不仅保护了企业形象和信誉,而且更提高了企业知名度,起到了比2亿多法郎做广告更大的宣传效果.皮里耶矿泉水公司处理美国市场矿泉水含苯量超标事例,充分说明了无形质量损失是头等重大的损失,其损失代价,甚至是不可估量的.有形质量损失应通过核称质量成本中的内外损失成本及质量损失率来控制.质量损失率是内外损失成本之和与企业净产值之比,它是质量指标体系中一项重要的经济性指标,其计算公式为式中:F——质量损失率;C——内部损失成本,万元;1C——外部损失成本,万元;2——工业净产值,万元.PJ显然,质量损失率的大小,反映出企业质量损失的大小,它也是从经济上衡量质量体系有效性的重要依据.应该越小越好.如某玻璃厂1990年每季度的质量损失率如下表所示.从上表中对以看到,该玻璃厂1990年反座损失率呈下降趋势,已被控制住了,其质量管理是有效的.。
质量损失作为质量成本存在的问题及解决对策

中青年园地
质量损失在质量会计中反映方式的设想
质量损失是与质量管理工作密切相关的一个财务项 目 , 必须在质量会计中加以反映 。如果它不应计入质量 成 本 , 那么应如何在 质量会计中反映呢 ?本文认 为 , 可 以将质量损失的多少作为质量工作好坏的一个结果 , 从 而在质量损益中对其加以反映 。
- 28-
户 , 这个帐户是一个过渡帐户 , 在性质上类似于无形资 产帐户 , 但在期末将结清为零 。
在结算得到的 “质量损失减少收入”是正值时 : 借 : 质量管理水平
贷 : 质量损失减少收入 如果得到的 “质量损失减少收入”是负值时 : 借 : 质量损失减少收入
贷 : 质量管理水平 期末 “质量损失减少收入” 的余额如果在贷方 , 就 要转入 “质量损益”的贷方 ; 如果在借方就要转入 “质 量损益”的借方 。转入 “质量损益”的 “质量损失减少 收入”在期末不能与其他项目一起转入 “利润”科目 , 而要与 “质量管理水平”对冲 。 如果 “质量损益”中的 “质量损失减少收入”在贷 方, 则 : 借 : 质量损益 ———质量损失减少收入
传统的质 量成本 将质量 损失 作为 质量成 本的 一部 分 , 与预防成本和鉴定成本共同构成质量成本 。这样处 理的目的在于通过分析质量成本总额的构成结构 , 做出 最具经济性的质量管理决策 。由于质量损失与预防成本 和鉴定成本一般来说是成相反方向变化的 , 既投入的预 防成本和鉴定成本高 , 则质量损失会减少 ; 投入的预防 成本和鉴定成本少 , 则质量损失会增加 , 那么通过合理 的投入预防成本和鉴定成本 , 使质量损失维持在一个适 当的水平 , 就可以实现质量成本总额最低 。如果质量成 本没有达到最低 , 就应该对质量管理方式进行调整 。这 种处理方式虽然有一定的理论依据 , 而且对于做出质量 决策也有较好的使用价值 , 但笔者认为将质量损失作为 质量成本在理论上存在缺陷 , 有可能形成质量会计理论
质量损失成本遵循法则

质量损失成本遵循法则在质量管理中,质量损失成本是一个重要的考虑因素。
它涉及到与产品质量相关的各种成本,包括预防成本、鉴定成本、内部故障成本、外部故障成本和质量保证成本。
这些成本遵循一定的法则,下面将详细介绍。
1. 预防成本预防成本是指在产品设计、制造和销售过程中,为防止产品质量问题而采取的预防措施所发生的费用。
这些措施包括质量控制计划、工序控制、工作指南等。
预防成本通常随着产品复杂度的提高而增加,它是质量管理中最早产生的成本之一。
2. 鉴定成本鉴定成本是指为验证产品质量是否符合要求而进行的检验、测试和评估等活动中发生的费用。
这些活动包括原材料检验、过程检验和成品检验等。
鉴定成本在生产过程中是不可避免的,它对于确保产品质量是非常重要的。
3. 内部故障成本内部故障成本是指在产品交付前,由于产品未能满足质量要求而导致的损失。
这些损失包括废品、返工、重新检验等产生的费用。
内部故障成本通常随着产品质量的提高而降低。
4. 外部故障成本外部故障成本是指产品交付后,由于产品未能满足质量要求而导致的损失。
这些损失包括保修费用、产品退货、客户投诉处理等。
外部故障成本不仅影响企业的利润,还会对企业的声誉造成负面影响。
5. 质量保证成本质量保证成本是指为确保产品质量符合要求而进行的各种保证措施所发生的费用。
这些措施包括质量管理体系的建立和维护、员工培训、质量文化推广等。
质量保证成本是为了减少内部和外部故障成本而发生的,它对于提高产品质量和客户满意度是非常重要的。
总之,质量损失成本的遵循法则体现了质量管理中的一种因果关系。
为了降低质量损失成本,企业需要在产品设计、制造和销售过程中采取有效的预防措施,同时加强质量保证成本的投入,以提高产品质量和客户满意度。
质量损失成本分析报告
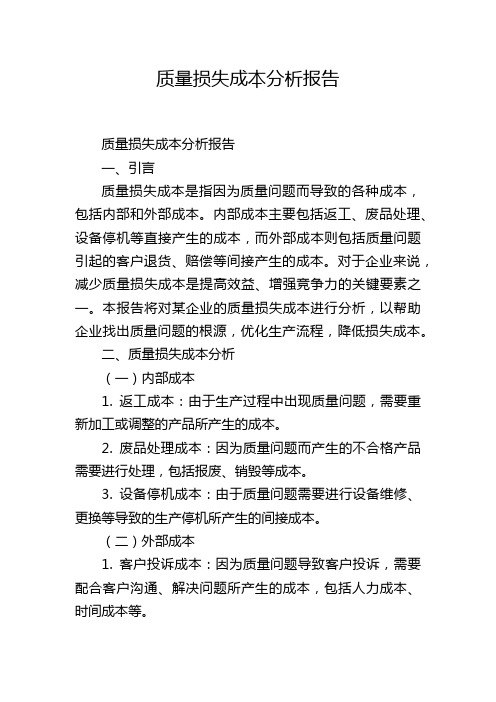
质量损失成本分析报告质量损失成本分析报告一、引言质量损失成本是指因为质量问题而导致的各种成本,包括内部和外部成本。
内部成本主要包括返工、废品处理、设备停机等直接产生的成本,而外部成本则包括质量问题引起的客户退货、赔偿等间接产生的成本。
对于企业来说,减少质量损失成本是提高效益、增强竞争力的关键要素之一。
本报告将对某企业的质量损失成本进行分析,以帮助企业找出质量问题的根源,优化生产流程,降低损失成本。
二、质量损失成本分析(一)内部成本1. 返工成本:由于生产过程中出现质量问题,需要重新加工或调整的产品所产生的成本。
2. 废品处理成本:因为质量问题而产生的不合格产品需要进行处理,包括报废、销毁等成本。
3. 设备停机成本:由于质量问题需要进行设备维修、更换等导致的生产停机所产生的间接成本。
(二)外部成本1. 客户投诉成本:因为质量问题导致客户投诉,需要配合客户沟通、解决问题所产生的成本,包括人力成本、时间成本等。
2. 客户退货成本:由于质量问题导致客户退货,需要进行退款、重新生产等成本。
3. 客户赔偿成本:由于质量问题导致客户损失,需要进行赔偿的成本。
三、案例分析以某汽车零部件制造企业为例,该企业生产的产品主要供应给汽车制造商。
在过去一年中,该企业出现了一系列的质量问题,导致内部和外部成本不断增加。
在内部成本方面,该企业需要进行大量的返工,造成了显著的人力和时间成本。
此外,由于质量问题导致部分产品不合格,需要进行废品处理,进一步增加了成本。
此外,由于质量问题频发,设备经常需要维修和调整,导致生产线的停机时间增加,进一步加剧了成本的上升。
在外部成本方面,由于质量问题频发,汽车制造商不得不退货,导致销售额大幅下降。
同时,由于客户投诉增加,企业需要投入更多的人力和资源来解决问题。
最严重的是, 一些客户由于质量问题导致的损失而要求企业进行赔偿,这导致了巨大的财务压力。
综上所述,该企业的质量损失成本明显上升,对企业的经营产生了很大的负面影响。
品质管理质量成本质量成本的定义以及内容分析

此处是大标题样稿字样十五字以内一.质量成本的起源谁发明了质量成本?质量成本是随着TQM的不断深入,在质量经济学研究的基础上,由美国的质量管理专家约瑟夫.朱兰发现的,于1951年所著的“质量控制手册”中对此作了介绍。
我国在七十年代末八十年代初开始引进质量成本概念和开展质量成本管理。
1、质量成本的含义1)较为正统的说法:当生产的产品质量达不到100%合格时,为产品质量而增加的成本。
2)较为不严格的定义质量成本是目前的实际生产成本与完美质量水平下的成本之间的差值。
2.“矿中金山”有人把质量故障造成的损失形象地比喻为“矿中金山”,也就是说,如果把因质量故障造成的损失有效地控制起来,并降低到最低限度,其效益好比是开采出“一座3.“冰河中的冰山”冰河中的冰山示意图Ⅰ—冰山露出水面部分(质量故障损失显见部分)“冰河中的冰山”含义为人们显而易见的质量故障损失好比是冰河中的冰山显露在水平面上的那个小小部分,而隐藏在水平面下的冰山是质量故障损失的隐见部分,约占整个损失的90%左4.降低质量损失的意义如果能把质量损失中的显见部分,特别是隐见损失控制住,降低下来,就会大大降低企业的总成本,所获的企业效益和社会效益将是十分可观的。
5.质量成本管理的基本任务如何正确的核标质量损失,如何采取有效措施去控制、去降低质量损失,并把这些工作用货币的形式表达出来,就构成了质量成本和质量成本管理的基本任务。
二、什么是质量成本?质量成本的定义质量成本是指为了确保和保证满意的质量而发生的费用以及达到满意的质量所造成的损失。
三、质量成本组成主要项目1. 内部故障损失成本2. 外部故障损失成本3. 鉴定成本4. 预防成本1. 内部故障损失成本指在产品运交顾客以前,因不能满足规定的质量要求造成的产成品、半成品、在制品、试生产产品等因报废而造成的净损失价值。
1. 内部故障损失成本a. 废品损失;b. 返工返修损失;c. 复检测试费用;d. 停工损失;1. 内部故障损失成本(续)e. 产量损失;f. 故障损失处理费用;g. 降级损失等。
质量损失成本核算项目细则

质量损失成本核算项目细则
1 目的
为了明确质量损失成本三级核科目,指导各部门进行质量损失成本核算。
2 范围
适用于公司对质量损失成本核算进行管理。
3 定义
3.1 质量损失成本——没有达到满意的质量所造成的损失成本。
4 职责
4.1 公司综合部负责确定质量损失成本三级科目。
4.2 公司公综合部负责按确定的三级科目进行质量损失成本核算、分析和报告。
4.3 各部门负责组织质量损失成本减少措施的制定、实施和效果验证。
5 工作程序
5.2 外部质量损失成本核算内容:
6 相关文件
6.1 TYQT-01《质量损失成本核算项目细则》
7 相关记录
7.1 TYQR-008《年月内部损失成本核算报表》
7.2 TYQR-009《年月外部损失成本核算报表》
7.3 TYQR-010《质量损失成本分析报告》
作业文件更改栏
编制:审核批准:。
质量损失成本管理项目

• 项目背景介绍 • 质量损失成本管理的意义 • 质量损失成本管理的方法 • 质量损失成本管理的实施步骤 • 质量损失成本管理的成功案例
01
项目背景介绍
质量损失成本的定义
质量损失成本
指因产品或服务质量未达到标准或客户需求而产 生的成本,包括内部损失成本和外部损失成本。
内部损失成本
检验和测试不足
检验和测试环节未能及时发现 和预防质量问题,导致产品出 厂后出现退货、维修等问题。
不良的设计和研发
产品设计或研发阶段未能充分 考虑客户需求和生产实际,导 致产品上市后出现质量问题。
质量损失成本对企业的影响
财务损失
质量损失成本直接导致企业的利润下降,影 响企业的盈利能力。
品牌形象受损
长期的质量问题会损害企业的品牌形象,影 响企业在市场上的竞争地位。
案例二
总结词
供应链协同、跨部门合作、信息化管理
详细描述
该电子产品制造企业通过加强供应链协同和跨部门合作,实现了质量损失成本的信息化 管理。通过及时传递质量信息,快速响应和处理质量问题,有效降低了质量损失成本,
提升了企业的运营效率和客户满意度。
案例三:某食品企业的质量损失成本管理
要点一
总结词
要点二
评估改进效果
总结词:效果评估
VS
详细描述:在实施改进措施后,对改 进效果进行评估,通过对比改进前后 的质量损失成本数据,分析改进措施 的有效性,并根据评估结果进行持续 改进。
05
质量损失成本管理的成功案例
案例一:某汽车制造企业的质量损失成本管理
总结词
全面质量管理、精细化核算、持续改进
详细描述
该汽车制造企业通过实施全面质量管理,对 质量损失成本进行精细化核算,识别出关键 问题所在,并采取有效措施持续改进,最终 实现了质量损失成本的显著降低,提高了企 业的盈利能力和市场竞争力。
工程施工中的质量成本控制
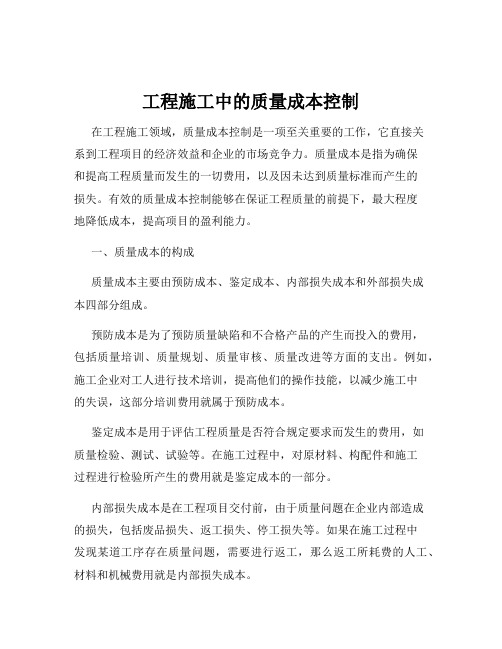
工程施工中的质量成本控制在工程施工领域,质量成本控制是一项至关重要的工作,它直接关系到工程项目的经济效益和企业的市场竞争力。
质量成本是指为确保和提高工程质量而发生的一切费用,以及因未达到质量标准而产生的损失。
有效的质量成本控制能够在保证工程质量的前提下,最大程度地降低成本,提高项目的盈利能力。
一、质量成本的构成质量成本主要由预防成本、鉴定成本、内部损失成本和外部损失成本四部分组成。
预防成本是为了预防质量缺陷和不合格产品的产生而投入的费用,包括质量培训、质量规划、质量审核、质量改进等方面的支出。
例如,施工企业对工人进行技术培训,提高他们的操作技能,以减少施工中的失误,这部分培训费用就属于预防成本。
鉴定成本是用于评估工程质量是否符合规定要求而发生的费用,如质量检验、测试、试验等。
在施工过程中,对原材料、构配件和施工过程进行检验所产生的费用就是鉴定成本的一部分。
内部损失成本是在工程项目交付前,由于质量问题在企业内部造成的损失,包括废品损失、返工损失、停工损失等。
如果在施工过程中发现某道工序存在质量问题,需要进行返工,那么返工所耗费的人工、材料和机械费用就是内部损失成本。
外部损失成本是在工程项目交付后,因质量问题给用户和社会造成的损失,以及企业为处理质量问题所支付的费用,如保修费用、赔偿费用、信誉损失等。
一旦工程项目在使用过程中出现质量问题,企业需要承担维修、赔偿等责任,这就产生了外部损失成本。
二、质量成本控制的重要性首先,质量成本控制有助于提高工程质量。
通过合理投入预防成本和鉴定成本,可以及时发现和解决质量问题,避免质量事故的发生,从而提高工程的整体质量水平。
其次,能够降低成本。
有效的质量成本控制可以在保证质量的前提下,优化资源配置,减少不必要的浪费和损失,降低工程项目的总成本。
再者,增强企业的市场竞争力。
高质量、低成本的工程项目能够赢得客户的信任和市场份额,为企业树立良好的品牌形象,提升企业在市场中的竞争力。
推行质量成本管理 减少质量损失

推行质量成本管理减少质量损失作者:林婉珍来源:《财经界·学术版》2014年第07期摘要:经济全球化大背景下,机械制造企业如何在日趋同质化、激烈的市场竞争中占有一席之地,成为各企业重要课题。
在质量管理工作中,推行质量成本管理,将减少质量损失,有效降低企业成本,创造更好经济效益。
本文探讨机械制造企业如何在生产过程推行质量成本管理,强化质量管理工作,从而减少质量损失的对策。
关键词:质量成本管理质量损失质量管理机械制造企业质量是企业生存根本,“持续质量改进、不断提高顾客满意度”是企业永恒主题。
机械制造企业在生产过程质量管理工作中,推行质量成本管理,能不断提高质量保证能力,减少质量损失,降低成本,实现机械制造企业“高质量,低成本、快速反应”的目标。
一、机械制造企业在生产过程质量管理工作中涉及质量成本概述质量成本:为获得顾客满意的质量并对组织外部做出质量保证而发生的费用以及没有达到顾客满意的质量而造成的损失。
包括预防成本、鉴定成本、内部故障损失、外部故障损失。
质量管理五要素“人、机、料、法、环”,即质量管理工作五重心。
五个方面的质量管理费用支出,构成机械制造企业生产过程中的质量成本。
(一)人工方面质量成本“第一次就把事情作对”是管理学家克劳士比先生理论之一。
员工第一次就生产出满足质量要求的产品即“一次交检合格品”,极大影响企业质量成本。
一次交检合格品,不需要返修或让步接受,也不是报废。
“返修”、“让步接受”、“报废”是质量成本支出。
不是“一次交检合格品”的情况还可能导致企业“不能及时交货”、“生产效率低下”等也属于质量成本支出。
企业设置“检验员”工作岗位,属于预防成本支出,但依靠多设置检验员控制质量,也可能是质量成本浪费。
(二)机器设备方面质量成本选择能满足加工产品质量等级要求的合适设备。
同等设备加工等级越高,往往价格也更高,如果采购加工等级高于产品质量要求的设备,投入更高设备资金就是企业额外的质量成本支出。
过程质量成本计算公式

过程质量成本(Process Quality Cost)是指与确保产品或服务质量相关的所有成本。
这些成品量成本通常被分为四个主要类别:预防成本、评估成本、内部失败成本和外部失败成本。
没有一个统一的“过程质量成本计算公式”,因为它会因组织和业务流程的不同而有所变化,但我们可以按以下方式进行概念性的划分和计算:1. 预防成本(Prevention Costs):与防止质量问题发生相关的成本。
这包括培训、质量计划的开发、供应商管理、新产品审查、质量改进项目等。
2. 评估成本(Appraisal Costs):与评估和监督产品质量相关的成本。
这包括测试、检验、校准设备、监控和审核等。
3. 内部失败成本(Internal Failure Costs):在产品或服务交付给顾客之前,由于质量不符引起的成本。
这包括返工、重造、废品、停机时间等。
4. 外部失败成本(External Failure Costs):产品或服务交付给顾客后,由于质量不符引起的成本。
这包括保修索赔、退货、投诉处理、维修服务以及因质量问题导致的声誉损失和未来生意损失等。
过程质量成本的总和可以用下面的公式表达:\[ \text{总过程质量成本} = \text{预防成本} + \text{评估成本} + \text{内部失败成本} + \text{外部失败成本} \]为了计算这些成本,组织通常会通过其财务和质量管理系统收集相关数据。
有效的成本计算不仅需要定期收集和分析数据,还需要所有相关部门的协作和透明的沟通。
请注意,这些成本的计算和分析目的是为了识别并减少质量相关的浪费,从而提高效率和盈利能力。
理想情况下,预防成本和评估成本的增加将导致内部和外部失败成本的减少,从而在长期内降低总的质量成本。
质量损失管理办法
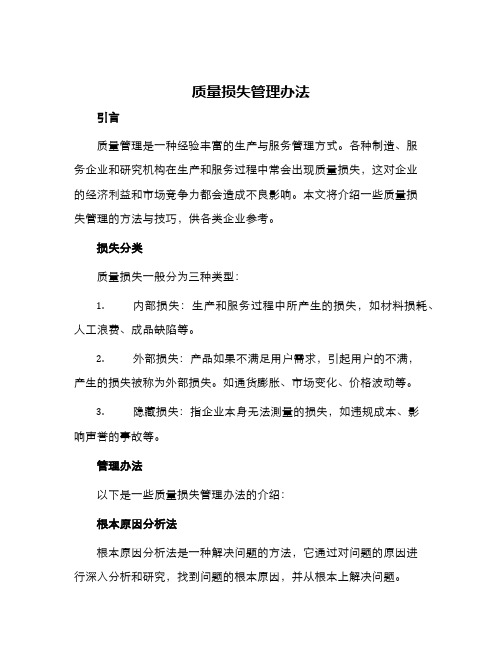
质量损失管理办法引言质量管理是一种经验丰富的生产与服务管理方式。
各种制造、服务企业和研究机构在生产和服务过程中常会出现质量损失,这对企业的经济利益和市场竞争力都会造成不良影响。
本文将介绍一些质量损失管理的方法与技巧,供各类企业参考。
损失分类质量损失一般分为三种类型:1.内部损失:生产和服务过程中所产生的损失,如材料损耗、人工浪费、成品缺陷等。
2.外部损失:产品如果不满足用户需求,引起用户的不满,产生的损失被称为外部损失。
如通货膨胀、市场变化、价格波动等。
3.隐藏损失:指企业本身无法測量的损失,如违规成本、影响声誉的事故等。
管理办法以下是一些质量损失管理办法的介绍:根本原因分析法根本原因分析法是一种解决问题的方法,它通过对问题的原因进行深入分析和研究,找到问题的根本原因,并从根本上解决问题。
根本原因分析通常包括以下五个步骤:1.收集数据:收集有关问题的数据和信息。
2.分析数据:对数据和信息进行分析,找到潜在的问题因素。
3.确定根本原因:确定潜在问题因素的根本原因。
4.提出解决方案:制定解决问题的计划和方案。
5.推广和实施:将解决方案应用到生产和服务过程中。
浪費检测法浪費检测法可以帮助企业发现各种浪费,包括过产量、过度加工、过多的库存、过多的运输等。
浪費检测法包括以下四个步骤:1.测量问题程度:确定产生浪费的程度和影响范围。
2.收集数据:收集有关浪费的数据和信息。
3.分析数据:对浪费数据进行分析和研究,找到浪费现象的原因和根源。
4.制定改善方案:制定改善浪费的方案和计划。
持续改进法持续改进法是指通过在规定周期内实施改善行动以不断提高生产和服务质量的方法。
它包括了以下五个步骤:1.确定目标:确立改进目标和进行评估。
2.收集数据:收集有关改善的数据和信息。
3.分析数据:对数据和信息进行分析,找到改善方案。
4.制定行动计划:制定针对改善方案的具体行动计划。
5.实施行动计划:在规定时间内实施改善行动计划。
结论质量损失管理是各种制造、服务企业和研究机构不可缺少的重要管理环节。
过程成本与质量损失
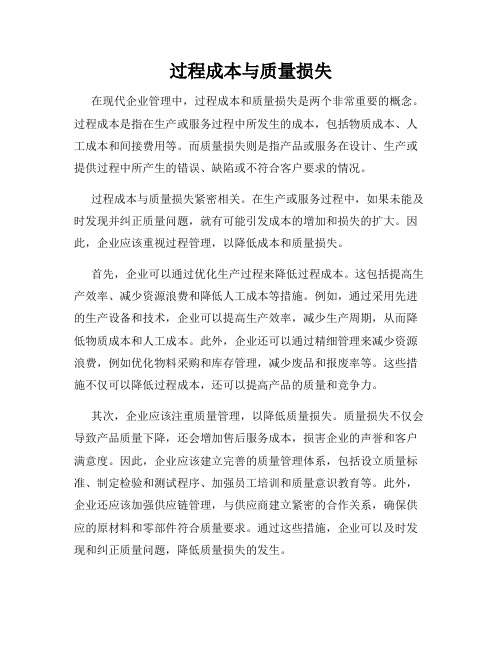
过程成本与质量损失在现代企业管理中,过程成本和质量损失是两个非常重要的概念。
过程成本是指在生产或服务过程中所发生的成本,包括物质成本、人工成本和间接费用等。
而质量损失则是指产品或服务在设计、生产或提供过程中所产生的错误、缺陷或不符合客户要求的情况。
过程成本与质量损失紧密相关。
在生产或服务过程中,如果未能及时发现并纠正质量问题,就有可能引发成本的增加和损失的扩大。
因此,企业应该重视过程管理,以降低成本和质量损失。
首先,企业可以通过优化生产过程来降低过程成本。
这包括提高生产效率、减少资源浪费和降低人工成本等措施。
例如,通过采用先进的生产设备和技术,企业可以提高生产效率,减少生产周期,从而降低物质成本和人工成本。
此外,企业还可以通过精细管理来减少资源浪费,例如优化物料采购和库存管理,减少废品和报废率等。
这些措施不仅可以降低过程成本,还可以提高产品的质量和竞争力。
其次,企业应该注重质量管理,以降低质量损失。
质量损失不仅会导致产品质量下降,还会增加售后服务成本,损害企业的声誉和客户满意度。
因此,企业应该建立完善的质量管理体系,包括设立质量标准、制定检验和测试程序、加强员工培训和质量意识教育等。
此外,企业还应该加强供应链管理,与供应商建立紧密的合作关系,确保供应的原材料和零部件符合质量要求。
通过这些措施,企业可以及时发现和纠正质量问题,降低质量损失的发生。
最后,企业可以采用一些成本与质量管理工具来辅助决策。
例如,企业可以运用成本控制技术,制定预算和成本控制指标,监控和控制过程成本的变化。
同时,企业还可以使用质量统计工具,如质量控制图和故障模式与影响分析,帮助分析和解决质量问题。
这些工具可以提供数据支持和决策参考,帮助企业降低成本和质量损失。
综上所述,过程成本与质量损失是企业管理中需要重视的两个方面。
通过优化生产过程和强化质量管理,企业可以降低成本和质量损失,提高竞争力和盈利能力。
此外,运用适当的管理工具,对过程成本和质量进行监控和分析也是一种有效的管理手段。
工程施工实际损失

工程施工实际损失在建筑工程领域,工程施工实际损失是一个普遍存在的问题,它涉及到工程质量、工程进度以及工程成本等方面。
工程施工实际损失是指在施工过程中,由于各种原因导致的工程成本增加、工程质量下降以及工程进度延误等损失。
在实际施工中,如何减少工程施工实际损失,提高工程质量和效益,是工程建设者和管理者面临的重要课题。
工程施工实际损失的主要表现有以下几个方面:一、工程质量损失工程质量是建筑工程的生命线,但由于各种原因,工程质量损失在施工过程中仍然难以避免。
例如,施工材料不合格、施工工艺不达标、施工人员素质不高、管理不善等,都可能导致工程质量问题。
工程质量损失不仅影响工程的安全和使用寿命,还需要额外投入进行修复和整改,从而增加了工程成本。
二、工程进度延误损失工程进度延误会导致工程投资的利息增加、工程效益下降,甚至可能导致工程项目的失败。
施工过程中,由于设计变更、施工方案不合理、施工现场管理混乱、自然灾害等因素,都可能导致工程进度延误。
工程进度延误损失不仅包括直接的经济损失,还包括声誉损失和信誉度下降等间接损失。
三、工程成本增加损失工程成本增加是工程施工实际损失的另一个重要方面。
在施工过程中,由于设计不合理、施工方案不科学、材料采购成本增加、管理不善等原因,可能导致工程成本的增加。
工程成本增加不仅降低了工程的利润空间,还可能影响到工程的投资回报。
针对工程施工实际损失,我们可以从以下几个方面进行预防和控制:一、加强质量管理提高工程质量是减少工程施工实际损失的关键。
施工企业应建立健全质量管理体系,加强施工过程的质量控制,严格把关施工材料、施工工艺和施工人员素质。
同时,加大质量检查和验收力度,确保工程质量符合国家标准和设计要求。
二、优化工程进度管理合理安排工程进度,确保施工过程中各阶段工作的顺利进行。
加强施工现场管理,提高施工效率,降低工程进度延误的风险。
对于可能导致工程进度延误的因素,如设计变更、施工现场条件变化等,要及时进行调整和应对,确保工程进度按计划进行。
桩基工程施工损失

桩基工程施工损失分析桩基工程是建筑工程中的重要组成部分,其质量直接关系到整个建筑工程的安全和稳定。
在桩基工程施工过程中,可能会出现各种损失,导致工程质量受到影响,甚至影响到整个建筑工程的进度。
本文将对桩基工程施工损失进行分析和探讨。
一、桩基工程施工损失的类型1. 质量损失:桩基工程的质量问题可能会导致桩基工程的承载能力下降,甚至影响到整个建筑工程的安全。
质量损失主要包括桩身完整性不足、桩长不足、桩偏位过大等。
2. 进度损失:桩基工程施工进度的延误可能会导致整个建筑工程的进度受到影响。
进度损失主要包括工期延长、施工效率低下等。
3. 成本损失:桩基工程施工过程中可能会出现各种意外情况,导致施工成本的增加。
成本损失主要包括材料浪费、设备损坏、人工费用增加等。
4. 安全事故损失:桩基工程施工过程中可能会发生各种安全事故,对施工人员和设备造成伤害,甚至导致人员伤亡。
安全事故损失主要包括人员伤亡、设备损坏、赔偿费用等。
二、桩基工程施工损失的原因1. 设计问题:设计不合理或设计不当可能会导致桩基工程施工损失。
例如,桩基设计时未充分考虑地质条件、桩型选择不当等。
2. 施工问题:施工质量不好是导致桩基工程施工损失的主要原因之一。
施工问题主要包括施工工艺不当、施工管理不善、施工人员素质不高等。
3. 地质条件:地质条件的不稳定可能会导致桩基工程施工损失。
例如,地质断层、地下障碍物、地下水等因素都可能影响到桩基工程的施工质量。
4. 外界环境因素:外界环境因素也可能导致桩基工程施工损失。
例如,气候变化、交通不便、场地限制等。
三、桩基工程施工损失的防范措施1. 加强设计管理:在桩基工程设计阶段,应充分考虑地质条件、工程需求等因素,合理选择桩型和施工方案,确保设计合理性和科学性。
2. 提高施工质量:加强施工管理,确保施工工艺的正确执行,提高施工人员素质,严格把控施工质量。
3. 充分考虑地质条件:在桩基工程施工前,应进行详细的地质勘察,了解地质条件,根据地质条件制定合理的施工方案。
大型设备产品质量成本内部损失

大型设备产品质量成本内部损失
大型设备的产品质量成本内部损失通常包括以下几个方面:
1. 内部不合格品:内部不合格品是指在生产过程中出现的不符合产品质量标准的产品,包括材料不合格、加工不良、装配错误等问题。
这些内部不合格品会增加生产成本,降低产品质量,并可能导致后续的返工和修复工作。
2. 内部报废品:内部报废品是指在生产过程中被判定为无法修复或不符合再利用要求的产品。
这些产品可能出现严重的质量问题,无法投入市场销售,导致生产成本的浪费。
3. 生产中断成本:如果在生产过程中出现严重的质量问题,可能需要停止生产进行修复或调整。
这样的生产中断会导致生产计划的推迟,增加生产成本,甚至影响客户的交付期限。
4. 返修和保修成本:如果在产品交付给客户后出现质量问题,通常需要进行返修或保修。
这将增加公司的售后成本,包括人力、物料和运输费用等。
为了减少大型设备产品质量的内部损失,企业可以采取以下措施:
1. 加强供应链管理,确保原材料和零部件的质量符合要求。
2. 实施严格的质量控制流程和标准,加强生产过程的监控和检验,及时发现并处理问题。
3. 培训和提升员工的质量意识和技能,确保每个员工都能够理解和执行质量要求。
4. 建立健全的质量管理体系,包括质量管理部门、质量指标和评估体系,持续改进产品质量的过程。
5. 加强售后服务,及时响应客户的质量问题,提供有效的返修和保修服务。
总之,通过有效的质量管理措施和持续改进,企业可以降低大型设备产品质量的内部损失,提高产品质量和客户满意度。
内部差错成本的名词解释

内部差错成本的名词解释在管理学领域,内部差错成本是指组织内部发生的错误所产生的各种费用和损失的总和。
它包括了员工误差、系统缺陷、机械故障等非预期的和错误的事件所导致的影响。
内部差错成本是组织效率和盈利能力的重要指标,也是管理者决策和改进的基础。
本文将深入探讨内部差错成本的含义、计算方法以及减少内部差错的策略。
一、内部差错成本的含义内部差错成本由多个方面的费用组成,包括:1. 人力资源成本:员工因为出错而需要加班加点加以弥补,或需要重新做一项工作,从而造成劳动力资源的浪费。
2. 质量损失成本:产品或服务的质量问题会给组织带来不同程度的损失,需要进行售后服务、退货退款等。
3. 生产效率成本:错误导致生产线停工,从而延迟交货期限,增加加工时间和生产成本。
4. 维修和更换成本:机器故障需要维修或更换零部件,不仅会带来维修成本,还会导致生产线暂时停工,进一步增加生产成本。
5. 管理成本:管理者需要耗费时间和资源来查找、解决和预防内部差错,增加了管理成本。
二、计算内部差错成本的方法为了准确计算内部差错成本,需要明确网点统计包括等多项数量,建立数据收集系统。
具体方法如下:1. 建立差错损失分类:主要根据差错类型,如生产差错、售后差错、人力资源差错等,对损失进行分类。
2. 收集差错数据:通过员工报告、事务处理系统和客户反馈等渠道收集差错数据。
3. 评估损失程度:根据每个差错所产生的具体损失,量化衡量其对组织造成的影响。
4. 估算差错频率:根据历史数据估算差错的平均发生频率。
5. 计算内部差错成本:将差错损失程度和差错发生频率相乘,即可得到每个差错类型的成本。
最后将所有差错类型的成本相加,得到内部差错成本的总额。
三、减少内部差错的策略为了降低内部差错成本,组织可以采取以下策略:1. 培训和技能提升:通过培训和技能提升计划,提高员工的专业素质和技能水平,以减少因为员工误差而引发的错误。
2. 流程优化和自动化:优化和简化工作流程,避免繁琐的手动操作。
班组质量成本控制应知应会3件事:预防成本、鉴定成本、损失成本

质量成本控制应知应会3件事一、预防成本控制(一)预防成本构成预防成本是指企业为了保证产品质量达到规定的标准或提高产品质量,防止产品质量水平低于某一所需水平而开展的预防活动和采取的各种预防措施所发生的费用。
预防成本包括的内容如表6-1所示。
预防成本的内容(二)预防成本控制方法1.质量工作费控制建立严格的费用申请审批及报销制度,在班组员工中深入宣传节约理念,通过自我控制及财务部的监督控制,降低质量工作费。
2.质量培训费控制班组长在对质量培训费进行控制时,应遵循“先预算、后使用,先审批、后执行”的原则,在明确本班组质量培训计划后,对支出费用进行预算,待人力资源部批准后方可执行。
3.质量改进费控制班组长对质量改进费进行控制时,应先找出影响质量改进费用高低的因素,针对存在的问题,采取相应的控制措施,提高产品质量,降低因产品质量问题造成的损失。
4.质量评审费控制进行质量评审之前,班组长应协助质量评审人员对前期已发生的评审咨询费用和本次评审目标、范围进行调查,制定评审费用预算,根据财务部相关规定报批。
5.质量奖励费控制班组长应协助人力资源部制定合理的奖励标准及奖励程序并严格落实,奖励标准要在即能充分调度班组人员及质量人员的积极性,又能本着节约支出、奖励先进的基础上设计。
6.工资及福利费控制班组长应协助人力资源部落实薪酬管理制度,积极配合质量管理人员的工作,减少其工作量及加班时间,从而降低企业工资及福利费的指出。
二、鉴定成本控制(一)鉴定成本构成鉴定成本是指产品在第一次验收合格的情况下,对原材料、零部件和成品进行质量检验的费用。
鉴定成本主要包括以下内容,如图6-4所示。
图6-4 鉴定成本的构成(二)鉴定成本控制方法1.通过改善检验手段降低鉴定成本(1)通过科学分析及工作实践,在确保达成检验目的的基础上,班组长可提出取消无价值的检验程序或采取更简便、更经济的新检验手段的建议。
(2)在生产过程中,班组长应尽量减少相关检验材料、检测计量仪器的消耗量。
- 1、下载文档前请自行甄别文档内容的完整性,平台不提供额外的编辑、内容补充、找答案等附加服务。
- 2、"仅部分预览"的文档,不可在线预览部分如存在完整性等问题,可反馈申请退款(可完整预览的文档不适用该条件!)。
- 3、如文档侵犯您的权益,请联系客服反馈,我们会尽快为您处理(人工客服工作时间:9:00-18:30)。
过程成本和质量损失质量管理的过程监控原理告诉我们:所有的质量工作都是通过过程来完成的质量体系的基本构成单元就是过程。
任何组织都要通过过程网来创造、改进和提供持续稳定的产品质量。
因此,核算和分析过程成本,降低质量损失是研究质量管理经济效益必须重视的一个问题。
一、过程成本1.什么是过程成本过程成本由符合性成本和非符合性成本构成,任何过程都存在符合性成本和非符合性成本。
(见GB/T 19004· 1-ISO9004· 1 《质量管理和质量体系要素第一部分指南》第6.2.2条)。
符合性成本是在现行过程无故障情况下,完成所有规定的和指定的顾客要求所支付的费用。
如某客车制造厂为生产社会需求的客车所支付的正常生产成本费用,即原材料费、工资与福利费、设备折旧费、电费、辅助生产费等等。
非符合性成本是由于现行过程的故障造成的费用。
如生产过程中产生的废次品损失费,设备故障而导致的停工损失费,设备维修费等。
显然,质量管理中核算过程成本的根本目的是要不断降低非符合性成本。
2.降低不良品损失是降低非符合性成本的主要途径不良品损失是指产品生产经营过程中,因产品不符合顾客要求的质量标准或合同规定的质量要求而造成的损失。
不良品,包括废品、次品、返修品和回用品,直接造成原材料、能源、人员和设备使用等方面的浪费和损失;它们是非符合性成本的主要组成部分。
据一些工业化国家的报道,每年不良品给企业造成的经济损失占企业增值的15%~18%,如法国质量协会(AFQ)在80年代初的调查估计,法国不良品损失大约是增值的15%左右,大约损失额达2700亿法郎。
我国的工业不良品损失,据有关方面调查,高达工业产值的10%~15%。
如市经委80年代中期对52家企业实测,关键工序一次合格率平均为64%,这意味着整个生产过程的不良品率高达36%。
因此,不良品损失是一座有待挖掘的金山,开采这座金山,即降低不良品损失是降低非符合性成本的重要途径。
它对提高质量管理经济效益有巨大作用。
具体来说,体现在下列三个方面:(l)保证产品质量,提高产品质量等级品率如某化工厂对聚氯乙烯树脂产品生产过程中对影响聚氯乙烯残留单体含量指标的三道关键工序(过程)进行工艺改进,加强设备管理,实行质量奖惩后,产品合格率由75.8%提高到94.4%;一级品率由10%以下显著上升到70.69%,获得显著经济效益。
(2)促进文明均衡生产,即保证质量也增加产量某洗衣机厂原洗衣机生产线,因返修量大,导致生产线流动不畅,生产均衡性差,工人每天生产九小时,也只能完成设计能力的55%。
尔后,该厂通过过程成本分析,装配过程的一次合格率仅43%,非符合性成本较大。
为此,该厂认真开展岗位培训,加强工艺监督,降低返修率,不仅提高了产品质量,而且实现了文明均衡生产,日产量也提高到设计能力,取得良好经济效益。
(3)降低物耗、能耗,实现扭亏转盈某味精厂,因原材料价格大幅度上升,面临亏损。
该厂经过过程质量分析,对发酵、提取和精制过程确定新的收得率质量目标,然后从抓基础管理入手,加强原材料管理,健全计量工作,狠抓工艺实施与监督,并实行质量否决权,使每吨味精产品消耗原材料从原来11吨多下降到6.82吨,还节约了能源,很快就实现扭亏转盈。
3.提高关键工序一次合格率是降低非符合性成本的有效方法企业生产经营过程由许多大大小小的过程所构成,其中主干过程往往起到关键性的作用。
因此,降低非符合性成本和不良品损失,最有成效的方法就是提高关键工序(过程)的一次合格率。
90年代初,我国各地开展的提高关键工序一次合格率活动实践,充分证明其有见效快、成效大的优点。
一般来说,提高关键工序一次合格率有下列六道步骤:(1)实测准备实测准备包括技术性准备和管理性准备两个方面。
技术性准备是要做好以下四项准备工作:①确定产品对象(一般应是主导产品);②明确产品生产工艺或流程;③确定关键工序;④提出关键工序或再制品、中间品的质量指标项目,确定抽样检测方案等。
管理性准备是指作好人员、仪器工具和时间计划等方面的准备工作。
(2)实测关键工序的一次合格率按照准备好的方案和方法实测预定质量指标的一次合格率,如合格率、成材率、收得率等,并作好实测记录。
(3)分析、计算、攻关,采取纠正措施对关键工序一次合格率的实测记录进行分析和计算,寻找非符合性成本大的过程及因素,运用统计技术和专业知识分析原因,并制定和采取相应的纠正措施,实施质量改进。
(4)复测关键工序一次合格率在实行质量改进后,再用同样的方法对关键工序一次合格率进行测试与计算,并作好复测记录。
(5)评价成效对提高关键工序一次合格率的投人和产出也就是过程质量改进的成效进行评价和总结。
既要定量地计算获得的经济效果,也要定性地总结取得的经济效益。
(6)巩固成绩,继续改进提高关键工序一次合格率的有效措施和方法应纳入相应的标准、规程、规等程序文件,以巩固已取得的成绩。
同时,寻找新的质量改进对象,即可提高过程质量的新工序(过程),转入新的关键工序一次合格率提高活动中去。
据市42家企业统计,在提高关键工序一次合格率活动中,平均提高一次合格率13.6%,采取的纠正措施中,有78%是管理性措施,技术性措施仅占22%,其中38家企业取得年经济效果3348万元。
可见,提高关键工序一次合格率确实是一项降低非符合性成本,提高质量管理效益的捷径。
二、质量损失1.什么是质量损失告诉我们:质量损失是“由于质量低劣造成的部损失和外部损失,并分为有形和无形损失两类”(见GB/T 19004.1-ISO 9004.1《质量管理和质量体系要素第一部分指南》的第6章)。
质量损失的构成如下图所示。
(1)外部无形损失“典型的外部无形损失是由于顾客不满意而造成的进一步销售损失。
”“要考虑有缺陷的产品能导致形象和信誉损失,丧失市场,意见、索赔、责任和人力财力资源的浪费等风险。
”(见GB/T 19004.1—ISO 9004.1)这就是说,由于顾客不满意而造成的形象和信誉损失,以及由此导致的丧失市场是最大的外部无形损失。
市场经济条件下,企业间的剧烈竞争不仅是产品质量与价格的竞争,也是企业人才和组织质量的竞争,企业形象与信誉的竞争。
企业形象并不是简单的企业外在表现,而是企业在产品质量、设备水平、科技进步、管理艺术,经济实力,员工素质等各方面质量的综合表现。
企业信誉,首先也是其质量信誉。
它们绝不只是靠广告、促销、新闻发布等宣传出来的,而是依赖其卓越而持久的产品质量和组织质量,在顾客心中逐步树立起来的。
比如,你无论走到世界何地,只要看到深红色的衬底托出金黄色的M形拱门,就知道这里是麦当劳餐店,就会想到里面装饰一致、干净优雅的饮食环境,着装统一、服务规、笑脸相迎的服务人员,还有那质量、口味、规格一致的“汉堡包”。
这就是说“麦当劳”已在各国顾客心目中树立了良好的企业形象和信誉。
名牌产品,驰名商标,荣获美国波多里奇奖(1987年创立)、日本戴明奖(1951年创立)和欧州质量奖(1991年创立)等荣誉的企业都是企业形象和信誉的良好表现。
相反,伪劣产品、冒牌商标等都是有损企业形象和信誉的不正当行为,势必因引起顾客不满意而丧失市场,甚至导致企业衰亡。
(2)部无形损失GB/T 19004.1—ISO 9004.1中明确指出:“典型的部无形损失是由于返工、低效的人机控制,丢失机会等低工作效率引起的。
”这就是说,企业生产经营过程中故障多,返工多,人流、物流与信息流不畅等引起的劳动生产率低下是部无形损失的主要表现形式。
高质量,必然产生高效率,也就带来高效益。
我国现代化钢铁企业——宝钢,建设一流队伍,培养一流作风,掌握一流技术,实行一流管理,生产一流产品,成为一流企业。
其劳动生产率也是我国同类企业中最高的,到2000年,全员实物劳动生产率可达到80G吨/人·年,居世界一流水平。
相反,劳动生产率低的企业也必定是一个质量低劣、效益差的企业,迟早会被淘汰。
因此,我们要十分重视工作效率即劳动生产率问题,减少和避免这种无形的质量损失。
(3)有形损失有形的质量损失是指那些可以定量计算或可以用货币衡量的质量损失。
GB/T 19004.1—ISO 9004.1第六章中明确地指出:“有形的损失是部和外部故障费用”。
也就是说,部有形损失即部故障费用,如废次品损失费、返工和复检费、质量故障处理费、质量降级损失费等等;外部有形损失即外部故障费用,如索赔费、退货或降等降级损失费返修费等等。
2.质量损失的核算和控制尽管无形的质量损失不能定量核算,但却是首先应该控制和预防的,凡是企业形象和信誉好的企业都十分重视和做好这一点。
如法国是世界上最大的矿泉水生产国,皮里耶集团公司的矿泉水更是行销天下,在美国矿泉水市场处于“霸主”地位。
但是,有一年,美国卫生部下属的食品与药品管理局(FDA)通知皮里耶公司产并公布在北卡罗来州市场上销售的皮里耶矿泉水中,有13瓶中含苯量达到10~17μg/L,这一指标虽然所在欧洲市场的食品卫生标准之,但却超过美国FDA规定的5μg/L标准。
法国皮里耶公司毅然决定把在世界120个国家和地区行销的1.6亿瓶皮里耶矿泉水全部撤下市场,并就地销毁;直接经济损失2亿多法郎。
同时,由皮里耶公司总裁等主要领导人举行记者招待会,宣布公司三项决定。
①宣布皮里耶矿泉水有些产品中含有苯成分是由于在矿泉水充入CO2的工序中,过滤器没有按规定定期更换而造成,该工序负责人已被革职。
同时经由各方专家反复检验,使里耶矿泉水绝对安全可靠。
②邀请两位在国际上享有较高知名度的法国医学院院士,毒理学家和癌症专家,由他们解释:10~17μg/L的含苯量几乎与人站在离吸烟者一米远处闻吸烟者吸一支烟的含苯量相等,如在30年每天饮用半升皮里耶矿泉水,也只会增中1%的致癌可能性。
③向广大消费者宣布:即使皮里耶矿泉水含毒度微乎其微,仍决定把过滤器事故发生之前的全部矿泉水撤下市场,是因为不愿意看到公司一向追求尽善尽美的产品质量会受到丝毫怀疑,为此,不惜付出任何代价。
皮里耶公司的上述处理立即引起巨大的反响和效应,成为法、英、美等国许多大报的头版重要新闻;皮里耶公司股市行情立即刹住下跌势头,而且回升6.3%,不仅保护了企业形象和信誉,而且更提高了企业知名度,起到了比2亿多法郎做广告更大的宣传效果。
皮里耶矿泉水公司处理美国市场矿泉水含苯量超标事例,充分说明了无形质量损失是头等重大的损失,其损失代价,甚至是不可估量的。
有形质量损失应通过核称质量成本中的外损失成本及质量损失率来控制。
质量损失率是外损失成本之和与企业净产值之比,它是质量指标体系中一项重要的经济性指标,其计算公式为式中:F——质量损失率;C1——部损失成本,万元;C2——外部损失成本,万元;P J——工业净产值,万元。