轮对参数测量
轮对知识

货车车轴
B型
货车车轴
A型
货车车轴
C型
货车车轴
通过对车轴卸荷槽加工工艺研究 ,铁道部
2004年12月下文规定了新制RD2型车轴的B、D
车轮
车轴
一. 车
轴
.
车轴有滑动轴承车轴与滚动轴承车轴之分。 我国铁道车辆上使用的车轴,大多为圆截面的实心车轴。由于车轴各 部位的受力状况不同,其直径大小也不一样。 从材质上看,目前的车轴一般都是用 40 钢或 50 钢 —— 优质碳素钢 锻制而成。 从技术要求上看,车轴表面须锻造光滑平整,不得有起皮、裂纹、熔 渣、或其他危害性缺陷存在。
●
货车车轴
因RE2 型车轴载荷中心距短,增加了转向架结
构的设计难度,加上早期设计的197730型轴承比
较笨重,所以该车轴仅进行了装车运用试验而未
大量推广使用。
货车车轴
RE2A型车轴
1998年,开始设计 RE2A型车轴。设计进程 ——
货车车轴
A型
货车车轴
C型
货车车轴
B型
货车车轴
RE2A型车轴主要参数 商业运营速度:120km/h ● 轴重:25t (245kN) ● 全长:2191mm ● 载荷中心距:1981mm ● 轴肩距:1731mm ● 轴颈长度:230mm ● 载荷中心到轴颈根部距离:125mm ● 轴身长度:1228mm,突悬 ● 轴颈及防尘板座型式:3种
货车车轴
RE2B 型车轴轮对主要结构特点
1981 1761 (RE2A:1731)
轮对尺寸人工测量作业指导书
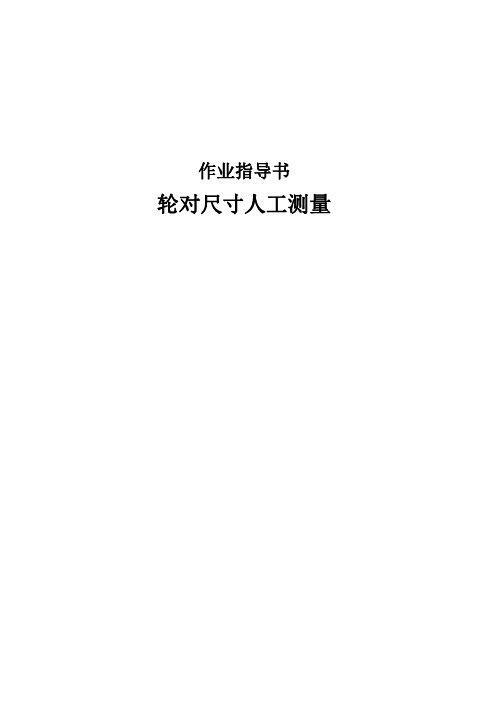
作业指导书轮对尺寸人工测量目录一、作业介绍 (4)二、工具物料 (5)1.工具清单 (5)2.物料清单 (5)三、作业流程示意图 (6)四、作业程序、标准及示范 (7)1.班前准备 (7)2.开工准备 (7)3.工序控制 (7)4.轮对尺寸人工测量作业 (8)一、作业介绍作业地点:动车所检修库。
适用范围:适用于CRH2A统型动车组二级修轮对尺寸人工测量作业。
人员要求:取得《CRH岗位培训合格证》人员。
检修要求:轮对检查、测量等。
符号说明::质检员过程质检;:质检员结果质检;:作业人员拍照留存;:作业人员摄像留存;:质检员拍照留存;:质检员摄像留存;:当心触电;:注意安全;:当心坠落作业分工:本项目检修由两名机械师分1、2号位进行作业,1、2号位相互作业过程互控,为质量互控小组。
二、工具物料1.工具清单序号名称规格型号单位数量备注1头灯通用型个22对讲机通用型个23钢板尺150mm个14轮径尺GF922-D型套1测量范围必须包含790-860mm5动车组车轮轮缘踏面检测量具LMA型第四种检测器把16LMA踏面样板LMA原型套17世达16件公制塞尺09402套18内距尺GF218(1345-1365mm)套19游标卡尺0-150mm个12.物料清单序号物料名称物料号单位数量备注1抹布张22防护手套副2二、作业流程示意图轮对尺寸人工测量作业开始检查,测量轮缘厚度、轮缘高度、轮径、内侧距、制动盘及闸片等数据完工整理穿戴劳保用品、清点作业工具检查作业准备反馈信息处理填写轮对尺寸人工测量记录单三、作业程序、标准及示范1.班前准备按规定穿戴好劳动保护用品,参加班前点名会。
2.开工准备检查作业工具车内工装设备、检测器具、工具清单,须齐全、状态良好,发生异常情况时通知工长处理。
3.工序控制确保轮对尺寸人工测量作业在规定时间内全部检查完毕。
4.轮对尺寸人工测量作业序号作业项目作业内容作业标准作业工具作业材料作业图示1工前准备准备作业工具及作业材料;确认安全条件。
浅谈电客车轮对参数的几种测量方法

浅谈南京地铁电客车轮对参数的几种测量方法张晓明、吕震洲南京地铁运营分公司检修一中心江苏南京 210012摘要:对电客车轮对几个关键参数值含义以及目前南京地铁采用的几种测量方法进行简要阐述和分析。
关键词:电客车,轮对, QR,轮缘高,测量方法1 轮对参数概述电客车轮对承载着车辆的全部重量,运行时承受着从车体以及钢轨两方面传来的静、动作用力,受力复杂,是影响车辆运用安全的关键部位。
轮对参数包括轮对内侧距L,轮径尺寸D,轮缘高度Sh,轮缘厚度Sd,轮缘综合值qR。
目前南京地铁一号线采用的轮对参数测量技术标准是:1350mm<L<1356mm;D>770mm;26mm<Sh<32mm;22mm<Sd<33mm;6.5<qR<12.7;同一轴轮径差<2mm,同一转向架轮径差<4mm,同一节车轮径差<7mm等。
如果轮对参数尺寸超标或者踏面有擦伤、剥离超限等现象,需按照要求进行镟轮,满足车辆轮对参数技术标准的要求。
本文重点对轮缘高度Sh,轮缘厚度Sd,轮缘综合值qR三个轮缘参数进行分析。
正常情况下,车辆直线运动产生的蛇形运动对轮缘磨耗的影响并不大。
而下面两种情况容易造成轮缘的较大磨耗:一是车辆通过曲线或道岔时,轮对承受横向作用力与外轨内侧面摩擦造成轮缘磨耗;另一种情况是轮对原因或转向架组装不正,使轮对与钢轨间的相对位置不正常,造成轮对偏向一侧,从而导致轮缘发生偏磨。
轮缘磨耗会造成轮缘高度Sh,轮缘厚度Sd,轮缘综合值qR发生变化。
轮缘厚度磨耗变小,强度会下降,当轮对通过曲线或作蛇形运动时,轮缘受到来自钢轨横向力作用,可能会发生崩裂缺损,造成行车事故。
另外一方面,轮缘厚度变小,会影响到车轮与钢轨的安全搭载量,也造成安全隐患。
轮缘高度和轮缘综合值qR的变化是轮缘垂直磨耗的直观体现。
轮缘垂直磨耗过限时,轮缘根部与钢轨内侧面形成平面接触,没有弧形,严重时可能造成脱轨事故。
南京地铁电客车轮缘综合值(qR)测量问题初析

南京地铁电客车轮缘综合值(qR)测量问题初析南京地铁电客车轮缘综合值(qR)测量问题初析吴井冰摘要:介绍了南京地铁电客车轮对检修规程,重点分析了车轮轮缘外形尺寸对车辆运行性能的影响。
对比分析了用于检查车轮爬轨脱轨安全性的两种指标——轮缘综合值qR与垂直磨耗。
最后对南京地铁在qR测试方面存在的问题进行了初步的探讨。
关键词:轮对检修,轮缘磨耗,轮缘综合值qR,垂直磨耗1 概述轮对承担着车辆的全部重量,车辆在钢轨上高速运行时轮对承受着从车体与钢轨两方面传递来的各种静、动作用力,受力复杂,它是影响车辆运用安全的关键部位。
南京地铁电客车的正常维修按照技术规程对车辆尤其是走行部分的各类部件及尺寸进行全面检查测量。
对轮对各类尺寸,如轮对内侧距、轮径尺寸、轮缘高度、轮缘厚度、轮缘综合值、轮径差等测量的技术标准如表1所示:表1 轮对检修技术标准轮对内侧距L 轮径尺寸D 轮缘高度Sh 轮缘厚度Sd 轮缘综合值qR 轮径差 1353mm770mm 26mm 2 轮缘磨耗与车辆脱轨安全性轮缘磨耗形式车辆在正常的工作条件下,轮缘的磨耗并不严重,轮缘只在车辆通过曲线和道岔时,才因承受水平力的作用,与外轨内侧面摩擦而产生磨耗。
在直线区段,轮对蛇行前进,轮缘磨耗并不大。
如果轮对踏面磨耗严重或转向架组装不正,使轮对与钢轨间的相对位置不正常,则轮对易偏于线路一侧,使轮缘生产偏磨。
轮缘磨耗有以下三种形式:即轮缘厚度减小、轮缘顶部形成锋芒及轮缘垂向磨耗。
轮缘磨耗过甚时,1会产生如下不良后果:轮缘厚度磨耗变薄后,强度下降,当轮对通过曲线或作蛇行运动时,轮缘在来自钢轨水力的作用下,会导致崩裂缺损,甚至会造成行车事故。
同时,车轮与钢轨的安全搭载量是根据轨距和车轮内侧距以及轮缘厚度等因素而定的,如果轮对的一侧车轮轮缘磨损过薄,则会影响一侧车轮与钢轨的安全搭载量。
轮缘形成锋芒后,在轮对通过道岔时,可能挤开尖轨而造成脱轨事故,所以轮缘磨损成锋芒时,必须更换轮对。
机车车辆轮对内距尺检定装置计量比对

·17·2021年1月(总第411期)第49卷Vol.49第1期No.1铁道技术监督RAILWAY QUALITY CONTROL计量工作MEASUREMENT WORK收稿日期:2020-05-15作者简介:武文君,工程师;孙涛,工程师;李晓峥,工程师;李明旺,助理工程师0引言机车车辆轮对内距尺(以下简称“内距尺”)是一种专门测量铁路机车车辆轮对内侧距离的铁路计量器具,在车辆检修过程中广泛使用。
内距尺量值准确度直接影响轮对检修质量,关系到行车安全。
为保障中国铁路太原局集团有限公司(以下简称“太原局”)内距尺量值传递得准确一致,掌握太原局内距尺检定工作现状及技术水平,开展内距尺检定装置计量比对(以下简称“比对”)工作。
1比对定义在JJF 1001—2011《通用计量术语及定义》中,关于“比对”的定义为“在规定条件下,对相同准确度等级或指定不确定度范围的同种测量仪器复现的量值之间比较的过程”[1]。
具体讲,比对是指在规定时间范围内,由2个或2个以上实验室,按照预定条件,对同一个性能稳定的传递装置实施测量,并且分析测量结果量值,以确认量值间的一致程度和实验室测量结果是否在要求的范围内,最终判断实验室量值传递是否准确的一种活动。
2比对方案2.1比对实验室比对实验室由主导实验室和参比实验室组成。
2.1.1主导实验室主导实验室是在比对中起主导作用的实验室[2]。
主要负责:①制定比对方案;②提供传递装置,并为其赋予参考值、确定传递方式;③保障传递装置在传递过程中的安全,以及数据的准确可靠和稳定;④汇总试验数据,分析比对结果,完成比对报告;⑤遵守与比对相关的保密规定;⑥监督比对进程,解决比对中出现的问题。
2.1.2参比实验室参比实验室是指参加比对的实验室。
主要负责:①在收到比对组织者发布的比对计划后,及时书面表明是否参加比对;②参与比对方案的讨机车车辆轮对内距尺检定装置计量比对武文君,孙涛,李晓峥,李明旺(中国铁路太原局集团有限公司计量所,山西太原030013)摘要:在阐述计量比对定义基础上,分别从比对实验室、比对项目和方法、比对路线和时间安排、传递装置、比对试验过程、参考值及其测量不确定度、参比实验室结果报告共7个方面,论述机车车辆轮对内距尺检定装置的计量比对方案。
铁路车辆轮对自动检测系统的研制

铁路车辆轮对自动检测系统的研制本文详细讲述了一种不靠外力能够自动测试铁路货车车轮的参变量同时完成计算机不靠外力就能够自动进行管制的体系,对其构造以及一些重要的技巧展开了比较具体的解析。
解析表述,这项体系使用工业掌控电脑、精密传感设备、摄像设备以及其他的各种各样的测试以及掌控技巧,对车轮的轮对外觀大小、轮对接触面擦伤、轮对以及标志板的标记、剥离和车轴等20多个方面的参变量完成了在线动态的测试,在很大程度上提升了工作效率以及测量精确度,完成了当前对车轮进行测量的落后方法、测试偏差大、工作量大等方面的困扰。
标签:铁路车辆;轮对;检测系统1 轮对测量系统结构及工作原理根据对轮对的检测技术以及车间的真实状况,检测装备使用龙门架经过样式的构造,图1所展现的图片就是其外貌。
主要的工作内容包括带动总成、进给总成、抬升降低总成、测量设备以及各种各样的测试传感设备等。
当轮对顺着车间的铁道到了对轮对进行测试的设备之后,经过各种各样的测试传感设备和每个配件的协助,不依靠外力自动实现对轮对的测试。
龙门架要使用全密封式的构造,从龙门架的外表上看不见任意的一根电线或者气管,整体构造简单明了、美观易懂。
图2是龙门架体系的构造图。
下面主要讲解其装备体系的主要构造和作用。
1.1 升降总成装置起落设备的用途是把轮对升起来,让它可以转动。
起落设备的工作原理是利用工业掌控电脑掌控电磁阀,使用气动装备把轮对升到最高的位置同时顶死。
起落设备两侧都有气缸,其功能是支撑轮对两侧的轴承同时能够升起轮对。
为了避免在轮对被升起时出现倾斜的现象,两侧的气缸同时工作。
轮对的中心轴就是测试的标准。
起落设备升起的速度要均匀,不能太快也不能太慢,太快会出现猛烈的冲击现象,太慢用的时间又会太长。
1.2 带转总成装置带转设备其用处就是带动轮对运转,从而对轮对进行测试。
其工作原理分为两个部分:首先,利用电脑、电磁阀以及气缸掌控带转设备升起,以便让主动以及从动的轮子和轮对进行接触产生转动摩擦现象;其次,利用电脑、变频设备、具备减速功能的交流电动设备M1和传动设备来完成对轮对滚动的掌控。
轮对故障动态检测系统测量精度分析
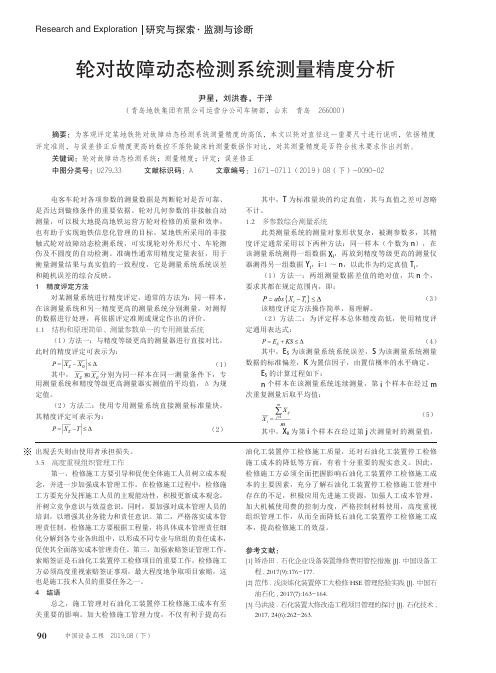
电客车轮对各项参数的测量数据是判断轮对是否可靠、 是否达到镟修条件的重要依据。轮对几何参数的非接触自动 测量,可以极大地提高地铁运营方轮对检修的质量和效率, 也有助于实现地铁信息化管理的目标。某地铁所采用的非接 触式轮对故障动态检测系统,可实现轮对外形尺寸、车轮擦 伤及不圆度的自动检测。准确性通常用精度定量表征,用于 衡量测量结果与真实值的一致程度,它是测量系统系统误差 和随机误差的综合反映。 1 精度评定方法
(1)方法一:两组测量数据差值的绝对值,共 n 个, 要求其都在规定范围内,即:
该精度评定方法操作简单,易理解。
(3)
(2)方法二:为评定样本总体精度高低,使用精度评
定通用表达式:
(4) 其中,ES 为该测量系统系统误差,S 为该测量系统测量 数据的标准偏差,K 为置信因子,由置信概率的水平确定。 ES 的计算过程如下: n 个样本在该测量系统连续测量,第 i 个样本在经过 m 次重复测量后取平均值:
用测量系统和精度等级更高测量器实测值的平均值,Δ 为规
定值。
(2)方法二:使用专用测量系统直接测量标准量块,
其精度评定可表示为:
(2)
其中,T 为标准量块的约定真值,其与真值之差可忽略 不计。
1.2 多参数综合测量系统 此类测量系统的测量对象形状复杂,被测参数多,其精
度评定通常采用以下两种方法:同一样本(个数为 n),在 该测量系统测得一组数据 Xi,再放到精度等级更高的测量仪 器测得另一组数据 Yi,i=1 ~ n,以此作为约定真值 Ti。
2017, 24(6):262-263.
铁路车辆轮对检测技术综述

第27卷第6期增刊2006年6月仪器仪表学报ChineseJournalofScientificInstrumentV01.27NO.6Jun.2006铁路车辆轮对检测技术综述*郭琼崔建英张志峰(北京交通大学理学院北京100044)摘要车轮对作为铁路车辆重要的走行部件,对于铁路的安全运输起着关键性的作用。
因此准确的检测车轮的磨耗状况是非常重要的。
本文从静态和动态检测两方面介绍铁路车辆轮对检测技术状况,简述了相关检测装置的原理及其优缺点。
关键词轮对静态检测动态检测OverviewofmeasurementmethodforwheelsofrailwayvehiclesGuoQiongCuiJianyingZhangZhifeng(schoolofScience,BeijingJiaotongUniversity,Beijing100044,China)AbstractWheelsplaykeyroleforthesafetyofrailwaytransportation,asimportantpartsoftherailwayvehicles.‘Fherefore,itiscrucialtodetecttheabrasionofwheelsaccurately.Thisarticledescribesthecurrenttechnologiesusedtodetectthewheelsofrailwayvehicles,intermsofstaticanddynamicdetection.Italsobriefstheworkprinciples,advantagesanddisadvantagesrelateddetectingsystems.KeywordsWheelsStaticdetectionDynamicdetection1引言车轮对作为铁路车辆重要的走行部件,对于铁路的安全运输起着关键性的作用。
落轮式轮对综合参数自动检测系统的开题报告

落轮式轮对综合参数自动检测系统的开题报告一、选题背景与意义在铁路行业中,落轮式轮对是列车运行过程中最关键的部件之一。
检测落轮式轮对的质量和运行状态,可以及时发现和排除各种安全隐患,保障列车运行安全和稳定。
目前国内外大部分铁路局和车辆制造厂都配备了相关的离线轮对检测设备,通过轮对处理线下轮轮轴轴承、车轮轮轮扣耳、轮径、新轮与旧轮悬挂软硬度等多项指标进行无损探伤实现轮对质量检测。
然而,离线检测设备存在一些缺陷。
首先,它们需要列车停靠专门的检测车间进行检测,而这又会影响列车的运行效率;其次,轮对检测需要手动操作,检测效率不高,检测结果的可重复性也无法得到保证;再次,无法对轮对的实际使用环境进行模拟和检测,因此无法提供真实的评估结果。
为了解决这些问题,研究人员开发了一种新型的自动化落轮式轮对综合参数检测系统。
该系统可以实现落轮式轮对在线检测,检测设备可以直接安装在铁路线路上,不需要让列车停靠在专门的检测车间,因此不会影响列车的正常运行。
此外,该系统利用了先进的技术,如机器视觉技术、声学信号处理技术、智能控制技术等,可以实现对各种轮对参数的自动检测和评估。
该系统的研发和应用将会在轨道交通行业中具有重要的意义。
其一,可以提高轮对检测的效率、准确性和可重复性;其二,可以降低列车维护和运行成本,同时提高列车的运行安全和稳定性;其三,可以促进我国轨道交通技术的发展和进步,同时增强我国铁路行业的核心竞争力。
二、项目内容和技术路线落轮式轮对综合参数自动检测系统是一种基于先进技术的智能化设备,可以实现落轮式轮对的在线自动检测和评估。
该系统主要由以下部分组成:1、采集子系统:该子系统可以对落轮式轮对进行采集,包括图像、声音和振动等多种数据。
其中,图像采集主要利用了机器视觉技术,可以对轮对的外观形态、轮胎磨损程度、轨距和轮径等参数进行测量和评估;声音采集主要利用了声学信号处理技术,可以对轮对的轮轴轴承进行检测,如轴承的声音、轴承的振动等;振动采集主要利用了结构动力学理论,可以对轮对的悬挂系统进行评估,如悬挂软硬度等。
基于图像处理的列车轮对参数检测方法的研究及系统设计(精)

中国农业大学硕士学位论文基于图像处理的列车轮对参数检测方法的研究及系统设计姓名:张红波申请学位级别:硕士专业:计算机应用技术指导教师:叶海建20040501中国农业大学研究生毕业论文摘要摘要列车轮对作为重要的可互换行走部件,对列车安全{亍驶起着关键性的作用。
目前,我国列车轮对的参数检测仍停留在手工测量阶段,技术落后、工作效率低。
而日本、美国等国在轮对自动检测方面进行了大量的研究,并研制出各种类型的检测装置,产生了巨大的经济效益。
随着我国r业控制技术领域的巨大进步和市场的开放,给计算机控制技术、信息技术在铁路系统的应用带来了前所未有的机遇。
本文介绍了一种应用CCD(ChargeCoupleDevice的缩写,称为电荷耦合器件)图像测量技术实现列车轮对外形尺寸非接触检测的方法,并在此基础上完成了“列车轮对参数检测装置”软件系统的研制。
本文阐明了型像的分通道自动采集过程,以及对采集到的原始图像进彳j:预处理过程,逃剑图像去噪声的目标,本课题采用了阈值分割中迭代阀值和闽值插值相结合的方法.Sobel算r、LoG算子边缘检测算法,基于数学形态学的膨胀运算子进行边缘断点连接以及目标提取中的投影法和边缘跟踪方法,使得提取轮对图像边缘达到测量精度的要求。
对系统进行标定时,采抖j了非线性模型.提高了幽像的测量精度。
同时对测量结果的精度进行了试验验证和分析,满足』’测量的要求。
本课题软fl。
存Windows2000系统上开发,实现了基于图像处理技术的轮对参数检测,完成了预期的H标,各项功能都满足了系统要求,软件的稳定性也得到了测试。
关键词:轮对,北接触检测,图像处理,图像分析。
‘,1AbstraetTrainwheelsetistheodeofmostimportantinter-changeablecomponentsinthevehicle,playskeyroleinsafetyofrailwaytransportation,butinourcountry,thewheelisstillmeasuredusinghandsleadinglowefficencyIndevelopedcountriessuchasUS,Japan.AdvancedresearchhasbeendoneandmanyMeasurementEquipmentshasbeendeveloped,thushighefficiencyandeconomics.Withthedevelopmentoftheindustrialcontroltechnologyandinformationtechnology,RailwaytransportmeetsGreatchallenges.Thispapermainlyintroducedannon—contactmeasurementofwheelsetdimensionsusingCCDimagemeasuringtechniqueAndsoftwaresystemoftrainwheelsetparametermeasuringdevicehasbeenresearchedThispaperclarifiesimagecollectautomaticallyprocessofmulti-channels,andpre—processingprocessoforiginalimageinordertonoisereduction.Inimageprocessing,methodasfollowswillbeintroducedinthispaper:amethodcombiningimagethresholditerativesegmentationwiththresholdinterpolation,edgedetectionoperatorSobelandLoGedgelinkingmethodusingdelationoperatorbasedonmathematicalmorphology,usingboundarytrackingandprojectionmethodinedgedistillprocess.Throughthismethod,measurementofwheelsetwillbemetprecisiondemand.Insj7stemstandardizationprocessing,thispaperadoptsDon—linearitymodel,andimpovemeasurementprecisionFinally,measurementresultprecisionpassestrialvalidatationandanalysis,andmeetrequestofmeasurement.SoftwareofthisprojectdevelopmentontheWindows2000,wheelsetparametermeasurementbasedOnimageprocessinghasrealized,allfunctionsalsomeetsystemrequestandstabilizationofSOftwarehastesedKeywords:wheelset,non—contactinspect,imageprocessing,imageanalysis独创性声明本人声明所呈交的论文是我个人在导师的指导下进行的研究工作及取得的研究成果。
轮对参数测量
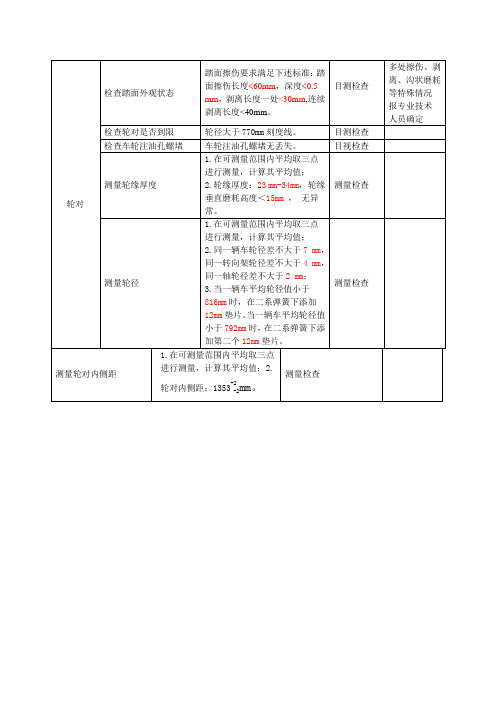
2.轮缘厚பைடு நூலகம்:23 mm-34mm,轮缘垂直磨耗高度<15mm,无异常。
测量检查
测量轮径
1.在可测量范围内平均取三点进行测量,计算其平均值;
2.同一辆车轮径差不大于7 mm,同一转向架轮径差不大于4 mm,同一轴轮径差不大于2 mm;
3.当一辆车平均轮径值小于816mm时,在二系弹簧下添加12mm垫片。当一辆车平均轮径值小于792mm时,在二系弹簧下添加第二个12mm垫片。
轮对
检查踏面外观状态
踏面擦伤要求满足下述标准:踏面擦伤长度60mm,深度0.5 mm,剥离长度一处<30mm,连续剥离长度<40mm。
目测检查
多处擦伤、剥离、沟状磨耗等特殊情况报专业技术人员确定
检查轮对是否到限
轮径大于770mm刻度线。
目测检查
检查车轮注油孔螺堵
车轮注油孔螺堵无丢失。
目视检查
测量轮缘厚度
测量检查
测量轮对内侧距
1.在可测量范围内平均取三点进行测量,计算其平均值;2.轮对内侧距:1353+2 -2mm。
测量检查
轮对参数检测与分析系统设计
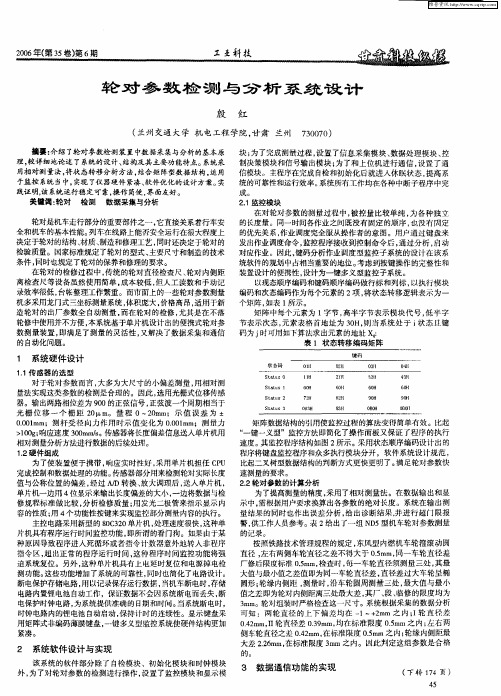
离检查尺等设备虽然使用简单, 成本较低 , 但人工读数和率很低 , 台帐整理工作繁重 。而市面上 的一些轮对参数测量 编码和次态编码作 为每个元素 的 2 , 项 将状态转移逻 辑表示为 一
机 多采用龙 门式三坐标 测量系统 , 体积庞大 , 价格高 昂 , 适用于新 个矩阵 , 如表 1 所示 。 造 轮对 的出厂参数全 自动测量 , 而在轮对 的检修 , 尤其是在不 落 矩 阵中每个元 素为 1 字节 , 高半 字节表示模块 代号 , 半字 低 轮修中使用并不方便, 本系统基于单片机设计出的便携式轮对参 节表示次态 , 元素表格 首地址 为 3 H, 0 则当系统 处 于 i 态且键 状 数 测量装置 , 即满足 了测量 的灵 活性 , 又解 决 了数据采集 和通信 码 为 ‘ i 时可用如下算法求 出元素 的地址 X 的 自动化 问题 。 表 1状 态转移 编码矩阵
> 0g响应速度 30 ms 传感 器将长度偏差信息送入单 片机用 10 ; 0m / 。 相对测量分析方法进行数据 的后续处理。
矩阵数据结构 的引用使监控过程 的算法变得简单有 效。比起 键一义型”监控方法 即简化 了操作 面板 又保证 了程序 的执 行 速度。 其监控程序结构如 图 2 所示 。 用状 态顺 序编码设计出的 采 12硬件组成 . 程序将键 盘监控程序和众多执行模块 分开 ,软件 系统设计规范 , 满足轮对参数快 为 了使装 置便 于携带 , 响应实时性好 , 采用单 片机担 任 C U P 比起二叉树 型数据结构的判断方式更快更明 了。 完成控制和数据处理 的功能 。 传感器部分 用来检测轮对实际长度 速测量的要求 。 值与公称位置 的偏差 , 经过 AD转换 、 大调理后 , / 放 送入单 片机 。 22轮对 参数的计算分析 - 单片机一边用 4位显示来输 出长度偏差 的大小 , 一边将数 据与检 为了提高测量 的精度 , 用了相 对测量 法 。在数据输 出和显 采 修规程标准做比较, 分析检修质量; 用发光二极管来指示 示内 示 中, 需根据用户要求换算 出各参 数的绝对长度 。系统在输 出测 量 结果 的 同时也作 出误差分 析 , 出诊 断结果 , 行超 门限报 给 并进 容 的性质 ; 4 用 个功能性按键来实现监控部分测量 内容的执行。 供工作人员参考 。 2给 出了一组 N 5型机车轮对参数测量 表 D 主控电路采用新型的 8C 2 单片机, 0 30 处理速度很快, 这种单 警 , 片机具有程序运行时间监控功能 , 即所谓 的看门狗 。如果 由于某 的记 录 。 按照铁路技术管理规程 的规定 , 东风型 内燃 机车轮 箍滚动 圆 种原 因导致程序进入死 循环或者指令计数 器意外地转入非 程序 左右两侧车轮直径 之差不得大 于 0 mm, . 5 同一 车轮直径差 指令区, 超出正常的程序运行时间, 这种程序时间监控功能将强 直径 , 迫 系统复位 。另外 , 这种单片机具有上 电延时复位和 电源掉 电检 厂修后 限度标准 0 m , . m 检查 时 , 5 每一车 轮直径须测量 三处 , 最 其 直 测功 能。 这些 功能增加 了系统 的可靠性 , 同时也简化 了电路设计 。 大值 与最小值之差值即为同一 车轮 直径差 , 径差过大车轮呈椭 轮缘 测量时 , 沿车轮圆周测虽 三处 , 大值与最 小 最 断电保护存储电路, 用以记录保存运行数据, 当机车断电时, 存储 圆形 ; 内侧距 , 电路 内置锂 电池 自动工作 ,保证数据不会 因系统 断电而丢失 , 断 值之差 即为轮对内侧距离三处最大差 , 其厂 、 、 段 临修 的限度 均为 电保护 时钟 电路 , 为系统提供准确 的 日 期和时间。 当系统断电时 , 3 m。轮刘组装时严格 检查 这一 尺寸 。系统根据采集 的数据 分析 m 1~ 2 m a I 时钟电路内的锂 电池 自动启动 , 保持计时 的连续性 。显示键盘采 可 知 :两 轮赢 径 的上下偏 差 均在 一 + r 之 内 ; 轮 直径 差 04 r I . a I轮直径差 03 mm, 2m . 9 均在标 准限度 05 m之 内 ; 右两 .m 左 用矩阵式非编码薄膜键盘 , 多义 型监控 系统使硬件结构更加 一键 紧凑。 侧车轮直径之差 0 2 m, . m 在标准 限度 0 tn 内; 4 . r之 5 u 轮缘 内侧距最 大差 2 6 m, m 在标准 限度 3l 之 内。凶此判定这组参数是 合格 2 nl n
动车组轮对粗糙度在线测量方法研究

动车组轮对粗糙度在线测量方法研究摘要:较大轮对粗糙度给动车组带来安全性和稳定性的问题,本文介绍目前使用的地面静态和在线动态两种测试方法,对比其各自的优缺点,提出了新的测试方法-地面间接动态测试方法,该方法即能客观地反映粗糙度的真实结果和演变规律,又能不影响动车组日常运行,大大地提高了效率。
关键词:车轮;粗糙度;振动;静态;动态动车组以其速度快为最大优势的特点已经逐渐被人们接受。
行驶速度不断加快,使得动车组运行的安全问题也变得更加突出。
作为列车重要的旋转部件,轮对的质量问题是影响车辆运行安全的重要环节。
在实际运用过程中,由于恶劣的工作环境,加上滚动接触(轮轨型面及材质匹配)、转向架及车辆振动、频繁地牵引、制动及防滑操作等原因,导致运行一段时间后车轮踏面和轮缘磨耗加剧,产生擦伤、剥离等缺陷,同时型面也不再保持理想形状,形成了一些有规律的多边形现象。
无论是轮对缺陷、轮缘磨耗还是车轮非圆化都会加剧轮轨间的动态作用,产生更高频的异常振动,对车辆部件产生损坏,影响列车的运行安全,恶化乘座舒适性。
因此,及时、快速、有效地测量出轮对在运用过程中的关键参数(如粗糙度、不圆度等),掌握车轮的状况是非常重要的。
基于对动车组服役性能的调查,研究动车组轮对磨耗及动力学性能演变衰减的规律,青岛四方庞巴迪铁路运输设备有限公司(简称“BST公司”)对典型动车组开展相关的跟踪测试,包括地面静态测量、在线动态测试等。
从长期跟踪调查的角度来看,很多时候都要与动车组的维护作业相冲突,特别是在线动态测试,定期化的工作会给动车组使用部门造成一定影响。
通过对地面静态测试、在线动态测试的实践工作进行分析总结,我们发现,振动信号含有较大的信息量,对其从中进行相关参数或故障的特征信息提取是有效可靠的。
振幅可以反映故障的严重程度,频率可以体现故障的类型,振动相对其它信号处理起来直观,也比较成熟。
因此,我们基于以上考虑,提出在钢轨侧面上加装振动传感器来测试轮对关键参数或状态的方法。
南京地铁电客车轮缘综合值(qR)测量问题初析

南京地铁电客车轮缘综合值(qR)测量问题初析南京地铁电客车轮缘综合值(qR)测量问题初析吴井冰摘要:介绍了南京地铁电客车轮对检修规程,重点分析了车轮轮缘外形尺寸对车辆运行性能的影响。
对比分析了用于检查车轮爬轨脱轨安全性的两种指标——轮缘综合值qR与垂直磨耗。
最后对南京地铁在qR测试方面存在的问题进行了初步的探讨。
关键词:轮对检修,轮缘磨耗,轮缘综合值qR,垂直磨耗1 概述轮对承担着车辆的全部重量,车辆在钢轨上高速运行时轮对承受着从车体与钢轨两方面传递来的各种静、动作用力,受力复杂,它是影响车辆运用安全的关键部位。
南京地铁电客车的正常维修按照技术规程对车辆尤其是走行部分的各类部件及尺寸进行全面检查测量。
对轮对各类尺寸,如轮对内侧距、轮径尺寸、轮缘高度、轮缘厚度、轮缘综合值、轮径差等测量的技术标准如表1所示:表1 轮对检修技术标准轮对内侧距L 轮径尺寸D 轮缘高度Sh 轮缘厚度Sd 轮缘综合值qR 轮径差 1353mm770mm 26mm 2 轮缘磨耗与车辆脱轨安全性轮缘磨耗形式车辆在正常的工作条件下,轮缘的磨耗并不严重,轮缘只在车辆通过曲线和道岔时,才因承受水平力的作用,与外轨内侧面摩擦而产生磨耗。
在直线区段,轮对蛇行前进,轮缘磨耗并不大。
如果轮对踏面磨耗严重或转向架组装不正,使轮对与钢轨间的相对位置不正常,则轮对易偏于线路一侧,使轮缘生产偏磨。
轮缘磨耗有以下三种形式:即轮缘厚度减小、轮缘顶部形成锋芒及轮缘垂向磨耗。
轮缘磨耗过甚时,1会产生如下不良后果:轮缘厚度磨耗变薄后,强度下降,当轮对通过曲线或作蛇行运动时,轮缘在来自钢轨水力的作用下,会导致崩裂缺损,甚至会造成行车事故。
同时,车轮与钢轨的安全搭载量是根据轨距和车轮内侧距以及轮缘厚度等因素而定的,如果轮对的一侧车轮轮缘磨损过薄,则会影响一侧车轮与钢轨的安全搭载量。
轮缘形成锋芒后,在轮对通过道岔时,可能挤开尖轨而造成脱轨事故,所以轮缘磨损成锋芒时,必须更换轮对。
- 1、下载文档前请自行甄别文档内容的完整性,平台不提供额外的编辑、内容补充、找答案等附加服务。
- 2、"仅部分预览"的文档,不可在线预览部分如存在完整性等问题,可反馈申请退款(可完整预览的文档不适用该条件!)。
- 3、如文档侵犯您的权益,请联系客服反馈,我们会尽快为您处理(人工客服工作时间:9:00-18:30)。
测量检查
轮对
检查踏面外观状态
踏面擦伤要求满足下述标准:踏面擦伤长度60mm,深度0.5 mm,剥离长度一处<30mm,连续剥离长度<40mm。
目测检查
多处擦伤、剥离、沟状磨耗等特殊情况报专业技术人员确定
检查轮对是否到限
轮径大于770mm刻度线。
目测检查
检查车轮注油孔螺堵
车轮注油孔螺堵无丢失。
目视检查
测量轮缘厚度
1.在可测量范围内平均取三点进行测量,计算其平均值;
2.轮缘厚度:23 mm-34mm,轮缘垂直磨耗高度<15mm,无异常。
测量检查
测量轮径
1.在可测量范围内平均取三点进行测量,计算其平均值;
2.同一辆车轮径差不大于7 mm,同一转向架轮径差不大于4 mm,同一轴轮径差不大于2 mm;
3.当一辆车平均轮径值小于816mm时,在二系弹簧下添加12mm垫片。当一辆车平均轮径值小于792mm时,在二系弹簧下添加第二个12mm垫片。