铝合金压铸技术ppt课件
压铸成型工艺PPT课件
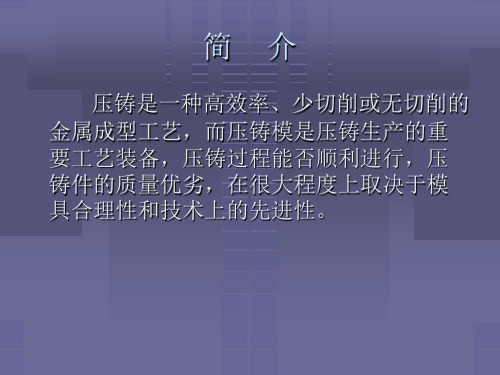
▪ 压铸温度
2)压铸模的预热温度与工作温度
压铸前,为了有利于金属液的充填、成 型和保护压铸模具、便于喷涂涂料,需要 将压铸模具加热到某一温度,这一温度即 为压铸模具的预热温度。
生产中,应将压铸模具的温度控制在一 定的范围内, 这一温度称为压铸模的工作 温度。
▪ 压铸时间
压铸时间包括填充、保压及压铸件在压铸模 中的留模时间。
▪ 压铸机和压铸模具价格昂贵,不宜小批量
生产。
金属压铸的应用范围
▪ 压铸是近代金属加工工艺中发展较快的一
种高效率、少切削或无切削的金属成型方 法,能成型形状复杂、尺寸精确、轮廓清 晰、表面质量及强度、硬度都较高的压铸 件,故应用广泛。目前,铝合金压铸件产 品最多,其次为锌合金压铸件。
▪ 应用场合
压铸工艺
从经济角度考虑,选择比压时,应根据压铸 件的形状、尺寸、壁厚、合金的性质、温度、浇 口的排溢系统等来确定,一般在保证压铸成型和 使用要求的前提下,宜选用较低的比压。
▪ 胀型力
压铸过程中,充填结束并转为增压阶段 时,在比压的作用下,金属液作用在型腔 壁和分型面上的压力称为胀型力。
胀型力的大小是为压铸件初选压铸机型 号及对板进行强度和刚度校核的重要参数。
3)留模时间
留模时间是指从保压时间终了到开模推 出压铸件的时间。
▪ 压铸用涂料
压铸过程中,为了避免压铸件与压铸具 的黏合,减少从模具型腔中推出压铸件的 阻力,需喷涂润滑材料和稀释剂,这样的 混合物称为压铸涂料。
简介
压铸是一种高效率、少切削或无切削的 金属成型工艺,而压铸模是压铸生产的重 要工艺装备,压铸过程能否顺利进行,压 铸件的质量优劣,在很大程度上取决于模 具合理性和技术上的先进性。
金属压铸过程
压铸技术培训(PPT7)

现代阶段
近年来,随着计算机技术和数值模拟 技术的发展,压铸技术不断实现创新 ,向着高精度、高质量、高效率的方 向发展。
2024/1/28
5
压铸技术应用领域
汽车工业
电子工业
压铸技术在汽车工业中应用广泛,如发动 机缸体、缸盖、曲轴箱、刹车系统等零部 件的制造。
பைடு நூலகம்
压铸技术可用于制造电子产品的外壳、散 热器、连接器等零部件。
压铸技术培训 (PPT7)
2024/1/28
1
目录
2024/1/28
• 压铸技术概述 • 压铸工艺及设备 • 压铸材料选择与性能要求 • 压铸件设计要点与优化方法 • 生产过程中的质量控制与检测手段 • 环境保护、安全生产与节能减排举措 • 总结与展望
2
2024/1/28
01
CATALOGUE
压铸技术概述
2024/1/28
压铸工艺原理
利用高压将熔融金属压入模具型 腔,并在压力下凝固成型,从而 获得所需形状和性能的压铸件。
压铸工艺流程
合金熔炼、压铸机准备、模具准 备、压铸生产、压铸件后处理。
8
压铸机类型与结构
压铸机类型
热室压铸机、冷室压铸机。
压铸机结构
合模机构、压射机构、液压系统、电气控制系统等。
2024/1/28
13
材料选用原则及注意事项
根据压铸件的使用环境和性能要求选 择合适的压铸合金材料。
注意材料的可回收性和再利用性,以 降低生产成本和减少环境污染。
2024/1/28
考虑材料的成本、加工难度和环保性 等因素,选择经济合理的材料。
在使用新材料或改变材料成分时,需 进行充分的试验和验证,确保压铸件 的质量和性能符合要求。
压铸技术培训课件

压铸分类
根据压铸机的类型和工作原理,压铸可分为热室压铸和冷室压铸两大类。热室 压铸主要用于锌、镁等低熔点金属的成型,而冷室压铸则适用于铝、铜等高熔 点金属。
2024/1/25
4
压铸技术发展历程
2024/1/25
早期阶段
压铸技术起源于19世纪初,最初主要用于印刷业和艺术品 制造。随着工业革命的推进,压铸技术逐渐应用于机械制 造领域。
。
模具锁模力控制
确保模具在压铸过程中保持紧 密闭合,防止飞边和毛刺产生
。
氮气压力控制
对于采用氮气辅助压铸的工艺 ,需要精确控制氮气压力,以 获得理想的压铸件内部质量。
2024/1/25
17Βιβλιοθήκη 产品质量检测与评估方法外观检查
通过目视或借助放大镜等工具检查压 铸件的表面质量,如毛刺、飞边、冷 隔等。
金相分析
通过观察压铸件的金相组织,了解其 显微结构和相组成,评估其冶金质量 和热处理效果。
01
02
尺寸测量
使用卡尺、千分尺等测量工具对压铸 件的尺寸进行精确测量,确保符合设 计要求。
03
力学性能检测
对压铸件进行拉伸、弯曲、冲击等力 学性能测试,评估其机械性能是否达 标。
05
04
无损检测
采用X射线、超声波等无损检测技术对 压铸件内部缺陷进行检测和评估。
定期开展安全检查和 隐患排查,及时消除 安全隐患,确保生产 安全。
2024/1/25
建立健全安全生产规 章制度,明确各级管 理人员和操作人员的 安全职责。
24
设备操作安全注意事项
操作人员必须熟悉设备的性能 、结构、原理和操作规程,严 禁违章操作。
2024/1/25
设备运行过程中,严禁触摸运 动部件,防止发生机械伤害事 故。
压铸工艺 ppt课件
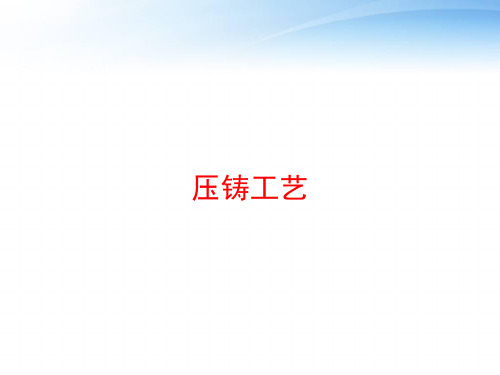
19
压铸介绍
20
合金的成型制程
铸造方法一般可分为:
(1)重力浇注 (Gravity Die casting) (2)低压铸造 (Low pressure die casting) (3)半固态铸造(Thixo-casting) (4)半熔注塑法,触变成形(Thixo-molding) (5) 压铸 (High pressure die casting)-
(Hot Chamber,Cold Chamber 热室法 冷室法)
21
热室法 (Hot Chamber)
热室机的射出系统硬件 (柱塞、套筒或鹅颈管) 为浸炮在熔融金属液中, 射出时藉由油压驱动柱塞下压而将金属液射入模穴中冷却得到铸件。因铸造 压力较,比压要求 (约300-400 bar)(70~350kg/cm2),故适合熔点低,肉薄成 品小之铸件,例如3C类之产品。
机台数量 36
18
0
0
16
0
0
0
0
0
镁
镁
镁
镁
镁
镁
铝
铝
锌
锌
合计:
125T 150T 200T 350T 500T 600T 125T 250T 75T 100T
54
69
9
11
39
16
29
1
2
8
共计: 238
5
冷室机台特性
1入模腔成型。
2、冷室特性为密度及硬度高,使用在 气油压,防漏油、漏气。
18
提升可动率(Ⅱ)
一、消除因设备故障造成的间隙停机(充分落实定期维护保) 二、缩短模具(铸造.加工)的更换时间,平均应在1小时
铝合金压铸工艺基础知识培训PPT课件

二、压铸过程主要工艺参数
3. 3 快压射速度的作用和影响
快压射速度对合金机械性能的作用和影响,提高压射 速度,动能转化为热能,提高了合金熔液的流动性,有利 于消除流痕,冷隔等缺陷,提高了机械性能和表面质量, 但速度过快时,合金熔液呈雾状和气体混合,产生严重裹 包气,机械性能下降。
第33页/共49页
C
椭圆中心详见局部视图
椭圆 2 (长轴 22mm,短轴 21.4mm) 椭圆 1 (长轴 15.6 mm,短轴 14.6mm)
第34页/共49页
三、压铸件设计
7.压铸件设计中的嵌入嵌件设计 压铸件中能铸入金属或非金属嵌件,主要为了提高局部的强度耐磨性或
形成难以成型的内腔,嵌件埋入金属的部分要设计防转和防止轴向移动的形 状同时要考虑嵌件放入模具的方便性和承受金属液冲击的稳定性
第22页/共49页
二、压铸过程主要工艺参数
4. 1 浇注温度的作用和影响
➢ 合金温度对铸件机械性能的影响。随着合金温度的提高 。机械性能有所改善,但超过一定限度后,性能恶化, 主要原因是:
➢ 气体在合金中的溶解度,随温度的升高而增大,虽然溶 解在合金中的气体,但在压铸过程中难以析出,影响机 械性能
3. 1 冲头速度与内交口速度的关系
➢ 根据连续性原理,在同一时间内金属流以速度V1流过 压室截面积为F1的合金液体积,应等于以速度V2流过 内浇口截面积为F2的合金液体积 F1室V1射=F2内V2内
➢ 因此,压射锤头的压射速度越高,则金属流经内浇口的 速度越高。
第17页/共49页
二、压铸过程主要工艺参数
三、压铸件设计
3.压铸件的圆角设计 铸件除有特殊配合要求的地方,尽量所有的部位都设计圆角,
铝合金铸造实用技术(15%) ppt课件
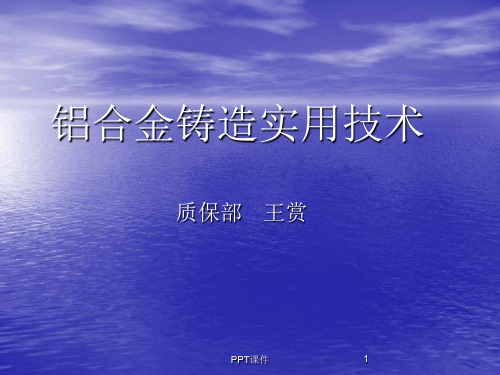
20~100 150±5 2 ~4
℃水
空冷
用于要求较高 强度和塑性的 零件
T6 淬火+完全人 535±5 2~6
工时效
20~100 200±5 3~5
按造型材料分:
• 砂型铸造 • 硬模铸造 • 熔模铸造 • 实型铸造 • 壳型铸造 • 其它精铸
按铸型受力情况分:
• 压力铸造 • 挤压铸造 • 低压铸造 • 真空吸铸 • 离心铸造
PPT课件
3
2、正确选择铸造方法应从以下三方 面考虑:
• 零件的使用性能 • 零件的铸造工艺性能 • 经济的合理性
PPT课件
(2)不承受载荷或承受轻微载荷且没有特 殊物理性能和使用要求的III类铸件, 经用户同意,可不进行成分分析。
PPT课件
24
2、供应状态
铸件供应状态分为两种:铸态和热 处理状态,一般由设计部门在图样中 规定。
PPT课件
25
铸造合金的热处理规范
代
淬火
时效
号 合金状态 加热温度 保温时间 冷却
(℃)
(h)
PPT课件
8
4、为防止和消除铸件在冷却,热处理和 机械加工过程发生变形和挠曲,应设 置合理的加强筋。
PPT课件
9
5、根据铸件的复杂程度,尺寸大小确定 适当的最小壁厚,铸造圆角,最小铸 孔和铸造斜度。
PPT课件
10
6、铸件设计应尽量较少加工表面,减少 机械加工量,这样可以保存铸件表面 的细结晶层。
介质
加热温度 保温时间
(℃)
(h)
冷却 介质
用途
F
铸态
不承受载荷的 零件
T1 人工时效
175±5 3~5
《压铸基本知识》课件

压铸技术逐渐应用于航空航天领域,如飞机零部件、卫星结构件等 。
环保要求
1 2
环保法规
随着全球环保意识的提高,各国政府对压铸行业 的环保法规日益严格,要求企业采取有效措施降 低环境污染。
节能减排
压铸企业应积极采取节能减排措施,如余热回收 、废弃物再利用等,以降低能耗和减少排放。
3
绿色生产
项参数。
02
操作过程
按照工艺流程,依次完成合模 、填充、增压、保压、开模等 步骤,确保压铸件的质量和稳
定性。
03
注意事项
注意安全操作,避免烫伤和机 械伤害,同时要定期维护和保 养设备,确保设备的正常运行
和使用寿命。
03
压铸模具
模具设计
03
模具结构设计
分模面选择
浇注系统设计
根据产品需求,设计合理的模具结构,确 保产品成型效果和生产效率。
推广绿色生产技术,使用环保材料和工艺,从源 头减少污染物的产生,促进压铸行业的可持续发 展。
THANKS
模具维护
定期检查
维修与更换
定期对模具进行检查,确保其处于良 好状态。
Hale Waihona Puke 对于损坏的模具部件,应及时进行维 修或更换。
保养与润滑
定期对模具进行保养和润滑,延长其 使用寿命。
04
压铸工艺
压铸温度
压铸温度
压铸过程中,模具和金属液的温 度是影响压铸件质量的重要因素 。合适的温度可以提高金属液的 流动性,减少气孔和裂纹等缺陷
《压铸基本知识》ppt课件
目录
• 压铸简介 • 压铸机 • 压铸模具 • 压铸工艺 • 压铸产品缺陷及防止措施 • 压铸行业发展趋势
铝合金铸造基础知识PPT课件
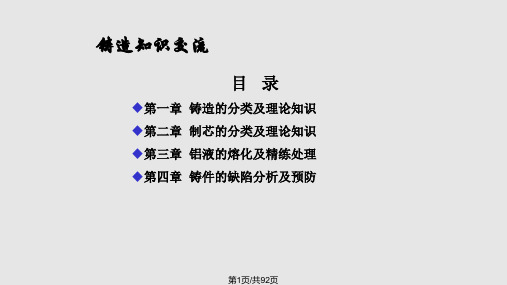
铸造培训讲义
第一章 铸造的分类 及理论知识
第2页/共92页
铸造的分类 按照铸造工艺的不同,一般将铸造
分为三类: ✓金属型铸造 ✓低压铸造 ✓压力铸造
第3页/共92页
金属型铸造
金属型铸造:金属液(铝液)用重力浇注法浇入金 属型,以获得铸件的一种铸造方法。 由于铸型(模具)可以反复使用很多次,故有永久 型铸造之称。也曾经有过硬模铸造的称谓。 金属型铸造已被广泛地用于生产铝合金铸件,如发 动机的气缸盖、活塞、轮毂和各种壳体。 代表产品:五菱B11/12D缸盖
低压铸造
c)增压、保压 待金属液(铝液) 充满型腔后,增 大气压,型腔里 的金属液(铝液) 在一定压力下凝 固成形。
第11页/共92页
低压铸造
d)卸压、冷却 最后卸除压力, 未凝固的金属液 (铝液)回落到 坩埚中,冷却后 开型便得到所需 的铸件。
第12页/共92页
低压铸造
低压铸造的优点:
1.金属液(铝液)是自下而上平稳充填铸型,且型腔 中液流方向与气体排出方向一致,因而避免金属液 (铝液)对型壁和型芯的冲刷、卷气等,提高铸件质 量;
第28页/共92页
型砂的结构
原砂是骨干材料,占树脂砂总质量的99﹪;一方 面它为坭芯提供了必要的耐高温性能和热物理性能; 另一方面原砂砂粒能为坭芯提供众多孔隙,保证坭 芯具有一定的透气性。 树脂(粘结剂)起粘结砂粒的作用,以粘结薄膜形 式包覆砂粒,使树脂砂具有必要的强度和韧性 添加剂是为了改善坭芯所需要的性能而加入的物质。 如改善坭芯的起模性能。
第38页/共92页
壳芯制芯
壳芯制芯的缺点: (一)壳芯表面易疏松 覆膜砂流动性差; 排气不当,在深凹处疏松和缺肉的,多是排气不好; 射砂压力太低; 射砂时间太短; 覆膜砂所使用的原砂太粗。
压力铸造工艺介绍ppt课件
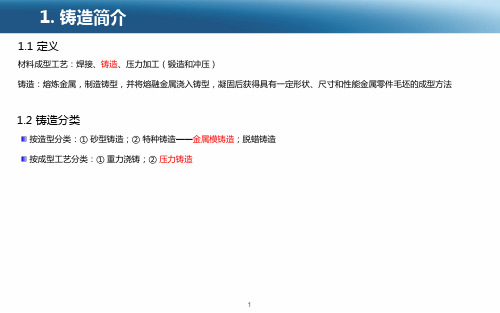
液态金属充型速度高,流态不稳定,铸件易产生气孔 设备费用昂贵,压铸机、熔化炉、保温炉、压铸模等费用都很昂贵 高熔点合金(铜、铁等),压铸模寿命短
2
3.压铸工艺三大要素
压铸工艺的三大要素分别是:压铸合金;压铸机;压铸模 压铸工艺则是将三大要素作有机的组合并加以运用的过程,使各种工艺参数满足压铸生产的需要。
1. 铸造简介
1.1 定义
材料成型工艺:焊接、铸造、压力加工(锻造和冲压) 铸造:熔炼金属,制造铸型,并将熔融金属浇入铸型,凝固后获得具有一定形状、尺寸和性能金属零件毛坯的成型方法
1.2 铸造分类
按造型分类:① 砂型铸造;② 特种铸造——金属模铸造;脱蜡铸造 按成型工艺分类:① 重力浇铸;② 压力铸造
3
3.压铸工艺三大要素
主要压铸合金 铝合金
锌合金
镁合金 铅锡合金 铜合金
浇铸温度 650~680℃
420~440℃
640~680℃ 200℃左右 900~980℃
特点及性能
1. 密度低,可生产要求减轻质量的零部件 2. 强度高,塑性好 3. 抗氧化腐蚀性能好
1. 良好的压铸特性:容易压铸形状复杂,尺寸精度高的产品 2. 抗拉强度高和硬度高,冲击韧性和伸长率较好 3. 良好的加工性能:产品表面,容易做各种表面处理 4. 生产高效
1. 密度低,比强度高 2. 流动性好 3. 减震性、磁屏蔽性能好
1.熔点低,流动性好,收缩小 2.可塑性好 3.铸件表面光滑,易做各种表面处理 因熔点高,模具寿命低,应减少使用
4
3.压铸工艺三大要素
3.2 压铸机
压铸机一般分为冷压室压铸机和热压室压铸机两大类。 冷压室压铸机按其压室结构和布置方式分为卧式压铸机和立式压铸机两种。
压铸工艺学课件(PPT 57页)
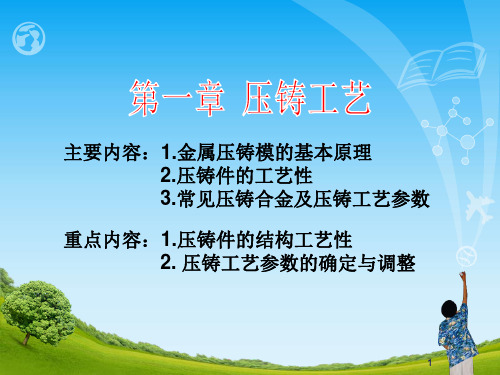
4.全立式冷压室压铸机的压铸过程
(2)冲头下压式
1 2
3
4 5 6 7
8 (余料)
1—压射冲头 2—压室 3—型腔 4—动模 5—定模 6—熔融合金 7—反料冲头
a)合模→熔融合金浇入压室
b)压射→反料冲头下降→熔融合金充满型腔
c)开模
d)冲头回程→推出压铸件
9
<压铸模、锻模及其他模具>
二.压铸生产的工艺特点
12
压铸模、锻模与其他模具
第一章 压铸工艺
Chapter2 The technology of die casting
重庆三峡学院机械工程学院
13
<压铸模、锻模及其他模具>
第二节 压铸件的工艺性
压铸件的工艺性包括以下三方面的内容: 压铸件的精度、压铸件的表面质量和压铸件的结构工艺性。
一.压铸件的精度
压铸工艺参数:是指压射压力、压射速度、浇注温度和 压铸模温度以及充填时间等工艺参数。
正确地选择和调整压铸工艺参数,是保证压铸件质量、 发挥压铸机的最大生产率和正确设计压铸模的依据。尤其 是压射压力、压射速度、浇注温度和铸模温度以及充填时 间等工艺参数合理选择,是生产合格压铸件的必要条件。
充填时间则是有关工艺参数的协调和综合的结果。
压铸过程循环图
2
<压铸模、锻模及其他模具>
二、压铸分类
热压室压铸机压力铸造 立式
冷压室压铸机压力铸造 卧式 全立式
3
<压铸模、锻模及其他模具>
压力铸造车间
4
<压铸模、锻模及其他模具>
1.热压室压铸机的压铸过程
1 2345
9 8 76
铝合金压铸件机加工工艺流程制作 ppt课件

ppt课件
8
3点组成一个平面
ppt课件
9
与C基准面平行
ppt课件
10
定位孔选取
• B)定位孔选取,这里叙述的定位孔是广义 的,部分产品用两孔定位,部分产品用侧 面定位,不管哪种方式,只要和定位面能 限制产品被加工工件6个自由度即可
• (1)部分产品在设计时,就规定压铸基准, 直接选取即可如图2所示,X,Y基准,X一点, Y两点,并是上面叙述的侧面定位
ppt课件
25
8)各个工序之间工时是否平衡
• 对于多工序产品,尽量避免工序之间工时不平衡, 否则加工过程中部分机床待机,造成机床浪费, 在制作工艺流程时一定注意
• A)对于公差大的加工位置,在能保证品质的情况 下,尽量分配到工时较少工序
• B)看多工序是否能安排在一台机床上 • C)工时较少工序能否安排在一台机床上 • D)对工时较多工序,看能否合并一些刀具,减
• 2)局部切削力较大的产品,需要增加辅助 支撑(如S3002/03M)见图C2
• 3.加工部位与定位点悬伸力臂太大的产品, 需要增加辅助支撑,见图C3
• 4.局部位置比较薄弱的产品,需要增加辅助 支撑,见图C4
ppt课件
17
图C1Βιβλιοθήκη ppt课件18图C1 (辅助支撑)
ppt课件
19
图C2(铣螺纹局部切削力大,增加辅 助支撑)
瓷等等选择 • 我个人认为刀具选择应遵循以下原则: • A)首要保证加工质量 • B)加工时间最短 • C)性价比好 • D)利于维修 • 下面以图1产品工艺流程讲解刀具选择
ppt课件
23
6)机床类型确定
• A)机床精度必须能保证产品精度 • B)机床工作台及各轴行程符合工件 • C)机床性价比好 • D)最好用现有机床
压铸工艺ppt课件
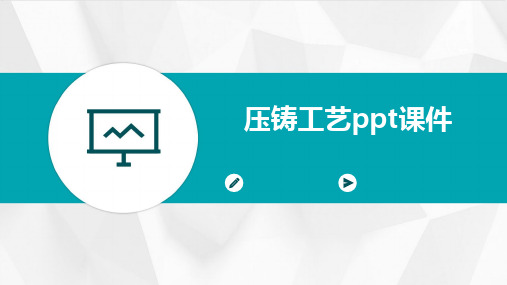
目录•压铸工艺概述•压铸设备与模具•压铸合金与熔炼•压铸工艺参数与操作•压铸件缺陷分析与防止措施•压铸工艺发展趋势与展望压铸工艺概述压铸定义压铸是一种金属成型工艺,通过高压将熔融金属注入模具型腔,并在压力下凝固成型,从而获得所需形状和性能的金属零件。
压铸工艺可获得高精度、高质量的金属零件,尺寸精度可达IT6-IT8级。
压铸机生产效率高,可实现自动化生产,提高生产效率。
压铸工艺可节约原材料,减少加工余量,降低生产成本。
压铸工艺可应用于各种金属材料的成型,如铝合金、锌合金、铜合金等。
高精度节约材料广泛应用高效率压铸定义及特点压铸工艺发展历程01早期阶段压铸工艺起源于19世纪初,最初用于制造印刷机零件和钟表零件等小型精密零件。
02中期阶段随着工业革命的推进和机械制造技术的进步,压铸工艺得到迅速发展,逐渐应用于汽车、摩托车、家电等领域。
03现代阶段近年来,随着计算机技术和数值模拟技术的发展,压铸工艺实现了数字化、智能化转型,提高了生产效率和产品质量。
汽车工业压铸工艺在汽车工业中应用广泛,如发动机缸体、缸盖、曲轴箱、刹车盘等关键零部件的制造。
摩托车工业摩托车工业中大量采用压铸工艺生产零部件,如车架、轮毂、发动机零件等。
家电行业家电行业中的许多零部件也采用压铸工艺制造,如洗衣机内桶、空调压缩机壳体等。
其他领域压铸工艺还应用于航空航天、兵器制造、仪器仪表等领域,为这些领域提供了高精度、高质量的金属零件。
压铸工艺应用领域压铸设备与模具压铸机类型及结构01压铸机类型热室压铸机、冷室压铸机02压铸机结构合模机构、压射机构、液压系统、电气控制系统等模具分型面的选择根据产品形状、尺寸精度、脱模斜度等因素确定分型面位置排气系统设计设置合理的排气槽和溢流槽,避免压铸件产生气孔和缩松等缺陷浇注系统设计包括内浇口、横浇道、直浇道等部分的设计,确保金属液充型顺畅冷却系统设计根据模具温度和产品要求,设计合理的冷却水道和冷却方式压铸模具设计原则模具材料及热处理常用模具材料01热作模具钢、冷作模具钢、塑料模具钢等热处理工艺02淬火、回火、表面强化处理等,提高模具的硬度、耐磨性和抗疲劳性能模具寿命与维护03通过合理的使用和维护,延长模具使用寿命,降低生产成本压铸合金与熔炼01020304铝合金密度小、强度高、耐腐蚀、良好的铸造性能和机械加工性能。
- 1、下载文档前请自行甄别文档内容的完整性,平台不提供额外的编辑、内容补充、找答案等附加服务。
- 2、"仅部分预览"的文档,不可在线预览部分如存在完整性等问题,可反馈申请退款(可完整预览的文档不适用该条件!)。
- 3、如文档侵犯您的权益,请联系客服反馈,我们会尽快为您处理(人工客服工作时间:9:00-18:30)。
浇口速度:熔汤通过浇口的速度
厚铸件 >5mm
浇口速度(m/sec) 15~20
一般铸件 2~5mm
20~30
薄铸件 1~2mm
30~40
柱塞的高速速度值计算: Vp=VgAg/Ap
其中:Vp柱塞速度; Vg浇口速度; Ag浇口面积; Ap柱塞面积
超薄件 <1mm
16
铝合金熔解
1.冷室机:熔解温度630~650℃ 2.压铸铝合金的熔解温度(For ADC-12熔点为
516~582℃),另加高50~70℃以防热损.
17
射出速度
射出依柱塞的运动速度可分为两个阶段:
>第一个阶段,柱塞是以低速前进将熔汤充满 料管到浇口的空间.
>第二个阶段,柱塞是以高速前进,以便将熔汤 高速射入模穴.
GD-AlSi12(Cu) GD-AlSi10Mg GD-AlMg9 ----GD-AlSi9Cu3 GD-AlSi9Cu3 -------------
6
压铸铝合金材料成份规范
编号
ADC-1
Cu
1.0
ADC-3 0.6max
ADC-5 0.2max
ADC-6 0.1max
ADC-10 2.0~4.0
13
熔汤在料管中的流动
1.柱塞速度小于临界速度料管的空气排不出 2.柱塞速度大于临界速度料管的空气包卷 3.柱塞速度等于临界速度料管的空气能排出
14
慢射阶段的临界速度( in/sec )
料 管 直 径 ( in )
1.00 1.25 1.50 1.75 2.00 2.25 2.50
50 11.3 12.6 13.8 15.0 16.0 17.0 17.9
份 Zn
0.5max 0.5max 0.1max 0.4max 1.0max 3.0max
9.6~12.0 9.6~12.0
0.3max 0.3max
1.0max 3.0max
16.0~18.0 0.45~0.65 1.5max
Fe
1.3max 1.3max 1.8max 0.8max 1.3max 1.3max
出铸件并取出→洒离型剂→合模→(进入下 一循环) 3.从时间上看,制程流程为:a.充填;b.凝固; c.铸件 取出;d.开模等待
11
压铸制程熔汤的流动方式
低速流动是连续性的 中速流动是断续的呈粗颗粒状 压铸是高速流动,进入型腔是呈雾状喷入
12
熔汤在模穴中的流动
1.熔汤通过浇口 2.高速喷入反弹 3.回包卷气
Mn
0.3max 0.3max 0.3max 0.4~0.6 0.5max 0.5max
Ni
0.5max 0.5max 0.1max 0.1max 0.5max 0.5max
Sn Al
0.1max 其余 0.1max 其余 0.1max 其余 0.3max 其余 0.3max 其余 0.3max 其余
1.3max 1.3max
0.5max 0.5max
0.5max 0.5max
0.3max 其余 0.3max 其余
1.3max 0.3max 0.3max 0.3max 其余
7
压铸概论
压铸机分冷室压铸机和热室压铸机二种: 1.冷室压铸机适合:铝合金和铜合金. 2.热室压铸机适合:锌合金,镁合金和锡铅合金.
CNS编号 JIS编号(H5302) AA/ASTM(1984) DIN1725(1986)
1种 3种 5种 6种 10种 10种Z 12种 12种Z 14种Z
ADC-1 ADC-3 ADC-5 ADC-6 ADC-10 ADC-10Z ADC-12 ADC-12Z ADC-14
A413 A360.0 518.0 515.0 B380.0 A380.0 383.0 383.0 B390.0
铝合金压铸技术
整理: 陈达福
1
课程内容
>压铸概论与压铸铝合金 >压铸制程条件与设定 >模具方案设计 >实例研讨
2
压铸铝合金
压铸用铝合金全世界超过3000种型号
3
压铸铝合金的基本要求
1.流动性好 2.收缩率.龟裂倾向小 3.等温凝固比率大,如此方可产生致密之表面化铸
肌,避免缩孔之危害 4.有一定之高温强度,顶出时才不致变形 5.常温下有足够强度,以利生产薄壁件 6.不易与模具起化学或物理反应,否则粘模,影响量
7.0 7.5
8.1
8.5 9.0
% 80 4.6 5.2
5.7 6.1
6.6
7.0 7.3
85 3.6 4.0
4.4 4.7
5.0
5.4 5.6
90 2.5 2.8
3.0 3.3
3.5
3.7 3.9
95 1.3 1.5
1.6 1.8
1.9
2.0 பைடு நூலகம்.1
15
压铸制程条件
>合金熔解
>射出速度 >高速切换位置 >铸造压力 >温度控制
8
铝合金压铸制程
铝合金压铸的过程首先将铝合金锭熔解, 然后将熔汤送至压铸机内,再将熔汤射入模穴 内,待铸件成形冷却后,开模,顶出铸件并取出, 然后对模具喷离型剂,合模后等待射出即完成 一个循环.
9
压铸制程特性
>高速充填 >充填时间很短 >高压 >熔汤和冷却速度快
10
铝合金压铸制程流程
1.合金熔解 2.将熔汤送至压铸机→射出→成形→开模→顶
ADC10Z
ADC-12
2.0~4.0 1.5~3.5
ADC12Z
ADC-14
1.5~3.5 4.0~5.0
化 Si
11.0~13.0 9.0~10.0 0.3max 1.0max 7.5~9.5 7.5~9.5
学成 Mg
0.3max 0.4~0.6 4.0~8.5 2.5~4.0 0.3max 0.3max
55 10.1 11.3 12.4 13.4 14.3 15.2 16.0
起 60 9.0 10.0 11.0 11.9 12.7 13.5 14.2
始 65 7.8
8.8
9.6 10.4 11.1 11.8 12.4
充
填 70 6.8
7.6
8.3 9.0
9.6
10.2 10.7
率 75 5.7 6.4
产 7.良好的被加工性和抗腐蚀性
4
压铸铝合金的种类
Al-Si合金 调质,高温强度,机械性质,耐蚀性 Al-Cu合金 热处理,精度要求 Al-Mg合金 机械性质,耐蚀性,机械加工,延性 Al-Si-Cu合金 Al-Si-Mg合金
5
各国压铸铝合金材料规范对照表
合金系
Al-Si系 Al-Si-Mg系 Al-Mg系 Al-Mg系 Al-Si-Cu系 Al-Si-Cu系 Al-Si-Cu系 Al-Si-Cu系 Al-Si-Cu系